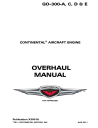
advertisement
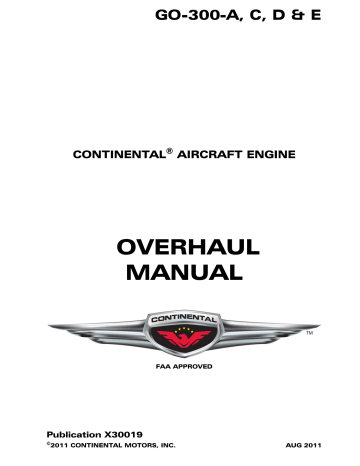
GO-300-A, C, D & E
CONTINENTAL
®
AIRCRAFT ENGINE
OVERHAUL
MANUAL
FAA APPROVED
Publication X30019
© 2011 CONTINENTAL MOTORS, INC.
AUG 2011
Supersedure Notice
This manual revision replaces the front cover and list of effective pages for Publication Part No. X30019, dated
August 1981. Previous editions are obsolete upon release of this manual.
Effective Changes for this Manual
0 .................August 1981
1 ............ 31 August 2011
List of Effective Pages
Document Title: GO-300 Series Engine Overhaul Manual
Publication Number: X30019
Page Change Page Change Page
Cover............................ 1
A................................... 1 i Blank added ............... 1 ii thru vi.........................0
1 thru 67 ....................... 0
Initial Publication Date: August 1981
Change Page Change
A
Published and printed in the U.S.A. by Continental Motors, Inc.
Available exclusively from the publisher: P.O. Box 90, Mobile, AL 36601
Copyright © 2011 Continental Motors, Inc. All rights reserved. This material may not be reprinted, republished, broadcast, or otherwise altered without the publisher's written permission. This manual is provided without express, statutory, or implied warranties. The publisher will not be held liable for any damages caused by or alleged to be caused by use, misuse, abuse, or misinterpretation of the contents. Content is subject to change without notice. Other products and companies mentioned herein may be trademarks of the respective owners.
GO-300 Series Engine Overhaul Manual
31 August 2011
INTENTIONALLY
LEFT
BLANK
TABLE OF CONTENTS
Section
I
n
III
IV
V
VI vn
VIll
IX
X
XI
XII
XllI
XIV
XV
Introduction • . • . • • • . • • •
Specifications, Limits and Charts
General Description • . • . . . • .
Unpacking and Preparation for Service, storage or Shipment
Installation in Aircraft and Removal
Maintenance Instructions
Disassembly
Cleaning Parts • • • • •
Inspection . . • • • .
Repair and Replacement
Assembly of Subassemblies
Final Assembly • • • • • . •
Repair and Testing of Accessories •
Testing After Overhaul
Table of Limits • • . . • . • • . •
Page
49
53
55
59
8
9
12
21
32
34
39
46
I
2
4 ii
LIST OF TABLES
Table
I n
III
IV
V
VI
VII
VIll
IX
X
XI
Xll
XllI
XIV
XV
XVI
XVII
XVIII
XIX
Purchased Accessories
Ignition System Details
Characteristics and Dimensions •
Fuel System Details
Temperature Limits • •
Pressure Limits • • • • •
Oil Viscosity Grades • •
Trouble Shooting Chart
Magnaflux Inspection Thl.ta
Critical New Parts Dimensions
Stud Identification •• stud Setting Heights • • • • • •
Test Operating Limits
Top or Minor Overhaul Test Run
Major Overhaul Test Run. • • • • •
Table of Limits . • • • • • • • .
Table of Tightening Torques • • • •
General Use - Tightening Torques
Pipe Plugs • • • • • • • • • • • . •
Page
40
56
57
57
58
62
63
63
3
3
15
34
2
2
2
3
3
36
40
LIST OF ILLUSTRATIONS
Figure
1
18
19
20
21
14
15
16
17
8
9
10
11
12
13
4
5
2
3
6
7
22
23
24
25
26
27
28
Three-Quarter Right Front View of Model GO-300-A Aircraft Engine
Three-Quarter Left Rear View of Model GO-300-A Aircraft Engine
Gear Train Diagram • . • • • • .
Section through Hydraulic Tappet
Installation Drawing starter and Adapter
Ignition System and Accessories
Induction System & Oil Sump •
Cylinder & Piston
Propeller Reduction Gear Unit •
Crankcase
Left Crankcase Mounted on Engine stand
Crankcase Cover • • . • • • . •
Cylinder Dimensional Drawing
Installing Helical Coil Inserts
Rocker Arm Bearing Dimensions
Measuring of Dampener Bushing
Connecting Rod and Bushing Dimensions starter Adapter Bearing Installer •
Installing starter Adapter Bearing
Installation of Valve Spring Locks
Installing Propeller Shaft Oil Seal
Installing Propeller Shaft Oil Seal Spring
Alignment of Timing Marks ••
Limits and Lubrication Chart
Limits and Lubrication Chart
Limits and Lubrication Chart
Limits and Lubrication Chart •
Page v
42
. . . . . .
42
43
27
28
29
30
38
41
43
44
46
64
65
66
67
48
48
50
10
22
23
24
25 vi
6
7 iii
iv
DEFINITIONS AND ABBREVIATIONS
Term
A.B.C. :
Approx. :
A.T.C. :
Bar. :
B.B.C. :
B.H.P. :
B.T.C. :
C.A.R. : c.f.m. :
C.G. :
OF:
F.A.A.
Fig. :
Front: ft. :
G.P.M. :
H20 :
Hg. :
I.D. : in. (It) :
Hex. : hr. :
Left Side:
Lbs. :
Lock wire:
Man. :
Min. :
30' :
N.P.T. :
N.C. :
N.F. :
O.D. :
Press.: p.s.i. :
Rear:
Right Side:
R.P.M. :
Std. :
T.D.C. :
Temp. :
Torque:
Explanation
After Bottom Center
Approximate ly
After Top Center
Barometric
Before Bottom Center
Brake Horsepower
Before Top Center
Civil Air Regulations
Cubic feet per minute
Center of Gravity
Diameter
Degrees of Angle
Degrees Fahrenheit
Federal Aviation Administration
Figure (Illustration)
Propeller End
Foot or feet
Gallons per minute
Water
Mercury
Inside Diameter
Inches
Hexagon
Hour
Side on which No.' s 2, 4 and 6 cylinders are located
Pounds
Soft steel wire used to safety connections, etc.
Manifold or manometer
Minimum
Thirty minutes of angle (60' equal one degree)
National pipe thread 1tapered)
National Coarse (thread)
National Fine (thread)
Outside Diameter
Pressure
Pounds per square inch
Accessory end of engine
Side on which No.' s 1, 3 and 5 cylinders are located
Revolutions per minute
Standard
Top dead center
Temperature
Force x lever arm (125 ft. -lbs. torque = 125 lbs. force applied one ft. from bolt center or 62-1/2 lbs. applied
2 ft. from center)
13
14
11
12
1. No. 1 cylinder upper ignition cable
2. No. 3 cylinder
3. No. 3 cylinder upper ignition cable
4. No. 5 cylinder upper ignition cable
5. No. 5 cylinder
6. Oil cooler
7. Propeller reduction unit housing
8. Propeller shaft bearing cage
9. Propeller shaft oil seal
10. Propeller shaft
11. Vernatherm valve
12. Crankshaft cover
13. Accessory drive front cage
14. Manifold riser
15. Vacuum pump drive cover
16. Right front mount bracket
17. No. 5 cylinder inta"ke pipe
18. No. 5 cylinder lower ignition cable
19. Carburetor
20. Throttle lever
21. No. 3 cylinder intake pipe
22. No. 3 cylinder lower ignition cable
23. Right rear mount bracket
24. No. 1 cylinder lower ignition cable
25. No. 1 cylinder intake pipe
26. No. 1 cylinder
Figure 1. Three-Quarter Right Front View of Model GO-300-A Aircraft Engine v
vi
1. No. 6 cylinder upper ignition cable
2. No. 4 cylinder upper ignition cable
3. Crankcase breather
4. No. 2 cylinder upper ignition cable
5. Two-wire ignition cable bracket
6. Lifting eye
7. Oil filler cap
8. Oil filler neck
9. Three-wire ignition cable bracket
10. Nut, lockwasher and washer
11. Nut, lockwasher and washer
12. Starter
13. Three-wire ignition cable bracket
14. Nut, lockwasher and washer
15. Left magneto
16. Wire harness band
17. Right magneto
18. Magneto switch wire terminals
19. Nut, lockwasher and washer
20. Nut, lockwasher and washer
21. Nut and washer
22. Generator
23. Bolt, lockwasher and washer
24. Generator blast tube
25. Oil screen
26. Oil screen
27. Balance tube
28. Mixture control lever
29. Crankcase cover
30. Bolt, lockwasher and washer
31. Oil sump drain plug
32. Oil gauge rod
33. Oil sump
34. Left rear mount bracket
35. No. 2 cylinder intake pipe
36. Two-wire ignition cable bracket
37. No. 2 cylinder lower ignition cable
38. No. 2 cylinder
39. No. 4 cylinder lower ignition cable
40. No. 4 cylinder intake pipe
41. No. 6 cylinder lower ignition cable
42. No. 4 cylinder
43. No. 6 cylinder intake pipe
44. No. 6 cylinder
Figure 2. Three-Quarter Left Rear View of Model GO-300-A Aircraft Engine
SECTION
INTRODUCTION
1-1. SCOPE.
1-2. Material in this publication is applicable to model
GO-300-A,B,C,D and E aircraft engines. A brief explanation of construction features and functional systems is included. This information is supplemented by the Limits and Lubrication Chart, which is composed of sectional drawings printed on the final pages. Tables of specifications, performance characteristics, operation limitations and performance charts are included in Section II. Dimensional specifications in the Table of Limits govern the permissible tight fits of "permanently" assembled parts and clearances of running parts as a guide for the determination of service-ability at overhaul.
Other sections are devoted to instructions for operation, inspection, routine maintenance, trouble shooting and overhaul procedure. Description, text, specifications and part numbers mentioned herein are correct as of the date of publication;however, changes may be made in specifications and/or part numbers.
Therefore, all replacement parts should be ordered in accordance with information contained in the Spare
Parts Catalog, Form X-30020, and operation limitations herein should not be construed to authorize any departure from limits published in the applicable
F .A.A. Type Specification. If more detailed information is necessary concerning any of the purchased accessories listed in Table I, it is requested that inquiries for such be made of the manufacturer or agency whose name and address is listed immediately behind the accessory in Table I.
1-3. AVAILABILITY.
1-4. Further copies of this and other Continental aircraft engine service publications may be purchased through Continental Approved Distributors and Parts Dealers of aircraft engine parts. It is requested that all orders fMsuch publications be placed with these facilities when not immediately available from their stock.
1-5. SERVICE BULLETINS.
1-6. Important changes in part numbers, interchangeability of parts, urgent inspections, mandatory replacements and modernization information are among the subjects of limited interest and duration covered by factory Service Bulletins, which are distributed to all Approved Distributors of aircraft engines and parts and are available for study at their offices.
Service Bulletins of interest to aircraft owners, operators and maintenance personnel may be obtained by direct mail on an annual subscription basis. The charge for this service covers only postage and handling.
Subscriptions are received by the factory Publications
Department, to whom inquiries on this subject may be addressed.
1-7. SERVICE REPORTS AND INQUIRIES.
I-S. It is the policy of Teledyne Continental Motors to handle all reports of service difficulty and requests for information through Approved Distributors. These facilities are constantly in touch with operation and repair. You will find them more than willing to help solve your maintenance problems and well equipped with experience and facilities to perform any necessary maintenance work on Continental aircraft engines. There is an Approved Distributor at every major airport.
FEATURE
Starter
GO-300-A
Manual engagement
COMPARATIVE LIST OF MODEL DIFFERENCES
GO-300-B
Manual engagement
GO-300-C
Manual engagement
GO-300-D
Right angle automatic engagement
Pressed in Crankcase
Breather
Flange mounted
Vacuum Pump Lower right
Drive Side of reduchon housing
Propeller
Governor Drive
None
Flange mounted
Lower right side of reduction housing
Upper rear of reduction housing
Pressed in
Lower right side of reduction housing
None
Rear of starter adapter
None
GO-300-E
Right angle automatic engagement
Pressed in
Rear of starter adapter
Upper rear of reduction housing
1
Accessory
Carburetor
Magneto
Magneto
(Optional)
Spark Plug
Starter
Starter
Generator
Regulator
Oil Cooler
SECTION II
SPECIFICATIONS, LIMITS AND CHARTS
TABLE I PURCHASED ACCESSORIES
Manufacturer
Marvel-Schebler Div., Borg Warner Corp.
Slick Magneto Co. , Rockford Illinois
Bendix
Model or
Serial No.
MA-4-5
667
S6RN-21
AC Spark Plug Company
Delco-Remy Div., General Motors Corp.
Delco-Remy Div., General Motors Corp.
Delco-Remy Div., General Motors Corp.
Delco-Remy Div., General Motors Corp.
Harrison Radiator Div.,General Motors Corp.
SR-87
1109677
1109514
1101910
1118736
8531835
TABLE II IGNITION SYSTEM DETAILS
Feature
Left magneto fires lower right and upper left side plugs
Right magneto fires upper right and lower left side plugs
Firing order (cylinder numbers)
Spark plug gap settings SR-87
Permissible R.P.M. spread when switched from
"Both" to either "Left" or "Right" magneto
Value
28
0
B.T.C.
28
0
B.T.C.
1,4,5,2,3,6
.018 - ,022 in.
100 R.P.M.
TABLE III CHARACTERISTICS AND DIMENSIONS
------------~~--------------------
Dimension Value
-------------------------------------
Dimension Value
2
Piston strokes per cycle
Number of cylinders
Cylinder bore (in.)
Piston stroke (in.)
Compression ratio
Total displacement (in.)
Propeller gear reduction
Over-all length (in.) A, B & C
4
6
4.0625
3.875
7.3:1
301.37
0.75:1
39.12
Over-all length (in. ) D, E
Over-all width (in.)
Over-all height (in.) GO-300-A,-B
Over-all height (in.) GO-300-C, -D,-E
Number of mounting brackets
Rated maximum crankshaft R.P.M.
Rated maximum B.H.P.
Total dry weight (lbs.)
39.19
31.50
27.62
26.56
4
3200
175
311. 92
12
1
1
1
1
1
2
2
Oty
1
TABLE IV FUEL SYSTEM DETAILS
Feature
Minimum fuel octane rating
Fuel pressure required (psi)
Fuel inlet to carburetor (N.P.T.)
Venturi diameter
Value
80/87
0.5 - 6.0
1/4 in.
1-13/16 in.
TABLE V TEMPERATURE LIMITS
Indicated Condition
Oil temperature at take-off . . . . . . . . • . . . .
Oil temperature in flight . . . . . . . . . . . . . . . . . . . . • . • . . . .
Desired oil temperature . . . . . . . . . . . • . • . . . . . . . . . . . . .
Cylinder head temperature (downstream spark plug gasket) • . . .
Cylinder base temperature (bayonet thermocouple)* . . . • . • . .
Minimum
Magneto temperature (at coil hold-down screw) A, B, C & D.
Magneto temperature (at coil hold-down screw) E • • • • • • •
Maximum
200 0 F
*
Installed in tapped hole in bottom of cylinder head. Applicable only with downdraft cooling system.
TABLE VI PRESSURE LIMITS
Indication
Oil pressure (idling)
Oil pressure (in flight)
Minimum Maximum
5 p.s.i.
30 p.s.i. 60 p.s.i.
TABLE VII
Above 40°F
OIL VISCOSITY GRADES
Ambient Air Temperature
Below 40 0 F
S.A.E. Grade
30
50
Ambient air temperature is the controlling factor on all engines having Vernatherm valves installed.
2-1. OIL SUPPLY AND MEASUREMENTS.
2-2. The capacity of the oil sump is 10 U.S. quarts.
The minimum quantity of oil in the sump necessary to adequately lubricate the engine at 20 0 nose up to 15 0 nose down attitudes of flight is 7 U.S. quarts. The oil filler cap is marked "OIL 10 QUARTS". It is attached over the oil filler neck which is located on the upper left side of the crankcase cover. The oil sump is equipped with an oil level gauge which is graduated in
2-quart increments and stamped with the numerals 4 through 10. The oil gauge is located on the crankcase left side between No. 2 cylinder and the crankcase cover.
2-3. OIL FLOW, HEAT REJECTIONANDCONSUMP-
TION.
2-4. When operated on a rigid test stand, at normal rated power and speed, with an oil inlet temperature of 220 0 F (with S. A. E. 50 oil) and oil pressure of 35 p. s. i. (plus or minus 2 p. s. i.) oil flow shall not exceed 50 lbs. per minute. Heat rejection to the oil shall not exceed 280 BTU's per minute at 3200 rpm.
Oil consumption shall not exceed 2.75 lbs. per hour at 3200 rpm.
3
SECTION III
GENERAL DESCRIPTION
3-1. CONSTRUCTION.
3-2. GENERAL. The arrangement and appearance of engine parts and components are illustrated in figures 1 and 2. Additional information will be found in the installation drawing andin the limits and lubrication charts.
3-3. CRANKCASE. Two aluminum alloy castings are joined along the vertical center plane to form the complete crankcase, The individual castings (with studs and inserts) will be called "the left crankcase" and
"the right crankcase" throughout this publication.
The two crankcase halves are aligned one to the other by the use of eight dowel type through bolts. Four of the bolts are above the crankshaft centerline and four below.
3-4. Bosses molded in the crankcase castings are line bored, in the assembled castings, to form bearings for the camshaft and seats for precision, steel backed, lead alloy lined crankshaft main bearing inserts. Guides are bored through lateral bosses for the hydraulic valve lifters,
3-5. Cylinder mounting pads on the left crankcase are farther forward than corresponding pads on the right crankcase to permit each connecting rod to work on a separate crankpin, Each pad has two holes for crankcase through bolts and four studs for the attachment of cylinder flanges. Two engine mount brackets are attached to studded pads on the side of each crankcase. (See 16 and 23, figure 1. )
3 -6, CRANKSHAFT. The six-throw steel alloy forging is machined all over excepting some surfaces of the crankcheeks. Main journals and crankpins are nitrided after grinding. The crankcheeks between
No's. 1 and 2, 3 and 4, 5 and 6 crankpins have side blades, each equipped with two hardened steel bushings for steel pins on which one of the pendulum counterweights is mounted. Oscillation of the counterweights on their pins damp out crankshaft torsional vibration at the gear end. The rear end of the crankshaft is tapped and doweled to provide features for the attachment of the crankshaft gear. The front end of the crankshaft has an internal spline which receives and drives the reduction unit quill shaft.
3-7. The crankshaft gear is heated prior to installation to obtain a shrunk fit with the crankshaft. The gear is driven by a pilot dowel of uniform diameter,
The gear is retained by four
1/
4-inch retaining bolts.
3-8. CONNECTING RODS. Automotive-type connecting rods have split bronze piston pin bushings and two identical precision inserts (of the same type as main bearings) at the crankpin end. Weight variation of rods in any engine set is limited to YS ounce in opposite bays.
4
3-9. CAMSHAFT. A steel alloy forging is machined on four journals, nine cam lobes and the gear mount flange at the rear end. The lobes and journals are ground and hardened. A groove around the front journal passes engine oil from the right crankcase cross passage to the left case passage. The camshaft gear is attached by four unequally spaced bolts to locate its timing mark in relation to the lobes. The male half drive coupling at the front of the shaft mates with and drives the front accessory drive gear on
Model GO-300-A, Band C engines.
3-10. PROPELLER REDUCTION HOUSING. The aluminum alloy propeller reduction housing mounted on the front of the engine contains front support bearing for the propeller shaft drive gear, the accessory drive gear, the accessory drive gear assembly, the propeller shaft rear bearing and the Vernatherm valve. The GO-300-B and E contain governor drive gears. Mounted on the top of the housing is the crankcase breather. For Model GO-300-A and B, the breather assembly is attached to a studded pad by four sets of attaching parts. For all other models, the breather is pressed into the housing. Mounted on the right side of the housing is the oil cooler and on the upper front is the propeller shaft cage assembly. The cage assembly contains the propeller shaft and its bearings. A rubber composition oil seal, held tightly between the cage halves, is sealed to the shaft by a helical spring inside the seal's cavity. A felt dust shield is cemented to the front of the oil seal to prevent abrasive materials working under the seal lip and scoring the shaft,
3-11. PISTONS, PINSANDRINGS. Pistons are heattreated aluminum alloy casting with cam ground skirts.
The top ring groove is fitted with a chrome-faced cast iron ring. The second ring groove is fitted with a plain cast iron ring, while the third and fourth grooves have tin-plated cast iron rings. The fourth, or oil control, ring is a slotted type. Oil drain holes are drilled through the piston just below and on a 30° angle to the third compreSSion ring. The full-floating piston pin is a case hardened, seamless, alloy steel tube with pressed in aluminum end plugs. The plugs are machine finished after assembly and the pin is ground to final size and polished.
3-12. CYLINDERS. Heat-treated aluminum alloy cylinder heads are screwed and shrunk onto the forged steel barrels. Cooling fins on both the cylinder head and barrel provide ample heat dissipating surface with a minimum reSistance to air flow. Cylinder bores are ground to a specific surface finish. Helical coil thread inserts are installed in the spark plug holes.
Rocker boxes are integrally cast in the cylinder head and are provided with lightweight cadmium-plated covers. Both intake and exhaust ports are on the downward side when the cylinder is installed.
3 -13. OIL SUMP. The oil sump is an aluminum alloy casting. An integral intake manifold riser was cast into the sump on the earlier models. This manufacturing process has been revised. On current sump assemblies, the riser is now a sheet metal tube, permanently sealedin place by beaded ends. A machined and studded pad at the front of the sump provides a mounting surface for the manifold riser. A similar pad located on the sump, lower rear, provides for the attachment of the updraft carburetor. The rear surface of the sump is machined, drilled and tapped for crankcase cover attaching parts. The current sump assembly utilizes a removable oil suction tube in lieu of the cored, integral suction passage, used in earlier production sumps.
3-14. The magnesium alloy crankcase cover casting at the rear of the engine houses the oil pump, suction and pressure oil screens, pressure relief valve, camshaft and crankshaft gears. The oil filler neck is on the upper left, the oil screen's lower center and the relief valve center right. studded mount pads are provided on the cover's rear surface for two magnetos, starter, generator and tachometer drive housing. The crankcase cover extends over the rear end of the sump and is attached to it by bolts, lockwashers and washers.
The crankcase cover is attached to the crankcase by studs, projecting from the crankcase, washers, lockwashers and nuts. A gasket seals the joint at the mating surfaces of the crankcase, cover and sump.
3-15. FUNCTIONAL SYSTEMS.
3-16. GEAR TRAIN. (See Figure 3.) The crankshaft gear, which is turned in a counterclockwise direction by the crankshaft, turns the camshaft gear clockwise.
The squared end of the oil pump and tachometer drive shaft is inserted in the square center hole of the camshaft gear and is turned in a clockwise direction. The magneto drive gears are driven in a counterclockwise direction by the camshaft gear. The generator drive gear is driven in a clockwise direction by the inner ring of gear teeth of the camshaft gear. The starter pinion rotates clockwise to turn the crankshaft gear counterclockwise. The propeller shaft drive gear is joined to, and driven by, the crankshaft through a quill shaft. The propeller shaft drive gear rotating in a counterclockwise direction drives the propeller shaftgear and shaft in a clockwise direction.
3-17. LUBRICATION SYSTEM. From the lowest point in the sump, oil enters the lubrication system through a suction passage, or tube, to the oil suction screen in the crankcase cover. From the oil screen cavity a cored passage leads to the suction side of the oil pump. From the pressure side of the pump a cored passage conducts the oil to another cored passage in the sump which in turn directs the pressurized oil to the right crankcase main gallery. The main gallery is a cored hole extending the full length of the crankcase. The rear exit of the gallery is aligned with a passage to the oil pressure relief valve. The front exit of the gallery aligns with the entrance to a passage in the reduction unit housing which directs the oil to the inlet side of the oil cooler.
3-18. The oil cooler mount pad, on the reduction unit housing, is formed so as to provide separate inlet and outlet compartments when the cooler is installed. Oil flows from the inlet, or lower, compartment into the bottom of the cooler, circulates upward through the cooler and empties into the outlet, or upper, compartment. A vertical passage directs the oil from the outlet compartment down to and around the Vernatherm valve. The temperature of the oil affects the length of the Vernatherm valve. As the temperature of the oil lowers, the length of the valve decreases, thus opening a direct oil passage from the oil cooler inlet compartment to the Vernatherm valve cavity and in so dOing, bypasses the oil cooler. As oil temperature rises, the valve expands in length, thus closing the direct passage, and routing the oil through the cooler.
3-19. From the Vernatherm cavity, oil passages direct the oil to the bearings of the reduction unit housing. The main supply of lubricating oil is conducted through passages of the housing to a hole at the right rear side which aligns with a Similar hole in the right crankcase. As the oil re-enters the right crankcase it is directed to the front camshaft bearing.
The front camshaft bearing journal is grooved to permit the oil to pass freely to a passage in the left crankcase. The passage in the left crankcase directs the oil from the camshaft bearing to the left crankcase main gallery.
3-20. From the left crankcase gallery oil is directed to the intermediate and rear camshaft bearings and to the crankshaft main bearings. Oil is conducted from the crankshaft main bearings to the connecting rod bearings through steel tubes which are permanently installed in the crankshaft.
3-21. VALVE MECHANISM. (See Figure 4.) Oil is fed to the hydraulic valve lifters through passages drilled from the lifter guides to the main oil galleries.
