advertisement
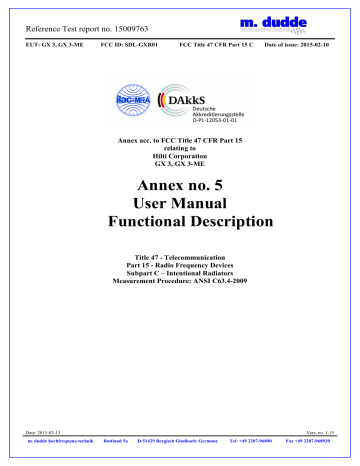
Reference Test report no. 15009763
EUT: GX 3, GX 3-ME FCC ID: SDL-GXR01 FCC Title 47 CFR Part 15 C Date of issue: 2015-02-10
Annex acc. to FCC Title 47 CFR Part 15 relating to
Hilti Corporation
GX 3, GX 3-ME
Annex no. 5
User Manual
Functional Description
Date: 2015-03-13
m. dudde hochfrequenz-technik
Title 47 - Telecommunication
Part 15 - Radio Frequency Devices
Subpart C – Intentional Radiators
Measurement Procedure: ANSI C63.4-2009
Rottland 5a D-51429 Bergisch Gladbach/ Germany Tel: +49 2207-96890
Vers. no. 1.15
Fax +49 2207-968920
Reference Test report no. 15009763
EUT: GX 3, GX 3-ME FCC ID: SDL-GXR01 FCC Title 47 CFR Part 15 C Date of issue: 2015-02-10
User Manual / Functional Description of the test equipment (EUT)
Date: 2015-03-13
m. dudde hochfrequenz-technik Rottland 5a D-51429 Bergisch Gladbach/ Germany Tel: +49 2207-96890
Vers. no. 1.15
Fax +49 2207-968920
GX 3
Original operating instructions en
Contents
1 Information about the documentation . . . . . . . . . . . . . . . . . . . . . . . . . . . . . . . . . . . . 2
1.1 Conventions . . . . . . . . . . . . . . . . . . . . . . . . . . . . . . . . . . . . . . . . . . . . . . . . . . . . . 2
1.1.1 Warnings . . . . . . . . . . . . . . . . . . . . . . . . . . . . . . . . . . . . . . . . . . . . . . . . . . 2
1.1.2 Pictograms . . . . . . . . . . . . . . . . . . . . . . . . . . . . . . . . . . . . . . . . . . . . . . . . . 2
1.1.3 Typographic emphasis . . . . . . . . . . . . . . . . . . . . . . . . . . . . . . . . . . . . . . . . . . 2
1.2 Using the operating instructions . . . . . . . . . . . . . . . . . . . . . . . . . . . . . . . . . . . . . . . . . 2
1.3 Type designation and serial number . . . . . . . . . . . . . . . . . . . . . . . . . . . . . . . . . . . . . . 3
2 Safety . . . . . . . . . . . . . . . . . . . . . . . . . . . . . . . . . . . . . . . . . . . . . . . . . . . . . . . . . 3
2.1 Intended use . . . . . . . . . . . . . . . . . . . . . . . . . . . . . . . . . . . . . . . . . . . . . . . . . . . . . 3
2.2 Safety instructions . . . . . . . . . . . . . . . . . . . . . . . . . . . . . . . . . . . . . . . . . . . . . . . . . 3
3 Description . . . . . . . . . . . . . . . . . . . . . . . . . . . . . . . . . . . . . . . . . . . . . . . . . . . . . 5
3.1 Items supplied . . . . . . . . . . . . . . . . . . . . . . . . . . . . . . . . . . . . . . . . . . . . . . . . . . . . 5
3.2 Parts and operating controls . . . . . . . . . . . . . . . . . . . . . . . . . . . . . . . . . . . . . . . . . . . 6
3.3 Fastener guide . . . . . . . . . . . . . . . . . . . . . . . . . . . . . . . . . . . . . . . . . . . . . . . . . . . 7
3.4 Fasteners . . . . . . . . . . . . . . . . . . . . . . . . . . . . . . . . . . . . . . . . . . . . . . . . . . . . . . . 7
3.5 Guidelines for use on concrete and steel . . . . . . . . . . . . . . . . . . . . . . . . . . . . . . . . . . . 7
3.6 Slider for fastener driving depth adjustment and for releasing the fastener guide . . . . . . . . . . . 7
3.7
‚RESET‘ button . . . . . . . . . . . . . . . . . . . . . . . . . . . . . . . . . . . . . . . . . . . . . . . . . . . 7
3.8 Support leg . . . . . . . . . . . . . . . . . . . . . . . . . . . . . . . . . . . . . . . . . . . . . . . . . . . . . 7
3.9 Belt hook . . . . . . . . . . . . . . . . . . . . . . . . . . . . . . . . . . . . . . . . . . . . . . . . . . . . . . . 7
