advertisement
▼
Scroll to page 2
of
12
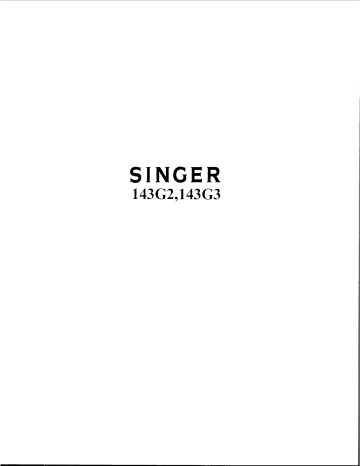
SINGER 143G2,143G3 "AD # Form K6485 (Form 2646w Rev.) (663) USE SINGER’ OILS INSTRUCTIONS and LUBRICANTS FOR USING AND ADJUSTING They insure freedom from lubricating trouble and give “ longer life to sewing equipment © ] М С Е R The following are the correct lubricants for this machine: | S EW N G MAC H | N E S TYPE B — MANUFACTURING MACHINE OIL, HEAVY GRADE When an oil is desired which will produce a minimum of _ . » ” a "r stain on fabrics, even after a long period of storage, use: TYPE D — MANUFACTURING MACHINE OIL, HEAVY GRADE OTHER SINGER* LUBRICANTS TYPE E — THREAD LUBRICANT For lubricating the needle thread of sewing machines for stitching fabrics or leather where a thread lubricant is required. TYPE F — MOTOR OIL For oil lubricated motors and plain bearings in power tables and transmitters. ] NOTE: All of the above oils are available in 1 quart, | 1 gallon and 5 gallon cans. = | .. GEAR LUBRICANT aw. | bE specially prepared grease is recommended for gear | 143 G 2 and 143 G3 ALSO ro. icati turi ines. N „er, | ubrication on manufacturing sewing machines | APDUES TO _ ВАМ. BEARING LUBRICANT we E This pure greose is specially designed for the lubrication MACHINES “of ball bearings and ball thrust bearings of motors and ln electric tronsmitters, ball bearing hangers of power tables, THE SINGER COMPANY etc. Furnished in 1 Ib. and 4 Ib. fins. *A Trademark of THE SINGER COMPANY Printed in Great Britain Copyright under International Copyright Union DESCRIPTION HIGH SPEED MACHINE 143G2 has an aluminiumalloy vibrating needle bar frame and a rotary hook, and is intended for over- seaming and Zigzag stitching on fine lingerie, general fabrics and light weight leather. It has ball bearings on the rear end of the arm shaft and hook driving shaft. The needle has a maxi- mum throw of 3/16 inch, vibrating both sides of a centre line. The speed of this machine is especially valuable in zigzag work and long overseaming in fine fabrics such as women's under- wear, slips, also reducing corsets, dresses, etc. It is success- fully used in general tailoring work and the manufacture of articles such as trousers, coats, gloves, and for certain opera- tions in the manufacture of shoes, such as attaching side and top facings to the linings and butting canvas or felt toe pieces to the end of the vamp. In the manufacture of table covers, draperies, scarfs, etc., an ornamental effect can be produced by overseaming a cord with thread of a contrasting colour. The raw edges of fabric may be overseamed by taking one stitch in the fabric and the other over the edge. MACHINE 143G3 is similar to Machine 143G2 except that the needle has a maximum throw of 5/16 inch. 1% is designed for basting and tacking coat pads. Speed The maximum speed recommended for either machine 13 3000 stitches per minute, the speeds depending on the material being sem. The machines should be run slower than the maximum speed at first until the parts which are in moving contact have become glazed by their action on each other. When the machine 13 in operation, the machine pulley should turn over toward the oper- ator. 4 To Oil the Machine Use "ТУРЕ В" or "TYPE D" OIL, sold by Singer Sewing Machine Company. For description of these olls, See inside front cover of this book. The machine should be oiled at the places designated by un- lettered arrows in Figs. 2 to 6, and when in continuous use it should be oiled at least twice a day. Che Sine *Mapeiacion va Vo “. o an BRA Fig. 2. Front View of Machine, Showing Olling Points Slip the belt off the machine pulley, turn the machine back on its hinges and apply oil to the points shown in Fig. 6, then Dring the machine forward into place. Fig. 3. Otling Points and Adjustments at Rear of Machine D Remove the face plate and apply oil to the places indicated in Fig. 4, then replace the face plate. Mo ys о! PO 72:89 Fig. 4. Face Plate Removed, Showing 911115 Points Turn back the cap at the top of the machine, and apply oil to the places shown in Fig. 5. | Е2?278 Fig. 5. Olling Points and Adjustments at Тор of Machine Fig. 6. Oiling Points and Adjustments Underneath the Machine 011 the bobbin case bearing in the hook race each time a bobbin is replaced, Needles Needles for Machines 143G2 and 143G3 are Catalogue 1901 (135x7), made in sizes 7,8,9,10,12,14,16,18,20,22 and 24. The size of the needle to be used should be determined by the size of the thread which mst pass freely through the eye of the needle. If rough or uneven thread is used, or if it passes with difficulty through the eye of the needle, the successful use of the machine will be interfered: