- Home
- Do-It-Yourself tools
- Power tools
- Paint Sprayer
- Graco
- 3A6948D, ProControl™ 1KE Plus Models for Management of Fluid and Air
- Instructions
Graco 3A6948D, ProControl™ 1KE Plus Models for Management of Fluid and Air Instructions
Add to my manuals106 Pages
advertisement
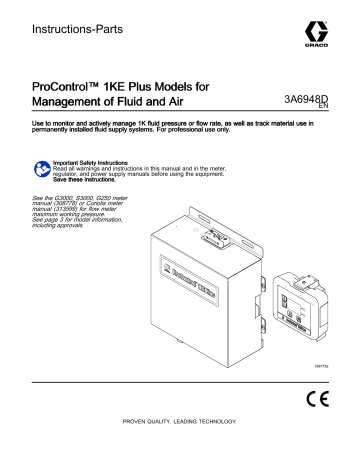
Instructions-Parts
Use permanently
Important
Read all warnings and instructions in this manual and in the meter, regulator, and power supply manuals before using the equipment.
Save
See the G3000, S3000, G250 meter manual (308778) or Coriolis meter manual (313599) for flow meter maximum working pressure.
See page 3 for model information, including approvals.
3A6948D
EN
PROVEN QUALITY. LEADING TECHNOLOGY.
Related Manuals .................................................. 3
ProControl 1KE Plus Models ................................. 4
ProControl 1KE Plus ADCM............................ 4
ProControl 1KE Plus Pressure Ratings............ 5
ProControl 1KE Plus Model Selection
Matrix .............................................. 6
ProControl 1KE Plus Selection Guide.............. 7
Power Supply Selection Guide ........................ 8
Component Entity Parameters ...................... 10
Drawing ......................................... 12
Warnings ........................................................... 13
Overview............................................................ 17
Components ................................................ 18
Installation.......................................................... 20
Non-Hazardous Locations ............................ 20
Hazardous Locations.................................... 21
Grounding ................................................... 24
Cable Connections to the Advanced Display
Control Module (ADCM) .................. 24
Air Connections ........................................... 25
Fluid Connections ........................................ 26
Communication Options ............................... 27
Operation ........................................................... 29
Pressure Relief Procedure............................ 29
Fluid Regulator Operation............................. 29
Flow Meter Operation................................... 29
ADCM Module .................................................... 30
Display Information ...................................... 30
Operation Modes ......................................... 30
Screen Navigation and Editing ...................... 30
Icons ........................................................... 31
Control Method Considerations............................ 33
Run Screens ...................................................... 35
Screen 1: Run Operations ............................ 35
Screen 2: Job Log Totalizer.......................... 40
Screen 3: Job Log History ............................ 41
Screen 4: Event Log History ......................... 42
Password Screen ............................................... 43
Setup Screens.................................................... 44
Setup Screen 1: Job Target.......................... 44
Totalizer......................................... 45
Setup Screen 3: Grand Totals ...................... 46
Setup Screen 4: Calibration.......................... 46
Setup Screen 5: Flow Rate........................... 47
Setup Screen 6: Pressure Transducer ........... 48
Setup Screen 7: Pressure ............................ 49
Setup Screen 8: Operator Input Limits ........... 50
Setup Screen 9: Additional Operator Input
Limits and Timeouts........................ 51
Setup Screen 10: PID Data .......................... 52
Setup Screen 11: Fill Mode .......................... 52
Setup Screen 12: Flush Mode ...................... 53
Setup Screen 13: Control Method ................. 54
Setup Screen 14: Modbus ............................ 55
Setup Screen 15: Date and Time .................. 55
Setup Screen 16: Password ......................... 56
Setup Screen 17: Internal Pressure Control
Variables........................................ 57
Setup Screen 18: Internal Flow Control
Variables........................................ 59
Setup Screen 19: Internal Set Point and
Flowmeter Information .................... 61
Setup Screen 20: Modbus status .................. 62
Calibrate the Meter ............................................. 63
Set the Modbus Address ..................................... 63
Deviations and Advisories ................................... 64
Update the Software ........................................... 66
Troubleshooting.................................................. 67
Battery Replacement Procedure ................... 72
Parts.................................................................. 73
Accessories........................................................ 89
Electrical Schematic ........................................... 91
Mounting Dimensions ......................................... 92
Appendix A - Modbus Variable Map ..................... 93
Device Identification Registers ...................... 93
Command Registers .................................... 94
Run Registers.............................................. 95
Run Setpoint Registers................................. 96
Setup Registers ........................................... 97
Appendix B - Upgrading ProControl 1KE to
ProControl 1KE Plus............................ 101
Upgrading a ProControl 1KE to ProControl
1KE Plus...................................... 101
Installing the 25B323 Air Control Upgrade
Kit................................................ 101
Technical Specifications.................................... 103
California Proposition 65 ................................... 105
Graco Standard Warranty.................................. 106
2 3A6948D
3A0427
3A1244
3A7521
308778
313599
332013
332196
332356
Low Flow Fluid Regulator, Instructions-Parts Manual
Graco Control Architecture Module Programming, Instructions Manual
I.S. Light Tower, Genuine Graco Parts and Accessories Manual
Volumetric Fluid Flow Meter, Instructions-Parts Manual
Coriolis Meter Kits, Instructions-Parts Manual
DCM and ADCM, Instructions Manual
IS Power Supply Modules, Instructions-Parts Manual
Communications Kits, Instructions-Parts Manual
3A6948D 3
All Advanced Display Control Modules (ADCM) are base hardware model number 24L097 (Ref. 1) without application software. Model 24L097 is not available for separate sale.* See approval information in Manual
332013 and on this page. The small label (Ref. 2) on the back of the module shows the ProControl 1KE
Plus model number.
Model No.
Series
B Advanced Display Control Module (ADCM), with no software loaded. See Manual
332013.
9902471
Class I, Div.
1,
Group D T3
Ex ia [ia]
Ta=0°C to 50°C
Intrinsically Safe Apparatus
Part of Intrinsically Safe System.
For use in Class I, Division 1, Group D T3 Hazardous Locations
*** See the
, for replacement ADCM with software.
4 3A6948D
N/A
N/A
100
100
100
100
100
100
N/A
N/A
0.689
0.689
0.689
0.689
0.689
0.689
N/A
N/A
6.89
6.89
6.89
6.89
6.89
6.89
N/A
4000
300
4000
300
N/A
N/A
100
N/A
27.58
2.07
27.58
2.07
N/A
N/A
0.689
N/A
275.8
20.7
275.8
20.7
N/A
N/A
6.89
3A6948D 5
The numbered columns in the following table correspond to the numbered steps in
ProControl 1KE Plus Selection Guide, page 7
.
Power supply modules are discussed in
Power Supply Selection Guide, page 8
.
ADCM w/software and bracket only
Flow Monitor (ADCM w/G3000 and 5 ft
(1.5 m) cable, no fluid panel)
Flow Monitor with open setpoint fluid pressure control
(includes fluid panel and I/P to operate fluid pressure regulator)
Gun Atomizing Air
Control
Closed Loop Fluid
Pressure Control
N/A
✔
✔
✔
—
—
N/A
N/A
Closed Loop Fluid
Pressure or Fluid
Flow Control
Closed Loop Fluid
Pressure/Flow + Gun
Atomizing Air Control
N/A
N/A
N/A
✔
✔
—
—
✔
✔
—
—
✔ = Included
— = Not included. However, the system will accommodate a user-supplied component.
*** A Graco G3000 high-pressure meter (289813) is used in models sold with a fluid flow meter. If you intend to supply your own fluid flow meter, order a model without a checkmark below. Make sure the fluid flow meter is appropriate for fluid compatibility, viscosity, flow rate range, etc.
✔
—
✔
—
N/A
✔
—
✔
—
✔
—
✔
—
✔
—
N/A
N/A
N/A
✔
✔
✔
✔
✔
✔
✔
✔
✔
✔
1
1
1
1
1
1
1
2
2
2
2
1
1
1
1
25B285
25B286
25B287
25B288
25B289
25B290
25B291
25B292
25B293
25B294
25B295
25B296
25B297
25B298
25B299 regulator, order a model without a checkmark below.
Make sure the fluid regulator is appropriate for fluid pressure range, material compatibility, viscosity, flow regulator outlet must be a minimum of 10 psi (0.7
bar).)
N/A
N/A
N/A
N/A transducer come with a low-pressure 100 psi (6.9
bar) transducer.
N/A
N/A
25B283
25B284
(24C375) is used in models sold with a fluid regulator.
If you intend to supply your own air-operated fluid number below indicates the quantity included.
6 3A6948D
(Numbered steps 1–4 correspond to the numbered columns in the
ProControl 1KE Plus Model Selection Matrix, page 6
.)
1.
Choose level of application control needed.
2.
Determine flow meter, if applicable for level of control chosen. (Gun Atomizing Air Control and
Closed Loop Fluid Pressure Control units do not use a flow meter.)
The G3000 meter is the standard recommended meter.
locations. See your flow meter manual for details.
3.
Determine fluid pressure regulator, if applicable for the level of control chosen. (The Gun
Atomizing Air Control unit, 25B289, does not use a fluid pressure regulator.)
The Graco 24C375 1:1 Low Flow Regulator is standard.
4.
Select base ProControl 1KE Plus model part
number from the ProControl 1KE Plus Model
.
Note
ProControl 1KE Plus units come with 5 ft.
(1.5 m) cable lengths to allow mounting the user control interface (ADCM) near the fluid panel. If a more remote mounting is required, purchase the appropriate extension cables, available in 50 ft. (16 m) lengths.
See
.
3A6948D 7
To determine the correct power supply module, answer these questions:
To prevent Fire and Explosion, when using a Pro
Control 1KE Plus system in a hazardous location, use a power supply with an IS barrier.
Power supply modules are ordered separately and depend on whether your ProControl 1KE Plus system is being used in a non-hazardous or hazardous location. Additional considerations for each location are discussed below.
Note
Power supply modules come with power cables to connect to port 3 of the ProControl
1KE Plus ADCM user interface.
Order power supply 16V680 (AC/DC Converter) and choose a power cord below.
Note
The 16V680 AC/DC Converter has an
IEC-320-C13 female input power connection and a 68 in. (1.7 m) output cord to connect to port 3 of the ProControl 1KE Plus ADCM user interface.
Will you be using ProControl 1KE
Plus models 25B296–25B299 for fluid and atomizing air control?
Would you potentially want to upgrade a ProControl 1KE Plus model in the future for use with fluid and atomizing air control?
Do you need to power more than one ProControl 1KE Plus unit, or want the ability to power up to three units from one power supply module in the future?
Will your application ever require greater than 50 psi (3.4 bar) of fluid pressure at the outlet of the
ProControl 1KE Plus for units with the standard Graco 24C375 1:1
Low Flow Regulator; or, for units using an alternate air-operated fluid regulator, will your application ever require greater than 50 psi (3.4 bar) of air pilot pressure to the fluid regulator?
• 245202 – 120 in. (3 m) North American 120 VAC power cord.
• 116281 – 72 in. (1.8 m) extension (Male x Female)
IEC-320 cord.
• 242001 – 8 in. (0.2 m) IEC-320 European-style power cord.
• 242005 – 8 in. (0.2 m) IEC-320 ANZ-style power cord.
If you answered “Yes” to any of these questions, order the 26C724 IS G-Barrier Power Supply Module.
Note
Up to three total ProControl 1KE Plus models of any configuration can be powered by a single G-Barrier. If you are adding a
ProControl 1KE Plus model to an existing
26C724 G-Barrier Power Supply Module, order a power cable kit 19Y499 (50 ft (16 m)) or 19Y502 (100 ft (32m)).
If you answered “No” to all of these questions, you may consider ordering the 16M167 Single IS Barrier
Power Supply Module.
Note
The 16M167 Single IS Barrier Power Supply
Module has power limitations. It cannot be used on ProControl 1KE Plus models that require greater than 50 psi (3.4 bar) of fluid pressure (50 psi (4.4 bar) of pilot air pressure for alternate air-operated fluid regulator use), or on units that control fluid and atomizing air.
8 3A6948D
ProControl 1KE Plus Model Selection Matrix, page 6
).
• For models 25B296–25B299, or models that may need to be upgraded to include atomizing air control and fluid pressure or flow control, the power consumption will require a Graco IS approved
G-Barrier power module (26C724). Systems that may operate above 50 psi (3.5 bar) require the
G-Barrier power module (26C724) to guarantee optimal performance.
• For models 25B284–25B295, these can be powered by a Graco G-Barrier power module
(26C724) or a single IS barrier output power module (16M167).
3A6948D 9
Ui = 17.9 V
Ii = 725 mA
Pi = 2.9 W
Ci = 2.3 μF
Li = 50 μH
Ui = 17.9 V
Ii = 725 mA
Pi = 2.9 W
Ci = 2.3 μF
Li = 50 μH
Ui = 30 V
Ii = 110 mA
Pi = 800 mW
Ci = 0.4 μF
Li = 10 μH
10
Ui = 30 V
Ii = 1000 mA
Pi = 3400 mW
Ci = 0 μF
Li = 0 μH
The following entity parameter values are taken from the ADCM control drawing for base model 24L097
(16M169) and from the IS Power Supply Module manual.
Uo = 15.75 V
Io = 723 mA
Po = 2.84 W
Co = 5.38 μF
Lo = 570 μH
Uo = 16.4 V
Io = 592.2 mA
Po = 2.82 W
Co = 2.4 μF
Lo = 64 μH
Uo = 17.9 V
Io = 100 mA
Po = 441 mW
Co = 4.8 μF
Lo = 20,000 μH
Uo = 17.9 V
Io = 217 mA
Po = 937 mW
Co = 4.8 μF
Lo = 5000 μH
3A6948D
Ui = 6 V
Ii = 61 mA
Pi = 90 mW
Ci = 5310 ρF
Li = 8.52 μH
Ui = 17.9 V
Ii = 73 mA
Pi = 1.25 W
Ci = 10,800 ρF
Li = 9.119 μH
Ui = 30 V
Ii = 125 mA
Pi = 700 mW
Ci = 10,800 ρF
Li = 9.119 μH
Uo = 5.88 V
Io = 61 mA
Po = 90 mW
Co = 700 μF
Lo = 50,000 μH
Uo = 17.9 V
Io = 124 mA
Po = 540 mW
Co = 2 μF
Lo = 15,000 μH
Uo = 17.9 V
Io = 124 mA
Po = 540 mW
Co = 2 μF
Lo = 15,000 μH
Ui = 17.9 V
Ii = 73 mA
Pi = 1.25 W
Ci = 1995.3 ρF
Li = 8.133 μH
Uo = 5.88 V
Io = 61 mA
Po = 90 mW
Co = 700 μF
Lo = 50,000 μH
*** Simple Apparatus in accordance with UL/EN/IEC 60079–11, clause 5.7.
3A6948D
11
NON-HAZARDOUS
LOCATION
Module pow e r s upply
Part number 16M167
OR
Module Pow e r s upply
G-Ba rrier
P a rt num be r 26C724
P ort 3
ADCM
Part number 25B2 83
HAZARDOUS LOCATION
Cla s s I, Div. 1, Group D, T3
Cla s s I, Zone 1, IIA, T3
II 2 G
Ex ia IIA T3 Ga
Fluid panel assem bly
Port 8
P re s s ure s witch
Sim ple Appartus
Part number 513937
I/P Tra ns ducer
P a rt num be r 16P784
P ort 10
P ort 4
S plitte r for optiona l light kit
Air Flow S witch
Sim ple Appartus
Part number 119159
Gra co Fluid Me te r
W/24W650 or
24W651 s e ns or
Indica tor light
P a rt numbe r 19A993
P ort 9
P ort 7
P re s s ure s witch
S imple Appa rtus
P a rt numbe r 513937
Fluid pre s s ure tra ns duce r
S imple Appa rtus
P a rt numbe r 16H282
I/P Tra ns duce r
P a rt numbe r 16P 784
Figure 1 Component Circuit Connector Drawing
3
8
9
4
7
10
16K509
16K615
18B244
16V381
16V071
16V071
16V381
50 ft (15.2 m)
100 ft (30.5 m)
50 ft (15.2 m)
50 ft (15.2 m)
50 ft (15.2 m)
50 ft (15.2 m)
50 ft (15.2 m)
12 3A6948D
The following warnings are for the setup, use, grounding, maintenance and repair of this equipment. The exclamation point symbol alerts you to a general warning and the hazard symbol refers to procedure-specific risks. When these symbols appear in the body of this manual or on warning labels, refer back to these
Warnings. Product-specific hazard symbols and warnings not covered in this section may appear throughout the body of this manual where applicable.
