Flowserve Worcester Controls 39 Series User Instructions
Add to my manuals
8 Pages
Flowserve Worcester Controls 39 Series, with its double-acting pneumatic quarter-turn valve actuator, provides precise control for industrial applications. Featuring a rugged design and modular construction, it allows for easy customization with various accessories, including limit switches, Namur proximity sensors, and integral solenoids. The ASI (Actuator Sensor Interface) enables simple two-wire connection and communication, making it suitable for both stand-alone and integrated systems.
advertisement
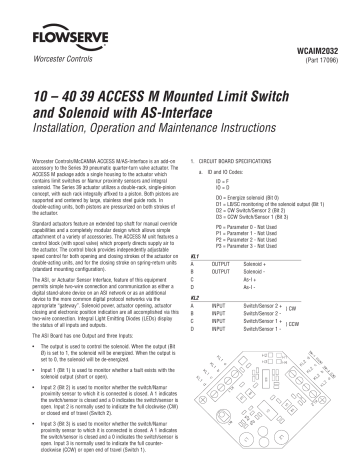
Worcester Controls
WCAIM2032
(Part 17096)
10 – 40 39 ACCESS M Mounted Limit Switch and Solenoid with AS-Interface
Installation, Operation and Maintenance Instructions
Worcester Controls/McCANNA ACCESS M/AS-Interface is an add-on accessory to the Series 39 pneumatic quarter-turn valve actuator. The
ACCESS M package adds a single housing to the actuator which contains limit switches or Namur proximity sensors and integral solenoid. The Series 39 actuator utilizes a double-rack, single-pinion concept, with each rack integrally affixed to a piston. Both pistons are supported and centered by large, stainless steel guide rods. In double-acting units, both pistons are pressurized on both strokes of the actuator.
Standard actuators feature an extended top shaft for manual override capabilities and a completely modular design which allows simple attachment of a variety of accessories. The ACCESS M unit features a control block (with spool valve) which properly directs supply air to the actuator. The control block provides independently adjustable speed control for both opening and closing strokes of the actuator on double-acting units, and for the closing stroke on spring-return units
(standard mounting configuration).
The ASI, or Actuator Sensor Interface, feature of this equipment permits simple two-wire connection and communication as either a digital stand-alone device on an ASI network or as an additional device to the more common digital protocol networks via the appropriate “gateway”. Solenoid power, actuator opening, actuator closing and electronic position indication are all accomplished via this two-wire connection. Integral Light Emitting Diodes (LEDs) display the status of all inputs and outputs.
The ASI Board has one Output and three Inputs:
• The output is used to control the solenoid. When the output (Bit
Ø) is set to 1, the solenoid will be energized. When the output is set to 0, the solenoid will be de-energized.
• Input 1 (Bit 1) is used to monitor whether a fault exists with the solenoid output (short or open).
• Input 2 (Bit 2) is used to monitor whether the switch/Namur proximity sensor to which it is connected is closed. A 1 indicates the switch/sensor is closed and a 0 indicates the switch/sensor is open. Input 2 is normally used to indicate the full clockwise (CW) or closed end of travel (Switch 2).
• Input 3 (Bit 3) is used to monitor whether the switch/Namur proximity sensor to which it is connected is closed. A 1 indicates the switch/sensor is closed and a 0 indicates the switch/sensor is open. Input 3 is normally used to indicate the full counterclockwise (CCW) or open end of travel (Switch 1).
