Bennett 3711, 3712, 3724, 3811, 3812, 3912, 3922, 3924 Quick Install Manual
Add to My manuals18 Pages
Bennett 3712 is a versatile electronic dispenser designed for high-volume fueling applications. With its advanced features and robust construction, it is ideal for use in commercial fueling stations, fleet operations, and other demanding environments. The 3712 offers a wide range of options to meet your specific needs, including multiple hose configurations, flow rates, and protocols. Its user-friendly interface and advanced diagnostic capabilities make it easy to operate and maintain.
advertisement
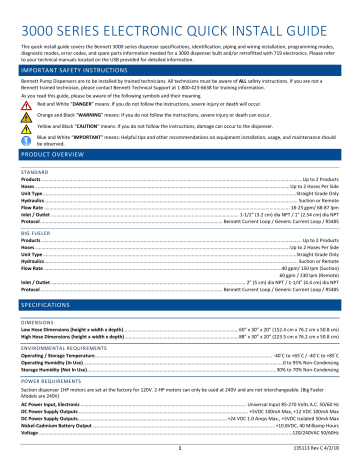
3000 SERIES ELECTRONIC QUICK INSTALL GUIDE
This quick install guide covers the Bennett 3000 series dispenser specifications, identification, piping and wiring installation, programming modes, diagnostic modes, error codes, and spare parts information needed for a 3000 dispenser built and/or retrofitted with 719 electronics. Please refer to your technical manuals located on the USB provided for detailed information.
IMPORTANT SAFETY INSTRUCTIONS
Bennett Pump Dispensers are to be installed by trained technicians. All technicians must be aware of ALL safety instructions. If you are not a
Bennett trained technician, please contact Bennett Technical Support at 1-800-423-6638 for training information.
As you read this guide, please be aware of the following symbols and their meaning.
Red and White “ DANGER ” means: If you do not follow the instructions, severe injury or death will occur.
Orange and Black “ WARNING ” means: If you do not follow the instructions, severe injury or death can occur.
Yellow and Black “ CAUTION ” means: If you do not follow the instructions, damage can occur to the dispenser.
Blue and White “ IMPORTANT ” means: Helpful tips and other recommendations on equipment installation, usage, and maintenance should be observed.
PRODUCT OVERVIEW
STANDARD
Products .................................................................................................................................................................................................. Up to 2 Products
Hoses .............................................................................................................................................................................................. Up to 2 Hoses Per Side
Unit Type ............................................................................................................................................................................................. Straight Grade Only
Hydraulics ............................................................................................................................................................................................. Suction or Remote
Flow Rate ....................................................................................................................................................................................... 18-23 gpm/ 68-87 lpm
Inlet / Outlet ............................................................................................................................................ 1-1/2” (3.2 cm) dia NPT / 1” (2.54 cm) dia NPT
Protocol ........................................................................................................................................ Bennett Current Loop / Generic Current Loop / RS485
BIG FUELER
Products .................................................................................................................................................................................................. Up to 2 Products
Hoses .............................................................................................................................................................................................. Up to 2 Hoses Per Side
Unit Type ............................................................................................................................................................................................. Straight Grade Only
Hydraulics ............................................................................................................................................................................................. Suction or Remote
Flow Rate .................................................................................................................................................................................40 gpm/ 150 lpm (Suction)
60 gpm / 230 lpm (Remote)
Inlet / Outlet ................................................................................................................................................. 2” (5 cm) dia NPT / 1-1/4” (4.4 cm) dia NPT
Protocol ........................................................................................................................................ Bennett Current Loop / Generic Current Loop / RS485
SPECIFICATIONS
DIMENSIONS
Low Hose Dimensions (height x width x depth) ...................................................................................... 60" x 30” x 20” (152.4 cm x 76.2 cm x 50.8 cm)
High Hose Dimensions (height x width x depth) ..................................................................................... 88” x 30” x 20” (223.5 cm x 76.2 cm x 50.8 cm)
ENVIRONMENTAL REQUIR EMENTS
Operating / Storage Temperature .................................................................................................................................... -40
C to +65
C / -40
C to +85
C
Operating Humidity (In Use) ..................................................................................................................................................... 0 to 95% Non-Condensing
Storage Humidity (Not In Use) ............................................................................................................................................. 30% to 70% Non-Condensing
POWER REQUIREMENTS
Suction dispenser 1HP motors are set at the factory for 120V. 2-HP motors can only be used at 240V and are not interchangeable. (Big Fueler
Models are 240V)
AC Power Input, Electronic ............................................................................................................................ Universal Input 85-270 Volts A.C. 50/60 Hz
DC Power Supply Outputs ............................................................................................................................... +5VDC 100mA Max, +12 VDC 100mA Max
DC Power Supply Outputs ............................................................................................................... +24 VDC 1.0 Amps Max., +5VDC Isolated 50mA Max
Nickel-Cadmium Battery Output ........................................................................................................................................ +10.8VDC, 40 Milliamp Hours
Voltage ............................................................................................................................................................................................. 120/240VAC 50/60Hz
1 135113 Rev C 4/2/18
STEP 1
- D
ISPENSER
I
DENTIFICATION
N
UMBER (DIN)
Identifying the features of the unit prior to installation will provide an understanding of how to perform an accurate installation. Follow the steps below to determine what type of 3000 Series Electronic Dispenser you are installing.
DIN numbers are used to identify what type of dispenser or pump is being used and options used. Determine the model number of the dispenser from the serial label located on Side 1 of the dispenser. Use the charts below to determine the features of the dispenser to be installed. Note: The letter X denotes options not identified.
EXAMPLE:
3 X X X S N R – X X X X 2
3000 SERIES ELECTRONIC STANDARD SPEC 300
Position Description
Field 1 Dispenser Series
Field 2 Computer 7 = Commercial Electronic
8 = Retail Electronics (1-Tier Pricing)
Field 3 Number of Products
9 = Retail Electronics (2-Tier Pricing)
1 or 2
Field 4 Number of Hose Outlets 1, 2, or 4
Field 5 Flow Rate
Field 6 Hydraulic Details
S = Standard 18gpm
N = None
Field 7 Hydraulics
Field 12 Fueling Positions
Options
3000 Series
R = Remote
S = Suction
P = Suction with Prepay Valve(s)
1 = One Side
2 = Two Sides and 4 Hose Quads
4 = 4 Hose Active 4 Units
3000 SERIES ELECTRONIC BIG FUEL ER SPEC 300
Position Description Options
Field 1
Field 2
Dispenser Series
Computer
3000 Series
7 = Commercial Electronic
8 = Retail Electronics (1-Tier Pricing)
Field 3 Number of Products
9 = Retail Electronics (2-Tier Pricing)
1 , 2, or 4
Field 4 Number of Hose Outlets 1 or 2 for Side Mount Nozzle Boots
Field 5 Flow Rate
Field 6 Hydraulic Details
1, 2, or 4 for Front Mount Nozzle Boots
B = Big Fueler
Remote Dispensers
M = Master
S = Satellite
Field 7 Hydraulics
C = Combo
D = Combo with Satellite In Use Light
L = Master with In Use Light
Suction Pumps
M = Master
L = Master with In Use Light
R = Remote (60 gpm)
S = Suction (40 gpm)
Field 12 Fueling Position 1 = 1 Side
2 = 2 Sides
Example
3
X
X
X
S
N
R
2
Example
3
X
X
X
B
M
R
4
2 135113 Rev C 4/2/18
STEP 2 – DETERMINE SIDE 1 AND SIDE 2 OF THE UNIT
Before placing, the unit onto the island verify the proper orientation and product pipe location of the unit. A common error is placing the unit on the island backwards resulting in a longer installation time.
Side 1 of the dispenser has the Battery located on the left hand side. The optional junction box is also located on Side 1 in the lower (hydraulics) area.
STEP 3 –DETERMINE THE TYPE OF DISPENSER SUMP
Before placing a 3000 Series Electronic Dispenser onto an island, determine what type of dispenser sump is used and follow the original manufacturer’s installation instructions. Review the Bennett 3000 Series Electronic Dispenser Footprint for your unit and get the measurements of the existing or new dispenser sump to determine if any adjustments are needed prior to mounting the unit onto the island.
