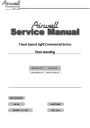
advertisement
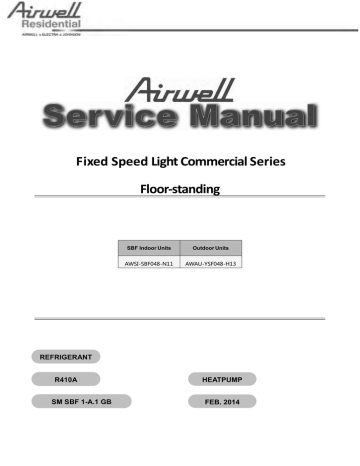
Fixed Speed Light Commercial Series
Floor-standing
REFRIGE
REFRIGERANT
R410A
SM SBF 1-A.1 GB
SBF Indoor Units
AWSI-SBF048-N11
Outdoor Units
AWAU-YSF048-H13
HEATPUMP
FEB, 2014
CONTENTS
1. Safety Precautions
1.1 Precaution
To prevent injury to the user or other people and property damage, the following instructions must be followed.
Incorrect operation due to ignoring instruction will cause harm or damage.
Before service unit, be sure to read this service manual at first.
1.2 Installation
For electrical work, contact the dealer, seller, a qualified electrician, or an Authorized service center.
Do not disassemble or repair the product by yourself.
Sharp edges could cause injury, be especially careful of the case edges and the fins on the condenser and evaporator.
Be sure the installation area does not deteriorate with age.
Take care to ensure that power cable could not be pulled out or damaged during operation.
Do not place anything on the power cable.
Do not plug or unplug the power supply plug during operation.
Do not store or use flammable gas or combustible near the product.
When flammable gas leaks, turn off the gas and open a window for ventilation before turn the product on.
If strange sounds, or small or smoke comes from product. Turn the breaker off or disconnect the power supply cable as soon as possible.
When the product is soaked (flooded or submerged), contact an Authorized service center.
Be caution that water could not enter the product.
Turn the main power off when cleaning or maintaining the product.
When the product is not be used for a long time, disconnect the power supply plug or turn off the breaker.
1.3 Caution
Always check for gas (refrigerant) leakage after installation or repair of product.
Install the drain hose to ensure that water is drained away properly.
Keep level even when installing the product.
Do not install the product where the noise or hot air from the outdoor unit could damage the neighborhoods.
Use two or more people to lift and transport the product.
Do not install the product where it will be exposed to sea wind (salt spray) directly.
1.4 Operational
Do not expose the skin directly to cool air for long periods of time. (Do not sit in the draft).
Do not use the product for special purposes, such as preserving foods, works of art, etc. It is a consumer air conditioner, not a precision refrigerant system.
Do not block the inlet or outlet of air flow.
Use a soft cloth to clean. Do not use harsh detergents, solvents, etc.
Do not touch the metal parts of the product when removing the air filter. They are very sharp.
1
Do not step on pr put anything on the product. (outdoor units)
Always insert the filter securely. Clean the filter every two weeks or more often if necessary.
Do not insert hands or other object through air inlet or outlet while the product is operated.
Do not drink the water drained from the product.
Use a firm stool or ladder when cleaning or maintaining the product.
Replace the all batteries in the remote control with new ones of the same type. Do not mix old and mew batteries or different types of batteries.
Do not recharge or disassemble the batteries. Do not dispose of batteries in a fire.
If the liquid from the batteries gets onto your skin or clothes, wash it well with clean water. Do not use the remote of the batteries have leaked.
2
2. Specification
Model Indoor Unit
Model Outdoor Unit
Installation Method of Pipe
Characteristics
Rated Capacity
Input power
EER/Energy Label
Power supply
Circuit breaker rating
Fan type & quantity
Fan speeds
Air flow
(3)
External static pressure
Sound power level
(4)
Sound pressure level
(5)
H/M/L
H/M/L
Min-Max
H/M/L
H/M/L
Moisture removal
Dimensions
Weight
Package dimensions
Packaged weight
Stacking height
Refrigerant control
Compressor type. model
Fan type & quantity
Fan speeds
WxHxD
WxHxD
Air flow
Sound power level
(4)
Sound pressure level
(5)
Dimensions
Weight
Package dimensions
Packaged weight
Stacking height
Refrigerant type
H/L
H/L
H/L
H/L
WxHxD
WxHxD
Refrigerant charge (standard connecting tubing length)
Additional charge per 1 meter
Liquid line
Suction line
Connections between units
Max.tubing length
Max.height difference
Operation control type
AWSI-SBF048-N11 m3/hr dB(A) dB(A) mm kg mm kg units kg(5m) gr / 1m
In.(mm)
In.(mm) m. m.
RPM m3/hr
Pa dB(A) dB(A) l/hr mm kg mm kg units
RPM
AWAU-YSF048-H13
Flared
Units Cooling
kW 12,4
Heating
13,6(+3,5) kW
W/W
V/Ph/Hz
A
4,62
2,68 / D
4,84(+3,5)
2,81 / D
380-415V~ 50Hz, 3Ph
25
Centrifugal fan x1
580/500/400
1850/-/1500
/
66
56/-/48
4,6
550x1800x350
48
685x1910x540
63.3
6
Capillary
Scroll
Axial x 2
142/127
5600
71
61
938x1369x392
111
1095x1505x495
123.4
2
R410A
3.3
60
1/2"(Φ12.7)
3/4"(Φ19)
50
25
Remote control
3
3. Dimension
3.1 Indoor Unit
Dimension
W(mm)
Mode
AWSI-SBF048-N11 550
D(mm)
350
H(mm)
1800
4
3.2 Outdoor Unit
Dimension
W(mm) D(mm) H(mm) W1(mm) A(mm) B(mm)
Mode
AWAU-YSF048-H13 938 392 1369 1023 633.5 404
5
4. Refrigerant cycle diagram
INDOOR
LIQUID SIDE
2-WAY VALVE
HEAT
EXCHANGE
(EVAPORATOR)
T1 Room temp.
sensor
OUTDOOR
CHECK VALVE
(Heating Model only)
CAPILIARY TUBE
T3 Condenser temp. sensor
T4 Ambient temp. sensor
HEAT
EXCHANGE
(CONDENSER)
T2 Evaporator temp. sensor
GAS SIDE
3-WAY VALVE Accumulator
Compressor
Low pressure switch
4-WAY VALVE
High pressure switch
T5 Discharge temp. sensor
COOLING
HEATING
6
5. Wiring diagram
AWSI-SBF048-N11
7
AWAU-YSF048-H13
8
6. Installation details
6.1 Installation place
6.1.1 Indoor Unit a. A place which provides the spaces around the indoor unit as required above in the diagram. b. A place where is no obstacle near the inlet and outlet area. c. A place which can bear the weight of the indoor unit. d. A place which allows the air filter to be removed downward. e. A place where the reception range is not exposed to direct sunlight. f. In the center of the room where possible.
