- Home
- Domestic appliances
- Climate control
- Split-system air conditioners
- ICP
- MF200024C
- Installation Guide
ICP MF200024C Air Handler installation Guide
Add to my manuals
12 Pages
ICP MF200024C is a modular blower cabinet that can be used for cooling or heat pump applications either with or without electric heat. It has a 208/230V PSC blower motor with an electronic fan control board. The MF200024C can be installed in an upflow, downflow, or horizontal position. It has a variety of features, including:
- Factory approved, field installed, UL listed heater packages are available.
- A NO HEAT KIT is required for installations without electric heat.
- The cabinet can be installed in a closet with a false bottom to form a return air plenum, or mounted on an open platform inside the closet.
advertisement
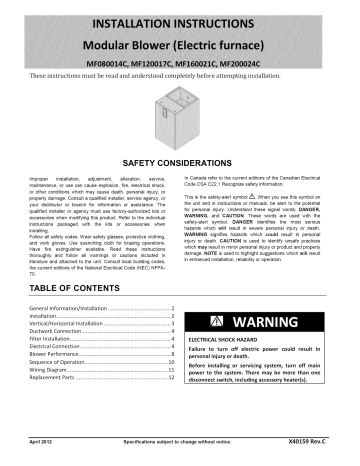
SAFETY CONSIDERATIONS
Improper installation, adjustment, alteration, service, maintenance, or use can cause explosion, fire, electrical shock, or other conditions which may cause death, personal injury, or property damage. Consult a qualified installer, service agency, or your distributor or branch for information or assistance. The qualified installer or agency must use factory-authorized kits or accessories when modifying this product. Refer to the individual instructions packaged with the kits or accessories when installing.
Follow all safety codes. Wear safety glasses, protective clothing, and work gloves. Use quenching cloth for brazing operations.
Have fire extinguisher available. Read these instructions thoroughly and follow all warnings or cautions included in literature and attached to the unit. Consult local building codes, the current editions of the National Electrical Code (NEC) NFPA-
70.
In Canada refer to the current editions of the Canadian Electrical
Code CSA C22.1 Recognize safety information.
This is the safety-alert symbol A\. When you see this symbol on the unit and in instructions or manuals, be alert to the potential for personal injury. Understand these signal words; DANGER,
WARNING, and CAUTION. These words are used with the safety-alert symbol. DANGER identifies the most serious hazards which will result in severe personal injury or death.
WARNING signifies hazards which could result in personal injury or death. CAUTION is used to identify unsafe practices which may result in minor personal injury or product and property damage. NOTE is used to highlight suggestions which will result in enhanced installation, reliability or operation.
TABLE OF CONTENTS
TTS
General Information/Installation .........ccccccccccsseeeseeeseeeseees 2
INStAN ATION... ccccceceseseeeeeeceesneeeeeseeeeeeesseeeeeeeesessseeneeeeeseneess 2
Vertical/Horizontal Installation oo... cee cecceseeeeesseeeesseees 3
Ductwork Connection .....c.ccccccccccccceceeessessesseeeeeeseessesseaeeeesesess 4
Filter Installation..........cccccccecsesssseceeeeesceesseseeeeeeseessseneeeeseseess 4 ELECTRICAL SHOCK HAZARD
Electrical CONNECTION... ccccccccesceceeseeesceseeeeeeeeeessestaeeeeeesess 4
Failure to turn off electric power could result in
Blower Performance ......ccccccccccscssssceceeecsessesreaeeeeeesesesseeeeesesess 8 personal injury or death.
Wiring Diagram .........ccccccccceeceeeeceeeeeeeeeeeeecnaeeeeeeeseeennareeeeenees 11
Replacement Parts ......c.ccccccccccccccssseeececsesesesseeeeeecsesesseeeseeess 12
Before installing or servicing system, turn off main power to the system. There may be more than one disconnect switch, including accessory heater(s).
Sequence Of Operation ........ccccccccccccesecceceseeeeeeeeeeeeeessnreeensnees 10
April 2012 Specifications subject to change without notice.