The lifters are composed of four main parts; the cup, cylinder, piston and body. The piston and cylinder are not interchangeable. The lifters are automatically adjusted to function properly with valve lash ranging from .030 inch to . 110 inch between the valve stem end and rocker arm with the lifter fully deflated. Oil under pressure from the lubricating system of the engine is supplied to the hydraulic lifter through hole
(H) to supply chamber (J).
3-22. With face oflifter on the base circle of the cam, and the engine valve seated as shown in figure 4, the light plunger spring (K) lifts the hydraulic plunger so that its outer end contacts pushrod, taking up the clearance at this point and all along the valve train, giving zero lash. As the plunger increasing the vol u m e in the pressure adjusting chamber (L), the ball check valve (D) moves off its seat and oil from the supply chamber fills chamber (L).
(C) moves outward,
(J)
(C) flows in and
5
6
1. Crankshaft gear, rotates at engine speed counterclockwise
2. Camshaft gear, rotates at 1/2 engine speed clockwise
3. Magneto drive gears, rotates at 1-1/2 engine speed counterclockwise
4. Oil pump drive gear, rotates at 1/2 engine speed clockwise
5. Oil pump driven gear, rotates at 1/2 engine speed counterclockwise
6. Generator drive gear, rotates at 2.035:1 engine speed clockwise
7. Starter gear, rotates at 5.111 engine speed clockwise
Figure 3. Gear Train Diagram
L
•
Figure 4. Section through Hydraulic Tappet
3-23. As the camshaft rotates, the cam pushes the lifters body outward, tending to decrease the volume of chamber (L) and forcing the ball check onto its seat.
Further rotation of the camshaft moves the lifter body (A) outward and the confined body of oil in chamber (L) acts as a member in the valve operating mechanism, the engine valve being lifted on a column of oil. So long as the engine valve is off its seat, the load is carried by this column of oil.
3-24. During the interval when the engine valve is off its seat, a pre-determined slight leakage occurs between plunger and cylinder bore, which is necessary to compensate for any expansion or contraction occurring in the valve train. Immediately after the engine valve closes, the amount of oil required to refill the adjusting chamber (L) flows in from the supply chamber
(J), thus establishing the proper length of oil column to maintain zero lash during the next cycle.
3-25. The basic principle ofthe hydraulic lifter is that it provides, between the cam and the pushrod, a column of oil which carries the load while the engine valve is off its seat, and the length of which is automatically adjusted so that each camshaft cycle gives zero lash.
3-26. The pushrod assemblies are made up of lightweight steel tubes with pressed-in ball ends. The ball ends are drilled to provide an oil passage from the valve lifters to the rocker arm. The rocker arms are drilled to provide an oil passage from the pushrod end to the rocker arm bearings. Oil is sprayed from the rocker arm to lubricate the valve springs and valve guides. Oil is returned to the crankcase by flowing through the pushrod housings.
3-27. IGNITION SYSTEM. High voltage current is generated and distributed to the upper spark plugs of the right side cylinders and lower spark plugs of the left side cylinders by a magneto mounted on the right side of the crankcase cover. An identical magneto mounted on the left side of the crankcase cover produces the current for the upper spark plugs of the left side cylinders and lower spark plugs of the right side cylinders. The high tension cables pass through braided, flexible, shielded conduit assemblies which are connected to the magneto by coupling nuts and to the spark plugs by elbows. The magnetos are driven through impluse couplings which incorporate springs and counterweighted latches. At cranking speed, the latches engage magneto body stops to retard the rotors and ignition spark. Retarding the magneto rotors at cranking speed serves to retard ignition spark until the piston reaches top center at the beginning of the power stroke and to attain full secondary coil voltage as the rotor is spun rapidly through the breaker opening position at which the spark occurs. As engine speed increases, centrifugal force disengages the latches, and the magnetos are driven at full advance.
7
SECTION IV
UNPACKING AND PREPARATION FOR SERVICE, STORAGE OR SHIPMENT
4-1. UNPACKING.
4-2. Detach the assembly of shipping crate top and side panels from the crate base by removing the nails around the bottom and side edges; then lift off the cover assembly. Engines received from the factory are covered by a moisture proof paper shroud. Lift off the shroud and remove from the crate base the packages containing the spark plugs. Attach a chain hOist to the engine lifting eye, located at the top crankcase flange, before loosening the engine mount bracket attaching bolts. Take up slack in the holst; then remove the attaching parts. Lift the engine straight up until clear of the crate. It is advisable to support the engine on an assembly stand while removing packing materials and installing accessories.
4-3. Remove dehydrator plugs from the upper spark plug holes. If the engine is to be installed at once, turn the crankshaft as necessary, and inspect the interior of each cylinder with the aid of a flashlight.
If a pool of oil is standing in any cylinder it must be drained before engine is installed. If compression can.not be built up in any cylinder by turning the crankshaft while the upper spark plug hole is plugged, remove the valve rocker cover from that cylinder, and check valve action. If a valve stem is sticking in its guide, apply castor oil or engine lubrication oil thinned with gasoline while the crankshaft is rotated and until the valve operates freely. Use a new gasket when replacing the valve rocker cover.
4-4. Remove the plastic caps from the breather elbow and the generator blast tube connector. Remove the bolts, spacers and cover from each cylinder exhaust port flange. Remove plastic protectors from spark plug cable elbows. Remove any moisture proof adhesive tape installed to cover vent holes during shipment.
4-5. PREPARATION FOR SERVICE.
4-6. The corrosion-preventive oil fed into the lubricating system and sprayed into cylinders before shipment of a new engine will mix with normal engine lubricating oil and will do no harm; hence, it does not need to be flushed out.
4-7. Install spark plugs and tighten to specified torque. Insert the cable terminals and screw on the elbow hex coupling nuts.
Tighten coupling nuts only moderately.
4-8. Install the proper type of washer thermocouple under the lower spark plug of the cylinder specified by the aircraft manufacturer.
4-9. To install the oil gauge pressure line fitting,
8 remove the 1/8-in. pipe plug located in the crankcase between No.2 and 4 cylinders. Coat the pipe threads of the fitting with a thin film of Ledplate #250 before installing.
4-10. Install the proper connector fitting for the intake manifold pressure gauge line in the 1/8-inch pipe tapped hole in the manifold riser.
4-11. PREPARATION FOR STORAGE.
4-12. If an engine which has been in operation is to be stored much longer than a week under normal climatic conditions, and if periodiC running to circulate oil is not carried out, it is advisable to prepare it for storag.e in the following manner: a. Operate the engine until the oil temperature reaches the normal range. Drain the oil sump as completely as possible; then replace the drain plug. b. Fill the oil sump to the full (F) mark on the level gauge with a corrosion-preventive oil which will mix with normal oil and which is suitable as a lubricant.
This oil must be preheated to 225°F. (See Service Bulletin
M81-3 Rev 1.) c. Run the engine at least five minutes at a speed between 1200 and 1500 R.P.M. with the oil temperature between 215 and 225 0 F. The cylinder head temperature must not exceed 450 0 F. d. Inject the same type of corrosion-preventive oil used in the lubricating system into the carburetor intake, while the engine is running, at a rate of 1/2 gallon per minute until smoke comes from the exhaust pipe; then increase the spray until it stops the engine. e. If possible, spray the corrosion-preventive oil into the cylinder exhaust ports. f. Do not turn the crankshaft at any time after completion of the preceding steps. g. Remove all spark plugs, and spray corrosionpreventive oil, without air, into the upper spark plug holes, then into the lower spark plug holes to assure complete coverage of the interior cylinder surfaces.
This oil should be at a temperature of 150 to 180 0 F. h. Replace the lower spark plugs, or install solid plugs in their places. Install dehydrator plugs in the upper spark plug holes.
t.
Install plastic shipping plugs or other suitable covers on the detached spark plug cable terminals.
Cover all engine and accessory vents and other openings, including the crankcase breather, with nonhygroscopic tape or other vaporproof material. j. Drain the corrosion-preventive oil from the sump and replace the drain plug. k. Post a conspicuous warning regarding drainage of the oil supply and other measures which must be taken before operation of the engine. If a propeller is installed, attach a warning placard against movement.
SECTION V
INSTALLATION IN AIRCRAFT AND REMOVAL
5-1. ACCESSORIES.
5-2. OPTIONAL ACCESSORIES. If a hydraulic pump or a vacuum pump is to be installed on a GO-300-A,
-B or -C engines, remove the pad cover from lower right side of reduction unit housing. If the pump is to be installed on GO-300-D or -E engine, remove the pad cover from the rear of the starter adapter.
(See figure 6.) Install a new gasket and attach the pump with plain washers, new lock washers and the original cover attaching nuts. If the aircraft has an oil dilution valve, install the fitting in place of the plug immediately above the pressure oil screen in the crankcase cover. For GO-300- Band -
E engines remove the governor mount pad cover and install the propeller governor. The governor pad is located on the upper right rear of the reduction unit housing. Install a new gasket and attach the governor with plain washers, new lock washers and plain nuts.
5-3. INSTALLATION.
5-4. DIMENSIONS. Principal dimensions of the engine which affect mounting and locations of control and instrument connections are shown in the installation drawing (Figure 5).
5-5. PRECAUTION. The engine assumes a slightly tail heavy attitude when suspended by its lifting eye.
It may be necessary to hold down on the front end in order to align the engine mount brackets with attaching brackets of the aircraft. Make sure that the mount bushings all contact the aircraft brackets uniformly and seat fully on the engine mount bracket when the mounting bolts are installed. Tighten the mounting bolts to the torque specified by the aircraft manufacturer.
5-6. CONTROL CONNECTIONS. The magneto switch wires should be installed first. Before installing the switch wire terminals in the magneto sockets, check each with a buzzer and battery for continuity with the switch in "LEFT" and "RIGHT" positions. Remember that the left magneto should be grounded through the switch when the switch is turned to "RIGHT" pOSition and the right magneto should be grounded with the switch in the "LEFT" position. This is important when shooting ignition troubles. Connect the wires to the magnetos.
5-7. Connect the throttle and mixture controls where indicated on installation drawing and check each for full range of operation. For GO-300-A, -B and -C engines, connect the starter detent cable to the lever, on the starter, then operate the control to make certain the starter pinion is fully engaging the crankshaft gear. On all models connect the electrical lead to the starter switch. dilution system.
Connect the generator field coil "F" and armature "A" electrical leads to the terminals so designated on the installation drawing.
Remove the pipe plug and install the necessary fittings for oil dilution at the location indicated on the installation drawing if the aircraft incorporates an oil
5-8. INSTRUMENT CONNECTIONS. Apply a film of grease to the flexible shaft end of the mechanical drive tachometer, and connect the drive to the tachometer drive housing. Make sure the flexible shaft conduit is properly supported and without sharp bends. Connect the oil pressure gauge tube in the location indicated on the installation drawing. Remove the plug and gasket below the oil cooler and install the oil temperature gauge capillary with a new gasket. Connect the cylinder head temperature gauge to the thermocouple previously installed. Connect the intake manifold pressure gauge to the intake manifold riser.
5-9. BLAST TUBE AND BREATHER. To provide the generator with COOling air, connect the aircraft blast tube to the connector projecting from the generator brush access cover. Install the aircraft breather hose on the crankcase breather and secure it with hose clamps.
5-10. FUEL SUPPLY LINE. Connect the fuel line to a suitable fitting installed in the 1/4 in. N.P. T. hole of the carburetor on the level of the manual mixture control lever.
5-11. AIRCRAFT PARTS. Install whatever engine baffles are required by the cowling of the aircraft in such a manner as to form a tight seal between the upper and lower compartments so that all cooling air will be forced to travel through the cylinder fins and the oil cooler fins. Attach the overboard drain lines
Install the carburetor air scoop and air filter parts and the heat valve control. Make sure that the control will move the valve through its full range. Complete the installation of any other aircraft parts removed from the engine compartment, and install all parts of the cowling.
5-12. LUBRICATION. There are no grease fittings or points to be lubricated other than filling of the oil sump. Fill the sump with clean engine lubricating oil of a reputable brand and of the viscosity grade recommended in Table VTI, according to climatic condition. The choice of detergent or straight mineral oil should be based on operating experience in the climate and the conditions of operation anticipated. Detergent oil is recommended only if it is used conSistently from the time the engine is installed, since it will
9
10
NOTE
INSTALL PROP SHAFT WITH DOWEL
HOLES IN LOCATION SHOWN WHEN
NO,I CVL IS ON TOP DEAD CENTER
ON COMPRESSION STROKE
~---'5.75
-----\--k=
2~DOWEL HOLES
500-.501 DIA r
6 SOL THOLES
I
.501- .503 DIA
OIL GAGE ROD
~I·
tv
TEMPERATURE
CONNECTION
500-14NPTF
'rir;~ ~
I
I
11 /
EXHAUST n
. !
AN~G'
ACCESSORY DRIVE PAD ----..I srD AN020000 TYPE X
DRIVE EXCEPT SPEED =
A
"
I
2.81
~7.l8
.8947 X ENGINE SPEED r---
9.38
MANIFOLD PRESSURE-I
CONNECTION .125-27 NPTF
.755-.7480IA (TYP)
.4680IA(TVP)
PLUG-OIL SUMP
DRAIN PLUG
\
FIELD TERMINAL
ARMATU.RE TERMINAL
2160-24 THREAD
2: TERMINALS
,
+,-'''jLcd-'-f---\-~--VACUUM PVMP
AETURN
.375-18 NPTF
~"-~~"i'<:""~
RELIEF VALVE
TACH DRIVE
ASM TYPE I
- BALANCE
TUBE
MANIFOLD DRAIN CONNECTION
.12:5-27 NPTF
OIL DILUTION
CONNECTION
.125-27
(ORYSEALl
STARTER TERMINAL
.375-16 THO
LIFTING EYE
.625 OIA. HOLE
CRANKCASE BREATHER
CONNECTION
-.3125-24NF3
STUD EXT .8BHIGI;
/
/ r l 2 VOLT STARTER
/STARTER AND GENERATOR
REMOVAL CLEARANCE r-
2 .OO
!
MAGNETO
GROUND
TERMINAL
TEMPERATURE
CONNECTION
OIL PRESSURE CONNECTION
,125-27 NPTF
FUEL PRIMING CONNECTION
.125- 27 NPTF
.25701A HOLE
MARVEL CARB.-
MODEL MA-4-5
Figure 5. Installation Drawing.
GENERATOR
20AMP
12 VOLT
.Be X 1.00 LENGTH
6.41 BLAST TUBE
1
OIL SCREEN
CLEARANCE
REMOVAL
FUEL INLET
.250 STO BRIGGS TAPER TAP
loosen and circulate deposits of sludge precipitated from regular oil previously used in the lubricating system.
5-13. INITIAL OPERATION. A new or newly overhauled engine should be operated with lighter than normal loads for the first two hours to seat new running parts and avoid excessive temperatures atpoints not subj ect to measurement. Running on the ground should be conducted during the cool hours of the day in warm climates and should be interrupted whenever oil or cylinder temperatures approach dangerous levels. Full throttle operation on the ground should be limited to very short periods to check performance and instruments, since the ram effect of flying speed is necessary for cooling at normal power output or higher. During the first few hours of operation inspect all control, wire and tube connections frequently. buretor fuel inlet, and replace it with a 1/4-in. pipe plug. Disconnect the oil temperature gauge capillary below the oil cooler, and replace it with a plug and gasket. Disconnect the oil pressure gauge tube, remove its connector, and replace it with a l/8-in. pipe plug. Disconnect the intake manifold pressure gauge line from the manifold riser. Disconnect the blast tube from the generator. Disconnect the breather hose at the engine elbow. If an oil dilution line is installed, disconnect the tube and replace its connector fitting with a 1/8-in. plug.
5-17. ELECTRICAL CONNECTIONS. Disconnect the two wires from the generator terminals and label them liA" and "F". Disconnect the two lead wires from the cylinder thermocouple. Disconnect the battery power cable to the starter switch. Disconnect the grounding strap from the engine. Immediately after detaching each wire, replace the attaching parts.
All ground operation must be conducted with the manual mixture in the "FULL RICH" position.
5-14. REMOVING ENGINE FROM AIRCRAFT. Remove all engine cowling, baffles, the carburetor air scoop and other aircraft parts which will interfere with hoisting of the engine.
5-15. LUBRICATING OIL. Drain the oil sump as completely as possible, then replace the drain plug.
NOTE
If the engine is to be shipped or stored, it is advisable to preserve it as described in Section
IV, either before removal from the aircraft or on a test stand where it can be operated with corrosion-preventive oil and at the recommended temperature.
5-16. TUBE CONNECTIONS. Shut off the fuel supply; then disconnect the fuel line at the carburetor. Remove the 1/4-in. square-head pipe plugs atthe bottom of the front side of the carburetor, and drain the fuel; then replace the plug. Remove the fitting from the car-
5-18. CONTROL CONNECTIONS AND DRIVES. Disconnect the controls from the tachometer drive, starter detent control (on GO-300-A, -B and -C engines), the carburetor-throttle lever, and the mixture-control lever.
5-19. HOISTING. When all Wires, tubes and other parts attached to the aircraft have been detached from the engine and supported so as not be become entangled when it is lifted out, attach a hoist to the engine lifting eye and take up all slack without lifting the engine. Since the engine tends to assume' a tailheavy attitude, loosen the rear mounting bolts first; then remove the front mount bolts. Hold down on the propeller mounting flange as necessary while removing the front mounting bolts. While still holding the engine in the same attitude, lift it until it can be swung to the horizontal position without striking the aircraft; then hOist it clear and either roll the aircraft away, or move the hoist away from it.
5-20. PRECAUTIONS. Do not allow any part of the engine to touch the floor. If the engine is to be overhauled, it should be mounted on the disassembly stand at once. If it is to be shipped, the preservation procedure recommended on paragraph 4-11, covering of all openings, should be carried out before the engine is mounted in the shipping crate.
11
SECTION VI
MAINTENANCE INSTRUCTIONS
6-1. DAILY INSPECTION. Beforethefirstflighteach day a general inspection should be made of engine control connections and operation, electrical wire terminal connections, and for leakage or looseness at fuel supply, primer and oil dilution tube connections.
The oil level gauge should be inspected and oil added if the level is near the "L" mark. After the engine has been started and warmed up, the engine instruments should be observed for possible irregularities in performance at various speeds from idling up to full throttle, with the propeller in the low pitch position.
Operation at full throttle should be limited to the minimum time required to observe oil pressure and to test the individual ignition systems for excessive drop in
R.P.M. by switching from "BOTH" to "L"thenback to
"BOTH", then to "R" then back to "BOTH". Leave the ignition switch in "L" and "R" positions only long enough to stabilize R.P.M. If no drop in speed is observed when operating on either magneto alone, the switch circuit should be inspected for loose connections.
6-2. 100-HOUR INSPECTION. At intervals of approximately 100 hours of operating time, it is advisable to perform a thorough inspection of the engine installation to detect incipient troubles due to looseness of parts and connections, normal wear, fatigue cracks in visible metal parts and obstructions to air flow.
This inspection should be made to coinCide with a routine oil change. Any instance of improper attachment, leakage, support, fit or operation should be corrected to assure continued reliable performance of the engine and its accessories and to prevent small troubles from becoming dangerous ones, resulting in higher repair costs. The following pOints should be given particular attention: a. Remove all cowling and surrounding baffles necessary to give full access to the engine, accessories and controls. Clean cowling and baffles to permit inspection for cracks and looseness of parts. b. Drain and refill the engine lubricating system, as described in paragraph 6-3. The engine warm-up must be carried out before removal of the COWling. c. Inspect fuel lines, gauge tubes and the breather tube, connectors and supports, for security of attachment, cracks, and the possibility of tubes touching electrical wires or rigid members. Tubes are most likely to crack near end fittings and intermediate supports. Inspect tube grommets at the fire wall for secure installation and close fit. d. Inspect all control linkages for range of movement, wear at pin jOints, unusual friction or binding, and interference with other members. e. Inspect all hoses and clamps for tightness of jOints and general appearance. Ascertain that tightening of hose clamps at the jOints has not deformed intake manifold parts so as to cause leakage. f. Inspect visually all attaching bolts and nuts, plugs and lock wires. If any appear to be loose test it with a wrench and tighten as necessary. Usually, oil leakage around parts attached to the crankcase will precede other evidence of looseness and should be corrected by tightening of the attaching parts unless the extent of leakage indicates that a gasket or oil seal should be replaced. Especially at the first periOdic inspection after installation of a new or rebuilt engine, it is advisable to test tightness of base attaching nuts with a wrench. g. Shut off the fuel supply to the carburetor. Disconnect the fuel supply line at the carburetor. Remove and clean the fuel strainer; then replace it, and reconnect the supply line. h. Remove, clean, inspect and measure gaps of all spark plugs. (Refer to Table n.) Replace any plug with a damaged insulator, loose or badly eroded electrode or damaged thread. Before replacing a plug, make sure that its gasket is smooth. Before reconnecting cables to the spark plugs, inspect the terminal elbows, springs and sleeves for damage. Inspect all cables for breaks or ruptures in the insulation and for secure attachment to the magneto outlet plate. i. If there was any sluggishness in the engine operation which was not traced to the fuel or induction system or to the spark plugs, the breaker covers may be removed for inspection of pOint gap and condition. Ordinarily it is not necessary to check ignition timing; however, wear of the magneto breaker cam follower can result from lack of lubrication and make the timing late. For corrective procedure refer to paragraphs 6-9, 6-10 and 6-11. j. Remove all valve rocker covers and inspect valve stems, springs, retainers, keys and rockers for evidence of inadequate lubrication and breakage. All parts should be covered with oil. If there is any lash in any valve train when the valve is fully closed, the hydraulic tappet is not operating properly.
For removal procedure refer to paragraph 6-18.
Use new gaskets and lock washers when replacing rocker covers. k. Inspect cylinder fins for possible obstructions.
Make sure that intercylinder baffles are securely attached and held in contact with the cylinders.
1. Remove, clean and replace the carburetor air cleaner according to the aircraft manufacturer's instructions. m. Inspect the oil cooler fins for obstructions, and blowout any dirt with compressed air or flush with cleaning solvent. n. Test engine mount bolt and retighten to specified torque if found loose. o. It is advisable to wipe any oil or caked dirt from
12
the engine surfaces in order to reduce the fire hazard and to enable early detection of any possible oil leakage.
6-3. OIL CHANGE PROCEDURE. Undernormaloperating conditions the oil sump should be drained and refilled with fresh oil of seasonal grade (Table VII) at intervals of 25 to 30 hours of flying time. In order to drain out as much as possible of the old oil it is advisable to drain it as soon as possible after a routine flight, and with the oil temperature not lower than
120 0 F. When sump drain plug is reinstalled use a new copper-asbestos gasket. While the sump is draining remove the two oil screens. Slush screens in solvent to remove all solid matter adhering to the outside of the screen; then dry it with dehumidified compressed air or allow it to drain until dry. Make sure that the housing threads are clean. It is advisable to use a new copper-asbestos gasket under the screen flanges when reinstalled.
6-4. ADJUSTMENTS AND MINOR REPAIRS.
6-5. CARBURETOR. The carburetor manual mixture control lever should be at its extreme left position
(toward fuel inlet) when the cabin control is in the
"IDLE CUT-OFF" position. If the engine cannot be stopped from idling speed by operation of the control, the lever may not be reaching its stop due to looseness or flexure in the control linkage. The same lever should reach its extreme right position when the cabin control is set for full "RICH" operation. The angle between the extreme lever positions is 64 0 , and each
32 0 from the straight forward position.
6-6. The idling mixture control is located at the rear of the carburetor, above the manual mixture control lever.
It should be set slightly rich to avoid stalling at idling speed. First, adjust the lever to produce smoothest operation and maximum RPM with the throttle closed.
If speed is much above or below 600 RPM adjust it to that value by turning the idle speed stop screw (with spring) beside the throttle lever; then move the idling mixture lever slightly toward the" R n (rich) side. Then if the manual mixture control is moved to "IDLE
CUT-OFF" position, the speed should increase 10 to
20 RPM before starvation begins to stop the engine, since leaning the mixture with the cut-off momentarily corrects a slightly over-rich condition. If a greater increase in RPM was observed, the idling mixture setting is too rich, and if no increase occurs, it is too lean. Always return the manual mixture control to the full "RICH" position before the engine stops if further running is desired. To avoid false results due to spark plug fouling, run up the engine speed to above 1500 RPM after idling periods.
6-7. The carburetor may be removed for repair or replacement by detaching the air scoop from its bottom flange, shutting off the fuel supply and detaching the fuel supply tube at the carburetor inlet, disconnecting the throttle and mixture controls and removing the four nuts, washers and lock washers which attach the carburetor to the sump. To drain the fuel from the float chamber remove the pipe plug at the bottom of the rear Side (below the mixture control lever).
6-8. IGNITION CABLES. Cable assemblies to lower spark plugs of cylinders No.2, 4, and 6, and those to lower spark plugs of cylinders No.1, 3 and 5 are held together, as they cross the rear of the engine, by a band clamp. Two three-wire cable brackets are attached to each side of the crankcase cover; one two-wire cable bracket to each side of the sump flange; and one two -wire cable bracket to the upper parting flange of the left crankcase to support the cables and prevent excessive movement. The cables and the brackets securing them must be removed as a unit if one or more of the cables are'to be replaced.
6-9. MAGNETO BREAKER. Mark and tag each cable and its receptacle as the cables are disconnected from the magneto. Remove four sets of attaching parts and detach the magneto cover carefully. Do not separate the cover from the magneto more than necessary to insert a thumb and forefinger between them and detach the grounding lead from the breaker assembly. Absorb any oil around the breaker into a clean cloth. If the breaker pOints are oily remove the oil with a cloth moistened with unleaded gasoline.
