Graco 308588A TexSpray EXT Owner's Manual
Add to My manuals24 Pages
Graco 308588A TexSpray EXT is an electric texture sprayer with a compressor, designed for professional use with water-based materials. It features a 5-gallon pressure pot and a 110/230 Vac motor with an oil-less single-stage air compressor. The system has a maximum working pressure of 100 psi (7 bar) and is equipped with a pot safety valve, a pot cover storage hook, and an air pressure regulator. The TexSpray EXT also includes a spray gun with a fluid valve and an air valve, and a hose set consisting of a 1-inch ID x 25 ft. (25 mm x 7.6 m) fluid hose and a 3/8-inch ID air hose.
advertisement
▼
Scroll to page 2
of
24
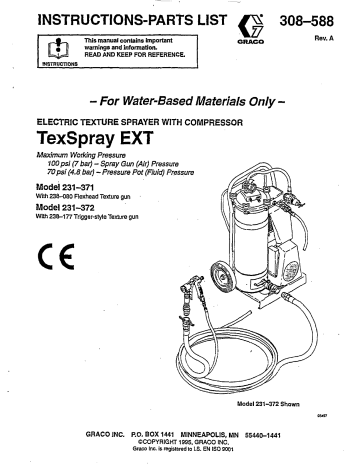
~ _ _, ~ ~- 1NSTRUCTIONS-PARTS LIST warnings and information. 308-588 GRACO READANDKEEPFORREFERENCE. INSTRUCTIONS - For Wafer-BasedMaterials Only ELECTRIC TEXTURE SPRAYER WITH COMPRESSOR TexSpray EXT Model 231-372 Shawn BOX 1441 MINNEAPOLIS, M N @COPYRIGHT1995, GRACO INC. Graco Inc. is registered to I S . EN IS0 9001 GRACO INC. P.O. 55440-1441 Rev. A Table of Contents ...................................... 2 ............ 4 .................................... 5 ...................................... 9 ............................. 10 ........................ 12 13 ............................... Warnings Repair and Identification Component Preparation Startup.. Spray Techniques Shutdown and Cleanup Troubleshooting ................................. ............................ ........................................ ............................... .................................. ................................ Cooler Repair Compressor Parts Wiring Diagram Accessories Technical Data Graco Phone Numbers.. ....................... 14 15 18 19 23 24 24 Symbols Warning Symbol Caution Symbol This symbol alerts you to the possibility of serious if you do not follow the instructions. injury or death This symbol alerts you to the possibility of damage to if you do not follow the or destruction of equipment instructions. EQUIPMENT MISUSE HAZARD Equipment misuse can cause the equipment to rupture or malfunction and result in serious injury. This equipment is for professional use only. Read all instruction manuals, tags, and labels before operating the equipment 0 Use the equipment only forits intended purpose. If you are not sure, call Graco Technical Assistance at 1-800-543-0339. Do not expose the system to rain. Always store the system indoors. 0 Do not alter or modify this equipment. 0 Check equipment daily. Repair or replace worn or damaged parts immediately. 0 Do not exceed the maximum working pressure of the lowest rated component in your system. This equipment, with the exception of the pressure pot, has a 100 psi (7 bar) maximum working pressure at 100 psi (7 bar) maximum air pressure. The pressurepot must not be pressurized above its70 psi (4.8 bar) working pressure. 0 To reduce ihe risk of serious injury, including electric shock and splashing fluid In theeyes, follow the Pressure Relief Procedure on page7 before checking or repairing the compressor. Do not use hoses to pull equipment 0 Route hoses away from traffic areas, snarp edges, movlng parts, and hot surfaces. Do not ex(180°F) or below-40°C (-4O'F). pose Graco hoses to temperatures above 82'C Do not lift pressurized equipment. Do not lay equipment down or allow material in pressure pot to plug the port to the pressure pot cover safety valve. Do not use the pot cover storage hook tolift the sprayer. 2 308-588 TOXIC FLUID HAZARD Hazardous fluid or toxic fumes can cause serious injury orif death splashed in the eyes oron the skin, inhaled, or swallowed. Know the specific hazards of the fluid you are using. . . 0 Store hazardousfluid inan approved container. Dispose of hazardous fluid according to all local, state and national guidelines. 0 Always wear protective eyewear, gloves, clothing and respirator as recommended by fluid the and solvent manufacturer. 