advertisement
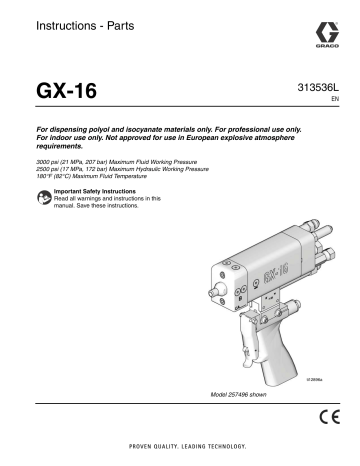
Instructions - Parts
GX-16
For dispensing polyol and isocyanate materials only. For professional use only.
For indoor use only. Not approved for use in European explosive atmosphere requirements.
3000 psi (21 MPa, 207 bar) Maximum Fluid Working Pressure
2500 psi (17 MPa, 172 bar) Maximum Hydraulic Working Pressure
180°F (82°C) Maximum Fluid Temperature
Important Safety Instructions
Read all warnings and instructions in this manual. Save these instructions.
313536L
EN
Model 257496 shown ti12896a
2
Contents
Models . . . . . . . . . . . . . . . . . . . . . . . . . . . . . . . . . . . 3
Warnings . . . . . . . . . . . . . . . . . . . . . . . . . . . . . . . . . 4
Important Two-Component Material Information . 6
Isocyanate Conditions . . . . . . . . . . . . . . . . . . . . . 6
Material Self-ignition . . . . . . . . . . . . . . . . . . . . . . 6
Keep Components A and B Separate . . . . . . . . . 6
Moisture Sensitivity of Isocyanates . . . . . . . . . . . 7
Foam Resins with 245 fa Blowing Agents . . . . . . 7
Changing Materials . . . . . . . . . . . . . . . . . . . . . . . 7
Grounding . . . . . . . . . . . . . . . . . . . . . . . . . . . . . . . . 8
Trigger Lock . . . . . . . . . . . . . . . . . . . . . . . . . . . . . . . 9
Setup . . . . . . . . . . . . . . . . . . . . . . . . . . . . . . . . . . . . 10
Gun Connections . . . . . . . . . . . . . . . . . . . . . . . 10
Fluid Line . . . . . . . . . . . . . . . . . . . . . . . . . . . . . 11
Gun Setup . . . . . . . . . . . . . . . . . . . . . . . . . . . . . 11
Shutoff Valve Setup . . . . . . . . . . . . . . . . . . . . . 12
Mounting . . . . . . . . . . . . . . . . . . . . . . . . . . . . . . 12
Startup . . . . . . . . . . . . . . . . . . . . . . . . . . . . . . . . . . 13
Operation . . . . . . . . . . . . . . . . . . . . . . . . . . . . . . . . 14
Theory of Operation . . . . . . . . . . . . . . . . . . . . . 14
Pressure Relief Procedure . . . . . . . . . . . . . . . . . . 15
Shutdown . . . . . . . . . . . . . . . . . . . . . . . . . . . . . . . . 15
Maintenance . . . . . . . . . . . . . . . . . . . . . . . . . . . . . 16
Recommended Tools . . . . . . . . . . . . . . . . . . . . 16
Grease the Gun . . . . . . . . . . . . . . . . . . . . . . . . 16
Recommended Hydraulic Oil . . . . . . . . . . . . . . 16
Clean and Service the Orifices and Filters . . . . 17
Proximity Switch Replacement Procedure . . . . 18
Troubleshooting . . . . . . . . . . . . . . . . . . . . . . . . . . . 19
Parts . . . . . . . . . . . . . . . . . . . . . . . . . . . . . . . . . . . . 20
Gun Models 257496, 257498, 257499,
257505, 257506, 257507, 24J187, 24E876 20
Gun Models 257492, 257493, 257494, 257495 22
Gun Models 257497, 257502, 257503, 257504,
24E877, 24E878 . . . . . . . . . . . . . . . . . . . . . 24
Gun Models 24K233, 24K234 . . . . . . . . . . . . . . 26
Dispenser Models 257513, 257514, 257515 . . . 28
Orifices . . . . . . . . . . . . . . . . . . . . . . . . . . . . . . . 30
Gun Handle Kit 24K223 . . . . . . . . . . . . . . . . . . . 31
Gun Handle Models 257509, 257510 . . . . . . . . 32
Pour Handle Models 257594, 257596 . . . . . . . . 33
Optional Shutoff Valve Kit . . . . . . . . . . . . . . . . . 34
Accessories . . . . . . . . . . . . . . . . . . . . . . . . . . . . . . 35
Technical Data . . . . . . . . . . . . . . . . . . . . . . . . . . . . 36
Weight . . . . . . . . . . . . . . . . . . . . . . . . . . . . . . . 36
Dimensions . . . . . . . . . . . . . . . . . . . . . . . . . . . . 37
Graco Standard Warranty . . . . . . . . . . . . . . . . . . . 38
Graco Information . . . . . . . . . . . . . . . . . . . . . . . . . 38
313536L
Models
Part No.
Description
257492
257493
257494
257495
GX-16 Pour Gun, 24:1, Pour Handle, Right Side Chemical Tubes,
Star-Shaped Trigger Switch Connector
GX-16 Pour Gun, 24:1, Pour Handle, Left Side Chemical Tubes,
Star-Shaped Trigger Switch Connector
GX-16 Pour Gun, 24:1, Pour Handle, Right Side Chemical Tubes, Circular Trigger Switch Connector
GX-16 Pour Gun, 24:1, Pour Handle, Left Side Chemical Tubes, Circular Trigger Switch Connector
257496
257497
257498
257499
257502
257503
257504
257505
GX-16 Pour Gun, 24:1, Isolated Pistol Handle
GX-16 Pour Gun, 24:1, No Handle
GX-16 Pour Gun, No Handle, No Orifice
GX-16 Pour Gun, Reverse Block, No Handle, No Orifice
GX-16 Pour Gun, 1:1, No Handle
GX-16 Pour Gun, 1:1, No Handle, No Fittings
GX-16 Pour Gun, 1:1, No Handle, 3 ft Hoses
GX-16 Pour Gun, 1:1, Pistol Handle, No Orifice, Proximity Switch
257506 GX-16 Pour Gun, 1:1, Isolated Pistol Handle, Proximity Switch
257507 GX-16 Pour Gun, 1:1, Isolated Pistol Handle, No Orifice, Proximity
Switch
24E876 ◆
GX-16 Pour Gun, HFR
™
, NVH, Straight, Basic
24E877 ◆ GX-16 Pour Gun, HFR, NVH, Right, 24:1
24E878 ◆ GX-16 Pour Gun, HFR, NVH, Right, Basic
24J187 ◆ GX-16 Pour Gun, HFR, NVH, Straight, 24:1
24K233 ◆ GX-16 Pour Gun, HFR, NVH, Left, 24:1
24K234 ◆ GX-16 Pour Gun, HFR, NVH. Left, Basic
◆ Models used specifically for HFR machines.
