advertisement
▼
Scroll to page 2
of
42
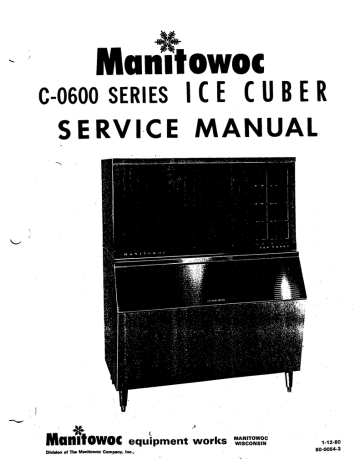
se / anITOWOC C-0600 SERIES ICE CUBER SERVICE MANUAL MANITOWS Manitowoc equipment works vi 1200 Division of The Manitowoc Company, Inc., - : 80-0054-3 MANITOWOC ICE CUBERS — C-0600 Series TABLE OF CONTENTS Forward..............oeeeoresccsceocarrecaorerrarereven. Page 1 Inspection ..........._eeceeoresccocorororecrereonar e recae Page 2 Uncrating ............0200000 0000000 a a 00 0000 0 ee see 10000000 Page 3 Location..........02020200002 0000400 ua 000 0000000 0000 0000000 Page 3 Serial & Electrical Plate................20020000000 0000000» Page 3 Removal or Installing Panels .............. coils. Page 3 Removal of Internal Packing.............e—.eeeeorerceoreo. Page 3 General Requirements .................80.0000000 00 0000006 Page 3 Electrical Rating ....... Le a ee a 0 a a 0 ae 0e es aa aa ses ue sa 000000 Page 3 Connecting Power Supply ..............0.0.00000000 00 0000000 Page 4 Connecting Water Supply .......... PP eee Page 4 Drain Connections ............eew_eeesccccssrccrorovecoce Page 4 -Check List for Starting Machine ..............ocereseveco. Page 4 Final Check List ...... aocooreacaracarevacacoA caro cgonoa Page 5 Fig. 1 Cuber Dimensions....................... cac cn ans Page S Fig. 2 Cuber with Panels Removed ....................... Page 6 Fig. 3 Compressor Compartment...........e....e.eeeore... Page 7 Fig. 4 Ice Making Section ....... rete ea Page 8 Fig. 5 Ice Making Section . | with Ice Chute 8% Curtain Removed...... reais Page 9 Fig. 6 Control Box Assembly ..................eeeee.—.. .. Page 10 Fig. 7 Water Pump Assembly .............ee.eeercccroo. Page 11 System Control & Sequence of Operation................ Page 12 Refrigeration Cycle..................... a... PRE . Pages 12-13 Operating Characteristics. .............._eoeeceor. SR Page 13 Wiring Diagram for C-0600 ...... eae Ca ea ea sa ae 0000 Page 14 Schematic-Refrigeration Cycle ................ cc oii. Page 15 Specifications. ............eoer_erecccosccerrecorereeceecan e. Page 16 Component Check-Out Procedure................. ... Pages 17-18 Control Description & Check-Out Procedure........... Pages 19-22 C-0690N Cuber with AC-0695A Remote Condenser...... Page 23 General Information, C-0600 Remote .................... Page 23 Installation, C-0600 Remote........ ne ra ace as 00000000 Pages 23-24 Fig. 8 Electrical Hook Up......0.000000000000 0001000000000 Page 24 Fig. 9 Installation Hlustration, C-0600 Remote............ Page 25 Start-Up Procedure ,...... eoacaorocracerecac een PT Page 26 System Control! % Sequence of Operation, C-0600 Remote. ........000000000000000000000 0400000 Pages 26-28 Wiring Diagram for C-O690N 0....0.0000000000000 0000000000 Page 29 Refrigeration Cycle for C-O690N............... ace ace 0e Page 30 Fig. 10 Refrigeration Schematic ...................e.. ... Page 31 Fig. 11 C-O690N Remote Cuber Compressor Comp. ..... . Page 32 Service Analysis .............. ae sea ana aan 00000 .... Pages 33-35 . Cleaning Instructions ........ 0.00.00... PA Page 35 ‘Ordering Parts... PS Page 36 Serial Number Nomenclature............... eeeeee...... Page 37 В | ‚ММаггату.................... оовоооновеовавоввоасоенаевове Раде 38 MANITOWOC ICE CUBER — C-0600 Series Page 1 FORWARD Manitowoc Equipment Works, Division of The Manitowoc Company, Inc., Manitowoc, Wisconsin, presents this Service Manual to assist the service man with information concerning CONSTRUCTION, INSTALLA- TION, and MAINTENANCE of the MANITOWOC ICE MAKER. The problems of the user and the service man have been given special emphasis in the development of the latest MANITOWOC ice Machines. If you encounter a problem which is not answered by this manual, please feel free to write or call the Service Department of the Manitowoc Equipment, Works, Division of The Manitowoc Company, inc. Manitowoc, Wisconsin, describing the problem you have encountered. The Service Department will be happy to give you particularized advice and assistance. Whenever calling or writing, please state the complete model and serial number of the ice making equipment. MANITOWOC EQUIPMENT WORKS Div. of THE MANITOWOC CO., INC. | 2110 South 26th Street Manitowoc, Wisconsin 54220 | (414) 682-0161 | CUBER MODELS CR-0600A ~~ CD-0602A CY-0604A CY-0614AS - CR-0600AS — CD-0602AS CY-0604AS : CY-0615WS CR-0601W CD-0603W CY-0605W | CR-0601WS CD-0603WS CY-0605WS CR-0690N CD-0692N CY-0694N | Remote Condenser — AC-0695A WARRANTY N Parts and Material One year — parts only Compressor | Five years — parts only See page 36 for returning of In Warranty Parts. (See “Ice Machine and Bin Warranty” page 38 and registration card shipped with the unit for warranty conditions.) | _ | Page 2 MANITOWOC ICE CUBERS — C-0600 Series FOR YOUR PROTECTION INSPECTION The carrier who delivers this merchandise to your door is responsible for loss and damages. Acceptance of this shipment by the transportation company is acknowledgment that the articles delivered to them were in good condition and properly packed. it is your responsibility to file a claim with the carrier if any of the following conditions exist. A. VISIBLE DAMAGE 1. If cartons appear damaged in any form, please open at once in presence of driver. 2. Have deliveryman note on freight bill the nature and extent of damages. 3. Notify the transportation company’s office to inspect the merchandise. 4 File claim for damages at once. In filing a claim with the transportation company, you may elect to: (A) Make a cash adjustment for full value, (B) Arrange to have repairs made, or - (C) Replace the merchandise. B. CONCEALED DAMAGE ab » if damage is noticed when merchandise is unpacked, notify the transportation company’s office immediately and ask to have it inspected. Do not destroy packing materials until shipment IS inspected. 2 3. Unless these conditions are met, it is very difficult to file a claim against a transportation company. C. SHORTAGES | 2 Check number of cartons delivered with the quantity shown on your receipt. If quantities do not tally, have driver note shortage and file your claim with them. IMPORTANT All claims for loss and damage should be filed immediately with the transportation company making delivery to your door. We are willing to assist you in every possible manner in collecting claims for loss or damage on this shipment, but this willingness on our part does not make us responsible for filling or collecting claims, or replacing merchandise. Under no circumstances will we accept the return of any merchandise unless written permission has been given by us. MANITOWOC ICE CUBERS — C-0600 Series NOTE: See C0600 remote section for additional installation information. (Page 23.) — UNCRATING Page 3 } The C-0600 Series cuber is shipped separate from the storage bin, in a corrugated carton. Remove the staples around the lower edge of the carton. Lift the carton upwards and off. The shipping skid is mounted to the cuber with 4 bolts located on the underside of the skid. Remove the bolts and set the cuber on the storage bin. LOCATION For maximum efficiency, pick a location away from sources of heat like radiators, ovens, other refrigeration condensing units, direct sunlight, etc. Provide a minimum of 5 inches around the cuber for proper air circulation through the compressor compartment. For air cooled models, louvered openings should be 5 inches from the nearest obstruction for best operation. Reduction of clearance may result in increased heat load and reduced ice capacity. A self-contained air cooled cuber will operate more efficient in a room of 70° F. than in a room of 90% F. Recommended minimum room temperature is 55° F. for self-contained air cooled models. If cuber is located in an unheated area, it must be protected from freezing or shut down and drained, see low ambient operation. LOW AMBIENT OPERATION AND WINTER SHUTDOWN - If the ambient temperature is below 55° F. for a self-contained air cooled C-0600, a low ambient kit, Fancycling switch, P/N 89-5009-9, should be installed. This is not required on water cooled and remote models. All Manitowoc cuber models must be protected from freezing temperatures or be shutdown and the water lines drained. This includes blowing out the ice water supply lines and drains and the water cooled condenser. To blow the water out of the water cooled condenser the waterlines flare fittings must be removed from the water regulating valve. The water lines and the condenser can now be blown out. See Fig.6 Item 9. SERIAL & ELECTRICAL PLATE (Fig. 2) , The combined serial and electrical plate is located inside the cuber above the water pump. Be sure to give | } the complete model number and serial number when calling for service or ordering parts. REMOVAL OR INSTALLING FRONT PANEL Caution: when removing front panel mounting screws, hold panel in place until both screws are removed. Secure panel with both hands and lift up slightly and out. To install front panel with cover on, slide the top of front panel under the lip of the cover and set in place. Replace the two screws to secure panel. REMOVING TOP COVER & COMPRESSOR COMPARTMENT PANELS The top cover is held in place with four sheet metal screws, two on each end. The rear grille must be removed before the R.H. end panel can be taken off. The rear grille is held in place with four sheet metal screws. The R.H. end panel is held in place with five screws along the bottom edge; (1) on front flange, (3) on side, (1) on rear flange. REMOVAL OF INTERNAL PACKING Remove the following: — The tape securing the splash curtain, water pump & ice chute. — Remove the ice chute and the corrugated board from around the chute and the. plastic sheet from over the chute. Then replace the ice chute and damper door and secure the chute with the clips and thumb screws provided. — Remove the packing from under the water pump. — Remove the wooden wedges from under the compressor. — The box taped in the evaporator section contains the strainer for the ice making water supply line. GENERAL REQUIREMENTS All electrical, water supply, and drain connections must conform to local and national codes. ELECTRICAL RATING MINIMUM. | MAXIMUM MODEL CIRCUIT FUSE SERIES ELECTRICAL AMPACITY SIZE C-O600A 208/230V-60-1Ph 12.8 amps ‘ 20 amps C-0600A 208/230V -50-1Ph 13.4 amps — 20 amps C-0600W 208/230V -60-1Ph 12.1 amps 20 amps C-0600W 208/230V -50-1Ph 12.7 amps 20 amps C-0690N 208/230V -60-1Ph 13.3 amps 20 amps Page 4 MANITOWOC ICE CUBERS — C-0600 Series CONNECTING POWER SUPPLY 1. Use electrical wire rated equal or greater than the minimum ampacity rating given on serial plate. 