advertisement
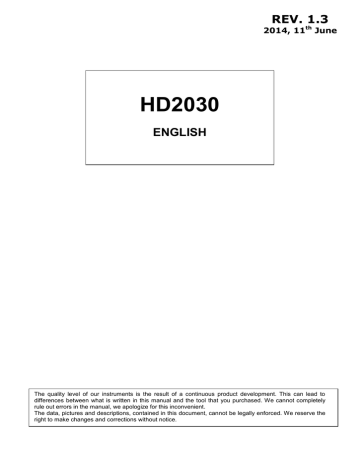
REV. 1.3
2014, 11
th
June
HD2030
ENGLISH
The quality level of our instruments is the result of a continuous product development. This can lead to differences between what is written in this manual and the tool that you purchased. We cannot completely rule out errors in the manual, we apologize for this inconvenient.
The data, pictures and descriptions, contained in this document, cannot be legally enforced. We reserve the right to make changes and corrections without notice.
Vibration Analyzer
HD2030
- 2 -
CONNECTORS AND KEYBOARD
The tool is endowed with keyboard with 13 keys, six connectors on the top and three connectors on the bottom. On the top there is also the memory card slot.
With reference to the figure at page 2 there are:
1 Slot for SD memory card with a maximum size of 2GB.
2 4 poles LEMO-B type connector for the connection of a triaxial or monoaxial accelerometer with integrated electronics (type IEPE or compatible).
3 6 poles LEMO-B type connector for the analog outputs (LINE) of the 4 input channels.
4 LEFT arrow key on the keypad: in the graphic mode it moves left the cursor or the two active cursors (blinking). In VLM mode it allows to scroll the VLM_1, …, VLM_4 screens. In the spectrum mode, it allows to switch from acceleration viewing to speed and displacement viewings.
5 CURSOR key on the keypad: in graphic mode it allows to select one of the two cursors or both of them. Holding pressed the CURSOR key for at least 2 seconds when the third-octave spectrum is displayed, the limit acceleration curve tracking is activated.
6 HOLD key: it temporarily stops the display update.
7 MENU key: it allows to access the configuration menu and the programs list. With the same key, the menu is exited to go back to the measure mode.
8 REC (recording) key: in combination with START / STOP / RESET, it activates the continuous data recording in the memory. If it is hold pressed for at least 2 seconds, it is possible to memorize what it is displayed as single record or to start the vocal recording.
9 PAUSE/CONTINUE key: to put in pause mode the integrated measures. From PAUSE mode, press the same key to start again the integrated measures. In PAUSE mode, the measures are reset if the
START / STOP / RESET key is pressed.
10 UP arrow key: in menu mode, it selects the previous row or increases the selected parameter. In
VLM screen, it adjusts the boundaries of the horizontal bar. In graphical mode it decreases the initial and final levels of the vertical scale; in this way, the graph is moved upward.
11 LEFT arrow key: in menu mode, it is used to edit the parameters with attribute. In VLM screen, it changes the measure unit. In graphic mode, it compresses the vertical scale.
12 MiniDin type connector for RS232C serial port. For the connection to a PC RS232 port or to the
HD40.1 printer, it is necessary to use the adequate null-modem serial cable (HD2110CSNM code), provided with a D-sub 9 poles connector.
13 Male connector for external power supply (∅ 5.5mm-2.1mm socket). It requires a
9…12Vdc/300mA power supply. The power supply positive pole must be connected to the central pin.
14 USB connector type B to connect the vibration analyzer to the USB port of a PC using a standard
USB cable with type A and B connectors (CP22 code).
15 DOWN arrow key: in menu mode, it selects the subsequent row or decreases the selected parameter. In VLM screen, it changes the limits of the horizontal bar. In graphic mode, it increases the initial and final levels of the vertical scale; in this way, the graph is moved downward.
16 RIGHT arrow key: in menu mode, it is used to edit the parameters with attribute. In graphic mode, it expands the vertical scale. In the VLM screen, it changes the measure unit.
17 ENTER key: it confirms the insertion of the data or the modification of a parameter.
18 START/STOP/RESET key: if pressed in STOP mode, it starts the measurements (RUN mode). In
RUN mode, it stops the measurements. If pressed in PAUSE mode, it resets the values of the integrated measures like Aeq, MAX/MIN levels, etc ...
19 CHN key: it selects the four measuring channels CH1, ..., CH4 (circular scrolling).
20 MODE key: it selects in a circular sequence the different instrument visualizing modes: VLM, timing profile, octave or third-octave spectra, distribution of probability and percentile levels.
21 ON/OFF key: to turn on and shutdown the instrument.
22 RIGHT arrow key on keypad: it moves right the cursor or the two active cursors (blinking). In VLM mode, it allows to scroll the VLM_1, …, VLM_4 screens. In the spectrum mode, it allows to switch from acceleration viewing to speed and displacement viewings.
23 4 poles LEMO-B type connector for the connection of a monoaxial accelerometer with an integrated electronics (type IEPE or compatible).
24 3.5 mm jack connector for the connection of a microphone for vocal recordings.
25 4 poles LEMO-00 type connector for the trigger output.
26 3.5 mm jack for the connection of headphones.
- 3 -
CERTIFICATO DI CONFORMITÀ DEL COSTRUTTORE
MANUFACTURER’S CERTIFICATE OF CONFORMITY rilasciato da issued by
DELTA OHM SRL
STRUMENTI DI MISURA
DATA
DATE
2014/06/11
Si certifica che gli strumenti sotto riportati hanno superato positivamente tutti i test di produzione e sono conformi alle specifiche, valide alla data del test, riportate nella documentazione tecnica.
We certify that below mentioned instruments have been tested and passed all production tests, confirming compliance with the manufacturer's published specification at the date of the test.
Le misure effettuate presso un Laboratorio di Taratura Accredia sono garantite da una catena di riferibilità ininterrotta, che ha origine dalla taratura dei campioni di prima linea del Laboratorio presso l’istituto metrologico nazionale.
Measurements performed in an Accredia Calibration Laboratory are guaranteed by a uninterrupted reference chain which source is the calibration of the Laboratory first line standards at the national metrological institute.
Tipo Prodotto:
Product Type:
Nome Prodotto:
Product Name:
Vibration Analyzer
Analizzatore di vibrazioni
HD2030
DELTA OHM SRL
35030 Caselle di Selvazzano (PD) Italy
Via Marconi, 5
Tel. +39.0498977150 r.a. - Telefax +39.049635596
Cod. Fisc./P.Iva IT03363960281 - N.Mecc. PD044279
R.E.A. 306030 - ISC. Reg. Soc. 68037/1998
- 4 -
INSTRUMENT OVERVIEW
Block Diagram of HD2030
Channels
XYZ
Channel
E
LINE output
Screen
Keyboard
Memory card
Flash Memory
RS232 Port
USB Port
I/O Trigger
Block Diagram of the tool
The block diagram represents the main elements of the HD2030 vibration analyzer.
Measure channels
HD2030 has four input channels polarized with direct current at 25V. It is possible to connect accelerometers with an amplifying integrated electronics IEPE (or similar) type that needs a maximum current of 2mA. It’s possible to connect to the RIGHT input a tri-axial type accelerometer or up to three monoaxial accelerometers; to LEFT input it’s possible to connect a monoaxial type accelerometer.
The amplified electrical signal of the four channels is sent to the LINE output.
The instrument
The amplified signal of the four channels is converted into digital samples through as many 25-bit A/D converters and digitally elaborated by two DSP.
The weighted levels and the related spectra of each channel are then transferred from the DSP to the microprocessor that manages the display and the storage.
The microprocessor supervises all the instrument processes: the management of the calibration, the Flash memory and the memory card, the display, the keyboard and the serial multi-standard RS232C/USB interface.
- 5 -
How to connect the accelerometers to the analyzer
The following diagram illustrates the different parts necessary to connect the accelerometers to the HD2030. The left input is monoaxial, the right input is triaxial.
- 6 -
INTRODUCTION
The HD2030 is a portable vibration analyzer able to perform spectral and statistical analysis. The instrument can supply all the measurement parameters required by the current normative concerning the operators protection from the risk connected with the vibra-
tions and is able to measure in hand-arm and whole body modes. It is also possible to evaluate the annoyance on persons due to vibration in buildings.
The instrument has been designed mixing the easy to use concept with the maximum flexibility and the possibility to update the instrument with the evolving standards on vibrations. The firmware can be updated directly by the user through the supplied Noise Studio
software (basic version).
HD2030 analyzer can perform all measurements requested by technical standards concerning workers protection from the risk of mechanical vibrations exposure.
The HD2030 complies with the specifications of ISO 8041 (2005) and ISO 5349-1 (2001
- vibrations transmitted to the hand-arm system) and ISO 2631-1,2 and 4 (1997 – vibrations transmitted to the whole body).
The octave and third-octave filters comply with the class 1 specifications of IEC 61260.
The HD2030 is a vibration analyzer suitable for the following applications:
• Evaluation of the exposure of operators to the risk connected with the vibrations transmitted to the hand-arm system through vibrating tools or items subjected to vibrations or impacts;
• Evaluation of the operator exposure to the risk connected with vibrations transmitted to the whole body also through the use of movement or transportation ways;
• Evaluation of the operator exposure to the risk connected with vibrations transmitted to the whole body by buildings subjected to vibrations or impacts;
• Octave or third-octave bands spectral analysis;
• Statistical analysis with calculation of the percentile levels from L
1
to L
99
;
• Attenuation of vibrations and reclamations.
The HD2030 analyzer simultaneously acquires the acceleration value in 4 channels and calculates, in parallel for all channels, both the weighted acceleration values and the
octave or third-octave bands spectra. In addition to the instant and average acceleration values, the analyzer also elaborates peak levels, vibration dose (VDV) and crest factors.
The frequency weighting can be chosen freely according to the specific application.
The possibility to connect any type of accelerometer with integrated electronics (type
IEPE or compatible), both triaxial and monoaxial, ensures the maximum ease of use and reduces the possibility of making mistakes or taking measures affected by electromagnetic interference or noise. The acquisition of the acceleration in 4 channels allows, for example, to make objective evaluation of the vibrations transmitted by a transportation way through to the driving seat or to evaluate, during the design and the production verification, the effectiveness of damping introduced by the suspension and by the absorbent material of the seat itself.
A versatile data logging function stores, both in the 8MB internal memory and in the memory card (SD up to 2GB), multiple profiles and spectra. Moreover it is possible to add to the profiles the accelerometers signals recording directly the digital samples. When analyzing the memorized data, it is then possible to examine the signals provided by the accelerometers and calculate additional parameters or verify the absence of source of errors such as those due to the DC-shift phenomenon. Each recording can be associated with a vocal comment. Using the available audio channel, it is possible to record an audio signal up to one hour, as a further opportunity to document the measures.
The performed recordings can be reviewed using the provided "Memory Navigator" program of the HD2030 analyzer. The vocal comments associated with the recordings can be listened using the appropriate headphones output.
- 7 -
Simultaneously to the acquisition of the profiles, it is performed the octave or third-
octave bands real time spectral analysis. The vibration analyzer calculates the spectrum of the sound signal every second and integrates it linearly up to 99 hours. It is also possible to associate with the spectrum a frequency weighted measurement parameter whose value is calculated from the acceleration values of each octave or third-octave spectrum band. In addition to the acceleration values for each band of the spectrum, it is possible to display the speed or displacement value.
The choice to measure hand-arm (HA) or whole-body (WB and BV) modify the extension of the spectral analysis: while for the hand-arm measures the frequency range extends from
3.15Hz to 3.15kHz (from 4Hz to 2kHz octave band spectrum), for whole-body measurements the range of the central frequency is shifted towards low frequencies from 0.315Hz to 315Hz
(from 0.5Hz to 250Hz in octave bands) .
As statistical analyzer, the HD2030 calculates the probability distribution of a measurement parameter at choice and analyzes it in classes of 1dB. In addition to the chart of probability distribution, it is also supplied the graph with percentile levels from L
1
to L
99
.
The LINE type not weighted analog outputs allows to record, for subsequent analysis, the accelerometers signal on a tape or directly in a PC with an acquisition board.
The calibration can be done using the accelerometers calibration data or using a vibrations generator able to produce a known and stable acceleration. A reserved and protected area in the permanent memory is used to record the last 120 calibrations performed. The supplied Noise Studio interface software allows to control the instrument and accelerometers and to document the measurements by downloading automatically the register file of the instrument calibrations.
In order to easily carry out the different measurements on the field, in the HD2030 it is possible to store up to 10 customizable and editable setups, also using the Noise Studio software. A title is associated with each setup in order to easily choose the desired one.
Considering that in order to measure in every possible situation it is necessary to use different types of accelerometers, up to 9 different sensor configurations both for the right channel (triaxial) and for the left channel (monoaxial) can be selected based on the requirements. The sensors calibrations and configurations files are associated with the analyzer setups, so that, by choosing one of the stored setups, the sensors to be connected to the input channels are indicated and the last associated calibration values are automatically uploaded.
To simplify the reading of the data on the display, it is possible to disable one of the two inputs or the single measurement channel.
The check of the vibration analyzer functionality can be done directly by the user, in the field, thanks to a diagnostic program.
HD2030 can be completely controlled by a PC through the RS232 and USB serial interfaces, using an adequate communication protocol.
The Noise Studio interface software allows to download and display data stored in the instrument, to handle the files related to setups, calibrations and configurations. With the software it is possible to load in the analyzer up to 10 different setups, chosen among the available ones. The file related to calibrations is downloaded at every connection and it is saved together with the measurement data. The different sensors configurations can be programmed through the PC, both inserting manually the accelerometers data and also using the proper CD-ROM associated with the accelerometers that can be supplied by Delta Ohm together with the instrument.
- 8 -
DESCRIPTION OF DISPLAY MODES
The acceleration values and the calculations made by the HD2030 analyzer are presented in 5 different screens. The instrument analyzes simultaneously the acceleration signals on 4 axis associated with four measurement channels (CH1,…, CH4.). It is possible, in each screen, to choose the channel to display by simply pressing the CHN key.
When the instrument is switched on, it briefly shows the Delta Ohm logo and the program version. Then it is requested the selection of the configuration for the sensors connected to the two inputs: first the right triaxial input, than the left monoaxial one.
CONFIG. RIGHT #02
PROD: DELTA
MOD: ACC_TRI
S.N.: 123456
TYPE: ACC
SENS: 10mV/g CAL
RANGE: 500
SEL. PREV. NEXT.
For both inputs, press PREV or NEXT to scroll the memorized sensor list, SEL to confirm.
Then, the instrument enters the VLM (Vibration Level Meter) mode, displaying in numerical form 3 instant or integrated measurement parameters. right input is disabled, CH1, CH2 and CH3 channels do not appear. If it is disables the left input, the CH4 channel does not appear.
The selection of the #00 (zero) configuration disables the corresponding input: if the
If there is an external memory card, after the initial screen, the configuration files are loaded and the following screen appears:
MC installed and ready.
1000MB Size:
ESC RD RD/WR
Press RD/WR to enable all the reading and writing functions and continue with the selection of the configurations.
Now the instrument is ready for the use (for the details about the sensors setup, see the
SENSORS SETUP program description).
- 9 -
The possible screen modes are:
• VLM (Vibration Level Meter): divided into four screens with three measurement parameters each. The values displayed in numerical form are updated every second. o
VLM_1: 3 profiles of instant or integrated measurement parameters calculated on each of the four channels; o
VLM_2: 3 profiles of instant or integrated measurement parameters calculated on the vector built with the data of the first three channels (RIGHT input); o
VLM_3: 3 parameters integrated in all the measurement time and calculated on each of the four channels; o
VLM_4: 3 parameters integrated on all the measurement time and calculated on the vector built with the data of the first three channels (RIGHT input).
• PROFILE: graphical form profile of a chosen parameter, related to the acceleration on each channel calculated at programmable intervals from 1s to one hour. The last 100 values of the chosen parameter are visualized.
• SPECTRUM: graph of the octave or third-octave bands spectrum graphic, related to the acceleration on each channel. A wide band parameter, calculated from the measured spectra, is associated with the spectrum. In addition to the accelerations, it is possible to visualize the speeds or the displacements, making a single or double integration on the spectrum. The spectrum can be visualized in multi-spectrum mode (MLT: one spectrum per second) or in averaged spectrum (AVR) where the spectrum is linearly integrated in all the measurement time.
• PROBABILITY: graph of the probability distribution of the parameter visualized in the
PROFILE screen for each channel. The values are analyzed in classes of 1dB.
• PERCENTILES: graph of percentile levels related to the parameter visualized in the
PROFILE screen for each channel.
The transition from one screen to the next one can be made at any time by pressing the
MODE key. At start-up, after the selection of the inputs configuration, the instrument displays the VLM screen.
Some indications appear in all the modes, they are:
The indicator of the acquisition status,
The overload indicator,
The indicator of the remaining batteries charge.
Current Overload
Overload memory
Subfield memory
Current subfield
RUN
PAUSE
REC
STOP
Hold
Replay
The first symbol in the top left corner of the display indicates the acquisition status of the vibration analyzer.
RUN: the instrument is acquiring.
PAUSE: the calculation of the integrated measures and the eventual measures recording are paused. The instant parameters continue to be measured and visualized.
REC: The instrument is acquiring and recording.
- 10 -
STOP: the instrument does not perform any measurement.
H (HOLD): the calculation of the integrated measurements has come to the end of the integration interval or the HOLD key was pressed.
P (Print): the printing of the current data is running.
R (Replay): it appears (blinking) when the “MEMORY NAVIGATOR” program is used to display a file saved in the instrument memory.
Immediately to the right of the symbol indicating the acquisition mode, there is the symbol indicating the possible overload. An arrow pointing up indicates that the input level has exceeded the maximum level measurable, a down arrow indicates that the input level is below the minimum according to the selected gain.
The maximum measurable level in the different settings of the measurement range selector is indicated in the technical specifications (see the chapter "TECHNICAL
SPECIFICATIONS").
An internally empty arrow reminds that an overload occurred, while a full arrow indicates that the signal is currently exceeding the limit.
To the right of the overload indicator it is displayed the integration time Tint of the instrument, which is programmable from 1s to 99h. When the integration mode is set to
multiple, the "Tint" symbol in the VLM screen blinks. If Tint = 0, the integration is becomes continue.
In the upper right corner there is the battery symbol. The batteries discharge appears as a gradual emptying of the symbol. When the remaining working time of the instrument is about 10%, which is roughly correspondent to 30 minutes in the continuous acquisition, the battery symbol blinks. A protective device prevents the instrument from taking measurements with insufficient charge level and automatically shuts the instrument off when the charge level is reduced to a minimum.
The charge level of the batteries, expressed in percentage, is visible in the menu main screen, that can be accessed pressing the MENU key once. Press the MENU key again to return to the measurement screen.
For details, see the chapter "REPORTING OF LOW BATTERIES AND REPLACEMENT OF
BATTERIES."
Pressing the ENTER key, the parameters related to the visualized screen can be selected in sequence. While the selected parameter is blinking, it is possible to change it pressing the
UP and DOWN arrow keys. Pressing ENTER, or automatically after about 10s, the parameter is confirmed and the selection mode is exited.
In graphic visualization mode it is possible to change the parameters of the vertical scale using the UP, DOWN, LEFT and RIGHT arrow keys: the LEFT and RIGHT keys compress and expand the vertical scale respectively, the UP and DOWN keys decrease and increase the initial and final levels of the vertical scale; in this way the graphic is moved upwards and downwards respectively.
- 11 -
VLM S
CREEN
Integration Interval
Minimum Level
Visualized channel
Acquisition time
Maximum Level
Weighting
Bar indicating the
Instant level
Visualized parameters
The VLM screens shows, in numerical form, three frequency weighted parameters related to each of the four measurement channels or to the acceleration vector calculated with the data of the first three channels. It is possible to scroll in sequence the screens using the
right and left cursor keys.
The horizontal bar visualizes the instant levels of the four measurement channels expressed in dB.
VLM_1 and VLM_2
The first two screens VLM_1 and VLM_2 present instant and integrated parameters that are acquired, and in case memorized, as a profile form with 1 second acquisition interval or integrated with intervals programmable from 10s to 1 hour. In the VLM_2 screen are visualized the parameters related to the channels of the vector acceleration sum (CHΣ) and maximum (CHM). The measurement parameters to be displayed can be set entering the menu Parameters >> Vibration Analyzer.
VLM_3 and VLM_4
The last two screens VLM_3 e VLM_4 present global parameters integrated in all the
measurement period. It is possible to automatically memorize the value of these parameters at the end of each measurement session. In the VLM_4 screen are visualized the parameters related to the channels of the vector acceleration sum (CHΣ) and maximum
(CHM). These measurement parameters can be set entering the menu Parameters
>> Data Logger >> Global.
To change the measurement unit without entering the instrument menu, it is suffi-
cient to use the RIGHT and LEFT arrow keys. The measurement units are dB, m/s 2 , cm/s 2 , ft/s 2 , in/s 2 , g. The measurement unit selected is unique and it is applied to all the visualized parameters.
The CHN key allows to change the visualized channel. The measurement channels of single axis acceleration are four (CH1,…, CH4) while the measurement channels of the vector acceleration are two: the “sum” vector (CHΣ) and the “maximum” vector (GHM), both calculated with the data of the first three measurement channels (RIGHT input).
The “sum” vector is defined by the relation: a
SOMMA v
=
(
C 1 * ch 1 a
P 1
2
) (
C 2 * a
P ch 2
2
2
) (
C 3 * a ch 3
P 3
)
2
While the “maximum” vector is defined by the relation: a
MASSIMO v
= max
[
(
C 1 * ch 1 a
P 1
) (
C 2 * a ch 2
P 2
C 3 * ch 3 a
P 3
)
]
2
- 12 -
Where:
• C1, C2 and C3 are the multiplying coefficients for each channel that can be set through the menu Parameters>> Instrument >> Measurement>> Coeff.1, Coeff.2 and Coeff.3
• a ch1
P1
, a ch2
P2
, a ch3
P3
are pondered acceleration found on each of the three channels. The frequency weightings are set in the menu Parameters>> Instrument >> Measurement>> Pond.1, Pond.2 and Pond.3.
From the menu (MENU>> Parameters>> Instrument >> Measure>> Ch1-4), it is poss-
ible to disable one or more measurement channels, for example because they are not in use. The status of each channel is indicated in the menu with a number: 0 (zero) indicates a disabled channel, 1 indicates an active channel.
The four channels are indicated in the order CH1, CH2, CH3, CH4: in order to have all the channels activated, the menu item must be Ch1-4=1111. To disable the CH1 channel, for example, the menu item must be Ch1-4=0111. It is not possible to disable all the channels at the same time.
When one or more of the channels CH1, CH2 or CH3 are disabled, the measurements related to the “sum” and “maximum” vector are not visualized on the display.
The visualized measurement parameters can be changed without entering the menu of the instrument. Pressing the ENTER key while the instrument is in STOP mode, the di-
rectly editable parameters can be scrolled in sequence. When the selected parameter blinks, it is possible to modify it using the UP and DOWN arrows.
The changeable parameters are:
• Integration time (Menu >> Parameters >> Instrument >> Measurement >> Integration Interval).
Settable from 1s to 99 hours (when it is set to 0 the integration is continuous). Pressing the RIGHT arrow while the value is blinking, the multiple integration mode is selected
(Menu >> Parameters >> Instrument >> Measure >> Integration Mode). To set the
single integration mode, it is sufficient to press the LEFT arrow. When the integration mode is multiple, the symbol “Tint” blinks to indicate that the instrument will execute many integration intervals in sequence, each of them with a duration equal to the integration time set.
• The three measurement parameters of acceleration (Menu >> Parameters >> Vibration Analyzer) for the three parameters related to each channel, to sum vector and maximum value associated with VLM_1 and VLM_2 screens. For VLM_3 and VLM_4 screens, the acceleration measurement parameters changeable directly, are the ones in
Menu >> Parameters >> Data Logger >> Global.
When one of the acceleration measurement parameters is selected, the parameter symbol blinks. Pressing the UP and DOWN arrows it is possible to scroll in sequence all the measurement parameters available.
• The frequency weighting applied to each measurement channel (Menu >> Parameters
>> Instrument >> Measure >> Pond. Ch-x with x=1,..,4). While the frequency weighting symbol blinks, it is possible to modify the weight using the UP and DOWN arrows. The weighting can be changed only in VLM_1 and VLM_3 screens. The VLM_2 and VLM_4 screens report the abbreviation of the weightings applied to the three channels CH1, CH2 and CH3: e.g. “zch” means CH1=Fz, CH2=Fc and CH3=Wh.
- 13 -
P ROFILE S CREEN
Integration Interval
Visualized Parameter
Integration Time
Maximum Level
Scale Factor
Profile
Minimum Level
Frequency Weighting
Selected Channel
Sampling Interval
This screen presents in graphic form the profile of a frequency weighted parameter related to each of the 4 measurement channels.
The values can be visualized in dB or in m/s 2 (Menu >> Parameters >> Instrument >>
Measure >> Measurement Unit).
The CHN key allows to change the visualized channel.
With the LEFT and RIGHT arrow keys it is possible to change the vertical scale of the graph while with the UP and DOWN arrow keys it is possible to choose the reference value of the vertical scale.
It is possible to activate two cursors to read the value in two points at choice of the graph. Pressing the CURSOR key once, the first cursor is activated, pressing the second time, the second cursor is activated while pressing the CURSOR key the third time, both cursors are activated in tracking mode. To place the cursors in the desired points, the arrow keys next to the CURSOR key can be used.
Using the HOLD key, the graph updating is paused, allowing a comfortable reading of the measured values. Press again the HOLD key to return to real time visualization.
The sampling time of the graph can be selected from 1s up to 1 hour per point.
The parameter selected for this screen is the same used for the statistical analysis (see
PROBABILITY and PERCENTILES screens) with a 1s sampling interval.
The visualized measurement parameters can be modified without entering the menu of the instrument. Pressing the ENTER key while the instrument is in STOP mode, the di-
rectly changeable parameters can be scrolled in sequence. When the selected
parameter blinks, it is possible to modify it using the UP and DOWN arrows.
The editable parameters are:
• The acceleration measurement parameter (Menu >> Parameters >> Vibration Analyzer >> Profile). Pressing the UP and DOWN arrows, it is possible to scroll in sequence all the measurement parameters available.
• The sampling interval of the measurement parameter (Menu >> Parameters >> Instrument >> Measurement >> Sampling Profile). It can be set from 1s up to 1 hour.
• The integration interval (Menu >> Parameters >> Instrument >> Measurement >>
Integration Interval). It can be set from 1s to 99 hours (when it is set to 0, the integration is continuous).
• The frequency weighting (Menu >> Parameters >> Instrument >> Measurement
>>Wh. Ch-x with x=1,..,4). The parameter is associated with the measure channel visualized. To modify it, use the UP and DOWN arrows.
- 14 -
S PECTRUM S CREEN
Integration Interval
Visualized Parameter
Integration Time
Maximum Level
Octave and third octave band spectrum
Scale Factor
Level with a large band
Minimum Level
Frequency Weighting
Selected Channel
The SPECTRUM screen presents in graphic form the octave or third-octave bands spectrum related to each of the 4 measurement channels. The order of the visualized spectrum, in octave or third-octave bands, is set entering the Menu >> Parameters >> Spectrum Analyzer
>> Order.
The values can be visualized in dB or in m/s 2 .
The CHN key allows to change the visualized channel.
With the LEFT and RIGHT arrow keys it is possible to change the vertical scale of the graph while with the UP and DOWN arrow keys it is possible to choose the reference value of the vertical scale.
The spectral analysis is made both in multi-spectrum mode (MLT), where a spectrum every second is visualized, and in average spectrum mode (AVR), where the spectrum integrated in all the measurement time is visualized.
It’s possible to associate with the octave or third-octave bands spectrum, the value of the frequency weighted acceleration, calculated from the spectrum.
CURSORS OPERATION
It is possible to activate two cursors to read the value of the visualized bands. Pressing the CURSOR key once, the first cursor is activated, pressing the second time, the second cursor is activated while pressing the CURSOR key the third time, both cursors are activated in tracking mode. To place the cursors in the desired points, the arrow keys next to the CURSOR key can be used.
When the cursors function is not active, it is possible to pass from the visualization of the acceleration for each band to the speed or displacement visualization, pressing in sequence the left and right cursor keys.
Using the HOLD key, the graph updating is paused, simplifying the reading of the measured values. Press again the HOLD key to return to the real time visualization.
Keeping pressed the cursors activation key, the limit acceleration curve is
visualized. This curve is based on the acceleration value in the band selected with the cursor
L1 and presents for each band the limit value of the acceleration corresponding to a displacement equal to that of the selected band.
For example, it is possible to choose as reference band with the cursor L1 the band corresponding to the dominant frequency of the spectrum and, supposing that the displacement component at this frequency is also dominant, visualize the maximum acceleration levels on the other bands of the spectrum that cause displacement values equal to or lower than the one of the selected band. Eventual phenomena of DC-shift happen with acceleration values at low frequencies with unreal associated displacements and so can be easily localized because they
- 15 -
will be associated with values of acceleration at low frequencies greater than the visualized limit.
To disable the limit acceleration curve keep pressed the CURSOR key.
The visualized measurement parameters can be modified without entering the
menu of the instrument. Pressing the ENTER key while the instrument is in STOP mode, the directly changeable parameters can be scrolled in sequence. When the selected parameter blinks, it is possible to modify it using the UP and DOWN arrows.
The changeable parameters are:
• The integration interval (Menu >> Parameters >> Instrument >> Measure >> Integration Interval). It can be set from 1s to 99 hours (when it is set to 0, the integration is continuous)
• The frequency weighting of the acceleration value associated with the spectrum
(Menu >> Parameters >> Spectrum Analyzer >> Auxiliary weight). This parameter is changeable also in measuring mode.
