- Home
- Do-It-Yourself tools
- Power tools
- Paint Sprayer
- Graco
- 311104B, LT Series Gravity Feed Air Spray Guns, U.S.
- Owner's manual
Graco 311104B, LT Series Gravity Feed Air Spray Guns, U.S. Owner's Manual
Add to my manuals10 Pages
advertisement
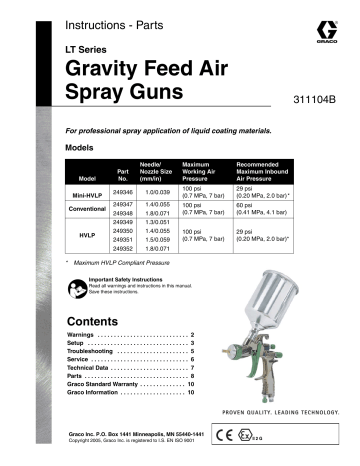
Instructions - Parts
LT Series
Gravity Feed Air
Spray Guns
For professional spray application of liquid coating materials.
Models
Model
Part
No.
Mini-HVLP
Conventional
HVLP
249346
249347
249348
249349
249350
249351
249352
Needle/
Nozzle Size
(mm/in)
1.0/0.039
1.4/0.055
1.8/0.071
1.3/0.051
1.4/0.055
1.5/0.059
1.8/0.071
* Maximum HVLP Compliant Pressure
Maximum
Working Air
Pressure
100 psi
(0.7 MPa, 7 bar)
100 psi
(0.7 MPa, 7 bar)
100 psi
(0.7 MPa, 7 bar)
Recommended
Maximum Inbound
Air Pressure
29 psi
(0.20 MPa, 2.0 bar) *
60 psi
(0.41 MPa, 4.1 bar)
29 psi
(0.20 MPa, 2.0 bar)*
Important Safety Instructions
Read all warnings and instructions in this manual.
Save these instructions.
Contents
Warnings . . . . . . . . . . . . . . . . . . . . . . . . . . . . 2
Setup . . . . . . . . . . . . . . . . . . . . . . . . . . . . . . . 3
Troubleshooting . . . . . . . . . . . . . . . . . . . . . . 5
Service . . . . . . . . . . . . . . . . . . . . . . . . . . . . . . 6
Technical Data . . . . . . . . . . . . . . . . . . . . . . . . 7
Parts . . . . . . . . . . . . . . . . . . . . . . . . . . . . . . . . 8
Graco Standard Warranty . . . . . . . . . . . . . . 10
Graco Information . . . . . . . . . . . . . . . . . . . . 10
311104B
Graco Inc. P.O. Box 1441 Minneapolis, MN 55440-1441
Copyright 2005, Graco Inc. is registered to I.S. EN ISO 9001
II 2 G
2
Warnings
Warnings
The following general warnings are related to the safe setup, use, grounding, maintenance and repair of this equipment. Additional more specific warnings may be found throughout the text of this manual where applicable.
WARNING
FIRE AND EXPLOSION HAZARD
Flammable fumes, such as solvent and paint fumes, in work area can ignite or explode. To help prevent fire and explosion:
• Use equipment only in well ventilated area.
• Eliminate all ignition sources; such as pilot lights, cigarettes, portable electric lamps, and plastic drop cloths (potential static arc).
• Keep work area free of debris, including solvent, rags and gasoline.
• Do not plug or unplug power cords or turn lights on or off when flammable fumes are present.
• Ground equipment and conductive objects in work area.
• If there is static sparking or you feel a shock, stop operation immediately.
Do not use equipment until you identify and correct the problem.
• Keep a fire extinguisher in the work area.
EQUIPMENT MISUSE HAZARD
Misuse can cause death or serious injury.
• Do not exceed the maximum working pressure or temperature rating of the lowest rated system component. See Technical Data in all equipment manuals.
• Use fluids and solvents that are compatible with equipment wetted parts. See Technical Data in all equipment manuals. Read fluid and solvent manufacturer’s warnings.
• Check equipment daily. Repair or replace worn or damaged parts immediately.
• Do not alter or modify equipment.
• Use equipment only for its intended purpose. Call your Graco distributor for information.
• Route hoses and cables away from traffic areas, sharp edges, moving parts, and hot surfaces.
