advertisement
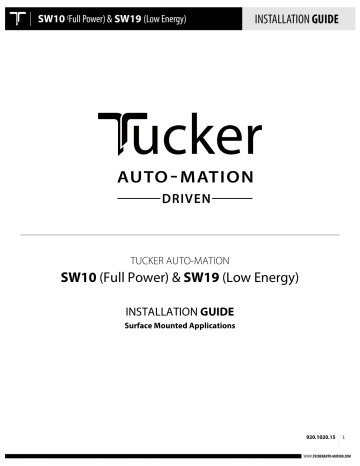
TUCKER AUTO-MATION
SW10
(Full Power) &
SW19
(Low Energy)
INSTALLATION GUIDE
Surface Mounted Applications
920.1020.15
1
TABLE OF CONTENTS:
PAGE
3
4
5-10
11-14
15-17
17-18
19
20
21-24
25
26
27
28
29-31
32-33
25 (KP EVO 1-25)
CONTENTS
Important Notices
Product Description & Specifications
Header Installation
Mounting The Operator & Control Assembly
Push Arm Installation
Pull Arm Installation
120 Volt AC Connection
Power On & Indications
Set-Up Procedures
Wiring Connections
Adjusting The Mechanical Door Stop
Troubleshooting
Job Documentation & Closeout / Accessories / Company Contact
Appendix - Wiring Diagrams
Appendix - Fire Rated Door Application
Appendix - Tap Programming Device - KP evo
920.1020.15
2
IMPORTANT
READ THIS SECTION BEFORE PROCEEDING WITH INSTALLATION
Tucker Auto-Mation, LLC (hereafter referred to as “Tucker”) recommends that all of its automated pedestrian door products be installed by a trained automatic door technician and that the resulting performance of the product be in full compliance with the most current version of the American National
Standards Institute document A156.10 or A156.19 (whichever is applicable) as well as any applicable building codes and/or fire codes. Tucker further recommends that a full inspection of the operating system be performed in accordance with the guidelines of the American Association of Automatic Door manufacturers
(AAADM). This inspection must be performed by a certified AAADM trained inspector. Tucker recommends this documented inspection be performed upon completion of the installation as well as, following the completion of every service call thereafter. If service is not performed within one year of the previous service action, a routine AAADM inspection should be performed and documented. Under no circumstance should the product operate for more than one year without an AAADM inspection. Tucker does NOT recommend installation or service, on any of their automated pedestrian door products, by any individual who is not certified as an AAADM inspector.
Following the installation or service of any Tucker automated pedestrian door product, if it is deemed unsafe, or is operating in an unsatisfactory manner according to national performance standards or recommended performance guidelines as defined by Tucker, repairs should be made immediately. If an immediate repair cannot be made, the product should be disabled, and appropriate measures should be taken to secure the door in a safe position or to enable the door to safely be used manually. During this situation, every effort should be made to notify the owner (or person responsible) of the condition and to advise on corrective actions that must be taken to return the product to safe operation.
LOW ENERGY APPLICATION NOTE
When using the SW10/19 for a low energy application, Tucker Auto-Mation recommends the use of a doormounted presence sensor on the approach side of the door to be used as a secondary activation device. This type of sensor can be installed at time of installation or can also be retrofitted. This device serves to re-activate the door to the open position should a person enter into the closing path at the approach side of the door, as it is closing. Once the door is fully closed, a "knowing act" device must then be used for initial activation.
Tucker Auto-Mation considers this device to be essential in reducing the possibility of doors "timing out" and closing before all pedestrians have passed though the doorway. Check with your Tucker sales representative to find out about special incentives that may be available for the Torpedo 1 door-mounted presence sensor.
920.1020.15
3
PRODUCT DESCRIPTION & SPECIFICATIONS
The Tucker Auto-Mation SW10 & drives. The unique design offers; non-including sensors, push plates, fire alarm, and electric locks. Troubleshooting when needed. Both units can be configured concealed application.
The Tucker Advanced Programmer (TAP) is provided as an option to access additional programming features.
Power Supply
Power Consumption
Current Consumption
Motor
Header Dimensions
Fused Protection
Weight
Ambient Operating Temperature
Ingress Protection
115 VAC (+6%, -10%) 60Hz
100W
1A
24 VDC Permanent Magnet With Belt Driven Encoder
20 3/4” x 4 1/8” x 4 3/4” (l x w x d)
3.5A Fuse (F1 located on I/O Board)
22 lbs Per Operator Assembly
-4 to 131º F
IP23 (protection from spray water up to 60º from the vertical – ie. Rainstorm)
Maximum Door Weight PUSH ARM PULL ARM
36” Door: 438 lbs 342 lbs
42” Door: 328 lbs 256 lbs
44” Door: 299 lbs 234 lbs
48” Door: 254 lbs 198 lbs
24 VDC Accessories Power Supply
24 VDC Electric Lock Power Supply
Adjustable Speeds & Timers
Standard Selector Switch Functions
Standard Control Outputs
Standard Control Inputs
Quick Disconnects
24 VDC / I A. Max
24 VDC / I A. Max
Opening Speed
Closing Speed
Hold Open Time
Closing Speed with power off
Automatic
Hold Open
Manual (Off)
Malfunction Alarm Signal
Electric Lock Relay
24 VDC Accessories Power Supply
Door Status
Interior Activation
Exterior Activation
Emergency Shutdown
Alarm Output
“Stop” Safety Device (door-mounted)
Safety Device Input
Secondary Activation
TAP-Controller (optional)
920.1020.15
4
HEADER INSTALLATION
Mount the pre-drilled back-plate to the top door frame using appropriate fasteners for the type of frame. (Refer to Door Prep drawings on pgs. 6-10.)
• Push side mounting: Pre-drilled back-plate is flush with bottom of door frame.
•
Pull side mounting: Pre-drilled back-plate is mounted 1.5” up from bottom door frame.
•
Back-plate should overlap each jamb tube by 1.5”.
•
Refer to the APPENDIX for fire rated door applications.
PUSH ARM APPLICATIONS :
Bottom of header is flush with bottom of top frame.
NOTE:
Tucker Auto-Mation is now using a 35mm spindle adaptor for all standard push arm applications – this requires that the header assembly be mounted as shown at left, flush with bottom of top frame.
PULL ARM APPLICATION: STANDARD PULL ARM
& DOUBLE EGRESS APPLICATIONS
Double egress applications require the use of an
80mm spindle adaptor for the side using the push arm.
920.1020.15
5
Door Prep drawings:
PUSH SIDE INSTALLATION SINGLE
Opening Width
36"
42"
44"
48"
Operator Width X Dim
39" 6.25"
45"
47"
51"
12.25"
14.25"
18.25"
920.1020.15
6
PUSH SIDE INSTALLATION DOUBLE
Opening Width Operator Width A Dim C Dim
72" 75" 12-7/16" N/A
84"
88"
87"
91"
N/A
N/A
10-7/8"
14-7/8"
96" 99" 24-7/16" 22-7/8"
920.1020.15
7
PULL SIDE INSTALLATION SINGLE
Opening Width Operator Width Y Dim
36"
42"
44"
48"
39"
45"
47"
51"
6.25"
12.25"
14.25"
18.25"
920.1020.15
8
PULL SIDE INSTALLATION DOUBLE
Opening Width Operator Width A Dim C Dim
72" 75" 12-7/16" N/A
84"
88"
96"
87"
91"
99"
N/A
N/A
10-7/8"
14-7/8"
24-7/16" 22-7/8"
920.1020.15
9
DOUBLE EGRESS INSTALLATION
Opening Width Operator Width A Dim C Dim
72" 75" 12-7/16" N/A
84"
88"
96"
87"
91"
99"
N/A
N/A
10-7/8"
14-7/8"
24-7/16" 22-7/8"
920.1020.15
10
MOUNT THE OPERATOR(S)
• Operator is non-handed – same operator for all hands of doors
• Handing is determined by how the operator is mounted inside the header
• The operator is mounted to a short aluminum “drive” plate that is held into the header by 5 mounting screws.
Four (4) of the screws secure the drive plate. One (1) screw is used to locate the drive plate using a ‘keyhole’ configuration. The keyhole allows for easy removal of the drive plate without the need to loosen to screw.
Removing the four (4) screws allows the drive plate & operator to be removed from the header and rotated 180 degrees to change from a push to a pull or vice versa.
Drive Plate mounted in standard position using four (4) screws to secure. Loosen the screws using an 5 mm allen wrench and slide each one off of the drive plate.
Drive plate removed by shifting to the left and lifting the drive plate off of the locating screw.
920.1020.15
11
Drive plate rotated 180 degrees to reverse the operator handing. Re-align locating screw to key slot, insert drive plate and shift to the right into position. Re-position the four (4) screws to secure the drive plate.
Key slot configuration & location screw mounted in backplate
920.1020.15
12
PUSH = I/O BOARD IS TOWARDS THE HINGE JAMB
920.1020.15
13
•
Mount the header to the doorframe with the screws provided.
• The header will overlap the doorframe by 1-1/2" at each side.
920.1020.15
14
PUSH ARM INSTALLATION
• All push arms come standard with 35mm spindle. 50mm and 80mm available as an accessory.
• Attach the primary door arm approx. 20 degrees past perpendicular and towards the closing direction as shown.
If more spring tension is desired, simply increase the mounting angle to greater than 20 degrees so it results in increased preload.
920.1020.15
15
• Adjust the secondary telescopic arm to the prescribed length according to chart:
Reveal Hinge Hung X Dim.
Center Pivot X Dim.
0"
5"
6"
7"
8"
1"
2"
3"
4"
13"
14"
15"
16"
17"
18"
19"
20"
21"
DEEPER REVEAL REQUIRES ARM EXTENSION
16"
17"
18"
19"
20"
21"
•
Before installing any portion of the door arm assembly, it is easiest to lay the arm out on a flat surface and insert the secondary and primary arm into the sleeve as it will be when installed on the door: o Slide the short arms within the sleeve to obtain the prescribed "X" dimension. o Tighten the screws on the short arm that is connected to the door shoe. o Double-check the "X" dimension of the arm - this is the distance between the center of the hole at the door shoe and the center of the hole at the pivot point of the primary arm (as shown). o Mark a pencil line at the edge of the sleeve where it overlaps the short arm that is connected to the primary arm. This will make it easier when positioning the primary arm for final installation.