3.10 Gas can . . . . . . . . . . . . . . . . . . . . . . . . . . . . . . . . . . . . . . . . . . . . . . . . . . . . . . . . 8
3.11 Indication of gas can status . . . . . . . . . . . . . . . . . . . . . . . . . . . . . . . . . . . . . . . . . . . 8
4 Technical data . . . . . . . . . . . . . . . . . . . . . . . . . . . . . . . . . . . . . . . . . . . . . . . . . . . 8
4.1 Fastening tool . . . . . . . . . . . . . . . . . . . . . . . . . . . . . . . . . . . . . . . . . . . . . . . . . . . . 8
4.2 Noise information in accordance with EN 60745 . . . . . . . . . . . . . . . . . . . . . . . . . . . . . . . 8
4.3 Total uniaxial vibration value (in z-direction) . . . . . . . . . . . . . . . . . . . . . . . . . . . . . . . . . . 8
5 Loading the fastening tool . . . . . . . . . . . . . . . . . . . . . . . . . . . . . . . . . . . . . . . . . . . 9
5.1 Loading for driving nails . . . . . . . . . . . . . . . . . . . . . . . . . . . . . . . . . . . . . . . . . . . . . . 9
5.1.1 Equipment required for driving nails . . . . . . . . . . . . . . . . . . . . . . . . . . . . . . . . . . 9
5.1.2 Loading the magazine . . . . . . . . . . . . . . . . . . . . . . . . . . . . . . . . . . . . . . . . . . 9
5.1.3 Inserting the gas can . . . . . . . . . . . . . . . . . . . . . . . . . . . . . . . . . . . . . . . . . . . 9
5.2 Loading for driving threaded studs . . . . . . . . . . . . . . . . . . . . . . . . . . . . . . . . . . . . . . . 9
5.2.1 Equipment required for driving threaded studs . . . . . . . . . . . . . . . . . . . . . . . . . . . 9
5.2.2 Inserting the single-fastener adapter . . . . . . . . . . . . . . . . . . . . . . . . . . . . . . . .
10
6
5.2.3 Inserting the gas can . . . . . . . . . . . . . . . . . . . . . . . . . . . . . . . . . . . . . . . . . .
10
Driving fasteners . . . . . . . . . . . . . . . . . . . . . . . . . . . . . . . . . . . . . . . . . . . . . . . .
10
6.1 Driving nails . . . . . . . . . . . . . . . . . . . . . . . . . . . . . . . . . . . . . . . . . . . . . . . . . . . .
10
6.2 Driving threaded studs . . . . . . . . . . . . . . . . . . . . . . . . . . . . . . . . . . . . . . . . . . . . . .
10
7 Unloading the fastening tool . . . . . . . . . . . . . . . . . . . . . . . . . . . . . . . . . . . . . . . . .
10
7.1 Removing the gas can . . . . . . . . . . . . . . . . . . . . . . . . . . . . . . . . . . . . . . . . . . . . . .
10
7.2 Unloading the magazine . . . . . . . . . . . . . . . . . . . . . . . . . . . . . . . . . . . . . . . . . . . . .
11
7.3 Removing the single-fastener adapter . . . . . . . . . . . . . . . . . . . . . . . . . . . . . . . . . . . .
11
8 Optional operating steps . . . . . . . . . . . . . . . . . . . . . . . . . . . . . . . . . . . . . . . . . . .
11
8.1 Checking the status of the gas can . . . . . . . . . . . . . . . . . . . . . . . . . . . . . . . . . . . . . .
11
8.2 Removing the magazine . . . . . . . . . . . . . . . . . . . . . . . . . . . . . . . . . . . . . . . . . . . . .
11
8.3 Fitting the magazine . . . . . . . . . . . . . . . . . . . . . . . . . . . . . . . . . . . . . . . . . . . . . . .
11
8.4 Removing the fastener guide . . . . . . . . . . . . . . . . . . . . . . . . . . . . . . . . . . . . . . . . . .
11
8.5 Inserting the fastener guide . . . . . . . . . . . . . . . . . . . . . . . . . . . . . . . . . . . . . . . . . . .
11
1
▶
Ensure that the operating instructions are with the fastening tool when it is given to other persons.