6.1.1.1 Please stand the unit in hard and flat ground;
Please reserve space for installation and maintenance.
6.1.2 Outdoor Unit
6.1.2.1 Before installing the outdoor unit, you should: a). Select a place where no direct sunlight or other heat-radioactivity may reach. A sunshade is needed if it is unavoidable. b). Select a place that is easy to connect indoor unit's pipe and electric wires. c). Avoid a place where combustible gas may leak or stay. d). Keep it in mind that water may drain out of the outdoor unit while in "Heat" mode.
Caution:
Installation in the following places may cause trouble. If it is unavoidable to use in such places, please consult with the dealer. a. A place full of machine oil. b. A saline place such as coast. c. Hot-spring resort. d. A place full of sulfide gas. e. A place where there are high frequency machines such as wireless installation, welding
machine, medical facility. f. A place of special environmental conditions.
6.1.2.2 If the outdoor unit is to be installed on a roof or where no constructions are around, you should avoid hard wind blows directly to the air outlet, because it may cause trouble for air-flow shortage.
9
6.1.2.3 Reserve enough space for installation, maintenance and unit-functioning.
Remove as many obstacles as possible nearby.
6.2 Installing
6.2.1 Indoor Unit:
1. Anti-falling;
To prevent the indoor unit from falling, you must: a. Pay full attention to the unit because its long outer shape makes it easy to fall; b. Firmly fix the unit to the wall or in the ground to avoid accidental falling.
2. Dismounting the lower front panel
Please take off the lower front panel before connecting the pipes/wires.
Pull down the two knobs on the grille, take off the two screws, then the air-inlet grille
10
goes free.
3. Take the Pipe Clip off before connecting the pipes and wiring; fit it when these finished.
Use accessories to connect the pipes/wires on both sides and back side.
6.2.2 Outdoor Unit:
1. Ship the a/c to the installation place originally packed;
2. Be careful while hanging the unit because the center of gravity of the unit is not centralized;
3. Do not make the angle of inclination more than 45 degrees while shipping;(Avoid horizontal storage)
4. Be sure the electric insulation work is well done if installed on metal ceiling / wall.
11
5. Fix the unit feet with bolts (M10/M8). Be sure the unit is fixed strongly enough to against blast or earthquake.
6. Make a concrete basement to the unit by the following references.
For the value of A and B, please refer to the dimension part.
6.3 Refrigerant pipe connection
6.3.1 Pipe length and the elevation
The correct refrigerant quantity filled in the 5-meter-long pipe of the outdoor unit is marked on the Product Data Plate. If you have to use longer pipe for every meter plus pipe, the refrigerant should be added according to the following calculation.
Pipe size Max. Additional
Model
Gas Liquid
Standard length
Max.
Elevation
(m)
B (m)
Length
A (m) refrigerant
(g/m)
AWSI-SBF
048-N11
3/4’’ (Ф19)
1/2’’
(Ф12.7)
5 10 20 60
Caution:
Capacity is base on standard length and maximum allowance length is base of reliability.
Oil trap should be installed per 5-7 meters.
12
6.3.2 Piping connection
6.3.2.1 Connecting Of Refrigerant Pipe a) Only the correctly installing of indoor and outdoor unit done, can the refrigerant pipe be connected. b) The cut-off valves are completely close before ex-work. Before connecting the refrigerant pipe, be careful to check whether the valves are completely close. c) The connecting procedure of refrigerant pipe: first, unscrew the two valves on the outdoor unit and the pipe-jointing nut on the indoor unit(please keep them care- fully). Please connect the refrigerant pipe according to the manual, the pipe-jointing nut should be screw tightly and no leakage. Note: you need two wrenches to make balance. d) When the connecting of refrigerant pipe is finished, before power on the system, you should vacuum the indoor unit through the maintenance port on the cut-off valves, or open the high-pressure valve, and exhaust the air through the maintenance port on the low-pressure valve(closed). It will take about ten seconds. Then screw tightly the maintenance port. (When supplement the refrigerant, fill through the maintenance port of the low-pressure valves on the outdoor unit ). e) Open all the valves completely before power on the system, or it will be sick for low efficiency. f) Gas leak check. Make sure no gas from connections with leak detector or soap water.
Caution:
A: Lo packed valve B: Hi packed valve
C and D are ends of indoor unit connection.
Caution in Handling the Packed Valve
a. Open the valve stem until it hits against the stopper. Do not try to open it further. b.
Securely tighten the valve stem cap with a spanner or the link.
13
Notes for the bendable pipe
a.
The bendable pipe should be used on the indoor side; b.
Bend angel may not exceed 90 degrees; c.
The bend location should be made on the center of the pipe if possible, as for bend radius, the bigger the better; d.
The bendable pipe may not be bent for more than 3 times.
Bend the thin pipe
a.
While bending, expose the pipe by cutting the concave gap on the bending heat-insulation pipe(roll it with soft band after bent). b.
To avoid pipe deformation, the radius is the bigger the better. c.
Use a pipe-bending device to make the compact bending pipe.
6.3.2.2 Using bronze pipe selling in market
Completely shut the cut-off valves of the outdoor unit (as ex-work status). After the refrigerant pipe has been connected with both the indoor and outdoor unit, let the air exhaust out from the maintenance gap on the low-pressure cut-off valves of the outdoor unit. Screw the nuts tightly on the maintenance gap after the air has been drained.
