advertisement
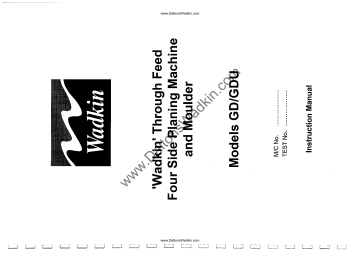
www.DaltonsWadkin.com
CD
C
"'C .-
CDJ:
CD (.)
LL ca
J::Ea>
en en"'C
::::SCo .-
::::s
I..
C 0
J:calllll::::
1--':::::
_ c.."'C
-
::J
C
(!)
........
C
(!)
U)
-
C CD C
~ .-
"'Ctn
ca
ca
I..
CD
"'C o
:E www.DaltonsWadkin.com
LL
. 0 o Z
Z I uCl)
c
-
(/) c·
.-
'0
... www.DaltonsWadkin.com
[
[
[
[
[
[]
[ c c o
D
[J
[
[;
C o
[
[
[
[ www.DaltonsWadkin.com
MANUFACTURERS E.C. DECLARATION OF CONFORMITY
The following machine has undergone "Conformity Assessment" and is "self' certified in accordance with:-
Supply of Machinery (Safety) Regulations 1992 and Amendment No. 2063
COMPANY
WADKIN LTD
Green Lane Road
Leicester
LE54PF
RESPONSIBLE PERSON
Mr A C Lott (Managing Director)
MACHINE DESCRIPTION
TYPE
MODELS
THROUGH FEED FOUR SIDE
PLANING MACHINE AND MOULDER
GD/GDU
DIRECTIVES COMPLIED WITH
www.DaltonsWadkin.com
Amendment No. 2063 1994
Draught Proposal CENITC 142
ISO 9001 Part 1
SIGNED ON BEHALF OF WADKIN PLC
www.DaltonsWadkin.com
[
[
C
C
C
C
C
[
[
[
C
C
C
C
C
0
C
C
C
[l www.DaltonsWadkin.com
CONTENTS
EXTENT OF MANUAL
Section
1
1.1
1.1.1
1.1.2
1.1.3
1.1.4
1.1.5
1.1.6
1.2
1.3
1.3.1
1.3.2
Extent of Manual
HEALTH AND SAFETY
Health and Safety
Factories Act
Health and Safety at Work Act
Electricity Regulations
Provisions and use of Work Equipment Regulations
Woodworking Machines Regulations
Other Documents for Reference
Supply of Machinery (Safety) Regulations 1992
Specific Information
Noise
Dust
Page
2
3
3.1
3.2
3.3
3.4
3.4.1
3.4.2
3.4.3
4
4-1
4.1.1
4.1.2
4.1.3
4.2
4.2.1
4.2.2
4.2.3
MACHINE SPECIFICATION
INSTALLATION
Receipt of the Machine
Preparation for Installation
Lifting and Locating the Machine
Connecting the Services
Electrical Supply
Pneumatic Air Supply www.DaltonsWadkin.com
MACHINE USAGE AND CONTROLS
Safe Practices
Pre-operation Checks
Checks During Operation
Safety Devices
Machine Controls
Machine Control Panel
Outfeed End Controls
Optional Equipment
4-1
4-1
4-1
4-1
4-2
4-2
4-2
4-5
4-6
2-1
3-1
3-1
3-1
3-1
3-2
3-2
3-3
3-3
1-1
1-1
1-1
1-2
1-2
1-2
1-2
1-2
1-4
1-4
1-4
1-5
Contents
Page 1 www.DaltonsWadkin.com
l
L
[
[
Section www.DaltonsWadkin.com
G
-'
C
[
[
[
[
5 SETTING-UP THE MACHINE
[]
[
['
,
[ fl
L
5.1
5.1.1
5.1.2
5.2
5.3
5.4
5.5
5.6
5.7
General
Preparation
Remove/Refit Cutter Block in Spindle
Setting First Bottom Head
Setting Fence Side Head
Setting Near Side Head
Setting Top Head
Top Head Pad Pressure and Chipbreaker
Setting Second Bottom Head
5.8 Setting the Feed Rolls r
5.9 Infeed Table and Fence Adjustment
6 OPERATION
6.1
6.1.1
6.1.2
General
Pre-operation Checks
Setting Controls and Adjustments
0
[]
7 MAINTENANCE
C
C
7.1
7.2
7.2.1
7.2.2
7.2.3
7.3
7.3.1
7.3.2
7.3.3
7.3.4
7.3.5
7.3.6
7.3.7
7.3.8
7.4
7.4.1
7.4.2
7.4.3
7.5
7.5.1
7.5.2
7.6
General
Scheduled Maintenance
Daily
Monthly
Three-Monthly
Unscheduled Maintenance
Re-tension Top/Bottom Head Drive Belt
Re-tension Fence/Side Head Drive Belt
Replace Spindle Drive Belt www.DaltonsWadkin.com
Replace Flange-Mounted Top Feed Rolls/Spacers
Replace BottomlTop Head Spindle
Replace Fence/Near Side Head Spindle
Fault Finding
General
Workpiece Faults
Machine Faults
Lubrication Chart
Lubricants Specified
Approved Lubricants
Tool and Toolholder Care
Page
5-1
5-1
5-1
5-2
5-4
5-6
5-8
5-11
5-14
5-16
5-18
5-22 www.DaltonsWadkin.com
6-1
6-1
6-1
6-1
7-1
7-1
7-1
7-2
7-2
7-2
7-4
7-4
7-5
7-5
7-6
7-7
7-8
7-9
7-10
7-12
7-12
7-12
7-13
7-15
7-15
7-15
7-16
- - - - - - - - . - - - - - -
Contents
Page 2
[,
[
[}
[] u n
[
[; o c
[
[
[
[ c
[
[ r 1
LJ
) '
--~
[
[ www.DaltonsWadkin.com
Section
8
8.1
8.1.1
8.1.2
8.1.3
8.2
8.2.1
8.3
8.4
ADDITIONAL EQUIPMENT APPENDICES
Universal Head
Equipment
Reversing Switch
Setting the Universal Head
Grooved Bed
Setting-up the Cutter Block
Intermediate Feed Roll
Random Side Head
GLOSSARY www.DaltonsWadkin.com
www.DaltonsWadkin.com
Page
8-1
8-1
8-1
8-2
8-2
8-9
8-10
8-11
8-12
Contents
Page 3
[
[
[
[
[ r
[]
[
-'
' c
[
[
[l
[J o
[J
[
[;
L
L
[ www.DaltonsWadkin.com
EXTENT OF MANUAL
This Operation and Maintenance Manual is intended to provide users with all relevant information concerning the operation and maintenance of a Through Feed Four Side
Planing and Moulding Machine, Model GD.
The document is produced in seven sections.
Section One gives advice general safety aspects of the machine usage including references to the various current statutory and safety regulations in force, advice on record keeping of machine operation and maintenance, and also instructions on recommended procedures when accepting and receiving the machine from the manufacturer.
Sections Two to Seven provide the information necessary to install, operate and maintain the machine including procedures for fault finding.
At the end of the manual is a Glossary of terms used throughout the body of the manual.
Also, depending upon any special machine features and/or nature of operation,
Additional Equipment Appendices are included to complement the standard sections within the manual. www.DaltonsWadkin.com
Extent of manual
The policy of the Company is one of continuous development, and the company reserves the right to alter specification without prior notice.
No part of this publication shall be produced in any way without the express permission of the Company.
© 1998.
Page 1 www.DaltonsWadkin.com
L
[
[ r:
[
[
[
C
['
[ c
1.1.1
[
[
[ o
[
[; o n u c
1.1
www.DaltonsWadkin.com
1 HEALTH AND SAFETY
Provision and use of Work Equipment Regulations.
Woodworking Machines Regulations.
Factories Act
This Act requires that rotating machinery shall be of good mechanical construction and that it shall be properly maintained and serviced by competent and experienced persons. www.DaltonsWadkin.com
Health and safety
This Section covers all aspects of safe operation and safe use of woodworking machinery. It refers to various statutory Health and Safety regulations, and also includes information and advice derived from many years' experience in the in the building, operation and maintenance of woodworking machinery.
It is of the utmost importance that the user or employer reads this Section of the document and understands clearly all of the stated requirements concerning safe operation of the equipment.
Health and Safety
There are a number of statutory regulations which apply to the safe operation of woodworking machinery in the UK. These regulations are listed below, and the user is advised to refer to the relevant parts of these regulations and ensure that the requirements are complied with.
Where the machinery is used outside the UK, then the regulations of that country will apply, and should be complied with.
Note:
The list below relates to the most recent published editions of the regulations including all amendments and supplements.
Factories Act.
Health and Safety at Work Act.
Page 1-1
[;
[
[
[
[
[
[
1.1.2
[
[
1.1.3
[
[
[ c
1.1.4
[ n o c
""' l
.~ c c
1.1.5
1.1.6 www.DaltonsWadkin.com
Health and safety
Health and Safety at Work Act
This Act imposes obligations to apply similar standards to those of the Factories Act as a minimum requirement, especially where a machine is installed in a place of work where no suitable legislation applies.
Electricity Regulations
These regulations place general requirements on the installation and maintenance of electrical equipment. Users should be aware of the requirements concerning the availability of lighting and free working space for maintenance personnel, and the importance of personnel being fully competent and trained when working on electrical equipment.
Provision and use of Work Eguipment Regulations
Compliance with these regulations is necessary for equipment to be considered to be conforming with the EC declaration of conformity.
The regulations also place obligations on the user (see Section 1.2).
Woodworking Machines Regulations
These regulations place absolute legal requirements on employers and users to ensure that all fitted guards and safety devices are always used, securely fitted, correctly adjusted and properly maintained.
The regulations also require that maintenance be undertaken only by suitably qualified and competent personnel, and that all power supplies are isolated from the machine before any maintenance is undertaken.
It is also required that operators (users) receive suitable training and instruction www.DaltonsWadkin.com
Other Documents for Reference
Other documents which refer to woodworking machinery operation and maintenance in the UK include:
Noise at Work Regulations.
Control of Substances Hazardous to Health Regulations. www.DaltonsWadkin.com
Page 1-2
[
L
[
[
[} o
[
[
[
[
[
[ r:
[
[
[
[
C
[
[ www.DaltonsWadkin.com
Code of Practice 8S5304 - Safeguard of Machinery.
Code of Practice 8S6854 - Safeguard of Woodworking Machines.
Health and Safety Executive note IND(G) 1 (L).