C
D
KL2
A
B
B
C
KL1
A
D
1. CIRCUIT BOARD SPECIFICATIONS a. ID and IO Codes:
ID = F
IO = D
D0 = Energize solenoid (Bit 0)
D1 = LB/SC monitoring of the solenoid output (Bit 1)
D2 = CW Switch/Sensor 2 (Bit 2)
D3 = CCW Switch/Sensor 1 (Bit 3)
P0 = Parameter 0 - Not Used
P1 = Parameter 1 - Not Used
P2 = Parameter 2 - Not Used
P3 = Parameter 3 - Not Used
OUTPUT
OUTPUT
INPUT
INPUT
INPUT
INPUT
Solenoid +
Solenoid -
As-I +
As-I -
Switch/Sensor 2 +
Switch/Sensor 2 -
Switch/Sensor 1 +
Switch/Sensor 1 -
} CW
} CCW
Flow Control Division
Worcester Controls
2 b. Electronic and Mechanical data of printed circuit board:
• supply power for AS-Interface module, solenoid and switches/NAMUR proximity sensors via AS-Interface
• AS-Interface voltage 26.5 - 31.6 VDC
• maximum supply current including activated solenoid
125 mA
• operating temperature -25 to +70°C
• storing temperature -25 to +85°C
• printed circuit board dimensions (51 x 51 mm)
• connection of two switches/NAMUR proximity sensors with wires
• connection of one solenoid with wires
• connection of AS-Interface with wires c. Indication:
• switching states of the switch/NAMUR proximity sensor inputs:
A = LED (H1, red), lights if the switch/NAMUR proximity sensor 2 is closed/on
B = LED (H2, green), lights if the switch/NAMUR proximity sensor 1 is closed/on
• one LED (H4, yellow) for the switching state of the solenoid, the LED lights if the solenoid is switched on
• one LED (H3, orange) for short-circuit and line break monitoring of the solenoid output; the LED lights if there is neither a short-circuit nor a line break on the solenoid output d. Specification of the Switch/NAMUR proximity Sensor inputs:
• Supply: 8 V, 8 mA for each switch/sensor
(NAMUR - specification)
• No line break and short-circuit monitoring
• These inputs are indicated via AS-Interface data bit D2
(Switch/Sensor 2) and D3 (Switch/Sensor 1) e. Specification of the valve output:
• output voltage: 24 - 30 VDC (depending on the voltage of the ASI-line and the load current of the solenoid)
• power consumption of the solenoid: max. 3 W/24 V
• the solenoid is switched on via the AS-Interface data bit
D0 (D0=1: solenoid is switched on)
• line break and short-circuit monitoring:
These failures are indicated via AS-Interface data bit D1
D1 = 0: line break or short-circuit at the solenoid output
D1 = 1: no line break and no short-circuit, solenoid is switched on.
10–40 39 ACCESS M Mounted Limit Switch and Solenoid with AS-Interface
Line break and short-circuit at the solenoid output are only monitored when the solenoid is switched on
When shipped for field installation, the limit switch
(sensor)/solenoid assembly will be broken down into subassemblies. The subassemblies are: (1) the switch
(sensor) operator assembly, consisting of the switches
(sensors), bracket, springs and buttons; and (2) the enclosure (housing), probes, solenoid, control block, block gasket, PC board and cover. Hardware items and gasket are packaged separately. Retaining rings and
O-rings shall be assembled.
Ambient temperature range of Access unit is 0°F minimum to 160°F maximum.
NOTE: Access M Mounted Limit Switch
(sensor)/Solenoid Kits fit only Revision R5 and later 39
Actuators. Included in the Access M Mounted Limit
Switch (sensor)/Solenoid Kits is a Rebuild/Accessory
Addition Label which is to be marked and applied to actuator after switch has been installed.
2. The Access M mounted limit switch (sensor)/solenoid assembly will be mounted on the right-hand end cap (when viewed from actuator nameplate) with conduit connection on the right side of the housing (when viewed from the cover side of the switch).
CAUTION: When actuator is installed in outdoor conditions, water can enter the exhaust hole(s) of the control block and then freeze. Flowserve suggests a cover be used, or mount the actuator such that the block exhaust hole(s) will not fill with water.
The “standard” mounting configuration of the 39 actuator to the valve is fail closed. In this configuration, SW-1, as described in
Section 7 and in the wiring diagram, will give indication when the actuator is in the open position (green LED is on). SW-2 gives indication of the closed position (red LED is on). Actuator shaft rotation will vary, depending on which fail closed mounting is used. See Section 8 for wiring instructions.
NOTE : The rotation of the actuator shaft CW (clockwise) or CCW
(counterclockwise) is determined when viewing the actuator from the nameplate side of the actuator, while being able to read the label from left to right.
Fail-open mounting configuration may be obtained by either inverting the actuator, using in-line coupling, or mounting the actuator cross-line (sizes 10–20) or indexing the coupling
(including valve ball and stem) 90° to the actuator shaft (sizes
25–40). In these cases SW-1 and SW-2 indication will be reversed from the above but actuator shaft rotation will vary, depending on which fail-open mounting is used. Wiring shall be done per the appropriate wiring diagram in Section 8 and adjustments per
Section 7.
3. Remove cover from enclosure.
CAUTION: The longer probe must be in the left-hand throughhole (looking at the housing from the cover side). (Both probes are the same length for the 1039 ACCESS only!)