• Attach the secondary arm mounting bracket to the door. The centerline of the bracket should be at 13-1/2” in from the inside face of the hinge jamb when using butt hinges on the door, and 16” when using a center pivoted door.
920.1020.15
16
• Rotate the primary arm in the opening direction as to reach the pivot point of the secondary. Attach the arms together with the hardware provided.
PULL ARM INSTALLATION
Standard Pull Arm
For 0-degree reveal
Use 20mm spindle
Offset (double egress) Pull Arm
For reveal greater than 0 degrees
Use 20mm Spindle
Slide Track
920.1020.15
17
• Install the slide track assembly at the pull side of the door at the proper location from the hinge end of the door as shown below:
• To install the pull arm, the operator must be powered to the full open position, as it is not possible to install the arm in the closed position as to allow proper preload.
• Power the door to the open position through the use of the hold-open switch on the side of the header. It may be necessary to first execute a “setup” on the operator prior to doing this. Refer to the applicable section within this User’s Guide for proper instruction.
• Once the operator is rotated to the full open position, manually move the door to the desired full open position and insert the slide track guide block into the track. When completed, the end caps to the track can be installed.
920.1020.15
18
120 VOLT AC ELECTRICAL CONNECTION
WARNING:
Ensure all incoming electrical power is shut off before proceeding with any wiring to
SW10/19. Use only with wire harness provided; failure to do so may result in damage to equipment or personal harm as well as voiding the warranty.
•
Connect the main power to the Black / White / Green connector on the back-plate. o Main power supply: 120 VAC, 15A, Single Phase, 60 Hz. circuit o Attach the incoming 120 volt AC line wires to the wiring provided in the header – as shown below.
•
DO NOT TURN POWER ON until all remaining wiring has been completed.
BLACK: 115 VAC Power
WHITE: Neutral
GREEN: Ground
920.1020.15
19
POWER ON & INDICATIONS
DL1 : GREEN USB CONNECTION
DL2: FLASHING RED LED
DL3: BLUE 5V POWER SUPPLY
DL4: BOARD VALUES DIFFER FROM DIP SWITCHES
(PRESS SW1 MOMENTARILY TO EXTINGUISH YELLOW LED)
Upon applying power, observe the above LED’s.
NORMAL OPERATION: DL3 will come on steady and then begin flashing after a few seconds.
FAULTY OPERATION; DL2 will be flashing red. This indicates…
• An error condition exists – correct as necessary
• Operator requires setup – launch a setup and proceed accordingly
NOTE: DL4 will illuminate yellow anytime a change has been made to the control, such as a speed or time adjustment.
Momentarily press on SW1 to acknowledge the change and extinguish the yellow LED.
HELPFUL NOTES:
•
Speed and time adjustment changes will not take effect until the door closes fully after the adjustment has been made.
•
Hold Open time affects the delay following activation from input 10, 11, and 13.
• When Dip Switch 5 is ON, the blue speed and time potentiometers are disabled and will have no effect.
920.1020.15
20
SET-UP PROCEDURES
• Perform a setup at the control as follows: o Ensure main power is on o At the I/O control board, depress the SW1 button for approximately 5 seconds.
When the red LED (LD2) at the Adjustment Board begins flashing rapidly, release the button. The blue LED will continue flashing. o Door will slowly go open, recycle partially, close and then re-open. o Do not interrupt the process and do not move the door manually during this time. o If the door does not open and the red LED (DL2) is flashing slowly, check to make sure the motor is plugged in properly at the control board. Correct as necessary. o Once the setup process is complete, the door will close and the LED will go out. o Setup is complete.
IMPORTANT NOTE: If the operator stroke is altered in any way, a re-learn must be accomplished.
•
Upon completion of the Setup, activate the door to open and ensure all performance is acceptable.
• Adjust opening and closing speed as necessary. If speeds are changed, a re-learn is not required.
•
A re-learn is not required following a main power recovery.
•
Adjust hold-open time as required.
•
Additional adjustments are available through the TAP.
920.1020.15
21
SETUP BUTTON
B1 – Battery – use CR1216 battery – required to maintain timer settings and date programmed by the TAP
TR1 – Opening speed adjustment
TR2 – Closing speed adjustment
TR3 – Hold-open time adjustment
TR4 – Closing speed adjustment when power is OFF TR4 will only be enabled when jumper J6 is moved to the correct pins. (it is enabled by default).
J2 – USB port
J4 – Ribbon cable connector between boards
J5 – Motor Connector
J7 – Power supply connector between boards
SW1 – “Parameter Changed” button
SW2 – 10 Position “Functions” Dip Switch
For adjustments beyond those mentioned herein, use the TAP. See TAP Users Guide for additional information.
920.1020.15
22
SET THE DIP SWITCHES ON THE I/O BOARD
•
Set the dip switches according to the application.
•
Dip switches are used to apply specific functions to the control.
•
There are 3 sets of dip switches. TWO 2 - POSITION on the I/O board (DS1 & DS2), and a 10position at the adjustment board (SW2).
DS2 DS1 NOT USED
SET THE DIP SWITCHES ON THE ADJUSTMENT BOARD
• Set the dip switches according to the application.
SW2
920.1020.15
23
Description ON
1 Closed Door Force Additional force applied while door is in closed position. Be sure to maintain
ANSI compliance if using on low
2 Push / Pull Arm energy application. Cannot exceed 30 lbf to get door moving from jamb.
Slide Arm Application. Operator stroke at 90
°
degrees or less. Visible
3 Night Function (Exit
Only) change in performance may not always be noticeable.
Allows activation at input 10 when
On-Off switch is in OFF (night function) position.
4
5 Full Power / Low
6
7
8
9
Push and Go
Energy
Lockout Function
Inhibit at 30
Degrees Before
Door Fully Open
Power Close
Assisted Manual
Closing***
10 FACTORY USE ONLY
OFF
Disabled (Default)
Push Arm Application.
Operator stroke 90 greater. (Default)
°
or
Enabled
Low Energy performance enabled. 5 seconds to open, 7 seconds hold open, 5 seconds to close. Speed & time potentiometers are disabled.
Settings are fixed.
Overhead presence sensor input (17) is inhibited during closing cycle unless input 14 is triggered. Connect COM and Input 14 to NC output of lockout safety beam.
Input is disabled at 30 degrees prior to full open door position. Eliminates need for external inhibiting switch.
Additional closing force applied for final 10 degrees of closing.
Enabled assisted closing following a manual opening
Disabled. The On/Off switch, when OFF, requires manual operation of the door. (Default)
Disabled (Default)
Disabled. Control can be adjusted for full power or low energy operation via potentiometers. (Default)
Disabled. Overhead presence sensor input (17) is inhibited during closing cycle. Otherwise, if commanded, it keeps an open door open and a closed door closed. A command at Input 14 will stall the door. (Default).
Stall function remains uninhibited for full door stroke. (Default)
Disabled (Default)
Disabled assisted closing following a manual opening
*** Tucker Auto-Mation recommends the use of a door-mounted secondary activation device when dip switch 9 is ON - Enabled.
920.1020.15
24
WIRING CONNECTIONS
(wiring diagrams are located in the Appendix)
I/O BOARD CONNECTIONS
Position Function Description
1
2
Electric Lock
Relay
Electric Lock
Relay
Common
3
4
5
6
Electric Lock
Relay
Door Status -
Closed
Door Status –
Common
Door Status -
Open
N.O. Dry contact – Contact closes upon activation. May be used for fail-secure locks by routing 1 leg of power though the relay. Relay is triggered by activation inputs 10, 11, or
16. Relay remains energized until door is fully closed again.
N.C. Dry Contact - Contact opens upon activation. May be used for fail-safe locks by routing 1 leg of power though the relay. Relay is triggered by activation inputs 10, 11, or
16. Relay remains energized until door is fully closed again.
N.O. Contact is closed when door is closed. The contact opens as soon as the door opens.
Common contact for door status
7
8
9
10
11
12
13
14
GND
GND
+ 24 VDC
Internal
Activation
External
Activation
Emergency
Closing
Secondary
Activation
“Stall” Safety
N.C. – Contact is closed when door is open. The contact opens as soon as the door starts to close. This input can be used for motor connection at lockout relay when power is looped through, thus switching power on when door is open.
Common GND
Common GND
I A. Max Current
Requires N.O. Contact between input 10 & COM. Remains capable to activate when dip switch 3 is ON AND On-Off switch is OFF.
Requires N.O. Contact between input 11 & COM.
Requires N.C. contact between 12 & COM. Upon open contact, door closes and overrides all other inputs. Remains jumpered if input is not used.
Requires N.C. contact between 13 & COM. Disabled in full closed position.
15
16
17
18
19
20
21
KEY
Alarm Input
Overhead
Presence
Sensor Input
GND
GND
Aux Relay
Aux Relay
Requires N.C. contact between 14 & COM. Upon open contact, (Dip 6 OFF) during opening, door stops, then resumes at reduced speed when input is released.
KEY IMPUT
N.O. contact, when closed causes door closing. All inputs inhibited during closed contact
(not available on all software versions)
Requires N.O. contact between 14 & +24 VDC (input 9). When input is closed it causes an open door to stay open and a closed door to stay closed. Works in conjunction with dip switch #6.
Common GND
Common GND
Auxiliary Relay NOTE: Relay is triggered by input 14
Auxiliary Relay N.O.
22
23
Aux Relay
Alarm Output -
Common
Auxiliary Relay N.C.
Common
24
25
26
Alarm Output N.O. output is closed upon closed contact from fire alarm. LED 2 also illuminates.
+ 24 VDC I A. Max Current
GND
Inputs 27 & 28 not used
Common GND
920.1020.15
25
ADJUSTING THE MECHANICAL DOOR STOP
• CAUTION – DO NOT REMOVE THE STOPS
• IMPORTANT - This step may be optional depending on your application
•
The mechanical stops are located on the top or bottom of the operator, depending on the hand of the door.