• The type of the visualized spectrum MLT or AVR (Menu >> Parameters >> Spectrum Analyzer >> Mode). This parameter is changeable also in measuring mode.
- 16 -
D ISTRIBUTION OF P ROBABILITY S CREEN
Visualized parameter Integration Time
Maximum Level
Scale Factor
Frequency Weighting
Minimum Level
Selected channel Probability
The PROBABILITY screen presents in graphic form the probability distribution of the values of the parameter visualized in the PROFILE screen for each of the 4 channels.
The values can be visualized in dB or in m/s 2 .
The CHN key allows to change the visualized channel.
With the LEFT and RIGHT arrow keys it is possible to change the vertical scale of the graph while with the UP and DOWN arrow keys it is possible to choose the reference value of the vertical scale.
CURSORS WORKING
It is possible to activate two cursors to read the probability in two points at choice in the graph or, when they are both selected, to calculate the probability to have a value between the two cursors. Pressing the CURSOR key once, the first cursor is activated, pressing the second time, the second cursor is activated while pressing the CURSOR key the third time, both cursors are activated in tracking mode. To place the cursors in the desired points, the arrow keys next to the CURSOR key can be used.
The statistical analysis is done in 1dB classes, sampling the value of the parameter selected for the PROFILE screen once per second for each of the 4 channels.
The visualized measurement parameters can be modified without entering the
menu of the instrument. Pressing the ENTER key while the instrument is in STOP mode, the changeable parameters can be scrolled in sequence. When the selected parameter blinks, it is possible to modify it using the UP and DOWN arrows.
The editable parameters are:
• The acceleration measurement parameter (Menu >> Parameters >> Vibration Analyzer >> Profile).
• The frequency weighting (Menu >> Parameters >> Instrument >> Measurement >>
Wh. Ch-x with x=1,..,4). The parameter is associated with the visualized measurement channel. To modify it, use the UP and DOWN arrows.
- 17 -
P ERCENTILES S CREEN
Visualized parameter Integration time
Frequency Weighting
Maximum Level
Scale Factor
Minimum Level
Selected Channel percentile level
Percentile screen presents in graphic form the percentile levels from L
1
to L with the parameter visualized in the PROFILE screen for each of the 4 channels.
99
associated
The values can be visualized in dB or m/s 2 .
CHN key allows to change the visualized channel.
With LEFT and RIGHT arrow keys you can change the vertical scale of the graphic while with UP and DOWN arrow keys you can chose the value in reference with the vertical scale.
CURSORS FUNCTIONS
It is possible to activate a cursor to examine the graph. Pressing the CURSOR key, the cursor is activated; in order to place the cursor in the desired point, the arrow keys next to the
CURSOR key can be used.
To facilitate the graph viewing, two dashed vertical bars are displayed in correspondence of 5 and 95%.
The visualized measurement parameters can be modified without entering the
menu of the instrument. Pressing the ENTER key while the instrument is in STOP mode, the changeable parameters can be scrolled in sequence. When the selected parameter blinks, it is possible to modify it using the UP and DOWN arrows.
Can be modified:
• The acceleration measurement parameter (Menu >> Parameters >> Vibration Analyzer >> Profile).
• The frequency weighting (Menu >> Parameters >> Instrument >> Measurement >>
Wh. Ch-x with x=1,..,4). The parameter is associated with the visualized measurement channel. To modify it, use the UP and DOWN arrows.
- 18 -
APPLICATIONS
The HD2030 analyzer can measure vibrations in three different applications selectable with the parameter Menu >> Parameters >> Instrument >> Measurement >> Application:
• Hand Arm (HA) for the measurements of vibrations transmitted to the hand-arm system, for example by tools through the grip.
• Whole Body (WB) for the measurements of vibrations transmitted to the whole body, for example to a driver through the seat.
• Building Vibration (BV) for the measurement of vibrations transmitted to the whole body by buildings.
In general, different applications require specific accelerometers which differ mainly for the sensitivity, frequency response, weight and mounting characteristics.
The accelerometers suitable for the HD2030 may be triaxial or mono-axial type with integrated electronics (IEPE or equivalent) and sensitivity from 1 mV/g to 1V/g.
These accelerometers are current-supplied by the analyzer with a bias voltage of 25V and a maximum current equal to 2mA.
Since the dynamic range of the accelerometer- analyzer chain is limited to about 100dB, in order to perform all types of vibration measurements (hand-arm and whole body vibration or buildings), accelerometers with different sensitivities are required. In fact, while for the measurement of vibration transmitted to the hand-arm can be used an accelerometer with a sensitivity from 1 mV/g to 10 mV/g, capable of measuring peak accelerations up to
5000 ÷ 50000 m/s2 , for the measurement of accelerations in buildings it is necessary to use accelerometers with a sensitivity of 1 V/g, in order to measure accelerations starting from
1 mm/s2.
H AND A RM
Many tools operated or gripped by hands generate vibrations. In some of these tools the vibration levels can be very high: for example, saws, hammers, grinders, drills, cleaners, vibrating plates, mowers, hammers, etc.. The vibration is transmitted to the operator's hands
(and arms) through physical contact with the utensil. In some cases vibration is transmitted directly by gripping the part to be machined (such as on a column grinder).
The procedures for measuring and assessing exposure of workers to hand-arm vibration are defined by ISO 5349-1 and ISO 5349-2. For measurements are used accelerometers with a sensitivity from 1 mV/g to 10 mV/g , reduced size and weight, capable to measure weighted accelerations of about 1m/s than 10000 m/s 2
2 while, at the same time, very high peak accelerations even higher
. In most practical situations will be used a miniature triaxial accelerometer, with a sensitivity of 10mV/g and resonant frequency greater than 10kHz. When the peak accelerations exceed 1000g repeatedly, it is necessary to use a shock accelerometer with 1mV/g sensitivity and resonant frequency greater than 50kHz. In this case also a mono-axial accelerometer is enough, taking care to orientate it so as to measure the accelerations along the dominant axis. For exposure assessment should be considered vibrations being transmitted to the center of the operator's hand during the tool’s grip and use. Since normally it is not possible to fix the accelerometer in that position, while this would constitute an obstacle to the operator, the accelerometer is fixed at the closest position to the one occupied by the hand (so that it would not constitute a disturbance to the use of the machine itself). The picture shows the position in which, according to ISO 5349-2, the accelerometer is attached to the handle of hammers and chipping hammers. In some cases, for the particular shape of the handles or the overall dimensions of the control lever, it is not possible to fix the accelerometer in accordance with the standard’s guidance. In this case an alternate location in the closest possible location to the operator's hand will be found. The demolition hammers have two handles, one of which cannot be used to fix
- 19 -
the accelerometer because it’s entire length it occupied by the operating lever: the transducer must be necessarily mounted on the handle without the lever.
These pictures show the possibility to mount the sensor for two different handles categories. The
ISO standard 5349-1 specifies the orientation of the reference system according to which are to be collected the three acceleration’s vector components; nevertheless, for each specific category of portable machine tool, ISO 8662 gives the definition of the specific coordinates to be adopted.
The standard defines the coordinate system:
• Z direction: the direction parallel to percussion direction; in ISO 5349-1 this axis takes the direction of the third metacarpal bone of the operator’s hand;
• Y-direction: the direction in the plane including the handle and the Z axis; orthogonal with the Z axis.
• X -direction: direction perpendicular to
Y and Z directions.
Since the ISO 5349-1 introduced as evaluation parameter the accelerations vector sum, the orientation of the coordinate system, purely conventional, does not affect the evaluation procedure; it is therefore independent of the reference system adopted.
Selecting the application Menu >> Parameters >> Instrument >> Measurement >> Application: HA, the HD2030 analyzer performs measurements in accordance with ISO 5349. The weighted acceleration (to simulate the the hand-arm system sensitivity), is calculated applying the filter named Wh on all measurement axes. Alternatively are available the band-pass filters
Fz and Fc, respectively, 1 Hz ÷ 3.5 kHz and 6.3 Hz ÷ 1250 Hz and the analyzer measures the accelerometer’s signals spectrum by octave bands from 4Hz to 2 kHz or third octave from
3.15 Hz to 3.15 kHz.
In the vibrations transmitted to hand-arm system, transducer’s mounting is the most delicate operation. The accelerometer weight should be less than 10% the weight of the tool and typically less than 30g including the weight of the mounting adapter. The accelerometer must be fixed to the handle so as to follow the oscillations, therefore allowing acquisition of vibrations effectively transmitted to the operator's hand.
HD2030AC1
The HD2030AC1 is a compact cube adaptor that is fixed with a plastic or metal strip to the handle of the tool to analyze. The position must be chosen as close as possible to that occupied by the hand according to the indications of ISO 5349-2. Light alloy built, it is suitable for measurements on lightweight tools where it is necessary to contain the weight of the measuring system. It can be used with accelerometers with a threaded hole (10-32 UNF or UNC 5-40); the accelerometer is secured by a screw on the adapter. This support ensures easy and quick mounting and optimum adaptation to different types of handles.
The accelerometer, equipped with a threaded hole (10-32 UNF 5-40 or
UNC), is secured to the adapter via a tightening screw which, passing through a hole on the
- 20 -
upper surface of the adapter, is screwed to the accelerometer base. The vibrations produced by percussive machine tools movement, are characterized by very high frequency and intensity acceleration’s spectral components. With this loads, the piezoelectric crystal, which implements acceleration’s transduction into electrical signal, is subjected to stress and generates a continuous spurious signal very high for a long time, even after the physical load has ended; the spurious signal overlaps the detected signal adding distortion to the measurement.
To avoid this phenomenon, called "DC shift", it is necessary to reduce the accelerometer’s loads at higher frequencies. Normally, the presence of dumping material on the handle or the interposition of a thin rubber layer (1-2 mm) between the support of the accelerometer and the handle, are sufficient to prevent the phenomenon (1 in the picture). The resilient material must be compressed to the maximum tightening of the clamp mounting of the support. To avoid damaging the resilient material while tightening, it is sufficient to interpose a alloy ring with a thickness of 1-2 mm between such material and the clamp (2 in the picture). The vibrations transmitted from the tool to the hand-arm will be properly represented only under certain conditions by the measurement made by fixing the accelerometer to the handle as previously described. In fact, by the tightening of the adapter to the handle depends the fraction of vibrational energy transmitted to the sensor and therefore measured. It’s evident that tightening the clamp to the maximum will be obtained a high mechanical coupling and therefore the measured acceleration will be maximum. However, not always by tightening the clamp to the maximum, it will be achieved a representative measure of the true stress the operator's hand is subjected to. Normally the operator tightening the handle exerts a variable grip strength, depending on the particular processing step and in any case a compromise between operational effectiveness and comfort. To detect the vibrations really transmitted by the tool to the operator it is sometimes convenient to use supports with specific shapes to be interposed between the hand and the handle.
HD2030AC2
HD2030AC2 and HD2030AC3 adapters must be gripped between the hand and the handle. As the accelerometer is fixed in a lateral position, the measurement must be repeated by placing the accelerometer on both sides of the hand.
These adapters are suitable for large cylindrical handles coated with resilient material.
HD2030AC3 having integrated screw (10-32 UNF); accelerometer is fixed to the adapter using the threaded hole. cured by a screw on the adapter.
The HD2030AC3 is steel made and has to be used with accelerometers
HD2030AC4
The HD2030AC2 is made of light alloy and fitted with accelerometers using a threaded hole (10-32 UNF or UNC 5-40); accelerometer is se-
The HD2030AC4 is an adapter to be held between the hand and the handle. The accelerometer is placed in central position between the middle finger and the ring finger or between the index and the middle fingers.
Light alloy made, it is suitable for anatomical shape, non-cylindrical and/or small dimension handles.
It must be uses with accelerometers fitted with a threaded hole (10-
32 UNF or UNC 5-40); accelerometer is secured by a screw on the adapter.
The spectral analysis is performed in the range 3.15Hz to 3150Hz. In the measurements of the vibrations transmitted to the hand-arm system, it is useful the visualization of the limit acceleration available in the SPEC-
- 21 -
TRUM screen.
In case of doubt, it is possible to enable the direct recording of the signal provided by the accelerometers (only with storage in memory card). The DC-shift phenomena can be easily detected analyzing the signal of the accelerometers with the Noise Studio software supplied.
W HOLE B ODY
The reference standard for assessing exposure to whole-body vibration is there-ISO
2631-1:1997. It defines standardized methods for measuring whole-body vibration and provides some guidelines for the assessment of health effects. The Vibration’s transmission can be through the feet of a person standing or sitting on a seat, through the buttocks and the back if the person is sitting, or through the support area for a person in a supine position.
The standard defines the coordinate systems for the measurement of acceleration; x, y and z axes are always directed in the same direction but with different origins, depending on the position of the operator is sitting, standing or lying down. In whole body vibrations the z axis, which is directed in the spinal column direction, is the higher risk organ to vibrations exposure.
The recorded magnitude is the r.m.s. weighted acceleration value (Root mean square value) in the frequency range from 0.5 Hz to 80 Hz. Below 0.5Hz the body, as a single mass, homogeneously follows the displacement of the vibrating surface with which it is in contact to. Higher frequencies than 80Hz involve only the surface of the body where the contact is; deeper layers of the epidermis leads to a rapid attenuation of vibrations not reaching internal structures of human body.
Procedures to measure and assess worker’s exposure to whole-body vibrations are defined in
ISO 2631-1 and ISO 2631-2. For whole body vibration measurement is used an accelerometer with a typical sensitivity of 100mV/g. The accelerometer may be fixed directly to the surface transmitting vibrations to the human body using a screw or using glue. Alternatively, if the surface is metallic, it is possible to fix the accelerometer using a magnetic support. The magnetic base can also be used for nonmagnetic surfaces; a metal disk can be glued to the surface, then the accelerometer (mounted on the magnetic base) fixed on it.
If the surface is not sufficiently planar, it is possible to use a mobile support where the accelerometer is fixed; the weight of the support must be sufficient to ensure acceleration measurement up to at least 1m/s 2 .
- 22 -
HD2030AC5
Support suitable for vibration measurements on floors and other surfaces.
Provides three different fixing points:
• in the hollow seat placed on the support’s lower face
• on the upper face with a threaded hole,
• on the adaptor cube fixed on upper face.
To access the hollow seat, unscrew the three screws used to close the back. The cavity has been sized for hosting a triaxial accelerometer with a central hole.
The accelerometer’s connecting cable passes through the side hole (see picture). To help analysis of acquired signals, we recommend that you reproduce, on the upper face, the same axial directions of the sensor.
On the upper face is present a threaded hole for mounting a triaxial or monoaxial accelerometer.
Usually the accelerometer’s sensitivity should be about 100 mV/g for working environment measurement and 1V/g for building vibrations annoyance measurements.
With the support is provided a cube adapter to be fixed on the upper face; this is for connection of three high sensitivity mono-axial accelerometers. To connect the three accelerometers to HD2030 analyzer is requested HD2030.CAB13 cable.
The support is provided with three support feet and a spirit level: if necessary, adjust the two mobile feet to adapt the horizontal position of the support using the spirit level as a reference.
To measure vibrations transmitted from seats and backs , the accelerometer is normally inserted in a rubber pad, made according to the requirements of EN 30326-1. This pad is positioned on the seat or fixed on the backrest with a tape so that is interposed between the seat itself and the body part submitted to vibrations.
Unlike the measurement of hand-arm vibrations, where the modulus of the acceleration vector is compared to the legal limits, to the extent of whole-body vibration it is the comparison with the dominant component, namely the one along the axis having the greatest strain. It’s therefore necessary to accurately orient the accelerometer’s axes according to the reference system established by ISO 2631-1 in order to avoid recalculating x, y and z acceleration components.
Selecting the Menu >> Parameters >> Instrument >> Measurements >> Application: WB, the
HD2030 analyzer performs measurements in accordance with ISO 2631-1.
The acceleration (frequency weighted to simulate the human body sensitivity to vibration) is calculated by applying the filters Wb, Wc, Wd, We, Wj, Wk to the measurement axes, as a function of the body’s part subjected to vibrations and the type of assessment needed: person’s health, comfort or perception. Alternatively are available Fz and Fa band-pass filters respectively 0.2 Hz ... 3.5 kHz and 0.4 Hz ... 100 Hz
The analyzer can calculate the accelerations spectra in octave bands from 1 Hz to 250 Hz or in third octave from 0.5 Hz to 315 Hz
B UILDING V IBRATION
With this application, the HD2030 analyzer performs the measures in accordance with
ISO 2631-2. For the evaluation of annoyance due to vibrations transmitted by the building structure, accelerometers are used with high sensitivity (typically from 1V/g) and resonance frequency greater than 1000Hz. The accelerometer is typically mounted on a heavy block to be placed on the floor, like HD2030AC5 (see description in the previous paragraph).
Selecting the Menu >> Parameters >> Instrument >> Measurements >> Application:
BV, the HD2030 analyzer performs the measurements according to ISO 2631-2.
The acceleration signal, weighted to simulate the human body sensitivity to vibration, is filtered with Wm weighting on all measurement axes. Alternatively Fz and Fm band-pass filters are available respectively 0.2 Hz ... 3.5 kHz and 0.8 Hz ... 100 Hz
The analyzer can calculate the accelerometer signal spectrum in octave bands from 1 Hz to 250 Hz or third octave from 0.5 Hz to 315 Hz
- 23 -
MEASUREMENT MODES
The HD2030 analyzer is able to measure in two different modes, selectable with the parameter Menu >> Parameters>> Instrument >> Measurement >> Integration Mode:
• Single Integration (SING) with measurement time programmable from 1s to 99 hours, and the possibility of manual stop.
• Multiple Integration (MULT) with manual stop of the measurement. The measurement time is divided in time intervals programmable from 10s to 1 hour.
The measurement starts pressing the START/STOP key.
At the beginning, the measurements are affected by the settling time of the accelerometers signals. To minimize the effect, after starting the measurement pressing the START/STOP key, the instrument keeps zeroed the instant and integrated parameters until it is elapsed the delay time, that can be set with the parameter "Menu>> Parameters>> Instrument >> Measurement >> Integration Delay", from a minimum of 1 second to a maximum of 99 seconds.
S INGLE I NTEGRATION
In this mode, the instrument calculates the integrated parameters, like the average time of acceleration for example, in the set measurement time Tint.
The measurement time is programmable from a minimum of 1 second to a maximum of
99 hours with the Menu>> Parameters>> Instrument >> Measurement >> Int. Integration.
It is possible to pause the measurement by pressing the PAUSE key, and restart the measurement by pressing the same key. While the instrument is paused it is possible to reset all the integrated parameters by pressing the START/STOP key.
The measurement ends automatically when the set integration time expiries, or manually by pressing the START/STOP key.
At the end of the measurement, the integrated parameters indicate the value calculated in all the measuring period, excluding the pause intervals.
The spectral analysis, if performed in AVERAGE mode (Menu>> Parameters>> spectrum analyzer>> Mode: AVERAGE), and the statistical analysis provide respectively the average spectrum, the probabilities and percentiles levels calculated in the measurement time.
M
ULTIPLE
I
NTEGRATION
In this mode the instrument calculates the integrated parameters, like the average acceleration for example, at regular time intervals with a set duration.
The duration Tint of each interval is set through the Menu>> Parameters>> Instrument
>> Measurement>> Int. Integration, from a minimum of 10 seconds to a maximum of 1 hour.
The measure ends pressing the START/STOP key.
It is possible to pause the measurement pressing the PAUSE key, to start again the measurement press the same key.
While the instrument is paused, it is possible to reset all the integrated parameters by pressing the START/STOP key.
At the end of each interval, the integrated parameters, the statistical analysis and the spectrum, when done in AVERAGE mode (Menu>> Parameters >> Spectrum analyzer>>
Mode: AVERAGE), are automatically reset.
This mode of integration can be used for purposes of monitoring, for example when it is necessary to detect the average value of acceleration every minute.
- 24 -
USE OF THE EXTERNAL MEMORY CARD
The HD2030 has an interface that handles an external memory card for storing the data, the configuration parameters of the instrument and sensors.
The memory card, supplied with the instrument, has Delta Ohm code HD2030MC. If cards not supplied by Delta Ohm are used, make sure they have the same read / write speed performances.
The card must be SD-type with a maximum capacity of 2GB.
To use a new memory card, it is necessary:
1. to format it using the Noise Studio PC software.
2. to initialize it using the HD2030: the initialization function creates the folder where the measurement files will be placed and copy the calibration log file (see the description of the calibration program).
The formatting operation requires a PC equipped with a memory card reader (not supplied with the instrument). Normally all the latest laptop and desktop PC are provided with it.
If not, it is possible to use an external memory card reader connectable to a USB port.
To format a SD card, proceed as follows:
• If the PC is without reader, connect an external SD cards reader to a PC USB port.
• Start the Noise Studio software.
• Press the instrument management key in Noise Studio: press the Format Memory Card key.
• Select the path of the card to be formatted and press ENTER.
• In the next screen make sure it is selected the parameter "File System = FAT" and press
START: the card is formatted.
• When it appears the message "Formatting completed”, press OK to confirm and CLOSE to exit.
• Close the Noise Studio software.
• The formatting procedure is complete.
To initialize a card, proceed as follows:
Two methods are provided:
• Use of the "Initialization MC" function in the programs menu of the instrument (see the details in the description of the programs): this feature erases the eventual data already existing in the card.
• If the card is new and already formatted, turn on the instrument after inserting the card into the front slot of the instrument: the initialization procedure starts automatically. At the end of the operation, it appears the message "MC installed and ready to use."
MC installed and ready.
Size: 1000MB
ESC RD RD/WR
- 25 -
Press RD/WR to enable all the reading and writing functions.
Press RD alone to read the content of a card. The recording of new data is disabled: in this way it is avoided to overwrite the files already stored in the card.
The card is ready to be used.
Note: the HD2030’s "Initializing MC" function also checks the read/wright speed of installed card. If the SD card fails this test for the first time, initialization function is repeated: may it happen more than three times, replace the card with a faster one. Do the same if the message
"Error reading memory" appears during initialization procedure.
- 26 -
RECORDING MODES
The HD2030 is able to perform three different types of storage:
• Single Record, it can be manual or automatic.
• Single Profile with a recording interval programmable from 1s to 1 hour. It can be manual or automatic.
• Continuous Multi Profile, with 1s recording interval or at intervals programmable from
10s to 1 hour.
The recordings are saved, for all the active channels, in the internal FLASH memory of the analyzer or in the SD memory card, following the setting of the parameter Menu >> Parameters>> Instrument >> Input/Output >> Memory.
Each recording is preceded by a summary screen reporting:
• the memory where the data are going to be saved (memory card or internal Flash memory);
• the sequential number that identifies the block of data;
• date and time;
• size of the file and memory space available.
DATA RECORDING
MEMORY CARD
Record N. 00001
2009/01/31 12:00:00
Dim: 3KB Free: 6.7%
COMM. EXIT STORE
Pressing the STORE key (right arrow on the keypad), the data are saved.
Pressing the EXIT key (left arrow of the keypad), the instrument exits without saving and returns to measure mode.
Pressing the COMM. key (CURSOR key on the keypad), it is possible to save the data file adding a voice comment by connecting a microphone to the appropriate input on the front of the instrument.
Setting the parameter Menu >> Parameters >> Data Logger >> Profiles >> ADC Channels, in parallel with the storage of measurement parameters in the HD2030 analyzer’s memory, it is also possible to store the accelerometers row signals. The parameter allows to select among the storage of all the channels of the analyzer, only one of the four channels or the first three channels (RIGHT input). The direct recording of the ADC channels can be activated only in the memory card and it is not available for the internal FLASH memory of the analyzer.
The Auto-Store function allows to automatically store the global parameters, i.e. integrated in all the measurement time.
To activate the recording of the global parameters, it is used the parameter Menu >> Parameters >> Data Logger >> Global >> Auto-Store.
- 27 -
Stored parameters are defined in the menu: Menu >> Setting >> Data Logger >> Global. Together with the global parameters are also recorded the average spectrum and the statistics.
S INGLE R ECORD
In this mode it is possible to memorize in a single record, the values visualized in the
VLM, SPECTRUM, PROBABILITY and PERCENTILES screens.
Manual Recording “Single record”
Data are saved manually pressing the REC key for at least two seconds. This op-
eration is allowed when the instrument is in STOP mode.
Are stored:
• two VLM_1 and VLM_2 screens, whose measurement parameters are defined in Menu >>
Parameters>> Vibration Analyzer.
• the average spectrum in octave or third octave bands, according to parameter Menu >>
Parameters >> Spectrum Analyzer>> Order: ….integrated on the measurement time;
• probability distribution of chosen parameter in the profile screen (Menu >> Parameters
>> Vibration Analyzer >> Profile:);
• percentile levels from L1 to L99 of chosen parameter in the profile screen.
Automatic Recording “Single record”
To activate the automatic recording, enable from the menu the Auto-Store parameter:
Menu >> Parameters >> Data Logger >> Global>> Auto-Store = ON.
The display shows the activation of the Auto-Store function with the alternated blinking of the REC and STOP symbols.
They will be recorded the two screens VLM_3 and VLM_4 (whose measurement parameters are defined in Menu >> Parameters >> Data Logger >> Global), the spectral analysis and the statistics.
The data are automatically recorded at the end of the set integration interval Tint or, before the Tint interval is elapsed, pressing the STOP key.
S INGLE P ROFILE
This mode allows the storage of the time profile of the measurement parameter
selected for the PROFILE screen. The parameter is memorized at intervals programmable from 1s to 1 hour.
To make a manual recording of a Single Profile set:
• The single integration mode: Menu >>Parameters >> Instrument >> Measurement>>
Integration Mode: SING
• The sampling interval of the time profile: Menu >> Parameters >> Instrument >> Measurement >> Profile Step: from 1 second to 1 hour.
• The measurement time: Menu >>Parameters >> Instrument >> Measurement >> Integration time: from 1 second to a maximum of 99 hours.
• The recording mode: Menu >>Parameters >> Data Logger >> Profiles >> Mode: PRO-
FILE
• The parameter whose time profile has to be acquired: Menu >>Parameters >> Vibration
Analyzer >> profile, choosing among those available.
The recording starts pressing at the same time REC and START/STOP keys, and stops when the set measurement time Tint expires or pressing the START/STOP key.
- 28 -
During the acquisition it is possible to temporarily pause the instrument pressing the
PAUSE/CONTINUE key and start again the recording pressing a second time the same key.
In the recording it is also possible to add markers that will are saved together with the profile and that can be visualized with the Noise Studio software.
There are 9 available markers, each of them with maximum 15 characters.
To insert a marker, press the REC key during the recording: with the UP and DOWN arrows choose one of the 9 markers and confirm with the REC key. Press the ESC key to exit without memorizing the marker.
2012/06/10 10:00:00
STORING
MARKER
1 TITLE_MARKER1
EXIT
It is possible to assign a name to a marker from the instrument menu (see “Menu >> Parameters>> Data Logger >> Profiles” in “DESCRIPTION OF THE MENU FUNCTIONS” chapter) or by using the Noise Studio software.
Automatic recording of a single profile
If the Auto- Store function is enabled (Menu >> Parameters>> Data Logger >> Global
>> Auto-Store = ON), at the end of chosen parameter’s time profile storage, a single record is recorded containing:
• two screens VLM_3 and VLM_4 whose measurement descriptors are defined in Menu >>
Parameters >> Data Logger >> Global;
• the average spectrum, integrated on the measurement time, in octave or third octave bands, according to the setting Menu >> Parameters >> Spectrum Analyzer >> Order;
• probability distribution of the chosen parameter in the profile screen (Menu >> Parameters >> Vibration Analyser >> Profile);
• percentile levels from L1 to L99 of the chosen parameter in the profile screen.
M ULTI P ROFILE
This mode allows to memorize the time profile of several parameters.
Two recording modes are provided: one continuous and one at intervals, corresponding respectively to the setting of the single and multiple integration mode (parameter Menu >>
Parameters >> Instrument >> Measurement >> Integration Mode).
To perform a Multi Profile recording, set the following parameters:
• The integration mode: Menu >>Parameters >> Instrument >> Measurement >> Integration Mode: SING o MULT.
• Recording mode: Menu >>Parameters >> Data Logger >> Profiles >> Mode: FULL
The measurement parameters that are memorized are indicated in the following table.
- 29 -
Parameter
MULTI PROFILE
Single Integration Multiple Integration
VLM_1 and VLM_2 screens:
- 3 parameters single axis
- 3 parameters for sum and maximum value vectors
SPECTRUM screen: octave or third-octave band spectrum
STATISTIC screens:
and PERCENTILES statistical analysis in 1dB classes with 1 second sampling frequency
X X
X X
--- X
Integration interval and calculation
1 second
Programmable from 10s to 1 hour (Instrument >> Measurement >> Int. Integration) with automatic reset of the parameters at the beginning of each interval.
The Multi Profile recording with single integration allows to memorize every second:
• The 3 instant or integrated parameters of the VLM_1 screen calculated for all the measurement channels
• The 3 parameters of the VLM_2 screen calculated on the vector formed by the first three channels (RIGHT input)
• The spectrum, in octave or third-octave bands.
The Multi Profile mode with multiple integration records, at intervals equal to the set integration time Tint (from 10 seconds to 1 hour):
• The 3 instant or integrated parameters of the VLM_1 screen calculated for all the measurement channels
• The 3 parameters of the VLM_2 screen calculated on the vector formed by the first three channels (RIGHT input)
• The spectrum, in octave or third-octave bands
• The statistical analysis in classes of 1dB with 1 second sampling interval.
All the measurement parameters, the spectra and the statistics are automatically reset at the beginning of each interval.
The continuous recording starts pressing simultaneously the REC and START/STOP keys.
In the single integration mode, the acquisition stops when the set integration
time Tint is elapsed (Menu >> Parameters>> Instrument > Measures > Int. Integration) or pressing the START/STOP key.
