roundhouse TALIESIN Owner's Handbook Manual
Add to My manuals24 Pages
The Roundhouse Taliesin is a working model locomotive that uses steam under pressure and highly flammable fuel. It's intended for use outdoors and must be operated in a well-ventilated area. The locomotive has a number of safety features, including a fire extinguisher and a wet cloth. It also comes with a tool kit for maintenance and repairs. The Taliesin is capable of running for several hours on a single tank of gas and water. It can be controlled remotely using the included radio control system.
advertisement
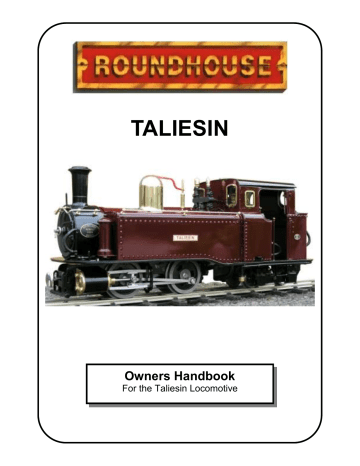
TALIESIN
Owners Handbook
For the Taliesin Locomotive
2
OPERATING INSTRUCTIONS
IMPORTANT: Read these instructions carefully before operating the locomotive.
The following items are required for running this engine and are not included with the model.
Fuel Butane gas. See 'Filling the gas tank'
Water See 'Filling the boiler'
Lubricating oil See 'Lubrication'
SAFETY PRECAUTIONS
This is a working model locomotive using steam under pressure and highly flammable fuel. Provided it is operated with reasonable care and attention, no problems should arise.
It is intended for use out of doors and must only be operated in a well ventilated area.
Whilst the locomotive is in use, hot gasses are exhausted up the chimney and excess steam frequently blows off through the safety valve even when stationary, so operator and spectators should not bend over the model.
As you will appreciate, this is not a toy and is therefore unsuitable for unsupervised children.
Follow manufacturer’s recommendations regarding the safe storage of Butane gas canisters.
Some areas of the model will get quite hot whilst it is operating, so a pair of gloves is provided in the tool kit for your protection.
Always have to hand either a fire extinguisher or wet cloth when operating the model.
Taliesin Instruction Booklet
CONTENTS
Tool kit.
Running in.
Access to the controls.
Identification of parts of the locomotive.
Preparing for operation.
1. Charging the batteries
2. Filling the Gas Tank.
3. Filling the Boiler.
3a. Quick filling when cold.
3b. Filling using the Pump bottle.
4. Lubrication.
5. Lighting the Burner.
Page 4
Page 4
Page 4
Page 5
Page 6
Page 6
Page 6
Page 7
Page 7
Page 8
Page 8
Page 9
Running the locomotive.
Water top-up system.
Storage between operating sessions.
Trouble shooting & maintenance.
Steam leaks.
Page 10
Page 12
Page15
Regulator not shutting.
Radio control.
Gas system.
Water top up valve
Page15
Page 15
Page 16
Page 17
Page 18
Page 19
Identification of gas burner parts. Page23
Boiler and Gas Tank Certificate, Pages 21 & 22
( EC Declaration Of Conformity ).
3
4
TOOL KIT
The following items are included with your locomotive.
One 60ml bottle of special steam oil for use in the lubricator.
One 60ml syringe with plastic tube for filling the boiler with water.
One water top-up pump bottle.
One gas filling adapter.
One set of spare washers and ‘0’ rings.
One spare gas jet.
One Allen key for cylinder socket cap screws.
One pair of protective gloves and one cleaning duster.
RUNNING IN
All locomotives are test run before leaving the factory, but will require several hours of running in, when new, to overcome initial tightness and allow valves etc. to ‘bed in’ completely. Also, the loco will waste a proportion of its water and steam until ‘run in’ due to leaking slide valves, a tendency to prime more, and simply overcoming the initial tightness of the moving parts.