2. Cuber must be on a separately fused circuit, which does not exceed the maximum fuse size on serial plate. 3. Check supply voltage, limits are 208 -5% to 230V + 10% A ground screw is provided in the supply box. 9. Connect supply wires to cuber leads L4 and Lo located inside electrical supply handbox, in the rear of the compressor compartment. Fig. 3. WATER SUPPLY Quality and ice making capacity are affected more by chemistry, temperature, and foreign matter in supply water than any other factor. A survey made of water departments of large cities all over the country made it obvious that external filters or strainers should be installed. Such equipment is very effective in improving ice quality and reducing the frequency of cleaning out the ice making section. Any questions as to the type of water filter or strainers to be used can be answered by your local water treatment company or water department. A minimum water pressure of 25 PSIG is required at the water cooled condenser for water cooled models. CONNECTING WATER SUPPLY (Fig. 1) A 1/2” female pipe fitting is provided in the rear panel of the ice cuber. Install the water strainer provided with the cuber. Use a 3/8 OD copper tubing for the ice making water supply, and a minimum of 12 OD copper tubing for water condenser supply, on water cooled cubers. L DRAIN CONNECTIONS It is essential that drain connections be made so waste water cannot back up into the head unit or bin. On water cooled models, a separate drain connection is provided for discharging condenser water (Fig. 1). All connections are labeled. We recommend covering all incoming water and drain lines with a plumbing insulation material to prevent condensation. We recommend that the bin and cuber drains are not tied together and they are run to an open trapped and vented drain. If the cuber drain line is tied in directly to the drain, we recommend using a у 1.D. tubing and a stand pipe vented to the atmosphere to prevent water traps. Drains must be at least ¥2" inside diameter copper tubing or %" piping and have 1%" drop per 5 feet of run. If drains are not close enough to allow drop for proper drainage, or water is to be drained in a stationary sink higher than ice machine drains, use an automatic condensate disposal pump. (Check and follow local plumbing codes.) Bin Drain — The bin is supplied with 34” FPT fitting and a min. 3%” pipe or 34" 1.D. copper tubing is recommended for the drain line. CHECK LIST FOR START-UP 1. Remove all internal packing! 2. Be sure the cuber is level! This is to insure proper water flow in the cuber. 3.- Turn the supply water on for the sump and the condenser (if water cooled). 4 . Turn the toggle switch Fig. 4 to “water pump”, position. This will start the water pump only, pumping water to the water distributor and over the evaporator. Check the position of water distributor to see that it is distributing water properly and evenly over the evaporator. See Fig. 5 for proper distributor MANITOWOC ICE CUBERS — C-0600 Series Page 5 location. Set the float in the sump to maintain a level of 1/4" below the top of the overflow tube, while the cuber is running. Should the float valve require adjustment, bend the float rod carefully until desired water leve! is achieved. . Turn the water pump on and off (at approx. 2 minute intervals) several times to flush clean water through the system, and to observe that the flush water drains properly. . Check all the refrigerant lines and conduit to guard against vibrations and possible failure. 7. Check all the water connections for leaks. . Bend the water curtian hooks slightly to the outside to secure the water curtain in place. These hooks can be seen in Fig. 4. 9. Replace the panels except for the front panel. 10. To start cuber place the toggle switch in the “ICE” position. FINAL CHECK LIST AFTER START-UP 1. With the cuber operating, reach in and push the damper door open about 1” to 1". This should open the damper (bin) door switch which will shut down the entire cuber. The cuber will remain OFF until the damper door is released. If the bin switch needs adjustment, bend the metal arm until proper operation is obtained. Cuber should be checked for several harvests of cubes to see that the cuber functions properly, and that the ice cube bridging between cubes is 1/8” in the center of the ice slab. If the bridging needs adjustment see timer check-out procedure. Page 20. Is there 5” clearance around cuber for proper air circulation? Is the room ambient maintained at a minimum of 55° F during winter months, air cooled cubers? NOTE: A. condenser fan motor thermostat is available for operations below 55° F. (This does not protect the cuber from freezing temperatures.) 5. Check water and drain connections for water leaks. 6. Has owner been instructed on how to operate and clean the cuber? Has installation and warranty registration card been filled out? This is for owner protection. “600” SERIES CUBER- C-610 BIN 606 ADJUSTABLE LEGS = | ELECT. SUPPLY | = LEPT CONO. 3 F PT. ICE MAKING =P E NATER NET 7 / INLET 242 - = MATER COOLED >— [4 16 | = UNITS ONLY 2 7 8 . = 8 к 28 Ite Cuba я Pa | „= tz 71.5 8 — SECT, WATER LE —// 37 === == (ua Doo | ml № — 4% cor sume | — ORAIN az | 293 APPROX. 6 f 1 J" I 2 ERT, BIN DRAIN | y V RZ o MANITOWOC ICE CUBERS — C-0600 Series Page 6 FIG. 2 «= Service valve, h Receiver. Drier. Compressor. Water pump. WN=0WWONONH WN ond — and and ig 24174) 727 7 4 KOrcreccecececcczceerçecse задана EEE Serial and electrical plate. 1/2” water supply tube. h side. Condenser water drain. Water condenser. Water regulating value. Water sump trough assembly. Float valve assembly. Expansion valve (covere 777. 777 777, OIEA 27 ry. Aa. . к к traca, “... FIG. 2 WATER COOLED C-0600 CUBER WITH PANELS REMOVED E d with insulation). Nn” MANITOWOC ICE CUBER — C-0600 Series Page 7 FIG. 3 COMPRESSOR COMPARTMENT AIR COOLED FIG. 3 Air condenser assembly. Service valve, high side. Thermodisc (covered with insulation). . Hot gas solenoid valve. Suction service valve. - Compressor, | Electrica! supply box and leads. Start relay and capacitor box. Condenser fan motor assembly. CONONHWN = Page 8 MANITOWOC ICE CUBERS — C-0600 Series FIG. 4 ICE MAKING SECTION r . . „щен тб © вт сое Di E —]]]—] e! В «Al = ———————— к = Co ed CERT LS 7 AD ió . ro = Le е == 4 NOA Koh EE A e Mido MO A 1. Control box assembly. 2. Main On-Off toggle switch. 3. Harvest rack. 4. Damper bin door switch assembly. 5. Damper door. | 6. lce chute. . 7. 1/4" water supply tubing. 8. Overflow elbow. 9. Float valve assembly. | | A 0. Sump trough assembly. a o 1. Water pump. | A 2. Water curtain. — sans MANITOWOC ICE CUBERS — C-0600 Series Page 9 FIG. 5 ICE MAKING SECTION WITH CURTAIN, ICE CHUTE & WATER PUMP REMOVED 11 В + A y Eo Te == A 7 en a 7 Lb. - na EA 5 ; 5 a у : жд = = . = de + e A LEE EN Bu MEL a BM TE RAR FADER te, ` Tos , = нь 2 al il > — - r a . a us ; a : a - 7 e == - - pm 1 > ” ? Y = = ` # № F7 vy ! YN e 1 и г 1 Ся . - Во A mE * , hte SRE = , | de € = Y E Lier * Gr _ Oh Ey € E ; AL at TH 4; “ Tr 75 EA 5 an a3 a & » : EU Zur rd в cf E 1 5 = E ” 54 Fi “E ХА 3 Ч , 4 \ : an * к T "© ao к m ur ' 5 } м . Shyer e x =r * a Hs 4 CRA) ; + 4 = "8. = = AL 3 \ a > F — = 3 of . x т * a, = AC , и N A A + + x > ENE из ZE NL a | ; y 3 12 x rT x = Hu y № | gic KA Y y Ул A A я , a 7 LA by 7 A = A A E +‘ = В on , ; A La Fr cf LE > e > ver. . й re. в >. E ES PE, am 7e <r > - Le : | . i > L “gh En Le de ma? ; tas НИ) U ure vez ï . e ve f y 1006 NE 1 2 , "NE : ЕЕ i ; CE Lu - FIG. 5 Control box with cover removed. Main On-Off toggle switch. Evaporator. Damper bin door switch. Harvest rack. Sump trough assembly. Float valve mounting bracket. Float valve assembly. Overflow elbow. 1/2” water supply tubing. Water distributor. Locating clamps for distributor. NAODONAGAIRSON- euh mb «=^ Page 10 MANITOWOC ICE CUBERS — C-0600 Series FIG. 6 CONTROL BOX ASSEMBLY FIG. 6 | | CONTROL BOX ASSEMBLY чото Timer, solid state. Mounting track, timer. Main On-Off toggle switch. Low pressure cut-in adjustment screw. Low pressure cut-in control. High pressure cut-out water, water cooled only. High pressure cut-out manual reset, water coo ed only. pe MANITOWOC ¡CE CUBERS — C-0600 Series Page 11 WATER PUMP ASSEMBLY ER rd ge. EL м . ADA a oe FIG. 7 Inlet screen. Impeller housing. impeller thumb nut. Impeller. Motor shaft housing & mounting nuts. Pump bracket. Pump motor. Pump cover. Cover mounting nuts. Water pump is available as a complete pump assembly less cover & bracket. Motor not available separately. WOON DWN Page 12 MANITOWOC ICE CUBERS — C-0600 Series ^-9600 SYSTEM CONTROL AND SEQUENCE OF OPERATION _.¢ main ON-OFF toggle switch for the cuber is located on the control box. The toggle switch has three positions; the center or “OFF” position, the “WATER PUMP” position (only the water pump runs), and the “ICE” position. Placing the toggle switch in the Ice position will start the compressor, the condenser fan motor (air cooled cubers), and the water pump through terminals 4 & 5 on the solid state timer. The cuber is now in the freeze cycle. As water flows over the evaporator ice will begin to form on the cube plate. As the ice forms the suction pressure will continually decrease. At a preset point the reverse acting low pressure cut-in control will close its contacts. 