advertisement
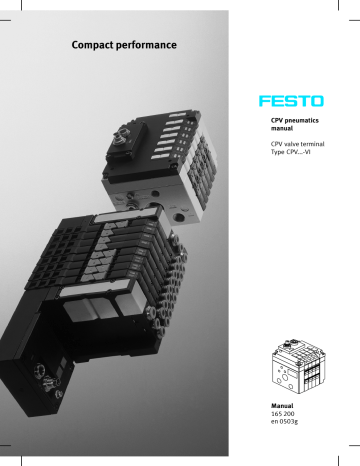
Compact performance
CPV pneumatics manual
CPV valve terminal
Type CPV...−VI
Manual
165 200 en 0503g
Contents and general instructions
Author . . . . . . . . . . . . . . . . . . . . . . . . . . . . . . . . . M. Simons
Editors . . . . . . . . . . . . . . . . . . . . . . . . H.J. Drung, M. Holder
Original . . . . . . . . . . . . . . . . . . . . . . . . . . . . . . . . . . . . . . . de
Layout . . . . . . . . . . . . . . . . . . . Festo AG & Co., Dept. KG−GD
Type setting . . . . . . . . . . . . . . . . . . . . . . . . . . . . . . . . . . KI−DT
Edition . . . . . . . . . . . . . . . . . . . . . . . . . . . . . . . . . . en 0503g
Designation . . . . . . . . . . . . . . . . . . . . . . . . . . . . P.BE−CPV−EN
Order no.
. . . . . . . . . . . . . . . . . . . . . . . . . . . . . . . . . 165 200
AS−Interface ® is a registered trademark of AS−Interface
Association
E (Festo AG&Co., D73726 Esslingen, Federal Republic of
Germany, 2002)
Internet: http://www.festo.com
E−Mail: [email protected]
The copying, distribution and utilization of this document as well as the communication of its contents to others without expressed authorization is prohibited. Offenders will be held liable for the payment of damages. All rights reserved, in par ticular the right to carry out patent, utility model or orna mental design registrations.
Festo P.BE−CPV−EN en 0503g
I
Contents and general instructions
II
Festo P.BE−CPV−EN en 0503g
Contents and general instructions
Contents
Designated use
Target group
. . . . . . . . . . . . . . . . . . . . . . . . . . . . . . . . . . . . . . . . . . . . . . . . . . . . . . . .
. . . . . . . . . . . . . . . . . . . . . . . . . . . . . . . . . . . . . . . . . . . . . . . . . . . . . . . . . .
Service . . . . . . . . . . . . . . . . . . . . . . . . . . . . . . . . . . . . . . . . . . . . . . . . . . . . . . . . . . . . . . .
Notes on the use of this manual . . . . . . . . . . . . . . . . . . . . . . . . . . . . . . . . . . . . . . . . . . .
Important user instructions
List of abbreviations
. . . . . . . . . . . . . . . . . . . . . . . . . . . . . . . . . . . . . . . . . . . . . .
. . . . . . . . . . . . . . . . . . . . . . . . . . . . . . . . . . . . . . . . . . . . . . . . . . . .
1.
1.1
1.2
Sysytem summary . . . . . . . . . . . . . . . . . . . . . . . . . . . . . . . . . . . . . . . . . . . . . .
Description of variants . . . . . . . . . . . . . . . . . . . . . . . . . . . . . . . . . . . . . . . . . . .
Description of components . . . . . . . . . . . . . . . . . . . . . . . . . . . . . . . . . . . . . . .
1−1
1−3
1−6
V
VI
VI
VI
X
XII
2.
2.1
2.2
2.3
2.4
2.5
Fitting . . . . . . . . . . . . . . . . . . . . . . . . . . . . . . . . . . . . . . . . . . . . . . . . . . . . . . . .
CPV valve terminal with individual tubing
2.1.1
Fitting onto a wall
. . . . . . . . . . . . . . . . . . . . . . . . . . .
. . . . . . . . . . . . . . . . . . . . . . . . . . . . . . . . . . . . . . .
2.1.2
Fitting onto a hat rail . . . . . . . . . . . . . . . . . . . . . . . . . . . . . . . . . . . . .
2.1.3
Fitting onto a stand . . . . . . . . . . . . . . . . . . . . . . . . . . . . . . . . . . . . . .
2.1.4
Fitting the CPV valve terminal to the SIMATIC ET200X . . . . . . . . . .
CPV valve terminal with pneumatic multipin
2.2.1
Fitting the pneumatic multipin
. . . . . . . . . . . . . . . . . . . . . . . . .
. . . . . . . . . . . . . . . . . . . . . . . . . . . . .
2.2.2
Fitting the CPV valve terminal to the pneumatic multipin . . . . . . . .
Fitting the valve extensions . . . . . . . . . . . . . . . . . . . . . . . . . . . . . . . . . . . . . . .
Fitting the identifier support . . . . . . . . . . . . . . . . . . . . . . . . . . . . . . . . . . . . . .
Fitting the manual override cover . . . . . . . . . . . . . . . . . . . . . . . . . . . . . . . . . .
2−1
2−3
2−4
2−9
2−12
2−14
2−17
2−18
2−22
2−23
2−24
2−25
3.
3.1
3.2
3.3
Installation . . . . . . . . . . . . . . . . . . . . . . . . . . . . . . . . . . . . . . . . . . . . . . . . . . .
Preparing the compressed air . . . . . . . . . . . . . . . . . . . . . . . . . . . . . . . . . . . . .
3.1.1
Operation with non−lubricated compressed air . . . . . . . . . . . . . . . .
3.1.2
Operation with lubricated compressed air . . . . . . . . . . . . . . . . . . . .
General connecting methods . . . . . . . . . . . . . . . . . . . . . . . . . . . . . . . . . . . . . .
Connecting the CPV valve terminal . . . . . . . . . . . . . . . . . . . . . . . . . . . . . . . . .
3.3.1
Auxiliary pilot air . . . . . . . . . . . . . . . . . . . . . . . . . . . . . . . . . . . . . . . .
3.3.2
Connecting the supply and work lines . . . . . . . . . . . . . . . . . . . . . . .
3.3.3
Connecting the electric cables . . . . . . . . . . . . . . . . . . . . . . . . . . . . .
3−1
3−8
3−8
3−11
3−16
3−3
3−3
3−4
3−6
Festo P.BE−CPV−EN en 0503g
III
Contents and general instructions
5.3
5.4
5.5
5.6
5.7
5.8
4.
4.1
4.2
4.3
5.
5.1
5.2
A.
A.1
A.2
B.
B.1
B.2
C.
C.1
Commissioning . . . . . . . . . . . . . . . . . . . . . . . . . . . . . . . . . . . . . . . . . . . . . . . . 4−1
General instructions . . . . . . . . . . . . . . . . . . . . . . . . . . . . . . . . . . . . . . . . . . . . .
Testing the valves . . . . . . . . . . . . . . . . . . . . . . . . . . . . . . . . . . . . . . . . . . . . . . .
4.2.1
Checking the valve functions . . . . . . . . . . . . . . . . . . . . . . . . . . . . . .
4.2.2
Checking the valve−cylinder combination . . . . . . . . . . . . . . . . . . . .
Eliminating faults . . . . . . . . . . . . . . . . . . . . . . . . . . . . . . . . . . . . . . . . . . . . . . .
4−3
4−6
4−7
4−9
4−13
Maintenance and conversion . . . . . . . . . . . . . . . . . . . . . . . . . . . . . . . . . . . . . 5−1
Cleaning/replacing the large surface−mounted silencer . . . . . . . . . . . . . . . .
Fitting/removing CPV valve terminal components . . . . . . . . . . . . . . . . . . . . .
5.2.1
Removing components from valve locations . . . . . . . . . . . . . . . . . .
5.2.2
Fitting components in valve locations . . . . . . . . . . . . . . . . . . . . . . .
Conversion from non−locking to locking manual override . . . . . . . . . . . . . . .
Converting the end plates . . . . . . . . . . . . . . . . . . . . . . . . . . . . . . . . . . . . . . . .
Conversion to internal or external auxiliary pilot air . . . . . . . . . . . . . . . . . . .
Conversion to individual tubing/central tubing . . . . . . . . . . . . . . . . . . . . . . .
Conversion of the CPV valve terminal to two pressure zones . . . . . . . . . . . .
Converting the CPV valve terminal to a variant with different electrical connections . . . . . . . . . . . . . . . . . . . . . . . . . . . . . . . . . . . . . . . . . . .
5−3
5−4
5−6
5−10
5−16
5−17
5−19
5−20
5−21
5−22
Technical appendix . . . . . . . . . . . . . . . . . . . . . . . . . . . . . . . . . . . . . . . . . . . . . A−1
Technical specifications . . . . . . . . . . . . . . . . . . . . . . . . . . . . . . . . . . . . . . . . . .
Accessories . . . . . . . . . . . . . . . . . . . . . . . . . . . . . . . . . . . . . . . . . . . . . . . . . . . .
A−3
A−10
Summary of components . . . . . . . . . . . . . . . . . . . . . . . . . . . . . . . . . . . . . . . .
Overview of valve sub−bases and vacuum generator plates . . . . . . . . . . . . .
Overview of end plates . . . . . . . . . . . . . . . . . . . . . . . . . . . . . . . . . . . . . . . . . .
B−1
B−3
B−8
Index . . . . . . . . . . . . . . . . . . . . . . . . . . . . . . . . . . . . . . . . . . . . . . . . . . . . . . . . .
Index . . . . . . . . . . . . . . . . . . . . . . . . . . . . . . . . . . . . . . . . . . . . . . . . . . . . . . . . .
C−1
C−3
IV
Festo P.BE−CPV−EN en 0503g
Contents and general instructions
Designated use
The CPV valve terminals described in this manual are in tended for fitting into a machine or automated system. The user must at all times observe the safety regulations speci fied in this manual as well as the instructions concerning the designated use of the relevant CPV valve terminal. CPV valve terminals may only be used as follows: in accordance with designated use in their original state without any modifications by the user in faultless technical condition.
When used together with commercially available compo nents, such as sensors and actuators, the specified limits for pressures, temperatures, electrical data, torques etc. must be observed. National and local safety regulations must also be observed.
Warning
If the terminal is to be used as an explosion−proof operat ing media, make sure that:
· the electrical connections are not disconnected when power is applied.
· the completely fitted product with all plugs, adapters and protective caps used complies at least with protec tion class IP64.
Festo P.BE−CPV−EN en 0503g
V
Contents and general instructions
Target group
This manual is intended exclusively for technicians trained in control and automation technology, who have experience in fitting, installing, commissioning, servicing and converting pneumatic components.
Service
Please consult your local Festo service centre if you have any technical problems.
Notes on the use of this manual
This manual contains specific information on fitting, installing, commissioning, servicing and converting the CPV valve ter minal. This manual describes only the pneumatic components and refers to the CPV valve terminal variants listed in the table below.
VI
Festo P.BE−CPV−EN en 0503g
Contents and general instructions
Variants of the CPV valve terminal type CPV...−VI..
With IC connection
Information on the electric/electronic components:
In this manual
With MP connection
Information on the electric/electronic components:
See leaflet with product
With CP connection
Information on the electric/electronic components:
See manual "CP system, installation and commis sioning
With CP direct connection
Information on the electric/electronic components:
See manual "CPV valve terminal, with direct connection" for the relevant field bus
Ò Ò Ò Ò Ò Ò Ò Ò Ò Ò Ò Ò Ò Ò Ò Ò
Tab.0/1: Variants of the CPV valve terminal
With AS−Interface connection
Information on the electric/electronic components:
See leaflet with product
Ò Ò Ò Ò Ò Ò Ò Ò Ò Ò Ò Ò Ò Ò Ò Ò
ÒÒ Ò Ò Ò Ò Ò Ò Ò Ò Ò Ò ÒÒ ÒÒ
Information on further CP modules, as well as basic informa tion which must be observed in conjunction with the higher− order system, can be found in the manuals for the relevant modules/systems.
The table below gives an overview.
Festo P.BE−CPV−EN en 0503g
VII
Contents and general instructions
Manuals on the CP system
Description CP system, installation and commissioning"
Type P.BE−CPSYS−...
Contents General basic information on the method of operation, fitting, installation and commissioning of CP systems.
Description CP field bus node, programming and diagnosis"
Type P.BE−CP−FB...
or P.BE−VIFB...−10...
CPV valve terminal, pneumatics" or
"CPA valve terminal, pneumatics"
Type P.BE−CPV−...
or P.BE−CPA−...
CP modules, electronics"
Type P.BE−CPEA−...
Contents Special information on commissioning, programming and diagnosing related to the node used.
Information on fitting, installing and com missioning CPA or
CPV valve terminals
Information on fitting, installing and commissioning CP
I/O modules
Periph erals
ÔÔ
Ô Ô Ö ÔÔ ÔÔ Ô Ô
ÔÔ Ô ÔÔ Ö ÔÔ Ô Ô
Ò Ò Ò Ò Ò Ò Ò Ò
Ò Ò Ò Ò Ò Ò Ò Ò
Tab.0/2: Manuals on the CP system
VIII
Festo P.BE−CPV−EN en 0503g
Contents and general instructions
Manuals on the SPC200 Smart Positioning Controller
Manuals SPC200 Smart Positioning
Controller, User manual
Type P.BE−SPC200−...
WinPISA manual
Type P.SW−WIN−PISA−...
Peripherals
Manuals on:
Proportional directional
Contents Installation, commissioning and diagnosis with SPC200; standard components and modules
Functions of the WinPISA software package
Description CPV valve terminal, pneumatics
Contents
Type P.BE−CPV−...
Information on the CPV valve terminals
CP modules, electronics
Type P.BE−CPEA−...
Information on the CP
I/O modules
Service unit
Measuring system
Cylinder or linear drives
Tab.0/3: Manuals on the SPC200
Festo P.BE−CPV−EN en 0503g
IX
Contents and general instructions
Important user instructions
Danger categories
This manual contains instructions on the possible dangers which may occur if the product is not used correctly. These instructions are marked (Warning, Caution, etc.), printed on a shaded background and marked additionally with a picto gram. A distinction is made between the following danger warnings:
Warning
This means that failure to observe this instruction may result in serious personal injury or damage to property.
Caution
This means that failure to observe this instruction may result in personal injury or damage to property.
Please note
This means that failure to observe this instruction may result in damage to property.
The following pictogram marks passages in the text which describe activities with electrostatically sensitive compo nents.
Electrostatically sensitive components may be damaged if they are not handled correctly.
X
Festo P.BE−CPV−EN en 0503g
Contents and general instructions
Marking special information
The following pictograms mark passages in the text contain ing special information.
Pictograms
Information:
Recommendations, tips and references to other sources of information.
Accessories:
Information on necessary or sensible accessories for the
Festo product.
Environment:
Information on environment−friendly use of Festo products.
Text markings
· The bullet indicates activities which may be carried out in any order.
1. Figures denote activities which must be carried out in the numerical order specified.
Hyphens indicate general activities.
Festo P.BE−CPV−EN en 0503g
XI
Contents and general instructions
List of abbreviations
The following product−specific terms and abbreviations are used in this manual:
Term Meaning
AS−Interface A ctuator S ensor I nterface
AS−Interface connection CPV valve terminal variant with serial connections which enables the CPV valve terminal to be connected to the AS−Interface bus.
Blanking plate
Components
Connecting the tubing
CP
CPcable
CPconnection
CP modules
Plate without valve function in order to fill an unused location.
Common term for sub−bases, end plates, relay plates, blanking plates, separator plates, valve sub−bases, valve extensions, vacuum generator plates and pneumatic multipin.
Connecting the supply lines (tubing) to the CPV valve terminal
C ompact P erformance
Special cable for coupling the various CP modules
CPV valve terminal variant with plug and socket which enables the
CPV valve terminal to be connected to a field bus node and further
CP modules.
Common term for various modules which can be incorporated in a
CP system.
CP system
CPV valve terminal
CPV10
CPV14
CPV18
DI connection
Complete system consisting of CP field bus node and CP modules.
Note the following on CPV valve terminals (type 10) with IC, MP, DI or
AS−Interface connections.
Size designations of the CPV valve terminals:
with micro valve sub−bases (CPV10),
with mini valve sub−bases (CPV14)
with midi valve sub−bases (CPV18)
Electrical sub−base
CPV valve terminal variant with plug and socket which can be connected directly with the field bus and with further CP modules, depending on type.
Note the following with the MP, AS−Interface, DI and CP connections.
XII
Festo P.BE−CPV−EN en 0503g
Contents and general instructions
Term
End plate
Meaning
Cover plate at the left and right−hand ends of the CPV valve terminal with channels or connections for supplying the valves with compressed air and for conducting the exhaust air.
IC connection
(individual connection)
I/O
Manual override
MP connection
(multipin connection)
Pneumatic multipin
CPV valve terminal variant on which every valve solenoid coil can be connected individually with a special CP cable.
Input/output modules
Manual override
CPV valve terminal variant with sub−D plug via which all valve solenoid coils are connected centrally.
Plate for central tubing connections on the valve terminal (supply air, exhaust air and work air connections).
Relay plate
Separator plate
Plate with relay coils for actuating two electrically−isolated outputs.
Plate for dividing the valve terminal into two/four pressure zones.
Vacuum generator plate Plate with vacuum generator (with or without reject pulse)
Valve block Basic unit with valve sub−base, vacuum generator plate, separator, blanking, relay and end plates
Valve sub−base
5/3G valve extension
Plate with single−solenoid or double−solenoid valves
Module with two unlockable non−return valves. With the CPV10/14 valve terminals, the valve function 5/3−way in mid−position blocked" is implemented with this module and the valve sub−base Ident. code C.
Tab.0/4: Product−specific terms and abbreviations
Festo P.BE−CPV−EN en 0503g
XIII
Contents and general instructions
XIV
Festo P.BE−CPV−EN en 0503g
Sysytem summary
Chapter 1
Festo P.BE−CPV−EN en 0503g
1−1
1. Sysytem summary
Contents
1.
1.1
1.2
Sysytem summary . . . . . . . . . . . . . . . . . . . . . . . . . . . . . . . . . . . . . . . . . . . . . .
Description of variants . . . . . . . . . . . . . . . . . . . . . . . . . . . . . . . . . . . . . . . . . . .
Description of components . . . . . . . . . . . . . . . . . . . . . . . . . . . . . . . . . . . . . . .
1−1
1−3
1−6
1−2
Festo P.BE−CPV−EN en 0503g
1. Sysytem summary
1.1
Description of variants
Festo assists you in solving your automation tasks at machine level with valve terminals. The modular structure of the CP system enables you to incorporate the CP valve terminals and
I/O modules optimally in your machine or system.
Due to its compact structure the CP valve terminal can be mounted close to the actuators to be controlled. Short com pressed air tubing can therefore be used. System losses can therefore be minimized and the times required for pressuriz ing and exhausting the tubing can be minimized. This is made possible by the use of very compact valves with high flow rate, therefore helping to reduce costs.
