DTM System DTM-SWIFT 350 Assembly Instructions For The Installer
Add to My manuals16 Pages
DTM System DTM-SWIFT 350 is an electromechanical actuator designed to control swing gates, providing convenient operation via radio transmitters. Its robust aluminum housing and powerful motor, capable of handling gates up to 350W and weighing up to 250kg, ensure reliable and secure gate automation. With a maximum gate width of 3m, this system is suitable for various residential and commercial applications.
advertisement
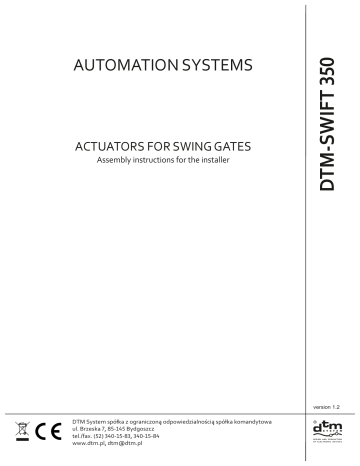
AUTOMATION SYSTEMS
ACTUATORS FOR SWING GATES
Assembly instructions for the installer
DTM System spółka z ograniczoną odpowiedzialnością spółka komandytowa ul. Brzeska 7, 85-145 Bydgoszcz tel./fax. (52) 340-15-83, 340-15-84 www.dtm.pl, [email protected]
version 1.2
DESIGN AND PRODUCTION
O F E L E C T R O N I C D E V I C E S
AUTOMATION MUST BE IMPLEMENTED IN ACCORDANCE WITH EUROPEAN STANDARDS:
EN 12100
EN 12445
EN 12453
(Safety of machinery. Electrical equipment of machines. General requirements)
(Gates. Safety in use of power operated doors. Test methods)
(Gates. Safety in use of power operated doors. Requirements)
= The installer should provide the device with a residual current circuit breaker ensuring that the devices are disconnected from the power supply (EN 60335-1).
= Automatic swing gates should comply with the standards as well as with any applicable local regulations.
= The electrical installation to which the automation is connected must comply with the applicable standards and be properly made.
PLEASE START BY READING THE IMPORTANT SAFETY RULES!
Non-observance and non-compliance with the notes marked with these symbols may lead to an accident in which people will be injured or property damage will occur. Please read these warnings carefully. The gate drive ensures correct and safe operation only if the installation and use comply with the following safety rules. DTM System is not responsible for accidents resulting from improper use or unprofessional installation of devices.
When installing or repairing the automatic gate, be careful not to wear jewelery, watches or loose clothing.
The gate should always move freely. A jammed gate must be repaired immediately. Do not try to repair the gate yourself. A specialist should be employed for this.
Lay the electric wires in accordance with the local building and electrical installation regulations. Electric cables may only be connected to a properly grounded network by an authorized electrical engineering specialist.
Remove any locks installed on the gate to avoid damaging it.
Keep additional accessories away from children. Do not allow children to operate the control buttons or the remote control. It should be remembered that an automatic gate is a device in which the risk of serious injury cannot be completely eliminated in the event of remote operation, not controlled by an adult.
Control devices should allow for visual verification of the gate itself and its immediate surroundings.
After installation, it is necessary to check that the mechanism is correctly set and that the drive, restraint system and emergency unlocking function properly.
During maintenance work, such as cleaning, lubrication, etc., the gate automation must be disconnected from the mains. In the electric installation of the gate, a device for disconnecting all phases by means of a switch
(distance between contacts at least 3mm) or separate fuses should be provided.
The gate drive cannot be started and continue to operate when there is a wicket in the gate and it is not properly closed.
Any possible movement of the gate towards the wall should be blocked or limited (e.g. by installing limiters).
Thanks to this, we will eliminate the possibility of being crushed while opening the gate.
Please make sure that the persons who install, maintain or operate the gate automation follow these instructions. Keep these instructions in a place where you can refer to them quickly when needed.
Crush or injury protection systems (e.g. photocell systems) must function properly after the drive has been mounted and connected to the mains.
Warranty.
