advertisement
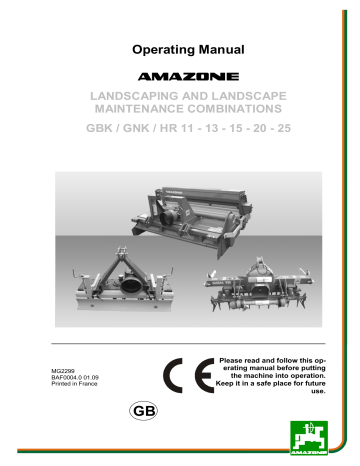
Operating Manual
az
LANDSCAPING AND LANDSCAPE
MAINTENANCE COMBINATIONS
GBK / GNK / HR 11 - 13 - 15 - 20 - 25
MG2299
BAF0004.0 01.09
Printed in France
GB
Please read and follow this operating manual before putting the machine into operation.
Keep it in a safe place for future use.
2
READING THE INSTRUCTION
manual and adhering to it should not appear to be inconvenient and superfluous as it is not enough to hear from others and to realise that a machine is good, to buy it and to believe that now everything should work by itself. The person concerned would not only harm himself but also make the mistake of blaming the machine for the reason of a possible failure instead of himself. In order to ensure good success one should go into the mind of a thing, make himself familiar with every part of the machine and to get acquainted with its handling. Only in this way would you be satisfied both with the machine as also with yourself. To achieve this is the purpose of this instruction manual.
Leipzig-Plagwitz 1872.
GBK / GNK / HR BAF0004.0 01.09
Identification data
Identification data
Enter the machine identification data here. You will find the identification data on the rating plate.
Soil tillage implement
Machine identification number:
(ten-digit)
Type:
Year of manufacture:
Basic weight (kg):
Permissible total weight
(kg):
Maximum load (kg):
Seed box
Machine identification number:
(ten-digit)
Type:
Year of manufacture:
Basic weight (kg):
Permissible total weight
(kg):
Maximum load (kg):
GBK / GNK / HR
Manufacturer's address
AMAZONE S.A. FORBACH
17, rue de la Verrerie
BP 90106
F-57602
Phone:
Fax:
E-mail:
Forbach, France
+33 (0) 3 87 84 65 70
+33 (0) 3 87 84 65 71 [email protected]
Spare part orders
AMAZONEN-WERKE
H. DREYER GmbH & Co. KG
Postfach 51
DE-49202 Hasbergen
Phone:
Fax:
E-mail:
+ 49 (0) 5405 501-290
+ 49 (0) 5405 501-106 [email protected]
Online spare parts catalogue: et.amazone.de
When ordering spare parts, always specify the (ten-digit) machine identification number.
Formalities of the operating manual
Document number:
Compilation date:
MG2299
01.09
GBK / GNK / HR BAF0004.0 01.09
3
Foreword
Foreword
Operator evaluation
ã
Copyright AMAZONEN-WERKE H. DREYER GmbH & Co. KG, 2008
All rights reserved.
Reprinting, even of sections, permitted only with the approval of A-
MAZONEN-WERKE H. DREYER GmbH & Co. KG.
Dear Customer,
You have chosen one of the quality products from the wide product range of AMAZONEN-WERKE, H. DREYER GmbH & Co. KG. We thank you for your confidence in our products.
On receiving the machine, check to see if it was damaged during transport or if parts are missing. Using the delivery note, check that the machine was delivered in full, including the ordered special optional equipment. Replacement will be made only if a claim is filed immediately.
Please read and follow this operating manual — in particular, the safety instructions — before putting the machine into operation. Only after careful reading will you be able to benefit from the full scope of your newly purchased machine.
Please ensure that all the machine operators have read this operating manual before they put the machine into operation.
Should you have problems or queries, please consult this operating manual or give us a call.
Regular maintenance and timely replacement of worn or damaged parts increases the lifespan of your machine.
Dear Reader
We update our operating manuals regularly. Your suggestions for improvement help us to create ever more user-friendly manuals.
Please send your suggestions to:
AMAZONE S.A. FORBACH
17, rue de la Verrerie
BP 90106
F-57602 Forbach, France
Phone:
Fax:
E-mail:
+33 (0) 3 87 84 65 70
+33 (0) 3 87 84 65 71 [email protected]
4
GBK / GNK / HR BAF0004.0 01.09
1
1.1
1.2
1.3
Table of Contents
Operator information .................................................................................. 8
Purpose of the document.................................................................................................... 8
Locations in the operating manual ...................................................................................... 8
Diagrams used ................................................................................................................... 8
2 General safety instructions ........................................................................ 9
2.1
2.2
2.3
2.4
2.5
2.6
2.7
Obligations and liability ....................................................................................................... 9
Representation of safety symbols ..................................................................................... 11
Organisational measures .................................................................................................. 12
Safety and protection equipment....................................................................................... 12
Informal safety measures.................................................................................................. 12
Operator training .............................................................................................................. 13
Safety measures in normal operation................................................................................ 14
2.8
2.9
Danger from residual energy............................................................................................. 14
Maintenance and repair work, fault elimination.................................................................. 14
2.10
Structural changes............................................................................................................ 14
2.11.
Spare and wear parts and auxiliary materials.................................................................... 15
2.12
Cleaning and disposal ...................................................................................................... 15
2.13
Operator workstation ........................................................................................................ 15
2.14
Warning symbols and other labels on the machine............................................................ 15
2.14.1
Positioning of warning symbols and other labels ............................................................... 21
2.15
Dangers if the safety information is not observed.............................................................. 26
2.16
Safety-conscious working ................................................................................................. 26
2.17
Safety information for the operator.................................................................................... 27
2.17.1
General safety and accident prevention information.......................................................... 27
4
4.1
4.2
4.3
3
3.1
3.2
3.3
General safety and accident prevention information............................. 30
Attached equipment.......................................................................................................... 31
PTO shaft operation ......................................................................................................... 32
General safety and accident prevention regulations for maintenance, servicing and care .. 33
Machine data ............................................................................................. 34
Declaration of conformity .................................................................................................. 34
Details required for enquiries ............................................................................................ 34
Intended use .................................................................................................................... 34
5 Implements for soil tillage ........................................................................ 35
5.1
Reciprocating power harrow ............................................................................................. 35
5.1.1
Technical data – reciprocating power harrow (basic machine)........................................... 35
5.1.2
Technical data - tine bars.................................................................................................. 35
5.1.3
Installing and adjusting the reciprocating power harrow..................................................... 37
5.1.4
PTO shaft......................................................................................................................... 37
5.1.5
Attaching the PTO shaft.................................................................................................... 37
5.1.6
Adjusting the PTO shaft the first time the machine is coupled............................................ 38
5.1.7
Input speed for the reciprocating power harrow gearbox ................................................... 39
5.1.8
Maintenance..................................................................................................................... 39
5.2
Rotary harrow................................................................................................................... 41
5.2.1
Technical data - rotary harrow (basic machine)................................................................. 41
5.2.2
Attaching to the tractor...................................................................................................... 41
5.2.3
PTO shaft......................................................................................................................... 42
5.2.4
Attaching the PTO shaft.................................................................................................... 42
5.2.5
Adjusting the PTO shaft the first time the machine is coupled............................................ 42
5.2.6
Input speed for the rotary harrow ...................................................................................... 43
5.2.7
Lubrication........................................................................................................................ 43
5.2.8
Maintenance..................................................................................................................... 44
5.2.9
Replacing tines................................................................................................................. 44
5.3
Stone burier...................................................................................................................... 45
GBK / GNK / HR BAF0004.0 01.09
5
6
6.1
6.2
6.3
6.4
6.5
6.6
Table of Contents
5.3.1
Technical data - stone burier (basic machine)....................................................................45
5.3.2
Attaching to the tractor ......................................................................................................45
5.3.3
PTO shaft..........................................................................................................................45
5.3.4
Attaching the PTO shaft.....................................................................................................46
5.3.5
Adjusting the PTO shaft the first time the machine is coupled ............................................46
5.3.6
Input speed for the stone burier .........................................................................................46
Screen roller and smooth roller................................................................ 47
Technical data - screen roller.............................................................................................47
Technical data - smooth roller............................................................................................47
Scraper .............................................................................................................................47
Uncoupling the screen roller ..............................................................................................48
Water connection on smooth roller.....................................................................................49
Maintenance .....................................................................................................................50
7 Seed box..................................................................................................... 51
7.1
7.2
7.3
7.4
Technical data...................................................................................................................51
Fitting the seed box ...........................................................................................................51
Filling the seed box ...........................................................................................................52
Emptying the seed box ......................................................................................................53
7.5
Setting the sowing rate ......................................................................................................54
7.6
Tips on drilling in slow or fast gear.....................................................................................55
7.6.1
Adjusting the gearbox in fast mode....................................................................................56
7.7
7.8
7.9
Quantity table....................................................................................................................57
Calibration test ..................................................................................................................57
Maintenance .....................................................................................................................59
8
8.1
AMAZONE GBK combination seeding system........................................ 60
Fields of application...........................................................................................................60
8.2
GBK combination seeding system with reciprocating power harrow ...................................61
8.2.1
Setting the working depth ..................................................................................................61
8.2.2
Adjusting the lateral weeders.............................................................................................62
8.2.3
Adjusting the chute............................................................................................................63
8.2.4
Levelling blade ..................................................................................................................64
8.3
GBK combination seeding system with rotary harrow.........................................................65
8.3.1
Setting the working depth ..................................................................................................65
8.3.2
Adjusting the lateral weeders.............................................................................................65
8.4
GBK combination seeding system with stone burier...........................................................66
8.4.1
Commissioning..................................................................................................................66
8.4.2
Setting the working depth ..................................................................................................67
8.4.3
Driving...............................................................................................................................68
8.4.4
Stone burier operation.......................................................................................................68
9 AMAZONE GNK Overseeder..................................................................... 69
9.1
Fields of application...........................................................................................................69
9.2
Working with the overseeder .............................................................................................69
9.2.1
Adjusting the overseeding tine bars ...................................................................................69
9.2.2
Adjusting the chute............................................................................................................70
10 AMAZONE HR hard court reconditioner.................................................. 72
10.1
Technical data...................................................................................................................72
10.2
Fields of application...........................................................................................................72
10.3
Working with the hard court reconditioner ..........................................................................72
10.3.1
Regenerating hard courts ..................................................................................................72
10.3.2
Adjusting the reciprocating power harrow working depth....................................................72
10.3.3
Adjusting the lateral weeders.............................................................................................74
10.3.4
Adjusting the lateral brushes..............................................................................................75
10.3.5
Adjusting the rear brush.....................................................................................................76
6
GBK / GNK / HR BAF0004.0 01.09
Table of Contents
10.3.6
Use on heavily compacted sports courts ........................................................................... 77
10.3.7
Weekly maintenance of compacted soil ............................................................................ 77
10.3.8
Adjusting the front scarifier bar ......................................................................................... 77
10.3.9
Adjusting the rear brush.................................................................................................... 78
10.4
Care of sandy artificial turf ................................................................................................ 78
10.5
Adjusting the brush bars ................................................................................................... 78
GBK / GNK / HR BAF0004.0 01.09
7
Operator information
1 Operator information
The "Operator information" section supplies information on using the operating manual.