Festo P.BE−CPV−EN en 0503g
1−3
1. Sysytem summary
CPV valve terminal variants The CPV valve terminals are available with the following types of electrical connections:
IC connection MP connection
CP direct connection
CP connection
AS−Interface connection
Fig.1/1: Variants of the CPV valve terminal
CPV valve terminal with
IC connection
The CPV valve terminal with IC connection is available with 2 to 8 valve sub−bases (also in odd gradation). The electrical connection is made individually on each valve solenoid coil.
CPV valve terminal with
MP connection
This CPV valve terminal is available with 4, 6 or 8 valve sub− bases. The electrical connection of the valve solenoid coils is made centrally via the multipin connection.
CPV valve terminal with
CP connection
The CPV valve terminal with CP connection is available with
4, 6 or 8 valve sub−bases. The connection to the higher− order field bus node is made via special ready−to−use CP cables.
1−4
Festo P.BE−CPV−EN en 0503g
1. Sysytem summary
CPV valve terminal with
DI connection
The CPV valve terminals with direct connection are available for the following field bus systems in the sizes
CPV10/14/18:
CANopen
DeviceNet
Honeywell SDS
Interbus Local bus (only in sizes CPV10/14)
PROFIBUS DP, Festo field bus, ABB CS 31, Klöckner−
Moeller SUCOnet K
These valve terminals can be connected directly to the rel evant field bus. These CPV valve terminals are fitted with 4 or
8 valve sub−bases depending on the field bus system.
CPV valve terminal with
AS−Interface connection
This CPV valve terminal is connected to the AS−Interface bus via special AS−Interface cables. It is available with 2, 4 or 8 valve sub−bases depending on the variant and with four different kinds of electrical connections: with additional supply connection for implementing an emergency stop function, with additional supply connection and 4 or 8 inputs (not
CPV18), without additional supply connection, without additional supply connection with 4 or 8 inputs
(not CPV18).
Festo P.BE−CPV−EN en 0503g
1−5
1. Sysytem summary
The CPV valve terminals with AS−Interface connection can be fitted with max. following valve sub−bases:
Valve sub−base with ...
... two 2/2−way valves (single−solenoid)
... two 3/2−way valves (single−solenoid)
... 5/2−way valve (single−solenoid)
... 5/2−way valve (double−solenoid)
... 5/3−way valve
2
1
1
1
1
ASI−2 (...−Z) ASI−4 (...Z)
...ASI−4E4A (...−Z)
...ASI−8E8A−Z
4
2
2
2
2 −
8
4
4
4
Tab.1/1: Maximum number of sub−bases on the CPV valve terminals with AS−Interface connection
The CPV valve terminals with AS−Interface connection and 4 or 8 inputs have 4 or 8 valve sub−bases. These CPV valve ter minals also have blanking plates depending on the number of valve sub−bases.
1.2
Description of components
Sizes of the CPV valve terminals
The CPV valve terminals are available in the following sizes:
CPV10
CPV14
CPV18
10mm
14mm
18mm
Tab.1/2: Sizes of the CPV valve terminals
Micro valves
Mini valves
Midi valves
1−6
Festo P.BE−CPV−EN en 0503g
1. Sysytem summary
Identification code
With the identification code (I.C.) you can ascertain the equip ment fitted on your CPV valve terminal. The code is printed on the front between manual overrides 12 and 14.
I.C.
Pneumatic components
C
H
N
Valve sub−bases with 2/2−way valves
D Two 2/2−way valves, single−solenoid, basic position closed
I Two 2/2−way valves, basic position control side 14 open, control side 12 closed
Valve sub−bases with 3/2−way valves
Two 3/2−way valves, single−solenoid, basic position closed
Two 3/2−way valves, basic position control side 14 open, control side 12 closed
Two 3/2−way valves, basic position open
J
M
Valve sub−bases with 5/2−way valves
F 5/2−way valve, single−solenoid, fast−switching
5/2−way valve, double−solenoid
5/2−way valve, single−solenoid
Valve sub−bases with 5/3−way valves
G CPV10/14:
CPV18:
Two 3/2−way valves, basic position closed + valve extension 5/3G
5/3−way valve, mid−position blocked
Vacuum generator plates
A Without reject pulse
I With 2/2−way valve for reject pulse
Separator plates
S Exhaust channel (3/5) and compressed air channels (1.11) blocked
T Compressed air channels (1, 11) blocked
Blanking plate
L Plate without valve function for placing in an unused valve location
Festo P.BE−CPV−EN en 0503g
1−7
1. Sysytem summary
I.C.
Pneumatic components
Relay plate
Q
V
R Plate with two electrically−isolated relays
Valve extensions
P One−way flow control valve for restricting the supply air
One−way flow control valve for restricting the exhaust air
Flow control valve for setting the reject pulse
Tab.1/3: Identification codes of the pneumatic components
Further information on the valve sub−bases and vacuum gen erator plates can be found in Appendix B.
Valve extension 5/3G (only CPV10/14)
The valve extension 5/3G contains the function of two unlock able non−return valves. A function 5/3−way in mid−position blocked" can be implemented in conjunction with the valve sub−base with Ident code C (two 2/3−way valves in basic posi tion blocked).
Further information on valve extension 5/3G can be found under Fitting the valve extensions" in chapter 2 and under
General instructions" in chapter 4.
1−8
Festo P.BE−CPV−EN en 0503g
1. Sysytem summary
Festo P.BE−CPV−EN en 0503g
Flow control valve or one−way flow control valve extension
With the following valve extensions you can adapt the CPV valve terminal to the requirements of your machine or sys tem.
For restricting the supply or exhaust air of the valve sub− bases use valve extension:
CPV−..−BS−2xGRZZ−... for restricting the supply air
CPV−..−BS−2xGRZZ−... for restricting the exhaust air.
For restricting the reject pulse of the vacuum generator plate with Ident code E use valve extension:
CPV−..−BS−GRZ−V−...
The valve extensions are flange−fitted directly onto the valve sub−bases. It is not intended that the above−mentioned valve extensions should be combined.
Further information on the valve extensions can be found under Fitting the valve extensions" in chapter 2 and under
General instructions" in chapter 4.
Vacuum generator plates
CPV valve terminals can be fitted with vacuum generator plates for generating vacuum. Work items with a smooth and tight surface can then be sucked in.
Two types of vacuum generators are available:
Plate with switchable vacuum generator.
Plate with switchable vacuum generator and additional
2/2−way valve for generating the reject pulse.
Further information on the vacuum generator plates can be found under Vacuum generator plates" in chapter 3.3.2.
1−9
1. Sysytem summary
Separator plate
By means of separator plates you can divide the CPV valve terminals into 2 to 4 pressure zones. Two types of separator plates are available:
Separator plate with blocked compressed air channels
(1 and 11).
Only CPV10/14: Separator plate with blocked exhaust channel (3/5) and blocked compressed air channels
(1 and 11).
Relay plate
CPV10/14 valve terminals which have holding current reduc tion can be fitted witht relay plates. This applies to CPV valve terminals with the following connection:
CP connection
CPV direct connection
AS−Interface connection (only CPV10 valve terminals)
IC connection (only in combination with connector socket
KMYZ−7−24−...−LED (CPV10/14)
MP connection
Each relay plate possesses two relays for actuating two elec trically−isolated outputs.
1−10
Festo P.BE−CPV−EN en 0503g
1. Sysytem summary
Pneumatic multipin
The pneumatic multipin serves as a common connection for power supply and work tubing. The CPV valve terminal is screwed together with the pneumatic multipin and sealed with it by means of sets of seals. The pneumatic multipin per mits fast separation of the CPV valve terminal from the supply and work tubing. The pneumatic multipin is available in two forms:
Without assembly step: This variant for mounting on a stand or wall opening fits flush with the end plates. The fastening holes are in the connection side of the pneu matic multipin.
With assembly step: In this variant for fitting onto a wall or onto a stand the fastening holes are in the assembly step.
Pneumatic multipin (without step) Pneumatic multipin (with step)
1
1 1
1
Mounting holes
Fig.1/2: Variants of the pneumatic multipin
Festo P.BE−CPV−EN en 0503g
1−11
1. Sysytem summary
The CPV valve terminal can consist of the following compo nents, depending on what has been ordered:
Overview of components
1
4
6
5
1
Electrical sub−base (only CPV valve terminals with MP, AS−Interface or
CP connections)
2
Right−hand end plate (designs see
Appendix B Overview of end plates")
3
Relay plate (see also compatibility list in chapter 5)
4
Blanking plate or separator plate
(with blocked compressed air channels
1 and 11 and exhaust channel (3/5) or only blocked compressed air channels
1 and 11)
5
Valve sub−bases fitted with single− solenoid, double−solenoid or vacuum valves
6
Left−hand end plate (designs see
Appendix B Overview of end plates")
Fig.1/3: Components of the CPV valve terminal
2
3
1−12
Festo P.BE−CPV−EN en 0503g
1. Sysytem summary
Supplementary components of the CPV valve terminal
The CPV valve terminal can be supplemented optionally by the following components:
6
5 1
4
1
Manual override cover and support for identification signs, not in conjunction with relay plate
2
Pneumatic multipin
4
Support for hat rail fitting for
CPV10/14 or CPV18
5
Support for wall fitting for CPV10/14 or CPV18
3
Valve extensions (5/3G function (only
CPV10/14), vacuum restrictor valve or one−way flow control valve)
6
Fig.1/4: Supplements to the CPV valve terminal
Support for wall fitting for CPV10/14 or CPV18
2
3
Festo P.BE−CPV−EN en 0503g
1−13
1. Sysytem summary
1
Connecting, display and operating elements
You will find the following connecting, display and operating elements on the CPV valve terminal:
2 3 4
8
6
5
6
7 6 7
1
Valve location for identification signs
2
Manual override cover and support for identification signs
3
Manual override (per pilot solenoid, locking or non−locking)
6
Supply air connections (1, 11, 12/14), exhaust air connections (3/5, 82/84): with individual tubing on the left and/or right−hand end plate with central tubing on the pneumatic multipin
4
Removing the manual override cover
5
Clip of the non−locking manual override
7
Work connections (2, 4) per valve
8
Pneumatic multipin
Fig.1/5: Pneumatic connecting, display and operating elements of the CPV valve terminal
Instructions on the electrical connecting and display elements of the CPV valve terminals with direct connection can be found in the appropriate electronics manuals.
1−14
Festo P.BE−CPV−EN en 0503g
1. Sysytem summary
You will find the following electrical connecting and display elements on the CPV valve terminal with IC connection:
1 2
3
6
5
4
1
Ready−to−use connector socket (for each pilot solenoid), can be turned
180°
2
Identification sign (for each connector socket)
3
Yellow LED, signal status displays for pilot solenoid (for each connector socket)
4
Earth/ground connection
5
Terminal lugs of pilot solenoid coil 14
6
Terminal lugs of pilot solenoid coil 12
Fig.1/6: Electrical connecting and display elements of the CPV valve terminal with
IC connection
Festo P.BE−CPV−EN en 0503g
1−15
1. Sysytem summary
You will find the following electrical connecting and display elements on the CPV valve terminal with MP connection:
1
2
3
4
1
Sub−D multipin plug (9−pin for terminals with 4 valves, 25−pin for terminals with 6 or 8 valves)
2
Identification labels
3
4
Yellow LED, signal status displays of the pilot solenoids
Earth/ground connection
Fig.1/7: Electrical connecting and display elements of the CPV valve terminal with
MP connection
1−16
Festo P.BE−CPV−EN en 0503g
1. Sysytem summary
1
8
7
You will find the following electrical connecting and display elements on the CPV valve terminal with MP connection:
Î Î ÎÎ Î Î ÎÎ Î ÎÎ Î Î Î Î Î Î Î
Î ÎÎ Î Î Î ÎÎ Î Î Î Î Î Î Î Î
2
3
4
5
6
1
Incoming CP cable
2
Continuing CP cable
3
Identification labels
4
Yellow LED, signal status display of the relays
5
Yellow LED, signal status display of the pilot solenoids
6
Relay connections with connecting cable
7
Earth/ground connection
8
Green LED, status display of the
CP connection
Fig.1/8: Electrical connecting and display elements of the CPV valve terminal with
CP connection
Festo P.BE−CPV−EN en 0503g
1−17
1. Sysytem summary
9
8
7
6
You will find the following electrical connecting and display elements on the CPV valve terminal with AS−Interface connection:
Î Î Î Î
Î ÎÎ Î Î Î Î Î Î
Î Î Î Î Î Î Î Î Î Î Î ÎÎ ÎÎ Î Î
Î Î Î Î Î Î Î Î
1
AS−Interface cable cap,
(only CPV..−GE−ASI−.−Z)
2
Cable socket of the additional supply with black cable,
4
(only CPV..−GE−ASI−.−Z)
3
Sensor cable with plug
(only CPV..−GE−ASI−..E..A−...)
Identification labels
5
Yellow LED, signal status displays of the pilot solenoids
6
Earth/ground connection
7
BUS LED 1 (green),
BUS LED 2 (red),
(only CPV..−GE−ASI−..E..A−...)
8
Green LED status displays of the inputs, (only CPV..−GE−ASI−..E..A−...)
9
AS−Interface bus socket with yellow bus cable
Fig.1/9: Electrical connecting and display elements of the CPV valve terminal with
AS−Interface connection
1−18
Festo P.BE−CPV−EN en 0503g
1
2
3
4
5
Fitting
Chapter 2
Festo P.BE−CPV−EN en 0503g
2−1
2. Fitting
Contents
2.
2.1
2.2
2.3
2.4
2.5
Fitting . . . . . . . . . . . . . . . . . . . . . . . . . . . . . . . . . . . . . . . . . . . . . . . . . . . . . . . . 2−1
CPV valve terminal with individual tubing
2.1.1
Fitting onto a wall
. . . . . . . . . . . . . . . . . . . . . . . . . . .
. . . . . . . . . . . . . . . . . . . . . . . . . . . . . . . . . . . . . . .
2.1.2
Fitting onto a hat rail . . . . . . . . . . . . . . . . . . . . . . . . . . . . . . . . . . . . .
2.1.3
Fitting onto a stand . . . . . . . . . . . . . . . . . . . . . . . . . . . . . . . . . . . . . .
2.1.4
Fitting the CPV valve terminal to the SIMATIC ET200X . . . . . . . . . .
CPV valve terminal with pneumatic multipin . . . . . . . . . . . . . . . . . . . . . . . . .
2.2.1
Fitting the pneumatic multipin . . . . . . . . . . . . . . . . . . . . . . . . . . . . .
2.2.2
Fitting the CPV valve terminal to the pneumatic multipin . . . . . . . .
Fitting the valve extensions . . . . . . . . . . . . . . . . . . . . . . . . . . . . . . . . . . . . . . .
Fitting the identifier support . . . . . . . . . . . . . . . . . . . . . . . . . . . . . . . . . . . . . .
Fitting the manual override cover . . . . . . . . . . . . . . . . . . . . . . . . . . . . . . . . . .
2−3
2−4
2−9
2−12
2−14
2−17
2−18
2−22
2−23
2−24
2−25
2−2
Festo P.BE−CPV−EN en 0503g
2. Fitting
Warning
Switch off the following power supplies before undertaking installation and/or maintenance work:
· the compressed air supply
· the power supply for the valve solenoid coils
You can thereby avoid: uncontrolled movements of loose tubing, unexpected movements of the connected actuators, non−defined switching states of the electronic compo nents.
2.1
CPV valve terminal with individual tubing
Fitting variants
The CPV valve terminal with individual tubing has already been prepared for integration in a system or machine for the following fitting variants:
Fitting onto a wall
Fitting onto a hat rail
Fitting onto a stand
Please note
If vibrations, which exceed the following values, occur on your application:
0.15 mm path at 10...58 Hz
2 g acceleration at 58...150 Hz
You should mount the CPV14 or CPV18 valve terminal on a wall or on a stand.
Festo P.BE−CPV−EN en 0503g
2−3
2. Fitting
2.1.1
Fitting onto a wall
In order to fit the CPV valve terminal onto a wall, you will require the appropriate mounting kit, depending on the type of mounting. The following table provides an overview.
For rear fitting of the CPV10/14 valve terminals with direct connection for Interbus Loop (type CPV..−GE−IL−..) or
AS−Interface connection with inputs/outputs (type CPV..−GE−
ASI..E/..A) there is a special mounting kit which is not listed here.
Type of mounting
Rear
On the top (only CPV10/14 with
IC connection)
Mounting kits (consisting of 2 profile sections and 4 self−threading screws)
CPV10/14−VI−BG−RWL−B CPV10−VI−BG−ET200X
CPV18−VI−BG−RW CPV14−VI−BG−ET200X
Tab.2/1: Fastening profile sections for fitting onto a wall
2−4
Festo P.BE−CPV−EN en 0503g
2. Fitting
Proceed as follows:
· Make sure that the fastening surface can support the weight of the CPV valve terminal.
· Fit the fastening profile section to the left−hand and right− hand end plates (see Fig. 2/2). Use here the self−thread ing screws supplied (see table). When fitting the
CPV10/14 valve terminals from the rear," make sure that the fixing bolts of the fastening profile sections grip into the recess in the end plates.
Valve terminal Type of mounting rear:
Self−threading screw
Tightening torque
CPV10/14
CPV18
M4 x 10
M5 x 10
1.5 Nm
4Nm
Tab.2/2: Fitting onto a wall, tightening torques
Type of mounting top:
Self−threading screw
Tightening torque
M3 x 18 1.5 Nm ±0.2 Nm
Festo P.BE−CPV−EN en 0503g
2−5
2. Fitting
Type of mounting rear Type of mounting top
ÓÓÓ
1
1 1
ÓÓÓ
ÓÓÓ
ÓÓÓ
2
3
2
2
ÓÓÓ
2
ÓÓÓ
4
2
ÓÓÓ
ÓÓÓ
1 1
ÓÓÓ
1
M4 (CPV10/14) or M5 screw (CPV18) for fastening onto a wall
2
Additional self−threading screw with
CPV18 valve terminals
3
Self−threading screws for fastening the profile sections onto the CPV valve terminal
4
Fixing bolts (only CPV10/14)
1
5.5 mm bore for wall fastening
2
Self−threading screws for fastening the profile sections onto the CPV valve terminal
Fig.2/1: Connecting the CPV valve terminal
· Make sure there is sufficient space for connecting the power supply and compressed air tubing. For top" fit ting, a suitable spacer or appropriate cut−out wall section is required for the electrical connections (see Fig. 2/3).
Please note
The hole dimensions for rear fitting of the CPV valve terminal (Fig. 2/3) do not apply to CPV10/14 valve terminals with direct connection for Interbus Loop
(type CPV..−GE−IL−..) or AS−Interface connection with inputs/outputs (type CPV..−GE−ASI..E/..A).
