advertisement
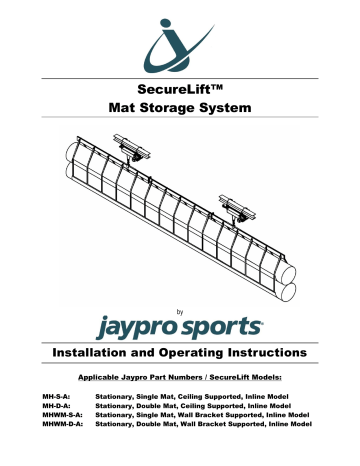
SecureLift™
Mat Storage System
by
Installation and Operating Instructions
Applicable Jaypro Part Numbers / SecureLift Models:
MH-S-A:
MH-D-A:
Stationary, Single Mat, Ceiling Supported, Inline Model
Stationary, Double Mat, Ceiling Supported, Inline Model
MHWM-S-A: Stationary, Single Mat, Wall Bracket Supported, Inline Model
MHWM-D-A: Stationary, Double Mat, Wall Bracket Supported, Inline Model
0.
Contractor Responsibilities
INSTALLER
The installer shall install the winches to support structure as instructed in section 1, assemble the load
and, once the electrician has completed power and control wiring, attach the load bar to the winches and set the winch limits (section 3).
ELECTRICIAN
The electrician shall run power and control wires per local and national code. o If the winches have not been installed, runs may be installed ahead of time using locations from prints.
Once the winches are installed, the electrician must wire the winches and keyswitch controller in order for installer to complete installation.
INSTALLER
INSTALL WINCHES
►
ELECTRICIAN
RUN POWER &
CONTROL WIRES
ASSEMBLE
LOAD BAR
►
INSTALL
KEYSWITCH
JUNCTION BOX
SET LIMIT
SWITCHES
►
WIRE WINCHES AND
KEYSWITCH
Figure 0: Workflow/Order of Operations
S ECURE L IFT M AT H OIST I NSTRUCTION M ANUAL
E
FFECTIVE
D
ATE
: 4/01/2014
L
AST
E
DITED
: 5/7/2015
P
AGE
2
OF
34
Table of Contents
S ECURE L IFT M AT H OIST I NSTRUCTION M ANUAL
E
FFECTIVE
D
ATE
: 4/01/2014
L
AST
E
DITED
: 5/7/2015
P
AGE
3
OF
34
Table of Figures
S ECURE L IFT M AT H OIST I NSTRUCTION M ANUAL
E
FFECTIVE
D
ATE
: 4/01/2014
L
AST
E
DITED
: 5/7/2015
P
AGE
4
OF
34
1.
Installation Instructions
⚠
EQUIPMENT TO BE INSTALLED BY QUALIFIED PERSONNEL ONLY
1.1.
Required installation equipment & Personnel
Installation to be carried out by no fewer than two qualified installers.
Fork lift strongly recommended for lifting winches—they are ~250lbs each—onto installation lift. o In the absence of a fork lift, it will require 4 individuals to safely raise winch onto lift.
Lift for installation capable of lifting 2 people plus one 250lb winch. o Installation of winches to support structure is a 2-person job.
1.2.
Inspection of structure
Due to the size and nature of this product the architect or structural engineer must verify structural adequacy. This product must not be installed until an authorized construction representative provides final written approval.
⚠ IMPORTANT : JAYPRO IS NOT RESPONSIBLE FOR THE STRUCTURE; JAYPRO WILL
PROVIDE DESIGN LOAD AND ATTACHMENT DETAILS ONLY
WARNING: DO NOT INSTALL PRODUCT UNLESS AN AUTHORIZED PARTY HAS DEEMED
BUILDING STRUCTURE TO BE ADEQUATE.
For an overhead unit (ceiling or roof structure supported), there must be beams (by others) located and
be installed parallel to or perpendicular to SecureLift load bar. The two winches supplied with the system are to be located on these beams. Beam flanges must be parallel and level with the floor.
If any of these criteria are not met or on-site inspection and approval has not been completed, STOP – DO
NOT PROCEED WITH INSTALLATION.
Figure 1: Beams must be large enough and spaced to install winches 22' apart on center
S ECURE L IFT M AT H OIST I NSTRUCTION M ANUAL
E
FFECTIVE
D
ATE
: 4/01/2014
L
AST
E
DITED
: 5/7/2015
P
AGE
5
OF
34
For a wall-mounted unit, the wall must be of sufficient strength to support the unit. There are wall brackets supplied with the system to hold the hoists. These wall brackets are to be installed in conformance with
below instructions (see section 1.5 for wall mount installation).
⚠ IMPORTANT: THE INTEGRITY OF THE WALL AND ITS’ CAPABILITY TO SUPPORT THIS UNIT
MUST BE VERIFIED BY THE STRUCTURAL ENGINEER OR ARCHITECT.
Figure 2: Wall Supports Shown @ 22' Apart
1.3.
Check equipment inventory
Verify all equipment is on site and in place according to the following list:
All systems: o MW4600 Mat hoist winches, 2X o Load bar sections & hardware:
2 end sections: LB15-S (single) or LB15-D (double)
1 middle section: LB13-S (single) or LB13-D (double) o Dual Operation Key Switch/Controller, 1X (Up/Down) o Shackles, 2X o Miscellaneous hardware (see parts list shipped with order for quantities) o MAT-LOK® Safety belt, 2X (optional – consult purchase order) o Mat Slings, 1X for single systems, 2X for double systems
Double mat systems only: o 5/16-3/8” Swivel pulleys, 2X
Wall mounted systems only: o Left and right wall brackets, plus cross bracing and hardware (anchors not included)
1.4.
Overhead unit winch installation
Orient both winches in the same direction (both parallel or both perpendicular to load bar). Direction of cable travel is not a critical factor, but the two hoists must be oriented identically and must be located 22 ft
There will be a slight sideways or lengthwise travel (1/4” horizontal travel for every 1ft of vertical travel) of the load bar and the suspended mats while the unit is being lifted as a direct result of the orientation of the winch drums. In either case, as shown in the images below, the distance from the wall (or other
S ECURE L IFT M AT H OIST I NSTRUCTION M ANUAL
E
FFECTIVE
D
ATE
: 4/01/2014
L
AST
E
DITED
: 5/7/2015
P
AGE
6
OF
34
obstructions) in the direction of arrows is critical. Make sure to take this into consideration when locating hoist.
Make sure winches are oriented in such a way as to allow for easy access to the limit switch access cover,
and the dead-end cable attachment holes (for double mat systems only); see Figure 4.
WARNING: MATS WILL TRAVEL AWAY FROM THE MOTOR END OF THE WINCH WHEN
RAISED, AND TOWARDS
THE MOTOR WHEN BEING LOWERED (SEE FIGURE 3).
MATS WILL TRAVEL ~¼” HORIZONTALLY FOR EVERY 1FT OF VERTICAL TRAVEL (2.5”
FOR EVERY 10 FT).
PAY PARTICULAR ATTENTION TO ORIENTATION WHEN INSTALLING SYSTEM WITH
REGARDS TO NEAREST WALL. DEPENDING ON HEIGHT OF THE WINCH ATTACHMENTS
TO THE BUILDING STRUCTURE, THIS TRAVEL CAN BE AS MUCH AS 2 FEET (24”).
DO NOT INSTALL SYSTEM SO CLOSE TO THE WALL THAT A PERSON COULD GET
INJURED! KEEP A MINIMUM OF 24” BETWEEN OUTSIDE OF MATS AND THE CLOSEST
WALL.