Changes and errors excepted.
1.3 Type designation and serial number
The type designation and serial number are printed on the type identification plate.
▶
Copy these details to the table below and provide this information when making an enquiry to your Hilti representative or to Hilti Service.
Product information
Type:
Generation:
Serial number:
01
2 Safety
2.1 Intended use
The intended use of the gas-actuated fastening tool (“fastening tool”) is the driving of suitable fasteners into concrete, steel, sand-lime block, concrete block masonry, rendered masonry and other materials suitable for the direct fastening technique.
Further details can be found in the Fastening Technology Manual copies of which can be obtained from a
Hilti Service Center or from the following address:
Internet: http://www.hilti.com
The fastening tool is designed for professional use in drywall construction, general construction work and in various installation trades.
The fastening tool, gas can and fasteners form a technical unit. This means that trouble-free fastening with this fastening tool can be ensured only when it is used together with the fasteners and gas cans specially manufactured for it by Hilti . The fastening and application recommendations made by Hilti apply only when this condition is observed.
This fastening tool may be used only hand held or in conjunction with the special “pole tool” extension
(accessory).
The fastening tool may be operated, maintained and cared for only by suitably trained personnel. This personnel must be informed of any particular hazards that may be encountered.
The fastening tool and its ancillary equipment may present hazards when used incorrectly by untrained personnel or when used not as intended.
2.2 Safety instructions
Working safely with the fastening tool
▶
Pressing the nosepiece of the fastening tool against a part of the body may lead to serious injury due to inadvertent firing and release of a fastener.
Never press the nosepiece of the tool against your hand or any other part of the body. When inserting/loading an application-specific type of fastener, never press the fastener or nosepiece of the tool against a hand or any other part of the body.
▶
Never point the fastening tool towards yourself or any other person.
▶
Keep your arms flexed when operating the tool (do not straighten the arms).
▶
Never use a hand or any other part of the body to pull the fastener guide back when a fastener
(e.g. soft washer, clip or clamp etc.) is inserted in the nosepiece of the tool . This presents an increased risk of accident.
▶
Stay alert, watch what you are doing and use common sense when operating the fastening tool.
Do not use the fastening tool while you are tired or under the influence of drugs, alcohol or medication.
A moment of inattention while operating the fastening tool may result in serious personal injury.
▶
When pulling back the nail pusher, always take care to ensure that it engages.
▶
When disengaging the nail pusher, do not release it and allow it to jump forward. Guide it forward slowly.
There is a risk of pinching the fingers.
▶
Do not attempt to drive fasteners into materials that are too hard , such as welded steel or cast steel.
Attempting to drive fasteners into these materials may lead to malfunctions, incorrectly driven fasteners or breakage of fasteners.
3
▶
Do not attempt to drive fasteners into materials that are too soft , such as wood or drywall/gypsum board. Attempting to drive fasteners into these materials may lead to malfunctions and fasteners being driven incorrectly or driven right through the material.
▶
Do not attempt to drive fasteners into materials that are too brittle , such as glass or tiles. Attempting to drive fasteners into these materials may lead to malfunctions, fasteners being driven incorrectly and may cause the material to shatter.
▶
Before driving fasteners, check that there is no risk of injuring persons or of damaging objects present behind or below the working surface.
▶
Pull the trigger only when the fastening tool is pressed against the working surface in such a way that the fastener guide is pushed into the nose of the tool as far as it will go.
▶
Always wear gloves if you have to carry out maintenance work on the fastening tool while it is still hot.
▶
If fasteners are driven at a high rate or if the tool used for a long period, surfaces of the tool beyond the grip areas may get hot. Wear protective gloves to avoid burning injuries.
▶
If the fastening tool overheats, remove the gas can and allow the tool to cool down. Do not exceed the specified maximum fastener driving rate.
▶
Driving fasteners may cause flying fragments or result in parts of the nail strip material being forcibly ejected from the tool. Flying fragments present a risk of injury to the body and eyes. Wear eye protection and a hard hat. Other persons in the vicinity must also wear eye protection and a hard hat.