Heallh and safety www.DaltonsWadkin.com
Page 1-3 www.DaltonsWadkin.com
[
[
[,
[
[
[
1.2
[ o c c
D
1.3
[
[
[
[
[
[
[J
[J
[
1.3.1 www.DaltonsWadkin.com
Health and safety
Supply of Machinery (Safety) Regulations 1992
A machine manufactured in accordance with the Essential Health and Safety
Requirements of the Supply of Machinery (Safety) Regulations 1992, complies with the
EC conformity requirements and can thus have the CE mark appended (Harmonised
Standard PREN 12750: 1997) .
These regulations also impose legal requirements on both the employer and the user of the machine with regard to proper usage, user working conditions, risks of injury and many more. These requirements are wide ranging, and in some cases specific to only certain types of machine or process. Some of the more general requirements which apply to woodworking machinery are briefly detailed below.
1 An employer shall ensure that the equipment is constructed/adapted as to be suitable for the purpose that it is used.
2 In selecting the equipment, the employer shall have due regard to the working conditions and the risks to health and safety of persons which exist in the premises in which the equipment is to be used.
3 The employer shall ensure that the equipment is used for the operations for which, and under the conditions for which it is suitable.
Other requirements include provision of suitable training of users, provision of suitable documentation (information and instructions), and declarations of any specific risks.
Specific Information
Section 4 of this manual - Machine Usage and Controls identifies and details general safe working practices and specific local practices which should be adopted when using the machine. In addition to this information two hazards, specific to woodworking machinery should be considered in more detail.
Noise www.DaltonsWadkin.com
Noise levels can vary widely depending upon the machine and the conditions of use.
Planing and moulding machines produce high noise levels, typically in the region of 95dB to 115dB when cutting.
The Noise at Work Regulations require that an operator is not subjected to continuous noise levels above 90dB over an 8 hour period. Thus, some form of noise protection is necessary. www.DaltonsWadkin.com
Page 1-4
[;
C
C
C
~
[
[
C
0
C
[
C
C
[ r-
[ e
C
[ lJ
1.3.2 www.DaltonsWadkin.com
Health and safety
A machine manufacturer may supply (or provide information) a suitable sound enclosure. It is possible that, given the types of materials available in the works
(ie sawmill),a suitable enclosure may be produced on site.
It should be noted however, that even with an enclosure, noise levels might still exceed the 90dB limit (especially at the machine infeed end).
As a precaution suitable ear protection should be worn by all machine operatives.
Refer to use of ear defenders in Section 4.1.2 of this manual.
Dust
Wood dust can be harmful to health through inhalation and also skin contact.
The Control of Substances Hazardous to Health Regulations place legal requirements on employers to prevent exposure of the user to substances hazardous to health or, where prevention is not practicable, to adequately control the exposure. Adequate control should be achieved by measures other than provision of personal protective equipment.
The Regulations require that airborne dust levels should not exceed 5mgfm 3
• www.DaltonsWadkin.com
Page 1-5 www.DaltonsWadkin.com
[
[
[ c
[
D o c c
[ c
[
C c
[ o
[
[
[
[ www.DaltonsWadkin.com
2 MACHINE SPECIFICATION
Specification
Machine Details
Model
Dimensi.ons
Services
GD220
Refer to machine Foundation Plan
Refer to the machine Specification
Plate located on the machine frame
Capacities and Adjustments
Maximum timber size admitted
Maximum finished work size
Feed speeds
Pneumatic Air Requirement
Motors
Feed motor
Rise and fall motor
Spindle motors
230mm x 130mm
220mm x 120mm
6 to 22mlmin (standard)
6 bar/0.15m3/min
2.2kW
0.375kW
5.5kW/7.5kW
6000rev/min (standard) Spindle speed www.DaltonsWadkin.com
Note
This unit will operate between 41 & 104 Oeg. F (5 to 40 Oeg. C); upto 3300ft (1000m);
20% to 95% RH (non condensing); and transportation and storage conditions of -13 to
131 Oeg. F (-25 to 55 Oeg. C). www.DaltonsWadkin.com
Page 2-1
C
[
[
-.
.
~
~
D
[
[
[
[
[
[
'l ~
"'. I
[
[
[ c o
3.2
[
D o o
3.3 www.DaltonsWadkin.com
3 INSTALLATION
Lifting and Locating the Machine
Position a steel levelling plate at each machine jacking screw point (refer to the machine
Foundation Plan).
Lift and position the machine on the prepared location.
Level the machine (as detailed below) using an engineer's level by adjusting the jacking screws located at each machine foot position.
Levelling longitudinally
With the engineer's level lengthways on the table of the machine, adjust the machine longitudinally by adjusting the jacking screws. Check level at approximately every 300mm along the machine length. Deviation should not exceed O.1mm/m.
Page 3-1 www.DaltonsWadkin.com
Installation
Receipt of the t.1achine
Before accepting the machine at its destination check the packages/items against the bill of loading. Confirm that all listed fittings/accessories have been received and carry out a visual inspection of the packages/items for obvious signs of damage.
Report any omissions or damage; note these for any future reference.
Preparation for Installation
Ensure that all the necessary external services are available ie electricity, pneumatic air, etc., as identified in Section 2 Machine Specification.
Check also that adequate space is available on the installation site for lifting and manoeuvring access.
Check that suitable and approved lifting equipment is available and is of adequate capacity:
Refer to the Foundation Plan for details of the floor area required and for any special foundations necessary
Ensure that the final location of the machine has been levelled.
[ r:
CJ
[J
G
D
0
0
0
0
[
0
~ fi
-'
[~
[J
0
[:
G o
3.4
3.4.1 www.DaltonsWadkin.com
Connecting the Services
Electrical Supply
The customer is responsible for an electrical supply suitable to meet the power requirements of the machine. These requirements are shown on the machine
Specification Plate on the machine frame, and are also shown on the electrical schematic/connection diagram accompanying the machine.
Electrical connections should be made to the isolating switch on the electrical control cubicle.
WARNING:
Connection of the supply must be made by a competent and experienced electrician.
US & Canada - All supply wiring and conduit sizes must be sized in accordance with the NEC (National Electric Code - NPFA 70) and applicable state, county or jurisdictional codes, or CEC (Canadian Electric Code)
The connection procedure should include, but not be limited to:
Confirm that the supply is of the correct voltage, phase and frequency to that identified on the machine SpeCification Plate. www.DaltonsWadkin.com
machine Specification Plate.
Connect the incoming supply to the relevant terminals on the electrical control cubicle
(L 1, L2 and L3).
Make a good earth connection to the machine.
WARNING:
Before continuing further, refer to Section 4 for advice on safe operation of the machine. Also, ensure that when undertaking any of the following operations all relevant safety requirements and procedures detailed in Section 1 are complied with. www.DaltonsWadkin.com
Installation
Levelling transversely
Position the engineer's level across the table (at right angle to the fence), and adjust the machine transversely by adjusting the jacking screws. Repeat this action at points similar to the longitudinal checks. Deviation should not exceed
O.1mm/m.
WARNING:
The machine must be firmly bolted down before connecting any services.
Page 3-2
[J
[
[
[
[
[:
[
[ o
3.4.2
[
[l
-,
[J o o c
[
[ 1
.' o c o
3.4.3 www.DaltonsWadkin.com
Installation
Close the isolator on the electrical control cubicle, and run each spindle in turn to ensure direction of rotation is correct:
Bottom horizontal spindles - clockwise when viewed from front.
Top heads - counterclockwise when viewed from front.
Fence side head - counterclockwise when viewed from above.
Near side head - clockwise when viewed from above.
Note:
Incorrect rotation of the spindles can be corrected by reversing any two of the incoming supply connections to the terminals of the electrical control cubicle.
WARNING:
Phase changes must be made by a competent and experienced electrician.
Pneumatic Air Supply
The customer is responsible for a pneumatic air supply suitable to meet the requirements of the machine as shown on the machine Foundation Plan (6 bar
O.15
m 3/ m in).
The air supply connection in the machine base is Y-BSP female.
Check the condition of the air connectors, confirm their cleanliness, and make the air connection.
Dust Extraction
The customer is responsible for the supply and fitting of suitable dust extraction equipment. should be as shown on the machine Foundation Plan.
See the machine Foundation Plan for:
Airflow requirements in m 3 /hour.
Cross-sectional dimensions of machine extraction connections.
Duct air velocities in m/second.
Average pressure drop at machine extraction connections are shown below.
Duct Diameter (mm) Required Air Volume
(m 3 /hour at 30m/sec)
Pressure Drop
(Pa)
Page 3-3 www.DaltonsWadkin.com
www.DaltonsWadkin.com
o o o
~ o to
CO
CD o
CD
~ o to
~
L...J www.DaltonsWadkin.com
www.DaltonsWadkin.com
[
[
[
[
[
[
[ c
4.1
[] o o o
4.1.1
[J
D
D
[J
[] o u
4.1.2
[ www.DaltonsWadkin.com
Pre-operation Checks
All guards and fences are fitted securely and properly adjusted to suit their purpose.
Cutter blocks are correct for the work to be undertaken, are suitable for the spindle speed, are securely fitted and their direction of rotation is correct.
Dust extraction equipment is working correctly.
Machine controls are functioning correctly (see Section 4.2).
Adequate working space is provided and lighting is available. www.DaltonsWadkin.com
immediate locality have been read and fully understood.
Checks During Operation
Proper protective equipment is available and employed (goggles, ear defenders, face mask, etc).
Area around the machine is kept clean and free of wood refuse.
Any machine malfunction is recorded and reported to person in authority.
Machine is made stationary and electrically isolated before any cleaning of work area or ANY adjustments are made to the machine or ancillary equipment.
Page 4-1 www.DaltonsWadkin.com
Machine usage and controls
4 MACHINE USAGE AND CONTROLS
Note:
Refer also to Section 1 for information on general statutory requirements when operating woodworking machinery.
Safe Practices
Safe and proper working practices must be followed when setting-up and operating the machine. Adequate advice and information are readily available in the form of local working practices, notices, warnings and the inforrnation contained in this manual.
IT IS THE OPERATOR'S RESPONSIBILITY TO USE THE MACHINE FOLLOWING
THE PROCEDURES LAID DOWN AND ONLY FOR THE PURPOSES FOR WHICH IT
WAS DESIGNED.
[
D
[J
0
[
C
0
0
[J
0
[
[
C
[]
[1
C
[
[
[
[i
4.1.3 www.DaltonsWadkin.com
2
3
Figure 4.1.3
A splinter catching device protects against splinters at the machine infeed (fitted optionally when the machine is specified for splitting use).
If the enclosure door is opened during normal operation all spindles and feed rolls stop.
4
5
6 purposes only.
The machine feed does not operate unless the spindles are running and the enclosure is closed.
Brakes are fitted to all spindles. www.DaltonsWadkin.com
Machine usage and controls
Safety Devices
In order to avoid injury or accidental damage to personnel or equipment, a number of interlocking features have been incorporated into the machine operation. These are:
1 Infeed trip device (1) will trip the operation of the machine feed. The spindles will continue to run. This trip level is set through the height of the beam setting. (See
Figure 4.1.3).