6.3.2.3 To make the refrigerant pipe unblocked completely
You should keep the cut-off valves of the outdoor unit completely open after you have finished the above steps (5.3.2.1 or 5.3.2.2)
Note:
1.Before screwing the reamer nut, smear the pipe and the connecting surface with refrigerant oil;
2.Check and make sure there is no leakage by soap-water or leakage-checker after connecting;
3.Be sure the connecting joint on the indoor side is insulated.
4.Use two wrenches to connecting the pipes.
14
Outside diameter mm
Ф9.52
inch
3/8
Ф12.7
Ф16
Ф19
6.3.3 Installation for the first time
1/2
5/8
3/4
Torque
N.cm
3270
4950
6180
9720
Additional tightening torque
N.cm
3990
6030
7750
11860
Air and moisture in the refrigerant system have undesirable effects as below:
● Pressure in the system rises.
● Operating current rises.
● Cooling or heating efficiency drops.
● Moisture in the refrigerant circuit may freeze and block capillary tubing.
● Water may lead to corrosion of parts in the refrigerant system.
Therefore, the indoor units and the pipes between indoor and outdoor units must be leak tested and evacuated to remove gas and moisture from the system.
Gas leak check (Soap water method):
Apply soap water or a liquid neutral detergent on the indoor unit connections or outdoor unit connections by a soft brush to check for leakage of the connecting points of the piping. If bubbles come out, the pipes have leakage.
1. Air purging with vacuum pump
15
(Indoor unit)
(Liquid side)
Two-way valve
Close
Vacuum
pump
(Gas side)
Manifold valve
Compound meter
Pressure gauge
-0.1MPa
Lo Hi
Three-way valve
Close
Handle Lo
Charge hose
Handle Hi
Charge hose
(Outdoor unit)
Vacuum pump
1) Completely tighten the flare nuts of the indoor and outdoor units, confirm that both the
2-way and 3-way valves are set to the closed position.
2) Connect the charge hose with the push pin of handle lo to the 3-way valves gas service port..
3) Connect the charge hose of handle hi connection to the vacuum pump.
4) Fully open the handle Lo of the manifold valve.
5) Operate the vacuum pump to evacuate.
6) Make evacuation for 30 minutes and check whether the compound meter indicates -0.1Mpa.
If the meter does not indicate -0.1Mpa after pumping 30 minutes, it should be pumped 20 minutes more. If the pressure can’t achieve -0.1Mpa after pumping 50 minutes, please check if there are some leakage points.
Fully close the handle Lo valve of the manifold valve and stop the operation of the vacuum pump. Confirm that the gauge needle does not move (approximately 5 minutes after turning off the vacuum pump).
7) Turn the flare nut of the 3-way valves about 45° counterclockwise for 6 or 7seconds after the gas coming out, then tighten the flare nut again. Make sure the pressure display in the pressure indicator is a little higher than the atmosphere pressure. Then remove the charge hose from the 3 way valve.
16
8) Fully open the 2 way valve and 3 way valve and securely tighten the cap of the 3 way valve.
2. Air purging by refrigerant
Procedure:
1). Confirm that both the 2-way and 3-way valves are set to the closed position.
2). Connect the charge set and a charging cylinder to the service port of the 3-way valve.
3). Air purging.
Open the valves on the charging cylinder and the charge set. Purge the air by loosening the flare nut on the 2way valve approximately 45’ for 3 seconds then closing it for 1 minute; repeat 3 times.
After purging the air, use a torque wrench to tighten the flare nut on the 2-way valve.
4). Check the gas leakage.
Check the flare connections for gas leakage.
5). Discharge the refrigerant.
Close the valve on the charging cylinder and discharge the refrigerant by loosening the flare nut on the 2way valve approximately 45’ until the gauge indicates 0.3 to 0.5
Mpa.
6). Disconnect the charge set and the charging cylinder, and set the 2-way and 3-way valves to the open position.
Be sure to use a hexagonal wrench to operate the valve stems.
7). Mount the valve stems nuts and the service port cap.
Be sure to use a torque wrench to tighten the service port cap to a torque 18N ·m.
Be sure to check the gas leakage.
17
3. Adding the refrigerant if the pipe length >5m
Electronic scale
Procedure:
1). Connect the charge hose to the charging cylinder, open the 2-way valve and the
3-way valve.
Connect the charge hose which you disconnected from the vacuum pump to the valve at the bottom of the cylinder. If the refrigerant is R410A, make the cylinder bottom up to ensure the liquid charge.
2). Purge the air from the charge hose.
Open the valve at the bottom of the cylinder and press the check valve on the charge set to purge the air (be careful of the liquid refrigerant).
3) Put the charging cylinder onto the electronic scale and record the weight.
4) Operate the air conditioner at the cooling mode.
5) Open the valves (Low side) on the charge set and charge the system with liquid refrigerant.
6).When the electronic scale displays the proper weight (refer to the table), disconnect the charge hose from the 3way valve’s service port immediately and turn off the air conditioner before disconnecting the hose.
7). Mount the valve stem caps and the service port
Use torque wrench to tighten the service port cap to a torque of 18N.m.
18
Be sure to check for gas leakage.
6.3.4 Adding the refrigerant after running the system for many years
Electronic scale
Procedure:
1). Connect the charge hose to the 3-way service port, open the 2-way valve and the
3-way valve.
Connect the charge hose to the valve at the bottom of the cylinder. If the refrigerant is
R410A, make the cylinder bottom up to ensure liquid charge.
2). Purge the air from the charge hose.
Open the valve at the bottom of the cylinder and press the check valve on the charge set to purge the air (be careful of the liquid refrigerant).
3) Put the charging cylinder onto the electronic scale and record the weight.
4) Operate the air conditioner at the cooling mode.
5) Open the valves (Low side) on the charge set and charge the system with liquid refrigerant.
6).When the electronic scale displays the proper weight (refer to the gauge and the pressure of the low side), disconnect the charge hose from the 3way valve’s service port immediately and turn off the air conditioner before disconnecting the hose.