WALL
3’-6” MIN*
22’ 0”
Direction of travel
3’-6” MIN*
LOAD BAR LENGTH: 43’ 0”
22’ 0”
Direction of travel
WALL
*LOAD BAR MUST BE 5ft MINIMUM FROM WALLS FOR DOUBLE SIDE-BY-SIDE SYSTEMS, SEE FIGURE 26
Figure 3: Mat Travel While Lifting
S ECURE L IFT M AT H OIST I NSTRUCTION M ANUAL
E
FFECTIVE
D
ATE
: 4/01/2014
L
AST
E
DITED
: 5/7/2015
P
AGE
7
OF
34
Figure 4: Limit Switch Access & Cable Attachment
direct attachment to flanged I-beam or bar joist.
Some jobs may have custom attachments other than what is shown here – consult drawings supplied with installation packet for more details.
Make sure safety cable wraps around beam or other suitable structure.
Use ONLY GRADE 8 HARDWARE (supplied with equipment) – no substitutions allowed.
Supplied clamps and fittings will fit MOST standard beam flanges.
S ECURE L IFT M AT H OIST I NSTRUCTION M ANUAL
E
FFECTIVE
D
ATE
: 4/01/2014
L
AST
E
DITED
: 5/7/2015
P
AGE
8
OF
34
Figure 5: Flat Beam Direct Attachment Details
EACH HOIST MUST BE LEVEL WITH THE FLOOR . If this is impossible due to the orientation of the steel structure, STOP – DO NOT PROCEED WITH INSTALLATION . Support beams must be level with the floor or slippage of the winches is possible and a dangerous situation will result.
HOISTS MAY BE LOCATED AT DIFFERENT ELEVATIONS AS SHOWN IN FIGURE 6 BELOW.
Pay particular attention to leveling of hoists. Hoists must be perfectly level with floor, even when installed at different heights. Add shims or adjust nuts on threaded rods as needed. Consult installation drawings supplied with equipment for more details.
Figure 6: Hoist System Installed on Sloped Beam
S ECURE L IFT M AT H OIST I NSTRUCTION M ANUAL
E
FFECTIVE
D
ATE
: 4/01/2014
L
AST
E
DITED
: 5/7/2015
P
AGE
9
OF
34
1.5.
Wall Mount Unit Winch Installation
at this point. If for any reason you do not feel comfortable with the integrity of the wall, STOP – HAVE AN
ARCHITECT OR STRUCTURAL ENGINEER REVIEW AND VERIFY THE WALL IS CAPABLE OF
HANDLING THE LOAD.
Each winch mount may be installed at a different elevation. Make sure top surfaces of the left and right brackets of each winch mount are even with each other and are level and square with the floor.
Twelve (12) ½” Diameter thru-bolts or suitable wall anchors are required for installation of wall brackets.
USE GRADE 8 HARDWARE OR BETTER.
These anchors are the responsibility of either the installer or general contractor. Jaypro does not supply these items.
mounted installation, the winches must be oriented as shown to allow for access to wiring terminals and limit switches. If for any reason this cannot be accomplished due to obstructions or space availability,
STOP – DO NOT PROCEED WITH INSTALLATION UNTIL OBSTRUCTIONS ARE REMOVED OR
OTHER ISSUES ARE RESOLVED.
Figure 7: Wall Brackets
S ECURE L IFT M AT H OIST I NSTRUCTION M ANUAL
E
FFECTIVE
D
ATE
: 4/01/2014
L
AST
E
DITED
: 5/7/2015
P
AGE
10
OF
34
Figure 8: Example Wall Installation - Thru-Bolts
1.6.
Installer Next Steps
After securing the winches to the supporting structures, It will be necessary to call in the electrical contractor to provide and install wiring before limit switches can be set and load bar can be installed onto winch cables.
Once wiring has been completed, refer to section 3 to continue installation.
⚠ IMPORTANT: ONCE THE WINCHES ARE INSTALLED, IT IS THE ELECTRICAL
CONTRACTOR’S RESPONSIBILITY TO COMPLETE ALL WIRING IN ORDER FOR THE
INSTALLER TO BE ABLE TO COMPLETE SETUP OF SYSTEM.
S ECURE L IFT M AT H OIST I NSTRUCTION M ANUAL
E
FFECTIVE
D
ATE
: 4/01/2014
L
AST
E
DITED
: 5/7/2015
P
AGE
11
OF
34
2. WIRING INSTRUCTIONS
⚠ GROUND ALL DEVICES PER THE NATIONAL ELECTRIC CODE (NEC).
⚠ ALL WIRING TO BE SUPPLIED AND INSTALLED BY A QUALIFIED ELECTRICAL
CONTRACTOR.
⚠ WIRING TO BE IN ACCORDANCE WITH ALL NATIONAL AND LOCAL ELECTRICAL CODES.
2.1.
Required Wiring Equipment & Personnel
Wiring to be carried out by a qualified electrical contractor o Experience with Ethernet cables is recommended
RJ45 crimpers and connectors (4X) required if building Ethernet cables
LAN tester for testing Ethernet runs is strongly recommended
2.2.
Key Switch Location and Installation
Figure 9: Key switch location & complete system overview
Key switch must be installed WITHIN SIGHT of both hoists and GREATER THAN 4 feet from the end of
the suspended mats, see Figure 9
The key switch must be installed flush with the wall surface in a 3-1/2” deep1-gang masonry box (RACO
695 or equivalent).
S ECURE L IFT M AT H OIST I NSTRUCTION M ANUAL
E
FFECTIVE
D
ATE
: 4/01/2014
L
AST
E
DITED
: 5/7/2015
P
AGE
12
OF
34
Mount key switch placard as close as possible to key switch. Placard comes with an adhesive backing and should read as follows:
Figure 10: Key Switch Placard
Replacement or additional keys can be obtained directly from Jaypro. Enter the key number in the space below and make sure to have your key number handy when calling:
KEY NUMBER:
Wire key switch according to accompanying wiring diagram and as described below.
2.3.
Wiring the Controller and Winches
, Figure 13, and Figure 14 for details on power and control wiring. Details shown
are for key switch operation.
Some jobs may have custom wiring requirements (e.g. control by external device) other than what is shown here – consult drawings supplied with installation packet for more details.
Remove limit access cover (Figure 4) to access winch power wiring terminals and control jack.
Unless otherwise specified, each winch runs on 208-240VAC, 3-phase* power.
* Other voltages are available upon request (check order to confirm voltages): o 120VAC, 1Ø o 208 – 240VAC, 1Ø o 400 – 480VAC, 3Ø o 600VAC, 3Ø
These voltages are non-stock, and will incur additional costs and lead times. Please call customer service for more info
Winches are wired to the keyswitch control board via straight-through Ethernet cables. When building Ethernet cables from scratch, use of the straight-through EIA 568A or EIA 568B convention for wiring connectors is required, see Figure 11. Crossover Ethernet cables should
not be used and will cause injury or damage to the equipment or building structure.
A LAN tester is recommended to test Ethernet cables after connectors have been crimped on.
Winch numbering is not critical; i.e. either winch can be winch #1 or winch #2 as designated at key swtich control board.