▶
Wear your personal protective equipment and always wear protective glasses. Depending on the application and type of tool in use, wearing personal protective equipment such as a dust mask, non-slip safety footwear, hard hat and ear protection reduces the risk of injury.
▶
Wear suitable ear protection. Fasteners are driven through ignition of a gas/air mixture. The resulting noise exposure may cause damage to the hearing. Other persons in the vicinity should also wear suitable hearing protection.
▶
Observe the application guidelines concerning minimum fastener spacing distances and distances from edges of the material ( → page 7).
▶
When driving a fastener, always hold the fastening tool securely and at right angles to the supporting material. This helps to avoid deflection of the fastener by the supporting material.
▶
Never drive a second fastener at the same location. This may lead to breakage or jamming of fasteners.
▶
Alway remove the gas can and ( → page 10) empty the magazine ( → page 11) before changing the magazine, before cleaning, servicing or maintenance work on the tool, before storage or transport and before leaving the fastening tool unattended.
▶
To ensure that the fastening tool functions faultlessly and as intended, always check the tool and accessories for possible damage before use. Check that moving parts function faultlessly, without sticking, and that no parts are damaged. In order to ensure faultless operation of the tool, all parts must be fitted correctly and must meet the necessary requirements. Damaged protective devices or other parts must be properly repaired or replaced by Hilti Service unless otherwise stated in the operating instructions.
▶
Have the fastening tool repaired only by trained and qualified specialists using genuine Hilti spare parts.
This will ensure that the safety of the fastening tool is maintained.
▶
Tampering with or modification of the fastening tool is not permissible.
▶
Do not use the fastening tool where there is a risk of fire or explosion.
▶
Take influences of the surrounding area into account. Do not expose the fastening tool to rain or snow and do not use it in damp or wet conditions.
▶
Use the fastening tool only in well-ventilated working areas.
▶
Select the correct combination of fastener guide and fastener. The wrong combination may result in damage to the tool and in reduced fastening quality.
▶
Always observe the application guidelines → page 7.
Hazards presented by electricity
▶
Before beginning work, check the working area (e.g. using a metal detector) to ensure that no concealed electric cables or gas and water pipes are present.
▶
Hold the fastening tool only by the insulated grip when working in areas where fasteners may be driven inadvertently into concealed electric cables. Contact with a live electric cable may cause metal parts of the tool also to become live, leading to a risk of electric shock.
Instructions for handling the propellant gas
▶
Observe the instructions printed on the gas can and in the accompanying information.
▶
Escaping gas is harmful to the lungs, skin and eyes. Keep your face and eyes away from the gas can compartment for up to about 10 seconds after removing the gas can.
4
▶
Do not operate the gas can valve manually.
▶
If a person has inhaled gas, take the person into the open air and place the person in a comfortable position.
▶
Should a person becomes unconscious, bring the person into a well-ventilated area and place the person in a stable recovery position (i.e. lying on the side). If the person is not breathing, administer artificial respiration and, if necessary, supply oxygen.
▶
After eye contact with gas, rinse the open eyes thoroughly under running water for several minutes.
▶
After skin contact with gas, wash the contact area carefully with soap and warm water. Subsequently apply a skin cream.
▶
Consult a doctor if necessary.
General instructions concerning personal safety
▶
Take care to adopt an ergonomic body position. Work from a safe stance and take care to stay in balance at all times. This will allow you to control the fastening tool better, even in unexpected situations.
▶
Keep other people away from the working area, especially children.
3 Description
3.1 Items supplied
1 gas-actuated fastening tool with fastener guide, 1 toolbox, 1 operating instructions
Accessories and consumables
Approved accessories and consumables (gas cans and fasteners) can be found here:
Internet: http://www.hilti.com
5
3.2 Parts and operating controls
@
;
=
Grip
Slider for fastener driving depth adjustment and for releasing the fastener guide
Fastener guide
6
%
&
(
)
Support leg
Magazine
Type identification plate
Gas can compartment
+
§
/
:
·
Gas can compartment cover
Cooling air slots
Magazine lockbutton
Trigger
‚RESET‘ button
$
£
|
¡
Nail pusher
Belt hook
Gas can status indicator
Inlet/outlet valve
3.3 Fastener guide
The fastener guide holds the studs or, respectively, guides the nails and, when the tool is fired, thus directs the fasteners into the supporting material at the desired position. Application-specific fastener guides (IF or ME) are available for the ‚GX 3‘ and ‚GX 3-ME‘ fastening tools (see type identification plate for exact designation).