Before attempting to restart the machine electrically isolate the machine. The feed must be restarted at the control panel after removal of the cause of the trip.
1
Page 4·2
[
C
D
C
D
[
[J
0
0
C
0
C
[l
[
C
4.2
4.2.1
[
[
[
C
C
Machine usage and controls
Machine Controls
Machine Control Panel
Before using the machine, operators should familiarise themselves with the machine control panel and other controls.
The machine control panel is mounted at the infeed end of the machine and consists of a number of buttons, switches and indicators (see Figure 4.2.1). Depending upon the model of the machine and special features fitted, the illustration of the control panel may differ slightly from the panel on the machine being installed.
Feed Stop/Start (1)
Toggle start/stop button with indicator lamp which controls the operation of the feed rolls.
Inch Forward/Reverse (2)
Two buttons and a keyswitch enable the feed to be inched forward or backwards - for setting-up or other maintenance purposes.
~
~ www.DaltonsWadkin.com
www.DaltonsWadkin.com
Figure 4.2.1 www.DaltonsWadkin.com
~
~
Page 4-3
[
[
L
[
[
D
D
D
[
C
[ o o c o o o o o o www.DaltonsWadkin.com
Machine usage and controls
Beam Raise/Lower (3)
Two buttons enable the beam to BE raised or lowered within predetermined limits.
Similar buttons are also on the local control panel located beneath the first top head (see
Figures 4.2.2 and 5.5).
Enclosure Override (4)
Two-position keyswitch which enables the machine drives to operate when the enclosure is raised - for setting-up and other maintenance purposes.
Emergency Stop (5)
Emergency stop button shuts down machine operation when depressed. Must be unlocked to reset.
Emergency stop buttons are also located at other pOints on the machine in compliance with Machinery Directive requirements.
Spindle Head Brake Release (6)
Releases the spindle brakes to enable free rotation of the spindles for changing cutter blocks, belts, etc; lamp indication when enabled.
Spindle Start/Stop (7)
Each spindle has a toggle start/stop button with lamp indicator. These enable spindles to be started and stopped independently.
Sets feed roll pressures.
Other optional controls not shown on Figure 4.2.1, but which can be mounted on the machine control panel include:
Power On/Off
Toggle power on/off button with lamp indicator. Controls power through the control panel.
Page 4-4 www.DaltonsWadkin.com
[ c
[
[J
0
0
0
0
0
0
C
0
0
0 o
U2
0
0
0
D
D www.DaltonsWadkin.com
Clamp On/Off
Two buttons enable the vertical movement of the top head to be clamped/unciamped.
Emergency Stop (1)
Emergency stop button shuts down machine operation when depressed. Must be unlocked to reset.
Inch Forward (2)
A button enables the feed to be inched forward - for setting-up purposes.
Beam Raise/Lower (3)
Two buttons enable the beam to be raised or lowered within predetermined limits.
~ www.DaltonsWadkin.com
Machine usage and controls
Automatic Lubrication
Two-position on/off switch providing automatic lubrication to machine bed when set on.
Associated 'Iow oil level' lamp indicator.
Outfeed End Controls
A local control panel (see Figure 4.2.2) is located below the top head, and provides the following controls.
Figure 4.2.2
~
Page 4-5
[
[J
0
0
0
0
0
0
0
0
0
0
I ' l,
C
4.2.3
0
0
0
[j
C
C www.DaltonsWadkin.com
Universal Head
Universal head device with start, stop buttons and direction of rotation switch.
Electronic Positioning Unit
Electronic positioning device for top head and near side heads. It locates and memorises the position of the head through a microprocessor.
Grooved Bed
Used mainly in furniture making, this feature processes short lengths of twisted timber.
Random Side Head
This option enables various widths of timber fed into the machine to be automatically processed to a single width.
Glazing Saw Unit
Used when processing window components, it permits a glazing bead to be removed from the frame and be re-used.
This option is fitted to an existing feed roll to add an intermediate feed roll when necessary (when processing short lengths of timber). www.DaltonsWadkin.com
Machine usage and controls
Optional Equipment
Other optional equipment can be fitted to the machine. (When fitted, the options are described fully in the Additional Equipment Section of this manual). This equipment includes:
Page 4-6
[J rJ
[
[' c o
[J c o o o o c o
5.1
D o o
[J
[j o
5.1.1 www.DaltonsWadkin.com
5 SETTING-UP THE MACHINE
4 in the direction of the workpiece to their final positions, but move the top head and feed rolls in an upward direction.
Secure the tool in pOSition, and note the digital indicator display reading (where fitted).
1
2
Preparation
Before beginning the setting-up procedure carry out the following checks:
Cutter blocks are securely fitted (see Section 5.1.2).
Adequate working space is provided and lighting is available. www.DaltonsWadkin.com
Setting-up the machine
General
This Section describes the procedures to set-up a five-spindle Model GO machine for a planing operation.
Because the number and combination of features which can be built into the Model GO machine cover a wide variety, these procedures describe the setting-up of those features which appear on all types of Model GO machine. The differences between individual machines will be only in the number and combination of the features described.
Setting-up comprises setting tool spindles to basic positions relative to the table and the fence using a straight edge, and setting feed roll height.
To achieve a good product, the tool must be adjusted very accurately to the table or fence behind the tool.
2
3
The basic procedure for setting-up all cutting tools is as follows:
1 Place the straight edge on the table or against the fence behind the tool and hold in position.
Rotate the tool by hand in the opposite direction of the cut.
Adjust the position of the tool using the crank handle until a cutting edge of the tool touches the straight edge.
Page 5-1
C
[
[
C
C
[j
D
0
0
0
C
C
[
[
[
[
[
[
C
5.1.2
[J www.DaltonsWadkin.com
Setting-up the machine
4
5
3 Proper protective equipment (goggles, ear defenders, face mask, etc) is available and employed if required.
Area around the machine is clean and free of wood refuse.
Machine spindles and feed rolls are stationary and the machine is electrically isolated.
Equipment required:
1 Straight edge.
2 Standard tool kit.
RemovelRefit Cutter Block in Spindle (Figure 5.1.2)
WARNING:
ENSURE THAT THE MACHINE IS ELECTRICALLY ISOLATED (EMERGENCY STOP
ACTIVATED) BEFORE PROCEEDING.
Notes:
All spindles have right-hand threads.
Do not strike any component; do not use a box or extension spanner. www.DaltonsWadkin.com
www.DaltonsWadkin.com
Page 5-2
[
[
[
[ c c c
[
[] o o o
[
[
[
[
[ c c o
[2J
1 www.DaltonsWadkin.com
www.DaltonsWadkin.com
Setting-up the machine
2
3
4
5
1
2
Figure 5.1.2
Open or remove any guards to permit easy access to the cutter block.
Using a combination spanner, unscrew the spindle nut from the spindle by locating the spanner on the hexagon (1) of the spindle and the two flat faces of the cutter block locknut (2), (unscrew counterclockwise).
Before refitting the cutter block, carefully clean the spindle and the cutter block.
Locate the cutter block on the spindle and the locking collar, and tighten the hexagon (clockwise) using a combination spanner.
Page 5-3
[
[
[
[
[
[
~ r:
. c
Q
0
C
0
[:
0
5.2
[
[J c
[
0 c
Horizontal Setting www.DaltonsWadkin.com
Setting First Bottom Head (Figure 5.2)
Setting the first bottom head involves a radial (vertical) and axial (horizontal) adjustment.
It sets the cutter block level with the outfeed side bed of the head, the actual cut size being set by the infeed table adjustment (see a later procedure); it also sets the edge reference knives.
WARNING:
ENSURE THAT THE MACHINE IS ELECTRICALLY ISOLATED (EMERGENCY STOP
ACTIVATED) BEFORE PROCEEDING.
6
7
4
5
Vertical Setting
1
2
3
Open or remove any guards to permit easy access and ensure that the bottom head outfeed side bed is clear .
Place a straight edge on the outfeed side bed extending over the bottom head cutter block.
Release the spindle brake.
Release locking handle (1).
Turn the cutter block by hand counterclockwise and using the crank handle, adjust shaft (2) until a cutting edge of the cutter block just touches the straight edge. The final movement of the spindle should be towards the workpiece.
Lock handle (1 ).
Check that adjustment is correct across whole width of the cutter block.
8
9
Release locknut (3).
Place the straight edge along the reference fence extending over the bottom head cutter block.
10 Rotate adjuster (4) until the edge reference knives just touch the straight edge.
The final movement of the spindle should be towards the workpiece.
11
12
Tighten locknut (3).
Refit/replace guards. www.DaltonsWadkin.com
Setting-up the machine
Page 5-4
www.DaltonsWadkin.com
<1>
"
'"
<1>
,s i
C.
"
" rn
EJ EJ
, www.DaltonsWadkin.com
r-------,
L--.J www.DaltonsWadkin.com
:g
<1>
Cl
'"
[
[
[
[
[
[
C
0
C
C
C
C
[
[]
[~
[]
L r
5.3
C
[ www.DaltonsWadkin.com
Figure 5.3
1
2
3
4
5
Open or remove any guards to permit easy access and ensure that the fence side head outfeed bed is clear.
Place a straight edge against the outfeed side fence extending over the fence side head cutter block.
Release the spindle brake.
Release locking handle (1).
Turn the cutter block by hand counterclockwise and using the crank handle adjust shaft (2) until a cutting edge of the cutter block just touches the straight edge. The final movement of the spindle should be towards the workpiece.
Page 5-6 www.DaltonsWadkin.com
Setting-up the machine
Setting Fence Side Head (Figure 5.3)
Setting the fence side head involves a radial (horizontal) and axial (vertical) adjustment.
It sets the cutter block level with the outfeed side bed of the fence, the actual cut having been set by the infeed fence adjustment (see a later procedure). It also sets the depth of the cutter block below the bed.
WARNING:
ENSURE THAT THE MACHINE IS ELECTRICALLY ISOLATED (EMERGENCY STOP
ACTIVATED) BEFORE PROCEEDING.
~
~
~
~
[
[]
[J o
L
[
[
[
[
[
[J
[
[
[
[
[
[
[
[~
[ www.DaltonsWadkin.com
Settingwup the machine
6
Clockwise rotation of the crank handle moves the cutter block away from the fence), counterclockwise rotation moves it towards the fence (giving a positive count on the digital indicator - where fitted).
Maximum achievable adjustment is 65mm horizontally (radially).
Lock handle (1).
8
9
Vertical Setting
7 Establish depth of the cutter block below the bed, and note the reading on the digital indicator - where fitted).
10
13
Release locking handle (1) and clamp (3).
Using the crank handle, adjust shaft (4) until the spindle flange is 5mm below the level of the bed.