S ECURE L IFT M AT H OIST I NSTRUCTION M ANUAL
E
FFECTIVE
D
ATE
: 4/01/2014
L
AST
E
DITED
: 5/7/2015
P
AGE
13
OF
34
⚠ IMPORTANT: ONCE THE POWER AND CONTROL WIRING ARE COMPLETE, TEST THAT THE
WINCHES ARE OPERATIONAL BY JOGGING EACH WINCH DOWN AND THEN UP, USING
THE BUTTONS ON THE BACK OF THE KEYSWITCH CONTROLLER.
⚠ IMPORTANT: BE SURE TO JOG WINCHES DOWN BEFORE JOGGING UP TO AVOID
PULLING CABLE INTO WINCH.
EIA 568A
STRAIGHT-THROUGH
1 2 3 4 5 6 7 8 1 2 3 4 5 6 7 8
EIA 568B
STRAIGHT-THROUGH
1 2 3 4 5 6 7 8 1 2 3 4 5 6 7 8
1 - Green/White
2 - Green
3 - Orange/White
4 - Blue
5 - Blue/White
6 - Orange
7 - Brown/White
8 - Brown
RJ45 Connector
PIN 8
PIN 1
Figure 11: Ethernet connector required wiring (EIA 568A or EIA 568B)
1 - Orange/White
2 - Orange
3 - Green/White
4 - Blue
5 - Blue/White
6 - Green
7 - Brown/White
8 - Brown
POWER
TERMINALS
(L1, L2, L3, EG)
RJ45 (ETHERNET) JACK
UP LIMIT SWITCH DOWN LIMIT SWITCH
Figure 13: Internal winch wiring
S ECURE L IFT M AT H OIST I NSTRUCTION M ANUAL
E
FFECTIVE
D
ATE
: 4/01/2014
L
AST
E
DITED
: 5/7/2015
P
AGE
14
OF
34
Individual
Winch
Operation
Buttons
Status Indicator LED
GREEN: OK
RED: FAULT
Dry Contacts
( for alternate control)
BACK
Winch 1
JACK*
Winch 2
JACK*
FRONT
*Winch numbering not critical, either winch can be #1 or #2
Figure 14: Front & back of key switch / controller
2.4. Testing the Winches
Once power is supplied to the winches, connect the Ethernet cable to the port on each winch. Test that each winch is operational by jogging each winch down and then up using the buttons on the back of the key switch controller. It is not necessary to have both winches connected to the key switch during testing. However, if only one winch is connected, it must be connected to the "Winch 1" jack. When testing, use the following precautions:
WINCH1
DOWN
WINCH1
UP a. Only push one button at a time. NEVER push a
BLUE and WHITE button simultaneously.
b. Use the push buttons only when testing one winch at a time. If you would like to test both winches at the same time, utilize the key switch by turning the key.
c. *** IMPORTANT *** When pushing the individual buttons, ensure the "WINCH1 DOWN" button causes the limit rod travel towards the
"LOWER" limit. Test all buttons and verify direction. If the buttons & limits do not coincide, DO NOT PROCEED with the installation.
Contact Jaypro Sports.
2.5. Electrian Next Steps
WINCH1
PORT
Figure 8: Back of Key
Switch Control Board
⚠ IMPORTANT: ONCE THE POWER AND CONTROL WIRING IS COMPLETE IT IS THE
INSTALLER’S RESPONSIBILITY TO COMPLETE INSTALLATION AND SETUP OF SYSTEM.
S ECURE L IFT M AT H OIST I NSTRUCTION M ANUAL
E
FFECTIVE
D
ATE
: 4/01/2014
L
AST
E
DITED
: 5/7/2015
P
AGE
15
OF
34
3. Final Setup
3.1.
Load Bar Assembly
1. Lay out three pieces of the load bar on the floor under where the winches are installed. For both splices, use eight (8) each hex head bolts, nuts, and lock washers as shown in drawing below, and assemble the sections of the load bar together. Use a torque-tightening pattern as shown to insure proper compression of lock washers. Repeat pattern as necessary until all bolts are tight.
⚠ IMPORTANT: BOLT TIGHTENING AND TORQUING SEQUENCE DIRECTLY AFFECTS THE
STRESS ON THE SPLICE PLATES AND ALIGNMENT OF THE LOAD BAR SECTIONS. BE
SURE TO FOLLOW THE TIGHTENING PATTERN AS SHOWN TO MINIMIZE THE AMOUNT OF
BOW PRESENT IN THE ASSEMBLED LOAD BAR. TORQUE FOR EACH BOLT/NUT SHOULD
BE SET TO 110 FT-LBS .
Figure 15: Load Bar Splice Hardware Assembly & Bolt Tightening Sequence
2. No substitution of factory provided hardware is allowed. Use ONLY GRADE 8 NUTS and BOLTS or
Figure 16: Hex Bolt Grade Markings
S ECURE L IFT M AT H OIST I NSTRUCTION M ANUAL
E
FFECTIVE
D
ATE
: 4/01/2014
L
AST
E
DITED
: 5/7/2015
P
AGE
16
OF
34
⚠ IMPORTANT: LOAD BAR WEIGHS APPROXIMATELY 600 LBS BY ITSELF. TAKE GREAT
CARE IN PROTECTING FINISHED FLOORING DURING THE ASSEMBLY AND HOISTING
OPERATION. ALL PERSONNEL SHOULD WEAR APPLICABLE SAFETY EQUIPMENT TO
PREVENT INJURY.
3.
After loading the load bar for the first time with weights or rolled wrestling mats double check all bolted connections and retighten as necessary.
3.2.
Cable Routing and Installation
Prior to paying out any cable, move the UPPER and LOWER limit switches outward to the ends of their
tracks (see Figure 22), but not so far as to remove them.
⚠ AT THIS POINT, THE POWER AND CONTROL WIRING TO THE WINCHES AND KEYSWITCH
CONTROLLER MUST HAVE BEEN COMPLETED TO CONTINUE WITH INSTALLATION.
CONTACT ELECTRICAL CONTRACTOR IF WIRING IS NOT COMPLETE.
In order to operate the winches individually, the key switch controller will need to be wired to the winches but removed from the junction box on the wall to allow access to the winch operation buttons on the rear of
the control board, see Figure 14.
⚠ DRUM ROTATION IS FACTORY SET. IF THE LIMIT ROD DOES NOT TRAVEL TOWARD THE
LOWER LIMIT WHEN PRESSING THE DOWN BUTTON AND THE UP LIMIT WHEN PRESSING
THE UP BUTTON, CONTACT JAYPRO SPORTS AT 800-243-0533.
3.2.1.
DOUBLE MAT HOIST SYSTEMS ONLY:
1.
First pay out enough cable (comes preassembled to drum of hoist) to reach the load bar at floor level.
2.
Pass cable end through the swivel pulley and feed back up to hoist. a.
It will be necessary to remove the side plate from the pulley to feed thimble end of cable through.
Side plate MUST be replaced before installation may proceed.
3.
Fasten the thimble end of the cable to the winch housing. a.
Choose the attachment hole for the ceiling elevation as shown in the image below. This will put the cable in the optimum position when the load bar is at the maximum raised height.
NEVER ALLOW CABLE WRAPS TO BUILD UP ON TOP OF ONE ANOTHER ON THE HOIST DRUM.
There should be more than adequate drum length to provide for sufficient lifting of hoist load bar without multiple wraps on drum.
S ECURE L IFT M AT H OIST I NSTRUCTION M ANUAL
E
FFECTIVE
D
ATE
: 4/01/2014
L
AST
E
DITED
: 5/7/2015
P
AGE
17
OF
34
⚠ IMPORTANT: THE CABLE TERMINATION POINTS ARE FOR REFERENCE ONLY. INSTALLER
SHOULD CHOOSE THE ATTACHMENT HOLE THAT ALIGNS MOST CLOSELY WITH THE
SWIVEL PULLEY WHEN THE MAT IS IN THE HIGHEST (STORAGE) POSITION AND ADJUST
AS NEEDED.