BENNETT RECOMMENDED DISPENSER SUMPS FOR THE 3000 SERIES ELECTRONIC DISPENSER
OPW
DS-1229
DSF-1229
DP1123
FRANKLIN FUELING
LM(M/D) 2313-T
LM(M/D) 1811
STEP 4 – DISPENSER BASE (PRODUCT PIPING)
Refer to the section below to determine the product piping required for your dispenser.
Step 1 : Determine the type of supply line needed from the model number’s 7th position on the serial label.
R = Remote Dispensers will require a submerged pump and pressurized supply line for each product.
S = Suction Pumps will require a suction supply line for each product.
Step 2: Determine the number of product pipes required by finding the model number below.
Model No. Product Supply Lines Required
3711 / 3811 / 3911 Use 1 product line plumbed to position 1
3712 / 3812 / 3912 Use 1 product line plumbed to position 1
3722 / 3822 / 3922 Use 1 product line plumbed to position 1 and 1 product line plumbed to position 2
3724 / 3824 / 3924 Use 1 product line plumbed to position 1 and 1 product line plumbed to position 2
3 135113 Rev C 4/2/18
STANDARD MODELS
The following Inlets and Outlets sizes are used for Standard models.
Pump Inside Dispenser Sump (Opening) 13“ x 30” (33 cm x 76 cm)
Product Inlets (Female)
Satellite Outlets (Female)
Hose Outlets
1-1/2” (3.8 cm) NPT
1” (2.54 cm) NPT
1” (2.54 cm) NPT
CAUTION : Dispensers must be installed with provisions for expansion relief, which will relieve at pressures not to exceed 50 psi (345 mPA). Do not use line check valve between dispenser and tank unless provided with relief valve.
BIG FUELER MODELS
The following Inlets and Outlets sizes are used for Big Fueler models.
Pump Inside Dispenser Sump (Opening) 13“ x 30” (33 cm x 76 cm)
Master Inlets (Female)
Satellite Inlets (Female)
Satellite Outlets (Female)
2” (5.08 cm) NPT
1-1/2” (3.8 cm ) NPT
1-1/2” (3.8 cm ) NPT
STEP 5 – FIND FOOTPRINT
Use the chart below to determine what footprint to use for your model number. Note: The letter X denotes options not identified.
3000 SERIES ELECTRONIC STANDARD
Model Number
3XXXSNR
3XXXSNS
3XXXSNR-XXXX2
3XXXSNR-XXXXA
3XXXSNS-XXXX2
Part # Drawing # Description
135103 P5300 3700, 3800, 3900 Models | High Hose and Low Hose | Standard Flow Rates | Remote
135104 P5301 3700, 3800, 3900 Models | High Hose and Low Hose | Standard Flow Rates | Suction
135105
135106
P5302
P5303
3700, 3800, 3900 Models | High Hose | Standard Flow Rates | Remote | Quad or Active 4
3700, 3800, 3900 Models | High Hose | Standard Flow Rates| Suction | Quad
3000 SERIES ELECTRONIC BIG FUELER
Model Number
3XXXBMR /
3XXXBCR
3XXXBSR
3XXXBMS
3XXXBMR
3XXXBSR
3XXXBCR
Part # Drawing # Description
135107 P5304 3700, 3800, 3900 Models | Low Hose | Remote | Master / Combo | High Flow Big Fueler
135108 P5305
135109 P5306
135110 P5307
135111 P5308
135112 P5309
3700, 3800, 3900 Models | Low Hose | Remote | Satellite | High Flow Big Fueler
3700, 3800, 3900 Models | High Hose and Low Hose | Suction | High Flow Big Fueler
3700, 3800, 3900 Models | High Hose | Master | Remote | High Flow Big Fueler
3700, 3800, 3900 Models | High Hose | Satellite | Remote| High Flow Big Fueler
3700, 3800, 3900 Models | High Hose | Combo | Remote | High Flow Big Fueler
STEP 6 – ANCHORING THE DISPENSER TO THE ISLAND
The dispenser must be bolted firmly to the concrete island. The dispenser base is provided with anchor bolt holes refer to the footprint drawing for dimensions. Anchor bolts embedded in the concrete island must be no less than ½” (1.3 cm) diameter. The threaded ends of the anchor bolts should project 1-1/2” (3.8 cm) above the concrete.
On the Low Hose dispenser, 2 anchor bolts required minimum.
On the High Hose dispenser, 4 anchor bolts required minimum in the outer 4 mounting holes.
Refer to the Footprint Drawing used for your dispenser model.
When anchoring the dispenser, always level the dispenser with metal shims before bolting to the island. Place the metal shims at the location of the anchor bolts so the dispenser frame is not distorted when the anchor bolts are tightened down. Improper shimming that result in misaligned frames is NOT covered under the Bennett Limited Warranty!
STEP 7 – PREPARING FIELD WIRING
The dispenser’s field wiring connections are in the upper electronics head (electrical enclosure) of the dispenser or in the lower area of the dispenser if the unit was ordered with the optional explosion proof junction box. Pull 72” (182.9 cm) extra wire to reach the top of the dispenser.
Note: All field wiring must be stranded copper, oil and gas resistant (THHN) color coded, with a 600-volt insulation rating. See wiring diagrams for proper wire sizes. DO NOT use wire nuts. The ends of the wires should be clean and free from oxidation
1.
Using the door keys shipped with the dispenser, (on side 1) unlock the two locks on the lower door and/or upper door panel of the electronics enclosure, and open the door.
2.
Pull the dispenser wires through the underground conduit and through the primary or optional secondary conduit locations located on the vapor deck and terminate wires according to the wiring diagrams provided in the upper electronic enclosure.
3.
If there is an optional junction box, follow the wiring diagrams provided in the upper electronics enclosure and wire to the terminal strip and flying leads in the junction box.
4.
Make sure that the copper ends of the wires are clean and free of oxidation.
4 135113 Rev C 4/2/18
STEP 8 - FIELD WIRING
Follow the sections below for proper equipment grounding, dispenser AC power, and console communication. The 3k dispenser can be ordered as a one or two hose unit. Note: 1, 2, or 4 hose units have one CPU board an Active 4 unit will have two CPU boards. The CPU board is where the field wires will connect if the optional junction box is not ordered.
PROPER EQUIPMENT GRO UNDING
Grounding provides a path of least resistance for electric current to reduce the risk of electric shock. Grounding is also required to protect the dispenser’s computer from external electrical noise generating devices. The ground wire connection must provide 1 ohm (or less) resistance to earth ground.
1.
Connect a 12-gauge (minimum), green or green/yellow stranded wire to the grounding terminal on the electronics enclosure deck. Only one ground wire is required per dispenser.
2.
Pull a continuous (one-piece) green or green/yellow, 12 gauge stranded THHN ground wire through the junction box and 3/4” (1.9 cm) conduit and secure at ground lug near the terminal strip in the dispenser’s Junction Box. Terminate the other end at the main panel breaker box ground bar. Do not terminate at the neutral bar of a sub-panel or rely on metal conduit for this ground connection.
Each dispenser’s grounding post must be within 1-ohm resistance to earth ground potential. You must verify to within 1 ohm of the ground rod. Do not use wire nuts on ground circuits, use only compression type connectors. This is required to initiate Bennett’s Limited Warranty.
DISPENSER AC POWER
Each dispenser uses one 120V, 50/60 Hz, or 240V, 50/60 Hz circuit for dispenser power. Make sure the power source has the correct frequency and voltage. Connect the electrical circuit to the terminal strip on the CPU board. Only one dispenser electronics Hot and Neutral needs to be pulled per dispenser.
WARNING: ALL DISPENSER AC POWER CIRCUITS (FOR REMOTES ONLY) MUST BE ON THE SAME PHASE OR DAMAGE WILL OCCUR TO
THE DISPENSER 719 CPU OR THE SUB-PUMP RELAY BOX.
Qty Description Connect To Connector Connect To Connector
1 Green or Green/Yellow #12 Wire - Ground
White #14 Wire - 120V Neutral Electronics Power
1 OR
Red #14 Wire - 240V L2 Electronics Power
1 Black #14 Wire – L1 Electronics Power
Chassis
719 CPU
Ground Lug
Terminal 2, TS2
OR
Junction Box
Junction Box
Ground Lug
Terminal 1
719 CPU Terminal 3, TS2 Junction Box Terminal 2
1.