with. Orders for needles must specify the QUANTITY required, the SIZE and also the Catalogue number. The following is an example of an intelligible order: "100 size 14, Catalogue 1901 Needles". Best results will be obtained with needles sold by Singer Sewing Machine Company. Relative Sizes of Needles and Thread Size Numbers For Cloth Work of Needles Cotton Silk le 70 to 100 00 to A 14 50 to 70 A, B 16 40 to 50 В, С 18 30 to 40 C, D 20 24 to 30 D, E To make a smooth, even stitch with your sewing machine, use good, firmly twisted and smoothly finished thread, that passes freely through the eye of the needle, 7 In using slack twist or uneven silk,should it be frayed or roughened, see whether the needle is too fine or too sharp, or has a hooked point, made by striking the throat plate, For ordinary work use the same size of thread on the bobbin as in the needle. Always use soft finished thread on the bobbin. Thread Left twist thread should be used in the needle. Either right or left twist thread can be used in the bobbin. Fig. 7. How to Determine the Twist Hold the thread as shown above. Turn the thread over toward you between the thumb and the forefinger of the right hand; if left twist, the strands will wind tighter; 11 right twist, the Strands will unwind. Use soft finish thread of the same size for the needle and the bobbin. Fig. 8. Removing the Bobbin case To Remove the Bobbin Case Lift the bobbin case latch, as shown in Fig. 8, and draw the bobbin case out from you, turn its open end down and release the latch and the bobbin will drop out. 8 To Wind the Bobbin (See Fig. 9) Fasten the bobbin winder to the table with its driving pulley in front of the machine belt so that the pulley will drop away from the belt when sufficient thread has been wound upon the bobbin, Fig. 9. Winding the Bobbin Place the bobbin on the bobbin winder spindle and push it on as far as it will go. Pass the thread down through the thread guide (1) in the ten- efon bracket, around the back and between tne tension discs (2), Then wind the end of the thread around the bobbin a few times, push the bobbin winder pulley over against the machine belt and start the machine. When sufficient thread has been wound upon the bobbin, the bobbin winder will stop automatically. If the thread does not wind evenly on the bobbin, loosen the screw (A) in the tension bracket and move the bracket to the right or left as may be required, then tighten the screw. The amount of thread wound on the bobbin is regulated by the screw (B). To wind more thread on the bobbin, turn the screw (B) inwardly. To wind less thread on the bobbin, turn the screw out- wardly. Bobbins can be wound while the machine is stitching. 4 + m nn 9 To Thread the Bobbin Case Hold the bobbin between the thumb and forefinger of the right hand, the thread drawing on the top from the left toward the right, as shown in Fig. 10. With the left hand, hold the bobbin case as snown in Fig. 10, the tension spring being at the front, and place the bobbin into the bobbin case. t рол Fig. 11 Then pull the thread into the slot in the edge of the bobbin case as shown in Fig. 11, and back under the ten- Sion spring into the slot at the end of the tension spring, as shown in Fig. 12, ce Fig. 12 10 To Replace the Bobbin Case After threading, take the bobbin case by the latch, holding it between the thumb and forefinger of the left hand: place the bobbin case on the centre stud of the bobbin case base, release the latch and press the bobbin case back until the latch catches the groove near the end of the stud. Allow the thread to hang free and replace the slide in the bed of the machine. To Set the Needle Push the needle up in the needle bar as far as it will go, with the long groove to the front, and secure it firmly with the set screw, It may be necessary to turn the needle slightly to the right or left for some threads if stitches are missed. Operators are liable to use needles which are too fine, Better results usually follow the use of a needle of a larger size. Threading the Needle (See Fig. 13) Turn the machine pulley until the thread take-up (10) is at its highest position. | Pass the thread from the unwinder, from back to front through the lower hole (1) in the pin on top of the machine, from right to left through the upper hole (2) in the pin, downward through the hole (3), upward through the middle hole (4) and downward through the hole (5) of the thread straightener, down and to the left between the tension discs (6), and against the pressure of the controller spring into the fork at (7), to the right of the wire guard (8), up through the thread guide (9), from right to left through the thread take-up eyelet (10), down again through the gulde (9), against the auxiliary thread take-up and back of the guide (11), into guide (12), down through the hole (13) at the lower end of the needle bar, and from front to back through the eye of the needle (14). Draw about two inches of thread through the eye of the needle with which to commence sewing. um —г 11 Fig. 13. Threading the Needle To Prepare for Sewing With the left hand hold the end of the needle thread, leav- ing 1t slack from the hand to the needle, tum the machine pul- ley over toward you until the needie moves down and up again to its highest point, thus catching the bobbin thread; draw up the needle thread and the bobbin thread will come up with 1t through the hole in the throat plate. Lay both threads back under the presser foot. To Commence Sewing Place the material beneath the presser foot, lower the press- ег foot and commence to sew, turing the machine pulley over to- ward you. | 12 To Turn a Corner Stop the machine while the needle ís rising, but before 1t 1s out of the material, raise the presser foot and turn the work, using the needle as a pivot. To Remove the Work Raise the presser lifter, tum the machine by the machine pulley until the take-up lever 13 at its highest point and draw the work from you. If the threads do not draw out easily, the take-up Lever 18 not in the right position, as directed. If the | machine is stopped as directed, the needle will not be unthreaded in starting to sew, even 1f only a short end is left through the needle. For convenience in taking out the work, the tension of the upper thread is released by raising the presser foot with the lifter; but is not released by thick goods or seams passing under the presser foot. Do not try to adjust the upper tension when the presser lifter is up as the tension is then loose. Causes of the machine not working properly will usually be found in the tension not being correctly adjusted, or its discs may be clogged with lint or knots of thread or the thread con- troller spring may not have the correct tension (this is impor- tant); the thread may be too coarse or too fine for the needle, or the needle and thread too coarse or too fine for the throat plate, or the needle bent or blunt. See that a straight needle {is pushed up in the needle bar as far as it should go; any particle of lint or dirt which prevents it from going up can be removed through the cross hole in the needle bar. To Regulate the Pressure on the Material The pressure of the presser foot on the material should be heavy enough so that the material is fed properly at all speeds. The pressure on the material 18 regulated by the thumb screw (F,Fig.4) at the top of the machine. Loosen the set screw (a, Fig.4) at the back of the machine and turn the thumb screw down- ward for more pressure or upward for less pressure, then tighten the set screw (G,Fig.4). 13 Tensions The needle and bobbin threads should be locked in the centre of the thickness of the material, thus: Y. ‘i Fig. 14. Perfect Stitch If the tension on the needle thread is too tight, or if that on the bobbin thread is too loose, the needle thread will lie straight along the upper surface of the material, thus: an (ee fo À ZA ZA ГИР ez CA | CA | ZA | CZ Fig. 15. Tight Needle Thread Tension If the tension on the bobbin thread is too tight, or if that on the needle thread is too loose, the bobbin thread will lie Straight along the under side of the material thus: Fig. 16, Loose Needle Thread Tension To Regulate the Tensions THE TENSION ON THE NEEDLE THREAD SHOULD ONLY BE REGULATED WHEN THE PRESSER FOOT IS DOWN. Having lowered the presser foot, turn the thumb nut (S,Fig.18) at the front of the tension discs over to the right to increase the tension. To decrease the ten- sion, turn this thumb nut over to the left. The tension on the bobbin thread is regulated by the screw (A,Fig.10) in the tension spring on the outside of the bobbin case. To increase the tension, turn this screw over to the right. To decrease the tension, turn this screw over to the left. When the tension on the bobbin thread has been once properly adjusted, it is seldom necessary to change it, as a correct stitch can usually be obtained by varying the tension on the needle thread, 14 To Regulate the Length of Stitch Press the stitch regulator lever (A, Fig.17) and at the same time tum the machine pulley over toward you until the lever (A) Fig. 17. Stitch Regulator engages the notch in the stitch regulator flange (B, Fig. 17). Continue to hold the lever (A) in the notch in the flange (B) and at the same time turn the machine pulley backward or for ward, as required, until the number of the desired length of stitch 1s opposite the arrow, as shown in Fig. 17, then release the lever (A). To Regulate the Width of Bight The width of bight or zigzag stitch ts regulated by means of the needle vibrator regulating spindle head (A,Fig.2) at the front of the machine. To increase the width of Zigzag stitch, turn the regulating spindle head over to the left. To decrease the width of zigzag stitch, turn the regulating spindle head over to the right. The extreme width of zigzag stitch is 3/16 inch for Machine 143G2, and 5/16 inch for Machine 143G3. 