D.A.C.E SOLO Installation & Owner's Manual
Add to My manuals30 Pages
D.A.C.E Solo, a gate automation system, offers a host of features for controlling and securing gates. With built-in collision sensing, it detects obstructions and reverses the gate's direction to prevent accidents. Its auto-close function enhances convenience by automatically closing the gate after a set time. For added security, the system allows for programming multiple remotes and supports external status LED and vehicle detector connections. Furthermore, the Solo operator boasts a user-friendly digital business card and LCD screen for clear communication of gate status and settings.
advertisement
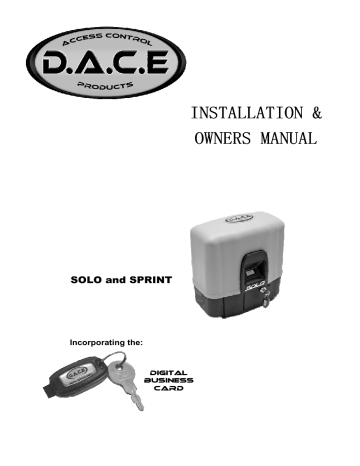
INDEX
INTRODUCTION; RECOMMENDATIONS & LEGAL REQUIREMENTS
RECOMMENDED TOOLS
GENERAL INFORMATION
GENERAL SITE LAYOUT
OPERATOR LAYOUT
SITE INFORMATION
GATE MASS, START UP & RUNNING FORCE
REMOVING THE LID
MANUAL OVERRIDE
PC BOARD LAYOUT
ELECTRICAL WIRING (SOLO 500; CONDO)
ELECTRICAL WIRING CONDO AC/DC ONLY
ANCHORING THE OPERATOR
SECURING THE OPERATOR TO THE FOUNDATION PLATE
MOUNTING THE MAGNET
MOUNTING THE RACK
FILLING THE GEARBOX WITH OIL (CONDO & CONDO AC/DC ONLY
SETTING THE MOTOR DIRECTION
PROGRAMMING THE OPERATOR
DIGITAL BUSINESS CARD
LCD SCREEN
LED INDICATIONS ON MAIN PC BOARD
SETTING PARTY MODE
SETTING OVERCURRENT SENSITIVITY
CONNECTING AN EXTERNAL STATUS LED
WIRING INFRARED SAFETY BEAMS
CONNECTING AN EXTERNAL RECEIVER
CONNECTING A VEHICLE DETECTOR
CONNECTING A SOLAR PANEL
DIPSWITCH SETTINGS
PROGRAMMING & ERASING REMOTES
TECHNICAL SPECIFICATIONS
WARRANTY
ADVERTORIAL
P17
P17
P17
P18
P18 - 19
P20
P21
P21
P22
P22
P23
P24
P25
P26
P27
P28
P28
P30 - 31
P3
P4
P5
P6
P7
P8
P9
P10
P10
P11
P12
P13
P14
P15
P15
P16
2
INTRODUCTION, RECOMMENDATIONS & LEGAL REQUIREMENTS
•
•
••••
•
Congratulations on your purchase of a D.A.C.E gate operator. D.A.C.E has proven to be a leader in the automation field and strives to manufacture high quality products using the latest technology available. D.A.C.E. is constantly working on upgrading their products to bring you, the customer, a product of the highest quality. Other products manufactured by D.A.C.E. include:-
•
•
•
•
•
Swing gate operators:
Infra-red safety beams:
Remotes and receivers :
Slide gate operators:
Vehicle detection loop:
DuraSwing
DuraOptics
DuraTronic
SOLO 500; CONDO & CONDO AC/DC
DuraLoop
It is recommended that an experienced gate installer is used to install your gate operator. If you intend installing this operator yourself please read this manual carefully before any installation begins.
D.A.C.E has taken all reasonable steps to ensure that the gate operator is safe to install and use.
However it must be remembered that a gate is a heavy piece of moving equipment and may cause serious damage or injury if the gate strikes an object or person. The gate operator has built in collision sensing electronics. Having struck an object the gate will stop and reopen, however this does mean that the gate will physically strike the object before it stops. It is therefore strongly recommended that
DuraOptics infrared safety beams are installed to reduce the risk of the gate striking an object.
Note: The installation of beams does not guarantee against the gate striking an object in its path.
Ensure the following items are checked before any installation is done :
•
•
•
•
•
•
•
•
•
•
•
The rail is level – the gate must not move on its own at any stage.
The wheels are turning freely and are not jammed.
The gate is not bent or bowed in any way.
The rail has sufficient end stops so that the gate can never run off the end of the rail.
The portal is constructed in such a way that the gate can not fall over.
The rollers are turning freely and are not jammed.
The anti lift device is sufficient in order to stop the gate from being lifted off the rail.
The gate mass or start-up force does not exceed the maximum as stated in the specifications.
The gate does not jam in the catch bracket when closing or opening.
Extreme care should be taken when automating a gate that is constructed out of any solid type of material such as wood, as wind resistance can cause over current problems.
The gate must not exceed the maximum number of operations stated in the specifications.