As the model heats up and cools down each time you raise steam, screws and nuts have a tendency to stretch and loosen a little so you will also need to make regular checks and ‘nip up’ any that become loose. Most are quite visible and easy to get to however if there is any steam leaking from the valve chests on top of the cylinders, refer to the Trouble Shooting section.
ACCESS TO THE CONTROLS
For normal operation, all controls are accessible without the need to remove any part of the locomotive, however, to give access to the lubricator when filling, the cab roof hinges up. Care should be taken when opening the cab roof. Gently grasp either side of the roof hinge at the rear of the cab and lift the hinge vertically upwards. This will lift the hinge clear of the cab and allow the roof to then tilt to the rear.
The gas tank filler is under the dummy coal load in the rear bunker.
The gas regulator is accessible in the right hand cab doorway.
The On / Off switch for the locomotive R/C equipment is under the tool box lid on top of right hand side tank.
IDENTIFICATION OF PARTS OF THE LOCOMOTIVE a) Boiler filler and top-up valve (dome removed). b) Safety valve. c) Steam regulator. d) Gas regulator. e) Gas filler valve. f) Gas jet holder. g) Pressure gauge. h) Water gauge. i) Lubricator filler cap. j) Lubricator drain screw (under footplate).
5
6
PREPARING FOR OPERATION
The locomotive must be serviced before being operated. It is important to perform all the following operations.
1) CHARGING THE BATTERIES.
The batteries in the locomotive are Ni-MH and are rechargeable via a socket under the toolbox lid on top of the right hand side tank.
Plug the battery charger supplied, into a 3 pin power socket and switch on the power. A red LED on the charger will light to show it is working.
Lift up the lid of the tool box on the right hand side tank and ensure that the R/C switch is in the off position. Plug the charging lead into the socket next to the R/C On /Off switch. Leave to fully charge for sixteen hours.
If the model is to be stored for any length of time, ensure that the batteries are fully charged before storage. This will help to prevent any loss of battery performance.
Note that the batteries in the transmitter are not re-chargeable and are housed in the base of the unit.
2) FILLING THE GAS TANK
The filling of the gas tank should only be carried out in a well ventilated area, where there are no naked lights or other lighted locomotives close by. Ordinary Butane or Iso-butane gas (as used in gas cigarette lighters) is the preferred fuel, though for economy, the larger canisters as used for blowlamps or camping stoves etc. are better. The larger canisters have an EN417 threaded self sealing valve on top and require a special adapter to couple up to the filler valve on the locomotive. A special brass gas filler adapter is obtainable from your local garden railway supplier or direct from
ROUNDHOUSE.
Mixed gasses are also available and may be used if ordinary butane or Iso-butane are not available, but see ‘Gas System’ section for more information on this subject.
Before attempting to fill the gas tank, make sure that the gas control valve is closed by turning it clockwise.
The filler valve for the gas tank is on top of the tank under the dummy coal load. Invert the gas canister and place its nozzle over the gas filler valve. Support the tank from underneath and press the canister down. The gas will be heard hissing as it enters the tank and a small amount will escape around the valve. This is quite normal and is the tank venting as the liquid enters. After about 20 to 30 seconds, liquid gas will emerge from the valve showing that the tank is full. Remove the canister immediately.
3) FILLING THE BOILER
There are two methods of filling the boiler.
3a) Quick filling when cold.
The brass steam dome can be lifted completely off to access the filler plug. The brass dome is a substantial and heavy item, being turned from solid brass. Care is needed when removing the dome, especially when the engine is hot, as the dome itself will be hot.
Take care not to drop the dome onto the locomotive, as the weight of it may damage the model.
Remove the filler plug / filler valve assembly by unscrewing it.
Using the 60ml syringe and plastic tube supplied, fill the boiler fully to the top with clean water. Distilled water is recommended if available. As an alternative in soft water areas, clean tap water can be used. Also, rain water or water from a dehumidifier may be used provided that it is adequately filtered.