Do not touch the cam, since gaSOline or any solvent would remove the oil with which it is impregnated.
If, on the other hand, the breaker appears to be very dry, its felt wick may need a drop or two of S.A.E.
60 oil. Allow about 15 minutes for the oil to be absorbed; then blot off any excess. AVOid gett~ng oil on the breaker pOints. The felt wick does not need oil if pressure with a fingernail causes oil to appear on the surface. It should never appear damp.
6-10. To check the breaker pOints for opening and surface condition, turn the propeller backward until the breaker cam follower is at the highest point of either cam lobe. The amount of gap is not specified.
Contact surfaces should have a gray matte appearance.
Pitting, burning, or transfer of metal from one point to another usually indicates a weak condenser. Do not file the contact surfaces. If they are unserviceable, replace the entire breaker assembly and the condenser.
6-11. MAGNETO INSTALLATION AND TIMING.
NOTE
In order to turn propeller shaft with ease while timing the engine, the upper spark plug in each cylinder should be removed. a. With the assistance of a second person to turn the propeller shaft in direction of rotation, block the spark plug hole of No. 1 cylinder until compression of the air in the cylinder indicates the piston is coming up on the compression stroke. b. Remove the hex head plug and gasket from the left side of the crankshaft cover (12, figure 1) and have the propeller shaft turned until the line below the etched letters "TC" is aligned with the pOinter. c. Turn the propeller shaft backwards until the line below the etched "28 0 " and above the "BTC" is aligned with the pOinter. The engine is now timed to fire No.
1 cylinder.
13
d. Detach ignition switch lead and high tension cables from magneto. Remove magneto attaching parts, then withdraw magneto and gear assembly from the crankcase cover. e. Remove cotter pin, shaft nut and gear from the magneto. Reinstall nut with spacer sleeve to keep impulse coupling in place. Remove nut from shaft of replacement magneto. Install gear, tighten nut and install cotter pin. f. Install a spare ignition cable in the No.1 cylinder outlet of the replacement magneto. Hold spark plug terminal of cable near a bare metal area of the magneto and turn drive gear clockwise (facing drive end) until a spark jumps from terminal to magneto upon release of the impulse coupling. Stop rotation as soon as spark is observed. Insert a 3/32-inch diameter pin into timing hole at bottom of magneto case. Hold pin inward and turn gear counterclockwise (facing drive end) until pin drops in and locks rotor shaft. g. While holding pin in place, mount magneto and a new gasket on the crankcase cover pad and secure with attaching parts. Tighten nuts only snug by hand, remove pin and spare cable. h. Position a timing light (one containing its own source of illumination) so it may be easily observed; then connect its red 'lead to the magneto ground switch terminal and the black ground lead to any bare metal part of the engine. i. Turn the magneto to extreme counterclockwise position; then, with a nonmarring hammer, tap the m:tgneto case clockwise until timing light indicates opening of breaker pOints. j. Tighten the magneto attaching nuts to approximate ly 200 inch -pounds. k. Check timing by backing up propeller shaft approximately five degrees, then tap gently forward until timing light indicates opening of breaker pOints. If timing is correct the line between the etched "28 0 " and the "BTC" will be aligned with the pointer of the crankshaft cover. a. Remove three sets of nuts, lock washers and plain washers attaching the adapter to crankcase cover studs. b. Remove a nut, lock washer and plain washer from the bolt that passes through the adapter, crankcase cover and crankcase rear flange. Remove the bolt and a plain washer. Pull the adapter assembly straight back. c. For disassembly, repair and reassembly procedures refer to the overhaul instructions.
6-13. GENERATOR. a. The generator is attached to a pad atthe lower rear side of the crankcase cover by three cover studs, elastic stop nuts and plain washers. The generator gasket extends under the tachometer drive hOUSing, which must be removed to replace the gasket. b. The drive assembly, retained on the generator shaft by a slotted nut and cotter pin, is removed with the generator. It consists of a coupling hub, keyed to the shaft, two rubber bushings and a steel retainer, which fit into the hub slot, a steel sleeve, which extends from the retaining nut to the hub, and a gear, whose drive lugs fit between and drive the bushings.
6-14. OIL COOLER. To detach the oil cooler it is necessary to remove only its eight attaching nuts and washers.
6-15. VERNATHERM CONTROL VALVE. Toremove the valve (11, figure 1) after removing the lower cowling, it is only necessary to cut the lock wire which secures its hex cap and uns'crew it. No repair parts are supplied for the Vernatherm valve, and readjustment is not recommended since special testing equipment is required to assure correct performance. The assembly may be cleaned with a solvent and inspected for damage. Normally, it will operate properly if its spring-loaded poppet valve has a true face and if the seat in the crankcase is not damaged; however, sludge may lodge on the seat and prevent the valve from closing.
6-12. STARTER. (For Model GO-300-A, -B and
GO-300-C engines.)
6-12A. STARTER.
GO-300-E engines.)
(For Model GO-300-D and a. The starter may be removed for inspection and repair by first disconnecting the switch wire and power cable from the solenoid. b. Remove two sets of parts attaching the starter motor to the adapter, then withdraw motor straight outward.
6-12B. STARTER DRIVE ADAPTER ASSEMBLY.
(For Model GO-300-D and GO-300-E engines.)
Do not remove the locking pin staked in a drilled hole in the hex adjusting nut at the poppet valve end. Do not remove the valve from the crankcase when the engine oil temperature is above
145 0 F.
6-16. OIL PRESSURE RELIEF VALVE. The relief valve is not adjustable. Its spring is designed to produce normal oil pressure when the oil pump and bearing clearances are within specified limits and undamaged. If low or fluctuating oil pressure indicates improper relief valve action, the valve parts may be removed for cleaning and inspection by unscrewing the brass cap and withdrawing the spring and plunger. Clean the parts in a solvent and wipe the seat in the cover with a clean cloth. Inspect the
14
seat and the plunger face for scratches and other deformation. Use a new copper-asbestos gasket when replacing the cap. the pushrod housings until clear of the pushrod housing flange. f. Remove cylinder base nut locks and flange nuts, starting with lower ones first. g. Support the cylinders in either arm, pull it straight outward, keeping the pushrods in place.
Grasp the piston as it leaves the cylinder to prevent the connecting rod from striking the crankcase.
6-17. PROPELLER SHAFT OIL SEAL. If an oil leak should develop around the seal at the front of the propeller shaft cage, the rubber ring may be pried out with a pointed tool inserted at the outer edge, using a wood block as a fulcrum and moving around the circle several times until it is free. Lift out the inner spring, and unhook its end loops.
Twist the rubber ring to remove it from the shaft.
Before installing a new seal assembly, clean out the cage counterbore and inspect the shaft surface for roughness. Smooth it with crocus cloth, if it is at all rough. Spread a film of lightweight TiteSeal paste in the cage recess and on the periphery of the new seal. Use only enough to form the thinnest possible film in the cage. Remove and unhook the spring of the new seal. Spread on the seal lip a coat of Gredag
No. 44 grease. Twist the seal as before, and slide it over the propeller shaft; then align the ends. Hook the new spring around the shaft behind the seal, and lift it into the groove, starting at the split and working both ways. Position the split 5/8-inch on either side of the cage parting line above the propeller shaft, and push the ring in evenly with two flat bars prying against blocks behind opposite sides of the shaft flange until the front side is flush with the surface.
6-18. REMOVAL OF HYDRAULIC VALVE LIFTER
UNITS. a. Detach ignition cables and remove spark plugs from cylinder. b. Remove valve rocker cover and gasket from cylinder. c. Turn propeller until both valves and cylinders are closed and piston is at Top Dead Center. d. Relieve the tension of hose clamps and move them off the rubber connections back onto the pushrod housings. e. Push the pushrod housing connections back onto
Do not lift or carry the cylinder by the pushrod housing. Any side force will loosen them and cause oil leakage. h. Push the pin through the piston until it clears the connecting nut. Remove the piston and return the pin to its working position. i. Remove three sets of attaching parts, the pushrod housing flange and gasket. Insert a hand through the cylinder opening of the crankcase, push the valve lifter body to its outward-most position. j. In the event that an old style lifter, without a retaining ring is used, the following procedure should be used. USing a hook made of lockwire, engage the oil hole of the pushrod socket and withdraw it from the body. With the same piece of lockwire, hook under the head of the hydraulic unit and withdraw the unit assembly. k. Remove the inner parts of the second valve lifter assembly in the same manner as in the two preceding steps.
1. Refer to Section XIII, paragraphs 13-1 through 13-6 for repair instructions of the hydraulic unit. m. Reinstall hydraulic valve unit in the lifter body, piston and rings assembly and cylinder assembly in the reverse order of removal. n. Install new pushrod housing flange gasket and rocker cover gasket, impregnate with lightweight
TiteSeal Compound.
Trouble
Engine will not start
TABLE VIII TROUBLE SHOOTING CHART
Probable Cause
Fuel tank empty
Mixture control in "I D L E
CUTOFF" position
Fuel supply line plugged
Fuel line shutoff valve closed
Carburetor screen plugged
Carburetor flooded
Remedy
Fill with 80/87 octane gasoline.
Move to full "RICH" position.
Dis con n e c t at carburetor.
Check flow. Clean out. Check starter.
Open valve.
Clean thoroughly. moisture.
Remove
Disassemble and clean. Check float needle and seat.
15
16
Trouble
Engine will not run at idling speed
Rough idling
TABLE VIII TROUBLE SHOOTING CHART (cont.)
Probable Cause
Cylinders over-primed
Insufficient priming (puffs of white smoke and weak combustion)
Remedy
Place mixture control in
"IDLE CUTOFF" position.
Switch ignition off. Open throttle wide. Turn propeller several revolutions.
Prime more. In cold weather draw plunger slowly back, push hard. Check pump output at priming jet.
Install terminals. Switch wires disconnected from both magnetos
Magnetos improperly timed to engine
Magneto internal timing incorrect or timed for opposite rotation. Latch studs improperly set. Weak condenser. Breakers improperly adjusted
Spark plugs fouled
Refer to timing instructions in Section VI.
Refer to magneto manufacturer's data.
Weak spark, magneto coils burned out by overheating, moisture in distributors
Spark plugs loose
Leak in intake manifold
Remove and clean; check gaps and insulators. Use new gaskets. Check cables to persistently fouled plugs.
Remove and ground upper spark plugs, with mixture control at "IDLE CUT-OFF", throttle open, switch at
"BOTH", turn propeller forward slowly. Listen for clicks of impulse couplings and observe sparks at plug gaps. If weak, inspect distributors. If dry, test cables. If good, overhaul magnetos.
Tighten to specified torque.
Check and correct hose connector positions. Tighten the flange attaching bolts.
Idle stop screw or idle mixtUre lever incorrectly adjusted
Carburetor idling jet plugged
Refer to paragraph 6-5.
Air leak in intake manifold
Spark plugs fouled by oil escaping past piston rings
Clean carburetor and fuel strainer.
Tighten loose connection or replace damaged part.
Top overhaul.
Idling mixture lever improperly adjusted
Refer to paragraph 6-5.
Trouble
Engine runs too lean at cruising power
Engine runs too rich at cruising power
Engine does not accelerate properly
Engine does not accelerate properly, but runs satisfactorily with slow throttle movements
TABLE VIII TROUBLE SHOOTING CHART (cont.)
Probable Cause
Manual mixture control set for lean mixture
Fouled spark plugs
Remedy
Use full rich mixture for all ground operation.
Remove and clean. Adjust gaps. Test cables. Inspect magneto breakers. If persistent, perform top overhaul.
Small air leak into induction system
With mixture control at "IDLE
CUTOFF", ignition switch at
"OFF" and throttle open, brush soap lather around tube jOints and carburetor mount flange, one at a time, and turn propeller backward to check for bubbles at pOints of leakage. Tighten connection or replace damaged gasket or seal.
Top overhaul. Burned or warped exhaust valves, worn seats, scored valve guides
Hydraulic tappet fouled
Leaking carburetor discharge nozzle
Listen for loud tappet noise.
Refer to Section XIll.
Overhaul carburetor.
Fuel pressure too low
Plugs missing or loose
Manual control in wrongposition
Restriction in air scoop
Carburetor air heat valve open
Cold engine
Check fuel strainer and fuel system.
Check all liS-inch and taper seat plugs for tighteness.
Check control linkage.
Extend warm-up period.
Mixture control set for lean mixture
Restrictions in carburetor air intake
Restrictions in carburetor jets, low float level, plugged fuel screen
Idle setting too lean
Set control at full "RICH" position.
Clean air filter.
Clean and repair carburetor.
Adjust, refer to paragraph
6-5.
17
18
Trouble
Engine does not shut off with manual mixture control in "IDLE CUTOFF" position
Continuous fouling of spark plugs
Engine runs rough at high speed
Regular missing at high speed
Sluggish operation and low power
TABLE VIII TROUBLE SHOOTING CHART (cont.)
Probable Cause
Mechanism does not permit poppet valve to close completely
Remedy
Overhaul carburetor.
Linkage does not permit
"IDLE CUTOFF" lever to reach "OFF" position
Piston rings not seated
Piston rings excessively worn
Piston ring gaps aligned
Piston rings inverted
Broken piston ring
Mounting bolts of rubber bushings loose
Propeller out of balance
Spark plug gasket leaking, gap too large or insulator damaged
Ignition cable insulation damaged
Excessively lean fuel-air mixture
Valve spring broken
Valve warped or burned
Hydraulic tappet dirty or worn
Throttle not opening wide
Spark plugs fouled or improperly gapped
Carburetor air heat valve open
Incorrect magneto timing
Damaged magneto breaker or condenser
Allow approximately 50 hours of operation for new rings to seat properly.
Replace.
Space gaps 90 degrees apart, with oil control ring gap to the top.
Install with side etched "TOP" toward piston head.
Replace ring (and cylinder if damaged).
Tighten bolts or replace bushings.
Remove and repair.
Replace damaged part.
Test for leakage at high voltage. Replace damaged cable.
Clean strainer, carburetor screen, carburetor main jet.
Measure flow through supply line.
Replace.
Top overhaul.
Remove and clean or replace.
Adjust linkage.
Close valve or readjust control.
Refer to timing instructions in Section VI.
Refer to paragraph 6-10.
Trouble
High cylinder head temperature
High oil temperature
Low oil pressure
TABLE VIII TROUBLE SHOOTING CHART (cont.)
Probable Cause
Fuel-air mixture too rich or too lean
Valve seats worn and leaking
Piston rings worn or stuck in grooves
Remedy
Overhaul and adjust carburetor.
Top overhaul.
Top overhaul.
Low octane fuel
Lean fuel-air mixture
Excessive carbon deposits in cylinder head and on pistons
Cylinder baffles loose or bent
Dirt between cylinder fins
Exhaust valves leaking
Cooler fins plugged with dirt
Cooler core plugged
Vernatherm control valve damaged or held open by solid matter
Refer to Table IV for correct fuel octane rating.
On ground and in flight below
5000 ft. altitude operate with mixture control in "RICH" position. At higher altitudes operate with mixture adjusted slightly on rich side of best power position.
Install new cylinders and piston rings or new engine.
Check all baffles and correct.
Clean thoroughly.
Top overhaul.
Clean thoroughly.
Remove cooler and flush thoroughly.
Remove. Clean valve and seat. If still inoperative, replace.
Low oil supply
Oil viscosity too high
Prolonged high speed operation on ground
Low oil supply
Oil viscosity too low
Replenish.
Refer to Table VII for recommended seasonal grades.
Hold ground running above
1500 RPM to a minimum.
Replenish.
Drain and refill with correct seasonal grade. Refer to
Table VII.
Remove and clean valve parts. Sludge or foreign material in relief valve
Foam in oil due to emulsification of alkaline solids
Scored pressure pump
Defective pressure gauge
Drain and refill with fresh oil.
Replace pump.
Test gauge. Clean gauge tube
(or test connecting wire and engine unit of electric gauge).
19
2U
Trouble
Oil leak at front of engine
Oil leak at pushrod housing
Low compression
TABLE VIII TROUBLE SHOOTING CHART (cont.)
Probable Cause
Internal leak, burned bearing or damaged gasket
Worn bearings
Damaged propeller shaft oil seal
Damaged gasket pushrod housing
Cylinder wall worn out-ofround.
Intake valve guides worn
Valve faces and seats worn
Piston rings excessively worn
Cylinder barrel worn out-ofround
Valves sticking to guide
Remedy
Major overhaul.
Major overhaul.
Replace.
Replace.
Replace cylinder and piston rings.
Top overhaul.
Top overhaul.
Top overhaul.
Replace cylinder and piston rings.
Refer to paragraph 4-3.
SECTION VII
DlSASSEMBl Y
7-1. DISASSEMBLY STAND.
7-2. Use a stand with a pivoted engine bed of sufficient length to permit working space at each end of the engine. Refer to the applicable installation drawing for all dimensions affecting mounting provisions, clearances required, and the center of gravity location.
7-3. PARTS TO BE DISCARDED.
7-4. Discard all palnuts, shakeproof lock washers, lock wires, tab washers, rubber seal rings, oil seals, gaskets, cotter pins, hose connectors and generator coupling (rubber) bushings in such a manner that they will not be used again inadvertently. The bearings and bushings (29, 31, 84, 86, figure 10 and 43,44,
45, figure 11) will be replaced with new parts at each overhaul.
7-5. PRELIMINARY CLEANING.
7-6. Spray or apply with a clean paint brusha solvent used for general cleaning of engine parts. Remove caked dirt on bolt heads and nuts especially. At the same time the oil· sump drain plugs should be removed to drain any remaining oil. If the disassembly stand has no drip pan the valve rocker covers should be removed and oil allowed to drain from the rocker boxes away from the disassembly area.
7-7. AIRCRAFT PARTS AND OPTIONAL AC-
CESSORIES.
7-8. Instructions in this section are based on the assumption that all parts attached by the aircraft manufacturer have been removed from the engine.
7-9. DISMANTLING.
7-9A. STARTER AND ADAPTER, Model GO-300-D and GO-300-E. (See figure 6.) a. Remove two sets of attaching parts (1,2, and 3).
Withdraw starter (4). Remove and discard "0" ring
(5). b. Remove one set of attaching parts (6,7,8 and 9).
Remove three sets of attaching parts (10,11 and 12).
Withdraw adapter assembly straightaway from crankcase cover.
7-10. ACCESSORIES AND CRANKCASE COVER.
(See figure 7.) a. For Models GO-300-A and GO-300-C engines, remove two sets of attaching parts (1,2 and 3), three sets of parts (4, 5 and 6), withdraw starter (7) and remove gasket (8). b. Disconnect ignition cables from spark plugs.
Detach ignition cable brackets and remove band clamp (16). Mark the magneto outlet of each cable as it is removed from the magneto. c. Remove two sets of attaching parts (34,3& and
36) from each magneto (40), withdraw the magnetos from the crankcase cover and remove gaskets (37). d. Remove the band clamp securing the balance tube to the generator. Remove three sets of generator attaching parts (41 and 42), then withdraw generator
(53) . e. Remove the oil gauge rod (63, figure 11) and
"0" ring (62). Remove all twelve spark plugs (55, figure 7). Loosen both oil screens (25 and 26, figure 2) and the oil pressure relief valve cap. f. Remove two sets of attaching parts (1, 2 and 3, figure 13), five sets of attaching parts (4,5 and B) from the mounting flange of the crankcase cover; then withdraw the cover from the crankcase studs.
Make certain all traces of gasket (11) is removed.
7-11. INDUCTION SYSTEM AND OIL SUMP. (See figure 8.) a. Rotate the engine stand bed to place the engine in the inverted position. Remove four sets of attaching parts (1,2,3), lift off carburetor (4) and gasket
(5) or "0" ring(6). b. Loosen hose clamps (22), slide them off hoses
(23), then work hoses back on tubes until clear of jOints and remove balance tube (11). Remove four sets of attaching parts (12, 13 and 14), manifold riser (16) and gasket (17) or"O" ring (18). Remove twelve sets of attaching parts (19,20 and 21) and intake tubes. Remove clamps (22) and hoses (23) from intake tubes. Lift gaskets (27) from cylinder ports. c. Remove attaching parts (28,29 and 30), sump
(51) and gasket (52).
7-12. CYLINDERS AND PISTONS. (See figure 9.) a. With the aid of Corbin clamp pliers, move the hose clamps (7) from the connectors (8) back onto the pushrod housings (33). b. Remove one set of attaching parts (1, 2) and two sets of attaching parts (3, 4) from the lower part of each cylinder flange. c. Rotate engine stand bed to place engine in upright position. Cylinders may be removed in any order desired; however, before removing the three sets of attaching parts from the upper part of the cylinder
21
flange, the piston in the cylinder to be removed must be at Top Dead Center. d. Remove the remaining cylinder attaching parts, support the cylinder by placing one arm underneath it with the hand positioned to grasp and hold in place the pushrods. e. Pull out on the cylinder slowly, catch the piston as it emerges from the cylinder barrel and lower it gently until the connecting rod rests on the crankcase. f. Set the cylinder upright on a soft surface after removing the pushrods. g. Support the piston with one hand while pushing the piston pin sideways until free of the connecting rod.
The pin should be kept with the piston in its normal position.
42
\
41
\ \
~~
35 39
/
\
3~/~,7
~ I~
e;J
38
/
~
40
19
20
22
1. Deleted
2. Nut
3. Washer
4. Starting motor
5.
"a"
ring
6. Nut
7. Lockwasher
8. Washer
9. Bolt
10. Nut
11. Lockwasher
12. Washer
13. Gasket
14. Nut
15. Lockwasher
16. Washer
17. Cover
18. Gasket
19. Washer
20. Lockwasher
21. Bolt
22. "0" ring
23. Oil seal
24. Stud
25. Pin
26. Bushing
27. Adapter cover
28. Screw
29. Tab washer
30. Clutch spring
Figure 6. Starter and Adapter
31. Needle bearing
32. Worm wheel
33. Starter shaftgear
34. Retaining ring
35. Pin
36. Bushing
37. Worm gear
38. Woodruff key
39. Ball bearing
40. Worm shaft
41. Needle bearing
42. Stud
43. Dowel
44. Adapter housing
54-~
1. Bolt
2. Lockwasher
3. Washer
4. Nut
5. Lockwasher
6. Washer
7. Starter
8. Gasket
9. Rivet
10. Clamp bracket
11. Clamp bracket
12. Clamp bracket
13. Nut
14. Screw
15. Clamp bracket
16. Band clamp
17. No. 6 cylinder upper cable
18. No. 6 cylinder lower cable
19. No. 4 cylinder upper cable
20. No. 4 cylinder lower cable
21. No. 2 cylinder upper cable
22. No. 2 cylinder lower cable
23. No. 1 cylinder upper cable
24. No. 1 cylinder lower cable
25. No. 3 cylinder upper cable
26. No. 3 cylinder lower cable
27. No. 5 cylinder upper cable
28. No. 5 cylinder lower cable
29. Nail
30. Connector
31. Elbow assembly
32. Grommet
33. Cable
34. Nut
35. Lockwasher
36. Washer
37. Gasket
Figure 7. Ignition System and Accessories
38. Cotter pin
39. Magneto gear
40. Magneto
41. Nut
42. Washer
43. Gasket
44. Cotter pin
45. Nut
46. Generator gear
47. Sleeve, gen. coupling
48. Coupling bushings
49. Bushing retainer
50. Coupling hub
51. "0" ring
52. Oil seal
53. Generator
54. Regulator
55. Spark plug
23
1. Nut
2. Lockwasher
3, Washer
4. Carburetor
5, Gasket
6. "0" ring
7. Plug
8. Nut
9. Screw
10. Clamp
11. Balance tube
12. Nut
13. Lockwasher
14. Washer
15. Plug
16. Manifold riser
17. Gasket
18, "0" ring
19. Nut
20. Lockwasher
21. Washer
22. Hose clamp
23. pose
27. Gasket
28. Nut
29. Lockwasher
24. No. 6 cylinder intake tube 37. Plug
25. No. 4 cylinder intake tube 38. Plug
26. No. 2 cylinder intake tube 39. Screw
40. Washer
41. "0" ring
42. Washer
30. Washer
31. Plug
43. Spring
44. Suction tube
32. Plug 45. Thread insert
33. Copper-asbestos gasket 46. Diffuser ring
34. Plug 47. Diffuser tube
35. Copper-asbestos gasket 48. Retaining ring
36. Plug 49. Stud
50. Stud
51. Oil sump
52. Gasket
53. Heli-Coil insert
Figure 8, Induction System and Oil Sump
24
23
1. Deleted
2. Nut
3. Deleted
4. Nut
5. Cylinder base packing
6. Pushrod
7. Hose clamp
8. Pushrod housing connector
9. Screw
10. Lock washer
11. Washer
12. Valve rocker cover
13. Gasket
14. Rocker shaft
15. Rocker bushing
16. Plug
16A. Intake valve rocker
16B. Exhaust valve rocker
17. Valve locks
18. Valve spring seat
19. Outer valve spring
20. Inner valve spring
21. Intake valve spring retainer
22. Exhaust valve spring retainer
23. Exhaust valve
24. Intake valve
25. Exhaust valve guide
26. Intake valve guide
27. Spark plug hole thread insert
28. Plug
29. Stud
30. Nut
31. Exhaust gasket
32. Stud n.
Pushrod housing
34. Cylinder
35. Piston pin
36. Oil control ring
37. Third compression ring
38. Second compression ring
39. Top compression ring
40. Piston
Figure 9. Cylinder and Piston
1110
\
\
9
~@~
~
25
7-13. PROPELLER REDUCTION GEAR UNIT AND
OIL COOLER. (See figure 10. ) a. Remove eight sets of attaching parts (1, 2,3), oil cooler (4) and gasket (5). Loosen the Vernatherm valve (49). b. Remove two sets of attaching parts (6, 7, 8), eight sets of attaching parts (9, 10, 11) and withdraw the propeller shaft and cage assembly (18 through 43). c. Cut the lock wire, remove two sets of attaching parts (12, 13), ten sets of attaching parts (14, 15, 16), two lower sets of parts (63,64,65) and withdraw the reduction unit and gasket (17) from the crankcase studs.