3A6948D or solvent flowing through the equipment can cause static sparking. To help prevent fire and explosion:
• Use equipment only in well ventilated area.
• Eliminate all ignition sources; such as pilot lights, cigarettes, portable electric lamps, and plastic drop cloths (potential static sparking).
• Never spray or flush solvent at high pressure.
• Keep work area free of debris, including solvent, rags and gasoline.
• Do not plug or unplug power cords, or turn power or light switches on or off when flammable fumes are present.
• Use only grounded hoses.
• Hold gun firmly to side of grounded pail when triggering into pail. Do not use pail liners unless they are anti-static or conductive.
equipment until you identify and correct the problem.
• Keep a working fire extinguisher in the work area.
Static charge may build up on plastic parts during cleaning and could discharge and ignite flammable vapors. To help prevent fire and explosion:
• Clean plastic parts only in a well ventilated area.
• Do not clean with a dry cloth.
This equipment must be grounded. Improper grounding, setup, or usage of the system can cause electric shock.
• Turn off and disconnect power at main switch before disconnecting any cables and before servicing or installing equipment.
• Connect only to grounded power source.
• All electrical wiring must be done by a qualified electrician and comply with all local codes and regulations.
13
Intrinsically safe equipment that is installed improperly or connected to non-intrinsically safe equipment will create a hazardous condition and can cause fire, explosion, or electric shock.
Follow local regulations and the following safety requirements.
• Installation should be in accordance with ANSI/ISA RP12.06.01 “Installation of Intrinsically
Safe Systems for Hazardous (Classified) Locations” and the National Electrical Code®
(ANSI/NFPA 70).
• Installation in Canada should be in accordance with the Canadian Electrical Code, CSA
C22.1, Part 1, Appendix F.
• For ATEX, install per EN 60079–14 and applicable local and national codes.
• Equipment that comes in contact with intrinsically safe terminals must meet the entity parameter requirements specified in Control Drawing 16M169. See Appendix A in Manual
332013. This includes safety barriers, DC voltage meters, ohmmeters, cables, and connections. Remove the unit from the hazardous area when servicing.
• Without the safety barrier, the equipment is no longer intrinsically safe and must not be operated in hazardous locations, as defined in article 500 of the National Electrical Code
(USA) or your local electrical code.
• Do not install equipment approved only for non-hazardous location in a hazardous area. See the ID label for the intrinsic safety rating for your model.
• Do not use intrinsically safe equipment with a power supply that has no barrier. Intrinsic safety may be compromised.
• Ground the power supply. A voltage limiting safety barrier must be properly grounded to be effective. For proper grounding, use a 12 gauge minimum ground wire. The barrier’s ground must be within 1 ohm of true earth ground.
• Do not remove any cover until power has been removed.
• Do not substitute system components as this may impair intrinsic safety.
14 3A6948D
High-pressure fluid from gun, hose leaks, or ruptured components will pierce skin. This may
• Do not spray without tip guard and trigger guard installed.
• Engage trigger lock when not spraying.
• Do not point gun at anyone or at any part of the body.
• Do not put your hand over the spray tip.
• Do not stop or deflect leaks with your hand, body, glove, or rag.
or servicing equipment.
• Tighten all fluid connections before operating the equipment.
• Check hoses and couplings daily. Replace worn or damaged parts immediately.
3A6948D
Misuse can cause death or serious injury.
• Do not operate the unit when fatigued or under the influence of drugs or alcohol.
• Do not exceed the maximum working pressure or temperature rating of the lowest rated
For complete information about your material, request Safety Data Sheet (SDS) from distributor or retailer.
• Do not leave the work area while equipment is energized or under pressure.
• Check equipment daily. Repair or replace worn or damaged parts immediately with genuine manufacturer’s replacement parts only.
• Do not alter or modify equipment. Alterations or modifications may void agency approvals and create safety hazards.
• Make sure all equipment is rated and approved for the environment in which you are using it.
• Use equipment only for its intended purpose. Call your distributor for information.
• Route hoses and cables away from traffic areas, sharp edges, moving parts, and hot surfaces.
• Do not kink or over bend hoses or use hoses to pull equipment.
• Keep children and animals away from work area.
• Comply with all applicable safety regulations.
15
Toxic fluids or fumes can cause serious injury or death if splashed in the eyes or on skin, inhaled, or swallowed.
• Read Safety Data Sheets (SDSs) to know the specific hazards of the fluids you are using.
• Store hazardous fluid in approved containers, and dispose of it according to applicable guidelines.
Wear appropriate protective equipment when in the work area to help prevent serious injury, including eye injury, hearing loss, inhalation of toxic fumes, and burns. Protective equipment includes but is not limited to:
• Protective eyewear, and hearing protection.
• Respirators, protective clothing, and gloves as recommended by the fluid and solvent manufacturer.
16 3A6948D
The ProControl 1KE Plus is an electronic flow control and fluid monitoring system. Depending on the model, the ProControl 1KE Plus can perform the following functions:
• Manages fluid pressure or flow rate by either open-loop or closed-loop control for manual or automatic systems.
• Shows real-time fluid flow rate or pressure.
• Monitors and reports overall fluid use.
• Provides password protected settings to lock or limit the range of fluid and atomizing air setpoint adjustments that an operator may use.
• Alarms if the flow rate is too high or too low for the user-set targets.
• Alarms if the fluid pressure is too high or too low for the user-set targets.
• Manages atomizing gun air pressure by open-loop control.
• Alarms when the maintenance total is reached for the user-set target.
• Displays a log of the last 100 alarms.
• Tracks sprayed material and flush material usage by job.
• Displays logs of the last 500 jobs.
• Allows for integration to plant PLC/System Control and remote monitoring through available options listed in
3A6948D 17
Figure 2 View of Fluid Panel with cover removed system.
configuring system setup, selecting operating modes, setting flow/pressure targets, logging jobs, monitoring status, and viewing material usage, job, and alarm logs. Fiber optic ports are available for communicating with an external PLC.
hardware components.
Note
Alternative flow meters and fluid regulators can be installed adjacent to the fluid panel and plumbed in as needed for application and material compatibility.
devices and atomizing air for equipped models.
18
Current to pressure (I/P) transducers for controlling fluid and air regulator pressure settings by the ADCM.
regulator for controlling atomizing air pressure to the applicator gun.
used to determine when applicator gun is triggered. The AFS is required on systems for active closed-loop pressure or flow control.
material usage.
regulator for controlling fluid pressure to the applicator gun.
for measuring fluid pressure. The pressure transducer is required on systems for active closed-loop fluid pressure or flow control.
valve.
3A6948D
M* Air
Technical Specifications, page 103
for pressure and air-cleanliness requirements.
N* Air
P* Fluid
R* Fluid
Technical Specifications, page 103
pressure requirements.
AC Air protect the I/P transducers when air pressure is removed and the I/P transducers are being electrically powered by the ADCM.
AD Check Valve
*** Required components provided by user.
3A6948D 19
NOTE:
ProControl 1KE Plus Selection Guide, page 7
) are supplied with an AC/DC Converter. Users must select and order an appropriate power cord for the local region. In areas with power connections that are different than the options provided in the
female converter. See
Technical Specifications, page 103
Power Supply Module
ProControl 1KE Plus ADCM
Fluid Panel
2–Way Vented Valve
M* Air Supply Line
N* Air Outlet Line to Gun
P* Fluid Outlet Line
20
R* Fluid Inlet Line
S* Fluid Inlet Shut-off Valve
Accessory Light Tower
Ground Wire
V* Gun
*** User-provided
3A6948D
Do not substitute or modify system components as this may impair intrinsic safety. For installation, maintenance, or operation instructions, read instruction manuals. Do not install equipment approved only for non-hazardous locations in a hazardous location. See the identification label for the intrinsic safety rating for your equipment.
Do not use intrinsically safe (IS) equipment with a power supply that has no barrier. Do not move units from a non-IS setup to an IS setup. IS equipment that has been used with a non-IS power supply must not be returned to a hazardous location. Always use an intrinsically safe power supply with IS equipment.
• Installation should be in accordance with ANSI/ISA
RP12.06.01, “Installation of Intrinsically Safe
Systems for Hazardous (Classified) Locations,” and the National Electrical Code® (ANSI/NFPA
70).
• Installation in Canada should be in accordance with the Canadian Electrical Code, CSA C22.1,
Part 1, Appendix F.
• For ATEX, install per EN 60079-14 and applicable local and national codes.
• Multiple earthing of components is allowed only if a high integrity equipotential system is realized between the points of bonding.
• Do not remove any cover until power has been removed.
• Install ADCM according to Control Drawing Number
16M169. See Appendix A in Manual 332013.
3A6948D 21
Power Supply Module (see
ProControl 1KE Plus Selection Guide, page 7 ,
for alternate power supply module options)
ProControl 1KE Plus ADCM
Fluid Panel
2–Way Vented Valve
M* Air Supply Line
N* Air Outlet Line to Gun
P* Fluid Outlet Line
R* Fluid Inlet Line
S* Fluid Inlet Shut-off Valve
Ground Wire
V* Gun
*** User-provided.
22 3A6948D
Power Supply (see
ProControl 1KE Plus Selection Guide, page 7 ,
for alternate power supply module options)
ProControl 1KE Plus ADCM
Fluid Panel
2–Way Vented Valve
M* Air Supply Line
N* Air Outlet Line to Gun
P* Fluid Outlet Line
R* Fluid Inlet Line
S* Fluid Inlet Shut-off Valve
Ground Wire
V* Gun
AE Power cables, available for use with additional ProControl 1KE Plus units (see
ProControl 1KE Plus Selection Guide, page 7
*** User-provided.
3A6948D 23
1.
The equipment must be grounded to reduce the risk of static sparking and electric shock. Electric or static sparking can cause fumes to ignite or explode. Improper grounding can cause electric shock. Grounding provides an escape wire for the electric current.
Power
Refer to the IS Power Supply Modules manual.
2.
ProControl wire to the screw on the top of the bracket.
Connect the other end to a true earth ground. In an IS system, the ProControl 1KE Plus ADCM is also grounded by connection to the grounded power supply.
3.
External instructions in manual 308778 (G3000, S3000,
G250) or manual 313599 (Coriolis) to ground the flow meter and check its electrical grounding continuity.
4.
Fluid wire to the screw on the 1KE Plus fluid panel.
Connect the other end to a true earth ground.
5.
Fluid Supply:
1
2
8
9
6
7
10
3
4
5
Fiber Optic Receiver
Fiber Optic Transmitter
Power
Digital Input/Output
Fiber Optic Receiver
Fiber Optic Transmitter
Analog Input
Flow Control
Atomizing Air Control
Analog Input
Red Lead from TX on Fiber Optic Converter (PN 16K465) or from Port 6 on another ProControl 1KE Plus (or Informer)
Black Lead to RX on Fiber Optic Converter (PN 16K465) or to Port 5 on another ProControl 1KE Plus (or Informer)
From Power Supply
To/From Meter and Light Tower (Accessory)
Black Lead from Port 2 on another ProControl 1KE Plus (or Informer)
Red Lead to Port 1 on another ProControl 1KE Plus (or Informer)
To/From Pressure Transducer Cable
To/From Flow Control Cable
To/From Atomizing Air Control Cable
From Air Flow Switch (AFS) or Gun Trigger
24 3A6948D
Connect incoming air supply to the air supply shut-off valve (L) 1/4 npt (f). (See
To avoid damage to the I/P transducer, use clean, dry, oil-free air, filtered through at least a 40 micron filter.
See
Technical Specifications, page 103
air pressure and consumption ratings. The I/P transducer exhausts a small amount of air whenever air is connected, regardless of whether the system is operating. Refer to your applicator gun air pressure and consumption ratings and size your air supply accordingly.
The ProControl 1KE Plus uses an Air Flow Switch
(AFS) to detect when the applicator gun is triggered.
Do not bypass the AFS. See
for an alternate gun trigger air pressure switch that can be used in place of the provided AFS.
• The side port (AH) on the fluid regulator can be used for high-speed flushing with an independent air source. Set the air pressure
Setup Screen 11: Fill Mode, page 52
, and
Setup Screen 12: Flush Mode, page 53
, for the preferred method of controlling fill and flush pressure.
• Flushing air pressure must be removed from the side port (AH) to return to the previous flow setting.
3A6948D 25
applicator gun atomizing air control only and will have no fluid inlet or outlet connections.
For models that come equipped with the standard
G3000 Fluid Meter, connect incoming fluid to the provided meter check valve fitting 1/4 npt(m) inlet port. Refer to instruction manual 308778 for additional details regarding installation and operation of the G3000 meter.
Note
Users are responsible for providing a fluid inlet shut-off valve or other means of isolating the fluid supply.
See
Alternate Flow Meter and Fluid Regulator
. Users must provide fluid fittings and hose when using alternate Flow Meters or Fluid
Regulators.
The ProControl 1KE Plus fluid outlet connection will be made at the Fluid Pressure Transducer port 1/4 npt(f) for most models. For Flow Monitor models
(25B285–25B288), the fluid outlet connection will be made at the fluid regulator outlet.
Note
For proper operating performance using open- or closed-loop pressure or flow control, the ProControl 1KE Plus Fluid Pressure I/P
Transducer must operate at an outlet air pressure of at least 10 psi (0.7 bar). When using 1:1 air-operated fluid regulators, this means that the minimum pressure drop between the 1KE fluid outlet and the gun nozzle is at least 10 psi (0.7 bar) during the expected spray conditions (flow rate ranges) and material viscosities that will be used. If the back pressure drops below 7 psi (0.5 bar), the performance may become inconsistent.
Back pressure can be increased by using a smaller diameter fluid hose or a longer hose between the 1KE Plus and the spray gun. An alternate solution would be to use a
Graco 24E471 1:2 Ratio Fluid Regulator or a
24E472 1:3 Fluid Regulator, see instruction manual 3A0427 for details. These alternate ratio fluid regulators have lower fluid outlet pressure ranges, but will allow the 1KE Plus
Fluid Pressure I/P Transducer to operate at a higher air control pressure.
Note
If the application requires greater than 50 psi
(3.5 bar) of fluid pressure at the ProControl
1KE Plus outlet, you must use either 16V680 non-hazardous location power supply module or the 26C724 G-Barrier hazardous location power supply module. The 16M167 hazardous location power supply module output is limited and will not drive the fluid pressure I/P transducer to greater than 50 psi (3.5 bar).
26 3A6948D
For application of fluid compatibility, alternate flow meters or fluid regulators can be used with the
ProControl 1KE Plus. See
a list of optional Graco meters and regulators.
It is recommended that alternate meters or regulators be mounted adjacent to the fluid panel to ensure optimal control.
See
, for meter power and signal connections to the 1KE Plus.
For alternate fluid regulators, connect a 5/32 in. OD air tubing line from the fluid I/P transducer control
“out” port to the fluid regulator air control inlet port.
The pilot air line should not exceed 10 ft (3 m).
Graco Accessories are available to enable communication with a Programmable Logic
Controller (PLC) or Personal Computer (PC).
• The Fiber Optic Converter (Graco Kit 24N978) enables Modbus RTU communication with a user-supplied PLC using a serial cable.
• The Fiber Optic-to-Serial Converter Module (Graco
Kit 24R086) includes the fiber optic-to-serial converter and power supply inside of an enclosure.
See the Communication Kits instruction manual
(332356) for additional details.
The communication kits come with installation and setup directions necessary for their use with the ProControl 1KE Plus. See
Appendix A - Modbus Variable Map, page 93 , for
registration details.
3A6948D 27
A
B1 and B2
C1 and C2
X
Y
Z
AA
AB
Power Supply Module (26C724 shown)
ProControl 1KE Plus ADCM
ProControl 1KE Plus Fluid Panel
Air Control Module
Communications Module (24R086)
PLC
Fiber Optic Cable
Power Cable
Supplied; ordered separately
Supplied
Supplied
Accessory
Accessory
Customer-Supplied
Accessory
Supplied
28 3A6948D
Follow instructions in the fluid regulator manual to set up, flush, and adjust the fluid regulator prior to use.
Follow the Pressure Relief Procedure whenever you see this symbol.
This equipment stays pressurized until pressure is manually relieved. To help prevent serious injury from pressurized fluid, such as skin injection, splashing fluid and moving parts, follow the
Pressure Relief Procedure when you stop spraying and before cleaning, checking, or servicing the equipment.
1.
Turn off the fluid supply to the meter or fluid panel.
2.