If any of the above points are not satisfactory do not install the operator until all the points are rectified.
Remember that if a gate causes damage or injury due to faulty installation then the installer of the equipment will be held liable.
It is recommended that your local E.C.A. (Electrical Contractors Association) is contacted in order to obtain the legal wiring regulations pertaining to the area.
Electrical Shock may occur while installing this equipment.
Injury or death by electrocution may lead to law suits against the installer/homeowner.
If you intend to run 230V/AC directly from the Mains supply (house supply) to the transformer, the wiring should be done by a qualified/registered electrician. This is a legal requirement and failure to do so may lead to non-compliance of property or law suits against the property owner in the event of an accident.
3
•
•
•
•
•
•
•
•
•
•
•
•
INTRODUCTION, RECOMMENDATIONS & LEGAL REQUIREMENTS cont.
It is a legal requirement to run all cabling in conduit. The power supply must be run in a separate conduit to ANY other cables.
Mains supply may only be run in a guarded cable. Under no circumstances may 230V/AC be run using Communication cable, Ripcord or Cabtyre.
Ensure that all electrical power is switched off before any electrical connections are made.
Do not open, tamper or modify any of the electrical components of this equipment in any way.
Do not attempt to repair the equipment, this should only be done by a qualified D.A.C.E. technician.
D.A.C.E will not be held liable for any accident / incident resulting in damage, injury or death ensuing from the installation of the automatic gate operator.
Although these operators have built-in collision sensing, substantial damage may still occur.
For this reason DuraOptics safety beams should be used on all installations.
Do not allow children to play near or with any gate, gate operator or remote control.
It is the responsibility of the installer to ensure that the gate is in good working condition before automating the gate.
D.A.C.E cannot be held responsible for any gates bumping the ends stops when a gate on a slope is automated.
It must be noted that an automatic gate is a heavy piece of equipment and injury, even death, may occur due to incorrect installation or operation of the equipment. There are a number of areas that may cause entrapment which could lead to injury.
Do not operate the gate unless within direct sight.
Shaded areas show the possible entrapment areas of an automated gate.
●
●
●
●
●
•
●
RECOMMENDED TOOLS
Drilling machine
8mm / 13mm / 17mm Spanners
13 / 17mm Socket
Spade
Multimeter
Wire cutters
Hacksaw
●
●
●
●
●
●
●
Steel & masonry drill bits
Assorted screwdrivers
Spirit level
Pick
Tape measure
Angle grinder
Hammer
4
GENERAL INFORMATION
• Auto-close : allows the gate to close automatically after a selected period of time. If Auto-close is selected, DuraOptics Infrared Safety Beams should be fitted.
• Multi-user mode : used in town house situation, allows the gate to open and will not accept any other trigger while opening, thus preventing accidental closure on a vehicle/person.
• Pedestrian access : allows only partial opening of the gate and will auto-close after 6 seconds.
• Anti-lift device : stops the gate being lifted off the rail.
• Battery : the battery is used to drive the operator. ( The CONDO AC/DC operator can operate without a battery ). The mains power supply is used to charge the battery only. I n the case of a mains power failure, the battery will continue to operate the operator until it runs flat. This should be for ± two days under normal conditions. The LCD will show “MAINS FAIL” if the mains power has failed and ”LOW BATT” if the battery is going flat.
• Battery Back-up : the CONDO AC/DC uses mains power to drive the operator, and the battery is used in the case of mains power failure.
• Safety Beams : These reduce the risk of the gate closing on a vehicle. DuraOptics (DOPT01) beams should always be used when auto-close is selected.
• Transformer : the transformer reduces the 230V mains power to 16 VAC.
• Charger module : the on-board charger receives 16 VAC from the transformer and then delivers a trickle charge to maintain ± 13.4 VDC charge to the battery.
• Main PC board : this is the printed circuit board that contains all the electronic components that operate the operator.
• Remote/Transmitter : this is usually a hand held device which transmits a radio signal to the receiver to trigger the gate ( DuraTronic TM002,TM003, TM004, TM006)
• Receiver : the receiver triggers the operator after receiving a radio signal from the transmitter.
• Test button : this is a button on the main PC Board that can be used to activate the operator. This is usually used during the programming of the operator.
• Rack : this is a length of toothed gear mounted on the gate.
• Pinion gear : this is the gear on the operator that meshes with the rack gear on the gate to move the gate.
• Foundation plate : this is the steel plate that is mounted to a concrete plinth in the ground. The operator is mounted onto the foundation plate using the three mounting bolts.
• Thumbwheel : this allows the operator to be put into Manual Override mode so that the gate can be pushed open/closed by hand.
• Free exit vehicle loop detector : this allows the gate to automatically open when a vehicle drives over a loop in the driveway.
• B.A.C. mode : “Beams Auto Close”. This allows the gate to close as soon as a vehicle passes through the Infrared Safety Beams. This prevents the gate going to the fully open position unnecessarily and remaining open awaiting the Auto-Close function to close the gate.