Figure 17: Bottom of Beam to Finish Floor (Double Mat Hoist Only)
Figure 18: Cable Through Pulley on Load Bar - Double Mat Hoist
S ECURE L IFT M AT H OIST I NSTRUCTION M ANUAL
E
FFECTIVE
D
ATE
: 4/01/2014
L
AST
E
DITED
: 5/7/2015
P
AGE
18
OF
34
3.2.2.
SINGLE MAT HOIST SYSTEMS ONLY:
Pay out just enough cable to reach the load bar on the floor, then assemble the dead end of the cable to the eyebolt on the load bar as shown below.
Figure 19: Cable Attached to Eyebolt via Shackle - Single Mat Hoist
NEVER ALLOW CABLE WRAPS TO BUILD UP ON TOP OF ONE ANOTHER ON THE HOIST DRUM.
There should be more than adequate drum length to provide for sufficient lifting of hoist load bar without multiple wraps on drum.
3.3.
MatLok™ Fall Arrester (Optional Equipment)
System may have been shipped with a MatLok™ fall arrester or safety strap assembly. See figure below for a general beam mounted installation. See installation drawings that accompany the MatLok™ for more information. MatLok’s™ can be ordered directly from Jaypro.
S ECURE L IFT M AT H OIST I NSTRUCTION M ANUAL
E
FFECTIVE
D
ATE
: 4/01/2014
L
AST
E
DITED
: 5/7/2015
P
AGE
19
OF
34
MLS-BM2
Parallel
Safety Strap
Sytem
MLS-BM3
Perpendicular
Safety Strap
Sytem
Figure 20: MatLok Fall Arrester Systems
3.4.
Limit Switches
3.4.1.
Limit Switch Safety Feature Description
BUFFER ZONE
SECONDARY LIMIT (REDUNDANT)
PRIMARY LIMIT
LOWER LIMITS (EACH WINCH)
Figure 21: Operating Range Between Limits
Lower Limits
The lower limit switches are wired to stop each winch independently. This means both hoists will continue to operate in the downward direction, as long as the key switch is held, until they contact their own lower limit switch.
This arrangement ensures that the system self-levels at the bottom of each up/down cycle.
o The level of the load bar is maintained by means of highly accurate vector speed controllers at the winches to ensure that they travel at identical speeds.
o It is therefore CRITICAL that the lower limits are set accurately with each end at 36±1/8”.
S ECURE L IFT M AT H OIST I NSTRUCTION M ANUAL
E
FFECTIVE
D
ATE
: 4/01/2014
L
AST
E
DITED
: 5/7/2015
P
AGE
20
OF
34
Upper Limits
The upper limits are wired in series such that they will stop at the first of the two upper limits encountered. This is by design for several reasons: o It prevents any discrepancies between the two upper limits from driving the load bar out of level when run all the way up. o It allows one of the limits to be a secondary limit that functions as a backup to the primary limit in case the primary limit fails.
This redundancy is a safety feature unique to Jaypro’s mat hoist control system.
Up Limit
(Red Leads)
Limit Rod*
*Check direction of travel
Down Limit
(Blue Leads)
Figure 22: Adjusting Limit Switches Inside Winch (Limit Cover Removed)
3.4.2.
SETTING LOWER LIMITS
1.
Use the key switch and/or individual winch controls (inside key switch box) to raise (or lower) load bar until the bottom of the bar is approximately 3’ above the floor.
2.
Using the individual winch controls on the controller (inside key switch box,
of the winches until the bottom of the load bar at the lift point is 36±1/8” off the ground.
3.
Slide the bottom limit switch of that winch into position against the limit rod and fasten it into place.
4.
Raise that winch about a foot and then lower it back down to the lower limit to confirm that it shuts off at a height of 36±1/8” off the ground. a.
If not, repeat process until desired height is reached repeatedly.
When limit is set, leave winch at lower limit and repeat process to set lower limit at other winch.
b.
5.
Once both lower limits are set individually, use the key switch to run winches until load bar moves upward approximately 24”, then back down to verify limit switches are set accurately and functioning properly. Leave load bar at lower limits.
6.
When both lower limits are set satisfactorily, keyswitch controller may be fastened to wall.
S ECURE L IFT M AT H OIST I NSTRUCTION M ANUAL
E
FFECTIVE
D
ATE
: 4/01/2014
L
AST
E
DITED
: 5/7/2015
P
AGE
21
OF
34
3.4.3.
SETTING UPPER LIMITS
1.
Use the key switch to run load bar until it is at highest safe position. This is the highest point you ever want the load bar to safely travel to, NOT the desired top resting position. a.
Typically this is about 12 – 24” above desired top resting position.
2.
Slide upper limit switch on ONE WINCH ONLY into position against limit rod and, such that switch is bottomed out against rod, and fasten into place. a.
This will be the secondary (redundant) limit and will function only as a backup in case of failure of the primary limit set below. b.
Test the secondary limit by lowering the load bar (using key switch) about 12” and raising it again to be sure that the load bar stops as expected when it reaches the secondary limit.
3.
Use key switch to lower load bar into final desired upper position (at least 12” down from previous position).
4.
Slide upper limit switch on OTHER WINCH ONLY into position against limit rod, such that switch is bottomed out against rod, and fasten into place. a.
This will be the primary upper limit and is the point where the load bar will rest when raised into its upmost position. b.
Test the primary limit by lowering the load bar (using key switch) about 12” and raising it again to be sure that the load bar stops as expected when it reaches the primary limit. i.
If set correctly, it will be lower than the secondary limit set earlier.
S ECURE L IFT M AT H OIST I NSTRUCTION M ANUAL
E
FFECTIVE
D
ATE
: 4/01/2014
L
AST
E
DITED
: 5/7/2015
P
AGE
22
OF
34
4.
Operating Instructions
4.1.
Loading Mats & Raising Mat Hoist
1.
Roll mat sections evenly and tightly before wrapping into the load bar sling.
⚠ IMPORTANT: MAT SECTIONS MUST BE CENTERED ON THE SLING.
IF THERE ARE LESS THAN THREE 15’ WIDE SECTIONS, OR THE TOTAL LENGTH OF THE
MAT IS LESS THAN 42’, THE LOAD SHOULD BE CENTERED AS BEST POSSIBLE WITHIN
THE SLING ( KEEP THE SAME NUMBER OF UNUSED STRAPS AT EACH END ).
MAT SHOULD BE NO GREATER THAN 36” IN DIAMETER WHEN ROLLED UP. IF THE
DIAMETER IS MUCH LARGER THAN THIS, SLING MAY NOT ADEQUATELY SUPPORT THE
Figure 23: Do's and Don'ts for Mat Loading on Sling
36”
Figure 24: End View of Rolled Mat - 36" Diameter
S ECURE L IFT M AT H OIST I NSTRUCTION M ANUAL
E
FFECTIVE
D
ATE
: 4/01/2014
L
AST
E
DITED
: 5/7/2015
P
AGE
23
OF
34
⚠ IMPORTANT: REPLACEMENT SLINGS SHOULD BE ORDERED AT THE FIRST SIGN OF
WEAR ON THE STRAPS. CALL FACTORY AT 1-800-243-0533 FOR ASSISTANCE.
