GREAT PLANES fairchild PT-19 Instruction Manual
Add to my manuals
24 Pages
GREAT PLANES Fairchild PT-19 is an easy-to-fly sport scale model airplane designed for those starting in scale modeling, with everyday flyer durability. Its simple build is perfect for beginners, and its docile flight characteristics make it easy to control. Whether you're a seasoned pro or just starting out, the GREAT PLANES Fairchild PT-19 is a great choice for anyone looking for a fun and rewarding flying experience.
advertisement
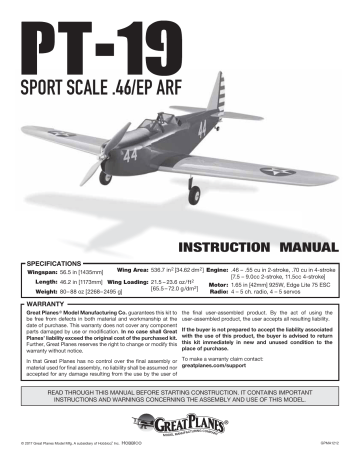
SPORT SCALE .46/EP ARF
INSTRUCTION MANUAL
SPECIFICATIONS
Wingspan: 56.5 in [1435mm]
Wing Area: 536.7 in 2 [34.62 dm 2 ] Engine: .46 – .55 cu in 2-stroke, .70 cu in 4-stroke
[7.5 – 9.0cc 2-stroke, 11.5cc 4-stroke]
Length:
Weight:
46.2 in [1173mm] Wing Loading: 21.5 – 23.6 oz /ft 2
80– 88 oz [2268– 2495 g]
[65.5 – 72.0 g /dm 2 ]
Motor:
Radio:
1.65 in [42mm] 925W, Edge Lite 75 ESC
4 – 5 ch. radio, 4 – 5 servos
WARRANTY
Great Planes ® Model Manufacturing Co.
guarantees this kit to be free from defects in both material and workmanship at the date of purchase. This warranty does not cover any component parts damaged by use or modification. In no case shall Great
Planes’ liability exceed the original cost of the purchased kit.
Further, Great Planes reserves the right to change or modify this warranty without notice.
the final user-assembled product. By the act of using the user-assembled product, the user accepts all resulting liability.
If the buyer is not prepared to accept the liability associated with the use of this product, the buyer is advised to return this kit immediately in new and unused condition to the place of purchase.
In that Great Planes has no control over the final assembly or material used for final assembly, no liability shall be assumed nor accepted for any damage resulting from the use by the user of
To make a warranty claim contact: greatplanes.com/support
READ THROUGH THIS MANUAL BEFORE STARTING CONSTRUCTION. IT CONTAINS IMPORTANT
INSTRUCTIONS AND WARNINGS CONCERNING THE ASSEMBLY AND USE OF THIS MODEL.
® Inc.
GPMA1212
TABLE OF CONTENTS
INTRODUCTION . . . . . . . . . . . . . . . . . . . . . . . . . . . . . . . . 2
ADDITIONAL ITEMS REQUIRED . . . . . . . . . . . . . . . . . . . 2
Radio/Servos . . . . . . . . . . . . . . . . . . . . . . . . . . . . . . . . 2
Glow Engine. . . . . . . . . . . . . . . . . . . . . . . . . . . . . . . . . 2
Brushless Electric Motor . . . . . . . . . . . . . . . . . . . . . . . 3
LiPo Battery Charger . . . . . . . . . . . . . . . . . . . . . . . . . . 3
Adhesives, Hardware and Other Accessories . . . . . . . 3
REPLACEMENT PARTS LIST . . . . . . . . . . . . . . . . . . . . . . 3
KIT CONTENTS . . . . . . . . . . . . . . . . . . . . . . . . . . . . . . . . . 4
PREPARATION . . . . . . . . . . . . . . . . . . . . . . . . . . . . . . . . . 4
ASSEMBLE THE WING . . . . . . . . . . . . . . . . . . . . . . . . . . . 5
Hook Up the Ailerons. . . . . . . . . . . . . . . . . . . . . . . . . . 5
Join the Wing Halves . . . . . . . . . . . . . . . . . . . . . . . . . . 6
Mount the Landing Gear . . . . . . . . . . . . . . . . . . . . . . . 8
ASSEMBLE THE FUSELAGE . . . . . . . . . . . . . . . . . . . . . . 8
Install the Electric Motor . . . . . . . . . . . . . . . . . . . . . . 10
Mount the Glow Engine . . . . . . . . . . . . . . . . . . . . . . . 12
Hook Up the Throttle . . . . . . . . . . . . . . . . . . . . . . . . . 13
Install the Fuel Tank . . . . . . . . . . . . . . . . . . . . . . . . . . 13
Fit the Cowl Over the Engine . . . . . . . . . . . . . . . . . . . 14
Mount the Cowl . . . . . . . . . . . . . . . . . . . . . . . . . . . . . 16
Finish Cutting the Cowl . . . . . . . . . . . . . . . . . . . . . . . 17
Install the Radio . . . . . . . . . . . . . . . . . . . . . . . . . . . . . 19
Scale Details . . . . . . . . . . . . . . . . . . . . . . . . . . . . . . . 20
PREPARE THE MODEL FOR FLIGHT . . . . . . . . . . . . . . 21
Set the Control Throws . . . . . . . . . . . . . . . . . . . . . . . 21
Check the C.G. . . . . . . . . . . . . . . . . . . . . . . . . . . . . . 21
Balance the Model Laterally . . . . . . . . . . . . . . . . . . . 22
PREFLIGHT . . . . . . . . . . . . . . . . . . . . . . . . . . . . . . . . . . . 22
Engine/Motor Safety Precautions . . . . . . . . . . . . . . . 22
Battery Precautions . . . . . . . . . . . . . . . . . . . . . . . . . . 23
Range Check . . . . . . . . . . . . . . . . . . . . . . . . . . . . . . . 24
AMA SAFETY CODE . . . . . . . . . . . . . . . . . . . . . . . . . . . . 24
General. . . . . . . . . . . . . . . . . . . . . . . . . . . . . . . . . . . . 24
Radio Control. . . . . . . . . . . . . . . . . . . . . . . . . . . . . . . 24
FLYING . . . . . . . . . . . . . . . . . . . . . . . . . . . . . . . . . . . . . . . 24
INTRODUCTION
Congratulations and thank you for purchasing the Great
Planes Sport Scale PT-19 .46/EP ARF. The PT-19 is an easy start to scale modeling, with easy sport fl ying characteristics and the durability of an every-day fl yer.
