Kärcher HDS 1295-4 SX Eco High pressure washer Operating instructions
Add to my manuals
23 Pages
Kärcher HDS 1295-4 SX Eco hot water pressure washer tackles stubborn dirt and grime effortlessly thanks to its impressive 3200 PSI and flow rate of 2.7 GPM. Ideal for cleaning vehicles, buildings, tools, and more, it features infinitely variable pressure and temperature settings, allowing you to adjust the cleaning intensity to suit the task at hand. The machine also offers detergent metering for precise application of cleaning agents.
advertisement
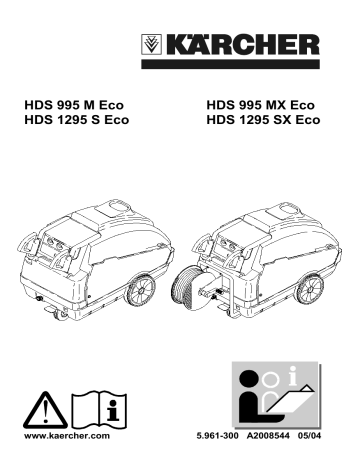
HDS 995 M Eco
HDS 1295 S Eco
HDS 995 MX Eco
HDS 1295 SX Eco
www.kaercher.com 5.961-300 A2008544 05/04
Dansk
Norsk
Svenska
Suomi
2
Deutsch
English
Français
Italiano
Nederlands
Español
Português
38
55
72
88
104
7
23
120
138
153
168
183
Magyar
Č esky
Slovensko
Polska
Române ş te
Türkçe
Русский
Slovensky
Hrvatski
Srpski
Български
198
214
230
246
263
280
296
314
330
346
362
1
2
3
4
5
6a
6b
7
10
11a
8
9
11b
12
13
14
15
16
17
18
19
Operating Instructions
Contents
Environmental protection
Unit illustration
Operating controls
Reference to operating instructions
Commissioning
Operation
After every operation
Decommissioning
Maintenance
Maintenance tasks
Faults
Warranty
General notes
EC conformity declaration
Technical data
Parts list
30
30
31
32
25
25
27
29
35
35
36
37
379
23
24
24
English
Warning!
Prior to initial operation it is mandatory to read the operating instructions and the notes on safety no. 5.951-949!
Inform retailer immediately of any transportation damage.
Environmental protection
Please dispose of packaging environmentally responsibly
The packaging materials are recyclable.
Please do not throw the packaging in with household rubbish but take it to a recycling centre.
Please dispose of scrapped units environmentally-responsibly
Scrapped units consist of valuable recyclable materials that should be taken to a recycling centre. Batteries, oil and similar products must not be allowed to contaminate the environment. Therefore, please dispose of scrapped units via appropriate disposal systems.
Please ensure engine oil, fuel oil, diesel and petrol to contaminate the environment. Please protect the ground and dispose of used oil ecologically.
Danger: Steam!
Danger of scalding! Steam escapes here.
23
Unit illustration
Operating controls
1 Fuel tank inlet
2 Handle
3 Instrument panel
4 Window with the
maintenance/fault display
5 Cover latch
6 Compartment für accessories
7 Short operating instructions
8 Cover for compartment
9 Unit cover
10 Cover for tank inlet
11 Tank inlet für scale inhibitor
12 tank inlet for cleaning agent
13 High-pressure nozzle
14 Handle grips in the chassis
15 Steel pipe
16 Pressure and flow control
17 Swivel caster with parking brake
18 Water connection with strainer
19 High-pressure connection
20 Handgun with high-pressure hose
22 Electric power cord
23 Unit switch
24 Temperature regulator
25 Fuel indicator lamp
26 Scale inhibitor indicator lamp
27 CHEM1, CHEM2 indicator lamp
(applies only to HDS 1295)
28 Engine/electronics indicator lamp
29 Ready for working indicator lamp
30 Pressure gauge
31 Metering valve for cleaning agent
32 Hose reel (applies only to MX/SX)
33 Crank (applies only to MX/SX)
34 Fine filter
24
Operating Instructions English
Reference to operating instructions
!
For other water hardnesses request services of a Kärcher service station and have it adapted to local conditions.