7). Mount the valve stem caps and the service port
19
Use torque wrench to tighten the service port cap to a torque of 18N.m.
Be sure to check for gas leakage.
6.3.5 Re-installation while the indoor unit need to be repaired
1. Collecting the refrigerant into the outdoor unit
Procedure
1). Confirm that both the 2-way and 3-way valves are set to the opened position
Remove the valve stem caps and confirm that the valve stems are in the opened position.
Be sure to use a hexagonal wrench to operate the valve stems.
2). Connect the charge hose with the push pin of handle lo to the 3-way valves gas service port.
3). Air purging of the charge hose.
Open the handle Lo valve of the manifold valve slightly to purge air from the charge hose for 5 seconds and then close it quickly.
4). Set the 2-way valve to the close position.
5). Operate the air conditioner at the cooling cycle and stop it when the gauge indicates 0.1MPa.
6). Set the 3-way valve to the closed position immediately
Do this quickly so that the gauge ends up indicating 0.3 to 0.5Mpa.
Disconnect the charge set, and tighten the 2-way and 3way valve’s stem nuts.
Use a torque wrench to tighten the 3-way valves service port cap to a torque of
18N.m.
Be sure to check for gas leakage.
20
2. Air purging by the refrigerant
Procedure:
1). Confirm that both the 2-way and 3-way valves are set to the closed position.
2). Connect the charge set and a charging cylinder to the service port of the 3-way valve
Leave the valve on the charging cylinder closed.
3). Air purging.
Open the valves on the charging cylinder and the charge set. Purge the air by loosening the flare nut on the 2way valve approximately 45’ for 3 seconds then closing it for 1 minute; repeat 3 times.
After purging the air, use a torque wrench to tighten the flare nut on the 2-way valve.
4). Check the gas leakage
Check the flare connections for gas leakage.
5). Discharge the refrigerant.
Close the valve on the charging cylinder and discharge the refrigerant by loosening the flare nut on the 2way valve approximately 45’ until the gauge indicates 0.3 to 0.5
Mpa.
6). Disconnect the charge set and the charging cylinder, and set the 2-way and 3-way valves to the open position
Be sure to use a hexagonal wrench to operate the valve stems.
7). Mount the valve stems nuts and the service port cap
Be sure to use a torque wrench to tighten the service port cap to a torque 18N.m.
Be sure to check the gas leakage.
21
6.3.6 Re-installation while the outdoor unit need to be repaired
1. Evacuation for
the whole system
Procedure:
1).
Confirm that both the 2-way and 3-way valves are set to the opened position.
2). Connect the vacuum pump to 3-way valve
’s service port.
3). Evacuation for approximately one hour. Confirm that the compound meter indicates -0.1Mpa.
4). Close the valve (Low side) on the charge set, turn off the vacuum pump, and confirm that the gauge needle does not move (approximately 5 minutes after turning off the vacuum pump).
5). Disconnect the charge hose from the vacuum pump.
2. Refrigerant charging
22
Electronic scale
Procedure:
1). Connect the charge hose to the charging cylinder, open the 2-way valve and the
3-way valve
Connect the charge hose which you disconnected from the vacuum pump to the valve at the bottom of the cylinder. If the refrigerant is R410A, make the cylinder bottom up to ensure liquid charge.
2). Purge the air from the charge hose
Open the valve at the bottom of the cylinder and press the check valve on the charge set to purge the air (be careful of the liquid refrigerant).
3) Put the charging cylinder onto the electronic scale and record the weight.
4). Open the valves (Low side) on the charge set and charge the system with liquid refrigerant
If the system cannot be charge with the specified amount of refrigerant, or can be charged with a little at a time (approximately 150g each time) , operating the air conditioner in the cooling cycle; however, one time is not sufficient, wait approximately 1 minute and then repeat the procedure.
5).When the electronic scale displays the proper weight, disconnect the charge hose from the 3way valve’s service port immediately
If the system has been charged with liquid refrigerant while operating the air conditioner,
23
turn off the air conditioner before disconnecting the hose.
6). Mounted the valve stem caps and the service port
Use torque wrench to tighten the service port cap to a torque of 18N.m.
Be sure to check for gas leakage
6.4 Drain Pipe of The Indoor Unit
1. Make sure the drain pipe is connected to the outdoor side downward;
2.The hard polyvinyl chloride(PVC)plastic pipe (external diameter 26 mm) sold is the market is suitable for the attached soft drain pipe;
3.Please connect the Soft Drain Pipe with the Drain Pipe, then fix it with band;
4.If you have to connect the Drain Pipe indoors, to avoid condensing caused by air intake, you must cover the pipe with heat-insulation material (polyethylene with Specific Gravity of
0.03, at least 9 mm in thickness), and use Glue Band to fix it.
5.After the Drain Pipe has been connected, please check if the water drains out of the pipe efficiently and has no leakage.
6.Refrigerant pipe and Drainpipe should be heat-insulated to avoid condensing and water-dropping later on.
6.5 Wiring
Please refer to the Wiring Diagram.
Note: The power supply of the air conditioner is different according to the models. Please refer to the WIRING DIAGRAM pasted on the indoor and outdoor units before wire connection.
Model Power supply
Input Rated Amp
(Switch/Fuse)
Power Cord Size
AWSI-SBF048-N11
380-420V~ 50Hz 32/25A
≥2.5mm
2
AWAU-YSF048-H13
24
NOTE: The cable size and the current of the fuse or switch are determined by the maximum current indicated on the nameplate which located on the side panel of the unit.
Please refer to the nameplate before selecting the cable, fuse and switch.
6.6 Test run
Perform test operation after completing gas leak and electrical safety check. The test operation time should last more than 30 minutes.
1. Open the panel and lift the panel up to angle which remains fixed. Do not lift the panel any further when it stops with a "click" sound.
2. Press the manual switch button twice until the operation indicator lights, the unit will operate on manual cool mode.
3.
Check if all the functions works well while testing the air conditioner. Especially check whether the drainage of indoor unit is smooth or not.
4.
Press the manual switch button again till the operation indicator turns dark after finishing the test operation and the unit stops operation.
25
7. External view and display
7.1 External view
This unit consists of indoor unit and outdoor unit.