•
Apply 120 VAC Main power to the control o Place the On-Off-Hold switch to the Hold Open position
920.1020.15
26
TROUBLESHOOTING
Door will not open
Door will not close
Door will not reach its full open or closed position
Slow flashing red LED (LD2) at the
Adjustment Control Board
Door closes too fast at last 5 to 10 degrees of closing
•
Check On-Off switch for proper position
•
Check LED status for LD 5, 6, and 7. If any of these LED’s are OFF, the door will not open. They require a normally closed circuit.
•
Launch a new setup – see page 26
• Check status of emergency input 12
•
Door has traveled close past the 0 degree position
•
Check status of LEDs” LD2, 3, 4, 8 on the I/O board.
•
If any of the LED’s are ON, check the associated input
•
Check the mechanical stops on the operator for proper adjustment
•
Indicates a possible fault in the control. o Check LED status for the other inputs. This will identify if any inputs are currently active.
•
Indicates a potential faulty setup. o Loose or incorrect motor connection o Possible loose chain tensioner - refer to Appendix for chain tensioner adjustment procedures. o Launch a new setup. If problem repeats and there are no other discrepancies noted, replace the operator/control subassembly.
•
Ensure dip switch 8 is OFF.
•
Ensure there is no binding of the door as it is closing through the last few degrees of closing. If binding exists (from a tight bottom sweep, for example), correct the condition and then re-launch a new setup.
920.1020.15
27
JOB DOCUMENTATION & CLOSEOUT
•
Upon completion of the installation, provide the following to the Owner or their assigned agent: o Completed & signed work ticket. Be certain to record any serial numbers for items that were replaced. o Completed and signed copy of the AAADM inspection form o AAADM Owner’s Manual
• Additionally, advise the Owner of the work that was performed and ask if there are any other doors that may require service.
ACCESSORIES
•
Tucker BAT Microwave Motion Sensor - PN: 200.1068
•
Tucker TORPEDO ONE door-mounted presence sensor - PN: 200.1087
•
Spindle Adaptors 20, 50, 80 mm
• TAP Controller – KP EVO
COMPANY CONTACT
•
Tucker Auto-Mation Supply, LLC
Toll Free: 1-855-8 TUCKER (1-855-888-2537) – Service: Tel. 412-823-2537
Email: [email protected]
• WWW.TUCKERAUTO-MATION.COM
920.1020.15
28
APPENDIX - WIRING DIAGRAMS
LOW ENERGY APPLICATION: PUSH PLATES WITH APPROACH SIDE DOOR-MOUNTED SENSOR
• Non-Swing Side (approach) door-mounted sensor is wired into the secondary activation input (13) at the SW19 I/O board. It is a normally closed circuit.
•
Door-mounted sensor will cause re-activation when in detection during the closing cycle.
•
Secondary activation input is disabled at the full closed door position.
• Jumpers must be installed between terminal 8 and 12 & 14 if those inputs are not required for the application. If they are used for the application, they must be connected to a N.C. circuit.
920.1020.15
29
SIMULTANEOUS PAIRS
920.1020.15
30
• When wiring controls for use as a simultaneous pair, all required inputs need to be sync’d (connected) between Door #1 and Door #2 (shown as dotted lines in above diagram).
• Example shown above: Push plates are connected to inputs 8, 10 and 11 at door #1 and are connected via sync line to Door #2.
• When using pairs of controls, N.C. inputs 12, 13 and 14 may be sync’d to each other,
OR each control may have it’s own jumpers installed. If any of these inputs are required for the application, the jumper will be removed for the respective input – in place of the jumper, a N.C. switching circuit will connected to Door #1, and a sync line will be connected to Door #2.
• For simultaneous pairs, Tucker Auto-Mation provides a dual harness for the On-Off-
Hold switch. Each plug-in connector for the control is wired in parallel to the On-Off-
Hold switch located in the header end-cap. One switch will control both doors.
• All control adjustments (speed & time delay) must be made independantly at each control.
• All dipswitches at each control must be set independantly and must match between controls.
• When using the TAP programmer, settings must be made independantly at each control and must match between controls.
920.1020.15
31
APPENDIX - FIRE RATED DOOR APPLICATION
•
Perform the installation according to the instructions outlined in this manual.
Additionally, ensure the following conditions have been met: o When attaching the door arm to the door, use steel binding posts (Sex Bolts) to attach.
Do NOT use sheet metal screws into the face of the door. The door arm bracket must be through-bolted. o When attaching the header to the hollow metal door frame, ensure there are 5 attaching screws spaced equally apart.
They should be #12 sheet metal type screws.
920.1020.15
32
o Fire rated power operated doors must close and latch during a fire alarm condition.
Ensure proper procedures have been followed to allow a main power disconnect during a fire alarm condition. Always check to ensure compliance to local building codes.
§ Upon job completion, always perform a functional test to ensure that the door(s) close and latch following a power loss. o Other hardware may be required to complete the installation. For example, for pairs of doors, if an Astragal is installed, a mechanical door coordinator may be required to ensure a proper coordinated closing during a power loss. o Only fire rated hardware shall be used on a fire rated door & frame assembly. o Ensure the Tucker SW10/19 that is being installed has the proper fire rated label applied to the header.
920.1020.15
33
APPENDIX - TAP PROGRAMMING DEVICE
Please note, some functions of the SW10/19 controller require the use of a hand-held “TAP” programming device.
The following functions require use of this device for programming:
ü Logic Assignment For Inputs
ü Logic Assignment For Outputs
ü Opening & Closing Acceleration
ü Opening & Closing Deceleration
ü Opening & Closing Strength (obstruction force)
ü Opening & Closing Strength Duration (time duration for obstruction force)
ü Night-Time Hold Open Time
ü Delay On Activation (up to 4 seconds)
ü Electric Lock Interfacing
ü Master/Slave Configuration
ü Cycle Count – Maintenance Reset
ü 7-Day Programmable Timer (With Daylight Savings Time)
ü Troubleshooting & Data
920.1020.15
34
KP evo
- TAP CONTROLLER INSTALLATION GUIDE
T U C K E R A U T O - M AT I O N
KP evo
- TAP CONTROLLER
WWW.TUCKERAUTO-MATION.COM
KP evo
- TAP CONTROLLER
IMPORTANT
READ THIS SECTION BEFORE PROCEEDING WITH INSTALLATION
INSTALLATION GUIDE
Tucker Auto-Mation, LLC (hereafter referred to as “Tucker”) recommends that all of its automated pedestrian door products beinstalled by a trained automatic door technician and that the resulting performance of the product be in full compliance with themost current version of the American National
Standards Institute document A156.10 or A156.19 (whichever is applicable) as well as any applicable building codes and/or fire codes. Tucker further recommends that a full inspection of the operating system be performed in accordance with the guidelines of the American Association of Automatic Door manufacturers (AAADM). This inspection must be performed by a certified AAADM trained inspector. Tucker recommends this documented inspection be performed upon completion of the installation as well as, following the completion of every service call thereafter. If service is not performed within one year of the previous service action, a routine AAADM inspection should be performed and documented. Under no circumstance should the product operate for more than one year without an AAADM inspection. Tucker does NOT recommend installation or service, on any of their automated pedestrian door products, by any individual who is not certified as an AAADM inspector. Following the installation or service of any Tucker automated pedestrian door product, if it is deemed unsafe, or is operating in an unsatisfactory manner according to national performance standards or recommended performance guidelines as defined by
Tucker, repairs should be made immediately. If an immediate repair cannot be made, the product should be disabled, and appropriate measures should be taken to secure the door in a safe position or to enable the door to safely be used manually. During this situation, every effort should be made to notify the owner (or person responsible) of the condition and to advise on corrective actions that must be taken to return the product to safe operation.
T U C K E R A U T O - M AT I O N
KP evo - TAP CONTROLLER
920.1003.02 | 01
WWW.TUCKERAUTO-MATION.COM
KP evo
- TAP CONTROLLER INSTALLATION GUIDE
TABLE OF CONTENTS
KP evo
TABLES
1. KP EVO
. . . . . . . . . . . . . . . . . . . . . . . . . . . . . . . . . . . . . . . .
1.1 Installation and connections
. . . . . . . . . . . . . . . . . .
1.2 Switching on and the home screen
1.3 SELECTION menu
1.4 FUNCTIONS menu
. . . . . . . . . . . .
. . . . . . . . . . . . . . . . . . . . . . . . . . . . .
. . . . . . . . . . . . . . . . . . . . . . . . . . . .
3
3
4
5
6
A P EVO menu ................................................................. 07
B Access permissions and passwords ............................... 13
C I/O board LEDs .............................................................. 14
D Logic board LEDs .......................................................... 14
E Status ........................................................................... 14
F Warnings ...................................................................... 15
2. DIAGNOSTICS
. . . . . . . . . . . . . . . . . . . . . . . . . . . . . . . . .
44
2.1 LEDs check
. . . . . . . . . . . . . . . . . . . . . . . . . . . . . . . . . . .
44
I/O board LEDs
. . . . . . . . . . . . . . . . . . . . . . . . . . . . . . . . .
44
G Errors ............................................................................ 16
H Selecting the upload/download function ...................... 18
I Scheduled maintenance ............................................... 21
Logic board LEDs
. . . . . . . . . . . . . . . . . . . . . . . . . . . . . . . . . . . . . . . . . . . . . . . . . . . . . . . . . . . . . . . . . . . . . . . . . . . . . . . . . . . . . . . . . . . . . . . . .
14
2.2 Inputs and outputs status check
. . . . . . . . . . . . . . . . . . . . . . . . . . . . . . . . . . . . . . . . . . . . . . . . . . . . . . . . . . . . . . . . . . . . . . . . . . . . . . . . .
14
2.3 Automation status check
. . . . . . . . . . . . . . . . . . . . . . . . . . . . . . . . . . . . . . . . . . . . . . . . . . . . . . . . . . . . . . . . . . . . . . . . . . . . . . . . . . . . . . . .
14
2.4 Warnings . . . . . . . . . . . . . . . . . . . . . . . . . . . . . . . . . . . . . . . . . . . . . . . . . . . . . . . . . . . . . . . . . . . . . . . . . . . . . . . . . . . . . . . . . . . . . . . . . . . . . .