• Do not kink or over bend hoses or use hoses to pull equipment.
• Keep children and animals away from work area.
• Comply with all applicable safety regulations.
TOXIC FLUID OR FUMES HAZARD
Toxic fluids or fumes can cause serious injury or death if splashed in the eyes or on skin, inhaled, or swallowed.
• Read MSDS’s to know the specific hazards of the fluids you are using.
• Store hazardous fluid in approved containers, and dispose of it according to applicable guidelines.
PERSONAL PROTECTIVE EQUIPMENT
You must wear appropriate protective equipment when operating, servicing, or when in the operating area of the equipment to help protect you from serious injury, including eye injury, inhalation of toxic fumes, burns, and hearing loss. This equipment includes but is not limited to:
• Protective eyewear
• Clothing and respirator as recommended by the fluid and solvent manufacturer
• Gloves
• Hearing protection
PRESSURIZED EQUIPMENT HAZARD
Fluid from the gun/dispense valve, leaks, or ruptured components can splash in the eyes or on skin and cause serious injury.
• Follow Pressure Relief Procedure in this manual, when you stop spraying and before cleaning, checking, or servicing equipment.
• Tighten all fluid connections before operating the equipment.
• Check hoses, tubes, and couplings daily. Replace worn or damaged parts immediately.
311104B
Setup
Setup
1.
Install an air pressure regulator on gun air supply line to control air pressure.
2.
Install a shutoff valve downstream of the air regulator to shut off gun air.
3.
Connect a clean, dry, filtered air supply.
4.
Connect air supply line to gun air inlet (21). F IG . 1.
Connect other end to shutoff valve.
5.
Install fluid filter (29) into fluid inlet (6). Refer to
6.
Screw on gravity cup (30).
7.
Remove gravity cup cover (A) and fill cup with solvent to flush if this is first time using equipment.
Pressure Relief Procedure
WARNING
Follow
Pressure Relief Procedure when you stop
spraying and before cleaning, checking, or servicing
equipment. Read warnings, page 2.
1.
Turn off gun air supply.
Adjust Spray Pattern
1.
Rotate air cap to change spray pattern direction.
F IG . 2.
A
6
30
21
F IG . 1
Flush Spray Gun
CAUTION
Flush spray gun before using it. Use solvent that is compatible with gun wetted parts and fluid that will be sprayed. Use lowest possible pressure, and spray into grounded metal waste container. Read warnings,
Vertical Pattern Adjustment
F IG . 2
7
20
22
F IG . 3
2.
F IG . 3. For maximum fluid flow and to prevent pre-
mature fluid nozzle wear, turn fluid adjustment knob (20) left until no trigger restriction is felt; trigger should be able to touch gun handle. Then turn knob out 1/2 turn more.
3.
If further fluid flow restriction is needed, use different size needle/nozzle/air cap combination.
If necessary, fluid adjustment knob (20) can be turned right to reduce volume of fluid output. However, continuously spraying with fluid adjustment knob closed causes accelerated abrasive wear on fluid needle and trigger/air valve shaft interface.
If fluid adjustment knob (20) is turned in all the way, the gun emits only air.
After flushing, follow Pressure Relief Procedure
.
311104B 3
4
Setup
4.
Test spray pattern and atomization while holding gun about 6-8 inches (150-200 mm) from test piece. a.
If pattern is too wide, turn pattern adjustment knob (7) right to narrow pattern.
b.
To create a round pattern, turn pattern adjustment knob (7) fully right. c.
If pattern is too narrow, turn knob (7) left.
d.
Check atomization. Increase gun air supply pressure in 5 psi (34 kPa, 0.3 bar) increments until you have the desired atomization.
CAUTION
Do not exceed maximum working air pressure shown
on front cover. Read warnings, page 2.
Applying Paint
For the best results:
• Keep gun perpendicular to surface and consistent distance of about 6-8 inches (150-200 mm). Do not
angle the gun as you spray. F IG . 4.
Daily Cleaning and Maintenance
WARNING
Follow Pressure Relief Procedure
when you stop spraying and before cleaning, checking, or servicing
equipment. Read warnings, page 2.