2−6
Festo P.BE−CPV−EN en 0503g
2. Fitting
Type of mounting rear
4 5 4
1
2
3
6
CPV10/14
1
2
3
4
5
69 mm 1)
80 mm 1
92 mm 1)
)
14 mm (18 mm) 2)
10 mm x number of plates
(14 mm x number of plates) 2)
6 28 mm + 5 (36 mm + 5 ) 2)
CPV18
120 mm
15 mm
18 mm x number of plates
30 mm + 4
1) With CPV10/14 valve terminals the following applies:
Dimension 1 for CPV10/14 valve terminals with IC connection.
Dimension 2 for CPV valve terminal with MP, CP or AS−Interface connection
(without inputs/outputs).
Dimension 3 for CPV valve terminal with DI connection.
2) Values in brackets for CPV14.
Tab.2/3: Dimensions of the fastening holes
Festo P.BE−CPV−EN en 0503g
2−7
2. Fitting
Type of mounting top
2 3 2
1 5
7
4
6
1
2
3
CPV10
109.5 mm
26 mm
10 mm x number of plates
CPV14
109.5 mm
10 mm
14 mm x number of plates
4
5
6
7
52 mm +
120 mm
Wall cut−out if a spacer is not used
Spacer
3
1)
20 mm +
120 mm 1
3
)
1) Depends on the design of the electrical connector sockets
Tab.2/4: Dimensions of the wall cut−outs
2−8
Festo P.BE−CPV−EN en 0503g
2. Fitting
Drill four mounting holes or threaded holes in the fastening surface (see table).
Valve terminal Type of mounting rear:
Dimensions of the fastening holes
Threaded hole for
CPV10/14
CPV18
4.5 mm
5.5 mm
M4 screw
M5 screw
5.5 mm
Type of mounting top:
Dimensions of the fastening holes
Threaded hole for
M5 screw
Tab.2/5: Holes for wall fitting
· Fasten the CPV valve terminal with four M4 or M5 screws of sufficient length to the wall.
2.1.2
Fitting onto a hat rail
In order to fit the CPV valve terminal onto a hat rail you will require the following mounting kits:
CPV10/14 valve terminal:
Mounting kit CPV10/14−VI−BG−NRH−35
CPV18 valve terminal:
Mounting kit CPV18−VI−BG−NRH−35
Both mounting kits consist of 2 brackets, 2 or 4 M4x10 self− threading screws (CPV10/14) or M5x10 (CPV18) and 2 M4x10 screws with clamping elements and springs.
Festo P.BE−CPV−EN en 0503g
2−9
2. Fitting
2−10
Proceed as follows:
· Make sure that the fastening surface can support the weight of the CPV valve terminal.
· Fit the following hat rail:
Hat rail for CPV10/14 valve terminal
Hat rail for CPV18 valve terminal
Support rail DIN 50022 − 35x7.5; width 35 mm, height 7.5 mm)
Support rail DIN 50022 − 35x15
(width 35 mm, height 15 mm)
Tab.2/6: Hat rails
· Make sure that there is sufficient space for connecting the supply cables and tubing, and that extra space is avail able for fitting CPV valve terminals with large surface− mounted silencers.
· Fasten the hat rail to the fastening surface approximately every 100 mm.
· Fasten the two brackets to the end plates with the screws supplied as shown in the diagram below. With CPV10/14 valve terminals, make sure that the fastening bolts of the brackets grip into the recess in the CPV valve terminal.
CPV valve terminal
CPV10/14
CPV18
Self−threading screw
M4x10
M5x10
Tightening torque
1.5 Nm
4 Nm
Tab.2/7: Hat rail adapter, tightening torques
Festo P.BE−CPV−EN en 0503g
2. Fitting
1
Per end plate one
M4x10 screw
(CPV10), two M4x10 screws (CPV14) or M5x10
(CPV18)
2
Hat rail
3
Fixing bolts
(only CPV10/14)
4
Hat rail clamping unit
1
2
3
4
Fig.2/2: Fitting the valve terminal on a hat rail
· Hang the CPV valve terminal onto the hat rail. Secure the
CPV valve terminal on both sides with the hat rail clamp ing unit against slipping or sliding down.
Festo P.BE−CPV−EN en 0503g
2−11
2. Fitting
2.1.3
Fitting onto a stand
In order to fit the CPV valve terminal onto a stand (fitting on the level of work connections 2 and 4), you will require the following fastening screws:
4 M4x45 socket head screws (CPV10)
4 M4x50 socket head screws (CPV14)
4 M6x65 socket head screws (CPV18)
Proceed as follows:
· Prepare the mounting surface. Make a suitable bracket.
The position of and distances between the mounting holes of the CPV valve terminal are shown in the following diagram:
1
2−12
2 3 2
CPV10 valve terminal
CPV14 valve terminal
CPV18 valve terminal
1
2
3
53 mm
4 mm
10 mm x number of plates
66 mm
5 mm
14 mm x number of plates
87 mm
8.1 mm
18 mm x number of plates
Tab.2/8: Position of the fastening holes
Festo P.BE−CPV−EN en 0503g
2. Fitting
1
Socket head screws: M4 x 45 or M4 x 50 or M6 x 65
2
End plates
3
Fastening bracket
1
2
· Make sure that there is sufficient space for connecting the supply cables and tubing, and that extra space is avail able for fitting CPV valve terminals with large surface− mounted silencers.
· With CPV valve terminals with IC connection: insert the four socket head screws supplied into the holes in the left−hand and right−hand end plates (see diagram).
CPV10
M4x45
CPV14
M4x50
CPV18
M6x65 Socket head screws
Tab.2/9: Mounting on a stand, fastening screws
1
2
3
Fig.2/3: Position of the fastening holes
· Screw the CPV valve terminal to the connection surface or to the fastening bracket.
Festo P.BE−CPV−EN en 0503g
2−13
2. Fitting
2.1.4
Fitting the CPV valve terminal to the SIMATIC ET200X
Instructions on the decentral periphery device ET200X can be found in the relevant manual from SIEMENS AG.
A CPV valve terminal with:
· IC connection,
· 8 valve sub−bases,
· mounted fastening CPV..−VI−BG−ET200X
· and appropriate flat seal.
can be mounted on a pneumatic interface module type
EM 148−P−DO 16 x P/CPV.. for the decentral periphery device
ET200X.
When the terminal is fitted into place, the switching status of the valve soleoid coils can be seen on the relevant LED on the pneumatic interface module.
Fitting
Proceed as follows:
1. The fastening is already fitted to the CPV valve terminal.
Make sure that the flat seal is placed correctly over the terminal lugs and the centring bolt which lies between
2−14
Festo P.BE−CPV−EN en 0503g
2. Fitting
1
2. Mark the positions of the four holes for the fastening screws on the background (see diagram).
Tip: Hold the pneumatic interface module against the mounting surface and mark the positions of the holes.
Drill the four fastening holes for screws of size M5.
2
3
4
1
Fastening CPV..−VI−BG−ET200X
2
Terminal lug with centring bolt
3
4
109.5 mm
132 mm
Fig.2/4: Preparing for fitting onto the SIMATIC ET200X
3. Place the valve terminal carefully and without tilting onto the pneumatic interface module.
Insert the centring pins in the appropriate holes.
Do not bend the terminal lugs.
Screw tight the valve terminal and the pneumatic inter face module on the mounting surface with four screws
(see diagram).
Festo P.BE−CPV−EN en 0503g
2−15
2. Fitting
1
M5 screws, at least 60 mm long
(ISO1207/
ISO1580
DIN 84 or
DIN 912)
2
Centring pins
1
2
Fig.2/5: Fitting the CPV valve terminal onto the Siemens SIMATIC ET200X
Please note
Removing the CPV valve terminal from the pneumatic interface module.
· Pull the CPV valve terminal carefully upwards without tilting.
When refitting the CPV valve terminal onto the pneumatic interface module:
· Replace the flat seals on the following CPV valve terminals if they have been operated in a dirty environ ment:
type CPV10−GE−8
type CPV14−GE−8
2
2−16
Festo P.BE−CPV−EN en 0503g
2. Fitting
2.2
CPV valve terminal with pneumatic multipin
Only CPV valve terminals fitted with appropriate end plates may be mounted on the pneumatic multipin. CPV valve ter minals with end plates for individual tubing need to be con verted before they can be fitted onto the pneumatic multipin.
For this purpose fit the appropriate end plates (see chapter 5
Converting the end plates" and Appendix B Summary of the end plates").
The pneumatic multipin is available in two forms:
Without asssembly step: This pneumatic multipin fits flush with the end plates. The fastening holes for fitting onto a wall or floor are in the connection side of the pneu matic multipin.
With assembly step: This pneumatic multipin projects over the end plates. The fastening holes are in the step, thereby facilitating fitting. Two additional holes running diagonally through this pneumatic multipin also enable the CPV valve terminal to be fitted from the rear (see chapter Summary of system" Fig. 1/2).
CPV valve terminals with large surface−mounted silencers, which are fitted onto the pneumatic multipin with assembly step, can only be fitted onto a wall. Use here the holes run ning diagonally through the pneumatic multipin. The mount ing holes running vertically through the pneumatic multipin are covered by the large surface−mounted silencer.
Festo P.BE−CPV−EN en 0503g
2−17
2. Fitting
2.2.1
Fitting the pneumatic multipin
Make sure that the fastening surface can support the pneu matic multipin and the CPV valve terminal. Make sure that there is sufficient space for connecting the supply cables and tubing, and that extra space is available for fitting CPV valve terminals with large surface−mounted silencers.
Fitting the pneumatic multipin (connection side)
Proceed as follows in order to fit the pneumatic multipin with the connection side onto a mounting surface:
· Cut out an opening in the fastening surface (dimensions see table 2/11 or table 2/12).
· Drill four mounting holes in the fastening surface (diam eter see table). Position of and distance between these holes (see table 2/11 or table 2/12).
· Screw the pneumatic multipin to the fastening surface with four screws of sufficient length (see table).
Pneumatic multipin
(without step)
CPV10/14
4.5 mm
M4
CPV18
5.5 mm
M5
Pneumatic multipin
(with step)
CPV10/14/18
6.5 mm
M6
Tab.2/10: Diameter of the fastening holes and screw size
2−18
Festo P.BE−CPV−EN en 0503g
2. Fitting
CPV10/14
7
8
1
CPV18
4
3 2
7
8
1
5 6 5 5 6
1
2
3
4
5
6
7
8
CPV10 valve terminal CPV14 valve terminal
29.5 mm +
60 mm
55 mm
R4
11.25 mm
6
10 mm x number of plates
31.5 mm
Diameter 4.3 mm
39.5 mm +
76.6 mm
68.6 mm
R4
12.75 mm plates
38.3 mm
6
14 mm x number of
Diameter 4.3 mm
1
2
3
4
5
6
CPV18 valve terminal
59.0 mm + 6
98 mm
25.5 mm
18 mm x number of plates
7
8
54 mm
Diameter 5.5 mm
Tab.2/11: Dimensions of wall cut−out for pneumatic multipin (without step)
5
2
Festo P.BE−CPV−EN en 0503g
2−19
2. Fitting
CPV10/14 CPV18
1
1 aB aA aJ
3
2 aB
7
6
3
8 9 8
4
5
8 9
1
2
3
4
5
6
7
8
9 aJ aA aB
CPV10 valve terminal CPV14 valve terminal
30 mm + 9
73 mm
R12
6.3 mm
21 mm
10 mm x number of plates
21.5 mm
18.5 mm
Diameter 6.5 mm
40 mm + 9
89 mm
R14
9.0 mm
4.7 mm
5.55 mm
R8
26 mm
14 mm x number of plates
29.5 mm
29.5 mm
Diameter 6.5 mm
CPV18 valve terminal
1
2
3
4
5
6
7
8
9
60 mm +
118 mm
R22
15 mm
9
35.5 mm
18 mm x number of plates aJ aA aB
44 mm
44 mm
Diameter 6.5 mm
Tab.2/12: Dimensions of wall cut−out for pneumatic multipin (with step)
8
4 aA
2 aJ
2−20
Festo P.BE−CPV−EN en 0503g
2. Fitting
Festo P.BE−CPV−EN en 0503g
Fitting the pneumatic multipin (rear side)
Proceed as follows in order to fit the pneumatic multipin (with step) with its rear side onto a mounting surface:
· Drill two mounting holes in the fastening surface for screws of size M6. Position of and distance between these holes see table.
1
6
8
2
4
Number of valve locations
CPV10
Dimensions 1
CPV14
62 mm
82 mm
102mm
122 mm
80 mm
108 mm
136 mm
164 mm
CPV18
107 mm
143 mm
179 mm
215 mm
Tab.2/13: Hole dimensions for rear fitting
· Screw the pneumatic multipin to the fastening surface with two M6 screws of sufficient length.
2−21
2. Fitting
2.2.2
Fitting the CPV valve terminal to the pneumatic multipin
Proceed as follows:
· With CPV valve terminals with IC connection, insert the socket head screws supplied into the fastening holes.
With MP, AS−Interface, DI or CP connections, the socket head screws are already in the fastening holes under the electrical sub−base and are secured against loss.
· Place the 3−part or 4−part seal for sealing the supply chan nels into the grooves in the left or right−hand end plate.
· In order to seal the work channels, carefully press the two seals into the thread of the work connections.
· Fasten the CPV valve terminal with the 4 socket head screws on the multipin. Tighten the screws in diagonally opposite sequence with 2 Nm (CPV10/14) or 4 Nm
(CPV18).
1
3−part seal in the connections of the left−hand end plate
2
2 seals per valve sub−base for the work connections
3
4−part seal in the connections of the right−hand end plate
4
Socket head fastening screws of the pneumatic multipin
1
4
2
3
Fig.2/6: Fitting the CPV valve terminal onto the pneumatic multipin
2−22
Festo P.BE−CPV−EN en 0503g
2. Fitting
2.3
Fitting the valve extensions
Please note
If the pneumatic multipin is used with assembly step, the outer valve sub−bases cannot be fitted with valve extensions.
The valve extension 5/3G is intended for use with one working pressure for each valve sub−base, i.e. it must not be used in two−pressure operation (different pres sure at connections 1 and 11).
If other valve sub−bases are to be fitted onto the CPV valve terminal in two−pressure mode, the valve plate fitted with the 5/3G valve extension must be separated from compressed air channels 1 and 11 by means of a dividing plate.
Proceed as follows:
· Place the seals supplied with the product into the re cesses in the appropriate valve extension.
· Fasten the valve extension with the screws supplied with
0.8 Nm (CPV10) or 1.2 Nm (CPV14).
· Connect the work lines as described under Connecting the supply and work lines" in chapter 3.
· Note that the flow control valve extensions or one−way flow control valve extensions (Ident. code P, Q and V) require a minimum operating pressure of 0.5 bar.
Festo P.BE−CPV−EN en 0503g
2−23
2. Fitting
2.4
Fitting the identifier support
Before the valve identifier signs can be fitted, the CPV valve terminal must be fitted with an identifier support. This will also protect the manual overrides against unauthorised operation. It should be fitted at the front above the manual override.
The identifier support cannot be fitted if the CPV valve ter minal is equipped with relay plates.
Proceed as follows:
· Clip the identifier support into the recess in the left and right−hand end plates (see diagram).
· Clip the identifier signs into the grooves in the identifier support (see diagram).
1
2
2−24
1
Valve identifier labels
2
Identifier support
Fig.2/7: Fitting the identifier support
Festo P.BE−CPV−EN en 0503g
2. Fitting
2.5
Fitting the manual override cover
Covers can be fitted onto the manual override to protect it against unauthorized use. The covers must be fitted over each manual override.
The manual override covers are not intended for re−use. Fit the manual override covers only when you do not require the manual override any more (e.g. after testing the valves).
Proceed as follows:
· Clip the covers into the grooves in the manual override
(see diagram).
If your CPV valve terminal is equipped with non−locking man ual override, you must remove the safety clips before fitting the manual override covers (see chapter 5, section Conver sion from non−locking to locking manual override").
1 1
Festo P.BE−CPV−EN en 0503g
1
Guide grooves of the manual override
2
Manual override cover
Fig.2/8: Fitting the manual override covers
2
2−25
2. Fitting
2−26
Festo P.BE−CPV−EN en 0503g
Installation
Chapter 3
Festo P.BE−CPV−EN en 0503g
3−1
3. Installation
Contents
3.
3.1
3.2
3.3
Installation . . . . . . . . . . . . . . . . . . . . . . . . . . . . . . . . . . . . . . . . . . . . . . . . . . . 3−1
Preparing the compressed air . . . . . . . . . . . . . . . . . . . . . . . . . . . . . . . . . . . . .
3.1.1
Operation with non−lubricated compressed air . . . . . . . . . . . . . . . .
3.1.2
Operation with lubricated compressed air . . . . . . . . . . . . . . . . . . . .
General connecting methods . . . . . . . . . . . . . . . . . . . . . . . . . . . . . . . . . . . . . .
Connecting the CPV valve terminal . . . . . . . . . . . . . . . . . . . . . . . . . . . . . . . . .
3.3.1
Auxiliary pilot air . . . . . . . . . . . . . . . . . . . . . . . . . . . . . . . . . . . . . . . .
3.3.2
Connecting the supply and work lines . . . . . . . . . . . . . . . . . . . . . . .
3.3.3
Connecting the electric cables . . . . . . . . . . . . . . . . . . . . . . . . . . . . .
3−8
3−8
3−11
3−16
3−3
3−3
3−4
3−6
3−2
Festo P.BE−CPV−EN en 0503g
3. Installation
3.1
Preparing the compressed air
Caution
Dirty or incorrectly lubricated compressed air will reduce the service life of the valve terminal.
3.1.1
Operation with non−lubricated compressed air
Caution
Too much residual oil content in the compressed air will reduce the service life of the valve terminal.
If bio−oils are used (oils with synthetic ester or true ester basis, e.g. rape oil methylester) the resuidual oil content must not ecxceed 0.1 mg/m 3 (see ISO 8573−1 class 2).
If mineral oils are used (e.g. HLP oils as per DIN 51524 parts 1 to 3) or corresponding oils on a polyalphaolefine basis (PAO), the residual oil content must not exceed
5mg/m 3 (see ISO 8573−1 class 4).
You will thereby avoid functional damage of the valves.
Excessive residual oil cannot be permitted irrespective of the compressor oil, as otherwise the basic lubrication will be washed out during the course of time.
Festo P.BE−CPV−EN en 0503g
3−3
3. Installation
3.1.2
Operation with lubricated compressed air
Please note
Please use non−lubricated air in your system if possible in order to protect the environment. Festo pneumatic valves and cylinders have been designed so that, if used as in tended, they will not require additional lubrication and will still achieve a long service life.
Please note the following instructions if lubricated com pressed air must be used.
The compressed air prepared with the compressor must correspond in quality to non−lubricated compressed air.
If possible, do not operate the complete system with lubricated compressed air.
If possible, always install the lubricators directly in front of the relevant cylinder.
Caution
Incorrect additional oil and too much residual oil content in the compressed air will reduce the service life of the valve terminal.