All of the item numbers described below in the operating instructions are referenced in the illustration of the unit.
Filling with fuel
Commissioning
Warning!
Never operate unit with fuel tank empty!
Fuel pump would otherwise be destroyed!
Warning!
Unit, piping, high-pressure hose and connections must be in perfect working order!
!
Lock the hand brake.
Checking oil level
Fig. 1
Fig. 3
Warning!
Only fill with diesel fuel or light fuel oil.
It is forbidden to use unsuitable fuels, e.g. benzine (explosion hazard, damage to unit).
!
Close tank cap
!
Wipe off excess fuel
Warning!
Immediately consult the Kärcher service station when oil turns milky!
!
If oil level is approaching MIN mark, fill up with oil as far as MAX mark.
!
Seal oil filler inlet.
Refer to technical data for oil grade.
Filling with scale inhibitor
Fig. 2
(sample pack included with scope of delivery)
Scale inhibitor stops heating coil becoming calcified when using hard tap water. Is is metered in at the inlet in the water reservoir one drop at a time.
By the manufacturer metering is set to a mean water hardness.
Fill with cleaning agent
— Use only Kärcher products.
— Never pour in solvent (petrol, acetone, thinner etc.)!
— Avoid contact with eyes and skin
— Pay attention to cleaning-agent manufacturer's instructions on safety and handling
Kärcher offers a customised cleaning and care agent range.
Your dealer will be pleased to advise you.
Fig. 4
Fill with cleaning agent
25
Installing the handgun (units without hose reel)
!
Connect steel pipe (item 15) with handgun (item 20)
!
Insert high-pressure nozzle in union nut
!
Mount and tighten unit nut
!
Install the high-pressure hose to highpressure connection of unit. (Figure 6a)
Installing the handgun and the hose reel (units with hose reel)
!
Connect steel pipe (item 15) with handgun (item 20)
!
Insert high-pressure nozzle in union nut
!
Mount and tighten unit nut
!
Install the hose reel (item 32) with the provided Allen screws, washers and nuts (4 of each). (Figure 5)
!
Install the high-pressure hose at the high-pressure connection of hose reel and unit. (Figure 6b)
!
Connect high-pressure hose of handgun to hose reel
!
Wind high-pressure hose onto hose reel with the smallest possible bends
(direction of turns – clockwise -)
Drawing in water from tank
When you suction water out of an open container you should
!
remove water connection at pump head.
!
screw off the top supply hose with the fine filter to the water tank and connect to pump head.
!
Use a water suction hose with a suction filter and a diameter of at least 3/4".
Until the pump sucks up water you should:
!
Turn the pressure and flow control to
"MAX".
!
close the metering valve for the cleaning agent.
Warning!
Never suction up water out of a potable water tank.
Never suction up solvent-bearing liquids such as paint thinner, benzine, oil or unfiltered water. The seals in the unit are not resistant to solvents. The mist of solvents is highly inflammable, explosive and poisonous!
Mounting of spare high-pressure hose
Fig. 7
Mains connection
See technical data and rating plate for connected load.
Mounting handle
Fig. 8
Water connection
!
See Technical Data for connected loads.
!
Install supply hose at water connection
(item 18) of unit.
(supply hose is not part of scope of delivery)
Warning!
It is not permissible to exceed the maximum permissible mains impedance at the electrical terminal (see Technical Data).
Warning!
Whenever socket is changed, check direction of rotation of motor
26
Operating Instructions English
— If direction of rotation is correct, powerful jet of air will be felt at exhaust-gas opening of burner.
— If the direction of rotation is wrong: Change the poles at the unit plug. See Fig. 18.
!
When an extension cable is used it should always be complety unwound and have an adequate cross-section.
Setting cleaning temperature
!
Set the remperature regulator (item 24) to the required temperature
30°C to 90°C
Hot water cleaning
100°C to 150°C
Cleaning with steam
!
Replace high-pressure nozzle by the steam nozzle (see operation using steam)
Operation
Switch on the machine
!
Set unit switch (item 23) to "I"
Ready for working indicator lamp (item 29) is lit
Warning!
The temperature regulator (item 24) must be set to "0", since otherwise the burner possibly switches on
Unit starts up briefly and is switched off as soon as operating pressure is reached.