1.1
1.2
Purpose of the document
This operating manual
· Describes the operation and maintenance of the machine.
· Provides important information on safe and efficient handling of the machine.
· Is a component part of the machine and should always be kept with the machine or the traction vehicle.
· Keep it in a safe place for future use.
Locations in the operating manual
All the directions specified in the operating manual are always viewed in the direction of travel.
1.3 Diagrams used
Instructions for action and reactions
Tasks to be carried out by the operator are presented as numbered instructions. Always keep to the order of the instructions. The reaction to instructions is given by an arrow.
Example:
1. Instruction for action 1
→ Reaction of the machine to instruction for action 1
2. Instruction for action 2
Lists
Lists without a mandatory sequence are presented as a list with bullet points.
Example:
· Point 1
· Point 2
Item numbers in diagrams
Numbers in round brackets refer to the item numbers in the diagrams.
The first digit refers to the diagram, the second digit to the item number in the illustration.
Example (Fig. 3/6)
· Figure 3
· Item 6
8
GBK / GNK / HR BAF0004.0 01.09
2 General safety instructions
General safety instructions
This section contains important information on the safe operation of the machine.
2.1 Obligations and liability
Comply with the instructions in the operating manual
Knowledge of the basic safety information and safety regulations is a basic requirement for safe handling and fault-free machine operation.
Obligations of the operator
The operator is obliged only to let those people work with/on the machine who
· Are aware of the basic workplace safety information and accident prevention regulations.
· Have been trained in working with/on the machine.
· Have read and understood this operating manual.
The operator is obliged
· To keep all the warning symbols on the machine in a legible state.
· To replace damaged warning symbols.
If you still have queries, please contact the manufacturer.
Obligations of the operator
Before starting work, anyone charged with working with/on the machine is obliged
· To comply with the basic workplace safety instructions and accident prevention regulations.
· To read and understand the section "General safety information" of this operating manual.
· To read the section "Warning symbols and other labels on the machine" (page 16) of this operating manual and to follow the safety instructions represented by the warning symbols when operating the machine.
· To get to know the machine.
· To read the sections of this operating manual important for carrying out your work.
If the operator discovers that a function is not working properly, they must eliminate this fault immediately. If this is not the task of the operator or if the operator does not possess the appropriate technical knowledge, they should report this fault to their superior (operator).
GBK / GNK / HR BAF0004.0 01.09
9
General safety instructions
Risks in handling the machine
The machine has been constructed to the state-of-the art and the recognised rules of safety. However, there may be risks and restrictions which occur when operating the machine
· For the health and safety of the operator or third persons,
· For the machine,
· For other goods.
Only use the machine
· for the purpose for which it was intended.
· when it is in a perfect state of repair.
Eliminate any faults that could impair safety immediately.
Guarantee and liability
Our "General conditions of sales and business" are always applicable.
These shall be available to the operator at the latest on the completion of the contract. Guarantee and liability claims for damage to people or goods will be excluded if they can be traced back to one or more of the following causes:
· Improper use of the machine.
· Improper installation, commissioning, operation and maintenance of the machine.
· Operation of the machine with defective safety equipment or improperly attached or non-functioning safety equipment.
· Non-compliance with the instructions in the operating manual regarding commissioning, operation and maintenance.
· Unauthorised structural changes to the machine.
· Insufficient monitoring of machine parts that are subject to wear.
· Improperly executed repairs.
· Catastrophic events as a result of the impact of foreign objects or force majeure.
10
GBK / GNK / HR BAF0004.0 01.09
2.2 Representation of safety symbols
General safety instructions
Safety instructions are indicated by the triangular safety symbol and the highlighted signal word. The signal word (DANGER, WARNING,
CAUTION) describes the gravity of the risk and has the following significance:
DANGER
Indicates an immediate high risk, which will result in death or extremely serious physical injury (loss of body parts or long term damage) if not avoided.
If the instructions are not followed, this will result in immediate death or serious physical injury.
WARNING
Indicates a medium risk which could result in death or (extremely serious) physical injury if not avoided.
If the instructions are not followed, this may result in death or serious physical injury.
CAUTION
Indicates a low risk, which could incur minor or medium level physical injury or damage to property if not avoided.
IMPORTANT
Indicates an obligation to special behaviour or an activity required for proper machine handling.
Non-compliance with these instructions can cause faults on the machine or in the environment.
NOTE
Indicates handling tips and particularly useful information.
These instructions will help you to use all the functions of your machine to the optimum.
GBK / GNK / HR BAF0004.0 01.09
11
General safety instructions
2.3 Organisational measures
The operator must provide the necessary personal protective equipment, such as:
· Protective glasses
· Protective shoes
· Protective suit
· Skin protection, etc.
The operating manual
· Must always be kept at the place at which the machine is operated.
· Must always be easily accessible for the operator and maintenance personnel.
Check all the available safety equipment regularly.
2.4 Safety and protection equipment
Before each commissioning of the machine, all the safety and protection equipment must be properly attached and fully functional. Check all the safety and protection equipment regularly.
Faulty safety equipment
Faulty or disassembled safety and protection equipment can lead to dangerous situations.
2.5 Informal safety measures
As well as all the safety information in this operating manual, comply with the general, national regulations pertaining to accident prevention and environmental protection.
When driving on public roads and routes, you should comply with the statutory road traffic regulations.
12
GBK / GNK / HR BAF0004.0 01.09
2.6 Operator training
General safety instructions
Only those people who have been trained and instructed may work with/on the machine. The operator must clearly specify the responsibilities of the people charged with operation, maintenance and repair work.
People being trained may only work with/on the machine under the supervision of an experienced person.
Activity
Loading/Transport
Commissioning
Set-up, tool installation
Operation
People Person specially trained for the activity
1)
Trained person
2)
Person with specialist training (specialist workshop)
3)
--
--
X
--
X
X
--
X
X
--
X
--
Maintenance
Troubleshooting and fault elimination
Disposal
Legend:
--
--
--
X
X
X
X
X..permitted --
--
..not permitted
--
1) A person who can assume a specific task and who can carry out this task for an appropriately qualified company.
2)
Instructed persons are those who have been instructed in their assigned tasks and in the possible risks in the case of improper behaviour, have been trained if necessary, and have been informed about the necessary protective equipment and measures.
3)
People with specialist technical training shall be considered as a specialist. Due to their specialist training and their knowledge of the appropriate regulations, they can evaluate the work with which they have been charged and detect possible dangers.
Comment:
A qualification equivalent to specialist training can be obtained through long term activity in the appropriate field of work.
Only a specialist workshop may carry out maintenance and repair work on the machine, if such work is specifically designated "Workshop work". The personnel of a specialist workshop shall possess the appropriate knowledge and suitable aids (tools, lifting and support equipment) for carrying out the maintenance and repair work on the machine in a way which is both appropriate and safe.
GBK / GNK / HR BAF0004.0 01.09
13
General safety instructions
2.7 Safety measures in normal operation
Only operate the machine if all the safety and protection equipment is fully functional.
Check the machine at least once a day for visible damage and check the function of the safety and protection equipment.
2.8 Danger from residual energy
Note that there may be residual mechanical, hydraulic, pneumatic and electrical/electronic energy from the machine.
Use appropriate measures to inform the operating personnel. You can find detailed information in the relevant sections of this operating manual.
2.9 Maintenance and repair work, fault elimination
Carry out prescribed setting, maintenance and inspection work in a timely manner.
Secure all media such as compressed air and the hydraulic system against unintentional start-up.
Carefully fix and secure larger subassemblies to lifting gear when carrying out replacement work.
Check all the bolted connections for a firm seat. On completing maintenance work, check the function of safety and protection equipment.
2.10 Structural changes
You may make no changes, expansions or modifications to the machine without the authorisation of AMAZONEN-WERKE. This also applies when welding support parts.
Any expansion or modification work shall require the written approval of AMAZONEN-WERKE. Only use the modification and accessory parts released by AMAZONEN-WERKE so that the operating permit, for example, remains valid in accordance with national and international regulations.
Vehicles with an official type approval or with equipment connected to a vehicle with a valid type approval or approval for road transport according to the German road traffic regulations must be in the state specified by the approval.
WARNING
Risk of being crushed, cut, caught, drawn in or struck if supporting parts break.
It is forbidden to:
· Drill holes in the frame or on the chassis.
· Increase the size of existing holes on the frame or the chassis.
· Weld support parts.
14
GBK / GNK / HR BAF0004.0 01.09
2.11. Spare and wear parts and auxiliary materials
General safety instructions
Immediately replace any machine parts which are not in a perfect state.
Only use genuine spare and wear parts or the parts cleared by AMAZONEN-WERKE so that the operating permit retains its validity in accordance with national and international regulations. If you use wear and spare parts from third parties, there is no guarantee that they have been designed and manufactured in such a way as to meet the requirements placed on them.
AMAZONEN-WERKE accepts no liability for damage arising from the use of unapproved spare parts, wear parts or auxiliary materials.
2.12 Cleaning and disposal
Handle and dispose of any materials used carefully, in particular:
· When carrying out work on lubrication systems and equipment and
· When cleaning using solvents.
