advertisement
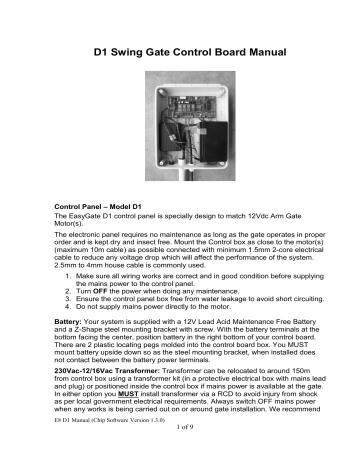
D1 Swing Gate Control Board Manual
Control Panel
– Model D1
The EasyGate D1 control panel is specially design to match 12Vdc Arm Gate
Motor(s).
The electronic panel requires no maintenance as long as the gate operates in proper order and is kept dry and insect free. Mount the Control box as close to the motor(s)
(maximum 10m cable) as possible connected with minimum 1.5mm 2-core electrical cable to reduce any voltage drop which will affect the performance of the system.
2.5mm to 4mm house cable is commonly used.
1. Make sure all wiring works are correct and in good condition before supplying the mains power to the control panel.
2. Turn OFF the power when doing any maintenance.
3. Ensure the control panel box free from water leakage to avoid short circuiting.
4. Do not supply mains power directly to the motor.
Battery: Your system is supplied with a 12V Lead Acid Maintenance Free Battery and a Z-Shape steel mounting bracket with screw. With the battery terminals at the bottom facing the center, position battery in the right bottom of your control board.
There are 2 plastic locating pegs molded into the control board box. You MUST mount battery upside down so as the steel mounting bracket, when installed does not contact between the battery power terminals.
230Vac-12/16Vac Transformer: Transformer can be relocated to around 150m from control box using a transformer kit (in a protective electrical box with mains lead and plug) or positioned inside the control box if mains power is available at the gate.
In either option you MUST install transformer via a RCD to avoid injury from shock as per local government electrical requirements. Always switch OFF mains power when any works is being carried out on or around gate installation. We recommend
E8 D1 Manual (Chip Software Version 1.3.0)
1 of 9
a minimum 1.5mm x 2 core direct burial garden lighting cable up to 50m and a larger
2.5 to 4 mm cable is commonly used to around 150m (requires larger VA transformers). Protect the wire ends so as not to make contact with the transformer.
DIP SWITCH setting on the control board:
[1] ON = Delay Close motor A (MT A) for 2 seconds after MT B
[1] OFF
- used in conjunction with solenoid lock
= Gate(s) open/close at same time
[2] ON
[2] OFF
= Small Reverse before opening used with 12V lock
= Gates open immediately without small reverse movement
[3] OFF & [4] OFF = Light ON (gate open) & cut off 1 min. after gate closed
[3] ON = LAMP permanently ON when Photocell detect dark ambient.
LAMP OFF, 1 minute after photocell detect bright ambient
[5] ON
[6] OFF
= Single Gate Operation (MT A) for external Push Switch
= Not in use
[7] OFF & [8] OFF = Disable Auto Close
[7] OFF & [8] ON = 015 sec. Auto Close (Pre-wired)
[7] ON & [8] OFF = 030 sec. Auto Close (Pre-wired to External Switch)
[7] ON & [8] ON = 060 sec. Auto Close
Solar Power: The system can be solar powered via an optional solar kit. You must fit a 12v solar voltage regulator connected directly to the battery.
DO NOT USE BOTH solar and mains power at the same time. Solar panel must face north and best suited within 10m of the battery. Have a minimum of 8 hours of direct sun exposure to be effective. Use a suitable 12V solar regulator installed inside your control box connected directly to your battery leads.
When connecting Solar, it’s a good practice to connect directly to the battery via a solar regulator using a piggy back female connector.
Solid Gate-Stops must be fitted in the center of driveway to give a solid pressure point between the stop and the end of each gate. Place a gate stop at the fully open position if desired. This will add strength to the system in the fully closed position and preventing damage to the arm internal parts.
Arm Condensation Drain Hole: Always mount arms with condensation drain holes facing down or water will enter motors and damage the electrics voiding the warranty. This is indicated on your arm with the red “THIS SIDE DOWN ” marking.
E8 D1 Manual (Chip Software Version 1.3.0)
2 of 9
Wiring Double Gates: Connect your arms to block MT1 and MT2. We recommend
1.5mm wire or greater. Lighter cable will restrict the performance of the system. Use a suitable electrical junction box to protect cable joints from moisture damage.