7-14. CRANKCASE. (See figure 11.) a. Rotate engine bed to place left side of crankcase downward. Support the crankcase with a length of pipe placed over the top stud on No.4 cylinder mount pad. b. Remove nine sets of attaching parts (1, 2, 3), the lifting eye (4), spacers (5), and ten washers (6) and bolts (7 and 8). c. Remove cotter pins (9) and attaching parts (10,
11, 12, 13), attaching parts (14, 15, 16) and parts
(17, 18, 19) and tap the through bolts (20, 21, 22) down until the right crankcase is free. d. Wrap the used cylinder base packings around the right crankcase valve lifters, engaging one end of the packing around the pushrod housing flanges to prevent dropping the lifters as the right crankcase is lifted. e. Remove the screw (25), tab washer (26) and retainer (27). Detach the right mount brackets from the stand adapters. f. Have a second person remove the starter pinion pivot (24 or 28) or the bearing (29) as soon as the crankcase is raised clear. g. The second person should hold and then lower
No.1, 3 and 5 connecting rods as they clear the right crankcase. h. Place the right crankcase, parting flange down on a clean, smooth top, workbench.
7-15. CRANKSHAFT AND CAMSHAFT. (See figure
12. ) a. Cut the lock Wire, remove retaining ring (1), screws (3), and retaining plate (2). b. Withdraw the propeller drive shaft gear (4) slowly and carefully until the quill shaft can be grasped and withdrawn from the crankshaft with the gear. Carefully withdraw the quill shaft from the propeller drive shaft gear. c. Lift the camshaft (5) and gear (15) assembly from the crankcase. d. Two persons are required to lift the crankshaft, connecting rods and gear assembly from the crankcase safely. Lift the assembly by grasping the No.1
(14), 3 (13), and 5 (8) connecting rods. e. Lay the crankshaft on a clean work bench with the front and rear main bearing journals supported by wooden blocks which have been grooved to a slightly larger diameter than that of the journals.
7-16. DISASSEMBLY.
7-17. CRANKCASE. (See figure 11. ) a. With the aid of a pushrod, push the complete hydraulic valve lifter up until it is free of the lifter guide. Use extreme caution when removing the lifters as the pushrod sockets and hydraulic units are loose
(if of early design) and may be easily damaged if dropped. b. Lift out the eight through bolts (22) and remove
"0" rings (23). If the boIts are tight in the left crankcase, tap them upward lightly, with a nonmarring hammer. ' c. Detach the left crankcase from the engine stand and place it on a clean, smooth top workbench, parting flange down. d. Remove three sets of attaching parts (30, 31, 32), the housing flanges (33) and gasket (34). e. If necessary, the engine mount brackets (39 through
42) may be lifted off after removing two sets of attaching parts (35, 36, 37)from each bracket. f. Invert the crankcases, on the bench, so parting flanges are up; rotate, lift out and discard the main and thrust bearing inserts (43, 44, 45).
7-18. CRANKSHAFT AND CAMSHAFT. (See figure
12. ) a. Remove two sets of attaching parts (20,21,22) from each connecting rod. Rotate, remove and discard crankpin bearing inserts. Loosely reassemble the rods, bolts and nuts with position numbers matched. b. With Truarc No. 1 or 21 pliers, compress the retaining rings (11); then remove retaining plates
(12) and pins from counterweights (10). Remove counterweights from crankshaft. c. Cut lock wire, remove four attaching screws and remove crankshaft gear (16). d. Cut lock wire, remove four attaching screws and remove camshaft gear (15).
7-19. PROPELLER REDUCTION GEAR UNIT. (See figure 10.) a. Remove and discard the "0" ring (18) and "0" ring (19). Remove two sets each of cage left halfto-cage right half attaching parts (20 through 28).
Separate the cage halves, rotate and remove the bearings (29, 31). Lift the seal spring (33) from its recess in the seal (34), unhook the spring ends and remove it. Twist the ends off the seal in opposite direction until it can be removed from the propeller shaft. b. For GO-300-B and -E engines, remove retaining ring (37); then withdraw the governor oil transfer collar assembly from the propeller shaft. Remove the retaining ring (38), washer (39) and transfer collar (40) from the propeller shaft plug (41). If visual inspection of the governor drive gear (42) indicates replacement, it is recommended that the shaft and gear assembly be returned to the factory for this operation. c. For GO-300-A and -B engines, remove four sets of attaching parts (44,45,46), crankcase breather
(47) and gasket (48). d. Remove Vernatherm valve (49) and gasket (50).
Remove four sets of attaching parts (53,54,55), the crankshaft cover (56) and gasket (57). The plug
(51) and gasket (52) may be left in the cover.
26
1. Nut
2. Lockwasher
3. Washer
4. Oil cooler
5. Gasket
6. Washer
7. Lockwasher
8. Bolt
9. Nut
10. Lockwasher
11. Washer
12. Washer
13. Bolt
14. Nut
15. Lockwasher
16. Washer
17. Gasket
18. "0" ring
19. "0" ring
20. Nut
21. Lockwasher
22. Washer
23. Washer
24. Bolt
25. Deleted
26. Nut
27. Washer
28. Bolt
29. Bearing
30. Cage left half
31. Bearing
32. Cage right half
33. Oil seal spring
34. Oil seal
&35. Hubbard plug
&36. Shaft, propeller drive
**37. Retaining ring
**38. Retaining ring
**39. Special washer
**40. Oil transfer collar
**41. Plug, propeller shaft
**42. Governor drive gear
**43. Shaft, propeller drive
+44. Nut
+45. Lockwasher
+46. Washer
+47. Crankcase breather
+48. Gasket
49. Vernatherm valve
50. Gasket
51. Plug
52. Gasket
53. Nut
54. Lockwasher
55. Washer
56. Crankshaft cover
57. Gasket
*58. Nut
*59. Lockwasher
*60. Washer
*61. Vacuum pump drive gear cover
*62. Gasket
63. Nut
64. Lockwasher
65. Washer
*66. Accessory drive bevel gear
*67. "0" ring
*68. Ball bearing
*69. Accessory drive cage
#70. Accessory drive cover
#71. Accessory drive cover gasket
*72. Accessory drive gear
**73. Nut
**74. Lockwasher
**75. Washer
**76. Governor drive gear cover
**77. Gasket
# Used only on GO-300-D, -E engines
** Used only on GO-300-B, -E engines
**78. Retaining ring
**79. Thrust washer
**80. Governor drive gear
**81. Screw
**82. Tab washer
**83. Oil transfer tube
84. Bushing
85. Screw
86. Bushing
*87. Oil seal
*88. Bushing
*89. Plug
90. Plug
91. Plug
92. Plug
93. Ball
94. Stud
95. Stud
96. Stud
+97. Stud
+98. Stud
99. Stud
100. Stud
**101. Stud
102. Heli-Coil insert n03. Breather
104. Housing
+ Used only on GO-300-A, -B engines
* Used only on GO-300-A, -B, -C engines
& Used only on GO-300-A, -C,-D engines t Used only on GO-300-C, -D,-E engines
Figure 10. Propeller Reduction Gear Unit
27
28
I. Nut
2. Lockwasher
3. Washer
4, Lifting eye
5. Spacer
6. Washer
7. Bolt
** 8. Bolt
9. Cotter pin
10. Nut
II. Washer
12, Washer
13. Bolt
14. Nut
15, Lockwasher
16. Washer
17. Deleted
18. Flanged nut
19. Washer
20. Through bolt
21. Through bolt
22. Through bolt
23, "0" ring
,
lI;-62
+24, Starter pinion pivot t25. Screw t26. Tab washer t27. Retainer
*28. Removable pivot
#29. Starter shaft bearing
30. Nut
3I. Lockwasher
32. Washer
33. Pushrod housing flange
34. Gasket
35. Nut
36. Lockwasher
37. Washer
38. Washer
39. Right rear mount bracket
40. Right front mount bracket
4I. Left front mount bracket
42. Left rear mount bracket
43. Propeller drive shaft gear bearing
44. Crankshaft thrust bearing
45. Crankshaft main bearing
+ Used only on GO-300-A and -B engines
* Used only on GO-300-C engines t Used only on GO-300-C, -D, -E engines
# Used only on GO-300-D, -E engines
** Used only on GO-300-E engines
Figure 11. Crankcase
46. Stud
47, Stud
48. Stud
49. stud
50. Stud
51. Stud
52. Stud
53, stud
54. Stud
55. stud
56. stud
57, Dowel
58. Dowel
*59. Oil line pin
60. Thread insert
61. Plug
62. "0" ring
63. Oil gauge rod
64. Retaining ring
65. GUide, oil gauge rod
66. Drive screw
67. Identification plate
68. Right crankcase
69. Left crankcase
1. Retaining ring
2. Retaining plate
3. Screw
4. Propeller drive shaft gear
5. Camshaft
6. Through bolts
7. Crankshaft
8. No. 5 connecting rod
9. Crankshaft oil transfer tube
10. Crankshaft counterweight
11. Retaining ring
12. Retaining plate
13. No. 3 connecting rod
14. No. 1 connecting rod
15. Camshaft gear
16. Crankshaft gear
17. Starter pinion pivot
18. Thread
19. Left crankcase
20. Cotter pin
21. Nut
22. Connecting rod bolt
23. Crankcase support
24. No. 4 connecting rod
25. No. 6 connecting rod
26. Engine bed adapter
27. Left front mount bracket
Figure 12. Left Crankcase Mounted on Engine Stand
29
28
~
~
/
29
30
~o
/
~8 ~
~~~~
\ \ VJ~
21 20
1~ 1~
26
\ 27
,~~'.
25
~I
"', (@J
~
23" /(@;
22
30
I. Nut
2. Lock washer
3. Washer
4. Bolt
5. Lock washer
6. Washer
# 7. Nut
# 8. Lock washer
# 9. Washer
#10. Bolt
II. Gasket
12. Oil screen
13. Gasket
14. Plug
15. Gasket
16. Oil screen
17. Gasket
18. Cap
19. Gasket
20. Spring
21. Plunger
22. Nut
23. Lock washer
24. Gasket
25. Cap
26. Oil Seal
27. Tachometer drive housing
28. Screw
29. Tab washer
30. Oil pump cover
# Used only on GO-300-D, -E engines.
39.
40.
4I.
42.
43.
44.
31.
32.
33.
34.
35.
36.
37.
38.
Oil pump driven gear
Oil pump drive gear
Plug
Gasket
Plug
Plug
Stud
Stud
Stud
Stud
Bushing
Oil filler cap
Oil filler neck
Crankcase cover
Figure 13. Crankcase Cover
e. For GO-300-A, -B and -C engines, remove four sets of attaching parts (58,59,60), the cover (61) and gasket (62). f. For GO-300-A, -B and -C engines, remove two sets of attaching parts (63,64,65), withdraw the assembly of cage and drive gear. Remove drive gear (66), "0" ring (67), and bearing (68). Remove accessory drive gear (72). g. For GO-300-D and -E engines, remove two sets of attaching parts (63, 64, 65), the cover (70) and gasket (71). h. For GO-300-B and -E engines, remove four sets of attaching parts (73,74,75), the cover (76), gasket
(77), retaining ring (78) and thrust washer (79).
Withdraw governor drive gear (80). Remove screw
(81), tab washer (82) and oil transfer tube (83). b. Remove oil screen (16) and gasket (17). It is not necessary to disassemble the plug (14) and gasket
(15) at this time. c. Remove cap (18), gasket (19), spring (20) and plunger (21). d. Remove attaching parts (22, 23), discard gasket
(24), remove cap (25), remove and discard the seal
(26) • e. Remove attaching parts (28, 29), oil pump cover
(30), and lift out the gears (31, 32).
7-20. CYLINDERS AND PISTONS. (See figure 9.) a. Place the pistons open end down, on a clean surface, spread, remove upward and discard rings
(37, 38, 39). Invert piston, spread, remove and discard oil ring (36). Be extremely cautious not to score the piston lands with the ring edges. b. Use of a cylindrical wood block anchored to a workbench, with provisions for clamping the cylinder in place, is recommended to aid in the removal of valves springs and to prevent dropping the valves. c. Remove pushrod housing connectors (8) and clamps
(7). d. Remove six sets of attaching parts (9,10,11), the cover (12) and gasket (13). e. Push rocker shaft (14) sideways until rockers
(16A and 16B) can be removed. Slide the shaft back into its normal operating position so it may be used as a fulcrum for a lever-type spring compressor. f. Compress the valve springs (19, 20) with force applied at diametrically opposite pOints on the valve spring seats (18), taking care not to allow the seats to cock and score the valve stems. While the springs are depressed, remove the locks (17). Release pressure on compressor slowly, lift off seats (18), springs (19, 20) and retainers (21, 22). g. Grasp valve stems and lift cylinder from support. Lay cylinder on its Side, stone down any burrs on valve stems; then remove valves (23, 24).
7-21. CRANKCASE COVER. (See figure 13. ) a. Remove oil screen (12) and gasket (13).
7-22. GENERATOR DRIVE COUPLING. (See figure
7.) a. Remove cotter pin (44) and nut (45). b. Slide off generator drive gear (46) and sleeve (47). c. Lift out and discard the rubber bushings (48). d. Lift off bushing retainer (49) and hub (50). e. Remove and discard "0" ring (51) and seal (52).
7-23. STARTER ADAPTER. (See figure 6.) a. Remove four sets of attaching parts (14, 15, 16), the cover (17) and gasket (18). Remove one set of attaching parts (19, 20, 21), and the adapter cover assembly (22 through 27). Remove and discard "0" ring (22). b. To remove shaftgear and clutch spring from adapter, support vacuum pump drive end of adapter on wood blocks, then tap around front end of spring with a brass drift. c. Use an arbor press to remove starter shaftgear
(33) from bearing (31) and worm wheel (32). d. Clamp worm wheel between lead covered vise jaws. Bend ears of tab washer (29) away from hex flats of screw (28). Remove screw and tab washer.
Turn clutch spring (30) until its depressed rear end lies across the 1/4 inch hole, in worm wheel hub.
Insert a screwdriver blade, 3/16 inch wide, into hole and pry spring outward clear of drum groove.
Hold spring end out while pulling spring from drum. e. Remove retaining ring (34) and withdraw worm drive assembly. Drive the pin (35) through the shaft and bushing. Remove bushing (36), worm gear (37), woodruff key (38) and bearing (39) from worm shaft
(40) •
31
SECTION VIII
CLEANING PARTS
8-1. MATERIALS AND PROCESSES.
8-2. Equipment, processes and materials in general use in aircraft engine overhaul shops will be entirely satisfactory for cleaning the parts of these engines.
All light metal parts of these engines are aluminum alloys, excepting the crankcase cover which is of magnesium alloy.
8-3. Do not use any strong alkaline solution to clean aluminum alloy castings or wrought aluminum alloy parts, because all such solutions attack the bare surfaces too rapidly to permit cleaning without destruction of the finish. For these parts use a fortified mineral spirit solvent, sold under various trade names, for degreasing. If rosin (oil varnish) or stubborn carbon deposits must be removed from aluminum alloy parts, they may be imme rsed in an agitated bath of an inhibited mild alkaline cleaning solution marketed for that purpose. The bath should be maintained at a temperature of 180 o
F. to 200
0
F., and the parts should remain in it only long enough to loosen the deposits. Immediately after such cleaning flush away all traces of the alkaline material with a jet of wet steam or by repeated brush application of a mineral spirit solvent.
Any alkaline deposits remaining on engine interior parts will react with acids formed in the lubricating oil to form soap, which will cause violent foam and may result in failure of the lubricating system.
8-4. Trichlorethylene condensation plants provide excellent degreasing action for steel, aluminum and bronze parts. Their disadvantages lie in the toxic quality of the vapors, removal of enamel from painted parts, and the drying and hardening effect on carbon deposits.
8-5. No polishing compound or abrasive paste or powder should be needed or employed for cleaning engine parts. Do not use wire brushes or wire brush wheels, putty knives, or scrapers to remove hard carbon deposits, since scratches resulting from such methods allow a concentration of stress at the scratch and may cause fatigue failure.
8-6. Various hot and cold working solutions have been marketed for loosening carbon. Any of these may be employed for that purpose if they do not attack the metal; however, most such materials are ineffective against hard carbon deposits, since they loosen by dissolving adheSive rosins which cannot be dissolved after they have been carbonized by heat.
8 -7. VariOUS blasting techniques can be employed to remove hard carbon deposits if suitable equipment is available. The most suitable types of grit for dry blasting are plastic pellets and processed natural materials, such as wheat grains and crushed fruit pits or shells. Air pressure should be the lowest that will produce the desired cleaning action. Small holes and finished surfaces which do not require cleaning should be protected from the blast by seals and covers, particularly if the grit is sharp. Sand and metal grit and shot used for blasting industrial metals are too abrasive and too heavy for use on soft metals such as aluminum. The vapor grit process employs abraSive grit, but of much smaller size and carefully controUedgrades for various purposes. Carbon may be removed from piston heads by the vapor grit blasting process, using No. 80 grit, which is also suitable for cylinder head interiors, but much too coarse for finished piston walls and ring grooves.
No. 50 vapor blast grit may be used on cylinder heads for more rapid cleaning. In any event, the cylinder walls and valve guides must be shielded.
After any blasting process, blow off all dust with dehumidified compressed air and make sure that no grains have lodged in crevices.
8-8. SPECIFIC PARTS.
8-9. VALVES. Hard carbon may be scraped from valve heads with a smooth edge scraper, preferably while the valve is rotated in a high speed polishing head or lathe. After removal of carbon, polish the stems first with crocus cloth moistened in kerosene, then with dry crocus cloth.
8-10. CYLINDERS. Remove oil and loose material with a solvent by spraying or brushing. Remove carbon from the combustion chambers by soft grit or vapor grit blasting if equipment is available.
Mechanically driven wire brushes are not recommended for this purpose, due to the difficulty of avoiding abrasion of the top ends of the barrels.
8-11. PISTONS. Do not use wire brushes or scrapers of any kind. Soft and moderately hard carbon deposits may yield to solvent action, which should be tried first in preference to harsher methods. If deposits remain, blast the heads with soft grit or by the vapor grit method, first having installed tight-fitting skirt protectors. Ring grooves may be cleaned by pulling through them lengths of binder
32
twine or very narrow strips of crocus cloth. Do not use automotive ring groove scrapers, since the corner radii at the bottoms of the grooves must not be altered, nor any metal removed from the sides.
Discoloration and light scoring need not be removed from piston skirts. The use of abrasive cloth on the skirts is not recommended, because the diameters must not be altered. Heavily scored or burned pistons should be discarded.
8-12. CAMSHAFT, CRANKSHAFT AND PROPELLER
SHAFT. All parts may be degreased by brushing or spraying with mineral spirit solvent. Pay particular attention to threads, oil holes and recesses. Before magnetic inspection, the crankpins, main journals, oil seal race of the crankshaft and all journals, cam lobes and gear mount flange of the camshaft must be smoothed with crocus cloth, moistened in a mineral spirit. If possible, this should be accomplished while shaft is rotated in a high speed lathe (about 100 rpm).
All gum (varnish) depOSits must be removed to permit reliable magnetic indications.
8-13. CONNECTING RODS. If a mineral spirit solvent does not clean these parts thoroughly, they may be immersed in a chemical carbon solvent. They should be immersed only long enough to loosen and soften the deposits without adversely affecting the metal. The parts should be pre- soaked in mineral spirit fortified with organiC solvents to soften the hardest deposits. After removal from the carbon solvent the part should be rinsed or sprayed with mineral spirit.
Do not use a wire brush or other coarse abrasives.
Vapor blasting may be employed if bushings and bearing slots are protected from the abrasive. Discoloration need not be removed from piston pin bushings, and no abrasive cloth or paste should be used. All vapor blast grit or chemical must be removed.
8-14. CRANKCASE AND REDUCTION GEAR HOUS-
ING. If possible, the oil passages should be pressure-flushed with the usual mineral spirit solvent and inspected as well as possible with the aid of a flashlight. If the castings are immersed in an alkaline bath, it is strongly recommended that such treatment be followed by spraying with a jet of wet steam and this followed by flushing of the oil passages with solvent. After the castings have dried, inspect them thoroughly for alkaline reSidues, and remove any traces of scum.
8-15. GEARS. Gears without bushings may be freed of hard deposits by immersion in a caustic stripping bath, when cold solvents are not effective. Bushings are discolored by such treatment, hence bushed gears should be cleaned by other methods such as spraying and/or brushing with a mineral spirit solvent and brushing with a brass wire brush.
8-16. BALL BEARINGS. Soak the ball bearing in solvent or spray with solvent, and dry with compressed air.
Do not spin unlubricated ball bearings or allow an air blast to rotate them. Spinning does not give any indication of the bearing condition and will cause unnecessary wear.
8-17. Immediately after cleaning bare steel parts and ball bearings, spray them with or dip them in clean engine oil, or, for longer storage, in a corrosionpreventive oil mixture. Wrap ball bearings in waxed paper. Wrap or cover other clean parts to protect them from abraSive dust in the air.
33
SECTION IX
9-1. PROTECTION FROM CORROSION.
9-2. Bare steel parts should be covered with oil or a corrosion-preventive oil mixture except during the actual inspection operations. Since inspection involves handling of dry steel parts, it is advisable to apply a fingerprint remover solution after such handling, particular ly since perspiration and skin oils often have a high acid content. Application of lubricating oil or corrosion-preventive mixture will not necessarily stop corrosion from this cause.
9-3. VISUAL INSPECTION.
INSPECTION
parts, as well as running parts and others of major importance, should be inspected visually under good light for surface damage such as nicks, dents, deep scratches, visible cracks, distortion, burned areas, pitting, pick-up of foreign metal and removal of enamel coating. Visual inspection should also determine the need for further cleaning of obscure areas. Inspect all studs for possible bending, looseness or partial removal. Inspect all threaded parts for nicks and other damage to the screw threads. After visual inspection the engine parts should be in three groups: apparently serviceable parts, repairable parts and parts to be discarded.
9-4. Parts without critical dimensions and all small 9-5. MAGNETIC PARTICLE INSPECTION.
Part
Crankshaft
Connecting rod
Camshaft
Piston pin
Rocker arms
Gears to 6 inch diameter
Gears over 6 inch diameter
Shafts
Thru Bolts,
Rod Bolts
TABLE IX MAGNAFlUX INSPECTION DATA
FLUORESCENT METHOD PREFERRED,
WET CONTINUOUS PROCEDURE REQUIRED
* Method of
Magnetization
Ci rcu lar or
Longitudinal
AC or DC
Ampres
2000
Critical Areas
Journals, fi Ilets, oi I holes, thrust flanges, prop flange.
All areas.
Possible
Defects
Fatigue cracks, heat cracks. F lange cracks from prop strike
Fatigue cracks. Circular or
Longitudinal
Circular or
Longitudinal
1500
1500
Circular or
Longitudinal
1000
On Conductor Bar and Single Between
Heads
1000
800
1000 to
1500
Circular or on Center
Conductor
Shaft Circular
Teeth Between
Heads two times
90 0
Circular or
Longitudinal
Circular or
Longitudinal
1000 to
1500
1000 to
1500
500
Lobes, Journals, drilled hole edges.
Shear planes, ends, center.
Pad, socket under side arms and boss.
Teeth, Splines,
Keyways.
Teeth, Splines.
Splines, Keyways
Change of Section.
Threads Under Head.
Heat cracks,
Fatigue cracks
Fatigue cracks
Fatigue cracks.
Fatigue cracks.
Fatigue cracks.
Fatigue cracks, heat cracks.
Fatigue cracks.
34
TABLE IX MAGNAFLUX INSPECTION DATA (cont.)
Part
Method of
Magnetization Amperes
Method of
Inspection
Criitical:
Areas
Possible
Defects
Propeller drive Circular and gear
Quill shaft
Oil pump gears
Longitudinal
Circular and
Longitudinal
Circular
2500
1500
1800
Wet
Continuous
Wet
Continuous
Wet
Continuous
Gear teeth, spline
All areas
Teeth, shaft drive
Fatigue cracks
Fatigue cracks
Fatigue cracks
Starter Shaftgear Circular and
Longitudinal
1500 Wet Teeth, drum shaft Fatigue heat cracks,
Continuous between spur gear Fatigue cracks and drum
Starter worm shaft
Circular 1500 Wet
Continuous
Slotted end around key
Fatigue cracks, slot
Starter worm gear
Longitudinal
9-6. Inspection by the Magnaflux method should be conducted on all ferrous parts listed in Table IX and in accordance with the methods and data in that table before they are inspected dimensionally. The Magnaglow method is recommended whenever the necessary equipment is available. This method employs magnetic particles coated with a fluorescent organic material which may be illuminated with "black light," as in the Zyglo process, to amplify weak indications.
If a crankshaft is doubtful after circular magnetization and inspection, demagnetize and remagnetize it longitudinally for further inspection.
Wet
Residual
Teeth Fatigue cracks
9-9. DIMENSIONAL INSPECTION.
9-10. INSTRUMENTS. Areas of running parts and bushings subj ect to wear should be inspected for serviceable fit with mating parts by comparative linear measurements and alignment measurements, using standard pattern precision measuring instruments such as micrometer calipers, telescoping gauges and dial indicators. The use of a dial-type cylinder bore gauge is recommended in preference to other tools not specifically designed for this purpose.