DTM System delivers the equipment in working order and ready for use and provides a warranty for a period of 24 months from the date of purchase by the end customer. The warranty period is determined on the basis of warranty seals. DTM System undertakes to repair the device free of charge if during the warranty period there are defects due to the manufacturer's fault. The defective device must be delivered to the place of purchase at your own expense, with a short, unambiguous description of the damage. The cost of disassembly and assembly of the device is borne by the user. The warranty does not cover any damage resulting from improper use, unauthorized adjustments, alterations and repairs as well as damage caused by lightning, overvoltage or short circuit in the power supply network. The detailed terms and conditions of granting a guarantee are regulated by relevant legal acts.
1. Introduction
1.1. Basic information
Electromechanical actuators are designed to control swing gates. The assembled and started system can be conveniently operated by radio transmitters. Make sure you have all the elements shown in Figure 1, and then read the entire manual.
1
2
6
M A D E N D I N
P O L A
ECO
VARIA m o n t a d l a i n s t a
Profesjonalny zestaw automatyki bramowej dla bram skrzydłowych
I n s t r u k c j a
Zestaw ECO
VARIA
oparty o siłowniki: l a t o r a
4
7
5
5
6
7
8
3
4
1 actuators
2 two elements fixing the actuator's piston to the gate fitting two sets of elements fixing the actuator drive to the pillar fitting manual two keys for the drive clutch two motor capacitors for actuators screws for mounting drives in holders 2 and 3 with plugs mechanical limit switch
Fig. 1.
Necessary mechanical components.
8
1.2. Technical data of selected elements of the DTM300 / DTM400 / DTM600 set
• housing material
• mains supply (motor)
• current consumption
• power consumption
• capacitor
• maximum gate width
• maximum gate weight
• protection class
•
•
thermal protection
arm stroke
• leaf movement speed
• drawbar pull
• lubrication
• work intensity
• temperature range
• actuator weight
• spacing of the actuator pin sockets min-max aluminum with plastic parts
230V AC, 50Hz
1,6A
350W
8uF, 400V
3m
250kg
IP-44
150 C
350mm
12mm/s
2200 N
TS10
30%/h (18 cycles/h) o
10 kg
476-826mm
3
1
2. MECHANICAL ASSEMBLY
2.1. Preparation of the workplace
In order to install it correctly, we must properly prepare the workplace. It is necessary to test the door system in terms of the requirements presented below:
4 The drive mechanism requires space on the sides of the arms and assembly. Make sure that this place is available. If there is no place, please provide it!
4 Gates, which operate heavy loads (wind) must be secured with an additional electric lock.
4 Check that the gate opens and closes freely.
Gateway parameters that affect the operation of the system:
4 Gate size: The size of the gate is a very important factor. Wind can brake the gate or cause certain stresses, significantly increasing the amount of force required to move it.
4 Gate weight: The weight of the gate is an approximate parameter. However, the maximum permitted weight of the door should not be exceeded. The actual weight transferred by the drive is influenced by the type of gate, wind, and the space around the gate.
4 Temperature influence: Low external temperatures may hinder or prevent commissioning (soil changes, etc.), while high temperatures may cause jamming of elements that fit too tightly due to thermal expansion of the metal.
4 Service frequency / switch-on time: Drives have a maximum switch-on time of approximately 30% (18 cycles) per hour.
left actuator junction box photocell external photocell photocell photocell junction box right actuator antenna signal lamp
2 photocell
DTM System remote
2
4
3
1 gate controller external photocell
Fig. 2.
Illustrative view of the gate automation installation.
CAUTION!
The actuator must not work so that the piston extends or retracts to the end. A correctly set actuator makes a movement of up to 99% of stroke when the gate is closed and to 1% when the gate is open. Failure to do so will damage the actuator and void the warranty!
CAUTION!
The drives are not designed for continuous operation within their maximum duty cycle (continuous operation). The drive becomes too hot and switches off until the temperature reaches the switch-on parameters again. The outside temperature and gate parameters are important factors that influence the actual start-on time.
CAUTION!