CAUTION
• Do not submerge gun in solvent. Solvent dissolves lubricant, dries out packings, and may clog air passages. You can immerse front end of gun in solvent just until cup connection is covered.
• Do not use metal tools to clean air cap holes as this may scratch them and distort the spray pattern.
• Use a compatible solvent.
1.
Follow Pressure Relief Procedure , page 3.
2.
Clean fluid and air line filters.
3.
Check for fluid leakage from gun and fluid hoses.
Tighten fittings or replace equipment as needed.
4.
Flush gun before changing colors and when you are done spraying.
5.
Remove cup (30) and filter (29) and clean them.
6.
Remove air cap (1) and nozzle (2) as instructed on
page 6 and soak them in compatible solvent.
F IG . 4
• Use smooth, even strokes, with about 50% overlap.
• Mini-HVLP and HVLP Guns: Use a slightly slower hand movement and make fewer passes than you would with a conventional air spray gun. Take care to avoid runs or sags.
CAUTION
Trigger gun and use gun tool (27) whenever you tighten or remove nozzle (2) to avoid damaging needle seat (4) and nozzle,
7.
Use a rag moistened in solvent to wipe down outside of gun.
8.
Before reinstalling air cap and nozzle, clean them and front of gun with a soft-bristle brush dipped into compatible solvent.
Do not use a wire brush or metal tools. To clean out air cap holes, use a soft implement, such as a toothpick.
311104B
Troubleshooting
Troubleshooting
WARNING
Follow Pressure Relief Procedure
, page 3, before troubleshooting or servicing. Read warnings, page 2.
Problem Cause
One side of air cap (1) dirty or clogged
Solution
Clean air cap orifices. See page 4. Blow air through orifices until
clean. If air cap holes are damaged, replace air cap.
Spitting a. Loose air cap (1).
a. Tighten.
b. Dried or damaged air cap (1) or fluid nozzle (2). b. Rotate air cap 180°.
If pattern follows air cap, problem is in air cap. Clean and inspect.
See page 4. If pattern is not corrected, replace air cap.
If pattern does not follow the air cap, the problem is with the fluid
nozzle. Clean and inspect the nozzle. See page 4. If the pattern
is not corrected, replace nozzle.
a. Atomization air pressure set too high.
a. Reduce air pressure.
b. Spraying a thin material in too wide of a pattern. b. Increase material control by turning fluid adjustment knob (20) to left, while reducing spray width by turning pattern adjustment knob (7) to right.
Or increase material viscosity.
Air getting into paint stream.
a. Cup almost empty.
b. Dry needle packing (3).
c. Fluid nozzle (2) too loose.
d. Dried material between nozzle (2) and gun body.
a. Fill cup.
b. Loosen packing seat (4) and put a few drops of machine oil on packing (3). Retighten seat (4).
c. Tighten.
d. Clean nozzle and front of gun. See page 4.
Other spray pattern problems
Unable to get round pattern.
Will not spray.
Fluid leaking from packing nut (4).
e. Damaged needle seal a. Gun not properly adjusted.
b. Sluggish needle (18).
b. Clean and lubricate.
Pattern adjustment knob (7) not seating properly.
Clean or replace knob.
a. No air pressure at gun.
a. Check air supply and air lines.
b. Cup empty.
b. Fill cup.
c. Fluid adjustment knob (20) turned too far right.
c. Adjust knob (20) to the left.
d. Fluid too thick for gravity feed.
a. Packing nut (4) loose.
b. Packing (3) worn or dry.
Fluid nozzle (2) dripping.
a. Dry packing (3).
Thin, coarse finish.
Thick, dimpled finish
(resembling orange peel) b. Sluggish needle (18).
c. Packing nut (4) too tight.
d. Worn fluid nozzle or needle.
a. Gun held too far from surface.
b. Atomization air pressure set to high.
Gun held too close to surface.
d. Thin material.
a. Tighten, but not so tight as to grip needle.
b. Lubricate or replace.
a. Lubricate.
b. Clean and lubricate.
c. Loosen.
d. Replace.
a. Hold gun about 6-8 inches (150-200 mm) from surface.
b. Reduce air pressure.
Hold gun about 6-8 inches (150-200 mm) from surface.