In the multiple integration mode, the recording must be ended manually pressing the START/STOP key.
During the acquisition it is possible to temporarily pause the instrument pressing the
PAUSE/CONTINUE key and start again the recording pressing a second time the same key.
In the recording it is also possible to add markers that will are saved together with the profile and that can be visualized with the Noise Studio software.
There are 9 available markers, each of them with maximum 15 characters.
To insert a marker, press the REC key during the recording: with the UP and DOWN arrows choose one of the 9 markers and confirm with the REC key. Press the ESC key to exit without memorizing the marker.
- 30 -
2012/06/10 10:00:00
STORING
MARKER
1 TITLE_MARKER1
EXIT
It is possible to assign a name to a marker through the instrument menu (see “Menu >>
Parameters >> Data Logger >> Profiles” in “DESCRIPTION OF THE MENU FUNCTIONS” chapter) or by using the Noise Studio software.
If the Auto-Store mode is enabled (Menu >> Parameters >> Data Logger >> Global >> Auto-Store = ON) at the end of the Multi Profile storage, a single record is stored containing:
• two screens VLM_3 and VLM_4 whose measurement parameters are defined in Menu >>
Parameters >> Data Logger >> Global;
• the octave or third octave average spectrum, calculated on the measurement time, according to the setting Menu >> Parameters >> Spectrum Analyzer >> Order;
• the probability distribution of the chosen descriptor in the profile screen (Menu >> Parameters >> Vibration Analyser >> Profile);
• percentile levels from L1 to L99 of the parameter chosen in the profile screen.
R ECORDING OF VOICE COMMENTS
The HD2030 can be used as an audio recorder connecting an external microphone (code
HD2030AM) at the MIC input. The recording can be saved as single audio file or it can be associated with a data file as vocal commentary.
To record audio only, keep the REC key pressed for at least two seconds when the instrument is in STOP mode. The following screen appears:
WARNING !
RECORDING OF
ESC VOICE DATA
Press the VOICE key. The recording starts. To finish the operation, press the STOP key.
To add a voice comment to a data file, connect a microphone to the appropriate MIC input on the instrument front and, when you are going to save, press the COMM (comment) key.
- 31 -
DATA RECORDING
MEMORY CARD
Record N. 00001
2012/06/10 12:00:00
Dim: 3KB Disp: 6.7%
COMM. ESC SAVE
To end the audio comment recording and save the data file, press the STOP key.
The recordings can be listened directly from the instrument equipped with headphones or through the Noise Studio software.
See the details in the Memory Navigator Program description at paragraph “4) To listen vocal commentaries”).
- 32 -
PROGRAMS DESCRIPTION
The HD2030 analyzer has several programs that are accessed by Menu>> Programs. To start a program, select it with the UP and DOWN arrow keys and press ENTER.
The programs available are:
• Memory Navigator: it allows to examine what it is stored in the internal FLASH memory of the instrument and in the memory card. It is also possible to listen to the audio recordings and the vocal commentaries associated with the data files using the headphones.
• Setup Management: it allows to save or load the analyzer settings. To facilitate the choice, each setup has a title.
• Calibration: it sets the sensitivity of the accelerometers connected to the instrument, both through manual insertion of the calibration values and through the measurement of the acceleration produced by a vibrations generator.
• Diagnostic Check: it checks the main functions of the instrument.
• Sensors Config.: insertion and modification of the parameters of the sensors that can be connected to the analyzer.
• Initialize MC: it deletes the data in the memory card and set it for the use with the
HD2030.
M EMORY N AVIGATOR P ROGRAM
The Memory Navigator Program allows to operate in the internal FLASH memory and in the external Memory card.
To enter the Memory Navigator Program, press the MENU key: Menu >> Programs >> Memory Navigator.
If the Memory card is present, the following screen appears:
MEMORY NAVIGATOR select memory unit
EXIT FLASH MC
Press the FLASH or MC keys to respectively manage the internal memory of the instrument or the memory card.
- 33 -
If there is no Memory Card, the following screen appears:
FLASH NAVIGATOR
Batt: 80% Mem: 75%
BACK EDIT READ
In the internal FLASH memory it is possible:
• to review the memorized files.
• to copy the single recording or all the files from the internal memory to the memory card.
• to erase all the memory content. It is not provided the possibility to erase the sin-
gle files in the internal memory.
In the Memory Card it is possible:
• to review the memorized files.
• to listen to the vocal recordings.
• to erase single files contained in the Memory Card. To erase all the Memory Card content, run the program “Menu >> Programs >> Initialize MC”, as described below.
Note: the deleted files in the Memory Card are still in the card memory, even if new recordings are added; this allows an eventual recovery through the Noise Studio software supplied with the analyzer.
To clear the Memory Card it is always possible to use the program "Format Memory
Card" in the Noise Studio software. See the chapter “USE OF THE EXTERNAL MEMORY CARD".
1) To review a file saved in the internal Flash memory
From measure mode, press in sequence the buttons: Menu>> Programs>> Memory Navigator and select the internal Flash memory.
The following screen appears:
FLASH NAVIGATOR
Batt: 80% Mem: 75%
BACK EDIT READ
Press the READ key: the display shows the characteristics of the first file in memory.
- 34 -
To scroll the memory and display the properties of the other files, press the RIGHT arrow key. After the last file is visualized, the display returns to the starting screen.
The properties of a file in the memory appear like in the following example:
FLASH NAVIGATOR
Batt: 80% Mem: 75%
Type Int.T
SING 00s
N.
00001
2012/06/10 15:00:00
Tm:00:02:05
BACK COMM. COPY
For each file are indicated:
• Type indicates the file type: single report (SING), single profile (PROF) or multi profile
(REP).
• Int.T is the integration interval.
• N is the sequential number that identifies the file.
• Tm represents the total recording time.
To visualize the current file content, press the ENTER key: the STOP symbol alternates with the R letter (Replay).
During the replay it is possible to use the MODE key to display the different measure modes: VLM, PROFILE, SPECTRUM, PROBABILITY, PERCENTILES.
In the same way, with the CHN key it is possible to scroll the different measurement channels.
To stop or start again the review, use the PAUSE/CONTINUE key.
While the replay is paused, it is possible to visualize the next data pressing the START key.
If the START key is hold pressed in pause mode, the fast replay mode is entered.
At the end the instrument enters the STOP status.
To exit from REPLAY mode, press the MENU key.
The review operation mode depends on the memorized file type (see the chapter
“RECORDING MODE”):
• “Manual single record” Recording
The file is “Single Report” type: when the ENTER key is pressed, the parameters of the
VLM_1 and VLM_2 screens are automatically loaded and displayed.
• “Automatic single record” Recording
For the recording the Auto-Store function has been enabled, the file is “Single Report” type: When the ENTER key is pressed, the global parameters of the VLM_3 and VLM_4 screens are automatically loaded and displayed.
• “Manual Single profile” Recording
The time profile of a single parameter has been memorized. Pressing the ENTER key, the display shows the Profile screen with the timer at 0.
- 35 -
When the START key is pressed, the profile is reviewed automatically. It is possible to switch from a measurement channel to another one with the CHN key but there are no other active screens because this mode records only the time profile of the four channels.
• “Automatic Single Profile with Auto-Store” Recording
A single profile recording enabling the Auto-Store function was done. When the ENTER key is pressed, the global parameters of the VLM_3 and VLM_4 screens are automatically loaded and displayed: the GLOBAL indication appears at the top of the display. With the
MODE key it is possible to scroll the spectrum, probability and percentiles screens calculated on the global parameters:.
Pressing the START key, the profile is reviewed automatically. It is possible to switch from a measurement channel to another one with the CHN key.
• “Multi profile with single integration” Recording
A multi profile recording with single integration mode was done. The data file includes the VLM_1 and VLM_2 screens and the spectrum. When the ENTER key is pressed, the instrument goes into VLM_1 screen: at the top it appears the indication “PROFILE”.
Pressing the START/STOP key, the data replay starts. With the MODE key it is possible to switch from a screen to another one, with the CHN key from a measurement channel to another one.
• “Multi profile with multiple integration” Recording
A multi profile recording with multiple integration mode was done. The data file includes the VLM_1 and VLM_2 screens, the spectrum and the statistics.
When the ENTER key is pressed, the instrument goes into VLM_1 screen: at the top appears the indication “REPORT”.
- 36 -
The “Tint=” tag blinks to signal that the integration is multiple. When the START/STOP key is pressed, the instrument displays the data related to the first integration interval and enters the pause mode. With the MODE key it is possible to switch from a screen to another one, with the CHN key from a measurement channel to another one. While the replay is paused, it is possible to display the following data pressing the START key.
Holding pressed the START key while in pause mode, the fast replay mode is entered.
Pressing the PAUSE/CONTINUE key, the review proceeds up to the end.
• “Multi Profile with single or multiple integration with Auto Store” Recording
The two previous modes can be integrated during the recording phase with the addition of the Auto-Store function: in this case, when the ENTER key is pressed, the global parameters of the VLM_3 and VLM_4 screens are automatically loaded and displayed; the
GLOBAL indication appears at the top of the display. With the MODE key it is possible to switch from spectrum, probability and percentiles screens.
Pressing the START key, the parameters are reviewed as described in the previous two points.
- 37 -
2) To review a file saved in the Memory Card
From measure mode, press in sequence the keys:
Menu >> Programs >> Memory Navigator.
If a Memory Card is present, it appears the screen to select the memory to review: press MC to select the Memory Card.
FLASH NAVIGATOR select memory unit
EXIT FLASH MC
The following screen with the file list appears:
MC NAVIGATOR
NAME DATE TIME
CAL 2012/01/01 10:00
0001 2012/01/31 15:00
0002 2012/02/28 16:00
0003 2012/03/31 17:00
BACK CLEAR.
Note: the first file of the list called “CAL” is the file of sensors calibration. It is a read/write protected file, no operations are allowed on this file.
With the UP and DOWN arrow keys, select the file to be visualized and press ENTER.
The properties of the selected file are indicated:
PROPERTIES 0001-AAD
#0003 Tipo: REP
2012/01/31 15:00:00
2012/01/31 15:05:00
Tm:00:05:00 44KB
BACK
For each file are indicated:
• The sequential number in the browser file list (“0001” in the example, next to “Properties”).
• three characters code (“AAD” in the example) with the following meaning:
- 38 -
o
The first character identifies the recording type:
S Single type recording
A Autostore type recording
M Multi type recording
R Report type recording
V Audio file recording. In this case the second character is A. o
The second character, if present, can be A only; it identifies a vocal recording or a file with an audio comment attached. o
The third character, if present, can be D only; it identifies a file that includes the
ADC channels data.
• # is the sequential number given to a specific file and identifying it.
• Type indicates the file type: if single report (SING), single profile (PROF) or multi profile
(REP). If there is also an audio comment, the “+AUDIO” indication appears.
• Date and time of file opening.
• Date and tome of file closing.
• Tm represents the total recording time. On the side it is indicated the file dimension.
To display the content of the current file, press the ENTER key: the STOP symbol alternates with the R letter (Replay).
During the replay it is possible to use the MODE key to visualize the different measurement modes: VLM, PROFILE, SPECTRUM, PROBABILITY, PERCENTILES.
In the same way, with the CHN key it is possible to scroll the different measurement channels.
For the details on how to proceed to visualize the memorized data, see the detailed description reported in the previous point.
To exit from REPLAY mode, press the MENU key.
3) File management in the internal Flash memory
The allowed operations on the files stored in the internal memory are the copy of a file or of the entire internal memory into the Memory Card, and the memory clear. It is not possible to delete single files in the internal memory.
Press in sequence the keys: Menu >> Programs >> Memory Navigator.
It appears the screen:
MEMORY NAVIGATOR
Select memory unit
EXIT FLASH MC
Press the FLASH key to access to the internal memory of the instrument.
- 39 -
FLASH NAVIGATOR
Batt: 80% Mem: 75%
BACK EDIT READ
Press the EDIT key to enter the submenu for the management of the memorized files.
FLASH NAVIGATOR
Batt: 80% Mem: 75%
BACK CLEAR COPY
With the CLEAR. Key all the FLASH memory content is deleted.
With the COPY key all the FLASH memory content is copied into the Memory Card.
When one of the two keys is pressed, the instrument asks to confirm the selected operation, pressing YES.
FLASH NAVIGATOR
Batt: 80% Mem: 75%
CONFIRM
MEMORY CLEAR?
YES NO
FLASH NAVIGATOR
Batt: 80% Mem: 75%
CONFIRM COPY OF
SELECTED FILES ON MC?
YES NO
To copy a single file from the internal memory into the Memory Card, select in sequence the keys: Menu >> Programs >> Memory Navigator.
It appears the screen:
- 40 -
MEMORY NAVIGATOR select memory unit
EXIT FLASH MC
Press the FLASH key to access to the internal memory of the instrument.
FLASH NAVIGATOR
Batt: 80% Mem: 75%
BACK EDIT READ
Press READ and with the UP and DOWN arrow keys select the file to copy.
FLASH NAVIGATOR
Batt: 80% Mem: 75%
Type Tint.
SING 10s
Tm:00:02:05
N.
00001
2012/06/30 15:00:00
BACK COMM. COPY
Press the COPY key and confirm the operation in the next screen.
FLASH NAVIGATOR
Batt: 80% Mem: 75%
CONFIRM COPY OF
SELECTED FILE TO MC?
YES NO
Press YES to copy, NO to go back to the previous screen without copying.
- 41 -
4) To listen to the voice comments
The voice comments can be listened again through Noise Studio Software or directly from the HD2030 if equipped with headphones (code HD2030AM).
• Connect the headphones to the appropriate connector on the front of the instrument.
• Select in sequence the keys: Menu >> Programs >> Memory Navigator.
• Select the internal memory bank (FLASH) or the external Memory Card (MC).
• Select with the UP and DOWN arrow keys the file with the comment and press ENTER to load it.
• Press the COMM key to listen to the vocal comment.
• With the << and >> arrows of the keypad it is possible to adjust the volume of the headphones.
• Press STOP to finish in advance the listening of the comment.
• Press BACK to go back to the main screen of the Browser.
End of the procedure.
- 42 -
S ETUP M ANAGEMENT P ROGRAM
This program allows to choose one of the 10 reference setups stored in the HD2030 analyzer. To rapidly identify the desired one, to each setup is associated with a title.
The PC software Noise Studio allows to edit the setups, to save them into the PC memory and to load into the instrument memory the ones you want to use.
Each setup is associated with a configuration for the sensors to be connected to the
RIGHT and LEFT inputs (see the Sensor Configuration Program).
Once the setup is loaded in the instrument, it is possible to manually modify the settings, including the sensors configuration: once edited the setup can be stored inside any of the 10 reference setups.
Note: to proceed with the creation of a new setup to load in the instrument, it is necessary to have installed in the PC the Noise Studio software.
1) How create a new setup with Noise Studio Software
Proceed in the following way:
• Connect the analyzer to the PC with the serial or USB cable.
• Start the Noise Studio software.
• Press Instrument management key in Noise Studio: start the connection with the Con-
nect key (for details on how to connect, see the software manual).
• Press the Instrument configuration tool in Noise Studio: the software downloads the current settings of the analyzer.
• Modify the General, Channels and Sensors screens in Noise Studio according to your needs: o
In the General screen the system, input/output and measure parameters can be set. o
In the Channels screen the measurement variables for the different screens
(VLM, profile, spectra, global parameters), the recording modes and the trigger can be selected. o
In the Sensors screen the accelerometers to use during the test can be configured. Insert all the parameters and save the configurations pressing the
Save Config. Key, assigning to each configuration a number from 1 to 9 (see in the following of this chapter the specific program Sensors Configuration).
• Select the Predefined screen and press Save Current Settings: insert a name and a description (optional) to identify the setup.
• Press the “Copy custom settings in the predefined setups of the instrument” key. In this way the just created setup is added to the setups list in the memory of the instrument and can be selected directly from the instrument menu, without the need to connect instrument to a PC.
• To make the current setup active, push Apply All key in Noise Studio.
The setup is loaded into the instrument memory, ready to be used.
2) How to load a new setup
To apply a setup previously stored in the instrument’s memory, press the following sequence of keys: MENU >> Programs>> Setup Management.
• With the UP and DOWN arrows select the setup to apply: press ENTER to confirm.
• In the following screen, press the LOAD key to apply the settings of the new setup.
- 43 -
SETUP MANAGEMENT
2012/05/30 12:00:00
SETUP N.01
TEST_001
2012/05/01 10:00:00
BACK STORE LOAD
• The next screen visualizes the setup features of the sensor for the RIGHT input:
CONFIG RIGHT. #02
OHM
MOD: ACC_TRI
S.N.: 123456
TRI
SENS: 10mV/g CAL
SEL. PREV. NEXT
• Press SEL to confirm, PREV or NEXT to scroll the list of the sensors that are in the memory. Following are the setup features of the sensor for the LEFT input.
CONFIG LEFT . #02
OHM
MOD.: ACC_MONO
S.N.: 654321
MON
SENS: 100mV/g CAL gpk
SEL. PREV. NEXT
• Press SEL to confirm, PREV or NEXT to scroll the sensors list of the sensors that are in the memory.
Now the instrument is ready to perform a new measurement.
3) How to save an instrument configuration in a setup
A special configuration of the instrument can be saved in one of the ten setups available in the memory to be recalled at a second time.
Proceed as follows:
• Select through the menu the different instrument parameters, the sensors configuration, the measurement and recording modes.
• It is possible to start from an already memorized setup, loading it in the memory as described in the previous paragraph.
- 44 -
• Press in sequence the keys: MENU >> Programs >> Setup Management.
• With the UP and DOWN arrows, select the setup number to be assigned to the new configuration: the current configuration will be overwritten by the new one so do not select a setup you want to keep. Press ENTER to confirm.
• It appears the screen with the name of the current setup that will be overwritten by new one.
SETUP MANAGEMENT
2009/01/31 12:00:00
SETUP N.07
TEST_007
2009/01/01 10:00:00
BACK STORE LOAD
• Press the STORE key.
• The screen for the insertion of the title to apply to the new setup appears:
TITLE OF SETUP #01
D
C
B
ANNNNNNNNNNNNNNNNNN
BACK
• With the UP and DOWN arrows, select the first character and confirm it with ENTER.
• The cursor skips to the second character.
• Repeat the selection with the UP and DOWN arrows and confirm with ENTER. Proceed in the same way for the other characters of the title.
• Inserting a SPACE (blank) the remaining characters of the title are cancelled.
• Press RET to save.
• Press ESC to exit from the Setup Management program
4) How to modify a setup in the memory
The setups in the memory can be changed directly through the menu of the instrument
(for the change of a setup through the Noise Studio Software, see point 1 of this paragraph).
Proceed in the following way:
• Start the setup management program pressing in sequence the keys: MENU >> Programs >> Setup Management.
• Load the setup to modify following the steps indicated in point 2 if this paragraph.
• Modify the instrument configuration as desired (for example: displayed units, parameters of the menu, recording mode,….).
• Go back to the setup management program pressing in sequence the keys MENU >>
Programs >> Setup Management. With the UP and DOWN arrows select again the setup previously loaded and confirm with ENTER.
- 45 -
• In the following screen, press the STORE key.
SETUP MANAGER
2009/01/31 12:00:00
SETUP N.01
TEST_001
2009/01/01 10:00:00
BACK STORE LOAD
• The new settings are saved in the place of the previous ones.
• It appears the screen for the insertion of the title to apply to the updated setup:
TITLE OF SETUP #01
D
C
B
ANNNNNNNNNNNNNNNNNN
BACK
• If it is desired to maintain the name of the previous setup, press RET and then ESC to exit from Setup management, otherwise, with the UP and DOWN arrows, select the first character and confirm it with ENTER.
• The cursor skips to the second character.
• Repeat the selection with the UP and DOWN arrows and confirm with ENTER. Proceed in the same way for the other characters of the title.
• Inserting a SPACE (blank) the remaining characters of the title are cancelled.
• Press RET to save.
• Press ESC to exit from the Setup Management program.
The setup modification procedure is completed.
C ALIBRATION P ROGRAM
This program calibrates the sensors connected to the HD2030 analyzer.
It is possible to manually insert the calibration parameters of the accelerometers using the values indicated on the certificates or calibration sheets, or using a vibrations generator specific for the calibration of the accelerometers.
The calibration parameters are saved in an specific log file where the last 120 calibrations performed are stored. When the instrument is connected to the PC through the Noise Studio software, this file is automatically downloaded and saved in the PC as a reference for the documentation of the measurements performed with the instrument.
Any measurement made with the HD2030 analyzer, therefore, will be associated with a calibration according to the date.
- 46 -
1) Calibration of a sensor through the direct input of parameters
If the calibration data of the sensor are available, proceed in the following way:
• Start the calibration program of the sensors pressing in sequence the keys: MENU >>
Programs >> Calibration.
• The main screen appears:
CALIBRATION
Date: 2009/01/31 10:00
DELTA OHM DELTA OHM
ACC_M ACC_T
Choose the channel
EXIT LEFT RIGHT
The indicated date refers to the last saving of the log file. On the left side are reported the manufacturer and the name assigned to the monoaxial sensor, and on the right side the correspondent information for the triaxial one.
• Press the LEFT Key to select the monoaxial sensor, RIGHT for the triaxial one.
The screen that resumes the current data of the selected sensor appears: o manufacturer, o type, o name, o serial number, o sensitivity expressed in mV/g.
CALIBRATION
DELTA OHM ACC_TRI
ACC_T 123456
Axis: 1
SENS: 10mV/g
Calibration Type
EXIT SENS. MEAS.
• To insert manually the sensitivity, press the SENS key.
• If the sensor is triaxial type, a sensitivity for each axis must be inserted: with the UP and
DOWN arrows select the first axis and confirm with ENTER.
- 47 -
CALIBRATION
DELTA OHM ACC_TRI
ACC_T 123456
Axis: 3
SENS: 10mV/g Axis: 1
Calibration Type
EXIT SENS. MEAS.
• The following screen appears:
CALIBRATION
DELTA OHM ACC_TRI
ACC_T 123456
Axis: 3
10.15
mV/g
Sensitivity +-
BACK
• With the UP and DOWN arrows modify the proposed value and press ENTER. At the following request of confirmation, press again ENTER.
CALIBRATION
DELTA OHM ACC_TRI
ACC_T 123456
Axis: 1
SENS: 10mV/g Axis: 1
Calibration Type
BACK
• Select the other axes and proceed in the same way. Press BACK To go back to main screen.
• If the sensor is monoaxial, the sensitivity is unique: only one value must be inserted.
- 48 -
CALIBRATION
DELTA OHM ACC_MON
ACC_M 654321
100.5
mV/g
Sensitivity +-
BACK
• With the UP and DOWN arrows change the proposed value and press ENTER. At the following request of confirmation, press again ENTER. Press BACK key to go back to main screen
• From the main screen, press ESC to exit from the calibration program.
2) Calibration of a sensor through the vibrations generator
If a calibrator is available, proceed in the following way:
• Set the acceleration level of the calibrator through the item Menu> Parameters > Calibration.
• Start the sensors calibration program pressing in sequence the keys: MENU >> Programs
>> Calibration.
• The main screen appears:
CALIBRATION
Date: 2009/01/31 10:00
DELTA OHM DELTA OHM
ACC_M ACC_T
Choose channel
EXIT LEFT RIGHT
The indicated date refers to the last saving of the log file. On the left side are reported the manufacturer and the name assigned to the monoaxial sensor, and on the right side the correspondent information for the triaxial one.
• Press LEFT Key to select the monoaxial sensor, RIGHT for the triaxial one.
The screen that resumes the current data of the selected sensor appears: o manufacturer, o accelerometer type, o name, o serial number, o sensitivity expressed in mV/g.
- 49 -
CALIBRATION
DELTA OHM ACC_TRI
ACC_T 123456
SENS: 10mV/g
Calibration Type
EXIT SENS. MEAS.
• Apply the transducer to the calibrator and press the MEASURE key: the level that appears is the calibrator nominal value.
With the RIGHT and LEFT arrows the measure unit can be changed between g and m/s 2 .
• If the sensor is triaxial type, the three axes have to be calibrated separately: with the UP and DOWN arrows select the first axis and confirm with ENTER.
CALIBRATION
Level 10.00 m/s 2
Axis: 1
Select axis
BACK.
• The following screen appears:
CALIBRATION
Level 10.00 m/s 2
A1s Fz
----
m/s 2
Turn On calibrator
NEXT EXIT
- 50 -
• Switch on the calibrator and press FORWARD.
CALIBRATION
Level 10.00 m/s 2
A1s Fz
9.985
m/s 2
Waiting for level stabilisation
STOP
• The instrument verifies that the signal level is stable and then asks to confirm the measured value.
CALIBRATION
Level 10.00 m/s 2
A1s Fz
9.985
m/s 2
Confirm?
YES NO
• Pressing YES the current value is memorized.
• If the sensor is triaxial, the procedure has to be repeated selecting the other two axes: repeat the operation from the beginning.
• From the main screen, press ESC to exit from the calibration program.
D IAGNOSTIC CHECK P ROGRAM
This program perform a check of the main functions of the HD2030 analyzer.
The following functional parameters are checked, in automatic sequence:
• Power Supply: it checks that the voltage supplied to the instrument allows the measurements execution. If this point fails, replace the batteries and repeat the test.
• IEPE Power Supply: it checks that the power supply of the accelerometers is within the technical specifications.
• Accelerometers Polarization: it checks that the polarization voltage of the connected accelerometers is within the technical specifications.
• DSP Working: it checks that the analog to digital conversion and the DSPs are able to transmit the measures to the microprocessor.
• Environmental Parameters: it checks that the environment temperature is within the working specifications of the analyzer.
When one of the checks fails, it is displayed the list of the checks done and the steps that failed.
In this case it is always suggested to repeat the diagnostic check and, in case of confirmation, contact the technical service.
- 51 -
In case of failure of the power supply test, replace the batteries before repeating the diagnostic check.
To perform the diagnostic test, proceed as follows:
• Connect the accelerometers to the appropriate inputs and switch on the instrument.
• Start the diagnostic test pressing in sequence the keys: MENU >> Programs >>
Diagnostic check.
• The test program starts and the different steps are executed:
HD 2030
DIAGNOSTIC TEST
2011/10/01 10:00:00
Power supply OK
IEPE power supply OK
Accelerometer Pol TEST
EXIT
• At the end it is displayed the test report; if at least one of the steps failed, the message
“FAULT IN DIAGNOSTIC CHECK!” appears. The passed steps are marked with OK, the failed steps are marked with NO.
Power Supply OK
IEPE power supply OK
Accelerometer Pol. NO
DSP engine OK
Amb.Parameters OK
Diagnostic error
EXIT
• If all the steps have been completed without faults, it appears the message
“DIAGNOSTIC CHECK DONE”.
H D 2 0 3 0
DIAGNOSTIC TEST
2011/10/01 15:30:00
Diagnostic check done
EXIT
• Press ESC to exit. To repeat the test, enter the menu again as described above.
The test procedure is completed.
- 52 -
S ENSORS C ONFIGURATION P ROGRAM
This program allows to configure the sensors that will be used for the measurements with the HD2030 analyzer.
It is possible to memorize up to 9 different sensors for the right input and 9 for the left input. The sensors related to the right input are triaxial type while the ones related to the left input are monoaxial type.
The parameters of the sensors are saved in a specific file in the internal memory of the analyzer and, if present, they are also saved in the Memory Card.
The requested parameters are:
• Manufacturer
• Model
• Serial Number
• Type: triaxial or monoaxial accelerometers for the right input and monoaxial for the left input.
• Nominal Sensitivity: Sensitivity nominal factor of the accelerometer (mV/g)
• Range: the maximum acceleration value measurable (g pk)
At startup the instrument load the file with the parameters of the sensors and it is requested to select a configuration for each of the two sensors. With the PREV. and NEXT. keys of the keypad it is possible to scroll the different sensors, and with the CURSOR key a sensor for each input can be selected.
The blinking warning “NO CAL” next to the nominal sensitivity value indicates that, for that sensor, the calibration data are missing: in this case the nominal sensitivity is used.
The same process is used when a complete setup is loaded (see the Setup Management program description): the instrument verifies the existence of the calibration file for the two accelerometers included in the selected setup. If the sensors have been calibrated, the sensitivity parameters are loaded automatically, otherwise it will be used the nominal sensitivity associated with the configuration.
Note: even if it is possible to operate directly on the instrument, the management of the sensors configuration can be more easily done with the PC software Noise Studio (see the details in the software manual).
To configure the sensors, proceed as follows:
• Connect the accelerometers to the appropriate inputs and switch on the instruments.
• Start the program pressing in sequence the keys: MENU >> Programs >> Sensors Config..
SENSORS
CONFIGURATION
Choose channel
ESC LEFT RIGHT
• Select the channel where it is connected the sensor to configure.
• A screen similar to the following appears:
- 53 -
#01
OHM
MOD: ACC_ABC
SERIAL N.: 654321
TYPE: ACC
SENS: 10mV/g CAL
BACK.
• With the right and left arrows, select the sensor among the nine available.
• With the UP and DOWN arrows, select the row to change.
• Press ENTER to go to the parameter of the selected row.
• With the UP and DOWN arrows, set the desired value.
• Press ENTER to confirm.
• Repeat for all the parameters.
• Press RET (CURSOR key) to go back to the initial screen and select the other input.
• Repeat the steps described above for the sensor connected to the second input.
• Press ESC to go back to measurement mode.
The configuration process is completed.
MC I NITIALIZATION P ROGRAM
This program prepare the memory card for the use with the HD2030 and erases the files previously stored in the card. For the details see the chapter dedicated to the memory card.
Proceed as follows:
• After inserting the card in the slot placed in the front of the analyzer, switch on the instrument.