Use Festo special oil OFSW−32 or the other oils listed in the Festo catalogue (as per DIN51524−HLP32, basic viscosity 32cST at 40 °C).
The additional lubrication must not exceed 25 mg/m 3
(ISO 8573−1 class 5).
Make sure that the lubricator setting is correct (see following section).
You will thereby avoid functional damage of the valves.
Setting the lubricator
With the machine running (typical operating status) 0.2 to max. 1 drop/min. or 0.5 to 5 drops/1000 l air.
3−4
Festo P.BE−CPV−EN en 0503g
3. Installation
Checking the lubricator setting
Proceed as follows:
· Check the service unit in respect of condensate and lubri cator setting twice a week.
1. Ascertain the cylinder which is furthest from the lubricator.
2. Ascertain the valve terminal which controls this cylinder.
3. Remove the silencer, if fitted, from connection 3/5.
4. Hold a piece of white cardboard 10 cm in front of the exhaust port.
5. Let the system run for a short period.
There must only be a slight yellow colouring on the cardboard. If oil drops out, this is an indication that too much oil has been used.
A further indication of excessive lubrication is the colouring or status of the exhaust silencer. A distinctly yellow colouring of the filter element or drops of oil on the silencer indicate that the lubricator setting is too high.
Festo P.BE−CPV−EN en 0503g
3−5
3. Installation
3.2
General connecting methods
Warning
Switch off the following power supplies before undertaking installation and/or maintenance work:
· the compressed air supply
· the power supply for the valve solenoid coils
You can thereby avoid: sudden uncontrolled movements of loose tubing, unexpected movements of the connected actuators, non−defined switching states of the electronic compo nents.
Pay particular attention to the following:
The components of the valve terminal contain electrostatically sensitive elements. The components will be damaged if you touch the contact surfaces of the plug connectors and if you do not observe the regulations for handling electrostatically sensitive components.
Laying the tubing
Please note
· If necessary, place a suitable seal under each screw connector or silencer in order to avoid leakage.
If elbow screw connectors or multiple distributors are used, the airflow will be reduced slightly.
3−6
Festo P.BE−CPV−EN en 0503g
3. Installation
Festo P.BE−CPV−EN en 0503g
Basic information
Connecting
1. Push the tubing as far as possible over or into the tube connection of the screw connector.
2. If necessary, pull locking ring (A) over the tube connection or tighten locking screw (B).
3. For reasons of clarity, group the tubing together with
tube straps or
multiple hose holders.
Removing
1. Loosen the locking screw or locking ring of the screw con nector.
2. Pull out the tubing.
3. If necessary, replace the screw connector with a blanking plug (C).
(B)
Connecting
(A)
Removing
(C)
Fig.3/1: Fitting the tubing
3−7
3. Installation
3.3
Connecting the CPV valve terminal
In order to guarantee the optimum efficiency of your CPV valve terminal, we recommend in the following cases that you connect the compressed air tubing and, if necessary, also the exhaust air tubing on both sides (appropriate end plate pairs see Appendix B Overview of the end plates"): when large volume cylinders are operated at high speeds.
when several valves are switched simultaneously to the flow position.
Please note
· CPV valve terminal with two pressure zones. Connect the supply pressures to the end plates or to both sides of the pneumatic multipin.
3.3.1
Auxiliary pilot air
Caution
If possible, operate the CPV valve terminal with non−lu bricated auxiliary pilot air (connections 12/14). Other wise observe the instructions in the section Operation with lubricated compressed air."
With CPV valve terminals with internally branched auxili ary pilot air, the above mentioned remark also applies to the supply air (connection 1/11).
With CPV valve terminals with two pressure zones and internally branched auxiliary pilot air:
Due to the internally branched auxiliary pilot air in the right−hand end plate, the pressure in the right−hand pressure zone must be 3...8 bar.
3−8
Festo P.BE−CPV−EN en 0503g
3. Installation
The CPV valve terminal is intended for internal or external pilot air, depending on the end plates fitted. Please refer to your order forms or to the table in Appendix B to ascertain which types of end plates are fitted on your CPV valve ter minal.
Internal pilot air
If the supply pressure of your CPV valve terminal lies between
3...8 bar, you can operate the terminal with internally branched auxiliary pilot air. In this case the auxiliary pilot air will be taken from connection 1 or 11 in the left or right−hand end plate.
Please note
Using the CPV valve terminal with internal auxiliary pilot air
· Seal connection 12/14 with a blind plug.
Festo P.BE−CPV−EN en 0503g
External pilot air
If the supply pressure of your CPV valve terminal lies between
3...8 bar, you can operate the terminal with external auxiliary pilot air. In this case the auxiliary pilot air is supplied via con nection 12/14 on the CPV valve terminal. End plates for sup plying the CPV valve terminal with external auxiliary pilot air see Appendix B Overview of end plates."
Please note
· Used closed−loop controlled auxiliary pilot air (3...8 bar).
Reliable faultless operation of the CPV valve terminal is then possible.
· Please note that the closed−loop controlled auxiliary pilot air for all valve sub−bases on the CPV valve terminal need only be supplied or branched at one position with common tubing. This also applies if the CPV valve ter minal is operated with different pressure zones (see diagram).
3−9
3. Installation
1
Separator plates
2
Blanking plug
3
Pressure zone 2
4
Pressure zone 1
Fig.3/2: Auxiliary pilot air
ÓÓÓÓÓÓÓÓ
ÓÓÓÓÓÓÓ ÓÓÓÓÓÓÓÓ
ÎÎÎ ÓÓÓÓ
ÎÎÎ ÓÓÓ ÓÓÓÓ ÓÓÓÓ
4 3
1
2
3−10
Festo P.BE−CPV−EN en 0503g
3. Installation
3.3.2
Connecting the supply and work lines
Please note
· Unused connections. Seal all connections not required for functioning with blind plugs (see Appendix B).
· Unused connections. Seal work connections 2 and 4 with blind plugs.
· Valve sub−base with Ident. code C (two 3/2−way valves closed in basic position):
With the 5/3G valve extension you can implement the function in mid−position blocked" with this CPV10/14 valve sub−base. This valve extension is mounted on the connection side of the above−mentioned valve sub−base
(see 2.3 Fitting the valve extensions").
· Connect the work lines as follows, depending on the tool you are using:
screw connector with hexagon socket head: Any sequence is possible.
screw connector with external hexagon socket head:
Connection must be made from left to right (space for wrench).
Festo P.BE−CPV−EN en 0503g
3−11
3. Installation
Pneumatic multipin
4
Fit the screw connector or the silencers according to the table below. Then connect the pneumatic tubing.
1
CPV valve terminal
4
1
3/5
11
12/14
82/84
1
82/84
3/5
2 11 2 11 12/14
Connection identifier
ISO 5599
1 or 11
2 or 4
3/5
12/14 or
82/84
Tubing
Compressed air/ vacuum
Connection size ISO 228, specifications in brackets are for pneumatic multipin with ste p
CPV10 CPV14 CPV18
G1/8 G1/4 G3/8
Connection
Work air/vacuum M7 G1/8
Exhaust right−hand/ left−hand end plate
Pneumatic multipin
Auxiliary pilot air or exhaust right−hand/ left−hand end plate
Pneumatic multipin
G3/8
G1/4
M5
M7 (M5)
G1/2
G3/8
G1/8
G1/8
G1/4
G1/2
G1/2
G1/4
G1/4
Screw connector in end plates or pneumatic multipin
Screw connector
Screw connector
for ducted exhaust air
for silencers
Screw connector at connection 82/84
for ducted exhaust air
for silencers
Tab.3/1: Sizes of the pneumatic connections
3−12
Festo P.BE−CPV−EN en 0503g
3. Installation
Please note
If you have several systems with central ducted exhaust air: use non−return valves in the common exhaust lines in order to prevent functional impairment due to back pressures.
1 2 3 2 4
1
CPV valve terminal 1
2
Common 3/5
3
Common 82/84
4
CPV valve terminal 2
5
Central 3/5
6
Central 82/84
2
Fig.3/3: Common lines with non−return valves
6 5 3
Please note
The exhaust is passed through channels 3/5 and 82/84.
These connections must not be sealed with blanking plugs.
Exhaust channels 3 and 5 are grouped together in the CPV valve terminal. Separate exhaust restriction of channels
3 or 5 is not therefore possible.
Restriction of exhaust 3/5 on the vacuum generator plates
(Ident. codes A and E) is not permitted.
Festo P.BE−CPV−EN en 0503g
3−13
3. Installation
3−14
Please note
With CPV valve terminals with ducted supply air:
Seal connections 11 and 12/14 with blind plugs
Pressure zones of the CPV valve terminals
The CPV valve terminal can be operated with up to four pres sure zones, depending on the components fitted. The maxi mum possible number of pressure zones is determined by the combination of the following components:
Separator plate
(see 1.2 Description of components")
End plate pairs (see Appendix B.2)
Valve plates (see Appendix B.1)
Please note
With CPV valve terminals with two pressure zones and internally branched auxiliary pilot air in the right−hand end plate:
Due to the internally branched auxiliary pilot air, the pressure in the right−hand pressure zone must be 3...8 bar.
Vacuum/low pressure operation
The CPV valve terminal can be operated with vacuum or low pressure ( t 3 bar), if closed−loop controlled auxiliary pilot air is applied separately. An overview of the end plates required can be found in Appendix B.2.
Festo P.BE−CPV−EN en 0503g
3. Installation
Vacuum generator plates
Please note
A high back pressure in exhaust channel 3/5 will impair the functioning of the vacuum generator.
· Make sure that there is optimal exhausting.
If the CPV valve terminal is fitted with valve sub−bases and vacuum generator plates, the exhaust air from the valve sub−bases (in channel 3/5) can influence the vacuum gen eration.
· In this case, separate exhaust channel 3/5 between the vacuum generator plates and the valve sub−bases by means of the separator plate with Ident. code S.
Connect the work lines to the vacuum generator plate:
Vacuum valve sub−base with Ident. code A:
· Connect the vacuum suction nozzle to work connection 4.
· Seal work connection 2 with a blind plug.
Vacuum valve sub−base with Ident. code E:
· Connect the vacuum suction nozzle to work connection 4.
· Connect work connections 2 and 4 together with tubing or with vacuum valve extension CPV..−BS−GRZ−V... .
Festo P.BE−CPV−EN en 0503g
3−15
3. Installation
3.3.3
Connecting the electric cables
Information on the connection procedure as well as on cables and current requirements can be found in the manual
CP System, installation and commissioning."
Warning
· Use only PELV circuits as per IEC/DIN EN 60204−1 (Pro tective Extra−Low Voltage, PELV) for the electrical supply.
Consider also the general requirements for PELV circuits in accordance with IEC/DIN EN 60204−1.
· Use power supplies which guarantee reliable electrical isolation of the operating voltage as per IEC/DIN EN
60204−1.
By the use of PELV circuits, protection against electric shock
(protection against direct and indirect contact) is guaranteed in accordance with IEC/EN 60204−1 (Electrical equipment for machines, General requirements).
Please note
Check within the framework of your EMERGENCY STOP circuit, to ascertain the measures necessary for putting your machine/system into a safe state in the event of an
EMERGENCY STOP (e.g. switching off the operating voltage for the valves and output modules, switching off the com pressed air).
3−16
Festo P.BE−CPV−EN en 0503g
3. Installation
1
Earth/ground connection
Earthing the CPV valve terminal
For earthing purposes, all variants of the CPV valve terminal have an earthing connection. This is on the left−hand end plate (see diagram).
1
Fig.3/4: Earthing connections on the CPV valve terminal
Please note
Earth your CPV valve terminal.
· Connect the earth connection on the left−hand end plate
(see Fig. 2/5) with low impedance (short cable with large cross−sectional area) to the earth potential.
· Tighten the earthing screw with max. 1 Nm.
In this way, you will avoid interference caused by electro magnetic influences.
Festo P.BE−CPV−EN en 0503g
3−17
3. Installation
Connecting current−consuming devices to the relay plate
Please note
· Use only ready−to−use connector sockets KRP−1−24−...
from Festo for connecting current−consuming devices to the relay outputs.
Connect the current−consuming devices to the relay outputs as follows:
· Carefully place the socket first on the terminal lug of the lower relay output (see diagram).
· Screw the socket together with the central locking screw with 0.15 Nm.
· Fit the second socket in the same way to the upper relay output.
3−18
Fig.3/5: Fitting the relay output sockets
Festo P.BE−CPV−EN en 0503g
3. Installation
CPV valve terminal with IC connection
With this CPV valve terminal variant each valve solenoid coil is connected separately.
Please note
· Use only the following ready−to−use sockets from Festo for connecting the valve solenoid coils:
For CPV10/14:
KMYZ−7−24−...−LED, an LED and the holding current reduction are incorporated in the transparent socket.
The LED indicates the switching status of the valve solenoid coil.
For CPV18:
KMYZ−2−24−...−LED, an LED is incorporated in the trans parent socket. The LED indicates the switching status of the valve solenoid coil.
Address assignment of the valves
· The addresses must be assigned in ascending order with out gaps.
· Counting begins from left to right, on the individual valve
plates from the front to the rear (see Fig.3/6).
Festo P.BE−CPV−EN en 0503g
Fig.3/6: Address assignment of a CPV valve terminal with
IC connection and 8 valve locations
3−19
3. Installation
Connect the valve solenoid coils as follows:
· Use connector socket KMYZ−7−... (CPV10/14) or
KMEB−2−... (CPV18). Connector socket KMYZ−7−... is fitted with current reduction.
· Insert the socket onto the terminal lugs of the appropriate pilot solenoid (see diagram). The socket can also be fitted turned 180°. Make sure that the centring bolt between the terminal lugs grips into the hole in the socket. Screw the socket together with the central locking screw with
0.15Nm.
3−20
Fig.3/7: Fitting the individual connecting sockets
Festo P.BE−CPV−EN en 0503g
3. Installation
CPV valve terminal with multipin or AS−Interface connection
Connecting the multipin or AS−Interface cable
Detailed instructions on wiring up the electrical connections of the CPV valve terminal with multipin or AS−Interface con nection can be found in the leaflet supplied with the product.
CPV valve terminal with CP connection
Connecting the CP cables
Detailed instructions on connecting the CPV valve terminal with CP connection can be found in the manual CP system
General installation and commissioning," chapter 3.
CPV valve terminal with direct connection
Connecting the field bus cable
Detailed instructions on connecting the CPV valve terminals with direct connection can be found in the manual CPV valve terminal with direct connection."
Festo P.BE−CPV−EN en 0503g
3−21
3. Installation
3−22
Festo P.BE−CPV−EN en 0503g
Commissioning
Chapter 4
Festo P.BE−CPV−EN en 0503g
4−1
4. Commissioning
Contents
4.
4.1
4.2
4.3
Commissioning . . . . . . . . . . . . . . . . . . . . . . . . . . . . . . . . . . . . . . . . . . . . . . . . 4−1
General instructions . . . . . . . . . . . . . . . . . . . . . . . . . . . . . . . . . . . . . . . . . . . . .
Testing the valves . . . . . . . . . . . . . . . . . . . . . . . . . . . . . . . . . . . . . . . . . . . . . . .
4.2.1
Checking the valve functions . . . . . . . . . . . . . . . . . . . . . . . . . . . . . .
4.2.2
Checking the valve−cylinder combination . . . . . . . . . . . . . . . . . . . .
Eliminating faults . . . . . . . . . . . . . . . . . . . . . . . . . . . . . . . . . . . . . . . . . . . . . . .
4−3
4−6
4−7
4−9
4−13
4−2
Festo P.BE−CPV−EN en 0503g
4. Commissioning
4.1
General instructions
Before commissioning
· Switch off the power supply before connecting or discon necting plugs (otherwise this could lead to functional damage).
· Earth the CPV valve terminal on the left−hand end plate.
· Commission only a valve terminal which has been fitted and wired completely.
· Make sure that there is a sufficient supply of fresh air
(cooling) for the following operating conditions:
when the maximum number of valves are fitted,
when the maximum operating voltage is applied,
when the solenoid coils are constantly under stress.
· If necessary, use the flow control valve extension or the one−way flow control valve extension.
Please note
When unscrewing the adjusting screw, make sure that you do not unscrew it beyond the resistance, as this would damage the cover.
Note that the flow control valve extensions or one−way flow control valve extensions (Ident. codes P, Q and V) require a minimum operating pressure of 0.5 bar.
Festo P.BE−CPV−EN en 0503g
4−3
4. Commissioning
Warning
If the build−up in pressure of the auxiliary pilot air is too slow or delayed, this may cause the actuators to perform sudden unexpected movements.
Switch on the compressed air with a safety start−up valve (slow build up of pressure) and
When there are electric signals (e.g. after EMERGENCY
STOP).
This can cause damage to the machine or system and even injury to human beings.
· Supply the auxiliary pilot air via the left−hand end plate
(3...8 bar).
The auxiliary pilot air must reach a pressure of 3...8bar as soon as it is switched on, otherwise the valve cannot be guar anteed to switch (see diagram).
If the pressure is less than 3 bar, there may be a delay before the valve is switched, in spite of an electric signal being pres ent. The slow increase in pressure of the complete supply does not then affect the cylinder. Depending on the valve function, the cylinder would extend or retract suddenly.
4−4
Festo P.BE−CPV−EN en 0503g
4. Commissioning
82/84
4 2
14
12/14
1
5 3
2
12
3
1
12/14
1
1
Externally supplied auxiliary pilot air (3 to 7 bar), branched from the safety start−up valve
2
Safety start−up valve (slow build up of pressure of complete supply)
Fig.4/1: Example of valve−cylinder combination with slow increase in pressure of the complete supply
2
Festo P.BE−CPV−EN en 0503g
4−5
4. Commissioning
The table below shows the effects of slow start−up pressuriza tion when there are electric signals.
External auxiliary pilot air
Pressure increase in complete supply
Branched after the safety start−up valve slow
Branched in front of the safety start−up valve slow
Pressure increase in the auxiliary pilot air (12/14) slow fast
Tab.4/1: Effects of slow start−up pressurization
Time of switching point of a valve
Movement of the cylinder after pressure increase with (1) fast before pressure increase with (1) slow
4.2
Testing the valves
Please note
Before commissioning the CPV valve terminal, note the specifications concerning the medium in chapter 3.
The CPV valve terminal should be commissioned as follows:
Commissioning variants
Preliminary test of the pneumatic tubing
Complete commissioning of the complete system
Activity
Testing the valve−cylinder− combination by means of the manual override
Installing and connecting the complete system. Program control via PLC/industrial PC
Tab.4/2: Commissioning variants
4−6
Festo P.BE−CPV−EN en 0503g
4. Commissioning
Commissioning the pneumatic components by means of the manual override is described below. Commissioning of the CP system is described in the appropriate manual for the CP node.
4.2.1
Checking the valve functions
Manual override
Warning
Before actuating the manual override:
· Disconnect the power supply to the valve solenoid coils of the relevant connections (IC, MP, ASI, DI or CP connec tions). You will thereby avoid undesired actuation of the valve solenoid coils.
