advertisement
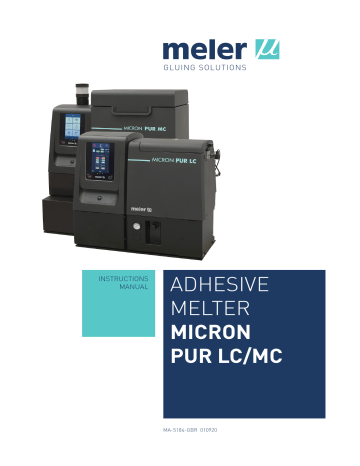
GLUING SOLUTIONS
INSTRUCTIONS
MANUAL
ADHESIVE
MELTER
MICRON
PUR LC/MC
MA-5184-GBR 010920
Published by:
Focke Meler Gluing Solutions, S. A.
Pol. Arazuri-Orkoien, c/B, nº3 A
E-31170 Arazuri - Navarra - Spain
Phone: +34 948 351 110 [email protected] - www.meler.eu
Focke Group
Edition August 2020
© Copyright by Focke Meler
All rights reserved. Its reproduction, diffusion or use by electronic or other means of all or any part of this document without the express authorization of its owner is strictly prohibited.
The specifications and information contained in this manual may be modified without prior notice.
The official language of this manual is only the English language. The remaining versions of the manual in other languages are mere translations without any official value or efficacy. In case of discrepancies or contradictions between the English version of the manual and any other version of the manual written in another language, the English version will prevail.
TABLE OF CONTENTS MA-5184-ENG MICRON+ PUR LC/MC ADHESIVE MELTER
TABLE OF CONTENTS
General 1-1
Symbols 1-1
Mechanical components 1-2
Electrical components
Hydraulic components
Pneumatic components
Thermal components
1-2
1-2
1-2
1-3
Materials 1-3
Noise emission declaration 1-3
Intended use 1-4
Limited use 1-4
Description 2-1
Hot-melt melter/applicator identification
Main components
Main components de Micron PUR Gear with two motor-pumps
Control panel components
Micron PUR series range
Micron PUR gear range option accessories
2-3
2-4
2-5
2-6
2-7
Bypass valve pressure control system
Optional equipment
2-7
MELER GLUING SOLUTIONS TABLE OF CONTENTS
Introduction 3-1
Installation requirements 3-1
Unpacking 3-3
Mounting the equipment
Electrical power connection
Pneumatic connection
Parameter Programming
Establecer temperaturas de trabajo
3-4
3-4
3-5
3-6
Selección del valor de sobretemperatura
Mantener la visualización de un elemento
Conexión de I/O externas
Salida de errores de tarjeta de bombeo
External I/O connections
Connecting external inputs and outputs
3-7
Interpretation of external inputs and outputs
External signals of pumping control
Connection of externar singnals for pumping control
3-13
TABLE OF CONTENTS
General information
Air- tight tank lid
Opening the air-tight tank lid
Filling the tank
Starting up the melter equipment
Manual pumping permmision
Melter equipment display
Interpretación de las pantallas
Home display
Temperature and Heating Shortcut displays
Menú Calendars
Units and Lenguage Menu
Date and time configuration
Alarms and warnings
Pumping control menu
MA-5184-ENG MICRON+ PUR LC/MC ADHESIVE MELTER
4-1
4-2
4-4
4-4
4-5
4-6
4-8
4-11
4-12
4-13
4-13
4-13
4-14
MELER GLUING SOLUTIONS TABLE OF CONTENTS
Modes of operation
Operating mode with internal pumping control and internal speed control
Operating mode with internal pumping control and external speed control
Operating mode with external pumping control and internal speed control
Operating mode with external pumping control and external speed control
Configuring speed ramp
Main Menu
‘1. Heating’ Menu
1.5 Extra temperature settings
‘2. General settings’ Menu
4-16
2.3 Configuration of input and output signals 4-27
‘3. Load’ Menu
Screen 1: Minimum adhesive level sensor
4-28
Screen 2: Automatic adhesive feeder
Screen 3: Dry air/gas injection
Screen 4: Pressurisation (only for units with an airtight tank lid)
‘4. Statistics’ Menu
Menu ‘5. Pumping’
Automatic pumping block function
‘Automatic pumping block’ enabled
‘Automatic pumping block’ disabled
‘Turning off after resetting’ function
‘Turning off after resetting’ enabled
4-29
4-30
4-31
4-33
‘Turning off after resetting’ disabled 4-34
4-20
4-20
4-21
4-25
TABLE OF CONTENTS MA-5184-ENG MICRON+ PUR LC/MC ADHESIVE MELTER
Configuration of turning on and activating pumping
Wireless communication (Wi-Fi)
Standby function
By-pass valve regulation
Adjust pneumatic valve control(DP1 / DP2) (optional)
Using the air drying system (optional)
Turning off the melter equipment
Application for PC
Equipment cleaning
System depressurisation
Access to the interior of the equipment
Filter maintenance
Cleaning the tank
Pump maintenance
Gear motor maintenance
Safety Thermostat
Air dryer filter maintenance
Remove the equipment from its base
5-7
5-7
5-8
5-8
5-9
5-4
5-5
5-1
5-3
5-3
4-34
4-36
4-37
4-38
4-39
4-39
4-40
MELER GLUING SOLUTIONS TABLE OF CONTENTS
6. TECHNICAL CHARACTERISTICS 6-1
Generals 6-1
Dimensions 6-2
Micron PUR gear range option accessories 6-3
Air drying system for PUR adhesives 6-3
Pneumatic by-pass valve pressure control system 6-4
Optional equipment
6-4
Components list
Pneumatic by-pass valve control system (optional)
A. TANK ASSEMBLY
B. DISTRIBUTOR UNIT
C. DISTRIBUTOR SIMPLE/ DOUBLE ASSEMBLY
D. GEARED MOTOR-PUMP ASSEMBLY
E. CHASSIS ASSEMBLY
F. ELECTRIC ASSEMBLY
G. ELECTRONIC ASSEMBLY
H. PNEUMATIC COMPONENTS
J. AIR DRYER ASSEMBLY (OPTIONAL)
EC DECLARATION OF CONFORMITY
9-9
9-10
9-11
9-12
9-4
9-5
9-6
9-7
9-8
8-1
SAFETY GUIDELINES MA-5184-ENG MICRON+ PUR LC/MC ADHESIVE MELTER
1. SAFETY GUIDELINES
General
The information contained in this section applies not only to everyday equipment operation, but also to any procedure carried out on it, whether for preventive maintenance or in the case of repairs and the replacement of worn out parts.
It is very important to observe the safety warnings in this manual at all times.
Failure to do so may result in personal injury and/or damage to the equipment or the rest of the installation.
Before beginning work on the equipment, read this manual carefully, and in case of any doubt, contact our Technical Service Center. We are available for any clarification that you might need.
Keep manuals in perfect condition and within reach of personnel that use the equipment and perform maintenance on it.
Also provide necessary safety material: appropriate clothing, footwear, gloves and safety glasses.
In all cases, observe local regulations regarding risk prevention and safety.
Symbols
The symbols used on both the melter/applicator equipment and in this manual always represent the type of risk we are exposed to. Failure to abide by a warning signal may result in personal injury and/or damage to the equipment or the rest of the installation.
Warning: Risk of electrical shock. Carelessness may produce injury or death.
Warning: Hot zone with high temperatures. Risk of burns. Use thermal protective equipment.
Warning: System under pressure. Risk of burns or particle projection. Use thermal protective equipment and glasses.
Warning: Important information for the correct use of the system. May include one or several of the previous hazards, and therefore must be kept in mind to avoid damage and injury.
Warning: Dangerous area. Risk of entrapment. Carelessness may produce injury or death.
1-1
1-2
MELER GLUING SOLUTIONS SAFETY GUIDELINES
Mechanical components
The hot-melt installation, which is installed to this device, requires moving parts that can cause damage. Use the equipment correctly, and do not remove the safety guards while the equipment is in operation; prevent the risk of possible entrapment due to moving mechanical parts.
Do not use the equipment if the safety devices are not in place or appear to be inadequately installed.
For maintenance or repair operations, stop the movement of moveable parts by turning off the main switch.
The device has no moving mechanical parts, so it does not pose risks to consider in this section.
Electrical components
The system works with single-phase or three-phase current of a certain power. Never handle the equipment with the power connected, as this may result in powerful electrical shocks.
The installation must be correctly grounded.
The installation’s power cable conductors must match the required electric current and voltage.
Periodically inspect the cables to check for crushing, wear and tear, as well as to prevent tripping and falls as a result of their placement.
Although the system meets EMC requirements, it is inadvisable to use devices that transmit high levels of radiation, i.e., mobile phones or soldering equipment in their vecinity.
Hydraulic components
As this is a pressurized system, precautions related to this type of equipment must be observed.
Before each operation, always make sure that the adhesive circuit is completely free of pressure. There is a high risk of hot particle projection, along with the corresponding danger of burns.
Use caution with the residual pressure that may remain in the hoses when the adhesive cools. When reheated, there is a risk of hot particle projection if the outputs are left open.
Pneumatic components
Some equipment uses compressed air to 6 bar pressure. Before any manipulation, please ensure that the circuit has lost fully air pressure. The risk of projection of particles at high speed can cause injury to a certain severity.
Extreme precautions with the residual pressure that could be contained in the circuit, before disconnecting any pneumatic feeding tube.
SAFETY GUIDELINES MA-5184-ENG MICRON+ PUR LC/MC ADHESIVE MELTER
Thermal components
The entire system works with temperatures that can exceed 200°C (392°F).
The equipment must be operated using adequate protection (clothing, footwear, gloves and protective glasses) that completely cover exposed parts of the body.
Keep in mind that, due to the high temperatures reached, the heat does not dissipate immediately, even when the power (in this case, electric) source is disconnected. Therefore, use caution, even with the adhesive itself. It may remain very hot, even in a solid state.
In case of burns:
1. If the burn is the result of contact with melted adhesive, do not try to remove the adhesive material from the skin. Do not try to remove it once it has solidified either.
2. Cool the affected area down immediately with lots of cold and clean water.
3. Seek medical attention as soon as possible either from the company’s medical service or the nearest hospital. Provide the medical staff with the
Safety Information Sheet of the adhesive.
Materials
Meler systems are designed for use with hot-melt adhesives. They should not be used with any other type of material, and especially not with solvents, which may cause personal injury or damage to internal system components.
Some units are specifically designed to use polyurethane reactive (PUR) hotmelt adhesives. Using PUR on a unit that is not prepared for that purpose may cause severe damage to the unit.
When using adhesive, follow the corresponding guidelines found in the
Technical and Safety Sheets provided by the manufacturer. Pay special attention to the advised work temperatures in order to prevent adhesive burning and degradation.
Ventilate the work area adequately in order to remove the vapors produced.
Avoid the prolonged inhalation of these vapors.
Always use original Meler components and replacement parts, which guarantee the correct system operation and service.
Noise emission declaration
The A-weighted emission sound pressure level (L pA does not exceed 70 dB(A) under any circumstances.
) of the unit in operation
The maximum C-weighted sound pressure level (L pCpeak sound power level (L
WA
) and the A-weighted
) do not exceed values worthy of mention and thus do not represent a specific risk that must be taken into account.
1-3
1-4
MELER GLUING SOLUTIONS SAFETY GUIDELINES
Intended use
The equipment are designed to be used in the following conditions:
• Hot-melt adhesive fusion and pumping at temperatures up to 200 °C
(392 ºF). Consult with Meler technical service to operate with higher working temperatures.
• Use of equipment with Meler accessories.
• Installation of equipment according to the security regulations currently in force and the instructions provided in this manual
(anchoring, electrical connection, hydraulic connection, etc).
• Use of equipment in non-explosive, non-chemically aggressive environments.
• Use of equipment following the safety instructions indicated in this manual, as well as on the labels accompanying the equipment, using adequate means of protection during each mode of operation.
Limited use
The equipment should never be used under the following conditions:
• Use with reactive polyurethane or any other material that might cause safety or health risks when heated.
• Use of equipment in environments where cleaning is necessary using water jets.
• Use of equipment to heat or melt food products.
• In potentially explosive atmospheres, aggressive chemical environments or outdoors.
• Use or operation without adequate safety protection.
• If the person in question does not have the necessary training to use the unit or to apply all of the necessary safety measures.
Note: Do not modify the equipment or use components that were not supplied by Meler. For any modification of a component of the equipment or part of the installation, you must firstly consult the After-Sales Service
INTRODUCTION MA-5184-ENG MICRON+ PUR LC/MC ADHESIVE MELTER
2. INTRODUCTION
In this manual you will find information about the installation, use and maintenance of the hot-melt adhesive melter in Meler’s ‘Micron PUR’ series
(hereinafter also referred only as Micron).
This melters series includes the PUR LC (low consumption) y PUR MC
(medium consumption) range of hot-melt adhesive melters and they are mainly designed to be used with thermo-reactive PUR based adhesives in block format. In case of Micron PUR LC can melted 2-2.5 kilos blocks of adhesive with maximal dimensions of Ø150mm and 160mm heigh and in case of Micron PUR MC, 20 kilos blocks of adhesive with maximal dimensions of
Ø290mm and 360mm heigh
Most of the photographs and illustrations that appear in this manual refer to the 5 Micron LC melter. This model has been used as a reference for writing this manual as its main characteristics, with the exception of the tank capacity and the connection outputs are the same as those in the rest of the equipments of the serie.
Description
These melters are designed for use with Meler hoses and applicators in hotmelt adhesive applications. Their different variations – line, coating or swirlspray – cover a wide range of applications, being very versatile in all markets where they are used.
2-1
MELER GLUING SOLUTIONS
MICRON+ ENGRANE
POMPA 1
Velocità reale: 53 rpm
Riferimento esterno 1
Permesso esterno 1
Switch 1
POMPA 2
Velocità reale:
50 rpm
49 rpm
Riferimento esterno 2
Permesso esterno 2
Switch 2
INTRODUCTION
Modes of operation
The hot-melt melters/applicators may be used in all of the following modes:
• READY Mode (Prepared). The melter keeps the components hot at the programmed working temperature. The pump is kept idle, awaiting an adhesive pump request.
• RUNNING Mode (in Operation). The unit pumps adhesive, and all programmed working conditions are correct.
Internal control of pumping and speed _ In this mode of operation, the user has full control of pumping and the set speed of the pump rotation.
Control of internal pumping and external speed_ This mode of operation is performed through internal pumping control and speed control by means of an external 0-10 V signal sent from the main machine.
Control of external pumping and internal speed_ This mode of operation is performed through external pumping control and manual speed control.
Control of external pumping and speed_ In this working mode, both pumping and speed are controlled from the main machine.
Speed is controlled by means of an external 0-10 V signal sent from the main machine.
• STOPPED Mode (Pumping disabled). The pump is kept disabled until the pump is either manually or automatically activated.
• Heating Mode. The unit heats the areas up to the programmed temperature. The pump is kept disabled.
• STANDBY Mode (Low consumption). The melter remains in standby while maintaining all active areas at a programmable temperature. The pump remains disabled.
• WARNING Mode. The melter detects an incorrect operation or warns the operator about the event. The unit can continue to operate.
• ALARM Mode. The melter detects an operation error or warns the operator about the event. Depending on the type of alarm, the unit may continue to operate for a programmed amount of time.
• ERROR Mode. The melter detects an operation error or warns the operator about the event. The unit cannot continue to operate, and pumping is stopped immediately. Depending on the type of error, the unit disconnects heating from all the areas.
• OFF Mode. The unit remains off with no areas heated and the pump disabled. The power and pneumatic supply from the network to the unit is maintained.
Hot-melt melter/applicator identification
When placing orders for replacement parts or requesting help from our service center, you should know the model and reference number of your hotmelt melter/applicator.
This and other technical information will be found on the identification plate located on the side of the lower part of the hot-melt melter.
2-2
INTRODUCTION MA-5184-ENG MICRON+ PUR LC/MC ADHESIVE MELTER
Main components
1. Front control card.
2. Access door to the electric/pneumatic area.
3. Tank access lid.
4. Main switch ON/OFF.
5. I/O card pumping control.
6. Air pressure gauge for pneumatic by-pass valve.
7. Pressure regulator of by-pass valve (opcionally pneumatic or mechanical regulator).
8. Pneumatic by-pass valve (optional mechanic valve).
9. Purge valve.
10. Hose output distributor (3 or 6 hydraulic connections depending on the type of pump-motor set).
11. Hose-applicator electrical connections.
12. Compressed air hook-up (max. 6 bar).
13. Characteristics plate.
14. Sistema secador de aire.
1 2 3
4
5 6 7
9
8
2-3
MELER GLUING SOLUTIONS INTRODUCTION
14
2-4
1
2
10 12 11 13
Main components de Micron PUR Gear with two motorpumps
3
Marking of the Micron PUR gear components is the same for all models with two motor-pumps. In this case the pictures refers to the PUR LC model.
For each motor-pump assembly installed:
1. Pumping control card 1
2. Pumping control card 2
3. Pressure regulator 1
4. Pressure regulator 2
5. Hoses output 1
6. Hoses output 2
7. Gear motor 1
8. Gear motor 2
5 7
4 6 8
INTRODUCTION
Control panel components
1. Touch screen.
2. Status central leds (GREEN, YELOW, RED).
3. RED led ‘pumping OFF’.
4. STOP RED Button ‘Start/Stop Pump’.
5. Touch screen ON/OFF button.
6. GREEN led ‘power ON’.
1
MA-5184-ENG MICRON+ PUR LC/MC ADHESIVE MELTER
2
3 6
4 5
2-5
2-6
MELER GLUING SOLUTIONS INTRODUCTION
Micron PUR series range
MICRON+ PUR LC / 2 M01 200 BE S4 PC A CL LD2 B1 SW MB S E UL
Certifications _ (in blank): CE
Control fusor _ (in blank): Internal •
E: Prepared for external melter control
Starbi integration (in blank): Not integrated •
S: Starbi integrated (2 channels)
Communications _ (in blank): No communication •
MB: ModBus • PB: ProfiBus • PN: ProfiNet •
EN: Ethernet-IP • W: Wifi
Pump on/off connector _ (in blank): No switch connector •
SW: with switch connector
Light tower _ (in blank): No light tower • B1: Low level•/ B2: Low level & temperature ok • B3: temperature ok
Level detector _ (in blank): No level detector • LD1: buoy detector installed • LD2: with capacitive detector installed • LD3: with high & low capacitive detectors installed
Automatic feeder _ (in blank): No feeder system • CL: external feeding from premelter
Air-dryer system _ (in blank): without dryer system •
A: with dryer system
Bypass valve pressure control _ MC: Mechanic control • PC: Pneumatic control • VP:
Proportional valve • P1: double pressure (regulator + network) • P2: double pressure
(external regulation)
Gear pump size __ S1: 1cc/rev • S2,5: 2,5cc/rev • S4: 4cc/rev • S8: 8cc/rev
D0,93: 2x0,93cc/rev • D1,86: 2x1,86cc/rev • D3,71: 2x3,71cc/rev • D4,8: 2x4,8cc/rev
* repeat for each pump installed separated by ‘/’ ; if there are two equal, once a ‘2’ before
Maximum temperature _ 200: 200°C • 230: 230°C
Sensory type _ M01: Pt100 • N01: Ni120 • R01: NTC-R
Electrical outputs _ 2 • 4 • 6
Tank capacity _ 5: 5kg • 10: 10kg • 20: 20 kg • 35: 35 kg
MICRON+ PUR series
(1) In case of simple pump up to 6 outputs but in case of double pump up to 4.