Stop the unit immediately when one of the indicator lamps (items 25-28) light up during operation. Eliminate fault, refer to
Faults.
Fig. 9
!
Release the safety of the handgun (A)
Actuation of handgun switches unit back on again.
Bleed pump if no water emerges from highpressure nozzle. See problems, "Unit does not build up pressure"
Setting operating pressure and flow rate
Fig. 10
— Turning control spindle clockwise: Increasing operating pressure
(MAX)
— Turning it counterclockwise: Reducing operating pressure (MIN)
Servopress control
!
Set the temperature regulator (item 24) to max. 98°C.
!
Set regulator to maximum operating pressure.
Fig. 9
Adjust operating pressure and flow rate by turning (infinitely variable) at the pressure and flow control (B) (+/-)
Set pressure on unit if use is to be made of reduced pressure for a lengthy period.
See Fig. 10
27
Measuring out cleaning agents
— Use cleaning agents sparingly to protect the environment
— The cleaning agent must be appropriate for the surface to be cleaned.
!
Using the cleaning agent metering valve
(item 31) set the concentration of the cleaning agent as specified by the manufacturer
Approximate values at maximum operating pressure
Intended use
For cleaning: machines, vehicles, buildings, tools, facades, patios, gardening implements, etc.
Warning!
— Heed appropriate safety regulations for use at petrol stations or in other hazardous environments.
Please ensure waste water containing mineral oil does not contaminate soil, lakes and rivers or the sewerage system. Therefore, please wash engines and underbodies only in appropriate washing installations provided with oil traps.
Working with high-pressure nozzle
Spray angle is crucial to efficiency of highpressure jet.
Use is normally made of 25°fan jet nozzle
(included).
Recommended nozzles, available as accessories
— For stubborn dirt
0°full jet nozzle
— For sensitive surfaces and superficial dirt
40°-fan jet nozzle
— For thick-film, stubborn dirt
Dirt blaster
— Nozzle with adjustable spray angle, adaptable to many cleaning tasks
Variable-angle nozzle
Cleaning
!
Set pressure/temperature and detergent concentration appropriately to surface to be cleaned
Always start by directing high-pressure jet from a good distance at object to be cleaned to avoid damage caused by excessive pressure.
Recommended cleaning method
Loosen up dirt:
!
Spray on cleaning agent sparingly and allow to react for 1...5 min (do not allow to dry on).
Remove dirt:
!
Spray off loosened-up dirt with highpressure jet.
Operation with cold water
Removal of slight contamination and rinsing e.g: gardening implements, patio, tools, etc.
!
Set operating pressure as required
!
Set temperature control (item 24) to "0"
28
Operating Instructions English
Operation with hot water
Warning!
Danger of scalding
!
Set the remperature regulator (item 24) to the required temperature
We recommend the following cleaning temperatures
— Slight contamination 30-50°C
— Protein soiling, e.g. in foodstuffs industry max. 60°C
— Motor vehicle cleaning, machine cleaning 60-90°C
Safety deactivation
If the handgun is not opened or closed for more than 30 minutes, for safety reasons the pump switches off automatically.
— To switch it on again turn the main switch to "0" and then back to "I".
(EPROM without shut down 6.682-595 available from service)
Operation with steam
Danger: Steam!
At operating temperatures above 98°C operating pressure must not exceed 32 bar
(HDS 1295: 28 bar).
Therefore the following steps must be taken without fail:
!
Replace high-pressure nozzle by steam nozzle
Manufacture no.:
4.766-023
4.766-024
!
See Figure 9 (B)
HDS 995
HDS 1295
Fully open water delivery control at the handgun, in the + direction to the stop.
!
Set operating pressure to minimum value. See Fig. 10
!
Set the temperature regulator (item 24) to min. 100°C
Danger: Steam!
Danger of scalding!
We recommend the following cleaning temperatures
— Preservative removal, extremely greasy dirt 100-110°C
— Thawing of aggregates, certain facade cleaning operations up to 140°C
After every operation
Warning!
Danger of scalding with hot water.
After operating it with hot water or steam, to cool it the unit must be operated at least two minutes with cold water with an open handgun.
Following operation with cleaning agent
!