Models
313536L 3
4
Warnings
Warnings
The following warnings are for the setup, use, grounding, maintenance, and repair of this equipment. The exclamation point symbol alerts you to a general warning and the hazard symbol refers to procedure-specific risk. Refer back to these warnings. Additional, product-specific warnings may be found throughout the body of this manual where applicable.
WARNING
TOXIC FLUID OR FUMES HAZARD
Toxic fluids or fumes can cause serious injury or death if splashed in the eyes or on skin, inhaled, or swallowed.
• Read MSDSs to know the specific hazards of the fluids you are using.
• Store hazardous fluid in approved containers, and dispose of it according to applicable guidelines.
• Always wear chemically impermeable gloves when spraying, dispensing, or cleaning equipment.
PERSONAL PROTECTIVE EQUIPMENT
You must wear appropriate protective equipment when operating, servicing, or when in the operating area of the equipment to help protect you from serious injury, including eye injury, hearing loss, inhalation of toxic fumes, and burns. This equipment includes but is not limited to:
• Protective eyewear, and hearing protection.
• Respirators, protective clothing, and gloves as recommended by the fluid and solvent manufacturer.
SKIN INJECTION HAZARD
High-pressure fluid from dispensing device, hose leaks, or ruptured components will pierce skin. This may look like just a cut, but it is a serious injury that can result in amputation. Get immediate surgical treatment.
• Engage trigger lock when not dispensing.
• Do not point dispensing device at anyone or at any part of the body.
• Do not put your hand over the fluid outlet.
• Do not stop or deflect leaks with your hand, body, glove, or rag.
• Follow the Pressure Relief Procedure when you stop dispensing and before cleaning, checking, or servicing equipment.
• Tighten all fluid connections before operating the equipment.
• Check hoses and couplings daily. Replace worn or damaged parts immediately
313536L
313536L
Warnings
WARNING
EQUIPMENT MISUSE HAZARD
Misuse can cause death or serious injury.
• Do not operate the unit when fatigued or under the influence of drugs or alcohol.
• Do not exceed the maximum working pressure or temperature rating of the lowest rated system component. See Technical Data in all equipment manuals.
• Use fluids and solvents that are compatible with equipment wetted parts. See Technical Data in all equipment manuals. Read fluid and solvent manufacturer’s warnings. For complete information about your material, request MSDS from distributor or retailer.
• Do not leave the work area while equipment is energized or under pressure. Turn off all equipment and follow the Pressure Relief Procedure when equipment is not in use.
• Check equipment daily. Repair or replace worn or damaged parts immediately with genuine manufacturer’s replacement parts only.
• Do not alter or modify equipment.
• Use equipment only for its intended purpose. Call your distributor for information.
• Route hoses and cables away from traffic areas, sharp edges, moving parts, and hot surfaces.
• Do not kink or over bend hoses or use hoses to pull equipment.
• Keep children and animals away from work area.
• Comply with all applicable safety regulations.
FIRE AND EXPLOSION HAZARD
Flammable fumes, such as solvent and paint fumes, in work area can ignite or explode. To help prevent fire and explosion:
• Use equipment only in well ventilated area.
• Eliminate all ignition sources; such as pilot lights, cigarettes, portable electric lamps, and plastic drop cloths (potential static arc).
• Keep work area free of debris, including solvent, rags and gasoline.
• Do not plug or unplug power cords, or turn power or light switches on or off when flammable fumes are present.
• Ground all equipment in the work area. See Grounding instructions.
• Use only grounded hoses.
• Hold gun firmly to side of grounded pail when triggering into pail.
• If there is static sparking or you feel a shock, stop operation immediately.
Do not use equipment until you identify and correct the problem.
• Keep a working fire extinguisher in the work area.
BURN HAZARD
Equipment surfaces and fluid that’s heated can become very hot during operation. To avoid severe burns:
• Do not touch hot fluid or equipment.
5
6
Important Two-Component Material Information
WARNING
PRESSURIZED ALUMINUM PARTS HAZARD
Use of fluids that are incompatible with aluminum in pressurized equipment can cause serious chemical reaction and equipment rupture. Failure to follow this warning can result in death, serious injury, or property damage.
• Do not use 1,1,1-trichloroethane, methylene chloride, other halogenated hydrocarbon solvents or fluids containing such solvents.
• Many other fluids may contain chemicals that can react with aluminum. Contact your material supplier for compatibility.
Important Two-Component Material Information
Isocyanate Conditions Keep Components A and B
Separate
Spraying or dispensing materials containing isocyanates creates potentially harmful mists, vapors, and atomized particulates.
Read material manufacturer’s warnings and material
MSDS to know specific hazards and precautions related to isocyanates.
Prevent inhalation of isocyanate mists, vapors, and atomized particulates by providing sufficient ventilation in the work area. If sufficient ventilation is not available, a supplied-air respirator is required for everyone in the work area.
To prevent contact with isocyanates, appropriate personal protective equipment, including chemically impermeable gloves, boots, aprons, and goggles, is also required for everyone in the work area.
Material Self-ignition
Cross-contamination can result in cured material in fluid lines which could cause serious injury or damage equipment. To prevent cross-contamination of the equipment’s wetted parts, never interchange component A (isocyanate) and component B (resin) parts.
Some materials may become self-igniting if applied too thickly. Read material manufacturer’s warnings and material MSDS.
313536L
Important Two-Component Material Information
Moisture Sensitivity of
Isocyanates
Isocyanates (ISO) are catalysts used in two component foam and polyurea coatings. ISO will react with moisture
(such as humidity) to form small, hard, abrasive crystals, which become suspended in the fluid. Eventually a film will form on the surface and the ISO will begin to gel, increasing in viscosity. If used, this partially cured ISO will reduce performance and the life of all wetted parts.
NOTE: The amount of film formation and rate of crystallization varies depending on the blend of ISO, the humidity, and the temperature.
To prevent exposing ISO to moisture:
• Always use a sealed container with a desiccant dryer in the vent, or a nitrogen atmosphere. Never store ISO in an open container.
• Keep the ISO lube pump reservoir (if installed) filled with Graco Throat Seal Liquid (TSL
™
), Part 206995.
The lubricant creates a barrier between the ISO and the atmosphere.
• Use moisture-proof hoses specifically designed for
ISO, such as those supplied with your system.
• Never use reclaimed solvents, which may contain moisture. Always keep solvent containers closed when not in use.
• Never use solvent on one side if it has been contaminated from the other side.
• Always lubricate threaded parts with ISO pump oil or grease when reassembling.