15 INSTRUCTIONS FOR ADJUSTERS AND MECHANICS Thread Controller The function of the thread controller spring (Q,F1g.18) 1s to hold back the slack of the needle thread until the eye of the needle nearly reaches the goods in its descent, as without this controlling action of the spring, the slack thread or silk (more especially silk) will sometimes be penetrated by the point of the needle as the needle is descending. Fig. 18. For more controller action on the thread, loosen the stop screw (U,Fig.18) and set the stop (R) lower. For less action, set the stop higher. The position of the controller spring (Q) shown in Fig. 18 is the best average setting for stitching fine fabrics and light leathers. To strengthen the action of the controller spring on the thread, loosen the tension stud screw (V,Fig.18), and turn the tension stud (T) slightly to the left with a screwdriver. To lighten the spring action, turn the stud to the right, then tighten the tension stud screw (У). 16 To Set the Needle Bar See that the needle is up in the bar as far as it will go. There are two lines 3/32 inch apart across the needle bar about two inches above the lower end. When the needle bar is at its lowest position, the UPPER MARK should be just visible at the lower end of the needle bar frame. vem SS oe ty O E D X Y | Fig. 19. Face Plate Removed In case the needle bar is not correctly set, loosen the needle bar connecting stud set screw (H1,Fig.19) and move the needle bar to the correct position, then tighten the set screw, TO SET A NEEDLE BAR WHICH HAS NO MARK: Set the needle bar so that when 1t rises 3/32 inch from its lowest position, the eye of the needle will be about 1/16 inch below the point of the hook as the hook point enters the thread loop. To Set and Time the Needle Bar Frame First turn the needle vibrator spindle head (A,Fig.2) all the way to the right so that the needle will not vibrate when the ma- chine is running. A straight needle should now come in the cen- tre of the needle hole in the throat plate. If it does not, Loosen the set screw which holds the eccentric stud (K1,Fig.19) and turn the stud (K1) until it does, then tighten the set screw. 17 Now turn the needle vibrator regulating spindle head to the left for the widest throw. Tum the machine pulley toward you until the needle 13 at its lowest position. As the needle bar starts to rise, the needle bar frame should start to move side- wise. If it does not, advance or retard the vibrator gear pin- fon (М, Fig.5). To Remove the Needle Vibrator Gear Shaft Remove the needle vibrator regulating spindle head (A,Fig.2) and the eccentric bracket cover (C,Fig.2); remove the locking and adjusting screws (Al and Bl,Fig.20), also the screw and spring (E1). Loosen the two set screws in the gear (Dl) and remove the needle vibrator gear shaft collar (L,Fig.3) at the back of the arm, then draw the shaft out. When replacing these parts be careful that the large washer (C1,Fig.20) 1s in place between the gear and arm, that the posi- tion screws are set firmly against the flat spots on the shaft and that the set screws are at the right of the position screws when the shaft has been returned to its place. TO SET THE NEEDLE VIBRATOR REGULATING SPINDLE HEAD SO HAT A WIDER THROW THAN THE ONE DESIRED CANNOT BE MADE: E1478 Fig. 20. Transparent View Showing the Needle Vibrator Regulating Spindle Head in Front of Machine Turn the spindle head (A,Fig.2) to make the widest bight possible; remove locking screw (Al,Fig.20) and turn in screw (B1) until the stitch is of the width desired; then turn screw (Al) down tightly on screw (Bl) as a check. The width of stitch may then be decreased by turning the regulating spindle head, but operators cannot make stitches wider than the adjusting screw (Bl) is set to produce. 