• When the “MC installed and ready to use” message appears, press the RD/WR key to enable all read and wright functions.
• Start the program MENU >> Programs >> MC Initialization.
INITIALIZE MC
Batt: 90% Mem: 50%
CONFIRM
MEMORY CLEAR?
YES NO
• Press YES to proceed, NO to cancel the operation.
• At the end the following screen appears:
- 54 -
MC installed and ready.
Size: 1000 MB
ESC RD RD/WR
Press RD/WR to activate all the reading and writing functions.
The card is ready for the use.
- 55 -
DESCRIPTION OF THE MENU FUNCTIONS
The menu provides all the functions to set the parameters for the instrument functioning.
The menu is entered with Menu key> Parameters.
The access to the menu is allowed also with the instrument in measure mode, while for the modification of a parameter the instrument must be in stop mode, If not, it appears a message requesting to stop the current measurement: WARNING! Stop the measure to proceed”.
WARNING!
Stop the measure to proceed.
YES NO
Pressing YES the instrument enters the STOP mode and it is possible to proceed with the modification of selected parameter.
Some of the parameters listed in the menu (for example the integration time Tint, VLM screen parameters,….) are editable directly from the measurement screens: see the chapter
“DESCRIPTION OF THE SCREENS” dedicated to the different modes of visualization.
The menu has a multi-level structure: with main categories and submenus. To select a menu item use the UP and DOWN arrows: the selected item blinks.
If the parameter placed on the right of a menu item does not blink, it means that the item cannot be modified.
SELECT PARAMETER
Instrument: HD2030
Serial N..: 123456789
Version: 108v3.6
Config. RIGHT: 1
Config. LEFT:
...
2
This parameter CAN’T be changed
This parameter is EDITABLE
Use the ENTER key to access the selected submenu or to modify the selected parameter.
The selected blinking parameter can be modified with the UP and DOWN arrows: to confirm the new value, press the ENTER key, while to cancel the modifications press the MENU key.
To exit from a menu and go back to the upper level till returning to the measurement screen, use the MENU key.
- 56 -
2011/10/25 10:00:00
Batt: 95% Mem: 99.5%
SELECT MENU
Instrument
Vibration Analyser
Spectrum Analyzer
…
Entering the menus, it is visualized the current date and time and, in the next line, the remaining charge of the batteries and the memory space available. The memory space refers to the external card, if any, otherwise to the internal Flash memory.
The message “SELECT MENU” becomes “SELECT SUB MENU” when the meter is inside a sub menu.
The points at the end of a list indicate that there are other items following the visible ones: to display them, press the DOWN arrow key.
Pressing MENU once, it appears the screen that allows to choose to access the Parame-
ters of the instrument or the programs.
2008/10/25 10:00:00
Batt: 95% Mem: 99.5%
Parameters
Programs
SELECT
The following table lists the available menus for the instrument setting.
MENU DESCRIPTION
Instrument:
• Identification
• System
• Input/Output
Identification of the instrument and configuration of the accelerometers.
Date and time, type of batteries and display settings.
Reading of the accelerometers polarization voltages. Menu language setting.
Setting of the automatic printing. Check of the RS232, USB,
Memory card interfaces.
• Measurements General coefficients for the calculation of the sum vector.
Vibration Analyzer Setting of the measurement parameters for the screens: VLM_1
(single axis), VLM_2 (vector), PROFILE, STATISTICS e PERCEN-
TILES.
- 57 -
MENU DESCRIPTION
Spectrum Analyzer Setting of the measurement parameters of the spectrum.
Data Logger:
• Profiles
• Global
Setting of the Data Logger mode and makers.
Setting of the global measurement parameters (VLM_3 and
VLM_4 screens). Auto-Store recording function.
Calibration
I NSTRUMENT
Setting of the calibrator acceleration.
The Instrument menu contains all the data related to the instrument identification, some instrument and interfaces management parameters, the input and output settings and the global acquisition parameters. It is composed by four submenus that are described below:
Identification
It contains the information that identifies the instrument and the accelerometers.
• Instrument: instrument model.
• Serial number: instrument serial number.
• Version: firmware version currently installed in the instrument.
• RIGHT configuration: number of the selected configuration for the RIGHT input. There are 9 configurations available. The parameter can be selected from 0 (deactivated channel) to 9.
• LEFT configuration: number of the selected configuration for the LEFT input. There are
9 configurations available. The parameter can be selected from 0 (deactivated channel) to 9.
• RIGHT Channel: it indicates OFF when the channel is deactivated, ON TRI when the input is connected to a triaxial accelerometer, ON MON when the input is connected to a monoaxial accelerator.
• Manufacturer: manufacturer of the accelerometer connected to the RIGHT input.
• Model: model of the accelerometer connected to the RIGHT input.
• Serial Number: serial number of the accelerometer connected to the RIGHT input.
• Sensitivity: nominal sensitivity (in mV/g) of the accelerometer connected to the RIGHT input.
• LEFT Channel: it indicates OFF when the channel is deactivated or ON MON when the input is connected to a monoaxial accelerator.
• Manufacturer: manufacturer of the accelerometer connected to the LEFT input.
• Model: model of the accelerometer connected to the LEFT input.
• Serial Number: serial number of the accelerometer connected to the LEFT input.
• Sensitivity: nominal sensitivity (in mV/g) of the accelerometer connected to the LEFT input.
• Memory Size: Size of the Memory Flash in the instrument. The standard size is
8Mbyte.
• Options: it indicates the installation of firmware options, if any.
System
It allows to set some system parameters.
- 58 -
• Hour: current hour.
• Date: current date in the format year/month/day.
• Vpol ch1: it indicates the polarization voltage of the accelerometer connected to the
RIGHT input channel n.1. The STOP indication, if displayed, indicates that the instrument is in stop mode or that the input is not connected to a sensor.
• Vpol ch2: it indicates the polarization voltage of the accelerometer connected to the
RIGHT input channel n.2. The STOP indication, if displayed, indicates that the instrument is in stop mode or that the input is not connected to a sensor.
• Vpol ch3: it indicates the polarization voltage of the accelerometer connected to the
RIGHT input channel n.3. The STOP indication, if displayed, indicates that the instrument is in stop mode or that the input is not connected to a sensor.
• Vpol ch4: it indicates the polarization voltage of the accelerometer connected to the
LEFT input. The STOP indication, if displayed, indicates that the instrument is in stop mode or that the input is not connected to a sensor.
• Battery: it indicates the battery type installed in the instrument. It is possible to choose between ALKALINE (alkaline batteries) or NiMH (rechargeable Nickel-metal hydride batteries).
• Display Lighting: it indicates the activation of the of the display backlit. The backlit can also be activated or deactivated through the keyboard, holding pressed the CURSOR key while one of the VLM screens is visualized.
• Display Contrast: it allows to adjust the display contrast. When the ambient temperature changes, the display contrast has a small variation: it can be compensated inserting a higher value in order to increase the contrast or a smaller value to decrease it. The value can be set from 3 (minimum) to 9 (maximum).
• Auto-Switching Off: the instrument has a function to switch itself off automatically after 5 minutes if the instrument is in STOP mode and no keys are pressed in this time interval. Before switching itself off, the instrument emits a series of warning beeps: press a key to avoid the switching off of the instrument.
• Language: it allows to choose the instrument’s menu language between Italian, English, French and Spanish.
Input/Output
Submenu for the choice of the parameters related to the inputs and outputs of the instrument.
• Type of print: it activates the printing of the measured levels and it allows to choose which data to print. When the parameter is set to OFF, the printing is disabled. In the other cases data are automatically printed when the measurement ends. The possible settings are: OFF indicates printing disabled, VLM for printing the numerical parameters visualized in the VLM screen, SPC for the printing of the octave or third-octave bands levels and VLM+SPC for printing both. See the chapter “CONNECTION TO A
PRINTER”.
• TRGOUT Source: the TRGOUT output, if activated with TRGOUT=RUN, switches from the pause level to the active level when the instrument enters the acquisition mode
(RUN). When the parameter is set to OFF, the TRGOUT output is deactivated.
• TRGOUT Polarity: the TRGOUT output can have a positive (POS) or negative (NEG) polarity, with low or high pause level respectively.
• RS232 Baud Rate: this parameter allows to select the data transfer speed for the
RS232serial connection from a minimum of 300 to a maximum of 115200 baud. A higher value indicates a faster communication, so, if there are no other contrary
indications, select the higher possible value to speed up the data transfer. If the instrument is connected to a printer with RS232 serial input or with serial/parallel converter, the value supplied by the printer manufacturer must be set.
WARNING: when the serial interface is used, the communication between the instrument and the PC (or device with serial input) works only if the Baud Rate
- 59 -
of the instrument and PC (or device) is the same. The supplied Noise Studio software sets automatically the serial port of the PC: on the instrument set
“RS232 Baud Rate = 115200”.
• Memory: it allows to select the memory device where the data will be recorded. It is possible to select between the internal memory (INT) or the SD memory card (CARD).
• Serial Device: it identifies the device connected to the serial interface.
The connection possibilities are:
RS232: connection to a PC with COM ports or to a printer with RS232 serial interface
(for example HD40.1).
USB: connection to a PC through USB port. The connection to the USB port of a PC requests the installation of the apposite driver included in the Noise Studio CD-ROM.
Measurements
Under the item MEASURES there are the general acquisition parameters.
• Application: it is possible to choose the type of measure between the vibrations transmitted to the hand-arm system (HA), to the whole body (WB) or by buildings
(BV).
• Input Gain: select the appropriate input gain among 0dB, 10dB or 20dB, according to the vibrations level to be measured (see the technical data).
• Integration Delay: It allows to start the measurement after a stabilization interval settable from a minimum of 2s to a maximum of 99s.
• Integration Mode: the instrument has two different integration modes: single (SING) and multiple (MULT). The single mode resets the integrated levels at the beginning of the measurement and integrates in the Tint time set in Menu>>Parameters >> Instrument >> Measurement >> Int. Integration. At the end, the instrument stops automatically the measure.
The multiple integration mode divides the measurement time in intervals equal to the Tint integration time set in Menu >> Parameters >> Instrument >> Measurement
>> Int. Integration. At the beginning of each interval the integrated parameters are reset automatically. For a description of the modes, see the “MEASUREMENT MODES” chapter.
• Profile Sampling: sampling interval in the visualization of the time profile, settable from a minimum of 1s to a maximum of 1 hour.
• Integration Interval: in single integration mode, this parameter acts as a timer that stops the display updating (HOLD), settable from a minimum of 1s to a maximum of 99 hours. If set to 0s, the timer is deactivated and the integration can only be stopped manually with the START/STOP key. In the multiple integration mode, this parameter determines the duration of each integration interval from a minimum of 10s to a maximum of 1 hour.
• Measure unit: the instrument shows in the VLM screens the acceleration levels with one of the following measure units: m/s 2 , cm/s 2 , ft/s 2 , in/s 2 , g and dB (referred to 10 -6 m/s 2 ). When a measure unit different from dB is selected, the acceleration values in the other screens are visualized in m/s 2 .
• Pond. CH-1: filter applied to the acceleration detected in channel 1 of the RIGHT input for the calculation of the vector acceleration.
• Pond. CH-2: filter applied to the acceleration detected in channel 2 of the RIGHT input for the calculation of the vector acceleration.
• Pond. CH-3: filter applied to the acceleration detected in channel 3 of the RIGHT input for the calculation of the vector acceleration.
• Pond. CH-4: filter applied to the acceleration detected in channel 4 of the LEFT input for the calculation of the vector acceleration.
• Coefficient 1: coefficient applied to the weighted acceleration related to channel 1 in the calculation of the vector acceleration.
- 60 -
• Coefficient 2: coefficient applied to the weighted acceleration related to channel 2 in the calculation of the vector acceleration.
• Coefficient 3: coefficient applied to the weighted acceleration related to channel 3 in the calculation of the vector acceleration.
• High-Pass: high-pass filter that cuts the frequencies lower than 0.6 Hz. It can be useful to decrease the settling time of the accelerometers signal and to improve the response to vibrations with frequent pulses.
• Ch1-4 0=OFF 1=ON: the function allows to disable one or more measurement channels that, for example, are not used. The status of each channel is described by a number: 0 (zero) indicates disabled channel, 1 enabled channel.
The four channels are indicated in the sequence CH1, CH2, CH3, CH4: to have them all active, the menu item must be Ch1-4=1111. To disable for example the channel CH1, the menu item must be Ch1-4=0111. It is not allowed to disable all the channels at the same time.
V IBRATION A NALYSER
Vibration Analyser Menu contains all the parameters related to the VLM_1, VLM_2 and
PROFILE screens.
These items can be modified directly in the correspondent screens as described in “DESCRIP-
TION OF DISPLAY MODES” chapter.
• Par. Axis. 1 ÷ Par. Axis. 3: measurement parameters visualized in the VLM_1 screen in relation with the measure of the acceleration values for a single axis.
• Par. Vect. 1 ÷ Par. Vect. 3: measurement parameters visualized in the VLM_1 screen in relation with the measure of the vector acceleration values.
• Profile: measurement parameter visualized in the PROFILE screen.
S PECTRUM A NALYZER
The Spectrum Analyzer menu contains the parameters related to the spectrum calculation and visualization modes. These items, excluded the parameter Order, can be modify directly in the Spectrum screen.
• Auxiliary Pond: the frequency weighting of the wide band channel associated with the spectrum and visualized with a vertical bar placed on the right of the display. The pondered level is calculated weighting, according to the selected filter, the octave or thirdoctave bands levels.
• Mode: the updating mode of the octave or third-octave bands spectrum. It can be Multi-Spectra (MULTISP), maximum (MAXIMUM), minimum (MINIMUM) or Integrated
(AVERAGE). The multi-spectral mode provides a spectrum per second while the AVER-
AGE, MAXIMUM and MINIMUM modes respectively visualize the average, maximum and minimum spectrum integrated in the measurement time.
• Order: it allows to choice the order of the visualized spectrum: 1/1 for the octave bands spectrum and 1/3 for the third-octave bands spectrum.
• Spectrum Integration: this function of frequency integration allows to switch from the visualization of the accelerations spectrum (by selecting OFF that is “no integration”) to the velocity spectrum (X1: single integration) or displacements (X2: double integration).
The same setting can be obtained directly in measure mode through the arrow keys of the keypad.
D ATA L OGGER
In the recording menu are contained the parameters related to the storage of the measured data. It is composed by the two submenus Profiles and Global that are described below.
- 61 -
Profiles
It contains the markers and the profile recordings settings.
• Mark1 … Mark9: represent the available markers. During the recording it is possible to insert the markers to signal interesting events for the current measurement (for the details see the chapter (“RECORDING MODES”)
To assign a name to a marker:
• Use the UP and DOWN arrows to select one of the nine markers and confirm with
ENTER.
• The first character of the marker is selected and it can be modified by pressing the
UP and DOWN arrows.
• Press the right arrow to move to the second character, use the UP and DOWN arrows to modify the character.
• Repeat the previous two steps for all the characters that form the marker name.
• at the end press MENU to exit from the name editing mode.
Note: the markers can also be set by using the Noise Studio software.
• Mode: they are the two recording modes available Profile and Full.
“Profile” allows to memorize the profile of a measurement parameter (PROFILE screen), with the sampling interval set in “Menu >> Parameters >> Instrument >> Measurement >>Profile step” from 1s to 1 hour.
The second recording mode “Full”, when the integration mode is single (Menu >> Parameters >> Instrument >> Measurement >> Integration Mode) allows the recording of the profiles of the parameters visualized in the VLM_1 and VLM_2 screens and the spectra every second. When the multiple integration mode is active, it is also recorded the statistical analysis together with the VLM_1 and VLM_2 parameters and the spectra.
The recording interval is programmable from 10s to 1 hour (Menu >> Parameters >>
Instrument >> Measure >> Integration Interval).
ADC Channels: it sets the direct recording of samples (row signals) supplied by the AD converters. Through the UP and DOWN arrows it is possible to choose to record all the four channels (1234), only one at choice (1---, -2--, …) or the first three of the RIGHT input (123-). When “ADC Channels” is set on “OFF”, the ADC samples are not stored.
Note 1: it is not possible to select an ADC channel if the corresponding measuring channel CH is disabled: enable the measuring channels selecting MENU >> Parameters >>
Instrument >> Measurement >> Ch1-4.
Note 2: storage of the ADC samples is possible only in the Memory card.
Global
It contains the settings related to the recording of the global measurement parameters.
• Par. Axis. 1 … Par. Sing. 3: global parameters visualized in the VLM_3 screen related to the measurement of the acceleration levels for a single axis.
• Par. Vect. 1 … Par. Vect. 3: global parameters visualized in the VLM_4 screen related to the measure of the vector acceleration levels.
• Auto-Store: it activates the automatic storage of global levels at the end of the measurement (for the details see the chapter “RECORDING MODES”).
C ALIBRATION
• Level: the acceleration value produced by the device used for the calibration of the measurement chain. The acceptable values vary from 0.90m/s resolution of 0.01m/s 2 .
2 to 110.00m/s 2 with a
- 62 -
FIRMWARE UPDATE
The firmware, the program that handles all the analyzer functions, can be updated transferring the file from a PC to the HD2030 through the serial port.
In this way it is possible to update the instrument functionality.
The updating files are available at the authorized dealers.
To proceed with the update, it is necessary to have installed in the PC the Noise Studio software.
Refer to the on line manual of the software for the operation details.
- 63 -
REPORTING OF LOW BATTERIES AND REPLACEMENT OF THE
BATTERIES
The battery symbol placed in the upper right corner of the display constantly indicates the charge status of the batteries of the analyzer. As the batteries run down, the symbol is gradually "emptied"…
... when the battery voltage reaches the minimum value to operate correctly, the symbol blinks. In this condition change the batteries as soon as possible.
Continuing to use the instrument, the battery voltage drops further, and the analyzer is no longer capable of providing a proper measure; any data recording is automatically stopped, finally the acquisition is also stopped and the instrument enters the STOP mode.
Below a certain level the instrument turns itself off automatically. The stored data remain. Below a certain level of batteries charge it will not be possible to turn on the instrument.
The charge level of the batteries is available in the main screen of the menu, expressed as a percentage value. The item is accessed pressing the MENU key. When the level is 0%, it is necessary to replace the batteries.
The battery symbol is replaced by a mains plug when the external power supply is connected.
Note: the battery symbol blinks also when it is disabled the automatic auto-switch off (Auto
Power OFF = OFF).
To replace the batteries, switch off the instrument and unscrew anti-clockwise the two closing screws of the battery compartment cover. After the replacement of the batteries (4 batteries type AA, 1.5 V alkaline or NiMH rechargeable), close the cover screwing the two screws clockwise. Check the date and time after the replacement of the batteries.
If the batteries replacement takes less than two minutes, it should not be necessary to adjust the clock.
- 64 -
Instead of alkaline batteries, it is possible to use rechargeable batteries NiMH type.
To allow the analyzer to properly manage the charge level of the batteries, it must be selected in the menu the type of batteries used (MENU >> Parameters>> Instrument >>
System>> Battery = Alkaline or NiMH).
The external power supply does not charge the batteries: rechargeable batteries must be charged separately with an external charger.
W ARNING ON B ATTERIES U SE
• If the analyzer is not used for a long period of time, remove the batteries.
• If the batteries are discharged, replace them immediately.
• Avoid leakage from the batteries.
• Use watertight and good quality batteries, alkaline or NiMH.
• If the product does not turn on after the change of the batteries:
• Remove the batteries
• Wait at least 5 minutes to allow a complete discharge of the vibrations analyzer internal circuit
• Insert the missing battery: with charged batteries, the instrument should switches itself on automatically.
INSTRUMENT STORAGE
Storage conditions of the instrument:
• Temperature: -25 ... 70 ° C.
• Humidity: less than 90% R.H. not condensing.
• In the storage avoid places where:
The humidity is high.
The instrument is exposed to direct radiation of the sun.
The instrument is exposed to a source of high temperature.
There are strong vibrations.
There are steam, salt and/or corrosive gas.
The casing of the instrument is made of ABS plastic material and the protective band is made of rubber: do not use solvents to clean them.
- 65 -
SERIAL INTERFACE
The instrument has a dual serial interface:RS232C and USB.
The RS232 port has an 8-pole Mini-Din connector and it can be connected to any COM port of a PC or to a printer (e.g. the HD40.1) using the proper connection cable HD2110CSNM.
The USB port allows the connection to a USB port of a PC through the supplied cable
CP22 type A/B.
The interface selection is done through the menu item "MENU>> Parameters >> Instrument >> Input/Output >> Serial Dev.:
• RS232: connection through RS232 interface to a PC provided with a COM type port. For the connection it can be supplied on request the HD2110CSNM cable, null-modem type with female 9-pole subD connector. This cable is also usable for the connection to the
HD40.1 portable printer.
• USB: connection through USB interface to a PC that has installed the appropriate driver
VCOM. The drivers are included in the CD-ROM of the Noise Studio software. For the connection is supplied the cable CP22.
Unlike the RS232 connection that requires no special programs for its operation, the USB connection requires the prior installation in the PC of a special program (driver USB) provided in the CD that is supplied with the instrument.
In the MiniDin female 8-pole connector of the instrument there are the following signals:
Description Pin Direction Signal
1 Output VDD
2 Output DTE
3 Input DCE - CD
4
5
6
Output
Output
Input
RTS
TD
RD
DCE ready – Carrier detect
Request to send
Channel data reception
Channel data transmission
External view 7 -
8 Input
GND
CTS
Reference ground
Clear to send
In the subD female 9-pole connector of the HD2110CSNM cable, there are the following signals:
Pin Direction
1
Signal
DCE >> HD2030 DCE - CD
Description
DCE ready – Carrier detect
HD2030 Channel data reception
3 HD2030>> DCE TD Channel data transmission
External view
5 -
7
8
9
DCE ready
HD2030>> DCE RTS
DCE >> HD2030 CTS
HD2030>> DCE VDD
Request to send
Clear to send
3.3V power supply
When the instrument is connected via a serial interface to an active terminal
(DCE active, for example a PC), the auto-switch off is disabled and it is not possible
to switch off the instrument.
If the analyzer is turned off, the connection to an active terminal (DCE active) will lead to the automatic switch on.
The standard serial transmission parameters of the instrument are:
• Baud rate 115200 baud
• Parity None
• N. bit
• Stop bit
• Protocol
8
1
Hardware.
- 66 -
It is possible to change the speed of the data transmission through the item "baudrate" in the menu (MENU >> Parameters >> Instrument >> Input/Output >> baudrate).
The available baud rates are: 115200, 57600, 38400, 19200, 9600, 4800, 2400, 1200,
600, 300. The other transmission parameters cannot be altered.
To enable the full control of the instrument through a PC, the HD2030 is equipped with a communication protocol with a complete set of commands described in detail in the appendix.
- 67 -
MEASURE PARAMETERS
The parameters that can be displayed in the VLM and PROFILE screens are selectable among the ones of the following lists:
VLM_1 screen: Single axis parameters.
Parameter Description
Pk instant peak value of the frequency weighted acceleration.
Pkmx Max peak value of the frequency weighted acceleration.
AeqS Time average (linear) of the frequency weighted acceleration calculated in the last second (“running r.m.s.”):
A eqS
( t )
=
⎛
⎜⎜ t t
∫
−
1 s a w
2
(
ξ
) d
ξ
⎞
⎟⎟
1 / 2
Where: a w
(ξ) is the frequency weighted single axis instant acceleration.
Aeq Time average (linear) of the frequency weighted acceleration, calculated in the time:
A eq
=
⎛
⎜⎜
1
T
∫
0
T a w
2
(
ξ
) d
ξ
⎞
⎟⎟
1 / 2
where: a w
(ξ) is the frequency weighted single axis instant acceleration
T is the measurement time.
A1s Time average (exponential) of the frequency weighted acceleration with time constant of 1 second:
A
1 s
( t )
=
⎛
⎜⎜
1
τ
− ∞
∫ t a w
2
(
ξ
)
⎛ exp
⎝
ξ
τ
− t d
ξ
⎞
⎟⎟
1 / 2
Where: a w
(ξ) is the frequency weighted single axis instant acceleration
τ = 1s is the time constant of the exponential function.
A8s
A1smx
A8smx
A1smn
Time average (exponential) of the frequency weighted acceleration with a time constant of 8 seconds.
Maximum value of the timed average (exponential) of the frequency weighted acceleration with time constant of 1 second.
Maximum value of the timed average (exponential) of the frequency weighted acceleration with time constant of 8 seconds.
Minimum value of the timed average (exponential) of the frequency weighted acceleration with time constant of 1 second.
A8smn Minimum value of the timed average (exponential) of the frequency weighted acceleration with time constant of 8 seconds.
A(1s) Equivalent value of the frequency weighted acceleration in the measurement time referenced to 1 second:
A ( 1 s )
=
⎛
⎜⎜
1
T
0
T
∫
0 a w
2
(
ξ
) d
ξ
⎞
⎟⎟
1 / 2
where: a w
(ξ) is the frequency weighted single axis instant acceleration
T is the measurement time.
- 68 -
A(8) Equivalent value of the frequency weighted acceleration in the measurement time referenced to 8 hours:
A ( 8 )
=
⎛
⎜⎜
1
T
8 h
∫
0
T a w
2
(
ξ
) d
ξ
⎞
⎟⎟
1 / 2
where: a
T w
8h
(ξ) is the frequency weighted single axis instant acceleration
= 28800 is the number of seconds in 8 hours.
VDV Vibrations Dose Value in the measurement time:
VDV
=
⎛
⎜⎜
∫
0
T a w
4
(
ξ
) d
ξ
⎞
⎟⎟
1 / 4
where: a w
(ξ) is the frequency weighted single axis instant acceleration.
VDV,d Daily evaluation (8 hours) of the vibrations dose:
VDV , d
=
⎛
⎜⎜
T
T
8 h
∫
0
T a
4 w
(
ξ
) d
ξ
⎞
⎟⎟
1 / 4
where: a
T w
8h
(ξ) is the frequency weighted single axis instant acceleration
T is the measurement time
= 28800 is the number of seconds in 8 hours.
MTVV Maximum value of the time average (linear) of the frequency weighted acceleration calculated in the last second.
CFeq Crest factor calculated as ratio between the maximum peak value and the time average of the frequency weighted acceleration:
CF eq
=
⎛
⎜⎜
1
T
∫
0
T
Pk mx a w
2
(
ξ
) d
ξ
⎞
⎟⎟
1 / 2
where: a w
(ξ) is the frequency weighted single axis instant acceleration
T is the measurement time.
CF Crest factor calculated as ratio between the instant peak value and the time average of the frequency weighted acceleration in the last second:
Pk ( t )
CF ( t )
=
⎛
⎜⎜
2
(
ξ
) d
ξ
⎞
⎟⎟
1 / 2 t t
∫
− 1 s a w
where: a w
(ξ) is the frequency weighted single axis instant acceleration.
CFmx Maximum value of the Crest factor CF calculated as ratio between the instant peak value and the time average of the frequency weighted acceleration in the last second.
VDVr Ratio between the vibrations dose value (VDV) and the time average (linear) of the frequency weighted acceleration in the measurement time:
VDV r
=
⎛
⎜⎜
1
T
∫
0
T
VDV a
2 w
(
ξ
) d
ξ
⎞
⎟⎟
1 / 2
where: a w
(ξ) is the frequency weighted single axis instant acceleration
T is the measurement time.
- 69 -
MTVVr Ratio between the maximum value calculated in the last second (MTVV) and the time average (linear) of the frequency weighted acceleration calculated in the measurement time:
MTVV
MTVV r
=
⎛
⎜⎜
1
T
∫
0
T a w
2
(
ξ
) d
ξ
⎞
⎟⎟
1 / 2
where: a w
(ξ) is the frequency weighted single axis instant acceleration
T is the measurement time.
OL Percentage of time with “overload”.
UR Percentage of time with “under-range”
VLM_2 screen: Parameters referred to the acceleration vector.
Parameter Description
Pk Instant peak value of the frequency weighted acceleration:
Pk ( t )
= c
1
2
Pk
1
2
( t )
+ c
2
2
Pk
2
2
( t )
+ c
3
2
Pk
3
2
( t )
where:
Pk c
1,2,3
1,2,3
(t) are the instant peak values of the frequency weighted acceleration in each axis
are multiplying coefficients dependent on the specific application.
Pkmx Maximum peak value of the frequency weighted acceleration.
AeqS Time average (linear) of the frequency weighted acceleration calculated in the last second (“running r.m.s.”):
A eqS
( t )
=
⎛
⎜⎜ t t
∫
−
1 s
( c
1
2 2 a
1 , w
(
ξ
)
+ c
2
2 a
2
2
, w
(
ξ
)
+ c
3
2 a
3
2
, w
(
ξ
)
) d
ξ
⎞
⎟⎟
1 / 2
where: a c
1,2,3,w
1,2,3
(ξ) are the instant frequency weighted accelerations in each axis
are multiplying coefficients dependent on the specific application.
Aeq Time average (linear) of the frequency weighted acceleration, calculated in the measurement time:
A eq
=
⎛
⎜⎜
1
T
∫
0
T ( c
1
2 a
1 ,
2 w
(
ξ
)
+ c
2
2 2 a
2 , w
(
ξ
)
+ c
3
2 2 a
3 , w
(
ξ
)
) d
ξ
⎞
⎟⎟
1 / 2
where: a c
1,2,3,w
1,2,3
(ξ) are the instant frequency weighted accelerations in each axis
are multiplying coefficients dependent on the specific application
T is the measurement time.