• Theft deterrent bracket : Deters the tampering or theft of an operator.
• Collision sensing/over current: When the gate is moving and it strikes an object, the software will sense the obstruction due to the higher current draw, this will prompt the operator to stop. If the over current is detected while the gate is closing, then the gate will stop and reopen at slow speed. If the over current is detected while the gate is opening, the gate will stop and remain still.
The gate will close on the next trigger that it receives or after the auto-close time has expired. It should be noted that D.A.C.E. recommends the use of DuraOptics safety beams on all installations to minimise the chance of the gate closing while there is an object in its path.
5
GENERAL INFORMATION cont.
• End stop: a physical stopper preventing the gate from running off the end of the rail and causing injury or damage.
• Intercom: equipment that allows communication between the gate and the house.
• LCD Screen: indicates information regarding the operator status.
• Manual override: allows the gate to be moved manually.
• Party-mode: allows the gate to remain open even when auto-close is selected.
• Positive close: This means that the gate will close up against the end stop / gate post leaving no gap between the gate and the stop. This ensures that any potential electrical contacts of an electric fence make a solid connection when the gate is closed.
GENERAL SITE LAYOUT
2
7
1
9
3
4
11
5
6
11
10
8
1.
End stop - minimum 70mm high
2.
Anti-lift device / rollers
3.
Rail
4.
Gate operator.
5.
Magnet
6.
Rack
7.
Goose neck with intercom gate station
8.
Catch bracket
9.
DuraOptics Infrared Safety Beams
10. 80mm wheels.
11. Conduit carrying electrical cables ( max. 16volts only)
12. Pillar courtesy lights
6
12
B.
OPERATOR LAYOUT
C.
H.
A.
B.
C.
D.
E.
F.
G.
H.
12V 7AH Battery
LCD Screen
Main PC Board
12V DC Electric Motor
Manual override access door with lock
Override access key
Transformer
Cable risers
A.
C.
A. Conduit entry holes.
B. 4 Holes for bolting the plate to the concrete plinth.
C. Jacking bolts to secure the operator to the plate and for height adjustment.
B.
SOLO/
SPRINT
FOUNDATION
PLATE
7
SITE INFORMATION
The site should be evaluated before the installation begins. The following items should be checked.
•
•
The operator should be installed above flood level to avoid any water damage to the operator.
To avoid the operator from malfunctioning the rail should be level and above ground level.
This will help to keep debris out of the path of the wheels. Any debris lying on the rail may cause the gate to jam or the PC Board to blow a fuse.
• The gate must not move on its own when left in any position along the rail, if this does occur, the rail must be leveled before the gate is automated.
• Keep all trees, branches, bushes and other growth clear of the gate. Failure to do this may lead to the gate jamming.
It is extremely important to evaluate the gate that is to be automated before any automation is done.
The following points must be checked. All of the points mentioned below are common causes of gate problems if not checked.
Ensure that the end stops are secure.
Min. height 70mm.
Recommended 80mm dia. wheels.
It is recommended that 16mm round bar is used to assist with the smooth operation of the gate.
8
Rollers must roll freely.
The roller mounting bracket can be used as an anti-lift device. The catch bracket must be used as an anti-lift device.
The gate must not jam in the catch bracket when opening or closing as this may cause the operator to over current or the fuse to blow.
All precautions must be taken to ensure that the gate cannot run free of the rollers. A device can be fabricated and fitted to prevent this
MAX. GATE MASS, START UP FORCE & RUNNING FORCE
It is important to check the start up force of the gate before the operator is installed. Place the gate in the fully closed position. Using a fishing scale, pull the gate open and check the kilogram force required to start the gate rolling. This is the start-up force.
At no stage while moving the gate must the reading exceed the force shown in the table below.
The D.A.C.E warranty will be void if the gate mass, start up force or running force exceeds the specifications as per the table below
OPERATOR
SOLO 500
MAX. GATE MASS
500kg
MAX. START UP
FORCE
18kgF
MAX. RUNNING
FORCE
12kgF
9
STEP 1
Open the access door
REMOVING THE LID
SOLO/CONDO
OPERATORS
STEP 2
Pull out the pin (the pin will move about 5 mm).
The lid can now be removed
PLACING THE OPERATOR IN MANUAL OVERRIDE
Step 1: Unlock and open the access door (as in step 1 above).
Step 2: To prevent the gate from knocking the end stoppers after reactivating the gate later, be sure to take note of the current position of the gate before proceeding to step 3.
Step 3: Turn the thumbwheel clockwise until the gate is free to move.
Thumbwheel
Step 4: Before putting the gate back into operational mode, place the gate back in the position it was in step 2.
Step 5: Turn the thumbwheel anti-clockwise to re-engage the operator. Move the gate until you hear a click.
Step 6: The gate must always be operated at least three times after it has been placed back into operational mode. This is called Calibration Mode as it recalibrates the gates end stoppers.
10
PC BOARD LAYOUT
•
•
•
•
•
•
The PC Board is a sensitive piece of electronic equipment and should be handled with care.
