- Home
- Do-It-Yourself tools
- Power tools
- Paint Sprayer
- Graco
- 3A4603A, LineLazer™ ES 1000 Airless Line Stripers
- Owner's manual
advertisement
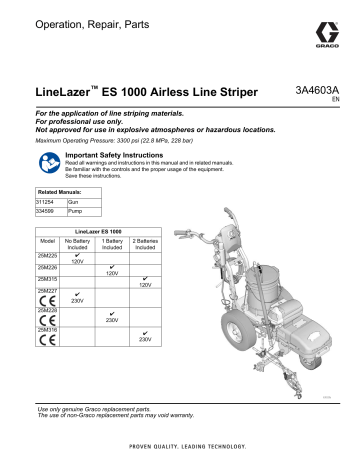
Operation, Repair, Parts
LineLazer
™
ES 1000 Airless Line Striper
For the application of line striping materials.
For professional use only.
Not approved for use in explosive atmospheres or hazardous locations.
Maximum Operating Pressure: 3300 psi (22.8 MPa, 228 bar)
Important Safety Instructions
Read all warnings and instructions in this manual and in related manuals.
Be familiar with the controls and the proper usage of the equipment.
Save these instructions.
Related Manuals:
311254
334599
Gun
Pump
Model
25M225
25M226
25M315
25M227
LineLazer ES 1000
No Battery
Included
120V
1 Battery
Included
120V
230V
25M228
230V
25M316
2 Batteries
Included
120V
230V
3A4603A
EN ti30320a
Use only genuine Graco replacement parts.
The use of non-Graco replacement parts may void warranty.
2
Table of Contents
Warnings . . . . . . . . . . . . . . . . . . . . . . . . . . . . . . . . . 3
Tip Selection . . . . . . . . . . . . . . . . . . . . . . . . . . . . . . 7
Component Identification (ES 1000) . . . . . . . . . . . 8
Battery and Charger . . . . . . . . . . . . . . . . . . . . . . . . 9
Battery Disposal . . . . . . . . . . . . . . . . . . . . . . . . . 9
Battery Type and Charging Profiles . . . . . . . . . . 9
Charging the Battery . . . . . . . . . . . . . . . . . . . . . 10
(AC Wall Power) . . . . . . . . . . . . . . . . . . . . . . . 11
Power Requirements . . . . . . . . . . . . . . . . . . . . 11
Extension Cords . . . . . . . . . . . . . . . . . . . . . . . . 11
Pails . . . . . . . . . . . . . . . . . . . . . . . . . . . . . . . . . 11
(Battery Power) . . . . . . . . . . . . . . . . . . . . . . . . 12
Pails . . . . . . . . . . . . . . . . . . . . . . . . . . . . . . . . . 12
Pressure Relief Procedure . . . . . . . . . . . . . . . . . . 13
Setup/Startup . . . . . . . . . . . . . . . . . . . . . . . . . . . . . 14
SwitchTip and Guard Assembly . . . . . . . . . . . . 15
Gun Placement . . . . . . . . . . . . . . . . . . . . . . . . . . . 16
Install Gun . . . . . . . . . . . . . . . . . . . . . . . . . . . . . 16
Position Gun . . . . . . . . . . . . . . . . . . . . . . . . . . . 16
Select Guns . . . . . . . . . . . . . . . . . . . . . . . . . . . 16
Gun Positions Chart . . . . . . . . . . . . . . . . . . . . . 17
Gun Arm Mounts . . . . . . . . . . . . . . . . . . . . . . . . 18
(Front and Back) . . . . . . . . . . . . . . . . . . . . . 18
(Left and Right) . . . . . . . . . . . . . . . . . . . . . . 18
Installation . . . . . . . . . . . . . . . . . . . . . . . . . . . . . 19
Gun Cable Adjustment . . . . . . . . . . . . . . . . . . . 19
Straight Line Adjustment . . . . . . . . . . . . . . . . . . 20
Handle Bar Adjustment . . . . . . . . . . . . . . . . . . . 20
Paint Stripe Width . . . . . . . . . . . . . . . . . . . . . . . . . 21
Spray Test Stripe . . . . . . . . . . . . . . . . . . . . . . . 21
Clearing Tip Clogs . . . . . . . . . . . . . . . . . . . . . . 21
Cleanup . . . . . . . . . . . . . . . . . . . . . . . . . . . . . . . . . 22
Fast Flush Drain Tube . . . . . . . . . . . . . . . . . . . 22
Fast Flush Hose and Gun . . . . . . . . . . . . . . . . . 23
Maintenance . . . . . . . . . . . . . . . . . . . . . . . . . . . . . . 24
Troubleshooting . . . . . . . . . . . . . . . . . . . . . . . . . . . 25
Mechanical/Fluid Flow . . . . . . . . . . . . . . . . . . . . 25
Electrical . . . . . . . . . . . . . . . . . . . . . . . . . . . . . . 27
Sprayer Will Not Run . . . . . . . . . . . . . . . . . . . . . 32