Check Motor Rotation Direction: After power supply has been connected to the
Control Panel, make sure the gate swings in the correct direction. The system will initiate an OPEN signal (green LED on board) the first time the remote is pressed.
The second time the remote is pressed the system initiates a CLOSE function (red
LED on board). Both gates should either OPEN or CLOSE in tandem.
This is important as wrong direction will cause the system work in the reverse manner.
Hint: Check the LED lights above Block 2. Green indicates an OPEN cycle and Red a CLOSING cycle. To reverse the direction of the motor, reverse the wire polarity at the Control Panel.
Setting the System:
DOUBLE Gate Operation
1. Unplug AC power and Battery (or solar positive wire if fitted) and make sure the gate(s) are completely CLOSED .
2. DIP switch 5 set to OFF position. Connect motor wires to
“MT A” and “MT B”
3. Set the ARMs in the CLOSED position and then power up the board. You will hear the relays clicking 4 times
4. Press your remote once and observe GREEN “MT A” and “MT B” Led indicating opening cycle on the D1 board. Gate is running on Slow Speed.
Note: If it is RED “MT A or B then switch OFF power and reverse the motor wire polarity to change the direction of the motor. Return to step 3. If remote does not activate check that it is tuned correctly to the receiver. If one gate only starts to open then you have pressed the single gate button on the remote…return to step 3 and use the other button on remote. You can activate the gate using an exit button/keypad if no remote is available.
5. Once the gate reaches the gate stop in the fully open position the board will automatically cutoff when high amp from the motor is measured. GREEN “MT
A” Led will go off.
6. Press transmitter again. Gates should start a close cycle. Observe the RED
“MT A and B Led indicating Closing cycle
7. When the gates stop in the fully closed position, the RED Led will go off.
High current cut-off by the circuit board is automatically achieved.
The system has now stored the range between opening and closing time. The microprocessor will automatically adjust the low speed and high speed opening / closing of the system.
Setup is now complete.
8. Test each cycle a few times to make sure the microprocessor has stored the correct range.
9. The gate will auto reverse when the system detects obstruction (high amp) during closing operation.
E8 D1 Manual (Chip Software Version 1.3.0)
3 of 9
10. The gate will stop when the system detects obstruction (high amp) during opening operation.
To Reset :
11. To RESET the Memory, remove all power sources (Mains and Battery). Wait for 30 seconds. System will reset the open / close calibration. Repeat Step #1
– 6 to set the memory.
SINGLE Gate Operation:
1. DIP switch 5 set to ON position and connect motor wires to “MT A” only
2.
Check you have no wire going to “2SIDE” at block 7. If there is you will need to reposition this to “1SIDE” as this will confuse the board and Motor B will not cut off.
3. Set the ARM in the CLOSED position and then power up the board. You will hear the relay click 4 times
4. Press your remote once and observe GREEN “MT A” Led indicating opening cycle on the D1 board. Gate is running on Slow Speed. If it is RED “MT A” then switch OFF power and reverse the motor wire polarity to change the direction of the motor. Return to step 3. If remote does not activate check that it is tuned correctly to the receiver. You can activate the gate using an exit button/keypad if no remote is available.
5. Once the gate reaches the gate stop in the fully open position the board will automatically cutoff when high amp from the motor is measured. GREEN “MT
A” Led will go off.
6. Press transmitter again. Gate should start a close cycle. Observe the RED
“MT A” Led indicating Closing cycle
7. When the gate is stopped in the fully closed position, the RED Led will go off.
Receiver Setup:
Double gate setup: The factory setting allows the operator to choose to have both gates opening or just one gate depending on the button they press on the remote.
You can change this so that either button will activate BOTH gates by moving the wire that is fitted to connector “1SIDE” to join the wire at “2SIDE” on block 7. Leave the white “COM”
Single gate setup: As the factory setting is for a double gate you will need change the wiring. Move the wire in connector “2SIDE” and place with wire in connector
“1SIDE”. Leave the white “COM”
You can relocate the receiver black box to another moisture-free location to increase signal strength using cat.5 network cable.
Antenna: The blue wire is the antenna with a tuned length. DO NOT CUT.
Adding New Remotes:
Hint: Move the main dip switches on the receiver inside your control box to the middle position and change all remotes to match this position.
Remove the back panel of remote (tiny Phillips screw) that is already working on your gate opener. Do the same to the new remote.
E8 D1 Manual (Chip Software Version 1.3.0)
4 of 9
Each switch has 3 positions (top, middle and bottom) so care must be taken when setting each DIP switch. Match the new remote DIP settings to the working (current) remote DIP switch positions.