9-8. This process, commonly known under the trade name of "Zyglo", is recommended for inspecting aluminum alloy parts for invisible cracks. The standard operating technique for the process is applicable.
NOTE
Before magnetic particle inspection, piston pins and valve rocker shafts must be polished with crocus cloth.
Before magnetic particle inspection of any part, plug small holes leading to obscure cavities with tight-fitting wood plugs or with a hard grease which is soluble in lubricating oil to prevent particles from lodging in places from which they would be difficult to remove and which places are not subject to visual inspection. After magnetic particle inspection, remove all such plugs and clean the part thoroughly in solvent; then dry with compressed air. Check for complete demagnetization.
9-7. FLUORESCENT PARTICLE INSPECTION.
9-11. DIMENSIONAL LIMITS. After comparative measurements of mating parts and determination of running clearances, refer to the Table of Limits,
Section XV, and to the Limits and Lubrication Chart to locate the reference number of each fit and the acceptable limits assigned to it. Limits under the column heading "New Parts" are manufacturing limits.
All running clearances in this column apply to mating parts, both of which are new, and the low limit applies in all instances; however, such clearances are allowed to increase with wear to, but not beyond, the values in the column headed "Serviceable Limit".
All press and shrink fits must be maintained as specified in the "New Parts" columns when the inserted member is replaced. Oversize parts are supplied, in some instances, to permit conformity to this requirement.
9-12. ORIGINAL DIMENSIONS. Although comparative measurements of mating parts will determine the serviceability of the fit, it is not always easy to determine which part has worn the most, and in some instances (e.g., main journals in new bearing inserts), accurate measurements of fit are not possible. While no limits of wear on critical dimensions have been assigned to speCific parts in most instances, it is helpful in estimating wear to know the original dimensions. Hence, the following list of manufacturing limits on important dimensions of new parts should be consulted with the serviceability of a specific part is in doubt.
35
3C
TABLE X CRITICAL NEW PART DIMENSIONS
Part Name
Cylinder barrel (Std.)
Cylinder barrel
(.015 O.S.)
Cylinder head
Valve rocker shaft
Val ve rocker bushings
Intake val ve
Exhaust val ve
Piston (Std)
Piston pin assembly
Connecting rod
Crankshaft assembly
Camshaft
Hydraulic valve tappets
Crankcase
Feature
Bore diameter
Bore diameter
Rocker shaft boss bore
Intake valve guide bore
Exhaust val ve guide bore
Outside diameter
Inside diameter
Stem diameter
Length
Stem diameter
Length
*Diameter above top groove
Diameter below top and second groove
Diameter below third groove
Diameter above fourth groove
Diameter below fourth groove
Pin bore diameter
Top ring groove width
Second and third ring grooves width
Fourth ring groove width
Outside diameter
Length (including plugs)
Bushing bore diameter
Bushing center to crankpin center
Main journal diameter
Crankpin diameter
Damper pin bushing I.D. (Not Installed)
Damper pin O.D.
Journal diameter
Cam lobes across heel and toe (large end)
Outside diameter
Camshaft bearings diameter
Tappet guides diameter
* Measure piston diameters at right angles to pin bore.
New Dimension
(Inches)
4.062-4.064
4.077-4.079
0.6089-0.6099
0.3432-0.3442
0.4370-0.4380
0.6082-0.6087
0.6097-0.6107
0.3412-0.3422
4.041-4.057
0.4320-0.4325
4.056-4.072
4.022-4.024
4.026-4.028
4.0476-4.0486
4.051-4.052
3.995-4.005
0.9988-0.9990
0.1000-0.1010
0.0985- 0.0995
0.189-0.190
0.9984-0.9986
4.032-4.052
1.0000-1.0005
6.373-6.377
2.247-2.248
1.936-1.937
0.7312-0.7322
0.4916-0.4921
1.3725-1.3735
1.4842-1.4867
0.7177-0.7182
1.3745-1.3765
0.7187-0.7197
Part Name
Oil pump driver gear
Oil pump driven gear
Oil pump housing and shaft assembly
Propeller shaft
Accessory drive bevel gear
Propeller shaft drive gear
TABLE X CRITICAL NEW PARTS DIMENSIONS (cont.)
Feature
Shaft diameter
Shaft diameter
Dri ven gear shaft hole diameter
Drive gear shaft hole diameter
Gear chamber depth
Bearing diameter
Shaft diameter
Bearing diameter
New Dimension
(I nches)
0.7160-0.7165
0.7160-0.7165
0.717 -0.720
0.717-0.720
1.002-1. 004
2.247-2.248
0.8120-0.8130
2.247-2.248
9-13. SPECIFIC INSPECTIONS.
9-14. CRANKCASE. If any cylinder base nut was loose at disassembly or if any of the cylinder attaching studs are bent, even slightly, or if there i~ definite evidence that a cylinder was loose at any hme, then it is possible that reversal of stress has fatigued the studs and through bolts installed on that cylinder pad, in which case all of them should be replaced. Test for bent studs with a toolmaker's square. When inspecting for casting cracks, pay particular attention to areas on and adjacent to the cylinder mount pads, tappet guides bottom flange and bearing bosses. Look for nicks 'on machined surfaces and scoring in shaft bearings and the shaftgear bushing. The castings must be clamped together at all attaching pOints before dimensional inspection of camshaft bearings.
NOTE
If camshaft bearings are excessively worn, the crankcase may be line bored to accomodate a O. 020 inch oversize camshaft.
9-15. CRANKSHAFT. In addition to magnetic particle, visual and dimensional inspection, the shaft should be mounted on matched "V" blockS on a surface plate
(supporting the front and rear main journals) and rotated under a dial indicator placed to bear on the center main journal in order to detect excessive bending.
9-16. CAMSHAFT. Inspect the journals for scoring, corrosion and overheating, and lobes for pitting atthe toes and evidence of overheating or unusual wear.
9-17. CONNECTING RODS. Use a telescoping gauge and an outside micrometer caliper to measure all worn bushings and locally-replaced bushings. If a bushing was replaced locally, it is also necessary to check its alignment with the big end bearing seat.
The Simplest method of making alignment measurements requires a push fit arbor, preferably at least eight inches long, for the bushing bore and another for the bearing seat, a surface plate, two matched
"V" blocks and two blocks of ground flat steel stock of equal height. To measure tWist, insert the arbors into the rod bores; then lay the big end arbor in the
"V" blocks on the surface plate, and place the ground steel blocks under the ends of the bushing arbor at a measured distance apart. A feeler gauge may be used to detect any clearance at either end under the bushing arbor. This, divided by the separation of the blocks in inches, will give the twist per inch of length.
(Refer to limit in Section XV.) To measure bushing and bearing convergence, mount a dial indicator on a surface gauge, and Swing the rod around the big end arbor to the vertical pOSition against a firm stop.
Pass the indicator over the bushing arbor at pOints an exact number of inches apart. The difference in readings at the two ends, divided by the distance between pOints of measurement, again gives the misalignment per inch, as specified in Section XV.
9-18. GEARS. Inspect gear teeth for signs of overheating and excessive wear. Normal wear produces a fine pOlish on the tooth thrust faces. Alteration of the tooth profiles, score marks and pitting are sufficient cause for rejection.
37
1 - - - - - - 0 - - - - - - < " i
SIZE
STANDARD
OVERSIZE
"0" DIAMETER (iNCHES)
NEW PART WORN PART
MINIMUM MAXIMUM MAXIMUM
4062 4.064
Figure 14. Cylinder Dimensional Drawing
9.911
9.901 use abrasives (including crocus cloth) on the skirt.
If the piston is dimensionally serviceable in other respects and apparently sound, measure side clearances of new rings (after measuring their gaps while squared in the cylinder barrel) by installing the slotted oil control ring in the bottom groove and the three compression rings in the top, second, and third grooves, with part numbers toward the piston head, and inserting various thickness gauges on either side of each ring.
The gaps of rings in the barrel should be measured first so that those selected may be left in the piston grooves, if the grooves are not excessively worn or distorted. When installing rings, take care not to allow their sharp ends to scratch the piston lands. If the cylinder barrel has not been ground to an overSize, and fits the piston within the allowable clearance limit, it is permissible to install either standard or O. 005 inch oversize rings, whichever have the specified gap, as measured with the ring pushed up by the piston head to a point in line with the base flange.
9-20. CYLINDERS. Measure the barrel bore near the top of the ring travel limit and at the open end in the thrust direction, and at right angles to that, in order to d.etect out-of-roundness and wear-in taper.
There should be little or no wear at the open end. Look for bent barrel fins and broken head fins. Barrel fins can be straightened if not badly bent or cracked. A reduction of not over 10% in area of head fins due to breakage is allowable. Look for cracked head fins, and specify repair of any radial crack by drilling a
'ry" notch to remove it. If a radial crack extends to the root of a fin, it may have penetrated the wall; hence, the cylinder should be rejected. If the cylinder base nuts were loose at disassembly, or if the base studs were loose or bent, test the machined side of the cylinder flange for bending, which is cause for rejection. Measure valve' guides for wear, and look for scoring in their bores. Valve seats should be inspected after refacing to make sure that their outside diameters are still less than the valve head diameters. Exhaust valves should be checked for warpage before refacing, and all valves should be measured in length if the stem tips were ground. Inspect the spark plug hole helical coil inserts for looseness, deformation and position. The outer ends should lie in the first full thread of the tapped holes in which they are installed. The spark plug hole helical coil has teeth at the outer end which are forced into the head metal and shouldnotbevisible. If there was any evidence of overheating of cylinder or piston, check as well as possible for turning of the head in relation to the barrel flange.
9-19. PISTONS AND RINGS. Inspect the skirt for long, deep scores which indicate overheating and are sufficient cause for rejection. If a telescoping gauge is used to measure the pin bore, do not allow the spring pin to expand rapidly so as to strike the wall hard. Inspect visually for thorough cleaning, including the oil relief holes in the bottom ring groove. It is not necessary to remove light scores or discoloration from the exterior surfaces, and it is not advisable to
NOTE
Cylinder assemblies with serviceable heads and worn standard-size barrels maybe reground to 0.015 inch oversize.
38
SECTION X
REPAIR AND REPLACEMENT
10-1. GENERAL.
10-2. CASTINGS. Remove the raised edges of nicks in machined surfaces with a hard Arkansas stone.
Unobstructed flat surfaces, such as cover plates, etc., may be returned to true flatness by lapping if a true lap plate is available. Use fine grade lapping compound and move the casting in a figure 8 motion evenly.
10-3. REPAIR OPERATIONS.
10-4. STUD REPLACEMENT. Remove damaged whole studs with a standard pattern stud remover or a small pipe wrench, turning slowly to avoid heating the casting. Remove broken studs which cannot be gripped by drilling on center to the correct diameter for unscrewing them with a splined stud extractor.
(Splined extractors and drills are usually sold in sets. )
Examine the coarse thread end of the damaged stud before discarding it to determine its size. standard studs have no marking. For oversize stud identification refer to Table XI. Clean the tapped hole with solvent and blow dry with compressed air; then examine the thread. If it is not damaged, install the next larger oversize stud. If the old stud was of the maximum oversize, or if the thread is damaged, the hole may be tapped and a helical coil insert installed for a standard-size stud. Coat the new stud's coarse thread with Alcoa thread lube if the hole is blind, or with National Oil Seal compound if the hole goes through to a cavity subject to oil spray. It is advisable to drive the new stud with a "T" handle stud driver. Turn it in slowly, and compare the estimated torque values listed in Section XV. Drive the stud in until it projects a distance equal to the appropriate "Setting
Height" listed in Table XII.
10-5. HELICAL COIL INSERT INSTALLATION.
Helical coil thread inserts are factory installed at various locations. These inserts may be replaced, if damaged, with the aid of a helical coil remover and replacer (See Figure 15).
10-6. Helical coil inserts are manufactured from wire with a diamond shaped cross section forming botha male and female thread. Drilling and tapping depths for inserts, being installed in blind holes, should be equal to twice the nominal diameter of the insert. The helical coil drills and taps must be absolutely perpendicular to the machined surface of the casting.
Drilling should be accomplished in
a
drill press after the casting is firmly supported, clamped and alignment checked. For drilling and tapping aluminum alloy castings, use a lubricant made of one part lard oil and two parts kerosene to prevent overheating the metal and tearing the thread.
10-7. To remove a damaged helical coil use the proper size extracting tool speCified for the nominal thread size. Tap the tool into the insert so the sharp edges get a good "bite". Turn the tool to the left and back the insert out. To install a new insert, blowout all chips and liquid, slide the insert over the slotted end of the mandrel, and engage the driving tang in the mandrel slot. Wind the insert into the tapped hole slowly (See figure 15). The outer end of the insert should lie within the first full thread of the hole. Break off the driving tang with long nose pliers.
10-8. CYLINDERS.
10-9. FIN REPAIRS. Straighten slightly-bent barrel fins with long-nose pliers. File to smooth the edges of broken head fins. If it becomes necessary to cut out a "V" notch to stop a head fin crack, a slotted drill bushing to fit over the fin and a 3/16-inch twist drill may be used to cut the notch. Its apex must be rounded and the edges should also be rounded. If such repairs and previous breakage have removed as much as 10% ofthe total head fin area, the cylinder assembly has reached the limit of such repair.
10-10. SPARK PLUG HOLE HELICAL COIL INSERTS.
Before attempting to back out a damaged insert, use a sharp pointed tool to pry the teeth at outer end away from the cylinder head metal. Tap a helical coil extracting tool into the insert until it has a good bite.
Place a new helical coil in the cut-out side of the installing tool sleeve with its driving tang toward the threaded end. Engage the tang with the slotted end of the driving mandrel and wind the insert into the sleeve thread thus compreSSing it. Hold the sleeve so that the helical coil can be seen through the slot in the threaded end, and turn the mandrel crank until the insert starts into the cylinder head hole. If the sleeve is then not in contact with the head surface, grip sleeve and mandrel and turn until the sleeve touches lightly. Wind the helical coil into the cylinder head until its toothed end lies just within the first full thread. The teeth should be in position to enter the depressions made by the original insert. If driven too far, the insert will emerge in the combustion chamber and will have to bewound on through. When the helical coil is in correct position, use long nose pliers to bend the driving tang back and forth across the hole until it breaks off at the notch. Coat an expanding tool threaded end with a mixture of white lead and oil, and screw it into the new insert until its final thread forces the teeth firmly into the cylinder head metal.
39
40
Typical
Part No.
XXXXXX
XXXXXXP003
XXXXXXP006
XXXX:X:X:P009 xxxxxxp007
XXXXXXP012
Oversize on
Pitch Dia. of
Coarse Thread
( Inches)
Standard
.003
.006
.009
.007
.012
TABLE XI STUD IDENTIFICATION
Optional Identification
Marks on Coarse Thread End
Stamped Machined
None
~
~
(@
~
@)
Figure
No.
11
11
11
11
11
13
13
13
13
13
10
11
11
11
11
11
11
10
10
10
10
10
10
6
6
8
8
9
9
10
TABLE XII STUD SETTING HEIGHTS
Index
No.
47
48
49
50
51
56
98
99
100
101
46
24
42
49
50
29
32
94
95
96
97
37
38
39
40
40
52
53
54
55 location
Vacuum pump pad
Starting Motor pad
Oil sump manifold riser pad
Oil sump carburetor pad
Cylinder inta...1;:e pipe pad
Cylinder exhaust pad
Front accessory drive cage pad
Crankshaft cover pad
Propeller shaft cage pad
Crankcase breather pad
Crankcase breather pad
Oil cooler pad
Vacuum pump drive cover pad
Propeller governor pad
Reduction gear housing pad
Cylinder pad
Cylinder pad
Pushrod housing flange pad
Engine mount bracket pad
Crankcase cover pad
Crankcase cover pad
Crankcase cover pad
Reduction gear housing pad
Reduction gear housing pad
Oil sump mount pad
Generator pad
Magneto pad
Tachometer drive pad
Starter pad (Models -A and -C)
Starter pad (Models - D and -E)
Thread Size
1/4-20 x 1/4-24
3/8-16 x 3/8-24
1/4-20 x 1/4-24
5/16-18 x 5/16-24
1/4-20 x 1/4-24
5/16-18 x 5/16-24
1/4-20 x 1/4-24
1/4-20 x 1/4-24
5/16-18 x 5/16-24
1/4-20 x 1/4-24
1/4-20 x 1/4-24
1/4-20 x 1/4-24
1/4-20 x 1/4-24
5/16-18 x 5/16-24
5/16-18 x 5/16-24
3/8-16 x 3/8-24
7/16-14 x 7/16-20
1/4-20 x 1/4-28
3/8-16 x 3/8-24
5/16-18 x 5/16-24
5/16-18 x 5/16-24
5/16-18 x 5/16-24
5/16-18 x 5/16-24
5/16-18 x 5/16-24
1/4-20 x 1/4-24
5/16-18 x 5/16-24
5/16-18 x 5/16-24
1/4-20 x 1/4-28
5/16-18 x 5/16-24
5/16-18 x 5/16-24
Quantity
1
14
3
4
1
2
2
3
3
3
9
12
12
18
2
8
4
4
8
4
4
2
2
2
4
2
4
4
8
2
Setting
Height
0.62
0.88
0.72
1. 03
0.66
0.75
0.56
0.94
0.78
0.62
1. 00
0.81
0.88
2.00
5. 50
1. 25
0.75
1. 36
0.75
0.62
0.75
0.62
1. 38
0.84
0.78
0.81
1. 00
0.69
1. 00
3.25
I dentificatio n
Color Code
None
RED
BLUE
GREEN
BLUE
GREEN
Figure 15. Installing Helical Coil Inserts
10-11. VALVE GUIDES. If the valve guides are to be replaced, the new guides must be installed so that the valve stem hole is accurately square and aligned with the valve seat. When pressing or driving out a worn guide, the cylinder assembly should be firmly supported in the inverted position with space below to allow the guide to drop out. The driving tool should pilot inside the guide and drive on its inner end. All carbon must be removed from the guide's inner end.
If the cylinder head hole is not scored or enlarged, a standard size guide may be installed as a replacement. If the head hole is rough, it must be broached or reamed to a diameter smaller than the next larger oversize guide by the amount of interference ("T") specified in Section XV. Valve guides are supplied in oversizes of 0.005, O. 010 and 0.020 inch. The cylinder assembly must be supported firmly while the new guide is driven or pressed into place with a driver, which fits over its end and bears on the filleted flange. Driving on the guide end will spread it. Before installing a new guide, dip the end to be inserted in engine lubricating oil. Watch for peeling of bronze and correct misalignment which causes it. It is not necessary to freeze the new guide before installing it.
10-12. VALVE AND VALVE SEAT REFACING.
Numerous grinding machines are marketed for these purposes. Operating instructions are furnished with each machine and need not be repeated here, except that certain precautions must be observed. These are: a. Use only soft stones on these hard alloy metals to avoid overheating and surface roughness. b. Keep stones trued to angles speCified in Section XV. c. Use the coolant system at all times when grinding. d. Replace chucks and pilots whenever results indicate excessive wear. e. Do not grind seats more than afew seconds without lifting the stone. Keep the grinding head of the valvefaCing machine in constant motion back and forth across the valve face without running off the edges. f. Break sharp edges at the outside of the valve faces with a hard Arkansas stone or a fine India stone. The face must never run into the roundecf edge of the head. Discard valves which must be ground to this condition to clean up.
10-13. After the valve seat has been ground, the concentricity, angle and angular relationship of the seat to the valve guide may be determined by the use of a blueing gauge. Coat the cone surface with a very thin film of Prussian blue oil base pigment, and insert the gauge end into the valve guide until the cone surface can be rotated in contact with the valve seat. The tool should have a flat, marking the limiting diameter of the seat. If regrinding has excessively enlarged the seat, it may be reduced once only with a stone which makes an angle of 6So - 78 0 with the stem axis.
10-14. After grinding all valve seats, insert two refaced valves in the guides of each cylinder, with a light spring under each valve, and a film of fine grade valve lapping compound on each valve face.
Use an automatic type valve lapping tool with an extended stem equipped with a suction cup, to lap the refaced valves and reground seats to line contact at the outer edge only, lifting the tool every few seconds to redistribute the compound. Carefully wash off all abrasive particles after this operation; then keep the valves with the cylinders in which they were lapped.
10-15. CYLINDER WALLS. Glazed cylinder walls will not seat new chromefaced piston rings quickly; therefore, they should be roughened by honing with No. 400 grit stones in a spring-loaded honing head or by abrasion with Aloxite cloth of No. 100 grit. The fine scratches produced should be crossed and those running in each direction should form an angle of
35 0 -55 0 with the end of the barrel.
10-16. VALVE ROCKERS. Worn bushings may be driven out with a suitable drift, and if properly designed, the same tool may be used to drive in new bushings. The rocker must be supported on a ring which will allow the old bushing to pass through.
Press the new bushing in flush with the rocker hub after dipping it in clean lubricating oil. Ream the new bushing to the diameter specified in paragraph
9-12. It is advisable to plug the oil holes with beeswax before reaming. Be sure to remove the wax after reaming. Lightly break the sharp edge at each end.
41
SECTION A-A
THESE SURFACE MUST
BE SQUARE AND PARALLEL
WITH BORE WITHIN
0.002 I N. FULL
INDICATOR READING
+-0.6107 IN DIA
0.6097' .
B b, If damper pin bushings in shaft or counterweights are worn, drive out or press out old bushings, and drive or press in replacements which have been chilled. Be sure to use correct bushings. c. Plug oil holes with soluble grease or fibre plugs before Magnaflux inspection. Remove plugs after inspection. d. Excessively worn shafts must be reground to . 010 inch undersize and re-nitrided. Undamaged shafts may be exchanged.
(1) Excessive localized brinelling of the crankshaft dampener pin bushings can affect propeller blade tip stresses. It is therefore recommended that at each major overhaul the pin bushings be inspected and replacedas required. This applies to both the dampener bushings and the crankshaft blade bushings.
SECTION B-B
THIS SURFACE
MUST BE PARALLEL
TO SHAFT HOLE
WITHIN 0.004 IN.
Figure 16. Rocker Arm Bearing Dimensions
10-17. CONNECTING RODS.
A c B
~----,.~.
In order to assure good dynamic balance, connecting rod assemblies for new engines are selected in sets with a maximum weight variation of Y2 ounce in opposite bays. This limit cannot be maintained if material is removed from any of the original in a set.
H a connecting rod must be replaced, specify the weight limits when ordering.
10-18. PISTON PIN BUSHING REPLACEMENT. The connecting rod does not need to be heated for this operation. Press out the old bushing in an arbor press, using a drift only slightly smaller than the bushing O.D. Make sure that the rod bore is smooth.
Dip the new bushing in engine lubricating oil before placing it in position, and locate the split as illustrated in figure 18. (The position number is stamped on the rod and cap bosses on the far side.) Ream or bore the new bushing to the size limits given in paragraph 9-12, and check alignment as described in paragraph 9-17. The center-to-center distance given in paragraph 9-12 will be held automatically ifthe bore is centered in the new bushing.
10-19. CRANKSHAFT ASSEMBLY. a. Before Magnaflux inspection, polish journals and crankpins. stone any nicks on finished surfaces.
42
1. The C measurement should be the point of maximum diameter, whichis generally a point perpendicular to the lengthwise centerline of the crankshaft.
2. Measurements A and B should be taken at points approximately 60° either side of point C.
3. After removing the bushings from the dampeners or the crankshaft blades, measure the inside diameter of the holes. Select a replacement bushing which will give an interference fit of
0.0015 to 0.005 inch.
Figure 17. Measurement of Dampener Bushing
(2) Inspect in the following manner: Measure the inside diameter of the bushing across paints A, Band
C, Take the average of A and B and deduct this from
C, If the difference exceeds 0,001 inch, the bushing should be replaced,
(3) Replacement bushings are available in standard,
0.0015, 0.003 and 0.005 inch oversize on the outside diameter.
f
A
-110005
10000 r l
BUSHING HOLE MUST BE
MAINTAINED WITHIN p;;==i===p;
I
,
0005 IN OUT OF
~-+---~~~m.
SECTION A-A
~
I THESE HOLES MUST 8E
WITHIN ,0005 PER
LENGTH
6377
6373 -"
",-1--1 i
I
0005,
MAX
I L
J_
1
1-
A.45
Q
-.J
SIDE VIEW
NOTE ALL DIMENSIONS IN INCHES
END VIEW
Figure 18. Connecting Rod Bushing Dimensions
(4) A special tool for removing and replacing these bushings has been developed by Borrough's Tool and
Equipment Corporation, 2429 North Burdick Street,
Kalamazoo, Michigan. It is recommended that this tool only be used for these operations. Removing and replacing bushings with makeshift tools and methods can result in irreparable damage to the crankshaft and/ or dampeners. Order tool direct from Borrough' s
Tool and Equipment Corporation.
NOTE
Crankshafts that are out of specified limits may be reground and renitrided to 0.010 inch undersize.
Crankshaft counterweights are matched inpairs with a maximum weight variation of 2 grams, and the complete crankshaft and counterweights assembly is dynamically balanced. As a result, if either counterweight is damaged it will be necessary to discard both on that cheek and to procure a matched pair for replacement.
10-21. TACHOMETER DRIVE HOUSING. Removethe oil seal with a suitable oil seal puller. If the housing counterbore is scored, smooth it with crocus cloth.
Spread a film of Lubriplate grease on the periphery of a new seal. Then press the seal squarely into the housing with its lip pointed outward, facing the oil source.
10-22. OIL PUMP ASSEMBLY. Except for stoning down nicks on parting flanges and replacement of worn parts, no repairs to the pump assembly are contemplated. The pump gear chamber must not be enlarged; hence, if it is scored the housing must be discarded. Heavy scoring on the gear contact area of the tachometer drive and pump cover renders this part unserviceable, unless the parting surface can be lapped smooth and perfectly flat.