• Never connect or remove wires on a PC Board while there is power on the board as this may lead to damage.
Never touch the board with any metal object.
Never allow the board to get water on it as this may lead to short circuiting and corrosion and will lead to the board malfunctioning.
No insecticide or other sprays should be used on a PC Board.
Do not attempt to repair the PC Board. Any repairs must be carried out by an authorized agent.
Do not apply 230volts to the board (16 VAC and 12 VDC only).
Never reverse the polarity of the battery wires as this will lead to extensive damage.
Pluggable
Charger
Battery wires
(red & black)
Motor wire connectors Earth wire
16 VAC connector from transformer
Dipswitches
20 amp motor fuses
Open / close
LED
Auxiliary connectors
Test button
Remote learn
Current sensing pots
Rev Counter
Marker
Light/lock
The charger circuit on the PC Board has a rectifier which converts AC voltage to DC voltage, this will generate some heat on the rectifier heat sink. Care should be taken that no wires touch the heat sink as this may cause the plastic insulation of the wire to melt and may lead to a short circuit.
11
ELECTRICAL WIRING (SOLO &
SPRINT
OPERATORS ONLY)
• Ensure that ALL power is switched off or isolated before any connections are made.
• The transformer must be plugged into a normal plug socket in the house. 16 VAC is then run directly to the PC board 16V AC connection
• Do not open or tamper with the transformer as this may cause electrical shock (this will also void any warranty).
• The Earth wire on the PC Board must be connected from the E on the transformer. Alternatively the
Earth wire must be connected to an earth spike buried in the ground.
• The cable should be run in a 500mm deep trench in a water proof conduit and must be terminated inside the operator.
• The conduit should have no sharp bends in it as this may cause problems in the future if the cable needs to be pulled out and replaced.
• There must be no joins in the cable underground.
• The cable should be a three core 1.5mm cable.
• Do not use Communication cable as this will void any warranty and is illegal.
• Do not run 230V in the same conduit a 16 VAC.
SOLO &
SPRINT operator
Transformer will be damaged if not wired correctly.
Transformer
Recommended distance = 50
500
Main PC Board
EARTH
16 VAC
12
ANCHORING THE OPERATOR
It is very important that the operator is mounted on a firm foundation that can not move or become loose over time. The foundation should be constructed from concrete. The size of the plinth should be about 300 by 300 mm square and about 200mm deep. The foundation plate supplied with the operator must be securely mounted to the concrete using coach screws and plugs. The foundation plate can also be welded to the gate rail if need be. The concrete should be allowed sufficient time to set before the operator is mounted onto the plate.
GATE CLOSING TO THE RIGHT GATE CLOSING TO THE LEFT
1
Place concrete plinth here
2
Place concrete plinth here
3
Dig a hole about 300mm
Foundation plate
Place the conduit in the correct position before filling the hole with concrete. Flexible conduit may also be used.
4
Use 8mm coach screws to mount the foundation plate to the concrete
Allow concrete to set and then place the foundation plate onto the concrete plinth
Top view
Trim the conduit and the cable to the correct length before placing the operator onto the foundation plate.
Gate
SOLO/
SPRINT
Foundation Plate NOTE: measurement is dependant on the type of rack used.
Always pre-measure the rack before fixing the foundation plate.
25mm
14
SECURING THE OPERATOR TO THE FOUNDATION PLATE
When anchoring the operator, it is important to ensure that the following points are checked:
• The electrical cable is in place.
• The concrete is fully set.
• The operator foundation mountings are secure and can not move or become loose.
• The operator should be set level and parallel to the gate.
• The operator must be set above the flood level or if this is not possible, a flood proof wall should be constructed around the operator.
Anti-lift device and rollers
TOP VIEW
PC
SIDE VIEW
Jack-up nuts for adjusting the operator height.
Conduit
After placing the operator onto the three jack-up bolts, place the three clamping nuts and washers over the bolts to clamp the operator in place.
Concrete plinth
8mm coach screws in plugs
MOUNTING THE MAGNET
Gate in CLOSED position!
700 mm
Magnet
Measure 700mm from the centre of the pinion gear towards the closed end of the gate. If it is not possible to mount the magnet at 700mm, this distance may be increased slightly. DO NOT invert the magnet . If the magnet is moved for any reason after the operator has been programmed, then the motor will have to be re-programmed.
Maximum gap between the magnet and the motor cover of 3 mm.
Place washers here if gap is not correct.
The gap between the operator cover and the magnet, when the magnet passes the motor, must not exceed 3mm . To check this, manually move the gate until the magnet is directly over the pinion gear then measure between the magnet and the motor lid. If the gap is more than
3mm, place washers behind the magnet until the correct gap is achieved
15
MOUNTING THE RACK
The rack is attached to the gate by means of self drilling TEK screws. These TEK screws have a built in drill bit at the tip of the screw. The rack meshes with the pinion gear on the operator which then drives the gate.
It is very important that the rack is mounted securely and that the rack meshes with the pinion gear for the full length of the gate . Any section of rack that meshes to too tight or too loose will cause problems with the operation of the gate.