(2) In the case of two single pumps or two double pumps, place a 2 before the pump type (SX or DX). In the case of one single pump and a double pump, place the single pump (SX) first followed by the double pump (DX). The maximum number of pumps is two per equipment.
INTRODUCTION MA-5184-ENG MICRON+ PUR LC/MC ADHESIVE MELTER
Micron PUR gear range option accessories
If some of the different machine configuration options have been chosen, it will be necessary to purchase the following accessories:
Air dryer system
The air dryer system must be requested separately and is the same for all the units.
Bypass valve pressure control system
Pressure control can be effected through pneumatic or mechanical regulation.
By default, the equipment is fitted with pneumatically regulated pressure control.
Level control system
To detect a low level of melted adhesive, there is a choice between capacitive or float level detectors. Either can be used with any of our equipment, although if the detector is ordered after the equipment is delivered you may only use the float detector; the capacitive detector requires a housing inside the tank that must be made by machine.
Warning light option
The warning light must be requested separately. There is a choice of the low level and colourless (white) indicator light or the low level and temperature OK indicator light (green). They are both the same for all machines.
Level control system
To control the level of hotmelt inside the tank, a capacitive sensor can be placed that warns when the adhesive reaches the programmed level by means of a low level signal.
Optional equipment
To increase the functionality of the melter machines, the following optional elements can be incorporated:
• Wheels: these can be fitted to all the machines.
2-7
2-8
MELER GLUING SOLUTIONS INTRODUCTION
This page is intentionally left blank.
INSTALLATION MA-5184-ENG MICRON+ PUR LC/MC ADHESIVE MELTER
3. INSTALLATION
Warning: The melters/applicators are equipment with current technology and with certain foreseeable risks. Therefore, only allow qualified personnel with sufficient training and experience to use, install or repair this equipment.
Introduction
The ‘MICRON PUR’ series melters/applicators are delivered with all the materials necessary for their installation. However, some components must be provided by the user himself, according to the location and connections in each particular installation:
• Anchoring screws for the melter/applicator equipment
• Power cord and plug for electrical power
• Pneumatic pipe and connection to the compressed air system
• Multicore cable for external electrical control
• Optionally, a gas ventilation system
Installation requirements
Before installing ‘MICRON PUR’ series melter/applicator equipment, we must make sure that the space assigned to it permits installing, connecting and using the entire system. Similarly, we must check to see that the electrical and pneumatic supplies meet the necessary requirements of the melter/ applicator equipment being installed.
Free space
Item
A
B
C
D
E
Description
EQUIPMENT LENGTH
EQUIPMENT WIDTH
EQUIPMENT HEIGHT
EQUIPMENT HEIGHT WITH LID OPEN
EQUIPMENT LENGTH WITH ELECTRICAL CABINET OPEN
LONGITUD DEL EQUIPO CON SOPORTE PARA
VARIADORES DEL ARMARIO ELÉCTRICO ABATIDO
Dimensions
LC 730mm
MC 740mm
LC 420mm
MC 520mm
LC 630mm
MC 870mm
LC 910mm
MC 1215mm
LC 920mm
MC 990mm
LC 1280mm
MC 1355mm
3-1
MELER GLUING SOLUTIONS INSTALLATION
3-2
B
A
E
To calculate the space necessary for the installation of the equipment with respect to its length, in addition to the measurements indicated in the table,
280mm (minimum) must be added to open the access door to the distributor drain.
Electrical Consumption
In order to install, we should take into consideration the total consumption of the installation, including the consumption of the installed hoses and applicators.
Before connecting, make sure that the voltage that is being connected to the melter/applicator is the correct one appearing on the equipment’s characteristics plate.
Connect the machine and check to see if it is well grounded.
Warning: Risk of electrocution. Even when the equipment is turned off, voltage remains in the intake terminals, which may be dangerous during internal equipment manipulations.
Install a power switch for disconnecting the melter/applicator equipment from the electrical network. It must be protected against overload and short circuits by circuit breaker and install appropriate personal protection leads to mass by differential switch.
Consumption figures, according to melter/applicator and output configuration, are included in the table in the section ‘Electrical power connection’.
INSTALLATION MA-5184-ENG MICRON+ PUR LC/MC ADHESIVE MELTER
Compressed air
To install , it is necessary to have a dry, non-lubricated compressed air system with a maximum pressure of 6 bar.
The applicator’s internal pneumatic equipment is able to work with a minimum of 0.5 bar, however, pressure lower than this will cause intermittent operational anomalies.
The air consumption is according to the number of stroke made by the pump cylinder, which in turn depends on the adhesive consumption during the application. It is therefore necessary to estimate this consumption in all cases.
Generally speaking, we can provide as a maximum consumption value 40-50 l/min for a pressure of 6 bar at maximum pump speed.
Other factors
While installing , other practical considerations should be kept in mind:
• Keep the load opening accessible for comfortable melter/applicator filling.
• Position the melter/applicator equipment in such a way that you can easily see the front panel display where temperatures and possible alarm signals are shown.
• As much as possible, try to avoid unnecessarily long hoses that result in elevated electrical energy consumption levels and pressure drops.
• Do not install the melter/applicator equipment beside powerful heat or cooling sources that may have distortional effects upon its operation.
• Avoid melter/applicator vibrations.
• Make sure that the melter/applicator maintenance areas (filter, purging valve, tank interior, etc.) are easily accessible.
Unpacking
Before proceeding with the installation of the melter/applicator, it should be removed from its location on a pallet and examined in order to detect any possible breakage or deterioration. Communicate any defect, even to the outer packing materials, to your ‘meler’ Representative or to the Main Office.
Contents
Packing materials may contain accessories that form part of the same order. If this is not the case, the following are the standard components that accompany the melter/applicator:
• Instruction manual.
• Guarantee card.
• Hose couplings.
• Set connectors for Inputs / Outputs.
3-3
MELER GLUING SOLUTIONS INSTALLATION
Mounting the equipment
For mounting the equipments set the base in the desired location using the indicated holes M8 screws. To move the equipment more comfortably use the eyebolts included for this purpose.
Warning: Make sure that the bench where the base plate is fastened is level, free from vibrations and is able to support the weight of the equipment in addition to the full tank load.
Besides, these melters may come with wheels (optional) so they can be easily moved and located near to the main machine.
The four wheels turn 360º, and two are equipped with brakes. To move the unit, unlock the two wheels by lifting the lever.
Slide the unit to its final position. Lock the wheels once again, lowering the levers.
Electrical power connection
‘MICRON+’ series melters/applicators are designed to be connected to the electrical power supply in three possible ways, depending on the power of different elements connected:
3-4
• 1-phase 230 VAC with neutral
• 3-phases 240/400 VAC with neutral
A good ground connection is required in all cases.
UNIT
Micron+ PUR
LC
Micron+ PUR
MC
No. OUTPUTS
6
2
2
4
4
6
Los valores de consumo, según equipo fusor y configuración de salidas, son los que se ven en la tabla adjunta. Para este cálculo se ha tenido en cuenta sólo el caso de llevar bomba simple, para consumos con bomba doble, consultar. Debido a la conexión de alta potencia, Meler recomienda conectar trifásico 400/230 VAC con neutro.
1
Pump
27 A (!)
27 A (!)
27 A (!)
-
-
-
1 Phases
(1)
230 VAC
2
Pump
27 A (!)
27 A (!)
27 A (!)
-
-
-
Maximum connection power for each hose-applicator pair: 1,800W
3 Phases
1
Pump
400 VAC Y
2
Pump
12,80
19,76
25,09
22,80
27 A (!)
27 A (!)
14,17
21,13
25,09
24,17
27 A (!)
27 A (!)
Warning: Risk of electrical shock. Carelessness may cause injury or death.
(1) La máxima corriente admisible de conexión es de 27 A por fase. En la tabla se indican las corrientes máximas en el caso de utilizar la máxima potencia posible. Estimar en cada caso la potencia que va a instalarse para elegir la conexión idónea.
INSTALLATION MA-5184-ENG MICRON+ PUR LC/MC ADHESIVE MELTER
L N PE L1 L2 L3 N PE
1/N ~ 230V 50/60Hz + PE 3/N ~ 400V 50/60Hz + PE
Open the door of the electrical cabinet to its maximum position. Pass the power cable (max. Ø14.5mm) through the Pg16 grommet and fix it taking care that the cable is perfectly secured.
Connect each wire in the power cord to its corresponding place on the power intake connector on the power card.
Consumption values concerning each equipment can be found in the characteristics plate.
Pneumatic connection
If a pneumatically controlled by-pass pressure control valve is installed, the equipment must have a compressed air supply.
Before connecting the pneumatic power to the melter, make sure the pressure regulator is completely closed. To do this, turn the regulator handle located on the equipment base next to the pressure gauge counterclockwise as far as it will go.
Connect the plant air supply (max. 6 bar) to the melter intake using flexible tubing with an outside diameter of 6 mm. The equipment is provided with a quick coupling for this purpose.
Once the pump operation has been checked, you may adjust the pressure to the operational value you wish.
In the pressure gauge can be found pneumatic and hydraulic pressure values, the relation between both are 1:13.
Warning: A 6 bar on the grid, the maximum pressure on the hydraulic circuit reaches 80 bar. There is a risk of burns or particle projection. Use thermal protective gear and goggles.
Attention: Never exceed 6 bars of pneumatic pressure. This can cause serious equipment damage. Risk of high-speed projection of particles that can cause serious injuries
Ø6mm
P
3-5
3-6
MELER GLUING SOLUTIONS
1 3 5
2 4 6
INSTALLATION
Hose and applicator connection
These series melters use standard Meler components. The entire range of
Meler hoses and applicators may be connected to this equipment.
Up to six hose-applicator outputs may be connected Micron gear melters.
Micron gear series melters are equipped with a simple hydraulic distributor with four posibilities of hydraulic connection and double hydraulic distributor up to eight positions to connect the hoses. The outputs are not numered so the hoses can be connected to the distributor in any order.
Warning: When connecting hose-applicator outputs, verify that the connected power is not above the maximum allowable power for each output.
Caution:
• It is preferable to use couplings at 45º and 90° angle to minimize the space the hoses occupy. Using straight couplings usually results in curves with very small radii that may damage the inside of the hose.
• Save the screw-on caps that are removed from the distributor in order to connect a hose. They may be necessary in the future if a hose is removed from its location.
• Perform the electrical hose and applicator connections with the equipment turned off. Failing to do so may result in electrical defects in the connection and the appearance of alarm messages on the melter display.
Parameter Programming
Once the melter/applicator and its components are installed, you will need to program the operational parameters appropriate for the specific application that will be performed.
Among the various parameters, it is necessary to program the set point temperature values for each component connected and the value for overheating warnings. There are two other parameters (weekly start-up and shut-down programming and the standby temperature value) left to program in advanced systems, although the factory default values are perfectly valid for operational purposes.
Chapter “4. MELTER OPERATION” details the operating modes of the machine and its configuration.
INSTALLATION MA-5184-ENG MICRON+ PUR LC/MC ADHESIVE MELTER
External I/O connections
The input and output (Input/Output) signals enable the melter to communicate with the main machine simply and directly. Six I/O different signals can be used, depending on the options installed on the unit. Function of these signals can be selected by the user
The signals that can be used to communicate with the main machine are as follows:
Type (1) Description
Input
Terminal/Connector
External ON/OFF
A closed contact switches the unit on; an open contact turns it off.
Under maintenance external ON/OFF
A closed contact activates the ‘Under maintenance’ function; an open contact deactivates it and the unit returns to the status indicated by the unit’s other signals.
Pumping external OFF
A closed contact activates pumping (if the required conditions are met); an open contact deactivates it.
Activity (Auto Standby - OFF)
Contact for the activity control signal, to switch the unit to Standby and off mode (2) .
ON/OFF communications
A closed contact activates the communications (Modbus/Profibus); an open contact deactivates them. Signals must be enabled in the unit (3) .
Inhibition of zones
Zone inhibition control inputs. The unit has 8 contacts to inhibit 8 groups of programmable zones (4) . When the contact is closed, the respective group is inhibited (off); when the contact is open, the inhibition of that group is disabled
(activated).
(1) See point ‘4 Use / Settings Menu / Configuration of input and output signals’.
Some inputs will not be shown on the menu, depending on which options are installed in the unit.
(2) See point ‘4 Use / Heating Menu / Auto Standby - OFF’.
(3) See point ‘4 Use / Settings Menu / Additional Settings’.
(4) See point ‘4 Use / Heating Menu / Inhibitions’
(5) Connectors available according to options installed on the equipment..
Terminal
XDI1.1 / XDI1.2
XDI2.1 / XDI2.2
------
Connector on
HMI card (5)
DI3
Temperature Control
Board
X21 (Signals 1 to 4)
X9 (Signals 5 to 8)
X9 X21
DI3
3-7
3-8
MELER GLUING SOLUTIONS INSTALLATION
Type (1)
Output
Description
Standby
Contact indicating that the unit is in STANDBY mode.
Zones Temperature OK
During the heating phase: contact that indicates that all of the system’s temperatures have reached a level that is 3°C below its set point value (and the delay time has elapsed).
During normal operation: indicates that the actual temperature value is neither below nor above the programmed alarm values.
Machine Ready
Contact indicating that the unit is in READY mode (zones with Temperature OK and no errors).
Running
Contact indicating that the unit is in RUNNING mode (zones with Temperature OK, no errors, and pumping activated).
Alarm
Contact indicating that the unit is in ALARM or ERROR mode.
Level
Contact indicating that the adhesive level in the tank has reached the maximum limit.
No Level
Contact indicating that the adhesive level in the tank has reached the minimum limit.
Terminal/Connector
Terminal
XDO3.1 / XDO3.2
XDO4.1 / XDO4.2
------
Connector on
HMI card (2)
DO2
(1) See point ‘4 Use / Settings Menu / Configuration of input and output signals’.
Some outputs will not be shown on the menu, depending on which options are installed in the unit.
(2) Connectors available according to options installed on the equipment.
DO2
X9 X21
Attention: The ‘Temperature OK’ output is not a contact relay and, as such, it cannot support voltages of 230 V.
INSTALLATION MA-5184-ENG MICRON+ PUR LC/MC ADHESIVE MELTER
Connecting external inputs and outputs
Warning: Risk of electric shock. Carelessness may cause injuries or death.
1. Disconnect the unit’s power.
2. Open the front door of the electric cabinet by giving the fastening screw a 1/4 turn.
3. Run the signal cable (max. Ø14 mm) through the bushing at the rear of the unit (P) and attach it to the interior fitting, making sure the cable reaches the corresponding terminals/connectors.
4. Connect the two cable wires to the corresponding terminal/ connector. The polarity of the connection must be correct:
Terminal
XDI 1.1
XDI 1.2
XDI 2.1
XDI 2.2
Polarity
+24 VDC 200mA
IN
+24 VDC 200mA
IN
XDO 3.1
+24 VDC 100mA
XDO 3.2
OUT-
XDO 4.1
+24 VDC 100mA
XDO 4.2
OUT-
Connector
DI3 1
DI3 2
DO2 1
DO2 2
Polarity
+24 VDC 200mA
IN
+24 VDC 2A
GND
5. Make sure that the cables are properly secured by the terminal’s screws.
6. Check that the cable is correctly connected and that its passage through the electric cabinet presents no risk of jamming, being cut or any other accidental damage.
7. To assign the function to be performed by the connected signal, see point ‘4 Operation / Settings Menu / Configuration of input and output signals’’.
DI3
DO2
P
3-9
3-10
MELER GLUING SOLUTIONS INSTALLATION
Input
ON/OFF
Standby
Pumping OFF
Activity
Communications
Open
Close
Open
Close
Open
XDI1
Close
Open
Close
Open
Close
Interpretation of external inputs and outputs
The following tables show a summary of the status of each input and output signal of the unit.
Connection
XDI2
Close
Open
Close
Open
Close
Open
Close
Open
Close
Open
DI3
Close
Open
Close
Open
Close
Open
Close
Open
Close
Open
Description
ON
OFF
Standby
No Standby
No pumping
No Action
Transition detected
Transition detected
No Comms
No action
+24
IN
GND
1
2
3
HMI
DI1
DI2
Melter
+24V
1
XDI1
XDI2
2
SIGNAL
External machine
6
CLOSE = 1
OPEN = 0
+24
IN
GND
1
2
3
HMI
DI3
+24V
Melter
SIGNAL
External machine
6
CLOSE = 1
OPEN = 0
INSTALLATION
Output
StandBy
Zones in
Temperature OK
Machine Ready
Running
Alarm
Level
No Level
+24V
GND
+24V
GND
DO2
+24V
GND
+24V
GND
+24V
GND
+24V
GND
+24V
GND
Close
Open
Close
Open
Close
Open
Close
Open
Connection
XDO3
Close
Open
Close
Open
Close
Open
XDO4
Close
Open
Close
Open
Close
Open
Close
Open
Close
Open
Close
Open
Close
Open
MA-5184-ENG MICRON+ PUR LC/MC ADHESIVE MELTER
Description
In "STADBY"
No "STANDBY"
In “ Temperature OK”
No “ Temperature OK”
Ready
No Ready
Pumping
Not Pumping
Alarms
No Alarms
Level “OK”
Level “No OK”
Level “No OK”
Level “OK”
CLOSE = 1
2
OPEN = 0
1 OUT+
HMI
DO3
DO4
2 OUT-
Melter
+24V
1
2
XDO3
XDO4
SIGNAL
CLOSE = 1
2
OPEN = 0
1 OUT+
HMI
DO2
2 OUT-
Melter
+24V
SIGNAL
3-11
MELER GLUING SOLUTIONS INSTALLATION
Connecting zone inhibition
Warning: Risk of electric shock. Carelessness may cause injury or death.
1. Disconnect the unit’s power.
2. Remove the electrical cabinet casing following the instructions given in the maintenance section ‘Removal and replacement of casing elements’.
3. Open the electrical cabinet side panel by loosening the screw indicated.
Use Allen wrench 3.x
.
3-12
X9
X21
P
4. Run the signal cable (max. Ø14mm) through the bushing at the rear of the unit and attach it to the interior fitting, taking care to ensure that the cable reaches the connectors (X21 / X9) in the temperature control board.
5. Remove the connectors from the board and connect the cable wires to their corresponding terminals. To activate it, all disabling signals must be switched with the GND pin.
X9 X21
+24 8 7 6 5 GND +24 4 3 2 1 GND
X
é é é é é
X
é é é é é
6. Reconnect the connectors to the board.
7. Check that the cable is correctly connected and that its passage through the electric cabinet presents no risk of jamming, being cut or any other accidental damage.
8. To configure the various inhibition groups and assign them the corresponding signal, see point ‘4 Use / Heating Menu / Inhibitions’’.
INSTALLATION MA-5184-ENG MICRON+ PUR LC/MC ADHESIVE MELTER
External signals of pumping control
The signals that can be used for pumping control externally are:
Type
Input
Description
External speed control pump 1 / pump 2
Contact for the external regulation of the pumping speed according to a programmed ramp.
External pump control pump 1 / pump 2
Contact for external activation and deactivation of the pump. The closed contact activates the pump and the open contact deactivates it.
Output
Drive error pump 1 / pump 2
Contact indicating that the pump drive is in error mode.
Connection of externar singnals for pumping control
Warning: Risk of electric shock. Carelessness may cause injury or death
1. Disconnect the unit’s power.
2. Open the front door of the electric cabinet by giving the fastening screw a 1/4 turn.
3. Run the signal cable (max. Ø14 mm) through the bushing at the rear of the unit (P) and attach it to the interior fitting, making sure the cable reaches the corresponding terminals.