Depending on the Control Method selected (see
Control Method Considerations, page 33
), enter a Target Fluid Value of at least 1/2 of maximum
(such as, 50%, 50 psi, 200 cc/min, or 12 mA).
a.
Put the system into Dispense Mode
(see
).
3.
Actuate your fluid system dispensing device.
4.
Put the system into Standby Mode
Run Mode Selection, page 35 ).
5.
Turn off the vented air supply valve (L).
(see
To reduce the risk of component rupture, which could cause injury from splashing fluid, do not exceed the maximum working pressure of your meter or any component or accessory in your system.
For information on the G3000, S3000, or G250 Graco flow meter, see manual 308778. For information on the Coriolis flow meter, see manual 313599.
Calibrate the meter as instructed before using the meter for production.
The flow meter gears and bearings can be damaged if they rotate at too high a speed. To avoid high-speed rotation, gradually open the fluid valve. Do not over-speed the gear with air or solvent. To prolong meter life, do not use the meter above its maximum flow rate.
To avoid damage to the I/P transducer, always put the system into Standby Mode (see
Run Mode Selection, page 35 ), or power the
system off, before reducing air pressure to the system.
3A6948D 29
The Display Module provides the interface for users to enter selections and view information related to setup and operation.
The screen backlight is factory set to remain on, even without screen activity. See
Setup Screen 15: Date and Time, page 55
, to set the backlight timer to your preference. Press any key to restore.
Keys are used to input numerical data, enter setup screens, navigate within a screen, scroll through screens, and select setup values.
To prevent damage to the softkey buttons, do not press the buttons with sharp objects such as pens, plastic cards, or fingernails.
1.
Use the menu.
to highlight the correct choice from
2.
Press
3.
Press to select.
to cancel.
1.
The first digit will be highlighted. Use change the number.
2.
Press to move to the next digit.
3.
When all digits are correct, press accept.
4.
Press to cancel.
to again to
The ProControl 1KE Plus has two operation modes: Run Mode and Setup Mode. For detailed information, see
, and
. Press between these two modes.
to toggle
A check box field is used to enable or disable features in the software.
1.
Press box.
to toggle between and an empty
2.
The feature is enabled if a is in the box.
The reset field is used for totalizers. Press reset the field to zero.
to
When all data is correct, press
Then use to exit the screen.
to move to a new screen, or move between Setup Mode and Run Mode.
to
Refer to this section if you have questions about screen navigation or about how to enter information and make selections.
1.
Use to move between screens.
2.
Press to enter a screen. The first data field on the screen will highlight.
to highlight the data you wish to 3.
Use change.
4.
Press to edit.
30 3A6948D
As you move through the ProControl 1KE Plus screens, you will notice that most information is communicated using icons rather than words to simplify global communication. The detailed screen descriptions in
, explain what each icon represents. Icon reference tables also are provided, on this page and the next. Softkeys are membrane buttons whose function correlates with the screen content to the immediate left of the button.
Press to toggle between Run Mode and Setup Mode.
Mode Selection.
Opens a menu of Run Mode
selections ( Run Mode Selection, page 35 ).
Error Reset: Use to clear alarm after cause has been fixed. Also used to cancel data entered and return to original data.
Enter Screen.
Highlight data that can be edited.
Also changes the function of the Up/Down arrows so they move between data fields on the screen, rather than between screens.
Up/Down Arrows: Use to move between screens or fields on a screen, or to increment or decrement the digits in a settable field.
Softkeys: Use varies by screen.
See column at right.
Exit Screen.
Exit data editing.
Enter.
Press to activate a field for editing or to accept the highlighted selection on a menu.
Right.
Move to the right when editing number fields. Press again to accept the entry when all digits are correct.
Reset.
Reset totalizer to zero.
Start
Stop
Job Log.
Saves the current job log data, resets totalizers, and initiates a new job logging cycle.
3A6948D 31
Set Flow Rate Units Maintenance Totalizer Alarm Enable
Screen number.
The arrows indicate more screens are available to view.
Batch Totalizer
Maintenance Totalizer Maintenance Target
Grand Totalizer Set Grand Total Units
Fluid Flow Percent
Target
Lock icon indicates the unit is in Setup.
Batch Units
Fluid Pressure
Fluid Flow Rate Set Modbus Mode
Set Modbus Address Set Serial Port Baudrate
Flow Rate Alarm
Enable
Set Alarm Auto Clear
(to clear alarm on accessories)
Set Backlight Timer Volume measured by the meter
Actual volume dispensed
K-Factor
Select Pressure
Transducer
Set Zero Offset
Display or adjust pressure transducer slope
F3
Flow Rate High Alarm
MF
Maintenance Alarm
F2
Flow Rate Low Alarm
Set Serial Port Parity Modbus Functionality is Off
Set Upper and Lower
Limits for Fluid Flow
Percent
Set Pressure Units
ProControl 1KE is
Modbus Slave
Set Maximum and
Minimum Flow Rates
Select Correct Date
Set the Correct Time
Select Date Format
Enter User-Set
Password
32 3A6948D
The ProControl 1KE Plus software allows for multiple control methods, which are selected and configured on the Setup screens. The control method you chose will determine the information and options available on the Run Screens.
2.
Select the icon for your control method.
Control methods are selected on
Setup Screen 13: Control Method, page 54
.
1.
The Control Method setup screen.
The control method options are described in the following table.
No active control. The system drives to the setpoint immediately, and will not adapt to changes in pressure or flow.
An ADCM that is not configured with specific pressure sensors, flow meters, or output controls has limited capabilities on the run screen. However, all of the system setup screens are still available for offline configuration.
Drives to a fluid pressure target, and may monitor flow. The system drives to the setpoint using the PID control. It will not adapt to changes in flow.
3A6948D 33
Drives to a fluid flow target. The system drives to the setpoint using a PID control for pressure, which is targeting from the PID control for flow.
For testing and setup. The system drives to the current output immediately.
Note
4–20 mA approximately corresponds to 0–100 psi
(0–6.9 bar) pilot air pressure.
Systems without the atomizing air control option do not have a separate control to enable it. The setting will remain on the screen. Leave the atomizing air setpoint at 0 in that case.
34 3A6948D
There are four Run modes that can be selected from the Run screen.
1.
Press the softkey next to the Mode Selection icon.
2.
Select one of the following mode icons from following table.
Standby Mode – depressurize system
• Gun atomizing air pressure is set to 0
• Fluid pressure is set to 0
Flush Mode – used for solvent flush
• Gun atomizing air pressure is set to 0
• Fluid pressure is set to a percent value
(see
Setup Screen 12: Flush Mode, page 53 )
Fill Mode – used for loading paint
• Gun atomizing air pressure is set to 0
• Fluid pressure is set to a percent value (see
Setup Screen 11: Fill Mode, page 52
)
Dispense Mode – used for painting
• Gun atomizing air pressure is set to the target percent value
• Fluid pressure is set to either the flow or pressure target
Dispense Mode – gain reset
• Used to put the system back into high gain mode where it will rapidly attempt to correct any off-target flow situation.
For more information, see
1KE Plus Gain Function, page 35
Note
To view the live current Gain value or edit the allowable Low Gain Limit, see
Setup Screen 10: PID Data, page 52
.
The Gain Function provides improved Closed
Loop Flow Control performance on manual spray applications where the operator partially triggers the gun occasionally. Common examples are
"feathering” the gun periodically to reduce the amount of fluid sprayed or partially triggering the gun to open the atomizing air without spraying fluid to dust off parts. The Gain function reduces system variation from the target set point for applications where occasionally the gun atomizing air is on without the fluid valve fully open to its normal operating point.
Automatic or manual gun applications that always maintain a gun full-off (no air or fluid flow) and full-on
(atomizing air flow and trigger pulled to full fluid opening set point) should use a Low Gain Limit of 20 to 30 to maintain stability at the set point.
The Gain value is the percentage of the flow rate
PID K-Factors that are used for the pressure target calculations. As the flow rate approaches the target, the gain will drop down to the minimum value. This reduces over-reaction by the flow control when feathering or dusting operations are happening.
Occasionally, when the ProControl 1KE Plus is not operating at the target flow rate, an operator may reset the Gain to maximum to aggressively drive the system back to the target flow set point. The Gain can be quickly reset from the main Run Screen 1:
1.
2.
Press Mode Selection .
Select Dispense Mode - Gain Reset
3.
Press Enter .
3A6948D 35
In Standby Mode, the atomizing air and the fluid pressure pilot regulators are set to zero (0). The flow meter remains operational, and the system will show fluid flow and accumulated fluid volume.
Residual pressure may be in the system depending on the nature of the air and fluid regulators, material properties, and other variances.
When the system is first powered up, the type of fluid in the system is unknown. This is indicated with checkerboard pattern on the gun. After a fluid Fill process, the gun is shown as black to indicate that it is loaded with sprayable material. After a fluid Flush process, the gun is shown as white to indicate that it is loaded with solvent.
Standby after power-up with an unknown fluid
Standby with paint loaded
The following icons are available on the Run Screen in Standby Mode:
Enter the screen.
Atomizing air regulator
Flow rate target (Closed Loop Flow
Control Mode)
% pilot air pressure target to fluid regulator
Pressure target (Closed Loop Pressure
Mode)
Current (mA) setpoint to pilot air control
Current fluid pressure
Standby Mode – Unknown fluid in system
Standby Mode – System filled with sprayable material
Standby Mode – System filled with solvent
Move between Run Screens.
Standby with solvent loaded
36 3A6948D
The data used to operate Flush Mode is configured in
Setup Screen 12: Flush Mode, page 53
.
When Flush Mode is activated, the fluid regulator is set to the percentage drive value from the setup screen. The atomizing air regulator is set to zero.
This runs for the selected amount of time. The fluid volume that flowed during the flush process is compared to the minimum flush volume from the setup screen. If the volume was not achieved, the
“SP” alarm is activated. The fluid volume is tracked as a solvent in the Job Log.
Flush Mode active
The following icons are available on the Run Screen in Flush Mode:
Enter the screen.
Atomizing air regulator
Flow rate target
Current fluid pressure
Flush Mode – No flow detected
Flush Mode Countdown Timer
Move between Run Screens.
Flush Mode complete
3A6948D 37
The data used to operate Fill Mode is configured in
Setup Screen 11: Fill Mode, page 52
.
When Fill Mode is activated, the fluid regulator is set to the percentage drive value from the setup screen.
The atomizing air regulator is set to zero. This runs for the selected amount of time. The fluid volume that flowed during the fill process is compared to the minimum fill volume from the setup screen. If the volume was not achieved, the “SN” alarm is activated.
Fill Mode active
The following icons are available on the Run Screen in Fill Mode:
Enter the screen.
Atomizing air regulator
Flow rate target
Current fluid pressure
Fill Mode – No flow detected
Fill Mode Countdown Timer
Move between Run Screens.
Fill Mode complete
38 3A6948D
When Dispense Mode is activated, the fluid regulator is opened and adjusted based on the control method.
The atomizing air regulator is opened to the setpoint.
The gun icon has several animation sequence components to indicate conditions of the gun trigger and fluid flow.
If the System Idle function is activated in
Setup Screen 9: Additional Operator Input Limits and Timeouts, page 51
, then if the gun trigger is not activated after the amount of time selected the system fluid pressure will be reduced to zero (0). The
“EU” event is activated. The Atomizing air pressure remains at the setpoint. Once the gun trigger is activated again, fluid pressure is returned to the setpoint, and Dispense mode resumes. Note that repressurizing the system takes some time, so fluid and spray dynamics may be different for the first few seconds of operation compared to a typical gun triggering cycle.
If the Dose Time function is activated in
Setup Screen 9: Additional Operator Input Limits and Timeouts, page 51
, then if there is no fluid flow while the gun trigger is activated after the amount of time selected on the screen the fluid pressure will be reduced to zero. The “QT” alarm is activated. The system is returned to Standby Mode. To return to
Dispense Mode, determine and repair the cause of no fluid flow, clear the alarm, and reactivate the mode.
Dispense
Mode with no atomizing air, fluid flowing
Dispense Mode with atomized spray (air and fluid flow)
The following icons are available on the Run Screen in Dispense Mode:
Dispense Mode with no gun trigger
Dispense Mode with atomizing air, no fluid flow
Enter the screen.
Atomizing air regulator percent open target
Flow rate target
% pilot air pressure target to fluid regulator
Pressure target (Closed Loop Pressure
Mode)
Current (mA) setpoint to pilot air control
Current fluid pressure
Dispense Mode idle with AFS off
Dispense Mode active with air flow only
Dispense Mode active with fluid flow only
Dispense Mode active with fluid and air flow
Dispense Mode during System Idle
Dispense Mode during Dose Time
Move between Run Screens.
3A6948D 39
This is the active Job Log screen. This totalizes the dispensed amounts of paint and solvent per job. It is tracked by job number, and includes an additional user-defined job identification number; station, part, or other code.
Sample totalizers
The following icons are available on the Job Log screen:
Enter the screen
Job Spray Totalizer
Job Flush Totalizer
Job Log – saves current job log data, resets totalizers, and initiates a new job logging cycle
Job Number – increments automatically
Job Identification Number – user-assigned
Move between Run Screens
The paint dispense totalizer ( ) accumulates the total amount of fluid dispensed in the job logging cycle.
This is reset to zero when the Job Log icon ( ) is pressed. This includes fluid from the Fill cycle, including any unsprayed paint in the hose.
Dispense Total The solvent dispense totalizer ( ) accumulates the total amount of fluid dispensed in the job logging cycle.
This is reset to zero when the Job Log icon ( ) is pressed. This only includes fluid from the
Flush cycle.
The job number ( ) is automatically assigned in increments, though it can be set at any time. When the Job Log icon ( ) is pressed, “1” is added to this value.
The job identification number ( ) does not change automatically, and can be set at any time. The same number will be logged with each job.
The job is completed and stored when the Job Log icon ( ) is pressed.
40 3A6948D
This displays information from the stored job logs.
Job log history data
The following icons are available on the Job Log
History screen:
Enter the screen.
Job Index
Year
Date
Time
Job Number
Job Identification Number
Job Spray Totalizer
Job Flush Totalizer
Move between Run Screens.
Index of logged jobs. The most recent job, which is always index “000”, is initially displayed when the screen is entered; the lower the index, the more recent the job. The Job
Index ( ) can be set directly by entering the number field and selecting a value from “000” to
“500” to quickly jump to any record, or the value can be incrementally increased or decreased using the keyboard arrow keys.
The Year ( ), Date
( ), and Time ( ) the job was completed.
The Job Number ( ) active when the job was logged.
The Job Identification
Number ( ) active when the job was logged.
The total volume of paint
( ) dispensed.
The total volume of solvent ( ) dispensed.
3A6948D 41
This displays information from the stored event logs.
Event log history data
The following icons are available on the Event Log
History screen:
Enter the screen.
Event Index
Year
Date
Time
Threshold
Outlier
Advisory
Deviation
Alarm
P2
Low
Pressure
Event Code
Event Description
Move between Run Screens.
42
Index of logged events.
The most recent event, which is always index
“000”, is initially displayed when the screen is entered; the lower the index, the more recent the event. The Event Index
( ) can be set directly by entering the number field and selecting a value from “000” to “500” to quickly jump to any record, or the value can be incrementally increased or decreased using the keyboard arrow keys.
The Year ( ), Date
( ), and Time ( ) the event was completed.
The Threshold ( ) of the alarm.
The measured value of the Outlier ( ) that exceeds the threshold of the alarm.
Events can be Deviations
( ), Advisories ( ), or Alarms ( ). Some events have a fixed type, while others can be selected depending on user preferences.
See
.
The Event Code.
See
.
A short description of the
Event Code.
3A6948D
If a password has been set, the Password
Screen displays when is pressed from any Run screen. Enter password to enable entry to the Setup screens. Set the password to 0000 to disable password protection. See
Setup Screen 16: Password, page 56
, to set or change the password.
Enter the screen to enter a password.
Press to activate a field for editing.
Move to the right when editing number fields. Press again to accept the entry when all digits are correct.
Enter the user-set password for the system.
Increment/decrement the digits when editing number fields.
3A6948D 43
The Setup Mode is used to set up a password (if desired) and to set parameters for controlling and monitoring fluid flow with the ProControl 1KE Plus.
See
Screen Navigation and Editing, page 30
, for information on how to make selections and enter data.
The Job Target screen is used to monitor the range of sprayed fluid per job. When a job is logged, and the dispensed volume is outside the limit, the alarm will be turned on. A limit value of 0 turns off the alarm.