Step 1 : ensure that the operator is at least 7 mm above the ground level and that the gate is in the closed position. Fig A
Step 2 : place a piece of the rack on the pinion of the operator, ensuring that the teeth of the rack and the pinion mesh correctly.
Step 3 : now fasten the rack to the gate using the TEK screws. The TEK screw should be placed in the centre of the slot in the rack so as to allow for adjustment later. FIG B
Step 4 : push the gate towards the open position continuing to secure the rack to the full length of the gate. Ensure that the rack is securely meshed with the pinion at all times during this operation.
Repeat step 4 until the full length of rack is attached to the gate.
Step 5 : using the jack-up bolts under the operator, drop the operator 2mm , this allows a slight gap between the teeth of the rack and the pinion so as to prevent any binding or tight spots on the rack.
FIG C
Step 6 : push the gate all the way open and closed to check that the rack is meshing with the pinion for the complete length of the gate.
Check that the rack is not touching the operator while running and also check that the rack covers at least three quarters of the pinion at all times when viewed from above.
A B
Place TEK screw here
Start with 7 mm space
IT IS RECOMMENDED THAT THE RACK
IS MOUNTED AS SHOWN AND NOT
INVERTED , AS THIS MAY CAUSE
OBSTRUCTION SENSING PROBLEMS.
C
Place the TEK screws as shown below for the complete length of rack.
Drop operator height by
2 mm when rack is secured to gate.
16
FILLING THE GEARBOX OIL
VERY IMPORTANT: GEARBOX MUST BE FILLED WITH THE SUPPLIED OIL BEFORE
COMMISSIONING THE OPERATOR.
Fill the gearbox as shown bellow. The entire bottle (70ml) needs to be emptied into the gearbox.
The gearbox oil level needs to be topped up periodically. Remove the oil level screw and add oil until the oil just starts to run out of the hole.
REPLACE THE SCREW!!!
Oil level screw
Use S.A.E.75W/90 oil to refill the gearbox
SETTING THE MOTOR DIRECTION
When programming the operator the gate must always move to the closed position first. If the operator opens first, reverse the motor direction by swopping the motors wires as per below and then reprogram the operator.
PROGRAMMING THE OPERATOR
4.
5.
6.
7.
To program the operator follow the steps below.
1.
Remove all power from the main PC Board.
2.
3.
Manually open the gate 1m -1.5m (this will be the pedestrian opening distance).
Engage the gearbox.
Switch dipswitch 1 on.
Apply battery power only. The Open, Close and Status LEDs will flash rapidly.
Press “TEST” button.
The gate MUST drive to the CLOSED end stopper and then drive to the OPEN end stopper
(the LEDs will remain flashing).
17
PROGRAMMING THE OPERATOR cont.
•
•
•
8.
Switch dipswitch 1 off.
Programming is now complete.
In step 5, the gate must close first. If the gate opens first, then the motor wires must be reversed. This will change the operator direction. (See Setting the motor direction)
Do not connect any other auxiliary wires to the PC Board until the operator is fully programmed.
Do not allow the infrared beams to be interrupted during the programming procedure.
Before pressing the Test Button in step 6, ensure the gate is clear of any obstacles.
Remove all power before connecting auxiliary equipment.
DIGITAL BUSINESS CARD (D.B.C)
The Digital Business Card (D.B.C) enables the installer to load his company details onto the operator
LCD. These details will constantly display on the LCD so that the installer can be called when technical assistance is required or a service is due.
For the installer to load his company details the following steps must be followed:
Step 1: Acquire a D.B.C.
Step 2: Installer details to be loaded onto D.B.C by dealer, merchant or agent of D.A.C.E products.
Step 3: Keep D.B.C at all times for future installations.
Step 4: When installation is complete remove all power from the operator (this includes mains power).
Step 5: Insert D.B.C on pins labelled DIGITAL B/CARD.
Step 6: Apply power to main PC Board.
Step 7: Remove D.B.C.
Step 5: Insert
D.B.C into pins labelled DIGITAL
B/CARD
LCD SCREEN
The LCD is an easy to use screen that gives the owner / installer information regarding programming and operator status. Whenever the operator is programmed or a fault occurs, refer to the screen for diagnostic assistance. In certain cases the screen will give a message that reads “Call Technician’ this means that the operator needs to be checked by an installer. The messages on the screen are generally self explanatory. However the following table gives a description of the messages and their meaning.
Continued on pg. 19
18
LCD SCREEN cont.
Some of the messages below have been shortened to show the main message. Certain messages will also show the action needed.
LCD Screen
MAINS FAIL
MESSAGE
LOW BATTERY
MEANING / ACTION
THIS MESSAGE WILL SHOW AFTER INITIAL START UP, IF
THE LOW BATTERY MESSAGE REMAINS AFTER THE
OPERATOR IS TRIGGERED,CHECK BATTERY VOLTAGE /
CHECK CHARGER VOLTAGE
CHECK THE MAINS POWER / CHECK TRANSFORMER /
CHECK CHARGER.