X40159 Rev.C
HAZARD
Figure 1 Nominal Installation Dimensions and Clearances - in(mm) a
3/4" (19)
12-7/16” (316)- MFO8
15-3/4” (400)~ MF12
19-1/4” (489)- MF16
22-3/4” (578)~ ME20
NO HEATERS
All Sides...0
From Supply Duct...0"
CLEARANCES
Recommended Service From Front...20"(508 mm)
Low Voltage |
Entrance
14-3/16” (360)- MFO8
17-112" (445)~ MF12
24” (533)~ MF16
24-1/2” (622)- MF20
~ el
P $
Line Voltage a
.
~
Oo
Entrance A |
, NA
IL a se a a a
24” (610)~ MFO8 & MF12
25” (635)~ MF16 & MF20
20%”
(821)
(Service for blower, filter if installed)
WITH HEATERS
All Sides...0"
From First Three Feet of Supply Duct to Combustibles...1" (25mm)
From Duct after Three Feet...0"
Recommended Service From Front...20" (508mm)
(Service for blower, heaters if installed)
Fire Hazard
Failure to follow this warning could result in personal injury, death, and/or property damage.
When heaters are installed maintain clearances from combustible materials as specified on unit rating plate. Do not use plastic lined or combustible flexible ducting within 36" (914 mm) of the supply end of the modular unit.
GENERAL INFORMATION
make sure adequate clearance is maintained from supply ductwork;
See Clearances and Warning in Figure 1.
e
If the unit is located in an area of high humidity, nuisance sweating of casing may occur. On these installations a wrap of 2” (51mm) fiberglass insulation with a vapor barrier should be used.
HEATER PACKAGES
DEATH, PERSONAL INJURY, AND/OR PROPERTY DAMAGE
Factory approved, field installed, UL listed heater packages are available from the equipment supplier. See unit rating plate for a list of factory approved heaters (electric heat accessory models EHIA only). Heaters that are not factory approved could cause damage which would not be covered under the equipment warranty.
Failure to carefully read and follow this warning could result in equipment malfunction, property damage, personal injury and/or death.
The information contained in this manual is intended for use by a qualified service technician familiar with safety procedures and equipped with the proper tools and test instruments.
Installation must conform with local building codes and with the National Electrical Code NFPA70 current edition.
IN CAUTION
CUT HAZARD
Failure to follow this caution may result in personal injury.
Sheet metal parts may have sharp edges or burrs. Use care and wear appropriate protective clothing and gloves when handling parts.
INTRODUCTION
The MF modular blower cabinet uses a 208/230V PSC blower motor, with an electronic fan control board. The MF may be used for cooling or heat pump applications either with or without electric healt.
Installations without electric heat require a NO HEAT KIT
(EHIAOOKN10). The cabinet can be installed in an upflow, downflow or horizontal position. Refer to Figure 3 and 4.
INSTALLATION
The unit is ready to install in any position without modifications.
Refer to the coil instructions for information on drain pan configurations etc. Make sure coil is set up properly for desired position of blower cabinet.
Coil must be secured to blower cabinet with the three tabs that are part of the blower cabinet base. Bend the tabs out from the bottom so they fit over the coil cabinet.
Position coil cabinet in relation to the blower so they will be correct for desired application.
LOCATION
Select the best position which suits the installation site conditions.
The location should provide adequate structural support, space in the front of the unit for service access, clearance for return air and supply duct connections, space for refrigerant piping connections and condensate drain line connections. If heaters are being installed,
2 Specifications subject to change without notice.
X40159 Rev.C
For upflow and horizontal applications apply foam seal strip around top of coil cabinet. For downflow application apply foam seal strip around bottom of coil cabinet. Set blower on top of coil cabinet so they are flush. Secure cabinets together using the three tabs on the bottom of the cabinet. Bend the tab out from the bottom so it fits over the coil cabinet. If no pilot holes are present, drill a hole as required for a screw.
Figure 2 Attach Coil to Blower Cabinet
Panels removed for clarity only
Place seal on top of
Bend Tabs (both sides and back) on Bottom of
Blower Cabinet to Fit
over Coil Cabinet
a a“ around perimeter
Coil Cabinet
DOWNFLOW INSTALLATIONS
Refer to instructions with Subbase Kit.