Sprayer Will Not Shut Off . . . . . . . . . . . . . . . . . 34
Inverter . . . . . . . . . . . . . . . . . . . . . . . . . . . . . . . 35
Battery Will Not Charge . . . . . . . . . . . . . . . . . . . 37
Parts Drawing - LineLazer ES 1000 . . . . . . . . . . . 38
Parts List . . . . . . . . . . . . . . . . . . . . . . . . . . . . . . . . . 39
Parts Drawing - LineLazer ES 1000 . . . . . . . . . . . 40
Parts List . . . . . . . . . . . . . . . . . . . . . . . . . . . . . . . . . 41
Parts Drawing - LineLazer ES 1000 . . . . . . . . . . . 42
Parts List . . . . . . . . . . . . . . . . . . . . . . . . . . . . . . . . . 43
Parts Drawing - LineLazer ES 1000 . . . . . . . . . . . 44
Parts List . . . . . . . . . . . . . . . . . . . . . . . . . . . . . . . . . 45
Swivel Wheel Assembly . . . . . . . . . . . . . . . . . . 45
Filter . . . . . . . . . . . . . . . . . . . . . . . . . . . . . . . . . . 45
Parts Drawing - LineLazer ES 1000 . . . . . . . . . . . 46
Parts List . . . . . . . . . . . . . . . . . . . . . . . . . . . . . . . . . 47
Gun Holder and Arm . . . . . . . . . . . . . . . . . . . . . 47
Gun Trigger . . . . . . . . . . . . . . . . . . . . . . . . . . . . 47
Parts Drawing - LineLazer ES 1000 . . . . . . . . . . . 48
Parts List . . . . . . . . . . . . . . . . . . . . . . . . . . . . . . . . . 49
Voltage Meter Box, 120V . . . . . . . . . . . . . . . . . . . . 50
Voltage Meter Box, 230V . . . . . . . . . . . . . . . . . . . . 50
Parts List . . . . . . . . . . . . . . . . . . . . . . . . . . . . . . . . . 51
Voltage Meter Box, 120V . . . . . . . . . . . . . . . . . . 51
Voltage Meter Box, 230V . . . . . . . . . . . . . . . . . . 51
Control Box, 120V . . . . . . . . . . . . . . . . . . . . . . . . . 52
Control Box, 230V . . . . . . . . . . . . . . . . . . . . . . . . . 52
Parts List . . . . . . . . . . . . . . . . . . . . . . . . . . . . . . . . . 53
Control Box, 120V . . . . . . . . . . . . . . . . . . . . . . . 53
Control Box, 230V . . . . . . . . . . . . . . . . . . . . . . . 53
Wiring Diagram . . . . . . . . . . . . . . . . . . . . . . . . . . . 54
120V . . . . . . . . . . . . . . . . . . . . . . . . . . . . . . . . . 54
230V . . . . . . . . . . . . . . . . . . . . . . . . . . . . . . . . . 55
Control Board Wiring Diagram . . . . . . . . . . . . . . . 56
110/120V . . . . . . . . . . . . . . . . . . . . . . . . . . . . . . 56
230V . . . . . . . . . . . . . . . . . . . . . . . . . . . . . . . . . 57
Technical Specifications . . . . . . . . . . . . . . . . . . . . 58
Electrical Specifications . . . . . . . . . . . . . . . . . . . . 59
Graco Standard Warranty . . . . . . . . . . . . . . . . . . . 60
3A4603A Operation, Repair, Parts
Warnings
Warnings
The following warnings are for the setup, use, grounding, maintenance, and repair of this equipment. The exclamation point symbol alerts you to a general warning and the hazard symbols refer to procedure-specific risks. When these symbols appear in the body of this manual or on warning labels, refer back to these Warnings. Product-specific hazard symbols and warnings not covered in this section may appear throughout the body of this manual where applicable.
GROUNDING
This product must be grounded. In the event of an electrical short circuit, grounding reduces the risk of electric shock by providing an escape wire for the electric current. This product is equipped with a cord having a grounding wire with an appropriate grounding plug. The plug must be plugged into an outlet that is properly installed and grounded in accordance with all local codes and ordinances.
• Improper installation of the grounding plug is able to result in a risk of electric shock.