Changing Materials
• When changing materials, flush the equipment multiple times to ensure it is thoroughly clean.
• Always clean the fluid inlet strainers after flushing.
• Check with your material manufacturer for chemical compatibility.
• Most materials use ISO on the A side, but some use
ISO on the B side.
• Epoxies often have amines on the B (hardener) side. Polyureas often have amines on the B (resin) side.
Foam Resins with 245 fa
Blowing Agents
Some foam blowing agents will froth at temperatures above 90°F (33°C) when not under pressure, especially if agitated. To reduce frothing, minimize preheating in a circulation system.
313536L 7
8
Grounding
Grounding
The equipment must be grounded. Grounding reduces the risk of static and electric shock by providing an escape wire for the electrical current due to static build up or in the event of a short circuit.
Pump: use ground wire and clamp (supplied). Connect ground clamp to a true earth ground.
Gun: ground through connection to a properly grounded fluid hose and pump.
Fluid supply container: follow local code.
Solvent pails used when flushing: follow local code.
Use only conductive metal pails, placed on a grounded surface. Do not place the pail on a non-conductive surface, such as paper or cardboard, which interrupts grounding continuity.
Maintain grounding continuity: When flushing or relieving pressure, hold metal part of the gun firmly to the side of a grounded metal pail, then trigger the gun.
313536L
Trigger Lock
Trigger Lock
Verify that the trigger lock is engaged whenever you stop pouring to avoid accidental triggering. Check daily for chemical build-up on trigger, trigger lock, and trigger lock spring that can prevent proper trigger lock function.
Engage
To engage the trigger lock, release the trigger. The trigger lock is spring loaded and automatically engages when the gun trigger is released.
To engage the trigger lock, press the trigger lock down.
Trigger Lock
F IG . 1: Models 257509, 257510 ti14491a1
F IG . 2: Kit 24K223 ti10442a
Disengage
To disengage the trigger lock, press trigger lock down.
See the following figure.
To disengage the trigger lock, press the trigger lock up.
ti12896a1
F
IG
. 3: Models 257509, 257510
313536L ti14491a1
F IG . 4: Kit 24K223 ti10441a
9
Setup
Setup
Gun Connections
D
B
G
F
C
A ti12897a
E
F IG . 5
Ref
A
Description
A Pressure Line
Tape Color †
Red
B A Return Line
B Pressure Line
Red and White
Blue C
D
E
B Return Line
Hydraulic Open Line
Blue and White
Green and White
F
G
Hydraulic Close Line
Proximity Switch or Plug
(depending on model)
† Only hoses are taped, fittings are not taped.
Green
NA
Fitting Size
7/16 ORG x
#6 JIC Female
7/16 ORG x
#6 JIC Male
7/16 ORG x
#5 JIC Female
7/16 ORG x
#5 JIC Male
7/16 ORG x
#4 JIC Male Extension
7/16 ORG x
#4 JIC Male Elbow
NA
HFR Systems Only
7/16 ORG x
#5 JIC Female
7/16 ORG x
#5 JIC Male
7/16 ORG x
#6 JIC Female
7/16 ORG x
#6 JIC Male
7/16 ORG x
#4 JIC Male Extension
7/16 ORG x
#4 JIC Male Elbow
NA
10 313536L
Setup
Fluid Line
Fluid Filter: Use a 25 micron stainless steel element to filter particles from the fluid as it leaves the pump.
Fluid Drain Valve: Required in your system, to relieve fluid pressure in the hose and gun.
NOTE: Pressure should not increase while air is purged from hoses.
5.
Turn off power pack. Verify no pressure exists in hoses.
6.
Remove the 7/16 in. JIC male-male adapter connecting the hydraulic hoses.
7.
Attach hydraulic hoses to the gun.
Gun Setup
Trapped air can cause the pump to cycle unexpectedly, which could result in serious injury from splashing or moving parts.
1.
Verify hydraulic power pack is off.
2.
Install hydraulic hoses to power pack. ti14496a
F IG . 7
Customer supplied hydraulic hoses must be at least
1/4 in. inner diameter and rated to at least 2500 maximum working pressure.
8.
Set power pack to manual mode.
9.
Attach trigger switch cable and proximity switch cable (if applicable) to gun and power pack.
3.
Use a 7/16 in. JIC male-male adapter at the gun end to connect hoses together. This creates a hydraulic fluid circulation loop.
ti14497a
F IG . 8 ti14495a
F
IG
. 6
4.
Turn on the power pack. Circulate oil for 10 minutes to purge air from hydraulic hoses.
10. Verify power pack pressure is 1800 - 2500 psi.
Adjust pressure as required.
313536L 11
Setup
11. Install chemical hoses to gun. See F IG . 5 on page
Mounting
Use the following mounting dimensions to mount the
GX-16 gun body.
F IG . 9
Shutoff Valve Setup
ti18184a
The shutoff valves are used to control chemical flow.
D ti14493a
B
A
C
B Diameter: 0.159 in. (4.04 mm),
10/32 UNF Thread on one side
C From edge: 0.188 in. (4.78 mm)
D From edge: 0.218 in.
(5.54 mm)
F IG . 11: Mounting Hole Dimensions ti14492a ti18185a
B
F IG . 10: Shutoff Valve Setup
1.
Perform pressure relief procedure. See Pressure
2.
Use four chemical hoses to connect shutoff valves
3.
Perform gun setup procedure to connect remaining hoses. See
4.
Perform
A
A Width: 0.578 in. (14.7 mm)
B Height: 0.440 in. (11.2 mm)
F IG . 12: Mounting Block Dimensions
12 313536L
Startup
Startup
1.
If your setup uses the optional shutoff valves, rotate the handles to the “open” position.
Open Position Closed Position
4.
Close dump valve on hydraulic power pack.
Hydraulic pressure must not exceed the maximum working pressure of 2500 psi (17 MPa, 172 bar).
5.
Start power pack and verify hydraulic pressure is
1800 - 2500 psi.
6.
Start chemical pumps.
ti18186a
F IG . 13: Shutoff Valves Positions
2.
Verify cables and hoses are correctly setup. See
Gun Connections section on page 10.
3.
Check for excessive wear on cables and hoses.
Replace as necessary.
Chemical pressure must not exceed the maximum working pressure of 3000 psi (21 MPa, 207 bar).
7.
Verify chemical pressure is in desired range.
8.
Dispense a test shot into a waste container.
9.
Clean any residual material from the tip of the gun.