THE GATE IS IN THE CLOSED POSITION. GATE CLOSED
GATE OPEN THE GATE IS IN THE OPEN POSITION.
OBSTRUCTION
NO REV PULSES
THE GATE HAS SENSED AN OBSTRUCTION. CHECK THE
WHEELS / ROLLERS/ RACK/ BRACKETS/ FUSES/ FORCE
SETTING POTS.
FAULTY REV COUNTER, PC BOARD MOUNTING MAY BE
LOOSE, REV COUNTER MAGNET HOLDER IS BROKEN.
THE GATE IS SET TO AUTO CLOSE. AUTO-CLOSE ACTIVE
PARTY MODE THE GATE IS IN AUTO-CLOSE OVERRIDE .
PROGRAM MODE
BEAMS BLOCKED
THE GATE IS IN PROGRAM MODE.
THE INFRARED SAFETY BEAMS ARE BLOCKED /
FAULTY/ THE BEAMS DIPSWITCH IS OFF.
PROGRAMMING CLOSE POSTION THE GATE IS CLOSING WHILE PROGRAMMING.
BEAMS AC MODE THE BEAMS AUTO CLOSE MODE IS ACTIVE
PROGRAMMING OPEN POSITION THE GATE IS OPENING WHILE PROGRAMMING.
PROGRAMMING COMPLETE PUT
SWITCH 1 OFF
THE PROGRAM IS COMPLETE.
MARKER OK
SERVICE DUE
INDICATES WHEN THE MAGNET ON THE GATE IS
SENSED BY THE MARKER.
THE OPERATOR REQUIRES A SERVICE.
19
LED INDICATIONS ON MAIN PC BOARD
STATUS LED .
ON:
OFF : gate open or in motion. mains power off
FLASHING: this LED will flash once every 2 seconds when the gate is closed and the mains power is on.
OPEN LED
ON: gate open.
CLOSED LED
ON:
12V LED
ON:
OFF: gate closed.
12V output fuse ok.
12V output fault.
INF LED
ON:
OFF: infrared beams circuit is ok. beams obstructed or faulty
TRIG LED
This LED should be off at all times and will flash when receiving a trigger.
ON:
OFF: permanent on indicates trigger fault normal
PED LED
This LED should be off at all times and will flash when receiving a pedestrian trigger.
ON:
OFF: permanent on indicates pedestrian trigger fault normal
LOOP LED
ON:
OFF:
REV vehicle parked on ground loop normal
This LED will flash when receiving a pulse from the rev counter when gate is in motion. If the LED does not flash when in motion this will indicate a faulty rev counter.
LOW BATT
This LED will flash indicating a low battery.
LED LAYOUT
CHARGE
TRIG
PED
LOOP
INF
LED/STAT
12/24V
OPEN
CLOSED
REV
LOW BATT
20
SETTING PARTY MODE (AUTO-CLOSE OVERRIDE)
This function is normally used when the gate is required to stay open but Auto-close function is active.
• To set the party mode, push and hold the gate’s trigger button until the gate starts to open.
Release the trigger. The gate will now stay open until it is reset into normal operating mode.
• To reset the gate into normal operating mode, push the gate’s trigger button twice within three seconds. The gate will now operate as normal.
SETTING OVERCURRENT SENSITIVITY
The PC Board is designed to detect overcurrents. This means that if the gate hits an object or is obstructed it will see an increase in the electrical current and the gates will stop driving.
The results of the detected overcurrent will be different depending on what the gate is doing at the time of the overcurrent.
• If the gate is closing and an overcurrent is detected the gate will stop and then re-open.
• If the gate is opening and an overcurrent is detected, the gate will stop and will not move until it receives another trigger; the auto-close time is reached or the obstruction has been removed.
Setting the overcurrent sensitivity:
The sensitivity can be adjusted dependent on gate’s requirements. It must be noted that if the sensitivity is set too low, the gate will drive harder when an obstruction is encountered increasing the risk of injury or damage to a vehicle/object. Before adjusting the sensitivity check that the gate is operating correctly i.e. dirt, branches or garden growth hindering operation etc.
There are two pots found on the PC Board. One pot is to set the open sensitivity and the other is to set the close sensitivity.
• To decrease sensitivity (usually because a heavier gate is being automated or due to wear and tear over time) use a small flathead screwdriver and turn the pot clockwise. The adjustment should be done in very small increments, until the desired sensitivity is achieved. Use extreme caution when setting the pots as this can cause severe injury or damage if the sensitivity is set too low.
• To increase sensitivity (usually because a very light gate is being automated) turn the pot anticlockwise. Take care not to set the pot too sensitive as this may cause the gate to overcurrent too easily due to other external forces such as wind, small pebbles, leaves, sand etc.
CLOSED
POT
OPEN
POT
Flathead Screwdriver
21
CONNECTING AN EXTERNAL STATUS LED
An external status LED can be connected to the main PC Board. This LED will indicate the status of the gate. The LED can be fitted to the intercom or any other convenient place.