10 PSIG for regular and dice cubes and 11 PSIG for half dice cubes. Closing of the low pressure cut-in control contacts energizes the time delay circuit of the solid state timer through terminal 1. The remaining freeze time is dependent upon the timer setting. At the end of the timing sequence the timer relay will energize. This will open the relay contacts between terminals 4 & 5 shutting off the water pump and condenser fan motor and close its contacts between terminals 3 & 4 energizing the hot gas solenoid valve. The cuber is now in the harvest cycle. NOTE: To manually place the cuber in harvest, see timer description and check-out procedure. Page 21. Shortly after the hot gas solenoid valve opens, the suction pressure will rise to 38 PSIG plus. This opens the low pressure control contacts. The solid state timer relay remains energized through the timer relay interlock circuit. As the harvest cycle progresses the hot gas will warm the evaporator allowing the ice to fall out of the evaporator and through the ice chute, opening the damper door. Opening of the damper trips the bin switch, momentarily de-energizing the entire cuber. The timer relay will return to its normal position, de-energizing the hot gas solenoid and energizing the water pump and condenser fan motor (air cooled cubers). The cuber ow in a new freeze cycle. The ice cuber will continue to cycle until the ice storage bin is full. The cuber automatically discontinues ice production as the ice fills the chute, holding the damper door and the bin switch open. If, for some reason, the bin switch would fail when the ice falls through the ice chute, the cuber would remain in the harvest cycle until the hot gas raised the suction temperature to 70° F + 5°. At this time the safety thermodisc, located on the suction line, would open its contacts, de-energizing the timer relay and hot gas solenoid valve, placing the cuber back into the freeze cycle. As the evaporator begins to cool, the thermodisc will reclose its contacts at 40° F + 5°. A high pressure cut-out control is used on the water cooled models only. This control shuts the entire cuber off should the condensing pressure become too high. : See page 22 Bin Thermostat for CY-O614AS & CY-0615WS models. REFRIGERATION CYCLE — C-0600 (See Page 15) *[Assume the cuber is operating at 90° F Air and 70° F Water) Freeze Cycle During the freeze cycle the high pressure discharge gas is pumped into the condenser. (*Air cooled-Ave. “ve, ® MANITOWOC ICE CUBERS — C-0600 Series Page 13 head 160-165 PSIG. Water cooled Ave. head 125-130 PSIG.) The high pressure gas is condensed to a high pressure liquid. The high pressure liquid leaves the condenser, goes through the filter-drier, and into the heat exchanger. On water cooled cubers the liquid will go from the condenser into a receiver. The receiver stores extra refrigerant when it is not used. This depends on operating conditions. The high pressure liquid leaves the heat exchanger at a reduced temperature making the system more efficient. The high pressure liquid is then metered into the evaporator by a thermostatic expansion valve. The expansion valve regulates the rate of refrigerant liquid flow into the evaporator in the exact proportion to the rate of evaporation of the refrigerant liquid in the evaporator. The expansion valve does this by responding to (1) the pressure in the evaporator (2) the temperature of the refrigerant gas leaving the evaporator using the valve feeler bulb to sense the gas temperature. After the low pressure liquid evaporates to a low pressure gas, it passes through the suction line heat exchanger and into the compressor. The ave. suction pressure will start at approx. 20 PSIG and drop to approx. 8-10 PSIG when the cuber goes into harvest. Harvest Cycle The harvest is initiated by the solid state timer energizing the solenoid valve allowing high pressure hot gas to flow through the evaporator and harvest the ice. The suction pressure during the harvest is approx. *45- 55 PSIG (air cooled) and 38-45 PSIG (water cooled). *The head pressure will drop to approx. 80-100 PSIG (air cooled). The cuber goes back into the freeze cycle automatically when the solenoid‘valve is closed by the harvesting ice tripping the bin switch. | The cuber is now in a new cycle. C-0600 OPERATING CHARACTERISTICS” | AIR_COOLED WATER_COOLED AIR FREEZE | HARVEST | FREEZE | HARVEST TEMP. CYCLE CYCLE CYCLE CYCLE 70 135-110 75-90 130-125 80-90 HEAD 80 150-125 80-95 130-125 80-90 PSIG 90 180-140 90-105 130-125 80-90 105 210-170 110-120 130-125 80-90 — 70 18-6 35-45 19-6 38-45 SUCTION 80 20-8 40-50 20-7 38-45 PSIG — 90 21-8 50-60 21-8 38-45 105 22-9 55-65 22-8 38-45 *These are approx. characteristics that vary depending on the operating conditions. ‚Page 14 MANITOWOC ICE CUBER — C-0600 Series : SOLID STATE TIMER RUN XN. | ETO _ CAPACITOR smart г - я CAPACITOR О! i THERMO HOT GAS | i DISC SOLENOID | | К j ’ | NO : a Lo START т нь Me de ie ; | Ka | | с | | I\R | | | o CTOR | | SERVICE CONNE BOX COMPRESSOR De | a / | ей L I ell! I | | ! l | ? | | | | ' о! = No Um NE нате PUMP — pea i Li lia OVER | a 208/7230 VAT A EEE e e o E a TOGGLE SWITCH | PHASE OPTIONAL Pat _| — JUMPER BIN THERMOSTAT 7 CONTROL TOGGLE ce | ( MATER COOLED UNITS ONLY) SWITCH | HIGH | CONDENSER PRESSURE FAN CONTROL \ | av AIR UNITS ONLY | 9 7 [ FRIESE | ay I $ re — Css hs A Mr SEE Ga —— 5 = RELAY 5 TO as 7 WIRING DIAGRAM SEQUENCE OF ICE-MAKING € HARVEST CYCLE L SET TOGGLE SWITCH TO ICE POSITION. THIS ENERGIZES THE WATER PUMP, COMPRESSOR, { CONDENSER RAN MOTOR. TOGGLE 2 AS ICE FORMS, GAS PRESSURE DECREASES, CAUSING THE LOW PRESSURE CONTROL TO CLOSE AND ENERGIZING THE TIME DELAY CIRCUIT. 3 AFTER THE TIME DELAY INTERVAL, THE TIMER RELAY CONTACTS TRANSFER FROM NORMALLY CLOSED TO NORMALLY OPEN, CAUSING THE WATER PUMP 4 CONDENSER FAN MOTOR TO SHUT OFF $ THE HOT GAS SOLENOID TO SWITCH INTO HARVEST. CO600 | PHASE SOLID STATE TIMING 50 OR 60 HZ. SHOWN AT BEGINNING OF ICE-MAKING CYCLE, HIGH PRESSURE CONTROL NORMALLY CLOSED, LOW PRESSURE CONTROL NORMALLY OPEN, CONDENSER RI BER 208/230 VOLT FAN ON AIR MODELS ONLY. SWITCH D680/72-4 REVISION A 81-0464-3 4 DURING HARVEST, GAS PRESSURE { TEMPERATURE BEGIN TO RISE, CAUSING THE LOW PRESSURE CONTROL TO OPEN, PREPARING IT FOR A NEW CYCLE. AS TEMPERATURE CONTINUES TO RISE, THE ICE SLAB DROPS f TRIPS THE DAMPER DOOR WHICH INTURN OPENS BIN SWITCH MOMENTARILY. THIS CAUSES THE HOT GAS SOLENOID TO SHUT OFF. CUBER GOES INTO NEW FREEZE CYCLE. NOTE: WHEN THE BIN THERMOSTAT CONTROL TOGGLE SWITCH IS IN THE OFF POSITION, THE THERMOSTAT WILL CONTROL THE ICE LEVEL IN THE STORAGE BIN. WITH TOGGLE SWITCH IN THE ON POSITION, THE BIN SWITCH CONTROLS THE ICE LEVEL. CAUTION: DISCONNECT POWER BEFORE WORKING ON ELECTRICAL CIRCUITRY. MANITOWOC ICE CUBER — C-0600 Series Page 15 C-0600 SERIES TUBING SCHEMATIC — REFRIGERATION CYCLE SUCTION- LIQUID LINE EN HIGH PRESS. HOT GAS (HEAT EXCHANGER) MN HIGH PRESS. LIQUID DRIER LOW PRESS. LIQUID {1} СЯ (04 PRESS. GAS COMPRESSOR 3» SUCTION | + y DISCHARGE = =) od EXPANSION VALVES A AIR OR i i CONDENSER \ © WATER COOLED | A a EEE NN C0) fo 1 SOLENOND É 1 VALVE hs LLAZ LE L aire afi, EN LES WHY TY EEN LD NARA |} EVAPORATOR = EE wr Ti TI [yl Я r 4 AED SH В die Ы LY pT i Lo Fa dE PRE RE TRE LE a a Piar aa ol " x | Г] | A = [= SP — N . TT, 1 РЯ — Tp —y eN AA E Ea qe === IC N o | o (WATER UNIT OP” Page 16 MANITOWOC ICE CUBERS — C-0600 Series * | C-0600 CUBER SPECIFICATIONS N . SELF- Incoming Room Temperature (F) CONDENSER WATER USAGE" / Water Temp. | (F) } 70° | 80° | 90° MODEL C-0600W SERIES «ONTAINED ‘600’ Air 50° 610 560 500 SERIES Cooled 70° 290 200 ; 470 Water Temp “F 509 709 90° ICE Models 90° 90 46 4 ED | PRODUCTION oo 0 еб 1 eso | ea Gal/ Day | 400 720 1650 io Cooled 70° | 530 | 520 | 510 *At factory head pressure setting of 125 PSIG Models 90° | 460 | 450 | 440 and a clean condenser. * Approximate production for Dice Cube and Half Dice Cube (Regular Cube production slightiy lower). “600” Series Stack-On unit also available (doubles the ice making output). Portable water consumption gallons per 24 hours = ’ 1.7 x 24 Hr. ice Production. 8.34 “600” SERIES Cube Exterior Approx. Ship. REMOTE SERIES 600 CUBER WITH AC-0695A CONDENSER MODELS Type Condenser | Finish Wt. — lbs. CR-0600A Regular Air Fawn 315 CR-0600AS Regular Air Stainless 315 Approximate Production CR-0601W Regular Water Fawn 305 Per 24 Hours" (Pounds) CR-0601WS Regular Water Stainless 305 Cond. Air Water Temperature °F OOO Dice Air ca 325 ° - ice ir tainless Temp. °F so | 70 | so CD-0603W Dice Water Fawn 315 -20 to 70 580 | 530 | 490 CD-0603WS Dice Water Stainless 315 90 560 | 510 | 470 CY-0604A Half Dice Air Fawn 335 : -0604. a ice ir tainiess 100 520 | 470 | 430 CY-0605W Half Dice Water Fawn 325 110 490 | 450 | 410 CY-0605WS Half Dice Water Stainless 325 “Based on 70° F air at ice maker. Model Minimum Cube Si Shipping Feayired = py R BIN OPTIONS C-610 c-9 ode mpacity u ize eight ondenser 600 SERIES o О 00 CR-0690N 13.3 Regular 370 AC-0695A Ice Storage* — lbs. 580 1040 CD-0692N 13.3 Dice 370 AC-0695A Height — inches 31-7/16 44 CY-0694N 13.3 Half Dice 380 AC-0695A h — inches 48 48 th — inches 29-9/16 34 » wProx. Shipping Wt. x Ibs. 128 220 : . = —— ne Carton Volume — cu. ft. 9 ander | Model я tandard interconnecting - NOTES: Cast aluminum Bin Legs. No. 606 adjusts from refrigerant lines. AE 20 feet 6-1/2" to 7-1/2" — No. 612 from 12” to 13-1/2". Casters RT-50 50 feet also available. *Rated storage capacity based on 35 Ibs. per cu. ft. at 90% internal volume. THREE CUBE SUES Regular (1-1/8” x 1-1/8" x 7/8” — 30 cubes per 1b.), “Dice” (7/8* x 7/8" x 7/8" — 48 cubes per Ib.) and “Half Dice” (3/8" x 7/8" x 7/8” — 98 cubes per Ib.). 60 CYCLE 50 CYCLE CUBER MODEL CD CR CY CD CR CY CD CR CY CD CR CY 600 SERIES 600- SERIES. 600 SERIES 600 SERIES WATER COOLED AIR COOLED WATER COOLED AIR COOLED 60 CYCLE 60 CYCLE 50 CYCLE 50 CYCLE [Compressor Model SSC4-0100-CAV-218 SSC4-0110-CAV-218/SSE4-0100-CAG-206 SSE4-0100-CAG-206 ICompressor Voltage 208/230-60Cy-1Ph 208/230V-60Cy-1Ph| 230V-50Cy-1Ph 230V-50Cy-1Ph Winding Resistance Common to Run 1.40-1.65 1.40-1.65 OHMS 1.38-1.58 1.38-1.58 OHMS Winding Resistance Common to Start 4.02-6.57 4.02-6.57 OHMS 8.43-9.69 8.43-9.69 OHMS Start Capacitor Rating 145-175MFD220V 145-175MFD220V | 145-175MFD-220V 145-175MFD-220V Run Capacitor Rating 20 MFD-370V 20 MFD-370V 20MFD-370V 20MFD-370V Fan Motor Amps — .7 AMPS — .54 AMPS Fan Motor Watts — 35 Watts — 23.2 Watts Fan Motor Volts — 230 Volts — 230 Volts ¡Fan Winding Resistance — 55 OHMS — 18 OHMS Solenoid Valve Volts 230 Volts 230 Volts 230 Volts 230 Volts Solenoid Valve Amps .1 AMPS .1 AMPS .6 AMPS 6 AMPS "Y Pump Volts 208/230 Volts 208/230 Volts 220 Volts 220 Volts Nr Pump Amperage .99 AMPS 99 AMPS 8 AMPS 8 AMPS Refrigerant Charge — R-12 30 Ozs. 42 Ozs. 30 Ozs. 42 Ozs. [Freeze Amperage 4.0-7.0 AMPS 5.0-8.5 AMPS — — [Defrost Amperage 10.1 AMPS 10.1 AMPS — — h Me “, N nn ~~ MANITOWOC ICE CUBERS — C-0600 Series Page 17 C-0600 COMPONENT CHECK-OUT PROCEDURE | Check out procedure for compressor and compressor start components. y (A) Compressor will not run — If the compressor fails to start and run properly; it is possible that the external electrical components may be defective, the protector may be open, a safety device may be tripped, or other conditions may be preventing compressor operation. 