· Before switching on the power supply: Make sure that all manual override locking actuations are in their basic positions. You will thereby avoid undefined switching states of the valves.
You should use the manual override especially when commis sioning the pneumatic system, in order to check the function ing and operation of the valve or the valve−cylinder−combina tion.
By actuating the manual override, you can switch the valve without an electric signal. You only need to switch on the compressed air supply.
Festo P.BE−CPV−EN en 0503g
4−7
4. Commissioning
Types of manual override
The manual override has been designed to be used as follows:
Types of manual override Method of operation
Manual override with automatic return (non−locking)
Locking manual override
Manual override covered
After actuation the manual override is reset by a spring.
The manual override remains actuated until it is reset by hand.
The manual override is covered for safety reasons. It cannot be actuated
Locking manual override
Tab.4/3: Designs of manual override
The diagram below shows the assignment of the manual over rides to the pilot solenoids.
Non−locking manual override
3
1
4
2
1
Slide of the locking manual override to pilot solenoid 14 (in basic position)
2
Slide of the locking manual override to pilot solenoid 12 (in basic position)
3
Push button of non−locking manual override to pilot solenoid 14
4
Push button of non−locking manual override to pilot solenoid 12
Fig.4/2: Assignment of manual overrides to the pilot solenoids
4−8
Festo P.BE−CPV−EN en 0503g
4. Commissioning
4.2.2
Checking the valve−cylinder combination
Carrying out the test Proceed as follows:
1. Switch on the compressed air supply.
2. Check the functioning and operation of each individual valve−cylinder combination by actuating the manual override as shown in the following diagrams.
Please note
Incorrect actuation of the non−locking manual override can lead to malfunctioning or damage to the manual override.
· Use a blunt pencil for actuating the non−locking manual override.
· Actuate the manual override only with max. 30 N.
3. In the case of the CPV valve terminal with pneumatic multipin: After testing the valves, make sure that all manual override actuations are in their basic positions.
4. Switch off the compressed air supply after checking the valves.
Festo P.BE−CPV−EN en 0503g
4−9
4. Commissioning
Actuating the manual override with automatic reset
(non−locking)
Reaction of the valve
Carefully press down the plunger of the manual override as far as possible.
The valve:
moves to the switching position
Hold the plunger of the manual override pressed down.
Release the plunger. The spring resets the plunger of the manual override to the starting position.
remains in the switch position
moves back to the basic posi tion ( not with 5/2−way double− solenoid valve, Ident. code J)
Tab.4/4: Non−locking actuation of the manual override
4−10
Festo P.BE−CPV−EN en 0503g
4. Commissioning
Caution
Before commissioning your machine/system:
· Make sure that double−solenoid valves (Ident. code J) are in their basic positions again. To do this actuate manual override 12 of the relevant valve or apply current to pilot solenoid 12.
· Bring the locking manual override actuations into the basic position again. The valve plates with Ident. codes
D, I, C, N, H and the vacuum generator plate with
Ident.code E are each fitted with two valves. With man ual override 14 you control the valve on control side 14; with manual override 12 you control the valve on control side 12 (see switching symbols of the valve sub−bases
Appendix B).
In this way you will avoid undefined switching states when commissioning the machine/system.
Festo P.BE−CPV−EN en 0503g
4−11
4. Commissioning
Actuating the manual override with stop (locking)
Press down the plunger of the manual override as far as possible.
Reaction of the valve
The valve:
moves to the switching position
Leave the plunger in the lower position.
remains in the switch position
Press the plunger of the manual override into the upper position as far as possible (basic position).
moves back to the basic posi tion ( not with 5/2−way double− solenoid valve, Ident. code J)
Tab.4/5: Locking actuation of the manual override
4−12
Festo P.BE−CPV−EN en 0503g
4. Commissioning
4.3
Eliminating faults
Impairment of function
After switching on the compressed air supply or when subse quently testing the individual valves, you can learn the follow ing about the operating status of the pneumatic system:
Operating status of the pneumatic system
Valve position Error treatment when the compressed air supply has been switched off
Air escapes from ...
the common line connections
the work line connections
between the modules
Basic position
Switch position
Basic position
· Checking the seal ring or the tube fittings
· Checking the seal ring or the tube fittings
· After switching on again, regulate external pilot air to 3...8 bar).
The valve or the pneumatic system
does not react as expected
does not react
does not react
Switch position
Switch position
Basic position
· Check the tubing
·
·
·
·
After switching on again check the operating pressure (e.g. pressure zones)
Bring the locking manual override into the basic position
Servicing required
Check the controller connection
(apply pressure u 3 bar at controller)
Tab.4/6: Function impairment of the pneumatic system
Festo P.BE−CPV−EN en 0503g
4−13
4. Commissioning
If the operating status of the pneumatic system differs from the desired pneumatic operating status, the following condi tions are probably not fulfilled:
Desired pneumatic operating status
Free of leakage
Prerequisites Remarks
Fast reaction
Faultless
Two pressure zones
Vacuum operation/ low−pressure operation
Maximum vacuum (created by vacuum generator)
Tubing connected with care
Regulated auxiliary pilot air
Sufficient pressure supply via pressure supply points
Non−return valves in common exhaust line
Limiting the pressure zones with a separator plate
Externally supplied auxiliary pilot air (3...8 bar)
Sufficient compressed air supply
Minimum supply pressure
No back pressure in exhaust channel 3/5
· Exhaust the valve terminal at the left and right−hand end plates (3/5, 82/84)
Applies in the case of several systems with centrally ducted exhaust
Subsequent conversion possible
Controller can only be operated with pressure
(between 3...8 bar)
·
·
·
The supply pressure must not break down even when several vacuum generators are switched on at the same time. If necessary, increase the supply pressure.
Silencers must not generate a high back pressure in ex haust channel 3/5. If necess ary, fit efficient silencers or increase the supply pressure.
In order to prevent the ex hausting of the valve affec ting the generation of vacuum, you must fit a separ ator plate with Ident. code S between the valve plate and the vacuum generator plate.
4−14
Festo P.BE−CPV−EN en 0503g
4. Commissioning
Desired pneumatic operating status
Prerequisites Remarks
EMERGENCY STOP of pressure zones
Guarantees the controller function for the auxiliary pilot air despite the complete supply being switched off
The controller regulates the auxiliary pilot air of all valves sub−bases on a valve terminal
Slow start−up after EMERGENCY
STOP
If there are control signals, the auxiliary pilot air must have a pressure of 3...8 bar immedia tely after being switched on.
Tab.4/7: Pneumatic operating states
LED display of the valves
There is a yellow LED for every valve solenoid coil (see dia gram). With a ready to operate CPV valve terminal, this LED indicates the switching status of the valve solenoid coils.
Please note
The LEDs show the signal states only when there are valve coils at the relevant valve locations. For this purpose the load voltage must lie within the permitted tolerance.
Note the assignment of the LEDs to the relevant manual override (see also following diagram).
Note the following with the IC connection:
LED in the front plug connector to upper manual override (14)
LED in the rear plug connector to lower manual override (12)
Note the following with the MP, ASI, DI and CP connec tions:
Lower LED in the connector cover to upper manual override (14)
Upper LED in the connector cover to lower manual override (12)
Festo P.BE−CPV−EN en 0503g
4−15
4. Commissioning
The diagram below shows the position of the LED in respect of the manual override actuations.
1
2
2
1
LED and manual override to pilot solenoid 14
2
LED and manual override to pilot solenoid 12
Fig.4/3: LED assignment
4−16
1
Festo P.BE−CPV−EN en 0503g
4. Commissioning
With valve sub−bases the LEDs indicate the switching status of the valve solenoid coils. The following table explains the meanings.
LED Switching position of the valve
Meaning yellow out yellow alight *)
Basic position
switch position or
basic position
Logical 0 (no signal)
Logical 1 (signal present)
Logical 1 but:
operating voltage of outputs below per mitted tolerance range (20.4...26.4 V DC) or
compressed air supply not OK or
pilot exhaust blocked or
servicing required
*) With double−solenoid valves (Ident. code J) the LED lights up only when the signal is present.
Tab.4/8: Meaning of the LED display
Festo P.BE−CPV−EN en 0503g
LED display of the relays
There is a yellow LED for every relay. This LED indicates the switching status of the relay coil when the CPV valve terminal is ready for operation.
Please note
Note the assignment of the LEDs to the relevant relay connection (see also following diagram).
Note the following with the MP, ASI, DI and CP connec tions:
Lower LED in the connector cover to upper relay connection
Upper LED in the connector cover to lower relay connection
4−17
4. Commissioning
The diagram below shows the assignment of the LEDs to the relay connections.
Fig.4/4: LED assignment of relay plate
4−18
Festo P.BE−CPV−EN en 0503g
Maintenance and conversion
Chapter 5
Festo P.BE−CPV−EN en 0503g
5−1
5. Maintenance and conversion
Contents
5.3
5.4
5.5
5.6
5.7
5.8
5.
5.1
5.2
Maintenance and conversion . . . . . . . . . . . . . . . . . . . . . . . . . . . . . . . . . . . . . 5−1
Cleaning/replacing the large surface−mounted silencer . . . . . . . . . . . . . . . .
Fitting/removing CPV valve terminal components . . . . . . . . . . . . . . . . . . . . .
5.2.1
Removing components from valve locations . . . . . . . . . . . . . . . . . .
5.2.2
Fitting components in valve locations . . . . . . . . . . . . . . . . . . . . . . .
Conversion from non−locking to locking manual override . . . . . . . . . . . . . . .
Converting the end plates . . . . . . . . . . . . . . . . . . . . . . . . . . . . . . . . . . . . . . . .
Conversion to internal or external auxiliary pilot air . . . . . . . . . . . . . . . . . . .
Conversion to individual tubing/central tubing . . . . . . . . . . . . . . . . . . . . . . .
Conversion of the CPV valve terminal to two pressure zones . . . . . . . . . . . .
Converting the CPV valve terminal to a variant with different electrical connections . . . . . . . . . . . . . . . . . . . . . . . . . . . . . . . . . . . . . . . . . . .
5−3
5−4
5−6
5−10
5−16
5−17
5−19
5−20
5−21
5−22
5−2
Festo P.BE−CPV−EN en 0503g
5. Maintenance and conversion
5.1
Cleaning/replacing the large surface−mounted silencer
Caution
Dirt in the large surface−mounted silencer can cause an increase in pressure in the exhaust channel.
· Clean the silencer if it is yellow/black or a dark colour or replace it by a new one.
In this way you can ensure that the large surface−mounted silencer functions correctly and that the valves operate correctly.
Proceed as follows:
1. Loosen and remove the screws in the fastening frame.
2. Remove the silencer from the end plate.
3. Replace the silencer or clean it in benzine or petroleum.
Do not use TRI for cleaning.
4. Place the cleaned or the new silencer and the fastening frame on the end plate.
5. Fasten the silencer only with the original screws (see table).
Fastening screws of the silencer as per DIN 912, strength class 12.9
Valve terminal
CPV10
CPV14
CPV18
Screw
M 2.5 x 8
M 3 x 10
M 5 x 28
Tightening torque
1.0 Nm ± 10 %
1.7 Nm ± 10 %
5.0 Nm ± 1 Nm
Tab.5/1: Tightening torques for large surface−mounted silencer
Festo P.BE−CPV−EN en 0503g
5−3
5. Maintenance and conversion
5.2
Fitting/removing CPV valve terminal components
Warning
Switch off the following power supplies before undertaking installation and/or maintenance work:
· the compressed air supply
· the power supply for the valve solenoid coils
You can thereby avoid: uncontrolled movements of loose tubing, unexpected movements of the connected actuators, non−defined switching states of the electronic compo nents.
5−4
Festo P.BE−CPV−EN en 0503g
5. Maintenance and conversion
Some components on the CPV valve terminal may only be operated in combination with other components, see the following compatibility list.
Components, Cover plate
Ident. code 1) AS−
Interface
CP IC 2) MP DI
Vacuum gener ator plates: A, E
Valve sub−bases:
C, D, H, I, J, M, N
Valve sub−base:
F (only CPV10)
No limits
Please note the recommendations in chapter 3
No limits
No limits No limits Only with connector socket with current reduction
KMYZ−7−...
Without HSA 3)
only every
2nd. valve sub−base
With HSA:
no limits
No limits
Valve sub−base: G CPV10/14: If the pneumatic multipin is used with assembly step, the outer valve sub−bases cannot be fitted with the necessary 5/3G valve extension.
CPV18: No limits
Blanking plate: L No limits
Relay plate: R
Separator plates:
S, T
Not permitted with CPV14
No limits Without HSA 3)
not permitted
With HSA:
no limits
Combination depends on end plate combination 4)
No limits
1) List of Ident. codes see chapter 1 Identification code."
2) CPV valve terminals for Siemens ET 200 X: Valve sub−base Ident. code F and relay plate not permitted.
3) MP connection with HSA (holding current reduction), CPV10: s from 10/2000, CPV14 as from
11/2000.
4) Combination list of end plates see section End plate combinations."
Tab.5/2: Compatibility list of valve location components
Festo P.BE−CPV−EN en 0503g
5−5
5. Maintenance and conversion
5.2.1
Removing components from valve locations
The components on the CPV valve terminal can easily be removed for maintenance and conversion work.
Proceed as follows:
Loosen the electrical connections
Note the following with the MP, AS−Interface and
CP connections
· Loosen the multipin lug or the AS−Interface, DI or CP con nector plug and pull it off carefully.
· Then loosen the four fastening screws in the electrical sub−base. Pull the sub−base carefully away from the terminal lugs of the valve sub−bases.
· If necessary remove the connector sockets on the relay outputs. Loosen first the locking screws of the upper con nector socket. Pull the socket carefully away from the terminal lugs. Then loosen the lower connector socket in the same way.
Note the following with the IC connection
· In order to remove the valve sub−bases, loosen the lock ing screws on the connector sockets of the valve sub− bases to be replaced.
· Pull the sockets carefully away from the terminal lugs.
Mark the connector sockets.
· With the CPV valve terminals with pneumatic multipin, we recommend that you remove the connector sockets from each valve sub−base.
5−6
Festo P.BE−CPV−EN en 0503g
5. Maintenance and conversion
Loosen the electrical connections
With the CPV valve terminal with individual tubing
(CPV valve terminal without pneumatic multipin)
· Loosen the tubing at work connections 2 and 4 of the valve sub−base or valve extension to be replaced (see section 3.2 General connection methods").
Remove the CPV valve terminal from the fastening surface
CPV valve terminal with pneumatic multipin
· Loosen the fastening screws of the pneumatic multipin in the left and right−hand end plates one turn in diagonally opposite sequence. Then remove the screws completely.
Remove the die CPV valve terminal from the pneumatic multipin.
Fitting the CPV valve terminal on a floor stand
· In this case loosen the fastening screws in the right−hand end plate and pull them out.
Fitting the CPV valve terminal onto a wall or onto a hat rail
· In this case loosen the right−hand wall fastening or hat rail clamping unit.
Festo P.BE−CPV−EN en 0503g
5−7
5. Maintenance and conversion
1
Components to be replaced
2
Tie rod
3
Distance approx.
2 mm
Remove the components
· Loosen the two lower tie rods one turn.
· Then loosen the upper tie rod and pull it out over the component to be replaced.
· Unscrew the two lower tie rods so that the screw heads are flush with the outer surface of the end plate (do not remove the tie rod).
· Pull the valve terminal apart so that the distance between the components to be replaced and the neighbouring components is approx. 2 mm in each case.
1
2
2
3 3
Fig.5/1: Removing the valves
5−8
Festo P.BE−CPV−EN en 0503g
5. Maintenance and conversion
1
Front tie rod
2
Rear tie rod
· Swing the component forwards around the front tie rod.
1 2
Fig.5/2: Position of the tie rods
· Pull the component so that it snaps out of the front tie rod.
Festo P.BE−CPV−EN en 0503g
5−9
5. Maintenance and conversion
5.2.2
Fitting components in valve locations
Please note
Please note the instructions in the brief description of the relevant CPV valve terminal with AS−Interface con nection or the instructions for fitting equipment on the valve sub−bases.
Please note the instructions on fitting the valve terminal with valve sub−bases and vacuum generator plates under Vacuum generator plates" in chapter 3.
If the CPV10 valve terminal is fitted with valve sub−bases with Ident.code F, please note the instructions on fitting and application in Appendix B1.
Please note the limits for fitting the CPV valve terminals with relay plates (Ident. code R). See compatibility list in this chapter.
Proceed as follows:
· Make sure that the seals are correctly seated between the components on the valve terminal. They must lie correctly in the appropriate seal grooves.
Only CPV10/14 valve terminals
· Check the position of the seals when fitting valve sub− bases with pneumatic spring valves or double−solenoid valves. It is not symmetrical (see diagram).
5−10
Festo P.BE−CPV−EN en 0503g
5. Maintenance and conversion
1 2 3
1
Pneumatic spring valve (Ident. code M or F):
The designation L" on the seal must face forwards.
2
Double−solenoid valve (Ident. code J):
The designation J" on the seal must face forwards.
3
The seal for valve plates with 2/2 or 3/2−way valves (Ident. codes D, I or C, H, and N as well as for all end plates is symmetrical and marked with 3/2 .
Fig.5/3: Position and designation of the seals with pneumatic spring valves or double− solenoid valves (only CPV10/14 valve terminals)
Festo P.BE−CPV−EN en 0503g
5−11
5. Maintenance and conversion
Please note
There is only one type of seal for all valve plates on the
CPV18 valve terminal. The position of the seal is the same on all valve plates.
· Place the component on the front tie rod. Press the com ponent so that it snaps onto the tie rod.
· Swing the component carefully backwards. Make sure that there is sufficient space for the flat seals.
· Push the upper tie rod as far as possible into the CPV valve terminal and screw it in a few turns.
· Align the CPV valve terminal components on a flat surface so that they are not offset.
· Tighten first the upper, then the lower tie rod with 0.3 Nm.
Then tighten all the tie rods with 2 Nm.
5−12
Festo P.BE−CPV−EN en 0503g
5. Maintenance and conversion
1
Flat seals
Note the following with the MP, ASI, DI and CP connections
Please note
The flat seals between the valve block and the sub−base have been modified. If the glued flat seals are more than one year old, replace them by new flat seals.
You can then be sure that your CPV valve terminal is sealed correctly.
The flat seals are situated on the bottom of the electrical sub− base (see diagram).
· Remove the self−adhesive flat seal from the recess. To do this, carefully loosen a corner of the seal with a screw driver (see Fig. 5/4). Then pull the seal carefully away from the electrical sub−base.
1
Fig.5/4: Position of the flat seal on the electrical sub−base
Festo P.BE−CPV−EN en 0503g
5−13
5. Maintenance and conversion
1
New flat seal
· The new one−piece flat seal is no longer glued onto the bottom of the electric sub−base, but simply on the ter minal lugs of the valve solenoid coils (see diagram).