0 Pipe and disposeof exhaust air safely, away from people, animals, and food handling areas. 0 Never directly inhale compressed air. Compressed air may contain toxic vapors. FIRE AND EXPLOSION HAZARD Improper grounding, poor ventilation, open flames or sparks can cause a hazardous condition and result in a fire or explosion and serious injury. e t h e system Is for use only withwater-based materials. Use fluids and solvents compatible to the Technical Data sectionof all equipment manuals. with the equipment welted parts. Refer Read the fluid and solvent manufacturer's warnings. Ground the equipment. Referto Grounding on page 6. 0 Ifthere is any static sparking or you feel an electric shock while using this equipment, stop spraying immediately. Do not use the equipment until you identify and correct the problem. 0 Provide fresh air ventilation to avoid the buildup of flammable fumes from solvents or the fluid being sprayed. 0 Keep the work area freeof debris, including solvent, rags, and gasoline. 0 The pressure pot is lined to prevent corrosion and aid pot cleanup. To prevent liner damage, do not mix texture material in the pot. Inspect the pot daily, and replace the pot if corrosion or other damage is present. 0 Locate the sprayer at least20 ft (6.1 m) away from any explosive vapors, due to arcing parts. e Comply with all applicable local, state, and national fire, electrical, and safety regulations. 308-588 , 3 Fig. 1 A B I Component I Potventvalve I CompressorSafetyValve C Allows quick venting of pot air pressure for refilling and cleanup Prevents supply and gun air pressure from exceeding100 psi limit Air Pressure Regulator Auxiliary Air Compressor Port D E Compressor F G Heat Exchanger Fluid Valve H I Spray Gun ONOFF Switch J K L Function 1 I - 5 Galion Pot Safetyvaive PotCoverStorageHook I I1 I Adjusts air pressure in pot to control flow rate of materialto spray gun Provides connectionto replacement or supplemental air compressor 110/230 Vac, open frame AC motor, 15A.1 phase, with oil-less single stage air compressor . Reduces temperatureof air from compressorto safe levels Shuts off fluid supply to spray gun Uses compressor airto break up and spray texture material Provides powerto the sprayer Holds texture material Pressure Pot PreventsDressure exceedina Dsi limit .Dot .from " 70Dressure AIIOW thecover to hangfromcartframeduringpressurepotrefilling . . ,.. i I Preparation Compressor Break-in Hose Size and Lengths The first time you use the system, run the compressor no load to break it perfomance andThesystem is providedwithahosesetconsisting of a re d,,,, 1 in. ID x 25 ft. (25 mm x 7.6 m) fluid hose and a 3/8 is life. lengthent in. ID air hose. For hard to pump materials,a 5 rn (16 1. Be'sure the air hose,without a gun. is connected ft) hose is also available (See Accessories.). at A so there is no load on the compressor. See Fig. 2 Do not use more than 75ft. (23 m) of fluid hose. 2. Turn on the switch (52). Run the system for15 minutes. Shutoff the switch. See Fig.2. Removing and Installing the Pressure Pot 1. To remove the pressure pot (70),loosen the knobs (4, Fig. 3) so they will slide through the notches in the mounting bracket(A) at the back of the cart. Loosen knob (5,Parts, page 20)at the bottom of lift the the pot, tilt the pot slightly forward and then pot offthe unit. 2 To install the pot, tilt the pot slightly forward and engage knob (5) in its slot. Lean the pot back until it is fully seatedin notches A. Tighten knobs(4) and knob (5)securely. See Fig. 3 and Parts,page 20. 05910 Fig. 3 308-588 5 ' Preparation iroupding * RRE AND EXPLOSION HAZARD To reduce the risk of statlc sparking, ground the sprayer and all other equipment used or locatedin the spray area. Also read FIRE OR EXPLOSION HAZARD on page3. :heck your local electrical code for detailed grounding nstmctions for your area andtype of equipment. Setup the System 1. Connectthe hoses and gun as shownin Fig. 4. 