3.4 Fasteners
Two types of fastener can be driven by the fastening tool: nails and threaded studs. Additional fastening components, which can be inserted in the fastener guide, are also available for various applications.
3.5 Guidelines for use on concrete and steel
Information about national regulations, and the Fastening Technology Manual containing further information, are available from the Hilti marketing organization responsible for your location.
The Fastening Technology Manual can also be obtained from:
Internet: http://www.hilti.com
3.6 Slider for fastener driving depth adjustment and for releasing the fastener guide
The slider can be used to reduce the depth to which the fastener is driven. In the «EJECT» position, it releases the fastener guide for removal.
Status
«+»
«»
«EJECT»
Meaning
• Standard fastener driving depth
• Reduced fastener driving depth
• Fastener guide release
3.7 ‚RESET‘ button
After driving a fastener, under certain circumstances, the fastener guide may not return to its outset position.
This is caused by the piston being incorrectly positioned. The incorrect piston position can be remedied by pressing the ‚RESET‘ button.
Status
‚RESET‘ button projects from the tool casing. Its white edge is visible.
‚RESET‘ button is flush with the tool casing.
Meaning
• Piston position is incorrect
• Piston position is correct
3.8 Support leg
On an even working surface, the support leg makes it easier to hold the fastening tool perpendicular as attention then only has to be paid to lateral alignment. On an uneven or undulating surface it may be necessary to remove the support leg in order to allow the fastener guide to be held perpendicular to the working surface.
3.9 Belt hook
The belt hook can be extended in two stages.
Status
First position
Second position
Meaning
• Position for attaching to a waist belt
• Position for attaching to ladders, scaffolds, platforms, etc.
7
3.10 Gas can
Note
Observe the safety instructions provided with the gas can!
In order to operate the fastening tool, the gas can must be inserted in the gas can compartment.
The gas can status can be read from the LED display after pressing the ‚GAS‘ button.
The gas can must be removed before breaks between working, before maintenance and before transporting or storing the fastening tool.
3.11 Indication of gas can status
After pressing the ‚GAS‘ button, the LED display indicates the status of the gas can.
Status
All four LEDs light green.
Three LEDs light green.
Two LEDs light green.
One LED lights green.
One LED blinks green.
One LED lights red.
Meaning
• Level is approx. 100 %.
• Level is approx. 75 %.
• Level is approx. 50 %.
• Level is approx. 25 %.
• Level is below 10 %. Replacement of the gas can is recommended.
• There is either no gas can in the fastening tool, the wrong type of gas can is fitted or the can is empty.
Note
Even when the level is indicated as “empty”, the gas can, for technical reasons, still contains a little gas.
4 Technical data
4.1 Fastening tool
Weight (empty)
Application temperature, ambient temperature
Maximum fastener length
Fastener diameter
3.9 kg
(8.60 lb)
−10 ℃ …45 ℃
(14.0 ℉ …113.0 ℉)
≤ 39 mm
(≤ 1.54 in)
• 2.6 mm (0.102 in)
• 3 mm (0.12 in)
Compression stroke
Magazine capacity in strips of 10 nails (Magazine capacity)
40 mm
(1.57 in)
1 …4
Maximum fastener driving frequency (Fasteners per hour) 1,200
4.2 Noise information in accordance with EN 60745
Sound (power) level (L
WA
)
Uncertainty for the sound power level (K
Emission sound pressure level (L pA
)
WA
)
Uncertainty for the sound pressure level (K pA
)
0 dB(A)
0 dB(A)
0 dB(A)
0 dB(A)
4.3 Total uniaxial vibration value (in z-direction)
The vibration emission level stated in these instructions has been measured in accordance with a standardized test given in EN 792-13/ISO 11148-13 and may be used to compare one direct fastening tool with another.
8
It may be used for a preliminary assessment of exposure. The declared vibration level represents the main applications of the direct fastening tool. However, if the direct fastening tool is used for different applications, with different items of equipment or accessories or is poorly maintained, the vibration level may vary. This may significantly increase the exposure to vibration over the total working period. An accurate estimation of exposure to vibration should also take into account the times when the tool is not actually in use. This may significantly reduce the exposure to vibration over the total working period.