1. Check for voltage at compressor terminals. If there is no voltage, check back from the compressor to the power supply to find where the circuit is interrupted. Check the bin switch, high pressure cut-out (water cooled units only — has a manual reset on the control) and the toggle switch for proper operation. 2. If power is available at the compressor terminals and the compressor does not run, check the voltage at the compressor while attempting to start the compressor. If the voltage is below 90% of the nameplate voltage, it is possible the motor may not develop sufficient torque to start. Check to determine if the power supply is adequate, electrical connections are loose, the circuit is over- loaded, or if supply wire sizes are adequate. 3. A defective capacitor or relay may prevent the compressor from starting. If the compressor attempts to start, but is unable to do so, or if the compressor hums or trips out on the overload protector, check: RELAY — Potential type. The relay contacts should open as the compessor comes up to speed. Remove the wire leads from the relay terminals. Use a high voltage ohmmeter to check for continuity through the relay coil. Replace the relay if there is no continuity. Use an ohmmeter to check across the relay contacts. Potential relay contacts are normally closed — when the relay is. not energized. Replace the relay if there is no continuity. ( J CAPACITORS Fig. 3 Any capacitor found to be bulging, leaking, or damaged should be replaced. CAUTION: Before removing leads for testing purposes, short across capacitor terminals to dis- charge capacitor. A quick check is to replace suspected capacitors with a known good capacitor. Be sure only specified capacitors are used. If a capacitor tester is not available, an ohmmeter may be used to check run and start capacitors for ' shorts or open circuits. Set the ohmmeter to its highest resistance scale, and connect prods t to capacitor terminals. A. With a good capacitor, the indicator should first move to zero, and then gradually increase to infinity. B. If there is no movement of the ohmmeter indicator, an open circuit is indicated. С. If the ohmmeter indicator moves to zero and remains there or on a low resistance reading, a short circuit is indicated. (В) If compressor fails to start or blows fuses (start relay and capacitors are functional) proceed to check compressor as follows: CAUTION: Turn power off. Before removing supply leads to compressor, short across both capacitor | terminals to discharge capacitors. 1. Using an ohmmeter check for continuity from terminals C to R and C to S. If the compressor is warm, wait one hour for compressor to cool and recheck. The internal overload protector can cause a lack of continuity. If continuity cannot be established through all motor windings, the compressc should be replaced. u 2. Check the compressor motor for ground by means of a continuity check between terminal C, R, and S to the compressor shell. If there is a continuity reading, the compressor is grounded and should be replaced. Page 18 MANITOWOC ICE CUBERS — C-0600 Series - AC) If compressor starts but trips repeatedly on the overload protector check: / 1. Operating pressures should be within limitations of normal operating conditions shown on Page 13. 2. Check line voltage at the compressor terminals at start-up. Design voltage is nominal 208 or 230 voltage. Minimum operating voltage 198 and maximum operating voltage is 250. 3. Check the amperage drawn while the compressor is operating. Under normal operating conditions, the continuous amperage drawn will seldom exceed 100% of compressor nameplate amperage and should never exceed 120% of nameplate amperage. High amperage can be caused by: Low voltage. High head pressure. High suction pressure. Defective running capacitors or starting relay. Compressor mechanical damage. FAN MOTOR Fig. 3 The fan motor is a shaded (4) pole, impedance protected fractional horsepower motor; normal speed approx. 1610 RPM. Check Out Procedure 1. Check wiring and voltage across terminals 5 & 19. 2. If there is power, place toggle switch into neutral position. Remove lead from the fan motor at timer terminal 5. Check fan motor resistance. ) If the windings appear to be open and fan motor is hot, allow 30 minutes for the overload to close and : recheck. If there is still no reading, the motor is defective. Replace. 4. If the motor appears hot and fan shaft is tight, remove oil plug and lubricate bearings. A good refrigeration oil can be used. If motor remains tight, replace. WATER PUMP Recirculating pump used to pump supply water to the water distributor tube. Fig. 7 shows dissembly of the water pump for cleaning and to remove the Stainless steel mounting bracket and pump cover. HOT GAS SOLENOID VALVE Fig. 3 The hot gas solenoid is a normally closed valve that is opened to permit hot gas flow through the evaporator to harvest the ice. Check Out Procedure 1. Check the coil resistance at lead No. 2 & 3. Remove one lead to isolate coil. 2. If the coil is good, check the thermodisc and timer. 3. If the solenoid valve leaks when closed or will not open, but the coil is 5 good, the internal parts should be examined and replaced if necessary. The refrigerant charge will have to be blown to accomplish this. nn MANITOWOC ICE CUBERS — C-0600 Series Page 19 C-0600 CONTROLS DESCRIPTION AND CHECK-OUT PROCEDURE ELECTRICAL CONTROL BOX Fig. 6 The control box contains the high pressure control (water cooled units only), low pressure cut-in, toggle switch, and the solid state timer. The control box is located inside the evaporator compartment, mounted on the partition panel. Fig. 4 TOGGLE SWITCH The main power “ON and OFF” toggle switch is a double pole, double throw switch with “OFF” in the center position. With the toggle switch in the “water pump” position, only the water pump will operate. This is for circulating cleaning solution and checking pump operation. With the toggle switch in the Ice position, the water pump compressor and condenser fan (air cooled models) operate for a normal ice making cycle. À | TOGGLE SWITCH 8 уро И ‚ (REAR VIEW) Len de A A Check Out Procedure о | | 1. Turn power off. Check toggle switch by removing all wires on one side (terminals B, 16 & 17) and make continuity check with ohmmeter. If the results are positive, rewire leads to assigned terminals. Likewise examine the opposite side of the toggle switch (terminals A, C & 14). 2. Check also the jumper for proper position and continuity. Jumper should be across terminals A & B. HIGH PRESSURE CUT-OUT — WATER COOLED UNITS ONLY. Fig. 6 tem: 6 This high pressure. cut-out shuts off the entire cuber, should the head pressure exceed 275 PSIG. If the cuber goes out on high head pressure, the high pressure cut-out control has to be manually reset after the cause of the high head pressure condition has been corrected. | Check Out Procedure With the power supply turned off to the cuber, place an ohmmeter across the terminals after removing one of the leads. Push reset button. If no continuity reading, replace control. LOW PRESSURE CUT-IN CONTROL Fig. 6 Item 5 This is a Robert Shaw low pressure reverse acting control that closes its contacts on a drop | in pressure and opens its contacts on a rise in pressure. The low pressure control contacts close at 10-1/2 PSIG for regular and dice cubes, and 11 PSIG for half dice cubes. The differential is fixed at 12 PSIG so the contacts will open at approx. 22 PSIG. The low pressure control is used to initiate the time delay circuit of the solid state timer. If the timer is set at its max. or min. setting and the proper bridge thickness cannot be obtained, the low pressure control cut-in point must be recalibrated. Check Out Procedure 1. install a service cage on the suction service valve and voltmeter prods on terminals 1 and the common binding post “19”. | | 2. Turn the cuber on. As it runs slowly close the suction service valve down (front seat) so the suction pressure will fall. When the suction pressure reaches 10-12 PSIG the contacts should close giving you a 208/230 volt reading. | 3. To change the cut-in point, turn the Phillip head screw clockwise to increase the cut-in point and counter-clockwise to decrease the cut-in point. Fig. 6 Item 4. 4. Allow the timer to time out and place the cuber in harvest. The suction pressure will rise, opening the low pressure control contacts at approx. 22 PSIG. Page 20 MANITOWOC ICE CUBERS — C-0600 Series SOLID STATE TIMER Fig. 6 ‘primary function of the timer is to control the ice bridge thickness and to initiate the harvest cycle by energizing the hot gas solenoid valve and de-energizing the water pump and condenser fan motor. The timer is activated by the low pressure cut-in control and is de-energized by the opening of the bin switch, or thermodisc. The Model C-0600 Ice Cubers are manufactured with several different make solid state timers. All these timers are interchangeable. The wiring is the same — be sure the numbered wires are placed on the terminals with corresponding numbers. When replacing the timer check for proper voltage setting — determined by the location of the jumper wire. — All Dual Voltage Timers P/N 24-0623-3, place a jumper wire across terminals 2 & A for 230 Volt or across terminals 2 & B for 115 Volt units. The jumper wire must be in place for the timer to operate. SOLID STATE TIMER ADJUSTMENT AND BRIDGING TIMER. ADJUSTMENT TO INCREASE OR DECREASE BRIDGING BETWEEN CUBES. To adjust the solid state timer — 1. Remove control box cover, Fig. 4, item 1. 2. Locate the timer and the dial. 3. To increase bridge thickness, rotate dial clockwise. 