A1s Time average (exponential) of the frequency weighted acceleration with time constant of 1 second:
A
1 s
( t )
=
⎛
⎜⎜
τ
1 t
∫
− ∞
( c
1
2 a
1 ,
2 w
(
ξ
)
+ c
2
2 2 a
2 , w
(
ξ
)
+ c
3
2 2 a
3 , w
(
ξ
)
) ⎛ exp
⎝
ξ
τ
− t d
ξ
⎞
⎟⎟
1 / 2
where: a c
1,2,3,w
1,2,3
(ξ) are the instant frequency weighted accelerations in each axis
are multiplying coefficients dependent on the specific application
τ = 1s is the time constant of the exponential equation.
A8s Time average (exponential) of the frequency weighted acceleration with a time constant of 8 seconds.
- 70 -
A1smx
A8smx
A1smn
A8smn
Maximum value of the time average (exponential) of the frequency weighted acceleration with time constant of 1 second.
Maximum value of the time average (exponential) of the frequency weighted acceleration with time constant of 8 seconds.
Minimum value of the time average (exponential) of the frequency weighted acceleration with time constant of 1 second.
Minimum value of the time average (exponential) of the frequency weighted acceleration with time constant of 8 seconds.
A(1s) Equivalent value of the frequency weighted acceleration in the measurement time referenced to 1 second:
A ( 1 s )
=
⎛
⎜⎜
1
T
0
∫
0
T ( c
1
2 2 a
1 , w
(
ξ
)
+ c
2
2 a
2
2
, w
(
ξ
)
+ c
3
2 a
3
2
, w
(
ξ
)
) d
ξ
⎞
⎟⎟
1 / 2
where: a
1,2,3,w c
1,2,3
(ξ) are the instant frequency weighted accelerations in each axis
are multiplying coefficients dependent on the specific application
T is the measurement time.
A(8) Equivalent value of the frequency weighted acceleration in the measurement time referenced to 8 hours:
A ( 8 )
=
⎛
⎜⎜
1
T
8 h
∫
0
T ( c
1
2 2 a
1 , w
(
ξ
)
+ c
2
2 a
2
2 , w
(
ξ
)
+ c
3
2 a
3
2
, w
(
ξ
)
) d
ξ
⎞
⎟⎟
1 / 2
where: a
1,2,3,w c
1,2,3
T
8h
(ξ) are the instant frequency weighted accelerations in each axis
are multiplying coefficients dependent on the specific application
= 28800 is the number of seconds in 8 hours.
MTVV Maximum value of the time average (linear) of the frequency weighted acceleration calculated in the last second.
CFeq Crest factor calculated as ratio between the maximum peak value and the time average of the frequency weighted acceleration:
CF eq
=
⎛
⎜⎜
1
T
∫
0
T ( c
1
2 2 a
1 , w
(
ξ
)
Pk mx
+ c
2
2 a
2
2 , w
(
ξ
)
+ c
3
2 a
3 ,
2 w
(
ξ
)
) d
ξ
⎞
⎟⎟
1 / 2
where:
Pk mx
is the maximum peak value of the frequency weighted acceleration vector a
1,2,3,w
(ξ) are the instant frequency weighted accelerations in each axis c
1,2,3
are multiplying coefficients dependent on the specific application
T is the measurement time.
CF Crest factor calculated as ratio between the instant peak value and the time average of the frequency weighted acceleration in the last second:
CF ( t )
=
⎛
⎜⎜
( c
1
2 a
1 ,
2 w
(
ξ
)
+
Pk c
2
2 a
2
2 , w
( t
(
ξ
)
)
+ c
3
2 a
2
3 , w
(
ξ
)
) d
ξ
⎞
⎟⎟
1 / 2 t t
∫
−
1 s
where:
Pk is the instant peak value of the frequency weighted acceleration vector a c
1,2,3,w
(ξ) are the instant frequency weighted acceleration in each axis
1,2,3
are multiplying coefficients dependent on the specific application.
CFmx Maximum value of the Crest factor CF calculated as ratio between the instant peak value and the time average of the frequency weighted acceleration in the last second.
- 71 -
MTVVr Ratio between the maximum value calculated in the last second (MTVV) and the time average (linear) of the frequency weighted acceleration calculated in the measurement time:
MTVV r
=
⎛
⎜⎜
1
T
∫
0
T ( c
1
2 a
1 ,
2 w
(
ξ
)
+
MTVV c
2
2 2 a
2 , w
(
ξ
)
+ c
3
2 2 a
3 , w
(
ξ
)
) d
ξ
⎞
⎟⎟
1 / 2
where: a
1,2,3,w c
1,2,3
(ξ) are the instant frequency weighted accelerations in each axis
are multiplying coefficients dependent on the specific application
T is the measurement time.
VLM_3 Screen: Single axis global parameters.
Parameter Description
Pkmx Maximum peak value of the frequency weighted acceleration.
Aeq Time average (linear) of the frequency weighted acceleration calculated in the measurement time:
A eq
=
⎛
⎜⎜
1
T
T
∫
0 a w
2
(
ξ
) d
ξ
⎞
⎟⎟
1 / 2
where: a w
(ξ) is the single axis frequency weighted instant acceleration
T is the measurement time.
A1smx
A8smx
A1smn
A8smn
Maximum value of the time average (exponential) of the frequency weighted acceleration with time constant of 1 second.
Maximum value of the time average (exponential) of the frequency weighted acceleration with time constant of 8 seconds.
Minimum value of the time average (exponential) of the frequency weighted acceleration with time constant of 1 second.
Minimum value of the time average (exponential) of the frequency weighted acceleration with time constant of 8 seconds.
A(1s) Equivalent value of the frequency weighted acceleration in the measurement time referenced to 1 second:
A ( 1 s )
=
⎛
⎜⎜
1
T
0
∫
0
T a w
2
(
ξ
) d
ξ
⎞
⎟⎟
1 / 2
where: a w
(ξ) is the frequency weighted single axis instant acceleration
T is the measurement time.
A(8) Equivalent value of the frequency weighted acceleration in the measurement time referenced to 8 hours.
A ( 8 )
=
⎛
⎜⎜
1
T
8 h
∫
0
T a w
2
(
ξ
) d
ξ
⎞
⎟⎟
1 / 2
where: a
T w
8h
(ξ) is the frequency weighted single axis instant acceleration
= 28800 is the number of seconds in 8 hours.
VDV Vibrations Dose Value in the measurement time:
VDV
=
⎛
⎜⎜
∫
0
T a w
4
(
ξ
) d
ξ
⎞
⎟⎟
1 / 4
where:
- 72 -
a w
(ξ) is the frequency weighted single axis instant acceleration.
VDV,d Daily evaluation (8 hours) of the vibrations dose:
VDV , d
=
⎛
⎜⎜
T
T
8 h
∫
0
T a
4 w
(
ξ
) d
ξ
⎞
⎟⎟
1 / 4
where: a w
(ξ) is the frequency weighted single axis instant acceleration
T is the measurement time.
MTVV
T
8h
= 28800 is the number of seconds in 8 hours.
Maximum value of the time average (linear) of the frequency weighted acceleration calculated in the last second.
CFeq Crest factor calculated as ratio between the maximum peak value and the time average of the frequency weighted acceleration:
CF eq
=
⎛
⎜⎜
1
T
Pk mx
∫
0
T a w
2
(
ξ
) d
ξ
⎞
⎟⎟
1 / 2
where: a w
(ξ) is the frequency weighted single axis instant acceleration
T is the measurement time.
CF Crest factor calculated as ratio between the instant peak value and the time average of the frequency weighted acceleration in the last second:
( t )
Pk ( t )
CF
=
⎛
⎜⎜ (
ξ
) d
ξ
⎞
⎟⎟
1 / 2 t t
∫
−
1 s a w
2
where: a w
(ξ) is the frequency weighted single axis instant acceleration.
CFmx Maximum value of the Crest factor CF calculated as ratio between the instant peak value and the time average of the frequency weighted acceleration in the last second.
VDVr Ratio between the vibrations dose value (VDV) and the time average (linear) of the frequency weighted acceleration in the measurement time:
VDV r
=
⎛
⎜⎜
1
T
∫
0
T
VDV a
2 w
(
ξ
) d
ξ
⎞
⎟⎟
1 / 2
where: a w
(ξ) is the frequency weighted single axis instant acceleration
T is the measurement time.
MTVVr Ratio between the maximum value calculated in the last second (MTVV) and the time average (linear) of the frequency weighted acceleration calculated in the measurement time:
MTVV r
=
⎛
⎜⎜
1
T
∫
0
T
MTVV a w
2
(
ξ
) d
ξ
⎞
⎟⎟
1 / 2
where: a w
(ξ) is the frequency weighted single axis instant acceleration
T is the measurement time.
OL
UR
Percentage of time with “overload”.
Percentage of time with “under-range”.
- 73 -
VLM_4 Screen: Acceleration vector global parameters.
Parameter Description
Pkmx Maximum value of the frequency weighted acceleration.
Aeq Time average (linear) of the frequency weighted acceleration calculated in the measurement time:
A eq
=
⎛
⎜⎜
1
T
∫
0
T ( c
1
2 a
1 ,
2 w
(
ξ
)
+ c
2
2 2 a
2 , w
(
ξ
)
+ c
3
2 2 a
3 , w
(
ξ
)
) d
ξ
⎞
⎟⎟
1 / 2
where: a
1,2,3,w c
1,2,3
(ξ) are the instant frequency weighted accelerations in each axis
are multiplying coefficients dependent on the specific application
T is the measurement time.
A1smx
A8smx
A1smn
A8smn
Maximum value of the time average (exponential) of the frequency weighted acceleration with time constant of 1 second.
Maximum value of the time average (exponential) of the frequency weighted acceleration with time constant of 8 seconds.
Minimum value of the time average (exponential) of the frequency weighted acceleration with time constant of 1 second.
Minimum value of the time average (exponential) of the frequency weighted acceleration with time constant of 8 seconds.
A(1s) Equivalent value of the frequency weighted acceleration in the measurement time referenced to 1 second:
A ( 1 s )
=
⎛
⎜⎜
1
T
0
∫
0
T ( c
1
2 2 a
1 , w
(
ξ
)
+ c
2
2 a
2
2
, w
(
ξ
)
+ c
3
2 a
3
2
, w
(
ξ
)
) d
ξ
⎞
⎟⎟
1 / 2
where: a c
1,2,3,w
1,2,3
(ξ) are the instant frequency weighted accelerations in each axis
are multiplying coefficients dependent on the specific application
T is the measurement time.
A(8) Equivalent value of the frequency weighted acceleration in the measurement time referenced to 8 hours:
A ( 8 )
=
⎛
⎜⎜
1
T
8 h
∫
0
T ( c
1
2 2 a
1 , w
(
ξ
)
+ c
2
2 a
2
2 , w
(
ξ
)
+ c
3
2 a
3
2
, w
(
ξ
)
) d
ξ
⎞
⎟⎟
1 / 2
where: a c
T
1,2,3,w
1,2,3
8h
(ξ) are the instant frequency weighted accelerations in each axis
are multiplying coefficients
= 28800 is the number of seconds in 8 hours.
MTVV Maximum value of the time average (linear) of the frequency weighted acceleration calculated in the last second.
CFeq Crest factor calculated as ratio between the maximum peak value and the time average of the frequency weighted acceleration:
CF eq
=
⎛
⎜⎜
1
T
∫
0
T ( c
1
2 2 a
1 , w
(
ξ
)
Pk mx
+ c
2
2 a
2
2 , w
(
ξ
)
+ c
3
2 a
3 ,
2 w
(
ξ
)
) d
ξ
⎞
⎟⎟
1 / 2
where:
Pk mx
is the maximum peak value of the frequency weighted acceleration vector a c
1,2,3,w
1,2,3
(ξ) are the instant frequency weighted accelerations in each axis
are multiplying coefficients dependent on the specific application
T is the measurement time.
- 74 -
CFmx Maximum value of the Crest factor CF calculated as ratio between the instant peak value and the time average of the frequency weighted acceleration in the last second.
MTVVr Ratio between the maximum value calculated in the last second (MTVV) and the time average (linear) of the frequency weighted acceleration calculated in the measurement time:
MTVV r
=
⎛
⎜⎜
1
T
∫
0
T ( c
1
2 a
1 ,
2 w
(
ξ
)
+
MTVV c
2
2 2 a
2 , w
(
ξ
)
+ c
3
2 2 a
3 , w
(
ξ
)
) d
ξ
⎞
⎟⎟
1 / 2
where: a
1,2,3,w c
1,2,3
(ξ) are the instant frequency weighted accelerations in each axis
are multiplying coefficients dependent on the specific application
T is the measurement time.
PROFILE Screen page (only single axis parameters):
Parameter Description
Pkmx Maximum peak value of the frequency weighted acceleration.
Aeq Time average (linear) of the frequency weighted acceleration calculated in the measurement time:
A eq
=
⎛
⎜⎜
1
T
∫
0
T a w
2
(
ξ
) d
ξ
⎞
⎟⎟
1 / 2
where: a w
(ξ) is the single axis frequency weighted instant acceleration
T is the measurement time.
A1smx
A8smx
A1smn
A8smn
Maximum value of the time average (exponential) of the frequency weighted acceleration with time constant of 1 second.
Maximum value of the time average (exponential) of the frequency weighted acceleration with time constant of 8 seconds.
Minimum value of the time average (exponential) of the frequency weighted acceleration with time constant of 1 second.
Minimum value of the time average (exponential) of the frequency weighted acceleration with time constant of 8 seconds.
The parameter selected in the PROFILE mode is used for the statistical analysis.
The attribute of the parameters that can be displayed in the VLM and PROFILE modes indicates the related frequency weighting.
Hand-Arm (HA)
Whole Body (WB)
Fz, Fc, Wh
Fz, Fa, Wb, Wc, Wd, We, Wj, Wk
Building Vibrations (BV) Fz, Fm, Wm
Fz: Flat weighting on the entire frequency range
Fa: Band limitation filter for whole body measurements: 0.4Hz … 100Hz
Fc: Band limitation filter for Hand-Arm system measurements: 6.3Hz … 1250Hz
Fm: Band limitation filter for vibrations transmitted by buildings measurements: 0.8Hz …
100Hz
Wb: filter for the measurement of the whole body vertical acceleration (z axis) for standing, sitting or supine people (ISO 2631-4)
Wc: filter for the measurement of the whole body horizontal acceleration (x axis) transmitted from back to sitting people (ISO 2631-1)
- 75 -
Wd: filter for the measurement of the whole body horizontal acceleration (x or y axis), for standing, sitting or supine people (ISO 2631-1)
We: filter for the measurement of the whole body angular acceleration (all directions) for sitting people (ISO 2631-1)
Wh: filter for the measurement of the acceleration transmitted to the hand-arm system (all directions) (ISO 5349-1)
Wj: filter for the measurement of the head vertical acceleration (x axis) for supine people
(ISO 2631-1)
Wk: filter for the measurement of the whole body vertical acceleration (z axis) for standing, sitting or supine people (ISO 2631-1)
Wm: filter for the measurement of the buildings transmitted acceleration (all directions) (ISO
2631-2)
Frequency Weighting graphs are shown in appendix on page 128
The acceleration values can be displayed also as acceleration level in decibel using the relation:
L w
=
20 log a w a
0
where: a w a
0
is the frequency weighted acceleration
is the reference acceleration equal to 10 -6 m/s 2 (ISO 1683).
The measurement parameters can be displayed with different units.
MEASURE PARAMETER
SYMBOL DESCRIPTION
MEASURE UNIT
Pkmx
Aeq
Maximum peak value in the measurement time
AeqS Average acceleration value calculated every second with linear integration
Average acceleration value linearly integrated in the measurement time
A1s Average acceleration value calculated every second with a time constant equal to 1 second
A8s Average acceleration value calculated every second with a time constant equal to 8 seconds m/s 2 , cm/s 2 , ft/s 2 , in/s 2 g, dB
,
A1smx Maximum value of the average acceleration calculated every second with 1s time constant
8smx Maximum value of the average acceleration calculated every second with 8s time constant
A1smn Minimum value of the average acceleration calculated every second with 1s time constant
A8smn Minimum value of the average acceleration calculated every second with 8s time constant
A(1s) Value referenced to 1 second of the acceleration linearly integrated in the measurement time
A(8) Value referenced to 8 hours of the acceleration linearly integrated in the measurement time
MTVV Maximum value of the average acceleration linearly integrated every second
VDV Vibrations dose value linearly integrated in the measurement time
VDV,d Value referenced to 8 hours of the vibrations dose linearly integrated in the measurement time m/s 1.75
- 76 -
MEASURE PARAMETER
SYMBOL DESCRIPTION
CFeq
CF
Crest factor calculated as ratio between the maximum peak and the average of the acceleration.
It is calculated in the measurement time
Instant crest factor calculated as ratio between peak and average value of the acceleration in 1 second
CFmx Maximum instant crest factor value calculated as ratio between peak and average value of the acceleration in 1 second. It is calculated in the measurement time
VDVr Ratio between vibrations dose and the average value of the acceleration linearly integrated in the measurement time
MTVVr Ratio between the maximum value of average acceleration integrated every second and the average acceleration integrated in the measurement time. The acceleration integration is linear.
OL Overload time percentage during measurement
UR Under-range time percentage during measurement
MEASURE UNIT without dimension
%
- 77 -
DIRECT PRINTER CONNECTION
The HD2030 analyzer can print the visualized levels in a format compatible with that of a portable printer with 24 columns like the HD40.1 printer.
The printer has to be connected to the serial port of the instrument.
Printer and vibrations analyzer must be properly configured.
HD2030 configuration
1. Set the parameter MENU >> Parameters
>> Instrument >> Input/Output >> RS232
Baud Rate: 38.4k.
2. Set the parameter MENU >> Parameters
>> Instrument >> Input/Output >> Serial
Dev.: RS232.
Printer configuration
1. The communication speed of the printer (Baud Rate) must be equal to the one set in the analyzer (38400 baud).
This is the only parameter requested for the HD40.1 printer.
The other connection parameters for printers different from the HD40.1 are:
2. Data bits: 8.
3. Parity: none.
4. Stop bit: 1.
5. Flow control (Handshaking): Hardware.
6. Automatic paper advance (Autofeed): enable.
Connect the HD2030 to the printer using the HD2110CSNM cable.
To proceed with the data printing:
• Switch on the instrument.
• Enter the MENU >> Parameters >> Instrument >> Input/Output and set the item: o
Printout =
VLM for printing the numerical parameters visualized in the VLM screen,
SPC for printing the octave or third-octave bands levels,
VLM+SPC for printing both.
• Start the measurement: when the instrument enter the stop mode, the data are automatically printed.
• To disable the printing, set the menu item Printout = OFF.
- 78 -
CONNECTION TO A PC WITH USB INTERFACE
The HD2030 can be connected to the USB port of a PC using the CP22 cable.
The connection through the USB port requires the installation of a driver supplied with the Noise Studio Software.
Before connecting the instrument to the USB port of the PC, install the Noise
Studio software.
With Windows 7 operating systems you need to start your PC by disabling driver sig-
nature, as explained in the USB drivers installation guide contained in the installation
CDROM of Noise Studio software
Proceed as follows:
1. Set the instrument menu item “MENU >> Parameters >> Instrument >> Input/Output >> Serial Device” to “USB”. Confirm and exit from the menu”.
2. Do not connect the instrument to USB port until requested from the wizard
3. Insert Noise Studio installation CD-ROM and wait for AutoPlay window to appear. In
Windows Vista and Windows 7 operating systems it’s shown the window below; select
“autorun.exe execution” (see “note 1” in the next paragraph)
4. The starting screen of Noise Studio will be opened: if the operating system prevents software to start, please see “note 1” in the next paragraph.
5. From starting window of Noise Studio click on “USB drive installation” to start the driver installation procedure.
6. The program checks the Windows ® a temporary folder. operating system version and copies related drivers in
7. At the end a message appears asking to plug the vibration meter connection cable to PC
USB port: press OK and close Noise Studio software pressing EXIT key.
8. Connect the vibration meter to USB port and turn it ON: when Windows recognise the instrument, it appears a message “ a new device has been detected”.
9. Wait some seconds until the message “new hardware is installed and ready to work” appears.
10. Driver installation procedure is ended: whenever the instrument will be connected it will be automatically recognized.
- 79 -
Installation Notes
Note 1: for Windows Vista and Windows 7 operating systems..
1. For software installation is requested Administrator permission
2. If the operating system prevents the software to open, boot the PC as administrator user
, insert installation CD-ROM and, when the following window appears, select “open folder to view files”
3. In the following screen, click with right mouse key on file “Autorun” and select “Execute as
administrator”:
4. Continue from point 5 of previous paragraph.
Note 2: if the vibration meter has been connected to USB port before USB driver installa-
tion, in Windows 2000 and XP operating systems it appears the window “new hardware
installation”. In Windows Vista and Windows 7 it appears an installation error under “device manager”: in both cases, cancel operation, disconnect instrument and restart the complete procedure starting from the beginning of this guide.
Verification of proper driver installation
To verify the proper installation procedure, proceed as follows.
On Windows 2000 and XP operating systems:
Select “START >> Settings >> Control Panel”, double click on SYSTEM icon. Select
“Hardware >> Device Manager”
On Windows Vista and Windows 7 operating systems:
Select “START >> Control panel”, then click on “Device Manager” icon.
Connect instrument to USB port.
The following items should appear:
• “Port (COM and LPT) >> USB Serial Port (COM#)”. The value # is the number as- signed to virtual serial port
• “Controller USB (Universal serial bus) >> USB serial converter”
- 80 -
When USB cable is unplugged, the above items will disappear and they will appear again as soon as the instrument is plugged to USB port.
In the documentation supplied with the Noise Studio CD-ROM, it’s available a detailed version, including pictures, of the USB driver management guide. Procedure to remove USB driver is also reported.
- 81 -
CONNECTORS DESCRIPTION
Front panel connectors
The following figure indicates the connectors in the HD2030 front panel.
Right connector
Identified with R letter, it is a male connector with 4 poles LEMO-B type for the connection of a triaxial or monoaxial accelerometer with integrated electronics (IEPE type or compatible). The pin numbering is seen from outside.
PIN DESCRIPTION
1 Ground
2 Accelerometer channel #3
3
4
Accelerometer channel #2
Accelerometer channel #1
LINE connector
Identified with AC_OUT indication, it is a 6 poles connector LEMO-B type for the analog outputs (LINE) of the 4 input channels.
The pin numbering is seen from outside
PIN DESCRIPTION
1 Ground
2 Line Output #1
3
4
5
Line Output #2
Line Output #3
Line Output #4
Left connector
Identified with L letter, it is a male connector with 4 poles LEMO-B type for the connection of a monoaxial accelerometer with integrated electronics (IEPE type or compatible).
The pin numbering is seen from outside
PIN DESCRIPTION
1 Ground
2 Accelerometer channel #4
- 82 -
Trigger Connector
Male connector with 4 poles LEMO-00 type for the trigger function, it is identified with TRG indication. The trigger input is differential type.
The pin numbering is seen from outside.
PIN DESCRIPTION
1 Negative input of trigger
3 Ground
4 Positive input of trigger
Headphones jack
Jack (Ø3.5mm) type output for the connection of the headphones.
Audio Signal
Microphone jack
Jack (Ø3.5mm) type input pin for the microphone.
NC
Ground Audio Signal
Bottom panel connectors
Following is the description of the connectors present in the bottom panel of the HD2030.
- 83 -
Power supply connector
Male connector for external power supply (∅ 5.5mm-2.1mm pin).
It requires a 9…12Vdc/300mA power supply.
The positive of the power supply is supplied to central pin.
MiniDin 8 poles connector
MiniDin 8 poles connector for RS232C serial port. For the connection use the null-modem dedicated serial cable (HD2110CSNM code), provided with a subD 9 poles connector.
Note: inserting the connector, be sure that the arrow printed on surface is upwards.
The connector description is indicated in the “SERIAL INTERFACE” chapter.
USB Connector
USB connector type B for the connection of the vibration analyzer to the USB port of a PC with
CP22 code cable.
The pin numbering is seen from outside.
PIN DESCRIPTION
1 +5Vdc
4 Ground
- 84 -
TECHNICAL SPECIFICATIONS
The HD2030 vibrations analyzer is able to detect the accelerations in four axis.
The sensors that can be connected are IEPE type with amplifying integrated electronics, triaxial or monoaxial type.
Three axes are grouped in the right channel that supports triaxial or monoaxial type accelerometers; the fourth axis is associated with the left channel that supports monoaxial accelerometers. The instrument analyzes the signal provided by the accelerometers and elaborates the four axes data at the same time. The instrument perform octave or third-octave bands spectrum analysis and statistical analysis.
The HD2030 vibrations analyzer complies with the following Rules:
ISO 8041:2005 “Human response to vibration – Measuring instrumentation”
ISO 5349-1:2001 “ Mechanical vibration – Measurement and evaluation of human exposure to hand-transmitted vibration – General requirements”
ISO 5349-2:2001 “ Mechanical vibration – Measurement and evaluation of human exposure to hand-transmitted vibration – Practical guidance for measurement at the workplace”
ISO 2631-1:1997 “Mechanical vibration and shock – Evaluation of human exposure to whole body vibration – General requirements”
ISO 2631-2:1989 “Evaluation of human exposure to whole body vibration – Continuous and shock-induced vibrations in buildings (1 to 80 Hz)”
ISO 2631-4:2001 “Evaluation of human exposure to whole body vibration – Guidelines for the evaluation of the effects of vibration and rotational motion on passenger and crew comfort in fixed-guideway transport systems”
ISO 2631-5:2004 “Evaluation of human exposure to whole body vibration – Method for evaluation of vibration containing multiple shocks”
IEC 61260:1995 “Electroacoustics – Octave band and fractional-octave band filters”
ISO 6954:2000 “Mechanical vibration - Guidelines for the measurement, reporting and evaluation of vibration with regard to habitability on passenger and merchant ships”.
Accelerometers models
It is possible to connect triaxial or monoaxial accelerometers with integrated electronics
(IEPE type or equal). The accelerometers are current supplied with a polarization voltage of 25V and a maximum current of 2mA. With the HD2030 analyzer can be supplied the following accelerometers:
Accessories
The following accessories are supplied on request:
HD6188: tube of hydro-repellent silicone grease and electrically insulating.
HD6273: tray with bonding wax.
080A90: glue for quick fastening.
081B05: double threaded screw 10-32 UNF. double threaded screw 5-40 UNC and 10-32 UNF.
081A90:
M081B05: double threaded screw 10-32 UNF and M6 X 0.75.
M081A27: double threaded screw 10-32 UNF and M3 X 0.5”.
081A27: double threaded screw 5-40 UNC. accelerometer push-rod.
HD6239:
HD6286: adhesive metallic plate for assembly through magnet. Used to magnetically couple the accelerometer on non-metal surfaces.
HD6284: insulated magnetic base with 10-32 UNF threaded hole.
HD6196: magnetic base with integrated 10-32 UNF screw.
HD6226: adhesive mounting base with threaded through hole (10-32 UNF).
HD6245: adhesive mounting insulated base with integrated screw 10-32 UNF.
HD6220: insulated base with integrated mounting 10-32 UNF screw and threaded hole 10-32 UNF for accelerometer mounting.
- 85 -
M ETROLOGICAL SPECIFICATIONS
The HD2030 vibrations analyzer can perform measurement on the hand-arm system, the whole body or vibrations transmitted by the buildings. The weighting filters and the frequency range of the filters with constant percentage octave or third-octave band depend on the chosen analysis mode.
Frequency Weighting for RMS measurements:
Fz, Fc e Wh for the measurement on the hand-arm system
Fz, Fa, Wb, Wc, Wd, We, Wj, Wk for the whole body measurements
Fz, Fm e Wm for the measurements of whole body transmitted by the buildings vibrations.
The Fz weighting is flat on all the frequency range with the following features:
Fz
High-pass OFF
Attenuation
[dB]
Frequency range
[Hz]
< 0.1
< 1
< 3
1.25 ÷ 1600
0.4 ÷ 3200
0.2 ÷ 3700
Activating the High Pass filter (Menu >>Parameters >> Instrument >> Measurement >>
High-Pass filter) the Fz weighting have the following features:
Fz
High-pass ON
Attenuation
[dB]
Frequency range
[Hz]
< 0.1
< 1
< 3
4 ÷ 1600
1.25 ÷ 3200
0.7 ÷ 3700
The Fa, Fm and Fc weightings are band-pass filters with the following features (High-Pass
OFF):
Filter Band Limits (to -3dB)
[Hz]
Fa
Fm
0.4 ÷ 100
0.8 ÷ 100
Fc 6.3 ÷ 1250
The Wb, Wc, Wd, We, Wj, Wk and Wm filters respect ISO 8041:2005 standard.
Octave or third-octave bands spectral Analysis
The constant percentage band filters comply with the rule IEC 61260. The range of the central frequencies depends on the selected application as reported in the following table.
Application
Central frequencies range
Octave bands Third-octave bands
[Hz]
Hand-Arm
Whole body
Building vibration
4 ÷ 2000
0.5 ÷ 250
0.5 ÷ 250
3.15 ÷ 3150
0.315 ÷ 315
0.315 ÷ 315
- 86 -
Self-generated noise
The intrinsic noise, for the different frequency weightings and for constant percentage bands, both in octave and third-octave, is measured short-circuiting the input channels.