Connect the White (Neutral) 14ga. wire in 120V circuits or the Red 14ga. wire in 240V circuits to terminal 2 of TS2 on the CPU board. The CPU board is located on the upper electronics deck.
2.
Connect the Black (Hot) 14ga. wire to terminal 3 of TS2 on the CPU board.
3.
Electronic power must be connected to a dedicated 15-amp neutral breaking circuit breaker. Electronic power for all dispensers at an installation must be wired to the same AC line phase or damage from cross phasing will result in the remote sub-pump relay control circuits.
CONSOLE COMMUNICATIO N
A specific Personality Module is needed for the Current Loop Communication, Generic Current Loop Communication, RS-485 Communication, and
Pulse Output for Fleet Management. The dispenser MUST have the correct module for the dispenser to communicate properly. Refer to the sections below for detailed instructions.
PERSONALITY MODULES PART #
Generic Current Loop and Bennett Current Loop 121982
RS-485 121992
Pulse Output Board 131480
BENNETT CURRENT LOOP FUEL COMMUNICATION (121982)
To be used with Bennett 515 Box, TMX, Comdata, FIS-CAL, VeriFone Commander, Ruby, and Sapphire remote consoles. Bennett Current Loop uses a 4-wire protocol.
Use the table below to determine how many wires your communication console requires and the connection points for this type of communication. Note: Connections will vary depending on the dispenser model and options.
1-SIDED DISPENSER COMMUNICATION = 2 FIELD WIRES (REQUIRED)
Qty
1
1
Description
Orange #18 Wire - Bennett Current Loop Communication (+positive)
Yellow #18 Wire - Bennett Current Loop Communication (-negative)
To Board
Current Loop Personality Module
To Connector
TS1, Terminal 1
Current Loop Personality Module TS1, Terminal 2
5 135113 Rev C 4/2/18
2-SIDED DISPENSER COMMUNICATION = 4 FIELD WIRES (REQUIRED)
Qty Description To Board To Connector
1 Orange #18 Wire - Bennett Current Loop Communication (+ positive) Current Loop Personality Module TS1, Terminal 1
1 Yellow #18 Wire - Bennett Current Loop Communication (- negative) Current Loop Personality Module TS1, Terminal 2
1 Orange #18 Wire - Bennett Current Loop Communication (+ positive) Current Loop Personality Module TS2, Terminal 1
1 Yellow #18 Wire - Bennett Current Loop Communication (- negative) Current Loop Personality Module TS2, Terminal 2
GENERIC CURRENT LOOP FUEL COMMUNICATION (121982)
To be used with Gilbarco Passport, VeriFone Commander, Wayne Fusion, and Wayne Nucleus remote consoles. Generic Current Loop uses a 2-wire protocol. Note: Refer to the wiring diagram included in the dispenser for wire, shunts, and field jumper wire connections.
Use the tables below to determine how many wires your communication console requires for this type of communication. Note: Connections will vary depending on the dispenser model and options.
1-SIDED DISPENSER COMMUNICATION = 2 FIELD WIRES AND 1 SHUNT (REQUIRED)
Qty Description To Board To Connector
1 Orange #18 Wire – Generic Current Loop Communication (+ positive) Current Loop Personality Module TS1, Terminal 1
1 Yellow #18 Wire – Generic Current Loop Communication (- negative) Current Loop Personality Module TS1, Terminal 2
1 Shunt Current Loop Personality Module Top 2 Pins at JP1
2-SIDED DISPENSER COMMUNICATION = 2 FIELD WIRES, 1 FIELD JUMPER, AND 2 SHUNTS (REQUIRED)
Qty Description To Board To Connector
1 Orange #18 Wire – Generic Current Loop Communication (+ positive) Current Loop Personality Module TS1, Terminal 1
1 Field Jumper Wire Current Loop Personality Module TS1, Terminal 2 to TS2,
Terminal 1
1 Yellow #18 Wire - Generic Current Loop Communication (- negative)
2 Shunt (All POS systems except Excentus)
2 Shunt (Use only if an Excentus POS system is used)
Current Loop Personality Module
Current Loop Personality Module
Current Loop Personality Module
TS2, Terminal 2
Top 2 Pins at JP1 and JP2
Bottom 2 pins at JP1 and
JP2
RS485 RETAIL & RS485 FLEET FUEL COMMUNICATION (121992)
To be used with Allied NeXGen remote consoles for retail communication or a fleet management system for commercial use. The RS485 uses a 2wire protocol. RS485 wires should be twisted together no less than 3 turns per foot to reduce the effects of electrical noise on the communication circuit. Bennett highly recommends the use of twisted wires. Note: Belden shielded cable is accepted but the “drain” must not be terminated.
RS485 RETAIL 1-SIDED DISPENSER COMMUNICATION = 2 FIELD WIRES
Qty Description
1 Orange #18 Wire - RS485 Communication (+ positive)
1 Brown #18 Wire - RS485 Communication (- negative)
To Board
RS485 Personality Module
RS485 Personality Module
To Connector
TS1, Terminal 1
TS1, Terminal 3
RS485 FLEET 1-SIDED DISPENSER COMMUNICATION = 2 FIELD WIRES
Qty Description
1 Orange #18 Wire - RS485 Communication (+ positive)
1 Brown #18 Wire - RS485 Communication (- negative)
To Board
RS485 Personality Module
RS485 Personality Module
CARD READER COMMUNIC ATION (OPTIONAL)
To Connector
TS2, Terminal 1
TS2, Terminal 3
Bennett Dispensers can interface with many POS terminals as well as site controllers. Refer to the sections below to determine what type of communication is used and what fueling controller is needed for communication.
CARD READER COMMUNICATION
RS485
Ethernet 2-Wire – *COMING SOON*
CAT5e – *COMING SOON*
Field installed communication wires located inside the electrical enclosure of the unit cannot be loose and must be tightly held in place by fasteners. RS485 wires should be twisted together no less than 3 turns per foot to reduce the effects of electrical noise on the communication circuit. Due to the risk of noise causing possible problems with communication, Bennett highly recommends the use of twisted wires. Note : Belden shielded cable is accepted but the “drain” must not be terminated.
Qty Description
1 Violet #18 Wire - RS485 Communication (+ positive)
1 Yellow #18 Wire - RS485 Communication (- negative)
To Board To Connector
Bennett SPM/SSP Payment System RS485 Data (+ positive)
Bennett SPM/SSP Payment System RS485 Data (- negative)
6 135113 Rev C 4/2/18
PUMP MOTOR POWER
The Submerged Pump Relay Control Signals are rated at 30 watts, 120VAC, or 240VAC maximum. This signal must be wired to an external
Submerged Pump Relay (with all coil control wires for this relay on the same AC phase) for controlling the submerged pump motors. Use Red Jacket or FE Petrol Control Box or equivalent.
REMOTE DISPENSERS PUMP MOTOR P OWER (135047)
A remote relay control wire will be required for each plumbed product. If there is only one product, only one submerged pump control wire is needed. If there is a second product, a second submerged pump control wire will be needed. Note: Jumpers are factory supplied and installed.
Description
Blue #14 Wire - Product “A” Hose Position
Brown #14 Wire - Product “B” Hose Position
Jumper Wire (Factory Supplied & Installed)
Qty
1
1
2
1.
Connect the Blue 14ga. wire to the 719 CPU Board at TS2 Terminal 2 or to the optional Junction Box at Terminal 3 as indicated in the diagram.
Connect the other end to the Submerged Pump Control Relay Box for Product A.
2.
Connect the Brown 14ga. wire to the 719 CPU Board at TS2 Terminal 3 or to the optional Junction Box at Terminal 4 as indicated in the diagram. Connect the other end to the Submerged Pump Control Relay Box for Product B.
3.
Place 1 blue jumper between P1 to P3 on the 719 CPU and 1 brown jumper between P2 to P4 on the 719 CPU.
SUCTION PUMP MOTOR RELAY
A separate circuit and circuit breaker will be required for each pumping unit motor. Place the pumping unit motor power circuit breakers on the opposite phase from the dispenser’s electronic power or on 240VAC. This will keep the dispenser’s electronic power free from electronic noise. The dispenser may have one motor (single product) or two motors (dual product). Each motor requires two or three field wires.