The final movement of the spindle should be towards the workpiece.
Clockwise rotation of the crank handle raises the cutter block (giving a negative count on the digital indicator - where fitted), counterclockwise rotation lowers it.
Maximum achievable adjustment is 38mm vertically (axially).
Lock handle (1) and clamp (3).
Refit/replace guards. www.DaltonsWadkin.com
Page 5-7 www.DaltonsWadkin.com
[
[
[
[ r~ c
[}
5.4
lJ
[
[ c:
-' c
,~ r'
0
0 c
0 c
[ c
Setting Near Side Head (Figure 5.4)
Setting the near side head involves a radial (horizontal) and axial (vertical) adjustment.
It datums the cutter block to the width of the product and also sets the depth of the cutter block below the bed, This procedure also includes the setting of the near side head chipbreaker and the near side head pad pressure.
WARNING:
ENSURE THAT THE MACHINE IS ELECTRICALLY ISOLATED (EMERGENCY STOP
ACTIVATED) BEFORE PROCEEDING.
~
QJ www.DaltonsWadkin.com
Figure 5.4 o
1
2
3
4
5
Open or remove any guards to permit easy access and ensure that the near side head outfeed bed is clear.
Place a datum block of known width between the near side head fence and the cutter block.
Release the spindle brake.
Release locking handle (1).
Turn the cutter block by hand counterclockwise and using the crank handle adjust shaft (2) until a cutting edge of the cutter block just touches the datum block. The final movement of the spindle should be towards the workpiece.
Page 5-8 www.DaltonsWadkin.com
Setting-up the machine
~
[
[
[J
[
[
[
[
[
[
C c
[ c
L o c
L o
L
[
6
7 www.DaltonsWadkin.com
Setting-up the machine
Clockwise rotation of the crank handle moves the cutter block towards the fence
(giving a negative count on the digital indicator - when fitted), counterclockwise rotation moves it away from the fence.
Check that the digital indicator indicates the width of the block. If not, slacken the grubscrew in the indicator collar and rotate the indicator collar only until the reading corresponds to the datum block. Retighten the grubscrew.
Lock handle (1 ).
Vertical Setting
8 Establish depth of the cutter block below the bed, and note the reading on the digital indicator.
9
10
Release locking handle (1) and clamp (3).
Using the crank handle, adjust shaft (4) until the spindle flange is 5mm below the level of the bed.
Clockwise rotation of the crank handle raises the cutter block (giving a negative count on the digital indicator - when fitted), counterclockwise rotation lowers it.
11
Maximum achievable adjustment is 38mm vertically (axially).
Lock handle (1) and clamp (3).
Chipbreaker and Pad Pressure Setting www.DaltonsWadkin.com
~ ~
Figure 5.4 www.DaltonsWadkin.com
Page 5-9
~
[
[
[
[
[
[] o n
[j c o c
[j o c c c
[] c o
Q www.DaltonsWadkin.com
Setting-up the machine
12 Slacken bolts (5) and move the chipbreaker forward to touch the datum block.
Check that the front face of the chipbreaker shoe is in line with the datum block.
Tighten bolts (5). 13
14 Slacken nuts (6) and move the pad pressure shoe until it is in line with the datum block and is between 3 and 5mm from the tip of the cutter.
15 Tighten nuts (6).
16 Refit/replace guards. www.DaltonsWadkin.com
Page 5-10 www.DaltonsWadkin.com
[
[
[
[
C
[
[
[
[
[
D
D
[
[ c
C
0
[
C
[
5.5
www.DaltonsWadkin.com
www.DaltonsWadkin.com
[2J
~
~
Figure 5.5 www.DaltonsWadkin.com
Setting-up the machine
Setting Top Head (Figure 5.5)
Setting the top head involves a radial (vertical) and axial (horizontal) adjustment. It can also datum the cutter block to the height of the product.
The vertical adjustment is accomplished by powered and/or manual adjustment of rise and fall of the beam.
WARNING:
ENSURE THAT THE MACHINE IS ELECTRICALLY ISOLATED (EMERGENCY STOP
ACTIVATED) BEFORE PROCEEDING.
Vertical SettinQ
1 Open or remove any guards to permit easy access and ensure that the first top head outfeed bed is clear.
2 Place a datum block of known height on the bed beneath the top head.
~ ~
Page 5-11
[
[
[
[
[
[
[
[ o o o o o o o c
[
[
[ c www.DaltonsWadkin.com
Setting-up the machine
5
6
3
4
7
8
9
10
11
Reset the emergency stop.
Release the spindle brake.
Release locking handle (1).
Lower lever (2) and hold until automatic adjustment engages. (If engagement does not occur, adjust shaft (3) to right or left until engagement is achieved).
Press the raise/lower buttons (4) on the local control station to position the cutter block close to the datum block.
Lower lever (2) to disengage the automatic adjustment.
Note:
The proximity of the spindle to the datum block is dependent on the beam setting
- Steps 9 to 12 achieve accurate setting.
Operate the emergency stop.
Turn the cutter block by hand counterclockwise and using the crank handle adjust shaft (3) until a cutting edge of the cutter block just touches the datum block. The final movement of the spindle should be away from the workpiece.
Clockwise rotation of the crank handle lowers the cutter block towards the block
(giving a negative count on the digital indicator - when fitted), counterclockwise rotation raises it.
Check that the digital indicator indicates the height of the block. If not, slacken the grubscrew in the indicator collar and rotate the indicator collar only until the reading corresponds to the datum block. Retighten the grubscrew.
12 Lock handle (1 ). www.DaltonsWadkin.com
o
Figure 5.5 www.DaltonsWadkin.com
Page 5-12
[
[ o o o o o o o c o o n
Li o c o u n o
['
LJ n www.DaltonsWadkin.com
Setting-up the machine
13
14
15
16
Slacken locknut (5).
Using the crank handle, adjust shaft (6) until the spindle flange is 5mm behind the fence line. The final
movement
of the spindle should be towards the workpiece.
Tighten nut (5).
Refit/replace guards. www.DaltonsWadkin.com
www.DaltonsWadkin.com
Page 5-13
[
[
0
0
D
0
[J
0
0
0
0
0
0
0
[
[
[
[
,~
0
[
5.6
www.DaltonsWadkin.com
Setting~up the machine
Top Head Pad Pressure and Chipbreaker (Figure 5.6)
This procedure sets the pad pressure and chipbreaker to the base cutting circle of the top head cutter block.
WARNING:
ENSURE THAT THE MACHINE IS ELECTRICALLY ISOLATED (EMERGENCY STOP
ACTIVATED) BEFORE PROCEEDING.
[2]
[J o
1
2
3
4
5
Open or remove any guards to permit easy access and ensure that the top head outfeed bed is clear.
Ensure that the face of the pad (1) is clean and place a datum block across the bed extending from the pad across the cutter block to the chipbreaker .
Rotate the handwheel (2) until the face of the pad just touches the datum block
(see Step 10 of Section 5.5).
Slacken locknuts (3) and position the pad nose 5mm from the cutter block.
Position the pad laterally over the bed to suit the product width and tighten locknuts (3). Ensure that the pad is in front of the fence line.
Page 5-14 www.DaltonsWadkin.com
[
[
[
[
[
[
[ o l: o o o o o o
[; c o
[ c
~ www.DaltonsWadkin.com
Setting-up the machine
5
6
Figure 5.6
Check that the chipbreaker shoe (4) is compatible with the diameter of the cutter block. (The top head is supplied with one of three different lengths of chipbreaker shoe to suit the diameter of the cutter block). Each shoe is secured by two countersunk screws through the bottom face.
7
The shoe should be as close as possible to the maximum cutting circle while also allowing only safe chipbreaker operation.
Slacken locknuts (5) and turn the adjusting screw (6) until the bottom face of the www.DaltonsWadkin.com
Tighten locknuts (5). 8
9 Remove the datum block.
10 Refit/replace guards.
Page 5·15 www.DaltonsWadkin.com
[
[
[
[
[ o
[ o c o o c c
[J
[ o
[
[
[
[ www.DaltonsWadkin.com
Setting-up the machine
5.7 Setting Second Bottom Head (Figure 5.7)
3
4
(When planing or moulding) the outfeed side bed of the second bottom head is shimmed to be nominally O.5mm above bed normal level.
Setting the second bottom head sets the cutter block between these two bed levels.
WARNING:
ENSURE THAT THE MACHINE IS ELECTRICALLY ISOLATED (EMERGENCY STOP
ACTIVATED) BEFORE PROCEEDING.
Vertical Setting
1
2
Open or remove any guards to permit easy access and ensure that the bottom head outfeed side bed is clear.
Place a straight edge on the outfeed side bed extending over the bottom head cutter block.
Release locking handle (1).
Release the spindle brake.
~ []
5
Figure 5.7
Turn the cutter block by hand counterclockwise and using the crank handle, adjust shaft (2) until a cutting edge of the cutter block just touches the straight edge. The final movement of the crank handle should be towards the workpiece.
Page 5-16 www.DaltonsWadkin.com
[
[
[
[
[
[
[
[
[
[
[
[
[
[
[
[
[J o o o www.DaltonsWadkin.com
Setting-up the machine
6
7
Lock handle (1).
Check that adjustment is correct across whole width of the cutter block.
8
9
10
11
12
Horizontal Setting
Release locknut (3) ..
Using the crank handle, adjust shaft (4) until the spindle flange is 5mm behind the fence line. The final movement of the spindle should be towards the workpiece.
Tighten locknut (3).
Refit/replace guards.
Place a piece of timber on the bed of finished product width and adjust the slide guide so that the timber is held lightly against the fence.
~ www.DaltonsWadkin.com
Figure 5.7 www.DaltonsWadkin.com
Page 5·17
[
[
[
[
[
[J
[
C
C
C
0
0
C
[
C
5.8
[
.. '
0
[J
0
[: www.DaltonsWadkin.com
Setting the Feed Rolls (Figures 5.8.1, 5.8.2 and 5.8.3)
Setting-up the machine
The throughfeed, gearbox-driven top feed rolls are mounted on the beam and pressure is exerted via pneumatic cylinders (with additional manual adjustment on feed rolls after the top head). The feed rolls are either flange-mounted (near side head position) or shaft-mounted (bottom head, fence side head and top head positions) .
Initial setting of the feed rolls is made through the beam control setting (beam
'raise/'Iower' buttons on the machine control panel). This setting should be the height of the finished product.
Maximum traction over the full width of the product is achieved by using spacers (flangemounted feed rolls) and by positioning of rolls at points along the shaft (shaft-mounted feed rolls).
Feed rolls shall be fitted not less than 4mm from a fence.
WARNING:
ENSURE THAT THE MACHINE IS ELECTRICALLY ISOLATED (EMERGENCY STOP
ACTIVATED) BEFORE PROCEEDING.