Example with a minimum volume of
125 cc. The logged job was 115 cc, so the alarm was activated.
Example with a range from 125 cc to
135 cc. The logged job was 138 cc, so the alarm was activated.
Enter the screen to set or change preferences.
Press to activate a field for editing or to accept the highlighted selection on a menu.
Move to the right when editing number fields. Press again to accept the entry when all digits are correct.
Job dispense alarm range.
Job dispense alarm enable (
Exit data editing.
).
Move between Setup Screens, fields on a screen, or to increment/decrement the digits when editing number fields.
44 3A6948D
Use this screen to view and reset the maintenance totalizer, and set the maintenance target value.
Maintenance totalizer units, shown on this Setup
Screen, are always cubic centimeters (cc).
No data or selections.
Example with the maintenance level set to 100 cc and the alarm enabled.
Once 100 cc is reached, the “MF” alarm is activated.
Clear the alarm by entering the screen, selecting the Reset option, and selecting the Clear Alarm button.
Enter the screen to set or change preferences.
Press to activate a field for editing or to accept the highlighted selection on a menu.
Move to the right when editing number fields. Press again to accept the entry when all digits are correct.
Reset Maintenance Totalizer - resets the maintenance totalizer to zero.
Maintenance Totalizer - Displays the current maintenance total in cubic centimeters (cc).
Set your desired maintenance total target value in this field in cubic centimeters
(cc).
Maintenance Totalizer Alarm Enable
( ).
Exit data editing.
Move between Setup Screens, fields on a screen, or to increment/decrement the digits when editing number fields.
3A6948D 45
Use this screen to view the Grand Total volumes and to set the Grand Total units.
Use this screen to calibrate your meter and to view or set your meter k-factor. See
, for procedure.
Enter the screen to set or change preferences.
Press to activate a field for editing or to accept the highlighted selection on a menu.
Move to the right when editing number fields. Press again to accept the entry when all digits are correct.
Grand Total for Spray Material
Grand Total for Flush Material
Volume Units – Select from the following options:
– Select if system has no flow meter
Enter the screen to set or change preferences.
Press to activate a field for editing or to accept the highlighted selection on a menu.
Move to the right when editing number fields. Press again to accept the entry when all digits are correct.
Start the calibration.
Stop the calibration.
Displays the volume measured by the system for the calibration test.
Enter the actual volume dispensed into the cylinder for the calibration test.
Displays the meter k-factor. User can set the k-factor manually. The system automatically updates to the correct k-factor when the meter is calibrated.
Flow Rate Units – Select from the following options:
– Select if system has no flow meter
Exit data editing.
Move between Setup Screens, fields on a screen, or to increment/decrement the digits when editing number fields.
Exit data editing.
Move between Setup Screens, fields on a screen, or to increment/decrement the digits when editing number fields.
46 3A6948D
Use this screen to set your flow rate maximum and minimum alarm values.
Enter the screen to set or change preferences.
Press to activate a field for editing or to accept the highlighted selection on a menu.
Move to the right when editing number fields. Press again to accept the entry when all digits are correct.
Set your desired maximum (first data field) and minimum (second data field) flow rates. Flow rates outside of these parameters will trigger an alarm.
Select ( ) if you want the alarm to be based on percent deviation from the current active target flow rate. When selected, the maximum and minimum values shown above will automatically update based on the selected +/- percent amount and the current active Flow Rate
Target on the Run Screen.
Set the +/- percent difference from the flow target that will trigger an alarm.
Alarm Auto Clear Enable. If enabled, when the flow rate returns to within the flow limit set points, the flow rate alarm will clear on the screen and on any attached accessories such as a light tower.
Select the type of alarm.
Advisory. System does not shut down.
It does not attempt to modify operation.
Event is logged.
Deviation. System does not shut down.
It may attempt to modify operation to adjust to the conditions. Event is logged.
Alarm. System shuts down. Event is logged.
Exit data editing.
Move between Setup Screens, fields on a screen, or to increment/decrement the digits when editing number fields.
3A6948D 47
Use this screen to specify your pressure transducer and set its offset and slope.
The default values for software version 1.04.060 and higher that are pre-loaded for each pressure sensor are:
100 psi (7 bar)
2000 psi
(138 bar)
4500 psi
(310 bar)
16H282
16P290
15M669
20
20
175
0
0
0
Note
For 2000 and 4500 psi pressure sensors, refer to the calibration tag for specific values.
Empty
With data
Enter the screen to set or change preferences.
Press to activate a field for editing or to accept the highlighted selection on a menu.
Move to the right when editing number fields. Press again to accept the entry when all digits are correct.
Select the correct pressure transducer.
• (None)
Pressure transducer slope. This number is a constant representing millivolts per bar. The default matches the selected pressure transducer. Operator adjustable. Default value is “090.000”.
Set the zero offset (the reading on the gauge when no pressure is on the system). Default value is “00.4500”.
Select units.
Exit data editing.
Move between Setup Screens, fields on a screen, or to increment/decrement the digits when editing number fields.
48 3A6948D
Use this screen to set your pressure maximum and minimum alarm values, and to select your preferred units.
Enter the screen to set or change preferences.
Press to activate a field for editing or to accept the highlighted selection on a menu.
Move to the right when editing number fields. Press again to accept the entry when all digits are correct.
Set your desired maximum (first data field) and minimum (second data field) pressure. Pressures outside of these parameters will trigger an alarm.
Select ( ) if you want the alarm to be based on percent deviation from the current active target pressure. When selected, the maximum and minimum values shown will automatically update based on the selected +/- percentage and the current active target pressure on the Run screen.
Set the +/- percent difference from the pressure target that will trigger an alarm.
Alarm Auto Clear Enable. If enabled, when the pressure returns to within the pressure limit set points, the pressure alarm will clear on the screen and on any attached accessories such as a light tower.
Select the type of alarm.
Advisory. System does not shut down.
It does not attempt to modify operation.
Event is logged.
Deviation. System does not shut down.
It may attempt to modify operation to adjust to the conditions. Event is logged.
Alarm. System shuts down. Event is logged.
Exit data editing.
Move between Setup Screens, fields on a screen, or to increment/decrement the digits when editing number fields.
3A6948D 49
This screen changes format and data based on the Control Method. See
Control Method Considerations, page 33 , for
more information.
The following table demonstrates how operator input limits may be set for the setpoints on the Run screen.
Note
These are not alarm limits.
Monitor and Accumulate Volume Only
Closed-Loop Pressure Control
Closed-Loop Flow Control
Open-Loop Current Setpoint Note
There are no input limits for the Open-Loop
Current Setpoint method.
Enter the screen to set or change preferences.
Press to activate a field for editing or to accept the highlighted selection on a menu.
Move to the right when editing number fields. Press again to accept the entry when all digits are correct.
Set your desired maximum (first data field) and minimum (second data field) pressure when in pressure control mode.
The system’s Pressure Target will not be allowed to be set outside of this range.
Set your desired maximum (first data field) and minimum (second data field) flow rate when in flow control mode. The system’s Flow Rate Target will not be allowed to be set outside of this range.
Exit data editing.
Move between Setup Screens, fields on a screen, or to increment/decrement the digits when editing number fields.
50 3A6948D
This screen contains the Atomization Air percentage input limits, the System Idle timeout, and the Dose
Time timeout.
Empty
With data
Enter the screen to set or change preferences.
Press to activate a field for editing or to accept the highlighted selection on a menu.
Move to the right when editing number fields. Press again to accept the entry when all digits are correct.
Set your desired maximum (first data field) and minimum (second data field) atomizing air percentage. The system’s atomizing air setpoint cannot be set outside of this range.
The number of minutes with the system in Dispense mode with no gun trigger activation before it sets the fluid regulator to zero. Once the gun trigger is activated the regulator will be driven to the previous value.
The number of seconds with the system in Dispense mode with no detected fluid flow while the gun trigger is activated. The alarm will shut down the system.
Exit data editing.
Move between Setup Screens, fields on a screen, or to increment/decrement the digits when editing number fields.
3A6948D 51
Enter the screen to set or change preferences.
Press to activate a field for editing or to accept the highlighted selection on a menu.
Move to the right when editing number fields. Press again to accept the entry when all digits are correct.
Pressure control loop.
Flow control loop.
Proportional gain.
Integral gain.
Derivative gain.
The first box displays the current gain, this number decreases as the system approaches its flow target and increases if the flow diverges from target.
The second box displays the lowest gain the system can use. You can edit this value. Higher numbers increase sensitivity but may cause errors in certain situations such as gun feathering and very short trigger times.
For more information, see
1KE Plus Gain Function, page 35
.
Exit data editing.
Move between Setup Screens, fields on a screen, or to increment/decrement the digits when editing number fields.
Use this screen to set up the parameters for Fill
Mode. When set, the Minimum Fill Volume is checked against the amount of material that flowed during the Fill process. The “SN” Minimum Fill
Volume alarm is set if this isn’t achieved. Selection of
Dispense Mode is not allowed until the programmed
Minimum Fill Volume is reached.
Enter the screen to set or change preferences.
Press to activate a field for editing or to accept the highlighted selection on a menu.
Move to the right when editing number fields. Press again to accept the entry when all digits are correct.
Set fluid regulator to a percentage open.
Set a fill duration time. The first box displays the remaining time when a Fill
Mode is active.
Minimum Fill Volume. Set to “0” to disable this feature.
Exit data editing.
Move between Setup Screens, fields on a screen, or to increment/decrement the digits when editing number fields.
52 3A6948D
Use this screen to set up the parameters for Flush
Mode. When set, the Minimum Flush Volume is checked against the amount of material that flowed during the Flush process. The “SP” Minimum Flush
Volume alarm is set if this isn’t achieved.
Enter the screen to set or change preferences.
Press to activate a field for editing or to accept the highlighted selection on a menu.
Move to the right when editing number fields. Press again to accept the entry when all digits are correct.
Set fluid regulator to a percent open.
The first box displays the remaining time when a Flush Mode is active.
Set a flush duration time.
Minimum Flush Volume. Set zero to disable this feature
Exit data editing.
Move between Setup Screens, fields on a screen, or to increment/decrement the digits when editing number fields.
3A6948D 53
Use this screen to set the system control method.
See
Control Method Considerations, page 33
, for more information.
With control method selected
With selection menu open
Enter the screen to set or change preferences.
Press to activate a field for editing or to accept the highlighted selection on a menu.
Move to the right when editing number fields. Press again to accept the entry when all digits are correct.
Control Method selection.
Scaled percentage of the 4mA to 20mA range of the control valve.
Direct pressure set point for closed-loop control.
Direct flow rate set point for closed-loop control.
Direct milliamp output selection to the control valve.
Gun trigger type.
Flow control is enabled by an air signal, such as an air flow switch for atomizing air, or a pressure switch for a valve tip solenoid. When the system is set to Dispense from Standby, the target pressure is driven to immediately.
Depending on the fluid pressure and hose configuration, the system may overshoot fluid pressure. The elevated pressure may get trapped in the line.
Flow control for airless guns is enabled by detected fluid flow through the meter.
If you select this option, set up the idle pressure and flow threshold for the system.
Not used.
When the system is set to Dispense from Standby, the target pressure is ramped up to over approximately 3 seconds. This attempts to limit any fluid pressure overshoot.
Idle pressure for the airless gun trigger.
Enable idle pressure with
Flow .
set to
Fluid flow threshold for the airless gun trigger. Enable fluid flow control with set to Flow
Exit data editing.
.
Move between Setup Screens, fields on a screen, or to increment/decrement the digits when editing number fields.
54 3A6948D
Use this screen to set your Modbus preferences for ports 1 and 2. Note that ports 5 and 6 are used as Modbus master devices for connecting to other
ProControl 1KE, Informer, or Graco Integrated Paint
Kitchen modules.
Use this screen to set your date format, date, time, and backlight timeout.
Modbus mode. Select off or Slave from the menu options.
Turn off Modbus functionality if not used.
Use ProControl 1KE as Modbus slave device.
Enter or change the Modbus address.
Value is between 1 and 247.
Select serial port baudrate from the menu options: 9600, 19200, 38400, 57600, or
115200.
Select serial port parity from the menu options: NONE, ODD, or EVEN.
Exit data editing.
Move between Setup Screens, fields on a screen, or to increment/decrement the digits when editing number fields.
Enter the screen to set or change preferences.
Press to activate a field for editing or to accept the highlighted selection on a menu.
Move to the right when editing number fields. Press again to accept the entry when all digits are correct.
Select your preferred date format from the menu.
MM/DD/YY
DD/MM/YY
YY/MM/DD
Set the current date.
Set the current time.
Backlight timeout in minutes. Set zero to disable backlight timeout.
Exit data editing.
Move between Setup Screens, fields on a screen, or to increment/decrement the digits when editing number fields.
3A6948D 55
Use this screen to enter a password that will be required to access the Setup screens. This screen also displays the software version.
Enter the screen to set the password.
Press to activate the field for editing.
Move to the right when editing number fields. Press again to accept the entry when all digits are correct.
Enter desired password. Enter “0000” to disable the password.
Select to view additional debug screens. Four additional screens display information you can use to troubleshoot operational problems:
•
Screen 17: Internal pressure control variables, page 57
•
Screen 18: Internal flow control variables, page 59
•
Screen 19: Internal setpoint and flowmeter information, page 61
•
Screen 20: Modbus status, page 62
Exit data editing.
Move between Setup Screens, fields on a screen, or to increment/decrement the digits when editing number fields.
56 3A6948D
This screen shows information about the internal operation of the pressure control process.
Label Definition pP pI
Pressure PID proportional term. The portion of the output drive current due to the immediate pressure error.
Pressure PID integral term. The portion of the output drive current due to the integration over time of the pressure error.
pD pA pE
Pr
Pressure PID differential term. The portion of the output drive current due to the change of the immediate pressure error.
Pressure PID accumulator total. The sum of the proportional, integral, and differential terms, which equals the output drive current to the current-to-pressure regulator valve.
Pressure set point error. The difference between the pressure set point and the measured fluid pressure. If the pressure set point is higher than the measured fluid pressure, this value is positive and the system increases pressure. If the pressure set point is lower than the measured fluid pressure, this value is negative and the system decreases pressure.
Positive value: The pressure control is allowed to raise the output current.
Negative value: The pressure control is not allowed to raise the output current.
mA mA mA mA psi
Not applicable
3A6948D 57
Pf
SB
Positive value: The pressure control is allowed to reduce the output current.
Negative value: The pressure control is not allowed to reduce the output current.
Internal binary control values displayed in two groups of four bits.
Group Bit Value Definition
1 1 0 Flow control is not allowed to raise the target pressure.
2
3
4
1
0
1
0
1
0
1
Flow control is allowed to raise the target pressure.
Flow control is not allowed to reduce the target pressure.
Flow control is allowed to reduce the target pressure.
Pressure control is able to reduce the system pressure.
Pressure control is not able to reduce the system pressure.
Pressure control is able to increase the system pressure.
Pressure control is not able to increase the system pressure.
2 1
2
3
4
0
1
0
0
1
0
1
Flow control is able to reduce the system flow rate.
Flow control is not able to reduce the system flow rate.
Flow rate is not high.
Flow rate is high.
Fluid flow is not stable.
Fluid flow is stable.
Not used. Always zero.
Note
Values available on Modbus may be different due to scaling factors.
Note
Displayed variables are subject to change.
Not applicable
58 3A6948D
This screen shows information about the internal operation of the flow control process.
Label Definition fP fI
Flow PID proportional term. The portion of the output pressure set point due to the immediate flow rate error.
Flow PID integral term. The portion of the output pressure set point due to the integration over time of the flow rate error.
fD fA fE
Pr
Flow PID differential term. The portion of the output pressure set point due to the change of the immediate flow rate error.
Flow PID accumulator total. The sum of the proportional, integral, and differential terms, which equals the output pressure set point to the pressure control.
Flow set point error. The difference between the flow rate set point and the measured flow rate. If the flow rate set point is higher than the measured flow rate, this value is positive and the system increases pressure. If the flow rate set point is lower than the measured flow rate, this value is negative and the system decreases pressure.
Positive value: The pressure control is allowed to raise the output current.
Negative value: The pressure control is not allowed to raise the output current.
psi psi psi psi cc/min
Not applicable
3A6948D 59
Pf
SB
Positive value: The pressure control is allowed to reduce the output current.
Negative value: The pressure control is not allowed to reduce the output current.
The internal binary control values displayed in two groups of four bits.
Group Bit Value Definition
1 1 0 Flow control is not allowed to raise the target pressure.
2
3
4
1
0
1
0
1
0
1
Flow control is allowed to raise the target pressure.