3-PHASE (380VAC) MOTOR A RELAY CONNECTION – PRODUCT A (135049)
Use a 15 AMP 3-phase circuit breaker (CB#2), which is supplied by the customer. Note: No more than 2 pumps per breaker.
Qty Description
1 Brown #14 – Product “A” Motor Control
1 Orange #14 – Product “A” Motor Control
1 Yellow #14 – Product “A” Motor Control
From
Circuit Breaker #2 – L1
Circuit Breaker #2 – L2
Circuit Breaker #2 – L3
To
Motor A Relay
Motor A Relay
Motor A Relay
To Connector
TS2, L1
TS2, L2
TS2, L3
3-PHASE (380VAC) MOTOR B RELAY CONNECTION – PRODUCT B (135049)
Use a 15 AMP 3 phase circuit breaker (CB#2), which is supplied by the customer. Note: No more than 2 pumps per breaker.
Qty Description
1 Brown #14 – Product “B” Motor Control
1 Orange #14 – Product “B” Motor Control
1 Yellow #14 – Product “B” Motor Control
From
Circuit Breaker #2 – L1
Circuit Breaker #2 – L2
Circuit Breaker #2 – L3
To
Motor B Relay
Motor B Relay
Motor B Relay
To Connector
TS2, L1
TS2, L2
TS2, L3
STANDARD SINGLE PHASE (120/240VAC) MOTOR A RELAY CONNECTION – PRODUCT A (135050)
Use a 15 AMP neutral breaking circuit breaker (CB#2), which is supplied by the customer. Note: No more than 2 pumps per breaker.
Qty Description
1 Blue #14 – Product “A” Motor Control
1 White #14 – Product “A” Motor Control
From To
Circuit Breaker #2 – L1 719 CPU
Circuit Breaker #2 – Neutral Motor A
To Connector
TS2, Terminal 1
N/A
STANDARD SINGLE-PHASE (120/240VAC) MOTOR B RELAY CONNECTION – PRODUCT B (135050)
Use a 15 AMP neutral breaking circuit breaker (CB#3), which is supplied by the customer. Note: No more than 2 pumps per breaker.
Qty Description
1 Red #14 – Product “B” Motor Control
1 White #14 – Product “B” Motor Control
From
Circuit Breaker #3 – L2
To
719 CPU
Circuit Breaker #3 – Neutral Motor B
To Connector
TS2, Terminal 3
N/A
BIG FUELER SINGLE PHASE (240VAC) MOTOR A RELAY CONNECTION – PRODUCT A (135085)
Qty Description
1 Blue #14 – Product “A” Motor Control
1 White #14 – Product “A” Motor Control
From
Circuit Breaker #2 – L1
Circuit Breaker #2 – L2
To
Motor A Relay
Motor A Relay
BIG FUELER SINGLE-PHASE (240VAC) MOTOR B RELAY CONNECTION – PRODUCT B (135085)
Qty Description
1 Red #14 – Product “B” Motor Control
1 White #14 – Product “B” Motor Control
From
Circuit Breaker #2 – L1
Circuit Breaker #2 – L2
To
Motor B Relay
Motor B Relay
7
To Connector
TS2, L1
TS2, L2
To Connector
TS2, L1
TS2, L2
135113 Rev C 4/2/18
INTERCOM SYSTEMS (OP TIONAL)
Intercom wiring must be in a separate conduit from the dispenser conduit. DO NOT install intercom wiring in the same conduit as the dispenser wiring or else the Bennett Warranty will be voided and improper system operation will result. If the dispenser is ordered with an intercom (speaker and call button), the Installer must pull wires for it.
Qty Description
2 #18 Wire - Speaker Wires
2 #18 Wire - Call Button (optional)
MECHANICAL PULSE OUT PUT 131480 (OPTIONAL)
The field wiring will be connected between a Bennett Pulse Output Board and the third party interface system. This board is mounted on the 719
CPU inside the electronics enclosure. One Pulse Output Board can handle up to two hoses (products). Note: Active 4 units can use two Pulse
Output Boards. Follow the recommended color-coding for field wires found on the Pulse Output Wiring Diagram (Part # 135046).
Qty Description
2 #18 Wire - Pulse Output Wires per CPU/Control Board (+) & (-)
2 #18 Wire - Pulse Output Wires per CPU/Control Board for Tank Gauge Interface (+) & (-)
2 #18 Wire - Handle Circuit Wires per CPU / Control Board (+) & (-)
1 #18 Wire - Authorization Wires per CPU / Control Board (+) & (-)
Used with Electronic Dispenser Models 3 X 11, 3 X 12, and 3 X 22 where X is 7, 8, or 9.
The pulse output board connects to the 719 CPU on connector J7. It supports up to two fueling positions on the single RS485 connection. The pulse output board interfaces with the fleet system using three signals. Refer to the programming section earlier in this manual to configure Pulse Type,
Pulse Period, and Pulse Resolution.
1.
Pulse Output – The pulse output allows the 3000 Series Mechanical interface to send pulse information to the Console and the Tank
Gauge. The system can be programmed to output pulse ratio from 1:1. 10:1. 100:1, and 1000:1. The fleet system and tank gauge connected to the dispenser must provide 5 – 12 volts DC for the pulse output channel. Refer to the Programming Section to for pulse output configuration.
2.
Handle Switch Signal – The handle switch is a 120-240-volt signal can be used to signal the console that the pump is “IN USE”. Some fleet systems require this signal and some do not.
3.
Authorization Signal – A fleet system can send authorization to a fueling point via a 120/240-volt signal that allows the fueling point to reset at the beginning of the sale. Without this signal, the dispenser will not reset when in the “Mechanical” mode.
Use the tables on the following pages to determine how many wires your communication console requires for this type of communication. Note :
Wiring may connect directly to the Pulse Output Personality Module or to the optional Junction Box. Terminal locations are different, please verify before wiring or the dispenser will not work properly if wired incorrectly. Refer to the wiring diagrams for detailed wiring information.
1 PRODUCT CONNECTION 8 FIELD WIRES REQUIR ED (135046)
DIRECT PULSE OUTPUT BOARD WIRING
Wiring is to be connected directly to the Pulse Output Board.
Qty Description
1 (Controller) Pulse Out (+positive)
1 (Controller) Pulse Out (- negative)
1 (Tank Gauge) Pulse Out (+ positive)
1 (Tank Gauge) Pulse Out (- negative)
1 (Source) In-Use Product 1
1 (Signal) In-Use Product 1
1 Authorize Signal Product 1
1 Authorize Neutral Product 1 Note: The Authorization’s Neutral for
Product 1 is jumpered to Product 2’s jumper.
OPTIONAL JUNCTION BOX WIRING
Wiring is to be connected to the terminal strip inside the optional junction box.
Qty Description
1 (Controller) Pulse Out (+positive)
1 (Controller) Pulse Out (- negative)
1 (Tank Gauge) Pulse Out (+ positive)
1 (Tank Gauge) Pulse Out (- negative)
1 (Source) In-Use Product 1
1 (Signal) In-Use Product 1
1 Authorize Signal Product 1
1 Authorize Neutral Product 1
Size
#18
#18
#18
#18
#18
#18
#18
#18
Size
#18
#18
#18
#18
#18
#18
#18
#18
Wire Color To Board
Red Pulse Output Board
To Terminal
1
Blue
Brown
Pink
Orange
Yellow
Black
White
Red
Blue
Brown
Pink
Orange
Yellow
Black
White
Pulse Output Board
Pulse Output Board
Pulse Output Board
Pulse Output Board
Pulse Output Board
Pulse Output Board
Pulse Output Board
Wire Color To Board
Junction Box
Junction Box
Junction Box
Junction Box
Junction Box
Junction Box
Junction Box
Junction Box
2
3
4
9
10
13
14
To Terminal
5
6
7
8
13
14
17
19
8 135113 Rev C 4/2/18
2 PRODUCT CONNECTION (135046)
16 Field Wires Required
DIRECT PULSE OUTPUT BOARD WIRING
Wiring is to be connected directly to the Pulse Output Board.