Note:
All the pictures in this manual are for explanation purpose only.
They may be slightly different from the air conditioner you purchased (depend on model).
The actual shape shall prevail.
26
7.2 Control Panel
Control Buttons and Functions
Indicators
27
Operation buttons
1.ON/OFFbutton:
Operation starts when this button is pressed and stops when you press the button again.
2.MODEbutton:
Press this button to select the appropriate operating mode. Each time the button is pressed, the operation mode is shifted in the direction of the arrow:
AUTO COOL DRY HEAT FAN
3.FAN SPEED button: This button is used to select the desired fan speed. Each time you push the button, a fan speed is shifted in the direction of the arrow:
AUTO LOW MED HIGH
4.ADJUST button:
a.Temperature adjust: Press the "▲"and"▼" to adjust the temperature in a range of 17℃
~30℃. b.Timer adjust: Adjust the timer on/off time under the Timer setting mode(0~24hs). c.Auxiliary function selection: Select the desired auxiliary function by pressing "▲"and"▼" button. d.Under the Test Running mode, press "▲"and"▼"to check information about T1, T2, T3,
P4 , P5 and P9 (if no protection function occurs, the code is shifted). e.Under malfunction condition: Press the "▲"and"▼" to check the malfunction code
E1,E2, E3 ,E6 and E9(details refer to TROUBLESHOOT).
5.AUXILIARY FUNCTION button:
Use this button to select or cancel the auxiliary feature.Press this button, then press the ADJUST"▲"and"▼"button to select the desired feature. Each time the button is pressed, the mode is shifted in the direction of the arrow:
When press the "▲" button:
When press the "▼" button:
Once the desired feature is established, press the AUXILIARTY FUNCTION button again to register .
6.TEST RUNNING button:
This button is specially designed for maintenance technicians.
Press this button to perform test running operation, press it again to stop the operation.
The test running operation will last 30 minutes regardless of the setting temperature.
Press the ADJUST button to check the protective code of T1,T2 and T3.
7.
LOCK button: When you press the LOCK button the first time, all the current settings are locked in but the remote controller operation is available. And the LOCK indicator ( ) illuminates. Push it again to cancel the LOCK mode.
28
8. Operation characteristics
Mode
Temperature
Room temperature
Outdoor temperature
Cooling operation
17℃~32℃
-7℃~43℃
Heating operation
0℃~30℃
-7℃~24℃
Drying operation
17℃~32℃
18℃~ 43℃
CAUTION:
1. If air conditioner is used outside of the above conditions, certain safety protection features may come into operation and cause the unit to function abnormally.
2. Room relative humidity less than 80%. If the air conditioner operates in excess of this figure, the surface of the air conditioner may attract condensation. Please sets the vertical air flow louver to its maximum angle (vertically to the floor), and set HIGH fan mode.
3. Optimum performance will be achieved within this operating temperature.
29
9. Electronic function
9.1 Main data Introduction
T1: Room Air Thermistor (RAT)
T2: Indoor Coil Thermistor (ICT)
T3: Outdoor Coil Thermistor (OCT)
T4: Outdoor Air Thermistor (OAT)
T5: Compressor Discharge Thermistor (CTT)
9.2
Main Protection
8.2.1 Time delay for the compressor start-up
At the beginning of energizing or after the stop of the compressor, certain time delay will be needed to start the compressor.
When switching over between cooling/heating/dehumidifying mode, the compressor stops automatically.
8.2.2 Sensor protection at open circuit and breaking disconnection.
8.2.3 Phase check function
If the phase seq uence is detected wrong or lack of 1 or 2 phase, the unit won’t start and there is error code displayed on outdoor PCB.
9.3 Operation Modes and Functions
9.3.1 Heating Mode
9.3.1.1 Four-way valve opens at once, while defrosting process closes.
9.3.1.2 Compressor and outdoor fan running rules:
Once the compressor starts up, it will follow the below rules:
T1-TS
Off
0
-1
On
When compressor is on, outdoor fan will follow the below rules::
Fan(below): When compressor is on, the outdoor fan runs all the time.
Fan(above):
30
T4
18
Off
16
On
9.3.1.3 Indoor fan running rules:
When the compressor is on, the indoor fan can be set to high/(med)/low/auto. And the anti-cold wind function has the priority.
Auto fan action:
T1-Ts
Low
-2
-3
Medium
-4
-5
High
9.3.1.4 Defrost (only available to heating mode)
---Defrosting Conditions
Starting Of Defrosting Condition (meet one of the following is ok):
(1)Accumulated time when temperature of outdoor heat exchanger coil T3 is below 3°C reaches to 40 minutes, then consecutive 3 minutes less than -5 degrees (Just for the
AC is turn on , whether or not the heating mode the temperature was detected, start to statistical time when reach the temperature condition . Shut down or defrosting calculate time again).
(2) Accumulated time when temperature of outdoor heat exchanger coil T3 is below 3°C reaches to 60 minutes, then consecutive 3 minutes less than -4 degrees (Just for the
AC is turn on , whether or not the heating mode the temperature was detected, start to statistical time when reach the temperature condition . Shut down or defrosting calculate time again).
(3) Accumulated time when temperature of outdoor heat exchanger coil T3 is below 3°C reaches to 80 minutes, then consecutive 3 minutes less than -2 degrees (Just for the
AC is turn on , whether or not the heating mode the temperature was detected, start to statistical time when reach the temperature condition . Shut down or defrosting calculate time again).
(4) Under evaporator high temperature protection, the accumulated time when outdoor fan motor is off and compressor is on reaches up to over 90 minutes .( Shut down or defrosting or T3 is over 15°C, calculate time again.)
31
--- Defrosting Action
Four-way valve, indoor fan, outdoor fan are shut down. Compressor keeps on.
--- Ending Of Defrosting Condition (meet one of the following is ok):
(1)Time of defrosting lasts 10 minutes.
(2) Temperature of outdoor coil T3 is up to 8°C and continues to 80 seconds.
(3) Temperature of outdoor coil T3 is up to 15°C.