4. Connect the two cable wires to the corresponding terminal. The polarity of the connection must be correct:
Borne
Pump 1
XV1.1
XV1.2
XP1.1
XP1.2
XE1.1
XE1.2
Polarity
+ ISOLATED 0-10V
GND
+24 VDC 400mA
IN
OUT+ 24 VDC 100mA
OUT- 24 VDC 100mA
Borne
Pump 2
XV2.1
XV2.2
XP2.1
XP2.2
XE2.1
XE2.2
Polarity
+ ISOLATED 0-10V
GND
+24 VDC 400mA
IN
OUT+ 24 VDC 100mA
OUT- 24 VDC 100mA
5. Make sure that the cables are properly secured by the terminal’s screws.
6. Check that the cable is correctly connected and that its passage through the electric cabinet presents no risk of jamming, being cut or any other accidental damage.
7. To assign the function to be performed by the connected signal, see point ‘4 Operation / Pumping control menu’ y ‘4 Operation / Modes of operation’.
Terminal
Pump 1: XV1.1 / XV1.2
Pump 2: XV2.1 / XV2.2
Pump 1: XP1.1 / XP1.2
Pump 2: XP2.1 / XP2.2
Pump 1: XE1.1 / XE1.2
Pump 2: XE2.1 / XE2.2
P
3-13
3-14
MELER GLUING SOLUTIONS INSTALLATION
This page is intentionally left blank.
MELTER OPERATION MA-5184-ENG MICRON+ PUR LC/MC ADHESIVE MELTER
4. MELTER OPERATION
In this section we will introduce the method for using the melter. Although its operation is very simple, it should not be used by untrained personnel.
Warning : Improper use may cause damage to the machine or injury and even death to the person using it.
General information
MICRON+ ENGRANE
There are three large groups of components with thermal control in a hotmelt installation: the fusion unit, the transport hoses and the applicators. All of these are controlled from the front panel of the melter.
The first large group is the tank-distributor group. Combined to form a single unit, they have separate controls even though their set point values are the same. Therefore, when you program a set point value for the tank, for example
170°C, the distributor adopts this same value. If two pumps are installed, the distributors occupy channels 1 and 2 with set point values and control that are independent to the tank and to each other.
The second group is the hose group. They are identified on the front panel, depending on the equipment model, by number, from No.1 to No.6 and by the corresponding hose picture. Each one has its own set point value.
The third group is the applicator group. It is identified on the front panel, depending on the equipment model, by number from No.1 to No.6 and by the corresponding applicator picture. Each one has its own set point value.
The hose and applicator numbers are automatically assigned to the hose/ applicator channel they are connected to on the rear part of the melter.
A 154
°C
08:31
154
154
1
2
85
00
185
154
100
---
42
1
2
3
4
5
6
15:35
170
154
100
---
42
1 3 5
2 4 5
4-1
MELER GLUING SOLUTIONS MELTER OPERATION
Air- tight tank lid
Micron PUR equipment comes with an air-tight tank lid. This tank lid is useful when the equipment is used with P.U.R. adhesives. As mentioned in previous sections, these adhesives require a completely dry environment before being applied as they deteriorate when they come into contact with humidity in the atmosphere.
The dry environment is achieved thanks to the incorporation of an air dryer that make possible the conservation of the adhesive without hardening premature inside the system of application of the unit.
For safety measures the system incorporates an inductive sensor that detects if the outer lid is opened or closed. When this outer lid gets up or when there is a cut in the electrical supply the exhaust valve opens, consequently pressure inside tank becomes the atmospheric one. The connections of the system can consult in the corresponding chapter ‘Electrical drawings‘.
4-2 magnetic sensor outer lid
1 air- tight tank lid
Opening the air-tight tank lid
If you need to open the air-tight tank lid the system acts as follows:
1. When the system detects the outer lid has been opened, by means of the lid detector, it automatically release the pressure of the tank to assure a safety handle of the air-tight tank lid.
De-pressurization is done through an exhaust valve, connected directly to the outer ambient. Then, the air-tight lid can be opened safely.
For the Micron PUR LC equipment:
2. Turn the handwheel on the air-tight tank lid counter-clockwise (2) until it is released.
3. Use the handle to lift the air-tight tank lid (3).
4. To close the air-tight tank lid, use the handle to lower it (3) and then turn the handwheel clockwise to lock it (2).
2
3
5. Close the outer lid.
For the Micron PUR MC equipment:
2. Turn the handle anti-clockwise sense until the position shown in the
MELTER OPERATION MA-5184-ENG MICRON+ PUR LC/MC ADHESIVE MELTER image (2).
3. Lift the air-tight tank lid using the handle (2)and put it on its maximum position. A blocking fastener fix it to remain opened.
4. To close the air-tight, unlock the fixing mechanism, holding the lid with the other hand.
5. Turn the handle in clockwise sense to fix it.
6. Close the outer lid.
When the system detects the outer lid closed acts as follows:
1. With the exhaust valve opened, it is injected dry air for 0.5 min. This restores the air into the tank.
2. The exhaust valve is closed and continue the injection of air for 0.5 min.
This refills the tank with dry air to the pressure regulated.
3. The injection valve is closed and starts the automatic cycle.
1
2 3 output valve
4-3
4-4
MELER GLUING SOLUTIONS MELTER OPERATION
Filling the tank
The tank can be equipped with a low level sensor (optional) that warns when the adhesive reaches the programmed level.
The unit will activate the external signal and, if it is connected, the corresponding warning device.
Warning : Before refilling the tank, make sure that the adhesive is the same type as that already in the tank. Mixing different types of adhesives can cause damage to the melter equipment.
To fill the tank:
1. Open the outer lid and the air-tight tank lid.
2. Fill the tank with adhesive block of 2-2.5 kg in case of Micron PUR LC and adhesive block of 20 kg in case of Micron PUR MC.
3. Open the adhesive block and insert it into the cylindrical tank.
4. Close the air-tight lid and the outer lid when you have finished refilling the tank.
Warning : Risk of burns. Always refill using protective gloves and goggles.
Starting up the melter equipment
Before starting up the melter equipment, it is necessary to check to see if the unit has been correctly installed and all its input/output and accessory connections are correctly established.
It is also necessary to make sure that the equipment has been filled with adhesive and that the operational parameters have been programmed.
To start:
1. Connect the melter’s switch.
When the switch is actuated, the GREEN POWER LED remains lit. The unit is powered but the screen stays off.
2. When you press the ON/OFF button, the screen lights up and the POWER
LED stays lit. The main screen shows the unit’s status.
One it has reached 3° below the programmed temperature (set point) of the all active elements, a programmable delay timer starts until, guaranteeing fusion, the pump receives permission to operate and the signal will be sent to the main machine by the external output ‘READY’.
While the system counts down the delay time, the temperature OK symbol flashes until the programmed time value is reached. The screen displays the actual temperature values for each zone at all times.
If the temperatures of all the active zones exceed the set point temperature -3° in under 5 minutes, the unit will pass to ‘Temperature OK’ status without taking the ‘Pumping Permission Delay’ into account.
MELTER OPERATION MA-5184-ENG MICRON+ PUR LC/MC ADHESIVE MELTER
Unit status
Heating
Symbol on the display
Central LED Description
The unit is heating the programmed zones.
Delay
Standby
08:31
The zones are at Temperature OK but the
‘Pumping Permission Delay’ is activated
The tank or the distributor are in standby mode.
Inhibition The tank or the distributor are inhibited.
Warning
The unit has an operating error but can continue operating.
Alarm
The unit has an operation error and continues to operate for a programmed amount of time.
Error
The unit has an operating error and cannot continue operating.
Zones in Temperature OK
3. Use the machine’s pressure gauge to make sure that the generated pressure is adequate. Values below 0.5 bar may cause erratic pump action.
The zones are at the set point temperature.
Manual pumping permmision
Warning: Automatic pumping permission depends on the type of set-up and the installation conditions of the unit. For more information, please see the
‘Automatic pumping block function’ and ‘Setting up the turning on and activation of pumping’ sections.
When the unit reaches the programmed operating temperature (Zones in
Temperature OK), and there are no errors, the pump can be activated (READY) or disabled (STOPPED) by pressing the ‘STOP’ key.
STOPPED
MODE
READY
MODE
When the pump is deactivated(STOPPED), the red LED next to the key stays lit.
Press to activate pumping
Press to deactivate pumping
4-5
MELER GLUING SOLUTIONS MELTER OPERATION
MICRON+ ENGRANE
HMI
TC
IO
IO
: S02001100 v1.0.106
: S02200100 v1.0.084
: S02102100 v1.0.106
: S02101100 v1.0.106
Alarms
RESET ALL
2018-05-20 11:15
RESET
A12: Over temperature zone 6.1
MICRON+ ENGRANE
HMI
TC
IO
IO
2018-05-20 10:45
2018-05-20 10:03
: S02001100 v1.0.106
: S02200100 v1.0.084
: S02102100 v1.0.106
: S02101100 v1.0.106
RESET
RESET
2018-05-20 08:32
W14: Low Temperature Tank
Allarms menu
MICRON+ ENGRANE
HMI
TC
IO
IO
: S02001100 v1.0.106
: S02200100 v1.0.084
: S02102100 v1.0.106
: S02101100 v1.0.106
General Standby General OFF
Temperature
General Set-Point
General Variation
State
-
150
5 +
Area
T: Tank
D: Distributor
1.1: Hose 1
1.2: Applicator 1
2.1: Hose 2
2.2: Applicator 2
Real
152
150
49
170
130
100
Set Point
150
150
OFF
155
145
100
Menú Heating menu
MICRON+ ENGRANE
HMI
TC
IO
IO
: S02001100 v1.0.106
: S02200100 v1.0.084
: S02102100 v1.0.106
: S02101100 v1.0.106
Deutsch
Italiano
Polski
Nederlandse
°C
Español
°F
Français
Portugues
Česky
MICRON+ ENGRANE
HMI
TC
IO
IO
: S02001100 v1.0.106
: S02200100 v1.0.084
: S02102100 v1.0.106
: S02101100 v1.0.106
Melter equipment display
The 7-inch touchscreen shows the main data and contains a user menu to customise how your unit is configured and operated.
HMI
TC
IO
IO
: S02001100 v1.0.106
: S02200100 v1.0.084
: S02102100 v1.0.106
: S02101100 v1.0.106
Calendar
Enable all the calendars
C1 C2 C3 C4 C5 C6
M T W T F S S
Hour
07:00
ON Standby OFF
Home display
A 154
°C
08:31
154
154
1
2
85
00
13:15
15:00
IO
00.00
00.00
: S02001100 v1.0.106
: S02200100 v1.0.084
: S02102100 v1.0.106
: S02101100 v1.0.106
Calendars menu
PUMP 1
Real speed: 53 rpm
External reference 1
External permission 1
Switch 1
PUMP 2
Real speed:
50 rpm
49 rpm
External reference 2
External permission 2
Switch 2
185
154
100
---
42
3
4
1
2
5
6
15:35
170
154
100
---
42
MICRON+ ENGRANE
HMI
TC
IO
IO
: S02001100 v1.0.106
: S02200100 v1.0.084
: S02102100 v1.0.106
: S02101100 v1.0.106
Pumping control menu
Password: ******
Restore password code A: 1285
2019-05-27
Date & Time
13:35
HMI
TC
IO
IO
: S02001100 v1.0.106
: S02200100 v1.0.084
: S02102100 v1.0.106
: S02101100 v1.0.106
Date
YYYY
2019
MM
05
DD
27
Time
HH
13
MM
35
Software version
HMI
TC
IO
IO
: S02001100 v1.0.106
: S02200100 v1.0.084
: S02102100 v1.0.106
: S02101100 v1.0.106
Sensor technology: PT100
Scan the code to download the user manual
1. Heating
3. Charge
5. Pumping
Menu
2. Settings
4. Statistics
Units and Language menu Date and time Menu Main menu
4-6
MELTER OPERATION MA-5184-ENG MICRON+ PUR LC/MC ADHESIVE MELTER
General characteristics
In general, there are several icons and pieces of information that are repeated throughout the screen navigation, so they will be explained at the beginning and then not in the next screens.
Navigation icons
Right arrow icon (FORWARD), located in the lower right part of the screen.
Appears when there is a possibility of navigation to a next screen. From the
HOME screen it provides access to the MENU.
Left arrow icon (BACK), located in the lower left part of the screen. This icon appears on all the menu screens, allowing you to return to the previous screen.
MICRON+ ENGRANE
From any screen you can return to the main screen by clicking on the icon
(HOME) located in the bottom centre of the screen.
HMI
TC
IO
IO
: S02001100 v1.0.106
: S02200100 v1.0.084
: S02102100 v1.0.106
: S02101100 v1.0.106
Save changes
Press to save
MICRON+ ENGRANE
Interpretación de las pantallas
IO
IO
White: editable text.
Blue: non-editable text.
BACK HOME FORWARD
The ‘SAVE CHANGES’ icon, located in the upper right part of the screen, appears in the data entry and programming screens. If the data shown on the screen is stored, the icon appears with a blue background. If the data has not been stored, the icon is shown with a green background.
Note: In some options, the unit does not automatically store programming data. Whenever you modify or program any data that you wish to keep press
“SAVE CHANGES”.
Alphanumeric keyboard
Temperature:
T: Tank
Real
152 °C
Standby
PID: Standard
Set Point
150 °C
-60 °C
!
Parameters saved
P:
I:
30
12
2.2 Extra Settings
Sound on alarm
Screen saver
10 min
Inside device temperature alarm
85 °C 60 s
!
D: 300
Green: press to save.
Blue: parameters saved.
White: editable parameter.
Grey: non-editable parameter.
Numeric keyboard
Green: activated.
White: deactivated.
Grey: disabled.
Pumping autolock
OFF after reset
Modbus
Node: 10 B: 57600
4-7
MICRON+ ENGRANE
HMI
TC
IO
IO
: S02001100 v1.0.106
: S02200100 v1.0.084
: S02102100 v1.0.106
: S02101100 v1.0.106
A
D
J
H
MELER GLUING SOLUTIONS
L
MELTER OPERATION
A 154
°C
08:31
154
154
1
2
185
154
100
---
42
3
4
1
2
5
6
15:35
170
154
100
---
42
Home display
It is the main screen where the most representative values of the equipment are shown.
85
00
E
F
G
B
C
I
K
A - Alarms status and alarms menu access.
B - Temperature status and Temperature and Heating
Shortcut menu access.
C - Calendar activated/deactivated.
D - Adhesive level status.
E - Adhesive tank real temperature.
F- Pumping activated/not activated. Pump speed.
G - Distributor real temperature.
H - Hoses real temperature zones.
I - Applicators real temperature zones.
J - Hose/applicator symbol.
K - Pattern controller connected to the equipment
L - Access to the Language menu
M - The system’s time and access to the system’s Date/
Time menu.
to MAIN MENU screen
General temperature status
Active zones in Temperature OK.
08:31
Unit heating up.
Unit heating up.
‘Pumping Permission Delay’ countdown timer, once all the active heated components have reached their set point temperature ± 3°.
Unit in Standby mode.
Unit in Inhibition mode.
Unit in overheating or low temperature alarm.
Moreover, this icon shows whether the temperature is indicated in °C or °F.
Access the Temperature and Heating Shortcut displays menu by pressing the icon .
4-8
MELTER OPERATION
Alarms status
MA-5184-ENG MICRON+ PUR LC/MC ADHESIVE MELTER
There are no errors.
The unit has an operating error but can continue operating.
The unit has an operating error and cannot continue operating.
Access the ALARMS menu by pressing the icon.
Calendar status
Calendar not activated.
Calendar activated
Access the CALENDAR menu by pressing the icon.
Adhesive level status
• WITHOUT automatic loading
• WITHOUT level sensor
• WITHOUT automatic loading
• WITH level sensor.
Adhesive level nearly empty
• WITHOUT automatic loading
• WITH level sensor.
Adhesive level sufficient
• WITH automatic loading
• Adhesive level nearly empty
• WITH automatic loading
• Adhesive level nearly empty and
LOADING
• WITH automatic loading
• Adhesive level sufficient and
LOADING (extra time)
• WITH automatic loading
• Adhesive level sufficient
4-9
4-10
MELER GLUING SOLUTIONS MELTER OPERATION
Pumping status
Pumping not activated.
Pumping activated.
Pumping error.
Access the PUMPING menu by pressing the icon.
Temperature status
083 Zone heating.
There is no physical connection of components in that zone.
---
150
120
Temperature sensor error in that zone.
Zone in Temperature OK.
Zone in Standby mode.
52 Zone in Inhibition mode (OFF).
165
170
Zone in overheating or low temperature warning.
Note: For a zone to be able to give a low temperature warning, it must have first reached its set point temperature.
Zone in overheating or low temperature alarm.
Note: For a zone to be able to give a low temperature warning, it must have first reached its set point temperature.
Access the SHORTCUTS menu by pressing the temperatures area.
MELTER OPERATION MA-5184-ENG MICRON+ PUR LC/MC ADHESIVE MELTER
Temperature and Heating Shortcut displays
HMI
TC
IO
IO
: S02001100 v1.0.106
: S02200100 v1.0.084
: S02102100 v1.0.106
: S02101100 v1.0.106
A
C
F
G
General Standby General OFF
Temperature
General Set-Point
General Variation
-
State
150
5 +
Area
T: Tank
D: Distributor
1.1: Hose 1
1.2: Applicator 1
2.1: Hose 2
2.2: Applicator 2
Real
152
150
49
170
130
100
Set Point
150
150
OFF
155
145
100
B
D
E
H
MICRON+ ENGRANE
HMI
TC
IO
IO
: S02001100 v1.0.106
: S02200100 v1.0.084
: S02102100 v1.0.106
: S02101100 v1.0.106
J
L
General Standby General OFF
Temperature
Group OFF
State
OFF Group: 1
Area
T: Tank
D: Distributor
1.1: Hose 1
1.2: Applicator 1
2.1: Hose 2
2.2: Applicator 2
Standby OFF
A - General standby of the unit (activate/deactivate).
B - General inhibition of the unit (activate/deactivate).
C - Programming of temperatures.
D - General set point temperature (all zones).
E - Temperature variation over the set point.
F - Temperature zones (14 zones).
G - Actual temperature.
H - Set point or control temperature.
• Unit ON: Setpoint temperature.
• Unit or Component on Standby: Standby Temperature.
• Component Disabled: OFF
Green: activated. Grey: deactivated
I
K
I - Programming of zone statuses.
J - Inhibition/activation by groups of zones.
K - Group selection.
L - Activation of Standby in each zone.
M - Activation of Inhibition in each zone.
M
4-11
MICRON+ ENGRANE
HMI : S02001100 v1.0.106
TC : S02200100 v1.0.084
IO : S02102100 v1.0.106
IO : S02101100 v1.0.106
MICRON+ ENGRANE
HMI : S02001100 v1.0.106
TC : S02200100 v1.0.084
IO : S02102100 v1.0.106
IO : S02101100 v1.0.106
MELER GLUING SOLUTIONS
General Standby General OFF
Temperature State
General Set-Point
General Variation
Area Real
T: Tank
D: Distributor
1.1: Hose 1
1.2: Applicator 1
2.2: Applicator 2
Temperature
152
150
49
170
130
1
100
-
150
5
Set Point
150
150
OFF
155
3
1
+
2
100
State
2
Group OFF
OFF Group: 1
3
T: Tank
Area
D: Distributor
1.1: Hose 1
1.2: Applicator 1
2.1: Hose 2
2.2: Applicator 2
Standby
4
OFF
5
3
MICRON+ ENGRANE
HMI : S02001100 v1.0.106
TC : S02200100 v1.0.084
IO : S02102100 v1.0.106
IO : S02101100 v1.0.106
Calendar
Enable all the calendars
C1 C2 C3 C4 C5 C6
M T W T F S S
Hour
07:00
11:00
13:15
15:00
00.00
00.00
ON Standby OFF
MELTER OPERATION
Programming of temperatures
1. Enter a temperature in ‘General set point’ to simultaneously program all the zones with that temperature value.
2. To make quick adjustments, enter a variation value in ‘General variation’ and add (+) or subtract (-) it from the ‘General set point’ value. The value is simultaneously added or subtracted in all zones.