15
2.5 Errors . . . . . . . . . . . . . . . . . . . . . . . . . . . . . . . . . . . . . . . . . . . . . . . . . . . . . . . . . . . . . . . . . . . . . . . . . . . . . . . . . . . . . . . . . . . . . . . . . . . . . . . . . .
16
2.6 Other board data
. . . . . . . . . . . . . . . . . . . . . . . . . . . . . . . . . . . . . . . . . . . . . . . . . . . . . . . . . . . . . . . . . . . . . . . . . . . . . . . . . . . . . . . . . . . . . . .
17
2.7 Firmware versions
. . . . . . . . . . . . . . . . . . . . . . . . . . . . . . . . . . . . . . . . . . . . . . . . . . . . . . . . . . . . . . . . . . . . . . . . . . . . . . . . . . . . . . . . . . . . . .
17
2.8 Log Data
. . . . . . . . . . . . . . . . . . . . . . . . . . . . . . . . . . . . . . . . . . . . . . . . . . . . . . . . . . . . . . . . . . . . . . . . . . . . . . . . . . . . . . . . . . . . . . . . . . . . . . .
17
3. UPLOAD / DOWNLOAD . . . . . . . . . . . . . . . . . . . . . . . . . . . . . . . . . . . . . . . . . . . . . . . . . . . . . . . . . . . . . . . . . . . . . . . . . . . . . . . . . . . . . . . .
18
4. PUT TING INTO SERVICE
. . . . . . . . . . . . . . . . . . . . . . . . . . . . . . . . . . . . . . . . . . . . . . . . . . . . . . . . . . . . . . . . . . . . . . . . . . . . . . . . . . . . . . .
19
4.1 Final checks
. . . . . . . . . . . . . . . . . . . . . . . . . . . . . . . . . . . . . . . . . . . . . . . . . . . . . . . . . . . . . . . . . . . . . . . . . . . . . . . . . . . . . . . . . . . . . . . . . . .
19
4.2 Final operations
. . . . . . . . . . . . . . . . . . . . . . . . . . . . . . . . . . . . . . . . . . . . . . . . . . . . . . . . . . . . . . . . . . . . . . . . . . . . . . . . . . . . . . . . . . . . . . .
19
Installing a plastic cover
. . . . . . . . . . . . . . . . . . . . . . . . . . . . . . . . . . . . . . . . . . . . . . . . . . . . . . . . . . . . . . . . . . . . . . . . . . . . . . . . . . . . . . . . . .
19
Installing an aluminium cover
. . . . . . . . . . . . . . . . . . . . . . . . . . . . . . . . . . . . . . . . . . . . . . . . . . . . . . . . . . . . . . . . . . . . . . . . . . . . . . . . . . .
20
5. MAINTENANCE
. . . . . . . . . . . . . . . . . . . . . . . . . . . . . . . . . . . . . . . . . . . . . . . . . . . . . . . . . . . . . . . . . . . . . . . . . . . . . . . . . . . . . . . . . . . . . . . .
20
5.1 Inserting / replacing the battery
. . . . . . . . . . . . . . . . . . . . . . . . . . . . . . . . . . . . . . . . . . . . . . . . . . . . . . . . . . . . . . . . . . . . . . . . . . . . . . .
20
5.2 Replacing the fuse
. . . . . . . . . . . . . . . . . . . . . . . . . . . . . . . . . . . . . . . . . . . . . . . . . . . . . . . . . . . . . . . . . . . . . . . . . . . . . . . . . . . . . . . . . . .
20
5.3 Routine maintenance
. . . . . . . . . . . . . . . . . . . . . . . . . . . . . . . . . . . . . . . . . . . . . . . . . . . . . . . . . . . . . . . . . . . . . . . . . . . . . . . . . . . . . . . . .
21
6. INTERCOM
. . . . . . . . . . . . . . . . . . . . . . . . . . . . . . . . . . . . . . . . . . . . . . . . . . . . . . . . . . . . . . . . . . . . . . . . . . . . . . . . . . . . . . . . . . . . . . . . . . . .
22
6.1 Intermode . . . . . . . . . . . . . . . . . . . . . . . . . . . . . . . . . . . . . . . . . . . . . . . . . . . . . . . . . . . . . . . . . . . . . . . . . . . . . . . . . . . . . . . . . . . . . . . . . . .
23
6.2 Interlock . . . . . . . . . . . . . . . . . . . . . . . . . . . . . . . . . . . . . . . . . . . . . . . . . . . . . . . . . . . . . . . . . . . . . . . . . . . . . . . . . . . . . . . . . . . . . . . . . . . . .
23
Interlock
with no memory
. . . . . . . . . . . . . . . . . . . . . . . . . . . . . . . . . . . . . . . . . . . . . . . . . . . . . . . . . . . . . . . . . . . . . . . . . . . . . . . . . . . . . . .
24
Interlock
with memory
. . . . . . . . . . . . . . . . . . . . . . . . . . . . . . . . . . . . . . . . . . . . . . . . . . . . . . . . . . . . . . . . . . . . . . . . . . . . . . . . . . . . . . . . . .
24
6.3 2 Leaves . . . . . . . . . . . . . . . . . . . . . . . . . . . . . . . . . . . . . . . . . . . . . . . . . . . . . . . . . . . . . . . . . . . . . . . . . . . . . . . . . . . . . . . . . . . . . . . . . . . . .
24
6.4 2 Leaves
+
Interlock . . . . . . . . . . . . . . . . . . . . . . . . . . . . . . . . . . . . . . . . . . . . . . . . . . . . . . . . . . . . . . . . . . . . . . . . . . . . . . . . . . . . . . . . . .
24
7. COMPANY ADDRESS
. . . . . . . . . . . . . . . . . . . . . . . . . . . . . . . . . . . . . . . . . . . . . . . . . . . . . . . . . . . . . . . . . . . . . . . . . . . . . . . . . . . . . . . . . . . .
25
920.1003.02 | 02
WWW.TUCKERAUTO-MATION.COM
KP evo
- TAP CONTROLLER
1. K P evo
1.1 INSTALLATION AND CONNECTIONS
CARRY OUT THE FOLLOWING OPERATIONS WITH THE
ELECTRICITY SUPPLY DISCONNECTED
1. Disassemble the parts (
0 1
).
2. Break the cable passage insert.
With reference to
0 2
, the KP EVO is designed for the cables to enter from the back (1) or from underneath (2).
3. Decide where to position the support and fix it using suitable screws (
0 1
1 ).
4. Connect the KP EVO to the 950N2 using a 4 pair twisted U/UTP AWG24 cable with a maximum length of 50m (
0 3
).
An optional key device can be connected between terminals G and K in order to enable/disable the KP EVO.
5. Reassemble the parts indicated in (
0 1
).
INSTALLATION GUIDE
1
2 max 50 m
0 2
J3 950N2
0 3
1
1
1
0 1
920.1003.02 | 03
WWW.TUCKERAUTO-MATION.COM
KP evo
- TAP CONTROLLER INSTALLATION GUIDE
1.2 SWITCHING ON AND THE HOME SCREEN
1. Turn power on to the 950N2
2. The display will show the following in sequence:
KP EVO
3. The 4 buttons are used to select controls that, depending on the screen, appear on the display above them.
4. By pressing the relative button on the home screen
(
0 4
) you can:
-
= set the NIGHT mode
BOOTLOADER X.X
in which the Bootloader version appears, then
KP EVO
VERSION X.X
in which the firmware version appears, and lastly
A951 xxx dd/mm/yy xxxxxx hh:mm
The content of this home screen, including the fixed icons and those that may appear under certain circumstances, is explained in
0 4
.
By pressing the button to set the NIGHT or MANUAL mode, the relative icon is highlighted and the description of the operating mode is updated on the display.
Once MANUAL mode has been set by pressing the relative button, press it again to return to the previous mode. current warnings KP EVO locked timer active
A951 xxx dd/mm/yy xxxxxx hh:mm
- product name
- day and date or error
- operating mode
- time set / deselect NIGHT mode switch to the SELECTION menu set / deselect MANUAL mode switch to the FUNCTIONS menu
0 4
920.1003.02 | 04
WWW.TUCKERAUTO-MATION.COM
KP evo
- TAP CONTROLLER
1.3 SELECTION MENU
To access the SELECTION menu from the home screen, press the
button (
0 5
).
4 New icons appear on the display that define the operating modes that can be set.
The possible combinations can be obtained by pressing the corresponding buttons (
0 5
).
After having set the operating mode, press the OK button to confirm and return to the home screen.
The description of the operating mode on the display is updated with the description of the one that has been set.
description of the current operating mode
INSTALLATION GUIDE
% OK xxxxxx
AUTOMATIC
INTERLOCK
(press for 5 s)
BI-DIRECTIONAL
100%
EXIT ONLY
%
ENTRY ONLY
0 5
920.1003.02 | 05
WWW.TUCKERAUTO-MATION.COM
KP evo
- TAP CONTROLLER
1.4 FUNCTIONS MENU
To access the FUNCTIONS menu from the home screen, press the entered.
button (
0 6
).
The display prompts for a 4-digit password to be
The factory-set password is: 0000
Set the first digit using the
and
buttons.
Confirm using the OK button to move to the next digit.
When all 4 digits have been entered, if the password is correct, access the FUNCTIONS menu as a
USER or a TECHNICIAN.
Select the item from the menu using the
and
buttons.
Confirm using the OK button to enter.