313536L 13
Operation
Operation
Theory of Operation
Circulation
F A B C D E
H
Dispense
F A B C D E
Key:
A A Pressure Line
B A Return Line
C B Return Line
D B Pressure Line
E Hydraulic Open Line
F Hydraulic Close Line
G Piston Rod
H Hydraulic Piston
H
G
Key:
A A Pressure Line
B A Return Line
C B Return Line
D B Pressure Line
E Hydraulic Open Line
F Hydraulic Close Line
G Piston Rod
H Hydraulic Piston
F
IG
G
. 14: Circulation F IG . 15: Dispense
Hydraulic pressure extends the piston rod to the circulation position. Material enters the material pressure line and is sent to the material return line.
When the piston rod is extended to this position, it removes gelled material from the nose assembly.
Hydraulic pressure retracts the piston rod to the dispense position. Material enters the A and B material pressure lines and mixes in the mixing chamber.
When the piston rod is in this position, it blocks material flow from entering the material return line.
14 313536L
Pressure Relief Procedure
Pressure Relief
Procedure
Shutdown
1.
If your setup uses the optional shutoff valves, rotate the handles to the “open” position.
2.
Shut down chemical pumps.
3.
Drain air pressure from the A and B side chemical tanks.
4.
After tank air pressure is at zero, close the A and B tank outlet valves.
5.
Verify pressures read zero on chemical pressure gauges.
6.
Turn off hydraulic power pack.
7.
Bleed hydraulic pressure via dump valve on power pack.
8.
Verify pressures read zero on hydraulic pressure gauges.
1.
Perform Pressure Relief Procedure .
2.
Perform any required maintenance. See Maintenance on page 16.
3.
If system will not be in use for longer than two weeks, the A and B chemical tanks must have
10 psi of dry air pressure.
NOTICE
Air must be dry. Moist air will react with isocyanate and cause crystallization resulting in significant component damage.
4.
If the gun will not be used for longer than four weeks, flush the gun.
313536L 15
Maintenance
Maintenance
Procedure
Inspect the gun, fluid lines, trigger switch cable and, if installed, the proximity switch cable for wear or damage
Grease the gun
Clean and service the orifices and filters
Frequency
Daily
Weekly or Every
15,000 Shots
As Needed
3.
Use a grease gun with the required synthetic grease, part 0553-6, to purge the gun body until grease exits the weep hole without evidence of hydraulic oil or hardened material.
Recommended Tools
• 7/16 in. open end wrench
• 3/8 in. open end wrench
• 1/8 in. allen key
• 1/4 in. allen key
• Pin vise 117661
• Drill bit (see etching on orifice for size, drill bit should be same size as orifice)
• O-Ring Pick
• Small brass brush
• 1/4 in. brass barrel brush
• Small flashlight
• Small solvent pump can
• Cleaning rags
• Chemically impermeable gloves
• Safety glasses
• Small chemical and solvent waste container
• Grease gun
• Grease, part 0553-6
Grease the Gun
1.
Perform pressure relief procedure. See Pressure
2.
Use a 1/8 in. allen key to remove the weep plug.
ti14494a1
F IG . 16: Grease Fitting
NOTE: The presence of hydraulic oil at the grease fitting may indicate the need to replace or rebuild the gun.
4.
Use a 1/8 in. allen key to install the weep plug.
Recommended Hydraulic Oil
NOTICE
Recommended Hydraulic Oil
Use Graco-approved Hydraulic Oil, Part No. 169236
(5 gal) or 207428 (1 gal)) or a premium, ISO grade
46 petroleum-based hydraulic oil containing rust and oxidation inhibitors and anti-wear agents.
Before using any other type of oil in this motor, contact your Graco distributor. Unauthorized use of lesser grade oil or substitutes may void the warranty.
Hydraulic Oil Working Temperature
The maximum hydraulic oil operating temperature is
180 °F (82 °C). ti12899a1
16 313536L
Maintenance
Clean and Service the Orifices and Filters
Cross-contamination can result in cured material in fluid lines which could cause serious injury or damage equipment. To prevent cross-contamination of the equipment’s wetted parts, component A (isocyanate) and component B (resin) parts.
F
E
G
J
H never
H
interchange
L
K
D
C
B
A
A Side
Key:
A Filter Plug
B Filter Plug O-Ring
C Filter O-Ring
D Filter
E Orifice O-Rings
F Orifice
F IG . 17:
B Side ti12899a
G Grease Port Plug
H Cleanout Plug
J Cleanout Plug O-Ring
K Weep Plug
L Weep Plug O-Ring
NOTE: See
Dispenser Models 257513, 257514,
257515 on page 28 for applicable part numbers.
1.
Perform pressure relief procedure. See
2.
If your setup uses the optional shutoff valves, rotate the handles to the “close” position
3.
Use a 7/16 in. wrench to remove the orifice.
4.
Use a 1/8 in. allen key to remove the cleanout plug next to the orifice.
5.
Use a 1/4 in. allen key to remove the filter plug (A).
6.
Remove the filter (D).
7.
Use a pick to remove any hardened material from filter.
8.
Use solvent to flush residue from this side of the gun block.
9.
Use a pin vise and drill bit to carefully clean the orifice.
10. Remove the orifice o-rings.
11. Use a pick to remove any hardened material from the orifice body.
12. Flush the orifice body with solvent then dry the orifice.
13. Install new o-rings on the orifice.
14. Install new filter.
15. Replace filter retainer o-ring if needed.
16. Apply grease to filter retainer threads then use a
1/4 in. allen key to install the filter retainer.
17. Apply grease to the o-ring plug threads.
18. Install o-rings then use a 1/8 in. allen key to install cleanout plug next to the orifice.
19. Apply grease to orifice threads then install the orifice assembly.
20. Repeat for opposite chemical side of gun.
313536L 17
Maintenance
Proximity Switch Replacement
Procedure
1.
Perform pressure relief procedure. See Pressure
2.
Remove proximity switch cable attached to proximity switch.
3.
Remove proximity switch from rear of gun body.
ti12897a
F IG . 18
4.
Install new proximity switch.
5.
Attach proximity switch cable to proximity switch.