Flow control is not allowed to reduce the target pressure.
Flow control is allowed to reduce the target pressure.
Pressure control is able to reduce the system pressure.
Pressure control is not able to reduce the system pressure.
Pressure control is able to increase the system pressure.
Pressure control is not able to increase the system pressure.
2 1
2
3
4
0
1
0
0
1
0
1
Flow control is able to reduce the system flow rate.
Flow control is not able to reduce the system flow rate.
Flow rate is not high.
Flow rate is high.
Fluid slow is not stable.
Fluid flow is stable.
Not used. Always zero.
Not applicable
Not applicable
Note
Values that may be available on Modbus may be different due to scaling factors.
Note
Displayed variables are subject to change.
60 3A6948D
This screen shows information about the internal set point and flowmeter.
fS fA mB mF pI cO pS pA
Pressure sensor differential input voltage.
4-20 mA fluid control current to pressure transducer output current.
Operational fluid pressure set point.
Actual measured fluid pressure.
Operational fluid flow rate set point.
Actual measured fluid flow rate.
Input state of the fluid flowmeter.
Measured frequency of the fluid flowmeter.
mV mA psi psi cc/min cc/min
Bit
Hz
3A6948D 61
This screen shows information about the Modbus status.
W
^
^
^
Previous, previous register write address.
Previous register write address
Last register write address.
Previous, previous register read address.
^
R
Previous register read address.
Last register read address.
(no label) Count of number of register writes.
Previous, previous register write value.
Previous register write value.
Last register write value.
Previous, previous register read value.
Previous register read value.
Last register read value.
Count of number of register reads.
62 3A6948D
NOTE:
Setup Screen 4: Calibration, page 46 , for
further screen information, if needed.
• The first time the system is operated.
• Whenever new materials are used in the system, especially if the materials have viscosities that differ significantly.
• As part of regular maintenance to retain meter accuracy.
• Whenever a flow meter is serviced or replaced.
6.
Press to end the calibration.
7.
Press to get to the dispensed volume field
, then press to enter the field. Enter the amount of material in the cylinder.
8.
After the volume is entered, the system calculates the new k-factor
Screen 4.
and shows it on Setup
• Meter k-factor on
Setup Screen 4: Calibration, page 46
k-factor if desired.
screens.
, is updated automatically after the calibration procedure is completed. You also may manually edit the
• All values on this screen are in cc or cc/pulse, regardless of the units set in the other Setup
• Before calibrating the meter, be sure the system is primed with material.
• Disable alarms before calibration.
calibration again, press , move briefly to another screen, then return to Setup Screen 4 and start over. If you press without leaving the screen, the counter will continue from where it is, without clearing.
9.
Press
10. Press to exit the screen.
to exit Setup Mode.
1.
Press
2.
Press to enter Setup Mode.
to move to Setup Screen 4.
3.
Press to enter the screen.
4.
Press to begin the calibration.
5.
Dispense about 300–500 cc of material into a graduated cylinder. The amount the system measures will display in the measured volume field .
See
Setup Screen 11: Fill Mode, page 52 . By
default, the Modbus is set to Off . If you need the Modbus, set the Modbus mode to
SLAVE . The address value is between
1 and 247. The modbus address corresponds to the address of the ProControl 1KE Plus. See
Appendix A - Modbus Variable Map, page 93 , for
more information.
3A6948D 63
There are three types of events that can occur.
Events are indicated on the display by alternately flashing between the event code and the event icon.
Note
If kit 25P594, IS Light Tower ProControl 1KE
Plus, is installed, see manual 3A7521 for information on the light sequences used to indicate status.
• Alarms, indicated by , will stop the system.
Fluid and atomizing air pressures are set to zero, and the system is returned to Standby mode.
• Deviations, indicated by , require attention but will not stop the system.
• Advisories, indicated by , will not stop the system.
If multiple events are active, the display will cycle through the events at the highest priority level. For instance, if F3, P3, and MF are all active, the display will cycle between only F3 and P3.
Alarms only) If Alarm Auto Clear is enabled, the system will not log the same alarm twice. For example, if the system goes back and forth between low flow (F2) and normal, the system will log this error only once to keep the log from filling up before the operator corrects the condition.
If Alarm Auto Clear is not enabled, each alarm will log only once if the operator corrects the condition and then clears the alarm. The alarm will log twice if the operator clears the alarm before correcting the condition.
Note
In Pressure Control or Flow Control mode, the setpoint target is not modified to keep system within the F2 and F3 range configured in
Setup Screen 5: Flow Rate, page 47
, or within the P2 and P3 range configured in
Setup Screen 7: Pressure, page 49
.
The alarms conditions are monitored independently of the control system.
The following table explains the error type that is associated with each error code and icon. Press to clear alarm after the cause has been addressed.
Code Icon Summary
F3
F2
P3
P2
High Flow Selectable event level. Active when the flow rate is higher than the user-set maximum for one second.
Low Flow Selectable event level. Active when the flow rate is lower than the user-set minimum for a variable time depending on operating conditions.
High
Pressure
Low
Pressure
Selectable event level. Active when the fluid pressure is higher than the user-set maximum for one second.
Selectable event level. Active when the fluid pressure is lower than the user-set minimum for one second.
Adjust flow rate, maximum flow limit, or disable alarm
(
Setup Screen 5: Flow Rate, page 47 ).
Press to clear alarm. The alarm will not clear until the flow rate is within limits.
Adjust flow rate, minimum flow limit, or disable alarm
(
Setup Screen 5: Flow Rate, page 47 ).
Press to clear alarm. The alarm will not clear until the flow rate is within limits.
Adjust pressure, maximum pressure limit, or disable alarm
(
Setup Screen 7: Pressure, page 49
).
Press to clear alarm. The alarm will not clear until the pressure is within limits.
Adjust pressure, minimum pressure limit, or disable alarm
(
Setup Screen 7: Pressure, page 49
).
Press to clear alarm. The alarm will not clear until the pressure is within limits.
64 3A6948D
Code Icon Summary
QT Dose
Time
SN
SP
B4
B1
F6
P6
EU
MF
G2
Minimum
Fill
Volume
Minimum
Flush
Volume
Job
Dispense
High
Job
Dispense
Low
Runaway
Flow
Runaway
Pressure
System
Idle
Maintenance
Counter
Gun Off
Setpoint
Alarm only. Active when the gun trigger is activated but no fluid flow is detected.
Alarm only. Active when the user-set fill volume is not achieved in a fill cycle.
Alarm only. Active when the user-set flush volume is not achieved in a flush cycle.
Alarm only. Active when the logged job spray volume is more than the threshold setpoint.
Alarm only. Active when the logged job spray volume is less than the threshold setpoint.
Determine cause of fluid flow stoppage.
Increase fill drive percentage, fill time, or check fluid supply
(
Setup Screen 10: PID Data, page 52
).
Press to clear alarm.
Increase flush drive percentage, flush time, or check fluid supply
(
Setup Screen 11: Fill Mode, page 52
).
Press to clear alarm.
Adjust flow rate, spray time, maximum volume limit, or disable alarm
(
Setup Screen 1: Job Target, page 44
).
Press to clear alarm.
Adjust flow rate, spray time, minimum volume limit, or disable alarm
(
Setup Screen 1: Job Target, page 44
).
Press to clear alarm.
Determine cause of fluid control failure.
Press to clear alarm.
Deviation only. Active when using flow control and the flow target is not achievable.
Deviation only. Active when using pressure or flow control and the pressure target is not achievable.
Advisory only. Active when in
Dispense mode and the gun trigger has not been activated for the user-set timeout time. Fluid pressure is dropped to zero.
Advisory only. Active when the maintenance totalizer reaches the user-set maintenance target.
Determine cause of fluid control failure.
Press to clear alarm.
Dispense pressure will resume immediately once the gun trigger is activated. The advisory will automatically clear. Press to clear alarm.
Perform maintenance. Reset to zero using (
). Press alarm.
to clear
Advisory only. The flow rate setpoint was changed to a lower value while the gun was off.
Instead of predicting a pressure target, the system will predict a current output target to the I/P. It may take extra time to stabilize in this situation.
Activate spraying. Press to clear alarm.
3A6948D 65
Before updating the software, flush the system to remove curable material. For more information, see
Updates to software may erase the configuration memory. Before you update the software, Graco recommends you make note of the configuration of each setup screen and the current software version, which is displayed on the
.
An easy way to do this is to take a picture of each setup screen.
Software updates are installed using a software token
(PN 25B324). Manual 3A1244 will accompany any necessary software updates. Follow all instructions and warnings in Manual 3A1244 to update your
ProControl 1KE Plus software.
The following are the abbreviated steps to update the software. Refer to Manual 3A1244 for complete details.
1.
Power down the system.
2.
Remove the access cover.
3.
Insert software token PN 25B324.
4.
Power up the system.
5.
Wait for the software to install. The update screen may be different than the screen shown in Manual 3A1244.
6.
Remove the token.
7.
Press the arrow to start the software. It can take up to one minute to re-initialize the memory.
8.
Navigate to the Password screen to verify that the new version of software is installed.
9.
Power down the system.
10. Reinstall the cover.
After the software update is complete:
• Compare the setting screens to your notes or pictures and adjust settings, as needed.
• Verify manual operations, such as load, flush, and spray to validate correct operation of the sensors and controls.
• If system is connected to a PLC, verify PLC operations as necessary, such as load, flush, spray, Job Log retrieval to validate correct operation of the sensors and controls.
• If system is connected to a PLC, some Modbus registers may have been changed or added.
Modify PLC programming, if needed.
66 3A6948D
ProControl 1KE Plus is completely dark.
Power is not on.
Loose or disconnected power cable.
Hardware failure.
ProControl 1KE Plus has power but does not function.
Pressure or Flow Rate reads 0 when fluid is flowing.
Loose or disconnected flow meter/pressure transducer cable.
Turn power supply on.
Tighten or connect cable.
Replace ProControl 1KE Plus.
Check the digital input/output cable going to/from the meter.
3A6948D 67
Pressure or Flow Rate reads “— — —” all the time.
Units in Setup are set to
NONE, indicating that the system has no pressure transducer and/or fluid meter.
No flow reading with
Coriolis meter
Choose preferred units for each device present. See
Setup Screen 6: Pressure Transducer, page 48 , for
pressure,
Setup Screen 4: Calibration, page 46
, for flow rate.
Refer to Coriolis Meter Kits manual 313599.
A digital multimeter with Resistance (Ohms) and Diode
Check functions can be used to verify if the 17A450 adapter works properly. These measurements apply
ADCM or to the Coriolis meter. For measurements when installed, see the cause: Graco 17A450 adapter
68
3
4
5
2
2
1
0 to 2 Ohm
2.2K +/- 0.2
kOhm
2.2K +/- 0.2
kOhm
3
4
5
4
1
1
4
Open - OL
0.67 +/- 0.3V
A digital multimeter with Resistance (Ohms) and Diode
Check functions can be used to verify if the 17A450 adapter works properly. These measurements apply and to the Coriolis meter. Take these readings with both the ADCM and the Coriolis powered off.
2
2
1
0 to 2 Ohm
2.1K +/- 0.2
kOhm
2.1K +/- 0.2
kOhm
4
1
1
4
2.2 +/- 0.3V
0.67 +/- 0.3V
3A6948D
Inaccurate flow reading.
Inaccurate pressure range.
Display readout faulty.
Communication failure.
Fluid is not flowing.
Low flow.
Flow control no settling to setpoint.
Flow control over-driving to high flow rates.
Higher fluid pressure cannot be achieved.
Faulty flow meter sensor or meter.
Meter needs calibration.
Replace sensor or meter.
Wrong transducer is selected.
Offset or slope are set incorrectly.
Calibrate meter. See
Calibrate the Meter, page 63 .
Choose the correct transducer from the options in
Setup Screen 6: Pressure Transducer, page 48
Review and correct settings for the pressure offset (mV) and slope (mV/bar). See
Setup Screen 6: Pressure Transducer, page 48 .
Excessive static discharge.
Replace ProControl 1KE Plus.
Ambient temperature too high.
Lower ambient temperature.
Incorrect data addresses.
Check address configuration.
Incorrect communication parameters.
Incorrect cabling.
Check communication parameters.
Clogs in fluid line or in meter.
Check cabling and wiring. See
Clean fluid line and/or meter. Consult meter manual
(see
).
Gears worn or damaged.
Service meter. Consult meter manual (see
Increase incoming air pressure.
Inadequate air supply through the I/P transducer.
Pressure or flow PID
K-Factors are not tuned.
Gun Trigger signal not synchronized with fluid flow valve.
See
Setup Screen 10: PID Data, page 52
For automatic operation, verify the pressure switch electrical connection. Check that the switch closes when the gun fluid solenoid is activated.
Low fluid pressure after the fluid regulator.
For manual operation, verify the air flow switch electrical connection. Check that the switch closes when the gun trigger is activated.
The flow control may activate when the atomizing air is flowing without any fluid flow.
• If this is because of a dusting procedure, the flow control may over-drive the fluid pressure until it can converge.
• If this is because of system startup, this is normal and the flow control should eventually react.
Check incoming system air pressure. This should be at least 10 psi (0.7 bar) higher than the target fluid pressure.
Check incoming fluid pressure from pump. This should be at least 10 psi (0.7 bar) higher than the target fluid pressure. The pump must be able to supply this pressure at the target flow rate.
Check I/P pilot line output pressure.
Check power output of the barrier that powers the system. At 20 mA, for 100 psi (6.9 bar), this should be at least 13.5 volts.
3A6948D 69
Unstable flow with
Coriolis meter.
Coriolis meter shows flow when no fluid is flowing.
Regulator pilot drives to high pressure.
Presence of bubbles or sediment.
Low-flow cutoff may be set too low.
Check for upwards settling of air bubbles.
Check for downwards settling of solids, such as metallics.
Consult the Coriolis Meter manaul (see
Increase the low-flow cutoff to just above the highest false flow rate that was observed.
Inadequate fluid supply in pressure control or flow control mode.
Check pressure and flow capabilities of the fluid supply.
70 3A6948D
The LEDs on the bottom of the ProControl 1KE give important information about system function.
Green On
Yellow
Red solid
Red flashing
Red flashing slowly
ProControl 1KE Plus is powered up.
Internal communication in progress.
ProControl 1KE failure. See Troubleshooting.
Software is updating.
Token error; remove token and upload software token again.
3A6948D 71
Replace the battery only if the clock stops functioning after disconnecting power or a power failure.
5.
Use a flathead screwdriver to pry out the old battery.
Sparking can occur when changing the battery.
Replace the battery only in a non-hazardous location, away from flammable fluids or fumes.
To avoid damage to the circuit board, wear Part No.
112190 grounding strap, and ground appropriately.
1.
Disconnect power.
2.
Remove the module from the bracket.
3.
Attach the grounding strap.
4.
Remove 4 screws, and then remove the access cover.
approved container and according to applicable local guidelines.
6.
Replace with new battery. Ensure battery fits under connector tabs before snapping other end in place.
replacement.
7.
Reassemble access cover and screws.
8.
Snap the module back into the bracket.
72 3A6948D
10
65
68
81
90▲
8
9
Ref Part
5 15U749
289813
114182
▲
19A908
—
BRACKET, wall-mount meter
METER, G3000 assembly gear
SCREW, hex-flange machine
CABLE, meter; 1.5 m
MODULE, ADCM
277853
244524
BRACKET, booth control mounting
WIRE, ground assembly with clamp
16P265 LABEL, warning safety (sheet includes labels in English, French, and Spanish)
Replacement safety labels are available at no cost.