4. To decrease bridge thickness, rotate dial counter-clockwise. Adjustments should not be greater than 10° to 16° at one time. After each adjustment allow the cuber to produce two ice harvests and observe bridge thickness. Repeat this procedure as required. For optimum ice production and maximum cube separation, the ice connecting the individual cubes should be 1/8” thick at the center of the ice slab. (Note: Bridging will vary in the thickness from top to bottom of e—norator.) BRIDGE 1/8 To change bridge thickness, an adjustment of the solid state timer is required. This timer is located inside the electrical control box. CAUTION: Before removing the control box cover, the cuber's main power supply should be turned off to prevent any electrical shock or accidental wire shorting. SOLID STATE TIMER | | — Timing Diala APPROX 240° TO 270° | > 10 MIN: 6 SEC. 10 MIN. 230 VOLT JUMPER 2TOA | MANITOWOC ICE CUBERS — C-0600 Series Page 21 Check Out Procedure 1. Check wiring of timer to wiring diagram page 14. Cd 2. Set toggle switch to OFF position. Place a jumper wire across the low pressure control. 3. Mark approximate position of timing dial and turn fully counterclockwise to get a short time delay period (30 to 60 sec.). 4 4. Place the toggle switch into ice making position. The timer, fan motor, water pump, and compressor should be energized. With the low pressure control jumpered, check for a 230 voltage reading at terminals 1 and 19 or N with a voltmeter. Note: After the hot gas valve opens, the suction pressure will rise opening the low pressure contacts. 5. At the end of a predetermined timing period, the timer relay contacts should transfer, turning the fan motor and water pump OFF, and energizing the hot gas solenoid. Using a voltmeter there should be a 230 voltage reading at terminals 3 and 2 confirming proper operations. 6. If the relay contacts fail to transfer after 2-3 minutes with the timer set at minimum setting, check to see if the thermo-disc and bin switch are in normally closed position. If the bin switch and thermo-disc are closed, replace timer. | | ВЕ 7. With the cuber in the harvest sequence, trip the bin switch or place the toggle switch in the “OFF” position and back into “ICE” position. Either of these actions should deactivate the timer relay placing the cuber back in freeze. If proper sequence of all operations is accomplished the timer is in working order. If not, replace timer. 8. Place toggle switch in “OFF” position. Remove jumper wire from low pressure control. Reset timer dial to previous position. Test cuber for proper operation. | : NOTE: If needed the solid state timers can be manually tripped to place the cuber in harvest. ZN Timers with H & Hq terminals can be placed in harvest by shorting across H & Hq terminals. This override ; the timing sequence. Timers without H & Hq terminals, place in harvest by shorting across terminalis 3 & 4 on the timer. This overrides the timer completely. SAFETY THERMO-DISC Fig. 3 The thermo-disc is a safety control located on the suction line. The control is temperature sensitive and opens at 70° F + 5° and closes at 40° F + 5° F. The thermo-disc prevents the cuber from overheating. If the ‘bin damper door switch should fail when the ice harvests, the cuber hot gas valve would remain open. The suction temperature would rise and the thermo-disc would open at 70° F. This will place the cuber back into the freezing cycle by de-energizing the timer and hot gas solenoid. Check Out Procedure | 1. The thermo-disc is a normally open control at 70° F and above, and recloses at 40° F. Closing IS accomplished by operating the cuber on for approx. 5 minutes. The thermo-disc will open only if the cuber sits idle in room temperature for a period of time, or the cuber bin switch fails in harvest. 2. Disconnect the thermo-disc leads at terminals 2 and № о the timer, after the cuber has been operating. Check continuity with ohmmeter. If there is no reading, check for contact between the suction-line and the thermo-disc. If contact is adequate, replace thermo-disc. 3. To check the cut-out temperature of the thermo-disc, remove the damper door from the ice chute. Start the cuber and wait for the evaporator to harvest. With the door removed, the unit will remain in its harvest cycle. This will increase the suction line temperature sharply until the thermo-disc reaches its calibrated opening point (70° + 5° F). From the time the ice has harvested to the point the thermo-disc opens, under normal ambient temperatures, it should take no longer that 2-3 minutes. | Page 22 MANITOWOC ICE CUBERS — C-0600 Series DAMPER DOOR (BIN) SWITCH Figs. 4 & 5 J ; micro switch is used to cycle the cuber from harvest to freeze cycles and shut the cuber OFF when the ice bin is full. The switch is tripped by the damper door counter-weight when the harvesting ice falls through the ice chute. Check Out Procedure 1. Check free movement of damper door. 2. Check bin switch arm for ON & OFF action, by opening or closing damper door. Switch should open when the damper door is open approx. 1 to 1-1/2". 3. Turn main power supply off to the cuber. Make a continuity check across the switch. Be sure to remove one lead first. Tripping the metal arm will open the switch contacts and releasing the arm will close the contacts. To verify switch action open and close the switch. Replace switch, if defective. LOW PRESSURE CUT-OUT — Fig. 11 item 10 (Used on the C-0690N Models Only) This is a Robert Shaw low pressure control that opens its contacts on a fall in suction pressure, 2 PSIG, and closes its contacts on a rise in pressure, 27 PSIG. The low pressure cut-out is used to start and stop the compressor. Check-Out Procedure 1. Install a service gage on the suction service valve or port (Fig. 1 Item 11). 2. Placing the toggle switch in the OFF position or holding the damper door open will de- -energize the Jiquid solenoid valve, Fig. 8, Item 12. The suction side will pump down until the low pressure cut-out pens its contacts at 2 PSIG. | 3. If the compressor shuts off several pounds above or below this 2 PSIG setting, reset by turning the adjustment screw clockwise to increase the cut-out point and counter- clockwise to decrease the cut- out point. BIN THERMOSTAT CONTROL (Used On CY-0614AS & CY-0615 WS The bin termostat is used to control ice level in the bin by stopping and starting the cuber. The location of the sensing bulb will determine the ice level. The toggle switch on the thermostat housing can be used to jumper out the thermostat. Placing the toggle switch in the upper position, the thermostat will control the ice level. With the toggle switch in the lower position, the bin switch (located in the ice chute) will control the ice level. ALTITUDE EFFECT The thermostat operating point shifts approximately 3/4° F lower for every 1000 ft. of elevation above sea level. For altitudes 2000 ft. and above the set point should be calibrated. RECALIBRATION Prepare a 32° F ice/water bath. Loosen the set screw and remove the black knob.* Place the thermostat bulb in the ice bath, rotate the loosened knob clockwise until the contacts just open (32° F). Then turn the dial counter-clockwise 1/4 turn. The cut-out point should then be at 36° Е. Replace the knob* in such manner that the built-in “stop” does not allow the knob to turn clockwise to a colder position. Tighten the set screw. В — Later models are screw driver instead of knob adjustable and have no “Stop”. " y Sean MANITOWOC ICE CUBERS — C-0600 Series Page 23 C-0690 CUBER WITH AC-0695A REMOTE CONDENSER Cuber Model Numbers: CR-O690N CD-0692N CY-0694N Condenser Model Number: AC-0695A Precharged Line Model Numbers: RT-20, RT-35, RT-50, MRT-28 GENERAL INFORMATION The cuber head sections listed above are used with the AC-0695A condenser and one of the four precharged line sets designated by the customer. Note: The standard C-0600 self-contained cuber is not designed to be used with the AC-O695A remote condenser. The CO-0690N Cubers and the AC-0695A Condenser are designed to be used with one of the RT-Line sets. Manitowoc cannot be responsible for improper operation if lines other than the RT-Sets are used and are of different diameter or over the 50 ft. maximum length. The precharged lines, cuber head and remote condenser are all shipped in separate crating. The ICE making sections of the standard C-0600 and C-0690N Cubers are identical. See Figures 4 & 5 on pages 8 & 9. **Cubers used with MRT-28 line set: The MRT-28 line set is a special flexible line to be used in conjunction with cubers mounted on casters. This special line has an 8 foot section of braided flexible stainless steel to ‘permit the cuber to be moved approximately 4 feet in any direction without damage to the precharged lines. This provides easy mobility for cleaning & servicing in back of cuber. INSTALLATION See Fig. 8 For Additional Information Cuber Set Up: “Follow the standard cuber instructions on pages 3 through 5, but do not place the cuber into it's final position until the refrigerant lines and electrical lines to the remote condenser are connected. - REMOTE AIR CONDENSER SET-UP 1. Assemble two legs to each of the two mounting tracks. This assembly provides for two separate height adjustments. The standard 12 inch height and a 15 inch height to be used in installations where heavy snow or debris may collect at base of condenser causing air flow restrictions. See Figure 1. 2. Lacate the remote condenser in a well ventilated area on the roof. Consult the Manitowoc office for other applications. 3.- Using the six mounting holes provided, secure the remote condenser to the roof. Seal with tar or pitch to prevent entrance of moisture. INSTALLING THE REFRIGERATION LINES 1. Each condenser is connected with two precharged lines. The precharged lines are ordered separately from the condenser to suit each individual application. The precharged line lengths are 20 ft. (RT-20), 35 ft. (RT-35), 50 ft. (RT-50) and 28 ft. (MRT-28). Remove the tubing from the carton. Carefully unwind the coil so the tubing doesn’t become kinked. 3. The refrigerant fittings on the cuber and remote condenser are oiled at the factory. Additional lubrica- tion should be used before assembly. Use Refrigeration Oil Onlyl | 4. Note: The MRT-28 lines are provided with a 90° bend at one end. This end is intended to be attached to the cuber to provide a minimum 6 inch clearance between cuber and wall. If additional bends are required, slide armaflex away from tubing. Using a tube bender, carefully bend tubing to required angle. Page 24 MANITOWOC ICE CUBERS — C-0600 Series =>. Follow step (6) and connect one refrigerant line to fitting #1 on the cuber, and fitting #1 on the ; condenser. Connect the other line to fitting #2 on both the cuber and condenser. Fig. 9. 