2.
After centering rolled mat onto sling, place rings at the ends of the straps over the hooks on the load bar. Do not skip any hooks or double up multiple straps on load bar hooks. Keep straps as straight and even as possible. a.
If model is designed for two 45’ x 45’ mats (double mat hoist) there will be an upper and a lower set of hooks on the load bar. There will be a pulley connected to the eyebolt on the load bar. If this is not the case then do not lift more than one 45’ x 45’ mat with the unit.
Figure 25: End View of Double & Single Load Bar Models
3.
Make sure the slings you have are the correct ones for the given storage method required (see Figure
a.
If alternate or replacement slings are needed call Jaypro directly at 1-800-243-0533. (There are three (3) different types of slings dictated by the three models shown below – single, double, and side-by-side double or offset.) b.
There are two models of double hoists (see Figure 26)
i.
Vertical:
1.
Two mats arranged one above the other, in two different slings. a.
The upper mat uses the inner sling (short straps) and is attached to the lower set of hooks. b.
The lower mat uses the outer sling (longer straps) and is attached to the upper set of
ii.
Side-by-side:
1.
Two mats arranged next to one another, in two identical slings. a.
Each sling is attached to the upper and lower sets of hooks on the same side of the load bar. b.
The bottom hooks are used for the inside set of straps, and the top hooks are used for
the outer set of straps (see Figure 26 below).
S ECURE L IFT M AT H OIST I NSTRUCTION M ANUAL
E
FFECTIVE
D
ATE
: 4/01/2014
L
AST
E
DITED
: 5/7/2015
P
AGE
24
OF
34
LOWER SLING
UPPER SLING
Figure 26: Three End Views – Strap Placement on Load Bar Hooks
4.
Insert the key into the key switch.
5.
Turn and hold the key in UP direction.
6.
Raise unit using the key switch just enough so that the mat(s) is(are) completely off the floor.
7.
Inspect the area and make sure everything is clear before lifting higher. Make sure all strap rings are fully seated on the load bar hooks.
⚠ IMPORTANT!
DO NOT CONTINUE LIFTING WITHOUT A COMPLETE INSPECTION OF THE
ENTIRE SYSTEM AND SURROUNDING AREA.
⚠ IMPORTANT!
IF THE MAT(S) IS(ARE) SWINGING, WAIT UNTIL THEY STOP SWINGING
BEFORE YOU PROCEED.
8.
FOR SINGLE MAT AND DOUBLE SIDE-BY-SIDE SYSTEMS: a.
Raise load bar until winches stop automatically at the upper limits* of travel.
9.
FOR DOUBLE VERTICAL SYSTEMS: a.
Raise load bar until there is enough room to load the lower set of mats onto the bar. b.
Raise unit using the key switch just enough so that the mat(s) is(are) completely off the floor. c.
Inspect the area and make sure everything is clear before lifting higher. Make sure all strap rings are fully seated on the load bar hooks. Important! Do not continue lifting without a complete inspection of the entire system and surrounding area. d.
If the mat(s) is(are) swinging, wait until they stop swinging before you proceed. e.
Raise load bar until winches stop automatically at the upper limits* of travel.
*These upper limits are preset during installation and can only be adjusted by trained & authorized personnel. If you would like to have the upper limits adjusted please contact your local dealer or
Jaypro Sports directly at 800-243-0533.
WARNING: DO NOT ALLOW THE LOAD TO SWING EITHER DURING THE LIFTING
OPERATION OR WHEN THE MAT IS IN A SUSPENDED POSITION. IMMEDIATELY LOWER
TO THE FLOOR IF UNIT BECOMES UNSTABLE OR BEGINS TO SWING. MAT HOIST
EQUIPMENT DAMAGE AND POSSIBLE DAMAGE TO PORTIONS OF THE BUILDING CAN
RESULT IF THE UNIT IS INTENTIONALLY SWUNG WHILE IT IS BEING LIFTED OR IN A
SUSPENDED POSITION.
S ECURE L IFT M AT H OIST I NSTRUCTION M ANUAL
E
FFECTIVE
D
ATE
: 4/01/2014
L
AST
E
DITED
: 5/7/2015
P
AGE
25
OF
34
WARNING: NEVER ALLOW ANYONE TO RIDE ON MAT WHILE IT IS BEING LIFTED.
PERSONAL INJURY OR DEATH MAY RESULT.
4.2.
Lowering Mat Hoist
1.
Insert the key into the key switch.
2.
Turn and hold the key in DOWN direction.
3.
FOR DOUBLE VERTICAL SYSTEMS: a.
Lower load bar until the bottom set of mats touches the ground and there is just enough slack to unhook the straps from the bar. b.
Unhook one set of straps and unload the bottom set of mats.
WARNING: DO NOT ALLOW THE LOAD BAR TO COME INTO CONTACT WITH THE UPPER
SET OF MATS OR ELSE THE CABLE CAN BECOME SLACK, WHICH CAN DAMAGE THE
CABLES TO THE POINT OF FAILURE. c.
Lower load bar until BOTH winches stop automatically (i.e. until they have each reached their lower travel limits*). i.
This will allow the system to level itself. d.
Remove remaining mats. e.
Slings may be removed and stored or left on the load bar for storage.
4.
FOR SINGLE MAT AND DOUBLE SIDE-BY-SIDE SYSTEMS: a.
Lower load bar until BOTH winches stop automatically (i.e. until they have each reached their lower travel limits*). i.
This will allow the system to level itself. b.
Unhook first one side of the straps, and unload mats. c.
Sling(s) may be removed and stored or left on the load bar for storage.
⚠ IMPORTANT: IT IS CRITICAL THAT WINCHES ARE RUN ALL THE WAY DOWN TO THE
LOWER TRAVEL LIMITS TO ENSURE UNIT MAINTAINS ITSELF LEVEL WITH THE FLOOR
FOR THE LIFE OF THE SYSTEM.
⚠ IMPORTANT: IF FOR ANY REASON THE LOAD BAR APPEARS OUT OF LEVEL, RUN IT TO
THE LOWER TRAVEL LIMITS TO CORRECT ITSELF. IF UNIT DOES NOT AUTOMATICALLY
LEVEL ITSELF THEN DO NOT OPERATE FURTHER – CALL FACTORY OR SERVICE
CONTRACT REPRESENTATIVE AND SCHEDULE AN IMMEDIATE ON-SITE INSPECTION
WARNING: NEVER LOWER THE LOAD BAR TO COME INTO CONTACT WITH THE UPPER
SET OF MATS OR ELSE THE CABLE CAN BECOME SLACK, WHICH CAN CAUSE DAMAGE
TO THE CABLES, TO THE POINT OF FAILURE.
S ECURE L IFT M AT H OIST I NSTRUCTION M ANUAL
E
FFECTIVE
D
ATE
: 4/01/2014
L
AST
E
DITED
: 5/7/2015
P
AGE
26
OF
34
WARNING: NEVER LOWER THE LOAD BAR IN A MANNER THAT WILL ALLOW THE
CABLES TO BECOME SLACK. THIS CAN HAPPEN IF THE MATS ARE LOWERED ONTO ANY
OBJECT OTHER THAN THE FLOOR, OR IF THE LOAD BAR IS LOWERED ONTO THE
WRESTLING MATS (AS CAN HAPPEN WITH DOUBLE VERTICAL ARRANGEMENTS).