Identify additional safety measures to protect the operator from the effects of vibration such as: maintenance of the direct fastening tool and its additional equipment or accessories, keeping the hands warm, organization of work patterns.
Driving fasteners (a h
)
Uncertainty for the given vibration value (K)
0 m/s²
0 m/s²
5 Loading the fastening tool
5.1 Loading for driving nails
5.1.1 Equipment required for driving nails
Nails are fed through the magazine in strip form (ready-to-use strips of nails).
Note
When driving nails there must be no single-fastener adapter present in the tool .
5.1.2 Loading the magazine
1. Pull the nail pusher back until it engages.
2. Slide the nail strips into the magazine as far as they will go.
Note
Strips of short nails could be inadvertently inserted the wrong way round. With short nails, take care to ensure that the tips of the nails point towards the nose of the tool.
WARNING
Risk of pinching fingers!
Fingers could be pinched when the nail pusher is released.
▶
When disengaging the nail pusher, do not release it and allow it to jump forward. Guide it forward slowly as far as it will go.
3. Release the nail pusher and guide it forward as far as it will go.
5.1.3 Inserting the gas can
1. Open the gas can compartment cover.
2. Remove the cap from the gas can.
Note
Keep the cap so that it can be used to close the gas can securely when it is removed from the tool, e.g. when unloading and for transport.
3. Slide the gas can into the gas can compartment, valve first, so that the gas can clip enters the opening for the clip and engages securely.
4. Close the gas can compartment cover.
5. Without pulling the trigger, firmly press the nose of the fastening tool twice against the working surface in order to force the air out of the gas supply tubes.
5.2 Loading for driving threaded studs
5.2.1 Equipment required for driving threaded studs
Threaded studs must be inserted singly in the fastener guide from the front. An adapter is required for driving single fasteners. Each package of threaded studs contains an adapter for driving single fasteners.
9
Note
In order to drive threaded studs, the magazine must first be emptied and an adapter for driving single fasteners inserted.
5.2.2 Inserting the single-fastener adapter
▶
Insert the single-fastener adapter ( → page 12).
5.2.3 Inserting the gas can
▶
Insert the gas can ( → page 9).
6 Driving fasteners
6.1 Driving nails
WARNING
Risk of injury!
Pressing the nosepiece of the fastening tool against a part of the body may lead to serious injury due to inadvertent firing and release of a fastener.
▶
Never press the nosepiece of the tool against your hand or any other part of the body.
1. Check the fastener driving depth setting.
2. Bring the nosepiece of the fastening tool and the support leg into contact with the working surface.
3. Press the nose of the fastening tool against the working surface as far as it will go (fully compressed).
4. Check that the nose of the tool is perpendicular to the working surface.
5. Pull the trigger to drive a fastener.
Note
It is not possible to drive a fastener if the nose of the tool is not pressed fully against the working surface.
6. Lift the fastening tool completely away from the working surface after driving a fastener.
7. Remove the gas can ( → page 10) and empty the magazine ( → page 11) when work with the fastening tool is finished or before leaving the tool unattended.
6.2 Driving threaded studs
WARNING
Risk of injury!
High risk of injury caused by inadvertently driving a fastener into a part of the body.
▶
When inserting fasteners, never press the fastener guide against a hand or other part of the body.
1. Check the fastener driving depth setting.
2. Insert a stud in the fastener guide.
3. Bring the nosepiece of the fastening tool and the support leg into contact with the working surface.
4. Press the nose of the fastening tool against the working surface as far as it will go (fully compressed).
5. Check that the nose of the tool is perpendicular to the working surface.
6. Pull the trigger to drive a fastener.
Note
It is not possible to drive a fastener if the nose of the tool is not pressed fully against the working surface.
7. Remove the gas can when work with the fastening tool is finished or before leaving the tool unattended
( → page 10).
7 Unloading the fastening tool
7.1 Removing the gas can
1. Open the gas can compartment cover.
10
2. Press the gas can clip to release the gas can.
3. Remove the gas can from the gas can compartment.
4. Fit the cap on the gas can.
5. Close the gas can compartment cover.
7.2 Unloading the magazine
1. Pull the nail pusher back until it engages.
2. Remove all nail strips from the magazine.
WARNING
Risk of pinching fingers!