The gate must operate smoothly and without impact, the movement must be smooth and unobstructed.
Please note that the ground level may rise by several centimeters in winter. The gate should be stable and as far as possible free from play in order to prevent undesirable and swinging movements. Determine what materials are needed to install the kit and provide them before starting the installation. This applies to glued anchors, bolts, stops, cables, distribution boxes, tools (fig. 3), etc.
Fig. 3.
Materials and tools necessary for assembly.
2.2. Preparing the gate, choosing the type of gate
The gate type determines the position in which the actuator drive will be mounted (Figure 4). When the gate stop is at the ground, the drive should also be installed as low as possible so that it cannot twist. Only frame parts should be used as a mounting base. When we have a steel gate, the gate hardware should be attached to the main frame. When the bracket is not sufficiently stable, it must be strengthened. If we have a wooden gate, the gate hardware must be screwed right through. In such cases, it is advisable to use the board from the outside so that the fastening cannot loosen over time. Thin wooden gates must be additionally reinforced to withstand the stresses that occur.
B
C
A
D E F
Fig 4.
Gate types and recommended places for mounting actuators.
2.3. Selection of the opening angle of the gate
The allowed angles range from 90 degrees to 110 degrees. If the gate has a tongue, we must remember about the correct order of opening and closing the leaves. Figure 7 will help in selecting the appropriate mounting dimensions for the actuators, which shows the A and B mounting dimensions and the corresponding opening angles.
3
2.4. Limiters swing gate requires a limiter in the OPEN and CLOSE directions. Stops protect the drive, gate and fittings against wear. Operating the gate without permanently fixed stops leads to its malfunction. It is often dangerous, this leads to premature wear and will invalidate the warranty!
4
90 0 90 0
Fig 5.
Configurations of the gate opening limiters - a mechanical limit stop on opening present in the gate and delivered with actuators.
The actuators are equipped with an internal actuator stroke limitation system consisting of adjustable and independent mechanical end stops (figs. 5 and 6), one for the opening stroke and one for the closing stroke
(optional). The use of internal stops is convenient when there are no limit switches or when there is no other way to limit the gate leaf stroke. Wherever possible, it is recommended to use gate stop limiters.
A open closed
B
B
Fig. 6.
Use of an additional set of mechanical limit switches in the actuators.
A
B
S
E
D
( a )
124
893
476 350
DTM-SWIFT350
If it is not possible to achieve the dimensions given in the table, other dimensions can be determined - for the leaf opening 90 ° A = B
(difference between A and B max. 4 cm) to the extent that allows the actuator to completely open and close the leaf.
I n c o r r e c t s e l e c t i o n o f t h e s e dimensions may result in the fact that the actuator stroke is not enough to fully open and / or close the gate.
( a ) max
90°
90°
90°
100°
100°
11 0 °
A
(mm)
150
150
180
130
150
130
B
(mm)
130
200
150
180
150
150
D
(mm)
350
E
(mm)
820
Fig. 7.
Definitions of dimensions of DTM-SWIFT350 actuators with tables with recommended values.
S
(mm)
40
(es.)
Fig. 8.
Execution of the pillar fittings.
Adjustment:
• remove the wormscrew cover and loosen the screws A (fig. 6);
• pre-screw the mechanical limit switch B to the wormscrew (Fig. 6)
• move the leaf in the direction of the maximum stroke of the actuator and tighten all the screws of the mechanical limit switches
• cycle to open and close to check the correct position of the stops, then reinstall the wormscrew cover.
5
6
2.5. Pole fitting
The correct position of the pillar fitting is decisive for the subsequent operation of the gate. The first step is to determine the distance between the motor pivot point and the gate pivot point (figure 7), and thus the opening angle (see point 2.3.). These dimensions are marked as dimension A and dimension B. The influence of these dimensions on the operation and movement of the door should not be underestimated. Achieve the best dimension for the opening angle we are interested in using the experimental method. Suggested A / B dimensions are shown in the table in Figure 7. It may also be necessary to shorten or lengthen the hinge plate to achieve optimal dimensions. Before defining the final installation dimensions, it is essential to check that the actuator does not hit anywhere when opening / closing.