For the Hand-Arm measurements, the detected values are indicated in the following tables:
HAND ARM
Center frequency octave bands
[Hz]
[uV]
4
Weightings Fz Fc Wh
[uV] 17 10 7
8 16 32 63 125 250 500 1000 2000
4 4 3 3 4 4 4 5 6 7
Center frequency third-octave bands
[Hz]
[uV]
3.2 4 5 6.3 8 10 12.5 16 20 25
2 2 2 2 2 2 2 2 2 2
Center frequency third-octave bands
[Hz]
[uV]
32 40 50 63 80 100 125 160 200 250 315
2 2 2 2 2 2 2 2 2 3 3
Center frequency third-octave bands
[Hz]
[uV]
400 500 630 800 1k 1.3k 1.6k 2k 2.5k 3.2k
3 3 3 3 3 4 4 5 5 5
For Whole-Body measurements, the detected values are indicated in the following tables:
WHOLE BODY
Weightings Fz Fa Wb Wc Wd We Wj Wk
[uV] 21 14 8 13 13 11 10 9
Central Frequency octave bands
[Hz]
Self-generated Noise
[uV]
0.5 1 2 4 8 16 32 63 125 250
8 6 5 3 5 2 2 3 3 3
Central Frequency third-octave bands
[Hz]
Self-generated Noise
[uV]
0.32 0.4 0.5 0.63 0.8 1 1.25 1.6 2 2.5
5 5 4 4 4 4 3 3 3 2
Central Frequency third-octave bands
[Hz]
Self-generated Noise
[uV]
3.2 4 5 6.3 8 10 12.5 16 20 25
2 2 2 2 2 2 1 1 1 1
Central Frequency third-octave bands
[Hz]
Self-generated Noise
[uV]
32 40 50 63 80 100 125 160 200 250 315
- 87 -
For building vibrations measurements, the values are indicated in the following tables:
BUILDING VIBRATIONS
[uV] 21 13 10
For the Buildings Vibration measurements, the detected values of the octave and thirdoctave bands noise is the same detected for the Whole Body measurements.
Linearity range
The linearity range is independent from the frequency and it is equal to 80dB. The maximum measurable level depends on the gain of the input amplifier as indicated in the following table:
Gain
[dB]
Lower Limit
[mVrms]
Upper Limit
[Vrms]
0 0.7 7
10 0.22 2.24
20 0.07 0.7
As an example, following are indicated the linear ranges for two different sensitivity of the accelerometer.
Gain
[dB]
0
10
20
Linear range with accelerometer
Sensitivity
10mV/g ∼ 1mV/m/s 2
0.7 ÷ 7000 m/s 2
0.22 ÷ 2240 m/s 2
0.07 ÷ 700 m/s 2
117 ÷ 197 dB
107 ÷ 187 dB
97 ÷ 177 dB
0.7 cm/s 2
0.22 cm/s 2
Sensitivity
1V/g ∼ 100mV/m/s
÷ 70 m/s 2
÷ 22.4 m/s
0.07 cm/s 2 ÷ 7 m/s 2
2
2
77 ÷ 157 dB
67 ÷ 147 dB
57 ÷ 137 dB
Integration Time
The integration time can be set from a minimum of 1s to a maximum of 99 hours.
Crosstalk
The crosstalk between channels is <100dB@1kHz.
Reference conditions
• The measure range is the one with input gain equal to 10dB.
• The level is equal to 10mV corresponding to 140dB or 10m/s a sensitivity equal to 10mV/g.
2
Operating conditions
for an accelerometer with
• Storage temperature: -25 ÷ 70°C.
• Working temperature: -10 ÷ 50°C.
• Protection Degree: IP64.
Drift
• Temperature: ± 0.3dB over the range -10 ÷ 50°C.
E LECTRICAL F EATURES
Pre-heating time
Less than 1 minute.
Power supply
• Internal batteries: 4 x 1.5 V alkaline or NiMH rechargeable batteries type AA. The instrument does not charge the batteries.
- 88 -
• Autonomy: > 10 hours in acquisition (RUN) mode with good quality alkaline batteries.
• External batteries: it is possible to connect an external battery pack to the instrument through the male connector for external power supply (∅ 5.5mm-2.1mm pin). The positive pole has to be connected to the central pin. The battery has to supply 9÷12V with at least 300mA/h. The maximum limit for external supply is 15V.
• Mains: mains adaptor with 9÷12Vdc/300mA direct voltage.
• Switching off: automatic, it can be disabled.
When the batteries voltage is less than 3.8V, the instrument is not able to measure.
However, it is still possible to view and download the memorized data.
Under 3.5V the instrument switches itself off automatically. The memorized data, the configuration and the calibration parameters are kept also without power supply.
Maximum input levels
The input signal must be in the range 0V÷25V.
LINE outputs
• Multi-pole circular connector (LEMO)
• Pre-amplified signal not pondered with an gain equal to 0.1V/V.
• Linearity: 110dB with maximum output level equal to 1.5Vrms.
• Series impedance: 1kΩ
• Typical load: 100kΩ
TRGOUT output
• Jack stereo socket ∅ 3.5mm
• Digital output 0 ÷ 3.3V short-circuit protected
• Pull-up impedance : 1kΩ
• Pull-down impedance: 30Ω
TRGIN input (Advanced Analyzer option)
• Jack stereo socket ∅ 3.5mm
• Current input: threshold 0.5mA max 20mA
• Voltage input: threshold 2V max 10V
• Series impedance: 470 Ω
RS232 Serial Interface:
• Socket: MiniDin 8 poles.
• Type: RS232C (EIA/TIA574) not isolated
• Baud rate: from 300 to 115200baud
• Data bit: 8
• Parity: None
• Stop Bit: 1
• Flow Control: Hardware
• Cable length: max 15m
USB Serial Interface:
• Socket: USB-B
• Type: USB 1.1 o 2.0 with 500mA
- 89 -
S TATISTICAL A NALYSIS
Statistical analysis is calculated on the chosen profile screen descriptor (Menu >> Parameters >> Vibration Analyzer >> Profile). Analysis is made with:
• 1s sampling.
• 1dB classes.
Calculation and display of the statistical graphs.
Graph of the levels probability distribution.
Graph of the percentile levels from L
1
to L
99.
S PECTRAL A NALYSIS
Acceleration signals spectral analysis is calculated in parallel with other calculations on all the four 4 channels
• Sampling: 8 kHz
• Resolution: 25bit
Average spectrum or Multi-spectrum with 1 second sampling period.
Octave bands from 4 Hz to 2kHz for hand-arm measurements and from 0.5Hz to 250Hz for whole body or buildings measurements.
Third-octave bands from 3.2Hz to 3.2kHz or from 0.32Hz to 315Hz
Ratio of the center frequencies: base 2
V ISUALIZATION
Graphic Display
128x64 pixel with 56x38mm wide backlit.
Mode:
VLM_1 and VLM_3 (vibration level meter) screens, each one with 3 parameters at choice for acceleration measurements related to the single channel.
VLM_2 and VLM_4 (vibration level meter) screens, each one with 3 parameters at choice for acceleration measurements related to the vector formed by 1,2 and 3 channels.
time profile of a parameter at choice with sampling time from 1s to 1 hour.
Octave or third-octave spectrum.
probability distribution of levels in 1dB classes.
Graph of the percentile levels from L
1
to L
99
.
M EASUREMENTS STORAGE
8MB permanent internal memory FLASH type
Card slot for SD memory type up to 2GByte
Safety of memorized data
Independent from the condition of the batteries charge.
- 90 -
O THER F EATURES
It is possible to activate the automatic printing of the acquired parameters at the end of the measurement. The printer must be connected to the RS232 interface.
Vocal comments
It’s possible to add a vocal comment to every measurement stored on the flash internal memory or on the memory card. Stored vocal comments can be listened using the “Navigator” program. For recording and listening vocal comments it’s necessary to connect a microphone and headphones on the dedicated connector placed on the frontal panel.
Digital recording
On the SD memory card, it’s possible to record raw digital samples coming from accelerometer’s signals, in parallel with the standard recording functions. Signals digitization has the following properties:
• Sampling frequency: 8 ksmp/s
• Resolution: 0.05%
• Dynamic: 100dB
By setting the parameter Menu >> Parameters >> Data Logger >> Profiles >> ADC Channels the digital recording function can be activated. The user can activate one single channel chosen from the four available, only the first three or all simultaneously.
Slot
• Dimensions (Length x Width x Height): 245x100x50mm,
• Weight: 740g (complete with batteries)
• Materials: ABS, rubber
Time:
Date and time: clock and calendar updated in real time
Maximum deviation: 1min/month
- 91 -
A
CCELEROMETERS TECHNICAL SPECIFICATIONS
The HD2030 analyzer can be supplied with the following monoaxial accelerometers:
HDD3200B5T Model
Type:
Sensitivity:
Measure range:
Frequency response:
Resonance frequency:
Linearity:
Transverse sensitivity:
Dytran production accelerometer with integrated electronics (LIVM TM ). This sensor is usually used for hand–arm measurements when extremely high vibration levels at high frequency need to be measured or for shock measurements.
1mV/g
±50000 m/s 2
0.5Hz ÷ 40kHz
130kHz
1% F.S.
3% max
Maximum Shock:
Working Temperature:
Polarization Voltage:
Mechanical features:
50000gpk
-50°C ÷ 120°C
8.5Vdc
• Weight:
• Dimensions:
• Mounting:
• Connector:
• Material:
• Isolation:
6gr
(hex-diameter x height) 12.7mm x 23.1mm integrated screw 10-32 UNF-2A upper micro coaxial 10-32 stainless steel
>10Mohm between the enclosure and the ground terminal
Cable (not included): HD2030.CAB13 + HD2030CAB1B to connect to the analyzer’s triaxial input and HD2030.CAB1-xM (3m, 5m e 10m) to connect the monoaxial input
HDD3019A1 model
Type:
Sensitivity:
Measure range:
Frequency response (±5%):
Resonance frequency:
Linearity:
Transverse sensitivity:
Maximum Shock:
Working Temperature:
Polarization Voltage:
Mechanical features:
• Weight:
• Dimensions:
• Mounting:
• Connector:
• Material:
• Isolation:
Cable (not included):
Dytran production accelerometer witn integrated electronics (LIVM TM ). This sensor is normally used for handarm measurements.
10 mV/g
±5000 m/s 2
1 Hz ÷ 10 kHz
50 kHz
2% F.S.
5% max
3000 gpk
-50 °C ÷ 150 °C
10 Vdc
8 gr
(hex-diameter x height) 9.6 mm x 18.6 mm integrated screw 10-32 UNF upper micro coaxial 10-32 stainless steel enclosure connected to ground terminal
HD2030.CAB13 + HD2030CAB1B to connect to the analyzer’s triaxial input and HD2030.CAB1-xM (3m, 5m e
10m) to connect the monoaxial input.
- 92 -
Modello HDP352C34
Type:
Sensitivity:
Measure range:
Frequency response (±5%):
Resonance frequency:
Linearity:
Transverse sensitivity:
Maximum Shock:
Working Temperature:
Polarization Voltage:
Mechanical features:
• Weight:
• Dimensions:
• Mounting:
• Connector:
• Material:
• Isolation:
• Screw:
Cable (not included):
5.8 gr
(hex-diameter x height) 11.2 mm x 22.4 mm threaded hole 10-32 UNF upper micro coaxial 10-32 titanium
>10Mohm between the enclosure and the ground terminal
Included accessories:
• Screw: double thread 10-32 UNF copper-beryllium alloy
(081B05) double thread 10-32 UNF and M6 copper-beryllium alloy
(M081B05)
HD2030.CAB13 + HD2030CAB1B to connect to the analyzer’s triaxial input and HD2030.CAB1-xM (3m, 5m e
10m) to connect the monoaxial input.
Modello HDD3056B2
PCB Piezotronics production accelerometer with integrated electronics (ICP TM ). This sensor is normally used for whole body measurements.
100 mV/g
2 ±500 m/s
0.5 Hz ÷ 10 kHz
50 kHz
1% F.S.
5% max
5000 gpk
-54 °C ÷ 93 °C
10 Vdc
Type:
Sensitivity:
Measure range:
Frequency response (±5%):
Resonance frequency:
Linearity:
Transverse sensitivity:
Maximum Shock:
Working Temperature:
Polarization Voltage:
Mechanical features:
• Weight:
• Dimensions:
• Mounting:
• Connector:
• Material:
• Isolation:
Dytran production accelerometer with integrated electronics (LIVM TM ). This sensor is normally used for whole body measurements.
100 mV/g
±500 m/s 2
1 Hz ÷ 10 kHz
32 kHz
2% F.S.
5% max
2000 gpk
-51 °C ÷ 120 °C
11 Vdc
10 gr
(hex-diameter x height) 12.7 mm x 23.2 mm threaded hole 10-32 UNF upper micro coaxial 10-32 titanium
>10Mohm between the enclosure and the ground terminal
Included accessories:
• Screw: double thread 10-32 UNF copper-beryllium alloy
(081B05)
Cable (not included): HD2030.CAB13 + HD2030CAB1B to connect to the analyzer’s triaxial input and HD2030.CAB1-xM (3m, 5m e
10m) to connect the monoaxial input.
- 93 -
Type: Accelerometer with integrated electronics (LIVM TM sensor is suitable for general use.
100mV/g
). This
Sensitivity:
Measure range:
Frequency response:
Resonance frequency:
Linearity:
Transverse sensitivity:
Maximum Shock:
Working Temperature:
Thermal Drift:
Polarization Voltage:
Mechanical features:
±50g
1Hz ÷ 10kHz (±5%)
32kHz
2% F.S.
5% max
2000g
-50°C ÷ 120°C
0.12%/°C
9Vdc ÷ 12Vdc
• Weight:
• Dim.(mm):
• Mounting:
• Connector:
• Material:
• Isolation:
10gr
(Hex-diameter x height) 12.7mm x 23.1mm
Threaded hole on the base with a depth of 3.8mm for 10-
32 UNF-2A screw (supplied) upper micro coaxial 10-32 titanium steel
>10Mohm between the enclosure and the ground terminal
The HD2030 analyzer can be supplied with the following triaxial accelerometers:
HDP356B20 type
Type:
Sensitivity:
Measure range:
Frequency response (±5%):
Resonance frequency:
Linearity:
Transverse sensitivity:
Maximum Shock:
Working Temperature:
Polarization Voltage:
Mechanical features:
• Weight:
• Dimensions:
• Mounting:
• Connector:
• Material:
• Isolation:
Included accessories:
• Screw:
PCB Piezotronics production triaxial accelerometer with integrated electronics (ICP TM ). This sensor is normally used for hand-arm measurements.
1 mV/g
±50000 m/s 2
2 Hz ÷ 10 kHz (Y and Z axes) , 2 Hz ÷ 7 kHz (X axis)
55 kHz
2.5% F.S.
5% max
7000 gpk
-55 °C ÷ 121 °C
9 Vdc
4 gr
(height x width x depth) 10.2 mm x 10.2 mm x 10.2 mm
2 threaded holes 5-40 UNC aligned with Y and Z axes side 8-36 4 pin titanium connector coupled with the ground terminal
• Screw:
• Screw:
• Screw:
Cable (not included): thread 5-40 UNC stainless steel to fix, using hexagonal wrench, to handle mounting adapters HD2030AC1-2-4 double thread 5-40 UNC and 10-32 UNF in copperberyllium alloy (081A27) double thread 5-40 UNC and 10-32 UNF in copperberyllium alloy (081A90) double thread 5-40 UNC and M3 in copper-beryllium alloy (M081A27)
HD2030.CAB3S-xM (3m, 5m e 10m) to connect accelerometer to analyzer.
- 94 -
HDD3023A2 Model
Type:
Sensitivity:
Measure range:
Frequency response:
Resonance frequency:
Linearity:
Transverse sensitivity:
Maximum Shock:
Working Temperature:
Thermal Drift:
Polarization Voltage:
Mechanical features:
• Weight:
• Dims. (mm):
• Mounting:
• Connector:
• Material:
• Isolation:
Included accessories:
• Screw:
Cable (not included):
HDP356A02 type
Type:
Sensitivity:
Measure range:
Frequency response (±5%):
Resonance frequency:
Linearity:
Transverse sensitivity:
Maximum Shock:
Working Temperature:
Polarization Voltage:
Mechanical features:
• Weight:
• Dimensions:
• Mounting:
• Connector:
• Material:
• Isolation:
Included accessories:
• Screw:
• Screw:
Cable (not included):
Triaxial miniature accelerometer with integrated electronics (LIVM TM ). This sensor is usually used for handarm measurement.
10mV/g
±5000 m/s
40kHz
1% F.S.
2
1.5Hz ÷ 10kHz (-5% / +15%)
5% max
5000g
-50°C ÷ 120°C
0.06%/°C
10Vdc
4gr
(height x width x depth) 12.5x9.15x9.15 hole at the base for screw 10-32 UNF-2A (supplied) side ¼-28 4 pin titanium steel enclosure connected to the ground terminal double thread 10-32 UNF in copper-beryllium alloy
(HD6200)
HD2030.CAB3S-xM (3m, 5m e 10m) to connect accelerometer to analyzer.
PCB Piezotronics production triaxial accelerometer with integrated electronics (ICP used for hand-arm measurements.
10 mV/g
±5000 m/s 2
1 Hz ÷ 5 kHz
25 kHz
2% F.S.
5% max
7000 gpk
-54 °C ÷ 121 °C
10 Vdc
10.5 gr
TM ). This sensor is normally
(height x width x depth) 14 mm x 20.3 mm x 14 mm threaded hole 10-32 UNF aligned with Z axis side ¼-28 4 pin titanium connector coupled with the ground terminal double thread 10-32 UNF in copper-beryllium alloy
(081B05) double thread 10-32 UNF and M6 in copper-beryllium alloy (M081B05)
HD2030.CAB3S-xM (3m, 5m e 10m) to connect accelerometer to analyzer.
- 95 -
HDP356B21 type
Type:
Sensitivity:
Measure range:
Frequency response (±5%):
Resonance frequency:
Linearity:
Transverse sensitivity:
Maximum Shock:
Working Temperature:
Polarization Voltage:
Mechanical features:
• Weight:
• Dimensions:
• Mounting:
• Connector:
• Material:
• Isolation:
Included accessories:
• Screw:
• Screw:
• Screw:
• Screw:
Cable (not included):
HDP356A22 type
Type:
Sensitivity:
Measure range:
Frequency response (±5%):
Resonance frequency:
Linearity:
Transverse sensitivity:
Maximum Shock:
Working Temperature:
Polarization Voltage:
Mechanical features:
• Weight:
• Dimensions:
• Mounting:
• Connector:
• Material:
• Isolation:
Included accessories:
• Screw:
• Screw:
PCB Piezotronics production miniature triaxial accelerometer with integrated electronics (ICP TM ). This sensor is normally used for hand-arm measurements.
10 mV/g
±5000 m/s 2
2 Hz ÷ 10 kHz for Y and Z axes, 2 Hz ÷ 7 kHz for X axis
55 kHz
1% F.S.
5% max
10000 gpk
-54 °C ÷ 121 °C
9 Vdc
4 gr
(height x width x depth) 10.2 mm x 10.2 mm x 10.2 mm two threaded holes 5-40 UNC aligned with Y and Z axes side 8-36 4 pin titanium connector coupled with the ground terminal thread 5-40 UNC stainless steel to fix, using hexagonal wrench, to handle mounting adapters HD2030AC1-2-4 double thread 5-40 UNC in copper-beryllium alloy
(081A27) double thread 5-40 UNC and 10-32 UNF in copperberyllium alloy (081A90) double thread 5-40 UNC and M3 in copper-beryllium alloy (M081A27)
HD2030.CAB3S-xM (3m, 5m e 10m) to connect accelerometer to analyzer.
PCB Piezotronics production miniature triaxial accelerometer with integrated electronics (ICP TM ). This sensor is normally used for whole body measurements.
100 mV/g
±500 m/s 2
0.5 Hz ÷ 4 kHz
25 kHz
1% F.S.
5% max
5000 gpk
-54 °C ÷ 77 °C
10 Vdc
5.4 gr
(height x width x depth) 11.4 mm x 11.4 mm x 11.4 mm two threaded holes 5-40 UNC aligned with Y and Z axes side 8-36 4 pin titanium connector coupled with the ground terminal double thread 5-40 UNC in copper-beryllium alloy
(081A27) double thread 5-40 UNC and 10-32 UNF in copperberyllium alloy (081A90)
- 96 -
• Screw:
Cable (not included):
HDP356B41 type
Type:
Sensitivity:
Measure range:
Frequency response (±5%):
Resonance frequency:
Linearity:
Transverse sensitivity:
Maximum Shock:
Working Temperature:
Polarization Voltage:
Mechanical features:
• Weight:
• Dimensions:
• Mounting:
• Connector:
• Material:
• Isolation:
Included accessories:
• Screw: double thread 5-40 UNC and M3 in copper-beryllium alloy (M081A27)
HD2030.CAB3S-xM (3m, 5m e 10m) to connect accelerometer to analyzer.
Sensitivity:
Measure range:
Frequency response (±5%):
Resonance frequency:
Linearity:
Transverse sensitivity:
Maximum Shock:
Working Temperature:
Polarization Voltage:
Mechanical features:
• Weight:
• Dimensions:
• Pad dimensions:
• Mounting:
• Connector:
• Material:
• Isolation:
Included accessories:
• Cable:
HDP356B18 type
Type:
PCB Piezotronics production low profile triaxial accelerometer with integrated electronics (ICP TM ) inserted in a rubber pad. This sensor is normally used for whole body measurements; while installed in the specific rubber pad it can be used to measure seat and seat-back transmitted vibrations.
100 mV/g
±100 m/s 2
0.5 Hz ÷ 1 kHz
27 kHz
1% F.S.
5% max
2000 gpk
-10 °C ÷ 50 °C
3.5 Vdc
10.8 gr (272 gr including the rubber pad)
(height x width x depth) 9 mm x 32 mm x 21.5 mm
(diameter x thickness) 200 mm x 12 mm threaded through-hole 10-32 UNF aligned with Z axis side ¼-28 4 pin titanium connector coupled with the ground terminal
HD2030.CAB3-3M (3m) to connect accelerometer to analyzer.
PCB Piezotronics production triaxial accelerometer with integrated electronics (ICP TM ). This sensor is normally used for whole body buildings transmitted vibration measurements.
1 V/g
±50 m/s 2
0.5 Hz ÷ 3 kHz
20 kHz
1% F.S.
5% max
5000 gpk
-29 °C ÷ 77 °C
10 Vdc
5.4 gr
(height x width x depth) 20.6 mm x 26.1 mm x 20.3 mm threaded holes 10-32 UNF aligned with Y and Z axes side ¼-28 4 pin light alloy connector coupled with the ground terminal double thread 10-32 UNF in copper-beryllium alloy
(081B05)
- 97 -
• Screw: Screw: beryllium alloy (M081B05)
Cable (not included): HD2030.CAB3S-xM (3m, 5m e 10m) to connect accelerometer to analyzer.
HDD3233A type
Type: Dytran production high sensitivity triaxial accelerometer with integrated electronics (LIVM TM ). This sensor is usually used for the measurement of the vibrations transmitted by the buildings.
Sensitivity:
Measure range:
Resonance frequency:
1V/g
±50 m/s
20kHz
2
Frequency response (±10%): 0.4 Hz ÷ 6 kHz axis 3 and 0.4 Hz ÷ 3 kHz exes 1 and 2
Linearity:
Transverse sensitivity:
Maximum Shock:
Working Temperature:
1% F.S.
5% max
5000 gpk
-51 °C ÷ 93 °C
Polarization Voltage:
Mechanical features:
12 Vdc
• Weight: 28gr
• Dimensions (mm): (height x width x depth) 13 mm x 33 mm x 25 central through hole (for M4 screw) aligned with axis 3 • Mounting:
• Connector:
• Material:
• Isolation: side ¼-28 4 pin titanium alloy
Body connected to the ground terminal and isolated from the mounting surface.
Included accessories:
• Screw: mounting
Cable (not included): HD2030.CAB3-xM (3m, 5m e 10m) to connect accelerometer to analyzer.
Accessories
With the accelerometers, the following accessories are supplied as optionally:
• HD6188: tube of hydro-repellent silicone grease and electrically insulating.
• HD6273: tray with bonding wax.
• 080A90: glue for quick fastening.
• 081B05: double threaded screw 10-32 UNF.
• 081A90: double threaded screw 5-40 UNC and 10-32 UNF.
• M081B05: double threaded screw 10-32 UNF and M6 X 0.75.
• M081A27: double threaded screw 10-32 UNF and M3 X 0.5”.
• 081A27: double threaded screw 5-40 UNC.
• HD6239: accelerometer push-rod.
• HD6286: adhesive metallic plate for assembly through magnet. Used to magnetically
• HD6284: insulated magnetic base with 10-32 UNF threaded hole.
• HD6196: magnetic base with integrated 10-32 UNF screw.
• HD6226: adhesive mounting base with threaded through hole (10-32 UNF).
• HD6245: adhesive mounting insulated base with integrated screw 10-32 UNF.
• HD6220: insulated base with integrated mounting 10-32 UNF screw and threaded
hole 10-32 UNF for accelerometer mounting.
- 98 -
REFERENCE STANDARDS
ISO 8041:2005 “Human response to vibration – Measuring instrumentation”
ISO 5349-1:2001 “ Mechanical vibration – Measurement and evaluation of human exposure to hand-transmitted vibration – General requirements”
ISO 5349-2:2001 “ Mechanical vibration – Measurement and evaluation of human exposure to hand-transmitted vibration – Practical guidance for measurement at the workplace”
ISO 2631-1:1997 “Mechanical vibration and shock – Evaluation of human exposure to whole body vibration – General requirements”
ISO 2631-2:1989 “Evaluation of human exposure to whole body vibration – Continuous and shock-induced vibrations in buildings (1 to 80 Hz)”
ISO 2631-4:2001 “Evaluation of human exposure to whole body vibration – Guidelines for the evaluation of the effects of vibration and rotational motion on passenger and crew comfort in fixed-guideway transport systems”
ISO 2631-5:2004 “Evaluation of human exposure to whole body vibration – Method for evaluation of vibration containing multiple shocks” IEC 61260:1995 “Electroacoustics –
Octave band and fractional-octave band filters”
ISO 6954:2000 “Mechanical vibration - Guidelines for the measurement, reporting and evaluation of vibration with regard to habitability on passenger and merchant ships”.
EMC S TANDARDS
Protection degree
Safety
IP64
EN61010-1
EN61000-6-2:2005
Electromagnetic compatibility. Generic standard for immunity.
Industrial environment.
Electromagnetic compatibility. Generic standard for emission.
EN61000-6-3:2007
Residential, commercial and light industry environments,.
Electrostatic discharge immunity
Susceptibility to EMI
EN61000-4-2 livello 3
EN61000-4-3 livello 3
Immunity to electrical fast transients
Immunity to conducted disturbances
Electromagnetic Interference - Conducted Emissions
Electromagnetic interference - Radiated Emissions
EN61000-4-4 livello 3,
EN61000-4-6
EN55022:2007 classe B
IEC/CISPR 22 classe B
I TALIAN STANDARDS
Vibrations in the workplace: : D.Lgs 81/2005 and 2002-44-CE European Directive.
- 99 -
ORDER CODES
HD2030.K1: Kit vibration analyser, 4 channels, for IEPE accelerometers
It includes: HD2030 analyzer with four channels, user manual, suitcase,
Noise Studio Software basic module, serial cable for USB (CP22) ports,
1GB memory card (HD2030MC), silicone grease (HD6188), wax tray for gluing (HD6273) and fast mounting wax (080A90). Calibration reports for
HD2030 according to ISO8041 and for octave and third octave filters bank according to IEC61260.
At the time of order, specify the accelerometers, the connection cables and the accessories.
HD2030.Ha-Wb: Kit HD2030 for four-axial measurement of hand-arm transmitted vibrations and whole body transmitted vibrations using a rubber
pad on the seat and seat back. The kit is composed of four channels vibration analyzer including spectral and statistical analysis , two triaxial accelerometers and rubber pad for the seat. The kit includes adapters for hand-arm accelerometer mounting.
Includes:
• HD2030.K1: 4-axis HD2030 vibration analyser, user manual, carrying case, Noise Studio basic software, serial cable for USB ports (CP22),
1GB SD memory card (HD2030MC), silicon grease (HD6188), tray with bonding wax (HD6273) and quick fastening glue (080A90). Calibration reports for vibration meter and filters according to ISO8041 and
IEC61260.
• IEPE tri-axial accelerometer with 10 mV/g sensitivity for the measurement of vibrations transmitted to the hand-arm. Includes mounting screw in copper-beryllium and HD2030.CAB3-3M connection cable to analyser. Sensor’s manufacturer calibration chart and calibration report according to ISO 8041 of the measurement chain composed of the three axes and the analyser with Wh weighting filters.
• IEPE triaxial accelerometer with 100mV/g sensitivity for the measurement of whole body transmitted vibrations; the accelerometer is mounted into a rubber pad for the measurement on seats and seat back. It includes HD2030.CAB3-3M connection cable to analyser. Sensor’s manufacturer calibration chart and calibration report according to
ISO 8041 of the measurement chain composed of the three axes and the analyser with Wd, Wd and Wk weighting filters for X, Y and Z axes respectively.
• Adapters to fix the accelerometer to the handles of tools
(HD2030.124). Are included: HD2030AC1 cubic adapter with metal clamp, HD2030AC2 adapter for cylindrical shape handles and
HD2030AC4 adapter for small tools with anatomic handles
HD2030.SL: Kit HD2030 "Safety in the Workplace" for the measurement of
noise and vibration in the workplace. The kit consists of HD2030 four-axes vibration analyzer with accelerometers to measure the vibration transmitted to the hand-arm and whole body and HD2010UC/A type 1 sound level meter and analyzer.
includes:
• HD2030.HA-WB: Kit for hand-arm and whole-body four-axis vibration measurements including the four-channels HD2030 vibration analyzer, two triaxial accelerometers and hand-arm adapters.
- 100 -
• HD2010UC/A type 1 sound level meter, octave bands spectrum analyzer and statistical analyzer, user manual, carrying case, HD2010PNE2 detachable preamplifier and pre-polarized (electret) microphone, 5m extension cable (CPA/5), windshield and USB serial cable. Calibration report of sound level meter and filters.
• Noise Studio "Worker Protection" (NS1) application module with hardware key (CH20) and license of use, for noise and vibration analysis in the workplace according to UNI 9432/11 and ISO9612/11.