2 Be sure the sprayer power cordis undamaged, with its ground prong intact. ' 3. Be sure the air filter (21) Is in place. See Fig. 4. 4. Plug the power cord into a properly grounded, 120V. 15A outlet. If the circuit is protected by a fuse, use a time delay fuse. 5. Extension cord requirements: a The cord hasan undamaged, 3 prong plug. b. For up to 25 ft. (7.6 m) cord, use three wire, 12 gauge minimum c For25 to 50 ft. (7.6 to 15.2 m) cords, use three wire, 10 gauge minimum. d Do not use an ungrounded adapter. Using an Auxiliary Air Compressor An extend air compressor may be connected to the auxiliary air compressor port (D) to supplement. or replace, the internal air compressor of the TexSpray. This may be useful when: ' 0 6 Additional air is needed to break up nard-to-spray marerials or. 308-588 . m e n the job site does not have the proper electric service, but a gasoline-powered compressor1s available. I nent hpture and-resultkg in serious injury. I To reduce the risk of over pressurizing the system, do not use a compressorwith and output pressure greater than 100 psi (7bar), and/or with a delivery greater than 6.8 sdm at 90psi (.19 m3/min. at 6.3 bar). Preparation Model 231472 Shown PRESSURIZED EQUIPMENTHAZARD The system pressure mustbe manually relieved to prevent the system from spraying accidentally. To accidental spray reduce the risk of an injury from from the gun, splashing fluid, ormoving parts. follow the Pressure Relief Procedure whenever you: are instructedto relieve the pressure, stopspraying, 0 NOTE: Be sure the gunair is adjustedso the it valve (10) DOES NOT operate while spraying. When will opens, it uses air required for the system and reduce sprayer performance. The motor hasa thermal overload switch which shuts down the motor If it overheats. To reduce the risk of serious bodily injury due to the system restarting unexpectedly, always turn off the system at theONOFF switch (52) If the motor shuts itself down. See Fig. 2. ,checkor senn'ce any ofthe system equipment, or install or clean the spray nozzle. A Pressure .Relief . .. Procedure 1. Shut off the system. 2. Trigger the gun. 3. Open the gunair valve (handle parallel with valve body).Open the vent valve on the pot cover. 4. Unplugthesystem. Operation Characteristics Always start the system with the compressor air relieved. Fig. 5 cat 1. Follow thePressure Relief Procedure, above. How to relieve pressure: Be sure the gunair valve (A) Is open (the handle parallel to the valve body), which relieves compressor air every time you shut off the system. See Fig. 5. 2 Air bleeds from the gun nozzle whenever the gun air valve (A) is open. Close the valveto stop the air, If desired. Otherwise, it can stay open except . during priming. See Fig. 5. See page 10 for more gun characteristics. 3. A compressor pressure relief valve(10) is located under the cart'stop panel(11). Air escapes from the valve, sometimes causinga popping sound, is too restricted. The valve when air flow at the gun resets automatically when theair flow is increased. See Fig. 6. 300-580 7 Preparation Wet the Hose Before Pumping Texture Mix the Material Material Wet the inside of the hose before each use to flushout sedimen! and to prevent the texture material from p a c h g out the hose. A CAUTION This systemis designed foruse with onlycertain types of material. Any otheruse could seriously damage unit. the . . 1. The pot capacity is 5 gal. (19 liters). Fillthe pot with a couple of gallons of clean water. 0 2 Close the gun air valve (A). (The system primes 0 Use only simulated acoustic and gypsum-based wall andceiling texture materialsin this system. 0 Do not spray cementious materials, which will damage the pot. only water-based materials. easier if no air is supplied to the gun.) 3. Turn on the switch (52). Adjust the regulator(102) to pressurize the pot to about 20 psi (1.4 bar). Trigger the gun into a pail. Spray water to wet the inside of the fluid hose. 4. Turn off the switch (52). 