3. To program each zone individually, click on the ‘Set point’ value and enter the new desired temperature value.
Programming of statuses
1. Press ‘General Standby’ to activate (green) or deactivate (grey) the Standby mode in all zones.
With the ‘General Standby’ mode activated (Equipment in Standby) it is not possible to activate each Zone individually.
2. Press ‘General Off’ to activate (green) or deactivate (grey) the Inhibition in all zones.
With the ‘General Off’ mode activated (Equipment OFF) it is not possible to activate each Zone individually.
3. To inhibit a group of zones, select the group and activate the inhibition
(green). To define the different groups, see the ‘Inhibitions’ point.
4. Press ‘Standby’ in each zone to individually activate (green) or deactivate
(white) the Standby mode.
5. Press ‘OFF’ in each zone to individually activate (green) or deactivate
(white) the inhibition..
Menú Calendars
This menu allows you to program a calendar with the unit’s status changes.
Once it is activated, the unit changes from one status to another automatically.
When the unit is switched on, it does so in the mode that has been programmed in the calendar, if the calendar is activated.
You can create up to six calendars (C1, C2, etc.) and up to six status changes per day, indicating whether the unit will be in ON, Standby or Inhibition (Off).
From the ‘Select all calendars’ option, you can simultaneously activate or deactivate all the calendars you have created.
You can add different days of the week to each calendar. Keep in mind that a single day cannot be programmed in two active calendars. Therefore, if a day of the week is programmed in an active calendar, it can only appear in other calendars if they are disabled.
4-12
MELTER OPERATION MA-5184-ENG MICRON+ PUR LC/MC ADHESIVE MELTER
MICRON+ ENGRANE
HMI : S02001100 v1.0.106
TC : S02200100 v1.0.084
IO : S02102100 v1.0.106
IO : S02101100 v1.0.106
Units and Lenguage Menu
• Units: To select whether the temperatures are displayed in °C/°F.
• Language configuration: Press the desired language.
°C °F
Español
Deutsch
Italiano
Français
Portugues
Polski Česky
Date and time configuration
MICRON+ ENGRANE
HMI : S02001100 v1.0.106
TC : S02200100 v1.0.084
IO : S02102100 v1.0.106
IO : S02101100 v1.0.106
This screen allows you to view and modify the date and time data of the system.
It also shows:
• The equipment software version.
• A QR code, to be able to download the user manual.
• The type of technology of the installed sensors.
Nederlandse
2019-05-27
Date & Time
13:35
Date
YYYY
2019
MM
05
DD
27
Time
HH
13
MM
35
Software version
HMI : S02001100 v1.0.106
TC : S02200100 v1.0.084
IO : S02102100 v1.0.106
IO : S02101100 v1.0.106
Sensor technology: PT100
Scan the code to download the user manual
Alarms and warnings
MICRON+ ENGRANE
It displays the alarms and warnings in chronological order. It shows 5 alarms on each screen, with a total of 3 screens.
HMI : S02001100 v1.0.106
TC : S02200100 v1.0.084
IO : S02102100 v1.0.106
IO : S02101100 v1.0.106
When an alarm/warning needs to be reset for the unit to return to operation, a button appears for you to press and confirm that the problem has been resolved.
The ‘Delete logs’ button appears on the screen to delete all the alarm/warning logs.
Alarms
RESET ALL
2018-05-20 11:15
RESET
A12: Over temperature zone 6.1
2018-05-20 10:45
RESET
A19: Over temperature applicator 2
2018-05-20 10:03
A66: Thermostat
2018-05-20 09:12
RESET
A53: Broken sensorzone hose 6
2018-05-20 08:32
W14: Low Temperature Tank
4-13
MELER GLUING SOLUTIONS
MICRON+ ENGRANE
HMI : S02001100 v1.0.106
TC : S02200100 v1.0.084
IO : S02102100 v1.0.106
IO : S02101100 v1.0.106
PUMP 1
Real speed: 53 rpm
External reference 1
External permission 1
Switch 1
PUMP 2
Real speed:
50 rpm
49 rpm
External reference 2
External permission 2
Switch 2
MICRON+ ENGRANE
HMI : S02001100 v1.0.106
TC : S02200100 v1.0.084
IO : S02102100 v1.0.106
IO : S02101100 v1.0.106
3
4
1
2
5
10
5
0
0
Pumping
Volt
0,0
3,0
4,0
7,0
10 rpm
0
20
50
60
100
Analog input 3,5 V
50 100
MELTER OPERATION
Pumping control menu
This menu allows you to configure the operating options for each of the pumps installed.
• Start or stop pumping: If external permission is deactivated, when you press the ‘Pump 1/2’ key, pumping is activated or stopped manually.
When the key is green, the pump is in operation. When it is grey, the pump is off.
• Pumping speed: If the external speed reference is deactivated, when this is pressed you can set the pump’s speed.
The minimum and maximum values that can be set are established in the pump’s minimum and maximum speed alarms. See the point ‘Menu 5.
Pumping/Pumping alarms’.
At the bottom, the display shows the actual pumping speed at that moment.
• External reference: Activates or deactivates the external speed control of the pump.
If it is activated, it takes you to a screen to set the pumping ramp speed.
See the point ‘Configuring ramp speed’.
• External permission: Activates or deactivates the external pumping permission.
When the contact is activated, the LED on the right is green. When it is deactivated, it is red.
• Switch: Activates or deactivates pump start-up from a switch connector installed on the unit (optional).
When the contact is activated, the LED on the right is green. When it is deactivated, it is red.
4-14
MELTER OPERATION MA-5184-ENG MICRON+ PUR LC/MC ADHESIVE MELTER
This page is intentionally left blank.
4-15
MELER GLUING SOLUTIONS
MICRON+ ENGRANE
HMI : S02001100 v1.0.106
TC : S02200100 v1.0.084
IO : S02102100 v1.0.106
IO : S02101100 v1.0.106
A 154
°C
08:31
154
154
1
2
85
1
00
MICRON+ ENGRANE
HMI : S02001100 v1.0.106
TC : S02200100 v1.0.084
IO : S02102100 v1.0.106
IO : S02101100 v1.0.106
MICRON+ ENGRANE
HMI : S02001100 v1.0.106
TC : S02200100 v1.0.084
IO : S02102100 v1.0.106
IO : S02101100 v1.0.106
PUMP 1
Real speed:
185 2 1
100 3 100
External permission 1
--4 ---
Switch 1 5
6
PUMP 2
42
Real speed:
42
50 rpm
49 rpm
External reference 2
Pump 1 speed alarm
30 s max
Pump 2 speed alarm
15 rpm min
85 rmp max
35 s
3
MICRON+ ENGRANE
HMI : S02001100 v1.0.106
MICRON+ ENGRANE
IO : S02101100 v1.0.106
TC : S02200100 v1.0.084
IO : S02102100 v1.0.106
IO : S02101100 v1.0.106
MICRON+ ENGRANE
HMI : S02001100 v1.0.106
TC : S02200100 v1.0.084
IO : S02102100 v1.0.106
IO : S02101100 v1.0.106
PUMP 1
Real speed:
53 rpm
4
External permission 1
PUMP 1 50 rpm
4
PUMP 2
53 rpm
50 rpm
50 rpm
4-16
External permission 2 4
Switch 2
PUMP 2 50 rpm
49 rpm
External reference 2
External permission 2
Switch 2
MELTER OPERATION
Modes of operation
Operating mode with internal pumping control and internal speed control
In this operating mode, the user manually controls the start-up, shutdown and speed of the pump.
The ‘External reference’ and ‘External permission’ options must be deactivated.
Follow the steps below to use this operating mode:
1. On the start screen, press the pump status icon to access the Pumping
Control menu.
2. On the Pumping Control menu, press the pump that you want to start up. When the key is green, the pump is activated. When it is grey, the pump is off.
The following conditions must be met for the pump to start operating:
• The unit must be at ‘Temperature OK’.
• The ‘Pumping permission delay’ time must have elapsed.
• If ‘Pumping safety’ is activated, pumping must be enabled with the
‘STOP’ button (red LED off).
• There must be no alarms preventing pumping.
If a speed has been previously set, this value will be shown on the display and the pump will start to rotate at the speed indicated provided that all prior conditions are met. Otherwise:
3. Press speed and set the new rotation speed. The pump will then start rotating at the set RPM.
The maximum full scale for permissible RPM is 100 (we recommend working at speeds no lower than 10 RPM and no greater than 80 RPM).
The minimum and maximum values that can be set are established in the pump’s minimum and maximum speed alarms. See the point
‘Menu 5. Pumping/Pumping alarms’.
The pump will stop whenever:
• The control board is disabled using the ON/OFF button.
• The pumping ‘STOP’ button is pressed (red LED is lit).
• When a variator error signal is activated.
• When the MAXIMUM RPM alarm is activated.
• When the MINIMUM RPM alarm is activated.
4. If the unit has a rear switch connector (optional), pumping can also be activated from the device associated with this connector. Both the pumping button and switch must be connected to allow the pump to be activated.
When the LED is green, the contact is closed and the pump can be started up; when it is red, the contact is open and the pump will remain off.
MELTER OPERATION MA-5184-ENG MICRON+ PUR LC/MC ADHESIVE MELTER
In this operating mode, the user manually controls the start-up and shutdown from the main machine.
MICRON+ ENGRANE
TC : S02200100 v1.0.084
IO : S02102100 v1.0.106
IO : S02101100 v1.0.106
of the pump. Speed is controlled by means of an external 0-10 V signal sent
The ‘External reference’ option must be activated and the ‘External permission’ option must be deactivated.
1. On the start screen, press the pump status icon to access the Pumping
Control menu.
HMI : S02001100 v1.0.106
TC : S02200100 v1.0.084
IO : S02102100 v1.0.106
IO : S02101100 v1.0.106
2. On the Pumping Control menu, press the pump that you want to start up. When the key is green, the pump is activated. When it is grey, the pump is off.
The following conditions must be met for the pump to start operating:
MICRON+ ENGRANE
•
•
The unit must be at ‘Temperature OK’.
HMI : S02001100 v1.0.106
TC : S02200100 v1.0.084
The ‘Pumping permission delay’ time must have elapsed.
• If ‘Pumping safety’ is activated, pumping must be enabled with the
‘STOP’ button (red LED off).
• There must be no alarms preventing pumping.
The system will wait for the speed signal from the main machine.
When this is received, the pump will start rotating at the set speed. The actual rotation speed is shown on the display.
3. To set the rotation speed to the necessary value for the application, change the ramp speed (see the ‘Configuring ramp speed’ section).
Together with the ramp speed graph, the display shows the voltage being delivered from the main machine at that moment.
The pump will stop whenever:
•
•
•
•
•
The control board is disabled using the ON/OFF button.
The pumping ‘STOP’ button is pressed (red LED is lit).
When a variator error signal is activated.
HMI
MICRON+ ENGRANE
MICRON+ ENGRANE
IO
When the MAXIMUM RPM alarm is activated.
When the MINIMUM RPM alarm is activated.
: S02001100 v1.0.106
: S02200100 v1.0.084
: S02102100 v1.0.106
: S02101100 v1.0.106
TC : S02200100 v1.0.084
IO : S02102100 v1.0.106
: S02101100 v1.0.106
TC : S02200100 v1.0.084
IO : S02102100 v1.0.106
IO : S02101100 v1.0.106
MICRON+ ENGRANE pumping button and switch must be connected to allow the pump to be activated.
HMI : S02001100 v1.0.106
TC : S02200100 v1.0.084
IO : S02102100 v1.0.106
IO : S02101100 v1.0.106
When the LED is green, the contact is closed and the pump can be started up; when it is red, the contact is open and the pump will remain off.
A 154
°C
08:31
154
154
1
2
85
1
00
PUMP 1
Real speed:
185 2 1
2
50 rpm
154
100 3
4
100
External permission 1
-----
Switch 1 5
PUMP 2
42 6
Real speed:
1
2
Volt
0,0
3,0
15:35
3
3
4
5
42
50 rpm
0
20
50
60
100
10
Analog input
3
3,5 V
3
5
0
0
PUMP 1
50 100
50 rpm
4
A 154
Switch 1
PUMP 1 50 rpm
4
PUMP 2
73 rpm
50 rpm
PUMP 2
External permission 2 4
Switch 2
PUMP 2 50 rpm
76 rpm
External reference 2
External permission 2
Switch 2
4-17
MELER GLUING SOLUTIONS MELTER OPERATION
HMI
TC
IO
IO
: S02001100 v1.0.106
: S02200100 v1.0.084
: S02102100 v1.0.106
: S02101100 v1.0.106
IO : S02101100 v1.0.106
MICRON+ ENGRANE
HMI : S02001100 v1.0.106
TC : S02200100 v1.0.084
IO : S02102100 v1.0.106
IO : S02101100 v1.0.106
MICRON+ ENGRANE
HMI : S02001100 v1.0.106
TC : S02200100 v1.0.084
IO : S02102100 v1.0.106
IO : S02101100 v1.0.106
°C
A 154
154
154
1
2
85
1
00
PUMP 2
42
Real speed:
10 rpm min
90 rmp max
30 s
15 rpm min
185
154
100
---
2
5
6
3
4
170
154
100
---
2
3
42
50 rpm
49 rpm
85 rmp max
External permission 2
Switch 2
35 s
HMI : S02001100 v1.0.106
MICRON+ ENGRANE
IO : S02101100 v1.0.106
TC : S02200100 v1.0.084
IO : S02102100 v1.0.106
IO : S02101100 v1.0.106
PUMP 1 50 rpm
73 rpm
External reference 1
4
MICRON+ ENGRANE
HMI : S02001100 v1.0.106
TC : S02200100 v1.0.084
IO : S02102100 v1.0.106
IO : S02101100 v1.0.106
External permission 1
Switch 1
Switch 1
PUMP 2 50 rpm
76 rpm
76 rpm
4
4
Switch 2
PUMP 2
4-18
Real speed:
50 rpm
49 rpm
External reference 2
Operating mode with external pumping control and internal speed control
In this operating mode, the pump is started and stopped via an external contact signal from the main machine. The pump’s speed can be set manually by the user.
The ‘External reference’ option must be deactivated and the ‘External permission’ option must be activated.
Follow the steps below to use this operating mode:
1. On the start screen, press the pump status icon to access the Pumping
Control menu.
2. The status of the external permission is shown on the Pumping Control menu. When the LED is green, the contact is closed and the pump can be started up; when it is red, the contact is open and the pump will remain off.
The following conditions must be met for the pump to start operating:
• The unit must be at ‘Temperature OK’.
• The ‘Pumping permission delay’ time must have elapsed.
• If ‘Pumping safety’ is activated, pumping must be enabled with the
‘STOP’ button (red LED off).
• There must be no alarms preventing pumping.
If a speed has been previously set, this value will be shown on the display and the pump will start to rotate at the speed indicated provided that all prior conditions are met. Otherwise:
3. Press speed and set the new rotation speed. The pump will then start rotating at the set RPM.
The maximum full scale for admissible revolutions is 100 (we recommend working at speeds of not less than 10 rpm and not greater than 80 rpm). The minimum and maximum values that can be set are established in the pump’s minimum and maximum speed alarms. See the point ‘Menu 5. Pumping/Pumping alarms’.
The pump will stop whenever:
• The control board is disabled using the ON/OFF button.
• The pumping ‘STOP’ button is pressed (red LED is lit).
• When a variator error signal is activated.
• When the MAXIMUM RPM alarm is activated.
• When the MINIMUM RPM alarm is activated.
4. If the unit has a rear switch connector (optional), pumping can also be activated from the device associated with this connector. Both the
‘External permission’ and switch must be connected to allow the pump to be activated.
When the LED is green, the contact is closed and the pump can be started up; when it is red, the contact is open and the pump will remain off
MELTER OPERATION MA-5184-ENG MICRON+ PUR LC/MC ADHESIVE MELTER
Operating mode with external pumping control and external speed control
In this operating mode, both pumping and speed are controlled externally from the main machine.
TC
IO
: S02001100 v1.0.106
: S02001100 v1.0.106
: S02200100 v1.0.084
: S02102100 v1.0.106
IO : S02101100 v1.0.106
The ‘External reference’ and ‘External permission’ options must be activated.
Follow the steps below to use this operating mode:
1. On the start screen, press the pump status icon to access the Pumping
Control menu.
HMI
TC
: S02001100 v1.0.106
: S02200100 v1.0.084
2. The status of the external permission is shown on the Pumping Control menu. When the LED is green, the contact is closed and the pump can be started up; when it is red, the contact is open and the pump will remain off.
The following conditions must be met for the pump to start operating:
• The unit must be at ‘Temperature OK’.
MICRON+ ENGRANE
•
•
The ‘Pumping permission delay’ time must have elapsed.
If ‘Pumping safety’ is activated, pumping must be enabled with the
‘STOP’ button (red LED off).
IO : S02102100 v1.0.106
IO : S02101100 v1.0.106
• There must be no alarms preventing pumping.
The system will wait for the speed signal from the main machine.
When this is received, the pump will start rotating at the set speed. The actual rotation speed is shown on the display.
3. To set the rotation speed to the necessary value for the application, change the ramp speed (see the ‘Configuring ramp speed’ section).
Together with the ramp speed graph, the display shows the voltage being delivered from the main machine at that moment.
The pump will stop whenever:
• When a variator error signal is activated.
MICRON+ ENGRANE
IO
• When the MAXIMUM RPM alarm is activated.
: S02001100 v1.0.106
: S02200100 v1.0.084
: S02102100 v1.0.106
: S02101100 v1.0.106
TC : S02200100 v1.0.084
IO : S02102100 v1.0.106
IO : S02101100 v1.0.106
• When the MINIMUM RPM alarm is activated.
4. If the unit has a rear switch connector (optional), pumping can also be activated from the device associated with this connector. Both the
‘External permission’ and switch must be connected to allow the pump to be activated.
MICRON+ ENGRANE
When the LED is green, the contact is closed and the pump can be started up; when it is red, the contact is open and the pump will remain off.