18 313536L
Troubleshooting
Troubleshooting
Poor mixing
Problem Cause Solution
One or both sides of gun are clogged Clean the gun, see
on
No fluid being dispensed
Chemical crossover
Hydraulic leak into divorce chamber
(hydraulic fluid found in purged grease when greasing the gun)
Proximity switch not working
Hydraulic piston not opening fast enough due to insufficient hydraulic pressure
Insufficient pressure to move hydraulic piston to the dispense position
Faulty proximity switch
Damaged piston u-cup seals
Seal failure on piston rod
Damaged seal u-cup
Damaged proximity switch
One or both orifices may need to be replaced
Verify hydraulic unit pressure and accumulator charge
Verify hydraulic unit pressure and accumulator charge
Replace proximity switch
Send gun to Graco for repair
Send gun to Graco for repair
Send gun to Graco for repair
Damaged proximity switch cord
Remove and test the switch, replace as needed
Remove and test the cord, replace as needed
313536L 19
Parts
Parts
Gun Models 257496, 257498, 257499,
257505, 257506, 257507, 24J187, 24E876
110
101a, c
101b, d
101
112
111
106
105
104
108
109
107
103
104
115
118
114
117
116
105
104
113
Model 257496 shown
104 ti12900a
102
Ref Part Description
101
257513
257514
DISPENSER, GX-16, 1:1, pre-assy
DISPENSER, GX-16, 24:1, pre-assy
257515
DISPENSER, GX-16, rev block, pre-assy
. 101a ◆
. 122685
. PLUG, sae02, socket head, m, ms, 6k
. 101b ◆
. 261500
. O-RING, #902, fluoroelastomer
. 101c ◆ . 122687 . PLUG, sae02, 316 ss
Quantity by Model
257496 257498 257499 257505 257506 257507 24J187 24E876
1
1
1
1
1
1
1
1
1
1
1
1
1
2
2
1
2
2
1
2
2
1 1
20 313536L
Parts
*
Ref Part Description
. 101d ◆ . 122679 . O-RING, epr, #902
257509 HANDLE, GX-16, pistol grip
102
257510
HANDLE, GX-16, pistol grip, isolated
103 122694 SCREW, bhsc, 10-32x1.00, ms
257496 257498 257499 257505 257506 257507 24J187 24E876
1 1 1
Quantity by Model
1
2
1
2
1
2
1
2
104
105
106
107
108*
109*
110
111*
112*
113
114
115
116
117
118
122707
O-RING, fluoroelastomer,
#904, 75a
122714 O-RING, ep, 904, 70a
122713 SWITCH, proximity
15Y178 PLUG, cavity, proximity switch
257724
RESTRICTOR, orifice assy,
0.061
257717
RESTRICTOR, orifice assy,
0.039
168518
PACKING, o-ring, fluoroelastomer
261500 O-RING, #902, fluoroelastomer
257701
RESTRICTOR, orifice assy,
0.011
RESTRICTOR, orifice assy,
0.039
257717
285967 O-RING, #006 epr
122679 O-RING, epr, #902
15Y177 FITTING, 7/16 org x 7/16 jic ext
298408 FITTING, 7/16 org x 9/16 jic ext
122710
122711
ADAPTER, jic05xsae04, mm, ss, 6k
FITTING, elbow, 90, jic04xsae04
122708
122709
ADAPTER, swivel, jic06xsae04, fm, ss, 6k
ADAPTER, swivel, jic05xsae04, fm, ss, 6k
122709
ADAPTER, swivel, jic05xsae04, fm, ss, 6k
ADAPTER, swivel, jic06xsae04, fm, ss, 6k 122708
122710
ADAPTER, jic05xsae04, mm, ss, 6k
298408 FITTING, 7/16 org x 9/16 jic ext
1
1
1
1
4
2
1
1
1
1
1
1
1
1
1
4
2
1
1
1
1
1
1
1
4
2
1
1
1
1
1
1
1
6
1
1
1
1
1
1
1
6
1
1
1
1
1
1
1
1
1
6
1
1
1
1
1
1
1
3
2
1
1
1
1
1
1
1
1
1
3
2
1
1
1
1
1
1
1
For all models, o-ring materials are marked on the gun below the A side orifice
◆ Parts are used in the maintenance of the gun. Parts are shipped loose.
313536L 21
Parts
Gun Models 257492, 257493, 257494, 257495
216
215
217
212
218
230
206
211
208
206
223
204
225
213
207
210
220
221
228
222
224
231
233
232
201
235
236
234
206
214
219
221
228
223
226
222
227
201b, d 201a, c
205 209
203
229 ti12901a
Model 257492 shown
202
22 313536L
Parts
228
229
230
231
232
233
234
235
236
221
222
223
224
225
226
227
Ref Part Description
201 257514 DISPENSER, GX-16, 24:1, pre-assy
. 201a ◆ . 122685 . PLUG, sae02, socket head, m, ms, 6k
. 201b ◆ . 261500 . O-RING, #902, fluoroelastomer
. 201c ◆ . 122687 . PLUG, sae02, 316 ss
. 201d ◆ . 122679 . O-RING, epr, #902
257594 HANDLE, GX-16, pour
202
257596 HANDLE, GX-16, pour
203 15Y246 BRACKET, hose, pour handle
204
205
122694
15Y247
SCREW, bhsc, 10-32x1.00, ms
BRACKET, hose, cylinder
206 122707 O-RING, fluoroelastomer, #904, 75a
207
208
122714
285874
O-RING, ep, 904, 70a
FITTING, 7/16 o-ring x 1/4 tube 90 elbow
209
210
122741
122730
SCREW, bhcs, 1/4-20x0.50, ms
ADAPTER, 1/4nptxsae04, fm, ss, 6k, 316
211
212
122731
122729
ADAPTER, 1/4nptxsae04, fm, ms, 6k
ADAPTER, 1/4nptx3/8tube, mf, ms, 5k
213
214
122732
122733
ADAPTER, 1/4nptx3/8tub, mf, ss, 5k
ADAPTER, sae04x1/4tub, mf, ms, 5k
215
216
15Y332 TUBE, a-return, left side
15Y326 TUBE, a-return, right side
15Y333 TUBE, a-supply, left side
15Y327 TUBE, a-supply, right side
217
218
219
220
15Y334 TUBE, b-return, left side
15Y328 TUBE, b-return, right side
15Y335 TUBE, b-supply, left side
15Y329 TUBE, b-supply, right side
15Y336 TUBE, hyd open, left side
15Y330 TUBE, hyd open, right side
15Y337 TUBE, hyd close, left side
15Y331 TUBE, hyd close, right side
122734 ADAPTER, 1/8nptx1/4tub, ff, ms, 5k
122735
122736
122721
122737
122727
122722
ADAPTER, 1/4nptx3/8tub, ff, ms, 5k
ADAPTER, 1/4nptx3/8tb, ff, ss, 5k, 316
ADAPTER, swivel, jic6x1/4npt, fm, ms, 5k
ADAPTER, swivel, 1/4nptxjic05, fm, ss, 6
ADAPTER, jic05x1/4npt, mm, ss, 6k, 316
ADAPTER, jic06x1/4npt, mm, ms, 6k
122726 FITTING, adapter, jic04x1/8npt
122742 SCREW, fhcs, 1/4-20x0.750, ms
122713
257724
168518
261500
257701
285967
122679
SWITCH, proximity
RESTRICTOR, orifice assy, 0.061
PACKING, o-ring, fluoroelastomer
O-RING, #902, fluoroelastomer
RESTRICTOR, orifice assy, 0.011
O-RING, #006 epr
O-RING, epr, #902
◆
Parts are used in the maintenance of the gun. Parts are shipped loose.