Many people use rain water passed through a wine or coffee filter to remove any particles or debris. Do not use deionised water as this type of water in the long term, may cause damage to the boiler and fittings. There has to be a space above the water to allow steam to be raised so, insert the end of the plastic pipe into the boiler and withdraw 30ml of water with the syringe. Replace the filler plug finger tight, and then place the brass dome over it. Note that there is a rubber ‘O’ ring around the body of the filler plug which helps retain the dome during normal operation.
7
8
3b) Filling using the Pump bottle when hot or cold.
The brass steam dome is open at the top and access to the filler valve can be gained with the pump bottle tube without removing the dome. Fill the pump bottle with clean water and pass the end of the tube down through the hole in the dome and into the top-up valve.
The socket has a slight taper in it, and a little downward pressure on the tube will ensure a good seal.
Pump the handle on the bottle to inject water into the boiler whilst maintaining downward pressure on the tube. Keep pumping until the water level in the water gauge (located inside the cab), is almost at the top of the glass.
Remove the plastic tube. Note that a small amount of water will remain in the top of the valve but will evaporate away as the valve heats up.
4) LUBRICATION
Regular lubrication of all working parts is important and should be carried out before each operating session. There are two types of lubrication required: The external moving linkages and bearings are lubricated with a medium oil such as motor engine oil, and the internal steam mechanisms such as cylinders, pistons and valves are lubricated with a special steam oil that is mixed with the steam.
Infrequent external lubrication will allow parts to run dry, and over oiling can form pools around operating parts that attract dirt and grit. If too thin an oil is used it will evaporate very quickly as the loco gets hot – leading to dry running. We recommend the use of a
20-50 motor oil for external lubrication.
As the valve gear is between the frames, the locomotive must be carefully laid on its side to gain access to all the moving parts when oiling
Internal lubrication is achieved by steam oil that is mixed with the steam in the displacement lubricator, housed in the left-hand side of the cab. Remove the knurled cap from the top and slacken the drain screw two or three turns at the bottom but do not remove it.
Any water in the lubricator will run out through the drain screw.
Tighten the drain screw and refill with the steam oil supplied, then replace the cap.
Take time filling the lubricator, especially when cold, as the oil takes time to run down and may trap an air bubble. Both cap and drain screw are fitted with ‘0’ rings and need only be closed finger tight.
NOTE: Only special steam oil as supplied should be used in the lubricator and under no circumstances should ordinary oil be substituted, or damage may result.
The gas and steam regulators will require periodic lubrication
– see the troubleshooting section for details.
5) LIGHTING THE BURNER
WARNING: Before lighting read the ‘Gas System’ section and be aware of potential problems. If the gas system is not operating correctly, shut it off immediately or damage may result.
Move the locomotive to another location before lighting. Butane is heavier than air and small pockets of gas can collect around the locomotive during filling.
To light the burner, hold a lighted match or cigarette lighter over the top of the chimney and slowly open the gas regulator by turning it anti-clockwise. The gas should ignite almost immediately with a pop as the flame travels down the chimney and into the boiler tube.
The burner should be audible but not too loud.
NOTE as stated above, the gas regulator should be opened slowly until the burner ignites. If opened too quickly, particularly when the engine is cold or if the gas tank has just been filled, it is possible that the flame may not travel back into the boiler flue but stay in the smoke box. If this should happen, the burner will sound quite different to normal and the blue flame will be visible in the smoke box if viewed down the chimney from a safe height. Should this
9
10 happen, turn off the gas immediately or damage may result and then re-light it. If the problem persists and it is not possible to ignite the burner correctly, then a dirty jet should be suspected and cleaned as shown in the ‘Gas System’ section.
For the first couple of minutes keep the burner on low. This is important, as until it warms up, the flame will be a little unstable and turning it up too much could cause it to go out. Also, with a completely full tank, liquid gas could be drawn off instead of vaporised gas, which can also extinguish the flame.
After a couple of minutes, the gas control valve can be opened more to speed up steam raising. Open the gas regulator slowly to about one full turn.