(mm)
55 d. 8,5
3 d. 8,5
55 32
105
70
Fig. 9.
Installation of gate fittings.
ASSEMBLY : The actuators in the swing gate installations exert very high forces on the pole.
Therefore, after determining the best dimensions, the hinge plate is best welded directly onto the pole. For thick stone or concrete columns, the hinge must be welded to the support plate and secured so that the dowel pins will not come loose during operation. Adhesive bonded anchors are recommended for the installation of the support plate, where the threaded stud is glued to the wall in a stress-free manner, which is more suitable than using expansion plugs, plastic or steel. In the case of brick poles, a relatively large steel plate should be screwed to cover several bricks and the hinge plate can then be welded to it. The angle plate can also be used as a support plate and screwed to the corner of the column.
a b min. 100 mm
Fig. 10.
Positioning the actuator in relation to the ground (a), mounting the bracket to the actuator (b).
2.6. Gate fitting
The gate hardware must be mounted horizontally in relation to the pillar fitting (Fig. 9). The distance between the fittings is determined by the fixing dimension. When the gate is closed, the drive should perform a closing maneuver of 99%. When open, the drive should leave 1% stroke.
Using the full travel of the actuator during operation may damage the actuator and void the warranty! The attachment dimensions must be complied with in all circumstances! (dimensions A and B). In the case of steel gates, the brackets should be welded or diagonally screwed. In the case of through-bolting, either large washers or a plate on the other side should be used. However, for wooden gates, use through drilling when fixing. It is recommended to fix the plate from the outside so that the bracket does not come loose. Thin wooden gates without a metal frame must be additionally reinforced to withstand constant stresses.
ATTENTION!
Sufficient space must be left for the drive to turn. Failure to do so will break the drive mounting!
2.7. Mounting the drive arms
Unlock the drive. Slide the unlocked drive onto the gate fittings and secure it with the provided fastening screws. Before the first start-up, it is necessary to check whether the actuator does not collide with the gate hardware and the gate itself throughout the entire range of operation. If we do not check it, we may break the drive mounting! When mounting the drive on the hinge, do not use a hammer or similar tool.
2.8. Lock / unlock the drive
These two operations are only required in the event of a power failure, the user or installer must be instructed by the installer and the instructions must be kept in a safe place with the release key. Before starting the procedure, make sure that the entire automation is disconnected from the power supply, even in the event of a power cut. All possible electric locks must be unlocked.
To unlock the operator: open the rubber plug, insert the key and turn it clockwise, lift the cover, grab the lever
(brightly colored) and turn it towards the front of the actuator, the leaf can now be moved by hand.
Reverse order of steps is required to lock the drive. Additionally, after blocking the drive, the gate must be moved manually to engage the gearmotor.
Fig.11.
Unlocking the drive.
ATTENTION!
THE FORCE IN THE GATE CONTROLLER SHOULD BE ADJUSTED SO THAT AFTER COMPLETELY
CLOSING THE GATE, IT WILL BE POSSIBLE TO EMERGENCY UNLOCKING!
Excessive force operation of the actuator, in addition to increased wear of the actuator components, will result in excessive stresses in the gear mechanism after the gate is completely closed. This can lead to a situation where it becomes impossible to disengage the clutch using the supplied release key. An attempt to unlock with excessive force may damage the actuator mechanism and / or the key, which is not subject to warranty repair.
7
2.9. Maintenance
The drive mechanics are maintenance-free. However, it is recommended that at regular intervals
(monthly) check that the gate hardware and the drive are securely fastened. Loosen the drive and check that the gate is functioning properly. Remember that the drive cannot eliminate problems caused by a malfunctioning gate.
3. Electrical installation
IMPORTANT REMINDER
Electrical installations and automation of the drive must be performed by experienced and qualified personnel in accordance with applicable legal regulations. There are dangerous voltages of 230V 50Hz in the devices, all connections must be made when the voltage is off. The installer's task is to mount the system safely enough to minimize the risks associated with its use. Anyone who installs the device without complying with all applicable regulations is responsible for any damage that the device may cause.