NON-DUCTED RETURN AIR CLOSET
INSTALLATION
The cabinet can be installed in a closet with a false bottom to form a return air plenum, or mounted on an open platform inside the closet.
Platform should be high enough to provide a free (open) area for adequate return airflow into the bottom of the cabinet. The open area can be on the front side or a combination of front and sides, providing there is clearance on the sides between cabinet and closet. Refer to ACCA Manual D for sizing and free area recommendations.
NOTE: Local codes may limit application of systems without a ducted return to single story dwellings.
HORIZONTAL LEFT AND RIGHT
INSTALLATIONS
The modular blower cabinets can be installed in either downflow, horizontal left or horizontal right applications. When a coil cabinet is applied, refer to the coil installation manual for proper drain pan and airflow requirements. They must have the drain pan repositioned for right hand airflow. Refer to coil installation manual.
IN CAUTION
Figure 3 Airflow Positions
UPFLOW
POSITION
DOWNFLOW
HEATER
POSTION
BLOWER com
IS
©
Subbase
Accessory
BLOWER
| l —
PROPERTY DAMAGE HAZARD
Failure to follow this caution may resuit in property damage.
A field fabricated auxiliary drain pan, with a separate drain is
REQUIRED for all installations over a finished living space or in any area that may be damaged by overflow from a restricted main drain pan. In some localities, local codes require an auxiliary drain pan for ANY horizontal installation.
Figure 4 Airflow Positions
AL RIGHT ®OS
Orn a oN © « iO ir
a
OD? wa
CO
2 it
[aiow>
Le
Ve
« o a“ ee
_-e
KO}
y
ie
S
8
CO _|O
SUSPENDED CABINET INSTALLATION
1. The cabinet may be supported on a frame or shelf, or it may be suspended.
X40159 Rev.C
Specifications subject to change without notice. 3
JAW
2. Use metal strapping or threaded rod with angle iron supports under the auxiliary drain pan to suspend cabinet. These supports
MUST run parallel with the length of the cabinet. Refer to Figure
5.
3. Ensure that there is adequate room to remove service and access panels after installing supporting brackets.
4. Place field installed vibration isolators in auxiliary drain pan to support cabinet.
DUCT CONNECTIONS
ELECTRICAL SHOCK or UNIT DAMAGE HAZARD
Failure to follow this warning could result in personal injury, death, and/or property damage.
If a disconnect switch is to be mounted on unit, select a location where drill and fasteners will not contact electrical refrigeration components.
Figure 6 | Fan Control Board
Supply Duct
Supply duct must be attached to the outside of flange on outlet end of unit. Flexible connectors may be used if desired. Maintain clearances from supply duct to combustibles when heaters are installed. Refer to Figure 1 and unit rating plate.
Return Duct
Return duct should be attached to bottom of unit using sheet metal screws or other fasteners.
FILTER INSTALLATION
Filters must be field supplied. A remote filter grille or other means must be provided. Refer to ACCA Manual D for remote filter sizing.
Figure 5 Horizontal installation
See Note
The power supply wiring to the unit MUST be provided with overcurrent protection. Governing codes may require this to be fuses
ONLY or circuit breakers. Refrigerant
Lines
Field-Fabricated
Vibration
Drain Pan
Isolators
Supports MUST run parallel with blower cabinet
Drain
Lines
98-29-O8o
NOTE: if increased structural strength is needed in the horizontal position, use field supplied two connecting plates in place of the tabs on the bottom of the blower.
OVERCURRENT PROTECTION
For blower cabinets without heaters, a 15 amp circuit may be used.
Before proceeding with electrical connections, make certain that supply voltage, frequency, phase, and circuit ampacity are as specified on the unit rating plate. See unit wiring label for proper field high and low voltage wiring. Make all electrical connections in accordance with the NEC and any local codes or ordinances that may apply. Use copper wire only. The unit must have a separate branch electric circuit with a field-supplied disconnect switch located within sight from and readily accessible from the unit.
ELECTRICAL CONNECTIONS
The MF modular blower utilizes an electronic fan control board which
NOTE: When a pull-out type disconnect is removed from the unit, has a low voltage circuit protective fuse (5 AMP), and pigtail only the Load side of the circuit is de-energized. The Line side connections for thermostat hook up. The fan control also has a relay for blower operation, and built in 90 second blower-off time delay relay (TDR). To disable the TDR feature, snip the jumper wire JW1.