2.13 Operator workstation
The machine may be operated by only one person sitting in the driver's seat of the tractor.
2.14 Warning symbols and other labels on the machine
Always keep all the warning symbols of the machine clean and in a legible state. Replace illegible warning symbols. You can obtain the warning symbols from your dealer using the order number (e.g. MD
075).
GBK / GNK / HR BAF0004.0 01.09
15
General safety instructions
Warning symbols - structure
Warning symbols indicate dangers on the machine and warn against residual dangers. At these points, there are permanent or unexpected dangers.
A warning symbol consists of two fields:
Field 1 is a symbol describing the danger, surrounded by triangular safety symbol.
Field 2 is a symbol showing how to avoid the danger.
Warning symbols - explanation
The column Order number and explanation provides an explanation of the neighbouring warning symbol. The description of the warning symbols is always the same and specifies, in the following order:
1. A description of the danger.
For example: Risk of cutting
2. The consequence of nonobservance of the risk-avoidance instructions.
For example: causes serious injuries to fingers or hands.
3. Risk-avoidance instructions.
For example: only touch machine parts when they have come to a complete standstill.
16
GBK / GNK / HR BAF0004.0 01.09
Order number and explanation
MD 075
Risk of fingers and hands being cut or severed by rotating machine parts.
This hazard can cause extremely serious injuries with the loss of body parts such as fingers or hands.
Never reach into the danger area when the tractor engine is running with the PTO shaft/hydraulic system connected.
Do not touch machine parts until they have come to a complete standstill.
MD 076
Risk of hands or arms being drawn in or caught by power-driven, unprotected chain or belt drives.
This hazard can cause extremely serious injuries, including loss of parts of the body from hands or arms.
Never open or remove protective equipment from chains or belt drives,
· while the tractor engine is running and the
PTO shaft is connected/hydraulic drive is engaged
· or the ground wheel drive is in motion
MD 078
Risk of fingers or hands being crushed by accessible moving machine parts.
This hazard can cause extremely serious injuries with the loss of body parts such as fingers or hands.
Never reach into the danger area when the tractor engine is running with the PTO shaft/hydraulic system connected.
MD 079
Hazard from materials or foreign objects that are thrown from or ejected by the machine.
This hazard can cause extremely serious injuries to any part of the body.
Ensure that persons not involved in the operation of the machine maintain a sufficient safety distance from the danger area created by the machine while the tractor engine is running.
GBK / GNK / HR BAF0004.0 01.09
General safety instructions
Warning symbols
17
General safety instructions
MD 082
Danger of falling from treads and platforms when riding on the machine or climbing on operating machinery.
This hazard can cause extremely serious and potentially fatal injuries.
Riding on the machine and/or climbing on operating machinery is forbidden. This also applies to machines with treads and platforms.
Make sure that no-one is riding on the machine.
MD 087
Risk of toes or feet being cut or severed by power-driven tools.
This hazard can cause serious injuries, including loss of parts of the body from toes or feet.
Maintain a sufficient safety distance from the danger area while the tractor engine is running and the PTO shaft/hydraulic system is connected.
MD 093
Risk of being caught or entangled in accessible, moving machine parts.
These dangers can cause extremely serious and potentially fatal injuries.
Never open or remove safety devices from driven parts of the machine
· while the tractor engine is running and the
PTO shaft is connected/hydraulic drive is engaged or
· the tractor engine can be started accidentally when the PTO shaft/hydraulic drive is attached.
MD 095
Read and understand the operating manual safety information before starting up the machine.
18
GBK / GNK / HR BAF0004.0 01.09
MD 097
Risk of crushing torso in the stroke range of the three-point suspension due to narrowing spaces when the three-point hydraulic system is actuated.
This would cause extremely serious injuries and even death.
Persons must not enter the stroke area of the three-point suspension when the three-point hydraulic system is actuated.
Actuate the operating controls for the tractor's three-point hydraulic system
· only from the designated workstation,
· if you are outside the danger area between the tractor and the machine.
MD 100
This symbol indicates lashing points for fastening slinging gear when loading the machine.
MD 102
Danger from unintentional machine starting and rolling during intervention in the machine, e.g. installation, adjusting, troubleshooting, cleaning, maintaining and repairing.
This hazard can cause extremely serious injuries to any part of the body, or even death.
· Secure the tractor and the machine against unintentional start-up and rolling before any intervention in the machine.
· Depending on the type of intervention, read and understand the information in the relevant sections of the operating manual.
MD 114
This symbol indicates a lubrication point
MD 118
This symbol indicates the maximum drive speed
(540 rpm) and direction of rotation of the drive shaft on the machine.
GBK / GNK / HR BAF0004.0 01.09
General safety instructions
19
General safety instructions
MD 145
The CE mark signifies that the machine complies with basic health and safety requirements.
MD 150
Risk of fingers and hands being cut or severed by rotating, unprotected, sharp-edged machine parts.
This hazard can cause extremely serious injuries with the loss of body parts such as fingers or hands.
Never open or remove guard devices from rotating, sharp-edged machine parts while the tractor engine is running with the PTO shaft connected/hydraulic drive engaged.
20
GBK / GNK / HR BAF0004.0 01.09
2.14.1 Positioning of warning symbols and other labels
Warning symbols
General safety instructions
The following diagrams show the arrangement of the warning symbols on the machine.
Stone burier
GBK / GNK / HR BAF0004.0 01.09
21
General safety instructions
22
Seed boxes
GBK / GNK / HR BAF0004.0 01.09
General safety instructions
Reciprocating power harrow
GBK / GNK / HR BAF0004.0 01.09
23
General safety instructions
Rotary harrows
24
GBK / GNK / HR BAF0004.0 01.09
General safety instructions
GBK / GNK / HR BAF0004.0 01.09
25
General safety instructions
2.15 Dangers if the safety information is not observed
Nonobservance of the safety information
· Can pose both a danger to people and also to the environment and machine.
· Can lead to the loss of all warranty claims.
Seen individually, non-compliance with the safety information could pose the following risks:
· Danger to people through non-secured working areas.
· Failure of important machine functions.
· Failure of prescribed methods of maintenance and repair.
· Danger to people through mechanical and chemical impacts.
· Risk to environment through leakage of hydraulic fluid.
2.16 Safety-conscious working
Besides the safety information in this operating manual, the national general workplace safety and accident prevention regulations are binding.
Comply with the accident prevention instructions on the warning symbols.
When driving on public roads and routes, comply with the appropriate statutory road traffic regulations.
26
GBK / GNK / HR BAF0004.0 01.09
2.17 Safety information for the operator
General safety instructions
WARNING
Risk of being crushed, cut, caught, drawn in or struck due to insufficient traffic and operational safety.
Before starting up the machine and the tractor, always check their traffic and operational safety.
2.17.1 General safety and accident prevention information
· Beside these instructions, comply with the general valid national safety and accident prevention regulations.
· The warning symbols and labels attached to the machine provide important information on safe machine operation. Compliance with this information guarantees your safety.
· Before moving off and starting up the machine, check the immediate area of the machine (children). Ensure that you can see clearly.
· It is forbidden to ride on the machine or use it as a means of transport.
· Drive in such a way that you always have full control over the tractor with the attached machine.
In so doing, take your personal abilities into account, as well as the road, traffic, visibility and weather conditions, the driving characteristics of the tractor and the connected machine.
Connecting and disconnecting the machine
· Only connect and transport the machine using tractors suitable for the task.
· When connecting machines to the tractor three-point hydraulic system, the linkages of the tractor and the machine must always be the same.
· Connect the machine to the prescribed equipment in accordance with the specifications.
· When coupling machines to the front or the rear of the tractor, the following may not be exceeded: o The approved total tractor weight o The approved tractor axle loads o The approved load capacities of the tractor tyres
· Secure the tractor and the machine against unintentional rolling, before coupling or uncoupling the machine.
· It is forbidden for people to stand between the machine to be coupled and the tractor while the tractor is moving towards the machine.
Any helpers may only act as guides standing next to the vehicles, and may only move between the vehicles when both are at a standstill.
GBK / GNK / HR BAF0004.0 01.09
27
General safety instructions
· Secure the operating lever of the tractor hydraulic system so that unintentional raising or lowering is impossible, before connecting the machine to or disconnecting the machine from the tractor's three-point hydraulic system.
· When coupling and uncoupling machines, move the support equipment (if available) to the appropriate position (stability).
· When actuating the support equipment, there is a risk of injury from nip and shear points.
· Be particularly careful when coupling the machine to the tractor or uncoupling it from the tractor. There are nip and shear points in the area of the coupling point between the tractor and the machine.
· It is forbidden to stand between the tractor and the machine when actuating the three-point hydraulic system.
· Coupled supply lines: o Must give without tension, bending or rubbing on all movements when travelling round corners. o May not scour other parts.
· The release ropes for quick couplings must hang loosely and must not release themselves when lowered.
· Also ensure that uncoupled machines are stable.
Use of the machine
28
· Before starting work, ensure that you understand all the equipment and actuation elements of the machine and their function.
There is no time for this when the machine is already in operation.
· Do not wear loose-fitting clothing. Loose clothing increases the risk of being caught by drive shafts.
· Only start-up the machine when all the safety equipment has been attached and is in the safety position.
· Comply with the maximum load of the connected machine and the approved axle and support loads of the tractor. If necessary, drive only with a partially-filled hopper.
· It is forbidden to stand in the working area of the machine.
· It is forbidden to stand in the turning and swivel area of the machine.
· There are nip and shear points at externally-actuated (e.g. hydraulic) machine points.
· Only actuate externally-actuated machine parts when you are sure that there is no-one within a sufficient distance from the machine.
· Secure the tractor against unintentional start-up and rolling before you leave the tractor.
For this: o Lower the machine onto the ground o Apply the parking brake o Switch off the tractor engine o Remove the ignition key
GBK / GNK / HR BAF0004.0 01.09
Machine transportation
General safety instructions
· When using public highways, national road traffic regulations must be observed.
· Before moving off, check: o the correct connection of the supply lines o the lighting system for damage, function and cleanliness o the brake and hydraulic system for visible damage o that the parking brake is released completely o the proper functioning of the braking system
· Ensure that the tractor has sufficient steering and braking power.