2
3
Positioning Shaft-Mounted Feed Rolls (Figure 5.8.11
1 Ensure that shaft is clean.
4
Slacken set screw (1 ).
Position feed roll(s) to suit product width.
Tighten set screw (1 ).
3
4
2
Figure 5.8.1
1
Page 5-18 www.DaltonsWadkin.com
[J
[J
[;
[
['
[' c
[
G o o
[ c
[J o c c o c
G www.DaltonsWadkin.com
Setting-up the machine
Positioning Flange-Mounted Feed Rolls (Figure 5.8.2)
1 Slacken the draw bolt (1), remove the 'C' washer (2) and withdraw the bolt.
2 Load spacers and feed rolls over the draw bolt engaging drive pins of spacers and feed rolls into opposite holes.
3
4
The combination of feed rolls and spacers will depend upon the product width.
Hold the assembly against the drive flange and screw in draw bolt until close to the face of the end feed roll.
Slot the 'C' washer (2) over the draw bolt (1) and tighten the draw bolt.
1
2
Figure 5.8.2
4
Setting Feed Rolls after the Top Head (Figure 5.8.3)
3
2
1
This procedure is undertaken after the beam control setting, and the setting should be www.DaltonsWadkin.com
Slacken nut (1 ).
Rotate handwheel (2) to adjust the height of the feed roll from the bed to approximately 3mm less than the height of the finished product.
Tighten nut (1 ).
Check height of the feed roll from the bed and reset if necessary. www.DaltonsWadkin.com
Page 5-19
[
[
L
[
[
[
[
[
[
[
[
[]
[; c c c
G
[
G c
1
2 www.DaltonsWadkin.com
Setting-up the machine
Figure 5.8.3
Setting Top Roller Pressure (Figure 5.8.1)
5
6
3
4
1
2
This procedure is undertaken after the beam control setting, using, if possible, a piece of timber the same thickness of the finished product.
Place the timber beneath the top roller assembly.
Slacken bolt (3) and move the roller laterally to be central to the cutter block.
Slacken bolt (4) and lower the roller until it touches the timber.
Rotate screw (5) to increase or decrease pressure on the roller.
Tighten bolts (2), (3) and (4).
Page 5-20 www.DaltonsWadkin.com
[
[
[
[
[
[
[
[ o o c c
[ c c
[
[
[
L_ n e www.DaltonsWadkin.com
Setting-up the machine
Setting Side Roller (when fitted)
This roller is fitted at the fence side head position.
The roller is adjusted to the width of the product to exert moderate force on the timber.
Adjustment is effected by releasing two locknuts which allow the roller, under spring pressure, to take up the required setting; the nuts are then retightened. www.DaltonsWadkin.com
Page 5·21 www.DaltonsWadkin.com
D
C
[;
0
C
[i
[;
[
[
[
C
[;
C
[J
[J
[;
[
[;
L
[;
5.9
www.DaltonsWadkin.com
Infeed Table Adjustment
1
2
Rotate knurled handle (1) counterclockwise to release locking mechanism.
Position handle until the indicator (2) reads the required cut depth.
3 Rotate handle (1) clockwise to lock the table.
~ o
~
~
~
Infeed Fence Adjustment
1
2
3
Rotate handle (3) counterclockwise to release locking mechanism.
Using handle (4) adjust the infeed fence until the scale (5) reads the required measurement.
Rotate handle (3) clockwise to lock the infeed fence. www.DaltonsWadkin.com
Setting-up the machine
Infeed Table and Fence Adjustment (Figure 5.9)
The height of the infeed table determines the cut to the first bottom head. There is a maximum adjustment of 10mm. When the adjustment is zero, the infeed table is level with the table after the first bottom head.
Infeed fence adjustment determines the cut at the first fence side edge. There is a maximum adjustment of 10mm.
WARNING:
ENSURE THAT THE MACHINE IS ELECTRICALLY ISOLATED (EMERGENCY STOP
ACTIVATED) BEFORE PROCEEDING.
Page 5-22
[
[l
[
[ c
6.1
[
[ o n
LJ c o c o o o c o o o o
6.1.1
6.1.2 www.DaltonsWadkin.com
6 OPERATION
8
Setting Controls and Adjustments
1 Close the electrical supply isolator and connect the pneumatic air supply at the electrical control cubicle.
2 Power-up the machine at the machine control panel.
3 Position the near side head, chipbreaker and pad pressure to the width of the finished product (see Section 5.4).
7
6
4
5
Set the top head to the height of the finished product (see Section 5.5). www.DaltonsWadkin.com
Before continuing, check all guards and check that the dust extraction system is switched on and working properly.
With the spindle brakes released, carefully rotate all cutter blocks by hand to ensure free rotation.
With the enclosure door open, turn the 'enclosure
override'
keyswitch to door open, and the 'inch feed' keyswitch to forward.
Start all spindles. www.DaltonsWadkin.com
Operating the machine
General
This Section gives a typical operating sequence for a Model GD machine using the controls described in Section 4 and the basic set-up procedures described in Section 5.
It should be noted that the sequence is typical only - the use of machine controls in conjunction with the setting-up procedures vary depending upon the features of the machine and also the process it is to undertake.
Users are expected to establish operating procedures which comply with local requirements and practices.
Pre-operation Checks
Undertake all the pre-operation checks detailed in Section 4.1.1.
Page 6-1
[
L o
[
[
D o c o c c o c c o
D o c o o www.DaltonsWadkin.com
Operating the machine
9
10
11
During the set-up procedure the main feed is inoperative; only the inch control forward is enabled allowing the workpiece to move forward a short distance at a time, each movement requiring a pressure on the button.
Using the 'inch forward' control pass a 'test piece' timber through the machine and check the dimensions for specification and the quality of finish.
Inspection of the timber should be carried out at each position and at this point, if necessary, adjustments of cut, pressure, side rollers, etc. should be undertaken.
WARNING:
ALWAYS ELECTRICALLY ISOLATE THE MACHINE BEFORE EACH AND
EVERY ADJUSTMENT DURING A 'TEST PIECE' PROCEDURE.
Repeat Step 9 until the 'test piece' timber meets all dimensional and quality requirements.
Set the machine to operate in production mode by setting the 'enclosure override' keyswitch to door closed, starting the main feed and setting feed speed to between 10 and 12m/min.
The machine is now ready for production operation. www.DaltonsWadkin.com
Page 6-2 www.DaltonsWadkin.com
[
[
[ c
7.1
D
D
[
D
D
[ o o
D o o o o
[ c o
7.2 www.DaltonsWadkin.com
7 MAINTENANCE
Maintenance
General
This Section covers scheduled and unscheduled maintenance of the machine, and also covers some basic fault-finding procedures.
Scheduled maintenance comprises the maintenance necessary, at regular intervals, to maintain the machine in good working order.
Unscheduled maintenance is that work necessary to replace or repair worn, unserviceable or damaged components.
Note:
Wadkin Limited offer a planned maintenance scheme - 'The Wadkin Service Club'.
Membership of this Club entitles the machine owner preferential rates on parts and labour. A copy of the Terms and Conditions of the Club, and an Application for
Membership Form is included in this Manual.
If machine maintenance is undertaken by the owner, it is recommended that maintenance procedures are carried out every 6 months or every 1000 hours of operation, whichever is the sooner.
Scheduled maintenance can normally be undertaken by a competent, but not necessarily specialised person (operator); unscheduled maintenance must be undertaken by an engineer experienced on this type of equipment and equipped with special tools.
3
4
5
6
1
2
Scheduled Maintenance
www.DaltonsWadkin.com
Equipment required:
Compressed air gun.
Standard tool kit.
Lubricants as detailed.
Grease gun.
Oil hand pump.
Replacement parts as necessary.
Page 7-1 www.DaltonsWadkin.com
[ u fl o o 7.2.1
[ o o
[i l~ o o o
[J o o o o o o
7.2.2 o www.DaltonsWadkin.com
www.DaltonsWadkin.com
Maintenance
Daily
WARNING:
ENSURE THAT THE MACHINE IS ELECTRICALLY AND PNEUMATICALLY
ISOLATED BEFORE UNDERTAKING ANY OF THE FOLLOWING TASKS.
LOCKABLE ELECTRICAL ISOLATORS ARE SUPPLIED WITH THIS MACHINERY TO
ALLOW STANDARD LOCK-OUT & TAG OUT PROCEDURES TO BE FOLLOWED
PRIOR TO UNDERTAKING ANY MAINTENANCE TASKS.
1 Clean the machine using a compressed air gun taking care not to direct the air jet directly on to spindles, shafts, bearing housings, etc.
Clean the spindles and cutter block collars and lightly lubricate with hydraulic oil
(see the lubrication chart at the end of this Section for oil types).
2
3
If a manual machine bed lubricating system is installed, operate the pump lever to lubricate the bed as is necessary. (The pump is located at the right-hand end, below the machine control panel).
Note:
The amount of lubrication and the frequency of application depends upon the type of wood being processed and speed of throughput. This requirement is based on experience and could well be necessary a number of times a day. A tap is fitted to the oil pump to preset the flow rate.
When it is necessary to replenish the oil reservoir use hydraulic oil.
Carry out a visual check of the machine and the surrounding area to check for any obvious signs of damage, wear, etc., and to ensure safe working conditions exist.
2
1
Monthly
If www.DaltonsWadkin.com
Apply hydraulic oil using a hand pump via the lubrication pOints on the front of the machine (see the lubrication chart at the end of this Section for oil types).
If the machine is manually lubricated:
Grease the machine slideways and handscrew mechanisms with lithium grease using a grease gun via the grease nipples on the front of the machine.
Grease spindle barrels, top head chipbreaker, pad pressures and feed roll shafts.
Grease Universal Head Rise & Fall, In & Out.
At the rear of the machine grease all rise & fall screws and slides & gib strips.
(See the lubrication chart at the end of this Section for grease types).
Page 7-2
[j
C
D
0
C
U
0
[J
J
0
0
0
0
0 lJ lJ
[: n o
7.2.3 www.DaltonsWadkin.com
Maintenance
Three-Monthly
1 Remove covers from all spindle drive belts (top, bottom, fence and side heads) and check the belt tension. (If re-tensioning is necessary, refer to Section 7.3).
2 Check the variable speed toothed drive belt for wear or cracking. (If replacement is necessary, refer to Section 7.3).
3 Remove the cowls from the electric drive motors and clean the motor fans; check for signs of overheating or excessive end-float of the motors. www.DaltonsWadkin.com
www.DaltonsWadkin.com
Page 7-3
[
[
7.3
[] o o
[] o o c c
[J o
-1
[
-, o
[J o o
[] o o
7.3.1 www.DaltonsWadkin.com
Maintenance
Unscheduled Maintenance
Unscheduled maintenance is that work necessary to replace or repair worn, unserviceable or damaged components.