Set cleaning agent metering valve
(item 31) to "0"
!
Set unit switch (item 23) to "I"
!
Actuate handgun and flush unit for approx. 1 min
Stopping machine
!
Set unit switch (item 23) to "0"
!
Shut off water supply
!
Switch the pump briefly on with the unit switch (item 23) (approx. 5 sec.)
!
Remove mains plug from socket ONLY with dry hands
!
Remove water connection
!
Actuate handgun to depressurise unit
!
Put on safety of handgun Figure 9 (A)
!
Engage spray lance in cover holder
29
!
Reel up the high-pressure hose and electric cables and attach them to fastenings
Note!
Take care not to kink high-pressure hose and cable!
Note!
Frost will destroy unit if water is not drained off completely!
!
Store unit in a frost-free location
Observe the following if the unit is connected to a flue:
Danger of damage caused by cold air entering through the flue. Disconnect unit from flue at outside temperatures below
0°C.
Immobilise unit if frost-proof storage is not possible.
Decommissioning
In the event of lengthy periods of non-use or if frost-free storage is not possible:
!
Drain off water and flush out equipment with antifreeze
!
Drain cleaning fluid tank
Drain off water
!
Unscrew water supply hose and highpressure hose
!
Screw off supply line at boiler base and completely drain heating coil
!
Run unit for max. 1 min until pump and lines are empty
Flushing unit with anti-freeze
!
Fill the float tank with a commercially available antifreezing compound
!
Swith the unit on (without the burner) until it is thoroughly purged
!
Observe handling instructions of antifreeze manufacturer
By this means, a certain degree of corrosion protection is achieved
Maintenance
Warning!
Disconnect unit from mains before carrying out any maintenance or repair work.
Always use genuine spare parts
Turn off unit prior to all work, see "After every operation".
!
Set unit switch (item 23) to "0"
!
Pull power plug out of socket
!
Shut off water supply
!
Actuate handgun to depressurise unit.
!
Remove water connection
!
Allow unit to cool down
Your Kärcher dealer will be pleased to inform you on the performance of regular safety inspections and conclusion of a maintenance contract
30
Operating Instructions English
Maintenance intervals
Display
Once a week
— Clean strainer in water connection
— Clean the fine filter
— Check oil level
Immediately consult the Kärcher service station when oil turns milky!
Once a month
— Clean strainer in low water protection
— Clean filter at cleaning-agent suction hose
After 500 hours of operation, at least once a year
— Change oil
Necessary maintenance work
!
Visual inspection
!
Check that the high-pressure connections do not leak
!
Clean the fuel tank and the filter
Display
Maintenance tasks
Engine/electronics indicator lamp (item 28) is lit
Necessary maintenance work
!
Check that the pump does not leak
!
Change the pump's oil
!
Clean strainer in water connection
!
Clean the strainer (coarse) fitted in front of the low water protection
Display
— This warning lamp lights up when certain maintenance work is necessary due to accumulated operating hours.
!
When you open the cover (item 8) of the compartment (item 6) the electronic display is visible in the window (item 4).
!
When the necessary maintenance work has been completed you should depress the RESET button next to the display for at least 7 seconds until the warning lamp goes out.
Necessary maintenance work
!
Decarbonise the heating coil *
!
Descale the heating coil *
!
Clean/replace the ignition electrodes *
!
Cleaning/replacing the burner nozzle *
!
Adjust the burner *
Display
Necessary maintenance work
!
Check the overflow valve for leaks *
!
Check the high-pressure hose *
!
Clean the handgun
!
Check the pulsation damper *
* This maintenance work should be performed only by after-sales service.
31
Clean strainer in water connection
Fig. 11
!
Remove strainer
!
Clean in water and re-insert
Clean the fine filter
Fig. 12
!
Cut pressure to unit
!
Screw off cover with filter
!
Clean filter with clean water or with compressed air
!
Assemble in the reverse order
Change oil
Fig. 16
!
Provide a collecting container for approx. 1 litres of oil
!
Unscrew drain plug
Dispose of used oil ecologically or hand it in at a dump.
!
Retighten drain plug
!
Top up oil slowly up to the MAX mark
Air bubbles must be able to escape
Refer to technical data for oil grade and quantity to be used.