3.1. Preparation of electrical installation components
WIRING - Before purchasing the wiring, check if we have a photocell with a built-in optical signaling device, if so, we must provide two additional wires in the photocell wires. The length of the cabling depends on the length of the gate, the width and height of the posts, and the space provided for distribution boxes, so we should estimate the length of the cables ourselves. The wiring layout is presented in Figure 12. As the actuators rotate in relation to the poles, cables with appropriate flexibility should be used in the section between the junction box and the actuator to reduce the risk of damage by twisting the actuator-controller connection. The starting capacitor can be connected inside the distribution box or in the controller.
3.2. Connecting devices to the controller
Connecting devices to the controller should be the last installation step, performed in accordance with the instructions attached to the control unit and figure 13. First, install the motors, arrange the necessary cables and attach the safety devices. During the assembly of the installation, use the main switch which cuts off the mains voltage. It should be remembered that moisture and water destroy electronic devices, therefore it is necessary to protect the controller against these factors. All openings and cable entries must be sealed to maintain the desired IP protection class.
ATTENTION!
Electrical installations and automation of the drive must be performed by experienced and qualified personnel in accordance with applicable legal regulations.
8
3x1,50
230V
2x1,50
4x0,50
4x 1,0
Rx
Fig. 12.
Elements of electrical installation.
Tx
2x0,50
4x 1,0
230V
OP CL
Fig. 13.
Location and description of connectors supplying the drive motor.
4. Acceptance tests
ATTENTION!
After installing the controller and all associated devices, especially safety devices, final tests should be made to check the entire automation. These tests should be performed by competent personnel who are aware of the risks involved! Final tests are the most important phase in the implementation of automation. Individual components such as the motor, photocells, etc. may require specific checks and therefore it is recommended to follow the checking procedures in the manuals for the relevant components.
ATTENTION!
Both leaves of the gate, both during opening and closing, should present the same resistance to the actuators. Therefore, wings of the same size and weight should be used. Moreover, the plane of the gate leaf should be positioned in relation to the ground in such a way that the resistance varies during opening and closing due to the force of gravity.
Final tests include the following steps
4.1. Direction control
Check whether the automation is physically moving in the opening direction when the OPENING function is activated. In a situation when the movement is in the direction of closing, or there is no movement, disconnect the power supply of the controller and switch the places of connecting the cables of the appropriate actuator to the OPEN and CLOSE terminals. Check the operation again.
4.2. Making any additional controller settings
All required parameters of the controller operation should be set. We perform this operation on the basis of the manual delivered with the control unit and this is where you should look for information on electrical connections and the configuration of the controller itself.
4.3. Security control
If photocells are installed, break the photocells and check that the controller reacts appropriately. Do the same for the other safety devices, if fitted.
4.4. Checking the functions controlling the movement of the actuator
Check that all devices (especially safety devices), buttons and radio transmitters properly control the movement of the gate. If not, make the necessary corrections.
4.5. Control of emergency gate opening mechanisms
Carry out a trial unlocking of the mechanism with the gate closed in order to check the forces required for this operation.
9
DTM System hereby declares that the drive complies with the EU directives. The full text of the EU declaration of conformity is available at the internet address: www.dtm.pl
10
CAUTION!
The presented symbol informs that a given electric or electronic device, after its end of use, must not be disposed of with household waste. The device should be delivered to a specialized collection point. Detailed information on the nearest collection point is available from your local authority. In addition, the product can be returned to your local distributor when purchasing another device with similar characteristics. By ensuring this product is disposed of correctly, you conserve valuable natural resources and avoid any negative effects on health and the environment which can be put at risk in case of inappropriate waste handling.
D E S I G N A N D P R O D U C T I O N
O F E L E C T R O N I C D E V I C E S
DTM System spółka z ograniczoną odpowiedzialnością spółka komandytowa
Ul. Brzeska 7, 85-145 Bydgoszcz, Polska http://www.dtm.pl
e-mail: [email protected]
advertisement
Related manuals
advertisement