Qty
1
1
1
1
Description
(Controller) Pulse Out (+) Product 1
1 (Controller) Pulse Out (-) Product 1
1 (Tank Gauge) Pulse Out (+) Product 1
1 (Tank Gauge) Pulse Out (-) Product 1
1 (Controller) Pulse Out (+) Product 2
1 (Controller) Pulse Out (-) Product 2
1 (Tank Gauge) Pulse Out (+) Product 2
1 (Tank Gauge) Pulse Out (-) Product 2
1 (Source) In-Use Product 1
1 (Signal) In-Use Product 1
1 (Source) In-Use Product 2
1 (Signal) In-Use Product 2
1 Authorize Signal Product 1
Authorize Neutral Product 1
Authorize Signal Product 2
Authorize Neutral Product 2
Size Wire Color
#18 Red
#18
#18
#18
#18
#18
#18
#18
#18
#18
#18
#18
#18
#18
#18
#18
Blue
Brown
Pink
Red
Blue
Brown
Pink
Orange
Yellow
Black
White
Black
White
Gray
White
To Board
Pulse Output Board
Pulse Output Board
Pulse Output Board
Pulse Output Board
Pulse Output Board
Pulse Output Board
Pulse Output Board
Pulse Output Board
Pulse Output Board
Pulse Output Board
Pulse Output Board
Pulse Output Board
Pulse Output Board
Pulse Output Board
Pulse Output Board
Pulse Output Board
To Terminal
1
2
3
4
5
6
7
8
9
10
11
12
13
14
15
16
OPTIONAL JUNCTION BOX WIRING
Wiring is to be connected to the terminal strip inside the optional junction box.
Qty
1
1
1
1
Description
(Controller) Pulse Out (+) Product 1
(Controller) Pulse Out (-) Product 1
(Tank Gauge) Pulse Out (+) Product 1
(Tank Gauge) Pulse Out (-) Product 1
1 (Controller) Pulse Out (+) Product 2
1 (Controller) Pulse Out (-) Product 2
1 (Tank Gauge) Pulse Out (+) Product 2
1 (Tank Gauge) Pulse Out (-) Product 2
1 (Source) In-Use Product 1
1 (Signal) In-Use Product 1
1 (Source) In-Use Product 2
1 (Signal) In-Use Product 2
1 Authorize Signal Product 1
1 Authorize Signal Product 2
1 Authorize Neutral Product 2
Size Wire Color
#18 Red
#18
#18
#18
Blue
Brown
Pink
#18
#18
#18
#18
#18
#18
#18
#18
#18
#18
#18
Red
Blue
Brown
Pink
Orange
Yellow
Black
White
Black
Gray
White
To Board
Junction Box
Junction Box
Junction Box
Junction Box
Junction Box
Junction Box
Junction Box
Junction Box
Junction Box
Junction Box
Junction Box
Junction Box
Junction Box
Junction Box
Junction Box
To Terminal
5
6
7
8
9
10
11
12
13
14
15
16
17
18
19
2 N D OPTIONAL CONTROLLER
A second optional controller can be used on the RS485 channel. This is used for a Fleet System that uses RS485 for communication and needs the pulse output signal for a Tank Gauge. Note : Field wiring for the second optional controller can be wired directly to the Pulse Output Board or through the optional Junction Box. Use the tables below to determine how many wires your optional controller requires for this type of communication.
The second optional controller connects to the Pulse Output Board Personality Module.
RS485 uses a 2-wire protocol.
PULSE OUTPUT BOARD CONNECTION - 2 FIELD WIRES (REQUIRED)
Qty Description
1 RS485 (+ positive)
1 RS485 (- negative)
Size
#18
#18
Wire Color
Orange
Brown
To Board
Pulse Output Board
Pulse Output Board
To Connection
TS4, Terminal 17
TS4, Terminal 19
OPTIONAL JUNCTION BOX CONNECTION - 2 FIELD WIRES (REQUIRED)
Qty Description
1 RS485 (+ positive)
1 RS485 (- negative)
Size Wire Color
#18 Orange
#18 Brown
To Board
Junction Box
Junction Box
To Connection
Terminal 20
Terminal 21
9 135113 Rev C 4/2/18
STEP 9 - PROGRAMMING AND DIAGNOSTIC MODES
Programming the 3000 series dispenser can be done using the Local Preset option or the Manager’s Keypad.
LOCAL PRESET PROGRAM MING
The Local Preset option can be ordered with any 3000 Series electronic dispenser. The attendant can select volume or currency and preset the amount of fuel for the customer. Note: The Mode , Enter, +/- (plus minus) buttons are not shown on the overlay, but you will be able to feel them.
HIDDEN PROGRAMMING B UTTONS
The Mode button is located to the right of the 0 key and below the 9 key.
The Enter button is located to the right of the Mode .
The +/( plus minus ) button is located to the right of the 9 key.
+/-
MODE ENTER
HOW TO PROGRAM THE DISPENSER USING THE LOCAL PRESET KEY PAD
1.
Make sure the handle for the hose position you want to program is hung up in the Nozzle Boot. If the handle is lifted, the hose position cannot go into Manager Mode.
2.
Press the +/- (plus minus) button and the Enter keys simultaneously and hold until the display shows “ Enter Side 1 ”.
3.
Press 1 to program Side 1 or Press 2 to program Side 2 (if applicable) and press Enter . Once the Enter button is pressed, the display will show
“ Code 00 ”.
4.
The +/- (plus minus) button can be used to toggle through manager mode selections.
5.
Once you are in the Manager Mode, you can program the dispenser as normal. To exit the Manager Mode, press and hold the Cancel and
Enter buttons together until the display returns to the normal sales display.
MANAGER’S KEYPAD PRO GRAMMING
The Manager’s Keypad can be used to program the 3000 series dispenser. Prior to programming, the keypad must be plugged into the 719 CPU, connector J11.
MANAGER’S KEYPAD OVE RVIEW
Use the provided multi-colored wire harness to connect the manager’s keypad to the 719 CPU.
0 - 9 Buttons – Used to enter a numeric value.
Up and Down Arrows – Used to cycle through selections within a mode.
+/ (Plus Minus) Button – Used to cycle through selections within a mode.
Cancel – Used to exit a mode or selection.
Enter – Used to execute a command or to cycle through a selection within a mode.
Mode – Used to enter a managers mode.
HOW TO PROGRAM THE DISPENSER USING THE MANAGER’S KEYPAD
1.
Connect the Manager’s Keypad to connector J11 for programming.
2.
Press the Enter and +/ button simultaneously. After a few seconds, press the Enter button. The display will show “ Enter Side 1 ”.
3.
Press 1 to program Side 1 or Press 2 to program Side 2 (if applicable) and press Enter . Once the Enter button is pressed the display will show
“ Code 00 ”.
4.
Once you are in the Manager’s Mode, you can program the dispenser as normal or run diagnostics.
5.
To exit a Manager’s Mode press the Cancel button until the display returns to the normal sales display.
10 135113 Rev C 4/2/18
SUGGESTED SETUP SEQU ENCE
Make sure the initial setup menu codes are programmed before testing any dispenser operations. Failure to do so may lead to difficulty getting the dispenser to operate properly. See Initial Setup Sequence below.
INITIAL SETUP
Menu Code
3
7
4
21
22
27
Initial Setup
Managers Access Code
Pump Type
Pricing – For each hose and 1 or 2-tier pricing
Communication Type (Current Loop, Stand Alone, RS485, Generic Current Loop, Fleet RS485)
Dispenser Address (Only used for Generic Current Loop & RS485)
Meter (Electronic) Calibration
REMAINING DISPENSER SETUP
Menu Code Remaining Dispenser Setup
20
22
24
28
15
16
17
18
10
11
12
14
5
6
8
9
30
31
37
50
60
70
96
99
Meter Value – Amount for each meter
Programming Selections Viewer
Decimal Location – For other than U.S. Standard
No Flow Time Out ( International Purposes Only)
Slow Flow Amount – Control for Prepay Sales
Volume Allocation for a sale at a pump ( International Purposes Only)
Pre-Charge, Idle, Last Sale, and Handle State Timer
Price Display – Control Operation
Fleet System – Interface Compatibility
Battery Timeout
Local Preset - Operation
Motor Delay – Suction Pumps
Masked Volume
Dispenser Address
Solenoid Valve Type
Rounding or Truncating the Sale Amount ( International Purposes Only)
Real Time Clock (YY/MM/DD/HH:MM)
Total Access
ATC – Petroleum Commodity Group
Pulse Output – Pulse Unit, Pulse Ratio, and Pulse Speed (PPS)
End Condition Prepay Sale
Marina Pulser Enable Delay
Proportional Valve (Start of Sale or End of Prepay / Preset Sale
Unit of Measure - (International Purposes Only)
DEFAULT SETTINGS
The software program for each new dispenser shipped from the factory is pre-programmed with the default settings in some of the Menu Codes.