THIS CAN CAUSE SEVERE DAMAGE TO THE CABLES, WHICH WILL LEAVE THEM PRONE
TO FAILURE, AND WILL REQUIRE THEIR IMMEDIATE REPLACEMENT.
IF THE CABLES EVER BECOME SLACK, UNLOAD THE MATS FROM THE LOAD BAR
BEFORE ATTEMPTING TO RESTORE TENSION. INSPECT CABLE AT THE DRUM FOR
DAMAGE ONCE TENSION IS RESTORED.
4.3.
Self-Leveling of Load Bar & System Fault Detection
Each winch has a proprietary speed controller (VFD) installed within the winch housing with built-in fault detection and fault reporting to ensure that a properly installed system stays level as long as the load bar is lowered all the way down to the lower travel limits with each cycle.
Should the wiring or the hoists ever become damaged or disconnected (mechanically or electrically), the unit will cease to operate and will have to be serviced. Faults will be indicated by a red status light on the
note of the message(s) displayed on each winch and refer to section 5.8 for more information.
S ECURE L IFT M AT H OIST I NSTRUCTION M ANUAL
E
FFECTIVE
D
ATE
: 4/01/2014
L
AST
E
DITED
: 5/7/2015
P
AGE
27
OF
34
5.
Regular Equipment Maintenance
5.1.
Key Switch
Key switch is dual direction momentary actuated. No maintenance or upkeep should ever be required. For additional or replacement keys call Jaypro (you must have the key number).
In case placard becomes worn or illegible, the correct text is included here. A replacement can be ordered from Jaypro directly.
Figure 27: Key Switch Placard
5.2.
Load Bar
The load bar has a baked on powder coat finish which will give years of reliable protection to the underlying steel but may wear away or flake off in some areas. Don’t mistake this normal wear and tear as being of structural importance; unit will continue to operate flawlessly despite significant loss of cosmetic coatings.
Spray paint can be used to touch up surfaces as needed.
Periodically inspect all welds for cracking. If any damage should be discovered, the best course of action is to have a local welding contractor inspect and repair on site as needed.
Inspect all sling hooks for spreading apart and/or wear. If hooks should become significantly worn through normal use, a local weld shop should be enlisted to make necessary replacements and/or repairs.
Warning labels should be kept clean and legible. If they should become worn, damaged, or otherwise illegible, replacements should be ordered.
S ECURE L IFT M AT H OIST I NSTRUCTION M ANUAL
E
FFECTIVE
D
ATE
: 4/01/2014
L
AST
E
DITED
: 5/7/2015
P
AGE
28
OF
34
Figure 28: Load Bar Warning Label
Inspect all splice plate bolted connections for tightness. A gap between the adjoining places of two adjacent load bar sections could be indicative of bolt loosening. Replacement bolts can be ordered from Jaypro or procured at any local hardware store. Important: Replace only with GRADE 8 or better ½”-13 hex head bolts (higher grade numbers are better – higher strength steel).
Figure 29: Hex Head Bolt Grade Markings
Tighten bolts if necessary using the outline below for proper tightening sequence of the bolts. Torque of each bolt/nut should be set to 110 ft-lbs.
Figure 30: Splice Plate Bolt Tightening
S ECURE L IFT M AT H OIST I NSTRUCTION M ANUAL
E
FFECTIVE
D
ATE
: 4/01/2014
L
AST
E
DITED
: 5/7/2015
P
AGE
29
OF
34
5.3.
Pulleys (Double Mat Hoist Systems only)
Inspect pulleys and shackles for signs of damage or wear. Replace if worn or damaged. Replacements can be ordered straight from Jaypro, or from a rated supplier.
Do not substitute with pulley or block & tackle assemblies that are not rated for adequate load.
A minimum of 1.6 Ton working load at a 5:1 safety rating is required.
Any cracks or deformation in any of the components of the pulley or shackles are cause for replacement.
5.3.1.
Pulley Inspection Criteria*:
Wear on pins or axles, rope grooves, side plates, bushing or bearings, and fittings. Excessive wear is cause to remove from service and replacement.
Deformation in side plates, pins and axles, fitting attachment points, trunnions, etc. Deformation can be caused by abusive service and or overload and is cause for removal from service and replacement.
Misalignment or wobble in sheaves.
Security of nuts, bolts, and other locking methods, especially after reassembly following a tear down inspection. Original securing methods should be used; e.g., staking, set screw, cotter pin, cap screw.
Pins retained by snap rings should be checked for missing or loose rings.
Sheave pin nuts should be checked for proper positioning. Pins for tapered roller bearing should be tightened to remove all end play during sheave rotations. Pins for bronze bushings and straight roller bearings should have a running clearance of .031 inch per sheave of end play and should be adjusted accordingly.
Hook or shackle to swivel case clearance is set at .031 to .062 at the factory. Increased clearance can result from component wear. Clearance exceeding .12 to .18 should necessitate disassembly and further inspection.
Deformation or corrosion of hook and nut threads is cause for removal from service and replacement.
Welded side plates for weld corrosion or weld cracking.
*Source: The Crosby Group, Inc., P.O. Box 3128, Tulsa OK 74101, 918-834-4611)
5.3.2.
Regular Pulley Maintenance:
Apply lubrication to the following according to schedule: o Tapered roller bearings – Every 30 days of intermittent operation. o Roller bearings – Every 14 days of intermittent operation. o Bronze bearings (not self-lubricated) – Every 14 days of intermittent operation. o Bronze thrust bushing or no bearing – Every 21 days for infrequent swiveling.
5.4.
Wire Rope
Wire rope should be lubricated regularly to insure long reliable life. Obtain a suitable wire rope lubricant from local supply or hardware store. Do not use heavy grease or engine oil for lubricant. A recommended
S ECURE L IFT M AT H OIST I NSTRUCTION M ANUAL
E
FFECTIVE
D
ATE
: 4/01/2014
L
AST
E
DITED
: 5/7/2015
P
AGE
30
OF
34
penetrating lubricant is MIL-G-18458 wire rope grease. Lubrication is best applied at the point of the wire rope bending over the pulley sheave, where the strands will be temporarily and partially separated allowing the lubricant to penetrate fully.
Inspect rope for excessive damage or broken ‘threads’. See image below – if wire rope looks like either of these pictures, it’s time to replace it:
Figure 31: Worn and Damaged Wire Ropes - Replacements Required
Replacement hoist cables (wire ropes) can be obtained directly from Jaypro, or from a qualified wire rope manufacturer or supplier. Cables are 5/16” 7/19 Galvanized Cable with one end terminated with a flemished eye splice and galvanized thimble, and a 5/16” safety shackle. Larger size shackles can be used as long as they fit through end termination of cable and/or eyebolt or other connection point (as installation method dictates).
5.5.
Electric Hoists (Winches)
Hoist is maintenance free and should provide years of repeated reliable service, barring damage from other equipment, electrical surges, or other problems. Unit should nonetheless be inspected regularly and, if there is any sign of wear on the visible internal components, a qualified service technician should be called in for further study.
Inspect all attachment hardware for both the winch and the cable (in the case of the double mat hoist, the terminated loop end of the cable will be attached to the body of the winch). Retighten or replace all hardware as necessary.
5.6.
Sling and Straps
Inspect sling and integrated straps regularly for wear and/or torn fabric, or separating sewn seams.
Replacement slings can be ordered from Jaypro directly, and are offered in several color options. Call factory for more information.
5.7.