Clean strainer in low water protection
Fig. 13
!
Unfasten union nut and detach hose
Fig. 14
!
Take out strainer
If necessary, screw-in screw M8 by approx. 5 mm and pull out the strainer with this screw
!
Clean strainer in water
!
Slide in strainer
!
Mount hose
!
Tighten union nut
Faults
Engine/electronics indicator lamp
(item 28) flashes
— This warning lamp flashes if there is a problem.
!
When you open the cover (item 8) of the compartment (item 6) the electronic display is visible in the window (item 4).
!
The warning lamp goes out when the problem has been resolved and the unit is switched on again.
Display
Clean filter at cleaning-agent suction hose
Fig. 15
!
Pull the cleaning agent suction inlet pipe out
!
Clean filter in water and re-insert Troubleshooting
!
Increase the water inlet volume
!
Clean strainer in water connection
!
Clean the strainer (coarse) fitted in front of the low water protection
32
Operating Instructions English
Display
Troubleshooting
!
Replace the reed switch for the low
!
water protection *
Clean the low water protection *
Display
Troubleshooting
!
Eliminate the leakage in the highpressure system
Display
Troubleshooting
Motor overloaded/overheated
!
Turn monitoring switch to "0" and allow engine to cool for at least 5 min
!
Have unit checked by After-Sales
Service if this does not remedy fault
!
Cbeck exhaust gas temperature limiter, reset, if necessary (Figure 19)
Display
Troubleshooting
!
This error code appears only on units equipped with the – accessory kit flame monitoring system -
!
See the assembly instructions – accessory kit flame monitoring system -
* This maintenance work should be performed only by after-sales service.
Ready for working indicator lamp
(item 29) goes out
— Motor overloaded/overheated
!
Set selector switch to "0" and allow engine to cool off for at least 5 min.
!
Have unit checked by After-Sales
Service if this does not remedy fault.
!
No mains voltage
(see – unit does not run -)
Fuel indicator lamp (item 25) lights up
— Fuel tank empty
!
Fill up
Liquid softener indicator lamp (item 26) lights up
— Scale inhibitor reservoir empty; for technical reasons there is always a residual quantity in the reservoir.
!
Fill up
— Dirt on electrodes in reservoir
!
Clean electrodes
Unit does not run
— No mains voltage
!
Check electric mains/power cord
Unit does not build up pressure
— Air in system
Bleed pump:
!
Set cleaning agent metering valve
(item 31) to "0"
!
Switch the unit switch on and off several times keeping the handgun open.
!
With handgun open, open and close regulator (Fig. 10).
Venting is accelerated by removing the high-pressure hose from the high-pressure connection.
33
!
Fill up cleaning-agent tank if empty.
!
Check connections and lines
— Pressure set to MIN
!
Set pressure to MAX
— Strainer in water connection is dirty
!
Clean strainer
!
Clean fine filter, replace it if necessary
— Insufficient water supply
!
Check water supply volume (refer to technical data)
Unit leaking, water dripping out at bottom
— Pump leaking
3 droplets/min are permitted.
!
In the event of a major leak, have unit checked by After-Sales Service.
Unit constantly switched on and off with handgun closed
— Leak in high-pressure system
!
Check high-pressure system and connections for leaks
Unit does not draw in cleaning agent
!
Run the unit with an opened cleaning agent metering valve and a closed water supply until the float tank is sucked dry and the pressure drops to "0".
!
Now reopen the water inlet.
If the pump still does not suction up cleaning agent the reasons can be as follows:
— Filter in cleaning-agent suction hose dirty
!
Clean filter
— Non-return valve gummed up
!
Pull the cleaning agent hose off and detach the non-return valve with a blunt object, see Figure 17.
34
Burner not ignited
— Fuel tank empty
!
Fill up
— Lack of water
!
Check water connection, check supply, clean low water protection.
— Fuel filter is dirty
!
Replace fuel filter.
— Incorrect direction of rotation. If direction of rotation is correct, powerful jet of air will be felt at exhaust-gas opening of burner.
!
Check direction of rotation. If necessary, change round poles of unit plug. See
Fig. 18.
— No ignition spark
!