HMI : S02001100 v1.0.106
TC : S02200100 v1.0.084
IO : S02102100 v1.0.106
IO : S02101100 v1.0.106
°C
A 154
154
154
1
2
85
1
00
3
4
1
2
5
10
185
154
100
2
---
5
42 6
3
4
170
154
100
---
42
3
2
Volt
15:35
0,0
3,0
4,0
7,0
10
3
0
20
50
60
100
Analog input
3
3,5 V
5
PUMP 1
0
Real speed:
50
50 rpm
100
73 rpm
External reference 1
External permission 1
Switch 1
Switch 1
PUMP 2
76 rpm
76 rpm
4
4
Switch 2
PUMP 2
Real speed:
External reference 2
50 rpm
76 rpm
4
4-19
External permission 2
Switch 2
HMI : S02001100 v1.0.106
TC : S02200100 v1.0.084
HMI
TC
HMI
HMI
TC
: S02001100 v1.0.106
: S02200100 v1.0.084
: S02001100 v1.0.106
: S02001100 v1.0.106
: S02200100 v1.0.084
IO : S02102100 v1.0.106
IO : S02101100 v1.0.106
MICRON+ ENGRANE
HMI : S02001100 v1.0.106
TC : S02200100 v1.0.084
IO : S02102100 v1.0.106
IO : S02101100 v1.0.106
Pumping
MELER GLUING SOLUTIONS rpm
1 0,0
3,0 20
3
5
5
10
10
10
Analog input
10
Analog input
Analog input
Pumping
100
3,5 V
3,5 V
3,5 V
3,5 V
1
2
3
4
5
0
0
0
0
0
0
Volt
0,0
3,0
4,0
7,0
10
50
50
50
50
Analog input
60
100
3,5 V
10
5
0
0 50 100
MICRON+ ENGRANE
HMI
TC
IO
IO
: S02001100 v1.0.106
: S02200100 v1.0.084
: S02102100 v1.0.106
: S02101100 v1.0.106
A
C
E
Menu
1. Heating 2. Settings
MELTER OPERATION
Configuring speed ramp
For equipment operating in external reference, the display will show the current pump rotation set point (input reference conversion as per the full scale and the conversion table).
The conversion table may be programmed with up to 5 points (input voltage
(Voltage) and output speed (RPM)).
By default the table is programmed (0 V = 0 rpm and 10 V = 100 rpm):
Notes on the editable values in the conversion table:
• The value for voltage must always be shown to one decimal place.
• Point 1 is the starting point for the speed ramp, and therefore the voltage will always be 0, while the value for output RPM is editable.
• The possible values for each point must be equal to or greater than the value corresponding to the previous point.
• Point 5 is the final point for the speed ramp, and therefore the voltage will always be 10, while the value for output RPM is editable.
• It is not necessary to program the value for MAXIMUM RPM in this table.
• If, at any point, the maximum value for Voltage = 10 V is entered, the corresponding values for Vin and RPM at higher points will be automatically updated according to the value for this point.
• If, at any point, the maximum value is entered, that is, RPM = MAXI-
MUM RPM, the corresponding values for RPM at higher points will be automatically updated to MAXIMUM RPM.
Main Menu
B
A - Heating options configuration.
B - General settings of the unit.
C - Automatic loading configuration.
D - Access to statistics.
E - Pumping options
D
3. Charge 4. Statistics
5. Pumping
4-20
MELTER OPERATION MA-5184-ENG MICRON+ PUR LC/MC ADHESIVE MELTER
HMI
TC
IO
IO
: S02001100 v1.0.106
: S02200100 v1.0.084
: S02102100 v1.0.106
: S02101100 v1.0.106
A
C
E
1.1 Zones 1.2 Sequential
1.3 Inhibition
1.4 Auto
Standby - OFF
B
D
A - Configuración de zonas de calentamiento.
B - Configuración de calentamiento secuencial por zonas.
C - Programación de Inhibiciones.
D - Configuración de modos de Standby.
E - Acceso a opciones extra.
1.5 Heating
Extra Settings
1.1 Heating zones
MICRON+ ENGRANE
HMI
TC
IO
IO
: S02001100 v1.0.106
: S02200100 v1.0.084
: S02102100 v1.0.106
: S02101100 v1.0.106
This menu lets you do the following for each zone:
• Change the name to identify it more easily.
• Edit the set point temperature.
• Edit the standby value. The value indicates the temperature reduction with respect to its set point.
• Apply PID values. By default the unit comes configured with a Standard
PID.
You can select from four PID options: Standard, Moderate, Quick or Manual.
P:
I:
D:
Temperature:
T: Tank
Real
152 °C
Standby
Set Point
150 °C
-60 °C
PID: Standard
30
12
300
Note. The PID values are directly involved in the heating process. Do not modify these values if you do not have the required technical knowledge or without the advice of
Meler’s After Sales Service.
4-21
MICRON+ ENGRANE
HMI : S02001100 v1.0.106
TC : S02200100 v1.0.084
IO : S02102100 v1.0.106
IO : S02101100 v1.0.106
MELER GLUING SOLUTIONS
MICRON+ ENGRANE
HMI : S02001100 v1.0.106
TC : S02200100 v1.0.084
IO : S02102100 v1.0.106
IO : S02101100 v1.0.106
MICRON+ ENGRANE
HMI : S02001100 v1.0.106
TC : S02200100 v1.0.084
IO : S02102100 v1.0.106
IO : S02101100 v1.0.106
1.2 Sequential
Enable sequential
Define groups
Group B
-20 °C 5 min
Group C
-10 °C 5 min
Sequential group A
T: Tank
1.1: Hose 1
2.1: Hose 2
3.1: Hose 3
4.1: Hose 4
5.1: Hose 5
6.1: Hose 6
T: Tank D: Distributor
1.1: Hose 1 1.2: Applicator 1
2.1: Hose 2
3.1: Hose 3
4.1: Hose 4
5.1: Hose 5
2.2: Applicator 2
3.2: Applicator 3
4.2: Applicator 4
5.2: Applicator 5
6.1: Hose 6 6.2: Applicator 6
Group 1: Robot Arm RIGHT
Manual OFF
External OFF Signal 1
D: Distributor
1.2: Applicator 1
2.2: Applicator 2
3.2: Applicator 3
4.2: Applicator 4
5.2: Applicator 5
6.2: Applicator 6
MELTER OPERATION
1.2 Sequential Heating
This lets you start heating the zones one after the other. This prevents a zone from being active for a long time until the slowest zone heats up.
This function allows you to create three heating groups: A, B and C. Press
‘Define groups’ to go to a screen where zones can be added to the groups:
• Group A: this always includes the Tank, which is the slowest and serves as a reference for the remainder of the zones. Other zones can be added so they begin to heat up with the Tank.
• Group B: other zones can be added and some degrees of temperature defined before the tank reaches its set point and a wait time.
• Group C: the zones that are not in group A or B can be added here.
If a component in group B or C is deselected, it goes back to group A. By default, all the zones belong to group A.
Example:
- Tank set point temperature: 150°C
- Programming of Group B: -20°C / 5 minutes.
Group B begins to heat up 5 minutes after the tank reaches 130°C.
1.3 Inhibitions
This menu allows you to create seven groups of zones and program the mode in which the Inhibition (Off) can be activated or disabled.
The following is indicated for each group:
• Name of the group. The name can be changed to identify it more easily.
• Manual inhibition of the group (Manual Off).
Whether it is possible to manually activate or deactivate the inhibition in that group from the ‘SHORT-
CUTS’ menu.
Manual inhibition takes priority over external inhibition.
• Automatic inhibition with external signal (External Off).
Whether it is possible to externally activate or deactivate the inhibition in that group.
You must indicate which of the seven possible external signals will perform this function.
One signal can never be enabled in two different groups.
• Selected zones.
A zone may be selected in more than one group or may not be in any grou.
4-22
MELTER OPERATION
1.4 Auto Standby - OFF
MA-5184-ENG MICRON+ PUR LC/MC ADHESIVE MELTER
MICRON+ ENGRANE
HMI : S02001100 v1.0.106
TC : S02200100 v1.0.084
IO : S02102100 v1.0.106
IO : S02101100 v1.0.106
1.4 Auto Standby - OFF
This function can program the following work parameters:
Standby desactivation
• Standby Deactivation: automatically deactivates the ‘General Standby’ mode activated manually. Once the minutes programmed in the unit have passed, the heating process will start again.
If the ‘Calendar’ is active, the unit will follow the programmed calendar.
Activity control
10 min
10 min
Standby
10 min
OFF
MICRON+ PISTÓN
HMI
TC
IO
: S02001100 v1.0.106
: S02200100 v1.0.084
: S02102100 v1.0.106
MICRON+ PISTÓN
HMI
TC
IO
: S02001100 v1.0.106
: S02200100 v1.0.084
: S02102100 v1.0.106
• Activity control: This lets you configure the times for changing to Standby mode and to Inhibition (OFF) when the activity signal ceases.
The activity of the line is monitored from a digital input. When it detects that there is no activity, the unit changes to Standby mode after the programmed time has passed, and changes to Inhibition mode when the second time has passed.
MICRON+ ENGRANE
HMI : S02001100 v1.0.106
TC : S02200100 v1.0.084
IO : S02102100 v1.0.106
IO : S02101100 v1.0.106
Imputs
MICRON+ PISTÓN
HMI
TC
IO
: S02001100 v1.0.106
: S02200100 v1.0.084
: S02102100 v1.0.106
2.3 Input / Output 1.4 Auto Standby - OFF
Standby desactivation
XDI1 10 min
Imputs
XDI1
XDI2
Standby due to lack of recharge
2.3 Input / Output
Standby
ON / OFF
10 min
ON / OFF
Activity control
DI3 Activity
10 min
Standby
10 min
OFF
Outputs
Off
Piece Piece
MICRON+ PISTÓN
HMI : S02001100 v1.0.106
TC : S02200100 v1.0.084
IO : S02102100 v1.0.106
Piece Piece Piece Piece
Alarms
Alarms
Modo ON
Adhesive Level
MICRON+ PISTÓN
HMI
TC
IO
: S02001100 v1.0.106
: S02200100 v1.0.084
: S02102100 v1.0.106
General Standby General OFF
10 min
Standby
DO2
XDO4
Temperature OK
Alarms
Adhesive Level
State
OFF Group: 1
C1 C2 C3 C4 C5 C6
M T W T F S S
Hour ON
2.1: Hose 2
OFF
Standby OFF
• Standby due to lack of recharging:
11:00
15:00
D: Distributor
after the programmed time.
the equipment automatically switches to
Standby when it detects a lack of adhesive and has not detected a recharge
00.00
1.2: Applicator 1
00.00
2.2: Applicator 2
4-23
MELER GLUING SOLUTIONS MELTER OPERATION
MICRON+ ENGRANE
HMI : S02001100 v1.0.106
TC : S02200100 v1.0.084
IO : S02102100 v1.0.106
IO : S02101100 v1.0.106
1.5 Heating Extra Settings
Pumping permission delay
10 min
Programmable limits
40 °C min
Temperature warning (+/-)
10 °C 10 °C
200 °C
60 s max
Temperature alarm in zone (+/-)
20 °C 20 °C 60 s
Total alarm due to temperature
230 °C 10 s
Adaptative time
60 s
1.5 Extra temperature settings
• Pumping permission delay: This is the time that the unit must wait to activate pumping after all the active zones have reached a temperature above [Set point temp. -3°].
• Programmable limits: Two limits can be set to prevent set point temperatures from being programmed above or below those values.
• Temperature warning: A temperate (±°C/°F) and a time are defined to indicate when the overheating or low temperature warning is activated in each zone.
• Temperature alarm: A temperature (±°C/°F) and a time are defined to indicate when the overheating or low temperature alarm is activated in each zone.
If either of those values are reached (±) and maintained for the set time, the unit disconnects the heating in the zone causing the error. If the error persists 3 minutes later, the remainder of the zones are automatically disconnected. If the affected zones are the tank or the distributor, the unit also stops the pumping.
• Alarma total por temperatura: Se define un valor (+°C/°F) y un tiempo que indican cuando se activa la alarma por sobretemperatura. Si cualquier zona alcanza esta temperatura y permanece el tiempo establecido, el equipo desconecta el calentamiento de todas las zonas y detiene el bombeo.
• Adaptive time: Automatic interval setting for warning and alarm temperatures, when the user reprogrammes the setpoint values.
4-24
(*) Example values
Status
Actual temperature*
Set point emperature*
Heating
150 150 ON
140
160
150 ON
130
170
190
150
150
Pumping
ON
ON
Temp.OK zones
OUTPUTS
Alarm
Activated
ON
ON
OFF
Unit
OFF
Zone in error
OFF when...
Error in Tank
Error in Distributor
ON when...
Error in the remainder of the Zones
OFF
All Zones
OFF
OFF
OFF
OFF
ON ON / OFF
ON
ON
Ready /
Running
ON / OFF
ON/OFF
OFF
MICRON+ ENGRANE
HMI
TC
IO
IO
: S02001100 v1.0.106
: S02200100 v1.0.084
: S02102100 v1.0.106
: S02101100 v1.0.106
A
MELTER OPERATION
2. Extra Settings
2.1 Password
2.2 Extra
Settings
C
2.3 Input / Output 2.4 Restore default
MA-5184-ENG MICRON+ PUR LC/MC ADHESIVE MELTER
B
A - Gestión de contraseñas.
B - Ajustes adicionales.
C - Configuración de señales de entrada y salida.
D - Restaurar sistema.
D
MICRON+ ENGRANE
HMI : S02001100 v1.0.106
TC : S02200100 v1.0.084
IO : S02102100 v1.0.106
IO : S02101100 v1.0.106
MICRON+ ENGRANE
HMI : S02001100 v1.0.106
TC : S02200100 v1.0.084
IO : S02102100 v1.0.106
IO : S02101100 v1.0.106
2.1 Password management
MICRON+ ENGRANE
HMI : S02001100 v1.0.106
TC : S02200100 v1.0.084
IO : S02102100 v1.0.106
IO : S02101100 v1.0.106
LOCKED MODE:
- Access is only provided to the HOME screen.
USER MODE:
- by default, the user level has no password. You can create a user level password by entering a value between 0000 and 9999
A 154 154 2 00
- Any parameter can be changed after entering a 4-digit password. By default the password is 0000.
- Direct access is provided to the HOME screen, product/select product,
MICRON+ ENGRANE
HMI
TC
IO
170
- USER or EXPERT operating mode can be selected or LOCKED.
100 3 100
---
A
42
154
4
°C
5
08:31
6
154
15:35
154
---
42
1
2
85
00
Password: ******
Restore password code A: 1285
2.1 Password
LOCKED USER EXPERT
New password
Repeat the new password
Shooting menu locked
******
******
4-25
185
154
100
---
42
5
6
3
4
1
2
15:35
170
154
100
---
42
MELER GLUING SOLUTIONS MELTER OPERATION
MICRON+ ENGRANE
HMI : S02001100 v1.0.106
TC : S02200100 v1.0.084
IO : S02102100 v1.0.106
IO : S02101100 v1.0.106
MICRON+ ENGRANE
HMI : S02001100 v1.0.106
TC : S02200100 v1.0.084
IO : S02102100 v1.0.106
IO : S02101100 v1.0.106
4-26
2.2 Extra Settings
Channel number
Liquid charger
Minimum level sensor
Regrid charger
Cover detector
Gas injection
Feeder
Pattern controller
External HMI
Wireless communication
6
If you try to access a restricted menu, a pop-up appears, requesting the password.
If the EXPERT password is entered, the unit remains unlocked for 15 minutes.
Whenever there is activity on the screen, the system remains in this mode. If the end of this 15 minutes is reached, the unit returns to USER mode.
If you forget the EXPERT level password, contact the Focke Meler main offices to find out how to proceed to recover it.
2.2 Extra Settings
Sound on alarm
Screen saver
10 min
Inside device temperature alarm
85 °C 60 s
Pumping autolock
OFF after reset
Modbus
Node: 10 B: 57600
2.2 Extra settings
• Activate or deactivate the alarm sound.
To stop the sound, press the
ALARM icon on the HOME screen.
• Activate or deactivate the screensaver. The screen switches off after the set time has passed. If you press the screen when it is off, it turns on and the HOME menu appears.
• Cabinet temperature alarm: A value (+°C/°F) and a time are defined to indicate when the alarm is activated due to overheating inside the unit’s electrical cabinet. If it reaches this temperature and maintains it for the set time, the unit disconnects the heating of all zones and stops the pumping.
• Automatic pumping block. Please see the ‘Automatic pumping block function’ section.
• Turning off after resetting. Please see the ‘Turning off after resetting function’ section.
• Modbus. Activate and disable external communications via Modbus.
• Number of channels.
Set up the number of electrical outputs enabled in the melter.
• Automatic feeder. Activate or disable the operation of the automatic feeder.
• Feeder. Activate or disable the operation of the external adhesive feed
(external liquid load or pellet level).
• Pattern controller. Activate or disable the pattern controller functions.
• Level sensor. Activate or disable the operation of the level sensor.
• External HMI. Activate or disable the operation of the external HMI control.
• Wireless communications. You can enable or disable the operation of the unit’s wireless communication system (Wi-Fi). Click on the arrow to go to the configuration screen. See the point on ‘Wireless communications’ for further information.
MELTER OPERATION MA-5184-ENG MICRON+ PUR LC/MC ADHESIVE MELTER
MICRON+ ENGRANE
2.3 Configuration of input and output signals HMI : S02001100 v1.0.106
TC : S02200100 v1.0.084
IO : S02102100 v1.0.106
This allows you to configure the unit’s digital input and output signals.
The inputs can be:
• ON/OFF: Switches the unit fully off or on.
• Standby: Activates or deactivates the Standby mode.
• Activity: Enables the activity control to measure the times for switching automatically to Standby and OFF.
• Pumping: Activates or deactivates the pumping.
• COMM.: Activates or deactivates the communications.
Imput
DI1
DI2
DI3
Output
DO2
DO3
DO4
2.3 Input / Output
Standby
COMs OFF
Pump OFF
Temperature OK
Alarms
Adhesive Level
The outputs can be:
• Standby: Indicates that the unit is in Standby mode.
• Zones in Temperature OK. Indicates that all active zones are in temperature OK.
• Ready. Indicates that the unit is ready to operate, with temperature OK and no operating errors.
• Running. The unit is pumping, with temperature OK and no operating errors.
• Alarm: Indicates that there is an active Alarm.
• Level: Indicates high level of adhesive in the tank.
• No Level: Indicates low level of adhesive in the tank.
MICRON+ ENGRANE
2.4 Restore default values
HMI : S02001100 v1.0.106
TC : S02200100 v1.0.084
IO : S02102100 v1.0.106
IO : S02101100 v1.0.106
Allows you to delete all the changes made to the system and leave the unit with the factory-set default parameters. After pressing, the following confirmation message will appear.
When you press ‘YES’, the device restarts with the default configuration.
Are you sure you want to restore to the default settings??
NO YES
4-27
MICRON+ ENGRANE
HMI : S02001100 v1.0.106
TC : S02200100 v1.0.084
IO : S02102100 v1.0.106
IO : S02101100 v1.0.106
MICRON+ ENGRANE
HMI : S02001100 v1.0.106
TC : S02200100 v1.0.084
IO : S02102100 v1.0.106
IO : S02101100 v1.0.106
MELER GLUING SOLUTIONS
Level alarm
Sound on alarm
120 s
MICRON+ ENGRANE
HMI : S02001100 v1.0.106
TC : S02200100 v1.0.084
IO : S02102100 v1.0.106
IO : S02101100 v1.0.106
Level alarm
Sound on alarm
120 s
Automatic charge
CHARGE
Automatic feeder alarm
60 s
Over charge time
Charge error alarm
Cover opened alarm
1 s
90 s
90 s
Sound on alarm
MELTER OPERATION
‘3. Load’ Menu
Esta pantalla permite controlar las diferentes cuestiones relativas a la carga de adhesivo.
Screen 1: Minimum adhesive level sensor
• Level alarm: Time after which the unit stops and activates a low-level alarm.
• Sound with alarm: Allows you to configure the sensor alarm to emit a sound
Screen 2: Automatic adhesive feeder
• Automatic feeder: Activates or deactivates automatic feeding .
When you press ‘ CHARGE’, This lets you activate manual loading. When pressed, it loads, and when released, the loading stops.
• Feeder alarm. Defines the time that must pass to give an external feed alarm.