Refer to Figure 6.
All electrical work MUST conform with the requirements of local codes and ordinances and the National Electrical Code NFPA 70 current edition.
The low voltage transformer and the fan control are standard on all models and are prewired at the factory. Line voltage connections are made to the heater accessory or the lugs on the No Heat Kit. remains live until the main (remote) disconnect is turned off.
4 Specifications subject to change without notice.
X40159 Rev.C
ELECTRICAL SHOCK or UNIT DAMAGE HAZARD
Failure to follow this warning could result in personal injury, death, and/or property damage.
Turn OFF electric power at fuse box or service panel before making any electrical connections and ensure a proper ground connection is made before connecting line voitage.
ELECTRICAL SHOCK HAZARD
Failure to follow this warning could result in personal injury or death.
Turn OFF the main (remote) disconnect device before working on incoming (field) wiring. Incoming (field) wiring on the line side of the disconnect found in the modular blower unit remains live, even when the pull-out is removed. Service and maintenance to incoming (field) wiring cannot be performed until the main disconnect switch (remote to the unit) is turned off.
MF units installed without electric heat require the use of a factory- authorized No Heat Kit (accessory part number EHIAQOKN10). This kit provides the electrical connections necessary to supply the unit with 208/230V power when electric heat is not present.
For units without electric heat:
1. Locate adapter and filler plates with screws inside package. If necessary, adjust plates to allow for installation of No Heat Kit required inside cabinet. Refer to Figure 7.
2. Secure No Heat Kit accessory with four (4) screws.
3. Connect the 9-pin plug from No Heat Kit wiring into the receptacle that attaches to fan control board.
4. Connect ground wire to unit ground lug.
5. Connect 208/230V power lead from field disconnect to No Heat
Kit.
For units with electric heat, see Electric Heater Installation
Instructions and blower airflow requirements.
NOTE: Transformer is factory-wired for 230V operation. For 208V applications the transformer must be rewired to the 208V tap. Refer to unit wiring label.
GROUNDING CONNECTION
Use a copper conductor(s) from the ground lug on the No Heat Kit or ground lugs on the electric heater to a grounded connection in the electric service panel or a properly installed grounding rod.
Low Voltage Control Connections
Wire low-voltage in accordance with wiring label on the blower (also refer to Figures 8 - 12. Use 18 AWG color-coded, insulated (35°C minimum) wire to make the low-voltage connections between: thermostat, indoor equipment, and outdoor equipment. If thermostat is located more than 100 feet (31m) from the unit (as measured along the low voltage wire), use 16 AWG color-coded, insulated
(35T minimum) wire. All wiring must be NEC Class 1 and must be separated from incoming power leads. Refer to outdoor unit wiring instructions for additional wiring recommendations.
Field supplied low-voltage wiring should be field connected inside control splice box area (secure with wire nuts), and strain relief bushing or rubber grommet to seal cabinet opening.
Figure 7 Electrical Controls
Low Voltage
Connections
~ ~
Filler Plate
Adapter Plate
No Heat Kit ~
Ground
Connection
Control Splice Box
X40159 Rev.C
Specifications subject to change without notice. 5
Table 1 Supply Circuit Supply | H.P. Max. MCA Max Recommended
Circuit
Volts | Phase | Hertz | No.
Motor | Branch
Amps _ | Circuit
AMP
Over- current Supply Wire Ground Wire
Protectio 75C copper n Devise! » of | min | Max. Ft.(m)| #of | Min
(Amps) Wires | Size Length Wires | Size
MF08* 208 1 60 Single 1/3 2.5 3.1 15 2 14 105 (32) 1 14
THERMOSTAT
230
MF12*
MF16*
MF20*
208
230
208
230
208
230
1
1
1
60
60
60
Single
Single
Single
1/2
1/2
3/4
2.9
2.9
6.0
3.6
3.6
7.5
15
15
15
2
2
2
14
14
14
105 (32)
105 (32)
90 (27) 1
1
1
14
14
14
Figure.8
(Cooling Only)
THERMOSTAT
Wiring Layout Air Conditioning Unit Figure 10 Wiring Layout Heat Pump Unit (Cooling
and Single-Stage Heat with No Outdoor
Thermostat)
[R| DA Rep
[¢] EA GRY
BRN
R
G
AIR COND. fA.