Service Plan & On-Site Maintenance Inspection
A thorough yearly inspection is recommended for entire system of hoists, cables, controller, wiring, etc. If there are no qualified personnel on site who can do this work, it is recommended that you retain the services of a maintenance technician who is experienced with this type of equipment. You can research the availability of such a service locally or call Jaypro directly for a factory representative recommendation,
800-243-0533.
S ECURE L IFT M AT H OIST I NSTRUCTION M ANUAL
E
FFECTIVE
D
ATE
: 4/01/2014
L
AST
E
DITED
: 5/7/2015
P
AGE
31
OF
34
5.8.
Investigating & Clearing a System Fault
The status LED on the key switch wall plate will turn red to when there is a system fault detected at either of the winches. When this happens, the system’s safety features will render the hoist inoperable until the fault can be cleared.
⚠ IMPORTANT: IT IS CRITICALLY IMPORTANT TO UNDERSTAND THE CAUSE FOR THE
SYSTEM FAULT BEFORE PROCEEDING WITH SYSTEM STARTUP. DO NOT PROCEED
UNLESS THE SYSTEM HAS BEEN DEEMED COMPLETELY SAFE.
5.8.1.
Fault Messages
If a fault is indicated on the key switch wall plate (status LED = red), it will be necessary to check the VFD
Status Indicator LED
GREEN: OK
RED: FAULT
FRONT
Figure 32: Fault Mode Indicator Light - Call for Service When Lit
Faults are reported on the message display of the VFD unit on the winch; remove access panel and check
details in the fault/alarm log provided(see section 5.9 on page 34).
⚠ IMPORTANT: ALWAYS USE A VOLTAGE DETECTOR TO CHECK FOR ELECTRIFICATION OF
THE METALLIC HOUSING BEFORE CONTACTING WINCH OR SUPPORT STRUCTURE
To clear a fault, cycle power to the winch(es). If the fault was only temporary, the fault message will disappear. If it reappears, the fault still exists and further corrective measures will be necessary. Contact
Jaypro Sports at 800-243-0533 for assistance.
S ECURE L IFT M AT H OIST I NSTRUCTION M ANUAL
E
FFECTIVE
D
ATE
: 4/01/2014
L
AST
E
DITED
: 5/7/2015
P
AGE
32
OF
34
Message display VFD
Figure 33: Winch VFD message display
Table 1: List of Fault Messages (F) and Warning Messages (AL)
Display
01
02
Designation
Overcurrent
Overvoltage
Possible Cause
The frequency inverter has detected an excessive current in the motor
Sudden load increase
Short circuit in motor
The DC intermediate circuit voltage has exceeded the internal safety limit
High overvoltage peaks in line power
An additional leakage current was detected when starting by means of a current measurement
Instructions
Check the load and drum for any additional loads or obstructions
Check the motor for electrical issues
Inspect building wiring
Check for local power surges
Check the electrical wiring and the motor for shorts
03 Ground fault
Insulation fault in the cables or in the motor
08
09
13
14
15
16
17
25
41
System fault
Undervoltage
Undertemperature The IGBT switch temperature is below 14°F (–10°C) Check the ambient temperature
Overtemperature
Motor stalled
CPU error message
Internal communication fault
The DC intermediate circuit voltage has exceeded the internal safety limit
Probable cause:
The supply voltage is too low
Internal device fault
Power failure
The IGBT switch temperature is above 248°F
(120°C)
An excessive temperature warning is issued if the
IGBT switch temperature goes above 230°F
(110°C)
The motor stall protection mechanism has been triggered
Reset error: Switch input voltage off and on (restart)
If the fault occurs again, contact your local representative
If a brief power failure takes place, reset the fault and restart the frequency inverter
Check the supply voltage. If it is okay, there is an internal fault If this is the case, contact your local representative
Make sure that there is an unobstructed flow of cooling air
Check the ambient temperature
Motor overtemperature
Motor underload
Watchdog (API)
IGBT overtemp
The frequency inverter’s motor temperature model has detected motor overheating.
The motor is overloaded
Motor idle, connection to load machine interrupted
(for example, torn drive belt)
Check the winch, motor, and gearbox for obstructions
&/or damage
Decrease the motor load
Allow motor to cool down 30 minutes before resuming operation
Check for obstructions to air flow around motor
Check that gearbox or drum hasn’t failed. If motor runs, but drum does not turn , there may b a failure of the gearing or drum.
Error in microprocessor monitoring
Malfunction
Component fault
The IGBT switch temperature is above 248°F
(120°C)
Reset: Switch input voltage off and on (restart)
If the fault occurs again, contact your local representative
Make sure that there is an unobstructed flow of cooling air
An excessive temperature warning is issued if the Check the ambient temperature
IGBT switch temperature goes above 230°F
(110°C)
S ECURE L IFT M AT H OIST I NSTRUCTION M ANUAL
E
FFECTIVE
D
ATE
: 4/01/2014
L
AST
E
DITED
: 5/7/2015
P
AGE
33
OF
34
5.9.
FAULT/ALARM LOG
Date
Record any faults or alarms reported by the on-board winch controller (VFD) in the table below. This will help uncover repeated failure modes and will help troubleshooting future issues.
Fault Code
(e.g. F1 10) Initials Description of problem and resolution
S ECURE L IFT M AT H OIST I NSTRUCTION M ANUAL
E
FFECTIVE
D
ATE
: 4/01/2014
L
AST
E
DITED
: 5/7/2015
P
AGE
34
OF
34
D
4
SIZE ACCORDING TO RUN
INSTALL DISCONNECTS AS REQUIRED BY CODE
(BY OTHERS)
3
MW4600
WINCH 1
MAX CURRENT: 4.3*
2
STRAIGHT-THRU
ETHERNET CABLE
Cat5 OR BETTER
(BY OTHERS)
1
KEYSWITCH INSTALLED IN 1-GANG
MASONRY BOX, RACO 695 OR EQUIVALENT
(3-½ ” DEEP MIN)
(BY OTHERS)
D
C
NOTES:
1. RJ45 CRIMPING TOOL REQUIRED IF RUNNING BARE ETHERNET CABLE.
2. ETHERNET CABLE AND RJ45 CONNECTORS BY OTHERS.
MW4600
WINCH 2
MAX CURRENT: 4.3*
*208-240VAC 3-Phase standard. Other voltages available upon request (may incur additional cost and lead time). See table below for current and circuit protection requirements.
Voltage Phases
Winch
Current
Circuit
Protection
(Each)
Circuit
Protection
(Shared Circuit)
208VAC 3 4.3
6 10
480VAC
600VAC
3
3
3.2
2
6
6
10
6
C
B
3. EIA 568A OR EIA 568B STRAIGHT-THROUGH ETHERNET CABLE CONVENTION ONLY. DO NOT USE
CROSSOVER ETHERNET CABLE CONVENTION OR DAMAGE MAY OCCUR. LAN CABLE TESTER
STRONGLY RECOMMENDED IF BUILDING ETHERNET CABLES. REFER TO INSTALLATION MANUAL FOR
ADDITIONAL INFORMATION.