Any machines and front/rear weights connected to the tractor influence the driving behaviour and the steering and braking power of the tractor.
· If necessary, use front weights.
The front tractor axle must always be loaded with at least 20% of the tractor empty weight in order to ensure sufficient steering power.
· Always fix the front or rear weights to the intended fixing points according to regulations.
· Comply with the maximum load of the connected machine and the approved axle and support loads of the tractor.
· The tractor must guarantee the prescribed brake delay for the loaded vehicle combination (tractor plus connected machine).
· Check the brake power before moving off.
· When turning corners with the machine connected, take the broad load and balance weight of the machine into account.
· Before moving off, ensure sufficient side locking of the tractor lower links, when the machine is fixed to the three-point hydraulic system or lower links of the tractor.
· Before moving off, move all the swivelling machine parts to the transport position.
· Before moving off, secure all the swivelling machine parts in the transport position against risky position changes. Use the transport safety catches intended for this.
· Before moving off, secure the operating lever of the three-point hydraulic system against unintentional raising or lowering of the connected machine.
· Check that the transport equipment, e.g. lighting, warning equipment and protective equipment, is correctly fitted on the machine.
· Before transportation, carry out a visual check that the upper and lower link pins are firmly fixed with the lynch pin against unintentional release.
· Adjust your driving speed to the prevailing conditions.
· Before driving downhill, change to a lower gear.
· Before moving off, always switch off the independent wheel braking (lock the pedals).
GBK / GNK / HR BAF0004.0 01.09
29
General safety and accident prevention information
3 General safety and accident prevention information
30
Basics:
Make sure the equipment is safe to drive and operate before starting it up.
1. Follow the generally applicable safety and accident-prevention regulations as well as the information in this operating manual.
2. The attached warning and information labels attached to the machine provide important details for avoiding danger; they should be followed for your own safety.
3. Observe the relevant regulations when driving on public roads.
4. Before starting work, ensure that you understand all the equipment and operating controls of the machine and their function.
When the machine is in operation, it is already too late.
5. Operators should wear tight-fitting clothing. Avoid wearing loose garments.
6. Check the surrounding area before starting and driving off (children!) Ensure that you can see clearly.
7. Riding on the equipment during work and transport is not permitted.
8. Couple machines according to the instructions and only attach them to the prescribed equipment.
9. Be especially careful when coupling or uncoupling equipment from the tractor.
10. Make sure the safety devices are in position during installation and removal (stability).
11. Always attach weights as instructed to the attachment points provided.
12. Do not exceed the permitted axle loads on the tractor (see registration document).
13. Observe external transport dimensions as per the StVZO (Road
Traffic Licensing Regulation).
14. Check and fit transport equipment such as lights, warning equipment and protective devices.
15. The release ropes for quick couplings must hang loosely and must not release themselves when lowered.
16. Never leave the driver's cab when driving.
17. Driving characteristics, steering and braking are affected by the equipment attached or coupled to the machine, as well as the loaded weight. Ensure adequate steering and braking function.
GBK / GNK / HR BAF0004.0 01.09
3.1
General safety and accident prevention information
18. The load on the front axle of the tractor can vary during lifting, depending on the size of the equipment. Observe the required front axle load (20 % of the tractor weight).
19. Keep an eye on protruding parts and/or shifting weight when driving around corners. To prevent the equipment swinging to and fro, brace the lower link arms of the three-point hydraulic system.
20. Only start equipment, when all the safety equipment has been attached and is in the safety position.
21. Standing in the working area is forbidden.
22. Do not stand where the equipment might turn or swing out.
23. Hydraulic folding frames should only be operated when no-one is in the swivel area.
24. There are nip and shear points on externally-actuated (e.g. hydraulic) machine parts.
25. Before leaving the tractor, lower the equipment, switch off the engine and remove the ignition key.
26. No-one should stand between the tractor and equipment unless the vehicle has been secured against rolling away by applying the parking brake and/or chocking the wheels.
27. The trailer attachment is used to attach equipment and twin-axle trailers, provided that:
· a forward speed of max. 25 km/h is not exceeded;
· the trailer has an overrun brake or brake system that can be operated by the tractor driver;
· the permissible total weight of the trailer is not more than 1.25
times the permissible total weight of the tractor and a maximum of 5 t .
Attaching single-axle trailers to rear-mounted attachments is forbidden .
Attached equipment
1. Before attaching or removing equipment to or from the threepoint support, place all controls in a position which makes it impossible to accidentally raise or lower the equipment.
2. In the case of a three-point connection, the linkages on the tractor and the equipment must match.
3. There is a danger of injury from nip and shear points in the area of the three-point linkage.
GBK / GNK / HR BAF0004.0 01.09
31
General safety and accident prevention information
4. Do not stand between the tractor and the equipment when operating the external controls on the three-point attachment.
5. When transporting the implement, always allow sufficient sideways lock for the tractor's three-point linkage.
6. When driving on the road with the implement raised, the control lever must be locked against lowering.
7. Hitch/attach the equipment in accordance with the instructions.
Check the operation of the trailer's brake system. Follow the manufacturer's guidelines.
8. Equipment should only be transported and driven using the appropriate tractor.
3.2 PTO shaft operation
1. Only PTO shafts prescribed by the manufacturer, which use the prescribed safety devices should be used.
2. Protective tubes and universal drive shaft guards, as well as universal joint protection must be fitted to the PTO shaft and be in proper working order.
3. Allow for the prescribed pipe overlap in the transport and working position (follow the shaft manufacturer's operating instructions).
4. Only attach and detach the shaft with the universal joint shaft at a standstill, the engine switched off and the ignition key removed.
5. Always attach and secure the shaft correctly.
6. Secure the PTO shaft guard against turning by attaching the chains.
7. Before switching on the universal joint shaft, make sure that the selected shaft speed of the tractor and the permitted shaft speed
(operating speed) of the equipment match. The shaft speed is usually 540 rpm.
8. Slow coupling protects tractor and equipment.
9. When using path-dependent universal joint shafts, make sure that the speed is suitable for driving and that the direction of rotation is reversed when driving backwards.
10. Before switching the shaft on, make sure that no-one is standing in the danger zone.
11. Never switch the shaft on when the engine is off.
12. Make sure no-one is in the area of the rotating universal joint shaft or PTO shaft when working on the joint shaft.
13. Always switch off the universal joint shaft if excessive bending occurs and the shaft is not needed.
32
GBK / GNK / HR BAF0004.0 01.09
3.3
General safety and accident prevention information
14. Caution - danger from flywheel run-on when the universal joint shaft is switched off. Do not approach the implement during this time. Only work on it after it is at a standstill.
15. Carry out cleaning, lubrication or adjustment of universal joint shaft driven implements or the PTO shaft only with the universal joint shaft switched off, the engine switched off and the ignition key removed.
16. Place the detached PTO shaft on the bracket provided (only if stone burier fitted).
17. After removing the PTO shaft, place the protective sleeve on the universal joint shaft stub.
18. Deal with any damage before working on the implement.
General safety and accident prevention regulations for maintenance, servicing and care
1. Servicing, maintenance and cleaning, as well as fixing problems should only be undertaken with the drive and engine switched off. Remove the ignition key.
2. Check the tightness of nuts and bolts regularly - initially after the hopper has been filled 3-4 times - and retighten if necessary.
3. Always support the raised implement during maintenance work.
4. Dispose of oil, grease and filters in the proper manner.
5. Disconnect power cables before working on the electrical system.
6. Disconnect the cables to the alternator and battery before carrying out electric welding on the tractor and attached implements.
7. Spare parts must at least meet the technical requirements of the implement manufacturer. This is guaranteed by using genuine spare parts.
GBK / GNK / HR BAF0004.0 01.09
33
4.2
Machine data
4 Machine data
4.1 Declaration of conformity
The machine complies with the requirements of the EC Machinery
Directives 89/392/EC and associated additional guidelines.
4.3
Details required for enquiries
When ordering special optional equipment and spare parts, please remember to quote the machine number .
Safety requirements are only fulfilled if genuine AMAZONE spare parts are used when a repair is undertaken. The use of other parts may remove liability for any consequences which may occur as a result.
Intended use
The Amazone grass seeder combination is designed exclusively to carry out conventional maintenance tasks in grassed open areas and parks (intended use).
Any use which goes beyond these limits is not regarded as the intended use. The manufacturer is not liable for any damages which may result from such use.
The risk involved in such use is borne solely by the operator.
Intended use also includes compliance with instructions specified by the manufacturer concerning operation, servicing and maintenance as well as the exclusive use of genuine AMAZONE spare parts .
The Amazone grass seeder combination may only be used, serviced and maintained by persons who are familiar with the machine and who have received instruction concerning the risks involved.
All relevant accident prevention regulations and any other generally recognised rules concerning safety, occupational health and traffic laws must be observed and the safety instructions listed on the labels attached to the machine must be strictly followed.
Any unauthorised modification of the machine will automatically render all warranty claims against the manufacturer for resulting damage invalid.
34
GBK / GNK / HR BAF0004.0 01.09
5 Implements for soil tillage
Implements for soil tillage
The AMAZONE GBK, GNK and HR landscaping and landscape maintenance combinations consist of:
· a soil tillage implement,
· a screen roller or a smooth roller,
· a seed box for grass seed (re)sowing.
5.1 Reciprocating power harrow
5.1.1 Technical data – reciprocating power harrow (basic machine)
Working width (m)
Weight - basic machine (kg)
Tractor power (HP)
REG02-15
1.50
271 from 25
REG02-20
2.00
284 from 35
REG02-25
2.50
297 from 50
5.1.2 Technical data - tine bars
The advantage of the reciprocating power harrow 'building-block system' (Fig. 5.1.2) is that only one reciprocating power harrow is needed for different applications.
The machine can only be used for the work listed in the table (Table
1) by replacing the tine bar.
Tine bars:
Fixed bar (for attaching to carrier bar)
Fixed bars are suitable for the regeneration of hard sports courts, bicycle and walking paths. Here, the reciprocating power harrow is used in combination with a smooth roller.