❍ Tactic TSX25 mini digital high-speed 2 ball bearing servo (TACM0225)
❍
Tactic TSX20 mini high-speed 2 ball bearing servo
(TACM0220)
OR
❍
Tactic TSX35 standard sport servo (TACM0235)
❍
(2) 12" [300mm] universal servo extensions (TACM2130)
For the latest technical updates or manual corrections, fi nd the Sport Scale PT-19 ARF page on the Great Planes Model
Manufacturing web site at www.greatplanes.com. If there is new technical information or changes to this model a “tech notice” box will appear on the page.
If mixing the aileron servos electronically with programmable mixing in the transmitter:
❍ (2) 6" [150mm] universal servo extensions (TACM2092)
ADDITIONAL ITEMS REQUIRED
If connecting the servos with a Y-harness:
❍
Futaba dual servo extension (FUTM4130)
Radio/Servos
A minimum 4-channels is required to fl y the Sport Scale
PT-19 ARF. The Tactic TTX660 is recommended because of its simple, fl exible computer programming and multiple model memory:
❍ Tactic TTX660 6-channel programmable radio
(TACJ2660)
❍ Tactic TR625 6-chanel receiver (TACL0625)
❍ Hobbico 2S 6.6V 1300mAh LiFe battery (HCAM6411)*
❍ On-off receiver switch (TACM2000)*
*If powering your PT-19 with a brushless electric motor the
BEC in the ESC may be used to power your receiver and servos, so no receiver battery or on/off receiver switch will be required.
Glow Engine
The PT-19 is suited for a .45 - .55 cu. in. 2-stroke or .70 cu. in 4-stroke. The O.S. Max .46AXII (OSMG0548) is illustrated in this manual.
Servos nowadays are smaller and stronger, so we’ve designed the servo mounts in the PT-19 to accommodate mini servos, but full-size servos may still be used simply by enlarging the openings in the servo mounts. Four or 5 channels are required depending on whether you connect the aileron servos to separate channels and mix them with programmable mixing in your transmitter, or if you use a Y-harness to connect the aileron servos to one channel.
2
Other accessories for a glow engine
❍ 1/4" [6.4mm] R/C foam rubber (HCAQ1000)
❍ Great Planes Dead Center Hole Locator (GPMR8130)
❍ 6-32 tap and drill set (DUBR0510)
❍ Propellers suitable for your engine
❍ Optional: Great Planes Aluminum Safety Spinner Nut
1/4"- 28 (GPMQ4630)
❍ O.S. Muffl er Extension Adapter E-3070 873
(OSMG2578)
Brushless Electric Motor
The electric setup for the PT-19 is straightforward: a Great
Planes Electrifl y Rimfi re .32 on a 13 x 8 E prop with a minimum
60A ESC powered by a 4S LiPo battery in the 3300mAh –
4000mAh range. A Castle Creations Edge Lite 75* is illustrated in the instruction manual because it is compact, easily programmable and features data logging.
❍
42-50-800 Rimfi re .32 (GPMG4700)
❍
APC 13 x 8 thin E prop (APCQ3080)
❍
Castle Creations Edge Lite 75 (CSEM1200)
❍ FPWP2234 FlightPower 4S 3300mAh 25C
OR
❍ FPWP2404 FlightPower 4S 4000mAh 25C
❍
3/16" heat shrink tubing (GPMM1056)
❍
T-style Star connector (HCAM4001)
❍
Optional: Great Planes Aluminum Safety Spinner Nut
5/16"- 24 (GPMQ4631)
*NOTE: The PT-19 has been tested with the servos and ESC recommended in this instruction manual. If you are using different servos that draw more current than the BEC in your ESC is recommended for (5A for the Edge Lite 75), or if setting the BEC voltage in the ESC higher than the factorydefault 5.0V, one option is to use a voltage regulator with a higher Amp rating that draws power from the 4S LiPo motor battery (such as the Castle Creations 10A BEC - CSEM0005).
Another option is to use a receiver battery.
A Robart Super Stand II (ROBP1402) is also indispensable for working on your PT-19.
A covering iron with a cover sock may be required for tightening and re bonding the covering to the model that may have loosened between the time the plane was manufactured and the time the model was removed from the box. The 21 st
Century iron is preferred because of its long cord, contoured shoe and precisely adjustable temperature range:
❍
Coverite 21 st Century Sealing Iron (COVR2700)
❍
Coverite 21 st Century Cover Sock (COVR2702)
REPLACEMENT PARTS LIST
LiPo Battery Charger
To charge a 4S 4000mAh LiPo at 1C, a charger capable of at least 70 Watts is required (4S x 4.2V/cell = 16.8V x 4A =
67 Watts). The Triton EQ2 (GPMM3156) is more than enough charger with 100W output AC and 120W output DC.
Adhesives, Hardware and
Other Accessories
Other than common hobby tools here is a list of other items required:
❍
30-minute epoxy (GPMR6043)
❍ Epoxy brushes (GPMR8060)
❍
Mixing cups (GPMR8056)
❍
Mixing sticks (GPMR8055)
❍
Threadlocker thread locking cement (GPMR6060)
❍ Thin CA (GPMR6001)
❍
Medium CA (GPMR6007)
❍
CA applicator tips (HCAR3780)
❍
CA accelerator (GPMR6035)
❍ Canopy glue (PAAR1300) or Zap Goo (PAAR3200)
Order No.