9.3.1.5 High evaporator coil temp.T2 protection:
Model
AWSI-SBF048-N11
TE7
65
TE8
58
TE9
51
9.3.2 Cooling Mode
9.3.2.1 Four-way valve is closed.
If four-way valve is open before the machine enters cooling mode, then four-way valve will be closed at the first time, the compressor starts under the cooling mode.
9.3.2.2 Compressor and outdoor fan running rules
Once the compressor starts up, it will follow the below rules:
32
T1-Ts
1
0
On
Off
When compressor is on, outdoor fan will follow the below rules::
Fan(below): When compressor is on, the outdoor fan runs all the time.
Fan(above):
T3
33
On
30
Off
9.3.2.3 Indoor fan running rules
In cooling mode, indoor fan runs all the time and the speed can be selected as high, medium, low and auto.
The auto fan:
5.0
High
4.0
Medium
3.0
2.0
Low
9.3.2.4 Low evaporator coil temperature T2 protection
AC will enter T2 protection if any of the following conditions is satisfied.
Condition 1:
33
T2
T2CoolExit
On
T2CoolIn
Off
When the evaporator coil temp.T2 keeps lower than T2CoolIn for 30 minutes, the compressor and outdoor fan will shut off. When T2 is higher than T2CoolExit, the compressor and outdoor fan will restart up.
Condition 2:
T2
On
T2CoolExit
T2CoolIn-2
Off
When the evaporator coil temp.T2 keeps lower than T2CoolIn-2 for 20 minutes, the compressor and outdoor fan will shut off. When T2 is higher than T2CoolExit, the compressor and outdoor fan will restart up.
Condition 3:
T2
On
T2CoolExit
T2CoolIn-4
Off
When the evaporator coil temp.T2 keeps lower than T2CoolIn-4 for 8 minutes, the compressor and outdoor fan will shut off. When T2 is higher than T2CoolExit, the compressor and outdoor fan will restart up.
9.3.2.5 Condenser high temperature T3 protection
When T3≥62℃ for 3 seconds, the compressor will shut off. When T3 <49℃,the compressor will restart.
34
9.3.3 Dehumidifying Mode
9.3.3.1 Indoor fan speed is low.
9.3.3.2 Four-way valve is closed, the compressor and outdoor fan will operate the same as in cooling mode.
9.3.4 Auto Mode
9.3.4.1. Under auto mode, the indoor fan is set to be auto and the temperature is 24°C.
9.3.4.2 When entering auto mode, the heating, fan only or cooling operation will be automatically chosen according to the room temperature T1 and the set temperature Ts.
Condition Mode
T1-Ts>1°C
-1°C≤ T1-Ts≤1°C
T1-Ts<-1°C
Cooling
Fan
Heating(fan for cooling only type)
9.3.4.3. If certain condition is met, then the corresponding protective function will be executed.
9.3.5 Fan Only Mode
9.3.5.1 Temperature setting function is disabled, and no setting temperature is displayed.
9.3.5.2 Under this mode, four-way valve, compressor and outdoor fan are shut down.
9.3.5.3 High/Low/Auto fan can be switched over through manual control. Auto fan will be controlled in line with cooling auto fan with temperature set to be 24°C.
9.4 Other Functions
9.4.1 LCD display
Mode, Set temp, fan speed, time, timer, protection etc.
9.4.2 Timer
The machine should be provided with max. Interval of 24h and min. resolution ratio of 30 minutes.
35
10.Trouble shooting
10.1 Self-diagnosis
P12
E1
E2
E3
E4
E5
E10
E13
E14
E15
EC
HS
Codes
P4
P5
P7
P9
P10
P11
Contents
Protection of temperature of indoor evaporator
Protection of temperature of outdoor condenser
Compressor discharge temperature protection
Protection of anti-cold wind
Low pressure protection
High pressure protection
Current overload protection
Open- or short-circuit of T1 temperature sensor
Open- or short-circuit of T2 temperature sensor
Open- or short-circuit of T3 temperature sensor
Open- or short-circuit of T4 temperature sensor
Communication malfunction between indoor unit and outdoor unit
Low pressure failure of compressor
Lack of phase
Default phase of compressor
Indoor fan speed is out of control
Refrigerant Leakage Detection
Defrosting
36
10.2 LEDs for the indication of outdoor trouble
Their codes are listed in the following table:
LED2(green) LED3(yellow) LED4(red) Contents
On
Off
Off
On
Off
Off
OK
Standby
Off
Off
Off
Off
Flash
On
Off
Flash
Flash
Off
Off
Off
Flash Lack of phase
Off Phase sequence error
Flash Indoor / outdoor units communication error
On
Off
On
Off
Open- or short-circuit of T3 temperature sensor
Open- or short-circuit of T4 temperature sensor
Temperature protection of compressor discharge
High pressure protection Flash
Flash
Off
Flash
Flash
Off
Flash
Flash
Flash
On
On
Low pressure protection
Overload of current
High temperature protection of condenser
Flash Flash
Flash Fan jump selection error
37
10.3 Troubles and Solutions
Before calling for service, please review the following list of common problems and solutions.
Problem
Air conditioner does not operate at all
Possible Cause
Power failure
The power supply is disconnected.
Solutions
Wait for power restoring
Switch on the main power switch
The power fuse is blown.
The timer is set.
Change the fuse
Wait or cancel timer setting
Change the batteries.
Air conditioner does not cool or heat well
The batteries of the remote control are exhausted
The temperature setting is too high or too low.
The air filter is clogged with dust
The air inlet or outlet of the outdoor unit is blocked
Set a more comfortable temperature.
Clean the filter
Clear up the block
Air conditioner does not cool or heat at all
Doors or windows are open
The air inlet or outlet of the outdoor unit is blocked
Three-minute protection feature
Unappropriated temperature setting
Close the doors or windows
Clear up the block first, then begin to operate.
Wait for a while
Set the temperature properly
If you still cannot solve the problem after trying the above, pull out the power plug and call the dealer.
38
10.3.1 Open or short circuit of temperature sensor
Open or short circuit of temperature sensor
Check the connections between temperature sensor and PCB. Are the connections good?
Yes
Check the resistance value of the sensor via Appendix 1
No Correct the connections.