Generally, following any procedure covered in this Section, a set-up procedure will need to be undertaken (see Section 5) before the machine is put into service.
This Section covers checks and replacement procedures in isolation. There will be times, depending upon the work to be undertaken, where many of these procedures will be carried out sequentially.
1
2
Equipment required:
3
Standard tool kit.
Hexagonal key.
Replacement parts as necessary.
WARNING:
ENSURE THAT THE MACHINE IS ELECTRICALLY AND PNEUMATICALLY
ISOLATED BEFORE UNDERTAKING ANY OF THE FOLLOWING TASKS.
ENSURE THAT PROPER PROTECTIVE CLOTHING IS USED THROUGHOUT THESE
TASKS.
LOCKABLE ELECTRICAL ISOLATORS ARE SUPPLIED WITH THIS MACHINERY TO
ALLOW STANDARD LOCK-OUT & TAG OUT PROCEDURES TO BE FOLLOWED
PRIOR TO UNDERTAKING ANY MAINTENANCE TASKS.
Re-tension Top/Bottom Head Drive Belt (Figure 7.3.1)
~
Figure 7.3.1 www.DaltonsWadkin.com
[]
Page 7-4
[
[
[
[
[ o o o c c o o
[J
[J
J n o
7.3.2
[
D c o
7.3.3
1
2
3
4
5
6
7
8 www.DaltonsWadkin.com
Remove the drive cover.
Slacken the four flange nuts (1).
Fit the screw block (2) using the drive cover mounting holes as the fixing position.
Screw in the tensioning bolt (3) until the bottom of the bolt just touches the motor flange.
Measure the distance between the bottom of the tensioning bolt head and the screw block. Screw in the tensioning bolt until the measured distance decreases by 9.5mm. (This applies the required tension on the belt).
Tighten the four flange nuts (1).
Slacken the tensioning bolt and remove the screw block.
Refit the drive cover. www.DaltonsWadkin.com
Maintenance
6
7
8
3
4
1
2
Re-tension Fence/Side Head Drive Belt (Figure 7.3.1)
Remove the drive cover.
Slacken the four flange nuts (1). Ease the motor away from the spindle.
Fit the screw block (2) using the drive cover mounting holes as the fixing position.
Screw in the tensioning bolt (3) until the bottom of the bolt just touches the motor flange.
5 Measure the distance between the bottom of the tensioning bolt head and the screw block. Screw in the tensioning bolt until the measured distance decreases by 9.5mm. Ease the motor towards the spindle by the required amount to apply the required tension on the bell. www.DaltonsWadkin.com
Slacken the tensioning bolt and remove the screw block.
Refit the drive cover.
Replace Spindle Drive Belt (Figure 7.3.3)
1
2
Remove the drive cover.
Slacken the four flange nuts (1).
3 Obtain assistance and lift the motor to release belt tension. Tighten the four flange nuts.
Page 7-5
[
[
C
L
[
0
LJ n
C
C
0
0
[J
[
0
[
C
C
C
[
[
7.3.4
4 www.DaltonsWadkin.com
Check that the barrellocknut (4) is tight.
QJ
~
Maintenance
Remove the two axial bolts (2).
Figure 7.3.3
5
6
7
Release the two banjo barrel clamp nuts (3).
Slide the banjo and motor away from the spindle sufficiently to allow the belt to be removed and replaced with a suitable belt.
Slide the banjo and motor towards the axial nut block and tighten nuts (3). 8
9
10 Tension the belt as described in Section 7.3.1.
2
3
Replace Variable Speed Drive Belt (Figure 7.3.4)
Note:
Before beginning this task ensure that the speed hand adjustment unit is set for maximum speed.
1 Remove the four capscrews (1) from the speed adjustment unit and remove the unit.
Support the gearbox, and remove the screws and nuts (2) from the housing.
Separate the housing to expose the belt.
Page 7-6 www.DaltonsWadkin.com
~
~
[
[ c
[J c c
C
0
C
0
[} c
0
0
[l
0 c
0
7.3.5
0
C
-~---~--------~-
4
5
6
7 www.DaltonsWadkin.com
Remove the belt from the pulleys.
Refit the replacement belt by first placing the belt over the upper pulley (3) and then over the rim of the lower pulley (4).
Reassemble the housing and refit and tighten screws and nuts (2).
Refit the speed adjustment unit and refit and tighten capscrews (1).
~
~ www.DaltonsWadkin.com
~D
~ry=" ~
Replace Shaft-Mounted Top Feed Roll (Figure 7.3.5)
1 Slacken set screw (1 ).
2 Ensure that the shaft is clean and withdraw the feed roll.
3 Replace the feed roll ensuring that the shaft key is correctly located.
4 Position the feed roll to suit the product width and tighten set screw (1).
Maintenance
Page 7-7
C
[
[J
C
7.3.6
0
[]
[J
-!
0
[
[
C
[J
0
[
[
[
['
[
0 c
1
2 www.DaltonsWadkin.com
Figure 7.3.5
Replace Flange-Mounted Top Feed RolIs/Spacers (Figure 7.3.6)
1
2
Slacken the draw bolt (1). remove the 'C' washer (2) and withdraw the bolt.
Dismantle spacers and feed rolls from the draw bolt.
3
4
5
Fit new spacers and feed rolls over the draw bolt engaging drive pins of spacers and feed rolls into opposite holes.
The combination of feed rolls and spacers will depend upon the product width.
Hold the assembly against the drive flange and screw in draw bolt until close to the face of the end feed roll.
Slot the 'C' washer (2) over the draw bolt (1) and tighten the draw bolt. www.DaltonsWadkin.com
1
Maintenance
Page 7·8
[
[
[
[
[
[
D
[J
0
L
0
D
0 c
0
[ c
0
C
[
7.3.7 www.DaltonsWadkin.com
Maintenance
4
5
2
3
Replace BottomlTop Head Spindle (Figure 7.3.71
Note:
Before beginning this procedure ensure that the working area is clean and that the area around the exposed spindle barrel is free of resin.
If
it is necessary to use a liquid remover to remove any resin, this must be used sparingly and care must be taken to ensure that no remover is allowed to enter the spindle end cap.
1 Remove the cutter block from the spindle (see Section 5.1.2).
6
Remove the drive belt (see Section 7.3.3).
Ensure that the barrel locknut (1) is tight.
Slacken further the two banjo barrel clamp nuts (2).
Obtain assistance and 'swing' the banjo and motor away from the spindle until they are almost free from the end of the barrel. Take the weight of the banjo and motor and when free of the barrel lower carefully to the floor taking care not to damage the electrical cable.
Slacken locknut (1) and insert a wedge into the split.
7
8 www.DaltonsWadkin.com
o
Figure 7.3.7
Withdraw the spindle rearwards from its housing and place in a clean area. necessary, use a hydraulic oil spray to release the spindle from its housing.
If
Before fitting a new or refurbished spindle ensure that the spindle and clamp housings are clean. www.DaltonsWadkin.com
~
Page 7·9
[' i
,
0
0
0
0
~
0
0
C
[
[
D
[
[ c c
0
0
0 o
7.3.8 www.DaltonsWadkin.com
Maintenance
9 Smear the inside face of the spindle bore with hydraulic oil, and before inserting the spindle, spray the barrel with a graphite grease. (see the lubrication chart at the end of this Section for oil/grease types).
10 Locate the spindle and remove the wedge from the spindle housing and tighten locknut (1 ).
11 Refit the banjo and motor onto the spindle and remove the wedge from the banjo barrel; tighten the barrel clamp nuts (2).
12 Ensure that the spindle rotates freely.
13 Fit the drive belt (see Section 7.3.3) and tension (see Section 7.3.1).
14 Fit the cutter block (see Section 5.1.2).
1
2
Replace Fence/Near Side Head Spindle (Figure 7.3.8)
Note:
Before beginning this procedure ensure that the working area is clean and that the area
around the exposed spindle barrel is free of resin. If it is necessary to use a liquid remover to remove any resin, this must be used sparingly and care must be taken to ensure that no remover is allowed to enter the spindle end cap.
Remove the cutter block from the spindle (see Section 5.1.2).
Remove the drive belt (see Section 7.3.3).
3
Figure 7.3.8
Wind up the spindle to its highest position (following the procedure in Section 5.3 or 5.4 depending upon the head spindle being replaced), and ensure that the locking handle and clamp are fully locked.
Page 7-10 www.DaltonsWadkin.com
[
[
[
[
[
[
[ o o o c o o o o o o c o c www.DaltonsWadkin.com
Maintenance
4
5
8
9
6
7
Release the two banjo barrel clamp nuts (1) and insert a wedge into the split.
Provide support beneath the banjo and motor and obtain assistance for the following Steps of the procedure.
Wind the banjo and motor down as far as possible without the banjo and motor fouling the support. (This action leaves the spindle in place while drawing the banjo and motor from the barrel).
Repeat the procedure of winding down the banjo and motor (steps 3, 4 and 6) until they are clear of the barrel.
Release the spindle locking handle and clamp.
Withdraw the spindle upwards from its housing and place in a clean area. If necessary, use a hydraulic oil spray to release the spindle from its housing.
10
11
Before fitting a new or refurbished spindle ensure that the spindle and clamp housings are clean.
Smear the inside face of the spindle bore with hydraulic oil, and before inserting the spindle, spray the barrel with a graphite grease. (see the lubrication chart at the end of this Section for oil/grease types).
12
13
Locate the spindle and tighten the spindle locking handle and clamp.
Refit the banjo and motor onto the spindle and remove the wedge from the banjo barrel; tighten the barrel clamp nuts (1).
14 Ensure that the spindle rotates freely.
15 Fit the drive belt (see Section 7.3.3) and tension (see Section 7.3.1).
16 Fit the cutter block (see Section 5.1.2). www.DaltonsWadkin.com
Page 7-11 www.DaltonsWadkin.com
[
[
[
7.4
7.4.1
[
D o o
D o o o o o o o o o
7.4.2
C
D
[ www.DaltonsWadkin.com
Maintenance
Fault Finding
General
Many of the faults occurring on woodworking machinery, apart from those caused by electrical or major mechanical failure, can be attributed to incorrect setting-up of the machine. Badly-tensioned drive belts, incorrectly set cutter blocks and loose components are frequent causes of irritating, often minor, faults.
When a fault occurs, unless the cause is because of a major mechanical or electrical failure or an operator error, it is recommended that the machine set-up is reviewed before any other investigative work is undertaken.
Workpiece Faults
Listed below are problems identified on the product after processing, with an indication of the diagnosis and remedy.
FAULT - Blips at leading end of underside of product
Diagnosis/Remedy
Cutter block set too low in relation to bedplate - Adjust cutter block.