1
1
1
1
2
2
1
1
1
1
1
1
1
2
2
1
2
2
2
2
1
1
2
1
4
2
1
2
2
Quantity by Model
257492 257493 257494 257495
1
1
1
1
1
1
1
1
1
1
1
1
1
1
1
1
1
1
1
1
1
1
1
2
1
4
2
1
2
2
2
2
2
1
1
2
2
2
1
2
1
1
1
4
2
1
2
2
2
2
2
1
2
1
1
1
4
2
1
2
2
1
1 1
1 1
1 1
1 1
1 1
1 1
1 1
1 1
1 1
1 1
2
2
2
1
1
1
1
2
2
1
1
1
1
1
1
1
1
1
1
1
2
2
1
1
1
1
1
1
1
2
2
1
2
1
1
1
1
1
1
1
2
2
1
1
1
1
2
2
2
313536L 23
Parts
Gun Models 257497, 257502, 257503, 257504, 24E877, 24E878
301a, c
301b, d
311
303
307
305
301
304
306
302
318
312
309
316
315
Model 257504 shown
308
313
314
317
308
310
319
317
322
323
320
321
324
325 ti13381a
Ref Part Description
257513 DISPENSER, GX-16, 1:1, pre-assy
301
257514 DISPENSER, GX-16, 24:1, pre-assy
. 301a
◆
. 122685 . PLUG, sae02, socket head, m, ms,
6k
. 301b
◆
. 261500 . O-RING, #902, fluoroelastomer
. 301c
◆
. 122687 . PLUG, sae02, 316 ss
. 301d
◆
. 122679 . O-RING, epr, #902
257724 RESTRICTOR, orifice assy, 0.061
302
257717 RESTRICTOR, orifice assy, 0.039
Quantity by Model
257497 257502 257503 257504 24E877 24E878
1 1 1
1 1 1
1
1
1
1
1
1
1
1
1
1
1
1
1
1
1
1
1
1
1
1
1
24 313536L
Parts
319
320
321
322
323
324
325
Ref
303
304
305
306
307
308
309
310
311
312
313
314
315
316
317
318
Part Description
257701 RESTRICTOR, orifice assy, 0.011
257717 RESTRICTOR, orifice assy, 0.039
168518 PACKING, o-ring, fluoroelastomer
285967 O-RING, #006 epr
168518 PACKING, o-ring, fluoroelastomer
261500 O-RING, #902, fluoroelastomer
122679 O-RING, epr, #902
261500 O-RING, #902, fluoroelastomer
122707 O-RING, fluoroelastomer, #904, 75a
122714 O-RING, fluoroelastomer, #904, 75a
122707 O-RING, fluoroelastomer, #904, 75a
15Y177 FITTING, 7/16 org x 7/16 jic ext
122713 SWITCH, proximity
298408 FITTING, 7/16 org x 9/16 jic ext
122710 ADAPTER, jic05xsae04, mm, ss, 6k
122720 ADAPTER, jic06xsae04, mm, ms, 6k, fluoroelastomer
124221 ADAPTER, jic05xsae04, mm, ss, 6k
122717 ADAPTER, swivel, jic06xsae04, fm, ms, 6k
125541 FITTING, swivel, jic05xsae04, fm, ss,
6k
122719 FITTING, elbow, swivel, 90, jic06, fm, ms
122715 FITTING, elbow, swivel, 90, jic05, fm, ss
122715 FITTING, elbow, swivel, 90, jic05, fm, ss
122719 FITTING, elbow, swivel, 90, jic06, fm, ms
122718 FITTING, elbow, swivel, 90, jic04, fm, ms
122708 ADAPTER, swivel, jic06xsae04, fm, ss, 6k
122709 ADAPTER, swivel, jic05xsae04, fm, ss, 6k
122711 FITTING, elbow, 90, jic04xsae04
24C481 HOSE, 3 ft, A-supply, yellow tape
24C482 HOSE, 3 ft, A-return, yellow/white tape
24C483 HOSE, 3 ft, B-supply, green tape
24C484 HOSE, 3 ft, B-return, green/white tape
24C485 HOSE, 3 ft, hydraulic open, black tape
24C486 HOSE, 3 ft, hydraulic close, black/white tape
Quantity by Model
257497 257502 257503 257504 24E877 24E878
1 1
1
1
1
1
1
1
1
1
1
1
1
1
1
1
1
1
3
2
1
3
1 1
3 3
2
3
2
1
1 1
1
2
1
1 1
1
2
1 1
1
1
1
1
1
1
1 1 1
1
2
2
2
1
1
1
2
2
2
1
1
1
2
2
2
1
1
1
1
1
1
1
1
1
1
2
2
2
1
1
1
1
2
2
2
1
1
◆ Parts are used in the maintenance of the gun. Parts are shipped loose.
313536L 25
Parts
Gun Models 24K233, 24K234
810
804
805
806
802
801
814
808
809
812
807
Model 24K233 shown
803
811
803
813 ti17784a
26 313536L
Ref Part Description
801 257514
DISPENSER, GX-16, 24:1, pre-assy
802 122714
O-RING, fluoroelastomer, #904, 75a
803 122707
O-RING, fluoroelastomer, #904, 75a
804 122720
ADAPTER, jic06xsae04, mm, ms, 6k, fluoroelastomer
805 122717
ADAPTER, swivel, jic06xsae04, fm, ms, 6k
806 122710
ADAPTER, jic05xsae04, mm, ss, 6k
807 122709
ADAPTER, swivel, jic05xsae04, fm, ss, 6k
808 122719
FITTING, elbow, swivel, 90, jic06, fm, ms
809 122715
FITTING, elbow, swivel, 90, jic05, fm, ss
810 122713
SWITCH, proximity
811 15Y177
FITTING, 7/16 org x 7/16 jic ext
812 122718
FITTING, elbow, swivel, 90, jic04, fm, ms
813 122711
FITTING, elbow, 90, jic04xsae04
814 257701
RESTRICTOR, orifice assy, 0.011
815 257724
RESTRICTOR, orifice assy, 0.061
1
1
1
1
1
2
1
1
1
2
2
Quantity
24K233 24K234
1 1
2 2
3
1
3
1
1
1
2
1
1
1
1
2
2
Parts
313536L 27
Parts
Dispenser Models 257513, 257514, 257515
921
926
927
922
917
925
928
929
924
925
922 r_257515_parts
922
930
922
924
921
923
Model 257515 shown
918
924
923
28 313536L
Ref Part
917 295229
918 295693
921 122687
122685
922 261500
122679
923 122687
122685
924 122679
261500
925 285917
926 15X857
15X858
927 122681
122680
928 15X858
15X857
929 122680
122681
930 16A582
Description
FITTING, grease, 1/4-28
PLUG, pipe
PLUG, sae02, 316 ss
PLUG, sae02, skt hd, ms, 6k
O-RING, #902
O-RING, #902
PLUG, sae02, 316 ss
PLUG, sae02, skt hd, ms, 6k
O-RING, #902
O-RING, #902
SCREEN, 230 micron
PLUG, filter
PLUG, filter
O-RING, #906
O-RING, #906
PLUG, filter
PLUG, filter
O-RING, #906
O-RING, #906
PLUG, weep, sae02, skt hd, ms
3
4
2
1
1
257513
1
1
3
5
Quantity
257514
1
1
3
1
1
1
4
2
1
5
3
1
1
1
1
4
2
1
1
1
1
1
257515
1
1
3
5
3
Parts
313536L 29
Parts
Orifices
Part
257715
257716
257717
257718
257719
257720
257721
257722
257723
257724
24K682
257700
257701
257702
257703
257704
257705
257706
257707
257708
257709
257710
257711
257712
257713
257714
Orifice Assembly Size
0.036 in.