1
Fig.5/5: Flat seal
· Place the connector cover onto the terminal lugs of the valve block. Carefully press down the connector cover.
· Tighten the screws on the electric sub−base in diagonally opposite sequence with 0.75 ± 0.15 (CPV10/14) or 3Nm
(CPV18).
With CPV valve terminals with relay plates
· Fit the connector plugs onto the relay outputs as de scribed under Connecting current−consuming devices to the relay plate" in chapter 3.
5−14
Festo P.BE−CPV−EN en 0503g
5. Maintenance and conversion
Fitting the CPV valve terminal
CPV valve terminal with pneumatic multipin
· In this case, place the 3−piece and 4−piece seals in the recesses in the left or fight−hand end plate. Press the
2−piece seals carefully into the threads in the work con nections.
· Place the CPV valve terminal on the pneumatic multipin and tighten the fastening screws in the left and right−hand end plates in diagonally opposite sequence with 0.3Nm.
Tighten the screws in diagonally opposite sequence with
2Nm (CPV10/14) or 4Nm (CPV18).
With floor mounting
· In this case, insert the fastening screws into the right− hand end plate and tighten the valve terminal.
Fitting onto a wall or hat rail
· Fasten the right−hand wall fitting to the wall with two M4 screws or tighten the right−hand hat rail clamping unit.
Fitting the pneumatic and electrical connections
· Fit the connections (see chapter 3).
Festo P.BE−CPV−EN en 0503g
5−15
5. Maintenance and conversion
5.3
Conversion from non−locking to locking manual override
By removing a safety clip, you can convert your CPV valve terminal from non−locking to locking manual override. Pro ceed as follows:
If you do not wish to re−use the safety clip:
· Use a screwdriver to press in the centre of the safety clip, as shown under 1 . The safety clip will then bend and snap out of the support.
If you wish to re−use the safety clip:
· Use a thin object (e.g. a spatula) to lift the safety clip out of the support, as shown in 2 .
2
1
1
Removing the safety clip by pressing it out
Fig.5/6: Safety clip for the manual override
2
Removing the safety clip by lifting it out (clip can be re−used)
5−16
Festo P.BE−CPV−EN en 0503g
5. Maintenance and conversion
5.4
Converting the end plates
By exchanging the end plates you can adapt the CPV valve terminal to new requirements of your machine or system. The following end plates are available:
End plates with supply connections for internal or external auxiliary pilot air.
End plates without supply connections.
End plates suitable for the pneumatic multipin for internal or external auxiliary pilot air.
End plates with large surface−mounted silencer.
A list of all available end plates can be found in Appendix B.2.
Proceed as follows:
· Loosen the electrical and pneumatic connections (see section Removing components from valve locations").
· Remove the CPV valve terminal from the fastening sur face. Proceed here in the reverse sequence to that de scribed under the section Fitting onto a wall," Hat rail clamping unit" or Fitting on the floor" in the chapter
Fitting."
· Remove the appropriate sub−base on CPV valve terminals with CP, AS−Interface, DI or MP connection (see the sec tion Removing components from valve locations").
· Place the CPV valve terminal on the left−hand end plate.
Loosen the outer tie rod maximum 1 turn (see Fig. 5/1).
You will then avoid overloading the centre tie rod.
· Then loosen the centre tie rod and remove it.
· Unscrew the outer tie rod.
· Remove the end plate from the CPV valve terminal. Make sure that the other components remain together.
Festo P.BE−CPV−EN en 0503g
5−17
5. Maintenance and conversion
· Place the right−hand end plate to be fitted on the CPV valve terminal and insert the tie rods.
· Place the CPV valve terminal on the right−hand end plate.
Make sure that the tie rods, which are not yet screwed tight, do not fall out of the CPV valve terminal.
· Remove the left−hand end plate from the CPV valve ter minal.
· Place the left−hand end plate to be fitted on the CPV valve terminal. Swing the CPV valve terminal onto the left−hand end plate.
· Screw in the tie rods and tighten them to the same amount with 0.3 Nm.
· Tighten first the centre and then the outer tie rods with
2+0.2Nm (CPV10/14) or 4 Nm (CPV18).
· Fit the appropriate sub−base on CPV valve terminals with
CP, AS−Interface, DI or MP connection (see the section
Fitting components in valve locations").
· Fit the CPV valve terminals onto the fastening surface
(see sections Fitting onto a wall," Hat rail clamping unit" or Fitting on the floor" in the chapter Fitting").
· Then fit the pneumatic and electrical connections
(see chapter Installation").
5−18
Festo P.BE−CPV−EN en 0503g
5. Maintenance and conversion
5.5
Conversion to internal or external auxiliary pilot air
By fitting the appropriate left and right−hand end plates, you can convert your CPV valve terminal to internal or external auxiliary pilot air.
Please note
Mixed operation of the CPV valve terminal with internal and external auxiliary pilot air is not intended. The auxili ary pilot air channel will not be divided into two pressure zones by means of separator plates.
With end plates CPV..−EPR−PG (part number 161373 and
162543), connection 12/14 is sealed internally.
Take into account the extra space required for end plates with large surface−mounted silencers.
Change the end plates of the CPV valve terminal as described in the section Converting the end plates."
Festo P.BE−CPV−EN en 0503g
5−19
5. Maintenance and conversion
5.6
Conversion to individual tubing/central tubing
In order to convert your CPV valve terminal from individual tubing to tubing on the pneumatic multipin, you will require: the pneumatic multipin special end plates for the CPV valve terminal.
Proceed as follows:
· Change the end plates of the CPV valve terminal as described in the section Converting the end plates."
· Fit the pneumatic multipin as described under Fitting the pneumatic multipin" in chapter 2.
5−20
Festo P.BE−CPV−EN en 0503g
5. Maintenance and conversion
5.7
Conversion of the CPV valve terminal to two pressure zones
In order to convert your CPV valve terminal to two pressure zones, you will require a separator plate (must be ordered separately).
Please note
· When installing the CPV valve terminal, note that the compressed air must be supplied on both sides of the valve terminal.
· Seal non−required connections (supply or auxiliary pilot air connections) with blind plugs.
Fit the separator plate as described in the section Fitting components on valve locations."
Festo P.BE−CPV−EN en 0503g
5−21
5. Maintenance and conversion
5.8
Converting the CPV valve terminal to a variant with different electrical connections
Due to the modular structure of the CPV valve terminal, you can easily convert it to IC, MP, AS−Interface, DI or CP connec tions.
Please note
Please note the instructions in the compatibility list in this chapter as regards combining versions with different elec trical connections with the following plates:
Single−solenoid 5/2−way valve (Ident. code F)
Relay plates (Ident. code R).
Proceed as follows:
CPV valve terminals with IC connection
· Loosen the locking screws on the connector sockets.
· Pull the sub−base carefully away from the terminal lugs of the pilot solenoids.
· Insert the MP, AS−Interface, DI or CP connection onto the terminal lugs of the pilot solenoids.
· Secure the sub−base with the 4 Philips screws. Tighten the screws in diagonally opposite sequence.
5−22
Festo P.BE−CPV−EN en 0503g
5. Maintenance and conversion
Note the following on CPV valve terminals with MP,
AS−Interface, DI and CP connections
· Loosen the 4 Philips screws in the sub−base.
· Pull the sub−base carefully away from the terminal lugs of the pilot solenoids.
· Insert the sub−base of the other connection variants (MP,
AS−Interface, DI or CP connection) into the terminal lugs of the pilot solenoids.
· Secure the sub−base with the 4 Philips screws.
· Tighten the screws in diagonally opposite sequence.
Festo P.BE−CPV−EN en 0503g
5−23
5. Maintenance and conversion
5−24
Festo P.BE−CPV−EN en 0503g
Technical appendix
Appendix A
Festo P.BE−CPV−EN en 0503g
A−1
A. Technical appendix
Contents
A.
A.1
A.2
Technical appendix . . . . . . . . . . . . . . . . . . . . . . . . . . . . . . . . . . . . . . . . . . . . . A−1
Technical specifications . . . . . . . . . . . . . . . . . . . . . . . . . . . . . . . . . . . . . . . . . .
Accessories . . . . . . . . . . . . . . . . . . . . . . . . . . . . . . . . . . . . . . . . . . . . . . . . . . . .
A−3
A−10
A−2
Festo P.BE−CPV−EN en 0503g
A. Technical appendix
A.1
Technical specifications
General
Permitted temperature range
Storage
Operation
Medium
Protection class as per EN 60 529
Relative humidity
Corrosion protection
(as per FN 940070)
Mounting position
Torques
Connector socket for IC connection
Connector socket for relay outputs
Field bus plug
Fastening screw for wall support or hat rail
Fastening screws of the CP valve terminal on the pneumatic multipin
Electrical sub−base
Earth/ground connection
Tie rod
Large surface−mounted silencer element on the end plate
Valve actuators
− 20 to + 40 °C
− 5 to + 50 °C (vacuum generator plates: 0 to + 50)
− 5 to + 50 °C (vacuum generator plates: 0 to + 50)
IP65 (with cable from Festo accessories)
90 %
KBK 2 (vacuum generator plates: KBK 1)
As desired
CPV10/14
0.15 Nm
0.15 Nm
1.15 ± 0.15 Nm
1.5 Nm
2.0 Nm
0.75 ± 0.15 Nm
1.0 Nm
1. Step 0.3 Nm
2. Step 2.0 Nm
CPV10: 1.0 Nm ± 10 %
CPV14: 1.7 Nm ± 10 %
CPV10: 0.8 Nm
CPV14: 1.2 Nm
CPV18
4.0 Nm
1.15 ± 0.15 Nm
4.0 Nm
3.0 Nm
1.0 Nm
1. Step 0.3 Nm
2. Step 4.0 Nm
5.0 Nm ± 1 Nm
Materials
Plates, covers, pneumatic multipin
Seals
AL, AL−GD, Ms, PAXMD6, PET, POM, PPS, PA, ST
NBR, HNBR
Festo P.BE−CPV−EN en 0503g
A−3
A. Technical appendix
General
Vibration (as per DIN/IEC 68 part 2−6)
Transport
Operation
Shock (as per DIN/IEC 68 part 2−27)
3.5 mm path at 2...9 Hz
1 g acceleration at 9...200 Hz
0.35 mm path at 10...60 Hz
5 g acceleration at 60...150 Hz
30 g acceleration at 11 ms duration
Tab.A/1: General technical specifications
A−4
Festo P.BE−CPV−EN en 0503g
A. Technical appendix
General
Approx. weights (in kg)
Electric sub−base with AS−Interface connection
on CP valve terminals with 2 valve locations
on CP valve terminals with 4 valve locations
Electrical sub−base with CP connection
on CP valve terminals with 4 valve locations
on CP valve terminals with 6 valve locations
on CP valve terminals with 8 valve locations
Electrical sub−base with MP connection
on CP valve terminals with 4 valve locations
on CP valve terminals with 6 valve locations
on CP valve terminals with 8 valve locations
End plates
Pneumatic multipin
on CP valve terminals with 2 valve locations
on CP valve terminals with 4 valve locations
on CP valve terminals with 6 valve locations
on CP valve terminals with 8 valve locations
Large surface−mounted silencer
Relay plate
Blanking plate
Separator plates
Valve sub−bases, vacuum generator plates
Valve extension: 5/3G function
Valve extensions: One−way flow control valves
CPV10
0.085
0.110
0.145
0.180
0.200
0.110
0.140
0.165
0.160
0.025
0.025
0.65
0.46
0.025
0.120
0.165
0.225
0.270
0.147
0.035
CPV14
0.130
0.175
0.230
0.250
0.300
0.170
0.230
0.275
0.280
0.045
0.045
0.110
0.105
0.054
0.270
0.390
0.510
0.630
0.234
0.055
Tab.A/2: Technical specifications weight of the CPV valve terminal
CPV18
0.275
0.355
0.375
0.450
0.540
0.400
0.425
0.515
0.740
0.520
0.750
0.870
1.300
0.090
0.090
0.260
0.125
Festo P.BE−CPV−EN en 0503g
A−5
A. Technical appendix
Caution
If possible, operate the CPV valve terminal with non−lu bricated auxiliary pilot air (connections 12/14). Other wise observe the instructions in the section Operation with lubricated compressed air" in chapter 3.
In the case of CP valve terminals with internally branched auxiliary pilot air, the above mentioned remark also applies to the supply air (connection 1/11).
Pneumatics
Medium
Design
Pressure range
Optimum operating pressure
Rated supply pressure
With internally branched auxiliary pilot air from 1 or 11
With externally supplied auxiliary pilot air 1 or 11 for vacuum generator plates
Connection 1
Connection 11
12/14
Manual override
Compressed air, filtered (40 ì m), lubricated (oil: VG 32) or non−lubricated/vacuum
Inert gases permitted
Valve plates with spool valves
CPV10/14 CPV18
5...7 bar
6 bar
3...8 bar
5...7 bar
6 bar
3...8 bar
− 0.9...10 bar − 0.9...10 bar
2...10 bar
0...10 bar
3...8 bar
Locking or non−locking
3.5...8 bar (Ident. code G)
2...8 bar (Ident. code J)
3...8 bar (all other valves)
Tab.A/3: Technical specifications medium and pressure ranges
Please note
The screw connectors of the pneumatic connections cause a reduction in the flow rate of the valves.
A−6
Festo P.BE−CPV−EN en 0503g
A. Technical appendix
Pneumatics
Flow rates
(without screw connector) in [I/min] from 11
å
2 or 1
å
4
CPV10 CPV14 CPV18
400 800 1600
1400 (5/3−way valve)
1600 from 2
å
3/5 or 4
å
4
Valve switching times in ms
400 800
Measuring method 10 % as per FN 942032
,
2/2−way valve (Ident. code D and I)
CPV10
On, change over
Off
15 17
(at 0 %)
CPV14
On, change over
Off
13 16
(at 0 %)
CPV18
On, change over
Off
14 20
(at 0 %)
2/2−way valve for reject pulse in vacuum generator plate
(Ident. code E)
15 17
(at 0 %)
13 16
(at 0 %)
14 20
(at 0 %)
3/2−way valve, open or closed
(Ident. codes C, H, N)
5/2−way,, single−solenoid
(Ident. code M)
5/2−way, single−solenoid
(Ident. code F)
5/2−way double−solenoid
(Ident. code J)
5/3−way valve, mid−position locked
(Ident. code G)
17
17
13
10
Vacuum generator plates
Vacuum (V max
Connections
)
(different values for pneumatic multipin in brackets)
Compressed air (1; 11)
Exhaust (3/5)
Auxiliary pilot air (12; 14; 82/84)
Work air (2; 4)
G 1/8
M5 (M7)
M7
25
27
17
G 3/8 (G 1/4)
24
25
12
G 1/4
30
35
G 1/2 (G 3/8)
G 1/8
G 1/8
18
18.5
12
14
G 3/8
G 1/2
G 1/4
G 1/4
24
26
32
− 0.85 bar (the highest possible vacuum is reached within the working pressure range.
CPV10 CPV14 CPV18
Tab.A/4: Technical specifications rated flows, valve switching times and connection sizes
Festo P.BE−CPV−EN en 0503g
A−7
A. Technical appendix
Electrics (CPV valve terminal with IC or CP connection)
Electromagnetic compatibility of the CPV valve terminal with
CP connection
Interference emitted
Resistance to interference (the maxi mum permitted signal cable length is
30 m)
Protection against electric shock
(protection against direct and indirect con tact as per IEC/DIN EN 60204−1)
Protection against explosion
(as per EU guideline 94/9/EG, EN 50021 and EN 50281−1−1) Do not disconnect elec trical connections which are under tension.
Relay plate
Tested as per DIN EN 61000−6−4 (industry) 1)
Tested as per DIN EN 61000−6−2 (industry) by means of PELV circuits
(ProtectiveExtra−Low Voltage)
II 3 G/D EEx nA II T5 − 5 °C
Ţ
Ta
Ţ
+ 50 °C T 80 °C
IP65 (year of manufacture see Ex−marking on product)
Plugs or adapters of the electric connections must comply at least with protection class IP64.
Consisting of two relays for controlling
2 electrically isolated outputs
Operating voltage
Tolerance
Residual ripple
Power consumption at 21 V
Values in brackets for 24 V
24 V DC
20.4...26.4 V
4 Vpp
CPV10 CPV14
CPV valve terminal all connection variants:
per valve solenoid coil valve sub−base with Ident. code F
CPV valve terminals:
per relay plate
CPV valve terminal with IC connection:
additional per IC connector plug
Input current consumption of electronics
CP valve terminal with CP connection
0.46 W
(0.6 W)
(0.65 W)
(1.2 W)
Ţ
0.26 W
0.65 W
(0.9 W)
(1.2 W)
Ţ
0.26 W
20 mA
Current consumption
CP valve terminal with IC connection 20 mA in 24 ms at 24 V
1) The component is intended for industrial use.
CPV18
1.16 W
(1.5 W)
Ţ
0.26 W
25 mA
63 mA
A−8
Festo P.BE−CPV−EN en 0503g
A. Technical appendix
Electrics (CPV valve terminal with IC or CP connection)
Data of load current circuit of the relay outputs (at 24 V + 10 %)
Switching times of the relay outputs
(at nominal voltage)
Pick−up
Drop−out
1 A; floating contacts
5 ms
2 ms
Tab.A/5: Technical specifications electric components
Please note
Data on the electric components of the CPV valve terminal with Multipin, AS−Interface or direct connection are en closed with the relevant product.
Festo P.BE−CPV−EN en 0503g
A−9
A. Technical appendix
A.2
Accessories
Components CPV10/14 CPV18
Mounting kits:
for hat rail fitting
for wall fitting
for wall (top) fitting the CPV valve ter minal onto the Siemens SIMATIC ET200X
Identifier labels
Identifier support
Manual override cover
Manual override security
Valve extensions:
5/3G
Supply air one−way flow control valve
Exhaust air one−way flow control valve
One−way flow control valve for reject pulse
Blanking plug
Socket with cable for relay plate
Socket without cable for relay plate
CP valve terminal with AS−Interface connection
Addressing device
Adapter cable
AS−Interface combi power pack
AS−Interface bus cable (yellow)
AS−Interface additional supply cable (black)
AS−Interface cable cap
AS−Interface cable sleeve
Sensor cable
CPV valve terminal with CP connection
CP cable
CPV10/14−VI−BG−NRH−35
CPV10/14−VI−BG−RWL−B
CPV..−VI−BG−ET200X
IBS6x10
CPV..−VI−BZ−T−..
CPV10/14−HV
CPV10/14−HS
CPV..−BS−5/3G−..
CPV..−BS−2xGRZZ−..
CPV..−BS−2xGRAZ−..
CPV..−BS−GRZ−V−..
B−M..
KRP−1−24−...
MSSD−ZBZC
KASI−PRG−ADR
KASI−ADR
ASI−CNT−115/230VAC−B
KASI−1.5−Y−100
KASI−1.5−Z−100
ASI−KK−FK
ASI−KT−FK
KM8−M8−GSGD
CPV18−VI−BG−NRH−35
CPV18−VI−BG−RWL−B
IBS9x20
CPV18−VI−BZ−T...