When used in combination with a screen roller and seed box, they are ideal for levelling ploughed soil and re-sowing all at the same time.
Spring-steel tine bars
The ruggedness of spring-steel tine bars means that the soil can be prepared before sowing, even under difficult conditions. The triangular teeth ensure that the soil is thoroughly broken up, and the flat double teeth level the soil and prevent sowing in strips.
Scarifier bar (for attaching to carrier bars)
GNK scarifiers guarantee broad-angle re-sowing over the entire working area. This combination can be used as a wide grass sower combination with soil prepared for re-sowing. Setting the tines to drag prevents any hidden stones being pushed to the surface.
GBK / GNK / HR BAF0004.0 01.09
35
Implements for soil tillage
Scraper bars
The combination of a scarifier at the front and a scraper bar behind can be used to level hard sports courts. Scraper bars front and rear are ideal for incorporating sand into synthetic turf.
Reciprocating harrow
Supporting bars
Rigid tine bars
Fig. 5.1.2
Table 1
Resowing
Difficult soil tillage
Medium to light soil tillage
Annual regeneration of tamped areas
Regular maintenance of tamped areas
Incorporating sand into artificial turf or paved areas
Resowing
Levelling surfaces
Levelling hard sports courts
excellent result
Bar weight (kit, incl. carrier bar)
REG02 - 15
REG02 - 20
REG02 - 25
66 kg
84 kg
98 kg
36
Overseeding tine bars front rear
good result
82 kg
106 kg
128 kg
Brush bars
53 kg
70 kg
81 kg
Spring steel tine bars
102 kg
128 kg
GBK / GNK / HR BAF0004.0 01.09
5.1.3 Installing and adjusting the reciprocating power harrow
Implements for soil tillage
The distance between the PTO shaft and the pivot points of the lower links will usually be different with different tractor types. Optional extension pieces are available for the lower headstock so the reciprocating power harrow harrow can be fitted to any tractor type.
The lower links on the tractor need to have a little free side movement.
The lower links on the tractor are connected and secured to the lower link sockets on the . The top link on the tractor should be set so that the reciprocating power harrow harrow is angled slightly backwards
(Fig. 5.1.2-1 and Fig. 5.1.2.-2).
Make sure that no-one stands behind or under the machine because it could swing backwards if both parts of the top links come undone or accidentally separate.
At least two seconds must be allowed for the machine to lower.
Adjust the three-point hydraulic system on the tractor appropriately. Set the loaded machine down gently on the ground.
5.1.4 PTO shaft
Only use PTO shafts recommended by the manufacturer.
Walterscheid W 2300
5.1.5 Attaching the PTO shaft
First clean the shaft in the housing and always install a greasedlubricated PTO shaft on the input shaft.
GBK / GNK / HR BAF0004.0 01.09
37
Implements for soil tillage
5.1.6 Adjusting the PTO shaft the first time the machine is coupled
Adjust the PTO shaft to the tractor the first time it is coupled. As this adjustment is only intended for one kind of tractor, check whether the PTO shaft needs to be modified for a different tractor when you install it.
During initial installation, attach the gearbox halves to the front of the universal joint shaft on the tractor. Do not insert the profile tubes inside each other.
1. Check, by holding the tubes next to each other, whether they can be installed in any position.
2. If they have been inserted firmly inside each other, they should not hit against the drive shaft crosspieces. A safe clearance of at least 10 mm is absolutely necessary.
3. To level the two lengths, hold the gearbox halves against each other in the shortest operational position and mark them.
4. Shorten the protective tubes equally inside and out.
5. Shorten the profile tubes equally.
6. Debur the edges of the tubes after cutting and carefully remove the metal residue.
7. Grease the tubes and insert them inside each other.
8. Hang the chains in the hole in the shackle fixing point of the top link in such a way that the drive shaft can move freely in any operating position, and make sure that the PTO shaft guard cannot turn at the same time.
9. Only work on a PTO shaft fitted with all the necessary safety devices.
The drive must be complete in relation to its safety devices and the protective cover on the tractor and machine. The safety devices are to be replaced immediately if damaged.
The maximum permissible bend in a PTO shaft universal joint can be found in the enclosed instruction manual from the manufacturer.
This manual also contains information on fitting and maintenance that must be observed.
To avoid damage, only connect the universal joint shaft slowly when the tractor engine is running at low revs.
38
GBK / GNK / HR BAF0004.0 01.09
5.1.7 Input speed for the reciprocating power harrow gearbox
Implements for soil tillage
The maximum permissible input speed for the gearbox is
540 rpm.
N = 540 rpm
Damage caused using speeds above 540 rpm is not covered by the guarantee.
5.1.8 Maintenance
The bearings on the drive shaft and the connecting rod must be lubricated every 50 hours or after cleaning with water.
Otherwise, the reciprocating power harrow is maintenance-free.
GBK / GNK / HR BAF0004.0 01.09
39
Implements for soil tillage
40
GBK / GNK / HR BAF0004.0 01.09
5.2 Rotary harrow
5.2.1 Technical data - rotary harrow (basic machine)
Implements for soil tillage
Working width
(m)
Weight of basic machine
(kg)
Tractor power
(HP)
F61-110
1.10
245 from 20
5.2.2 Attaching to the tractor
F61-130
1.30
275 from 25
F61-150
1.50
305 from 30
F61-200
2.00
405 from 45
F61-250
2.50
810 from 60
Depending on the type of tractor, the distance between the universal joint shaft and pivot points of the lower links is usually different. To enable the rotary harrow to be attached to any tractor type, the lower link arms on the implement can be adjusted horizontally in the direction of travel (Fig. 5.2.2-1) and can be turned (Fig. 5.2.2-2).
GBK / GNK / HR BAF0004.0 01.09
41
Implements for soil tillage
The lower links on the tractor should be connected to the lower link arms on the rotary harrow and secured with cotter pins. The top link on the tractor should be adjusted so that the rotary harrow tilts slightly backwards.
Make sure that no-one stands behind or under the machine because it could swing backwards if both parts of the top links come undone or accidentally separate.
At least two seconds must be allowed for the machine to lower.
Adjust the three-point hydraulic system appropriately. Set the loaded machine down gently on the ground.
5.2.3 PTO shaft
Use PTO shafts recommended by the manufacturer.
Walterscheid W 2300 SD 15-610 K34B-110 with a working width of up to 1.30 m
Walterscheid W 2400 SD 25-610 K34B-120 with a working width of over 1.50 m
Torque limiter
Each machine that uses a PTO shaft is supplied with a torque limiter to prevent the implement mechanism or the tractor being overloaded. The guarantee lapses immediately if the safety equipment is disconnected, replaced or modified.
5.2.4 Attaching the PTO shaft
First clean the shaft in the housing and always install a greasedlubricated PTO shaft on the input shaft.
5.2.5 Adjusting the PTO shaft the first time the machine is coupled
Adjust the PTO shaft to the tractor the first time it is coupled. As this adjustment is only intended for one kind of tractor, check whether the PTO shaft needs to be modified for a different tractor when you install it.
IMPORTANT
How to shorten the PTO shaft is detailed in section 5.1.6.
The maximum permissible bend in a PTO shaft universal joint can be found in the enclosed instruction manual from the manufacturer.
This manual also contains instructions which must be observed regarding fitting and maintenance operations.
To avoid damage, only connect the universal joint shaft slowly when the tractor engine is running at low revs.
42
GBK / GNK / HR BAF0004.0 01.09
5.2.6 Input speed for the rotary harrow
Implements for soil tillage
The maximum permissible input speed for the gearbox is 540 rpm.
N = 540 rpm
Damage caused using speeds above 540 rpm is not covered by the guarantee.
5.2.7 Lubrication
After the first 50 hours of operation, replace the oil in the reduction gears. To do so, open the S drain plugs (Fig. 5.2.7).
Clean inside the reduction gears with kerosene or gas oil. Add suitable oil through the filling opening -C- in Fig. 5.2.7 and check the level at opening L.
Repeat this procedure every 300 hours of operation.
The grease in the gear pan should be checked regularly - it must coat the gear wheels. This check can be made via the filling opening.
AGIP
BP
CASTROL
ELF
ESSO
MOBIL
SHELL
OIL
Blasia 150
Energol GR-XP 150
Alpha SP 150
Reductelf 150
Spartan EP 150
Mobilgear 630
Omala oil 150
GREASE
Gr Mu EP 0
Grease LTX 0
Spheerol EPL 0
Rolexa 0
Beacon 0
Mobilplex 0
Alvania grase R 0
GBK / GNK / HR BAF0004.0 01.09
43
Implements for soil tillage
5.2.8 Maintenance
Daily tasks to guarantee the functional efficiency of the machine:
· Make sure that the lower links on the tractor cannot dangle to the side.
· Check the tightness of all bolts, especially the mounting bolts on the central tine bracket.
· Check the tightness of the tine bolts and their condition; if they are damaged during use, we recommend replacing them immediately - see section 5.2.9.
5.2.9 Replacing tines
To replace the tines, place the harrow on two solid supports to prevent the implement dropping suddenly. To remove the tines, undo and remove the bolted connections in positions 1, 2 and 3 (see Fig.
5.2.9B).
The tine bolts are torqued to 400 Nm (Fig. 5.2.9A).
44
GBK / GNK / HR BAF0004.0 01.09
5.3 Stone burier
5.3.1 Technical data - stone burier (basic machine)
Implements for soil tillage
Working width
(m)
Weight - basic machine (kg)
Tractor power
(PS)
(ruggedised version)
Working width
(m)
Weight - basic machine (kg)
Tractor power
(PS)
G15-85
0.85
270 from 20
G35-150
1.50
621 from 70
5.3.2 Attaching to the tractor
G15-105
1.05
300 from 25
G25-200
2.00
781 from 80
G25-110
1.10
317 from 25
G25-130
1.30
347 from 30
G25-150
1.50
377 from 35
Connect the lower links of the tractor to the machine's lower threepoint system and secure with cotter pins. Adjust the top link on the tractor so that the machine is horizontal in the operating position.
5.3.3 PTO shaft
Only use PTO shafts recommended by us.