FAULT - Blips on trailing end of underside of product
Diagnosis/Remedy
Cutter block set too high in relation to bedplate - Adjust cutter block.
FAULT - Trailing end of product top face shows blips
Diagnosis/Remedy
Pad and roller pressures are set incorrectly - Adjust pressures. www.DaltonsWadkin.com
FAULT - Out of square product
Diagnosis/Remedy
Cutter block cutters not set parallel to bed plate or badly ground - Inspect/adjust cutter block.
FAULT - Burn marks on product
Diagnosis/Remedy
Cutter block cutters blunt - Inspect/tegrind.
Timber stationary in machine - Remove timber. www.DaltonsWadkin.com
Page 7-12
[
[j
~
[ lJ
[I
0
0
0
C
0
0
0
0
0
0
0
0
0
0
7.4.3 www.DaltonsWadkin.com
FAULT - A spindle motor or feed motor does not start
Diagnosis/Remedy
Circuit breaker out - Reset circuit breaker.
Motor fuse blown - Check fuse and replace.
Motor contactor failed - Check contactor for pitted contacts or mechanical failure.
Open circuit in motor line leads - Check circuit and correct.
If fuse or circuit breaker fault re-occurs, investigate for cause on the motor.
FAULT - Motor contactor makes noise on closing
Diagnosis/Remedy www.DaltonsWadkin.com
FAULT - After a motor has started, circuit breaker trips or a motor fuse blows
Diagnosis/Remedy
Motor/spindle seized on bearings _ Check and replace.
Failure in circuit to motor (line lead earthed or short circuit) - Check with resistance and continuity meter. www.DaltonsWadkin.com
Maintenance
Machine Faults
Detailed below is a number of fault conditions with associated diagnoses and the recommended remedial action. The diagnoses should be considered only advisory; a proper determination of any fault is more likely to be ascertained by the competent engineer called to rectify the problem.
Note that obvious operator errors (switches not closed, enclosure open, etc.) are not listed in the diagnoses below.
FAULT- None of the spindle drives nor the feed drive operates when the Start buttons are pressed
Diagnosis/Remedy
Circuit breaker out - Reset circuit breaker.
Main fuse or coptrol fuse blown - Check fuses and replace.
If either fault re-occurs, investigate for cause on the machine.
Page 7-13
[
[1
.J o o o o o o
C
[~ o o o o
0.
1
!
D o o fJ o www.DaltonsWadkin.com
Maintenance
FAULT - Motor overheats while running unloaded
Diagnosis/Remedy
Supply voltage too high Check supply voltage with meter.
Motor windings incorrectly connected - Check for correct starting/running connections.
Motor air ducts blocked impeding flow of cooling air - Clear ducts.
FAULT - Motor overheats while running loaded
Diagnosis/Remedy
Establish if mechanical problem - Check spindle for seizure/incorrect setting.
Single phase operation in motor line leads - Check circuit and correct.
FAULT - Motor noisy when running
Diagnosis/Remedy
Establish if mechanical or electrical problem - If mechanical, noise will change in intensity/frequency with change in motor speed; if electrical, noise will continue after motor has stopped. Carry out appropriate investigation.
FAULT - Spindle stops while motor is still running
Diagnosis/Remedy
Slipping or broken belt - Check and retighten or replace.
FAULT - Motor contactor remains closed after operation of Stop button
Diagnosis/Remedy
Contactor contacts have 'welded' together - Replace contacts. www.DaltonsWadkin.com
Page 7-14 www.DaltonsWadkin.com
[
[
,
~,
[J o o o o c
[
[
[~ c
7.5
7.5.1
[} c
7.5.2
D
[} o
Cl
[J o www.DaltonsWadkin.com
Lubrication Chart
Lubricants specified
Hydraulic oil with anti-corrosion, anti-oxidation and anti-foam qualities.
Grease - Lithium bearing grease with NLG1 NO.3 consistency.
Approved Lubricants
Hydraulic Oil
Gastrol Hyspin
AWS32
Grease
Gastrol Spheerol
AP3
BP Energol HLP32 Energrease LS3
Shell Tellus 32 Shell Alvania grease R3
Mobil DTE light 24 Mobilplex48
Esso Nuto
44/ESSTIG H44
Esso Beacon 3
Gulf Harmony
32AW
Gulf Grown NO.3
Elf Elfona 32 Elf Multi 3 grease www.DaltonsWadkin.com
www.DaltonsWadkin.com
Maintenance
Page 7-15
[
[
[
[J
0
0
0
0 c
0
0
[
0 c
C
C
C
C
[l
7.6
D www.DaltonsWadkin.com
Maintenance
Tool and Toolholder Care
When selecting tools, care must be taken to ensure that they are suitable for
6000rev/min oPeration (dynamically balanced and tested for cracks).
The life of the tool depends upon the quality of the steel used in its manufacture and the type of wood being machined.
When resharpening, care should be taken to ensure that the blade is not unduly heated by using the correct type of grinding wheel, coolant, chip removal process, etc.
Moreover, with multi-toothed tools, the correct tooth pitch is important to ensure effective cutting.
Whether a tool is effective depends much on how it is used. Careful handling will ensure longer service life and improved product quality.
Tooling should comply with the Tooling Standard PREN 847-1: 1997. www.DaltonsWadkin.com
Page 7-16 www.DaltonsWadkin.com
[
[
[
[
[ c
[ c c c
[ c c c c
-~ n c o o o
8.1
8.1.1 www.DaltonsWadkin.com
Additional Equipment
8 ADDITIONAL EQUIPMENT APPENDICES
This Section covers the additional equipment which can be added to the Model GD but which does not form part of the basic machine described in the previous Sections of this
Operation and Maintenance Manual.
Each Section gives a brief description of the equipment features, its purpose and any setting-up procedures necessary to integrate it into the machine operation.
All preparation and safety procedures detailed in the setting-up procedures given in
Section 5 must also be complied with when carrying out the procedures given in this
Section.
Universal Head (Figures 8.1.3 to 8.1.7)
The universal head is normally fitted to the machine at the time of ordering.
When fitted, it can be used in four pOSitions and for angled work in the range shown below.
Bottom head position: horizontal and between +15° and -90°.
Fence side head position: vertical and between +15° and -15°.
Near side head position:
Top head position: vertical and between +90° and -15°. horizontal and between +15° and -90°.
Equipment
The universal head equipment consists of the following: www.DaltonsWadkin.com
Two extraction hoods one for use in the bottom head position and a second for use in the fence, near side and top head positions.
Fence assembly allowing for conversion to suit all four positions.
Bedplates to convert to a solid bed for the fence, near side and top head positions and an open bed for the bottom head position.
Pressure rollers and a pad pressure shoe for use with the universal head.
0.5mm shim for use after the universal head. www.DaltonsWadkin.com
Page 8- 1
[
Q
8.1.2
C
[
-I
[
-"
[
6 o o c c o c o
8.1.3
[ c c c c c www.DaltonsWadkin.com
Reversing Switch
A reversing switch is fitted on the machine infeed end control panel which allows the direction of the universal head to be set according to the position of the head
WARNING:
THE DIRECTION OF ROTATION MUST BE CHECKED AFTER ANY CHANGE IN
POSITION OF THE UNIVERSAL HEAD.
When viewed from the front, the spindle rotates clockwise for the bottom and fence side
. positions, and counterclockwise for the near side and top head positions.
WARNING:
BECAUSE THE UNIVERSAL HEAD IS RUN IN BOTH CLOCKWISE AND
COUNTERCLOCKWISE DIRECTIONS, A LOCKING COLLAR MUST ALWAYS BE
FITTED.
Setting the Universal Head
Bottom Horizontal Head (Figures 8.1.3 and 8.1.7\
WARNING:
ENSURE THAT THE MACHINE IS ELECTRICALLY ISOLATED (EMERGENCY STOP
ACTIVATED) BEFORE PROCEEDING.
ENSURE THAT THE SPINDLE IS SET FOR CLOCKWISE ROTATION.
1 If necessary, remove the spindle dust cover and fit the bottom head extraction hood underneath the bedplate by locating the hood on the two studs underneath the table securing with the two 8mm nuts provided.
2 Fit the fence assembly components to provide a straight-through fence, fit the open bed and secure. www.DaltonsWadkin.com
Figure 8.1.3 www.DaltonsWadkin.com
Additional Equipment
Page 8- 2
[
[
[
[
[' c
[J
[ c o o o c
[ tJ
[
[J o o o www.DaltonsWadkin.com
Additional Equipment
Top Horizontal Head (Figures 8.1.4 and 8.1.7)
WARNING:
ACTIVATED) BEFORE PROCEEDING.
ENSURE THAT THE SPINDLE IS SET FOR COUNTERCLOCKWISE ROTATION.
1 If necessary, remove the spindle dust cover and fit the top head extraction hood above the bedplate securing with the bolts provided.
2
3
4
Fit the fence assembly components to provide a straight-through fence, fit the solid bed between the existing bed plate sections and secure with clamps located beneath the bed plate.
Fit the 0.5mm shim (if second bottom head is being used).
Fit the cutter block to the spindle (see Section 5.1.2).
Page 8- 3 www.DaltonsWadkin.com
II o
Q
[ c c c c c c
[
[ r
"'
.~ c c c
[] c lJ
J
[ '
5 www.DaltonsWadkin.com
Additional Equipment
Release the two locking bolts (1) (Figure 8.1.7) and cant the spindle to the horizontal position using a crank handle on shaft (2).
6
7
8
9
Lock bolts (1).
Figure 8.1.4 www.DaltonsWadkin.com
Adjust the vertical and horizontal position of the cutter block in relation to the fence side and the bedplate respectively by adjusting shafts (3) and (4) with the crank handle.
If necessary, remove the fence insert (at the centre of the fence) to avoid possible contact with the cutter block.
Set-up the cutter block accurately by following, generally, the procedure given in
Section 5.5 (using only the manual procedure when making the vertical adjustment).
Page 8- 4 www.DaltonsWadkin.com
l
[
[
[
[
C'
~ ~
[ c
[; o c c u c c
C r:
L
[
U c www.DaltonsWadkin.com
Additional Equipment
10
11 Fit the side guide to suit the timber width.
Caution:
When undertaking the following procedure ensure that the conditions stated in
Section 6.1.2 are followed with regard to passing a 'test piece' through the machine.
12
13
Fit the pressure rollers before after the cutter block to provide timber control when operating the machine. Details of setting the top roller pressure are given in
Section 5.8.
Pass a 'test piece' timber through the machine to check for dimensional accuracy.
Reset the pressure rollers and side guide if necessary.
Near Side Vertical Head (Figures 8.1.5 and 8.1.7)
WARNING:
ENSURE THAT THE MACHINE IS ELECTRICALLY ISOLATED (EMERGENCY STOP
ACTIVATED) BEFORE PROCEEDING.