CPV..−BS−2xGRZZ−..
CPV..−BS−2xGRAZ−..
CPV..−BS−GRZ−V−..
KVI−CP−1...
KVI−CP−2... (suitable for drag chain)
A−10
Festo P.BE−CPV−EN en 0503g
A. Technical appendix
Components
CP valve terminal with IC connection
IC connector plug
Socket with cable
Socket without cable
CPV valve terminal with MP connection
Ready−to−use multipin cable
Multipin cable (suitable for drag chain)
Multipin socket
CPV10/14 CPV18
KMYZ−7−24−...−LED
(with current reduction)
MSSD−ZBZC
KMEB−2−24−..−LED
MSSD−ZBZC
KMP3−..P−..−.
KMP4−..P−...
SD−SUB−D−BU−..
Tab.A/6: Festo accessories for CPV valve terminal
Festo P.BE−CPV−EN en 0503g
A−11
A. Technical appendix
A−12
Festo P.BE−CPV−EN en 0503g
Summary of components
Appendix B
Festo P.BE−CPV−EN en 0503g
B−1
B. Summary of components
Contents
B.
B.1
B.2
Summary of components . . . . . . . . . . . . . . . . . . . . . . . . . . . . . . . . . . . . . . . .
Overview of valve sub−bases and vacuum generator plates . . . . . . . . . . . . .
Overview of end plates . . . . . . . . . . . . . . . . . . . . . . . . . . . . . . . . . . . . . . . . . .
B−1
B−3
B−8
B−2
Festo P.BE−CPV−EN en 0503g
B. Summary of components
B.1
Overview of valve sub−bases and vacuum generator plates
The CPV valve terminals are available with the following valve sub−bases and vacuum generator plates:
Please note
The numbers in the following circuit diagrams are the des ignations of the connections, coils and manual overrides; e.g. designation 14 stands for manual override 14 or coil
14. They are not logic designations.
Valve sub−base
14
82/84
4 2
Remarks
12
Ident. code: D
Valves:
two 2/2−way valves
single−solenoid
blocked in output position
pneumatic spring return
12/14
82/84
4
1
14
12/14
1
3/5
3/5
11
2
11
12
Ident. code: I
Valves:
two 2/2−way valves
single−solenoid
control side 14 blocked in basic position
control side 12 open in basic position
pneumatic spring return
Tab.B/1: Overview valve sub−bases with 2/2−way valves
Festo P.BE−CPV−EN en 0503g
B−3
B. Summary of components
Valve sub−base (continued)
82/84
4 2
14
12/14
14
12/14
14
1
82/84
4
1
82/84
4
1
3/5 11
3/5 11
2
2
3/5 11
Remarks
12
Ident. code: N
Valves:
two 3/2−way valves
single−solenoid
open in basic position
pneumatic spring return
Function:
The function of a 5/3−way valve in mid−position pressurized can be implemented with these valves in basic position open.
12
Ident. code: C
Valves:
two 3/2−way valves
single−solenoid
blocked in basic position
pneumatic spring return
Function:
The function of a 5/3−way valve in mid−position exhausted can be implemented with these valves in basic position blocked.
Please note
If you control a double−acting cylinder with this valve sub−base, please note that the function of a 5/3−way mid−position valve can be implemen ted if both valve solenoid coils are actuated simultaneously.
12
Ident. code: H
Valves:
two 3/2−way valves
single−solenoid
control side 14 blocked in basic position
control side 12 open in basic position
pneumatic spring return
12/14
Tab.B/2: Overview valve sub−bases with 3/2−way valves
B−4
Festo P.BE−CPV−EN en 0503g
B. Summary of components
Valve sub−base (continued)
14
82/84
4 2
12/14
1
3/5
11
82/84
4 2
12
Remarks
Ident. code: F (only CPV10 valve terminal) or M
Valve:
5/2−way valve
single−solenoid
pneumatic spring return
with Ident. code F fast switching
Please note
In the case of CPV valve terminals with the following connections, please note the limits on using the valve sub−base with Ident. code F.
IC connection: "F valve sub−bases" may only be used with a connector socket for current reduction KMYZ−... .
Interbus direct connection type CPV10−GE−IL−..:
These CPV valve terminals must not be used with "F valve sub−bases."
Ident. code: J
Valve:
5/2−way double−solenoid valve
14 12
12/14
1
3/5
11
Tab.B/3: Overview valve sub−bases with 5/2−way valves
Festo P.BE−CPV−EN en 0503g
B−5
B. Summary of components
Valve sub−base (continued)
CPV10/14:
14
82/84
4 2
12
Remarks
Ident. code: G
Function:
5/3−way valve blocked in mid−position
Valve (CPV10/14):
two 3/2−way valves
single−solenoid
blocked in basic position
pneumatic spring return
5/3G valve extension
(two unlockable non−return valves)
12/14
1 3/5
CPV18:
82/84
4 2
14
12/14
1
3/5
11
11
12
Valve (CPV18):
5/3−way valves
blocked in mid−position
single−solenoid
pneumatic spring return
Tab.B/4: Overview valve sub−base or function (5/3−way valves)
B−6
Festo P.BE−CPV−EN en 0503g
B. Summary of components
Vacuum generator plate
14
82/84 4 2
11
12
Remarks
Ident. code: A
Function: Vacuum generator (control side 14)
Valve:
2/2−way valve
single−solenoid
blocked in basic position
air−assisted pneumatic spring return
flow control valve at output 4 12/14
1 3/5
14
82/84
12/14 1
4
3/5
2
11
12
Ident. code: I
Function:
vacuum generator (control side 14)
reject pulse (control side 12)
Valve at control side 14:
2/2−way valve
single−solenoid
blocked in basic position
air−assisted pneumatic spring return
flow control valve at output 4
Valve at control side 12:
2/2−way valve
single−solenoid
blocked in basic position
pneumatic spring return
Tab.B/5: Overview vacuum generator plates
Festo P.BE−CPV−EN en 0503g
B−7
B. Summary of components
B.2
Overview of end plates
By means of the part number (position see below) and the table below, you can ascertain which end plates are fitted on your CPV valve terminal. In the case of CPV valve terminals with AS−Interface, CP or MP connection, the electrical sub− base must be dismantled for this purpose.
1
Part number
1
Fig.B/1: Position of end plate part number
B−8
Festo P.BE−CPV−EN en 0503g
B. Summary of components
End plate
Left−hand end plates
CPV..−EPL: no connections 161 378 162 548 163 280
161 374 162 544 163 196 CPV..−EPL−E: axial connections, connections 1 and 11 separate
CPV..−EPL−G: axial connections, connections 1 and 11 connected 161 376 162 546 163 198
161 370 162 540 163 194 CPV..−EPL−PE: for pneumatic multipin, connections 1 and 11 separate
CPV..−EPL−PG: for pneumatic multipin, connections 1 and 11 connected
CPV..−EPL−EU: with large surface−mounted silencer
161 372 162 542 163 192
CPV..−EPR−PEU: with large surface−mounted silencer, for pneumatic multipin, connections 1 and 11 separate
188 454 188 458 192 939
188 452 188 456 192 938
Right−hand end plates
CPV..−EPR: no connections
CPV..−EPR−E: axial connections, connections 1 and 11 separate external auxiliary pilot air
CPV..−EPR−G: axial connections, connections 1 and 11 connected internal auxiliary pilot air
CPV..−EPR−PE: for pneumatic multipin, connections 1 and 11 separate external auxiliary pilot air
161 379
161 375
161 377
161 371
162 549
162 545
162 547
162 541
163 281
163 197
163 199
163 195
CPV..−EPR−PG: for pneumatic multipin, connections 1 and 11 connected internal auxiliary pilot air
CPV..−EPR−EU: with large surface−mounted silencer
CPV..−EPR−PEU: with large surface−mounted silencer, for pneumatic multipin, connections 1 and 11 separate, external auxiliary pilot air
CPV..−EPR−PGU:with large surface−mounted silencer, for pneumatic multipin, connections 1 and 11 connected, internal auxiliary pilot air
161 373
188 455
188 453
193 913
162 543
188 459
188 457
193 914
163 193
192 941
192 940
194 006
Tab.B/6: Overview end plate identification
Part number
CPV10 CPV14 CPV18
Festo P.BE−CPV−EN en 0503g
B−9
B. Summary of components
All available end plate combinations are listed in the following tables. Check the end plates you wish to use with regard to their compatibility, see following tables.
Description End plate pairs for internal auxiliary pilot air
(internal pilot air), with pneumatic connections
CPV..−EPL CPV..−EPR−G
Ident. code: U
Connections only in the right−hand end plate
Pressure zone separation not permitted
Cannot be used for vacuum
CPV..−EPL−E
CPV..−EPL−G
CPV..−EPR−G
CPV..−EPR
Ident. code: Y:
Connections in left and right−hand end plates
Pressure zone separation permitted
Maximum number of pressure zones 3
Valves to the left of the separator plate can be used for vacuum
· Connections, which are not required for the function of the valve terminal, must be sealed
(see also section 3.3.2 Connect ing the supply and work tubing).
Ident. code: V
Connections only in the left−hand end plate
Pressure zone separation not permitted
Cannot be used for vacuum
B−10
Festo P.BE−CPV−EN en 0503g
B. Summary of components
End plate pairs for internal auxiliary pilot air
(internal pilot air), with pneumatic connections
CPV..−EPL−G
CPV..−EPL−G
CPV..−EPR−E
CPV..−EPR−G
Description
Ident. code: −−−
Connections in left and right−hand end plates
Pressure zone separation permitted
Maximum number of pressure zones 3
Valves to the right of the separator plate can be used for vacuum
Connection 12/14 in the right− hand end plate must be sealed
· with a blind plug.
Connections, which are not required for the function of the valve terminal, must be sealed
(see also section 3.3.2 Connect ing the supply and work tubing).
Ident. code: −−−
Connections in left and right−hand end plates
Pressure zone separation only permitted with separator plate
Ident.code S for exhaust separ ation.
Maximum number of pressure zones 1
Cannot be used for vacuum
Tab.B/7: End plates for internal auxiliary pilot air
Festo P.BE−CPV−EN en 0503g
B−11
B. Summary of components
End plate pairs for internal auxiliary pilot air
(internal pilot air), with pneumatic connections and large surface−mounted silencer
CPV..−EPL−G CPV..−EPR−EU
ÎÎ
CPV..−EPL−EU
ÎÎ ÎÎ ÎÎ
ÎÎ Î Î ÎÎ ÎÎ
Î Î Î ÎÎ
Î
CPV..−EPR−G
ÎÎ ÎÎÎ
ÎÎ ÎÎÎ ÎÎÎ ÎÎ ÎÎ ÎÎ
ÎÎ ÎÎ ÎÎ ÎÎ ÎÎ
ÎÎ ÎÎ ÎÎ
Description
Ident. code: B
Connections in the left−hand end plate
Pressure zone separation not permitted
Cannot be used for vacuum
Ident. code: A
Connections in the right−hand end plate
Pressure zone separation not permitted
Cannot be used for vacuum
Tab.B/8: End plates for internal auxiliary pilot air, with large surface−mounted silencer
B−12
Festo P.BE−CPV−EN en 0503g
B. Summary of components
End plate pairs for internal auxiliary pilot air
(internal pilot air), with pneumatic connections
CPV..−EPL−E CPV..−EPR
Description
Ident. code: X
Connections only in the left−hand end plate
Pressure zone separation not permitted
Can be used for vacuum
CPV..−EPL CPV..−EPR−E
Ident. code: W
Connections only in the right−hand end plate
Pressure zone separation not permitted
Can be used for vacuum
CPV..−EPL−E CPV..−EPR−E
Tab.B/9: End plates for external auxiliary pilot air
Ident. code: Z
Connections in left and right−hand end plates
Pressure zone separation permitted
Maximum number of pressure zones 4
Can be used for vacuum
· Connections, which are not required for the function of the valve terminal, must be sealed
(see also section 3.3.2 Connect ing the supply and work tubing).
Festo P.BE−CPV−EN en 0503g
B−13
B. Summary of components
End plate pairs for external auxiliary pilot air
(external pilot air), with pneumatic connections and large surface−mounted silencer
CPV..−EPL−E CPV..−EPR−EU
ÎÎÎ
ÎÎÎ ÎÎ ÎÎ
ÎÎ ÎÎ ÎÎ Î ÎÎ ÎÎ
ÎÎ ÎÎ Î ÎÎ
CPV..−EPL−EU
ÎÎ ÎÎ
ÎÎ ÎÎ ÎÎ ÎÎ ÎÎ ÎÎ
ÎÎ ÎÎ ÎÎ ÎÎ ÎÎ
ÎÎ ÎÎ ÎÎ
CPV..−EPR−E
Description
Ident. code: D
Connections in the left−hand end plate
Pressure zone separation not permitted
Can be used for vacuum
Ident. code: C
Connections in the right−hand end plate
Pressure zone separation not permitted
Can be used for vacuum
Tab.B/10: End plates for external auxiliary pilot air, with large surface−mounted silencer
B−14
Festo P.BE−CPV−EN en 0503g
B. Summary of components
End plate pairs for internal auxiliary pilot air
(internal pilot air) and pneumatic multipin
CPV..−EPL−PG CPV..−EPR−PG
Description
CPV..−EPL−PE CPV..−EPR−PG
Ident. code: Y
Connections on the pneumatic multipin
Pressure zone separation only permitted with separator plate
Ident. code T.
Maximum number of pressure zones 2
Valves to the left of the separator plate can be used for vacuum
Right−hand end plate with inter nally branched auxiliary pilot air is marked with INT .
Ident. code: −−−
Connections on the pneumatic multipin
Pressure zone separation only permitted with separator plate
Ident. code T.
Maximum number of pressure zones 3
Valves to the left of the separator plate can be used for vacuum
Right−hand end plate with inter nally branched auxiliary pilot air is marked with INT .
Tab.B/11: End plate pairs for internal auxiliary pilot air and pneumatic multipin
Festo P.BE−CPV−EN en 0503g
B−15
B. Summary of components
End plate pairs for internal auxiliary pilot air
(internal pilot air) and pneumatic multipin, with large surface−mounted silencer
Description
CPV..−EPL−PEU
ÎÎ
ÎÎ ÎÎÎ ÎÎ
ÎÎ ÎÎ ÎÎÎ ÎÎ ÎÎ ÎÎ
ÎÎ ÎÎ ÎÎ ÎÎ
CPV..−EPL−PE
CPV..−EPR−PG
CPV..−EPR−PGU
ÎÎ
ÎÎ ÎÎ ÎÎ
ÎÎ ÎÎ ÎÎ ÎÎ ÎÎ
ÎÎ ÎÎ ÎÎ ÎÎ ÎÎ
ÎÎ ÎÎ
Ident. code: G
Connections on the pneumatic multipin
Exhaust conducted via a large surface−mounted silencer
Pressure zone separation only permitted with separator plate
Ident. code T.
Maximum number of pressure zones 3
Cannot be used for vacuum
Right−hand end plate with inter nally branched auxiliary pilot air is marked with INT .
Ident. code: K
Connections on the pneumatic multipin *)
Exhaust conducted via a large surface−mounted silencer
Pressure zone separation permitted
Maximum number of pressure zones 3
In conjunction with separator plate can be used for vacuum
CPV..−EPL−PG CPV..−EPR−PGU
ÎÎ ÎÎ ÎÎ
ÎÎ ÎÎ ÎÎ ÎÎ ÎÎ ÎÎ
ÎÎ ÎÎ ÎÎ ÎÎ ÎÎ
ÎÎ ÎÎ ÎÎ ÎÎ
Ident. code: −−−
Connections on the pneumatic multipin *)
Exhaust conducted via a large surface−mounted silencer
Pressure zone separation permitted
Maximum number of pressure zones 2
*) Close connections 11 and 12/14 on the pneumatic multipin below the right−hand end plate.
B−16
Festo P.BE−CPV−EN en 0503g
B. Summary of components
End plate pairs for internal auxiliary pilot air
(internal pilot air) and pneumatic multipin, with large surface−mounted silencer
Description
CPV..−EPL−PEU
ÎÎ
ÎÎ ÎÎ ÎÎ
ÎÎ ÎÎ ÎÎ ÎÎ ÎÎ ÎÎÎ ÎÎ ÎÎ ÎÎ ÎÎ
ÎÎ ÎÎ ÎÎ ÎÎ ÎÎ ÎÎ ÎÎ ÎÎ
ÎÎ
CPV..−EPR−PGU
ÎÎ
ÎÎ ÎÎÎ ÎÎ
ÎÎ
Ident. code: J
Connections on the pneumatic multipin *)
Exhaust conducted via a large surface−mounted silencer
Pressure zone separation permitted
Maximum number of pressure zones 3
Valves to the left of the separator plate can be used for vacuum
*) Close connections 11 and 12/14 on the pneumatic multipin below the right−hand end plate.
Tab.B/12: End plate pairs for internal auxiliary pilot air and pneumatic multipin, with large surface−mounted silencer
End plate pairs for external auxiliary pilot air
(external pilot air) and pneumatic multipin
CPV..−EPL−PE CPV..−EPR−PE
Description
CPV..−EPL−PG CPV..−EPR−PE
Ident. code: Z
Connections on the pneumatic multipin
Pressure zone separation only permitted with separator plate
Ident. code T.
Maximum number of pressure zones 4
Can be used for vacuum
Ident. code: −−−
Connections on the pneumatic multipin
Pressure zone separation only permitted with separator plate
Ident. code T.
Maximum number of pressure zones 3
Can be used for vacuum
Tab.B/13: End plate pairs for external auxiliary pilot air and pneumatic multipin
Festo P.BE−CPV−EN en 0503g
B−17
B. Summary of components
End plate pairs for external auxiliary pilot air
(external pilot air) and pneumatic multipin, with large surface−mounted silencer
CPV..−EPL−PE CPV..−EPR−PEU
ÎÎ
ÎÎ ÎÎ ÎÎ
ÎÎ Î ÎÎ ÎÎ ÎÎ
ÎÎ Î ÎÎ ÎÎ
ÎÎ Î
CPV..−EPL−PG CPV..−EPR−PEU
ÎÎ ÎÎ ÎÎ
ÎÎ ÎÎ ÎÎ ÎÎ Î ÎÎ
ÎÎ Î ÎÎ ÎÎ ÎÎ
ÎÎ Î
CPV..−EPL−PEU
ÎÎ ÎÎ
ÎÎ ÎÎ ÎÎ Î ÎÎ ÎÎ
ÎÎ Î ÎÎ ÎÎ ÎÎ
ÎÎ Î ÎÎ
CPV..−EPR−PE
Description
Ident. code: I
Connections on the pneumatic multipin
Exhaust conducted via a large surface−mounted silencer
Pressure zone separation only permitted with separator plate
Ident. code T.