WCAIM2032
4. Assemble the enclosure, with probe assemblies, to the actuator inserting the housing gasket between the actuator end cap and the housing. Important! Do not apply any grease to the gasket, it must be installed dry. Secure with four machine screws. For all ACCESS M units, four threaded tamper-proof plugs are installed over the machine screws. Once installed, no attempt should be made to remove these plugs. If it becomes necessary to remove enclosure from actuator end cap, consult Flowserve.
Check the probes for freedom of movement by moving them back and forth slightly.
5. With assembly complete to this point, it is convenient to make conduit connections and bring wiring through enclosure. The power supply to the solenoid coil is three watts. Required amperage is shown below. It should be noted that the successful use of this device in hazardous, wet, or other detrimental environments depends on proper conduit construction techniques.
Voltage
24 VDC
Holding Amps
.13
6. When the switch package is assembled, one of the probes will make contact with the switch button. Simply press the switch package until the mounting screws can be engaged. Tighten mounting screws until bracket is secure.
7. Switches/sensors (if installed) have been factory adjusted, but should be rechecked after installation. Adjustment is as follows:
LEDs
{ Red = Closed
Green = Open
Yellow = Solenoid Energized
Orange = Coil Continuity
Flow Control Division
Worcester Controls a. With actuator mounted in “standard” fail-closed mounting configuration (see Step 2) and wired per appropriate wiring diagram, set actuator in the full-closed position, with the adjustment screw near its loose limit. The orange LED indicating solenoid coil continuity will be lit. The orange LED will remain lit as long as there is power to the circuit board and there is no short circuit or open circuit with the coil.
However, it should be noted that if there is a short circuit or open circuit with the coil, the orange LED will only turn off when an attempt is made to energize the coil. This also applies to the Input 1 (Bit 1) status.
b. Adjust closed position switch or Namur proximity sensor SW-2
(see Wiring Diagram) by tightening the adjustment screw until red LED turns on. Then tighten adjustment screw one additional turn.
With air supplied to actuator, energize the solenoid to change actuator to its full open position. The yellow and orange LEDs should be lit indicating power to the coil and coil continuity, respectively. Adjust the open position switch/sensor SW-1 in the same manner as the closed position switch/sensor until the green LED turns on. Then tighten adjustment screw one additional turn. When the solenoid is de-energized, the actuator will return to its full closed position. The yellow and green LEDs will turn off indicating that the solenoid is deenergized and the actuator is no longer in the full open position and then the red LED will turn on indicating that the actuator is now in the full closed position.
Fail-Closed
(Sizes 10–40 In-line Operation)
(Sizes 25–40 Cross-line Operation)
Fail-Closed
(Sizes 10–20 Cross-line,
Inverted Operation)
Note: Wire colors in parenthesis are for proximity sensors only.
For units without switches/sensors, disregard switch/sensor wiring, and also their instructions in section 7.
WCAIM2032
Fail-Open
(Sizes 10–20 Cross-line Operation, or with In-line Coupling)
(Sizes 25–40 Cross-line Operation)
Fail-Open
(Sizes 10–20 In-line,
Inverted Operation)
10–40 39 ACCESS M Mounted Limit Switch and Solenoid with AS-Interface 3
Flow Control Division
Worcester Controls c. For fail-open mounting configuration (see Step 2), wire actuator per appropriate wiring diagram, set actuator in the full open position with adjustment screw near its loose limit.
Adjust open position switch or Namur proximity sensor SW-
2, by tightening the adjustment screw until the green LED turns on. Then tighten adjustment screw one additional turn.
With air supplied to actuator, energize the solenoid to change actuator to its full closed position. The yellow and orange LEDs should be lit indicating power to the coil and coil continuity, respectively. Adjust the closed position switch/sensor SW-1 in the same manner as the open position switch/sensor until the red LED turns on. Then tighten adjustment screw one additional turn. When the solenoid is de-energized, the actuator will return to its full open position. The yellow and red LEDs will turn off indicating that the solenoid is de-energized and that the actuator is no longer in the full closed position and then the green LED will turn on indicating that the actuator is now in the full-open position.
NOTE : If actuator is mounted in any configuration, other than
“standard” consult Step 2 of Installation Instructions to ensure proper orientation of probes and switches (sensors).
8. Wiring instructions for limit switches and proximity sensors. Refer to Step 2 for any actuator mounting configuration other than
“standard”.