1
1
1
1
1
1
1
2
✔
✔
✔
✔
✔
✔
✔
✔
✔
✔
✔
✔
3A6948D 73
74 3A6948D
49
50
51
52
54
55
56
57
58
35
36
37
38
40
48
17
25
26
27
28
34
10
11
12
13
14
16
7
8
9
5
6
Ref Part
1
2
19A780 PLATE, fluid mounting
25B213 COVER, fluid panel
4 551787 SCREW, button head cap
19A781
104123
BRACKET, inlet, fluid
WASHER, spring lock
GC2248 SCREW, socket head cap; .250 x .50
289813 METER, G3000 assembly gear
114182 SCREW, hex-flange machine
19A908 CABLE, meter; 1.5 m
24C375
501867
114339
REGULATOR, 1:1 ratio fluid
VALVE, check
FITTING, swivel union; 1/4 npt
191929 ADAPTER
112906 WASHER, spring lock (not shown)
GC2188
16P784
18A989
15T937
116007
111502
18B053
SCREW, socket head cap; .190 x .500
TRANSDUCER, miniature I/P
BRACKET, pressure switch mounting
FITTING, swivel elbow; 1/4 npt x 5/32 t
112925 SCREW, button head cap
513937 SWITCH, pressure
103982 SCREW, pan head machine
NUT, lock
FITTING, tube
CABLE, I/P
C38163 WASHER, #10 ext. tooth lock
19A785 MANIFOLD, air; 1/4 npt, 4 port
127023 SCREW, socket head cap; 10–32
19A910
116473
18B604
18B605
18B606
114380
FITTING, nipple; 1/4 npt, 3 inch
VALVE, vented; 2–way
100721 PLUG, pipe
18A988 FITTING, Y; 1/4 npt(m) x 5/32 tube
BRACKET, cable mounting
GLAND, multiple entry cable
PLUG, 5mm, cable gland
SCREW, M5 x 25mm, socket head cap
1
3
1
2
1
4
2
1
1
1
1
4
1
4
4
25B285 25B286 25B287 25B288
1 1 1 1
1
4
1
4
1
4
1
4
—
1
2
1
2
1
2
—
—
2
1
2
1
1
1
4
1
1
2
1
1
2
1
—
—
2
1
2
1
—
4
2
1
1
2
—
—
—
1
—
—
1
4
2
1
1
2
—
—
—
—
—
—
—
4
2
1
1
2
1
2
2
1
2
1
2
2
1
4
4
1
1
4
1
4
4
1
1
4
1
1
1
4
1
4
4
2
1
1
3
1
1
1
4
2
2
1
1
3
1
1
1
5
2
1
3
1
2
1
5
2
1
1
3A6948D 75
72
78
81
63
64
65
Ref Part
59
62
105332
116343
NUT, M5 lock
SCREW, ground
68
19A945
103546
CLIP, cable tie-down
STRAP, wire tie
25B283 MODULE, ADCM (includes ref. 68, 81, and 90)
277853 BRACKET, booth control mounting
(included with ref. 65)
18B393 CABLE, I/P, 2m, M12, 8 pin
551731 TUBE, 5/32 OD (quantity in ft.)
244524 WIRE, ground assembly with clamp
(included with ref. 65)
90▲
▲
16P265 LABEL, warning safety (sheet includes labels in English, French, and Spanish; included with ref. 65)
Replacement safety labels are available at no cost.
25B285 25B286 25B287 25B288
2
2
2
2
2
2
2
2
9
9
1
9
9
1
9
9
1
9
9
1
1 1 1 1
1
1.330
2
1
1
0.960
2
1
1
1.330
2
1
1
0.960
2
1
76 3A6948D
3A6948D 77
40
41
42
43
44
45
46
28
34
35
36
37
38
17
25
26
27
1
2
4
16
53
54
55
56
57
47
48
49
50
51
52
58
59
62
19A780 PLATE, fluid mounting
25B213 COVER, fluid panel
551787 SCREW, button head cap
112906 WASHER, spring lock (not shown)
GC2188 SCREW, socket head cap; .190 x .500
16P784 TRANSDUCER, miniature I/P
18A989 BRACKET, pressure switch mounting
15T937 FITTING, swivel elbow; 1/4 npt x 5/32 t
112925 SCREW, button head cap
513937
103982
SWITCH, pressure
SCREW, pan head machine
116007 NUT, lock
111502 FITTING, tube
18B053 CABLE, I/P
C38163 WASHER, #10 ext. tooth lock
19A899 SPACER, #10; 2 inches
120435 REGULATOR, remote piloted
514930 SCREW, socket head cap
C38211 FITTING, tube
112538
191892
108190
FITTING, street elbow; 90°
FITTING, street elbow; 90°
GAUGE, air pressure
19A785 MANIFOLD, air; 1/4 npt, 4 port
127023 SCREW, socket head cap; 10–32
19A910 FITTING, nipple; 1/4 npt, 3 inch
116473
100721
120389
VALVE, vented; 2–way
PLUG, pipe
FITTING, tube
18A988 FITTING, Y; 1/4 npt(m) x 5/32 tube
18B604 BRACKET, cable mounting
18B605 GLAND, multiple entry cable
18B606 PLUG, 5mm, cable gland
114380 SCREW, M5 x 25mm, socket head cap
105332 NUT, M5 lock
116343 SCREW, ground
78
1
4
4
4
2
1
1
4
4
1
1
2
1
2
1
1
3
4
8
1
1
1
1
5
1
1
2
1
1
2
1
1
2
2
2
3A6948D
72
78
79
81
90▲
63
64
65
68
▲
19A945 CLIP, cable tie-down
103546 STRAP, wire tie
25B283 MODULE, ADCM (includes ref. 68, 81, and 90)
277853 BRACKET, booth control mounting (included with ref. 65)
18B393 CABLE, I/P, 2m, M12, 8 pin
551731
054106
TUBE, 5/32 OD (quantity in ft.)
TUBE, .375 OD (quantity in ft.)
244524 WIRE, ground assembly with clamp (included with ref. 65)
16P265 LABEL, warning safety (sheet includes labels in English, French, and
Spanish; included with ref. 65)
Replacement safety labels are available at no cost.
1
1.160
0.760
2
1
1
1
9
9
3A6948D 79
80 3A6948D
2
4
Ref Part
1 19A780 PLATE, fluid mounting
25B213 COVER, fluid panel
5
551787 SCREW, button head cap
19A781 BRACKET, inlet, fluid
6
7
8
9
104123 WASHER, spring lock
GC2248 SCREW, socket head cap; .250 x .50
289813 METER, G3000 assembly gear
114182 SCREW, hex flange machine
10
11
12
13
14
15
19A908 CABLE, meter; 1.5
m
24C375 REGULATOR, 1:1 ratio fluid
501867 VALVE, check
114339 FITTING, swivel union; 1/4 npt,
191929 ADAPTER
19A782 BRACKET, air/fluid mounting
16
17
18
19
20
21
22
23
24
112906 WASHER, spring lock
GC2188 SCREW, socket head cap; .190 x
.500
19A788 WASHER, internal tooth lock; 3/4 inch
19A783 FITTING, fluid pressure sensor
19A789 NUT, hex jam; stainless steel,
3/4–16
166846 FITTING, Adapter
18F889 HOSE, coupled; 1.0
ft, ptfe
16H282 TRANSDUCER, control pressure
111316 PACKING, o-ring
25B290 25B291 25B292 25B293 25B294 25B295
1 1 1 1 1 1
1
4
1
2
2
—
—
—
1
—
—
1
1
7
5
2
1
1
1
1
1
1
1
4
—
—
—
—
—
—
—
—
—
—
1
7
5
2
1
1
1
—
1
1
1
4
1
2
2
1
2
1
1
1
1
1
1
7
5
2
1
1
1
1
1
1
1
4
1
2
2
1
2
1
—
1
—
—
1
7
5
2
1
1
1
—
1
1
1
4
1
2
2
—
—
—
1
—
—
1
1
7
5
2
1
1
1
1
1
1
1
4
—
—
—
—
—
—
—
—
—
—
1
7
5
2
1
1
1
—
1
1
3A6948D 81
52
53
54
36
37
38
40
Ref Part
25 16P784 TRANSDUCER, miniature I/P
26
27
18A989 BRACKET, pressure switch mounting
15T937 FITTING, swivel elbow; 1/4 npt x
5/32 t
28
29
30
31
32
33
34
35
112925 SCREW, button head cap
101641 FITTING, bulkhead
111763 FITTING, elbow; 1/4 npt
18B571 KIT, AFS
121141 FITTING, swivel elbow; 3/8 t, 1/4 npt(m)
113029 NIPPLE, 1/4 x 1/4 npt
513937 SWITCH, pressure
103982 SCREW, pan head machine
116007 NUT, lock
111502 FITTING, tube
18B053 CABLE, I/P
48
49
50
51
C38163 WASHER, #10 ext.
tooth lock
19A785 MANIFOLD, air; 1/4 npt, 4 port
127023 SCREW, socket head cap; 10–32
19A910 FITTING, nipple; 1/4 npt, 3 inch
116473 VALVE, vented;
2–way
100721 PLUG, pipe
120389 FITTING, tube
55
56
18A988 FITTING, Y; 1/4 npt(m) x 5/32 tube
18B604 BRACKET, cable mounting
18B605 GLAND, multiple entry cable
25B290 25B291 25B292 25B293 25B294 25B295
1 1 1 1 1 1
1
2
2
1
1
1
1
1
1
4
4
1
1
4
1
2
1
1
2
1
1
1
1
1
2
2
1
1
1
1
1
1
4
4
1
1
4
1
2
1
1
2
1
1
1
1
1
2
2
1
1
1
1
1
1
4
4
1
1
4
1
2
1
1
2
1
1
1
1
1
2
2
1
1
1
1
1
1
4
4
1
1
4
1
2
1
1
2
1
1
1
1
1
2
2
1
1
1
1
1
1
4
4
1
1
4
1
2
1
1
2
1
1
1
1
1
2
2
1
1
1
1
1
1
4
4
1
1
4
1
2
1
1
2
1
1
1
1
82 3A6948D
Ref Part
57 18B606 PLUG, 5mm, cable gland
58
59
62
114380 SCREW, M5 x
25mm, socket head cap
105332 NUT, M5 lock
116343 SCREW, ground
63
64
65
68
19A945 CLIP, cable tie-down
103546 STRAP, wire tie
25B283 MODULE, ADCM
(includes ref. 68,
81, and 90)
277853 BRACKET, booth control mounting
(included with ref.
65)
69
72
73
78
79
81
19A906 CABLE, M12, reverse key, non-IS
18B393 CABLE, I/P, 2m,
M12, 8 pin
18B570 CABLE, ADCM to
AFS
551731 TUBE, 5/32 OD
(quantity in ft.)
054106 TUBE, .375 OD
(quantity in ft.)
244524 WIRE, ground assembly with clamp (included with ref. 65)
25B290 25B291 25B292 25B293 25B294 25B295
3 3 2 2 3 3
2
2
2
9
9
1
1
1
1
1
1.330
0.620
2
2
1
1
1
1
0.960
0.620
2
90▲ 16P265 LABEL, warning safety (sheet includes labels in
English, French, and Spanish; included with ref.
65)
▲
1 1
Replacement safety labels are available at no cost.
2
2
9
9
1
2
2
2
9
9
1
1
1
1
1
1.330
0.620
2
1
2
2
2
9
9
1
1
1
1
1
0.960
0.620
2
1
2
2
2
9
9
1
1
1
1
1
1.330
0.620
2
1
2
2
2
9
9
1
1
1
1
1
0.960
0.620
2
1
3A6948D 83
84 3A6948D
Ref Part
1 19A780 PLATE, fluid mounting
2
4
25B213 COVER, fluid panel
551787 SCREW, button head cap
5
6
7
8
19A781 BRACKET, inlet, fluid
104123 WASHER, spring lock
GC2248 SCREW, socket head cap; .250 x
.50
289813 METER, G3000 assembly gear
9
10
11
12
13
114182 SCREW, hex-flange machine
19A908 CABLE, meter;
1.5 m
24C375 REGULATOR, 1:1 ratio fluid
501867 VALVE, check
114339 FITTING, swivel union; 1/4 npt,
14
15
16
17
18
19
20
21
22
191929 ADAPTER
19A782 BRACKET, air/fluid mounting
112906 WASHER, spring lock
GC2188 SCREW, socket head cap; .190 x
.500
19A788 WASHER, internal tooth lock;
3/4 inch
19A783 FITTING, fluid pressure sensor
19A789 NUT, hex jam; stainless steel,
3/4–16
166846 FITTING, Adapter
18F889 HOSE, coupled;
1.0 ft, ptfe
25B296 25B297 25B298 25B299 25B322 25B323
1 1 1 1 1 —
1
4
1
2
2
1
2
1
1
1
1
1
1
11
5
2
1
1
1
1
1
4
1
2
2
1
2
1
—
1
—
—
1
11
5
2
1
1
1
—
1
4
1
2
2
—
—
—
1
—
—
1
1
11
5
2
1
1
1
1
1
4
—
—
—
—
—
—
—
—
—
—
1
11
5
2
1
1
1
—
1
4
1
2
2
—
—
—
—
—
—
—
1
7
5
2
1
1
1
1
—
—
—
—
—
—
—
—
—
—
—
—
—
—
—
—
—
—
—
—
3A6948D 85
36
37
38
40
Ref Part
23 16H282 TRANSDUCER, control pressure
24
25
111316 PACKING, o-ring
16P784 TRANSDUCER, miniature I/P
26
27
18A989 BRACKET, pressure switch mounting
15T937 FITTING, swivel elbow; 1/4 npt x
5/32 t
28
29
30
31
32
33
34
35
41
42
43
44
45
46
112925 SCREW, button head cap
101641 FITTING, bulkhead
111763 FITTING, elbow;
1/4 npt
18B571 KIT, AFS
121141 FITTING, swivel elbow; 3/8 t, 1/4 npt(m)
113029 NIPPLE, 1/4 x 1/4 npt
513937 SWITCH, pressure
103982 SCREW, pan head machine
116007 NUT, lock
111502 FITTING, tube
18B053 CABLE, I/P
C38163 WASHER, #10 ext. tooth lock
19A899 SPACER, #10; 2 inches
120435 REGULATOR, remote piloted
514930 SCREW, socket head cap
C38211 FITTING, tube
112538 FITTING, street elbow; 90°
191892 FITTING, street elbow; 90°
25B296 25B297 25B298 25B299 25B322 25B323
1 1 1 1
— —
1
2
2
5
4
1
1
1
1
1
2
8
8
2
2
4
4
1
4
2
1
1
1
2
2
3
4
1
1
1
1
1
2
8
8
2
2
4
4
1
4
2
1
1
1
2
2
5
4
1
1
1
1
1
2
8
8
2
2
4
4
1
4
2
1
1
1
2
2
5
4
1
1
1
1
1
2
8
8
2
2
4
4
1
4
2
1
1
—
—
1
1
2
1
1
1
1
1
1
4
4
1
1
4
—
—
—
—
—
—
—
1
1
3
2
—
—
—
—
—
1
4
4
1
1
—
4
1
4
2
1
1
86 3A6948D
59
62
63
52
53
54
Ref Part
47 108190 GAUGE, air pressure
48
49
50
51
19A785 MANIFOLD, air;
1/4 npt, 4 port
127023 SCREW, socket head cap; 10–32
19A910 FITTING, nipple;
1/4 npt, 3 inch
116473 VALVE, vented;
2–way
55
100721 PLUG, pipe
120389 FITTING, tube
18A988 FITTING, Y; 1/4 npt(m) x 5/32 tube
18B604 BRACKET, cable mounting
56
57
58
64
65
68
69
72
73
78
18B605 GLAND, multiple entry cable
18B606 PLUG, 5mm, cable gland
114380 SCREW, M5 x
25mm, socket head cap
105332 NUT, M5 lock
116343 SCREW, ground
19A945 CLIP, cable tie-down
103546 STRAP, wire tie
25B283 MODULE, ADCM
(includes ref. 68,
81, and 90)
277853 BRACKET, booth control mounting
(included with ref.
65)
19A906 CABLE, M12, reverse key, non-IS
18B393 CABLE, I/P, 2m,
M12, 8 pin
18B570 CABLE, ADCM to
AFS
551731 TUBE, 5/32 OD
(quantity in ft.)
25B296 25B297 25B298 25B299 25B322 25B323
1 1 1 1
—
1
1
2
1
1
1
1
2
1
1
1
2
2
2
9
9
1
1
1
2
1
2.490
1
2
1
1
1
1
2
1
1
1
2
2
2
9
9
1
1
1
2
1
2.120
1
2
1
1
1
1
2
1
1
2
2
2
2
9
9
1
1
1
2
1
2.490
1
2
1
1
1
1
2
1
1
2
2
2
2
9
9
1
1
1
2
1
2.120
1
2
1
1
1
1
1
1
1
4
2
2
2
9
9
—
—
—
1
1
1.0
—
—
—
—
—
1
1
—
—
—
—
—
—
—
—
—
—
—
1
—
2.0
3A6948D 87
Ref Part
79 054106 TUBE, .375 OD
(quantity in ft.)
81 244524 WIRE, ground assembly with clamp (included with ref. 65)
90▲
91
▲
25B296 25B297 25B298 25B299 25B322 25B323
1.110
1.110
1.110
1.110
1.0
1.0
2 2
16P265 LABEL, warning safety (sheet includes labels in
English, French, and Spanish; included with ref.