The full range of adjustment (closed to fully open) is achieved within the first full rotation of the gas regulator knob any more is unnecessary.
RUNNING THE LOCOMOTIVE
If you are familiar with running Roundhouse steam locomotives, you may find Taliesin a little different. All models have a unique ‘feel’ and this single Fairlie is no exception and requires a little more driving than some of our other locomotives. Several factors come into play e.g. large diameter driving wheels, long flexible steam pipe, inside valve gear and valve chests and a separate articulated power bogie, all contribute to the overall performance. It is also important to maintain a good water level at all times using the water top up system.
When full working pressure has been reached (about 40psi), the safety valve will start to blow off steam. Steam generation can be controlled by the gas valve in the cab. If the safety valve blows off frequently during running, then too much steam is being produced, which wastes water and gas. Turning down the burner will decrease the amount of steam created. Conversely, if steam pressure is not maintained during a run, then the burner should be
turned up.
After a few minutes of running it may be noticed that the gas pressure through the burner has increased. This is due to the gas tank becoming warmer and so increasing the gas pressure. Simply turn the gas down – this may need to be performed several times during a run. The art of balancing steam generation to the operational requirement by the adjustment of the gas control valve will quickly be learned.
The gas tank has a duration of about 40 minutes, though this will vary a little depending on gas valve setting. The boiler should not be allowed to run dry, and, as the gas tank capacity is greater than that of the boiler, it is necessary to top up the water at frequent intervals as detailed in the water top up system section later in this booklet. When the gas is fully used up, the steam pressure in the boiler will be seen to gradually drop until the loco comes to a halt.
Should the water expire before the gas is fully used, the pressure will drop rapidly and the loco will stop. Check the pressure gauge and water gauge – if there is no steam pressure or visible water, turn off the gas. No damage will result if the gas is turned off immediately and the engine left to cool. Never add cold water to a hot, empty boiler in an attempt to cool it and never re-fill the gas tank without first checking the water level in the boiler.
Ensure that the gas valve is completely turned off before refilling the gas tank.
This model is fitted with 2.4 GHz R/C equipment. On a Radio
Controlled model, speed and direction are controlled by the transmitter. First, turn on the transmitter and then switch on the receiver on the locomotive. The left hand stick on the transmitter controls the steam regulator; down for stop and up for go. Moving to the left or right has no function.
The right hand stick operates the valve gear. Move the stick fully to the left for forward and fully to the right for reverse. This stick is
11
12 sprung loaded to return to its central position. Moving up or down has no function.
Using the transmitter, select the desired direction of travel and then slowly open the regulator. The locomotive will now move off as described in the manual control section.
The art of fine control will soon be learnt with a little practice.
NOTE: Always hold the reversing lever fully over in the required direction when the engine is moving. The model is fitted with a simple reversing valve gear and is not capable for 'notching up' (altering the valve cut off).
Always bring the locomotive to a halt by closing the regulator before changing direction. If an emergency stop is required, simply release the reversing control on the transmitter, which will spring back into mid gear and halt the train. Then close the regulator.
Always ensure that the regulator is closed before switching off the transmitter.
Always switch off the receiver and transmitter when not in use to preserve battery life.
It is good practice to switch on the transmitter before the receiver and switch off the receiver before the transmitter. In this way, the radio receiver is never on when the transmitter is switched off and so should always be under your control.
When the batteries are getting low a poor signal between transmitter and receiver will occur. This will cause control of the engine to become erratic. The batteries in the transmitter should be replaced immediately and the receiver batteries in the locomotive should be charged as previously described.
WATER TOP UP SYSTEM
A water top up system is fitted to this model. This enables the water level in the boiler to be monitored and topped up to keep the engine in steam for long periods.
Once the locomotive is in operation as detailed in the previous sections, water must be added to the boiler from time to time during the run as follows.
Fill the water pump bottle from your usual water supply.
Bring the locomotive to a halt in a convenient place.