Limit Switch/Proximity Sensor Ratings:
Mechanical Switch – 15.1 amps @ 125/250 VAC; .5 amps @
125 VDC.
Namur Proximity Sensor – < 1mA (Target present), > 3mA (Target absent) 15 mA max., 5-25 VDC, sensing range 2 mm, switching frequency 1 kHz. Not sensitive to polarity.
Make electrical connections in accordance with the appropriate wiring diagram on inside of cover or on page 3:
Place the lubricated O-ring down over the threaded section of the housing onto the machined shoulder. The cover must be threaded onto housing tightly for proper performance. The assembly is now complete.
NOTE : For units with a metal cover, a light coat of grease (such as a #1 grease) shall be applied to the cover threads. A minimum of
1 /
3 the circumference of the threads to be lubricated.
10. Control Block:
If control block is removed, be sure appropriate gasket is properly inserted between block and switch base (see Figure 1 below and
Access exploded view). Do not apply any grease to gasket, it must be installed dry.
11. Air Supply Connection:
Connect air supply to 1 /
4
" NPT connection on control block.
12. Operation:
A. Double-Acting with Control Block - Air is supplied to the 1 /
4
"
NPT port on the block. When the solenoid is energized, the spring-loaded plunger is withdrawn; allowing the supply air to shift the spring-loaded spool within the block, which opens the supply path to the center chamber of the actuator. Air from the end chambers of the actuator is allowed to pass through the block and exhaust to atmosphere.
When the solenoid is de-energized, the spring-loaded plunger blocks the flow of air to the spool seal within the block and the spool spring shifts the spool within the block to a position which opens the supply path to the end chambers of the actuator. Air from the center chamber of the actuator is allowed to pass through the block and exhaust to atmosphere.
The actuator is electrically fail-safe. That is, it will return to its de-energized position upon electrical failure.
Figure 1
Figure 2
4 10–40 39 ACCESS M Mounted Limit Switch and Solenoid with AS-Interface WCAIM2032
The unit has two independently adjustable speed control screws which can be used to adjust the speed of operation for the opening and/or closing stroke (see Figure 2). If the speed control screws are too tight, the unit will fail to operate.
NOTE : Speed control screws are shipped from the factory in the full-open position.
B. Spring-Return with Control Block - Air is supplied to the 1 /
4
"
NPT port on the block. When the solenoid is energized, the spring-loaded plunger is withdrawn; allowing the supply air to shift the spring-loaded spool within the block, which opens the supply path to the center chamber of the actuator. Air from the end chambers of the actuator is allowed to pass through the block and exhaust to atmosphere.
When the solenoid is de-energized, the spring-loaded plunger blocks the flow of air to the spool within the block and the spring-loaded spool returns to a position which allows air from the center chamber of the actuator to pass through the block and exhaust to atmosphere as the actuator is cycled by the springs in the end chambers of the actuator. The end chambers are exhausted to atmosphere at all times.
The actuator is fail-safe. That is, it will return to its deenergized position upon electrical or pneumatic failure.
The unit has one speed control screw, which can be used to adjust the speed of operation for the closing stroke (on a failclosed unit) or opening stroke on a fail-open unit, and one port plugged with a red plastic plug (see Figure 2 on page 4). If the speed control screw is too tight, the unit will fail to operate.
Flow Control Division
Worcester Controls
Note : Speed control screws are shipped from factory in the full-open position.
CAUTIONS: If converting a double-acting actuator to a spring-return actuator or vice-versa, be sure the correct control block gasket is used (see Figure 1 on page 4 and
Access exploded view).
Be sure red plastic plug is installed in plugged port (Figure 2 on page 4) for spring-return actuators.
In the event of air failure, the Series 39 actuator with Access unit can be cycled manually. This is accomplished by applying a wrench to the exposed top shaft of the actuator and turning it in the desired direction.
a WARNING: Care must be taken to ensure that the actuator is not operated automatically while manual operation is being performed.
If a routine cycle check is to be performed on an actuator with a control block, the actuator can be cycled manually by shifting the spool valve within the control block. This can be done by pushing the override button in the control block (See
Figure 2 on page 4 for location of button). Care must be taken to hold the spool valve in the desired position until the actuator has cycled. Provided the air supply is still on, the actuator will cycle to its original position as soon as the manually applied pressure on the override button is released.
WCAIM2032 10–40 39 ACCESS M Mounted Limit Switch and Solenoid with AS-Interface 5
ACCESS Exploded View
Flow Control Division
Worcester Controls
6 10–40 39 ACCESS M Mounted Limit Switch and Solenoid with AS-Interface WCAIM2032
Flow Control Division
Worcester Controls
1
1
3
2
1
4
1
1
1
QTY.