0.038 in.
0.039 in.
0.040 in.
0.042 in.
0.043 in.
0.044 in.
0.049 in.
0.052 in.
0.061 in.
0.085 in.
Orifice Plug
0.011 in.
0.013 in.
0.016 in.
0.018 in.
0.020 in.
0.022 in.
0.023 in.
0.024 in.
0.025 in.
0.026 in.
0.028 in.
0.029 in.
0.032 in.
0.035 in.
NOTE: O-rings and cleanout drill bits are included in all orifice parts listed.
30 313536L
Gun Handle Kit 24K223
1003
1002
1006
1004
1001
1005 ti17785a
Ref Part Description
1001 24D073 KIT, handle, EP
1002 16H435 ISOLATOR, handle, GX-16 to MD2
1003 16H436 ISOLATOR, handle, GX-16 to MD2, left
1004 16H437 ISOLATOR, handle, GX-16 to MD2, right
1005 122694 SCREW, button head
1006 121070 SCREW, machine
Qty
1
1
1
1
2
2
Parts
313536L 31
Parts
Gun Handle Models 257509, 257510
510
511
512
509
507
508
502
503
505
504
506
Model 257510 shown
Ref Part Description
501 257576 HANDLE
502 112095 SCREW, set
503 257578 SWITCH, trigger
504 299650 SPRING
505 257577 PLUNGER, spring
506 15Y159 NUT, retainer
507 257579 TRIGGER, safety, gun
508 295671 SCREW, mounting, trigger
509 295438 NUT, stop, elastic, 5-40
510 15Y160 ISOLATOR, handle
(Model 257510 only)
511 122706 WASHER, flat, #10, ms, 1/2od, 0.49 thick
(Model 257510 only)
512 105210 SCREW, 10-32 x 1 shcs (matrix)
(Model 257510 only)
Qty
1
1
1
1
1
1
1
1
1
1
2
2
501
32 ti13383a
313536L
Pour Handle Models 257594, 257596
602
601
608
604
609
602
Parts
607
610
605
606
Model 257594 shown 603
Ref Part Description
601 295438 NUT, stop, elastic, 5-40
602 122746 SCREW, shc, 10-32x.375, ms, nyloc
603 257595 CONTROL, circular connector/led
(assembly 257594 only)
257597 CONTROL, star-shaped connector/led
(assembly 257596 only)
604 295671 SCREW, mounting, trigger
605 15Y276 CLIP, expander, female
606 257593 CHOCK, male expander, w/pin
607 122747 SCREW, shc, 110-32x0.75, ms
608 15Y277 TRIGGER, pour gun
609 15Y278 MODULE, pour handle mount, w/holes
610 15Y280 FLANGE
Qty
1
4
1
1
1
1
1
1
1
1
1 ti14499a
313536L 33
Parts
Optional Shutoff Valve Kit
1 702
701
1 704
1 707
24L498 Shown
1
Apply items 8 and 9 as required
Ref Part Description
701 --VALVE, ball, 2 way, 1/4 NPT, female
702 ---
---
ADAPTER, 1/2-20 JIC x 1/4 NPT
ADAPTER, JIC08x1/4, MS
703 ---
704 ---
---
705 ---
ADAPTER, JIC06x1/4, SS
ADAPTER, JIC06x1/4 NPT, MS
ADAPTER, swivel, JIC05x1/4 NPT, MS
ADAPTER, swivel, JIC06x1/4 NPT, MS
---
706 ---
---
707 ---
---
708 ---
709 ---
ADAPTER, swivel, JIC05x1/4 NPT, MS
ADAPTER, JIC05x1/4 NPT, SS
ADAPTER, swivel, JIC06x1/4 NPT, MS
ADAPTER, swivel, 1/4 NPTxJIC05, SS
ADAPTER, swivel, JIC06x1/4 NPT, MS
TAPE, TFE, sealant
SEALANT, pipe, SST
34
703
1
701
706
1
705 1 ti18187a
24L498, KIT, valve shutoff,
GX-16
4
Quantity
24M596, KIT, valve shutoff,
GX-16, NVH
4
2
2
2
1
2
1
1
1
1
1
1
1
1
1
1
1
313536L
Accessories
Description
Hose Kit
Gun Cover, straight fittings
Gun Cover, 90 deg. fittings
Hose Cover, 12 ft
Right Fitting Adapter Kit
Left Fitting Adapter Kit
Grease Fitting Flush Kit
Part
24C999
123694
124226
123698
24K672
24K674
24T326
Accessories
313536L 35
Technical Data
Technical Data
Maximum Fluid Working Pressure . . . . . . . . . . . . . . . . . . 3000 psi (21 MPa, 207 bar)
Maximum Hydraulic Working Pressure . . . . . . . . . . . . . . 2500 psi (17 MPa, 172 bar)
Maximum Fluid Temperature . . . . . . . . . . . . . . . . . . . . . . 180°F (82°C)
Fitting Sizes . . . . . . . . . . . . . . . . . . . . . . . . . . . . . . . . . . . See
Gun Connections section on page 10
Max Sound Power Level. . . . . . . . . . . . . . . . . . . . . . . . . . 68.5 dB
Wetted Parts . . . . . . . . . . . . . . . . . . . . . . . . . . . . . . . . . . Aluminum, stainless steel, carbon steel, disogrin (urethane), Rulon, EPDM, fluoroelastomer, PTFE
Flow Rate, lb/min (kg/min) . . . . . . . . . . . . . . . . . . . . . . . . 4.6 to 40 (2 to 18)
Weight
Model
257492, 257493,
257494, 257495
257497, 257502,
257503, 257504,
24E877, 24E878,
24K233, 24K234
(no hoses)
257496, 257507
257505, 257506
257498, 257499,
24J187, 24E876
Weight*, lb (kg)
8.1 (3.7)
5.0 (2.3)
5.2 (2.4
5.1 (2.3)
4.6 (2.1)
* Weights are approximate.