Description
GPMA2555 Wing
GPMA2556
GPMA2557
Fuselage
Tail Surface Set
GPMA2558
GPMA2559
GPMA2560
Cowl Set
Hatch
Windscreen Set
GPMA2561
GPMA2562
Landing Gear Set
Rollover Pylon
GPMA2563
GPMA2564
GPMA2565
EP Motor Mount Parts Set
Fuel Tank
Landing Gear Covers Set
GPMA2566
TOWA4077
Decals
10- 24 x 2” Nylon Wing Bolts (2)
GPMA5406 Tail Gear Set
3
KIT CONTENTS
2
1
5
3
7
4 6
8
10
9
12
11
1. Cowl
2. Fuselage, Cockpit hatch
3. Wood Parts
4. Hardware Bag
5. Right Wing
6. Left Wing
7. Horizontal Stabilizer
8. Vertical Stabilizer
PREPARATION
13 14
9. Fuel Tank
10. Engine Mount
11. Nylon Hardware Bag
12. Fastener Hardware Bag
13. Crash Protector,
14. Landing Gear Wires
15. Pilot (not shown)
NOTE: The covering on your PT-19 requires less heat than you may be used to if you’re already familiar with iron-on coverings – too much heat causes seams and edges to pull and draw away from each other causing wavy, uneven edges or exposed balsa. Follow the instructions below to tighten the covering on your model.
The cockpit hatch is removed by pulling forward on the latch in the rear cockpit and lifting the rear of the cockpit up and off the fuselage.
4
❏
1. Stack two or three paper towel squares on top of each other and cut them into small squares. During various stages of assembly these squares may be dampened with denatured alcohol for epoxy clean up and other kinds of clean up.
ASSEMBLE THE WING
Hook Up the Ailerons
❏
2. Use a covering iron with a cover sock to tighten any loose covering and thoroughly bond it to the wood structure.
The optimum temperature measured on the surface of a covering iron with a protective cover sock is about 280°F
[140°C] which requires a dial setting of about 300°F [150°C] or “medium” heat on most covering irons. Wherever the covering is over wood (especially on the sheet balsa tail surfaces) press down on the iron to thoroughly bond the covering to the balsa underneath. If the covering blisters up over balsa and cannot be pressed back down, the iron may be too hot or you are leaving it in one location for too long—try reducing the heat or moving the iron a little faster.
❏
1. Attach a 9" [230mm] or 12" [300mm] servo extension to each aileron servo (6" [150mm] servo extensions aren’t quite long enough). Use 1/2" [13mm] heat shrink tubing, tape or a dab of glue to secure the connections so they cannot come undone inside the wing later.
❏
3. Give a generous tug on all control surfaces to check the hinges. Add thin CA where necessary to any loose hinges.
Residual CA or CA “fog” is removable with a paper towel square dampened with CA debonder.
Refer to this image while mounting the aileron servos and hooking up the ailerons. The holes in the control horn should be centered over the hinge gap. You can do both wings together, or one-at-a-time (the left wing is shown in the photos).
❏
4. If powering your PT-19 with a glow engine, apply a fi lm of epoxy or CA to edges of the covering around the nose and fi rewall to seal from fuel and exhaust residue.
❏
2. If your servo is too large for the servo opening in the wing, the opening may be enlarged by cutting along the inside and aft edges of the opening as shown by the dashed lines.
5
gear wire. Position the holes in the landing gear straps on the lines and mark the locations of the holes onto the wing.
❏
3. Cut the covering from the hole in the top of the wing for the servo wire.
❏
4. Use the string to pull the aileron servo wire through the wing (or just guide the servo wires down through the holes without the string) and fi t the servo into the servo openings.
❏
5. Drill 1/16" [1.6mm] holes for the servo mounting screws in the wing and in the aileron for the control horn screws (use care not to drill through the top of the aileron).
90º Connector
1/16" [1.5 mm]
❏
10. Drill 3/32" [2.4mm] holes into the wing at the marks.
❏
11. Remove the ink lines with a paper towel square dampened with denatured alcohol.
Join the Wing Halves
Servo Arm
❏
6. Enlarge the holes in the servo arm with a #48 [.076”] drill. Mount the servo in the wing. With the servo arm and aileron centered, make the pushrod and hook up the aileron using the hardware shown on the previous page.
❏
7. After mounting the aileron horns, remove the screws, harden the holes with a few drops of thin CA, allow to harden, and then reinstall the screws.
❏
8. Hook up the aileron servo in the right wing the same way.
It will be a little easier to mark and drill the holes for the main landing gear wires before gluing the wings together…
1/8" [3.2mm]
❏
1. Use epoxy or medium CA to glue together the two pieces of the plywood wing joiner.
1/8" [3.2mm]
Channel for landing gear wire
❏
9. Use a fi ne-point felt-tip pen to mark lines on the wing
1/8" [3.2mm] ahead of and behind the channel for the landing
6
❏
2. Glue the nylon alignment pin halfway into one of the wing halves.
❏
3. Test-fi t both wing halves together with the wing joiner and the pin. Make any adjustments necessary for a good fi t.
❏
4. Mix approximately 1/2 oz. of 30-minute epoxy. Working quickly, pour some epoxy into the spar cavities in both wings and distribute with a wire or small dowel. Coat one end of the joiner and insert it into one of the wing halves. Coat the protruding end of the joiner and both ends of both wing halves.
Then, join them together and wipe away excess epoxy as it squeezes out. Proceed quickly to the next step.
❏
5. Use a small clamp to clamp the front of the wing together at the tab and plenty of masking tape to tightly clamp the rest of the wing together. Use the paper towel squares dampened with denatured alcohol to wipe away excess epoxy as you proceed. Allow the epoxy to fully harden before removing the clamps and tape.
❏
6. Carefully remove the tape after the epoxy has hardened.
Residual tape adhesive may be cleaned with naptha (lighter fl uid). Areas of the covering that may have lifted from removing the tape should be retightened with your covering iron.
7
Mount the Landing Gear
❏
1. Install the landing gear wires into the landing gear rails.
Secure the gear with the straps and M3 x 10 sheet metal screws—don’t over tighten the screws – just enough for the straps to compress the balsa a little.