Check the signal transmission by pressing your new remote.
Changing Remote Codes: Positioned inside your gate opener control box is the remote Receiver box with 5 wires connecting to your control board. Open this up to view the code DIP switches which is adjustable to suit your remotes.
If you change these you must also change the remote DIP switch by removing the back panel of the remote (tiny Phillips screw) and matching the receiver DIP setting to match the remote DIP. Each switch has 3 positions (top, middle and bottom) so care must be taken when setting each DIP switch. After the receiver panel is connected to the control panel, check the signal transmission.
Hint: Move the main dip switches on the receiver to the middle position and change all remotes to match this position.
12Vdc power only used: When the system is running on battery only (in the event of AC failure) the cycle will be slightly slower than if powered with transformer.
Optional 12V devices: One number of 12Vdc Output (parallel to the Battery), protected with a 1 Amp in-line fuse has been pre-wired in your control panel.
Connect the Positive (+12V) of the optional device to the wire connector with the red cable and the (Com) to the connector with the black cable.
Keypad Output to Open the Gate: Connect keypad to block 7 on the control board wi th keypad. For double gates wire signal to “2SIDE and keypad common to “COM”.
This will activate both arms on double swing setup. For Single gate setup and you want only 1 gate to open (pedestrian acce ss) connect signal to “1SIDE” and keypad common to
“COM”.
Exit Button or Intercom gate release: Connect common to block 7 terminal 2
(COM) and signal to terminal 1 (dual open) or terminal 2 (single open). This will activate both arms on double swing setup. If double setup and you want only 1 gate to open (pedestrian access) connect signal to terminal 3.
For exit buttons it does not matter which way you connect the wires at block 7 terminal 1 and 2.
E8 D1 Manual (Chip Software Version 1.3.0)
5 of 9
External auto-close switch: The switch installed at the bottom of the control panel is hard wired as 30 sec Auto Close only.
Auto Close Switch (30sec and 15sec) .
Your D1 control board comes with a pre wired 30 sec Auto Close Switch installed at the bottom of the Control Box.
1. To use this Auto Close switch, keep DIP #7 and DIP #8 on the control panel in the OFF position.
2. Turn ON the auto close switch (position 1) to activate the 30sec auto close. Turn OFF the auto close switch (position O) to deactivate the auto close function.
3. Safety Beam Sensors (photocell) MUST be installed when Auto close function is enabled to safe guard against gates closing on people and objects.
15 Second Auto-close
1. In your control box there are another 2 cables marked as 15sec Auto-close.
To change from 30sec auto-close to 15sec auto-close on the external switch, remove the two pre-wired cables from the switch and replace them with cables marked {15 sec Auto-close}
Safety infrared beams: Connect beams 12V power to block 5, terminal 1 (+) and 2
(-). Connect beams common to terminal 3 (COM) and beams signal (normally closed or NC) to 4.
Note: You will need to remove the small loop / jumper wire that is positioned between terminal 3 and 4. Replace the loop / jumper wire when beams are not in use!
Lock: Used when a 12Vdc lock is used to keep gates from being forced open when fully closed. Connect to “lock” at block 3. DIP switch 2 is placed to ON to allow lock tongue to release freely a second before gate performs an open cycle.
Loop Detector / Free Exit Function: Connect the Loop Detector signal cables to
Block 6 “CLS ONLY FREE EXIT”.
In the Free-Exit-Mode, a command via the loop detector or underground motion sensor will cause the gate the open ONLY. If another command is made (i.e another car passes through) during the opening phase, it has no effect. The gate will continue the opening cycle.
When the gate has been fully opened and stopped, the auto-close timer begins. This is the Pause-Period. If not further command is received, the gate will automatically close back at the end of the pause-period (auto-close time).
E8 D1 Manual (Chip Software Version 1.3.0)
6 of 9
If another command is made during the Pause Period, the cycle for Auto-close timer will reset and gate auto closing will commence after the end of the new cycle.
If a command is made during the closing stroke (i.e. a car passes by the loop while the gate is closing), the gate will pause and reopens.
Important Note:
Photo beams must be fitted as an additional safety device when using Free-Exit
Function and / or Auto-Close function is used.
External Light connection:
D1 Arm gate Board has a 12Vdc output on the Lamp Relay Terminal. Left terminal is negative and right is positive. This output is to energize an EXTERNAL 12Vdc relay which in turn can be used to turn on /off a higher rating electrical item such as a
Pillar Light.
Warning: All 240V wiring MUST be done by a qualified electrical person.