Some menu codes must be changed immediately to make the dispenser operational. Refer to the Initial Setup table. The default settings are noted below:
Menu Code Description
21
22
24
27
28
31
37
50
14
15
16
17
18
20
9
10
11
12
3
4
7
8
Continued on next page …
Managers Access
Prices
Pump Type
Decimal Location
No Flow Time Out
Slow Flow Amount
Volume Allocation
Submerged Pump, Last Sale, Idle, and Handle State Timer
Price Display
Fleet Option
Battery Timeout
Local Preset
Motor Delay
Masked Volume
Communication Type
Dispenser Address
Solenoid Valve Type
Meter Calibration
Rounding or Truncating Sale Amount
Total Access
ATC Measurement
Pulse Output
Default Settings
2218
0000
Sides = 2, Grades = 1, Hoses = 1, Tier = 1
0 = U.S.A.
--- = Infinite Time
0.100 Volume Unit
0999 Volume Units
Pre-Charge = 2 seconds, Last Sale = 30, Idle = 15, Handle State = 0
0 = Flashing, 0 = Dash, Flip = 0
0 = No Fleet Interface
30 Seconds
0 = No Preset
0 = No Delay
.010 gallons or .10 liters
0 = Console Mode
0 = Only one dispenser on the communications loop
2 = Proportional Valve
0.00
1 = Rounding the Sale Amount
1 = Access allowed without manager password
0 = Long
0 = Disabled
11 135113 Rev C 4/2/18
Menu Code Description
60
70
96
99
End Condition Prepay Sale
Marina Pulser Enable Delay
Proportional Valve
Unit of Measure / Dispenser Model
Default
0 = Cash Drawer
0 Seconds
Start of Sale = 35 percent, End of Prepay Sale = 35 percent
1 = Gallons, 1 – Decimal position 3 places
STEP 10 - DISPENSER START-UP AND CHECKLIST
DANGER:
CAUTION:
FIRE, EXPLOSION, INJURY OR DEATH WILL OCCUR IF FUEL VAPORS ARE PRESENT. MAKE SURE THERE ARE NO VAPORS
PRESENT BEFORE STARTING THIS PROCEDURE.
TO PREVENT DAMAGE TO THE DISPENSER, FOLLOW THE PROPER START-UP PROCEDURES.
Before applying AC power to the dispenser, follow this procedure:
1.
Unlock and open the upper and lower dispenser doors.
2.
Check to make sure:
The boards and other components have not come loose from shipping and LCD display boards are not cracked or damaged.
The cables are properly connected to the boards. There are no torn cables or stranded harnesses.
Pulser and pump handle harnesses are connected properly to the CPU board.
3.
Make sure the shut off valves are closed.
4.
Turn off all submerged pump circuit breakers and all other circuit breakers to the dispenser.
Make sure the 12-gauge green or green/yellow ground wire is properly connected and measures 1 ohm (or less) resistance to earth ground. This measurement should be taken between neutral and ground at the dispenser. When taking this measurement, make sure the ground and the neutral are disconnected at the dispenser. This ensures that the resistance read is not across the electronics on the circuit board. If the resistance reading is more than 1 ohm, the dispenser electronics may not operate properly and will void the Bennett Limited Warranty.
5.
Turn on 120 or 240 volts ac dispenser power to the unit.
6.
Use a voltmeter to verify 120 or 240 Volts AC only at Terminal 3 on TS1 of the 719 CPU board. Terminal 2 of TS1 on the CPU Board is Neutral.
This AC circuit provides power to the electronic boards.
7.
Make sure displays are normal and not distorted.
8.
Program the dispenser for Stand Alone operation in Menu Code 21.
9.
Turn the dispenser power back on.
WARNING: MAKE SURE ALL DISPENSER POWER CIRCUITS FOR REMOTES ONLY ARE ON THE SAME PHASE/LEG OF THE BREAKER
PANEL OR DAMAGE WILL RESULT.
CHECK THE PUMP MOTOR CIRCUIT!
REMOTE DISPENSERS
WARNING: TO PREVENT INJURY, MAKE SURE IMPACT VALVES AND SUBMERGED PUMP BREAKERS ARE OFF.
CAUTION: MAKE SURE THAT THE JUMPER BETWEEN J1-J3 (FOR PRODUCT A) AND THE JUMPER BETWEEN J2-J4 (FOR PRODUCT B)
ON THE CPU BOARD ARE PRESENT!
1.
Lift Product A's lever. The dispenser's display will reset. Use a voltmeter to verify 120VAC on Terminal 2 of TS2 on the CPU Board and use
Terminal 2 of TS1 on the neutral.
2.
Lower Product A's lever.
3.
Repeat this process for the remaining levers. Product B can be measured on Terminal 4 of TS2 on the CPU Board.
4.
To ensure that all dispensers are on the same phase, lift the lever for the same product on all dispensers at the same time. If any of the dispensers are on a separate phase then the F6 Fuse (on the CPU Board) will blow. If this happens, resolve the issue by getting all dispensers on the same phase and replace the fuse with another fuse that has the same ratings (1 Amp, Fast Acting 5mm x 20mm).
SUCTION PUMP
WARNING: IF THE LOWER DOOR ON THE PULLEY SIDE OF THE UNIT IS OFF, REPLACE THE DOOR, AND LOCK IT TO PREVENT INJURY.
CAUTION: MAKE SURE THAT THE JUMPER BETWEEN J1-J3 (FOR PRODUCT A) AND THE JUMPER BETWEEN J2-J4 (FOR PRODUCT B)
ON THE CPU BOARD ARE PRESENT!
MAKE SURE THAT THE SWITCH ON THE PUMP MOTOR IS SWITCHED ACCORDING TO THE VOLTAGE USED TO OPERATE IT.
LOW = 120VAC OR HIGH = 240VAC!
The suction pump's motor for Product A has two wires coming into the electrical enclosure.
12 135113 Rev C 4/2/18
One motor wire connects to TS2, terminal 2 of the CPU Board (factory connected) and the other wire is left detached for the installer to connect the pump motor's neutral, which comes directly from the Circuit Breaker or Phase 2 if using 240 volts to run the Product A motor.
The Hot wire for the suction pump's motor comes directly from the Circuit Breaker for Product A and connects to TS2, terminal 1 of the
CPU Board.
If this is a two product pump, then the wire from the Product B motor goes to TS2, terminal 4 of the CPU Board (factory connected) and the other wire is left detached for the installer to connect the pump motor's neutral, which comes directly from the Circuit Breaker or
Phase 2 if using 240 volts to run the Product B motor.
The Hot wire for the suction pump's motor comes directly from the Circuit Breaker for Product B and connects to TS2, terminal 3 of the
CPU Board.
1.
Turn on the Product A's pump motor's Circuit Breaker. With the lever lowered, use a voltmeter to verify that 120vac is on TS2, terminal 1 of the CPU Board. If the pump's motor is switched to high (240VAC) then verify that 120VAC is on the wire that the installer connected directly from the circuit breaker to the pump motor's wire.
2.
Turn off the Product A's pump motor's Circuit Breaker.
3.
Repeat this test for Product B using TS2, terminal 3 of the CPU Board for 120vac. If the pump's motor is switched to high (240vac) then verify that 120VAC is on the wire that the installer connected directly from the circuit breaker to the pump motor's wire.
STEP 11A - PURGING PRODUCT LINES FOR REMOTE DISPENSERS
The remote dispenser product lines must be purged of all air that may be trapped in the lines. All electrical connections must be made and verified at this time.
CAUTION: DO NOT USE THE DISPENSER TO PURGE AIR FROM THE PRODUCT LINES. RUNNING THE METER IN A DRY CONDITION AND
AT THE HIGH SPEEDS RESULTING FROM PRESSURIZED AIR, WILL DAMAGE THE METER AND VOID THE BENNETT LIMITED
WARRANTY.