❏
3. Mount the wheels to the gear with a 4mm collar on both sides of each wheel held in place with an M3 set screw and threadlocker.
ASSEMBLE THE FUSELAGE
❏
2. If installing the optional landing gear covers, glue them to each other and to the landing gear wire with fl exible glue such as Zap Goo. It takes the Zap Goo approximately overnight to dry.
❏
1. If you haven’t yet done so, use a covering iron with a cover sock to tighten the covering over the fuselage and horizontal and vertical stabilizer. On the fuselage, pay special attention at the back around the fi n fi llet and the stab slots so the covering remains attached when it’s time to install the horizontal and vertical stabilizers (stab and fi n).
8
❏
2. If powering your PT-19 with a brushless motor, cut the covering from the air exit vents in the bottom of the fuselage.
For a better fi nish, cut the covering about 1/32" [1mm] inside the edges of each opening and use a trim iron with a rounded tip to seal the covering neatly down around the edges.
❏
5. Test-fi t the CA hinge and the tail gear into the rudder.
❏
3. Cut and remove the balsa spacer from the back of the fuselage under the fi n fi llet.
❏
4. Mount the wing to the fuselage with two 10-24 x 2"
[50mm] nylon wing bolts (for convenience, you may shorten the wing bolts by cutting off up to 5/8" [15mm]).
9
❏
6. Test fi t stab and fi n (with CA hinge and tail gear) into the fuselage. View the model from behind. Check the alignment of the stab to the wing—if necessary, you can use tape to hold the elevators level and even with the stab.
❏
7. If necessary, adjust the slot in the fuselage to get the stab horizontally aligned with the wing—in most cases, all that will be required is a small amount of weight on the high side of the stab. The stab saddle can also be sanded slightly to get the stab to align.
❏
8. Remove the stab and fi n from the fuselage. Leave the
CA hinge in the rudder, but take out the tail gear.
❏
9. Make sure you have your paper towel squares and denatured alcohol handy.
❏
10. Mix up a batch of 30-minute epoxy. First apply epoxy to the tail gear wire where it goes into the rudder and in the rudder. Install the tail gear. Now apply epoxy to all joining areas of the stab, fi n and fuselage. Fit the stab and fi n into position. If any weight was required to level the stab don’t forget to reposition the weight and double-check the alignment. T-pins may also be used to hold the fi n fairings tightly to the stab and fi n. Once all adjustments have been made wipe away excess epoxy before it hardens.
❏
11. After the epoxy has hardened remove the wing.
❏
12. Add three or four drops of thin CA to both sides of the bottom rudder hinge—allow a few seconds between drops to allow the CA to soak into the hinge slot.
❏
15. With threadlocker on the M3 set screws, use a 1.5mm wrench to tighten the collar up against the tail gear bracket and another collar to secure the tail wheel.
If installing a glow engine skip to Mount the Glow Engine on page 12.
Install the Electric Motor
❏
1. Press four 4-40 blind nuts into either side of the front motor mount plate and glue them in with CA. (The front motor mount plate is the one with the round hole in the middle.)
❏
13. Enlarge the three holes in the tail gear bracket with a 3/32" [2.4mm] drill. Position the bracket centered on the bottom of the fuselage. Use the holes in the bracket to drill
1/16" [1.6mm] holes into the fuselage. Temporarily mount the tail gear with three M2.5 x 8 sheet metal screws.
❏
14. Remove the tail gear bracket screws, add a few drops of thin CA to each of the three holes, allow to harden, and then reinstall the screws.
❏
2. Fit, then use thin CA to glue the motor mount box together (with the blind nuts on the inside).
10
❏
3. Pick the triangle stock reinforcements with a hobby blade and use medium CA to glue them into the mount box around the inside of the front and back mount surfaces.
❏
7. Connect your ESC to the motor and mount the ESC to the bottom of the motor mount box—for the Castle Creations
Edge Lite 75 ESC we soldered the female bullet connectors that came with the motor to the three motor wires (protected with 3/16" heat shrink tubing) and a Star connector to the battery wires, then mounted the ESC to the box with a piece of foam rubber and nylon ties.
❏
8. Power up the ESC and use the transmitter to run the motor to make sure it turns the correct direction. If the motor turns the wrong way swap any two of the three motor wires.
❏
4. Drill 1/16" [1.6mm] pilot holes through the “O” marks in the fi rewall, then enlarge the holes with a 5/32" [4mm] drill.
Insert 6-32 blind nuts into the back of the holes.
❏
9. Cut the two included 1/4" x 1/4" [6.5 x 6.5 mm] balsa sticks to a length of 1-7/8” [48mm], then glue them across the back of the fi rewall so the screws don’t puncture the LiPo battery in the event of a crash.
❏
10. Attach the rougher, “hook” side of the included adhesive-back hook-and-loop strip to the battery mount plate and the other, softer “loop” side to your battery.
Refer to this photo while mounting the motor and ESC in the steps that follow.
❏
5. Mount the motor mount box to the fi rewall with four
6-32 x 3/4" Phillips screws and #6 lock washers and fl at washers and threadlocker.
❏
6. Assemble the “X” mount and the propeller adapter shaft to your motor and mount the motor to the motor mount box with four 4-40 x 1/2" Phillips screws and #4 lock washers and fl at washers and threadlocker—notice that the motor wires are positioned on the side of the mount box for a smooth connection to the ESC.
11
❏
11. Make two 9" [230mm] battery straps by cutting two
6" [150mm] pieces from the rougher, “hook” side of the included hook-and-loop material and two 6" [150mm] pieces from the softer, loop side. Join the halves together with a 3"
[80mm] overlap.
❏
4. Temporarily mount the engine mount with four 6-32 x
1" [25 mm] screws and lock washers and fl at washers, but don’t tighten the screws all the way yet.
❏
12. Test-fi t the battery into place with the straps. The fi nal location of the battery will be determined during the
C.G. procedure.
Skip to Mount the Cowl on page 16.
❏
5. Position the engine on the mount so the drive washer will be 4-7/8" [120mm] from the fi rewall. Tighten the engine mount screws and hold the engine in place with a clamp.