311104B 5
6
Service
Service
WARNING
Follow
Pressure Relief Procedure when you stop
spraying and before cleaning, checking, or servicing
equipment. Read warnings, page 2.
Preparation
1.
Flush and clean gun before servicing. See page 4.
2.
Follow Pressure Relief Procedure , page 3.
Air Cap, Nozzle, and Needle
1.
Unscrew air cap (1). F IG . 6.
2.
Trigger gun while you remove the nozzle (2) with
CAUTION
Trigger gun and use gun tool (27) whenever you tighten or remove the nozzle (2) to avoid damage.
3.
Remove fluid adjustment knob (20) and spring (19).
4.
Pull needle (18) out the back of the gun.
2
27
3.
Remove air valve shaft (8).
4.
Remove fitting (17) with Allen wrench
(Mini-HVLP: 8 mm, Conventional/HVLP: 9 mm).
5.
Remove o-rings (13, 10) and holder (9) from fitting
(17).
6.
Remove spring (16), piston (14), and o-ring (10).
7.
Remove air valve seat (12) with o-ring (13) and gasket (11).
8.
Remove o-ring (10) and holder (9).
9.
Replace parts as needed.
10.
Reassemble in reverse order. Lubricate needle and o-rings. Tighten o-ring packing holders (9) until smooth movement of the air valve shaft (8) and air valve piston (14) is achieved. DO NOT overtighten the o-ring packing holders as a sluggish needle or sticky trigger condition will result. Be sure to trigger gun when installing nozzle (2).
1 2 5
6
30
29
8
4 3*
9* 10*
28 15* 27
11* 12
7
10* 9*
13* 10* 14 16* 13* 17
YES NO
F IG . 5
26* 24 24
23
25
15*
F IG . 7
18
22
21
19* 20
TI5088B
F IG . 6
20 19 18 2 1
Air Valve and Needle Packings
1.
Remove retaining ring (26), gaskets (24), pin (25)
2.
Remove packing nut (4) and packing (3).
311104B
Technical Data
Technical Data
Maximum Working Air Pressure . . . . . . . . . . . . . . . . . . . . . . . . . . . . . . . . .100 psi (0.7 MPa, 7 bar)
Maximum HVLP Inbound Air Pressure. . . . . . . . . . . . . . . . . . . . . . . . . . . .29 psi (0.2 MPa, 2 bar)
Fluid and Air Operating Temperature Range . . . . . . . . . . . . . . . . . . . . . . .32–109° F (0–43° C)
Weight
Mini-HVLP . . . . . . . . . . . . . . . . . . . . . . . . . . . . . . . . . . . . . . . . . . . . . .14 oz. (40 g)
Conventional. . . . . . . . . . . . . . . . . . . . . . . . . . . . . . . . . . . . . . . . . . . . .24 oz. (68 g)
HVLP . . . . . . . . . . . . . . . . . . . . . . . . . . . . . . . . . . . . . . . . . . . . . . . . . .24 oz. (68 g)
Air Inlet . . . . . . . . . . . . . . . . . . . . . . . . . . . . . . . . . . . . . . . . . . . . . . . . . . . .1/4-18 npsm (R1/4-19) compound thread
Wetted Parts . . . . . . . . . . . . . . . . . . . . . . . . . . . . . . . . . . . . . . . . . . . . . . . .Aluminum, stainless steel, brass, PTFE
Noise Data
Mini-HVLP
Conventional Sound Pressure . . . . . . . . . . . . . . . . . . . . . . . . . . . . . . . . . . .
Sound Power . . . . . . . . . . . . . . . . . . . . . . . . . . . . . . . . . . . . .