Press ESC at any time to return to the home screen.
menu items
1 LANGUAGE
2 PROGRAMMING
3 ERRORS
4 WARNINGS
5 CYCLES COUNT
6 DATE/TIME
7 TIMER
8 PASSWORD
8 INFO menu name
INSTALLATION GUIDE
ENTER PASSWORD
**** 2 xxxxxxxx
4 xxxxxxxx
MENU sets the value
0 6
920.1003.02 | 06
WWW.TUCKERAUTO-MATION.COM
KP evo
- TAP CONTROLLER INSTALLATION GUIDE
A KP EVO menu
1 LANGUAGE
1 ITALIANO
2 ENGLISH
3 FRANCAIS
4 DEUTSCH
5 ESPANOL
6 NEDERLANDS
2 PROGRAMMING
1 INPUTS / OUTPUTS
1 INPUTS I1-I8
I1…I8
0 DISABLED
1 EXTERNAL OPEN
4 INTERNAL OPEN
7 AUTOMATIC OPEN
8 SEMIAUTOM. OPEN
10 KEY
11 PARTIAL OPEN
20 CLOSING SAFETY
21 OPENING SAFETY
22 OVERHEAD PRES. SENS
30 EMERGENCY OPEN
31 EMERGENCY OPEN WITH MEM
34 EMERGENCY CLOSE
35 EMERGENCY CLOSE WITH MEM
36 FIRE ALARM
40 ALWAYS OPEN
41 EXIT ONLY
42 ONLY IN
43 NIGHT
44 MANUAL
45 PARTIAL
46 INTERBLOCK ON
60 TIMER
2 OUTPUTS O1/O2
01…O2
0 DISABLED
1 GONG
2 ERROR
4 EMERGENCY ACTIVATE
5 TEST
6 DOOR NOT CLOSED
7 DOOR OPENED
8 DOOR OPENING
9 LIGHT
10 INTRUSION ACTIVE
11 CLOSING SAFETY
12 SAFETIES
3 OP/CL RELAY
NORMALLY OPENED / NORMALLY CLOSED
4 EXTERNAL SELECTOR
POSITION 1…P OSITION 2
0 DISABLED
1 NIGHT
2 OPENED
3 EXIT ONLY
4 MANUAL
NORMALLY OPENED / NORMALLY CLOSED
NORMALLY OPENED / NORMALLY CLOSED
NORMALLY OPENED / NORMALLY CLOSED
NORMALLY OPENED / NORMALLY CLOSED
NORMALLY OPENED / NORMALLY CLOSED
NORMALLY OPENED / NORMALLY CLOSED
NORMALLY OPENED / NORMALLY CLOSED
NORMALLY OPENED / NORMALLY CLOSED
NORMALLY OPENED / NORMALLY CLOSED
NORMALLY OPENED / NORMALLY CLOSED
NORMALLY OPENED / NORMALLY CLOSED
NORMALLY OPENED / NORMALLY CLOSED
NORMALLY OPENED / NORMALLY CLOSED
NORMALLY OPENED / NORMALLY CLOSED
NORMALLY OPENED / NORMALLY CLOSED
NORMALLY OPENED / NORMALLY CLOSED
NORMALLY OPENED / NORMALLY CLOSED
NORMALLY OPENED / NORMALLY CLOSED
NORMALLY OPENED / NORMALLY CLOSED
NORMALLY OPENED / NORMALLY CLOSED
NORMALLY OPENED / NORMALLY CLOSED
TEST ENABLED / DISABLED
TEST ENABLED / DISABLED
NORMALLY OPENED / NORMALLY CLOSED
NORMALLY OPENED / NORMALLY CLOSED
NORMALLY OPENED / NORMALLY CLOSED
NORMALLY OPENED / NORMALLY CLOSED
NORMALLY OPENED / NORMALLY CLOSED
NORMALLY OPENED / NORMALLY CLOSED
NORMALLY OPENED / NORMALLY CLOSED
TIME 1...90 S
NORMALLY OPENED / NORMALLY CLOSED
NORMALLY OPENED / NORMALLY CLOSED
NORMALLY OPENED / NORMALLY CLOSED
NORMALLY OPENED / NORMALLY
CLOSED
920.1003.02 | 07
WWW.TUCKERAUTO-MATION.COM
KP evo
- TAP CONTROLLER INSTALLATION GUIDE
2 MOTION
1 OPENING ...2 CLOSING
1 SPEED
2 SLOWDOWN
3 STRENGTH
4 STRENGTH DURATION
5 ACCELERATION
6 DECELERATION
3 TIMING
1 PAUSE TIME
2 PAUSE TIME
3 NIGHT PAUSE TIME ]
4 NIGHT SENSOR NIGHT
4 MOTOR LOCK KIT
1 FUNCTION
DISABLED
NIGHT
EXIT ONLY
NIGHT + MONODIR
ALWAYS
2 LOCK DELAY
3 RELEASE TYPE
WHEN OPENING
CLOSED
0...60 tenths of a second
5 INSTALLATION
1 ARM TYPE
SKID
ARTICULATE
2 SENSOR TYPE
DOOR MOUNTED SYSTEM
OPS AND BEAM
3 START SETUP ARE YOU SURE ?
4 PUSH AND GO
0 DISABLED
1 ENABLED
2 FAST FOOD
5 PARTIAL STOP SEC.
DISABLED
ENABLED
6 LEAF DELAY
7 SCP
DISABLED
ENABLED
8 REVERSE STROKE
DISABLED
ENABLED
10 INOUT STATE
11 DOOR STATUS
12 OTHER BOARD DATA
6 INTERCOM
1 FUNCTION
DISABLED
INTERMODE
INTERLOCK
2 LEAVES
2 LEAVES + INTERBLOCK
2 MASTER/SLAVE NR.
3 INTERCOM REG.
4 NODE LIST
0...30 s
0...30 s
0...90 s
0...90 s
1...10
SLOWDOWN SPACE
0...10
0.1...3.0 s
1...10
1...10
0°...90°
IN1...IN8
V_MAIN V_ACC
01...02
WITH MEMORY
WITH MEMORY
/
/
0°...90°
POS I_MOT
WITHOUT MEMORY
WITHOUT MEMORY
SLOWDOWN SPEED 1...3
920.1003.02 | 08
WWW.TUCKERAUTO-MATION.COM
KP evo
- TAP CONTROLLER
7 MISCELLANEOUS
1 DEFAULT DEFAULT
ACTIVATE
NO
2 BOARD'S DISPLAY
STOPPED
3 INTRUSION
NOT BLOCKED
DISABLED
ENABLED
4 KPEVO KEY
WITHOUT USER PSW
BLOCK
5 CONSECUTIVE OBST.
CLOSING
OPENING
6 TEST ERROR
DISABLED
ENABLED
3 ERRORS
The display shows any current errors
4 WARNINGS the display shows any current warnings
5 CYCLES COUNT
1 CYCLES NUMBER
ABSOLUTE
RELATIVE
2 MAINTENANCE
MAINTENANCE DATE
3 CYCLES RESET ARE YOU SURE ?
DO YOU WANT TO LOAD
0...10
0...10
DEFAULT CONFIG
MAINTENANCE CYCLES resets the number of cycles
6 DATE/TIME
1 SET DATE
2 SET TIME
3 DAYLIGHT SAV TIME
DISABLED
ENABLED
7 TIMER
1 TIMER STATE
DISABLED
ENABLED
2 MONDAY
3 TUESDAY
4 WEDNESDAY
5 THURSDAY
6 FRIDAY
7 SATURDAY
8 SUNDAY
9 MON - SUN
10 MON - FRI
11 JOLLY
12 JOLLY SLOTS
SLOT 1
SLOT 2
SLOT 3
SLOT 4
SLOT 5
SLOT 6
APPLY (appears only if selected LUN - SUN or LUN - FRI )
?
INSTALLATION GUIDE
920.1003.02 | 09
WWW.TUCKERAUTO-MATION.COM
KP evo
- TAP CONTROLLER INSTALLATION GUIDE
FUNCTION : 0
FUNCTION : 1
FUNCTION : 2
FUNCTION : 3
FUNCTION : 4
FUNCTION : 5
FUNCTION : 6
FUNCTION : 7
FUNCTION : 8
FUNCTION : 9
FUNCTION : 10
8 PASSWORD
1 TECHNICIAN PSW
CHANGE TEC PSW
2 USER PSW
CHANGE USER PSW
9 INFO
E950E
E950E
KP EVO
BOOT
APP
APP
VER *.*
VER *.*
VER *.*
NO FUNCTION
AUTO BIDIR TOTAL
AUTO OUT TOTAL
AUTO BIDIR PARTIAL
AUTO OUT PARTIAL
TOTALLY OPEN
PARTIAL OPEN
AUTO IN TOTAL
AUTO IN PARTIAL
NIGHT
PARTIAL NIGHT
BEGINNING
END
REINSERT TEC PSW
REINSERT USER PSW hh:mm hh:mm
NEW PSW INSERTED
NEW PSW INSERTED
■ PROGRAMMING INPUTS/OUTPUTS
INPUTS
The inputs on terminal board J5 of the I/O board can be configured with the following functions
Each input can be set to NC or NO according to the device connected to it.
Disabled
No associated function.
External open
When activated, the door opens and remains open as long as the input is active. When released, the door waits for the pause time to elapse and then closes.
This has no effect in the EXIT ONLY or NIGHT modes.
Internal open
When activated, the door opens and remains open as long as the input is active. When released, the door waits for the pause time to elapse and then closes.
This has no effect in the ONLY IN or NIGHT modes.
Automatic open
When activated, the door opens and remains open as long as the input is active. When released, the door waits for the pause time to elapse and then closes.
Active in the BI-DIRECTIONAL, EXIT ONLY and ONLY IN modes.
This has no effect in the NIGHT mode.
Semiautom. open
When activated:
- if the door is not already open, it opens and remains open
- if the door is already open, it closes
Active in the BI-DIRECTIONAL, EXIT ONLY and ONLY IN modes.
This has no effect in the NIGHT mode.
Key
When activated, the door opens and remains open as long as the input is active. When released, the door waits for the night pause time to elapse and then closes.
Active in the BI-DIRECTIONAL, EXIT ONLY , IN ONLY and NIGHT modes.
Partial open
Only opens the master door when activated in the “ 2 leaves ” mode.
Closing safety
When activated:
- If the door is closing, it reopens
- If the door is already open, it prevents it from closing
- If the door is opening, it has no effect
Opening safety
When activated:
- If the door is opening, it stops until it is released
- If the door is already closed, it prevents it from opening
- If the door is closing, it has no effect
Emergency open
When activated, the door opens (always total) and remains open as long as the input is active. When released, the door waits for the night pause time to elapse and then closes.
Also active in NIGHT mode.
Emergency open with memory
When activated, the door opens (always total) and remains open as long as the input is active. When released, the door remains open until it is Reset
Emergency close
When activated, the door closes and remains closed as long as the input is active. When released, the door returns to normal operation.