HD2030.RV: Kit HD2030 "Noise and Vibration" for the measurement of noise and vibration in the workplace and for the assessment of noise
pollution and environmental noise in general. The kit consists of
HD2030 four-axes vibration analyzer with accelerometers to measure the vibration transmitted to the hand-arm and whole body and a HD2110L type 1 sound level meter and analyzer.
includes:
• HD2030.HA-WB: Kit for hand-arm and whole-body four-axis vibration measurements including the four-channels HD2030 vibration analyzer, two triaxial accelerometers and hand-arm adapters.
• HD2110L type 1 sound level meter with option HD2110.O1 “Third Octave”: octave and third octave (with double filter bank for tonal components assessment) bands spectrum analyzer and statistical analyzer, user manual, carrying case, HD2110P preamplifier and high sensitivity detachable microphone, 5m extension cable (CPA/5), HD
SAV windshield and USB serial cable. Calibration report of sound level meter and filters.
• Noise Studio NSLA package composed of hardware key (CH20) and license of use for:
• Noise Studio NS1 "Workers Protection" application module for noise and vibration analysis in the workplace according to UNI
9432/11 and ISO9612/11.
• Noise Studio NS5 “Environmental Noise” application module for assessment of environmental noise sources according to national and EU standards regarding environmental noise.
For availability and delivery time of the following accelerometers please contact your local distributor.
HDD3200B5T: accelerometer with integrated electronics (LIVM TM ) for hand–arm measurements in the presence of shock levels. Sensitivity 1mV/g, range
±50000 m/s 2 , Integrated mounting screw. Can be connected to left
(monoaxial) vibration analyzer input using HD2030.CAB1-xM cable or to right (triaxial) analyzer input using HD2030.CAB13 and HD2030CAB1BxM (not included).
HDD3019A1: Dytran production accelerometer with integrated electronics (LIVM TM ) for hand-arm vibration measurements. Sensitivity 10 mV/g, measure range
±5000 m/s 2 . Mounting screw included. Can be connected to left (monoaxial) vibration analyzer input using HD2030.CAB1-xM cable or to right
(triaxial) analyzer input using HD2030.CAB13 and HD2030CAB1B-xM (not included).
- 101 -
HDP352C34: PCB Piezotronics production accelerometer with integrated electronics
(ICP TM ) for whole body transmitted vibration measurements. Sensitivity
100 mV/g, range ±500 m/s 2 . Mounting screws 10-32 UNF and M6 included. Can be connected to left (monoaxial) vibration analyzer input using HD2030.CAB1-xM cable or to right (triaxial) analyzer input using
HD2030.CAB13 and HD2030CAB1B-xM (not included).
HDD3056B2: Dytran production accelerometer with integrated electronics (LIVM TM ) for whole body transmitted vibration measurements. Sensitivity 100 mV/g, measure range: ±500 m/s 2 . Mounting screw 10-32 UNF included. Can be connected to left (monoaxial) vibration analyzer input using
HD2030.CAB1-xM cable or to right (triaxial) analyzer input using
HD2030.CAB13 and HD2030CAB1B-xM (not included).
Triaxial accelerometers
HDP356B20: PCB Piezotronics production miniature triaxial accelerometer with integrated electronics (ICP TM ) for hand-arm vibration measurements in the presence of high peak levels. Sensitivity 1 mV/g, measure range ±50000 m/s 2 . Mounting screws 5-40 UNC, 10-32 UNF and M3 included. Can be connected to the right (triaxial) analyzer’s input using the
HD2030.CAB3S-xM cable (not included).
HDD3023A2: Dytran production triaxial miniature accelerometer with integrated electronics (LIVM TM ) for hand-arm measurements. Sensitivity 10mV/g, measure range: ±5000 m/s 2 . Mounting screw HD6200 is included. Can be connected to the right (triaxial) analyzer’s input using the
HD2030.CAB3S-xM cable (not included).
HDP356A02: PCB Piezotronics production triaxial accelerometer with integrated electronics (ICP TM ) for hand-arm vibration measurements. Sensitivity 10, mV/g, measure range ±5000 m/s 2 . Mounting screws 10-32 UNF and M6 included. Can be connected to the right (triaxial) analyzer’s input using the HD2030.CAB3S-xM cable (not included).
HDP356B21: PCB Piezotronics production miniature triaxial accelerometer with integrated electronics (ICP TM ) for hand-arm vibration measurements.
Sensitivity 10 mV/g, measure range ±5000 m/s 2 . Mounting screws 5-40
UNC, 10-32 UNF and M3 included. Can be connected to the right (triaxial) analyzer’s input using the HD2030.CAB3S-xM cable (not included).
HDP356A22 PCB Piezotronics production miniature triaxial accelerometer with integrated electronics (ICP TM ) for whole body transmitted vibration measurements. Sensitivity 100 mV/g, measure range ±500 m/s 2 .
Mounting screws 5-40 UNC, 10-32 UNF and M3 included. Can be connected to the right (triaxial) analyzer’s input using the HD2030.CAB3S-xM cable (not included).
HDP356B41: PCB Piezotronics production triaxial accelerometer with integrated electronics (ICP TM ) for whole body transmitted vibration measurements.
Sensitivity 100 mV/g, measure range ±100 m/s 2 . Accelerometer is mounted into a rubber pad for the vibration measurements in seats and seat back. HD2030.CAB3-3M cable for connection to analyzer input included.
- 102 -
HDP356B18: PCB Piezotronics production triaxial accelerometer with integrated electronics (ICP TM ) for vibration measurements in buildings. Sensitivity 1
V/g, measure range ±50 m/s 2 . Mounting screws 10-32 UNF and M6 included. Can be connected to the right (triaxial) analyzer’s input using the HD2030.CAB3S-xM cable (not included).
HDD3233A: Dytran production high sensitivity triaxial accelerometer with integrated electronics (LIVM TM ) for vibrations measurements in buildings. Sensitivity
1V/g, measure range ±50 m/s 2 . Mounting screw M4 included. Can be connected to the right (triaxial) analyzer’s input using the
HD2030.CAB3S-xM cable (not included).
Supports for hand-arm measurements
HD2030AC1:
HD2030AC2:
Cubic support for the accelerometer mounting on grips through plastic or metal bands as close as possible to the hand. It is suitable for measurements on small tools where the weight of the measurement chain must be minimized. Material: light alloy.
It includes:
• hex socket screw 10-32UNF
• 4mm hexagonal key
• 10 plastic cable ties, 4.5mm width, 200 mm length
• 1 metallic clamp , width 9 mm
Adapter to be placed between the hand and the grip. The accelerometer is fixed in lateral position, at the left or right of the hand. It is suitable for large cylindrical grips. Material: light alloy.
It includes:
• hex socket screw 10-32UNF
• 4mm hexagonal key
• 10 plastic cable ties, 4.5mm width, 200 mm length
• 1 metallic clamp 9mm width
• 2 velcro straps, width 25mm, length 300mm (HD2030FV)
HD2030AC3: adapter to be placed between the hand and the grip The accelerometer is fixed in lateral position, at the left or right of the hand. It is suitable for cylindrical grips with large dimensions and for accelerometer with integrated screw. Material: inox.
It includes:
• 10 plastic cable ties, 4.5mm width, 200 mm length
• 2 velcro straps 24.5m width, length 300mm (HD2030FV)
HD2030AC4: adapter to be place between the hand and the grip The accelerometer is fixed in central position, between the middle-finger and ring-finger or between the forefinger and middle-finger. It is suitable for anatomic grips even if not cylindrical and with small dimensions.
Material: light alloy.
It includes:
• hex socket screw 10-32UNF
• 4mm hexagonal key
• 10 plastic cable ties, 4.5mm width, 200 mm length
• 2 velcro straps, width 25mm, length 300mm (HD2030FV)
HD2030AC5: Support for triaxial and monoaxial accelerometers suitable for the measurement of the vibrations transmitted by floors and vibrating surfaces in general. It is provided with a spirit level and three support feet, two with adjustable height. The support has a cavity for the installation of a triaxial accelerometer with central through hole for M4 screws. The upper surface has a 10-32 UNF threaded hole for the
- 103 -
mounting of an accelerometer. For the assembly of three monoaxial accelerometers it is supplied a cubic adapter to be mounted on the upper surface. Material: Nickel-plated steel, weight 1.9kg.
HD2030AC5 includes:
• Steel support with three feet and leveling device. It has a 10-32
UNF threaded hole on the upper surface and a cavity on the bottom side with M4 threaded hole.
• Cubic adapter to be mounted on the upper surface through two M4 screws (included). The cube has 10-32 UNF threaded holes on three orthogonal sides.
• 3mm hexagonal key
HD2030.124: adapters kit for the measurement of the vibrations transmitted to the hand-arm system.
Includes:
• HD2030AC1: cube-shaped adapter to be fastened to the handle with plastic cable-tie or metallic clamp (included).
• HD2030AC2: adapter for cylindrical handles. The adapter is placed laterally with respect to the hand.
• HD2030AC4: general purpose adapter. The accelerometer is placed between the forefinger and the middle-finger or between the middle-finger and the ring-finger.
• hex socket screw 10-32UNF
• 4mm hexagonal key
• 10 plastic cable ties, 4.5mm width, 200 mm length
• 1 metallic clamp , width 9 mm
• 2 velcro straps, width 25mm, length 300mm (HD2030FV)
HD2030.1234: adapters kit for the measurement of the vibrations transmitted to the hand-arm system.
Includes:
• HD2030AC1: cube-shaped adapter for anatomical handles and small size tools. The adapter has to be fastened to the handle with plastic cable-tie or metallic clamp (included).
• HD2030AC2: adapter for cylindrical handles. The adapter is placed laterally with respect to the hand.
• HD2030AC3: adapter for cylindrical handles provided with threaded hole for accelerometers with 10-32 UNF screw. The adapter is placed laterally with respect to the hand.
• HD2030AC4: general purpose adapter. The accelerometer is placed between the forefinger and the middle-finger or between the middle-finger and the ring-finger.
• hex socket screw 10-32UNF
• 4mm hexagonal key
• 10 plastic cable ties, 4.5mm width, 200 mm length
• 1 metallic clamp , width 9 mm
• 2 velcro straps, width 25mm, length 300mm (HD2030FV)
Accelerometers mounting accessories
HD6188: Tube of hydro-repellent silicone grease and electrically insulating.
HD6273: Tray with bonding wax.
080A90: quick mounting glue
- 104 -
HD6284:
HD6196
HD6226:
HD6245:
HD6220:
HD2030FV
081B05:
081A27
081A90:
M081B05:
M081A27
HD6239:
HD6286:
Copper-beryllium alloy screw with dual threading 10-32 UNF.
Double thread screw 5-40 UNC.
Double thread screw 5-40 UNC and 10-32 UNF (copper-beryllium alloy).
Double thread screw 10-32 UNF and M6 x 0.75 (copper-beryllium alloy).
Double thread screw 5-40 UNC and M3 x 0.5” (copper-beryllium alloy).
Push-rod for accelerometer.
It can be used with all accelerometers.
Adhesive metallic disc. Used to magnetically couple the accelerometer to non-metallic surfaces.
It can be used with HD6284 and HD6196 magnetic bases.
Small magnetic base with threaded hole 10-32UNF.
It can be used with all accelerometers
Large magnetic base with integrated screw 10-32UNF.
It can be used with the following accelerometers: HDP356A02,
HDD3056B2, HDP352C34 and HDP356B41 (removing rubber pad).
Base with threaded thru-hole 10-32 UNF for adhesive mounting.
It can be used with all accelerometers.
Insulated Base with integrated screw 10-32 UNF for adhesive mounting.
It can be used with the HDP356A02, HDD3056B2, HDP352C34 e
HDP356B41 (removing the rubber pad).
Insulated Base with integrated mounting screw 10-32 UNF-2A and threaded hole 10-32 UNF for accelerometers assembly.
It can be used with all accelerometers.
Velcro strap, width 25mm, length 300mm
- 105 -
Cables for monoaxial accelerometers
HD2030.CAB13: cable for the connection of three monoaxial accelerometers to the triaxial input of the HD2030 analyzer, compete with connectors. 40 cm length with BNC connectors. It is necessary to use a HD2030.CAB1B-xM cable for each accelerometer.
HD2030.CAB1B-3M: coaxial cable for the connection of monoaxial accelerometers to the
HD2030.CAB13 cable, complete with connectors. 3m length.
HD2030.CAB.BNC-xM: coaxial extension cable for the connection of monoaxial accelerometers to the HD2030.CAB13 cable. The maximum cable length is 50m and both ends are terminated with BNC female connectors.
HD2030.CAB1-3M: low noise coaxial cable for the connection of monoaxial accelerometers to the HD2030 analyzer left input. 3m length, complete with connectors.
Can be used with accelerometers: HDD3200B5T, HDD3019A1,
HDP352C34 and HDD3056B2
HD2030.CAB1-5M: low noise coaxial cable for the connection of monoaxial accelerometers to the HD2030 analyzer left input. 5m length, complete with connectors.
Can be used with accelerometers: HDD3200B5T, HDD3019A1,
HDP352C34 and HDD3056B2
HD2030.CAB1-10M: low noise coaxial cable for the connection of monoaxial accelerometers to the HD2030 analyzer left input. 10m length, complete with connectors. Can be used with accelerometers: HDD3200B5T, HDD3019A1,
HDP352C34 and HDD3056B2.
Cables for triaxial accelerometers
HD2030.CAB3-3M: Cable for the connection of accelerometers to the HD2030 analyzer, complete with connectors. Length 3 m. It can be used with the accelerometers: HDP356B18, HDD3233A, HDD3023A2 and HDP356A02..
HD2030.CAB3-5M: Cable for the connection of accelerometers to the HD2030 analyzer, complete with connectors. Length 5 m. It can be used with the accelerometers: HDP356B18, HDD3233A, HDD3023A2 and HDP356A02..
HD2030.CAB3-10M: Cable for the connection of accelerometers to the HD2030 analyzer, complete with connectors. Length 10 m. It can be used with the accelerometers: HDP356B18, HDD3233A, HDD3023A2 and HDP356A02..
HD2030.CAB3S-3M: Cable for the connection of accelerometers to the HD2030 analyzer, complete with connectors. Length 3 m. It can be used with the accelerometers: HDP356B20, HDP356B21 and HDP356A22.
HD2030.CAB3S-5M: Cable for the connection of accelerometers to the HD2030 analyzer, complete with connectors. Length 5 m. It can be used with the accelerometers: HDP356B20, HDP356B21 and HDP356A22.
HD2030.CAB3S-10M: Cable for the connection of accelerometers to the HD2030 analyzer, complete with connectors. Length 10 m. It can be used with the accelerometers: HDP356B20, HDP356B21 and HDP356A22.
Other cables
HD2110CSNM: PC connection serial cable for COM ports and for the direct connection to
HD40.1 printer.
PC connection serial cable for USB ports with A and B type connectors. CP22:
Other accessories
HD2030MC:
HD2030AM:
SWD10:
VTRAP:
1GB SD memory card. headset with microphone. stabilized power supply 100-240Vac/12Vdc-1A. tripod with a maximum height of 1550mm.
- 106 -
HD40.1:
BAT-40:
RCT: kit including 24-column portable thermal printer, serial interface, paper width 57 mm, 4 x 1.2V NiMH rechargeable batteries, SWD10 power supply device, 5 rolls of thermal paper and user manual. spare battery pack for the printer HD40.1 with temperature integrated sensor. kit of four rolls of thermal paper; 57mm width, 32mm diameter.
- 107 -
HOW TO SOLVE THE PROBLEMS
The HD2030 analyzer is equipped with a diagnostic program (DIAGNOSTIC CHECK) that checks automatically the main instrument parameters. To run the program and check the analyzer functions, press the keys MENU >> Programs >> Diagnostic Checks (see “PROGRAMS
DESCRIPTION” chapter).
If the DIAGNOSTIC CHECK fails:
Repeat it with new batteries after waiting the stabilization time (at least 1 minute) and, if the problem persists, contact the technical service.
R ESTORE OF F ACTORY S ETUP
The factory configuration of the analyzer parameters (factory setup) can be recalled through a key combination. This operation does not cancel the content of the data
memory.
With the instrument switched off, turn on the HD2030 keeping the ENTER key pressed.
All the parameters present in the menu are simultaneously set to the factory default.
V ARIOUS P ROBLEMS
If the CALIBRATION program with the calibrator fails:
Make sure the analyzer is not subjected to noise and/or high vibrations.
Repeat after the waiting the stabilization time and, if the problem persists, contact the technical service.
After changing the batteries, the instrument does not switch on.
Remove one of the batteries and wait 5 minutes before inserting it again. The instrument should switch itself on automatically when the missing battery is inserted.
The levels detected by the analyzer seem not corrected.
Make sure there is no condensation. Do not turn on the instrument if there is the probability of condensation.
Wait for the measures stabilization time.
Check the accuracy of the measurement with the calibrator.
The analyzer switches itself off automatically after the startup screen.
The batteries are discharged.
The instrument does not communicate with PC:
If you are using a communication program like HyperTerminal, check that the communication speed of the PC and HD2030 are the same (Menu >> Parameters >>
Instrument >> Input/Output >> Baud rate).
Check that the connection cable is correctly inserted and it is connected to a RS232 serial port or USB of PC
Check that the item MENU>> Parameters >> Instrument >> Input/Output >> Serial
Dev. is set to the port type in use: RS232 or USB.
If using the USB interface, check if the driver is correctly installed.
If you are using Noise Studio software, try to disable the Auto Detect function (Menu
Option >> Port Settings) and set the connection directly to the COM where the instrument is connected.
It is not possible to activate the continuous recording. Pressing REC and RUN keys the analyzer starts the measurement without recording.
The instrument has no available memory for further data. Download the data and/or erase the memory.
- 108 -
KEYBOARD DESCRIPTION
HOLD key
The HOLD key can be used to stop temporarily the display updating while the analyzer still continues with the requested measurements. A “H” in the upper left corner indicates that the display is in this mode. Press again the key to go back to the normal measure.
While the device is in HOLD, it is possible to switch from a screen to another, activate the cursors of the graphic screens, print and save the data.
The recording is not affected by the HOLD status.
ON/OFF key
The instrument switching on and off can be done pressing, for at least a second, the
ON/OFF key. At startup the analyzer briefly shows the Delta Ohm logo and the program version. Then it is requested to select the configuration for the sensors that are connected to the two inputs: first the triaxial right input and then the monoaxial left one.
CONFIG RIGHT #02
PROD: DELTA
MOD: ACC_TRI
S.N.: 123456
TYPE: ACC
SENS: 10mV/g CAL
RANGE: 500
SEL. PREV. NEXT
For both inputs press PREV or NEXT to scroll the list of the sensors that are in memory,
SEL to confirm the visualized configuration.
Then the instrument enters the VLM (Vibration Level Meter) working mode, visualizing in numerical form 3 instant or integrated parameters.
If there is an external memory card, after the initial screen, the sensors configuration file is loaded and it appears the following screen:
- 109 -
MC installed and ready
Size: 500MB
ESC RD RD/WR
Press RD/WR to enable all the reading and writing functions and proceed with the selection of the configurations.
Before switching off the instrument, it is necessary to stop the current measurement pressing the STOP key. Otherwise a message requesting to stop the current measurement, appears:
WARNING!
Stop measurement before continue
YES NO
Pressing YES, the instrument enters the STOP mode and it is possible to switch it off with the ON/OFF button.
"Auto-Power Off" Function
The Auto-Power Off function works if instrument remains in STOP mode for at least 5 minutes without pressing any key. Before switching itself off, a series of warning beeps are emitted: in this phase, if desired, it is possible to press a key to avoid the switching off.
The function can be disable through the MENU acting on the “Auto-Switching Off” item
(MENU >> Parameters>> Instrument >> System >> Auto-Power Off = OFF). In this case the battery symbol blinks to remind that the instrument will not switch itself off automatically but only pressing the <ON/OFF> key.
The auto-power off function is temporarily disabled when the external power supply is used, when the instrument is in acquisition mode or it is running a program.
MENU Key
Pressing the MENU key, the two items Settings and Programs are accessed: the first contains all the instrument parameters that, depending on the use, can be modified by the user.
The second one contains some functions of frequent use; management of files in memory, setup, calibration, …
- 110 -
The Settings menu includes the following items:
• Instrument
• Vibration analyzer
• Spectrum Analyzer
• Data Logger
• Calibration
The Programs menu includes the following items:
• Memory Navigator
• Setup Management
• Calibration
• Diagnostic Check
• Sensors Configuration
• Initialize Memory Card
In the menu and programs it is possible:
• To move from an item to another one in the same menu, using the UP and DOWN arrows,
• To select an item to modify, pressing the ENTER key,
• To modify the selected blinking parameter using the UP and DOWN arrows,
• To confirm the modification with the ENTER key or cancel the modification with the MENU key,
• To exit from the submenu or from the menu with the MENU key.
Some of the parameters available in the menu are also settable directly in measure mode
(like for example the integration interval, the measurement range, etc.).
Entering the menu, it is possible to visualize the size of available memory, the remaining batteries charge, the date and the time.
A detailed description of the menu items is in the “MENU FUNCTIONS DESCRIPTION”
AND “PROGRAMS DESCRIPTION” chapters.
CHN Key
The CHN (Channel) key allows to select the measurement channel among the four available: CH1…CH3 refer to the triaxial right input, CH4 to the left monoaxial input.
The key works in all the screens.
From menu (MENU >> Parameters >> Instrument >> Measurement >> Ch1-4) it’s possible to disable one or more measurement channels, that for example are not used: in order to enable all available channels, set menu parameter “Ch1-4” = 1111)
When one or more of CH1, CH2 or CH3 channels are disabled, measurements of “sum” vector or “maximum” vector are not displayed.
MODE Key
The MODE key selects in sequence the different analyzer visualization modes, switching from VLM to temporal profile, to the octave or third-octave spectra, to the probability distribu-
tion and the percentiles levels.
All the working modes are simultaneously active even if they are not visualized: using the MODE key it is possible to choose the visualization mode without affecting the acquisition.
At startup, after the selection of the inputs configuration, the instrument displays the
VLM screen.
- 111 -
PAUSE/CONTINUE Key
The PAUSE key stops the calculation of the integrated measures (Leq, the maximum and minimum level, the spectra, etc.) and the eventual recording. The instant levels continues to be measured and visualized in the VLM screen. To start again the measurement, press again the PAUSE/CONTINUE key.
If in PAUSE mode, during a measurement session, the START/STOP/RESET key is pressed, the integrated parameters are reset.
If in PAUSE mode, during the review of a recording, the START/STOP/RESET key is pressed, the next memorized data is displayed.
If the START/STOP/RESET key is hold pressed, the fast review mode is entered.
REC Key
If the REC key is pressed for at least 2 seconds, what it is visualized is saved in memory as single report.
The REC key together with the START/STOP/RESET key activates the continuous recording of the data in memory.
To memorize the time profile (both single and multi-profile), press at the same time the
REC and START/STOP/RESET keys: the selection of the single or multiple mode depends on the settings of some parameters in menu. See the details in the “RECORDING MODE” chapter.
START/STOP/RESET Key
Pressing the START key, starting from the STOP mode, reset the initial values of the integrated measures like Leq, MAX/MIN levels, etc. and starts a new execution.
Pressing the STOP key the next time, it is stopped the execution of the integrated measures.
If pressed while in pause mode, all the integrated parameters are reset.
In the review mode of the memorized data, if the START/STOP/RESET key is pressed while in pause mode, the next data is displayed; if hold pressed, the fast review mode is entered.
UP arrow Key
The UP arrow key selects the previous row in the menu or increases the selected parameter.
In the VLM screen, it modifies the horizontal bar limits.
It decreases the vertical initial and full scale and of the time profile or frequency spectra moving in this way the graph up.
- 112 -
LEFT arrow Key
In the menu, the LEFT arrow key moves the cursor on the left during the insertion of a character.
After the modification of a parameter of the menu, it goes back to the selection of the whole line in order to move among the various items.
It compresses (ZOOM-) the vertical scale of the time profile and frequency spectra.
In the VLM screens it changes the measure unit of the visualized parameters.
When the integration mode is multiple, the “Tint” symbol blinks: to go back to the single integration mode, select the “Tint=…” symbol with the ENTER key and press the LEFT arrow.
ENTER Key
The ENTER key confirms the selected parameter. With the instrument in STOP mode, it allows the direct modification of the measurement parameters without entering the menu.
During the setting of the menu parameters, to exit from the setting mode of a parameter without saving it, press the MENU key.
Keeping ENTER pressed while switching on, the factory configuration of the parameters is loaded.
RIGHT arrow Key
In the menu, the RIGHT arrow key moves the cursor on the right during the insertion of a character. It allows to modify the parameter of the menu in the selected line.
It extends (ZOOM+) the vertical scale of the time profile and frequency spectra.
In the VLM screens it changes the measure unit of the selected parameters.
It allows to select the multiple integration mode directly from the measurement screen, avoiding to access the menu. Press ENTER until the time value shown on side of “Tint=” blinks.
Press the key “RIGHT arrow” key. The “Tint=” blinks to indicate that the multiple integration mode has been activated. To go back to single integration mode, press the “LEFT arrow” key.
DOWN arrow Key
The DOWN arrow key selects the next row in the menu or decreases the selected parameter.
In the VLM screen, it changes the limits of the horizontal bar.
It increases the vertical initial and full scale of the time profile or frequency spectra moving, in this way, the graph down.
- 113 -
CURSOR Key (keypad)
In a graphic mode, it activates the cursors. Pressing repeatedly the key, they are activated in sequence the first cursor (L1), the second cursor (L2) or both in “tracking” (ΔL): at the next pressing of the key, the cursors are disabled.
The selected blinking cursor is moved on the graphic with the LEFT and RIGHT arrows on the keypad.
In the upper part of the display the related values are displayed.
In time profile, they are indicated the level and the time or the difference of the level between the two cursors and the time distance.
In working mode as spectrum analyzer, they are visualized the level and the central frequency corresponding to the cursor selected band. The cursor can also select the wideband level placed on the right of the display.
When the function of the two cursors is not active, it is possible to switch from the visualization of the acceleration of each band to the speed or displacement visualization, pressing in sequence the left and right cursor keys.
Keeping the CURSOR key pressed, the limit acceleration curve is displayed.
To disable the limit acceleration curve, keep the CURSOR key pressed.
In the probability distribution, it is possible to read the probabilities in two points of the graph or, when they are both selected, to calculate the probability to have a value between two cursors.
In the percentile levels screen the cursor indicates the percentile level when the visualized parameter changes.
Keeping the CURSOR key pressed, while one of the VLM screens is displayed, it is possible to activate or deactivate the “beep” sound (activated each time a key is pressed).
Keeping the CURSOR key pressed, while one of the VLM screens is visualized, it is possible to activate or deactivate through the keyboard the backlit.
LEFT Key (keypad)
The LEFT arrow key moves on the left the cursor or the two active cursors (blinking).
In VLM mode, it allows to scroll the VLM_1, …, VLM_4 screens.
In working mode as spectrum analyzer, the left and right cursor keys allow to switch from acceleration to speed or displacement visualization.
RIGHT arrow Key (Keypad)
The RIGHT arrow key moves on the right the cursor or the two active cursors (blinking).
In VLM mode, it allows to scroll the VLM_1, …, VLM_4 screens.
In working mode as spectrum analyzer, the left and right cursor keys allow to switch from acceleration to speed or displacement visualization.
- 114 -
APPENDIX
A1. MEASURE PARAMETERS OF HD2030
In the following paragraphs are indicated the vibration levels with the related abbreviations used to identify them that can be visualized numerically or graphically and memorized.
LEVELS NUMERICALLY DISPLAYED
Frequency weightings
Application Weight
HA
Fz
Fc
Wh
Fz
Fa
DESCRIPTION
Filter with a flat frequency response.
Band-pass filter for hand-arm measurements 6.3Hz ÷
1250Hz
Filter for hand-arm measurements.
Filter with a flat frequency response.
Band-pass filter for measurements on the whole body:
0.4Hz ÷ 100Hz
WB
Wb
Wc
Wd
We
Wj
Filter for measures in the vertical axis (z), ISO 2631-4
Filter for measures in horizontal axis from the back to the shoulders (x), back for a sitting person, ISO 2631-1
Filter for measures on horizontal axis (x o y), ISO 2631-1
Filter for rotational vibrations measures in all the directions Sitting person, ISO 2631-1
Filter for measure of vibration at the top for vertical axis
(x), lying person, ISO 2631-1
Filter for measurements on vertical axis (z), ISO 2631-1
Filter with a flat frequency response.
Wk
Fz
BV Fm
Wm
Band-pass filter for building measurements: 0.8Hz ÷
100Hz
Filter for building measurements.