Is it normal?
Yes Replace indoor or outdoor PCB.
No
Replace the sensor
10.3.2 Default phase of compressor
39
10.3.3 Phase sequence error
Phase sequence error
Change the order of the wires to power supply.
Switch on the unit again.
If the problem cannot be solved, the outdoor PCB is defective
10.3.4 High temperature protection of condenser
High temperature protection of condenser
Check the resistance of the temp. sensor according to Appendix 1, is it normal?
Yes
Possible reason
1. Air or other gas in the refrigerant.
2. Heat exchanger is dirty
3. Outdoor fan or fan blade is defective
4. Outdoor unit is bad ventilation
5. Refrigerant is leakage
6. Outdoor PCB is defective
10.3.5 High pressure protection
40
No
Replace the sensor
10.3.6 Low temperature protection
Low temperature protection
Possible reason
1: The outdoor ambient temp. is low.
2: The wires are loose to the temp. sensor.
3: The temp. sensor is defective.
4: The evaporator or the filter is dirty.
5: System has block.
10.3.7 Low pressure protection
Low pressure protection
Possible reason
1: The wires are loose to the pressure switch.
2: The pressure switch is defective.
3: System has refrigerant leakage.
4: The evaporator or the filter is dirty.
41
10.3.9 Indoor / outdoor unit communication error
42
Power off, then turn on the unit 5 seconds later(reconnect the power wire).Is the error still displaying after several minutes?
Yes
Check all the wirings between indoor and outdoor, indoor PCB and outdoor PCB following the wiring diagram. Are all the wirings connected correctly?
Yes
Measure Vs, is it moving alternately between positive value and negative value?
(Vs is the voltage between S and N of outdoor unit.)
Yes
Is the wiring to the outdoor PCB connected correctly?
Yes
Change the outdoor main PCB.
No
Is the wiring to the indoor PCB connected correctly?
Yes
Change the indoor main PCB.
Power on. Is the error extinguished?
No
Change the indoor main PCB.
Power on. Is the error extinguished?
No
Change the outdoor main PCB.
43
10.3.10 Refrigerant Leakage Detection
Shut off the power supply and turn it on 5 seconds later. Is it still displaying the error code?
Yes
Is there cool air blowing out from indoor air outlet?
Yes
No
Is there any leakage? Especially the connection parts, such as the gas valve and the liquid valve.
No
Yes
Is there any block i n g ? (Such as the capillary or the welded points of the pipes.)
Yes
Clear the blocking.
Check if T2 sensor is well fixed. Correct the installation or replace T2 sensor. Does the problem remain again?
Yes
Replace indoor PCB.
Repair the leakage and recharge the refrigerant.
44
10.3.11 Indoor fan speed has been out of control
Shut off the power supply and turn it on 5 seconds later. Is it still displaying the error code?
Yes
Shut off the power supply, rotate the fan by hand.
Does it rotate properly?
No
No
The unit operates normally.
Find out the cause and have it solved. For example, check whether the fan is blocked or the bearing is broken?
Yes
Check the wires of fan motor. Are all the connections good?
Yes
Check whether the fan motor is normal through index 1?
No
No Correct the connections.
Replace the fan motor
If the malfunction is still existing, replace the main PCB
45
Index 1:
1 DC Fan Motor(control chip is in PCB)
1) Release the UVW connector. Measure the resistance of U-V, U-W, V-W. If the resistance is not equal to each other, the fan motor must has problems and need to be replaced.
46
10.3.12
Temperature protection of compressor discharge
Temperature protection of compressor discharge
Check whether the compressor discharge temp. is more than 115°C ?
Yes
No
Check whether the wiring connection is right between compressor discharge temp. sensor and PCB according to wiring diagrams?
Yes
Judge: The discharge temp. sensor is broken
No
Check whether the refrigerant is leak
Yes Stop leaking and add refrigerant
Correct the wiring connection
Method: Check whether the resistance of compressor discharge temp. sensor is right refer to the Appendix 2
Yes
Replace outdoor main board
No
Replace the compressor discharge temp. sensor
Trouble is solved
47
2
3
4
-2
-1
0
1
-5
-4
-3
-8
-7
-6
-14
-13
-12
-11
-10
-9
℃
-20
-19
-18
-17
-16
-15
12
13
14
15
16
17
18
19
8
9
10
11
5
6
7
Appendix Temp. Sensor Resistance Value Table (℃--K)
K Ohm
℃
K Ohm
℃
K Ohm
115.266
108.146
20
21
12.6431
12.0561
60
61
2.35774
2.27249
42
43
44
45
46
47
35
36
37
38
39
40
41
29
30
31
32
33
34
22
23
24
25
26
27
28
55
56
57
58
59
48
49
50
51
52
53
54
6.40021
6.13059
5.87359
5.62961
5.39689
5.17519
4.96392
4.76253
4.57050
4.38736
4.21263
4.04589
3.88673
11.5000
10.9731
10.4736
10.000
9.55074
9.12445
8.71983
8.33566
7.97078
7.62411
7.29464
6.98142
6.68355
3.73476
3.58962
3.45097
3.31847
3.19183
3.07075
2.95896
2.84421
2.73823
2.63682
2.53973
2.44677
46.5725
44.0000
41.5878
39.8239
37.1988
35.2024
33.3269
31.5635
29.9058
28.3459
26.8778
25.4954
24.1932
101.517
96.3423
89.5865
84.2190
79.3110
74.5360
70.1698
66.0898
62.2756
58.7079
56.3694
52.2438
49.3161
22.5662
21.8094
20.7184
19.6891
18.7177
17.8005
16.9341
16.1156
15.3418
14.6181
13.9180
13.2631
82
83
84
85
86
87
75
76
77
78
79
80
81
69
70
71
72
73
74
62
63
64
65
66
67
68
95
96
97
98
99
88
89
90
91
92
93
94
1.38703
1.34105
1.29078
1.25423
1.21330
1.17393
1.13604
1.09958
1.06448
1.03069
0.99815
0.96681
0.93662
2.19073
2.11241
2.03732
1.96532
1.89627
1.83003
1.76647
1.70547
1.64691
1.59068
1.53668
1.48481
1.43498
0.90753
0.87950
0.85248
0.82643
0.80132
0.77709
0.75373
0.73119
0.70944
0.68844
0.66818
0.64862
48
118
119
120
121
122
123
124
112
113
114
115
116
117
106
107
108
109
110
111
℃
100
101
102
103
104
105
132
133
134
135
136
137
138
139
125
126
127
128
129
130
131
0.44699
0.43482
0.42304
0.41164
0.40060
0.38991
0.37956
0.36954
0.35982
0.35042
0.3413
0.33246
0.32390
K Ohm
0.62973
0.61148
0.59386
0.57683
0.56038
0.54448
0.52912
0.51426
0.49989
0.48600
0.47256
0.45957
0.31559
0.30754
0.29974
0.29216
0.28482
0.27770
0.27078
0.26408
0.25757
0.25125
0.24512
0.23916
0.23338
0.22776
0.22231
11.Exploded View and Spare Part list
Exploded View of indoor unit: AWSI-SBF048-N11
49
Spare part list of indoor unit:AWSI-SBF048-N11
No.