79.01 dB(A)
88.91 dB(A)
HVLP
Sound Pressure . . . . . . . . . . . . . . . . . . . . . . . . . . . . . . . . . . . 64.08 dB(A)
Sound Power . . . . . . . . . . . . . . . . . . . . . . . . . . . . . . . . . . . . . 73.97 dB(A)
Sound Pressure . . . . . . . . . . . . . . . . . . . . . . . . . . . . . . . . . . . 72.98 dB(A)
Sound Power . . . . . . . . . . . . . . . . . . . . . . . . . . . . . . . . . . . . . 82.88 dB(A)
Air Consumption
Mini-HVLP . . . . . . . . . . . . . . . . . . . . . . . . . . . . . . . . . . . . . . . . . . . . . .4.9 cfm at 29 psi (200 kPa, 2 bar)
Conventional. . . . . . . . . . . . . . . . . . . . . . . . . . . . . . . . . . . . . . . . . . . . .11.9 cfm at 41 psi (283 kPa, 2.8 bar)
HVLP . . . . . . . . . . . . . . . . . . . . . . . . . . . . . . . . . . . . . . . . . . . . . . . . . .11.4 cfm at 29 psi (200 kPa, 2 bar)
311104B 7
8
Parts
Parts
Mini-HVLP - Part No. 249346
Ref.
6
7
2
3*
4†
5†
No.
Part No. Description
1
15G123 Air Cap
15G124 Fluid Nozzle, 1.0
Needle Packing
Needle Packing Seat
Gun Body
15G127 Fluid Inlet Fitting
15G128 Pattern Adjustment Knob
8†
Air Valve Shaft
9*
Packing Holder
10*
O-ring
11*
Gasket
12†
Air Valve Seat
13*
O-ring
14†
Air Valve Piston
15*
O-ring
30
Qty.
1
2
3
1
1
2
1
2
1
1
1
1
1
1
1
Ref.
17
18
19*
20†
21
22†
No.
Part No. Description
16*
15G135
Air Valve Spring
Air Valve Fitting
15G136 Fluid Needle
Needle Spring
Fluid Adjustment Knob
15G139 Air Inlet Fitting
Air Adjustment Valve
23
15G141 Trigger
24†
Gasket
25
Trigger Pin
26*
Retaining Ring
27†
Gun Wrench
28†
Brush
29
30
15G147 Fluid Filter
15G148 Cup
* Parts included in Repair Kit 249510
† Parts not available.
8
4
3*
1 2 5
9* 10*
6
29
26* 24 24
23
25
15*
11* 12
28
15*
27
7
10* 9*
10* 13* 14 16* 13* 17
TI5088B
18
22
21
19*
20
Qty.
1
1
1
1
2
1
1
1
1
1
1
1
1
1
311104B
Parts
Conventional - Part Nos. 249347 and 249348 and
HVLP - Part Nos. 249349, 249350, 249351, and 249352
Model No.
Conventional
Conventional
HVLP
HVLP
HVLP
HVLP
Part No.
Description
249347
249348
249349
249350
249351
249352
Conventional Air Spray, 1.4
Conventional Air Spray, 1.8
HVLP, 1.3
HVLP, 1.4
HVLP, 1.5
HVLP, 1.8
Includes:
Air Cap (1) Nozzle (2) Needle (18) Repair Kit
15G157
15G157
15G149
15G149
15G149
15G149
15G151
15G153
15G150
15G151
15G152
15G153
15G170
15G156
15G154
15G170
15G155
15G156
249511
249511
249511
249511
249511
249511
Ref.
6
7
2
3*
4†
5†
No.
Part No. Description
1
See table Air Cap
See table Fluid Nozzle, 1.0
Needle Packing
Needle Packing Seat
Gun Body
15G160 Fluid Inlet Fitting
15G161 Pattern Adjustment Knob
8†
Air Valve Shaft
9*
Packing Holder
10*
O-ring
11*
Gasket
12†
Air Valve Seat
13*
O-ring
14†
Air Valve Piston
15*
O-ring
Qty.
1
2
3
1
1
2
1
2
1
1
1
1
1
1
1
Ref.
17
18
19*
20†
21
22†
No.
Part No. Description
16* Air Valve Spring
15G169 Air Valve Fitting
See table Fluid Needle
Needle Spring
Fluid Adjustment Knob
15G173 Air Inlet Fitting
Air Adjustment Valve
23
15G175 Trigger
24†
Gasket
25†
Trigger Pin
26*
Retaining Ring
27†
Gun Wrench
28†
Brush
29
30
15G147 Fluid Filter
15G177 Cup
* Parts included in Repair Kit 249511.
† Parts not available.
Qty.