6. To connect the refrigerant lines to the cuber, remove the rear & right hand end panels on the cuber. 7. Carefully thread, by hand, the female hose fitting to the male fitting on the cuber and remote condenser. Using the proper size wrench, tighten the couplings until you feel them bottom out. Then add an additional % turn to insure proper seal. If a torque wrench is used follow these for %" to 36” fittings with %-18 thread size, the torque value is 10-12 ft. Ibs. For 1%” fittings with 1-1/16”-12 thread size, the value is 35-45 ft. Ibs. Important: Once the refrigerant lines are connected, the seal is broken in the fittings and if removed from the cuber or remote condenser, the refrigerant charge in the cuber and condenser will be depleted. WATER SUPPLY AND CONNECTIONS, See Page 4 ELECTRICAL HOOK-UP Min. Circuit Max. Fuse Voltage Amps Size C-0690N 208/230 1PH 13.3 Amps 20 Amps The electrical power supply is run through the standard opening at the rear of the cuber. The remote condenser electrical hook-up is connected to the cuber and condenser as shown in figures 8 & 9. There are 3 wires in the cuber electrical supply box labeled, L1, L2, & F1. The condenser motor has two leads, one should be connected to L2 and one to F1 in the supply box. | N | 7 ‘ PO 7 FIG. 8 | CUBER SUPPLY BOX 0 { | 1421 T 208/230 VOLT SUPPLYI | + 1 PHASE | | | | 471 | #7 Î i Lil: Minimum condenser fan motor amps. 1.2. The supply wiring and condenser fan motor wiring from the cuber to be supplied by customer. Follow all local and national codes. A SERVICE NOTE: To insure proper operation in all ambient conditions, the refrigerant charge in a Manitowoc remote system must be at nameplate charge. New packages supplied by Manitowoc are precharged. Subsequent repairs to the sealed system must include a total purge, complete evacuation, and a measured charge. This service procedure requires connections at three points within the sealed system. | 1. Receiver Service Valve — This evacuates the area between the head pressure control valve and the solenoids. 2. Suction Side at the Compressor or Low Side Service Port — This evacuates the suction side between the compressor and solenoid valves. Fig. 11 items 11 & 14. o. Discharge Side at the High Side Service Port or the Quick Connect Service Port. This evacuates the — high side between the compressor and the head pressure control. MANITOWOC ICE CUBERS — C-0600 Series Page 25 FIG. 9 INSTALLATION OF C-0690N CUBER AND THE AC-0695A RITERS LABORATORIES FILE NO. SA4027 UNDERW : REMOTE SOND EN ER NATIONAL SANITATION FOUNDATION FILE NO. 595 CANADIAN STANDARD ASSOCIATION FILE NO. LR.25608 FAN "ON/OFF" SWITCH LIQUID LINE DISCHARGE LINE 29 COIL EXCESS TUBING ABOVE ROOF NO a Ш |. SUGGESTED INSTALLATION . ALLOW A MINIMUM OF 6 INCHES OF CLEARANCE ON BOTH SIDES AND IN BACK OF UNIT. 2. MINIMUM WATER INLET PRESSURE 25 LES. - 3. ALL WIRING AND PLUMBING MUST COMPLY WITH LOCAL AND NATIONAL CODES. | BORE 25 DIA. HOLE IN ROOF OR WALLS FOR TUBING. SEAL | WITH TAR OR PITCH AND <3 SLOPE TO PREVENT ENTRANCE i | ' Hyp” «т (2) WIRE ELECT. INTERCONNECTION (BY с. К” CUSTOMER) WIRING MUST MEET ALL | “LOCAL & NATIONAL CODES. I MIN. REQUIRED FAN MOTOR AMPS. 1.2 M GROUND THROUGH CONDUIT OR 3 \ WIRE TO GROUND SCREW. Ÿ ELECTRICAL SUPPLY | 208 OR 230V., 60 HZ, | PH \ MINIMUM CIRCUIT AMPS. ( 13.3) \ MAXIMUM FUSE SIZE (20) \ — —-DISCHARGE REFRIG. LINE I ELECTRICAL SUPPLY == C-0690N | == CUBER 6 = FPT. ICE MAKING 8 2 I, INLET Fr №” - u“ 7 AL ” 36 | | “ C-610 a LIQUID REFRIG. LINE 7 3 ERT. BIN DRAIN Page 26 START-UP A MANITOWOC ICE CUBERS — C-0600 Series à start-up procedure and check list for the remote cubers are the same as for the standard cubers. Pages 4 & 5, with the following additions. 1. Before start-up, open (backseat) the receiver valve. 2. After the cuber is running, check the remote air condenser & verify that the condenser fan is running. Fan will be off during the defrost cycle. SYSTEM CONTROL AND SEQUENCE OF OPERATION The main on-off toggle switch for the cuber is located on the control box. Fig. 4. The toggle switch has three positions; the center or “off” position, the “water pump” position (only the water pump operates) and the “ice” position. SEQUENCE | FREEZE CYCLE FREEZE CYCLE — Sequence | Placing the toggle switch in the “ice” position will energize the liquid line solenoid valve and the water pump and condenser fan motor through terminals 4 & 5 on the timer. This will allow the suction or low side pressure to rise. When the low side pressure reaches approximately 25 PSIG, the low pressure cut-out control will close its contacts, energizing the compressor. The cuber is now in freeze cycle. As water flows over the evapor- «Jr, the ice will begin to form. As the ice cubes form, the suction or low side pressure will continually decrease. At a present point the low pressure cut-in control will close its contacts. 10% PSIG regular and dice cube size and 11 PSIG half dice cube size. SEQUENCE II FREEZE CYCLE WITH TIMER ENERGIZED Sequence || Closing of the low pressure cut-in control contacts will energize the time delay circuit of the solid state timer through terminal 1. The remaining freeze time is dependent upon the timer setting. ) —— er WF Le | 7 Wi - PRESS 208 0RZ30 VOLT A.C. 1 PHASE 15 fe Ÿ WIRING MANUAL HARVEST SWITOH LOW - PRESS CUT-1H e 4 My # - E. "A TIMER y RELAY Y HOT GAS SOLENOID LIQUID SOLENOID FHERMODISC ый DES(371-4 REVISION D 81-0495-3 у A a ъ a Ll A Fg: ” , HI- PA oN CUT OUT | NN SWITCH ro с A . 16 15 A AU? $ Lor N j TOGGLE SWITCH CUT-OUT re a 8 1 waa HARVEST SWITCH Y LOW - PRESS A CUY - iN я 4 i / HM 208 OR230 D Кост A.C. N.C. и 1 PHASE u A Я CAPACITOR 7 НЫ Г И TIMER Г] Г 4 | e | RELAY ‚о | Г НОТ GAS dr e | SOLENOID Ц H р | и Те — | LU mÓTOR Jj AYER MP Г REMOTE, WIRING SER LIQUID SOLENO! FHERMODISC MANITOWOC ICE CUBERS — C-0600 Series SEQUENCE lll BEGINNING OF HARVEST CYCLE WITH LOW PRESSURE CONTROL STILL CLOSED Sequence Hi At the end of the timing sequence, the timer relay will energize. This will open the relay contacts between terminals 4 & 5 shutting off the con- denser fan motor and water pump and close the relay contacts between terminals 3 & 4 energizing the hot gas solenoid valve. The cuber is now in the harvest cycle. Shortly after the hot gas solenoid valve opens the low pressure cut-in control con- tacts will re-open. Ls | | 7 Ni- PRESS CUT-OUT LON - CUT- OUT LOS ON EJO VOLY A.C. I PHASE Ems " zz | le ER A Sy — lr — Page 27 IN SWITCH Е e TOGGLE SWITCH | I NN, om $ J GIRAR nd WIRING LA MANUAL HARVEST SWITCH LOW - PRESS CUT-IN 8 / M ss. | LÀ LIQUIDO - SOLENON THERMODISC — и В О \ / REVISION D SEQUENCE IV HARVEST CYCLE WITH LOW PRESSURE CONTROL OPEN 7115 Sequence IV Note: To manually place the cuber in harvest, see - timer description and check-out procedure, page 21. | As the harvest cycle progresses, the hot gas will warm the evaporator releasing the ice. The ice will fall through the ice chute, opening the damper door that is mounted in the chute. (Fig. 4) As the damper door is pushed open, it will trip the damper door (bin) micro switch, momentarily de- energizing the timer and liquid solenoid valve. The timer relay will return to its normal position, de- energizing the water pump and condenser fan motor. The cuber is now in a new freeze cycle. The ice cuber will continue to cycle in this manner until the storage bin is full. The ice cuber automat- | ically discontinues ice production as the ice filis the chute, holding the damper door and bin micro switch open. Hi - PRESS LOW - CUT-QOUT 208 CRESO VOLT A.C. I PHASE cur-our - 18 le D681371-4 8/-0495-3 — — —— —— 7 môton REMOTE WINING XX om» ‹ SEXE [ MANUAL HARVEST LOW - PRESS Сите # ii a] L LIQUID SOLENO! THERMODISC DENSER | 60/3714 - ое REVISION D 8/-0495-3 Page 28 Sequence V Opening the bin micro switch or placing the toggle switch in the “off” position will de-energize the liquid line solenoid valve. The system will begin to pump down the low side. When the suction or low side pressure reaches 2 PSIG, the low pressure cut-out control will open, de-energizing the com- pressor. Within the electrical system there are two safety controls to protect the cuber, the suction line ther- modisc and the high pressure cut-out. И the bin switch would fail when the ice falls through the ice chute, the cuber would remain in the harvest cycle until the suction temperature reached 70% F +5”. At this time the safety thermo- disc, located on the suction line, would open its contacts, de-energizing the timer relay and hot gas solenoid valve, placing the cuber back into the freeze cycle. As the evaporator begins to cool, the *armodisc will reclose its contacts at 40% F + 5°. 