920.1003.02 | 10
WWW.TUCKERAUTO-MATION.COM
KP evo
- TAP CONTROLLER INSTALLATION GUIDE
Emergency close with memory
When activated, the door closes and remains closed as long as the input is active. When released, the door remains closed until it is Reset
Fire alarm
When activated, the door closes, regardless of the operating mode that has been set, with the lock kept in the released position. It has priority over any commands that may be active.
Always open
When activated, the ALWAYS OPEN mode is set.
Exit only
When activated, the EXIT ONLY mode is set.
Entry only
When activated, the ONLY IN operating mode is set.
Night
When activated, the NIGHT mode is set.
Manual
When activated, the MANUAL mode is set.
Partial
When activated, the PARTIAL mode is set.
Interblock ON
When activated, the INTERLOCK mode is set.
Timer
When activated, the TIMER mode is set.
OUTPUTS
The outputs on terminal board J5 of the I/O board can be configured with the following functions
Each input can be set to NC or NO according to the device connected to it.
Disabled
No associated function.
Gong
The output is activated and deactivated at 1-second intervals when the safety devices are engaged.
Error
The output is activated if there is an error.
Emrg. active
The output is activated when an Emergency is triggered.
Test
The output commands a FAILSAFE test on the inputs that are configured as safety devices on which the option of running a TEST before movement has been enabled.
Door not closed
The output remains active until the door is closed.
Door open
The output remains active as long as the door is open.
Door opening
The output remains active as long as the door is moving.
Light
The output is activated, for a programmable length of time, w hen the door is open in NIGH T mode.
Intrusion active
The output is activated when an intrusion is in progress (i.e. when an unexpected movement of the door from its closed position is detected).
Closing safety
The output is activated when a closing safety device is active.
Safeties
The output is activated when a closing or opening safety device is engaged.
OP/CL RELAY
Specifies the logic of the door status relay (NC/NO).
EXTERNAL SELECTOR
Specifies the operating mode associated with positions 1 and 2 of the selector on the side of the unit.
■ PROGRAMMING MOTION
OPENING/CLOSING
Speed
Sets the speed of movement.
Deceleration
Specifies the space (in degrees of rotation of the 950N2 shaft) and the deceleration speed (on 3 levels) of the door before reaching the final open / closed positions.
Strength
Specifies the maximum crushing force.
Strength duration
Specifies the maximum thrust time before an obstacle is recognised.
Acceleration
Specifies how quickly the door reaches the set opening speed when starting from stop.
Deceleration
Specifies how quickly the door stops.
■ PROGRAMMING TIMING
PAUSE TIME
Defines the pause time of the door when opened by a command, before closing automatically.
PAUSE TIME P&G
Sets the door pause time when opened by a Push & Go command, before closing automatically.
Night PAUSE TIME
Sets the door pause time when opened by a command in NIGHT mode, before closing automatically.
NIGHT SENSOR DELAY
When NIGHT mode is set, the internal detector remains active for the amount of time set in this parameter, to allow it to be opened only once. The internal detector is disabled immediately after opening and in any case upon expiry of the set delay.
■ PROGRAMMING MOTOR BLOCK KIT
FUNCTION
Specifies the operating mode in which the lock is activated.
LOCK DELAY
Specifies the opening delay time of the door to allow the lock to be released, particularly motorised locks.
RELEASE TYPE
Specifies when power is disconnected from the lock after it has been mechanically released:
Opening = during the opening phase
Closed = when the door is closed again
920.1003.02 | 11
WWW.TUCKERAUTO-MATION.COM
KP evo
- TAP CONTROLLER INSTALLATION GUIDE
■ PROGRAMMING INSTALLATION
ARM TYPE
Specifies the type of transmission arm installed (shoe or articulated)
START SETUP
Carries out a Setup cycle after confirmation.
PUSH AND GO
Sets the function that commands the automatic opening of the door after an initial manual push:
Disabled = Push & Go not enabled
Enabled = Push & Go enabled
Fast food = Push & Go enabled in “ FAST FOOD “mode (manual opening, motorised closing)
PARTIAL STOP SEC.
Specifies the detection area of the safety in opening:
Disabled = obstacle detection active over the entire opening stroke
Enabled = obstacle detection NOT active in proximity to the opening stop
LEAF DELAY
Specifies the opening delay between the doors of 2 leaf models.
SCP
Specifies the function that pushes the door with a greater force in the final section of the closure. It is useful to activate this function if there is high friction, if the seals are particularly rigid or if locks have a stiff latch.
Because activating the SCP function also reduces the sensitivity of the electronic anti-crushing system in the final section of closing, DO NOT activate the SCP function in " low energy " mode.
REVERSE STROKE
Sets the function that makes the door carry out a short reverse stroke before opening to make it easier to the release the lock.
2 EASY REG.
Registration of BUS 2easy devices.
INOUT STATE
The display indicates the status (on / off) of inputs I1-I8 and outputs
O1-O2 in real-time.
DOOR STATUS
The display indicates the status of the automation in real-time.
OTHER BOARD DATA
The display indicates useful diagnostics information in real-time.
■ PROGRAMMING INTERCOM
FUNCTION
Sets the operating mode.
MASTER/SLAVE NR.
Sets the network ID of the unit.
INTERCOM REG.
Registers the units of the network (to be performed only on the
950N2 with ID 1).
NODE LIST
Shows the ID of the units registered (on the master).
■ PROGRAMMING MISCELLANEOUS
CONFIG. DEFAULT
Shows whether the parameters have been modified, and if so, resets the factory defaults after confirmation.
BOARD'S DISPLAY
Not active.
INTRUSION
Sets the function in which the door resists attempts to open it manually.
KPEVO KEY
You can choose between:
Block = the user must enter the user password in order to access the menus that he is authorised to use.
Without user psw = the user doesn’t need to enter the user password in order to access the menus that he is authorised to use.
CONSECUTIVE OBST.
Specifies the maximum number of consecutive obstacle detections in the same direction of movement, before stopping in an error condition.
TEST ERROR
Specifies the effect that the TEST will have when it detects a safety device fault:
Disabled = the door will remain stationary in an error condition
Enabled = the door will continue to operate at minimum speed
■ ERRORS
In this menu, the display indicates any current errors that there may be in real time.
■ WARNINGS
In this menu, the display indicates any current alerts that there may be in real time.
■ CYCLE COUNTER
The 950N2 has two counters:
- total, non-resettable
- partial, resettable
This menu allows you to view the cycles performed by the automation and reset the partial counter.
It is also possible to set a deadline for scheduled maintenance according to:
- date (optional)
- number of cycles (from 1000 to 1000000)
Alert 60 will be displayed as soon as one of the two settings (date or number of cycles) is reached.
Logging in with the user to be viewed.
password only allows data
■ DATE/TIME
This menu allows you to set or modify the date, time and turn
European summer time on / off.
920.1003.02 | 12
WWW.TUCKERAUTO-MATION.COM
KP evo
- TAP CONTROLLER INSTALLATION GUIDE
To keep the settings even if there is no mains power, which is necessary for the TIMER to work correctly, a battery must be installed on the Logic board.
■ TIMER
This menu includes all the parameters for configuring the TIMER function.
When the TIMER is enabled, the operating mode of the door during the programmed time bands is set automatically.
A maximum of 6 daily time bands can be defined, and an operating mode, selected from those available, assigned to each one. Each time band has a start time and an end time.
The time bands must not overlap.
When the TIMER is enabled, the T icon appears on the home screen.
To manually change the operating mode set by the
TIMER , it first has to be disabled.
In order for the TIMER to work correctly, a battery must be installed on the Logic board.
In order to quickly program groups of days of the week with the same time bands, it is possible to simultaneously select all the days of the week ( MON - SUN ) and all weekdays ( MON - FRI ). Once the time bands that have been defined here have been confirmed using the
APPLY option, they will overwrite any time bands that have already been programmed for individual days.
If it is necessary to program specific days or periods (e.g. recurring holidays), you may use the JOLLY function.
A maximum of 6 JOLLY time bands can be specified and an operating mode, selected from those available, assigned to each one. Each time band has a start time and an end time.
The time bands must not overlap.
The JOLLY time bands are then assigned to a maximum of 6 INTER-
VALS. An interval can be a single day or a series of days.
If a single day is defined, the start and end date of the interval must be the same.
The interval must refer to same calendar year (example: for the period from 25/12 to 06/01, 2 intervals must be created, from 25/12 to 31/12 and from
01/01 to 06/01).
■ PASSWORD
This menu allows passwords to be set or modified.
To access the FUNCTIONS menu you are prompted to enter a 4-digit password .
The 950N2 has two passwords available, with different access rights
(
B )
B A c c e s s p e r m si is o n s a n d
TECHNICIAN
PSW p a s s w o r d s
USER
PSW
LANGUAGE
PROGRAMMING
ERRORS
WARNINGS
CYCLES COUNT
DATE/TIME
TIMER
PASSWORD
INFO
(*)
(*)
* with restrictions
The user is only allowed to modify the user password .
920.1003.02 | 13
WWW.TUCKERAUTO-MATION.COM
KP evo
- TAP CONTROLLER
2. DIAGNOSTICS
2.1 LEDS CHECK
I/O BOARD LEDS
Each input on the I/O board, has a LED that indicates the physical state of the contact:
C I/O board LEDs
LED
DL 1
DL 2 - DL9 open contact
accessories power on accessories power off closed contact
LOGIC BOARD LEDS
There are 4 LEDs on the Logic board:
E S t a t u s
CLOSED
OPENING
OPEN
PAUSE
NIGHT PAUSE
CLOSING
EMERGENCY ACTIVATE
MANUAL
NIGHT
STOP
SECURITIES TEST
ERROR
SETUP in progress
D Logic board LEDs
LED
DL 1 green no USB
DL 2 red normal condition
DL 3 blue no power or board failure
USB connected error
/
S e t u p quested
re normal condition
DL 4 yellow board parameters the same as trimmer and DIP switch values board par a m e t e r s different to trimmer and
DIP switch values
Button pressed
off
on
flashing
fast flashing
§
Setup in progress
/
/
2.2 INPUTS AND OUTPUTS STATUS CHECK
The status of each input and output can be checked via the KP EVO.
Go to menu 2.5.9. The display indicates the status of the logic as shown in
0 7
. Example:
IN1 = input active
IN1 = input not active
2 .