1
1
1
1
2
1
1
1
1
1
1
1
1
1
311104B 9
Graco Standard Warranty
Graco warrants all equipment referenced in this document which is manufactured by Graco and bearing its name to be free from defects in material and workmanship on the date of sale to the original purchaser for use. With the exception of any special, extended, or limited warranty published by Graco, Graco will, for a period of twelve months from the date of sale, repair or replace any part of the equipment determined by
Graco to be defective. This warranty applies only when the equipment is installed, operated and maintained in accordance with Graco’s written recommendations.
This warranty does not cover, and Graco shall not be liable for general wear and tear, or any malfunction, damage or wear caused by faulty installation, misapplication, abrasion, corrosion, inadequate or improper maintenance, negligence, accident, tampering, or substitution of non-Graco component parts. Nor shall Graco be liable for malfunction, damage or wear caused by the incompatibility of Graco equipment with structures, accessories, equipment or materials not supplied by Graco, or the improper design, manufacture, installation, operation or maintenance of structures, accessories, equipment or materials not supplied by Graco.
This warranty is conditioned upon the prepaid return of the equipment claimed to be defective to an authorized Graco distributor for verification of the claimed defect. If the claimed defect is verified, Graco will repair or replace free of charge any defective parts. The equipment will be returned to the original purchaser transportation prepaid. If inspection of the equipment does not disclose any defect in material or workmanship, repairs will be made at a reasonable charge, which charges may include the costs of parts, labor, and transportation.
THIS WARRANTY IS EXCLUSIVE, AND IS IN LIEU OF ANY OTHER WARRANTIES, EXPRESS OR IMPLIED, INCLUDING BUT NOT LIMITED
TO WARRANTY OF MERCHANTABILITY OR WARRANTY OF FITNESS FOR A PARTICULAR PURPOSE .
Graco’s sole obligation and buyer’s sole remedy for any breach of warranty shall be as set forth above. The buyer agrees that no other remedy
(including, but not limited to, incidental or consequential damages for lost profits, lost sales, injury to person or property, or any other incidental or consequential loss) shall be available. Any action for breach of warranty must be brought within two (2) years of the date of sale.
GRACO MAKES NO WARRANTY, AND DISCLAIMS ALL IMPLIED WARRANTIES OF MERCHANTABILITY AND FITNESS FOR A
PARTICULAR PURPOSE, IN CONNECTION WITH ACCESSORIES, EQUIPMENT, MATERIALS OR COMPONENTS SOLD BUT NOT
MANUFACTURED BY GRACO . These items sold, but not manufactured by Graco (such as electric motors, switches, hose, etc.), are subject to the warranty, if any, of their manufacturer. Graco will provide purchaser with reasonable assistance in making any claim for breach of these warranties.
In no event will Graco be liable for indirect, incidental, special or consequential damages resulting from Graco supplying equipment hereunder, or the furnishing, performance, or use of any products or other goods sold hereto, whether due to a breach of contract, breach of warranty, the negligence of Graco, or otherwise.
FOR GRACO CANADA CUSTOMERS
The Parties acknowledge that they have required that the present document, as well as all documents, notices and legal proceedings entered into, given or instituted pursuant hereto or relating directly or indirectly hereto, be drawn up in English. Les parties reconnaissent avoir convenu que la rédaction du présente document sera en Anglais, ainsi que tous documents, avis et procédures judiciaires exécutés, donnés ou intentés, à la suite de ou en rapport, directement ou indirectement, avec les procédures concernées.
Graco Information
TO PLACE AN ORDER, contact your Graco distributor or call to identify the nearest distributor.
Phone: 612-623-6921 or Toll Free: 1-800-328-0211, Fax: 612-378-3505
All written and visual data contained in this document reflects the latest product information available at the time of publication.
Graco reserves the right to make changes at any time without notice.
MM 311104
Graco Headquarters: Minneapolis
International Offices: Belgium, China, Japan, Korea
GRACO INC. P.O. BOX 1441 MINNEAPOLIS, MN 55440-1441 www.graco.com
Printed in USA 311104B
1/2006
advertisement
* Your assessment is very important for improving the workof artificial intelligence, which forms the content of this project
Related manuals
advertisement
Table of contents
- 2 Warnings
- 3 Setup
- 5 Troubleshooting
- 6 Service
- 7 Technical Data
- 8 Parts
- 10 Graco Standard Warranty
- 10 Graco Information