8 high pressure. cut-out control will shut the entire cuber off should the condensing or head pressure become too high. MANITOWOC ICE CUBERS — C-0600 Series SEQUENCE V TOGGLE SWITCH IN WATER PUMP POSITION Li | 7 Hi- PRESS CUT-OUT LOW - MESS CUT- OUT 208 OR230 VOLT A.C. ! PHASE ee | - \ TOGGLE SWITCN ” MANUAL HARVEST SWITCH LOW - PRESS CUT-1N 8 / M, q —— ——— — — — —" te man — MOTOR OR y ` CONDENSER WIRING r | | + > TIMER RELAY FHERMODISC LIQUID SOLENOID WATER PUMP ONLY SEQUENCE VI CUBER OFF ON. TOGGLE SWITCH, HIGH PRESSURE CUT-OUT OR “LOW PRESSURE CUT-OUT. Ll | | e Ni= PRESS CUT- OUT LOW - PRESS CcUT- OUT a 208 OR E30 РОСТ А. С. 1 PHASE ze | Do 3 FCH x 0 a 4 Dy GRADE мат | o e Sh SE ES ATER Tt MP REMOTE, TINO | Jd ‚410010 (3) FNERMODISC . REVISION D 68/37/-4 8/-0495- 3 REVISION D 681371-4 8r- 0495-3 isa MANITOWOC ICE CUBERS — C-0600 Series Page 29 SOLID STATE TIMER START Mi “0 MANUAL RUN CITOR CAPACITOR /732 9 HARVEST SERVICE 80X — == | @ y Le SUPPLY | Lr | | | Fi | LOW PRESS PT CUT-IN | 2087230 VOLT ras я THERMODISC SEE Г REMOTE CONDENSER | WIRING TO,F, TO Ls L Creen Toko TH TOGGLE SW 18 | MARK CAPACITOR 4 WIRING DIAGRAM CO690N CUBER W/ REMOTE CONDENSER AN 208/230 VOLT, 60 Hz, / PHASE or 230 VOLT, SOHz | PHASE . | 07 SHOWN AT BEGINNING OF FREEZE CYCLE , - | BN y ' SWITCH 9 с A 16 15 NN mee TOGGLE SWITCH CUT-OUT ve м a 17 . MANUAL : HARVEST LOW - PRESS | CUT -IN 8 “ 208 OR230 Кост А. с. 1 PHASE - LIQUIDO SOLENOID FHERMODISC REMOTE, WIRING Me Ш Dé81371-4 REVISION р 81-0495-3 Page 30 MANITOWOC ICE CUBERS — C-0600 Series PEFRIGERATION CYCLE — CO690N Cuber with AC-0695A Remote Condenser (Fig. 10) eze Cycle During the freeze cycle the high pressure discharge gas is pumped into the remote condenser. The high pressure gas is condensed into a high pressure liquid. The high pressure liquid leaves the condenser and goes through the head pressure control valve to the receiver. The purpose of the head pressure control valve is to maintain a minimum receiver head pressure of 90-100 PSIG for normal system operation. Because of the pressure drop this minimum pressure will be approxi- mately 10-15 PSIG higher at the compressor discharge valve. During colder weather this control will gradually flood the condenser and start by-passing hot gas to the receiver to maintain the 90-100 PSIG receiver head. An under charge will cause problems during cold weather (70° F. and below) and will show up in poor defrosting and premature energizing of the low pressure cut-in. During hot weather (80° F. and above) the receiver will be V2 to 3% full of liquid refrigerant. An overcharge can cause problems in hot weather when the refrigerant charge is more than the receiver can hold. The high pressure liquid leaves the receiver and goes through the heat exchanger reducing the liquid temperature making the system more efficient. The high pressure liquid is then metered into the evaporator by a thermostatic expansion valve. The expansion valve regulates the rate of refrigerant liquid flow into the evaporator in the exact proportion to the rate of evaporation of the refrigerant liquid in the evaporator. The expansion valve does this by responding to (1) the pressure in the evaporator (2) the temperature of the refrigerant gas leaving the evaporator using the valve feeler bulb to sense the gas temperature. After the low pressure liquid evaporates to a low pressure gas, it passes through the suction line heat exchanger and into the compressor. The ave. suction pressure will start at approx. 18 PSIG and drop to approx. 5-7 PSIG when the cuber goes into harvest. \ | ARVEST CYCLE The harvest is initiated by the solid state timer energizing the solenoid valve allowing high pressure hot gas to flow through the evaporator and harvest the ice. The suction pressure during the harvest is approx. 40- 60 PSIG. The head pressure will drop to approx. 70- 100 PSIG. When the hot gas solenoid valve opens, the head pressure will drop below the 100 PSIG minimum and the pressure drop across the head pressure control will be over 30 PSIG. This will cause the head pressure control valve to stop the liquid flow from the condenser and by-pass hot gas to the hot gas solenoid valve. The cuber goes back into the freeze cycle automatically when the solenoid valve is closed by the harvesting ice tripping the bin switch. The cuber is now in a new freeze cycle. C-0690N CUBER WITH AC- 0695A REMOTE CONDENSER OPERATING CHARACTERISTICS AIR FREEZE HARVEST TEMP. | CYCLE CYCLE 70 130-100 70-90 HEAD 80 | 140-100 70-95 PSIG 90 145-110 75-100 100 160-125 | 90-110 70 18-6 40-50 SUCTION 80 20-8 40-50 PSIG 90 . 21-8 50-60 100 22-9 55-65 *These are approx. characteristics that vary depending on operating conditions. «кото. y owns? MANITOWOC ICE CUBERS — C-0600 Series FIG. 10 Page 31 REFRIGERATION SCHEMATIC 600 SERIES WITH REMOTE AIR COOLED CONDENSER — _ = HEAT EXCHANGE SUCTION DISCHARGE EVAPORATOR COMPRESSOR Ces | { a | di ps | À HEAD PRESSURE "Il — RECEIVER , CONTROL Ÿ CHECK | DRIER E | —~ VALVE — | 7 e IS Борнео | : \ J = HOT GAS SOLE- ı | NOID VALVE | | AE NE (С) E To o eE ( HOT GAS- DURING) HARVEST CYCLE PUMP DOWN VALVE HIGH PRESSURE GAS BE HIGH PRESSURE LIQUID LOW PRESSURE LIQUID [J] LOW PRESSURE GAS E CONDENSER (REMOTE) Page 32 MANITOWOC ICE CUBERS — C-0600 Series FIG. 11 ; CO-0690N REMOTE CUBER COMPRESSOR COMPARTMENT . Compressor. Overload, compressor. Relay and capacitor box. Head pressure regulator. Mounting bracket for item 4. (No longer used) Mounting clip for item 4. (No longer used) Receiver. Drier. | - Expansion valve. Low pressure cut-out. Service ports. | Pump. down solenoid valve. Hot gas solenoid valve. Suction service valve. Sight glass. Thermodisc. Condenser lines quick connect fittings. NONPONHOSONOHIBON vb end «= ub «= «=й amb сей MANITOWOC ICE CUBERS — C-0600 Series GENERAL SYSTEM SERVICE ANALYSIS COMPLAINT Cuber will not run Cuber does not harvest or slow harvest CAUSE Toggle switch in neutral position Compressor or starting components defective Toggle switch defective High pressure cut-out tripped Blown fuse or power off Bin switch open (Remote Head) liquid solenoid not opening. Low pressure cut-out Control not set properly Low pressure control not closing Leaking cond. water valve (water cooled) Solid state timer defective, not energizing Safety thermodisc defective or loose on suction line Leaky hot gas valve during freeze cycle Ice bridge too thin, cubes should fall as sheet Defrost solenoid coil defective Suction pressure doesn’t drop - properly a. Defective expansion valve b. Leaky hot gas solenoid valve c. Expansion valve bulb loose Harvest rack bent-up restricting harvest Contaminated or limed water system, evaporator suction release holes plugged Low ambient (air cooled cubers) Cond. water valve set too low (water cooled) (Remote Cuber) Low Head Pressure during freeze cycle, min. 100 PSIG — low on refrigerant charge — head pressure control valve not -by-passing hot gas Page 33 CORRECTIVE MEASURE Turn switch to Ice-making position. See compressor check procedure. See toggle switch check procedure. Reset & check system. Replace fuse, check main switch Bend switch arm for proper action, Check free movement of damper door. See bin switch check procedure. Replace coil or complete valve assembly Re-calibrate or replace. (See Low Pressure cut-out (check procedure) See low pressure control check procedure. Replace water valve. See S.S. timer check f procedure. See safety thermodisc check procedure. | Replace valve. Adjust time up to increase bridge thickness. Replace solenoid coil or valve. “ - Replace expansion valve. Replace valve. - Tighten & insulate to suction line. . Bend center of rack down. Clean evaporator and water system. Ambient temperature must be above 55°. Set water valve to 125 PSIG head. measure in correct amount listed on name plate. Replace Page 34 COMPLAINT Ise shells instead if cubes or oridging too small Irregular size cubes & some cubes cloudy Too large cube bridge Low ice capacity High head pressure (Remote Cuber) MANITOWOC ICE CUBERS — C-0600 Series CAUSE Timer out of adjustment Low pressure cut-in control not opening Low refr. charge, leak in system Holes in water distributor plugged Shortage of water Distributor not in proper location Timer set too high — Low pressure cut-in set too low Sump overflow elbow out of position Defective Expansion Valve Sump water overflowing elbow during freeze cycle Float stuck in open position Water strainer dirty Leaky hot gas valve "Inefficient compressor High head pressure Fan motor or fan cycle switch defective Condenser water valve defective or not adjusted properly Dirty condenser Inadequate water supply (water cooled) Defective exp. valve Too hot cuber location with poor air circulation Air in refrig. system Overcharge of refrigerant Overcharge of refrigerant Head press. control valve malfunctioning, by passing hot gas when not needed CORRECTIVE MEASURE See check procedure. —. Check control, replace if defective. Locate leak, repair, evacuate & recharge if necessary. See major maintenance. Clean distributor. Check pump & water level in sump. Adjust. See timer check procedure. See L.P. cut-in check procedure. Adjust elbow. Replace. Adjust float to main- tain water level approx. 4" of flush elbow. Adjust until float moves freely. Remove & clean mesh screen. Check and replace if necessary. "NA т Check & replace if necessary. See high head pressure. Replace, see check procedure. ‘Replace water valve or adjust to 125 PSIG head. Clean condenser, see cleaning instructions. - Check supply line & water valve. Replace if considered necessary. Relocate or provide ventilation to area. Evacuate and recharge, see major maintenance. Correct charge. ; correct amount in. Remove charge & measure В Replace. — “ен” MANITOWOC ICE CUBERS — C-0600 Series Page 35 COMPLAINT CAUSE CORRECTIVE MEASURE Low head pressure Ambient temp. below 55° F Heat area or install low ambient fan switch. (Remote Cuber) Undercharge of refrigerant Leak Check. Remove charge & measure correct amount in. Head pressure valve Replace not functioning CLEANING INSTRUCTIONS AN PLACE CLEANING To clean the ice cuber water system without removing the components proceed as follows. NOTE — This is only recommended in locations where impurity build-up is not heavy. Remove ice cuber front panel. Shut off ice cuber. Remove ice from bin. Shut off water supply and remove water from water sump. Pour the recommended amount of ice machine cleaner into sump and turn water supply on. Place toggle switch to water pump position and circulate cleaner for about 30 minutes. After cleaning, shut machine off and remove cleaner. Flush water system thoroughly. Clean ice storage bin with ice machine cleaner also. о моя Бо ю DISASSEMBLING WATER SYSTEM FOR CLEANING To clean parts by removing proceed as follows: Shut machine off. | Remove splash curtain, water pump and water distrubutor. Disassemble distributor. Disassemble water pump as follows: PON. A. Turn pump over and remove the water inlet screen. See Fig. 7. B. Hold and depress impeller. Rotate plastic thumb nut counter-clockwise. C. Remove screws and pump housing. Pump is now ready for cleaning. D. Reassemble in reverse order as removed. 