65)
—
LABEL,
ProControl 1KE
Plus
1
—
1
—
Replacement safety labels are available at no cost.
2
1
—
2
1
—
1
1
1
—
1
—
88 3A6948D
Not all accessories and kits are approved for use in hazardous locations. To avoid serious injury or death from fire and explosion and electrical shock, refer to the specific accessory and kit manuals for approval details.
Part No.
Description
19Y499 IS Power Cable, 50 ft (15 m), for power supply
19Y502 IS Power Cable, 100 ft (30 m), for power supply
18B244 IS Meter Cable Extension, 50 ft (15 m), meter cable, port #4
16V381 IS Sensor Cable, 50’ (15 m), ports #7 and #10
16V071 IS Control Cable, 50’ (15 m), ports #8 and #9
Part No.
Description
16V680 Non-Intrinsically Safe (Non-IS) Power
Supply, 100-240 VAC input, 50/60 Hz,
15 VDC output
16M167 Intrinsically Safe (IS) Power Supply
Module, 100–240 VAC input. Includes
50 ft (15 m) IS power cable
26C724 G-Barrier Intrinsically Safe (IS) Power
Module, provides up to three IS power output circuits. 100-240 VAC, 50/60 Hz, input. Includes one IS 50 ft (15 m) IS power cable
Part No.
Description
17T898 10 ft (3 m) Fiber Optic Cable
16M172 50 ft (15 m) Fiber Optic Cable
16M173 100 ft (30 m) Fiber Optic Cable
Part No.
Description
18A987 Meter Cable Extension, 50 ft (15 m), for meter cable, port #4
16V069 Non-IS Power Cable, 50 ft (15 m)
16V070 Non-IS Power Cable, 100 ft (30 m)
16V380 Non-IS Sensor Cable, 50’ (15 m), ports
#7 and #10
16P791 Non-IS Control Cable, 50’ (15 m), ports
#8 and #9
18A986 Indicator Light Cable, 50’ (15 m), fluid panel to light
Part No.
Description
25B322 Basic Upgrade Kit to convert a previous generation ProControl1KE to the new
1KE Plus. Kit includes software token and fluid plate with basic hardware.
User must provide ADCM display,
I/P transducer, fluid meter, fluid regulator, pressure transducer, and power supply from original ProControl
1KE or purchase separately. See
Closed Loop Fluid Pressure/Flow and
Gun Atomizing Air Control, page 84 ,
for included parts.
See
Appendix B - Upgrading ProControl 1KE to ProControl 1KE Plus, page 101 , for
upgrade instructions. Gun air control is not included. If needed, order 25B323 separately for air control hardware.
3A6948D 89
25B323 Air Control Upgrade Kit adds air control to a ProControl 1KE Plus fluid plate.
See
Closed Loop Fluid Pressure/Flow and Gun Atomizing Air Control, page 84 ,
for included parts.
See
Appendix B - Upgrading ProControl 1KE to ProControl 1KE Plus, page 101 , for
upgrade instructions.
25B325 Pressure Switch Conversion Kit converts
ProControl 1KE Plus fluid plate gun air flow switch to a pressure switch for detection of gun on conditions.
Part No.
Description
25B324 ProControl 1KE Plus Software Token Kit with instruction manual 3A1244.
Part No.
Description
25P594 IS Indicator Light Tower, 2 color light with bracket and cables
Part No.
Description
289813
*
G3000 Meter — Positive displacement, gear flow meter, 0.02 to 1.0 gpm (75 to 3800 cc/min), for low to medium viscosity materials
280560
*
258718
*
HG6000 Meter — Positive displacement, helical gear flow meter, 0.013 to 6.0
gpm (50 to 22,712 cc/min), for high flow, high viscosity materials
S3000 Solvent Meter — Positive displacement, gear flow meter, 0.01 to
0.5 gpm (38 to 1900 cc/min), for light viscosity materials
25P592 Pressure Transducer Kit, 100 psi (7 bar, 0.7 MPa) Used to measure fluid pressure
25P593 High Pressure Sensor Kit, 4500 psi
(310 bar, 31.0 MPa) Used to convert to higher pressure operation
25B359 Medium Pressure Sensor Kit, 2000 psi
(138 bar, 13.8 MPa) Used to convert to higher pressure operation
* See manual 308778 for meter replacement components, including meter sensor.
Part No.
Description
570122 Dual Unit Air Filter and Regulator
Assembly with 5 μm filter, manual drain, and mounting bracket
Non-intrusive mass flow meter, for abrasive and filled materials and a range of flow rates.
Part No.
Description
24N525 1/4 in. Coriolis Flow Meter Kit
Part No.
Description
24R086 Fiber Optic to Serial Converter module with 24V, 2 amp power supply and enclosure, commicates from ProControl
1KE Plus to a PLC. See manual 332356 for details.
24N978 Fiber Optic to Serial Converter, communicates from the ProControl 1KE
Plus to a PLC. See manual 332356 for details.
Part No.
Description
24C375 1:1 Low Flow Regulator
24E471 1:2 Low Flow Regulator
24E472 1:3 Low Flow Regulator
234266 High Flow Regulator
90 3A6948D
289813,
16H282,
SENSOR
19A908,
M12 5 PIN CABLE
TO ADCM PORT #4
19A906,
M12 5 PIN CABLE
TO ADCM PORT #7
116343,
GROUND
SCREW
18B053, I/P CABLE
513937,
PRESSURE SWITCH,
COM1
NO3
NC2
16P784,
1
2
3
BLUE
1, WHITE, NC
2, BROWN, NC
3, GREEN, NC
4, YELLOW, NC
5, GRAY
6, PINK, NC
7, BLUE
8, DRAIN, NC
WHITE, PIN 1
GREEN, PIN 3
YELLOW, PIN 4
GRAY, PIN 5
PINK, PIN 6
BLUE, PIN 7
18B393,
M12 8 PIN CABLE,
TO ADCM PORT #8
GREEN/YELLOW
18B053, I/P CABLE
513937,
PRESSURE SWITCH,
GUN AIR CONTROL
COM1
NO3
NC2
16P784,
GUN AIR CONTROL I/P
1
2
3
18B571,
AIR FLOW SWITCH
ASSEMBLY
GREEN/YELLOW
BLUE
1, WHITE, NC
2, BROWN, NC
3, GREEN, NC
4, YELLOW, NC
5, GRAY
6, PINK, NC
7, BLUE
8, DRAIN, NC
WHITE, PIN 1
GREEN, PIN 3
YELLOW, PIN 4
GRAY, PIN 5
PINK, PIN 6
BLUE, PIN 7
18B393,
M12 8 PIN CABLE,
TO ADCM PORT #9
18B570,
M12 5 PIN CABLE
TO ADCM PORT #10
3A6948D 91
92 in. (mm)
9.5
(241.3) in. (mm)
9.0
(228.6) in. (mm)
0.5 (12.7)
16.6
(420.9)
8.7
(221.2)
7.2 (183) 6.0 (152)
4.5 (114.8)
2.8 (71) in. (mm)
8.5 x adjustable from 5.0–8.0
(212.5 x 127.0–203.2)
15.1 x 6.7
(382.8 x 170.2))
2.5 x 3.0
(64 x 76) in. (mm)
0.5 (12.7) in. (mm)
1.5 (38.1)
0.31 (7.9)
0.28 (7.0) n/a n/a
3A6948D
Appendix A - Modbus Variable Map
401040
401042
401044
401072
401074
401076
401078
401080
401082
401084
401086
Software Version Major
Software Version Minor
Software Version Build
Serial Number String - Bytes 0-3
Serial Number String - Bytes 4-7
Serial Number String - Bytes 8-11
Serial Number String - Bytes 12-15
Serial Number String - Bytes 16-19
Serial Number String - Bytes 20-23
Serial Number String - Bytes 24-27
Serial Number String - Bytes 28-31
Read Only
Read Only
Read Only
Read Only
Read Only
Read Only
Read Only
Read Only
Read Only
Read Only
Read Only
32 Bit
32 Bit
32 Bit
32 Bit
32 Bit
32 Bit
32 Bit
32 Bit
32 Bit
32 Bit
32 Bit
String, 4 Bytes
String, 4 Bytes
String, 4 Bytes
String, 4 Bytes
String, 4 Bytes
String, 4 Bytes
String, 4 Bytes
String, 4 Bytes
String, 4 Bytes
String, 4 Bytes
String, 4 Bytes
3A6948D 93
Appendix A - Modbus Variable Map
All registers are 32-bit.
Address
400300
400302
400304
400306
400308
Description
Fluid setpoint as percentage of 4 to 20 mA range
Fluid setpoint as drive current
Fluid setpoint as pressure
Fluid setpoint as flow rate
Atomizing air setpoint as percentage of 4 to 20 mA range
400310
400312
400314
Unused
Unused
Unused
Read/Write
Read/Write
Read/Write
Read/Write
Read/Write
Note
These are the registers a PLC writes to drive the set point. For the registers a PLC receives back, see
.
Percent
Low High
0 99.9
Scaled as 1% =
65536
Active when 403094
= 0 uA bar
0
0
32000
32-bit
See
1 mA = 1000
Active when 403094
= 3
See
Scaled as 1 bar =
65536
Active when 403094
= 1 cc/min
Percent
0
0
65535
99.9
See
Active when 403094
= 2
See
Scaled as 1% =
65536
See
94 3A6948D
Appendix A - Modbus Variable Map
All registers are 32-bit.
Address Description
402000 Date, Year
402002
402004
Date, Month
Date, Day
402006
402008
402010
402012
402014
402016
402018
402020
402022
Time, Hour
Time, Minute
Read/Write
Read/Write
Read/Write
Time, Second
Alarms Needing
Acknowledgment
Current Grand Total
Read/Write
Read
Current Batch Total Read/Write
Current Maintenance Total Read/Write
Current Flow Rate
Current Pressure
Read/Write
Read/Write
Read/Write
Read
Read
402024
402026 Read/Write
402028
402030
402032
Unused
Calibration Mode
Calibration, Measured
Volume
Calibration, Actual
Dispensed Volume
Dispense Mode
Read/Write
Read/Write
Read/Write
402034
402036
402038
402040
402042
Gun Trigger On Time
Current Job Spray Total
Current Job Flush Total
Current Job Number
Job Attribute
402044
402046
402048
Job Gun Trigger Time
Unused
Unused
Read
Read
Read
Read/Write
Read/Write
Read
YY
MM
DD
HH
MM
SS
Bitfield cc cc cc cc/min bar
Bit cc cc
0
0
0
Selection 0
0
0
0
0
0
0
0
0
0
1
1
Low High
1 99
12
31
Limited to 2099
23
59
59
32-bit See
32-bit
999999 Write 0 to reset
9999999 Write 0 to reset
65535
32-bit Scaled as 1 bar =
65536
0 = Off
1 = On
1
32-bit
32-bit
3 0 = Standby
1 = Flush
2 = Fill
3 = Dispense ms cc cc
Value
Value
0
0
0
0
0
32-bit
24-bit
24-bit
32-bit
32-bit
Automatically increments
Use for identification of the user, station, part, etc.
ms
0 32-bit
3A6948D 95
Appendix A - Modbus Variable Map
Clear an individual alarm by writing the value to the Modbus register 402012 (see
P3
P2
F6
P6
Code Summary
Any All alarms are cleared
F3
F2
MF
High Flow
Low Flow
Maintenance Counter
High Pressure
Low Pressure
SN
SP
EU
Runaway Flow
Runaway Pressure
Minimum Fill Volume
Minimum Flush Volume
System Idle
0x0000
0x0001
0x0002
0x0004
0x0008
0x0010
0x0020
0x0040
0x0080
0x0100
0x0200
Code Summary
QT
B4
B1
G2
Dose Time
Job Dispense High
Job Dispense Low
Gun Off Setpoint
0x0400
0x0800
0x1000
0x2000
All alarms may be cleared by writing 0x0 to the register. If alarms are to be cleared individually, write the bitmask of the alarms to be cleared. If the PLC write cycle does not allow writing the same value to the register, one of the presently unused bits, such as 0x80000000 or 0x40000000, may be added to the bitmask to allow the write cycle.
All registers are 32-bit.
Address Description
402050 Fluid setpoint as percentage of 4 to
20 mA range
402052 Fluid setpoint as drive current
Permissions Units
Read/Write
Low
Percent 0
High
99.9
Read/Write uA 0 32000
402054 Fluid setpoint as pressure
402056 Fluid setpoint as flow rate
Read/Write
Read/Write
402058 Readback current
402060 Atomizing air setpoint as percentage of 4 to 20 mA range
402062 Unused
402064 Unused
402066 Unused
402068 Unused
Read
Read/Write bar cc/min
0
0 uA 0
Percent 0
32-bit
65535
32000
99.9
Scaled as 1% = 65536
Active when 403094 = 0
(See
)
1 mA = 1000
Active when 403094 = 3
(See
)
Scaled as 1 bar = 65536
Active when 403094 = 1
(See
)
Active when 403094 = 2
(See
)
1 mA = 1000
Scaled as 1% = 65536
(See
)
96 3A6948D
Appendix A - Modbus Variable Map
All registers are 32-bit.