Walterscheid W 2300 SD 15-610 K34B-110 with a working width of up to 1.30 m
Walterscheid W 2400 SD 25-610 K34B-120 with a working width of above 1.50 m (standard version)
Walterscheid P 500 PG 20-710 EK64/2R-200 with a working width of above 1.50 m (ruggedised version)
Torque limiter
Each machine that uses a PTO shaft is supplied with a torque limiter to prevent the implement mechanism or the tractor being overloaded. The guarantee lapses immediately if the safety equipment is disconnected, replaced or modified.
GBK / GNK / HR BAF0004.0 01.09
45
Implements for soil tillage
5.3.4 Attaching the PTO shaft
First clean the shaft in the housing and always install a greasedlubricated PTO shaft on the input shaft.
5.3.5 Adjusting the PTO shaft the first time the machine is coupled
Adjust the PTO shaft to the tractor the first time it is coupled. As this adjustment is only intended for one kind of tractor, check whether the PTO shaft needs to be modified for a different tractor when you install it.
The angle defining the maximum joint bends in a universal joint on the PTO shaft can be found in the accompanying operating manual provided by the manufacturer.
This manual also contains instructions which must be observed regarding fitting and maintenance operations.
To avoid damage, only connect the universal joint shaft slowly when the tractor engine is running at low revs.
5.3.6 Input speed for the stone burier
The maximum permissible input speed for the gearbox is
540 rpm.
N = 540 rpm
Damage caused using speeds above 540 rpm is not covered by the guarantee.
46
GBK / GNK / HR BAF0004.0 01.09
6 Screen roller and smooth roller
6.1 Technical data - screen roller
Diameter (mm)
Working width (m)
(nominal width)
Weight (kg)
GIW 11
420
1.10
(1.20)
115
GIW 13
420
1.30
(1.40)
130
GIW 15
420
1.50
(1.60)
145
6.2 Technical data - smooth roller
Diameter (mm)
Working width (m)
(nominal width)
Weight (kg)
GLW 11
360
1.10
(1.20)
132
GLW 13
360
1.30
(1.40)
147
GLW 15
360
1.50
(1.60)
162
6.3 Scraper
Screen roller and smooth roller
GIW 20
420
2.00
(2.10)
170
GLW 20
360
2.00
(2.10)
187
GIW 25
420
2.50
(2.60)
195
GLW 25
360
2.50
(2.60)
212
The roller is fitted with a scraper as standard. Particularly when the screen roller is being used, the scraper must not touch the roller body.
The clearance is adjusted using the two M8 x 60 bolts at the side of the frame (Fig. 6.3/1). The scraper can be folded upwards for cleaning.
GBK / GNK / HR BAF0004.0 01.09
47
Screen roller and smooth roller
6.4 Uncoupling the screen roller
The screen roller is attached to the soil tillage implement by two carrying arms (Fig. 6.4-1/1).
Proceed as follows to separate it from the implement:
· Attach the machine to the tractor.
· Raise the machine until the soil tillage implement no longer touches the ground but the roller is still on the ground.
· Remove the retaining bolts (Fig. 6.4-1/1).
· The cams should no longer rest on the carrying arms (Fig. 6.4-1/2 and Fig. 6.4-1/3).
· Remove the retaining bolts (Fig. 6.4-2).
CAUTION:
This work should only be carried out by authorised specialists.
CAUTION:
The combination is susceptible to tipping over.
48
GBK / GNK / HR BAF0004.0 01.09
Screen roller and smooth roller
C A U T I O N
The screen roller must be secured before it is uncoupled, to stop it tipping over.
To attach a different implement, uncouple the reciprocating power harrow from the roller as follows:
· Move the implement and tractor forwards and separate the combination.
Work in the reverse sequence to coupling when uncoupling the roller.
6.5 Water connection on smooth roller
To achieve greater reconsolidation of the soil, fill the smooth roller with water. There is a flange with a water connection point on each side of the roller (Fig. 6.5-1). The water hose is connected to one side; then the other connection point is used to allow the air to escape during filling.
CAUTION:
Protect the roller from frost by emptying it if temperatures fall below zero or fill it with antifreeze.
GBK / GNK / HR BAF0004.0 01.09
49
Screen roller and smooth roller
6.6 Maintenance
The flange bearing should be lubricated every 50 hours of operation
(Fig. 6.6).
50
GBK / GNK / HR BAF0004.0 01.09
7 Seed box
7.1 Technical data
Seed box
Seed box
Working width (m)
Total width (m)
Height (m)
Length (m)
1.10 m
1.10
1.44
0.51
0.43
1.30 m
1.30
1.64
0.51
0.43
1.50 m
1.50
1.84
0.51
0.43
2.00 m
2.00
2.34
0.51
0.43
2.50 m
2.50
2.84
0.51
0.43
Empty weight (kg)
Capacity (l)
Seed quantity
85 90 95 110 125
143 167 194 275 320
……….……….……….…………..0-600 kg/ha (infinite)………..……….……….……….
Two-speed gearbox with oil bath
Capacity
WTL hydraulic oil, 16.5 C ST / 50 °C
1.80 l
7.2 Fitting the seed box
The seed box sits on rubber elements attached to the roller frame.
The drive chain is tensioned by a pulley attached to the roller frame
(Fig. 7.2-1/1).
GBK / GNK / HR BAF0004.0 01.09
51
Seed box
The chain drive is covered by a split chain guard.
Procedure for removing the seed box:
· Remove the upper and lower parts of the chain guard on the chain drive (Fig. 7.2-2).
^
7.3
· Use pliers to release the spring on the pulley.
· Remove the chain by opening the chain link provided for this.
· Remove the three M12 mounting bolts holding the seed box to the frame.
· Lift the seed box using a suitable hoist.
To refit the seed box, proceed in the reverse order to removal.
Filling the seed box
Before filling the seed box, make sure that the bottom plate is closed and locked. Attach the machine to the tractor and open the seed box cover. It is held open by a safety strut.
To close the seed box, lift the strut with one hand and lower the lid with the other. The lid forms a tight weatherproof seal.
Make sure that the seed box is sufficiently full while working to avoid irregular drilling.
52
GBK / GNK / HR BAF0004.0 01.09
7.4 Emptying the seed box
The seed box is emptied as follows:
· Undo the thumb bolts holding the emptying rail.
· Release the rail at the rear of the seed box (Fig. 7.4-1).
Seed box
· Attach a sack to the hook on the rails.
· Slide the rail along the chute until the opening is fully closed.
· Open the tenter hooks (Fig. 7.4-2) and drop the bottom plate down. The seed will flow into the chute and then into the sack when you pull the rail slowly away from the chute (Fig. 7.4-3),
· After emptying, reattach the rail to the rear wall of the seed box.
The seed box can be cleaned using a jet of water or a highpressure cleaner. If you clean the seed box with compressed air, do not breathe in the dust because the seed may have been treated with substances that are dangerous to your health.
The seed box must be emptied and cleaned several times a year.
When the machine is stored, the bottom plate of the seed box must be left in the open position. Rodents attracted by the smell of the seed may damage the plastic seed wheels while trying to gain entry to the seed box.
GBK / GNK / HR BAF0004.0 01.09
53
Seed box
7.5 Setting the sowing rate
Use the quantity table in section 7.7 to set the rate.
· To set the sowing rate, screw the handle onto the gear lever (Fig.
7.5/1).
· Set the pointer to the value selected from the quantity table.
· Bring the gear lever up to the selected position.
· After adjusting the handle, tighten it again.
C A U T I O N
The figures in the quantity table should only be used as a guide.
A calibration test is essential to determine the exact sowing rate for the seed box for the seed used. There will be differences between the theoretical and actual sowing rates, depending on the grain size, the shape and the specific weight of the seed and the medium.
54
GBK / GNK / HR BAF0004.0 01.09
Seed box
7.6 Tips on drilling in slow or fast gear
The gear of the sowing shaft, and therefore the sowing rate, can be set using the gearbox (Fig. 7.6/2). There is also a speed converter in the gearbox. Two gears can be set by turning a gear wheel: slow
(see Fig. 7.6/A) fast
(see Fig. 7.6/B)
The setting range is increased by changing from slow to fast (Fig.
7.5/3). The fast gear should only be selected if the desired sowing rate is not achieved when the lever is in the "10" position on the scale for the slow rate. The gearbox is set to slow mode at the factory.
The slow gear is recommended for sowing.
GBK / GNK / HR BAF0004.0 01.09
55
Seed box
7.6.1 Adjusting the gearbox in fast mode
To set the gearbox to fast mode, open the cover on the side of the gearbox (Fig. 7.6.1/1) by undoing the thumb bolts and both thumb nuts (Fig. 7.6.1/2).
Take the lower gear wheel (Fig. 7.6.1/3) off the shaft, reverse it and replace it on the shaft. If the gear wheel is difficult to remove from the shaft by hand, use pliers to move the sowing shaft slightly to release the pressure on the gearbox.
In slow mode, the gear wheel meshes with the wheel above it (Fig.
7.6.1/1), while in fast mode, the gear wheel will run freely (Fig.
7.6.1/2). Close the cover again after the changeover.
If possible only sow in slow mode. After sowing in fast mode, reset the gearbox of your seed box to slow mode.
56
GBK / GNK / HR BAF0004.0 01.09
7.7 Quantity table
7.8 Calibration test
Seed:
Specific weight:
Gear setting
7
8
5
6
10
3
4
1
2
Seed box
Resilient grass
0.37 kg/L
Sowing rate in kg/ha in selected gear
Slow
25 kg/ha
56 kg/ha
82 kg/ha
109 kg/ha
137 kg/ha
163 kg/ha
191 kg/ha
258 kg/ha
274 kg/ha
Fast
38 kg/ha
137 kg/ha
212 kg/ha
304 kg/ha
387 kg/ha
464 kg/ha
524 kg/ha
651 kg/ha
693 kg/ha
The calibration test checks whether the quantity sown corresponds to the desired quantity. Set the gear lever to the desired sowing rate in the table.
Only ever fill the seed box half way for the calibration test, so the crank will be easier to turn than with a full seed box.
· Raise the machine until the roller moves freely.
· Make sure the seed drill is horizontal.