5. Inspect weep holes located in the corners of each cube section, using a brush to remove any scale build-up. Scrub all parts using a nylon scouring pad, brushes, and cleaning solution such as LIME-A-WAY from Economics Laboratory, Inc., or Boss Brand Milk Stone Cleaner from Northern Laboratories. Rinse all parts with clear water. It is recommended that the ice be removed from the storage bin before scrubbing the base and evaporator assembly. Rinse with clear water. Check to see that overflow or drain hole in the base is clear and that water drains through freely. Reassemble unit. To sanitize unit, mix ONE TEASPOON OF SODIUM HYPOCHLORITE (CHLORINE BLEACH) IN ONE GALLON OF WATER. Pour solution. into sump, then turn toggle switch to the left to start water pump. Keep pouring solution into sump until system has enough to keep pump primed. After one minute turn off pump and remove solution from water sump. Repeat with clear water before turning switch back to the ice - making position. Make visual inspection for leaks and operation before replacing the front panel. и J Page 36 | MANITOWOC ICE CUBERS — C-0600 Series SERVICE AND PARTS PROCEDURES DER AND PRICING PROCEDURE replacement parts for Manitowoc ice machine equipment should be ordered directly from your local Manitowoc Ice Machine distributor. Parts are stocked by the distributor in order to provide prompt and efficient service for ice machines sold in their areas. Should you encounter difficulty in locating a Manitowoc distributor in your area, contact Manitowoc Service Parts Dept. for the name or names of distributors in your area. When placing your order, be sure to do as follows: 1. Print name and address plainly. 2. [If special routing is requested, please show the name of the carrier. 3. Indicate quantity desired, print catalogue part number plainly and print name as shown in the catalogue. 4. Indicate model and serial number of the unit. The complete serial number is needed. 5. If uncertain as to the proper part number, please give a complete description or sketch of the part and the location of the part which is needed. 6. Check to see that all required information is contained in your order to facilitate prompt shipment from the factory on a f.o.b. Manitowoc basis. It is company policy to bill for all field replacement parts, according to terms as specified by our Credit Department. All parts orders will be honored by the factory and will be billed according to our parts lists schedules. Parts which are covered by our warranty policy are to be returned to the factory for credit, transportation charges prepaid. Upon receipt of these parts here at the factory, they will be inspected; and if they are found to be defective, in material and workmanship, under normal use and service, credit will be issued. Transportation companies are responsible for damages in transit as all shipments are tendered to them in “od condition; and our responsibility ceases upon receipt of a signed bill of lading from the carrier. If the Aipment arrives in a damaged condition or is short, the delivery carrier should be notified immediatly. RETURN OF DEFECTIVE PARTS All defective parts returned to the factory, transportation prepaid, must be tagged with a return material tag properly filled in. It is especially important that the cabinet serial number be secured and recorded on the tag, securing as much information as possible about the nature of the defect to prevent any delays in issuing credit. All parts should be returned as they are removed from the cabinet and not mutilated or tampered with. The return material tags are provided on a no-charge basis by the factory upon receipt of your request. Our warranty and protection plan does not apply to cabinets that are not registered; therefore, it is necessary that, upon completion of the installation of the cabinet, the registration card be signed on the date of installation and mailed promptly to the factory Service Department in order for the cabinet to be registered. RETURN OF HERMETICALLY-SEALED UNITS Extreme care should be used in servicing the hermetically-sealed mechanism. It is important that the trouble be correctly determined before the unit is changed. Be sure it is not the control, relay, or overload causing the trouble. The defect must be listed on the return material tag. RETURN OF COMPLETE MACHINES No complete machines may be shipped back to the factory for repairs without first securing prior permission from the factory. If an unauthorized shipment is received at the factory, it will be refused by our warehouse and immediately returned to the sender. Upon receipt of your request to return a cabinet, if we feel that your request is legitimate, you will be sent an authorized return label authorizing you to return this cabinet to the factory freight prepaid. On water cooled models, water lines and condenser must be completely rained and blown out before returning. SERVICE AND LABOR CHARGES | | In accordance with our warranty and protection plan, which is included in each cabinet, this protection plan provided is available only through distributors and dealers who will be soley responsible for service and labor charges. ——- Ke | MANITOWOC ICE CUBERS — C-0600 Series Page 37 SERIAL NUMBER NOMENCLATURE (Located On Nameplate) USED IN 1979 SERIAL NUMBER A LETTER ASSIGNED LOT RUN TO INDICATE — NUMBER EXTERIOR VARIATIONS WITHIN FINISH ANY ONE MODEL 0 = FAWN 1 = mn STEEL | | + | o | | TTT ou O 1 T MONTH | 8 80 aay MODEL ELECTRICAL CODE C= 81 C = MARCH NUMBER © 01=115 VOLT. 60cy. 1 PH. D= 82 D = APRIL 02 = 208/230 VOLT. 60cy. 1 PH. Е = 83 Е = МАУ 03 = 110 VOLT. 50cy. 1 PH. F = 84 F = JUNE 04 = 230 VOLT. 50cy. 1 PH. G- 85 G = JULY | 05 = 208/230 VOLT. 3 PH. H= 86 H = AUG. J = 87 J = SEPT. к = 88 К = OCT. L= 89 L = NOV. M= 190 M = DEC. N= 91 Р = 92 a= 93 E STARTED USING IN 1980 SERIAL NUMBER | 81.04 12 3 4 | | | YEAR MONTH The 8 digit serial number has a built-in production date code. The first 2 digits indicate the year and the second 2 digits indicate the month. Always use the entire 8 digit serial number and model number when identifying the unit. Page 38 MANITOWOC ICE CUBERS — C-0600 Series Ire Machine and Bin Warranty From the date of original installation, we do hereby warrant each new Ice Machine and Bin to be free from defects in material and workmanship, under normal use and service, for a period of one year, and four additional years on the hermetic motor compressor in the Ice Machine. Our obligation under this warranty is limited solely to correcting or replacing without charge at the factory in Manitowoc, Wisconsin any part or parts of this equipment which shall have been returned, transportation prepaid, and which our examination discloses to our satisfaction to be defective. This warranty does not apply to any equipment that has been damaged by flood, fire, or suffered abuse, misuse, neglect or accident, or to any Ice Machine which has been altered so as to affect performance .or reliability, except where such alteration has been accomplished with our prior written consent. We further limit this warranty in that we shall not be held liable under this contract for any special, indirect, or consequential damages whatsoever resulting from any defect in material and workmanship which interferes with the normal use and service of such ice Machine and Bin. : This warranty is a complete and exclusive statement of all terms of the agreement between the Manitowoc Equipment Works and the owner of the equipment, and all representations of the parties. This agreement shall not be varied, supplemented, qualified or interpreted by any prior course of dealing \ between the parties or by any usage of the trade. J Sales are made on the express understanding that there are no express or implied warranties other than the express warranty herein contained and that there are no implied warranties that the goods shall be merchantable or fit for a particular purpose other than the expressed one year and five year warranty set forth above. | | To validate this warranty, the registration card must be signed on the date of installation and mailed promptly to the Manitowoc Equipment Works, Manitowoc, Wisconsin. DEALER INSTALLATION DATE MANITOWOC EQUIPMENT WORKS (A division of The Manitowoc Co., Inc.) 2110 South 26th St., Ph: 414-682-0161 Manitowoc, Wisconsin 54220 Form 80-0032-1 ALL ; IF | Co Page 38 MANITOWOC ICE CUBERS — C-0600 Series Ire Machine and Bin Warranty From the date of original installation, we do hereby warrant each new Ice Machine and Bin to be free from defects in material and workmanship, under normal use and service, for a period of one year, and four additional years on the hermetic motor compressor in the Ice Machine. Our obligation under this warranty is limited solely to correcting or replacing without charge at the factory in Manitowoc, Wisconsin any part or parts of this equipment which shall have been returned, transportation prepaid, and which our examination discloses to our satisfaction to be defective. This warranty does not apply to any equipment that has been damaged by flood, fire, or suffered abuse, misuse, neglect or accident, or to any Ice Machine which has been altered so as to affect performance .or reliability, except where such alteration has been accomplished with our prior written consent. We further limit this warranty in that we shall not be held liable under this contract for any special, indirect, or consequential damages whatsoever resulting from any defect in material and workmanship which interferes with the normal use and service of such ice Machine and Bin. : This warranty is a complete and exclusive statement of all terms of the agreement between the Manitowoc Equipment Works and the owner of the equipment, and all representations of the parties. This agreement shall not be varied, supplemented, qualified or interpreted by any prior course of dealing \ between the parties or by any usage of the trade. J Sales are made on the express understanding that there are no express or implied warranties other than the express warranty herein contained and that there are no implied warranties that the goods shall be merchantable or fit for a particular purpose other than the expressed one year and five year warranty set forth above. | | To validate this warranty, the registration card must be signed on the date of installation and mailed promptly to the Manitowoc Equipment Works, Manitowoc, Wisconsin. DEALER INSTALLATION DATE MANITOWOC EQUIPMENT WORKS (A division of The Manitowoc Co., Inc.) 2110 South 26th St., Ph: 414-682-0161 Manitowoc, Wisconsin 54220 Form 80-0032-1 ALL ; IF | Co Mm pn =?
advertisement
Related manuals
advertisement