LA
THERMOSTAT HEAT PUMP
(CONTROL)
R
Figure 9
R
G
Ww
Wiring Layout Air Conditioning Unit
(Cooling and Single-Stage Heat)
AIR COND.
Specifications subject to change without notice.
X40159 Rev.C
THERMOSTAT
Figure 11 Wiring Layout Heat Pump Unit (Cooling and
Two-Stage Heat with One Outdoor
Thermostat)
HEAT PUMP
(CONTROL)
R
When two-stage electric heat is desired (refer to Table 2 - Heat
Strip Staging), separate out the pink W3 wire from W2 & E connections. Refer to Table 2-2 and wiring diagram Figure 11. W3 can be separated and controlled by the indoor wail thermostat (if multi-stage capable), or by an outdoor thermostat (ODTS). Refer to
ODTS kit instruction for proper wiring.
When three-stage electric heat is desired, cut the W2 wire nut off and discard. Strip W2, W3, and E. Refer to Table 2-3, and wiring diagram Figures 12. Connect according to the thermostat kit instructions or ODTS kit instructions for proper wiring.
THERMOSTAT
Figure 12 Wiring Layout Heat Pump Unit (Cooling and
Two-Stage Heat with Two Outdoor
Thermostats)
HEAT PUMP
(CONTROL)
R
CHANGING MOTOR SPEED
To change the blower speed, disconnect the black wire at the blower motor terminal block and reconnect at the desired blower speed tap (refer to Table 4).
HEATER STAGING
The modular controls are factory circuited for single-stage electric heat operation. Refer to Table 2 for available heaters and Table 3 for unit airflow based without a coil, filter, or electric heat applied.
Table 2 Heat Strip Staging
2-1 2-2 2-3
Single-Stage Two-Stage Three-Stage
Capable Operation
(no staging - all
electric heat
Capable
(with ODTS
only) together)
Single- EHIAO5KB / KN EHIA15KB EHIA25KB10
Phase EHIA07KB / KN EHIA20KB
Three-
Phase
EHIA10KB / KN
EHIA15KB
EHIA20KB
EHIA25KB
EHIA10HB
EHIA15HB
EHIA25KB
EHIA10HB
EHIA15HB
EHIA20HB
EHIA25HB
KB is single-phase with circuit breaker
EHIA20HB
EHIA25HB
EHIA20HB
EHIA25HB
KN is single-phase with terminal block (no-breaker)
HB is three-phase with circuit breaker
Table 3 Minimum Motor Speed Tap Selection For
Electric Heater
Electric Heater SIZE kW
Model | 5 kW | 7.5 kW | 10 kW | 15 kW | 20 kW | 25 kW
LOW = low speed tap selection
MED = medium speed tap selection
HIGH - high speed tap selection
AIR FLOW CHECK
For proper system operation, the air flow through the indoor coil should be between 350 and 450 cfm per ton of cooling capacity.
The air flow through the unit can be determined by measuring the external static pressure to the unit and selecting the motor speed tap that will most closely provide the required air flow.
Set up to measure external static pressure at the supply and return duct connections. Refer to Figure 13.
2. Drill holes in the ducts for pressure taps, pilot tubes, or other accurate pressure sensing devices.
3. Connect these taps to a level inclined manometer or draft gauge.
4. Ensure the coil and filter are clean, and all the registers are open.
5. Determine the external operating. static pressure with the blower
X40159 Rev.C
Specifications subject to change without notice. 7
TEMPERATURE RISE CHECK
6. Refer to the Air Flow Data, Table 4, to find the speed setting that will most closely provide the required air flow for the system.
7. Refer to Motor Speeds and Airflow in these instructions if the speed is to be changed.
8. Recheck the external static pressure with the new setting, and confirm speed switch selection.
Figure 13 Static Pressure Check
Supply
Indoor
Section
=
Incline
Manometer
Return (
Temperature rise is the difference between the supply and return air temperatures.