The emergency shutoff valve contains a test port that may be used to bleed off air that may be trapped in the product lines. Manually close the emergency shutoff valve. Do not leave this process unattended while purging the air from the product lines.
Turn off the breaker to the submerged pump before removing the plug. Remove the plug and insert a hose with a ball valve to control fuel leakage. Turn on the breaker to the submerged pump after connecting the hose. Turn on the submerged pump and open the ball valve until fuel begins to come out. After fuel comes out close the ball valve, turn off the submerged pump using the circuit breaker, drain the hose by opening the ball valve, remove the hose, and reinsert the plug. If more than one dispenser is on a submerged pump product feed line, start this purging process at the dispenser furthest from the submerged pump and work backwards toward the submerged pump.
WARNING: TAKE APPROPRIATE MEASURES TO CONTAIN ANY PRODUCT EMERGING FROM THE TEST PORT. DISPOSE OF ANY SPILLED
PRODUCT IN PROPER MANNER CONSISTENT WITH APPLICABLE LAWS AND CODES.
Manually open the emergency shutoff valve and lock it into the “on” position according to the instructions from the valve manufacturer. Use a test prover can or other appropriate approved container to dispense 50 to 100 gallons or 175 to 350 liters through the dispenser. Begin dispensing by only slightly opening the nozzle to allow any entrapped air in the dispenser to slowly release through the nozzle. This prevents an over-speed pulser error.
Once the dispenser has dispensed 50 gallons of fuel, the SB100 meter should be tested for calibration.
STEP 11B - PURGING PRODUCT LINES FOR SUCTION SYSTEMS
The Suction pump product lines must be purged of all air that may be trapped in the lines. All electrical connections must be made and verified at this time.
The pumping unit evacuates all the air in the pipe before it gets to the meter. The air is expelled through the vent at the top of the pumping unit.
Nothing but fuel should pass through the meter. The meter will not turn until fuel enters the pump and pressurizes the system.
WARNING: TAKE APPROPRIATE MEASURES TO CONTAIN ANY PRODUCT EMERGING FROM THE AIR ELIMINATION CHAMBER TUBE.
CAUTION:
DISPOSE OF ANY SPILLED PRODUCT IN PROPER MANNER CONSISTENT WITH APPLICABLE LAWS AND CODES.
DO NOT RUN PUMPING UNITS FOR MORE THAN 5 MINUTES WITHOUT LUBRICATION OR DAMAGE TO THE UNIT CAN
OCCUR. TO AVOID DAMAGE TO PUMPING UNITS RUNNING MORE THAN 5 MINUTES, ADD A QUART OF OIL IN THE AIR
ELIMINATOR FOR LUBRICATION. REFER TO PRIMING THE PUMPING UNIT SECTION BELOW.
PRIMING THE PUMPING UNIT
Under normal circumstances, fuel is present before 5 minutes of pumping but if fuel is not present, the pumping unit MUST be primed. Prime the pumping unit using the Air Eliminator Vent or the Drain Plug located on the strainer cover to pour product into the pumping unit to prevent the pumping unit from running dry.
Use a test prover can or other appropriate approved container to dispense 50 gallons or 175 liters through the pump. Begin dispensing by only slightly opening the nozzle to allow any entrapped air in the dispenser to slowly release through the air eliminator. This prevents over-speeding of the meter.
Once the pump has dispensed 50 gallons of fuel, the SB100 meter should be tested for calibration.
13 135113 Rev C 4/2/18
STEP 12 - POTTING INSTRUCTIONS
1.
Wrap some CHICO X fiber around wires and push into conduit assembly to prevent potting from running down the length of the conduit.
2.
Using the wire separator provided, install one wire in each hole until all wires are separated.
3.
Push wire separator at least 3/4" (1.9 cm) into conduit.
4.
Prepare potting compound according to directions. Note : Use CHICO X potting compound for sealing fittings in hazardous locations.
5.
Using a funnel, pour potting into conduit, be sure to get potting in between each wire.
6.
Let stand until firm.
7.
Shorten field wiring to appropriate length when making connections. Ensuring clean bright wire ends.
8.
Attach field wiring to terminal strip in upper electrical enclosure according to the wiring diagram supplied for this dispenser.
STEP 13 - CALIBRATION PROCEDURE
Enter into Manager’s Mode 27 and slide the (E-Cal) switch to the right on the 719 CPU Board to gain access. If you attempt to dispense with this switch in E-Cal Mode, the dispenser will give you an Error.
THE BASIC CALIBRATIO N PROCEDURE
The basic calibration procedure assumes that the test can sight glass is graduated in units of cubic inches or cubic centimeters (milliliters). If the sight glass is in test can percentage units, refer to The Optional Calibration Procedure.
Prior to performing any E-Cal procedure, you must go to Mode 6 and make sure the dispenser configuration is correct. An incorrect configuration will prevent the use of un-configured meters. You also must make sure that every product has a price other than zero. A zero price will prevent the use of any configured meter.
1.
Press the number 2 and 7 , then the Mode button on the keypad. The first display shows the current electronic calibration correction constant of the first configured meter. Use the ↑ button to view the current electronic calibration correction constant for each configured meter. Once you are viewing the desired meter, press Enter .
2.
The main display shows the test can size entry prompt. Enter the test can size and press the Enter button. Once the test can size has been entered, the main display for the select dispenser side will show READY and the test can size will appear in the first PPV display. The second
PPV display if applicable will show the volume unit of measure (USG for United States Gallon or LIT for Liter).
3.
At this point, you are ready to run a test can sale. Turn on the pump handle. Once the product is selected, the main volume display will reset.
The main money display will show the current electronic calibration correction constant for the selected meter. The volume display will show the current sale volume.
4.
Run a sale as close as possible to the test can size entered in step 2 and turn off the pump handle. The display will change to the error entry display.
5.
Depending on the volume unit of measure, the error display will either show In Err for cubic inches or cc Err for cubic centimeters (milliliters).
Enter the amount of the error (positive or negative) and press the Enter button. You can only change the amount to a negative value after the entered amount is other than zero. Once the Enter key is pressed, the main display will show READY . Go to step 3 to run another test can until all meters are calibrated or press Cancel to exit.
6.
If calibration is complete, move the calibration switch back to the operate position and seal it.
14 135113 Rev C 4/2/18
THE OPTIONAL CALIBRATION PROCEDURE
This procedure assumes that the test can sight glass is graduated in test can percentage units rather than cubic inches or cubic centimeters
(milliliters) as in the basic calibration procedure. If the sight glass is in cubic inches or cubic centimeters, refer to The Basic Calibration Procedure.
1.
Press the number 2 and 7 , then the Mode button on the keypad. The first display shows the current electronic calibration correction constant of the first configured meter. Use the ↑ button or ↓ button to view the current electronic calibration correction constant for each configured meter. Once you are viewing the desired meter, press Enter .
2.
The main display now shows the test can size entry prompt. Press the +/- (plus/minus) button to enter the test can size. This switches the error entry mode from cubic units to percentage units.
3.
Enter the test can size (still in gallons or liters) and press the Enter button. Once the test can size has been entered the main display for the select dispenser side will show READY and the test can size will appear in the first PPV display.
4.
At this point, you are ready to run a test can sale. Turn on the pump handle.
5.
Once the product is selected, the main volume display will reset. The main money display will show the current electronic calibration correction constant for the selected meter. The volume display will show the current sale volume.
6.
The error display will show PC Err for percent error. Enter the amount of the error (positive or negative) and press the Enter button. You can only change the amount to a negative value after the entered amount is other than zero. Once the Enter key is pressed, the main display will show READY . Go to step 3 to run another test can until all meters are calibrated or press Cancel to exit.
7.
If calibration is complete, move the calibration switch back to the operate position and seal it.
THE DIRECT PERCENTAGE ENTRY PROCEDURE
The direct percentage entry procedure provides a way of zeroing or overwriting the electronic calibration correction constant. This procedure requires no test can.
1.
Press the number 2 and 7 , then the Mode button on the keypad. The first display shows the current electronic calibration correction constant of the first configured meter. Use the ↑ button to view the current electronic calibration correction constant for each configured meter. Once you are viewing the desired meter, press Enter .
2.
Record the E-Cal value from Menu Code 99.
3.
The main display now shows the test can size entry prompt. Press the ↑ button to bypass the test can prompt and access the direct percentage entry menu.