18 To Time the Sewing Hook Remove the throat plate and with needle vibration at zero, turn the machine pulley over toward you until the LOWER timing mark on the needle bar is Just visible at the end of the needle bar frame (or until the needle bar has risen 3/32 inch); if the needle and hook are in correct time, the potnt of the hook will be opposite the centre of the needle. To time the hook, loosen the set screws in the lower belt pulley (J,Fig.6) and turn the hook as required. Before tighten- ing the set screws, see that there is no end play in the shaft. Fig. 21 To Set the Hook To or From the Needle The point of the hook should come as close as possible to the needle without touching it. Loosen the four screws (X and AA, Fig.21) and slide the hook to the correct position, then tighten the two screws (X). Reset the gear on the hook shaft and tighten screws (AA). | To Remove the Hook Remove the bobbin case stop (Y,Fig.21), loosen the hook spindle screw (W) a few turns and tap it lightly to loosen the hook, Then remove the screw (W) and withdraw the hook from its socket. 19 To Remove the Belt from Within the Arm Slide the arm shaft connection belt off the hook driving - shaft belt pulley (J, Fig.6). and remove the machine pulley. loosen the arm shaft ball bearing bushing (back) set screw (D, Fig.3) at the back of the arm, and remove the bushing; lift the belt up through the arm cap hole as far as possible and draw it out through the space formerly occupied by the bushing. When replacing the belt see that the sewing hook and needle are in correct time before running the belt on the lower pulley and verify the correctness of the timing before commencing to sew. Fig. 22, Putting Belt on Lower Pulley with Belt Replacer 244005 To facilitate the replacing of the belt on the lower pulley, use belt replacer 244005 (A, Fig.22). Rest the replacer in the loop of the belt and slide it over the hub of the pulley, as shown in Fig.22, having the notches in the replacer engage the two set screws in the hub of the pulley. Turn the machine pul- ley toward you until the belt 1s fully over the pulley, then re- move the replacer. | NOTE: As belt replacer 244005 will serve for several machines, it is not regularly furnished with the machine, and must be ordered separately. 20 To Remove the Arm Shaft The Sane | TT Remove the arm shaft connection belt and the machine pulley Loosen the set screws and remove the position screws in the upper belt pulley and the feed lifting eccentric (N,Fig.5). Remove the top and bottom studs (Fl and Li,Fig.19) and the eccentric stud (KL) in the needle bar frame after loosening the set screws which hold them, and remove the needle bar frame. Remove the two gibs (Gl and J1,Fig.19) which hold the needle bar connecting link in the guide block. Loosen the set screw (at H,Fig.3) which holds the take-up lever stud. Also remove the position screw and loos- en the set screw in the perimeter of the needle bar crank,through | | the hole in the casting (B,Fig.2), and remove the take-up and machines... crank. Loosen the set screw (E,Fig.3) which holds the front bushing and withdraw the arm shaft, with the front bushing, from the needle bar end. If the bushing should stick, insert a brass BUY PARTS AND rod through the arm cap hole and drive the bushing out. , NEEDLES MADE BY SINGER Feed Mechanism that are the same as parts in new To take up lost motion of the feed driving and lifting con- TO BE DOUBLY SURE... nections, adjust their pinch screws (0,Fig.5). of new machine performance, make sure that all replacement parts and needles are precisely To prevent the feed dog from striking either end of the slots identical to those in new SINGER machines in the throat plate, loosen screw (K,Fig.6) and move the feed dog forward or backward until the longest stitch can be taken without the feed dog striking the throat plate, then tighten the screw | Look for the trademark (K). . To Raise or Lower the Feed Dog . SINGER or SIMANCO Usually when at its highest position, the feed dog should | show a full tooth above the throat plate. | о оп every package or container Remove the throat plate; clean the lint and dirt from be- 8 on the needle or numbered part tween the feed points and replace the throat plate; tip the ma- chine back and turn the machine pulley toward you until the feed dog 1s at its highest position; loosen screw (7, Fig. 21) and Needles in containers marked “For Singer Machines” are NOT made by SINGER, ralse or lower the feed dog as required, then tignten the screw | TO ALL WHOM IT MAY CONCERN: 2). | (2) : The improper placing or renewal of the Trademark “SINGER or Loosen the two screws (CC,Fig.21) and turn the eccentric stud any other of the Trademarks of The Singer Company (all of which are (BB, Fig .21) to level the feed dog, then tighten the screws (CC) . duly Registered Trademarks) on any machine that has been repaired, re - built, reconditioned, or altered in any way whatsoever outside a SINGER factory or an authorized SINGER agency is forbidden.
advertisement
Related manuals
advertisement