· Place the rail and sack under the chute (section 7.4)
· Place the calibration crank on the left end of the roller shaft
(Fig. 7.8-1)
GBK / GNK / HR BAF0004.0 01.09
57
Seed box
· Turn the roller until seed emerges from the seed wheels.
· Use the rail to empty the chute into the container and then push the rail back towards the chute.
The calibration test can now start.
Number of rotations of the roller corresponding to a worked area of one "are"
Screen roller Æ 420 mm
Smooth roller Æ 360 mm
1.10 m
1.30 m
1.50 m
2.00 m
2.50 m
67.5
57
49.5
37
29.5
80
67.5
58.5
44
35
The seed collected in the bag must be weighed (Fig. 7.8-2). The weight of the seed must be multiplied by 100 to obtain the sowing rate in kg/ha.
58
For 1 are (100 m²) calibrated seed rate x 100 = sowing rate in kg/ha
The sowing rate can be adjusted using the lever on the gearbox.
C A U T I O N
We recommend not exceeding a speed of 6 km/h when working with the grass seeding combination. In addition, the crank should not be turned more than 80 times per minute during the calibration test.
GBK / GNK / HR BAF0004.0 01.09
7.9 Maintenance
Seed box
The AMAZONE seed box is designed to require minimal maintenance. However, we recommend checking the following points at regular intervals:
Visual check of the oil level in the gearbox using the oil-level indicator.
It is not necessary to change the oil. To top up the oil, remove the cover plate on the box by undoing the M8 screw in the centre of the plate. Only use WTL hydraulic oil, 16.5 c ST/50 gr. The capacity is 1.8 l.
After approx. 50 hours of operation, check the condition of the chain and lubricate it if necessary.
GBK / GNK / HR BAF0004.0 01.09
59
AMAZONE GBK combination seeding system
8 AMAZONE GBK combination seeding system
8.1 Fields of application
With the AMAZONE GBK combination seeding system you can create your greens, such as e.g. sports fields, fairways, parks, etc…
Depending on the chosen soil tillage implement, in one working session, it is possible to:
· achieve optimal flatness of a turned area
· turn an area and broadcast sow the entire worked area using the seed box.
Comment:
When used for soil cultivation (without drilling), we recommend removing the seed drill so as not to subject it to vibrations.
60
GBK / GNK / HR BAF0004.0 01.09
AMAZONE GBK combination seeding system
8.2 GBK combination seeding system with reciprocating power harrow
8.2.1 Setting the working depth
The reciprocating power harrow must be supported continuously by the roller when working to guarantee a uniform working depth. The depth is set by the top cams of the support (Fig. 8.2.1-1).
Adjusting the top cams:
· Raise the machine until the top cams no longer touch the carrying arms.
· Use the crank to undo the securing bolts (Fig. 8.2.1-2),
· Turn the cams to set the working depth. Make sure that the setting is the same on both sides of the machine. The figures on the cams serve as reference points and do not represent the actual height.
· Tighten the securing bolts.
GBK / GNK / HR BAF0004.0 01.09
61
AMAZONE GBK combination seeding system
The lower cams allow you to lock the carrying arms and so transfer the weight of the roller to the reciprocating power harrow. That way, the teeth of the reciprocating power harrow can better penetrate hard soil.
Adjusting the lower cams:
· Set the working height using the upper cams.
· Lower the reciprocating power harrow and switch it on briefly with the machine stationary until the desired working depth is achieved.
· Undo the securing bolts on the lower cams.
· Adjust the lower cams until they touch the carrying arms (Fig.
8.2.1-3),
· Retighten the securing bolts.
8.2.2 Adjusting the lateral weeders
After the working depth has been set, you need to equalise the height of the lateral weeders on the side ends of the front tine bars.
Procedure:
· Switch on the universal joint shaft and lower the machine until the desired working depth is achieved.
· Switch off the universal joint shaft and tractor.
· Undo the securing bolts on the lateral weeders.
· Adjust the harrow until it is about 2 cm above the ground (Fig.
8.2.2),
· Retighten the securing bolts.
62
GBK / GNK / HR BAF0004.0 01.09
AMAZONE GBK combination seeding system
The lateral weeders should never penetrate the soil while the machine is in operation, otherwise they would create a small groove.
8.2.3 Adjusting the chute
The chute allows you to distribute the seed evenly, directing it to the ground and stopping it drifting in the wind.
The sowing depth is adjusted using the angle of the chute.
Principle of operation
As you work, a more or less sizeable earth wall forms behind the reciprocating power harrow, depending on the working depth and tractor speed. If the chute is angled to the rear (towards the roller), the seed is distributed on the surface of the soil. If the chute is angled forwards
(in the direction of the reciprocating power harrow), the seed is worked into the soil up to a depth of 3-4 cm.
Adjusting the chute:
· Undo both M10 nuts on both sides of the chute (Fig. 8.2.3)
· Angle the chute to the desired position.
· Retighten the nuts.
GBK / GNK / HR BAF0004.0 01.09
63
AMAZONE GBK combination seeding system
8.2.4 Levelling blade
The reciprocating power harrow can be fitted with an optional levelling blade for better forming of the surface. The levelling blade is adjusted as follows:
· Undo the securing pin on each crank (Fig. 8.2.4-1).
· Turn the crank to set the blade to the desired height (fig. 8.2.4-2).
· Push the pins back in.
64
GBK / GNK / HR BAF0004.0 01.09
AMAZONE GBK combination seeding system
8.3 GBK combination seeding system with rotary harrow
8.3.1 Setting the working depth
The working depth of the rotary harrow is set using the side supports.
To adjust the working depth, insert the locking pin into the desired hole and secure it there (Fig. 8.3.1). The left and right supports must be set to the same working depth.
8.3.2 Adjusting the lateral weeders
The shares prevent an earth wall forming to the left and right of the worked area. They must be adjusted to lightly ( ± 1 cm) penetrate the soil.
They are adjusted as follows:
· Bring rotary harrow to working position.
· Undo thumb nuts.
· Bring share to the desired position.
· Tighten the thumb nuts.
GBK / GNK / HR BAF0004.0 01.09
65
AMAZONE GBK combination seeding system
8.4 GBK combination seeding system with stone burier
8.4.1 Commissioning
The stone burier is designed to break up soil, plant residue and small stones on the surface and incorporate them into the soil. For problemfree operation, make sure the diameter of the stones does not exceed approx. 5 cm, and that there is sufficient loose soil to form a covering layer.
CAUTION Make sure no-one is standing directly behind the machine while the machine is in operation. Because the rotor turns anticlockwise, there is the danger of the entire vehicle combination moving backwards.
To work with the machine, proceed as follows:
· Make sure the tractor's parking brake is on securely.
· Lower rotor close to the ground.
· Engage universal joint shaft.
· Allow universal joint shaft to turn at about 540 rpm and slowly lower the whole machine.
· Switch off the engine and remove the ignition key.
· Set the working depth (the side guides should always be parallel to the ground); if necessary, adjust using the top link. The side parts should penetrate 2-3 cm into the soil.
· Raise the machine so that the rotor is slightly above the ground.
· For initial testing, select a forward speed of 1 – 1.2 km/h, and slowly uncouple while simultaneously lowering the machine.
The three-point hydraulic system must be fully lowered and able to move freely.
· If the rotor becomes blocked by an overlarge stone, uncouple the universal joint shaft immediately without raising the machine.
Continue with the machine lowered so the rotor turns in the direction of travel. In this way, most stones will free themselves from the rotor. This process can be assisted by moving the three point linkage up and down.
Never reach under the machine to remove foreign objects from the rotor.
· If it is not possible to unblock the rotor, remove the leveller cover
(Fig. 8.4.1-1).
66
GBK / GNK / HR BAF0004.0 01.09
AMAZONE GBK combination seeding system
· Remove the harrow sieve completely (Fig. 8.4.1-2).
· Remove the knife in which the object is blocked.
· Remove the object.
8.4.2 Setting the working depth
The working depth of the stone burier is set using the side supports.
To adjust the working depth, insert the locking pin into the desired hole and secure it there (Fig. 8.4.2). The left and right supports must be set to the same working depth.
GBK / GNK / HR BAF0004.0 01.09
67
AMAZONE GBK combination seeding system
8.4.3 Driving
In order to achieve a good result, the machine must be free to follow the soil contour. For this, the three-point hydraulic system on the tractor must be in the lowest position and able to move freely.
To make sure there is good separation between prepared rows when working at a considerable depth, it is advisable for the prepared part to lie to the right of the direction of travel.
When the implement is driven around a slight corner, the lower link arms on the tractor must be able to move freely to the left and right, i.e. do not fasten the lower link arms at the side.
8.4.4 Stone burier operation
The blades work the soil against the direction of travel. The raised earth is thrown up against the primary sieve, which allows stones and debris larger than 4 cm in diameter to return to the groove created by the rotor.
Fine material from the second sieve forms a covering layer. The sieved fine soil is directed downwards by the final leveller cover to ensure optimal distribution and coverage. The screen roller consolidates a roughened surface, making it ideal for seeding the lawn.
We recommend loosening the soil with a suitable implement to achieve a lasting and healthy green space, prevent water from pooling and allow the grass to grow well. The stone burier is responsible for the finish.
Because the rotor operates anticlockwise, all foreign material close to the knives is taken up. It is therefore essential to remove larger stones and obstacles from the area before starting work.
A PTO shaft with overload protection must be used to protect the machine.
68
GBK / GNK / HR BAF0004.0 01.09
9 AMAZONE GNK Overseeder
9.1 Fields of application
AMAZONE GNK Overseeder
With the AMAZONE GNK overseeder, it is possible to reseed existing lawns such as sports fields, fairways, parks, etc., and to seed prepared areas.
The tines on the scarifiers are a mix of spring blades and round rods made of spring steel, combined in such a way that
· they are fixed in the working direction of the reciprocating power harrow (lateral to the direction of driving) and ensure good agitation of the surface layer without damaging healthy grass;
· they are movable in the direction of travel and can avoid obstacles such as stones, roots, etc.
Before resowing lawn, we recommend cutting the grass very short (2 to 3 cm) and, if necessary, scarifying with an AMAZONE Grasshopper or Profihopper, and removing the scarified material.