Address Description
403000 Communication,
Modbus Mode
403002 Communication,
Modbus Address
403004 Communication,
Modbus Baud Rate
Permissions Units
Read/Write
Read/Write
Read/Write
Bit
Value
Value
0
1
0
403006 Communication,
Modbus Parity
Read/Write
403008 Communication,
Modbus Stop Bits
403010 Display, Date
Format
Read/Write
Read/Write
403012 Display, Backlight
Timer
403014 Display,
Maintenance
Totalizer Alarm
Enable
403016 Display, Flow Rate
Alarm Enable
Read/Write
Read/Write
Read/Write
403018 Display, Flow Rate
Alarm Auto Clear
Read/Write
Value
Value
Value minutes 0
Bit 0
Bit
Bit
0
0
0
1
0
403020 Unused
403022 Pressure
Transducer Enable
Read/Write
403024 Units, Flow Rate Read/Write
Bit
Value
0
0
403026 Units, Pressure Read/Write Value 0
403028 Units, Batch
Volume
Read/Write
403030 Units, Grand
Volume
Read/Write
403032 System,
Maintenance
Target
403034 Percentage Drive
Maximum Setpoint
Read/Write
Read/Write
Value
Value cc
0
0
0
Percent 0
3A6948D
1
247
4
0 = Off
1 = On
2
2
2
0 = 9600
1 = 19200
2 = 38400
3 = 578600
4 = 115200
0 = None
1 = Odd
2 = Even
99
1
0 = MM/DD/YY
1 = DD/MM/YY
2 = YY/MM/DD
0 = Always On
0 = Off
1 = On
1
2
1
1
2
2
2
9999999
0 = Off
1 = On
Used for F3 and F2 alarms
0 = Off
1 = On
Used for F3 and F2 deviations
0 = Off
1 = On
0 = cc/min
1 = l/min
2 = gal/min
0 = psi
1 = bar
2 = MPa
0 = cc
1 = l
2 = gal
0 = cc
1 = l
2 = gal
Used for MF advisory
99.9
Scaled as 1% = 65536
Active when 403094 = 0
97
Appendix A - Modbus Variable Map
Address Description
403036 Percentage Drive
Minimum Setpoint
403038 System, Flow Rate
Maximum
403040 System, Flow Rate
Minimum
403042 System, Meter
K-Factor
403044 System, Pressure
Transducer Type
Permissions Units
Read/Write Percent 0
Read/Write
Read/Write
Read/Write
Read/Write cc cc cc/pulse
Value
0
0
0x028F
0
99.0
999000
999000
Scaled as 1% = 65536
Active when 403094 = 0
Used for F3 alarm
0x3E7FFFF 1 cc = 65536
3
Used for F2 alarm
0 = Not Installed
1 = 16H282 100 psi
2 = 16P289 500 psi
3 = 15M669 7500 psi
403046 System, Pressure
Transducer Offset
403048 System, Pressure
Transducer Scale
403050 System, Job
Volume Units
Read/Write
Read/Write
Read/Write mV mV/bar
Value 0
403052
403054
403056
System, Pressure
Maximum
System, Pressure
Minimum
Display, Pressure
Alarm Enable
Read/Write
Read/Write
Read/Write
Read/Write bar bar bar
Value
0
0
0
0
2 0 = cc
1 = l
2 = gal
0x44E584 Scaled as 1 bar = 65536
Used for P3 alarm
0x44E584 Scaled as 1 bar = 65536
Used for P2 alarm
1 0 = Off
1 = On
Used for P3 and P2 alarms
32-bit 403058 Software version identifier
403060 Password
403062 Flow alarm range as percentage of setpoint
403064 Flow alarm range percentage of setpoint
403066 Pressure alarm range as percentage of setpoint
403068 Pressure alarm range percentage of setpoint
403070 Unused
403072 Logged job maximum target
403074 Logged job minimum target
403076 Logged job target alarm enable
403078 Display, Pressure
Alarm Auto Clear
Read/Write
Read/Write
Read/Write
Read/Write
Read/Write
Read/Write
Read/Write
Read/Write
Read/Write
Read/Write
Value
Bit
Value
Bit
Value cc cc
Bit
Bit
0
0
0
0
0
0
0
0
0
9999
1
99
1
99
999999
999999
1
1 0 = Off
1 = On
Used for P3 and P2 deviations
98 3A6948D
Address Description Permissions
403080 Pressure PID Kp Read/Write
Units
Value
403082 Pressure PID Ki Read/Write
403084 Pressure PID Kd Read/Write
403086 Fill mode fluid drive percentage
403088 Fill mode drive timeout
403090 Flush mode fluid drive percentage
Read/Write
Read/Write
Read/Write
403092 Flush mode drive timeout
Read/Write
403094 Operational Mode Read/Write
Value
Value
Value
Value
Value
Value
Value
0
0
0
0
0
0
0
0
403096 Pressure maximum setpoint limit
403098 Pressure minimum setpoint limit
403100 Pressure Control internal setpoint
403102 Unused
403104 Unused
403106 Flow PID Kp
Read/Write
Read/Write
Read/Write
Read/Write
Read/Write
Read/Write
403108 Flow PID Ki
403110 Flow PID Kd
403112 Flow Control internal setpoint
403114 Unused
403116 Unused
403118 Unused
403120 Unused
Read/Write
Read/Write
Read/Write
Read/Write
Read/Write
Read/Write
Read/Write
403122 Unused
403124 Unused
403126 Unused
403128 Unused
403130 Unused
403132 Unused
403134 Unused
403136 Unused
403138 Unused
403140 Unused
403142 Unused
403144 Unused
403146 Unused
403148 Unused
Read/Write
Read/Write
Read/Write
Read/Write
Read/Write
Read/Write
Read/Write
Read/Write
Read/Write
Read/Write
Read/Write
Read/Write
Read/Write
Read/Write bar bar bar
Value
Value
Value cc/min
0
0
0
0
0
0
0
Appendix A - Modbus Variable Map
999
999
999
100
500
100
500
3 0 = Monitor
1 = Pressure Control
2 = Flow Control
3 = Current
0x63E667 Scaled as 1 bar = 65536
0x63E667 Scaled as 1 bar = 65536
0x63E667 Scaled as 1 bar = 65536
999
999
999
32-bit
3A6948D 99
Appendix A - Modbus Variable Map
Address Description
403150 Unused
Permissions
Read/Write
403152 Flow Rate maximum setpoint limit
403154 Flow Rate minimum setpoint limit
403156 Atomizing Air percentage drive maximum
403158 Atomizing Air percentage drive minimum
403160 Flow Control PID gain percentage
Read/Write
Read/Write
Read/Write
Read/Write
Read/Write
403162 System Idle timeout
Read/Write
403164 Dose Time timeout Read/Write
Units cc/min cc/min
Percent
Percent
Percent minutes
0
0
0
0
1
0
403166
403168
Job Attribute code
Job trigger time
403170 Unused
Read/Write
Read/Write seconds 0
Value ms
0
0
403172 Unused
9999
9999
0x63E667 Scaled as 1 % = 65536
0x63E667 Scaled as 1 % = 65536
100
99
99
32-bit
32-bit
0 = Not used
0 = Not used
100 3A6948D
Appendix B - Upgrading ProControl 1KE to ProControl 1KE Plus
An upgrade from a previous generation ProControl
1KE to a ProControl 1KE Plus requires the 25B322
Upgrade Kit (see
Closed Loop Fluid Pressure/Flow and Gun Atomizing Air Control, page 84
, and
Hardware Upgrades in
To upgrade ProControl 1KE to a ProControl 1KE
Plus, transfer the ADCM display, I/P transducer, fluid meter, fluid regulator, pressure transducer, power supply, and associated components from your
ProControl 1KE model. See manual 3A2614 for details of what is included in the previous generation of your specific ProControl 1KE model.
Review the following table and order any additional components required to complete desired model upgrade. See
, for complete parts lists.
4.
Install a wire zip tie (64) around the two wires connected to the Pressure Switch (34) spade terminal connectors.
5.
Route the ADCM Display cable, I/P Transducer cable, Pressure Transducer cable, and Fluid
Meter cable through the upper cable entry gland
(56). Use the cable tie down clips (63) and wire zip ties (64) to secure the cabling and wires onto the fluid plate (1).
6.
Refer to
, for proper mounting and installation of the ADCM Display, Fluid Plate,
Power Supply, and Cable port connections to the ADCM Display, as well as, fluid and air line connections.
7.
When all of the components are installed and mounted properly, follow the procedure in manual
3A1244 to load the software onto the ADCM
Display from the Software Token included with the 25B322 Upgrade Kit.
B
T
A
N
S
C variable
)))
ADCM Display B
I/P Transducer E
Fluid Meter H
Fluid Regulator J
Pressure
Transducer
K
Power Supply A
Associated
Components variable
1.
Transfer and install the I/P transducer, fluid meter, fluid regulator, pressure transducer, and associated components from your ProControl
1KE onto the 25B322 Upgrade Kit fluid plate (1).
See
Closed Loop Fluid Pressure/Flow and Gun
Atomizing Air Control, page 84
.
2.
Refer to the
Electrical Schematic, page 91 , for
the proper connections of the I/P Transducer
(25), Pressure Switch (34), and the grounding of the fluid plate (1).
3.
Install a wire zip tie (64) around the two I/P
Transducer wires at the entry point of the DIN connector.
See Hardware Upgrades in
a description of the 25B323 Air Control Description
Kit, and see
Closed Loop Fluid Pressure/Flow and
Gun Atomizing Air Control, page 84 , for a detailed list
of its components.
1.
Install the I/P Transducer and Remote Piloted Air
Regulator assemblies onto the ProControl 1KE
Plus fluid plate (1) with the supplied hardware.
See
Closed Loop Fluid Pressure/Flow and Gun
Atomizing Air Control, page 84
, for the parts diagram and list. See the diagram for mounting location and air-line routing.
2.
Install air supply fittings (53 and 54) into the available air manifold (48) ports.
3.
Use the provided 5/32” OD tubing to connect one of the Y-fitting (54) supply ports to the I/P
Transducer (25) inlet port and a second separate line to the Pressure Switch (34).
4.
Use the provided 5/32” OD tubing to connect the
I/P Transducer (25) outlet control port to the Air
Regulator (42) air pilot line port.
3A6948D 101
Appendix B - Upgrading ProControl 1KE to ProControl 1KE Plus
5.
Use the provided 3/8” OD tubing to connect the
Air Supply Fitting (54) from the Manifold (48) to the Air Regulator (42) inlet port. For ProControl
1KE Plus systems with closed loop or flow control, use the 3/8” OD tubing to connect the Air
Regulator (42) outlet port to the existing Air Flow
Switch AFS (31) inlet port.
6.
Route the I/P Transducer Cable through the upper cable entry gland (56) and connect to Port
9 on the ADCM Display. Secure the cable to the fluid plate (1) with a wire zip tie (64).
7.
Refer to the
Electrical Schematic, page 91 , and
connect the green/yellow grounding wire to an available ground screw on the fluid plate (1).
102 3A6948D
Maximum inlet air pressure 100 psi 0.7 MPa, 6.9 bar
Maximum fluid working pressure – See
ProControl 1KE Plus Pressure Ratings, page 5 , for specific model
configurations
Components
289813 G3000 Meter
24C375 Fluid Regulator, Air inlet pressure
24C375 Fluid Regulator, Fluid inlet pressure
Fluid panel fluid fittings
Fluid regulator outlet hose, 18F889
Atomizing air regulator, 120435
4000 psi
100 psi
300 psi
4600 psi
3000 psi
300 psi
27.6 MPa, 275.8 bar
0.7 MPa, 6.9 bar
2.1 MPa, 20.7 bar
31.7 MPa, 317.2 bar
20.7 MPa, 206.8 bar
2.1 MPa, 20.7 bar
Voltage
Frequency
Phase
Amps
100 – 240 VAC
50 – 60 Hz
1
1.2 A maximum
See manual 332196 for power supply characteristics, requirements, and installation information.
Power Supply Module 16V680
Power Supply Module 16M167
Power Supply Module (w/G-Barrier) 24C724
15 VDC, 1.2 A maximum
15 VDC, 160 mA maximum
24 VAC, 160 mA maximum
I/P Transducer (use only clean, dry, oil-free air, filtered through at least a 40 micron filter)
Air Regulator, 120435
Operating Temperature
Storage Temperature
Humidity
Display housing is solvent resistant.
All Modules
Sound power
4.5 scfh (ea.) typical
32° - 122°F
–22° - 140°F
0 – 195 scfm
0° - 50°C
–30° - 60°C
0 to 95 percent, non-condensing
< 75 dB
3A6948D 103
Meter
Fluid Regulator
Fittings
ProControl 1KE Plus ADCM
Mounting Bracket
Power Supply 16V680
Power Supply 16M167
Power Supply 26C724
Fluid Panel (fully populated)
See G3000 meter manual (308778) or Coriolis meter manual (313599)
See Fluid Regulator Manual (3A0427)
17-4, 17-7, 303, 304, 316 Stainless Steel, PTFE
1.5 lb
1 lb
1.5 lb
9 lb
9.5 lb
27.4 lb
0.68 kg
0.45 kg
0.68 kg
4.1 kg
4.3 kg
12.45 kg
104 3A6948D
3A6948D 105
Graco warrants all equipment referenced in this document which is manufactured by Graco and bearing its name to be free from defects in material and workmanship on the date of sale to the original purchaser for use. With the exception of any special, extended, or limited warranty published by Graco, Graco will, for a period of twelve months from the date of sale, repair or replace any part of the equipment determined by Graco to be defective. This warranty applies only when the equipment is installed, operated and maintained in accordance with Graco’s written recommendations.
This warranty does not cover, and Graco shall not be liable for general wear and tear, or any malfunction, damage or wear caused by faulty installation, misapplication, abrasion, corrosion, inadequate or improper maintenance, negligence, accident, tampering, or substitution of non-Graco component parts. Nor shall
Graco be liable for malfunction, damage or wear caused by the incompatibility of Graco equipment with structures, accessories, equipment or materials not supplied by Graco, or the improper design, manufacture, installation, operation or maintenance of structures, accessories, equipment or materials not supplied by Graco.
This warranty is conditioned upon the prepaid return of the equipment claimed to be defective to an authorized Graco distributor for verification of the claimed defect. If the claimed defect is verified, Graco will repair or replace free of charge any defective parts. The equipment will be returned to the original purchaser transportation prepaid. If inspection of the equipment does not disclose any defect in material or workmanship, repairs will be made at a reasonable charge, which charges may include the costs of parts, labor, and transportation.
THIS
IMPLIED,
OF
Graco’s sole obligation and buyer’s sole remedy for any breach of warranty shall be as set forth above.
The buyer agrees that no other remedy (including, but not limited to, incidental or consequential damages for lost profits, lost sales, injury to person or property, or any other incidental or consequential loss) shall be available. Any action for breach of warranty must be brought within two (2) years of the date of sale.
GRACO
MERCHANTABILITY
ACCESSORIES,
GRACO.
are subject to the warranty, if any, of their manufacturer. Graco will provide purchaser with reasonable assistance in making any claim for breach of these warranties.
In no event will Graco be liable for indirect, incidental, special or consequential damages resulting from
Graco supplying equipment hereunder, or the furnishing, performance, or use of any products or other goods sold hereto, whether due to a breach of contract, breach of warranty, the negligence of Graco, or otherwise.
FOR GRACO CANADA CUSTOMERS
The Parties acknowledge that they have required that the present document, as well as all documents, notices and legal proceedings entered into, given or instituted pursuant hereto or relating directly or indirectly hereto, be drawn up in English. Les parties reconnaissent avoir convenu que la rédaction du présente document sera en Anglais, ainsi que tous documents, avis et procédures judiciaires exécutés, donnés ou intentés, à la suite de ou en rapport, directement ou indirectement, avec les procédures concernées.
For the latest information about Graco products, visit www.graco.com.
For patent information, see www.graco.com/patents.
All written and visual data contained in this document reflects the latest product information available at the time of publication.
Graco reserves the right to make changes at any time without notice.
Original Instructions. This manual contains English. MM 3A6948
Graco Headquarters: Minneapolis
GRACO
2019, www.graco.com
Revision D, July 2022
advertisement
* Your assessment is very important for improving the workof artificial intelligence, which forms the content of this project
Related manuals
advertisement
Table of contents
- 3 Related Manuals
- 4 ProControl 1KE Plus Models
- 4 ProControl 1KE Plus ADCM
- 5 ProControl 1KE Plus Pressure Ratings
- 6 ProControl 1KE Plus Model Selection Matrix
- 7 ProControl 1KE Plus Selection Guide
- 8 Power Supply Selection Guide
- 8 Non-Hazardous Locations
- 8 Hazardous Locations
- 10 Component Entity Parameters
- 12 Component Circuit Connector Drawing
- 13 Warnings
- 17 Overview
- 18 Components
- 20 Installation
- 20 Non-Hazardous Locations
- 21 Hazardous Locations
- 24 Grounding
- 24 Cable Connections to the Advanced Display Control Module (ADCM)
- 25 Air Connections
- 26 Fluid Connections
- 26 Fluid Inlet Connections
- 26 Fluid Outlet Connections
- 27 Alternate Flow Meter and Fluid Regulator Installation
- 27 Communication Options
- 29 Operation
- 29 Pressure Relief Procedure
- 29 Fluid Regulator Operation
- 29 Flow Meter Operation
- 30 ADCM Module
- 30 Display Information
- 30 Operation Modes
- 30 Screen Navigation and Editing
- 31 Icons
- 33 Control Method Considerations
- 35 Run Screens
- 35 Screen 1: Run Operations
- 35 Run Mode Selection
- 36 Standby Mode Operation
- 37 Flush Mode Operation
- 38 Fill Mode Operation
- 39 Dispense Mode Operation
- 40 Screen 2: Job Log Totalizer
- 40 Job Log Data and Functions
- 41 Screen 3: Job Log History
- 41 Job Log History Data
- 42 Screen 4: Event Log History
- 42 Event Log History Data
- 43 Password Screen
- 44 Setup Screens
- 44 Setup Screen 1: Job Target
- 45 Setup Screen 2: Maintenance Totalizer
- 46 Setup Screen 3: Grand Totals
- 46 Setup Screen 4: Calibration
- 47 Setup Screen 5: Flow Rate
- 48 Setup Screen 6: Pressure Transducer
- 49 Setup Screen 7: Pressure
- 50 Setup Screen 8: Operator Input Limits
- 51 Setup Screen 9: Additional Operator Input Limits and Timeouts
- 52 Setup Screen 10: PID Data
- 52 Setup Screen 11: Fill Mode
- 53 Setup Screen 12: Flush Mode
- 54 Setup Screen 13: Control Method
- 55 Setup Screen 14: Modbus
- 55 Setup Screen 15: Date and Time
- 56 Setup Screen 16: Password
- 57 Setup Screen 17: Internal Pressure Control Variables
- 59 Setup Screen 18: Internal Flow Control Variables
- 61 Setup Screen 19: Internal Set Point and Flowmeter Information
- 62 Setup Screen 20: Modbus status
- 63 Calibrate the Meter
- 63 Set the Modbus Address
- 64 Deviations and Advisories
- 66 Update the Software
- 67 Troubleshooting
- 72 Battery Replacement Procedure
- 73 Parts
- 89 Accessories
- 91 Electrical Schematic
- 92 Mounting Dimensions
- 93 Appendix A - Modbus Variable Map
- 93 Device Identification Registers
- 94 Command Registers
- 95 Run Registers
- 96 Alarm Bitfield Table
- 96 Run Setpoint Registers
- 97 Setup Registers
- 101 Appendix B - Upgrading ProControl 1KE to ProControl 1KE Plus
- 101 Upgrading a ProControl 1KE to ProControl 1KE Plus
- 101 Installing the 25B323 Air Control Upgrade Kit
- 103 Technical Specifications
- 105 California Proposition 65
- 106 Graco Standard Warranty