Mount the Glow Engine
The instructions illustrate installation of an O.S. Max .46 AX with the O.S. muffl er. If using a different engine and/or muffl er, slight adjustments may be required in the way your engine is rotated on the fi rewall. As long as the four engine mount screws are positioned over the circle inscribed on the fi rewall, the engine will be in the correct location.
❏
6. Use a Great Planes Dead-Center Hole Locator or similar tool to mark the engine mount bolt hole locations onto the mount.
❏
1. Drill 1/16" [1.6mm] pilot holes through the “X” marks in the fi rewall, then enlarge the holes with a 5/32" [4mm] drill. If using an engine or muffl er other than the O.S. .55AX/Bisson
Pitts-style muffl er, the engine mount may need to be rotated differently around the circle embossed in the fi rewall. However you orient your engine, be sure to keep all four engine mount holes on the circle embossed in the fi rewall so your engine and mount will be positioned properly.
❏
2. Press 6-32 blind nuts into the holes in the back of the fi rewall.
❏
3. Cut the “spreader bar” from both halves of the included engine mount and trim off any remaining material so they fi t together well.
12
❏
7. Remove the engine and drill #36 (.106" [2.7mm]) holes at the marks, then tap 6-32 threads into the holes—if available, a drill press is preferred for drilling the holes and the tap may be chucked in a hand drill to tap the threads.
❏
8. Mount the engine to the mount with four 6-32 x 3/4"
[19 mm] Phillips screws and #6 lock washers.
Hook Up the Throttle Install the Fuel Tank
❏
1. Glue together the two plywood fuel tank neck rings.
Then, glue them to the back of the fi rewall aligned with the hole in the fi rewall.
Refer to these images while hooking up the throttle.
❏
1. There are four throttle servo mount locations available.
Determine the location that makes the straightest run for the throttle pushrod from the servo to the carburetor arm (keeping in mind that the fuel tank will also be installed). Use a 3/16"
[4.8mm] K&S brass tube sharpened on the end or a 3/16"
[4.8mm] drill to drill holes where necessary for the throttle pushrod guide tube, or use the existing hole in the front former if your setup is the same as the one illustrated here.
❏
2. Mount the throttle servo in the servo tray location chosen. Cut the throttle pushrod guide tube to the correct length and roughen the outside with sandpaper so glue will adhere. Install the guide tube, but do not yet glue it in.
❏
3. Bend the throttle pushrod as necessary to connect to the servo arm and the carburetor arm with the hardware shown.
❏
4. A lite-ply “U” brace is included for stabilizing the end of the throttle pushrod guide tube. Cut the brace to the length required, then glue into position. Glue the throttle guide tube into place as well.
❏
2. Loosen the screw in the stopper in the fuel tank and take out the stopper/fuel line assembly. Check to make sure the clunks are present and secure on the lines and that the vent tube is pointed up toward the top of the tank. Also make sure the lines on the clunks are not so long that the clunks can contact the back of the tank (and possibly become stuck).
Make any adjustments necessary. Then, reassemble the tank as shown with the vent tube at the top of the tank. Make sure to securely tighten the screw to expand the stopper sealing the tank.
13
❏
3. Make a fuel tank strap from a 7" [180mm] piece of the softer, “loop” side and a 9" [230mm] piece of the rougher,
“hook” side of the included hook-and-loop material. Join the strips with about 4" [100mm] of overlap to complete the fuel tank strap.
❏
5. Install the fuel tank with the lines through the hole in the fi rewall. Then, tightly strap the tank into place.
❏
6. Test-fi t the canopy hatch to make sure the fuel tank is properly mounted and does not interfere with the hatch.
Make any adjustments necessary.
❏
7. Cut one of the fuel lines (from either of the two tubes on the bottom of the tank) to the correct length to fi t the carburetor. Leave the other two lines (one for fueling/defueling, the other for the pressure/vent line from the muffl er) the length they are now – we’ll cut them later after the cowl has been cut and fi tted.
Fit the Cowl Over the Engine
❏
4. Cut a 2-1/4" x 4-1/2" [55 x 115mm] sheet from a piece of 1/4" [6mm] RC foam rubber to cushion the bottom of the tank. Install the fuel tank strap under and up through the slots in both sides of the fuel tank fl oor and place the foam rubber sheet.
If you’ve installed a brushless motor, the cowl probably requires no cutting, so skip ahead to Mount the Cowl .
Cutting a cowl to fi t over a glow engine can be a little tedious.
It’s kind of a “catch 22” where you can’t know where to cut the holes in the cowl until you have the cowl in place, but you can’t position the cowl until you have the holes cut to fi t over the engine and muffl er. So the best way is to fi t and trim the cowl in small increments. The fewer obstructions there are to cut around the easier it will be to take small steps. The most accurate way is to remove as many parts from the engine as you feel comfortable. In these instructions we’ve removed the head and carburetor. All passages to the engine should be covered or stuffed with a paper towel or similar. If you would rather not remove any parts from the engine, the procedure for fi tting and cutting the cowl is the same, except you may have to cut larger holes to get the cowl to fi t.
A No. 569 or 570 Dremel grout removal bit and a sanding drum are indispensable for easily and accurately cutting a fi berglass cowl. Always wear eye and breathing protection when cutting fi berglass.
14
Follow these instructions with deviations as necessary for your comfort level and requirement for accuracy.
❏
1. Optional: Remove the engine head and carburetor from the engine. Cover any openings in the engine to seal out debris.
❏
3. Use your Dremel to cut the fi rst hole at your mark. Testfi t the cowl. Use a felt-tip pen to mark the outside of the cowl where more trimming is required. Residual ink can be wiped off with a paper towel square and denatured alcohol later.
❏
4. Continue to trim, fi t, mark and repeat until you can get the cowl to go on all the way over the engine.
❏
2. Fit the cowl over the engine as far as it will go (without the engine head and carburetor it should fi t most of the way). Use a pencil to mark the inside of the cowl where it interferes with whatever part of the engine is preventing the cowl from going on.