10-23. IGNITION CABLES. Normally, all ignition cable assemblies or both harness assemblies should be replaced at each overhaul. If cable assemblies are replaced, detach all cables from the high tension outlet by unscrewing the coupling nuts and withdrawing the cables. Observe the "1" mark on the exterior side of each outlet plate adjacent to the No. 1 cable outlet hole.
10-23A. STARTER ADAPTER. (See figure 6.) a. Do not attempt to replace the adapter sleeve if surface roughness is less than specified in Section
XV. b. If the needle bearing (41) is to be replaced, support the starting motor mounting flange on a wood block; then, drive the bearing from the adapter by inserting a drift through the bearing boss opening.
A bearing installer may be locally manufactured in accordance with the dimensions specified in figure
19. When installing the bearing, make certain it is properly aligned with the bore. Hold the adapter as illustrated in figure 20 and drive the installer with a medium weight hammer. c. If needle bearing (31) is to be replaced, press it from worm wheel (32), then install a new bearing so it is recessed 0.009 inch from either end of worm wheel hub. d. If bushing (26) is to be replaced, support the cover on the table of an arbor press with studs upward.
Make certain that clearance below the cover is sufficient to permit the bushing to fall free when it is separated from the cover. Mter the bushing is removed use a pair of diagonal cutters to pull pin (25).
Mter the new bushing is installed, drill a new hole
(0. 058-0.060 dia. X 0.31 inch depth) through the bushing flange and into the cover hub. Drive a new pin (25) into the hole. Pin must be flush with or below surface of bushing flange. e. Install a new oil seal (23).
BAR STOCK
\cOLD ROLLED STEEL
\ .010 MAX. R
.5625
.5620
Note: All dimensions in inches.
Figure 19. Starter Adapter Installer
10-24. PROTECTIVE COATINGS.
43
Figure 20. Installing Starter Adapter Bearing
10-25. The manufacturer protects aluminum parts from corrosion by coating them with "Alodine 1200".
This material is a product of the American Paint and
Chemical Company, Ambler, Penn. "Alodine" coated parts are easily distinguished by their gold color. In order to maintain a uniform appearance, the manufacturer is painting certain steel and magnesium parts with gold colored enamel.
10-26. REPAIR OF ENAMEL SURFACES.
10-27. Ferrous parts when painted with gold enamel will be baked with infra-red equipment, for 15 minutes at 275 0 -285
0
F following application of each coat.
Magnesium parts will be pickled and primed, then baked, with infra-red equipment, for 15 minutes at
275 0 -285 0 F following application of each coat of enamel.
NOTE
If a part which was originally "Alodized" is to be refinished with enamel, it will not be necessary to apply zinc chromate primer except to the surface areas completely stripped of "Alodine" .
Before application of primer and enamel to a part, c:arefully mask all connection jOints and mating- surfaces.
10-28. "ALODIZING" AND REPAIR OF "ALODIZED"
44
SURFACES.
No primer of enamel is permissible on interior surfaces of fuel pump adapter, tachometer and oil pump housing, oil sump, crankcase or any other parts contacted by eng-ine lubricating oil after assembly.
10-29. GENERAL. Aluminum alloy castings, sheet metal and tubing are protected from corrosion by treating all surfaces of the parts with" Alodine 1200"
(American Paint and Chemical Co., Ambler, Pa.).
"Alodine", unlike enamel or primer, will not flake or peel off to contaminate engine lubricating oil; therefore, corrosion protection can be afforded to all interior aluminum surfaces and parts. If an enamel coating is required for a part previously treated with
"Alodine", application of a primer before painting is not necessary. "Alodizing" will be performed after all machining and/or repair operations have been completed. The surface color of an "Alodized" part may vary from light gold to dark brown. When a part is treated with "Alodine 1200" the thickness of the film, or buildup, on the mating or bearing surfaces is so fine that the effect on dimensional tolerances is negligible.
10-30. APPLICATION OF "ALODINE 1200". In the event the original finish of an aluminum part has deteriorated or been removed, the part may be
"Alodized" as described in "Alodine" manufacturers
Technical Service DataSheetNo.AL-1200-D. Wrought or die cast (smooth surface) parts, such as valve rocker covers and intake tubes, should be tumbled or sand blasted to roughen before treatment.
10-31. REPAIR OF ALODIZED SURFACES. If "Alodized" parts have been remachined, rubbed with abraSives or scratched in handling so as to expose areas of bare aluminum, the surface may be repaired by local application of "Alodine" solution in the following steps: a. Clean the parts' bare area thoroughly with carbon tetrachloride. Do not under any circumstances use an oil base solvent such as General Specification, P-S-
661, TT-291 or alkaline cleaner. b. Mix a small quantity of hot water (180 0 F) with
1-1/2 to 2 ounces of "Alodine 1200" powder to form a paste, then gradually dilute with hot water until a solution of one gallon is attained. This solution is to be adjusted with nitric acid addition to a PH value of
1.6 (1.5 to 1. 7). c. Application shall be made, with a rubber set paint brUSh, in a manner so the solution flows over the area. d. Allow solution to remain on the part from one to five minutes or until color of the new film is approximately the same as the original. e. Flush part with clear water and dry with air. Do not blast or rub with cloth to dry new film area. If color is too light, repeat steps "c" and "d" until desired color is obtained.
NOTE
If "Alodine" does not adhere to metal, a more severe cleaning method must be used. A solution of 12 to 16 ounces of Oakite No. 61 per one gallon of water is preferred. Apply and remove the solution with caution because an alkaline cleaner of this type will remove any
"Alodine" film previously applied. Remove cleaning solution thoroughly with plenty of hot water and vigorous brushing.
SECTION XI
ASSEMBLY OF SUBASSEMBLIES
11-1. GENERAL.
11-2. NEW PARTS. Parts which require protection from atmospheric dust and moisture are wrapped or boxed individually or in sets. These should not be unpacked until they are to be installed. This is especially true of precision bearing inserts and anti-friction bearings. Check other new parts on receipt for damage done in transit. Refer to Section IV
& V of the Parts Catalog for part numbers of the complete gasket set, the main bearing set, the piston ring set and tubes of lightweight TiteSeal gasket paste, all of which should be on hand when work is started.
Use only new spring lock washers, tab washers, elastic stop nuts, cotter pins and annealed, corrosion-resistant lock wire.
11-3. TIGHTENING TORQUES. The accuracy of any torque-indicating wrench depends on a smooth application of force. Do not backup a nut or bolt and leave it in that condition. If a part is aCCidentally tightened too much, loosen it and retighten to a value within the specified limits. If a nut slot must be aligned with a cotter pin hole, tighten the nut to the minimum specified torque, and check for alignment. If necessary, tighten further until alignment is achieved or the maximum allowable torque reached, whichever occurs first. If the alignment cannot be obtained within allowable torque limits, substitute another serviceable part and tighten it in the same manner as before. If a cotter pin hole in a stud lies beyond the nut slots when the nut has been tightened correctly, then either the stud has been improperly installed or has backed out, or the attached part has been reduced in thickness, or either the nut or its washer is not the correct part for that location. The situation must be corrected by whatever replacement is indicated by inspection.
NOTE
Tightening-torque limits specified in Section
XV are based on oiled threads, but are not applicable when special thread lubricant is applied.
11-4. FINAL CLEANING. Immediately before asassembling a group of parts they should be washed in or sprayed with clean solvent and dried with dehydrated compressed air.
11-5. LUBRICATION. Immediately after final cleaning and before installation, coat all bare steel surfaces and journals with clean engine lubricating oil, except where special lubricants are mentioned in the text.
In some instances, where gears and other running parts are accessible after assembly in a housing, additional oil should be applied to assure full coverage. Before installing tapered pipe plugs or straight thread plugs, and to prevent seizure and leakage of oil, coat the first three male threads' with Penola anti-seize compound. This compound is fuel and oil resistant and has good lubricating properties.
11-6. SPECIFIC ASSEMBLY OPERATIONS.
11-6A. STARTER ADAPTER. (See figure 6.) a. Install bearing (39) on shaft (40). Install woodruff key (38), worm gear (37) and bushing (36). Align bushing and shaft holes, then install a new pin (35).
Insert worm gear and shaft assembly into adapter, then install retaining ring (34). b. Install spring (30) on worm wheel (32). Turn spring, so it tends to unwind, until offset end dro~s into gear hub groove. Position spring on gear so screw notch is aligned with screw hole in gear web.
Install a new tab washer (29) and screw (28). c. Slide starter shaftgear (33) through front of adapter housing (44). Lubricate spring, sleeve and shaftgear liberally with clean oil. Press worm wheel, bearing and spring assembly down onto s haftg ear •
Make certain worm wheel and worm gear teeth are aligned. d. Install a new "0" ring (22) on cover assembly.
Slide cover and seal assembly over shaft. Install one set of attaching parts (21, 20, 19). e. Apply a film of Tite Seal compound to both sides of gasket (18) before installing it on cover studs (24).
Install cover (17) and four sets of attaching parts
(16, 15, 14).
11-7. GENERATOR DRIVE COUPLING. (See figure
7. ) a. Press into the generator housing a new oil seal
(52) with the seal lip outward. Then install a new
"0" ring (51). b. Lubricate lip of oil seal and polished surface of hub with a film of Gredag No. 44 grease. c. Slide hub (50) over shaft and key and push slowly through seal lip to seat. d .. Insert two new rubber bushings (48) into the retainer (49) so that rounded edges on each side of shaft cut-out face outward. e. Slide retainer fUld bushings assembly on to generator shaft and seat in hub slot.
45
f. Slide gear (46) onto shaft so gear tongue is inserted between rubber bushings. g. Install and tighten nut (45) to 175 in. lb. torque.
Nut may be tightened further if necessary to align nut slots with shaft cotter pin hole, but do not exceed 200 in. lb. h. Install cotter pin (44),
11-8. CRANKCASE COVER. (See figure 13.) a. Apply a film Penola anti-seize compound to threads of plugs (35, 36) before installing. Install oil pressure relief valve plunger (21), spring (20), a new gasket (19) and the cap (18). Place new gaskets
(34) on two plugs (33) and install plugs in bottom of cover (44). b. Place oil pump drive gear (32) in lower bore of cover, with square shaft end forward. Install driven gear (31) in upper bore with slotted shaft end projecting rearward. Position pump cover (30) in place, install tab washers (29) and screws (28). c. Press a new seal (26) into the tachometer drive housing (27) with the seal lip toward the mounting flange. Impregnate a new gasket (24) with lightweight
Tite Seal compound and place it over the case studs.
Apply a film of Gredag No. 44 grease to the proj e cting slotted shaft; then car efully slide the tach-
0meter drive housing over it into place. Secure the housing with three sets of attaching parts (23, 22).
Install cap (25). d. Place a new gasket (13) on the oil screen (12) and screw the screen into the cover. Place a new gasket (15) on the plug (14), and install plug in screen (16). Place a new gasket (17) on the screen
(16); then install the assembly in the cover.
11-9. CYLINDERS. Assemble parts to make up each of the six cylinder and valve assemblies in the manner outlined below. Each cylinder should have a different position number (1 through 6) stamped on the edge of its base flange, which will be on top when installed. These numbers should be found on original cylinders, but they must be stamped on new parts. Mter assembly, cylinders should be laid on the bench in a row in the order of position numbers. a. Spread a film of Lubriplate No. 707 grease on the stems of the two valves previously lapped to the cylinder seats, and insert these into their guides. b. Hold the valve stems, and lift the cylinder onto a post which will support the valve heads. Clamp the cylinder base flange to prevent it from riSing.
Again coat the valve stems with Lubriplate No. 707 grease. c. Slide rocker shafts into the cylinder bosses. d. Place the valve spring retainers over the guides, cupped sides up, then install two sets of inner and outer springs and the spring seat.
Figure 21. Installation of Valve Spring Locks e. Using the same type of spring compressor as for disassembly, compress, in turn, the sets of springs, and insert the stem locks (See figure 21). The springs should be depressed only enough to admit the keys to the stem grooves. If they drop too far, the locks may be cocked and nick the stems when the springs are released. Make sure that the locks are seated in the stem grooves before releasing pressure. Do not allow the compressing tool to cock the seats so as to contact the stems, since they can cause score marks. f. Remove the cylinder from the assembly fixture.
Set it basedown on the bench, and with a rawhide mallet, strike each valve stem firmly to seat the keys. g. Slide out the rocker shafts far enough to admit the rocker arms. Coat the rocker arm feet with
Lubriplate 707, and install the rocker shafts and arms.
All GO-300 model engines, with the exception of a few very early model GO-300-A engines, are equipped with INTAKE valve rocker arms which do not have an oil squirt hole at the top of the rocker arm foot. Extreme care should be exercised to make certain that a rocker arm without the oil squirt hole is NOT installed at the EXHAUST valve position.
46
h. Lay all cylinders upside down on the bench, resting on the sloped head fins. Place a new base packing on the skirt of each cylinder, and push it against the flange. See that none are twisted. i. Coat the cylinder bore walls thoroughly with
Lubriplate No. 130AAA or castor oil. j. Place two hose clamps on each pushrod housing; then install a new rubber pushrod housing connector on each pushrod housing.
11-10. PISTON AND RINGS. Piston position numbers are stamped on the rims of their heads on the side which is to go toward the propeller
0
The part number is stamped on the rim at right angles to the pin hole and should be on top when installed. Install rings on pistons, lubricate pistons and rings with
Lubriplate No. 130AAA. Space ring gaps 90 apart with the oil control ring gaps so that they will be on top. Dip piston pin in castor oil and insert into piston.
11-11. PROPELLER REDUCTION GEAR UNIT. (See figure 10.) a. Ascertain that all studs, plugs, thread inserts and bushings are properly installed. b. For GO-300-A and -B engines, impregnate a new gasket (48) with Tite Seal compound. Install the gas}<;:et, breather (47) and secure with four sets of attaching parts (46, 45, 44). c. For GO-300-A, -B and -C engines, dip the gear
(72) in clean lubricating oil and insert into bushing
(88). Ascertain that bearing (68) is properly installed in cage (69). Install a new "0" ring (67). Dip the gear (66) in clean lubricating oil, insert its end into the ball bearing, then install the assembly in the housing (104). Make certain gear teeth are properly meshed. Secure cage with two sets of attaching parts (65, 64, 63). Impregnate a new gasket (62) with Tite Seal compound. Install gasket, cover (61) and four sets of attaching parts ( 60, 59, 58). d. For GO-300-D and -E engines, impregnate a new gasket (71) with Tite Seal compound. Install the gasket and cover (70), then secure with two sets of attaching parts (65,64,63) installed on housing studs. e. For GO-300-B and -E engines, install the oil transfer tube (83) and secure with two sets of attaching parts (81, 82). Install the governor drive gear (80), the thrust washer (79) and retaining ring (78). Impregnate a new gasket (77) with Tite
Seal compound. Install the gasket, cover (76) and four sets of attaching parts (75, 74, 73). Install collar (40) and washer (39) in propeller shaft plug
(41). Install retaining ring (38). t'lsert the assembly into the propeller shaft and install retaining ring
(37) . f. For all models of this engine, remove the spring
(33) from a new propeller shaft oil seal (34) and unhook its ends. g. Coat the lip of the seal with Gredag No. 44 grease; then twist the seal and slide it over the propeller shaft with the felt side toward the flange. (See figure
22.) Bring the ends back together. h. Pass the spring around the propeller shaft on the recessed side of the seal and hook its ends together.
Lift spring into seal recess at the split and work the remainder in progressively by moving the fingers in both directions from the starting point. (See figure
23). Make certain that spring is seated in recess all around. The hooked ends of the spring should be opposite the seal split. i. Install new thrust bearing inserts (29, 31, figure
10)in each cage half (30, 32); then coat each insert with a film of Gredag No. 44 grease. Apply a film of Tite Seal compound around the oil seal recess. j. Hold cage halves in position around propeller shaft and install two sets each of attaching parts
(20 through 28). Tighten these parts to the specified torque contained in Section XV. Place in position on the cage a new "0" ring (18) and "0" ring (19). k. Install plug (51) with a new gasket (52) in the cover (56). Impregnate a new gasket (57) with Tite
Seal compound, place it on the housing, install cover
(56) and secure with four sets of attaching parts
(55, 54, 53).
1. Install the Vernatherm valve (49) with a new gasket (50).
11-12. CRANKSHAFT AND CONNECTING RODS. a. Lay the shaft on two notched 2 x 4 inch wood blocks under its front and rear journals. b. Layout the six connecting rods, caps, bolts and nuts opposite the crankpins according to stamped pOSition numbers on bolt bosses, starting with No. 1 at the rear end and proceeding in numerical order. c. Obtain a set of twelve new crankpin bearing inserts and make sure they are thoroughly clean.
Snap an insert into each rod and each cap so that their ends project the same small distance. d. Lubricate with Sunoco Way Oil and install each connecting rod and cap with the position numbers on top when the odd-numbered rods are extended to the right, and even numbers to the left. Attach them with the special bolts and hex nuts. Tighten the nuts to specified torque, and secure each with a cotter pin.
Bend one leg of each pin down snug against the nut flat and the other over and against the bolt end. e. Install retaining plates and Truarc rings in the pin holes in one side of each counterweight. Attach the counterweights to the crankshaft blades with two pins in each; then install the retaining plates and
Truarc rings on the other sides. f. Heat the crankshaft gear to 300
0
F prior to installation on the crankshaft. Align the dowel hole on the gear with the shaft dowel and then tap the gear on. Secure the gear to the shaft with four hex drilled-head bolts and torque to the value specified in Section XV.
Lock the screw heads together in pairs with lock wire.
47
11-13. CAMSHAFT. The gear can be installed on the camshaft flange in only one position, due to the offset position of one screw hole. Attach the gear with four hex drilled-head bolts, and secure these in pairs with lock wire.
11-14. CRANKCASE. (See figure 11. ) a. Ascertain that all plugs, studs, dowels, thread inserts and 011 gauge supports are properly installed. b. Position the crankcase halves (68, 69), parting flange down, on a clean, smooth top workbench. c. Impregnate six new gaskets (34) with lightweight
TiteSeal compound, place on crankcase studs, install a pushrod housing flange (33) over each gasket and secure each flange with three sets of attaching parts
(32, 31, 30). d. Install the engine mount brackets (39 through 42) and secure each with two sets of attaching parts
(37, 36, 35). e. Turn crankcase halves over so parting flanges are up. Wipe out each bearing boss carefully. f. Install the main bearing inserts (43, 44, 45). g. Position the crankcase halves so that a pushrod may be inserted up through the pushrod housing flange to project above the valve lifter guide. Hold the pushrod with one hand and carefully invert a complete valve lifter onto the projecting pushrod so the socket is seated on the ball end; then slowly lower the pushrod until the valve lifter body is fully seated in its guide.
Repeat this operation until all lifters are installed. h. Wrap a discarded cylinder base packing around each pair of pushrod bodies, in the right crankcase, pass the slack of the packing through the cylinder opening of the case and hook it over the pushrod housing flange.
Figure 22. Installing Propeller Shaft Oil Seal
Figure 23. Installing Propeller Shaft Oil Seal Spring
48
SECTION XII
FINAL ASSEMBLY
12-1. GENERAL.
12-2. LUBRICATION. Apply clean engine lubricating oil liberally to all bare steel surfaces, journals, bearings and bushings before and/or after installation, depending on accessibility, except where special lubricants are mentioned. Lubricate all new rubber
"0" rings and packings with a lightfilm of clean engine lubricating oil.
12-3. TIGHTENING TORQUES. Instructions in paragraph 11-3 are applicable to final assembly work.
12-4. Deleted
12-5. CLEARANCES. When possible, measure clearances of running parts as they are installed. When end clearances, side clearances and backlashes cannot be measured with normal thickness gauges due to the inaccessible positions of the parts, test for binding and excessive looseness as well as possible by moving the running part.
12-6. COVERS. Unless the atmosphere is unusually free of dust and airborne grit, it is advisable to cover openings as soon as possible and to cover assemblies and the partial engine assembly whenever they are not in the process of being assembled. Cover all openings into which small parts might be dropped.
12-7. CRANKCASE. (See figure 12.) a. Attach the mount brackets on the left crankcase to the assembly stand in the same way as during disassembly, and place the support (23) under the casting. b. Lubricate all main bearing inserts and crankshaft journals. Lift the shaft assembly by the number 1 connecting rod and front end, while a second person holds up the number 3 and 5 connecting rods. Lower the assembly into position in the left crankcase bearings. The connecting rod position numbers should automatically be toward the upper case flange if erly installed. Lay the odd-numbered connecting rods on the upper case flange. c. Lay the camshaft assembly in its bearings in the left case, meshing the spur gear teeth with those of the crankshaft gear, so that the timing marks will align as illustrated in figure 24. d. With a feeler gauge, measure the crankshaft end clearance at either end of the thrust bearing with the shaft pushed toward that end. Similarly, measure the camshaft end clearance at either end of its rear bearing. e. Observe that the quill shaft has a diagonal relief, on the crankshaft end, to provide clearance for the crankshaft front oil transfer tube. The crankshaft front flange should be marked to indicate location of the tube. Align the quill shaft relief with the crankshaft mark and insert the quill shaft into the crankshaft. f. Observe on the front of the quill shaft that two splines are punch marked and on the front end of the propeller drive shaft gear (4) one of the splines is also punch marked. Align the gear and shaft so that the marked gear spline is located between the two shaft splines, and slide the gear into position. Lift the crankshaft slightly so gear can be seated properly. g. Install the plate (2), screws (3) and retaining ring (1). Tighten the bolts to the torque specified in
Section XV and install lock wire. h. Use lightweight TiteSeal and spread in a thin but continuous film all around the left crankcase parting flange, taking care not to get it on other parts. Lay a length of No. 50 silk thread on the parting flange as illustrated (18). The thread should be inside the bolt holes but never on the edge.
1. Install a new "0" ring on each side of the dowel section of each of the eight through bolts (6) and place in through bolt holes of left crankcase as illustrated. j. Stand up the oddilumbered connecting rods,and install the starter pinion pivot (24 or 28, figure 11) or starter shaft bearing (29, figure 11). Lay the right crankcase subassembly on the left case.
12-8. (See figure 11.) a. Place one set of attaching parts (14, 15,16)on one end of two each through bolts (20, 21). Insert through bolts up through the left crankcase and install a second set of attaching parts (14, 15, 16). The two longer bolts (21) serve as engine bracket attaching parts. b. Install ten sets of parts (6, 7) in the upper parting flange. For GO-300-A,-B,-C and -D engines, the two longer bolts are to be placed in the fifth and sixth holes, counting from the front. For GO -300-E engines, install bolts (8) in the fifth and sixth holes. Place a spacer (5) over each of the lifting eye (4) attaching holes, hold eye in place on the fifth and sixth bolts and install one set of attaching parts (1, 2) on the sixth bolt. A two-wire ignition cable bracket is to be installed on fifth bolt later. c. Install two sets of attaching parts (10, 11, 12, 13) and then tighten all attaching parts installed up to this point, to the torques specified in Section XV. Install cotter pins (9). Install the retainer (27) and attaching parts (26, 25). d. Install the right hand mount bracket-to-stand adapters. Tighten attaching parts firmly. Rotate engine bed to place engine in upright position. Do not allow connecting rods to strike chamfers of cylinder mount pads while turning engine.
12-9. PROPELLER REDUCTION GEAR UNIT. (See figure 10.)
49
Figure 24. Alignment of Timing Marks a. Timing marks of crankshaft and camshaft should be aligned. b. Impregnate a new gasket (17) with lightweight Tite
Seal compound and place it on the crankcase studs. c. Start the reduction gear unit housing onto the crankcase studs, then rotate the gear(66)as necessary to couple with the front of the camshaft.Seatthe housing on the crankcase, install ten sets of attaching parts
(14,15, 16)around the mounting flange, two sets of attaching parts (12,13) and two sets of attaching parts
(63, 64, 65). d. Tighten the attaching parts evenly and in progressive steps to the torque specified in Section XV.
Safety the two bolts (13) and the screw (85) together with lock wire. e. Start propeller shaft and cage subassembly into reduction housing. Rotate propeller shaft, as necessary, until the dowel hole in its flange, is located in the specified relationship to the parting line of the cage halves (See Figure 5). Push the subassembly into the housing, meshing the propeller drive gear with the propeller shaft.
50
Install ten sets of attaching parts (9, 10, 11, figure 10) and tighten to the torque specified in Section XV.
It is imperative that the preceding step be accomplished, as outlined, to prevent destructive engine vibration.
12-10. CYLINDERS AND PISTONS. (See figure 9.) a. Before installing each piston and cylinder, turn the crankshaft until the corresponding rod is at T .D.C. b. Place the piston over the connecting rod with the position number on its head forward, and push the pin (35) through until it is centered. c. Lubricate the piston and rings liberally with Lubriplate No. 130AAA. d. Hang a piston ring compressor on the connecting rod. Then hold the cylinder in the left arm, with the left hand holding the pushrods (6) in place, center the compressor over the piston rings, compress them
fully. Push the cylinder onto the piston, forcing the compressor off the piston. e. Remove the ring compressor and start the cylinder base flange onto the hold-down studs. f. After making sure the cylinder base packing (5) is in place and not tWisted, seat the flange on the crankcase cylinder pad. Make certain pushrods are seated in valve lifter and rocker arm sockets. g. Install pistons and cylinders in any desired order.