NOTE: The temperature rise can be adjusted by changing the heating speed tap at the unit’s blower terminal block. Refer to the unit’s Installation Instructions for airflow information.
A temperature rise greater than 60°F (33.3°C) is not recommended.
1. To check the temperature rise through the unit, place thermometers in the supply and return air ducts as close to the unit as possible,avoiding direct radiant heat from the heater elements.
Open ALL registers and duct dampers.
Set thermostat Heat-Cool selector to HEAT.
Set the thermostat temperature setting as high as it will go.
Turn electric power ON.
Operate unit AT LEAST 5 minutes, then check temperature rise.
NOTE: The maximum outlet air temperature for all models is 2007
(93.3).
7. Set thermostat to normal temperature setting.
8. Be sure to seal all holes in ducts if any were created during this process.
Airflow Based on no coil, no filter, no electric heat. Deduct heater static shown in heater static table.
Deduct coil static, See Coil Specification Sheet. Deduct .20 in we (50 Pa) for Downflow Subbase Kit.
Table 4 Airflow is blower only, no coil attached
MF08 In we
SPEED
Low
Med
High
VOLTS
230v
208v
230v
208v
230v
208v
0.20
1029
872
1286
1113
1500
1317
0.30
1020
860
1270
1105
1470
1305
0.40
1007
845
1254
1091
1432
1286
0.50
985
825
1220
1070
1380
1255
0.60
960
797
1180
1042
1315
1220
0.70
915
765
1125
1000
1250
1170
0.80
862
721
1058
947
1168
1008
MF012 In we
SPEED
Low
Med
VOLTS
230V
208
230V
High
208v
230V
208v
0.20
973
811
1284
1084
1663
1383
0.30
975
815
1295
1084
1670
1385
0.40
979
816
1301
1084
1671
1390
0.50
979
810
1305
1090
1655
1390
0.60
973
797
1302
1089
1631
1383
0.70
955
780
1280
1065
1585
1365
0.80
931
749
1246
1030
1519
1328
MF16 In we
SPEED
Low
Med
High
VOLTS
230V
208
230V
208
230V
208
0.20
1020
858
1379
1156
1776
1496
0.30
1015
845
1385
1154
1782
1496
0.40
1009
830
1386
1149
1783
1496
0.50
1002
815
1379
1144
1765
1495
0.60
991
801
1364
1134
1736
1495
0.70
975
780
1343
1120
1698
1470
0.80
950
749
1309
1098
1643
1433
MF20 In we
SPEED
Low
VOLTS
230V
0.20
1492
0.30
1495
0.40
1492
0.50
1475
0.60
1451
0.70
1395
0.80
1308
208v
Med
High
230V
208
230V
208
1246
1969
1641
2696
2417
1245
1955
1640
2600
2355
1238
1935
1633
2492
2287
1225
1890
1615
2350
2200
1203
1818
1584
2192
2092
1175
1700
1510
2020
1940
1125
1570
1406
1844
1774
* THE MAXIMUM EXTERNAL STATIC PRESSURE IS 0.8” W.C., WITHOUT COOLING COIL. DEDUCT STATIC PRESSURE OF COIL
FOR MAXIMUM STATIC PRESSURE.
8 Specifications subject to change without notice.
X40159 Rev.C
Table 5 - ELECTRIC HEATHER STATIC PRESSURE DROP
Single-Phase Three-Phase
EHIA EHIA EHIA EHIA EHIA EHIA EHIA EHIA | EHIA EHIA
CFM 05 07 10 15 20 25 N/A NIA 10 15 20 25
In we In we
600 0.01 0.01 0.04 - - - 0.01
700 0.01 0.01 0.04 - - - 0.01
800 0.01 0.01 0.04 0.01 - - 0.01
900 0.01 0.01 0.04 0.01 - - 0.01
1000 0.01 0.01 0.04 0.01 0.02 - 0.01
1100 0.01 0.01 0.04 0.02 0.02 -
1200 0.01 0.01 0.014 0.02 0.02 -
1300 0.01 0.02 0.02 0.02 0.02 -
1400 0.01 0.02 0.02 0.02 0.03 0.03
1500 0.01 0.02 0.02 0.02 0.03 0.04
1600 0.01 0.02 0.02 0.03 0.03 0.04
1700 0.01 0.02 0.02 0.03 0.03 0.04
1800 0.01 0.02 0.02 0.03 0.04 0.04
1900 0.01 0.02 0.02 0.03 0.04 0.05
2000 0.01 0.02 0.02 0.03 0.04 0.05
0.01
0.01
0.02
0.02
0.02
0.02
0.02
0.02
0.02
0.02
ACCESSORIES
ELECTRIC AIR CLEANER
The Electronic Air Cleaner may be connected to MF as shown in
Figure 14. This method requires a field supplied transformer. See
Electronic Air Cleaner literature for kit requirements.