5. Open the gun air valve (A) to relieve the compressor air. Open the pot vent valve (87) to vent the Pot 8 308-588 Do not use any solvent-based materials. Use Proper material mixture is essential. The sprayer won't operate if the material is too thick. Slowly add one bag of texture materialatopailof clean water as instructed on the bag instructions. For the best results, do notuse partial bagsof material. Thin or Agitate to a smooth, lump-free consistency. thicken the material as neededbefore pouring it Into the pot Startup Prime the System 1. Fill the pot(70)with the prepared texture material. Install float assembly(2) on top of the material to prevent air from disrupting material flow. 2. Install aup. Refer tothe Tip Selection Chart on page IO. 3. Close the gun air valve(A). (The system primes easier f no air is supplied tothe gun.) 4. To minimize material pack-upin the hose when using heavily sand-filled material: a Close fluid valve. Disconnect hose at fluid Valve. b. Thin one ortwo pints of material to 1/2 thickness and pour into hose at cam locks(e). c Install hose, open valve, and continue to push material throughhose. 5. Be sure there are no kinksin the hose, which restricts fluid flow. NOTE If spraying a simulated acoustic or coarse grain material, disconnect the hose at the gun, prime the seconds. hose, and circulate material into a pail10for Turn off the sprayer and vent the pressure pot.Install the gun and tip. 6. Turn on the switch (52). Trigger the gun into a pail. Continue until there is a solidstream of texture material 7. See Spray Techniques on pages 10 and 11 for how to balance the fluid pressure and gun adjustments for a good spray pattern. Spray Techniques 5. Start the sprayer with the gun air flow valve atits maximum setting (fully+). If needed, slowly Tip Seleciion Chart Application. Tq Orifice2 Simulated Acoustic or Full Spray fog Orange Peel 3 16. (fine, or small confinedareas) 114. (fine to mediom) 5/16" (coarse) 116' 118"to 3/16' Splatter Coat 114 to 5/16" Knockdown 5/16" Fan Air Voiume' High High Medium to High Low to Medium Low Control air volume with the gun air flow valve. 2 decrease the gun air flow until youget a good spray pattern. This may increase texture material output. For more material volume, try a larger orificetip or increase !he pot pressure. Adjusting the System ,6. Turning the air flow valve (6)toward (+) increases air flow through the gun which may decrease texture materialoutput. 7. Turning the air flow valve (8)toward (-) decreases air flow through the gun which may increase pot output. To Get Less Material Try anyone or a combination of these methods. 1. Tum the air flow valve (e) to increase (+). 2. Screw in the gun fluid knob (D). 3. Use a heavier material mixture. 4. Use a smaller tip. 5. Decreasepotpressure. To Get More.Material Sufficientfluid output (volume and pressure) and good TI^ any one or a combination of these methods. atomhation requires testing to balance the compressor air to thegun and pot andto select the right tip. Keep in mind these important points when adjusting the gun: 1. Turn the air flow valve ( 6 )to decrease (-). 1. Read a ! of pages 5 to 10 first. 2 Refer to the chart above fortip selection. Consider the size of aggregatein the material and the coarseness of !he spray pattern. Remember, the largertfie tip, the heavier the pattern. 3. The compressor providesair to bpth the gun and the pot: the more air you supply to the gun. the less that is available for the DO.: 4. Most spraying adjustments are made at the gun; changes for the material pressure andflow rate are made bychanging the pot pressure. NOTE: Adjustments to regulator(102) may take sevem seconds before pot pressure changes. Slow and deliberate adjustments give the best ~ s u l t sDo . not exceed the70 psi (4.9 bar) rating of ihe pot ! 2. Unscrew the fluidknob (D) until one or two threads show. 3. Usea shorter hose. (See Accessories.) 4.Use a lighter material mixture.' 