A
4. SIZE POWER CABLE (BY OTHERS) ACCORDING TO RUNS a. INSTALL DISCONNECTS AS REQUIRED BY CODE
5. KEYSWITCH-CONTROL BOARD INSTALLED IN 1-GANG MASONRY BOX.
a. 1-GANG BOX BY OTHERS, RACO 695 OR EQUIVALENT (3-½ ” DEEP MIN) b. MUST BE INSTALLED WITH CLEAR UNOBSTRUCTED VIEW OF MAT HOIST c. MUST NOT BE LOCATED DIRECTLY UNDER MAT HOIST i. MUST BE CLEAR OF 45' MATS BY AT LEAST 4 FEET WHEN MATS ARE IN LOWERED POSITION
6. EACH WINCH MUST BE TESTED INDIVIDUALLY AND DIRECTIONS OF OPERATION CONFIRMED BEFORE
HOOKING BOTH WINCHES TO THE KEY SWITCH CONTROLLER. FAILURE TO DO SO MAY RESULT IN
DAMAGE TO THE SYSTEM. REFER TO THE INSTALLATION MANUAL FOR ADDITIONAL INFORMATION.
4 3
SYSTEM
Mat Hoist, Single Mat
PART NUMBER
MH-S-A
Mat Hoist, Double Mat MH-D-A
Mat Hoist, Wall Mount, Single Mat MHWM-S-A
Mat Hoist, Wall Mount, Double Mat MHWM-D-A
B
PHONE:
800.243.0533
860.447.3001
FAX:
860.444.1779
860.440.0628
DESCRIPTI ON
MH-@-A
MATERIAL:
JAYPRO SPORT, LLC, 976 HARTFORD TURNPIKE, WATERFORD, CT 06385 USA
WWW.JAYPRO.COM
External Wiring System Overview - 3-Phase
PART NUMBER:
REV: DATE: DRAWN BY:
C 1/30/19 BSA
FINISH:
SHEET #:
1 of 1
TOLERANCES
X. = ±1.0
”
X.X = ±0.5"
X.XX = ±0.25"
X/X = 1/16"
X° = ±1°
PROJECTION METHOD
-UNLES S OTHE RW IS E SP ECI FIE D-
COLO R: UNITS:
INCH
THE SE DRA WINGS A RE THE SOLE P ROP ERTY OF J AY PRO SP ORTS I NC A ND MA Y NOT BE RE PRODUCED WITHOUT WRIT TEN PE RMI SS ION OR CONS ENT
A
2 1
D
4
SIZE ACCORDING TO RUN
INSTALL DISCONNECTS AS REQUIRED BY CODE
(BY OTHERS)
3
L/L1
N/L2
EG
MW4600
WINCH 1*
2 1
STRAIGHT-THRU
ETHERNET CABLE
Cat5 OR BETTER
(BY OTHERS)
KEYSWITCH INSTALLED IN 1-GANG
MASONRY BOX, RACO 695 OR EQUIVALENT
(3-½ ” DEEP MIN)
(BY OTHERS)
D
C
NOTES:
1. RJ45 CRIMPING TOOL REQUIRED IF RUNNING BARE ETHERNET CABLE.
2. ETHERNET CABLE AND RJ45 CONNECTORS BY OTHERS.
L/L1
N/L2
EG
MW4600
WINCH 2*
*208-240VAC 3-Phase standard. Other voltages available upon request (may incur additional cost and lead time). See table below for current and circuit protection requirements.
Voltage Phases
Winch
Current
Circuit
Protection
(Each)
Circuit
Protection
(Shared Circuit)
120VAC
208VAC
1
1
15
8.3
20
10
40
20
C
B
A
3. EIA 568A OR EIA 568B STRAIGHT-THROUGH ETHERNET CABLE CONVENTION ONLY. DO NOT USE
CROSSOVER ETHERNET CABLE CONVENTION OR DAMAGE MAY OCCUR. LAN CABLE TESTER
STRONGLY RECOMMENDED IF BUILDING ETHERNET CABLES. REFER TO INSTALLATION MANUAL FOR
ADDITIONAL INFORMATION.
SYSTEM
Mat Hoist, Single Mat
PART NUMBER
MH-S-A
Mat Hoist, Double Mat MH-D-A
Mat Hoist, Wall Mount, Single Mat MHWM-S-A
4. SIZE POWER CABLE (BY OTHERS) ACCORDING TO RUNS a. INSTALL DISCONNECTS AS REQUIRED BY CODE
Mat Hoist, Wall Mount, Double Mat MHWM-D-A
5. KEYSWITCH-CONTROL BOARD INSTALLED IN 1-GANG MASONRY BOX.
a. 1-GANG BOX BY OTHERS, RACO 695 OR EQUIVALENT (3-½ b. MUST BE INSTALLED WITH CLEAR UNOBSTRUCTED VIEW OF MAT HOIST c. MUST NOT BE LOCATED DIRECTLY UNDER MAT HOIST
” DEEP MIN) i. MUST BE CLEAR OF 45' MATS BY AT LEAST 4 FEET WHEN MATS ARE IN LOWERED POSITION
6. EACH WINCH MUST BE TESTED INDIVIDUALLY AND DIRECTIONS OF OPERATION CONFIRMED BEFORE
HOOKING BOTH WINCHES TO THE KEY SWITCH CONTROLLER. FAILURE TO DO SO MAY RESULT IN
DAMAGE TO THE SYSTEM. REFER TO THE INSTALLATION MANUAL FOR ADDITIONAL INFORMATION.
PHONE:
800.243.0533
860.447.3001
FAX:
860.444.1779
860.440.0628
DESCRIPTI ON
MH-@-A
MATERIAL:
JAYPRO SPORT, LLC, 976 HARTFORD TURNPIKE, WATERFORD, CT 06385 USA
WWW.JAYPRO.COM
External Wiring System Overview - 1-Phase
PART NUMBER:
REV: DATE: DRAWN BY:
C 1/30/19 BSA
FINISH:
SHEET #:
1 of 1
TOLERANCES
X. = ±1.0
”
X.X = ±0.5"
X.XX = ±0.25"
X/X = 1/16"
X° = ±1°
PROJECTION METHOD
-UNLES S OTHE RW IS E SP ECI FIE D-
COLO R: UNITS:
INCH
THE SE DRA WINGS A RE THE SOLE P ROP ERTY OF J AY PRO SP ORTS I NC A ND MA Y NOT BE RE PRODUCED WITHOUT WRIT TEN PE RMI SS ION OR CONS ENT
B
A
4 3 2 1
advertisement
Related manuals
advertisement
Table of contents
- 2 Contractor Responsibilities
- 5 Installation Instructions
- 5 Required installation equipment & Personnel
- 5 Inspection of structure
- 6 Check equipment inventory
- 6 Overhead unit winch installation
- 10 Wall Mount Unit Winch Installation
- 11 Installer Next Steps
- 12 WIRING INSTRUCTIONS
- 12 Required Wiring Equipment & Personnel
- 12 Key Switch Location and Installation
- 13 Wiring the Controller and Winches
- 16 Final Setup
- 16 Load Bar Assembly
- 17 Cable Routing and Installation
- 17 DOUBLE MAT HOIST SYSTEMS ONLY
- 19 SINGLE MAT HOIST SYSTEMS ONLY
- 19 MatLok™ Fall Arrester (Optional Equipment)
- 20 Limit Switches
- 20 Limit Switch Safety Feature Description
- 21 SETTING LOWER LIMITS
- 22 SETTING UPPER LIMITS
- 23 Operating Instructions
- 23 Loading Mats & Raising Mat Hoist
- 26 Lowering Mat Hoist
- 27 Self-Leveling of Load Bar & System Fault Detection
- 28 Regular Equipment Maintenance
- 28 Key Switch
- 28 Load Bar
- 30 Pulleys (Double Mat Hoist Systems only)
- 30 Pulley Inspection Criteria
- 30 Regular Pulley Maintenance
- 30 Wire Rope
- 31 Electric Hoists (Winches)