36 313536L
Dimensions
A
B
Technical Data
C
Model
A
Dimension
B C
257492, 257493,
257494, 257495
257497, 257502,
257503, 257504,
24E877, 24E878,
24K233, 24K234
(no hoses)
257496, 257507
257505, 257506
257498, 257499,
24J187, 24E876
15.1 (383) 9.6 (244) 7.9 (201)
10.3 (262) 3.6 (91) 3.7 (94)
9.3 (236)
9.3 (236)
9.3 (236)
3.0 (76)
3.0 (76)
2.8 (71)
8.9 (226)
8.1 (206)
3.7 (94)
Model 257496 shown ti12896a
313536L 37
Graco Standard Warranty
Graco warrants all equipment referenced in this document which is manufactured by Graco and bearing its name to be free from defects in material and workmanship on the date of sale to the original purchaser for use. With the exception of any special, extended, or limited warranty published by Graco, Graco will, for a period of twelve months from the date of sale, repair or replace any part of the equipment determined by
Graco to be defective. This warranty applies only when the equipment is installed, operated and maintained in accordance with Graco’s written recommendations.
This warranty does not cover, and Graco shall not be liable for general wear and tear, or any malfunction, damage or wear caused by faulty installation, misapplication, abrasion, corrosion, inadequate or improper maintenance, negligence, accident, tampering, or substitution of non-Graco component parts. Nor shall Graco be liable for malfunction, damage or wear caused by the incompatibility of Graco equipment with structures, accessories, equipment or materials not supplied by Graco, or the improper design, manufacture, installation, operation or maintenance of structures, accessories, equipment or materials not supplied by Graco.
This warranty is conditioned upon the prepaid return of the equipment claimed to be defective to an authorized Graco distributor for verification of the claimed defect. If the claimed defect is verified, Graco will repair or replace free of charge any defective parts. The equipment will be returned to the original purchaser transportation prepaid. If inspection of the equipment does not disclose any defect in material or workmanship, repairs will be made at a reasonable charge, which charges may include the costs of parts, labor, and transportation.
THIS WARRANTY IS EXCLUSIVE, AND IS IN LIEU OF ANY OTHER WARRANTIES, EXPRESS OR IMPLIED, INCLUDING BUT NOT LIMITED
TO WARRANTY OF MERCHANTABILITY OR WARRANTY OF FITNESS FOR A PARTICULAR PURPOSE .
Graco’s sole obligation and buyer’s sole remedy for any breach of warranty shall be as set forth above. The buyer agrees that no other remedy
(including, but not limited to, incidental or consequential damages for lost profits, lost sales, injury to person or property, or any other incidental or consequential loss) shall be available. Any action for breach of warranty must be brought within two (2) years of the date of sale.
GRACO MAKES NO WARRANTY, AND DISCLAIMS ALL IMPLIED WARRANTIES OF MERCHANTABILITY AND FITNESS FOR A
PARTICULAR PURPOSE, IN CONNECTION WITH ACCESSORIES, EQUIPMENT, MATERIALS OR COMPONENTS SOLD BUT NOT
MANUFACTURED BY GRACO . These items sold, but not manufactured by Graco (such as electric motors, switches, hose, etc.), are subject to the warranty, if any, of their manufacturer. Graco will provide purchaser with reasonable assistance in making any claim for breach of these warranties.
In no event will Graco be liable for indirect, incidental, special or consequential damages resulting from Graco supplying equipment hereunder, or the furnishing, performance, or use of any products or other goods sold hereto, whether due to a breach of contract, breach of warranty, the negligence of Graco, or otherwise.
FOR GRACO CANADA CUSTOMERS
The Parties acknowledge that they have required that the present document, as well as all documents, notices and legal proceedings entered into, given or instituted pursuant hereto or relating directly or indirectly hereto, be drawn up in English. Les parties reconnaissent avoir convenu que la rédaction du présente document sera en Anglais, ainsi que tous documents, avis et procédures judiciaires exécutés, donnés ou intentés, à la suite de ou en rapport, directement ou indirectement, avec les procédures concernées.
Graco Information
For the latest information about Graco products, visit www.graco.com.
TO PLACE AN ORDER, contact your Graco distributor or call to identify the nearest distributor.
Phone: 612-623-6921 or Toll Free: 1-800-328-0211 Fax: 612-378-3505
All written and visual data contained in this document reflects the latest product information available at the time of publication.
Graco reserves the right to make changes at any time without notice.
For patent information, see www.graco.com/patents.
Original instructions. This manual contains English. MM 313536
Graco Headquarters: Minneapolis
International Offices: Belgium, China, Japan, Korea
GRACO INC. AND SUBSIDIARIES • P.O. BOX 1441 • MINNEAPOLIS MN 55440-1441 • USA
Copyright 2010, Graco Inc. All Graco manufacturing locations are registered to ISO 9001.
www.graco.com
Revised September 2014
advertisement
* Your assessment is very important for improving the workof artificial intelligence, which forms the content of this project
Related manuals
advertisement
Table of contents
- 3 Models
- 4 Warnings
- 6 Important Two-Component Material Information
- 6 Isocyanate Conditions
- 6 Material Self-ignition
- 6 Keep Components A and B Separate
- 7 Moisture Sensitivity of Isocyanates
- 7 Foam Resins with 245 fa Blowing Agents
- 7 Changing Materials
- 8 Grounding
- 9 Trigger Lock
- 10 Setup
- 10 Gun Connections
- 11 Fluid Line
- 11 Gun Setup
- 12 Shutoff Valve Setup
- 12 Mounting
- 13 Startup
- 14 Operation
- 14 Theory of Operation
- 15 Pressure Relief Procedure
- 15 Shutdown
- 16 Maintenance
- 16 Recommended Tools
- 16 Grease the Gun
- 16 Recommended Hydraulic Oil
- 17 Clean and Service the Orifices and Filters
- 18 Proximity Switch Replacement Procedure
- 19 Troubleshooting
- 20 Parts
- 20 Gun Models 257496, 257498, 257499, 257505, 257506, 257507, 24J187, 24E876
- 22 Gun Models 257492, 257493, 257494, 257495
- 24 Gun Models 257497, 257502, 257503, 257504, 24E877, 24E878
- 26 Gun Models 24K233, 24K234
- 28 Dispenser Models 257513, 257514, 257515
- 30 Orifices
- 31 Gun Handle Kit 24K223
- 32 Gun Handle Models 257509, 257510
- 33 Pour Handle Models 257594, 257596
- 34 Optional Shutoff Valve Kit
- 35 Accessories
- 36 Technical Data
- 36 Weight
- 37 Dimensions
- 38 Graco Standard Warranty
- 38 Graco Information