Fingers could be pinched when the nail pusher is released.
▶
When disengaging the nail pusher, do not release it and allow it to jump forward. Guide it forward slowly as far as it will go.
3. Release the nail pusher and guide it forward as far as it will go.
7.3 Removing the single-fastener adapter
▶
After driving the fasteners, remove the single-fastener adapter ( → page 12) from the fastening tool.
8 Optional operating steps
8.1 Checking the status of the gas can
1. Without pressing the fastening tool against the working surface, press the ‚GAS‘ button.
2. Read the gas can status from the display. → page 8
8.2 Removing the magazine
1. Pull the nail pusher back until it engages.
2. Remove the loose nail strips from the magazine.
WARNING
Risk of pinching fingers!
Fingers could be pinched when the nail pusher is released.
▶
When disengaging the nail pusher, do not release it and allow it to jump forward. Guide it forward slowly as far as it will go.
3. Release the nail pusher and guide it forward as far as it will go.
4. Release the magazine locking catch.
5. Pivot the magazine about the pivot point towards the front.
6. Detach the magazine.
8.3 Fitting the magazine
1. Engage the front end of the magazine at the nose of the fastening tool.
2. Pivot the magazine towards the fastening tool.
3. Close the magazine locking catch.
8.4 Removing the fastener guide
1. Remove the gas can. → page 10
2. Move the fastener guide release slider to the «EJECT» position.
3. Remove the fastener guide.
8.5 Inserting the fastener guide
1. Remove the gas can. → page 10
2. Slide the fastener guide into the slot in the nose of the fastening tool.
3. Hold the fastener guide securely so that it cannot fall out and then press the nose of the tool (i.e. the tool with the fastener guide) against a firm surface until the fastener guide engages.
4. Check that the fastener guide has engaged.
◁
Once the fastener guide has engaged, the slider for releasing the fastener guide is again in the «+» position.
11
8.6 Removing the support leg
1. Release the support leg engaging mechanism by pressing lightly.
2. Rotate the support leg through 90°.
3. Remove the support leg.
8.7 Fitting the support leg
1. Bring the support leg into contact with the magazine at right angles and guide it into the slot.
2. Rotate the support leg through 90° relative to the magazine and allow it to engage while applying light pressure.
8.8 Inserting the single-fastener adapter
1. Remove the gas can. → page 10
2. Remove the magazine. → page 11
3. Insert the single-fastener adapter.
4. Fit the magazine. → page 11
8.9 Removing the single-fastener adapter
1. Remove the gas can. → page 10
2. Remove the magazine. → page 11
3. Remove the single-fastener adapter.
4. Fit the magazine. → page 11
9 Remedying possible malfunctions
9.1 Remedying an incorrect piston position
▶
Check the position of the ‚RESET‘ → page 7 button.
Result
• ‚RESET‘ button projects from the tool casing. Its white edge is visible.
To remedy the incorrect piston position, press the ‚RESET‘ button.
9.2 Removing foreign objects from the nose area
1. Remove the magazine. → page 11
2. Remove the fastener guide. → page 11
3. Remove all foreign objects from the nose area.
4. Insert the fastener guide. → page 11
5. Fit the magazine. → page 11
10 Care, cleaning and maintenance
10.1 Caring for the fastening tool
▶
Never operate the fastening tool if the cooling air slots are blocked.
▶
Keep the grip areas free from oil and grease.
▶
Clean the fastening tool regularly. → page 12
▶
Do not use spray devices, pressure jet washers or running water for cleaning.
▶
Do not use cleaning agents containing silicone.
▶
Do not use sprays or similar lubricating and cleaning agents.
10.2 Cleaning the fastening tool
1. Remove the gas can. → page 10
2. Unload the magazine. → page 11
3. Remove plastic fragments from the fastener guide.
4. Use a dry brush to clean the cooling air slots, taking care to prevent dirt or foreign objects entering the interior of the tool.
5. Use a damp cloth to clean the exterior of the tool.
12
10.3 Maintenance
▶
Check all external parts of the fastening tool regularly for damage and make sure that all operating controls function faultlessly.
▶
Do not use the fastening tool if parts are damaged or if operating controls do not function faultlessly.
▶
Have a defective fastening tool repaired by Hilti Service.
10.4 Checks after care and maintenance work
▶
Move the fastener driving depth adjustment slider to the «+» position.