Have unit checked by After-Sales
Service if no ignition spark is visible through inspection glass during operation.
Set temperature not attained when working with hot water
— Excessive operating pressure/flow rate
!
Reduce operating pressure/flow rate by way of regulator (Fig. 10)
— Soot deposits on heating coil
!
Have After-Sales Service remove soot deposits from unit
The unit must be checked by after sales service if the problem cannot be remedied.
Operating Instructions English
Warranty
The warranty terms and conditions issued by our responsible sales company apply in every country. Within the warranty period, any faults in the unit will be rectified free of charge provided that the problem was caused by a material defect or manufacturing error.
The warranty only applies if the dealer fills in, stamps and signs the enclosed reply card when the unit is sold and the purchaser then returns it to the appropriate local distributor.
In the event of a warranty claim, please contact your dealer or the nearest authorised After-Sales Service office and produce both accessories and proof of purchase.
General notes
Safety features
Overflow valve with two pressure switches
— When reducing water volume at pump head or with the servopress control, the overflow valve will open and part of the water will flow back to the pump suction side.
— If the handgun is closed off so that all the water flows back to the pump suction side, the pressure switch at the overflow valve turns off the pump.
— Reopening the handgun causes the pressure switch at the cylinder head to switch the pump back on again.
The overflow valve is set at the factory and lead-sealed. Adjustment can only be made by After-Sales Service.
Safety valve
— The safety valve opens if the overflow valve or pressure switch is defective.
The safety valve is set at the factory and sealed. Adjustment can only be made by
After-Sales Service.
Low water protection
— The low water protection prevents the burner switching on when water is insufficient.
— A strainer prevents dirt accumulation on the protection and must be regularly cleaned.
Motor protection switch
— The motor protection switch interrupts the circuit should overloading occur.
Switching on procedures
— Switching on procedures generate brief voltage drops.
— Impairments of other appliances can occur in cases of unfavourable mains conditions.
— No problems are to be expected with a mains impedance of less than 0,15 ohm.
35
EC conformity declaration
We hereby declare that the machine specified below as the marketed desigh, the machine specified below complies with the relevant fundamental safety and health requirements of the EC directives listed below.
Modification of the machine without our approval invalidates this declaration.
Product: High-pressure cleaner
with a steam stage
Type: 1.027-xxx, 1.028-xxx
Relevant EC directives
EC machine directive (98/37/EC)
EC low voltage directive (73/23/EEC) amended by 93/68/EEC
EC directive on electromagnetic compatability (89/336/EEC) amended by
91/263/EEC, 92/31/EEC, 93/68/EEC
EC high-pressure equipment directive
(97/23/EG)
EC guideline on noise emissions
(2000/14/EU)
Applied harmonised standards
DIN EN 60335-1
DIN EN 60335-2-79
DIN EN 55014-1:2000 + A1:2001
DIN EN 55014-2:1997
DIN EN 61000-3-2:2000
DIN EN 61000-3-3:1995 + A1:2001
(HDS 995)
DIN EN 61000-3-11:2000 (HDS 1295)
Applied national standards
---
Applied conformity valuation method
Appendix V
Measured sound power level:
HDS 995
HDS 1295
89 dB(A)
88 dB(A)
Guaranteed sound power level:
HDS 995 91 dB(A)
HDS 1295 89 dB(A)
Internal measures ensure that the in series produced units always comply with the requirements of current EC directives and applied standards. The signatories act for and in authority of management.
5.957-649 (02/04)
Alfred Kärcher Limited Partnership.
Registered office: Winnenden. Registration court: Waiblingen, HRA 169.
Personally liable partner. Kärcher
Reinigungstechnik GmbH. Registered office Winnenden, 2404 Waiblingen
Company Register, HRB
Managing directors:
Dr. Bernhard Graf, Hartmut Jenner,
Georg Metz
Alfred Kärcher GmbH & Co. KG
Cleaning Systems
Alfred-Kärcher-Strasse 28-40
P.O.Box 160
D-71349 Winnenden
Phone: ++49 7195 14-0
Fax :++49 7195 14-2212
36
379
380
advertisement
* Your assessment is very important for improving the workof artificial intelligence, which forms the content of this project
Related manuals
advertisement