The steam dome has an opening at the top to allow access to the
13
14 water top-up valve. The steam dome can be lifted off if preferred -
NOTE: when the locomotive is in service, the steam dome will be hot and a pair of cotton gloves are provided in the tool kit.
Push the end of the plastic tube down through the hole in the top of the steam dome and into the socket in the top of the water filling valve.
Whilst still holding the pipe in position and exerting slight downward pressure, pump the handle and this will inject water into the boiler.
You will sometimes see water and air bubbles passing through the sight glass as you pump so allow the level to settle after a few pumps. Carefully pull the plastic pipe out of the water filling valve whilst steadying the engine.
Sometimes, small particles of dirt will find their way in with the water and may cause the water filling valve to leak back a little when the pipe is removed. If this does happen, re-connect the pipe and give a further pump or two of water to clear it. As the filler valve sits vertically on top of the boiler, a small amount of water will remain in the socket once the plastic pipe has been removed and will boil off as the fittings return to normal operating temperature.
This is quite normal.
Once you start running your loco you will see the water level in the gauge slowly dropping. Note that air bubbles may sometimes form in the gauge giving a false reading but these can be pushed out by connecting the pipe from the water pump to the water filling connector and injecting a little more water.
It is better to pump small amounts of water into the boiler at frequent intervals as this maintains a more even boiler pressure and prevents long waits while the cold water heats up and pressure returns to normal operating level.
Aim to keep the water level between ½ and ¾ up the gauge and never let the boiler run dry as this may seriously damage the model.
Re-fill the gas tank as detailed earlier whenever it is empty. In this way, you can keep the loco in steam and at working pressure as long as you like.
Don’t forget to re-fill the displacement lubricator about every 45 minutes.
STORAGE BETWEEN OPERATING SESSIONS
At the end of an operating session, it is good practice to clean the locomotive carefully with a clean soft cloth, and to oil all bright metal parts.
Do not leave fuel or water in the tank or boiler for long periods.
Do not store in places where the temperature may drop below freezing, as water may still be present in the pipework.
Ensure all controls are closed and the valve gear in mid gear.
Ensure that radio control equipment is switched off and, if the engine is not to be used for some time, remove all batteries.
Periodically it may be necessary to wash off all traces of dirt and old oil from the moving parts with paraffin (not thinners). This will remove any accumulations of dirt or grit.
After washing with paraffin, leave to dry thoroughly overnight before re-oiling. It is most important that clean oil is applied and allowed to penetrate fully into all moving parts before the locomotive is run again.
Manually moving the locomotive back and forth will assist in distributing the oil fully. Under normal operating conditions this procedure should not be required more than once or twice per year.
15
16
TROUBLE SHOOTING & MAINTENANCE
On a working model of this nature, it is important to keep all working parts well lubricated. With constant heating up, cooling down and the stresses of hard work, screws etc. can work loose so, it is good practice to check all fixings and cylinder screws regularly but remember, never over tighten.
STEAM LEAKS
The cylinders are fitted with 'O' rings in the glands sealing both piston and valve rods. These can be adjusted if steam leaks develop. They should only be tightened just enough to stop the leak, as over tightening will affect the running of the model.
Cylinder covers are fitted with gaskets and valve chests with ’O’ rings. A little ‘bubbling’ of oil may sometimes occur around these and is quite normal; however, steam leaking past the gasket should be attended to.
If ‘nipping up’ the retaining screws does not stop a steam leak, a service kit is available which includes replacement gaskets and seals and full instructions for fitting. Valve chest screws can only be accessed by removal of the power bogie from the locomotive.
REGULATOR NOT SHUTTING
The steam regulator seating and seal can, after a period of time become worn or compressed so that when the lever on the radio control is fully closed, the locomotive still moves. To overcome this, a trimmer is fitted to the transmitter. As wear takes place in the regulator, it can gradually be adjusted to compensate. When no more adjustment is possible, it is time to reset the trimmer and adjust the linkage between the servo and the regulator in the cab.
If adjustment does not cure this problem, the internal '0' ring is probably damaged and requires replacement. Contact the factory for further advice.