1
1
1
1
2
1
4
2
2
2
2
8B
9
10
11
6
7
4
5
8A
ITEM
1
2A
2B
3
15
16
17
18
12
13
14
DESCRIPTION
ENCLOSURE
COVER “Z”
COVER “W”
O-RING - COVER
GASKET
NAMEPLATE
CAUTION LABEL “Z”
DRIVE SCREW
LIMIT SWITCH OR NAMUR PROXIMITY SENSOR
ASSEMBLY - LEFT
LIMIT SWITCH OR NAMUR PROXIMITY SENSOR
ASSEMBLY - RIGHT
BRACKET - SWITCH/SENSOR
MOUNTING SCREW - BRACKET
ADJUSTMENT SPRING - SWITCH/SENSOR
PARTS LISTING
ITEM
19
20
21
21A
22
23
24
25
26
27
28
29A
29B
BUTTON - SWITCH/SENSOR
SPRING - SWITCH/SENSOR
FLAT WASHER - SWITCH/SENSOR
MOUNTING SCREW - SWITCH/SENSOR
RETAINING RING - SWITCH/SENSOR
SCREW - SWITCH/SENSOR ADJUSTING
SOLENOID ASSEMBLY
30
31
32
33
1
1
1
1
1
2
4
1
4
QTY.
2
1
2
2
4
1
2
1
DESCRIPTION
SOLENOID EXHAUST PORT FITTINGS
SOLENOID EXHAUST TUBING
UPPER MOUNTING SCREW -
ENCLOSURE (1 1 /
8
" LONG)
LOWER MOUNTING SCREW -
ENCLOSURE (1" LONG)
THREADED TAMPER PROOF PLUG
ROD PROBE
PISTON PROBE
O-RING - PROBE
RETAINING RING - PROBE
WIRING DIAGRAM - NOT SHOWN
CONTROL BLOCK ASSEMBLY
GASKET-CONTROL BLOCK (DOUBLE-ACTING)
(SEE FIGURE 1 ON PAGE 4)
GASKET-CONTROL BLOCK (SPRING-RETURN)
(SEE FIGURE 1 ON PAGE 4)
CONTROL BLOCK BOLTS
PRINTED CIRCUIT BOARD
MOUNTING SCREW - PRINTED CIRCUIT BOARD
CONDUIT PLUG
WCAIM2032 10–40 39 ACCESS M Mounted Limit Switch and Solenoid with AS-Interface 7
Flow Control Division
Worcester Controls
Flowserve Corporation has established industry leadership in the design and manufacture of its products. When properly selected, this Flowserve product is designed to perform its intended function safely during its useful life. However, the purchaser or user of Flowserve products should be aware that Flowserve products might be used in numerous applications under a wide variety of industrial service conditions. Although Flowserve can (and often does) provide general guidelines, it cannot provide specific data and warnings for all possible applications. The purchaser/user must therefore assume the ultimate responsibility for the proper sizing and selection, installation, operation, and maintenance of Flowserve products. The purchaser/user should read and understand the Installation
Operation Maintenance (IOM) instructions included with the product, and train its employees and contractors in the safe use of Flowserve products in connection with the specific application.
While the information and specifications contained in this literature are believed to be accurate, they are supplied for informative purposes only and should not be considered certified or as a guarantee of satisfactory results by reliance thereon. Nothing contained herein is to be construed as a warranty or guarantee, express or implied, regarding any matter with respect to this product. Because Flowserve is continually improving and upgrading its product design, the specifications, dimensions and information contained herein are subject to change without notice. Should any question arise concerning these provisions, the purchaser/user should contact Flowserve Corporation at any one of its worldwide operations or offices.
For more information about Flowserve Corporation, contact www.flowserve.com or call USA 1-800-225-6989.
FLOWSERVE CORPORATION
FLOW CONTROL DIVISION
1978 Foreman Drive
Cookeville, Tennessee 38501 USA
Phone: 931 432 4021
Facsimile: 931 432 3105 www.flowserve.com
© 2003 Flowserve Corporation, Irving, Texas, USA. Flowserve and Worcester Controls are registered trademarks of Flowserve Corporation.
WCAIM2032 10/03 Printed in USA
advertisement
* Your assessment is very important for improving the workof artificial intelligence, which forms the content of this project
Related manuals
advertisement