If you do not have this equipment, you can scarify with the scarifying harrow without simultaneous sowing and gathering up the material, and later gather up the scarified material before actually reseeding.
9.2 Working with the overseeder
9.2.1 Adjusting the overseeding tine bars
Depending on the condition of the surface to be prepared, the overseeder can be set to be more or less aggressive by changing the angle of the tine bars.
The adjustment is made as follows:
· Couple machine to the tractor (see reciprocating power harrow section).
· Raise the machine
· Remove the parking supports:
- Remove the safety pin.
- Remove the locking pin.
- Remove the supports and fasten in the transport bracket
(Fig. 9.2.1-1).
· Undo mounting bolts on both sides of the overseeding tine bar
(Fig. 9.2.1-2).
· Angle overseeder in the desired position.
· Retighten the securing bolts.
GBK / GNK / HR BAF0004.0 01.09
69
AMAZONE GNK Overseeder
9.2.2 Adjusting the chute
The chute allows you to distribute the seed evenly, directing it to the ground and stopping it drifting in the wind.
Change the angle of the chute to set the sowing depth and/or and dispensing point so the seed makes optimal contact with the roughened surface and the loose soil.
Re-sowing - principle
As you work, a more or less sizeable earth wall forms behind the reciprocating power harrow, depending on the working depth and tractor speed. If the chute is angled to the rear (towards the roller), the seed is distributed on the surface of the soil. If the chute is angled forwards
(in the direction of the reciprocating power harrow), the seed is worked into the soil up to a depth of 3-4 cm.
To adjust the chute:
· Undo both M10 nuts on both sides of the chute (Fig. 9.2.2)
· Angle the chute to the desired position.
· Retighten both M10 nuts.
70
GBK / GNK / HR BAF0004.0 01.09
AMAZONE GNK Overseeder
GBK / GNK / HR BAF0004.0 01.09
71
AMAZONE HR hard court reconditioner
10 AMAZONE HR hard court reconditioner
10.1 Technical data
Working width (m)
Weight (kg)
Tractor power (HP)
Reciprocating power harrow with fixed tine bars + smooth roller + lateral brush + rear brush
HR 15 HR 20 HR 25
1.50
545 from 20
2.00
604 from 32
2.50
650 from 45
10.2 Fields of application
The AMAZONE HR hard sports court reconditioner consists of a reciprocating power harrow and a smooth roller fitted with a lateral and rear brush. The HR can be configured for the following work by changing the different tine bars:
· Regeneration of tamped areas and paths.
· Weekly maintenance of tamped areas.
· Proper artificial turf care.
10.3 Working with the hard court reconditioner
10.3.1 Regenerating hard courts
The Amazone hard court reconditioner, which is a reciprocating power harrow fitted with fixed tine bars, can work the surface of tamped areas in one pass. The reciprocating power harrow loosens the top layer, while the released tamped material simultaneously fills depressions and levels bumps.
10.3.2 Adjusting the reciprocating power harrow working depth
During operation, the roller height is controlled by that of the reciprocating power harrow to guarantee a uniform working depth. The depth is set by the top cams (Fig. 10.3.2-1).
72
GBK / GNK / HR BAF0004.0 01.09
AMAZONE HR hard court reconditioner
Adjusting the top cams:
· Raise the machine until the top cams no longer touch the carrying arms.
· Use the crank to undo the securing bolts on the cams
(Fig. 10.3.2-2).
· Turn the cams to set the working depth. Make sure that the setting is the same on both sides of the machine. The figures on the cams serve as reference points and do not represent the actual height.
· Retighten the securing bolts.
The lower cams allow you to lock the carrying arms and so transfer the weight of the roller to the reciprocating power harrow. That way, the teeth of the reciprocating power harrow can better penetrate hard ground.
Adjusting the lower cams:
· Set the working height using the upper cams.
· Lower the reciprocating power harrow and switch it on briefly until the desired working depth is achieved.
GBK / GNK / HR BAF0004.0 01.09
73
AMAZONE HR hard court reconditioner
· Undo the securing bolts on the lower cams.
· Adjust the lower cams until they touch the carrying arms
(Fig. 10.3.2-3),
· Retighten the securing bolts.
10.3.3 Adjusting the lateral weeders
After the working depth has been set, you need to bring the lateral weeders on the side ends of the front tine bars to the working depth.
Procedure:
· Switch on the universal joint shaft and lower the machine until the desired working depth is achieved.
· Switch off the universal joint shaft and tractor.
· Undo the securing bolts on the lateral weeders.
· Adjust the harrow until it is about 2 cm above the ground (Fig.
10.3.3),
· Retighten the securing bolts.
The lateral weeders should never penetrate the soil while the machine is in operation, otherwise they would create a small groove.
74
GBK / GNK / HR BAF0004.0 01.09
10.3.4 Adjusting the lateral brushes
AMAZONE HR hard court reconditioner
The two lateral brushes level the soil between the tracks. In their working position, the lateral brushes should be about 1 cm above the ground in order to achieve the best result.
They are adjusted as follows:
· Lower the machine to working depth and engage the universal joint shaft.
· Switch off the shaft and tractor.
· Set the brush height using the adjusting screw (Fig. 10.3.4-1/1).
· Secure the adjusting screw with the lock nut.
· The mounting bolt (Fig. 10.3.4-2) is used to adjust the angle of the brush.
GBK / GNK / HR BAF0004.0 01.09
75
AMAZONE HR hard court reconditioner
10.3.5 Adjusting the rear brush
The surface is smoothed again with the rear brush.
The scraper is pressed down under its own weight, so no further adjustment is needed.
The brush is merely lowered.
· Lower the machine to working depth.
· Lower the brush to the ground (Fig. 10.3.5-1).
· Lock the brushes in the upper position for transport.
(Fig. 10.3.5-2).
Raising the machine also raises the brushes off the ground.
76
GBK / GNK / HR BAF0004.0 01.09
10.3.6 Use on heavily compacted sports courts
AMAZONE HR hard court reconditioner
To loosen compacted soils, the carrying arms must be locked using the cams, so the weight of the roller is placed on the reciprocating power harrow (see section 8.2.1).
Comment:
Tamped areas must have a certain moisture content for the area to be revived - one or two days after rain, for example. The tines will wear prematurely if the machine is used in overly dry conditions.
10.3.7 Weekly maintenance of compacted soil
The weekly maintenance of hard sports courts involves loosening, sweeping and re-tamping 1 to 2 cm of the surface layer. This can be carried out using the HR hard court reconditioner, with the fixed tine bars of the harrow being replaced by a combination of a scarifier bar in front of and a scraper bar behind the reciprocating power harrow.
10.3.8 Adjusting the front scarifier bar
For hard sports courts, we recommend weekly maintenance with the scarifying bar at its maximum angle. Set the tine bars more vertically for more aggressive scarifying work. Adjustment of the angle is described in section 9.2.2.
GBK / GNK / HR BAF0004.0 01.09
77
AMAZONE HR hard court reconditioner
10.3.9 Adjusting the rear brush
The scraper bar, attached on the back of the reciprocating power harrow for weekly maintenance of tamped areas, levels the surface worked by the tines of the scarifier. The bar must be set so that the brushes touch the surface in their operating position.
To adjust the scraper bar:
· Lower machine to working depth.
· Undo the mounting bolts on both sides of the scraper bar
(Fig. 10.3.9).
· Set the bar to the desired height and lock it in this position using the mounting bolts.
10.4 Care of sandy artificial turf
You only need to fit the scraper bars to the front and rear of the reciprocating power harrow to brush sand into artificial turf surfaces and for their regular care. The brushes level the tracks of the players and brush the sand into the turf. The ground can be used immediately after treatment by the HR hard court reconditioner.
10.5 Adjusting the brush bars
Both brush bars must be set to the same working height for use on sanded artificial turf. The adjustment is described in section 10.2.9.
78
GBK / GNK / HR BAF0004.0 01.09
AMAZONE HR hard court reconditioner
NOTES
............................................................................................................................................................
............................................................................................................................................................
............................................................................................................................................................
............................................................................................................................................................
............................................................................................................................................................
............................................................................................................................................................
............................................................................................................................................................
............................................................................................................................................................
............................................................................................................................................................
............................................................................................................................................................
............................................................................................................................................................
............................................................................................................................................................
............................................................................................................................................................
............................................................................................................................................................
............................................................................................................................................................
............................................................................................................................................................
............................................................................................................................................................
............................................................................................................................................................
............................................................................................................................................................
............................................................................................................................................................
............................................................................................................................................................
............................................................................................................................................................
............................................................................................................................................................
............................................................................................................................................................
............................................................................................................................................................
............................................................................................................................................................
............................................................................................................................................................
............................................................................................................................................................
............................................................................................................................................................
............................................................................................................................................................
............................................................................................................................................................
............................................................................................................................................................
............................................................................................................................................................
............................................................................................................................................................
............................................................................................................................................................
............................................................................................................................................................
............................................................................................................................................................
............................................................................................................................................................
GBK / GNK / HR BAF0004.0 01.09
79
AMAZONE HR hard court reconditioner
H. DREYER GmbH & Co. KG
Postfach 51
D-49202 Hasbergen-Gaste
Germany
Phone: +49 5405 501-0
Fax: +49 5405 501-234 e-mail: [email protected] http:// www.amazone.de az S.A. FORBACH
17, rue de la Verrerie – BP 90106
F-57602 FORBACH Cedex
France
Tel.: + 33 (0)3 87 84 65 70
Telefax: + 33 (0)3 87 84 65 71 e-mail: [email protected] http:// www.amazone.fr
BBG Bodenbearbeitungsgeräte
Leipzig GmbH & Co.KG
Rippachtalstr. 10
D-04249 Leipzig
Germany
Branch plants: D-27794 Hude · D-04249 Leipzig, Germany ·
F-57602 Forbach, France
Subsidiary plants in England and France
Manufacturers of mineral fertiliser spreaders, field sprayers, seed drills, soil tillage machines, multipurpose warehouses and communal units
80
GBK / GNK / HR BAF0004.0 01.09
advertisement
* Your assessment is very important for improving the workof artificial intelligence, which forms the content of this project
Related manuals
advertisement