Periodic oiling of the gland will help keep the regulator working
freely. Place a spot of motor oil between the gland nut and the regulator arm and work the regulator a few times.
Contact the factory for further advice. Periodic oiling of the gland will help keep the regulator working freely. Place a spot of motor oil between the gland nut and the regulator arm and work the regulator a few times.
RADIO CONTROL
If the radio control gives problems, always check the batteries first and replace or re-charge if in doubt. AA size batteries are used in the transmitter and good quality alkaline or similar are recommended. The batteries in the locomotive that provide power for the receiver and the servos are Nickel Metal Hydride batteries.
These batteries will gradually lose their charge over a period of a few weeks. The batteries should be used and re-charged at least once every 4 to 6 weeks. Always fully re-charge the batteries after use. Failure to do this may damage the batteries so that they can no longer be charged and they will then need to be replaced.
The radio control receiver and batteries are housed in the right hand side tank and are only accessible by removing the body as follows. First, lift off the brass dome and dummy coal load and carefully lay the locomotive on its side on a protective cloth. Next, remove eight retaining nuts under the footplate. There are two on each side of the side tanks and two on each side of the cab. Note the cab fixing screws also hold on the dummy pipe castings under the footplate.
The body can now be lifted up enough to access the R/C receiver on the right hand footplate. Unplug the battery lead from the receiver then lift the body clear.
For further details of the R/C equipment, refer to the manufacturers literature supplied.
17
18
GAS SYSTEM
Taliesin locomotives are fitted with our 'FG' type gas burner, which is set up and fully tested at the factory. This system is designed for use with Butane or Iso-Butane gas. Mixed gasses, i.e. Butane with a proportion of Propane mixed in, are available, and may be used if straight Butane is unavailable. These come in a variety of mixes ranging from 90/10 to 60/40 with one of the most common being
70/30. The figures refer to the proportions of the mix i.e. 70/30 contains 70% butane and 30% propane.
If using mixed gasses, always choose the one with the largest proportion of butane. The addition of propane slightly alters the gasses properties. This can make the burner a little more difficult to light when cold or after filling the gas tank.
Always open the regulator very slowly when lighting, and only just sufficient for ignition to take place. Opening too much too soon may extinguish the flame until the burner reaches normal operating temperature.
The tiny jet in these units can become blocked by small particles of dirt making the burner difficult to light, burn weakly at normal operating temperatures*, burn in the smoke box or fail completely.
If any of these should happen, clean out the jet as follows.
(* On very cold days, a burner may start off burning weakly due to the temperature of the gas but should increase to its normal level as the engine warms up. This is quite normal). Carefully, disconnect the gas pipe from the gas jet holder using a 2BA spanner.
Note when connecting or disconnecting the gas pipe and gas jet holder, do not use excessive force. Always hold the end of the gas burner near the air holes to support it otherwise it is possible to cause damage by bending the body. Slacken the screw retaining the gas jet holder and slide it out to the rear. Remove the jet from the gas jet holder using a 4BA spanner.
Wash out the jet in fast evaporating thinner (Cellulose or similar).
Blow through the jet from the front, which should clear most blockages. Although the hole through the jet is tiny, if you hold it up to the light you should be able to see quite clearly if it is blocked or not. If in doubt, fit a new jet.
A spare gas jet is included with the toolkit. Do not use wire to clean the jet as this can damage the precision hole and may upset the delicate balance of the gas system. Reassemble in the reverse order, putting a small amount of PTFE tape round the thread of the jet. Ensure all connections are tight.
When re-positioning the gas jet holder in the burner, ensure that it is pushed in as far as it will go.
The gas regulator has a spindle ‘O’ ring housed inside the body which may need lubrication from time to time if the control becomes
‘spongy’ in operation, making precise gas control difficult.
As stated in the lighting instructions earlier, the full range of adjustment for normal burner operation is achieved within the first full rotation of the regulator knob, and it should only be unscrewed more than this for maintenance purposes and when the tank is empty, and there are no naked lights nearby.