1. Set Dip Switch [3] and [4] to OFF Position. Active for 1min.
2. Connect a 12Vdc relay as is shown in Figure 1.
Lamp
Photocell
Relay to
Lamp
Figure 1: Connection of 12Vdc Relay for 240V lights
Note: D1 board is designed with a Lamp Photocell (bottom right side of D1 board), so that Lamp Relay will be activated only in a dark ambient environment.
In a bright ambient, the Lamp Relay is not activated in the Opening Cycle of the Arm
(Green LED). This is due to the fact that the Lamp Photocell is exposed to significant lighting.
When connected to Pillar Lights, this design prevents the Pillar Light from turning
ON during the Day.
If you wish that the Pillar Lights be turned on, irrespective of the ambient lighting, use a Dark Tape to cover the Lamp Photocell or turn the Photocell inwards when mounted in the Control Box.
Lamp Relay Activated when Lamp Photocell is covered (black-out).
Please note however, that due to the different lighting intensity, direction of lights, reflection etc in the Control Panel Box, it is possible that that Lamp Relay is activated even if the external ambient is significantly bright.
Point the lamp photocell to the side Gills of the supplied box for ambient light detection.
E8 D1 Manual (Chip Software Version 1.3.0)
7 of 9
Trouble-Shooting.
Problem: The system does not response when transmitter is pressed.
Make sure the transmitter in good condition. Ensure that the battery is functioning and LED on the transmitter lights up when button is pressed.
Replace transmitter if the LED does not light after new battery is replaced.
Try any external push buttons or exit buttons. If they activate the gate but all transmitters do not activate the gate, check receiver wiring to board.
Check remote DIP switches match the transmitter DIP Switches.
Check the wiring of the receiver panel and make sure the power is connected in correct polarity. Check also the power to the control board with the red LED at block1 is ON and the battery has 12V. Ensure 12Vdc is supplied to the receiver box.
Check arm(s) are working using power direct from the battery.
Check wires are connected properly to the control board.
Problem: The gate will open but not close
Check the wire loop is still in place on block 5 between terminal 3 and 4. If beams are fitted, check beam wiring/setup/ obstructions.
Problem: The gate does not fully open and close, or stops half way.
Ensure there is no obstruction to the movement of the gate. This could also be high resistance such as poor gate installation or high winds activating the anti-obstruction sensing. This can be verified by releasing the gate to
Emergency release mode. Manual push the gate open and close to detect any obstruction.
Ensure that on the first setting setup, the gate is fully closed before the board is initialized. Short distance detection will result in error of count for the gate opening and closing angle.
Problem: The gate does not travel smoothly when opening or closing.
Ensure there is no obstruction to the movement of the gate such as hitting the ground. This can be verified by releasing the gate to Emergency release mode. Manually swing the gate open / close to detect any tight spots.
Ensure that the gate is properly leveled and that the dimension guide for the installation of the Automatic gate is followed. Arm must not be parallel to the gate when fully open or fully closed.
Problem: Gate running slower than it normally does
System is running on battery only (eg. Solar setup) and transformer AC not connected. Check power with volt meter.
Problem: One gate opens only on a double setup. Check that the receiver is correctly connected to the control board block 7 terminal 1 for double gate activation.
Short between block 7, terminal 1 and 2 to by-pass the receiver. Remove the 2 wires from arm of the side that is not working at the control board and carefully place one on the battery positive and the other wire on the negative. This will by-pace the control board. Warning remove the arm from gate and post and care is needed when operating this test. If the arm moves in and out freely then it could be a control board issue.
E8 D1 Manual (Chip Software Version 1.3.0)
8 of 9
EASYSYSTEMS D1 SWING GATE
CONTROL BOARD (version 1.3.0)
For Single Arm Use only MOTOR A and Set
DIP#5 to ON
IR Beam
Loop
Detector
RED
BLACK
Block 1
Transformer
Block 2
MT B MT A
Block 3
LOCK
Block 4
LAMP
RELAY
Block 5
IR BEAM
NC
Block 6
P. SW.
Block 7
1/2
LIGHT
SENSOR
Lock
8Vac 8Vac to Motor A to Motor B
AC 230VAC
MAIN SUPPLY to Transformer
1 A FUSE
+
12 Vdc
Relay
L N
Connect Keypad and
Solar Regulator
(observe Polarity)
BLACK
RED
Loop
Detector
Auto Open and
Apartment
Function
To Activate
2 Gate
To Activate
1 Gate
12V 7Ah Rechargeable
Battery
E8 D1 Manual (Chip Software Version 1.3.0)
9 of 9
advertisement
Related manuals
advertisement