15
More trimming will be required once the head and carbutetor have been replaced to the engine, but once you can get the cowl to fi t all the way on it’s time to mount the cowl. After the cowl has been mounted you can fi nish the trimming procedure for the engine head, carburetor, needle valve and muffl er.
Mount the Cowl
Decide whether you wish to attach the cowl to the fuselage with four sheet metal screws through the sides, or with a cowl ring and internal screws. Some pilots may prefer a cowl ring because the cowl mounting screws will not be visible, but a cowl ring takes a little more skill and patience to install.
Follow the instructions for the method you prefer:
Proceed to Finish Cutting the Cowl .
Mount the Cowl with Sheet Metal Screws
❏
5. After all four holes have been drilled, remove the cowl.
Enlarge the holes in the cowl with a 3/32" [2.4mm] drill.
❏
6. Test-mount the cowl with the screws. Remove the cowl and screws. Add a few drops of thin CA to each screw hole and allow to harden.
Mount the Cowl with the Cowl Ring
❏
1. Press 4-40 blind nuts into the four holes in the cowl ring. This side will be the front.
Option: Press the bottom two blind nuts into the back of the front former instead of into the cowl ring. Then, the screws may be accessed through the cowl. This requires a “clear shot” to the screws from the front of the cowl (not concealed by the engine muffl er, etc.) and a hex driver that is long enough.
❏
1. The cowl mounting screws are to be centered over the edge of the front former, or slightly aft so they are anchored in the hardwood triangle stock inside. Mark a line on masking tape applied to both sides of the fuselage 2-1/8" [54mm] aft of the front surface of the front former.
❏
2. Install the cockpit hatch. Fit the cowl and mount a propeller.
❏
3. Accurately position and hold the cowl so the crankshaft will be centered in the hole in the front of the cowl and so you will have adequate propeller clearance (masking tape may be used to hold the cowl if necessary). Mark two screw holes on both sides of the cowl 2" [50mm] forward of the lines on the tape (centering the screw holes in the edge of the front former).
❏
2. Mount the cowl ring to the fuselage with four 4-40 x
1/2" [13mm] socket-head cap screws and #4 lock washers and fl at washers.
❏
3. If you’ve installed a glow engine, refer back to the cowl cutting procedure on page 14 to fi t the cowl to the fuselage over the engine.
❏
4. Drill 1/16" [1.6mm] holes through the marks in the cowl into the fuselage sides. As you drill each hole, partially thread in a M2.5 x 10 washer-head Phillips wood screw through the cowl into the hole before drilling the next hole.
❏
4. Fit the cowl and a propeller. Be certain the cowl goes on far enough so there will be enough clearance between
16
the propeller and the cowl. Make adjustments if necessary.
(The outside edges of the cowl ring may be sanded slightly to allow the cowl to go on a little farther if necessary.)
❏
5. Remove the cowl and take the cowl ring off the fuselage.
Use medium-grit sandpaper to roughen the inside of the cowl where the cowl ring fi ts. Lightly spray the inside of the cowl and the front of the cowl ring with CA accelerator.
This will prevent excess CA from getting past the cowl ring inadvertently gluing it to the fuselage. Reinstall the cowl ring and cowl.
Finish Cutting the Cowl
❏
6. Stand the fuselage upright with the nose pointing up.
Drip a few small drops of thick or medium CA down inside the cowl where it contacts the cowl ring – this won’t be the fi nal glue job – just enough to tack the cowl to the cowl ring.
You won’t be able to reach the part of the cowl ring in the upper left-hand corner, but that can be glued in the next step.
❏
1. Now that the cowl has been mounted and its exact location has been set, continue to cut the cowl to accommodate the head of the engine.
❏
7. Remove the cowl/cowl ring assembly. Securely glue the cowl ring to the inside of the cowl with medium CA. Add a small amount of thin CA around the back of the cowl ring
– do not build up a fi llet of glue here or it may interfere with the fi t of the cowl.
❏
8. If you’re using a glow engine, fuelproof the cowl ring with epoxy thinned with denatured alcohol or any other fuelproof coating.
17
❏
2. Now install the carburetor. Mark, cut and fi t the cowl as necessary.
❏
3. Next, cut a hole for the needle valve.
MUFFLER INSTALLATION TIP
When fi tting the muffl er and muffl er extension (OSMG2578), lay the model on its side so the muffl er screws and extension won’t fall off the engine. Once the cowl has been installed, fi t the muffl er bolts and muffl er extension to the engine.
Connect the pressure line from the fuel tank to the fi tting on the muffl er, then fi t the muffl er and tighten the screws.
❏
4. Finally, see the following tip, then turn the model over and start cutting for the muffl er. The muffl er mounting bolt holes in the engine may be used as a guide to mark the locations of the holes in the top of the cowl for a hex wrench to tighten the muffl er screws. The tail pipe on the muffl er was also rotated to align the exhaust outlet with the bottom of the fuselage.
18
❏
5. After all the holes have been cut in the cowl, sand the edges of the cutouts to smooth the lines and remove any loose fi berglass fi bers.
[1.6mm] holes through the rudder. Mount the rudder horn with two M2 x 10 sheet-metal screws. Remove the screws, add a few drops of thin CA into the holes, allow to harden, then mount the horn again.
Here’s a couple images of the fi nished cowl.
Install the Radio
❏
3. Align the clevis holes in the elevator horn with the hinge line, then drill the holes for the elevator horn. Mount the elevator horn with two M2 x 12 machine-thread screws and the back plate on the top of the elevator.
❏
1. Make the elevator and rudder pushrods as shown.
❏
2. Install the pushrods into the guide tubes in the fuselage.
Using the holes in the rudder horn as a guide, drill 1/16"
❏
4. If necessary, enlarge the cutout in the servo tray to fi t your servos. Then, fi t the servos into the tray, but don’t screw them down yet. Center the servo arms and control surfaces, then mark the pushrods where they cross the holes in the arms.