5. Try a larger orifice tip. 6. Increasepotpressure. I I A CAUTION Turning the knob(D) out too farwill remove the knob andthegun willnotshut off whenthetrigger is [released. I 7. Test the spray pattern on cardboard. Hold the gun 18 to 30 in. (457 to 762 mm) from the surface. Use this spraying distancefor most applications. 8. Spray in a rotating pattern and overlap each stroke 50%. Spray Techniques NOTE: If the pressure setting on the pressure pot drops when youstart to spray, the spray gunis taking too much air. To keep the pressure pot at the desired setting, reduceair flow to the gun. How to Prevent Material Surge at the Beginning of a Spray Pattern Squeeze the trigger slowly to the fully triggered position while movingthe gun quickly. For Continuous Spraying Use the trigger bail(C) to hold the trigger open to reduce operator fatigue. Check Material Consistency Periodically Check and thin the material as needed to maintain the proper consistency.The material may thickenas it sits and slow down production or affect the spray pattern. Fig. 0 OQl NOTE: If the material continuously clogsin the spray gun, you may need to use the flexhead Texture Spray Gun(93). Fig. 9 308-588 11 Shutdown and Cleanup -air air valve (A) open See Fig. 10. Close the gun Be sure the compressor pressureis relieved gun 1. valve again Tum on the witch (52). See Fig.11. 2 Trigger the gun into apail to emptythe fluid in the Pa In cold weather, store the system whereit wil not freeze. If it does freeze, thawit thoroughly before using it. NO= 9. Remove the air filter(21), wash it thoroughly with soap and water, dryit and reinstall it.See Fig. 11. 9 Fill the pot (70) about half full with clean water, depending on the hose length. Clean the Inside Of the p o M i a brush, t needed. NOTI? The pot can be removed for cleaning. See page 5. 4. Triggerthe gun into a pail until the float stop (77) 10. Clean and dry the gun. Oil the gundailywith a few drops of SAE-10 light oil at the points indicatedin Fig. 10. 11. Remove any dry residue from the cooler (44). shuts off the materialflow. 5. Fill the pot with clean water. A 4 6. start the sprayer. Spray half the waterinto apail. Shut off the sprayer, and relieve the pressure. Remove the spray gun. Close the fluid outlet valve. (43) and Disconnect the hose from the coupler instan seveml hose cleaning balls(81) into the hose. Reconnect the hose. Open the fluid outlet VdV ?.f 7- Start the sprayer and pump the water into the pail to emptythe pot and the hose.Be sure to recover the hose cleaning balls. i E. Turn olf the switch (52). See Fig. 11. Open the gun air &e (A) t o relieve compressor pressure.See Fig. 10. Open the pot vent valve(87). A CAUTION To keep the unit in good operating condition, always clean P thoroughly and prepare it pmperly for storage, evenfor wemightstorage. Pay particular reas: attention to these a 0 Clein the sponge filter at least daily. A dirty filter allows conlamhants into the compressor, resulting in poor performance and damage. Oil thegun daily. lnsped the pot daily for corrosion or damage. See Ere and Explosion Hazard. 12 308-588 Fig. 11 05592 Troubleshooting To reduce the risk of injury, follow the Pressure Relief Procedure on page 7. System Troubleshooting I PROBLEM CAUSE SOLUTlON Materialtoo thick Thin material I Not enough air volume Increase air volume at the gun I Material volume too high 1. Decrease fluid pressure; see page 10 2. Change to smallernode 3.Turn fluid knob in; see page 10 ~ Spray patternis too fine or produces too much over spray. ~~ ~~ Decrease air volume at gun Too liffle material volume 1. Change to a larger nozzle 2. Increase fluid pressure; see page 10 3.Turn fluid knob out: see page 10 Thicken material Material too thin Speed of application seems slow.Pot pressure too low Increase pressure; see page 10 Nozzle too small Use larger nozzle Material too thick 1. Thin material, or 2. Use shorter hose(.