• Overfill time: This lets you configure for how much time the adhesive will continue to be loaded once the lower level sensor has activated (tank sufficiently full, but not completely full).
• Charge error alarm: This defines the maximum amount of time for filling the tank. If this time is exceeded, the unit displays an alarm.
• Open tank lid alarm: An alarm sounds when the tank lid is open and it stops loading immediately.
• Buzzer: This lets you set whether or not loading alarms emit a sound.
MICRON+ ENGRANE
HMI : S02001100 v1.0.106
TC : S02200100 v1.0.084
IO : S02102100 v1.0.106
IO : S02101100 v1.0.106
Auto. inject.
Cycle time
Injection time
Sound on alarm
INJECT
120 s
15 s
Screen 3: Dry air/gas injection
• Automatic injection: Activates or deactivates dry air/gas injection.
By pressing ‘INJECT’, you can activate and deactivate injecting manually.
• Cycle time: Sets the time that has to elapse between dry air/gas injections.
• Injection time: Sets the dry air/gas injection time.
• Sound with alarm: Allows you to configure the injection system alarms to emit a sound.
4-28
MELTER OPERATION MA-5184-ENG MICRON+ PUR LC/MC ADHESIVE MELTER
MICRON+ ENGRANE
HMI : S02001100 v1.0.106
TC : S02200100 v1.0.084
IO : S02102100 v1.0.106
Screen 4: Pressurisation (only for units with an airtight tank lid)
• Automatic pressure: Activates or deactivates the tank’s automatic pressure system.
By pressing ‘PRESSURISE’, you can activate and deactivate pressurisation manually.
• Cycle time: Sets the time that has to elapse between dry air injection cycles.
• Aeration time: Sets the dry air injection time and the output valve open time. This allows the tank’s air to be renewed.
• Injection time: Sets the dry air injection time and, therefore, the tank’s pressurisation time.
• Open tank lid alarm: An alarm sounds when the lid is open and the system stops.
• Sound with alarm: Allows you to configure the pressurisation system alarms to emit a sound.
Auto. press.
Cycle time
Injection time
Aeration time
Cover opened alarm
Sound on alarm
PRESSURIS.
120 s
15 s
15 s
90 s
‘4. Statistics’ Menu
MICRON+ ENGRANE
HMI : S02001100 v1.0.106
TC : S02200100 v1.0.084
IO : S02102100 v1.0.106
IO : S02101100 v1.0.106
This screen displays:
• Hours of operation: This counts all of the hours during which the unit is in Temperature OK.
To reset the counter to zero, you must press reset.
• Filter change. To program a countdown in hours. When it gets to ‘0’, the unit gives a warning to change the adhesive particles filter.
Once the filter has been changed, press reset to return the counter to the set value.
• Data logger: Time interval for logging the unit’s programming and operating data.
You can back up this data using the application for PCs.
4.4. Statistics
Working hours 4515
2018-05-20 10:45 RESET
Filter change
2018-05-20 10:45
1000
RESET
Datalogger 1 min
4-29
MICRON+ ENGRANE
HMI : S02001100 v1.0.106
TC : S02200100 v1.0.084
IO : S02102100 v1.0.106
IO : S02101100 v1.0.106
MELER GLUING SOLUTIONS
5. Pumping
Manual Control Pump 1
50 rpm
30 s
PLAY
Manual Control Pump 2
50 rpm
30 s
PLAY
MELTER OPERATION
Menu ‘5. Pumping’
To can configure the following options separately for each pump:
• Manual control pump 1 or 2: If ‘Manual control’ is activated, pumping can be activated or stopped by pressing ACTIVATE (with the unit in
Temperature OK).
The button changes from STOP to ACTIVATE every time it is pressed.
A maximum number of RPM and maximum pumping time can be programmed, after which the unit stops manual pumping.
MICRON+ ENGRANE
HMI : S02001100 v1.0.106
TC : S02200100 v1.0.084
IO : S02102100 v1.0.106
IO : S02101100 v1.0.106
5. Pumping
Pump 1 speed alarm
10 rpm min
90 rmp max
Pump 2 speed alarm
15 rpm min
85 rmp max
30 s
35 s
• Speed alarm pump 1 or 2: If this is activated, the unit will activate an alarm if the speed of the pump does not remain within the minimum and maximum speed range during the set time.
4-30
MELTER OPERATION MA-5184-ENG MICRON+ PUR LC/MC ADHESIVE MELTER
MICRON+ ENGRANE
HMI : S02001100 v1.0.106
TC : S02200100 v1.0.084
IO : S02102100 v1.0.106
IO : S02101100 v1.0.106
Automatic pumping block function
The unit has a function for to automatically block pumping due to a voltage drop, a direct disconnection from the network, or an operating error.
STARBI INTEGRADO v97
HMI : S02001100 v1.0.106
TC : S02200100 v1.0.084
IO : S02102100 v1.0.106
IO : svn97
2. Extra Settings
Extra settings
2.1 Password
2.2 Extra
Settings
2.3 Input / Output 2.4 Restore default
Sound on alarm
Screen saver
10 ms
Inside device temperature alarm
85 ºC
MICRON+ PISTÓN
HMI : S02001100 v1.0.106
TC : S02200100 v1.0.084
IO : S02102100 v1.0.106
60 s
‘Automatic pumping block’ enabled
When this function is enabled, whenever an event forces the unit to change to
ERROR mode, STANDBY mode or OFF mode, the pumping block is automatically enabled, and the STOP button’s red LED lights up.
If conditions allow the unit to return to READY mode, the block can be disabled by pressing the STOP button. The red LED turns off, and the unit stays in
READY mode.
Example: The unit is in RUNNING mode. At this moment, the temperature is not OK, and after the programmed time has passed, the unit changes to ERROR mode. The pumping block is automatically enabled, and the red LED lights up. The pumping block cannot be disabled while the temperature is not OK, and the error continues to be displayed.
When the temperature is OK again, the unit does not automatically change to READY mode. You must press STOP to disable the pumping block and prepare the unit for pumping.
2.2 Extra Settings
Sound on alarm
Screen saver
10 min
Inside device temperature alarm
85 °C 60 s
Pumping autolock
MODE
Off after reset
STOPPED
Modbus
Node: 10
READY
MODE
B: 57600
Press to activate pumping
Press to deactivate pumping
4-31
MICRON+ PISTÓN
HMI : S02001100 v1.0.106
TC : S02200100 v1.0.084
IO : S02102100 v1.0.106
2.2 Extra Settings
Sound on alarm
MELTER OPERATION
10 min
Inside device temperature alarm
85 °C 60 s
Pumping autolock
Off after reset
Modbus
Node: 10 B: 57600
STOPPED
MODE
READY
MODE
‘Automatic pumping block’ disabled
When this function is disabled, whenever an event forces the unit to change to
ERROR mode, STANDBY mode or OFF mode, it will automatically return to RE-
ADY mode once the conditions are met again. You do not have to press STOP.
The red LED will remain off.
Example: The unit is in RUNNING mode. At this moment, the temperature is not OK, and after the programmed time has passed, the unit changes to ERROR mode. When the temperature is OK again, the unit automatically changes to READY mode.
Warning: It is always possible to put the unit in STOPPED mode by pressing
STOP. The red LED will light up. In this case, even if permitted by the conditions, it will not be possible to return to READY mode until you press STOP again and the LED turns off.
Press to activate pumping
Press to deactivate pumping
Warning: Whenever the ‘Automatic pumping block’ function is disabled, it is recommended for the ‘ON/OFF’ or ‘OFF Pumping’ signal of the unit to be connected to the main machine, so that this signal can be used to enable the unit again in a controlled manner.
4-32
MICRON+ PISTÓN
HMI : S02001100 v1.0.106
TC : S02200100 v1.0.084
IO : S02102100 v1.0.106
MELTER OPERATION MA-5184-ENG MICRON+ PUR LC/MC ADHESIVE MELTER
‘Turning off after resetting’ function
The unit has a function to recover its current status (ON/OFF) after a voltage drop or a direct disconnection from the network.
‘Reset’ means turning off and turning on the unit using any main ON/OFF switch or any loss and recovery of power.
MICRON+ PISTÓN
HMI : S02001100 v1.0.106
TC : S02200100 v1.0.084
IO : S02102100 v1.0.106
2. Extra Settings 2.2 Extra Settings
2.1 Password
2.2 Extra
Settings
2.3 Input / Output 2.4 Restore default
Sound on alarm
Screen saver
10 min
Inside device temperature alarm
MICRON+ PISTÓN
HMI : S02001100 v1.0.106
TC : S02200100 v1.0.084
IO Pumping autolock
60 s
MICRON+ PISTÓN
HMI : S02001100 v1.0.106
TC
IO
Modbus
Node: 10 B: 57600
‘Turning off after resetting’ enabled
MICRON+ PISTÓN
HMI : S02001100 v1.0.106
TC : S02200100 v1.0.084
IO : S02102100 v1.0.106
When this function is enabled, whenever a ‘reset’ occurs, the unit remains in
OFF mode and the screen is turned off.
The unit can be turned on (ON) through:
MICRON+ PISTÓN
HMI : S02001100 v1.0.106
• External “ON/OFF” contact (if installed and enabled),
• or external communications (if installed and enabled),
• or the Calendar function (if programmed and enabled),
• or by pressing the “ON/OFF” button on the front screen,
!
2.2 Extra Settings
Sound on alarm
10 min
Sound on alarm
Inside device temperature alarm
Screen saver
85 °C
2.3 Input / Output
Hour
07:00
11:00
13:15
15:00
00.00
00.00
Imputs
XDI1 Standby
60 s
XDI2
DI3 Activity
Modbus
Outputs
Node: 10
DO2
B: 57600
XDO3
XDO4
Alarms
Enable all the calendars
Adhesive Level
C1 C2 C3 C4 C5 C6
M T W T F S S
ON Standby OFF
4-33
MICRON+ PISTÓN
HMI : S02001100 v1.0.106
TC : S02200100 v1.0.084
IO : S02102100 v1.0.106
MICRON+ PISTÓN
HMI : S02001100 v1.0.106
TC : S02200100 v1.0.084
IO : S02102100 v1.0.106
MICRON+ PISTÓN
HMI : S02001100 v1.0.106
TC : S02200100 v1.0.084
IO : S02102100 v1.0.106
MICRON+ PISTÓN
HMI : S02001100 v1.0.106
TC : S02200100 v1.0.084
IO : S02102100 v1.0.106
4-34
2.2 Extra Settings
Sound on alarm
10 min
Sound on alarm
Inside device temperature alarm
MELER GLUING SOLUTIONS
85 °C
2.3 Input / Output
Hour
07:00
11:00
13:15
15:00
00.00
00.00
Imputs
XDI1 Standby
60 s
XDI2
DI3 Activity
Modbus
Outputs
Node: 10
DO2
B: 57600
XDO3
XDO4
Alarms
Enable all the calendars
Adhesive Level
MICRON+ PISTÓN
C1 C2 C3 C4 C5 C6
M T
TC : S02200100 v1.0.084
IO
W
: S02102100 v1.0.106
ON Standby OFF
Initial status
MELTER OPERATION
‘Turning off after resetting’ disabled
When this function is disabled, whenever a ‘reset’ occurs, the unit recovers the
ON/OFF status that it was in at that time.
The unit can change status through:
• External “ON/OFF” contact (if installed and enabled),
• or external communications (if installed and enabled),
• or the Calendar function (if programmed and enabled),
• or by pressing the “ON/OFF” button on the front screen,
MICRON+ PISTÓN
HMI : S02001100 v1.0.106
TC : S02200100 v1.0.084
IO : S02102100 v1.0.106
2.2 Extra Settings 2.2 Extra Settings
Sound on alarm Sound on alarm
Important: if the unit is in ERROR mode when the ‘reset’ occurs, it will remain
OFF, even if the function is disabled.
10 min 10 min
Inside device temperature alarm Inside device temperature alarm
60 s
Off after reset
Modbus
Node: 10
Off after reset
Modbus
Node: 10
Equipment OFF
(Screen off)
Equipment ON
(Screen on)
Equipment in ERROR
(Screen on)
Equipment OFF
Equipment OFF
Equipment ON
Equipment OFF
Configuration of turning on and activating pumping
These are different possible pump turn on and activation modes depending on the installation and programming of the unit.
The following images provide a simplified example of the most typical sequences for turning on and activating the pumping. The unit status changes may change by pressing the ‘ON/OFF’ or ‘STOP’ buttons, or through external input signals, communications (ModBus, Profibus, etc.), programming states or operating errors:
MICRON+ PISTÓN
HMI
TC
IO
: S02001100 v1.0.106
: S02200100 v1.0.084
: S02102100 v1.0.106
MELTER OPERATION
MICRON+ PISTÓN
HMI
TC
IO
: S02001100 v1.0.106
: S02200100 v1.0.084
: S02102100 v1.0.106
MICRON+ PISTÓN
HMI : S02001100 v1.0.106
TC
IO
2.2 Extra Settings
Sound on alarm
Screen saver
10 min
Inside device temperature alarm
85 °C 60 s
Pumping autolock
Off after reset
Modbus
MICRON+ PISTÓN
HMI : S02001100 v1.0.106
TC : S02200100 v1.0.084
IO
2.2 Extra Settings
Sound on alarm
Screen saver
SWITCH ON
MICRON+ PISTÓN
HMI
TC
IO
: S02001100 v1.0.106
: S02200100 v1.0.084
: S02102100 v1.0.106
Inside device temperature alarm
85 °C 60 s
Pumping autolock
Off after reset
Modbus
MICRON+ PISTÓN
HMI : S02001100 v1.0.106
TC : S02200100 v1.0.084
IO
2.2 Extra Settings
Sound on alarm
Screen saver
SWITCH ON
MICRON+ PISTÓN
HMI
TC
IO
: S02001100 v1.0.106
: S02200100 v1.0.084
: S02102100 v1.0.106
Inside device temperature alarm
85 °C 60 s
Pumping autolock
Off after reset
Modbus
MICRON+ PISTÓN
HMI : S02001100 v1.0.106
TC : S02200100 v1.0.084
IO
2.2 Extra Settings
Sound on alarm
Screen saver
SWITCH ON
Inside device temperature alarm
85 °C 60 s
Pumping autolock
Off after reset
Modbus
Node: 10 B: 57600
SWITCH ON EQUIPMENT ON
2.2 Extra Settings
Sound on alarm
Screen saver
MA-5184-ENG MICRON+ PUR LC/MC ADHESIVE MELTER
Inside device temperature alarm
85 °C 60 s
Pumping autolock
Off after reset
Modbus
Node: 10 B: 57600
2.2 Extra Settings
Sound on alarm
READY ERROR
RUNNIG STANDBY
10 min
Inside device temperature alarm
85 °C 60 s
Pumping autolock
Off after reset
Modbus
Node: 10 B: 57600
2.2 Extra Settings
Sound on alarm
READY ERROR
RUNNIG STANDBY
10 min
Inside device temperature alarm
85 °C 60 s
Pumping autolock
Off after reset
Modbus
Node: 10 B: 57600
2.2 Extra Settings
Sound on alarm
READY ERROR
RUNNIG STANDBY
10 min
Inside device temperature alarm
85 °C 60 s
Pumping autolock
Off after reset
Modbus
Node: 10 B: 57600
READY ERROR
STOPPED
RUNNIG STANDBY
4-35
MICRON+ PISTÓN
HMI : S02001100 v1.0.106
TC : S02200100 v1.0.084
IO : S02102100 v1.0.106
MICRON+ PISTÓN
HMI : S02001100 v1.0.106
TC : S02200100 v1.0.084
IO : S02102100 v1.0.106
MICRON+ PISTÓN
HMI : S02001100 v1.0.106
TC : S02200100 v1.0.084
IO : S02102100 v1.0.106
MELER GLUING SOLUTIONS MELTER OPERATION
2.2 Extra Settings
Channel number
Regrind charger
Feeder
2.2 Extra Settings
Pattern controller
6
6
Pattern controller
Level detector
Extermal HMI
Wireless communication
Wireless Communication
Channel number
Connection Status
START
Online
SSID:
IP:
Network Name
0.0.0.0
Remote actuation
Remote SW update
Static Configuration
Wireless communication (Wi-Fi)
Optionally, the unit comes equipped with a wireless communication system to connect to a local network. This system connects the unit to a Meler Services
Platform(*) with the following main functions:
• Monitoring. Regularly sends the platform’s status and operating data.
The data can be configured according to user needs.
• Actions and Programming. It is possible to send specific actions or change the programming of a specific unit.
• Technical support. The unit provides direct information on its status and can schedule unit maintenance or keep a log of all interventions done on it.
(*) Check with the After-Sales Service or your Meler Sales Agent for more information about this service performance.
Connection configuration
1. Install the ‘Espressif Esptouch’ app on a smartphone device.
2. Connect the device to the local Wi-Fi network where you want to connect the melter, then run the app.
3. On the melter’s screen, click START to start syncing. Follow the instructions on the app to configure the melter’s Wi-Fi access.
4. The unit’s screen will show the connection status, the name of the Wi-Fi network, and the IP address automatically assigned.
You can also configure the following options from this screen:
• Remote control. Enables the unit to be able to receive actions.
• Remote software update.
Enables the unit to be able to receive software updates.
• Static configuration. Enables the configuration of a static IP address for the melter.
4-36
MELTER OPERATION
MICRON+ ENGRANE
MICRON+ PUR LC/MC ADHESIVE MELTER
HMI : S02001100 v1.0.106
TC : S02200100 v1.0.084
IO : S02102100 v1.0.106
IO : S02101100 v1.0.106
MICRON+ ENGRANE
Standby function
HMI : S02001100 v1.0.106
TC : S02200100 v1.0.084
IO : S02102100 v1.0.106
Using the standby function during periods of melter/applicator inactivity helps save energy and allows the heated elements to return quickly to their set point temperatures once you return to the operational mode.
When the function is activated, the target temperature of the heated zones is reduced to the programmed value for each zone (see ‘Heating menu / Heating zones’).
General Standby
Temperature
Temperature
1
General OFF
State
General OFF
Standby OFF
For example, if the target temperature of the tank is 160°C and the Under Main-
The priority protocol is as follows:
MICRON+ ENGRANE
HMI : S02001100 v1.0.106
pressed, the tank’s set point temperature will change to 130ºC.
IO : S02101100 v1.0.106
T: Tank
D: Distributor
OFF Group: 1
Standby
2
2.3 Input / Output
OFF
1st Under Maintenance external signal.
2nd ‘Under Maintenance’ function key.
Imput
DI1 Standby
or calendar programming.
COMs OFF
2
MICRON+ ENGRANE
Therefore, while the Under Maintenance external signal remains active, none of the other three systems can deactivate the function.
IO : S02101100 v1.0.106
The following criteria are suggested for standby function use:
2.2: Applicator 2
Output
DO2
Pump OFF
- If the period of inactivity is less than 2 hours, allow the melter applicator equipment to heat as normal.
- If the period of inactivity is more than 2 hours and less than 4 hours, use the standby function.
DO3
DO4
2
Alarms
Enable all the calendars
Adhesive Level
C1 C2 C3 C4 C5 C6
- If the period of inactivity is over 4 hours, use one of the following two options: turn off the equipment if you do not plan on using it for the rest of the day or keep the standby function on if you plan on using the equipment during that same day.
M T
Hour
W
ON
T F S
Standby
S
OFF
07:00
11:00
13:15
15:00
00.00
00.00
4-37
4-38
MELER GLUING SOLUTIONS MELTER OPERATION
By-pass valve regulation
The pumping system using a geared pump provides a constant flow of adhesive, according to the pump’s rotational speed.