19
❏
5. Make a 90-degree bend in the pushrod wire at the marks – it will be easier to make the bends with the pushrods out of the fuselage. Connect the pushrods to the servo arms and snap on a 90-degree pushrod keeper. Then, cut off the excess wire and install the servo arms back onto the servos.
Scale Details
❏
6. Drill 1/16" [1.6mm] holes in the servo tray for the servos.
Then, mount the servos with the screws that came with them.
❏
1. Use the lite-ply pilot mount doubler to mark and drill holes in the cockpit fl oor in the location where you want to install the pilot (we used a 3/32" [2.4mm] brass tube sharpened on the end to cut the holes).
❏
2. Use the doubler as a template to drill 1/16" [1.6mm] holes in the base of the pilot.
❏
7. Mount the receiver and receiver battery (if used) with straps made from more hook-and-loop material. Also mount the receiver switch if used.
❏
3. Glue the doubler to the bottom of the cockpit fl oor. Then, glue and screw the pilot to the cockpit fl oor with two #4 x
1/2" [13mm] sheet metal screws and #4 washers.
20
Refer to this image for gluing on the wind screens and the crash protector.
These are the recommended control surface throws:
LOW HIGH
ELEVATOR
Up & Down
RUDDER
Right & Left
AILERONS
Up & Down
3/8"
[10 mm]
9°
1"
[ 25 mm]
14°
3/16"
[ 5 mm]
8°
1/2"
[13 mm]
11°
1-1/2"
[ 38 mm]
20°
3/8"
[10 mm]
9°
❏
4. Use your preferred glue to glue the windshields to the canopy hatch. Of the viable choices (Zap Goo, CA or canopy glue), canopy glue is most recommended because it dries absolutely clear and is easier to clean up (before it dries). Use tape where necessary to hold the windshields into position until the glue dries.
❏
5. Glue on the crash protector. Zap Goo is best here.
❏
6. Apply the decals using images from the kit box cover as a guide.
❏
2. If necessary, adjust the throws with the programming in your transmitter and/or adjusting where the pushrods connect to the servo arms and/or control horns.
❏
3. Now would also be a good time to set your Fail Safe .
Set Fail Safe on the throttle channel so that, in the event of loss of signal, the motor (or engine) cuts off. With the propeller removed from brushless motors, test your fail safe by advancing the throttle slightly (just enough to make the motor turn) and turning off the transmitter. If the Fail Safe is correctly set the motor will stop (or the carburetor will close for glow engines).
Check the C.G.
❏
1. The model should be completely ready to fl y with all components installed (fuel tank empty if using a glow engine).
PREPARE THE MODEL FOR FLIGHT
Set the Control Throws
CAUTION: If you’ve installed a brushless motor, remove the propeller while operating the radio to check the throws.
70mm
95mm
2-3/4"
3-3/4"
❏
1. Prop up the fuselage so the stab will be level. Measure and compare the throws to the recommended throws provided.
Note: the throws are measured at the widest part of the elevator and rudder.
21
The recommended C.G. is 2-3/4" – 3-3/4"
[ 70 mm – 95 mm] back from the leading edge of the wing at the fuselage sides.
❏ 2
. Use a Great Planes C.G. Machine to balance the model according to the measurements specifi ed, or mark the balance range on the top of the wings and lift it upside-down with your
fi ngertips. As long as the model balances anywhere within the specifi ed range it is acceptable (but less-experienced pilots should perform fi rst fl ights with the PT-19 balanced in the middle or forward half of the range—slightly nose heavy).
❏
3. If the PT-19 doesn’t balance where specifi ed, move the receiver battery or motor battery or add stick-on lead ballast to the nose or tail to achieve the correct C.G.
❏
4. If you’ve made any adjustments by adding ballast or moving components, check the C.G. again before fl ying.
Balance the Model Laterally
❏
1. Lift the PT-19 several times by the propeller shaft and the tail to see if one wing drops.
❏
2. If one wing drops consistently, add weight to the opposite tip by sticking it to the outside or strategically concealing it inside the balsa tip. An airplane that has been laterally balanced will track better in fl ight and maintain its heading better during maneuvers when the plane is climbing.
body part to try to stop the engine. To stop a gasoline powered engine an on/off switch should be connected to the engine coil. Do not throw anything into the propeller of a running engine.
WARNING: For brushless electric motors, never have the motor battery connected to the ESC without the transmitter turned on – after each fl ight (or any time after running the motor) always disconnect the battery before turning off the transmitter. And when ready to fl y (or whenever running the motor for any reason), always turn on the transmitter fi rst before connecting the motor battery.
Also make certain your failsafe is programmed correctly so in the event the receiver ever loses signal (or, if you inadvertently turn off the transmitter before disconnecting the battery or vice-versa) the motor will not turn. Follow the instructions that came with your radio control system to check and set the failsafe.
PREFLIGHT
The recommended RimFire .32 is rated for 50A constant current and 80A surge current, so it is desirable to load
(prop) the motor to operate within that range. The closer to
50A the longer you can fl y full-throttle and the closer to 80A the less you can fl y full-throttle until the motor gets too hot.
Engine/Motor Safety Precautions
Failure to follow these safety precautions may result in severe injury to yourself and others.
● Keep all engine fuel in a safe place, away from high heat, sparks or fl ames, as fuel is very fl ammable. Do not smoke near the engine or fuel; and remember that engine exhaust gives off a great deal of deadly carbon monoxide. Therefore do not run the engine in a closed room or garage .
●
Get help from an experienced pilot when learning to operate engines.
●
Use safety glasses when starting or running engines.
● Do not run the engine in an area of loose gravel or sand; the propeller may throw such material in your face or eyes.
● Keep your face and body as well as all spectators away from the plane of rotation of the propeller as you start and run the engine.
●
Keep these items away from the prop: loose clothing, shirt sleeves, ties, scarfs, long hair or loose objects such as pencils or screwdrivers that may fall out of shirt or jacket pockets into the prop.
●
Use a “chicken stick” or electric starter to start the engine.
Do not use your fi ngers to fl ip the propeller. Make certain the glow plug clip or connector is secure so that it will not pop off or otherwise get into the running propeller.