Wiring Layout of Electronic Air
Figure 14
Cleaner to Modular Blower
Figure 15 Wiring Layout of Humidifier to Modu-
g lar Blower with Electric Heat
CONTROL BOARD
Rages THERMOSTAT
MODULAR BLOWER
CONTROL) FAN RELAY
[RI cA RED R
WIRE
NUT zo vac NO NG
COM as
SPT NONC
| |
[5] EA GRY |g
fe RR
208/230V
]
1 CONVERSION KIT
To TRANSFORMER | cones
COM _
HUMIDIFIER
Connect humidifier and humidistat to modular blower unit as shown in Figures 15 and 16.
| VIO}
VEY
|
|
| @ BRN
;
AIR COND.
L_le
X40159 Rev.C
Specifications subject to change without notice.
Sees
Figure 16
Wiring Layout of Humidifier to Heat
Pump
;
(CONTROL)
Aime | ole
HEAT PUMP
EA GRY] g oor BRN c eer
| RELAY |
115
{a th oe
me
| p
0 | HUMIDISTAT
be
L__,
blower motor. Y energizes the outdoor 24V low-voltage circuit in heat pump to energize compressor. O energizes reversing valve in cooling mode and typically remains energized until the mode is changed to heating. When thermostat cooling call is satisfied. Y drops out. O remains energized, and there is a 90 second TDR before indoor fan relay opens.
Heating Mode:
Thermostat energizes R to G and Y only (no O signal in heating). G energizes indoor fan relay on fan control board which completes high-voltage circuit to indoor blower motor. Y energizes the outdoor
24V low-voltage circuit in heat pump to energize compressor. The reversing valve is not energized in heating unless a defrost cycle should occur. When call is satisfied, Y drops out and there is a 90 second TDR before indoor fan relay opens.
D. HEAT PUMP HEATING WITH AUXILIARY
ELECTRIC HEAT
Cooling Mode:
Same operation as above in Heat Pump Cooling Mode.
Heating Mode:
Same operation as above in Heat Pump Heating Mode with the addition of W. Thermostat energizes R to G, Y, and W. W energizes electric heat relay(s) which completes circuit to heater element(s).
When W is de-energized, electric heat relay(s) open, turning off heater elements. The White wire in pigtail connects W2, W3, and E together. This may be separated for heater staging when available, see electric heat kit for more information.
E. ELECTRIC HEAT OR EMERGENCY HEAT MODE
SEQUENCE OF OPERATION
A. CONTINUOUS FAN
Thermostat closes R to W. W energizes electric heat relay(s) which completes circuit to heater elements(s). Blower motor is energized through N.C. (normally closed) contacts on fan relay. When W is de-energized, electric heat relay(s) opens.
CARE AND MAINTENANCE
Thermostat closes R to G. G energizes fan relay on FAN
CONTROL BOARD which completes the high voltage circuit to indoor blower motor. When G is de-energized, there is a built in 90 second blower-off time delay relay (TDR). To disable the TDR feature, snip the jumper wire JW1.
B. COOLING MODE
Air Conditioner Only:
The system should be regularly inspected by a qualified service technician. Consult the servicing dealer for recommended frequency. Between visits, the only consumer service recommended or required is air filter maintenance and condensate drain operation.
AIR FILTER
Thermostat energizes R to G and Y. G energizes fan relay on fan control board which completes high-voltage circuit to indoor blower motor. Y energizes the 24 low-voltage contactor in condensing unit.
When call is satisfied, Y drops out and there is a 90 second blower
TDR before fan relay opens.