$; see Accessories I Squeeze trigger slowly to fully open position while moving gun quickly; also see Spray Techniques on pages 10 and 11 Materialsurges when first trigger- Triggering toof a s t ing gun. (A slight surge is normal: t Refillpot. NOTE: Plate(2) shugoff material flow to prevent air from entering hose. Material does not flowisorerratic Pot Is nearly empty pot Clogged outlet clear Materialis too hick Air bubbles in fluid IInspect; IThinpage material; see 9 Leaking cover gasket Clean or replace gasket Plate (2) is not i d l e d Replace plate Insufficient air delivery from com- Lwse or damaged air lines pressor Air compressorworn oul prematurely leak valves Safely I I as needed Inspect and repair lines and fittings IRebuildcompressoc see page 15 I valves I Replace 1 i 30&588 13 Repair HOT SURFACE HAZARD Be SUIB !he compressor.duct workis cool before removingit. If the sprayer was operated recently, it will be very hot and can cause bums! FoUow the Pressure Relief Procedure, page 7. RemoveYhe screm (82A) and top cover (11). See Fig. 1 2 Remove the screws ( 8 2 8 ) and back cover(76). See Fig. 12 Remove the screws (82'2) and'front cooler cover (16). See Fig. 12 Fig. 12 MS% 6. Disconnect the hose (35) See Fig. 13. 7. Removethe screws (49) and cooler (44).Clean it. See Fig. 13. and inspect the cooler or replace Disconnectthe hose (92) located under the cooler. See Fia 13. 35 8. Wash the air filter (21) and reassemble unit. Compressor Repair 1. Follow the Pressure Relief Procedure, page 7. 2. Remove the pot. See page 5. HOT SURFACE HAZARD Be surethecompressorductwork is cool before removing It. If the sprayer was operated recently,it will be very hot and bums1 can cause 3. Removetheairfilter 4. (21). Remove the three screws (82A). Pull the cover (23) straight out. 5. Pull the bracket (22) up and off. NOTE: Clean the cooler whenever the compressor is sewiced A compressor rebuild kit, part no.224-989, is available. The kit includes instructions. For repair assistance or for compressor service center locations, c a l l your local Graco distributor or 1-800-888-2468. NO= 6. Remove thetwo screws (826) and the four screws (82C). Remove the shroud(e). 7. If you are only rebuilding the compressor (48). see the manual supplied with the rebuild kit. Clean the air filter (21) and reassemblethe unit. NOTE To remove the compressor, continue on page 16. Fig. 14 308-588 15 Compressor Repair . . Remove the m w s (82A)and the top cover (11). See Fig. 15. Remove the screws (828) and the back cover (76). See Fig. 15. 13. At the compressor. disconnect the other end of the tube (19).Be careful not to bend the tube. 14. Remove the front screws (25) and loosen the rear screws (27). Pull the compressor(48) forward. 0. Remove the screws (82C) and thelower back cover (13). 1. Disconnect the wires at the compressor motor. They are located behind the motor access Plate (E)1 2 Disconnect the hose (92). located under the cooler. See Fig. 15. 15. Replace the compressor motorin the reverse order of disassembly. Be sure the sleeve (53) is in place when securingthe tube(19) to the front of the compressor. . NOTE See the wiring diagram on page19. A Add sealant (100)to threads Fig. 15 16 05595 308-580 Notes . 308-588 17 Parts NOTE:See additional sprayer partslist and drawing on pages 20 through 23. 21 ’ 93 101 QSm7 Parts Model 231-371 with 238-080 Rexhead texture gun Model 231 -372 with 238-177 Trigger-style texture gun Ret Na Part No. Description Qty. Ref No Part No. Description 11 12 13 14 15 16 18 ID 20 21 189-264 TOP SHIELD, cooler 189-285 caution LABEL, 789-119 endbell SHROUD, 189-286 LABEL,warning 189-1 20 SHROUD, motor 184-452 SHIELD, splash 290-177 LABEL, 23&503 SHROUD, compressor, front 184-284 FILTER, air 789-251 BRACKET, intake, alr 189-1 43 HOUSING, air intake, 111-841 WASHER, Plain, 5/8 In. 113-115 WHEEL. semi-pneumatic. 