3 A U T O M A TION STATUS CHECK
The current status of the automation system can be checked via the KP EVO.
Go to menu 2.5.10. The display shows information regarding the status of the automation.
IN1
IN5
IN2
IN6
O1 O2
IN3
IN7
IN4
IN8
INSTALLATION GUIDE
0 7
920.1003.02 | 14
WWW.TUCKERAUTO-MATION.COM
KP evo
- TAP CONTROLLER INSTALLATION GUIDE
2.4
W A R N I N G S
Alerts provide information regarding the status or current phase of the automation and errors that do not prevent it from operating. It is possible to check any current alerts via the KP EVO.
Go to menu 4 to view the list of current alerts.
If there is at least one alert, an icon appears on the home screen.
F W a r n i n g s
41 Date and time missing
- Reset date/time via the KP EVO
42 Clock battery discharged or missing
44 Emergency active (including command memory)
45 Timer active
46 Timer function in progress
48 Night mode operation
49 Manual mode operation
50 Partial mode operation
51 Obstacle detected during closure
52 Obstacle detected during opening
53 Number of maintenance cycles on E 2 prom corrupted
- Carry out a Reset .
- If the alarm persists, replace the Logic board
58 Searching for strike on closing
60 Maintenance requested
61 KP EVO fault
- Check that the correct device is connected and check the connections.
- If the alarm persists, update the firmware
- If the alarm persists, replace the Logic board
63 Intrusion in progress
65 Set-up in progress
68 TEST alarm (only if the “ test error ” parameter is enabled)
- Check the operation of the connected devices
- If the alarm persists, replace the device
- If the alarm persists, replace the Logic board
In this condition, the door moves at a slower speed.
69 Door opened by a semi-automatic command
71 Slave Intercom mode
72 Intercom alarm
- Check the connections
- Check the ID
- If the alarm persists, replace the Logic board
73 Slave Error / Alarm
74 Interlock alarm
- Check the connections
- Check the ID
- If the alarm persists, replace the Logic board
80 Non-standard programming
920.1003.02 | 15
WWW.TUCKERAUTO-MATION.COM
KP evo
- TAP CONTROLLER INSTALLATION GUIDE
2.5 E R R O R S
Errors are malfunctions that prevent the automation system from working. They are indicated by a steady red LED on the Logic board.
After every 5 minutes in which a fault condition persists and for a maximum of 20 consecutive times, the 950N2 will perform a Reset to attempt to restore normal operation so as not to require any action if the condition that caused the error was temporary. If the fault persists, remove the cause in order to restore normal operation.
The type of error can be identified via the KP EVO
The error code appears on the home page. Go to menu 5; the display provides information regarding the current error.
G E r r o r s
When an error occurs:
1. Check all the electrical connections
2. Carry out a reset .
3. If the problem persists, carry out the operations described in the table one at a time until the problem is resolved.
E rr o r
01 Board failure
02 E2 prom failure
03 Motor driver failure
A tc oi n r e q u ri e d
- Replace the Logic board
- Replace the Logic board
04
05
07
09
11
12
15
Accessories power supply fault
Microcontroller error
Motor failure
Board voltage anomaly
Closing safety
Setup inhibited
TEST
Opening safety TEST
failed
failed
- Replace the Logic board
- Replace the motor
- Check that the accessories power supply is not short circuited
- Check that maximum load of the accessories has not been exceeded
- Replace the Logic board
- Replace the I/O board
- Reload/update the Logic board firmware
- Replace the Logic board
- Replace the motor
- Replace the Logic board
- Replace the Logic board
- Replace the I/O board
- Check the connections of the safety device
- Check that the safety device is working
- Replace the Logic board
- Check the connections of the safety device
- Check that the safety device is working
- Replace the Logic board
- Make sure that Night or Manual mode has not been set.
- Make sure that an Emergency command has not been activated
- Replace the Logic board 16 Encoder fault
18 Firmware not compatible
19 High mechanical friction
- Update with the correct firmware
22 Programming data corrupted
- Make sure that the leaf has been mounted correctly and that it moves smoothly, remove any friction
- Replace the Logic board
- Replace the gearmotor
- Reprogram the board or upload the program files that were saved to the USB storage device.
- Replace the Logic board
920.1003.02 | 16
WWW.TUCKERAUTO-MATION.COM
KP evo
- TAP CONTROLLER
24 Consecutive obstacles in closing
26 Lock failure
27 Motor rotation fault
31 Consecutive obstacles in opening
39 Setup data missing or corrupted
INSTALLATION GUIDE
- Remove the obstacle in closing.
- Make sure that the leaf has been mounted correctly and that it moves smoothly, remove any friction
- Check the wiring of the lock
- Check that the maximum load of the lock has not been exceeded
- Replace the lock
- Replace the Logic board
- Check the polarity of the motor cable
- Remove the obstacle in opening
- Make sure that the leaf has been mounted correctly and that it moves smoothly, remove any friction
- Perform Setup
- Replace the Logic board
2 .
6 O THER BOARD DATA
Go to menu 2.5.11 of the KP EVO. The display provides information on the following parameters:
-
-
-
V MAIN : input voltage to the Logic board (Volts)
V ACC : output voltage for accessories (Volts)
POS : position of the rotating shaft (degrees)
I MOT : current drawn by motor (Amperes)
2.7 FIRMWARE VERSIONS
Go to menu 9 of the KP EVO to view the firmware versions of the bootloader, the Logic board and the
KP EVO.
2.8 LOG DATA
The 950N2 records the last 512 system events. A battery must be installed on the Logic board in order to save the list of events in memory even if the system is switched off.
To download the data as a text file, see § .
920.1003.02 | 17
WWW.TUCKERAUTO-MATION.COM
KP evo
- TAP CONTROLLER INSTALLATION GUIDE
3.
UPLOAD / DOWNLOAD
There is a USB port on the Logic board via which the following operations can be carried out:
Load data from a USB pen drive ( UPLOAD ).
Save data to a USB pen drive ( DOWNLOAD ).
For both operations, the USB pen drive must be formatted with the FAT or FAT 32 file system.
The NTFS format is not recognised.
In order to upload, the files required, the names of which are indicated in
H must be present in the root directory of the USB pen drive.
1. Turn power off to the 950N2.
2. Insert the USB pen drive in the USB port (J2) on the Logic board.
3. Turn power on to the 950N2.
4. If the device is detected correctly, the green LED DL1 of the Logic (
0 8
) board lights up steadily.
5. The available functions are selected by briefly pressing button SW1 on the Logic board (
0 8
). The operation to be carried out is indicated by the number of flashes of the green LED. Each time the button is pressed, the operations selected are indicated in
H .
6. Press and hold the SW1 button for at least 3 seconds to use the function. The green LED flashes more quickly while the procedure is being carried out. When finished, the result is signalled by the status of the following LEDs: e n L 1 n t e m p l e t e d e s s f u
-
g r e L E D ( D ) o s a d li y = c o red LED (DL2) on steadily = error s u c c ll y
7. Turn power off to the 950N2 and remove the USB pen drive.
DL2 DL1
10 1
SW1
J2
H S e l e
Green LED DL1 c
1 flash
2 flashes
3 flashes
4 flashes it n g t h e upload/download function
Function
950N2 firmware update file required: 950N2.hex
KP EVO firmware update, including menu translations files required: KP EVO.hex e KP EVO_L.bin
950N2 and timer configuration upload files required:
950N2, timer and LOG data configuration download files written: 950N2.prg , 950N2.tmr , 950N2.log
0 8
920.1003.02 | 18
WWW.TUCKERAUTO-MATION.COM
KP evo
- TAP CONTROLLER INSTALLATION GUIDE
4 .
P U T TING INTO SERVICE
4.1 FINAL CHECKS
1. For doors in “ low energy ” mode, make sure that the forces generated by the leaf are within the limits permitted by the regulations. Use an impact force tester in accordance with standards EN 12453: 2002 and EN 12445: 2002. For non-EU countries, of there are no specific local regulations, the force must be less than 67 N.
2. For doors that are not in “ low energy ” mode, make sure that the test object is detected in all areas covered by the leaf movement.
4.2 FINAL OPERATIONS
1. Connect the cable of the functions selector at the side of the unit to the I/O board (connector J2).
2. Install the front cover.
3. Highlight all areas with adequate warning signs in which there are still residual risks, even if all possible safety measures having been adopted. In particular, for doors less than 2 meters high, apply the hazard warning pictograms in correspondence with the arm movement area.
4. Place a “DANGER, AUTOMATICALLY CONTROLLED” sign in a prominent position on the door.
5. Attach the CE marking on the door.
6. Fill out the EC declaration of conformity and the system register.
7. Give the EC Declaration, the system register with the maintenance plan and the instructions for use of the automation to the system owner/operator.
INSTALLING A PLASTIC COVER
1. Install the cover fixing plates with screws
0 9
-1 on both sides.
2. Partially tighten the screws
0 9
-2.
3. Insert the cover so that the screws fit into the slots, then tighten them.
4. As an alternative to fixing it from the side, use the template to fasten the cover with screws from the top or bottom (
1 0
5. Press the top and bottom slot covers on (
1 1
).
2
1
0 9
1 1 1 0
920.1003.02 | 19
WWW.TUCKERAUTO-MATION.COM
KP evo
- TAP CONTROLLER
INSTALLING AN ALUMINIUM COVER
1. Install the side profiles using the screws
1 2
-1 on both sides.
2. Press the aluminium cover on, aligning the slot with the side on which the transmission arm has been installed.
INSTALLATION GUIDE
1
1
1 2
5. MAINTENANCE
RISKS
PERSONAL PROTECTIVE EQUIPMENT
Always shut off the power supply before performing any maintenance operations. If the disconnect switch is not in view, apply a warning sign stating
“WARNING - Maintenance in Progress”. Restore the power supply only after finishing any maintenance work and restoring the area to normal.
Maintenance must be performed by the installer or a maintenance technician.
Follow all safety recommendations and instructions given in this manual.
Mark off the work site and prohibit access/transit. Do not leave the work site unattended.
The work area must be kept tidy and cleared after maintenance has been completed.
Before starting work, wait for any hot components to cool down.
Do not make any modifications to the original components.