• When repair or replacement of the cord or plug is required, do not connect the grounding wire to either flat blade terminal.
• The wire with insulation having an outer surface that is green with or without yellow stripes is the grounding wire.
• Check with a qualified electrician or serviceman when the grounding instructions are not completely understood, or when in doubt as to whether the product is properly grounded.
• Do not modify the plug provided; if it does not fit the outlet, have the proper outlet installed by a qualified electrician.
• This product is for use on a nominal 120V or 230V circuit and has a grounding plug similar to the plugs illustrated below.
120V US 230V ti24583a
• Only connect the product to an outlet having the same configuration as the plug.
• Do not use an adapter with this product.
Extension Cords:
• Use only a 3-wire extension cord that has a grounding plug and a grounding receptacle that accepts the plug on the product.
• Make sure your extension cord is not damaged. If an extension cord is necessary use 12 AWG (2.5mm
2 ) minimum to carry the current that the product draws.
• An undersized cord results in a drop in line voltage and loss of power and overheating.
3A4603A Operation, Repair, Parts 3
Warnings
FIRE AND EXPLOSION HAZARD
Flammable fumes, such as solvent and paint fumes, in work area can ignite or explode. To help prevent fire and explosion:
• Do not spray flammable or combustible materials near an open flame or sources of ignition such as cigarettes, motors, and electrical equipment.
• Paint or solvent flowing through the equipment is able to result in static electricity. Static electricity creates a risk of fire or explosion in the presence of paint or solvent fumes. All parts of the spray system, including the pump, hose assembly, spray gun, and objects in and around the spray area shall be properly grounded to protect against static discharge and sparks. Use Graco conductive or grounded high-pressure airless paint sprayer hoses.
• Verify that all containers and collection systems are grounded to prevent static discharge. Do not use pail liners unless they are antistatic or conductive.
• Connect to a grounded outlet and use grounded extensions cords. Do not use a 3-to-2 adapter.
• Do not spray flammable or combustible liquids in a confined area.
• Sprayer generates sparks. Keep spray area well-ventilated. Keep a good supply of fresh air moving through the area.
• Keep pump assembly in a well ventilated area when spraying, flushing, cleaning, or servicing. Do not spray pump assembly.
• Do not smoke in the spray area or spray where sparks or flame is present.
• Do not operate light switches, engines, or similar spark producing products in the spray area.
• Keep area clean and free of paint or solvent containers, rags, and other flammable materials.
• Know the contents of the paints and solvents being sprayed. Read all Material Safety Data Sheets (MSDS) and container labels provided with the paints and solvents. Follow the paint and solvents manufacturer’s safety instructions.
• Fire extinguisher equipment shall be present and working.
SKIN INJECTION HAZARD
High-pressure spray is able to inject toxins into the body and cause serious bodily injury. In the event that injection occurs, get immediate surgical treatment.
• Do not aim the gun at, or spray any person or animal.
• Keep hands and other body parts away from the discharge. For example, do not try to stop leaks with any part of the body.
• Always use the nozzle tip guard. Do not spray without nozzle tip guard in place.
• Use Graco nozzle tips.
• Use caution when cleaning and changing nozzle tips. In the case where the nozzle tip clogs while spraying, follow the Pressure Relief Procedure for turning off the unit and relieving the pressure before removing the nozzle tip to clean.
• Equipment maintains pressure after power is shut off. Do not leave the equipment energized or under pressure while unattended. Follow the Pressure Relief Procedure when the equipment is unattended or not in use, and before servicing, cleaning, or removing parts.
• Check hoses and parts for signs of damage. Replace any damaged hoses or parts.
• This system is capable of producing 3300 psi. Use Graco replacement parts or accessories that are rated a minimum of 3300 psi.
• Always engage the trigger lock when not spraying. Verify the trigger lock is functioning properly.
• Verify that all connections are secure before operating the unit.
• Know how to stop the unit and bleed pressure quickly. Be thoroughly familiar with the controls.
4 3A4603A Operation, Repair, Parts
Warnings
EQUIPMENT MISUSE HAZARD
Misuse can cause death or serious injury.
• Do not operate the unit when fatigued or under the influence of drugs or alcohol.
• Do not exceed the maximum working pressure or temperature rating of the lowest rated system component. See Technical Data in all equipment manuals.
• Use fluids and solvents that are compatible with equipment wetted parts. See Technical Data in all equipment manuals. Read fluid and solvent manufacturer’s warnings. For complete information about your material, request Safety Data Sheet (SDS) from distributor or retailer.
• Do not leave the work area while equipment is energized or under pressure.
• Turn off all equipment and follow the Pressure Relief Procedure when equipment is not in use.