CONNECTOR BLOCK ON MAIN PC BOARD
5mm leaded
LED
GND TRIG PED LOOP INF LED/
STAT
12/
24V
WIRING INFRARED SAFETY BEAMS (DuraOptics)
Covers must be in place when beams are active. Ensure that the correct cover is placed onto each beam after setup otherwise failure to do so may result in faulty operation of the beams.
Ensure that number 2 dipswitch is set
“ OFF ” after connecting the beams.
GND TRIG PED LOOP INF
LED/
STAT
12/
24V
Main PC Board
Note: although the installation of infrared safety beams does reduce the risk of the gate striking an object while closing it does not guarantee against it.
22
CONNECTING AN EXTERNAL RECEIVER
When connecting any auxiliary equipment to the PC Board ensure that all power is removed from the PC Board.
A DuraTronic external receiver can be connected to the PC Board. This will be necessary if there are more than 15 remotes to be used or if the range of the on-board receiver is not sufficient.
The DuraTronic external receiver can hold 128 remotes. The DuraTronic receiver should be mounted outside the operator housing for increased range.
CONNECTOR BLOCKS ON MAIN PC BOARD
GND TRIG PED LOOP INF LED/
STAT
12/
24V
CONNECTOR BLOCKS ON
EXTERNAL RECEIVER
12/
24
NEG COM N/C N/O
To program remotes to the receiver:
1.
2.
Press and hold the button on the remote.
Place the jumper over the two TX LEARN pins for 1 second.
3.
4.
Remove the jumper.
Release the button on the remote.
Repeat the above steps for each remote to be programmed.
PEDESTRIAN OPERATION: A separate receiver, keyswitch or keypad must be connected to operate the gate in the pedestrian mode. The connection is done in the same manner as the diagram above with the exception of the TRIG connection. Instead of TRIG to N/O it must be PED on the main PC
Board to N/O.
In pedestrian mode the gate will open partially and then close automatically after 6 seconds.
23
CONNECTING A VEHICLE DETECTOR
A vehicle detection loop is used to automatically open the gates when a vehicle approaches (most commonly in the exit direction). The following instructions are for a DuraLoop Vehicle Detector. Note that whatever product is used it is important to follow the manufacturers installation instructions as these may differ from one product to another.
It is extremely important that the loop is placed in the driveway far enough from the gate so that the vehicle does not collide with the gate
Connector block on main PC Board
GND TRIG PED LOOP INF LED/
STAT
12/
24V
PLEASE NOTE: LOOP input is used for slide operators ONLY!!
Dipswitches
●
Twisted feeder cable to driveway
24
CONNECTING A SOLAR PANEL
A REGULATOR IS NOT
REQUIRED WHEN
CONNECTING A SOLAR
PANEL
SOLAR PANEL
(min 20 Watts)
Negative wire
(-)
Positive wire
(+)
An external regulator is NOT required when connecting a solar panel. Ensure that the panel does NOT exceed the min and max specifications.
Solar Panel Specifications:
• Min output voltage 16.5 VDC
• Max output voltage 21 VDC
(an output voltage below 16.5 VDC will not charge the internal battery).
Connect the solar panel wires to the 16 VAC plug on the main PC Board.
(Wire polarity is not important)
16 VAC connector from transformer
25
DIPSWITCH SETTINGS
PROGRAM MODE
Refer to page 17 & 18 for program sequence.
No. 1: USED DURING PROGRAMMING SEQUENCE.
INFRARED SAFETY BEAMS
Number 2 dipswitch is used to activate the safety beams. If no safety beams are used, number 2 dipswitch must be in the ON position. If safety beams are connected, number 2 dipswitch must be set to the OFF position. NOTE if number 2 dipswitch is OFF and there are no beams connected, the gate will not close.
No.2: ON IF NO BEAMS
BEAMS AUTO-CLOSE
B.A.C. is not active with swing operators.
No. 4: ON TO ACTIVATE BEAMS AUTO-CLOSE.
AUTO-CLOSE
Auto-close is an option that allows the gate to close automatically after a chosen time delay, this delay can be from 10 to 70 seconds. Auto-close is selected by using the dipswitches on the main PC Board.
Dipswitch numbers 6,7 and 8 are the auto-close time select switches. The times are as follows.
6 off ; 7 off; 8 off = no auto-close
6 on; 7 off; 8 off = 10 seconds
6 off; 7 on; 8 off = 20 seconds
6 off; 7 off; 8 on = 40 seconds
6 on; 7 on; 8 on = 70 seconds
Any combination can be used to select the desired auto-close time.
It is strongly recommended that DuraOptics safety beams are used when Auto-Close is selected as this reduces the chance of the gate closing on an object and causing injury or damage.
No’s 6; 7 & 8: SETTING AUTO-CLOSE
26
MULTI-USER MODE
To set multi-user mode, place number 5 dipswitch in the ON position.
NOTE !!! If Multi-user is selected, an auto-close time must also be selected. If an auto-close time is not selected, the gate will immediately close after opening.