1
1.1
Part Name
Air inlet grille assembly
Air filter
Qty
1
BOM Code
201143700277
No.
15
Part Name
Front guard board for right side of evaporator
Qty
1
BOM Code
201243700226
1 P73001090755 16 Electric heater 1 202440300402
1.2 Air filter
2
Ambient temperature sensor assembly
1 P73001090752 17 Cover assembly
1 202440120100 18
Display assembly box
1 201243700181
1 203343390109
3
4
5
7
8
9
10
11
12
Ventilation ring
Volute shell assembly
Fixing board for volute shell
6 Centrifugal fan
Brushless
Motor
Chassis
DC
Right side plate assembly cabinet of
Top assembly cover
Bottom assembly plate of cabinet plate assembly of
1 201141100002 18.1
Display assembly board
1 201343390111
1 202243700191 19 Air outlet assembly 1 201143700278
1
1
1
201240300410
201140500401
202400310114
19.1
20
21
Synchronous motor
Cover of electronic control box
Electronic control box assembly
1
1
1
202400100065
201240300654
2033437A0116
1
1
1
1
201143700276
201243700335
201143700275
201243700007
21.1
21.2
21.3
21.4
Auxiliary heater control board
Indoor control assembly main board
Inverter control board assembly
Electronic control box
1
1
1
1
201343300060
201343790046
201319903024
201243600009
1 201243700334 21.5 Reactor 1 202301000950
13 1 202301300111 21.6 Wire joint 1 202301450114
14 sensor assembly
Evaporator assembly
1 201543700140 22 Remote controller 1 203355091552
50
Exploded View of outdoor unit: AWAU-YSF048-H13
51
Spare part list of outdoor unit: AWAU-YSF048-H13
No.
1
Part Name
Ambient temperature sensor assembly
Qt y
BOM Code No. Part Name
1 202440220061 22 Supporting bar
2
3
3.1
3.1
3.2
3.3
Rear net
Condenser assembly
Condenser
Condenser
Input pipe assembly
Output pipe
1 201175690001 23
Top assembly cover
1 201575890169 24 Compressor
1
1
201575890170
201575890171
25
25.1
Discharge pipe assembly
Pressure switch
1 201675890900 25.2 Muffler
1 201675890890 26
4-ways valve assembly
4
Pipe temperature sensor assembly
1 202450200331 26.1 4-ways valve
5
6
7
8
9
10
Big Handle assembly
Rear right clapboard
Handle
Water collector
Front assembly
Valve plate clapboard
1 201248100325 26.2 Gas valve
1 201248700199 27
Liquid valve assembly
2 201148700009 27.1 Liquid valve
1
1
201148790000 28
201248700204 28.1
1 201248790014 28.2
Electronic control assembly box
Electronic installing plate
Outdoor main control board assembly
Qt y
BOM Code
1 201275690066
1
1
1
1
1
1
1
1
1
1
1
1
1
201248300242
201400710570
201675890952
202301820020
201601000041
201675790946
201600600166
201600720425
201648790268
201600740519
2033487A002
6
201248700286
201348890015
11 Chassis 1 201248700285 28.3 Wire joint
12
Partition assembly board
1 201275690068 28.3 Wire joint
13 Accumulator cylinder 1 201601000636 28.4
Fan capacitor motor
14 Fix clamp of segregator 1 201248700067 28.7 AC contactor
15 Left supporter
16 Air outlet grille
Round sticker for air outlet grille
17 Front panel
18
19
20
21
Axial flow fan
Fan motor
Supporter assembly of fan motor
Supporter of fan motor holder
1 201275690067 28.8 Transformer
2
2
2011487A0002
2011374A0005
28.9
Installation box of electric parts
Low ambinet module
1 201248700201 29 Copper nut
2
2
1
201100300045
202400401375
201248700197
30
31
32
1 201248300232 32.1
Crankcase electric heater
Discharge temperature controller
Suction pipe assembly
Pressure switch
1 202301450127
4
2
1
1
1
1
1
1
1
1
1
202301450117
202401100505
202300850045
202300900127
201145000002
201319901033
201600320002
202403101716
202301610500
2016758A017
0
202301800118
52
SERVICE MANUAL
Fixed Speed Light Commercial Series
Floor-standing
53
advertisement
* Your assessment is very important for improving the workof artificial intelligence, which forms the content of this project
Related manuals
advertisement
Table of contents
- 4 1 .Safety Precautions
- 6 2. Specification
- 7 3.Dimension
- 7 3.1 Indoor Unit
- 8 3.2 Outdoor Unit
- 9 4.Refrigerant cycle diagram
- 10 5 . Wiring diagram
- 12 6.1 Installation place
- 13 6.2 Installing
- 15 6.3 Refrigerant pipe connection
- 27 6.4 Drain Pipe of The Indoor Unit
- 27 6.5 Wiring
- 28 6.6 Test run
- 29 7.1 External view
- 30 7.2 Control Panel
- 32 8.Operation characteristics
- 33 9.Electronic function
- 39 10.Trouble shooting