11 Troubleshooting
Note
If the fault you are experiencing is not listed or the recommended action to be taken does not successfully solve the problem, please contact Hilti Service.
Fault
Fasteners are frequently driven to inadequate depth.
Fasteners are frequently driven too deeply.
Fasteners break.
Fasteners bend.
The fastener doesn’t hold when driven into steel.
The content of the gas can is inadequate for the number of fasteners in the package.
The tool remains compressed
(nose does not extend when pressure is released).
Possible cause
Driving power is too low.
The fasteners are too long.
The supporting material is too hard.
The inlet/outlet valve is clogged or covered over.
Driving power is too high.
The fasteners are too short.
Driving power is too low.
The fasteners are too long.
The supporting material is too hard.
The fastener guide is not held perpendicular to the working surface.
Driving power is too low.
Action to be taken
▶
Move the fastener driving depth adjustment slider to the «+» position.
▶
Use shorter fasteners.
▶
Consider using a DX fastening tool.
▶
Clean the fastening tool and check how it is held.
▶
Move the fastener driving depth adjustment slider to the «‒» position.
▶
Use longer fasteners.
▶
Move the fastener driving depth adjustment slider to the «+» position.
▶
Use shorter fasteners.
▶
Consider using a DX fastening tool.
▶
Press the nosepiece against the working surface while keeping the tool perpendicular to the surface.
▶
Move the fastener driving depth adjustment slider to the «+» position.
The fasteners are too long.
The fastener guide is not held perpendicular to the working surface.
▶
Use shorter fasteners.
▶
Press the nosepiece against the working surface while keeping the tool perpendicular to the surface.
The supporting material is too thin.
▶
Use a different fastening method.
High gas consumption due to frequent compression of the tool nosepiece without driving a fastener.
Incorrect piston position.
▶
Avoid compressing the tool nosepiece without driving a fastener.
▶
Remedy the incorrect piston position. → page 12
13
Fault
The tool remains compressed
(nose does not extend when pressure is released).
Fastener driving failure rate is too high.
Possible cause
The nail detector is jammed and the ‚RESET‘ button is not flush with the casing when pressed.
A fastener has jammed in the fastener guide.
The fastener guide is not held perpendicular to the working surface.
No fastener is driven.
The fastening tool is hot and doesn’t work even after a break.
No fastener is driven (or driven only intermittently).
A fastener cannot be removed from the fastener guide.
Wrong type of fastener used.
The supporting material is too hard.
The nail pusher was not moved forwards.
Inadequate number of nails in the magazine.
Nail transport malfunction.
Gas can is empty.
One LED lights red.
Air in the gas lines.
Foreign object in the nose area.
The fastening tool is too hot.
Electronic fault.
Action to be taken
▶
Remove foreign objects from
▶ the nose area. → page 12
Release the jammed fastener.
▶
Press the nosepiece against the working surface while keeping the tool perpendicular to the surface.
▶
Use a suitable type of fastener.
▶
Consider using a DX fastening tool.
▶
Release the nail pusher and guide it forward as far as it will go.
▶
Load the magazine. → page 9
▶
Use a different nail strip.
▶
Clean the magazine.
▶
Check the status of the gas can. → page 11
▶
Check the status of the gas can. → page 11
▶
Press the nosepiece against the working surface twice without pulling the trigger.
▶
Remove foreign objects from the nose area. → page 12
▶
Allow the fastening tool to cool down.
▶
Remove the gas can and then reinsert it. If the problem persists, use a new gas can.
▶
Allow the fastening tool to cool down.
The fastener driving rate was well above 1,200 fastenings per hour.
Ambient conditions are outside the permissible range.
The gas can temperature is outside the permissible range.
Gas bubbles have formed in the gas regulating system.
The tool was not lifted completely away from the surface after driving a fastener.
A fastener has jammed in the fastener guide.
▶
Make sure that the permissible ranges, in accordance with the technical data, are observed.
▶
Make sure that the permissible ranges, in accordance with the technical data, are observed.
▶
Remove the gas can and then reinsert it.
▶
Lift the fastening tool completely away from the working surface after driving a fastener.
▶
Release the jammed fastener.
12 Disposal
Most of the materials from which Hilti tools, appliances and devices are manufactured can be recycled.
The materials must be correctly separated before they can be recycled. In many countries, Hilti has already
14
15
**
advertisement
Related manuals
advertisement