Maximum number of pressure zones 4
Can be used for vacuum
Ident. code: −−−
Connections on the pneumatic multipin
Exhaust conducted via pneumatic multipin and large surface− mounted silencer
Pressure zone separation only permitted with separator plate
Ident. code T.
Maximum number of pressure zones 3
Can be used for vacuum
Ident. code: F
Connections on the pneumatic multipin
Exhaust conducted via a large surface−mounted silencer
Pressure zone separation only permitted with separator plate
Ident. code T.
Maximum number of pressure zones 4
Can be used for vacuum
B−18
Festo P.BE−CPV−EN en 0503g
B. Summary of components
End plate pairs for external auxiliary pilot air
(external pilot air) and pneumatic multipin, with large surface−mounted silencer
Description
CPV..−EPL−PEU
ÎÎ
CPV..−EPR−PEU
ÎÎ ÎÎ ÎÎ ÎÎ ÎÎÎ ÎÎ
ÎÎ ÎÎ ÎÎ ÎÎ ÎÎ ÎÎÎ ÎÎ ÎÎ ÎÎ ÎÎ
ÎÎ ÎÎ ÎÎ ÎÎ ÎÎ ÎÎ ÎÎ ÎÎ
CPV..−EPL−EU
ÎÎ ÎÎ ÎÎ ÎÎ
CPV..−EPR−PEU
Ident. code: H
Connections on the pneumatic multipin
Pressure zone separation permitted
Maximum number of pressure zones 4
Can be used for vacuum
ÎÎ ÎÎ ÎÎ ÎÎ ÎÎÎ ÎÎ
ÎÎ Î ÎÎ ÎÎ ÎÎ ÎÎÎ ÎÎ ÎÎ ÎÎ ÎÎ
ÎÎ ÎÎ ÎÎ Î ÎÎ ÎÎ ÎÎ ÎÎ
ÎÎ Î ÎÎ ÎÎ
Ident. code: −−−
Connections on the pneumatic multipin
Pressure zone separation not permitted
Can be used for vacuum
Tab.B/14: End plate pairs for external auxiliary pilot air and pneumatic multipin, with large surface−mounted silencer
Festo P.BE−CPV−EN en 0503g
B−19
B. Summary of components
B−20
Festo P.BE−CPV−EN en 0503g
Index
Appendix C
Festo P.BE−CPV−EN en 0503g
C−1
C. Index
Contents
C.
Index . . . . . . . . . . . . . . . . . . . . . . . . . . . . . . . . . . . . . . . . . . . . . . . . . . . . . . . . . C−1
C−2
Festo P.BE−CPV−EN en 0503g
C. Index
C.1
Index
Festo P.BE−CPV−EN en 0503g
A
Abbreviations . . . . . . . . . . . . . . . . . . . . . . . . . . . . . . . . . . . . XII
Accessories . . . . . . . . . . . . . . . . . . . . . . . . . . . . . . . . . . . . . 1−13
Address assignment
Outputs . . . . . . . . . . . . . . . . . . . . . . . . . . . . . . . . . . . . . . 3−19
AS−Interface connection . . . . . . . . . . . . . . . . . . . . . . . . . . . 1−5
Auxiliary pilot air
Branched internally
Supplied externally
. . . . . . . . . . . . . . . . . . . . . . . . . . . . .
. . . . . . . . . . . . . . . . . . . . . . . . . . . . .
3−9
3−9
B
Blanking plate . . . . . . . . . . . . . . . . . . . . . . . . . . . . . . . . . . . 1−7
C
Common pneumatic lines . . . . . . . . . . . . . . . . . . . . . . . . . 3−13
Compatibility list . . . . . . . . . . . . . . . . . . . . . . . . . . . . . . . . . 5−5
Components
5/3G valve extension
End plates
. . . . . . . . . . . . . . . . . . . . . . . . . . . .
. . . . . . . . . . . . . . . . . . . . . . . . . . . . . . . . . . . . .
1−8
B−8
Flow control valve . . . . . . . . . . . . . . . . . . . . . . . . . . . . . . .
Identification code . . . . . . . . . . . . . . . . . . . . . . . . . . . . . .
One−way flow control valve . . . . . . . . . . . . . . . . . . . . . . .
Pneumatic multipin . . . . . . . . . . . . . . . . . . . . . . . . . . . .
1−9
1−7
1−9
1−11
Relay plate . . . . . . . . . . . . . . . . . . . . . . . . . . . . . . . . . . .
Separator plates . . . . . . . . . . . . . . . . . . . . . . . . . . . . . . .
1−10
1−10
Vacuum generator plates
Valve sub−bases
. . . . . . . . . . . . . . . . . . . . . 1−9, B−3
. . . . . . . . . . . . . . . . . . . . . . . . . . . . . . . . B−3
Compressed air, requirements . . . . . . . . . . . . . . . . . . . . . . 3−3
Connection variants . . . . . . . . . . . . . . . . . . . . . . . . . . . . . . . 1−4
C−3
C. Index
C−4
Connections, electrical, CPV valve terminal with
AS−Interface connection . . . . . . . . . . . . . . . . . . . . . . . . .
CP connection
IC connection
MP connection
. . . . . . . . . . . . . . . . . . . . . . . . . . . . . . . . .
. . . . . . . . . . . . . . . . . . . . . . . . . . . . . . . . .
. . . . . . . . . . . . . . . . . . . . . . . . . . . . . . . .
1−18
1−17
1−15
1−16
Connections, pneumatic . . . . . . . . . . . . . . . . . . . . . . . . . . 1−14
CP connection . . . . . . . . . . . . . . . . . . . . . . . . . . . . . . . . . . . . 1−4
CP system
Description . . . . . . . . . . . . . . . . . . . . . . . . . . . . . . . . . . . . VIII
CPV valve terminal
Components . . . . . . . . . . . . . . . . . . . . . . . . . . . . . 1−12, 1−13
Simatic ET 200 X
Size
. . . . . . . . . . . . . . . . . . . . . . . . . . . . . . .
. . . . . . . . . . . . . . . . . . . . . . . . . . . . . . . . . . . . . . . . . .
2−14
1−6
Vacuum generator plates
Valve sub−bases
Variants
. . . . . . . . . . . . . . . . . . . . . . . . .
. . . . . . . . . . . . . . . . . . . . . . . . . . . . . . . .
. . . . . . . . . . . . . . . . . . . . . . . . . . . . . . . . . . . .
B−7
B−3
VI, 1−4
CPV valve terminal
Address assignment of the outputs
Earthing the valve terminal
. . . . . . . . . . . . . . .
. . . . . . . . . . . . . . . . . . . . . .
Pressure zones . . . . . . . . . . . . . . . . . . . . . . . . . . . . . . . .
3−19
3−17
3−14
D
Description . . . . . . . . . . . . . . . . . . . . . . . . . . . . . . . . . . . VIII, IX
Designated use . . . . . . . . . . . . . . . . . . . . . . . . . . . . . . . . . . . . V
DI connection . . . . . . . . . . . . . . . . . . . . . . . . . . . . . . . . . . . . 1−5
Display elements, CPV valve terminal with
AS−Interface connection . . . . . . . . . . . . . . . . . . . . . . . . .
CP connection
IC connection
MP connection
. . . . . . . . . . . . . . . . . . . . . . . . . . . . . . . . .
. . . . . . . . . . . . . . . . . . . . . . . . . . . . . . . . .
. . . . . . . . . . . . . . . . . . . . . . . . . . . . . . . .
1−18
1−17
1−15
1−16
E
Earthing the CPV valve terminal . . . . . . . . . . . . . . . . . . . . 3−17
EMERGENCY STOP . . . . . . . . . . . . . . . . . . . . . . . . . . . . . . . 4−15
End plate pairs . . . . . . . . . . . . . . . . . . . . . . . . . . . . . . B−9, B−10
Festo P.BE−CPV−EN en 0503g
C. Index
Festo P.BE−CPV−EN en 0503g
F
Fastening accessories
Fitting onto a hat rail
Fitting onto a wall
. . . . . . . . . . . . . . . . . . . . . . . . . . .
. . . . . . . . . . . . . . . . . . . . . . . . . . . . . . .
2−10
2−5
Fitting the
Identifier support . . . . . . . . . . . . . . . . . . . . . . . . . . . . . .
Manual override cover . . . . . . . . . . . . . . . . . . . . . . . . . .
Valve extensions . . . . . . . . . . . . . . . . . . . . . . . . . . . . . . .
2−24
2−25
2−23
Fitting variants . . . . . . . . . . . . . . . . . . . . . . . . . . . . . . . . . . . 2−3
Flow control valve . . . . . . . . . . . . . . . . . . . . . . . . . . . . . . . . 1−9
Flow rates . . . . . . . . . . . . . . . . . . . . . . . . . . . . . . . . . . . . . . . A−7
H
Hat rail . . . . . . . . . . . . . . . . . . . . . . . . . . . . . . . . . . . . . . . .
Clamping unit . . . . . . . . . . . . . . . . . . . . . . . . . . . . . . . . .
2−10
2−11
I
IC connection . . . . . . . . . . . . . . . . . . . . . . . . . . . . . . . . . . . . 1−4
Identification code . . . . . . . . . . . . . . . . . . . . . . . . . . . . . . . . 1−7
Identification labels . . . . . . . . . . . 1−14, 1−15, 1−16, 1−17, 1−18
Identifier labels . . . . . . . . . . . . . . . . . . . . . . . . . . . . . . . . . 2−24
Impairment of function . . . . . . . . . . . . . . . . . . . . . . . . . . . 4−13
Important user instructions . . . . . . . . . . . . . . . . . . . . . . . . . . . X
Input current consumption . . . . . . . . . . . . . . . . . . . . . . . . . A−8
C−5
C. Index
C−6
L
Large surface−mounted silencer
Cleaning/replacing . . . . . . . . . . . . . . . . . . . . . . . . . . . . . . 5−3
LED display
Position of the LEDs . . . . . . . . . . . . . . . . . . . . . . . . . . . .
Relay
Valves
. . . . . . . . . . . . . . . . . . . . . . . . . . . . . . . . . . . . . . . .
. . . . . . . . . . . . . . . . . . . . . . . . . . . . . . . . . . . . . . .
4−16
4−17
4−15
Low−pressure operation . . . . . . . . . . . . . . . . . . . . . . 3−14, 4−14
M
Manual override
Conversion
. . . . . . . . . . . . . . . . . . . . . . . . . . . . . . . . .
. . . . . . . . . . . . . . . . . . . . . . . . . . . . . . . . . . .
Cover
Types
. . . . . . . . . . . . . . . . . . . . . . . . . . . . . . . . . . . . . . . .
. . . . . . . . . . . . . . . . . . . . . . . . . . . . . . . . . . . . . . . . .
1−14
5−16
1−14
4−8
Materials . . . . . . . . . . . . . . . . . . . . . . . . . . . . . . . . . . . . . . . . A−3
Micro valves . . . . . . . . . . . . . . . . . . . . . . . . . . . . . . . . . . . . . 1−6
Midi valves . . . . . . . . . . . . . . . . . . . . . . . . . . . . . . . . . . . . . . 1−6
Mini valves . . . . . . . . . . . . . . . . . . . . . . . . . . . . . . . . . . . . . . 1−6
Mounting kit
Fitting onto a hat rail
Fitting onto a wall
. . . . . . . . . . . . . . . . . . . . . . . . . . . .
. . . . . . . . . . . . . . . . . . . . . . . . . . . . . . .
Simatic ET 200 X . . . . . . . . . . . . . . . . . . . . . . . . . . . . . . .
2−9
2−4
2−14
MP connection . . . . . . . . . . . . . . . . . . . . . . . . . . . . . . . . . . . 1−4
N
Notes on the use of this manual . . . . . . . . . . . . . . . . . . . . . . VI
Festo P.BE−CPV−EN en 0503g
C. Index
Festo P.BE−CPV−EN en 0503g
O
One−way flow control valve . . . . . . . . . . . . . . . . . . . . . . . . . 1−9
Operating elements
Pneumatic . . . . . . . . . . . . . . . . . . . . . . . . . . . . . . . . . . . . 1−14
Operating status . . . . . . . . . . . . . . . . . . . . . . . . . . . . . . . . 4−14
Operating voltage . . . . . . . . . . . . . . . . . . . . . . . . . . . . . . . . A−8
Overview of components . . . . . . . . . . . . . . . . . . . . . 1−12, 1−13
P
Pictograms . . . . . . . . . . . . . . . . . . . . . . . . . . . . . . . . . . . . . . . XI
Pneumatic
Connections . . . . . . . . . . . . . . . . . . . . . . . . . . . . . . . . . . . A−7
Pneumatic multipin . . . . . . . . . . . . . . . . 2−17, 2−18, 2−21, 2−22
Pneumatic operating status . . . . . . . . . . . . . . . . . . . . . . . 4−14
Power consumption . . . . . . . . . . . . . . . . . . . . . . . . . . . . . . . A−8
Pressure range . . . . . . . . . . . . . . . . . . . . . . . . . . . . . . . . . . . A−6
Pressure zones . . . . . . . . . . . . . . . . . . . . . . 3−8, 3−9, 3−14, 4−14
R
Relay outputs
Load current
. . . . . . . . . . . . . . . . . . . . . . . . . . . . . . 1−17, 3−18
. . . . . . . . . . . . . . . . . . . . . . . . . . . . . . . . . . . A−9
Switching times . . . . . . . . . . . . . . . . . . . . . . . . . . . . . . . . A−9
Relay plate . . . . . . . . . . . . . . . . . . . . . . . . . XIII, 1−7, 1−10, 1−12
S
Separator plates . . . . . . . . . . . . . . . . . . . . . . . . . . . . . . . . . . 1−7
Service . . . . . . . . . . . . . . . . . . . . . . . . . . . . . . . . . . . . . . . . . . VI
Simatic ET200X . . . . . . . . . . . . . . . . . . . . . . . . . . . . . . . . . 2−14
Size of the pneumatic screw connectors . . . . . . . . . . . . . 3−12
C−7
C. Index
C−8
SPC 200
Manuals . . . . . . . . . . . . . . . . . . . . . . . . . . . . . . . . . . . . . . . IX
Start−up pressurization . . . . . . . . . . . . . . . . . . . . . . . . . . . . 4−6
Supply pressure
External auxiliary pilot air
Internal auxiliary pilot air
. . . . . . . . . . . . . . . . . . . . . . . .
. . . . . . . . . . . . . . . . . . . . . . . . .
3−9
3−9
Switching status display . . . . . . . . . . . . . . . . . . . . . . . . . . 4−17
T
Target group . . . . . . . . . . . . . . . . . . . . . . . . . . . . . . . . . . . . . . VI
Text markings . . . . . . . . . . . . . . . . . . . . . . . . . . . . . . . . . . . . . XI
Tightening torques . . . . . . . . . . . . . . . . . . . . . . . . . . . . . . . . A−3
Tubing variants . . . . . . . . . . . . . . . . . . . . . . . . . . . . . . . . . . . 3−7
V
Vacuum generator . . . . . . . . . . . . . . . . . . . . . . . . . . . . . . . . A−7
Vacuum generator plates . . . . . . . . . . . . . . 1−7, 1−9, 3−15, B−7
Vacuum operation . . . . . . . . . . . . . . . . . . . . . . . . . . 3−14, 4−14
Valve extension
5/3G . . . . . . . . . . . . . . . . . . . . . . . . . . . . . . . . . . . . . . . . .
Flow control valve . . . . . . . . . . . . . . . . . . . . . . . . . . . . . . .
One−way flow control valve . . . . . . . . . . . . . . . . . . . . . . .
1−8
1−9
1−9
Valve sub−bases . . . . . . . . . . . . . . . . . . . . . . . . . . . . . . 1−7, B−3
Valve switching times . . . . . . . . . . . . . . . . . . . . . . . . . . . . . A−7
Valve test . . . . . . . . . . . . . . . . . . . . . . . . . . . . . . . . . . . . . . . 4−9
Vibration . . . . . . . . . . . . . . . . . . . . . . . . . . . . . . . . . . . . . . . . A−4
W
Weights . . . . . . . . . . . . . . . . . . . . . . . . . . . . . . . . . . . . . . . . . A−5
Festo P.BE−CPV−EN en 0503g
advertisement
* Your assessment is very important for improving the workof artificial intelligence, which forms the content of this project
Related manuals
advertisement
Table of contents
- 5 Contents
- 7 Designated use
- 8 Target group
- 8 Service
- 8 Notes on the use of this manual
- 12 Important user instructions
- 14 List of abbreviations
- 17 Sysytem summary
- 18 Contents
- 19 1.1 Description of variants
- 22 1.2 Description of components
- 35 Fitting
- 36 Contents
- 37 2.1 CPV valve terminal with individual tubing
- 38 2.1.1 Fitting onto a wall
- 43 2.1.2 Fitting onto a hat rail
- 46 2.1.3 Fitting onto a stand
- 48 2.1.4 Fitting the CPV valve terminal to the SIMATIC ET200X
- 51 2.2 CPV valve terminal with pneumatic multipin
- 52 2.2.1 Fitting the pneumatic multipin
- 56 2.2.2 Fitting the CPV valve terminal to the pneumatic multipin
- 57 2.3 Fitting the valve extensions
- 58 2.4 Fitting the identifier support
- 59 2.5 Fitting the manual override cover
- 61 Installation
- 62 Contents
- 63 3.1 Preparing the compressed air
- 63 3.1.1 Operation with non-lubricated compressed air
- 64 3.1.2 Operation with lubricated compressed air
- 66 3.2 General connecting methods
- 68 3.3 Connecting the CPV valve terminal
- 68 3.3.1 Auxiliary pilot air
- 71 3.3.2 Connecting the supply and work lines
- 76 3.3.3 Connecting the electric cables
- 83 Commissioning
- 84 Contents
- 85 4.1 General instructions
- 88 4.2 Testing the valves
- 89 4.2.1 Checking the valve functions
- 91 4.2.2 Checking the valve-cylinder combination
- 95 4.3 Eliminating faults
- 101 Maintenance and conversion
- 102 Contents
- 103 5.1 Cleaning/replacing the large surface-mounted silencer
- 104 5.2 Fitting/removing CPV valve terminal components
- 106 5.2.1 Removing components from valve locations
- 110 5.2.2 Fitting components in valve locations
- 116 5.3 Conversion from non-locking to locking manual override
- 117 5.4 Converting the end plates
- 119 5.5 Conversion to internal or external auxiliary pilot air
- 120 5.6 Conversion to individual tubing/central tubing
- 121 5.7 Conversion of the CPV valve terminal to two pressure zones
- 122 5.8 Converting the CPV valve terminal to a variant with different electrical connections
- 125 Technical appendix
- 126 Contents
- 127 A.1 Technical specifications
- 134 A.2 Accessories
- 137 Summary of components
- 138 Contents
- 139 B.1 Overview of valve sub-bases and vacuum generator plates
- 144 B.2 Overview of end plates
- 157 Index
- 158 Contents
- 159 C.1 Index