3
4
5
7
ENSURE THAT THE SPINDLE IS SET FOR CLOCKWISE ROTATION (LOOKING
FROM ABOVE).
1
2
If necessary, remove the spindle dust cover and fit the near side head extraction hood securing with the bolts provided, and fit the fence assembly components to provide a straight-through fence. Fit the solid bed between the existing bedplate sections and secure with clamps located beneath the bed plate.
Release the two locking bolts (1) (Figure 8.1.7) and cant the spindle to the vertical position using a crank handle on shaft (2).
Lock bolts (1 )
If necessary, slide the solid bed underneath the fence to suit the width of timber.
Adjust the vertical and horizontal position of the cutter block in relation to the timber size by adjusting shafts (3) and (4) with the crank handle.
7
8
9
Set-up the cutter block accurately by following, generally, the procedure given in
Section 5.4.
Fit the pressure rollers before after the cutter block to provide timber control when operating the machine. Details of setting the top roller pressure are given in
Section 5.8.
Fit the side guide to suit the timber width.
Page 8- 5 www.DaltonsWadkin.com
[
[
[
['
[J
L~
[
[J c c
[
[] c
[ c
C
[
[
[
C www.DaltonsWadkin.com
Additional Equipment
Figure 8.1.5
Caution:
When undertaking the following procedure ensure that the conditions stated in
Section 6.1.2 are followed with regard to passing a 'test piece' through the machine.
10 Pass a 'test piece' timber through the machine to check for dimensional accuracy.
11 Reset the pressure rollers and side guide if necessary.
WARNING:
ENSURE THAT THE MACHINE IS ELECTRICALLY ISOLATED (EMERGENCY STOP
ACTIVATED) BEFORE PROCEEDING.
ENSURE THAT THE SPINDLE IS SET FOR COUNTERCLOCKWISE ROTATION.
1
2
If necessary, remove the spindle dust cover and fit the fence side head extraction hood securing with the bolts provided. Remove the fence section and replace with two nose piece sections.
Fit the solid bed between the existing bedplate sections and secure with clamps located beneath the bed plate.
Page 8· 6 www.DaltonsWadkin.com
Lj iJ
[
C u r c
L
[
[
D n
I'
,~-
[
[ o
[
[
[
[
[
[ www.DaltonsWadkin.com
Additional Equipment
3
4
5
6
7
Figure 8.1.6
Release the two locking bolts (1) (Figure 8.1.7) and cant the spindle to the vertical position using a crank handle on shaft (2).
Lock bolts (1)
Fit the cutter block to the spindle (see Section 5.1.2).
Adjust the vertical and horizontal position of the cutter block in relation to the fence side by adjusting shafts (3) and (4) with the crank handle www.DaltonsWadkin.com
Section 5.3.
8 Fit the pressure rollers before after the cutter block to provide timber control when operating the machine. Details of setting the top roller pressure are given in
Section 5.8,
9 Fit the side guide to suit the timber width.
Caution:
When undertaking the following procedure ensure that the conditions stated in
Section 6.1.2 are followed with regard to passing a 'test piece' through the machine.
Page 8-7 www.DaltonsWadkin.com
[
1] r
~
L
G
C
C
[l
[
[
[
[
[
[
[l o
[ c
C
-' •
[~ www.DaltonsWadkin.com
Additional Equipment
10
11
Pass a 'test piece' timber through the machine to check for dimensional accuracy.
Reset the pressure rollers and side guide if necessary.
1
2
3 www.DaltonsWadkin.com
4
Figure 8.1.7 www.DaltonsWadkin.com
1
Page 8- 8
C
[
C c
"-' n c
D
L
[
[
0
.'
[
[
[
[ r
8.2
[ c
C fl,
~ www.DaltonsWadkin.com
Additional Equipment
Grooved Bed (Figure 8.2)
Typically used in furniture making, processing short lengths of twisted timber, this equipment comprises a cutter block (used in the first bottom head position) and a grooved bed which extends to the second bottom head position.
Two spur cutters located an exact distance from the fence side edge of the bed, cut a groove in the underside of timber. This (master) groove locates in the groove nearest the fence side of the grooved bed plate to provide exact location of the timber as it feeds through the machine.
Note:
In this mode of operation the fence through the machine has no timber location function.
When setting-up the fence side head (see Section 5.3) with a grooved bed fitted, locate the cutting edge of the cutter block approximately O.2mm in front of the fence. r~-';::7/:~?/ . -" ~:: ::~::~;~~,."_,oo.:':>:o
!;;/~: .~. -7>~ ~;T>
// 1--1 ' i-I - _
. !....._l~
... -; ,
I i I , ' ,
'--~- ~-~
~'_~i~1
L .::.... __
~:::....j
,---, ,---, ,---,
,---,J
T--
Figure 8.2 www.DaltonsWadkin.com
ur w
2
~
W
~
W
"
Page 8- 9
0
[j
[]
C
C
C
[
L
[
[
C
C c r c
[
[
[ r--·
L
[
8.2.1 www.DaltonsWadkin.com
www.DaltonsWadkin.com
Additional Equipment
3
4
Setting-up the Cutter Block
1 Fit the cutter block (see Section 5.1.2) and set the edge of the first spur cutter exactly in line with the inside edge of the master groove of the grooved bed (this acts as the machine fence).
2 Shim the cutter block and fit the second spur cutter 12mm from the first cutter.
Fit the second cutter block.
Set the vertical position of the cutter block (see Section 5.3) taking into account that the first spur cutter must align with the inside edge of the master groove and that the planing cutter tips are level with the top of the grooved bed.
Align the tips of the grooving cutters with the top surface of the grooved bed.
Page 8- 10 www.DaltonsWadkin.com
r
L www.DaltonsWadkin.com
Additional Equipment
[}
[
[
C
[
0
[
D
[J
C
L r~'
L
[
[
[
C
[
8.3
[
C
---~---~--
-------- - - - -
Intermediate Feed Roll (Figure 8.3)
The intermediate feed roll is fitted to facilitate the feeding of short lengths of timber through the machine. The unit replaces the second shaft-mounted feed roll at the fence side head position.
The unit consists of a mounting bracket (1), pneumatic cylinder (2) and mounting plate
(3) for two shaft-mounted feed rolls.
The intermediate feed roll is set up by the beam control setting procedure.
QJ www.DaltonsWadkin.com
~ o
Page 8-11
D r
U
C
L
C
C
[
0 l
!~
'-'
C c
0
[
[
L
8.4
C
L f
C r~
Random Side Head (Figure 8.4)
The random side head is fitted to the near side head of the machine.
The purpose of this unit is to randomly plane timber to a width. Positioning is achieved automatically with· a fast motor directly driving the near side head radial winding screw.
The system enables various widths of timber to be fed into the machine one after another to finish plane them. When operating under the random side head mode, the timber is not planed to a known width. The permits only a 'known amount' to be planed from the side of each piece of timber.
The unit consists of a large pneumatically-loaded cam (1) fitted with three switches (2).
As the timber is fed into the machine, the cam is pushed back, contacting the first switch. If the timber is wider than the immediately preceding piece of timber, the first two switches are 'made'. This drives the head out until the switches are 'clear'. The head positions inwards until the first switch is made.
If the timber is over 100mm wider than the previous piece, the third switch is contacted sending the head out to its maximum safe position. When this happens, all of the switches are 'clear'; the cam then moves forward to touch the side of the timber and then drive the head in, until it contacts the first switch.
The random side head can also be used as a normal near side head with the random side head switched off. In this mode, the head is set in the usual way (see Section 5.4).
~ www.DaltonsWadkin.com
D
D www.DaltonsWadkin.com
Additional Equipment
Figure 8.4
Setting and Operation
1 Set the random side head on/off switch on the machine control panel to on.
Page 8-12 www.DaltonsWadkin.com
[2J o
~
C
[
[
[
[ r c c o c
[
[ c n
~ r
L
r··
L r
L
"-. r
<~ r
[
2
3
4
5
6 www.DaltonsWadkin.com
Additional Equipment
Set the automatic random side head switch on the machine control panel to automatic
Set the top roller pressure (3) as detailed in Section 5.8 but position it slightly in front of the spindle centre line. This roller pressure carries a switch (4) which senses that timber is in the machine.
The random side head may be set as a unit in relation to the cutting circle of cutter block being used.
Slacken bolts (5) and adjust the position of the cam - this achieved in a similar manner to setting-up a side roller assembly (see Section 5.8).
Set the cam operating pressure with the regulator/gauge (6) to between 1 and 2 bar.
The 'feed' lamp on the machine control panel must be illuminated before a piece of timber is feed into the machine.
Capacities
Maximum feed speed
Max cut on any piece of timber
Maximum finished width
Maximum timber width variation
Maximum timber height
Minimum timber length
Minimum timber width
15m/min
15mm
220mm
100mm
100mm
400mm
50mm www.DaltonsWadkin.com
Page 8· 13 www.DaltonsWadkin.com
C o o o o c u r c
L n e c c c c
L
[ c c c
L www.DaltonsWadkin.com
GLOSSARY
www.DaltonsWadkin.com
Glossary
Below is a Glossary of terms used in this manual specific to the equipment being described. Other documents which should be referred to are listed in Section 1.1.6.
Bed
Blips
Chipbreaker
Cutter block
Machine level on which timber travels during· machining.
Marks on planed timber indicating fault in processing.
Tool which provides pressure to hold the timber on to the machine bed; it also prevents the breaking of wood chips.
Cutting tool(s) mounted on a spindle of the machine.
Datum block dB
Drive belt
Feed rolls
Feed speed
Block of timber of known height/width used as tool to datum machine settings.
Decibel of noise (measurement of noise level).
Flat, 'V' or toothed belt which drives the spindles from the drive shaft.
Rotating rolls which move the timber through the machine while exerting necessary pressure to enable proper processing.
Speed at which timber is passed through the machine.
First bottom head
First top head
Infeed
Planing process on the right-hand side of the timber
(when viewed from the infeed end of the machine).
First process on the machine; planes the bottom face of the timber.
Planing process on the top of the timber.
End of machine where timber is introduced.
Page 1
[
[
[
C
C
L r
[ r
L o o o c o
[
[ n
~ c
[
[ c
Near side head
Outfeed
Spindle
Spindle backlash
Test piece www.DaltonsWadkin.com
Glossary
Planing process on the left-hand side of the timber
(when viewed from the infeed end of the machine).
End of machine where finished product is produced.
Rotating shaft carrying the cutter block.
Natural movement of rotating cutter block towards/away from workpiece depending upon direction of rotation.
Timber on which setting-up processes are conducted. www.DaltonsWadkin.com
Page 2 www.DaltonsWadkin.com
advertisement
Related manuals
advertisement