No.5: ON FOR MULTI-USER
PROGRAMMING THE REMOTES
To program remotes to the on-board receiver complete the following steps. It is recommended that the remotes are numbered in order of programming. This will assist with erasing any lost or stolen remote at a later stage.
Step 1: press and hold the button that is to trigger this application on the remote. It is important that this button is continuously held from step 1 through to 3.
Step 2: place the jumper over the two pins on the PC Board called TX- L for 2 seconds.
Step 3: remove the jumper from the two pins.
Step 4: release the button on the remote.
That particular button on the remote is now programmed to the receiver.
1 4
2 3
ERASING ALL REMOTES PROGRAMMED TO THE RECEIVER
Step1: place the jumper over the two pins called TX-E and count 4 flashes on the yellow LED on the receiver.
Step2: remove the jumper.
Step 3: replace the jumper and count 2 flashes on the LED.
Step 4: remove the jumper.
Step 5: replace the jumper and count 4 flashes on the LED
The LED will now flash rapidly for one second to indicate that all remotes have successfully been erased.
NOTE: The time between the jumper being removed and replaced on the pins must NOT exceed 2 seconds.
ERASING A SINGLE REMOTE PROGRAMMED TO THE RECEIVER
If the remotes are not numbered all remotes will need to be erased and reprogrammed once again. If all remotes are numbered it is possible to erase a single remote. The preceding remote is needed to erase the required remote. For example remote number 6 will erase remote number 7 etc.
Step 1: place the jumper over the TX-E pins.
Step 2: press the button of the preceding remote.
Step 3: remove the jumper.
The remote will now be erased. The next remote to be programmed will take the place of the erased remote. In this example it will take the place of number 7 and must be numbered as such.
27
TECHNICAL SPECIFICATIONS
SOLO
/SPRINT
Application:
Single Dwelling
Only
Town House
Maximum number of openings for a 4m gate: (7Ah battery)
Pull force 7.2kgF 95
Pull force 9.1kgF
Pull force 13.5kgF
70 n/a
Maximum Gate Mass:
Max. Start up force:
Max. Running force:
Maximum Gate Size:
Collision Sensing:
Duty Cycle:
Electric Voltage:
Motor Power:
Supply Voltage at Gate:
500kg
18kgF
12kgF
100m
Electronic
50%
12 Volt
120 watts
16V AC
On board receiver:
Packaged operator weight (excl. rack & battery):
Yes
9.1kg
Packaged operator dimensions (excl. rack & battery):
32(L) x 24(W) x 36
(H) cm
24 MONTH WARRANTY
D.A.C.E. offers a Factory Warranty on this equipment. The following terms and conditions apply to all warranty claims.
• D.A.C.E. warrants the original purchaser, at the point of sale, that the product is in good working order and is free from any defect.
• Any warranty claim must be accompanied by the original invoice.
• The original purchaser is responsible for checking that the equipment is free from any visible defect before it leaves the point of sale.
• The warranty period is 24 months from date of purchase.
• The warranty is a “walk in “ warranty. No warranty claim will be entered into “on site” .
Continued on pg. 29
28
24 MONTH WARRANTY cont.
• The equipment must be returned to the factory with the original invoice for any repair or replacement.
• The transport cost is for the end users account.
• If the equipment was purchased at a dealer, merchant or agent of D.A.C.E. the claim must be directed to said merchant, dealer etc.
• The warranty will become void if any of the following apply in any way:
1. Incorrect installation of the equipment.
2. Any physical conditions exceed the D.A.C.E specifications.
3. Incorrect wiring of the equipment.
4. Any circumstances out of the control of D.A.C.E such as lightning, flooding, power-surges, fire, corrosion & insect infestation.
∼
NOTE: the transformer is not guaranteed due to power fluctuations.
∼
Any warranty claim must be inspected and tested by a D.A.C.E. representative before any further claim is entered into.
29
DACE, being the innovators they are, have come up with a World First, the
Digital business card
Gone are the days when you gave your client your business card and knew they would either lose it or throw it away. Come they day when your services were urgently required or they wished to refer you to friends, they couldn’t remember your company details and were forced to refer to the yellow pages or the internet. Now the job that was rightfully yours has been given to someone else.
That was then! Now you simply get your details loaded onto your Digital Business Card by your supplier.
Having completed an installation of a COMPACT
300/500; SOLO; CONDO; CONDO AC/DC or any of the
LAZER Garage Door Operators, plug your Digital
Business Card into the PC Board and, VOILÄ, in 5 seconds your details are stored safely on the operator’s
LCD screen, always promoting your company and ensuring repeat business.
Your supplier will download your details onto the Digital
Business Card via their computer using DACE software.
DON’T LOSE YOUR DIGITAL BUSINESS CARD!
Keep it with you at all times and after each installation of a DACE product (excluding DuraSwing), simply load your details onto the PC Board and let it keep working for your. Never fear, should your details change, merely take your Digital Business Card to your supplier and get your new details loaded over your old ones. A smart and affordable alternative to your old printed business card. www.dace.co.za ● [email protected]
31
32
advertisement
Related manuals
advertisement