In order to minimize turning of the crankshaft and to prevent excessive unbalance, it is suggested that
No's 1 and 2 be installed first; then the shaft turned for No's 3 and 4 and these assemblies installed; then the shaft positioned for No's 5 and 6 and the last two installed in those positions. h. As soon as a cylinder has been installed, attach it with the upper three nuts (2, 4) and tighten moderately. i. After the cylinders are installed, rotate stand bed to place engine in inverted position. Install the three sets of lower attaching parts (2,4) on each cylinder. j. Tighten the cylinder attaching parts evenly and in progressive steps around the flange to the torques specified in Section XV. Install nut locks (1, 3). k. Slide the pushrod housing connectors (8) down over the pushrod housing flanges and install the clamps
(7).
1. Impregnate new rocker cover gaskets (13) with lightweight TiteSeal compound, place them on cylinders, position covers (12) on cylinders and secure each with six sets of attaching parts (9, 10, 11). m. Use new gaskets and install the six lower spark plugs.
12-11. INDUCTION SYSTEM AND OIL SUMP. (See figure 8.) a. Make certain the diffuser ring (46) or tube (47) is properly installed in the induction air passage. (Refer to the Parts Catalog, Form No. X-30020, for part number to serial number and model application.) After the ring is installed a small bead or fillet (approximately 1/16 inch wide) of Epoxy Resin Adhesive
(Conely Weld or equivalent) is to be applied between the front face of the ring and the air passage wall. b. Ascertain that a new "0" ring (41) has been installed on the suction tube (44). The suction tube assembly is retained in place by one set of attaching parts (40, 39). Use lockwire to safety the screw (39) to the suction tube. c. Impregnate a new gasket (52) with Tite Seal compound and place it on the crankcase. Lower oil sump
(51) into place carefully to avoid damaging the studs.
Secure the sump in place with fourteen sets of attaching parts (30, 29, 28). d. For earlier model sumps, impregnate a new gasket (5) with Tite Seal compound and place it on sump studs. For current model sumps, install a new "0" ring (6). Install carburetor (4) and secure with it four sets of attaching parts (1, 2, 3). e. For earlier model sumps, impregnate a new gasket (17) with Tite Seal compound and place on sump studs. For current model sumps, install a new "0" ring (18). Install manifold riser (16) and secure it with four sets of attaching parts (14, 13, 12). f. Place a new hose (23) and two hose clamps (22) on the longest side of each of the intake pipes (26,
25, 24) and on each end of the balance tube (11). g. Impregnate six new gaskets(27)with TiteSeal compound and place them on the cylinder intake parts. h. Install the intake pipe assemblies, secure each with two sets of attaching parts (21, 20, 19), work hoses from one pipe to the next until evenly spaced over adjoining jOints, pOSition and tighten hose clamps.
1. Work hoses on balance tube over beads of No. 1 and 2 cylinder intake pipes and position hose clamps.
Do not tighten these clamps until after installation of generator.
12-12. OIL COOLER. (See figure 10. ) a. Impregnate a new gasket (5) with lightweight Tite-
Seal compound and place it on the housing studs. b. Install the oil cooler (4) and secure it with eight sets of attaching parts (1, 2, 3).
12-13. CRANKCASE COVER. a. Impregnate a new gasket (11, figure 13) with lightweight Tite Seal compound and place it on the crankcase studs. b. Place the crankcase cover over the gasket, turning the oil pump drive shaft, as necessary, to align with cam gear hole. c. Secure the cover to the crankcase with one set of attaching parts (20, figure 2) and a second set below the right magneto. d. Secure the cover to the sump with five sets of attaching parts (30).
12-14. GENERATOR. (See figure 2). a. Turn the generator drive gear, as necessary, to mesh its teeth with those of the camshaft gear. b. Install the generator (22) on the crankcase cover, as illustrated, and secure with three sets of attaching parts (21). c. Install the clamp (10, figure 8)on the balance tube
(ll). Install the screw (9) and nut (8). Attach the balance tube clamp to the generator with a clamp. d. Tighten the balance tube hose clamps.
12-15. MAGNETOS. a. Plug the spark plug hole of No. 1 cylinder with thumb while propeller shaft is turned in direction of rotation until pressure of air in cylinder indicates piston is coming up on compression stroke. b. Remove hex head plug and gasket from left side of crankshaft cover (14, figure 2) and continue turning propeller shaft until the line between "28
0
" and "BTC" is aligned with the pOinter. c. Install an ignition cable in the No.1 cylinder outlet of the magneto. Hold spark plug terminal of cable near a bare metal area of the magneto and turn drive gear clockwise (facing drive end) until a spark jumps from terminal to magneto upon release of impulse coupling. d. Stop rotation as soon as a spark is observed. Insert a 2-3/32-inch diameter pin into timing hole at bottom of magneto case. Hold pin inward and turn gear counterclockwise (facing drive end) until pin drops in and locks rotor shaft. e. While holding pin in place, mount magneto and a new gasket on crankcase cover pad and secure with attaching parts (19, figure 2). Tighten nuts only snug by hand and remove cable.
51
f. Position a timing light (one containing its own source of illumination) so it may be easily observed; then connect its red lead to the magneto ground switch terminal (18, figure 2) and the black ground lead to any bare metal part of the engine. g. Turn the magneto to the extreme counterclockwise position; then, with a nonmarring hammer, tap the magneto case clockwise until timing light indicates opening of breaker point. h. Tighten the magneto attaching nuts to approximately 200 inch-pounds. i. Check timing by backing up propeller shaft approximately five degrees; then tap gently forward until timing light indicates opening of breaker pOints.
If timing is correct, the line between the "28 0
" and
"BTC" will be aligned with the pointer of the crankshaft cover.
12-16. IGNITION CABLES. a. Install spark plugs with new gaskets in the cylinder upper holes. b. No. 1 outlet of the magneto is identified as such by the number "1" on the breaker cover. The outlets are numbered consecutively 1 through 6 in a clockwise direction. On both magnetos, the ignition cables to No. 1 cylinder are connected to the number 1 outlet, No. 4 cylinder to number 2 outlet, No. 5 cylinder to number 3 outlet, No. 2 cylinder to No.
4 outlet, No.3 cylinder to number 5 outlet, and No.
6 cylinder to number 6 outlet. c. Place a plain washer on the stud, install the three-wire cable bracket (9, figure 2) and secure with attaching part (10). d. Place the two-wire cable bracket (5) on the lifting eye front bolt and secure with a lock washer and nut.
Connect cables to cylinders No.2, 4, and 6 upper plugs. e. Place a plain washer on the stud, install the threewire cable bracket (13) and secure with attaching parts (14). f. Install the two-wire cable bracket (36) on the long stud at the sump mounting flange and secure it with a lock washer and nut. g. Connect ignition cables to cylinder No.2, 4, and 6 lower spark plugs. h. Cables for No.1, 3, and 5 cylinders are to be installed in the same manner as No.2, 4, and 6, except there is no two-wire cable bracket attached to the crankcase upper parting flange. i. Install the band (16, figure 2) as illustrated.
12-17. STARTER FOR GO-300-A, -C. (See figure
7. ) a. Impregnate a new gasket (8) with Tite Seal compound, place it on the crankcase cover studs and install the starter (7). b. Secure the starter with three sets of attaching parts (6, 5, 4) at the rear and two sets of attaching parts (3, 2, 1) at the front.
12-18. STARTER FOR GO-300-D, -E. (See figure
6. ) a. Impregnate a new gasket (13) with Tite Seal compound and install it on crankcase cover studs. Place the starter adapter assembly over the gasket. Install three sets of attaching parts (12, 11, 10) and one set of attaching parts (9, 8, 7, 6). b. Install a new
"0"
ring(5) on starter flange. Mount starter (4) on adapter studs and install two sets of attaching parts (3, 2, 1).
52
SECTION XIII
REPAIR AND TESTING OF ACCESSORIES
13-1. HYDRAULIC VALVE TAPPETS.
13-2. DISASSEMBLY. When lifters are disassembled, it is essential that a suitable rack be available for storage of parts in their original relations. This is an absolute necessity with regard to parts of hydraulic units. It is advisable to disassemble these units immediately before they are to be cleaned and to carry out disassembly" cleaning, inspection and assembly operations in one continuous process. Use the following disassembly procedure. a. Invert lifter, and socket and hydraulic unit will fall into the palm of the hand. Place body and socket in rack. b. Usually hydraulic unit plunger may be removed from cylinder by pulling outward, while turning in direction which tends to "wind up" spring under its head. If plunger appears to be "frozen" in cylinder, it may be held tightly between oil under it and a ring of carbon on cylinder wall. To test for this condition and to release plunger simultaneously, insert a medical swab stick or similar hard wood dowel into open end of inlet tube, and depress ball check valve. This will release oil from cylinder, and plunger may be depressed, unless it is actually stuck to cylinder. A ring of carbon may be disintegrated and plunger may be removed by both turning and pulling outward in an oscillating fashion, while gripping plunger head with tape-covered pliers.
13-3. CLEANING. All parts of each lifter assembly should be degreased thoroughly by dipping and brushing in clean, approved solvent in a small cake pan, or similar container, which can be placed near the parts rack on a well-lighted bench. All traces of dirt must be removed. Extreme care must be exercised to avoid interchanging parts of the assemblies.
Cleaning procedure should be carriedoutimmediately prior to inspection and testing to avoid an additional cleaning and preserving operation. Parts and assemblies must not stand for more than a few minutes without application of a corrosion-preventive coating.
13-4. INSPECTION AND TESTING. a. Inspect face of cam follower on body for any types of damage. Inspect body bearing surface for scoring and corrosion. Discard any lifter body which exhibits any of these faults. b. Inspect pushrod socket for excessive wear and roughness in spherical cavity. Wear is indicated by a polished area at bottom of cavity with a sharp boundary. Diameter of worn area and its apparent depth below original, smooth contour give a visual indication of extent of wear; however, appearance is usually deceptive, hence a socket should not be discarded unless there is some evidence of penetration of the hardened surface layer, or unless unit produces an excessive "dry" lash wherever it is installed in an engine. c. Check roughly for diametrical clearance and check valve wear in hydraulic unit by starting dry plunger into dry cylinder, then pushing in and releasing it quickly.
For this test, hold cylinder between thumh and middle finger, and depress piston with index finger. Compression of air in cylinder should make plunger kick back instantly. If piston does not return fully either it is excessively worn, or check valve is leaking. To check for a leaking valve, repeat compression test while plugging end of oil inlet tube with other hand. If plunger still does not kick back promptly, it and cylinder are excessively worn. If it does kick back on second test, either check valve seat is worn and leaking or dirty. In this event, clean cylinder again, and repeat first test (tube open). If plunger still does not kick back, the valve is defective. Any unit which fails to pass this rough test must be discarded. Discard both cylinder and piston, since these parts are selectively fitted and are not interchangeable.
13-5 REPLACEMENT. Hydraulic unit (piston, spring and cylinder) may be replaced as assemblies in any valve lifter. Parts of these units are selectively fitted at factory to produce desired leakdown rate, and must never be interchanged. Lifter bodies may be replaced independently of hydraulic units, if original parts were damaged. New bodies may be installed in any engine guide with new or original hydraulic units in them. Sockets may be replaced independently of other parts. In order to meet these reqUirements, lifter parts and units should be kept in their numbered positions in parts rack excepting those which were discarded. Place new parts in vacant spaces of rack to make up a complete set of lifters.
13-6. ASSEMBLY. a. Clean all parts with dry-cleaning solvent and drain dry immediately before starting assembly work. b. Lubricate interior and exterior surfaces of cylinder and surface of piston and spring with only a film of engine lubricating oil and corrosion-preventive mixture. Do not lay parts down after lubricating.
Start piston into cylinder and twist to wind up spring while pushing inward until spring snaps into cyUnder counterbore. c. See that valve lifter body is protected with only a film of engine lubricating oil and corrosion-preventive mixture inside and out. Insert hydraulic unit, tube first, against body inner shoulder. d. Place socket, grooved flat side inward, on piston. e. When all valve lifters have been assembled in this manner and replaced in their correct positions in the parts rack, cover them to exclude dust and grit until ready to install in engine.
13-7. HARRISON OIL COOLER.
13-8. CLEANING. a. Soak the assembly in a tank of mineral spirit solvent or cleaners' naptha to loosen a.nd wash out
53
heavy sludge deposits and oil. b. Blowout the cooling fins and dry the exterior with a jet of dry compressed air after draining the cooler. c. For a final cleaning operation, a tank of at least
10 gallons capacity with a solution-circulating pump system of apprOximately 35 gallons per minute deli very at 75-150 p.s.i. pressure should be used to circulate through the cooler core a solution of an inhibited, mild alkaline cleaning compound, such as Oakite
No. 61 (6 oz. Dakite per gallon of water), maintained at a temperature between 160 0 F and 180 0 F. A pressure gauge should be installed in the supply line and another in the return line to measure the pressure drop through the cooler The pressure drop will decrease, i.e., the gauge readings will come closer together as the solid depOSits are flushed out. An adapter for attachment of the hoses must be made locally and sealed to the cooler mount flange with a gasket and bolts, washers and nuts. The adapter may incorporate the two gauges. It may be made of steel plate and standard iron pipe fittings. The cleaning solution should enter through the normal cooler outlet port (upper in installed position). A filter must be interposed in the supply hose between the pump and the cooler. Circulate the solution until the discharge appears clean and the pressure drop across the cooler has stabilized at the lowest value obtained. This may require 30 minutes or so. d. Flush the cooler bore thoroughly with clean, hot water, and drain it as completely as possible. Blow off the exterior with dry compressed air. and attach a compressed air hose to the adapter inlet. The air line should be equipped with a pressure gauge and, between the gauge and the pump, a manual shutoff valve. Lower the cooler into a water tank until it is completely immersed; then slowly open the air line valve until the pressure has risen to
100 p.s.i. Close the valve, and watch for air bubbles escaping from the cooler, accompanied by a drop in gauge reading. If necessary to maintain pressure, open the air line valve long enough to locate the source of bubbles at the cooler surface, and if the point is acceSSible, circle the leak with a crayon mark to identify pOints which may be repairable.
13-10. REPAIR. a. Because of the welded constructions, repairs are not recommended by the oil cooler manufacturer; however, emergency repairs may be made to stop leaks in accessible locations, such as tube seams and header surfaces, when a new cooler is not available.
Do not attempt to repair an oil cooler with blown or bulged tubes. b. Clean thoroughly the area surrounding the crack or hole. c. Apply a thin coat of a solution of Alcoa No. 33 flux in water. d. To repair tube leaks, heat the metal with an acetylene torch equipped with a No.3 tip, and apply Alcoa
No. 716 welding wire 1/16-inch in diameter. e. To· repair header leaks or mounting pad cracks, heat the metal with an acetylene or hydrogen torch equipped with a No. 5 tip, and apply Alcoa No. 718 welding wire of 3/32 inch diameter or Alcoa No. 43S welding rod. f. Remove all traces of welding flux by wiping all accessible areas with a clean cloth wet with hot water; the scrub with a stiff bristle brush and hot water, and wipe again with a wet, hot cloth. Flush all inaccessible areas thoroughly with hot water and dry with compressed air. Repeat the flushing and drying operation several times. g. Repeat the air test described in paragraph 13-9.
Use only an inhibited, mild alkaline cleaning compound intended for cleaning aluminum parts.
Strong alkaline materials intended for use on other metals will destroy the cooler by corrosive action. If such a compound has been used in the Circulating equipment, it must be washed out thoroughly before filling with the solution to be pumped through the oil cooler. It is essential that all alkaline material be removed from exterior and interior surfaces of the cooler.
Residues left inside the core will react with acids in the engine oil to form soap, and this will cause violent foaming in the oil system.
After a cleaning operation, empty the solution filter, and examine the filtering element for metallic particles. If any Significant volume of such particles is found, the cooler from which they came should be destroyed, since there is no way of determining when all such particles have been removed.
13-9. INSPECTION. a. Look for obstructions between the air fins. b. Inspect the flat tubes, fins and headers for dents and bending. The assembly is allowed to be out of square 1/16-inch per foot in any direction. Any distortion will indicate the possibility of cracks and broken jOints. Fins must not be bent so as to restrict the COOling air flow. c. Inspect the mounting surface for deep scratches and cracks which would cause oil leakage. d. To test for invisible leaks, block either oil port with a gasket and adapter plate through which compressed air may be introduced into the other port,
54
All aluminum welding fluxes are highly corrosive. Exercise care to prevent the flux from entering the cooler core. Complete removal of the flux residue is essential for the same reason.
13-11. TESTING. Seal the flushing adapter to the cooler, and connect to a high pressure hose leading through a valve to a source capable of supplying a low viscosity lubricating oil at a static pressure of
200 p.s.!. Fill the cooler by Circulating oil until all air has been displaced. Then block the cooler, and apply a pressure of 200 psi. Close the supplyline valve, and allow the cooler to stand under this pressure for 20 minutes, during which time there should be no oil leakage , and the gauge pressure should remain constant.
13-12. LUBRICATION. Following completion of cleaning, testing and repair work, if any, and pending installation of the cooler, flush the core with clean, low viscosity lubricating oil at a temperature of apprOximately 160oF. Drain out the bulk of the flushing oil, leaving a coating on the interior surfaces, and store the cooler in a tightly-covered container.
SECTION XIV
TESTING AFTER OVERHAUL
NOTE ... Proper operation of the engine following cylinder replacement or major overhaul is extremely important. The following procedures should be followed to insure that adequate lubrication is being provided to newly installed components and that the piston ring seating will occur as soon as possible.
14-1. OPERATION AFTER MAJOR OVERHAUL OR
CYLINDER REPLACEMENT WITH ENGINE INSTALL-
ED IN THE AIRCRAFT.
14-2. THE AIRCRAFT CAN BE CONSIDERED A
SUITABLE TEST STAND FOR RUNNING-IN OVER-
HAULED ENGINES CONTINGENT ON THE FOLLOW-
ING CONDITIONS: a. Install engine cowling. b. Each cylinder must be equipped with a temperature sensing device to monitor the head temperature. c. The flight propeller may be used contingent on careful observation of cylinder temperatures. Head the aircraft into the wind for this test.
14-3. SERVICE AND PRE-STARTING PROCEDURES. a. Service the lubricating system with mineral oil (MIL-C-
6529 Type II) of the appropriate grade depending on ambient temperature. b. Rotate the propeller by hand through several cycles with the spark plugs removed. c. Pre-oil the lubrication system using an external pre-oiling pressure system. d. Install the spark plugs and ignition harness.
14-4. ENGINE STARTING AND GROUND OPERA-
TION. a. Assure that all engine and cylinder baffling is properly installed and in good condition. b. Start the engine and assure that oil pressure rises to within the specified limits within 30 seconds. c. Operate the engine at 750 RPM for one minute, gradually increasing toward 1000 RPM in three minutes. Check the magneto circuit for grounding prior to a normal shut-down.
Allow the engine to cool adequately and then make a visual inspection for any irregularities. d. Start the engine again and operate it at 750 RPM gradually increasing to 1500 RPM over a period of four minutes. If the engine is equipped with a controllable pitch propeller, cycle the propeller allowing only :t,JOO RPM drop. Return to the idle range and'make adjustments to the idle mixture and RPM as required on carburetor engines and to the low un metered fuel pressure, idle RPM and mixture on fuel injected engines,
Position the throttle to 1200 RPM to smooth the engine, Then do an idle mixture check. Refer to the appropriate service information for these fuel system adjustments, Run engine up to full power for a period not to exceed 10 seconds, Visually inspect and correct any discrepancies, Check the oil quantity,
Cowl the engine in preparation for test flight.
14-5. TEST FLIGHT. a. Ambient air and engine operating temperatures are of major concern during this test flight. Do a normal pre-flight run-up in accordance with the aircraft flight manual. Conduct a normal take-off with full power and monitor the fuel flow,
RPM, oil pressure, cylinder head temperatures and oil temperatures. Reduce to climb power in accordance with the flight manual and maintain a shallow climb attitude to gain optimum airspeed and cooling. Rich mixture for all operations ex~ept lean for field elevation where applicable and lean to maintain smoothness during climb in accordance with airframe manufacturers operating instructions. b. Level flight cruise should be at 75% power with best power or richer mixture for the first hour of operation, The second hour power settings should alternate between 65% and 75% power with the appropriate best power mixture settings.
Engine controls or aircraft attitude should be adjusted as required to maintain engine instrumentation within specifications. c. The descent should be made at low cruise power settings, with careful monitoring of engine pressures and temperatures. A void long descents with cruise RPM and manifold pressure below 18° hg.; if necessary decrease the RPM sufficiently to maintain manifold pressure. d. Any descrepencies detected during test flight or any final adjustments necessary should now be made. The engine can be operated in normal service in accordance with the aircraft flight manual.
14-6. OPERATION AFTER MAJOR OVERHAUL UTIL-
IZING AN ENGINE TEST CELL.
4-7. SERVICING AND PRE-STARTING PROCEDURES. a. Service the lubricating system with mineral oil (MIL-C-
6529 Type II) of the appropriate grade depending on ambient temperature. b. Rotate the propeller by hand through several cycles with the spark plugs removed. c. Pre-oil the lubrication system using an external pre-oiling pressue system. d. Install the spark plugs and ignition harness.
14-8 TEST EQUIPMENT.
14-9. TEST CLUB. Unless a dynamometer is used to apply controlled loads to the crankshaft, it will be necessary to install a wood test club such as those supplied by the Hartzell Propeller Fan Co. of Piqua
Ohio. Test clubs are customarily supplied in standard diameters, so that the blade length must be reduced by the "cut and try" method until the club will absorb
175 BHP at 3200 RPM when used in the cell, stand, and engine combination for which it was calibrated.
14-10. TEST STAND. Any rigid supporting stand of adequate strength and suitable shape and dimensions may be fitted with adapters to accept the engine mount bracket locations and shear rubber mount bushing dimensions shown in the installation drawings. The crankshaft should be at least five feet above the cell floor so that the test club will not cause excessive disturbance in the air at floor level. ~ the cell does not have a paved floor, the ground beneath the stand
55
and for a reasonable distance around it should be treated so as to hold the soil in place.
14-11. COOLING AIR SCOOP. It will be necessary to construct a scoop of heavy-gauge sheet metal to fit over the tops of all cylinders, with pads to seal it to the rear cylinders and to all valve rocker covers, in order to direct an adequate flow of air downward through the cylinder fins. Vanes may be necessary to direct a portion of the cooling air to the center cylinder and/or the oil cooler, therefore, the temperatures of all cylinder heads should be measured until uniformity within 50 0 F. has been obtained. It is advisable to provide a duct from the cylinder scoop to the generator vent tube or to provide a separate scoop for it.
14-12. CARBURETOR AIR INTAKE. An air filter and housing should be attached to the carburetor air inlet flange. The filter area must be sufficient to avoid excessive restriction of air flow, even when the filter is dirty, though it should be cleaned before each test.
The calculated area of a clean filter should be increased by at least 50%toallowfor dirt accumulation.
14-13. EXHAUST STACKS. For testing purposes the exhaust back pressure should be zero. Short stacks may be made locally to match the cylinder port diameter and the flange stud dimensions shown in applicable installation drawing.
14-14. CONTROLS. The only controls required are a carburetor throttle control, a starter detent control and a standard twin magneto switch with connections to the grounding terminals; however, the carburetor manual-mixture control lever may be connected to a suitable manual control in order to permit a very brief test of its operation and to permit stopping the engine with the idle cutoff feature. If the mixture control is not connected, it must be wired in the "RICH" position. For locations of all control connections and required throttle travel refer to the applicable installation drawing.
14-15. ELECTRICAL WIRING. A 12-volt storage battery must be connected by a No. 0 stranded copper cable from its positive terminal to the power terminal on the starter and the battery negative terminal must be connected to the engine, or both battery negative terminal and engine may be grounded. The switch terminal must be connected to the engine or both to a common ground. A Delco-Remy generator regulator designed for a 12-volt system should be connected to the generator "A" (armature) and "F"
(field coil) terminals, the latter of which is nearest to the crankcase, and to the battery and the ammeter to check generator performance. If desired, an electrical load may be connected across the battery terminals to provide a constant or variable drain so as to check generator output throughout the test
run.
14-16. INSTRUMENTS. The control panel should be equipped with the following engine instruments. (See installation drawing for connection points.) a. A mechanically-driven tachometer and flexible shaft assembly is required. b. An oil pressure gauge and tube c.onnection. c. An oil temperature gauge and capillary assembly. d. A cylinder head temperature gauge, wiring and spark plug washer thermocouple. (Install under a lower spark plug.) e. A water manometer to measure crankcase pressure. It is suggested that a simple method of attachment to the engine can be accomplished by brazing a fitting to an oil filler cap to be used for testing only. f. An ammeter connected in the generator circuit.
14-17. BREATHER. A substantial hose of 3/4 inchI.D. should be securely clamped over the crankcase breather elbow and support so as to lead to a point above and to the rear of the engine.
14-18. FUEL SYSTEM. The fuel supply tank should be elevated to provide the specified fuel pressure.
Connect the fuel supply line to the carburetor. If it is desired to measure the total fuel consumption per minute during the test run, a flowmeter may be interposed in the supply line, or a graduated alternate tank supported on a small platform scale may be connected to the supply line through a selector valve, and the time required to trip with a known fuel overbalance to the switchover time may be timed by a stop watch.
14-19. ENGINE TEST AFTER OVERHAUL. a. After a partial or complete disassembly and repair of an engine in which no major part (cylinder, piston, bushings, gears, etc.) was replaced, the engine will be tested in accordance with Tables XIlland XIV. b. Engines in which major parts were replaced will be tested in accordance with Tables XIII and XV. c. Extend the second period of each test schedule, if necessary, to raise the oil temperature to lOOoF.
NOTE
If tests must be conducted in extremely cold weather, it may be necessary to shield the crankcase from the cooling air stream, Since it takes some heat from the 011.
56
d. Take instrument readings at the beginning, in the middle, and at the end of the full throttle period.