8 in. x 1.75 in. 236370 FRAME, sprayer, texture 189-265 danger LABEL, 238-081 HOSE Sm,1 in. fluid x 3 8 In. air 22 23 29 31 34 37 39 Qty 1 4 1 4 1 1 1 1 -1 1 1 6 2 1 1 1 42 52 56 74 76 81 113-118 109-574 104-514 113-405 236-371 238-043 SCREW, shoulder, socket head 2 SWITCH, rocker 1 BUSHING, strain relief 1 RIVET, push, .25 in. dia 2 SHIELD, cooler 1 SPONGES, 1 hose cleaning (5 I pkg.) (not shown) 82 112400 SCREW, pnh, thrd forming 25 93 238-080 KIT, spray gun, flexhead 1 (included in 231971, see Manual 308403) 1 0 1 238-177 KIT, spray gun, texture 1 (included in 231-372. see Manual 308-162) 105 M71-511 RIVET, push, .19 in. dia. 2 Wiring Diagram i. 19 308-588 Parts i 71 Parts Model 231-371 with 238-080 flexhead texture gun Model 231-372 with 238-177 Trigger-styletexture gun Ref. No. Part No. 1 2 4 5 26 KNOB, 1/4-20 stud 1 PLATE, float 1 KNOB, 5/16 insert in. 2 1 KNOB, pronged 3 BOLT, carriage 8 WASHER, flat 100-840 ELBOW, street, 1/4npt in. 1 steellock, 2 107-527 NUT, 112-374 COUPLER, FemEie, 1 in. npt 1 100-016 WASHER, lock 1 headhex 3 100-021 SCREW, 169-970 FIlTING,air, line, (m) 1 stand. PLATE, 1 1!3C-809 1 238-074 POT, pressure (includes itemsa through d below) 5 190-966 KNOB,cover 30 32 36 43 46 47 63 69 70 70a 113-1122 190-803 . 112-116 108-471 111-570 110-755 Description Qty. Ref No 70b 70c 70d 71 75 77 83 e4 85 87 a8 103 I09 110 111 Part No. Description Qty 238-1 90 COVER, pressure pot (includes items c and below) d 190-964 GASKET. cover 190-965 VALVE, safely, cover 238-079 PLATE,retaining,pressure pot 238-075 BAND, retaining, pressure pot 190-804 STOP, float 113-119 ELBOW, Bronze, 90a 112-1120 NIPPLE,brass, 1 in.npt x 4 in. 113-121 VALVE, ball 113-379 VALVE, vent, 114 in. x 1/4 in. 113-096 MUFFLER, Valve, Bail 110-436 GAUGE, press, air, 0-60 psi. 190-938 GUARD, gauge 113-336 ADAPTER 1/4 in. npt (m x 9 113-373 WASHER, spring 10 mm 308-588 1 1 1 1 1 1 1 1 1 1 1 1 1 1 1 21 . 308-588 Parts Model 231 -372 with 238-177 Trigger-style texture gun Model 231-371 with 238-080 Flexhead texture gun Ref. NO. Part No. Description QW 113-385 BARB, 9 hose safety, 100 psi 190-951 VALVE, 10 SCREW, pnh 17 110 4 3 7 mach, 238-1 65 TUBE. air, outlet 19 111-585 PAD, vibration; compressor 24 112-389 SCREW, shoulder, hex hd. 25 head hex SCREW, 111-597 27 28 BRACKET, 187439 mounting street, 114 2npt 32 100-840 ELBOW, 113-382 CLAMP, Hose 33 35 Air, HOSE, 4 113-380 38 ' 104441 bulkhead FIlTING. 41 Pipe 183-663 TEE, 44 187-480 COOLER, air air, 3.5 HP 112-404 COMPRESSOR, 48 (see Manual 308-185for patts) head hex SCREW, 49 100-333 air line,Coupler, 206-536 50 outlet, compressor 111-573 SLEEVE, 53 111-572 NUT, compression 54 236-374 CORD SET 55 236369 CONDUCTOR, 57 ground ground symbol 1 186-620 LABEL. 58 electrical 236-375 CONDUCTOR, 59 ' 1 1 1 1 2 2 2 1 4 1 1 1 1 1 1 2 1 1 1 1 1 Ref No Part No. Description 90 91 169-970 111-583 111-586 111-962 111-593 190-806 162-453 92 94 96 100 113-381 106228 100-606 110-110 FllTING. line, air, (m) PAD, vibration, motor FAN,'compressor SCREW, buttonhead. 1/4-28 SCREW, grounding HOSE, air, W8 in. x 20 ft NIPPLE, adapter, 114 npt x 114 npsm HOSE, air, 1.5 TEE, street NIPPLE, Close SEALAM. thread, pipe (not shown) REGULATOR, air, 114 npt PLUG, pipe, 114 npt (included in 102) FITTING, line, air, (f) 63 65 66 68 80 102 113-406 102a 100-721 112 169-967 Qty 1 1 1 1 1 1 1 1 2 '3 1 1 2 1 Repair.Kits 224-909 Compressor Rebuild Kit Keep a repair kit on hand to reduce down time. Accessories HOSE SET. 5 m (165 ft) FLUSHING 238-185 ADAPTER Ruid and air hose set forhard-io-pumpmaterialsAllowsconnectionof 238-043 for faster hose cleanup HOSE CLEANUP BALLS 190-952 fluid hosetostandardgardenhose 5 sponge rubber ballsto help scrub interior surface of hose during cleanup ' 308-500 23 Technical Data ............ dadmum Alr andnuid Wetted Polyethylene. Parts Stainless Steel. Working Pressure 4ir Pressure Ope-g Range ;Jmpressor Specifications Sound Data Sound Pressure Level.. ................. 100 psi (6.9 bar) 25-1 00 psi (1.75-7 bar) .. AC brushless open motor. ................. 91.4 dB(A) .................... 