4.
The ↑ button is used to select the meter. Note : Only the top PPV display will display the selected meter as you press the up and down arrows.
5.
As the new electronic calibration correction constant is entered, it will show up in the main volume display. When the Enter button is pressed, the entered electronic calibration correction constant is loaded into the current meter and appears in the second PPV display (if applicable).
Go to step 3 to update another meter or press the Cancel button to exit this menu code.
DIAGNOSTIC MODES TABLE
Use the Diagnostic Modes Table for reference. Refer to the 719 Electronics Manual for detailed diagnostic information. Some diagnostic modes may not apply to your dispenser.
Diagnostic Code
0
1
2
3
5
6
8
9
Description
0.1 – Design Type
0.2 – Software Release Number
0.3 – 719 Software I.D. Number
0.4 – 419 Software I.D. Number
Display Segment Test
Error History
CPU Test (Error 99)
Pump Handle Test
6.1 - Power Failure Counter
6.3 - Cold Start Counter
6.4 - EEPROM Checksum Fails
6.5 - Software Restarts
6.6 – EEPROM Update Starts
Last Sale Limit Type (Prepay Money, Prepay Volume,
Allocation Limit, Preset Money, Preset Volume,
Maximum Money, Wayne Delivery)
Current Temperature and Volume Correction Factor
15 135113 Rev C 4/2/18
Error Code
00
02
03
47
48
51
52
53
54
55
43
44
45
46
35
36
37
38
25
26
27
28
33
34
17
18
23
24
13
14
15
16
04
05
06
07
08
09
73
74
75
76
77
83
93
56
58
59
60
70
71
72
94
99 d5
ERROR CODES TABLE
Error codes are displayed when there is a fault condition in the dispenser. In the event of an error, a message will be displayed on the side of the dispenser where the error occurred. Any error message will shut down the sale but not disable the pump. Note : Repair the problem that may have caused the error first and then clear the message by simply lowering the handle or put the nozzle back in the boot and remove the nozzle again. If an error message continues to be displayed, please contact Bennett Technical Support at 1-800-423-6638.
Error Text
6-Digit Display
NO ERR
DATA
2 COLD
8-Digit Display
NO ERROR
RAM DATA
ATC COLD
PLSRCR
PLSRCD
PLSRCG
619PRC
PLSRDS
PLSRDN
PLSRDR
PLSRDD
PLSRDG
619PRD
LOPRDA
LOPRDB
FFLO A
FFLO B
FFLO C
PLSRAG
619PRA
PLSRBS
PLSRBN
PLSRBR
PLSRBD
PLSRBG
619PRB
PLSRCS
PLSRCN
2 HOT
REVFLO
RFLO A
RFLO B
RFLO C
RFLO D
PLSRAS
PLSRAN
PLSRAR
PLSRAD
FFLO D
619PRE
BLEND
POSTAL
NOECAL
RANGE
VINTER
ETOTAL
UNSEAL
VSIDE1
VSIDE2
VAPOR
PLSRDC
PLSRCC
619DCN
GENERL
DOORSS
PULSERCR
PULSERCD
PULSERCG
619 PR C
PULSERDS
PULSERDN
PULSERDR
PULSERDD
PULSERDG
619 PR D
LOPROD A
LOPROD B
FORFLO A
FORFLO B
FORFLO C
ATC HOT
REV FLO
REVFLO A
REVFLO B
REVFLO C
REVFLOW D
PULSERAS
PULSERAN
PULSERAR
PULSERAD
PULSERAG
619 PR A
PULSERBS
PULSERBN
PULSERBR
PULSERBD
PULSERBG
619 PR B
PULSERCS
PULSERCN
FORFLO D
619 PR E
BLEND
GOPOSTAL
NO ECAL
OUTRANGE
VACINTER
ETOTFAIL
UNSEALED
VACSIDE1
VACSIDE2
VAPOR
PDISCONN
PCIRCUIT
619DISCN
GENERAL
DOORSENS
Description
No Error
Ram Error
The automatic temperature compensation probe reads less than -
30
The automatic temperature compensation probe reads less than +4 0
C
C
Reverse Pulser – Inactive Pulser Turning Forward or Backwards
Detected Pulser A Rotating Backwards
Detected Pulser B Rotating Backwards
Detected Pulser C Rotating Backwards
Detected Pulser D Rotating Backwards
Pulser A Error Same State Transition Limit Exceeded
Pulser A Next State Transition Limit Exceeded
Pulser A Reverse Flow
Pulser A Lead Channel Failed
Pulser A Lag Channel Failed
Grade A was Active when the Lower CPU Stopped Responding
Pulser B Same State Transition Limit Exceeded
Pulser B Next State Transition Limit Exceeded
Pulser B Reverse Flow
Pulser B Lead Channel Failed
Pulser B Lag Channel Failed
Grade B was Active when the Lower CPU Stopped Responding
Pulser C Same State Transition Limit Exceeded
Pulser C Next State Transition Limit Exceeded
Pulser C Reverse Flow
Pulser C Lead Channel Failed
Pulser C Lag Channel Failed
Grade C was Active when the Lower CPU Stopped Responding
Pulser D Same State Transition Limit Exceeded
Pulser D Next State Transition Limit Exceeded
Pulser D Reverse Flow
Pulser D Lead Channel Failed
Pulser D Lag Channel Failed
Grade D was Active when the Lower CPU Stopped Responding
Grade A Low
Grade B Low
Detected Pulser A Rotating When Not Allowed
Detected Pulser B Rotating When Not Allowed
Detected Pulser C Rotating When Not Allowed
Detected Pulser D Rotating When Not Allowed
Grade E was Active when the Lower CPU Stopped Responding
Blend ratios sent from the console does not match the dispenser ratio
Mailbox has exceeded its message limits
Not Calibrated or Bad Checksum
E-Cal Constant Out of Range Error
Vapor Vacuum – Interlock Error
One or more electromechanical totalizer output counters are corrupted
E-Cal Switch is in unsealed position and a normal sale started
Vapor Vacuum – Side 1 Error – Fast Flow or Over Current
Vapor Vacuum – Side 2 Error – Fast Flow or Over Current
TST Vapor Recover Error Signal Received
Pulser Disconnected
Pulser Circuitry Error
Lower I/O is Not Responding
CPU Failure – Addition Error
Door is open sensor (DS)
16 135113 Rev C 4/2/18
35
30
25
20
15
10
5
0
0
35
30
25
20
15
10
5
0
0
3000 SPARE PARTS LIST
The parts listed in the table below are basic components needed to retrofit an existing 3000 series dispenser, new, replaced, or refurbished dispenser. Some dispensers may require basic and/or additional materials such as bolts, fittings, fuses, washers, etc. These items can be found in your local hardware store. If not please feel free to contact our Bennett Customer Service Group at 1-800-719-6050.
Qty Part No. Description
1 RB131480 Pulse Output Board
1 108014 Pulser Kit
1 RB131363 Retail (1 Tier) Display Board
1 RB131299 Retail (2 Tier) Display Board
1 RB121992 RS485 Personality Board
1 107061 Satellite Controller Board
BIG FUELER FLOW CURVES
Qty Part No.
1
1
1
1
1
RB130396
RB130847
RB131306
RB121982
N/A
Description
419 Lower I/O Board
719 CPU Board
Commercial Display Board
Current Loop / Generic Loop Personality Board
Handle Switch Board
Flow Curve Big Fueler
5 10 15
Inlet Pressure (PSI)
20 25 30
Flow Curve Big Fueler
2 4 6 8 10
Pressure Drop (PSI)
12 14 16 18
17 135113 Rev C 4/2/18
advertisement
Key Features
- High flow rates (up to 60 gpm / 230 lpm) for fast and efficient fueling
- Versatile configuration options with up to 2 products and 2 hoses per side
- Advanced electronics with user-friendly interface and diagnostic capabilities
- Durable construction for long-lasting performance in demanding environments
- Optional features such as card readers, printers, and remote monitoring for added convenience and control
Related manuals
Frequently Answers and Questions
What is the maximum flow rate of the Bennett 3712?
How many hoses can be connected to the 3712?
What type of power supply does the 3712 require?
Can the 3712 be used for both suction and remote hydraulic configurations?
What type of communication protocols does the 3712 support?
advertisement