In this type of system, the pressure generated by the pump is the result of the retentions found on the circuit (the length and diameter of the hose, elbows in the connectors, the diameters of the nozzle outputs, etc.) and the adhesive itself (its viscosity).
For safety reasons, this pressure must be discharged when the circuit exceeds the operating value (normally with a closed circuit and the pump activated), which makes the use of a discharge valve or a by-pass valve necessary.
This valve may be a manual adjustment valve, using a threaded screw, or with pneumatic control, using a pressure regulator and a pressure gauge. In the latter case, the adhesive circuit pressure has a 1:13 ratio to the pressure displayed on the pressure gauge.ç
DOUBLE PRESSURE SOLENOID VALVE (DP2- Optional)
This solenoid valve has two air-inputs and one air-output.
When the solenoid valve is activated, the pressure to the bypass valve is equal to the net pressure supplied to the melter. At the moment this device is not activated, air at a regulated pressure is introduced into the bypass valve.
The valve should not be activated when not applying adhesive in order not to let the system pressure raise. Thanks to that, we avoid the initial overpressure once the applicator starts applying.
solenoid valve
Manual valve control
To adjust the pressure with this valve model (in an approximate manner), follow these steps:
1. Screw the spindle in clockwise, as far as possible. In this position, the maximum pressure is 81,5 kg/cm 2 (8,82 bar).
2. Gradually loosen by turning counterclockwise until reaching the desired pressure. Each millimeter that the spindle sticks out represents a reduction of approximately 9 kg/cm 2 (8,82 bar).
MELTER OPERATION MA-5184-ENG MICRON+ PUR LC/MC ADHESIVE MELTER
Adjust pneumatic valve control(DP1 / DP2) (optional)
To adjust the pressure with this valve model, follow these steps:
1. Unlock the pressure regulator control by pulling on it gently.
2. Turn it clockwise to increase the pressure. This will be seen reflected on the pressure gauge located next to it
Warning : Do not exceed 6 bar of pressure. This corresponds to 80 bar on the hydraulic circuit.
Using the air drying system (optional)
Polyurethane-based reactive adhesives require a completely dry environment before they can be applied, since when they come in contact with atmospheric humidity, they reticulate, hardening quickly.
As an option, these melting equipments ensure a dry environment thanks to the addition of an air-drying system to these models. This guarantees that the adhesive is preserved without premature reticulations inside the applicator unit.
To maintain the air drying system in perfect condition, we recommend periodically observing the green indicator for filter saturation control. If this indicator turns red, it is necessary to replace the filter cartridges. See the corresponding chapter for replacement parts.
inlet solenoid valve regulators limit valve pressure gauge
Turning off the melter equipment
If you need to disconnect the melter equipment:
1. Turn off the machine switch.
2. The depressurization valve frees pressure from the hydraulic circuit, returning the adhesive to the tank.
3. Disconnect the pneumatic power to the applicators and the electrical power to the control unit programmer, if there is one.
4-39
MELER GLUING SOLUTIONS MELTER OPERATION
Application for PC
An optional application for PC (*) allows you to connect the unit with a USB port and perform the following functions:
• Update the HMI board software.
• Update the IOC board software.
• Update the TC board software.
• Make a complete backup of the system.
• Restore a complete backup of the system.
• Flash memory deletion.
• Make a backup of the data logger.
4-40
(*) http://www.meler.eu/media/S00900010_PC_App_Installer.zip
Warning: For more information consult your Focke Meler Representative or the Focke Meler Main Office.
MAINTENANCE MA-5184-ENG MICRON+ PUR LC/MC ADHESIVE MELTER
5. MAINTENANCE
Warning: The melter equipment is equipped with current technology, but has certain foreseeable risks. Therefore, only allow qualified personnel with enough training and experience to operate install or repair this equipment.
The following table briefly summarizes the indications for adequate melter equipment maintenance. Always read the corresponding section carefully.
Operation
External cleaning
Frequency
Daily
Refer to
Equipment cleaning
System depressurization
Remove electrical cabinet
Emptying and cleaning the tank
Check for pump leaks
Check the lubrication (motor and gear)
Check thermostat operating
Before performing maintenance tasks and repairing the hydraulic system
Before performing maintenance of distributor, pump or gear motor
- When burnt adhesive is present
- With each adhesive change
Depending on the hours of operation and the temperature and speed parameters
(min. once per month)
Depending on the temperature and conditions of use (max. 8000 hours)
System depressurisation
Access inside the unit
Cleaning the tank
Pump maintenance
Gear motor maintenance
- Checking while working Safety thermostat
Air dryer filters (option)
Equipment change
- Purge water condensation (weekly)
- Clean the filter (at least twice a year)
- Equipment change or repair
Air filter maintenance
Remove the equipment from its base
Equipment cleaning
To continue to take advantage of the melter’s benefits and to ensure the perfect mobility of its components, it is necessary to keep all its parts clean, especially the ventilation grate on the upper part of the machine.
Warning: Risk of electric shock. Carelessness may result in injury or death.
Clean the exterior using a cloth moistened with water. Do not use flammable liquids or solvents.
5-1
5-2
MELER GLUING SOLUTIONS
D
E
C
A
B
D
MAINTENANCE
To carry out external cleaning:
• Use cleaning products compatible with polyamide materials.
• Apply the cleaning product with a soft cloth.
• Do not use sharp tools or scrapers with sharp edges.
Removing and changing exterior panels:
1. Turn off the melter.
2. Disconnect the compressed air from the machine intake.
3. To remove the casing from the machine, first you have to separate the electrical cabinet from the tank. To do this, slacken the 1/4 turn screw as indicated (A) and slide it along the guides.
4. To remove the electrical cabinet door, open the door by turning the
1/4 turn screw as indicated (B), lift the door, turn it and remove the screws (C).
5. To remove the electrical cabinet casing, slacken the screws (D) that hold it to the base of the machine and the screws (E) that hold it to the structure of the electrical cabinet.
6. To remove the tank casing, remove screws F and G that hold this casing to the base of the equipment. The lid and the casing are removed from the tank at the same time.
7. The tank lid of MICRON+ 5 and 10 is removed once the tank casing has been dismantled. It is simply a matter of sliding the shafts at the ends along the grooves in the casing. (See diagram 1).
The tank lid of MICRON+ 20 and 35 is removed loosening the side lid screws (See diagram 2).
1 2
G
F
8. To assemble the casing, follow the instructions in reverse order.
MAINTENANCE MA-5184-ENG MICRON+ PUR LC/MC ADHESIVE MELTER
System depressurisation
Even with the motor turned off, residual pressure may exist in the circuit. This must be kept in mind when performing any operation on the hydraulic circuit.
Before disconnecting any hydraulic element or opening any distributor outlet, it is necessary to perform the following steps:
1. Turn off the machine switch on the door of the electrical cabinet.
2. Operate the purge valve housed in each distributor to free any residual pressure from the circuit. Adhesive residues fall down by the laterally positioned chute for this purpose.
3. Purge all applicators that have been used either manually or with the corresponding program command.
Access to the interior of the equipment
Access to distributor
To access the distributor where both the bypass valve pressure regulator and the purge-filter assembly are located it is necessary to open the casing as indicated. To do this, loosen the quarter turn screw that keeps the access door in the closed position (A).
Access to pump gear- motor
To access the pump- gear motor assembly, it is necessary to remove the electrical cabinet from its location together with the portion of the chassis that lies underneath. To do this, loosen the quarter turn screw that keeps the equipment in the closed position (B) and slide it on the guides.
Next, open the access door to the distributor (A) and remove the front casing by releasing the screws as shown (C).
To access the interior of the equipment it is not necessary to open the electrical cabinet door.
A
B
C C
5-3
5-4
MELER GLUING SOLUTIONS purge zone
11
MAINTENANCE
Filter maintenance
Micron gear series melter equipment is equipped with a 50 mesh pump filter.
The filter prevents impurities and burnt adhesive remains from being pushed out from the tank by the pump.
Warning: It is a good idea to also use a grill in the tank. This grill performs a first-step filtration, preventing great impurities.
The adhesive flows from the inside to the outside of the filter, with impurities being trapped inside it.
The drain valve is included in the filter cap.
When the filter is removed from its housing, all the impurities remain trapped inside, and the inside of the distributor stays perfectly clean. The filter may be cleaned or replaced directly with a new one.
No rule exists for determining when to change the filter. Several factors influence this decision:
• The type and purity of the adhesives used.
• The adhesive work temperatures.
• Adhesive consumption in relation to the time it spends in the tank.
• Changes in the type of adhesive used.
In any case, we recommend checking and cleaning the filter at least every
1000 hours of operation (melter equipment turned on).
Warning: Always use protective gloves and goggles. Risk of burns.
To change the filter, it should be borne in mind that the filter and purge valve are the same assembly:
1. Depressurise the system and open the casing shown.
2. Using a flat blade screwdriver, open the drain valve contained in the filter head anticlockwise (1) and wait until any remaining adhesive has fallen down the ramp.
3. To remove the whole filter, unscrew the assembly’s hexagonal plug using a 22 mm socket driver and remove it.
4. Depending on the amount of dirt inside the cartridge, clean it or throw it away, following the applicable waste regulations.
5. Replace the joints if they are damaged.
6. Screw the assembly up again, clockwise.
MAINTENANCE MA-5184-ENG MICRON+ PUR LC/MC ADHESIVE MELTER
7. Replace the assembly inside the distributor and fasten it clockwise.
Tighten the purge screw clockwise with a flat blade screwdriver.
8. Continue working as usual.
Cleaning the tank
The hot-melt tank must be cleaned on occasion to maintain its fusion and anti-adherence properties. The tank is covered on the inside with PTFE and inclined enough to aid unloading the hot-melt and to avoid it from being retained inside when consequential burning occurs.
Furthermore, when adhesives are mixed, reactions may occur between them, causing a degeneration and thus problems in unloading in the direction of the pump.
Therefore, it is recommended to clean the deposit every time that:
• A change is made to a different type of hot-melt.
• Too much burnt material is generated in its interior.
Changing adhesive type
1. Use up as much of the adhesive as possible.
If it is necessary to unload the adhesive without having used it up as much as possible, follow the instructions in the section ‘Emptying the tank’.
2. Clean the remains of hot-melt adhesive on the inside of the tank.
Warning: Use appropriate protective equipment for high temperatures.
3. Add the appropriate type and quantity of the new adhesive, wait for it to melt and pump at least one full tank through the system (hoses and applicators).
Cleaning burnt adhesive
1. Empty the tank directly (see the section ‘Emptying the tank’) to prevent the burnt material from passing through the pump circuit.
2. Clean the adhesive remains and burnt material inside the tank. Do not use sharp objects that might damage the inside coating.
Warning: Use appropriate protective equipment for high temperatures.
3. Add the appropriate type and quantity of adhesive and wait for it to melt.
5-5
5-6
MELER GLUING SOLUTIONS MAINTENANCE
4. Remove the filter cartridge and clean it, if necessary (see the section
‘Filter maintenance’).
5. Reassemble the filter without the cartridge.
6. Pump a minimum of one tank through any distributor output.
7. Remove the filter and attach it to the corresponding cartridge. Reinstall it in the distributor.
8. Refill the tank with adhesive, wait for it to melt and continue working as usual.
Warning: Whenever you handle the filter or any other element subject to pressure, you must always perform a system depressurization first (see the corresponding section)
Emptying the tank
During normal maintenance activities, it is recommended, and sometimes necessary to empty the tank directly, without passing the adhesive through the pump system.
In the case of the Micron 5, the tank does not have a pouring chute so, to empty out the adhesive you need to wait until it has cooled and separate it from the walls of the tank, making it easier to remove.
For the other models, empty the tank following these indications:
1. Keep the tank at working temperature.
2. Remove the tank cover and then its casing.
3. Lower the emptying chute attached to the tank and put a suitable container in position.
4. Unscrew the plug and allow the adhesive to flow freely into the container.
5. Once it is completely empty, clean the exit hole and chute of remains of adhesive.
6. Put the plug back in position.
7. Raise the emptying chute and put the cover of the casing back in position.
Warning : Use appropriate protective equipment for high temperatures.
MAINTENANCE MA-5184-ENG MICRON+ PUR LC/MC ADHESIVE MELTER
Pump maintenance
Inspecting for leaks
The pump is equipped with a gasket system on the shaft to prevent adhesive from leaking through it. On occasion, some adhesive may leak out, which makes it necessary to retighten the screws or change the gasket.
Warning : Changing the gasket with a hot pump.
In the event of a leak through the seat gaskets between the pump and the distributor, re-tighten the pump-distributor binding screws; if the leak continues, replace the gaskets. To do this:
1. Release the shaft coupling from the pump.
2. Retighten or remove the screws that hold the gasket in place.
3. Replace the gaskets and reassemble the parts.
Occasionally, as a result of the system’s heating-cooling cycles, it may be necessary to retighten the screws.
Before making any changes, establish the location of the leak. However, before replacing any parts and in case of any doubt, we recommend that you consult the Meler Technical Service Centre.
Warning : Always wear protective gloves and goggles. Risk of burns.
Gear motor maintenance
Cleaning the motor fan
Periodically inspect the condition of the motor fan and its vent screen.
If dust has accumulated, blow gently with air to clean it (remove the protective cover, if necessary).
Checking the lubricant
The gear reducers are delivered filled with synthetic grease for lubrication
-free of outside contamination- ‘for life’. Ambient temperature 0 ÷ 40 °C, with peaks of as low as -20 °C and up to +50 °C.
Use only those lubricants recommended by the manufacturer. The use of other types may cause premature wear or damage to the gear reducer.
Approximately 0.1 kg of lubricating grease fits in the gear reducer model used.
5-7
5-8
MELER GLUING SOLUTIONS
0.01µm
5µm
MAINTENANCE
Recommended lubricants
BRAND
IP
SHELL
MOBIL
TYPE OF OIL
Telesia Compound A
Tivela Compound A
Glygoyle Grease 00
Safety Thermostat
If there is a deactivation of the thermostat, dismantle the tank casing with the cover and slide the electrical cabinet along. When you can see the thermostat, press the button indicated to reset it.
Air dryer filter maintenance
The filtering elements prior to the air dryer device on the melting equipment are equipped with a filter saturation indicator, which indicates the best time to change the filter cartrtidge:
- Green colour: Low level of cartridge contamination.
- Red colour: The cartridge is contaminated. Replace immediately, otherwise equipment performance cannot be guaranteed.
We recommend installing new cartridges once a year, regardless of the indicator reading (differential pressure).
Follow these steps to change the cartridge:
- Close the air valve.
- Release the drainage hose from the reservoir, if connected.
- Slowly turn the knurled screw clockwise. This will purge the air from the filter.
- Push the reservoir towards the head of the filter.
- Slowly turn the reservoir clockwise as far as possible (1/8 of a turn) and remove it, pulling down.
- Remove the cartridge and replace it with a new one (do not touch the filter screen with your hands).
- Mount the reservoir, following these instructions in reverse order.
- Pressurize the filter, opening the by-pass valve slowly.
Warning : It is necessary to keep the power connected to the unit in order to keep the air dryer system operational. The system may operate even with cold adhesive, in order to keep the internal environment moisture-free.
MAINTENANCE MA-5184-ENG MICRON+ PUR LC/MC ADHESIVE MELTER
Remove the equipment from its base
For more thorough equipment maintenance, it is necessary to remove it from its present location to be able to perform operations more comfortably and with greater accessibility.
To do this, the equipment should be removed from its base following these indications:
1. Turn off the machine switch on the door of the electrical cabinet.
2. Depressurise the system (1).
3. Disconnect the hoses connected to the distributor outputs both electrically and hydraulically.
4. Disconnect the input power supply and ground connection.
5. Raise the machine to extract it from the base.
1
5-9
5-10
MELER GLUING SOLUTIONS MAINTENANCE
Esta página no contiene texto.
TECHNICAL CHARACTERISTICS MA-5184-ENG MICRON+ PUR LC/MC ADHESIVE MELTER
6. TECHNICAL CHARACTERISTICS
Generals
MICRON PUR LC MICRON PUR MC
Tank capacity
Pumping rate simple pump double pump (per output)
Melting rate
Number of outputs
Temperature range
5,15 liters
1, 2.5, 4, 8 cc/rev (*)
2x0.93, 2x1.86, 2x3.71, 2x4.8 cc/rev (*)
2 kg/h (*)
2, 4 ó 6 with one pump
40 a 200°C (104 a 392°F)
37,4 liters
1, 2.5, 4, 8 cc/rev (*)
2x0.93, 2x1.86, 2x3.71, 2x4.8 cc/rev (*)
20 kg/h (*)
2, 4 ó 6 with one pump
40 a 200°C (104 a 392°F)
Temperature control
Max. working pressure (at 6 bar)
RTD ±0.5°C (±1°F)
Pt-100, Ni-120 o NTC-R
80 bar (1160 psi)
Max. installation power with a simple pump/2 outputs with a simple pump/4 outputs with a simple pump/6 outputs with two simple pumps/2 outputs with two simple pumps/4 outputs
External functions
Inputs
1 x 8,5KW / 3 x 4,5KW
1 x 12,1KW / 3 x 4,5KW
1 x 15,6KW / 3 x 5,8KW
1 x 9,8KW / 3 x 4,5KW
1 x 13,4KW / 3 x 4,6KW
Unit On-Off / Standby On-Off /
Activity Control / Pumping On-Off /
Communications On-Off / Electrical
Outputs Inhibition.
RTD ±0.5°C (±1°F)
Pt-100, Ni-120 o NTC-R
80 bar (1160 psi)
1 x 10,0KW / 3 x 4,3KW
1 x 13,5KW / 3 x 6,1KW
1 x 17,2KW / 3 x 7,9KW
1 x 11,3KW / 3 x 5,3KW
1 x 14,9KW / 3 x 7,1KW
Unit On-Off / Standby On-Off /
Activity Control / Pumping On-Off /
Communications On-Off / Electrical
Outputs Inhibition.
Outputs
Electrical requirements
Standby / Zones Temperature OK /
Machine Ready / Running / Alarm /
Level / No Level
LN ~ 230V 50Hz + PE
3N ~ 400V 50Hz + PE
Ambient temperature
Dimension (LxAxH)
Weight with one pump
0 a 40°C
730 x 420 x 630 mm
730 x 420 x 910 mm (lid open)
105 kg (empty)
Standby / Zones Temperature OK /
Machine Ready / Running / Alarm /
Level / No Level
LN ~ 230V 50Hz + PE
3N ~ 400V 50Hz + PE
0 a 40°C
740 x 520 x 870 mm
740 x 520 x 1215 mm (lid open)
147 kg (empty)
6-1
MELER GLUING SOLUTIONS
Dimensions
670+250mm
730mm
670mm
TECHNICAL CHARACTERISTICS
Micron PUR LC
740+250mm
740mm
425mm
Micron PUR MC
6-2
520mm
Note: if using equipment with a double motor-pump assembly, you must increase the height by 210 mm.
TECHNICAL CHARACTERISTICS MA-5184-ENG MICRON+ PUR LC/MC ADHESIVE MELTER
MOUNTING THE EQUIPMENT Micron PUR LC
13
9
96 377,5
569,5
MOUNTING THE EQUIPMENT PUR MC
13
Ø9
Ing. Fabricación
APROBACION
Nombre:
Calidad
Nombre:
Producción
Nombre:
EQUIPO
DE SEGURIDAD
ZAPATOS GUANTES GAFAS OTROS
MANTENER ORDEN Y LIMPIEZA
EN EL PUESTO Y
EN LA LINEA EN GENERAL
Formación requerida operario
Nº de Pokayokes
Piezas en proceso
Calibración requerida
96 529,5
721,5
Note: the indicated holes are for M8 screws.