FAAC S.p.A. shall bear no liability for damage or injury due to components that have been modified or otherwise tampered with.
The warranty shall be forfeited in the event of tampering with components. Only use original
FAAC spare parts.
5.1 INSERTING / REPLACING THE
BATTERY
CARRY OUT THE FOLLOWING OPERATIONS WITH THE
ELECTRICITY SUPPLY DISCONNECTED
1. Remove the cover.
2. Install or replace the CR1216 battery on the Logic board, as shown in
1 3
3. Reinstall the cover.
.
5.2 REPLACING THE FUSE
CARRY OUT THE FOLLOWING OPERATIONS WITH THE
ELECTRICITY SUPPLY DISCONNECTED
There is a power supply protection fuse on the I/O board.
To replace it:
1. Remove the cover:
2. Replace the following fuses
F 4A for the 230 V version
T 3.15A for the 115 V version
3. Reinstall the cover.
CR1216
1 3
920.1003.02 | 20
WWW.TUCKERAUTO-MATION.COM
KP evo
- TAP CONTROLLER INSTALLATION GUIDE
5.3 ROUTINE MAINTENANCE
T a b l e
I lists the operations which must be performed on a regular basis in order to keep the automation working reliably and safely; these are given purely as a guideline and should not be considered exhaustive. The installer/machine manufacturer is responsible for drawing up the maintenance plan for the automation, supplementing this list or modifying the maintenance operations on the basis of the machine characteristics.
I S c h e d u l e d m a i n t e n a n c e
Operations
Structures
Frequency/months
Check the structures and the parts of the building to which the door and the automation is fixed: make sure there is no damage, cracking, breaks or subsidence.
Frame
C
Check the frame: make sure that it is fixed correctly, that it is integral and that there is no deformation or damage. Tighten screws and bolts where necessary.
h e c k t h e el a :f t h a t ti i s ni t e g r la a n d t h a t t h e r e si n o d fe o r m a t oi n o r d a m a g .e
L
Check the hinges: make sure that they are fixed correctly, that they are integral, correctly positioned in their seats and that there is no deformation or damage.
u b r ci a t e h ni g e s o r ol c k ,s fi n e c e ss a r .y
G e n e r la yl c el a n o f t h e a r e a o f m o v e m e n t t h e d o o .r
Check the presence and condition of pictograms that highlight the glass part of the door. If they are missing or damaged, replace them.
Operator o f
Check that the cover/casing and all the movable guards are integral and that they are fastened correctly. Tighten screws and bolts where necessary.
Check the condition of the power cables, the sensor and accessory connection cables and the relative cable glands.
General cleaning.
Function set-up selector and keyboard
12
12
1
12
1
1
12
12
2
2
12
12
2
C
C
C h e c k t h a t t h e y a r e ni t a tc a n d o p e r a t ni g c o rr e c lt .y
Sensors, protective devices and control devices h h e e c c k k t h a t t h a t t h e y t h e a r d o o r
e o ni t p a e r tc a t a n d e s o p e p r o p e r a t lr y ni ni g c b o o t rr h e c d lt ri
.y
If applicable, check that the pictograms that identify the control devices for disabled persons are present and intact.
The door e tc oi n s w ti h a ll t h e d e v ci e s ni ts la el .d
C h e c k t h a t t h e d o o r m o v e s s m o o t h yl a n d u n fi o r m l y w ti h o u t m a k ni g a n y u n u s u la n o si e s .
Check that the opening and closing speed is correct. For doors in “ low energy ” mode, make sure that the opening and closing times are within the limits permitted by the regulations.
C
C
For doors in “ low energy ”, mode, make sure that it is possible to stop the movement of the door without excessive force (Max. 67N) at any point along its travel.
h e c k t h a t t h e d o o r o p e r a t e s c o rr e c lt y ni e v e r y o p e r a t ni g m o d .e
h e c k t h a t t h e ol c k i s w o r k ni g p r o p e lr ,y fi p r e s e n .t
1 2
1 2
12
1 2
1
1
6
6
6
2
2
Check that the safety system is working correctly (door reverses or stops when an obstacle is detected, that the door stops in the open position when there is an obstacle in the area of movement etc.)
6
Check the presence, integrity and legibility of the EC marking on the door and the DANGER AUTOMATIC MOVEMENT warning sign. 12
920.1003.02 | 21
WWW.TUCKERAUTO-MATION.COM
KP evo
- TAP CONTROLLER INSTALLATION GUIDE
6.
INTERCOM
■ DESCRIPTION
The 950N2 is capable of communicating with other 950N2 units via an Intercom network connection. This enables the following modes of operation to be used (KP EVO menu 2.6.1):
INTERMODE : a master door from which to set the operating mode for all the other doors that are connected to the network.
INTERLOCK : two single doors, where the opening of one is subject to the closing of the other and vice versa.
2 LEAVES : access consisting of a double leaf.
2 LEAVES + INTERLOCK : two interlocked accesses, each consisting of a double leaf.
Every network connected 950N2 should be programmed for the same Intercom mode.
■ CONNECTION
The units in the network are connected via 3 cascade connected-wires between the J8 connectors of the
I/O boards (
1 4
).
The sequence in which the units are wired is unimportant, but it is essential that a CASCADE connection is used.
The 2 DIP switches on the I/O board must be set as follows:
On the first and last units of the cascade connection: both ON.
On intermediate units (if any): both OFF.
■ ADDRESSING
A unique ID (KP EVO menu 2.6.2) must be assigned to each 950N2 in the network as indicated below.
Do not assign the same ID to more than one unit in the network.
■ REGISTRATION
After having wired up and assigned an address to each unit, registration (KP EVO menu 2.6.3), must only be carried out on the 950N2 that has been assigned ID 1.
G CH CL J8
ON
1 2
DS2
J8 G CH CL
DS2 ON
1 2
J8 G CH CL
DS2 ON
1 2
1 4
920.1003.02 | 22
WWW.TUCKERAUTO-MATION.COM
KP evo
- TAP CONTROLLER INSTALLATION GUIDE
6.1
INTERMODE
1 5
shows the ID to assign to the 950N2 units in the network.
The system consists of a Master unit and a maximum of 14 Slave units. The 950N2 Master unit is the only one on which the operating mode should be set, which is then also applied immediately to all the Slave units.
With INTERMODE , it is not possible to change the operating mode of an individual unit.
950N2 The Master must be assigned ID 1 and the Slave units with ID from 2 to 14.
6.2
INTERLOCK
1 6
shows the ID to assign to the 950N2 units in the network.
Either of the two units can be designated as the Master and the other as the Slave . In INTERLOCK mode, one door can open only if the other is closed. The available variations are shown below.
If the PARTIAL mode is associated with INTERLOCK , only the Master leaf opens.
Connect the devices and carry out the programming and Setup of the individual 950N2 units before configuring the INTERLOCK using KP EVO.
Select
INTERLOCK .
on the Master unit to activate the
950N2
MASTER
ID=1
950N2
SLAVE
ID=2
950N2
SLAVE
ID=3
950N2
SLAVE
ID=15
1 5
950N2
Master interlock
ID=1
950N2
Slave interlock
ID=3
1 6
920.1003.02 | 23
WWW.TUCKERAUTO-MATION.COM
KP evo
- TAP CONTROLLER INSTALLATION GUIDE
INTERLOCK WITH NO MEMORY
With 4 sensors: the second opening is not automatic.
In order to open the door, the internal/external sensor must be triggered when the other door is closed. If the sensor is activated while the door is not yet closed, it has no effect.
S 1
A1
S2 S3
A2
S 4
6.3 2 LEAVES
1 7
shows the ID to assign to the 950N2 units in the network.
If the two doors overlap, the one that opens first is designated as the Master . If there is no overlap, either of the two units can be designated as the Master and the other as the Slave .
The movement of the leaves 2 is synchronised.
The internal / external door sensors and safety devices must be connected to their own unit; all other devices are connected only to the Master .
Connect the devices and carry out the programming and Setup of the individual 950N2 units before activating the 2 LEAF function.
Only use the Master 950N2 to change the operating mode .
The leaf opening / closing delay can be set in menu
2.5.5 of the KP EVO.
A1 closed
A2 closed
A1 NOT closed
A2 closed
A1 closed
A2 NOT closed
S1 S2 S3 S4
A1 opens A1 opens A2 opens A2 opens
A1 opens A1 opens request opening of A2 request opening
A1 request opening
A1 request opening of A2
A2 opens A2 opens
A 1 S2
S1
S3
S4
A 2
950N2
2 leaves MASTER
ID=1
950N2
2 leaves SLAVE
ID=2
INTERLOCK WITH MEMORY
With 2 sensors or buttons: the second opening is automatic.
S1
A1 A2
S2
1 7
6.4 2 LEAVES + INTERLOCK
1 8
shows the ID to assign to the 950N2 units in the network.
This configuration integrates the 2 LEAVES function (on two double-leaf accesses) with the interlock function.
Refer to the operating modes described above.
A1 closed A2 closed
S1
A1 opens, then
A2
A1 NOT closed, A2 closed A1 opens and request opening of A2
A1 closed, A2 NOT closed request opening of A1
S2
A2 opens, then
A1 request opening of A2
A2 opens and request opening of A1
950N2
Master interlock
2 leaves MASTER
ID=1
950N2
2 leaves SLAVE
ID=2
950N2
Slave interlock
2 leaves MASTER
ID=3
950N2
2 leaves SLAVE
ID=4
1 8
920.1003.02 | 24
WWW.TUCKERAUTO-MATION.COM
KP evo
- TAP CONTROLLER INSTALLATION GUIDE
Tucker Auto-Mation, LLC
11075 Parker Dr,
Irwin, PA 15642
Toll Free: 1-855-8 TUCKER
Tel: 412-823-2537
Fax: 412-842-0260
Email: [email protected]
920.1003.02 | 25
WWW.TUCKERAUTO-MATION.COM
advertisement
* Your assessment is very important for improving the workof artificial intelligence, which forms the content of this project
Related manuals
advertisement
Table of contents
- 42 P EVO menu
- 48 Access permissions and passwords
- 49 board LEDs
- 49 Status
- 50 Warnings
- 51 Errors
- 53 function
- 56 Scheduled maintenance