MEASURE PARAMETERS CALCULATED IN EACH CHANNEL
Instant values calculated every second
Broadband aw,pk aw,1s
Linear Average aw,1s
Exponential Average aw,8s
Exponential Average
CF
Pk
AeqS
A1s
A8s
CF
Peak of weighted acceleration
Linear Average in 1 second of weighted acceleration
Exponential Average in 1 second of weighted acceleration
Exponential Average in 8 second of weighted acceleration
Crest Factor = aw,pk/aw,1s
- 115 -
Integrated values in the measurement time
Broadband
Aw,pkmax aw, T
Linear Average aw(eq,1s) aw(eq,8h)
VDV
VDV,8h
MTVV
Pkmx
Aeq aw,1s max
Exponential Average A1smx aw,1s min
Exponential Average A1smn aw,8s max
Exponential Average
A8smx aw,8s min
Exponential Average A8smn
A(1s)
A(8)
VDV
VDV,d
MTVV
Maximum peak of weighted acceleration
Linear Average in the measurement time of weighted acceleration
Maximum exponential average in 1 second of weighted acceleration
Minimum exponential average in 1 second of weighted acceleration
Maximum exponential average in 8 second of weighted acceleration
Minimum exponential average in 8 second of weighted acceleration
Equivalent value of the frequency weighted acceleration in the measurement time referenced to 1 second
(it is equivalent to SEL)
Equivalent value of the frequency weighted acceleration in the measurement time referenced to 8 hours
Vibration dose
Estimated daily vibration dose
Maximum Linear Average in 1second of the weighted acceleration
CF
Linear Average
Maximum CF
CFeq
CFmx
Average Crest Factor = aw,pkmax/aw,T
Maximum Crest Factor = aw,pk/aw,1s
VDV Ratio
MTVV Ratio
%OL
VDVr
MTVVr
OL
= VDV/aw,T/T 1/4
The limit value is equal to 1.75
= MTVV/aw,T
The limit value is equal to 1.5
Percentage of overload time
%UR UR Percentage of under-range time
MEASURE PARAMETERS CALCULATED ON THE ACCELERATION VECTOR
Instant values calculated every second
Broadband aw,pk aw,1s
Linear Average aw,1s
Exponential Average aw,8s
Exponential Average
CF
Pk
AeqS
A1s
A8s
CF
Peak of the weighted acceleration
Linear Average in 1 second of weighted acceleration
Exponential Average in 1 second of weighted acceleration
Exponential Average in 8 seconds of weighted acceleration
Crest Factor = aw,pk/aw,1s
- 116 -
Integrated values in the measurement time
Broadband
Aw,pkmax aw, T
Linear Average aw,1s max
Exponential Average aw,1s min
Exponential Average aw,8s max
Exponential Average aw,8s min
Exponential Average aw(eq,1s) aw(eq,8h)
MTVV
CF
Linear Average
Maximum CF
MTVV Ratio
Pkmx
Aeq
A1smx
A1smn
A8smx
A8smn
A(1s)
A(8)
MTVV
CFeq
CFmx
MTVVr
Maximum peak of weighted acceleration
Linear average in the measurement time of weighted acceleration
Maximum Exponential Average in 1 second of the weighted acceleration
Minimum Exponential Average in 1 second of the weighted acceleration
Maximum Exponential Average in 8 seconds of the weighted acceleration
Minimum Exponential Average in 8 seconds of the weighted acceleration
Equivalent value of the frequency weighted acceleration in the measurement time referenced to 1 second
(Equal to SEL)
Equivalent value of the frequency weighted acceleration in the measurement time referenced to 8 hours
Maximum Linear Average in 1 second of the weighted acceleration
Average crest factor = aw,pkmax/aw,T
Maximum crest factor = aw,pk/aw,1s
= MTVV/aw,T
The limit value is equal to 1.5
- 117 -
A2. MEMORY CAPACITY DURING THE RECORDING FUNCTION
The following table reports the indicative values of the storage capacity of the HD2030 analyzer in the different recording modes, expressed as the necessary time to fill the internal flash memory or as the number of recordings. The internal memory of the analyzer is 8MB.
Single recording and automatic storage
Profile recording
Profile interval = 1s
Only LEFT input.
Spectral analysis by octave bands.
Only RIGHT input.
Spectral analysis by octave bands.
LEFT+RIGHT inputs.
Spectral analysis by octave bands.
Only LEFT input.
Spectral analysis by third-octave bands
Only RIGHT input.
Spectral analysis by third-octave bands
LEFT+RIGHT inputs.
Spectral analysis by third-octave bands
Only LEFT input.
Only RIGHT input.
LEFT+RIGHT inputs.
Only LEFT input.
Spectral analysis by octave bands.
8500
3900
2700
8100
3300
2500
11 days
7 days
6 days
63 hours
Multiple profiles recordings.
Single integration.
Only RIGHT input.
Spectral analysis by octave bands.
LEFT+RIGHT inputs.
Spectral analysis by octave bands.
Only LEFT input.
Spectral analysis by third-octave bands
Only RIGHT input.
Spectral analysis by third-octave bands
22 hours
17 hours
28 hours
9 hours
Multiple profiles recording. Multiple integration with integration interval =
10s
LEFT+RIGHT inputs.
Spectral analysis by third-octave bands
Only LEFT input.
Spectral analysis by octave bands.
Only RIGHT input.
Spectral analysis by octave bands.
LEFT+RIGHT inputs.
Spectral analysis by octave bands.
Only LEFT input.
Spectral analysis by third-octave bands
7 hours
60 hours
20 hours
15 hours
55 hours
Only RIGHT input.
Spectral analysis by third-octave bands
LEFT+RIGHT inputs.
Spectral analysis by third-octave bands
18 hours
14 hours
When a voice comment is memorized, about 16kB/s are necessary. The internal memory of the analyzer can contain at maximum 8 minutes of audio recording corresponding, for example, to more than 48 recordings with 10s commentaries.
- 118 -
For a comparison, in the following table are reported the indicative values of the storage capacity with a 1GB memory card.
Single recording and automatic storage
Profile recording.
Profile interval = 1s
Multiple profiles recording.
Single integration.
Multiple profiles recordings.
Multiple integration with integration interval= 10s
Only LEFT input.
Spectral analysis by octave bands.
Only RIGHT input.
Spectral analysis by octave bands.
LEFT+RIGHT inputs.
Spectral analysis by octave bands.
Only LEFT input.
Spectral analysis by third-octave bands
Only RIGHT input.
Spectral analysis by third-octave bands
LEFT+RIGHT inputs.
Spectral analysis by third-octave bands
Only LEFT input.
Only RIGHT input.
LEFT+RIGHT inputs.
Only LEFT input.
Spectral analysis by octave bands.
Only RIGHT input.
Spectral analysis by octave bands.
LEFT+RIGHT inputs.
Spectral analysis by octave bands.
Only LEFT input.
Spectral analysis by third-octave bands
Only RIGHT input.
Spectral analysis by third-octave bands
LEFT+RIGHT inputs.
Spectral analysis by third-octave bands
Only LEFT input.
Spectral analysis by octave bands.
Only RIGHT input.
Spectral analysis by octave bands.
LEFT+RIGHT inputs.
Spectral analysis by octave bands.
Only LEFT input.
Spectral analysis by third-octave bands
Only RIGHT input.
Spectral analysis by third-octave bands
LEFT+RIGHT inputs.
Spectral analysis by third-octave bands
314 days
110 days
87 days
140 days
48 days
37 days
300 days
100 days
77 days
275 days
92 days
69 days
65000
65000
65000
65000
65000
65000
1350 days
910 days
780 days
- 119 -
A3.
COMMUNICATION PROTOCOL
The commands are made by ASCII strings with variable length ending with CR-LF.
The instrument always gives an answer when it receives a command. If the command is not accepted, the answer string is always NAK-CR-LF. It is possible to deactivate the answer, when it is not explicitly requested by the command, acting on VERBOSE parameter (see PAR paragraph).
The commands are divided in 5 groups, as indicated in the following table.
Group N. commands Description
STT 3 STATUS: Analyzer Status
CNF 10 CONFIG: Sensor Config.
Each group contains a certain number of commands. Each command is identified by a specified string. The generic syntax of a command is the following:
<group>:<key>:<value>:CR-LF e.g.: “PAR:INPUT_GAIN:10\r\n”
Set the parameter INPUT_GAIN to the value 10dB (see the paragraph SET).
Only capital characters are recognized. Each token can be shortened to the minimum number of characters that uniquely identifies it. The example can be shortened as follows:
“PAR:INP:10\r\n”
In the following the possible formats of the commands are reported.
A3 - PAR:INT_TIME:<{SS,MM,HH}>:<value>CRLF
A4 - PAR:TIME:<hh>:<month>CRLF
A5 - PAR:DATE:<year>:< month >:<day>CRLF
A6 - PAR:x_AXIS_PARAMETER:<Parameter abbrev. >:<Parameter attribute>CRLF
A7 - PAR:PROFILE_PARAMETER:< Parameter abbrev. >:< Parameter attribute >CRLF
A8 - PAR:<KEY>:<value>CRLF
A10 - PAR:< KEY >:?CRLF
C1 - KEY:< KEY >CRLF
C2 - KEY:< KEY >:<value>CRLF
D1 - STT:< KEY >:<OPTION>CRLF
E1 - DMP:< KEY >CRLF
F1 - CNF:<KEY >:<CHANNEL>:<#configuration>:<value or string>CRLF
Inserting appropriately the character “?” in the string, it is possible to get both help in order to fill the desired command and the current status of the instrument parameters.
Following we reported the formats of the commands that use the “?” character.
0 ?CRLF
A9 PAR:?CRLF
A10 PAR:<KEY>:?CRLF
It provides the list of the commands groups.
It provides the PAR group list.
It provides the current status of the parameter.
C3 KEY:?CRLF
D2 STT:?CRLF
D3 STT:<KEY>:?CRLF
It provides the KEY group list
It provides the STT group list
It provides the current status related to the specified command.
E2 DMP:?CRLF
F2 CNF:?CRLF
It provides the DMP group list
It provides the CNF group list
F3 CNF:<KEY>:<CHANNEL>:<#configuration>:?CRLF
It provides the current status of the configuration parameter.
- 120 -
PAR GROUP (PARAMETERS)
The following table indicates the key list of PAR group
Key Format
INSTR_NUMBER
INSTR_VERSION
RIGHT_CONFIG
LEFT_CONFIG
RIGHT_TYPE
RIGHT_MANUF
RIGHT_MODEL
RIGHT_NUMBER
RIGHT_SENS
LEFT_TYPE
LEFT_MANUF
LEFT_MODEL
LEFT_NUMBER
LEFT_SENS
A10
A10
A8
A8
A10
A10
A10
A10
A8
A10
A10
A10
A10
A8
Description
Instrument serial number - NOT CHANGEABLE
Instrument version - NOT CHANGEABLE
Configuration number of right channel (1÷9, 0 means that the channel is not active).
Configuration number of left input (1÷9, 0 means that the channel is not active).
Sensor type connected to the right input (ACC TRI for triaxial accelerometer or OFF).
Manufacturer of the sensor connected to the right channel.
Model of the sensor connected to the right channel.
Serial number of the sensor connected to the right channel.
Nominal sensitivity of the sensor connected to the right channel.
Type of sensor connected to the left channel (ACC
MON for monoaxial accelerometer or OFF).
Manufacturer of the sensor connected to the left channel.
Model of the sensor connected to the left channel.
Serial number of the sensor connected to the left channel.
Nominal sensitivity of the sensor connected to the left channel.
VERBOSE A8 Answer mode to the commands (default ON).
Polarization connected to the right channel. – Parameter available only for reading.
Polarization connected to the right channel. Parameter available only for reading.
VPOL_4 A8 connected to the right channel. Parameter available only for reading.
Polarization voltage of left sensor related to the sensor connected to the right channel. Parameter
BATTERY TYPE
BACKLIGHT
A8
A8 available only for reading.
ALKALINE (default) or NiMH Battery Type
Backlight Display (ON/OFF, default:ON)
PRINT_OUT A8 Results printing (ON/OFF, default: OFF)
TRG_OUTPUT A8
TRG_OUT_POLARITY A8 Polarity TRGOUT output (POS/NEG)
BAUD_RATE
MEM_TYPE
DEVICE
A8
A8
A8
Baud rate RS232 port
Memory type for data logging (FLASH/CARD)
Serial device (RS232/USB)
- 121 -
Key
INPUT_GAIN
Format
A8
Description
Input amplification (0/10/20)
POND_1
POND_2
POND_3
COEFF_1
COEFF_2
COEFF_3
HIGH_PASS
1_AXIS_PARAMETER
2_AXIS_PARAMETER
3_AXIS_PARAMETER
1_VEC_PARAMETER
2_VEC_PARAMETER
3_VEC_PARAMETER
PROFILE_PARAMETER
A6
A6
A6
A6
A6
A7
A8
A8
A8
A8
A8
A8
A8
A6
Axis 1 weight for the calculation of the vector
Axis 2 weight for the calculation of the vector
Axis 3 weight for the calculation of the vector
Axis 1 coefficient for the calculation of the vector
Axis 2 coefficient for the calculation of the vector
Axis 3 coefficient for the calculation of the vector
Activation high-pass filter 0.6Hz
Parameter 1 single axis (see parameter list)
Parameter 2 single axis (see parameter list)
Parameter 3 single axis (see parameter list)
Parameter 1 vector (see parameter list)
Parameter 2 vector (see parameter list)
Parameter 3 vector (see parameter list)
Profile parameter (see parameter list)
SPECT_TYPE
SPECT_ORDER
A8
A8
Spectrum Type (AVR/MLT)
Spectrum Order: octave (1/1), or third-octave
(1/3).
Spectrum double (X2).
1_MARKER
2_MARKER
A10
A10
Marker n.1 identification
Marker n.2 identification
3_MARKER
4_MARKER
5_MARKER
6_MARKER
7_MARKER
8_MARKER
9_MARKER
DLOG_TYPE
DLOG_ADC_SAMPLES
A10
A10
A10
A10
A10
A10
A10
A8
A8
Marker n.3 identification
Marker n.4 identification
Marker n.5 identification
Marker n.6 identification
Marker n.7 identification
Marker n.8 identification
Marker n.9 identification
Data logging type (PROFILE/FULL)
It activates the ADC samples recording: at choice axis 1,2,3 or 4 or the combinations 123 and 1234.
DLOG_AUTO_STORE
CAL_LEVEL
A8
A8
It activates the Auto-Store function (ON/OFF, default: OFF)
Calibration level in m/s 2 (0.1 ÷ 300, default: 10.0)
The value that some of the parameters can assume is indicated in the following table
(the default value is bolded).
- 122 -
Parameter
BATT_TYPE
PRINT_MODE
TRG_OUT_POLARITY
BAUD_RATE
MEM_TYPE
DEVICE
VIB_MODE
INPUT_GAIN
INT_MODE
MEAS_UNIT
SPECT_TYPE
SPECT_ORDER
SPECT_INTEGRATION
DLOG_TYPE
DLOG_ADC_SAMPLES
- 123 -
57.6k
115.2k
FLASH
CARD
RS232
USB
HA
WB
BV
0
10
20
SING
MULT dB m/s 2 cm/s 2 ft/s 2 in/s 2
Value
ALKALINE
NiMH
VLM
SPC
VLM+SPC
POS
NEG
300
600
1.2k
2.4k
4.8k
9.6k
19.2k
38.4k g
AVR
MLT
1/1
1/3
OFF
X1
X2
PROFILE
FULL
OFF
1
2
3
4
123
1234
KEY GROUP
The following table indicates the commands list of KEY group
Command
OFF
Format
C1
Description
It switches off the instrument
MENU C1 key
MODE C1 key
STORE C1 It simulates the pressure for more than 2 seconds of the REC key
DOWN
RIGHT
C1
C1
DOWN arrow key
RIGHT arrow key
CLEFT
CRIGHT
PRN_VAL
EXEC
C1
C1
C1
C2
LEFT CURSOR arrow key
RIGHT CURSOR arrow key
It sends to the serial interface the visualized levels
Execution of programs
- 124 -
STT (STATUS) GROUP
The following table indicates the commands list of STT (STATUS) group.
Command Description
In the following table are indicated the commands of the ACQUISITION subgroup that can be activated with the string: ACQUISITION:<key>.
Command
HOLD
UPDATE
PAUSE
RUN
STOP
CLEAR
Format
D1
D1
D1
D1
D1
D1
Description
It stops the updating of the display
It activates the display updating
It pause the measurement
It starts the measurements
It ends the measurements
It resets the measured levels
The command STT:ACQUISITION:? gives the information about the acquisition status as indicated in the following example.
STT:ACQ:?
STT:ACQUISITION:STOP
BATTERY: 32%
MEMORY: 95.4%
DUMP TIME:00:00:01
TEMP. CORR.: 0.01dB
LAST CALIBRATION: 2003/07/31 08:37
In the following table are indicated the commands of the DISPLAY subgroup that can be activated with STT:DISPLAY:<key> string.
Command
VLM_AXIS
VLM_VECTOR
PROFILE
OCTAVE
Format
D1
D1
D1
D1
Description
It visualizes the VLM screen related to a single axis
It visualizes the VLM screen related to the vector
It visualizes the PROFILE screen
It visualizes the SPECTRUM screen
CUMUL_DISTR D1 It visualizes the PERCENTILES screen
STT:DISPLAY:? command gives information about what it is currently visualized on the vibrations analyzer display as indicated in the following example.
STT:DIS:?
STT:DISPLAY:Mode:PROFILE
In the following table are indicated the commands of the SETUP subgroup.
Command
LOAD
STORE
Format
D2
D2
Description
It loads the specified setup
It memorizes the specified setup
- 125 -
The syntax of the setup reading command is:
STT:SETUP:LOAD:<# setup>
The specified setup is loaded into the instrument.
The syntax of the setup storage command is:
STT:SETUP:STORE:<# setup>:<title (max 21 characters)>
The current setup is memorized, with title, in the specified position.
The setup number must be chosen in the interval 1÷10.
DMP (DUMP) GROUP
The following table indicates the commands list of the DMP (DUMP) group.
Command
ON
Format
E1
Description
It starts the download of the memory.
OFF
NEXT_RECORD
RECORD
CLEAR
E1
E1
E1
E1
It stops the download of the memory.
It asks for the transmission of the next record.
It asks for the transmission of the current record.
It cancel the memory
The download of the data memorized in the FLASH memory of the instrument is performed with following the commands sequence:
• DMP:ON\r\n
If there are data in memory, it is printed the header that ends with the “MEMORY DUMP\r\n” string
• DMP:RECORD\r\n
It prints in binary format the previous record
• DMP:NEXT_RECORD\r\n
It downloads in binary format a block of 512 bytes (followed by checksum). If there are no other data in memory, the string “END OF DUMP\r\n” is printed.
• DMP:CLEAR\r\n (optional)
It resets the content of the FLASH memory
• DMP:OFF\r\n
It stops the data download.
In case of a fault during the transmission of the block (checksum fault) it is possible to request to transmit again the same block with the command:
• DMP:RECORD\r\n
It prints in binary format the current record
The data download can be stopped at any time with the command:
• DMP:OFF\r\n
It stops the data download.
CNF (CONFIGURE) GROUP
The following table indicates the command list of the CNF (CONFIGURE) group.
Key Format Description
MATR F1 Number
INDX
RANG
STOR
F1
F1
F1
Index of nominal sensitivity
Maximum level measurable
Storage of the configuration
- 126 -
A sensor configuration is performed with the following commands sequence:
• CNF:PROD:<CHANNEL>:<#configuration>:<manufacturer (max 10 characters)>\r\n
Set the sensor manufacturer
• CNF:MODL:<CHANNEL>:<#configuration >:<model (max 10 characters)>\r\n
Set the sensor model.
• CNF:MATR:<CANALE>:<#configuration>:<serial number (max 10 characters)>\r\n
Set the serial number of the sensor
• CNF:TIPO:<CANALE>:<#configuration>:<code type>\r\n
Set the sensor type according to the numerical code indicated in the following table.
Code Description
The right channel can use only triaxial accelerometers while the left channel can use only monoaxial accelerometers.
• CNF:INDX:<CHANNEL>:<#configuration>:<sensitivity index >\r\n
• Set the sensitivity nominal index of the sensor according to the numeric code indicated in the following table:
Code
Nominal sensitivity Sensitivity interval
[mV/g]
2 5 2.5 ÷ 7.5
4
5
6
7
20
50
100
200
10 ÷ 30
25 ÷ 75
50 ÷ 150
100 ÷ 300
8
9
500
1000
250 ÷ 750
500 ÷ 1500
The code to insert is the one related to the sensitivity interval more adequate to the sensor.
• CNF:RANG:<CHANNEL>:<#configuration>:<level>\r\n
Set the maximum level of acceleration measurable by the sensor (in g).
• CNF:STOR\r\n
Permanently memorize the modifications made to the table of the sensors configuration.
After the execution of this command, it is necessary proceed with the calibration of the inserted or modified sensors.
The CHANNEL code is R for the right channel and L for the left one. The configuration number is chosen in the interval 1 ÷ 9.
- 127 -
A4. WEIGHTING FILTERS
Frequency responses of the weighting filters are reported hereafter: for each filter are shown
W x
(curve 2) responses and corresponding band-pass filter F x
(curve 1) including the tolerances allowed by the technical standard.
Weighting filter Wb
Filter for whole body vertical acceleration measurement (axis Z) for seating, standing or supine persons (ISO 2631-4)
Frequency [Hz]
- 128 -
Weighting filter Wc
Filter for whole body horizontal acceleration measurement (X axis) transmitted from seat back to seated persons (ISO 2631-1)
Frequency [Hz]
Weighting filter Wd
Filter for horizontal whole body acceleration measurement (X or Y axes) for seated, standing or supine persons (ISO 2631-1)
Frequency [Hz]
- 129 -
Weighting filter We
Filter for angular whole body acceleration measurement (all directions) for seated persons
(ISO 2631-1)
Frequency [Hz]
Weighting filter Wh
Filter for hand-arm system transmitted vibration measurement (all directions) (ISO 5349-1)
Frequency [Hz]
- 130 -
Weighting filter Wj
Filter for head vertical acceleration measurement (X axis) for supine persons (ISO 2631-1)
Frequency [Hz]
Weighting filter Wk
Filter for whole body vertical vibration measurement (Z axis) for seated, standing or supine persons (ISO 2631-1)
Frequency [Hz]
- 131 -
Weighting filter Wm
Filter for building transmitted acceleration on persons (all directions) (ISO 2631-2)
Frequency [Hz]
- 132 -
NOTES ABOUT THE OPERATION AND USER SAFETY
Authorized use
Observe the technical specifications indicated in the chapter “TECHNICAL FEATURES”. It is authorized only the use in compliance with the instructions indicated in this manual. Any other use is to be considered not authorized.
General safety instructions
This instrument was built and checked in compliance with the EN 61010-1 safety rules for the electronic measurement instruments and left the factory in perfect technical safety conditions.
The regular functioning and the operational safety of the instrument can be warranted only if are observed all the normal safety measures as well as the specifications described in this manual.
The regular functioning and the operational safety of the instrument can be warranted only at temperature condition specified in “TECHNICAL FEATURES” chapter.
Do not use or store the instrument in ways and/or places where there are:
• Quick changes in temperature that could cause condense formation.
• Corrosive or flammable gas.
• Direct vibrations or instrument shocks.
• High intensity electromagnetic fields, static electricity.
If the product is transported from a cold to a warm place, the formation of condense can disturbs its operation. In this case it must be waited until the temperature of the instrument reaches the room temperature before putting it in operation.
User obligations
The user of the instrument must ensure the observation of the following rules and directives on the treatment of hazardous materials:
•
•
•
EC directives for safety at work national legal standards for safety at work prevention regulations
- 133 -
SUMMARY
CONNECTORS AND KEYBOARD ................................................................................... 3
INSTRUMENT OVERVIEW ............................................................................................ 5
B LOCK D IAGRAM OF HD2030 ....................................................................................... 5
M EASURE CHANNELS .................................................................................................. 5
T HE INSTRUMENT ...................................................................................................... 5
H OW TO CONNECT THE ACCELEROMETERS TO THE ANALYZER ..................................................... 6
INTRODUCTION .......................................................................................................... 7
DESCRIPTION OF DISPLAY MODES ............................................................................. 9
VLM S CREEN ............................................................................................................ 12
P ROFILE S CREEN ........................................................................................................ 14
S
PECTRUM
S
CREEN
..................................................................................................... 15
D ISTRIBUTION OF P ROBABILITY S CREEN ............................................................................. 17
P ERCENTILES S CREEN .................................................................................................. 18
APPLICATIONS ......................................................................................................... 19
H AND A RM ............................................................................................................... 19
W HOLE B ODY ............................................................................................................ 22
B UILDING V IBRATION ................................................................................................... 23
MEASUREMENT MODES ............................................................................................. 24
S INGLE I NTEGRATION .................................................................................................. 24
M ULTIPLE I NTEGRATION ................................................................................................ 24
USE OF THE EXTERNAL MEMORY CARD ..................................................................... 25
RECORDING MODES .................................................................................................. 27
S INGLE R ECORD ......................................................................................................... 28
S INGLE P ROFILE ......................................................................................................... 28
M ULTI P ROFILE .......................................................................................................... 29
R ECORDING OF VOICE COMMENTS ..................................................................................... 31
PROGRAMS DESCRIPTION ........................................................................................ 33
M EMORY N AVIGATOR P ROGRAM ....................................................................................... 33
S ETUP M ANAGEMENT P ROGRAM ....................................................................................... 43
C ALIBRATION P ROGRAM ................................................................................................ 46
D IAGNOSTIC CHECK P ROGRAM ........................................................................................ 51
S ENSORS C ONFIGURATION P ROGRAM ................................................................................ 53
MC I
NITIALIZATION
P
ROGRAM
........................................................................................ 54
DESCRIPTION OF THE MENU FUNCTIONS ................................................................. 56
I NSTRUMENT ............................................................................................................. 58
I DENTIFICATION ...................................................................................................... 58
S
YSTEM
............................................................................................................... 58
I NPUT /O UTPUT ....................................................................................................... 59
M EASUREMENTS ...................................................................................................... 60
V IBRATION A NALYSER .................................................................................................. 61
S PECTRUM A NALYZER ................................................................................................... 61
D ATA L OGGER ........................................................................................................... 61
P ROFILES ............................................................................................................. 62
G LOBAL ............................................................................................................... 62
C ALIBRATION ............................................................................................................ 62
FIRMWARE UPDATE .................................................................................................. 63
REPORTING OF LOW BATTERIES AND REPLACEMENT OF THE BATTERIES ................ 64
INSTRUMENT STORAGE ............................................................................................ 65
- 134 -
SERIAL INTERFACE ................................................................................................... 66
MEASURE PARAMETERS ............................................................................................ 68
DIRECT PRINTER CONNECTION ................................................................................ 78
CONNECTION TO A PC WITH USB INTERFACE ........................................................... 79
I NSTALLATION N OTES ............................................................................................... 80
V ERIFICATION OF PROPER DRIVER INSTALLATION ................................................................ 80
CONNECTORS DESCRIPTION .................................................................................... 82
TECHNICAL SPECIFICATIONS ................................................................................... 85
M ETROLOGICAL SPECIFICATIONS ...................................................................................... 86
E LECTRICAL F EATURES ................................................................................................. 88
S TATISTICAL A NALYSIS ................................................................................................. 90
S
PECTRAL
A
NALYSIS
.................................................................................................... 90
V ISUALIZATION .......................................................................................................... 90
M EASUREMENTS STORAGE ............................................................................................. 90
O THER F EATURES ....................................................................................................... 91
A CCELEROMETERS TECHNICAL SPECIFICATIONS ..................................................................... 92
REFERENCE STANDARDS .......................................................................................... 99
EMC S TANDARDS ....................................................................................................... 99
I TALIAN STANDARDS .................................................................................................... 99
ORDER CODES ........................................................................................................ 100
HOW TO SOLVE THE PROBLEMS .............................................................................. 108
R ESTORE OF F ACTORY S ETUP ........................................................................................ 108
V ARIOUS P ROBLEMS .................................................................................................. 108
KEYBOARD DESCRIPTION ....................................................................................... 109
APPENDIX .............................................................................................................. 115
A1. MEASURE PARAMETERS OF HD2030 ................................................................... 115
LEVELS NUMERICALLY DISPLAYED ................................................................................. 115
A2. MEMORY CAPACITY DURING THE RECORDING FUNCTION ..................................... 118
A3.
COMMUNICATION PROTOCOL ............................................................................ 120
PAR GROUP (PARAMETERS) ................................................................................... 121
KEY GROUP ...................................................................................................... 124
STT (STATUS) GROUP ........................................................................................ 125
DMP (DUMP) GROUP ........................................................................................... 126
CNF (CONFIGURE) GROUP .................................................................................. 126
A4. WEIGHTING FILTERS ....................................................................................... 128
NOTES ABOUT THE OPERATION AND USER SAFETY ................................................ 133
- 135 -
GUARANTEE
GUARANTEE CONDITIONS
All DELTA OHM instruments have been subjected to strict tests and are guaranteed for 24 months from date of purchase. DELTA OHM will repair or replace free of charge any parts which it considers to be inefficient within the guarantee period. Complete replacement is excluded and no request of damages are recognized. The guarantee does not include accidental breakages due to transport, neglect, incorrect use, incorrect connection to voltage different from the contemplated for the instrument. Furthermore the guarantee is not valid if the instrument has been repaired or tampered by unauthorized third parties. The instrument has to be sent to the retailer without transport charge. For all disputes the competent court is the Court of Padua.
The electric and electronic devices with the following symbol cannot be disposed in the public dumps. According to the Directive UE 2002/96/EC, the European users of electric and electronic devices are allowed to give back to the Distributor or Manufacturer the used device at the time of purchasing a new one. The illegal disposing of electric and electronic devices is punished by a pecuniary administrative penalty.
This guarantee must be sent together with the instrument to our service centre.
N.B.: Guarantee is valid only if coupon has been correctly filled in all details.
Instrument type
HD 2030
Serial number
RENEWALS
Inspector
C E C O N F O R M I T Y
Safety EN61010-1
Electromagnetic compatibility. Immunity general standard EN61000-6-2:2005
Electromagnetic compatibility. Emission general standard EN61000-6-3:2007
Electrostatic Discharge Immunity EN61000-4-2 level 3
Susceptibility to electromagnetic interference
Immunity to electrical fast transients
Immunity to conducted disturbances
EN61000-4-3 level 3
EN61000-4-4 level 3
EN61000-4-6
Electromagnetic Interference - Conducted Emissions
Electromagnetic Interference - Irradiated Emissions
EN55022:2007 class B
IEC/CISPR 22 class B
- 136 -
advertisement
Related manuals
advertisement