106.5 dB(A) thermally protected. honest: Sound Power L e v e l 110/230volt 15n.5AmD Air Consumption 11.9 displacement SCFM 8.5 sdm at 40 psi (0.238 mJ/min at2 8 bar) 6.8 sdm a 9 0 psi (0.19 m3/min at6.3 bar) . hp- vla%imumLk?keIywith TexIm Material %ssure Poi Ca~acihr 3imensions L e @ .......... 1-1.5 Graco Phone Numbers gpm (3.8-5.7 Ipm) . . ............ 5 aallons - (19 liters) .................17 In. (432 mm) with handle 21.5 in. (546 mm) without handle Wdth .......................... 21.5 in. (546 mm) ........................... .... Height 37 In. (940 mm) Weight System w/ohosesorgun 111 ib (50.5 kg) System with hoses andgun (231 -371) 112 Ib (51 kg) System with hoses and gun(231-372) 113 Ib (51.5 kg) Buna-N. Aluminum. Brass TO P U C E AN ORDER, contacl your Graco distributor. or cal this numberto identify the distributor closest to you: 1-800-367-4023 Toll Free FOR TECHNICAL ASSETANCE, repair service of informationor assistance regarding the application Graco equipment 1-800-543-9339 Toll Free The Graco Warranty and Disclaimers . WARRANTY 3racowarramal equipment manufactured by it and bearingits nameto be free from defects In material and workmanship on the date ofsaleby an authorized Graco distributorto the original purchaserfor use. As purchaser's soli remedy for breach t of hiswar- rarity. Gram win. for aperiod of twelve months from the date of sale, repair or replace any part of the equipment proven defective. iWs wananty applies only when the equipment is installed. operated and maintained in accordance with Graco's written recommendations. This warranty does not cover. and Graco shall not be liable for, any malfunction. damage orwear caused by faulty installation, misapplication. abrasion, COROSIU~, inadequate or improper maimenance, negligence, accident tampering, or substitution of nonGraco mmponent parts. Nor shall Graco be liable for malfunction. damage or c awear m d by the incompatibility with Graco equipmentof structures, accessories. equipment or materials not supplied by Gram, orthe improper design, mapdamre, instaila- , , 6on. operationormaintenanceofstructures,accessories,equipmentormaterials not suppliedbyGraco. This wimaroy is mndiioned upon the prepaid return of the equipment daimed to be defective to an authorized Graco distributor forverificafionof the claim. ifthe claimed defectis verified, Gracowil repair or replace free of charge any defective pat%The I equipm+$ll be refumedto the original purchaser transportation prepaid. if inspection of the equipment does not disclose any defect in material or workmanship, repairs will be made at a reasonable charge, which charges may Include the costs of parts, labor and lmsporgtion. DlSClAlMERS AND LIMITATIONS . The term ofthis wrranty constitute purchaser's sole and exclusive remedy and are In lieu of any other warranties or (express implied). lndudlngwananly of merchantabllltyor warranty of fitness fora partlcular purpose, and of any non-contractual ~abimies.inclrdingproductliabnities. based onnegligence orstrictiiability. Every form ofliabililfordirect, special orconsequentlal ' damages0 r l w S Is ercpressly excluded and denied.Inno case shall Graco's liability exceed the amount ofthe purchase price. Any action for h a c hOf Warranty must be brought within two (2) years of the dateofsale. mum- NOT COVERED BY GRACO WARRANIY Gram makes no Wamftj',and disclaimsal Implied warrantlesof merchantability andfitness tor a particular purpose, with r€!SPa.tO ZCCeSOrieS, equipment, materials, or components sold but not manufactured by Graco. These items sold, but not a$ electric motor, switches, hose, etc.) are subject to the warranty,I any, of their manufacturer. manufactured by Gram (such S~ZCO W a @de purchaser with reasonable assistance in making any claim for breach of these warranties. Sales Offlces: Atlanta, Chicago, DetroitLos Angeies, F m g n offices: Belgium; Canada; England; Korea: Switzerland; France; Germany; Hong Kong; Japan GRACOINC. 96 30R-SRR P.O. BOX 1441 MINNEAPOLIS, MN 55440-1441 PRINTED IN U.SA 308-588 October 1995
advertisement
Related manuals
advertisement