Micron PUR gear range option accessories
Ing. Fabricación Calidad Producción
APROBACION
Nombre: Nombre: Nombre:
EQUIPO
DE SEGURIDAD
ZAPATOS GUANTES GAFAS OTROS
MANTENER ORDEN Y LIMPIEZA
EN EL PUESTO Y
EN LA LINEA EN GENERAL
Formación requerida operario
Nº de Pokayokes
Piezas en proceso
Calibración requerida
Air drying system for PUR adhesives
Polyurethane-based reactive adhesives, known as P.U.R. (reactive polyurethanes), require a completely dry environment before they can be applied, since when they come in contact with atmospheric humidity, they reticulate, hardening quickly.
The Micron gear melting equipment ensures a dry environment thanks to the addition of an air-drying system to these models, which provides a level of dehumidification above 99.98%. This guarantees that the adhesive is preserved without premature reticulations inside the applicator unit.
6-3
6-4
MELER GLUING SOLUTIONS TECHNICAL CHARACTERISTICS
Pneumatic by-pass valve pressure control system
The equipment’s by-pass valve provides an important safety feature, as it limits the maximum pressure in the system, especially during continuous pumping periods with closed applicators.
This valve may be a manual adjustment valve, using a threaded screw, or with pneumatic control, using a pressure regulator and a pressure gauge. In the latter case, the adhesive circuit pressure has a 1:13 ratio to the hydraulic pressure.
Level control system
There are three methods for controlling the hot-melt level in the interior of the tank: by means of a capacitive sensor that issues a warning when the adhesive reaches the programmed level thanks to a low level signal, by means of a float sensor with a low level display on the control board, or from the main machine by means of a NO (normally open) voltage-free contact.
Optional equipment
Wheel system
For all the Micron+ gear machines there is the option to add 4 wheels to the base of the machine to make it easier to move.
ELECTRICAL DRAWINGS MA-5184-ENG MICRON+ PUR LC/MC ADHESIVE MELTER
7. ELECTRICAL DRAWINGS
To view the the electrical drawing of the purchased equipment, see the CD of electrical drawings included.
7-1
7-2
MELER GLUING SOLUTIONS ELECTRICAL DRAWINGS
This page is intentionally left blank.
PNEUMATIC DIAGRAM MA-5184-ENG MICRON+ PUR LC/MC ADHESIVE MELTER
8. PNEUMATIC DIAGRAM
Components list
Pneumatic by-pass valve control system (optional)
- 1
- 2
- 3
Pressure regulator 1-10 bar
Pressure gauge 0-10 bar
Pneumatic limit control valve
1 2
REGULADOR DE PRESIÓN
PRESSURE REGULATOR
P: 0-10 bar
MANÓMETRO
MANOMETER
P: 0-10 bar
3
VÁLVULA LIMITADORA / PRESSURE LIMIT VALVE
RELACIÓN / RATIO 1:15
ENTRADA AIRE
AIR INPUT
8-1
8-2
MELER GLUING SOLUTIONS
Air drying system (optional)
- 5
- 6
- 7
- 8
- 9
- 1
- 2
- 3
- 4
Filter– 1st stage, grade 7
Filter – 2nd stage, grade 5
Air dryer
3/2 solenoid valve with manual control
Pressure regulator 1-10 bar
Pneumatic relief valve 0.5 bar
Pressure regulator 0.1-0.7 bar
Pressure gauge 0-1.6 bar
Output nozzle
PNEUMATIC DIAGRAM
SPARE PARTS LIST MA-5184-ENG MICRON+ PUR LC/MC ADHESIVE MELTER
9. SPARE PARTS LIST
The list of the most common spare parts for MICRON+ PUR series machines appears in this section, providing a quick and reliable guide to choosing them.
The spare parts are grouped together naturally, in the same way as they are located in the melters.
As a visual aid, drawings of the parts are included and are numbered to help identify them in the list. For further information about the content of the spare parts, click on the number of the spare part.
The lists provide the reference and name of the spare part, indicating, when necessary, whether the reference corresponds to the PUR LC and PUR MC model.
9-1
9-2
MELER GLUING SOLUTIONS SPARE PARTS LIST
This page is intentionally left blank.
SPARE PARTS LIST
CHASSIS GROUP
E
MA-5184-ENG MICRON+ PUR LC/MC ADHESIVE MELTER
ELECTRIC
GROUP
F
I
DRY AIR ASSEMBLY
A
TANK GROUP
B
DISTRIBUTOR GROUP
C
DISTRIBUTOR
GROUP
G
ELECTRONIC GROUP
D
H
PNEUMATIC
UNIT
PUMP ASSEMBLY-
MOTORREDUCTOR
9-3
9-4
4
2
6
10
3
5
MELER GLUING SOLUTIONS SPARE PARTS LIST
A. TANK ASSEMBLY
1
9
3
4
2
3
1
2
Nº Ref.
1 150117350
Description
Complete tank assembly Micron PUR LC 230V
150117360
150117370
Complete tank assembly Micron PUR MC 230V
Tefloned coated tank Micron PUR LC 230V
150117380
150113370
150028830
150113870
Tefloned coated tank PUR MC 230V
Tank grid Micron PUR LC
Tank grid Micron PUR MC
Inlet tank Micron PUR LC
5
6
4
5
150117390 Inlet tank Micron PUR MC
150113410 Tank insulation mantle Micron PUR LC
150117600 Tank insulation mantle Micron PUR MC
150117410 Magnetic detector lid opening
9
9
7
8
150114500
10030007
150114530
150117570
Safety thermostat, up to 200°C
Power connection terminal
Sensor Pt100
Sensor Ni120
10 150110140 Capacitive sensor Rechner KXS-M12/25
8 7
SPARE PARTS LIST
B. DISTRIBUTOR UNIT
Nº
1
2
3
4
Ref.
150113570
150026380
150090360
150023950
Description
Tank-distributor union o-rings. Micron PUR LC
Coupling tank-distributor o-rings. Micron PUR LC
Tank-distributor union o-rings. Micron PUR MC
Coupling tank-distributor o-rings Micron PUR MC
MA-5184-ENG MICRON+ PUR LC/MC ADHESIVE MELTER
1
2
2
3
4
9-5
13
9-6
12
MELER GLUING SOLUTIONS SPARE PARTS LIST
6.3
6.2
11
11.1
C. DISTRIBUTOR SIMPLE/ DOUBLE ASSEMBLY
Ref.
150026270
150026300
150114390
150029260
150116050
150113260
10100082
10100083
150026260
150026280
150026290
150026060
150117180
10030007
150117190
150114530
150117570
150117330
150117340
150026410
150026420
Nº
10
10
11
11.1
12
13
8
9
6.1
6.2
6.3
7
5
6
3.1
3.2
3.3
4
1
2
3
Description
Pneumatic pressure regulator
Pneumatic pressure regulator o-rings
Complete purger
O-ring Ø23X3
O-ring Ø29.87 X 1.78
O-rings filter assembly kit
Tapón con junta
Pump o-ring Ø11,89 X 1,98
Mechanical pressure regulator
Mechanical pressure regulator o-rings
Mechanical pressure regulator spring
Closure needle of pneumatic pressure regulator
Coupling hydraulic outlets
Current connection strip
Heating element 315W Ø9.46.152mm 230V
Sensor Pt100
Sensor Ni120
Simple distributor insulation
Double distributor insulation
Plug M27x2 with o-ring
O-ring of M27x2 plug
10
9
8
7
4
5 4
6.1
2
1
3.2
3.5
3.3
3.4
3.1
3
6
SPARE PARTS LIST MA-5184-ENG MICRON+ PUR LC/MC ADHESIVE MELTER
D. GEARED MOTOR-PUMP ASSEMBLY
7
7
6
6
7
7
6
6
4
5
2
3
Nº
1
Réf.
150117170
150117150
150117160
150026430
150111890
150025960
150114020
150025930
150025970
150111860
150111870
150111880
150030050
Désignation
Geared motor 0.375 KW with booster fun
Simple pump motor coumpling
Double pump motor coumpling
Simple pump o-rings
Double pump o-rings
Simple gear pump 1 cc/rev
Simple gear pump 2.5 cc/rev
Simple gear pump 4 cc/rev
Simple gear pump 8 cc/rev
Double gear pump 0.93x2 cc/rev
Double gear pump 1.86x2 cc/rev
Double gear pump 3.71x2 cc/rev
Double gear pump 4.8x2 cc/rev
4 6 2
1
5 7 3
9-7
9-8
2
1
MELER GLUING SOLUTIONS SPARE PARTS LIST
E. CHASSIS ASSEMBLY
2
2
Nº
1 (*)
Ref.
150117140
150113290
150113360
Description
Micron electrical cabinet door casing Micron+
Electrical cabinet casing assembly without warning light
Electrical cabinet casing assembly with warning light
3
3.1
4
4.1
-
-
-
-
Micron PUR LC tank housing assembly
Micron PUR MC tank housing assembly
Micron PUR LC tank cover assembly
Micron PUR MC tank cover assembly
(*) For equipments with two motors, ask for the reference.
4
4.1
3
3.1
SPARE PARTS LIST
F. ELECTRIC ASSEMBLY
2
3
4
5
Nº
1
2
Ref.
16010003
150020720
150130450
150123000
150119190
150114470
Description
Female connector 8 pin (base housing)
Female connector 12 pin (base housing)
Female connector 8 pin NTC
Cable gland Pg 21 black
Cable gland Pg16 black
Main switch
MA-5184-ENG MICRON+ PUR LC/MC ADHESIVE MELTER
2 1
3
4
2
5
9-9
9-10
MELER GLUING SOLUTIONS
1
8
6 7
SPARE PARTS LIST
G. ELECTRONIC ASSEMBLY
4
5
2
3
1
2
Nº
1
8
9
6
7
150125580
150126180
9
9
150126170
150126160
(*) opcional
Ref.
150130780
150130790
150122980
150122990
1501123610
R0001938
150114760
150117110
150117120
Description
Control board Micron HMI micron+ 1 pressurized tank pump
Control board Micron HMI micron+ 2 pressurized tank pump
Power board Micron 2 outlets
Power board Micron 6 outlets
Card I/O pumping Micron+ PUR
Solid state relay 40A
Capacitive detector and amplifier kit (*)
Inverter Siemens G110 0,55KW
Power supply 24V 2,2A
Micron + wifi communication card kit with antenna
Fuse 10A 5x20
Fuse 10A 6,3x32
Fuse 16A 6x32
5
4
2 9
1
3
SPARE PARTS LIST MA-5184-ENG MICRON+ PUR LC/MC ADHESIVE MELTER
H. PNEUMATIC COMPONENTS
Nº
1
2
Ref.
150110730
150114480
Description
Pneumatic limit valve
Pressure gauge
3 10110031 Pressure regulator
Note: these elements are added to the equipment when by-pass pneumatic regulation.
1
2 3
9-11
9-12
MELER GLUING SOLUTIONS
J. AIR DRYER ASSEMBLY (OPTIONAL)
7
8
5
6
2
3
Nº
1
4
Ref.
150110410
150110390
150110400
10110031
150029540
150029550
150028380
150028420
Description
Air dryer excelon pro 92 series
Filter F92C-NND-AT0
Filter F92G-NNN-AT1
Pressure regulator
Pressure regulator 0,1-0,7 bar
Pressure gauge 0-1,6 bar
Pneumatic limit vale 0.5 bar 1/4’
Solenoid valve 3/2 1/8 24V DC 5.4W
SPARE PARTS LIST
8 4 5 6 1 2 3
7
EC DECLARATION OF CONFORMITY
Original Declaration
The manufacturer, Focke Meler Gluing Solutions, S.A.
Pol. Los Agustinos, c/G, nave D-43
E-31160 Orkoien, Navarra - Spain
— A Focke Group Company — declaring that the machinery, Type:
Model:
Serial Number: fulfils all the relevant provisions of the Directive 2006/42/EC on machinery, and the object of the declaration described above is in conformity with the relevant Union harmonisation legislation:
• Directiva 2014/30/EU on the harmonisation of the laws of the Member States relating to electromagnetic compatibility .
• Directiva 2011/65/EU and its amendments on the restriction of the use of certain hazardous substances in electrical and electronic equipment.
In reference to the harmonised standards:
• EN ISO 12100:2010. Safety of machinery - General principles for design - Risk assessment and risk reduction.
• EN ISO 13732-1:2008. Ergonomics of the thermal environment - Methods for the assessment of human responses to contact with surfaces - Part 1: Hot surfaces.
• EN ISO 13849-1:2015. Safety of machinery - Safety-related parts of control systems - Part 1: General principles for design.
• EN ISO 14120:2015. Safety of machinery - Guards - General requirements for the design and construction of fixed and movable guards.
• EN 60204-1:2006, +/A1:2009, +/AC:2010. Safety of machinery - Electrical equipment of machines - Part 1:
General requirements.
• EN 61000-6-2:2005, +/AC:2005. Electromagnetic compatibility (EMC) - Part 6-2: Generic standards - Immunity for industrial environments.
• EN 61000-6-4:2007, +/A1:2011. Electromagnetic compatibility (EMC) - Part 6-4: Generic standards - Emission standard for industrial environments.
• EN 50581:2012. Technical documentation for the assessment of electrical and electronic products with respect to the restriction of hazardous substances.
This declaration of conformity is issued under the sole responsibility of the manufacturer.
The person authorised to compile the technical file is the manufacturer established at the above address in this declation.
Signed in Orkoien, to date:
V0519
Javier Aranguren
Managing Director
For more information speak with your Focke Meler representative:
Focke Meler Gluing Solutions, S. A.
Pol. Los Agustinos, c/G, nave D-43
E-31160 Orkoien - Navarra - Spain
Phone: +34 948 351 110
Fax: +34 948 351 130 [email protected] - www.meler.eu
A Focke Group Company
advertisement
Related manuals
advertisement
Table of contents
- 9 General
- 9 Symbols
- 10 Mechanical components
- 10 Electrical components
- 10 Hydraulic components
- 10 Pneumatic components
- 11 Thermal components
- 11 Materials
- 11 Noise emission declaration
- 12 Intended use
- 12 Limited use
- 13 Description
- 14 Modes of operation
- 14 Hot-melt melter/applicator identification
- 15 Main components
- 16 Main components de Micron PUR Gear with two motor-pumps
- 17 Control panel components
- 18 Micron PUR series range
- 19 Micron PUR gear range option accessories
- 19 Air dryer system
- 19 Bypass valve pressure control system
- 19 Level control system
- 19 Warning light option
- 19 Level control system
- 19 Optional equipment
- 21 Introduction
- 21 Installation requirements
- 22 Electrical Consumption
- 23 Compressed air
- 23 Other factors
- 23 Unpacking
- 23 Contents
- 24 Mounting the equipment
- 24 Electrical power connection
- 25 Pneumatic connection
- 26 Parameter Programming
- 1 Establecer temperaturas de trabajo
- 1 Selección del valor de sobretemperatura
- 1 Mantener la visualización de un elemento
- 1 Conexión de I/O externas
- 1 Salida de errores de tarjeta de bombeo
- 27 External I/O connections
- 29 Connecting external inputs and outputs
- 30 Interpretation of external inputs and outputs
- 32 Connecting zone inhibition
- 33 External signals of pumping control
- 33 Connection of externar singnals for pumping control
- 35 General information
- 36 Air- tight tank lid
- 36 Opening the air-tight tank lid
- 38 Filling the tank
- 38 Starting up the melter equipment
- 39 Manual pumping permmision
- 40 Melter equipment display
- 41 General characteristics
- 41 Navigation icons
- 41 Save changes
- 41 Interpretación de las pantallas
- 42 Home display
- 42 General temperature status
- 43 Alarms status
- 43 Calendar status
- 43 Adhesive level status
- 44 Pumping status
- 44 Temperature status
- 45 Temperature and Heating Shortcut displays
- 46 Programming of temperatures
- 46 Programming of statuses
- 46 Menú Calendars
- 47 Units and Lenguage Menu
- 47 Date and time configuration
- 47 Alarms and warnings
- 48 Pumping control menu
- 50 Modes of operation
- 50 Operating mode with internal pumping control and internal speed control
- 51 Operating mode with internal pumping control and external speed control
- 52 Operating mode with external pumping control and internal speed control
- 53 Operating mode with external pumping control and external speed control
- 54 Configuring speed ramp
- 54 Main Menu
- 55 ‘1. Heating’ Menu
- 55 1.1 Heating zones
- 56 1.2 Sequential Heating
- 56 1.3 Inhibitions
- 57 1.4 Auto Standby - OFF
- 58 1.5 Extra temperature settings
- 59 ‘2. General settings’ Menu
- 59 2.1 Password management
- 60 2.2 Extra settings
- 61 2.3 Configuration of input and output signals
- 61 2.4 Restore default values
- 62 ‘3. Load’ Menu
- 62 Screen 1: Minimum adhesive level sensor
- 62 Screen 2: Automatic adhesive feeder
- 62 Screen 3: Dry air/gas injection
- 63 Screen 4: Pressurisation (only for units with an airtight tank lid)
- 63 ‘4. Statistics’ Menu
- 64 Menu ‘5. Pumping’
- 65 Automatic pumping block function
- 65 ‘Automatic pumping block’ enabled
- 66 ‘Automatic pumping block’ disabled
- 67 ‘Turning off after resetting’ function
- 67 ‘Turning off after resetting’ enabled
- 68 ‘Turning off after resetting’ disabled
- 68 Configuration of turning on and activating pumping
- 70 Wireless communication (Wi-Fi)
- 70 Connection configuration
- 71 Standby function
- 72 By-pass valve regulation
- 72 Manual valve control
- 73 Adjust pneumatic valve control(DP1 / DP2) (optional)
- 73 Using the air drying system (optional)
- 73 Turning off the melter equipment
- 74 Application for PC
- 75 Equipment cleaning
- 77 System depressurisation
- 77 Access to the interior of the equipment
- 77 Access to distributor
- 77 Access to pump gear- motor
- 78 Filter maintenance
- 79 Cleaning the tank
- 79 Changing adhesive type
- 79 Cleaning burnt adhesive
- 80 Emptying the tank
- 81 Pump maintenance
- 81 Inspecting for leaks
- 81 Gear motor maintenance
- 81 Cleaning the motor fan
- 81 Checking the lubricant
- 82 Recommended lubricants
- 82 Safety Thermostat
- 82 Air dryer filter maintenance
- 83 Remove the equipment from its base
- 85 Generals
- 86 Dimensions
- 87 Micron PUR gear range option accessories
- 87 Air drying system for PUR adhesives
- 88 Pneumatic by-pass valve pressure control system
- 88 Level control system
- 88 Optional equipment
- 88 Wheel system
- 91 Components list
- 91 Pneumatic by-pass valve control system (optional)
- 92 Air drying system (optional)
- 96 A. TANK ASSEMBLY
- 97 B. DISTRIBUTOR UNIT
- 98 C. DISTRIBUTOR SIMPLE/ DOUBLE ASSEMBLY
- 99 D. GEARED MOTOR-PUMP ASSEMBLY
- 100 E. CHASSIS ASSEMBLY
- 101 F. ELECTRIC ASSEMBLY
- 102 G. ELECTRONIC ASSEMBLY
- 103 H. PNEUMATIC COMPONENTS
- 104 J. AIR DRYER ASSEMBLY (OPTIONAL)