To lubricate it, remove the knurled knob which is retained by a M3 socket grub screw (M 1.5 AF Allen key required) in the side. This grub screw is accessed by first removing the brass lever which is screwed into the same hole.
Beneath the knob is a back-lash spring which will slide off the spindle. Unscrew the hexagon retaining nut then screw the spindle out of the body.
The ‘O’ ring can now be lubricated.
Replace the spindle followed by the retaining nut. Slide the backlash spring over the spindle and replace the knob. Note that
19
20 the grub screw that holds the knob in place tightens into a groove near the end of the spindle.
See photograph below.
Gas Regulator (Internal Parts)
Regulator
Body
‘O’ ring to be lubricated
Hexagon
Retaining
Nut
Back-Lash
Spring
Regulator
Spindle
White PTFE
Washer
Knurled
Knob
WATER TOP UP VALVE
Steam or water leaking back through the top up valve is usually caused by dirt particles preventing the valve from sealing correctly.
The valve consists of a simple silicone rubber tube over a brass valve body. To clean, remove the boiler filler plug and unscrew the hexagon valve body from the top. Once removed, the silicone tube on the lower half of the filler valve body can be carefully removed by sliding it off. Clean the tube and valve body and replace the tube. If the tube is damaged, a replacement is available from the
Roundhouse factory. Replace the filler valve in the top of the filler plug, not forgetting the copper washer.
The tip of the plastic tube on the pump bottle will, over time, become smaller in diameter and fail to seal correctly into the tapered socket of the top up valve. When this occurs, simply cut about 6mm from the end of the tube to restore the seal.
22
Please refer to the ‘owner’s handbook’ for your particular model of locomotive, for details on correct use of these pressure vessels.
Pressure vessel care and maintenance
Gas tank
The gas tank is used for the storage of LPG (liquefied petroleum gas) in the form of butane, iso-butane or as set out in the ‘owners handbook’.
The tank is fitted with a self-venting filler valve which contains no serviceable parts. Should the filler valve become defective in any way, it must be replaced with a new item.
It is recommended that the gas tank should undergo the following checks, carried out by a ‘competent person’, club, society or pressure vessel manufacturer, every year:-
1) thorough visual inspection.
And every five to ten years:-
1) hydrostatic pressure test to not less than 1.5 and not more
than 2 times the maximum working pressure.
Boiler
The boiler is fitted with a safety valve to prevent the steam pressure rising above the maximum allowable working pressure.
This is pre-set to open at between 2.38 bar (35 psi) and 2.72 bar
(40 psi) and must not be adjusted to increase this value.
If the safety valve becomes defective in any way, it should be replaced or returned to the factory for service and calibration.
It is recommended that the boiler should undergo the following checks, carried out by a ‘competent person’, club, society, or pressure vessel manufacturer, every one to two years:-
1) thorough visual inspection.
2) hydrostatic pressure test to not less than 1.5 and not more
than 2 times the maximum working pressure.
3) steam test to check the correct functioning of all steam
controls, gauge and safety valve.
Gas Burner
1). Superheater
Pipe.
2). Lubricator
Pipe.
3). Gas Jet Holder
retaining screw.
4). Gas Jet.
5). Gas Jet Holder.
6). Gas Pipe.
7). Gas Burner
fixing screw.
8). Air Inlet Holes.
23
SERVICE AND PARTS
If you any problems arise with this model which are not covered in these operating instructions or, spare parts are required, owners should first contact their local dealer. Your ROUNDHOUSE dealer is;
If your dealer is unable to help, you may contact the Factory directly:
ROUNDHOUSE ENGINEERING CO. LTD.
Units 6-9 Churchill Business Park. Churchill Road.
Wheatley. Doncaster. DN1 2TF. England
Telephone 01302 328035 Fax 01302 761312 email [email protected]
ONLINE www.roundhouse-eng.com
advertisement
Related manuals
advertisement