Heat Pump:
Inspect air filters at least monthly and replace or clean as required.
Disposable type filters should be replaced. Reusable type filters may be cleaned by soaking in mild detergent and rinsing with cold water. The frequency of cleaning depends upon the hours of operation and the local atmospheric conditions. install filters with the arrows on the side pointing in the direction of air flow. Clean filters keep unit efficiency high.
LUBRICATION
Same as above - except thermostat will also energize O for reversing valve operation in cooling mode. O will typically remain energized by the thermostat (after cooling cail is satisfied), or until The bearings of the blower motor are permanently lubricated. the mode is changed to heating.
CONDENSATE DRAINS
C. HEAT PUMP
Cooling Mode:
During the cooling season check the condensate drain lines to be sure that condensate is flowing from the primary drain but not from the secondary drain. If condensate ever flows from the secondary
Thermostat energizes R to G, Y and O. G energizes indoor an relay on fan control board which completes high-voltage circuit to indoor drain, the unit should be promptly shut off and the condensate pan and drains cleaned to insure a free flowing primary drain.
10 Specifications subject to change without notice. X40159 Rev.C
WIRING DIAGRAM
( COOUNGCONTROLONLY —}
FIELD POWER MAING GISCOMWECT PER NED CMC ( ang WD
SVS CN TRA SPORMET: O00 Wa
Fane he = Su
Ee se ey
I a
“
ol te |
i
cL} ° kh
war WS
& beret p See nc i i
| Ree
NOTES
+, Use Copper Wire 75°C Min) Only Babee Decinnect Switch And Unt
a. WAnge OO The Gregival Wire, Aa &
2, Te Be Wired In Qocomanos Wier WEG And Locel Codes,
4, Pages wow ollage Fue Yih the Gomme Thea 3 dong Fee,
§, Connect @ To #6 lo & Et. See Gutdowr Instruction For Qetele.
.
&, (2) Spend Weter Shan: Come lees VEL, BUN Uaed To Select HED aed ON, n st i
ad, Muat Be Meplace:, Jae The fare Or Equivalent Tyne Wire,
nH tit
SEE WOTE #4
LOW
wen oF Aa
LEGEND
CAP
COM
F
FAN MOC
Fe
FW
ALMAINING VAAN INLABLIS SHOWA
CA
Poe
RECP
THAR
MOAB PRCT EDS
conc ih
FUSE mc Ale MELAY
:
PLUG
TO
TAP I LOCATIIN
NS ORME
PIELO PACRW ES WII hARAED TCRWEVAL
Minimum Motor © a Mea r Electric Heater
Elesirig Tienier Skee Kw
Aibkw Skew
MIG Tu
MPD RAL
$33098-107 REVLA
X40159 Rev.C
Specifications subject to change without notice.
11
aa
REPLACEMENT PARTS
ITEM | CURRENT
NO. PART#
B60077-13 1 DOOR ASS'Y
B60077-14
B60077-15
B60077-16
B60093
Be0004
B60095
Be0096
B60101
BG60102
B60103
B60104
B60098
Be0099
BG60100
B60076-01
B60076-02
B60076-03
BG60076-04
BG60089-02
B60090-02
B60087-02
B60088-01
BG60088-02
B60089-01
B60090-01
TE HEATER ADAPTER
TE HEATER FILLER
CHANNEL
BLOWER RAIL RIGHT/LEFT
BLOWER DECK
BLOWER DECK
BLOWER DECK
TOP ASS'Y
SIDE WRAPPER
WRAPPER
SIDE WRAPPER
International Comfort Products, LLC
Lewisburg, TN 37091 USA
12
Specifications subject to change without notice.
X40159 Rev.C
advertisement
* Your assessment is very important for improving the workof artificial intelligence, which forms the content of this project
Related manuals
Frequently Answers and Questions
What is the nominal installation dimension of MF16?
How much clearance is needed from supply duct to combustibles with heaters installed?
What is the recommended service clearance from the front of the unit?
What type of flexible ducting should be used within 36" (914 mm) of the supply end of the modular unit?
What is the voltage of the MF series blower motor?
What is the electrical hazard associated with the unit?
What safety precautions must be taken when installing or servicing the unit?
advertisement