● Make all engine adjustments from behind the rotating propeller.
● The engine gets hot! Do not touch it during or right after operation. Make sure fuel lines are in good condition so fuel will not leak onto a hot engine, causing a fi re.
●
To stop a glow engine, cut off the fuel supply by closing off the fuel line or following the engine manufacturer’s recommendations. Do not use hands, fi ngers or any other
22
To begin, an APC 13 x 8E (on a 4S LiPo) draws about 58A static and momentary, maximum peaks of about 50–55A in the air, but averages a little less than 20A with “normal” throttle use. This is a suitable propeller choice and fl ies the
PT-19 well—it can be zoomed around boreing holes in the sky, or cruise at lower throttle settings for more scale-appearing fl ight and extended air time.
We’ve also fl own the PT-19 with a 13 x 10E on 4S which peps it up noticeably. Then, the static current rises to about
68A with momentary, maximum in-fl ight peaks up to around
70A and averages around 50A with normal throttle use. The
13 x 10E is another suitable propeller, but management prudent throttle
must be used so as not to overheat the motor and if necessary, it may be a good idea to allow the motor to cool between fl ights.
With every propeller, fl ight time depends greatly on how you use the throttle. Average current draw can be as low as 13
Amps up to as high as 50 Amps if you’re REALLY hard on the throttle.
In any case, use a fl ight timer initially set to a conservative time (4 minutes for example). When the timer sounds, land.
Resting (unloaded) voltage should not be below 3.75V/cell
measured with a volt meter after you land. When you charge the battery note how much capacity it took to recharge
(indicating how much was used for the fl ight). Strive to use no more than 80% of the battery’s capacity. Adjust your timer according to the voltage and capacity used for the fl ight.
You can also use the worksheet on page 24 to determine optimum flight times based on your flying style and battery capacity.
CAUTION: Never run the motor on the ground for more than a few seconds. Otherwise, you may overload the motor, battery or ESC.
Range Check
Don’t forget to perform your usual ground range checks as written in the instruction manual that came with your radio system to be certain it is operating correctly.
AMA SAFETY CODE
Read and abide by the following excerpts from the Academy of Model Aeronautics Safety Code. For the complete Safety
Code refer to Model Aviation magazine, the AMA web site or the Code that came with your AMA license.
Radio Control
1) I will have completed a successful radio equipment ground check before the fi rst fl ight of a new or repaired model.
2) I will not fl y my model aircraft in the presence of spectators until I become a qualified flier, unless assisted by an experienced helper.
3) At all fl ying sites a straight or curved line(s) must be established in front of which all fl ying takes place with the other side for spectators. Only personnel involved with fl ying the aircraft are allowed at or in the front of the fl ight line.
Intentional fl ying behind the fl ight line is prohibited.
4) I will operate my model using only radio control frequencies currently allowed by the Federal Communications Commission.
5) I will not knowingly operate my model within three miles of any pre-existing fl ying site except in accordance with the frequency sharing agreement listed [in the complete AMA Safety Code].
9) Under no circumstances may a pilot or other person touch a powered model in fl ight; nor should any part of the model other than the landing gear, intentionally touch the ground, except while landing.
FLYING
General
1) I will not fl y my model aircraft in sanctioned events, air shows, or model fl ying demonstrations until it has been proven to be airworthy by having been previously, successfully fl ight tested.
2) I will not fl y my model aircraft higher than approximately
400 feet within 3 miles of an airport without notifying the airport operator. I will give right-of-way and avoid fl ying in the proximity of full-scale aircraft. Where necessary, an observer shall be utilized to supervise fl ying to avoid having models fl y in the proximity of full-scale aircraft.
The PT-19 doesn’t exhibit any particular characteristics that you need to be aware of ahead of time. The PT-19 fl ies quite honestly and has no unusual tendencies. Same as any tail dragger, takeoffs and landings are usually smoother and more controllable in short grass, but takeoff from paved surfaces is fi ne too – you just have to be a little “quicker” on the rudder to optimize yaw control with the tail gear.
Landings usually work out a little better by “dragging” in the PT-19 with a few clicks above idle of throttle. Just let the PT-19 descend into a shallow, consistent sink rate and she’ll settle right in for landing.
3) Where established, I will abide by the safety rules for the fl ying site I use, and I will not willfully and deliberately fl y my models in a careless, reckless and/or dangerous manner.
Have a ball! But always stay in control and fl y in a safe manner.
GOOD LUCK AND GREAT FLYING!
5) I will not fl y my model unless it is identifi ed with my name and address or AMA number, on or in the model. Note: This does not apply to models while being fl own indoors.
7) I will not operate models with pyrotechnics (any device that explodes, burns, or propels a projectile of any kind).
23
1
2
3
4
5
6
7
8
A B
FORMULAS
Flight Time
(.10 ths )
Recharge
Capacity
C
B / A
mAh/minute
D
Battery
Capacity
E
D x .8
Target Capacity to Use in Flight
F
E / C
Recommended
Flight Time
G
B/1000 / (A/60)
Avg. In-Flight
Current
® Inc.
24
GPMA1212
advertisement
* Your assessment is very important for improving the workof artificial intelligence, which forms the content of this project
Related manuals
advertisement
Table of contents
- 2 Radio/Servos
- 2 Glow Engine
- 3 Brushless Electric Motor
- 3 LiPo Battery Charger
- 3 Adhesives, Hardware and Other Accessories
- 5 Hook Up the Ailerons
- 6 Join the Wing Halves
- 8 Mount the Landing Gear
- 10 Install the Electric Motor
- 12 Mount the Glow Engine
- 13 Hook Up the Throttle
- 13 Install the Fuel Tank
- 14 Fit the Cowl Over the Engine
- 16 Mount the Cowl
- 17 Finish Cutting the Cowl
- 19 Install the Radio
- 20 Scale Details
- 21 Set the Control Throws
- 21 Check the C.G
- 22 Balance the Model Laterally
- 22 Engine/Motor Safety Precautions
- 23 Battery Precautions
- 24 Range Check
- 24 General
- 24 Radio Control