Take one reading during each of the other periods as soon as conditions have stabilized. e. Make one check on performance of each magneto alone at 3200 RPM. (Refer to Table XIll.) Clear spark plugs by operating with both magnetos on for a few seconds between checks.
NOTE
The maximum allowable cylinder head temperature and the maximum allowable oil temperature (Table XIII) must not be exceeded at any time during the test.
14-20. PRESERVATION. If the engine is not to be installed in an aircraft and placed in service immediately, the last 15 minutes of operation should be used to circulate a corrosion-preventive oil mixture (suitable for flight operation). This will be an additional period, since the engine must be stopped to change oil. Install dehydrator plugs in the spark plug holes which are in the top position when the engine is mounted in the shipping base. Seal all other openings leading to the interior of the engine with shipping covers, suitable plugs or non-hydroscopic tape.
TABLE XIII TEST OPERATING LIMITS
Feature Value
Full throttle speed
Fuel consumption
Oil consumption
Oil viscosity
Fuel rating
Idling speed
Manifold vacuum
Magneto drop
*Crankcase pressure
Oil temperature (desired)
Oil temperature (maximum)
Oil pressure at full throttle
Oil pressure at idle (minimum)
CyUnder head temperature
(maximum on lower spark plug)
3200-3300 RPM
92-102 lbs/hr at full throttle
2.75 lbs/hr at full throttle
S.A. E. 50
80/87 octane
575-625 RPM
0.5-2.0 in. at full throttle
10.0-15.0 in. at idle
100 RPM at full throttle
0-1. 0 in. H20
150-200
225
0
F
0 F
40-60 PSI
20 PSI
525 0 F.
* A sudden increase in crankcase pressure and rapid fluctuation of manometer usually indicates sticking of rings. Before removing cylinders, check crankcase breather and manometer.
57
TABLE XIV TOP OR MINOR OVERHAUL TEST RUN TABLE XV MAJOR OVERHAUL TEST RUN
Period
10
11
12
5
6
7
8
9
1
2
3
4
Following period No. 12, stop engine, drain oil and clean screens. Measure out 10 quarts of new lubricating oil into a calibrated container. Weigh and record weight of oil and container, then pour oil into sump.
13
14
15
16
Time (M inutes)
10
10
10
5
5
5
5
5
5
5
5
5
10
30
30
10
RPM
900 Warm-Up
1200
1500
1800
2000
2200
2400
2600
2800
2900
3000
600
±
25
Idle Cooling
Period
Warm-Up
2900
3200-3300 100%
Power & Check
Mags. See Notes
A&B
600
:t
25 Idle
Cooling Period
Period
10
11
12
6
7
8
9
1
2
3
4
5
Time (Minutes)
5
5
10
10
10
10
10
10
15
15
15
10
RPM
900 Warm-Up
1200
1500
1800
2000
2200
2400
2600
2800
2900
3000
600
±
25 Idle
Cooling Period
Following period No. 12, stop engine, drain oil and clean screens. Measure out 10 quarts of new lubricating oil into a calibrated container. Weigh and record weight of oil and container, then pour oil into sump.
13
14
15
16
10
30
30
10
2900
Warm-Up
3200-3300 100%
Power & Check
Mags. See Notes
A&B
600 ± 25 Idle
Cooling Period
Following period No. 16, stop engine, drain oil into the same calibrated container and weigh it again. If oil consumption was in excess of 2. 75 lbs., replenish oil supply to original quantity and weight. Pour oil into sump and repeat periods 14, 15 and 16. Upon the second completion of period 16 again weigh and determine consumption of oil. If consumption is still in excess of 2.75 lbs., return engine to overhaul.
NOTES:
Following period No. 16, stop engine, drain oil into the same calibrated container and weigh it again. If oil consumption was in excess of 2. 75 lbs., replenish oil supply to original quantity and weight. Pour oil into sump and repeat periods 14, 15 and 16. Upon second completion of period 16, again weigh and determine consumption of oil. If consumption is still in excess of 2.75 lbs. , return the engine to overhaul.
A. Readings must be recorded after completion of each 15 minute interval during oil consumption run.
B. Magneto drop to be taken after completion of oil consumption run. Engine must be throttled to specified RPM, and temperature allowed to settle out before taking magneto drop.
58
SECTION XV
TABLE OF LIMITS
TABLE XVI TABLE OF LIMITS
21
22
23
24
2;:;
2fi
27
26
26
26
26
25
25
25
26
26
26
26
26
26
26
26
26
26
4
5
6
7
8
9
10
11
12
13
14
15
16
17
Ref.
No.
Figure
No.
1
2
18
19
20
25
25
26
26
26
26
26
26
26
26
Description
PROPELLER REDUCTION HOUSING
Reduction Housing to Crankcase Pilot . . . . , Dia:
Propeller Shaft Bearing Cage to Reduction
Housing Pilot. . . . . . . . . . • . . . . . . . .. Dia:
Propeller Shaft In Front Thrust Bearing of Bearing Cage . . • . . . . . . • . . . . • . .. Dia:
Propeller Shaft In Reduction Housing
Bushing . • . . . . . . . • . . . . . . . . . . . . . Dia:
Propeller Shaft Rear Bushing In Reduction
Housing. . . • . . . . . . . . . . . . . . . . . . .. Dia:
Propeller Shaft Drive Gear Bushing In
Reduction Housing. . . . . . • . . • . . . . . .. Dia:
Propeller Shaft Drive Gear In Crankcase
Front Bearing . . . . . . . . . . . . . . . . . . . Dia:
Propeller Shaft Drive Gear In Reduction
Housing Front Bushing . . • . . . . . . . . . . , Dia:
Prope 11er Shaft Drive Gear In Reduction
Housing . . . . . . . . . • . . . . . . . End Clearance:
Propeller Shaft In Bearing Cage
Bearing . . . . • . . . . . . . . . . . . End Clearance:
Accessory Dri ve Bushing In Reduction
HOUSing . . . . . . . . . . . . . . . . . . . . . . .. Dia:
Accessory Dri ve Bevel Gear In Bushing . . . . Dia:
Accessory Dri ve Oil Seal In Housing . . . . . , Dia:
Accessory Drive Front Bearing In Cage
O.D . . . . . . . . . . . . . . . . . . . . . . . . . . . Dia:
Accessory Dri ve Front Cage In Housing. . . . Dia:
Accessory Dri ve Gear In Bearing Ball. . . • . Dia:
Accessory Dri ve Front Cage--Check Thrust
Pad For Wear From Gear--From Flange to Thrust Pad . . . . . . . . . . . • . •• Dimension:
Bushing In Housing--Check For Wear On
Flange End Gauge From Center Line Of Cam
Bore to Thrust Flange On Bushing .. Dimension:
Accessory Drive Bevel Gear-- Check Dimension
From Sharp Point Of Gear Tooth To Thrust
Shoulder . . . . . . . . . . . . . . . . . • Dimension:
Accessory Drive Gear--Check Thrust End Of
Gear Shaft For Wear--From Sharp Point Of
Tooth To Thrust End . . . • . . . . . . Dimension:
Governor Driven Gear in Reduction
Housing ................
0 • • • • • • • • • • • • • •
Dia:
Governor Driven Gear ......... End Clearance:
Governor Drive Gear On Propeller
Shaft. . . . . . . . . . . . . . . . . . . . . . . . . . . . . . . . .. Dia:
Propelll'r Shaft Plug In Prop Shaft ....... Dia:
Oil Transfer Collar In Prop Shaft Plug ... Dia:
Oil Transfer Tube In Collar
Pru)Jeller Flange RUII-OUt
Dia:
F.1. R. :
New Parts
Minimum Maximum
.001L
.0019L
.008L
.004
.001 T
.0015L
.001 T
.0000
.0005L
.0001 T
.001L
.0005L
.001L
.0022L
.0025T
.0025T
.511
1.158
.137
.888
0.0014L
0.002
0.0030T
0.0005L
0.047L
O.OOlOL
.000
.004L
.005L
.033L
.0lD
.003T
.0035L
.007T
.001lL
.0025L
.0008T
.003L
.0035L
.004L
.0053L
.004T
.004T
.513
1.162
.139
.890
0.0034L
0.016
0.0045T
0.0030L
0.077L
0.0025L
.002
Serviceable
Limit
.0065L
.0078L
.0065L
.0075L
.050L
.020
.005L
.509
1.164
.141
.886
0.005L
0.025
0.092L
0.0035L
59
TABLE XVI TABLE OF LIMITS (cont.)
46
47
48
49
54
55
56
57
58
59
60
61
62
63
64
65
Ref.
No.
33
34
35
36
37
28
29
30
31
32
38
39
40
41
42
43
44
45
50
51
52
53
25
25
28
28
25
25
25
25
25
28
28
28
25
25
25
25
Figure
No.
26
26
26
26
26
25
25
26
26
26
26
26
26
26
26
26
26
26
26
26
26
25
Description
Valve Lifter in Guide ..................... Dia:
Cylinder in Crankcase Bore ............... Dia:
Tie Bolts in Crankcase .................... Dia:
Starter Pinion Pivot in Crankcase .......... Dia:
Run-out at Center Journals (Shaft
Supported at Front & Rear Journals) .... F. I. R. :
Main Journals ............................ Dia:
Crankpins ............................... Dia:
Crankpins & Journals ............. out-of-round:
Bushing in Crankcheek Blades ............... Fit:
Counterweights On Crankcheek
Blades ........................ Side Clearance:
Bushings In Counterweights ................ Dia:
Bushing In Crankcheek .............. Inside Dia:
Bushing In Counterweight ............ InSide Dia:
Damper Pin. • • •• • • • • Outside Dia:
Damper Pin
Damper Pin In
• • • • • . Length:
Counterweight ................. End Clearance:
Crankshaft In Front Bearing ..... End Clearance:
Crankshaft In Main Bearings ............... Dia:
CONNECTING RODS
Bearing and Bushing - Twist or Convergence
Per Inch Of Bearing Length ......... Dimension:
Bearing On Crankpin ...................... Dia:
Bushing In Connecting Rod ................. Dia:
Piston Pin In Connecting Rod Bushing ....... Dia:
CAMSHAFT
Camshaft Flanges To Crankcase .. End Clearance:
Gear To Camshaft - Pilot ................. Dia:
PUSHRODS
Pushrod Length (to theoretical
Ball Ends) ..••...••••..•.••.•.•••• Overall:
PISTONS, RINGS, PINS
Piston - Top Land In Cylinder Bore ......... Dia:
Piston - 2nd and 3rd Lands In Cylinder
Bore . . . . . . . . . . . . . . . . . . . . . . . . . . . . . . . . . . . Dia:
Piston - Below 3rd Land In Cylinder Bore ... Dia:
Piston - Above 4th Groove In Cylinder Bore. Dia:
Delete
Pin In Piston ............................. Dia:
Plug In Pin ....... , ....... , .... Dia (Press fit):
Pin Assembly In Cylinder ........ End Clearance:
Ring In Top Groove •............ Side Clearance:
Ring In 2nd Groove .............. Side Clearance:
Ring In 3rd Groove .•.......•... Side Clearance:
Ring In 4th liroove .............. Side Clearance:
New Parts
Minimum Maximum
.0005L
.003 L
.0005T
.001 T
.002 L
.012 L
.001 L
.001 L
.000
2. 247
1. 936
.000
.0015T
.015
2.248
1. 937
.0005
.003 T
.004
.0015T
.729
.729
.4916
.826
.001 L
.004 L
.001 L
.014
.003 T
.732
.732
.4921
.831
.030 L
.010 L
.004 L
.000
.0005L
.002 T
.0014L
.001 L
.004
.0005T
.0005
.003 L
.0045T
.0021L
.003 L
.008
.0015L
Serviceable limit
.0035L
.012 L
.015
2.2445
*
1. 9335
.001
.018
* tt tt
.040 L
.020 L
.0065L
.001
.006 L
.004 L
.005 L
.012
10.797
.038 L
.034 L
.0134L
.010 L
.0002L
.0005T
.006
.006 L
.0045L
.005 L
.002 L
10.827
.042 L
.038 L
.0164L
.013 L
.0006L
.0025T
.032
.008 L
.0065L
.007 L
.004 L
10.785
.0195L
.016 L
.0015L
.080 L
.010 L
,009 L
.009 L
.006 L
*
If Crankshaft is worn beyond these limits, regrind journals and crankpins to. 010 inch undersize and re- nitride. tt
If bushings in either counterweights or crankshaft blades are brinelled in excess of .001 inch the bushings should be replaced.
60
TABLE XVI TABLE OF LIMITS (cont.)
Ref.
No.
Figure
No. Description
New Parts
Minimum Maximum
Serviceable
Limit
66
67
68
69
70
71
78
79
80
81
82
83
84
85
86
87
72
73
74
75
76
77
88
89
90
91
92
93
94
95
28
28
28
28
28
28
25
25
28
28
28
25
25
25
25
25
28
28
28
28
25
25
25
Top Piston Ring In Cylinder ............... Gap:
Second Ring In Cylinder. •
Third Ring In Cylinder
Fourth Ring In Cylinder. .
Ring (Compression Ring) (closed to specified gap).
Ring (Oil Control) (closed to specified gap). o. 0 •
.Gap:
.Gap:
.Gap:
.Tension:
.Tension:
CYLINDERS AND VALVES
Valve Seat To Valve Guide Axis. . . . . . . Angle:
Intake Valve Seat Insert To Cylinder Head . . Dia:
Exhaust Valve Seat Insert To Cylinder Head. Dia:
Valve Guides In Cylinder Head . . . . . . . . . . Dia:
Cylinder Bore (Standard) . . . . . . . . . . . . . . Dia:
Cylinder Bore Roughness (In Micro-
Inches . . . . . . . . • . . . . • . . . . . . . . . R.M.S.:
Cylinder Bore Taper & Out-of-Roundness . . . •
Cylinder Bore--Allowable Oversize . . . . . . Dia:
Rocker Shaft In Cylinder Head Boss • . . . . . Dia:
Rocker Shaft In Rocker Bushing . . . . • . . . . Dia:
Rocker Bushing In Rocker . . . . • • . • • . • . • Dia:
Rocker In Cylinder Head Bosses .. Side Clearance:
Exhaust Val ve In Guide . • . . . . . . . . • . • . . Dia:
Intake Val ve In Guide . . . • . . . . . . . . . • . . Dia:
Valve Face To Stem Axis .••. . . . • . .. Angle:
Rocker Arm To Edge of Valve Spring
Retainer ....•.•.•..•....•••••.•..• Clearance:
Valve stem to Rocker Clearance (Lifter Peflated):
CRANKCASE COVER
Oil Pump Gears In Housing . . . . • . •• End Play:
Oil Pump Gears In Housing . . • . • • . . . . . • Dia:
Oil Pump Gear Shafts In Covers • • • • • . . . . Dia:
Starter Pilot In Cover . . . . . . . • . . . . . . . • Dia:
Generator Pilot In Cover . . . • . . . . . . . . . Dia:
Oil Seal In Tachometer Drive Housing. . . . • Dia:
Crankshaft Gear On Shaft •• . . . • • . • . • . . Dia:
.021
.013
.013
.013
9 Lbs.
11 Lbs.
44° 45'
.0055T
.005T
.001T
4.062
35
.000
4.077
.0002L
.001L
.002T
.004
.0045
.001L
45 0 45'
.030
.040
.030
.030
.030
12 Lbs.
15 Lbs.
45° 15'
.0085T
.008T
.003T
4.064
45
.001
4.079
.0017L
.0025L
.004T
.011
.006
.003L
46 0 15'
.110
.045 #
.035 #
.035 #
.035 #
8 Lbs.
10 Lbs.
4.069t
30
.002
4.081
.007
.004L
**
.016
.008L
.005L
.020
26
26
26
26
26
26
26
.002L
.003L
.0015L
.0005L
.001L
.001T
.000
.005L
.006L
.003L
.0055L
.005L
.008T
.0025T
.007L
.008L
.0045L
96
97
98
99
100
101
102
103
104
105
106
107
108
109
28
28
28
28
28
28
28
28
28
28
28
28
28
28
STARTER ADAPTER
Starter Shaft Gear In Bushing............ Dia:
Starter Shaft Gear Front Journal......... Dia:
Starter Shaft Gear In Needle Bearing. . . . . •• Dia:
Clutch Spring Sleeve In Adapter.... . . . . .. Dia:
Starter Shaft Gear In Cover Bushing...... Dia:
Bushing In Adapter Cover................ Dia:
Oil Seal In Adapter Cover............... Dia:
Cover Pilot In Adapter .......•.... . . . . .. Dia:
Worm Wheel Gear .......•...... End Clearance:
Clutch Spring On Clutch Drum........... Dia:
Clutch Spring On Starter Shaft Gear Drum Dia:
Clutch Spring To Sleeve (Sand Blasted
Finish) When Sand Blasted Finish Is
Worn to 75 RMS Replace Sleeve ....... .
From Centerline of Worm Gearshaft To
Starter Adapter Thrust Pads ........... .
Needle Bearing In Starter Adapter •......• Dia:
O.OOlL
1.059
0.0005L
0.003T
0.001 L
O.OOlT
O.OOlT
O.OOlL
0.0025
0.015T
0.006L
0.246
O.OOlL
0.003L
1.060
0.0029L
0.005T
0.0025L
0.003T
0.007T
0.003L
0.0115
0.022T
0.009L
0.248
O.OOlT
0.0045L
1.058
0.0031L
0.0035L
0.015
0.012T
0.013L
0.252
# If necessary, use 0005" oversize rings to maintain specified limits in cylinder bore to service limit. t
If Cylinder is worn beyond these limits, grind to .015 inch Oversize or re-barrel.
**
Install bushing in cylinder head bosses if this limit is exceeded.
61
TABLE XVI TABLE OF LIMITS (cont.)
123
124
125
126
127
117
118
119
120
121
122
Ref. Figure
No. No.
110
111
28
28
112
113
114
115
28
28
28
28
116 28
27
27
27
27
27
25
26
26
25
28
28
Description
Ball Bearing In Starter Adapter.......... Dia:
Worm Gear Shaft In Needle Bearing •.....
...•.........••.•......•.......•• Shaft Dia:
Worm Gear Shaft In Ball Bearing........ Dia:
Starter Worm Gear On Shaft........ . • . .. Dia:
Starter Pilot To Starter Drive Adapter •.. Dia:
Starter Drive Tongue To Worm Shaft
Drive Slot ..•.....••.•.•...•. Side Clearance:
Needle Bearing To Shaft Worm Gear ••.•. Dia:
GEAR TEETH BACKLASH
Crankshaft Gear To Camshaft Gear . . . . . . • . •
Magneto Drive Gear To Camshaft Gear ••.•••
Starter Gear To Crankshaft Gear . . . • . . • • . •
Generator Drive Gear To Camshaft Gear . . • • .
Oil Pump Gears . . . • • . • • • . • . . . . • . • • . . .
Propeller Shaft Drive Gear To Propeller
Shaft Gear . • • • . . . . • • • • . . . • . • • . . . . .
Accessory Drive Camshaft Gear To Accessory
Dri ve Gear (Vacuum Pump) . • . . • . • . . . • . .
Quill Shaft To Crankshaft and Drive Gear . . . •
Governor Drive Gear-To Governor Driven
Gear ..
It . . . . . . . . . . . <0 . . . . . . . . . . . . . . . . . . . . . . . . . . . . . . . . . .
<10 . . . . . . . . . . ..
Starter Gear To Crankshaft Gear ....•....
Starter Worm Wheel To Worm Gear ••••••
New Parts
Minimum Maximum
O.OOlL O.OOOlT
0.5615
O.OOOlL
0.0005L
0.0065L
0.5625
0.0007T
0.0025L
O.OOlL
0.010L
0.0005L
0.021L
0.0029L
Serviceable
Limit
0.5600
0.004L
0.030L
0.00311.,
.006
.012
.029
.010
.014
.000
.004
.0002
0.008
0.008
0.009
.009
.014
.043
.014
.022
.004
.008
0.012
0.012
0.013
62
T1
T2
T3
T4
T5
T6
T7
T8
T9
T10
Tll
T12
P-1
P-2
P-3
P-4
P-5
P-6
P-7
28
28
28
28
28
28
28 tt
SPRING TEST DATA
Oil Pressure Relief Valve Spring No. 534885
Compressed to 1.5625 inch length . . . . . . • load:
Valve Inner 'Spring No. 625957 Compressed to 1. 50 inch length • . . . • . • . . . . . . . . . . load:
Valve Inner Spring No. 625957 Compressed to 1.10 inch length . . • . . . • • • . • . • . . . . load:
Valve Outer Spring No. 625958 Compressed to 1.559 inch length . . . . • . . . . . . . . . . . load:
Valve Outer Spring No. 625958 Compressed to 1.168 inch length . . . . . . . . • • . . • • . • load:
Vernatherm Control Valve 0.090 inch minimum travel at . . • . • . • . . . . Temperature:
Valve Must Be Fully Closed Against
Seat At . . . . . . . . • . . • . . . • • • Temperature:
For Models GO-300-A & c. ttt
120 0
168 0
For Models GO-300-D
7.48 lbs.
33 lbs.
62 lbs.
43 Ibs.
77 Ibs.
&
F.
F .
E.
TABLE XVII TABLE OF TIGHTENING TORQUES
7.72 lbs.
37 lbs.
68 lbs.
47 Ibs.
83 lbs .
170 0 F.
170 0 F.
7.00 lbs.
30 lbs.
59 lbs.
40 Ibs .
74 lbs.
Ref.
No.
Figure
No. Torque (Irl./Lbs.)
25
25
26
25
26
26
26
26
26
26
26
Special Applications
TORQUE LIMITS
Crankcase Flange Nuts . . • . . . . . . . . . . • . .
Connecting Rod Nuts . . . . • . • . . . . . . . . . . .
Generator Shaft Nut . . . . . • . . . . . . . . . . . . .
Cylinder Base Stud Nuts . . . . . . . . . . . . . . . .
Cylinder Base Thru Bolt & Stud Nuts . . . . . .
Crankcase Tie Bolts and Stud Nuts . . . . . . . . .
Crankcase Tie Bolt Nuts . . . . . . . . . . . . . . .
Crankshaft and Camshaft Gear Screws . . . . . • .
Mount Leg Nuts . . . . . . . . . . • . . . . . . . . . . .
Propeller Shaft Cage Tie Bolt Nuts . . . . . . . . .
Propeller Shaft Cage Tie Bolt Nuts . . . . . . . . .
Spark Plugs . . . . . . . . . . . . . . . . . . . . . . . .
Thread Size
1/4-28
3/8-24
5/16-24
3/8-24
7/16-20
7/16-20
3/8-24
1/4-28
3/8-24
1/4-28
7/16-20
18 MM
100-125
400-475
175-200
410-430
490-510
370-390
370-390
140-160
275-325
90-110
340-360
300-360
.013
.019
.050
.019
.025 tt
.008
.012
.0015
0.016
0.016
0.025
Ht
Size
8-32
10-32
1/4-20
1/4-28
5/16-18
5/16-24
3/8-16
3/8-24
7/16-14
7/16-20
1/2-20
Size
1/8-27
1/4-18
3/8-18
1/2-14
3/4-14
TABLE XVIII GENERAL USE - TIGHTENING TORUUES
Bolts. Nuts
In. Lbs.
22.0-30.0
36.0-50.0
75.0-85.0
90.0-110
155-175
180-220
220-260
275-325
& Screws
Ft. Lbs.
1. 8-2. 5
3.0-4.2
6.3-7.1
7.5-9.2
13.0-14.6
15.0-18.3
18.3-21. 7
22.9-27.1
Driving Studs
In. Lbs.
50.0-70.0
100-150
200-275
300-425
Ft. Lbs.
4.2-5.8
8.3-12.5
16.6-22.9
25.0-35.4
400-450
550-600
33.3-37.5
45.8-50.0
TABLE XIX PIPE PLUGS
In. Lbs.
60-80
130-150
185-215
255-285
310-350
Ft. Lbs.
5.0-6.7
10.9-12.5
15.4-18.0
21. 2-23. 8
25.8-29.2
NOTE
Torque loads are listed for use with oil on threads, except for studs. Stud driving torques apply when the threads are coated with Alcoa thread lube if hole is blind, or with National Oil Seal compound if hole is through to a cavity subject to oil.
If cotter pin holes must be aligned set torque wrench at low limit and tighten nut to first hole beyond this torque. However, on connecting rod nuts the torque limits must be maintained. Replace nut and repeat as required. In no case shall connecting rod nuts be torqued below low limit or over high limit.
NOTE
Torque values for pipe plugs are for use with "Never
Seeze" (Snap- On Tool Corp. ) on threads.
63
12
11
E
SECTION D-D
64
Figure 25. Limits and Lubrication Chart
DRAIN OIL
SECTION
E-E
Figure 26. Limits and Lubrication Chart
65
66
SECTION
F-F
Figure 27. Limits and Lubrication Chart
P-6 P-7
6616710681\:0171
TO CRANK-
CASE CROSS-
OVER PASS-
AGE ____
FROM RIGHT
I
CRANKCASE
MAIN OIL
GALLERY
SECTION
A-A
OIL COOLER
MOUNT PAD
61
60
59
49
48
109
74 84
SECTION
C-C
SECTION
6-6
lOS 104
TO CRANKCASE
OIL GALLERY
FROM
SUMP
RIGHT CRANKCASE
GALLERY
FRONT PRESSURE
OIL SCREEN
P-1
SECTION
G-G
DRAIN TO
SUMP FROM PUMP
SECTION
H-H
Figure 28. Limits and Lubrication Chart
TO SUMP
SUCTION
OIL SCREEN
67
INTENTIONALLY
LEFT
BLANK
www.continentalmotors.aero
advertisement