• Check equipment daily. Repair or replace worn or damaged parts immediately with genuine manufacturer’s replacement parts only.
• Do not alter or modify equipment. Alterations or modifications may void agency approvals and create safety hazards.
• Make sure all equipment is rated and approved for the environment in which you are using it.
• Use equipment only for its intended purpose. Call your distributor for information.
• Route hoses and cables away from traffic areas, sharp edges, moving parts, and hot surfaces.
• Do not kink or over bend hoses or use hoses to pull equipment.
• Keep children and animals away from work area.
• Comply with all applicable safety regulations.
ELECTRIC SHOCK HAZARD
This equipment must be grounded .
Improper grounding, setup, or usage of the system can cause electric shock.
• Turn off, disconnect power cord, and disconnect battery before servicing equipment.
• Connect only to grounded electrical outlets.
• Use only 3-wire extension cords.
• Ensure ground prongs are intact on power and extension cords.
• Do not expose to rain. Store indoors.
• Wait thirty minutes after disconnecting power cord before servicing.
MOVING PARTS HAZARD
Moving parts can pinch, cut or amputate fingers and other body parts.
• Keep clear of moving parts.
• Do not operate equipment with protective guards or covers removed.
• Pressurized equipment can start without warning. Before checking, moving, or servicing equipment, follow the Pressure Relief Procedure and disconnect all power sources.
TOXIC FLUID OR FUMES HAZARD
Toxic fluids or fumes can cause serious injury or death if splashed in the eyes or on skin, inhaled, or swallowed.
• Read Safety Data Sheet (SDS) to know the specific hazards of the fluids you are using.
• Store hazardous fluid in approved containers, and dispose of it according to applicable guidelines.
BURN HAZARD
Equipment surfaces and fluid that’s heated can become very hot during operation. To avoid severe burns:
• Do not touch hot fluid or equipment.
3A4603A Operation, Repair, Parts 5
Warnings
PERSONAL PROTECTIVE EQUIPMENT
Wear appropriate protective equipment when in the work area to help prevent serious injury, including eye injury, hearing loss, inhalation of toxic fumes, and burns. This protective equipment includes but is not limited to:
• Protective eyewear, and hearing protection.
• Respirators, protective clothing, and gloves as recommended by the fluid and solvent manufacturer.
BATTERY HAZARD
The battery may leak, explode, cause burns, or cause an explosion if mishandled. Contents of an open battery can cause severe irritation and/or chemical burns. If on skin, wash with soap and water. If in eyes, flush with water for at least 15 minutes and get immediate medical attention.
• Only use the battery type specified for use with the equipment. See Technical Data .
• Connecting cables to the battery creates sparks. Replace battery only in well-ventilated area and away from flammable or combustible materials, including paints and solvents.
• Remove watches, rings or other metal objects before servicing.
• Only use tools with insulated handles. Do not lay tools or metal parts on top of battery.
• Do not dispose of battery in fire or heat above 50°C (122°F). The battery is capable of exploding.
• Do not throw into fire.
• Do not expose battery to water or rain.
• Do not disassemble, crush, or penetrate the battery.
• Do not use or charge a battery that is cracked or damaged.
• Follow local ordinances and/or regulations for disposal.
CALIFORNIA PROPOSITION 65
This product contains a chemical known to the State of California to cause cancer, birth defects or other reproductive harm. Wash hands after handling.
6 3A4603A Operation, Repair, Parts
Tip Selection
Tip Selection
LL5329
LL5331
LL5333
LL5335
LL5355
LL5417
LL5419
LL5421
LL5423
LL5425
LL5427
LL5429
LL5431
LL5435
LL5621
LL5623
LL5213*
LL5215*
LL5217
LL5219
LL5315
LL5317
LL5319
LL5321
LL5323
LL5325
LL5327
LL5625
LL5627
LL5629
LL5631
LL5635
LL5639
in.
(cm)
2 (5)
2 (5)
in.
(cm)
4 (10)
4 (10)
4 (10)
4 (10)
4 (10)
4 (10)
4 (10)
4 (10)
4 (10)
4 (10)
4 (10)
4 (10)
4 (10)
4 (10)
*Use 100 mesh filter to reduce tip clogs.
in.
(cm)
6 (15)
6 (15)
6 (15)
6 (15)
6 (15)
6 (15)
6 (15)
6 (15)
6 (15)
in.
(cm)
12 (30)
12 (30)
12 (30)
12 (30)
12 (30)
12 (30)
12 (30)
12 (30)
3A4603A Operation, Repair, Parts 7
Component Identification (ES 1000)
Component Identification (ES 1000)
1
2
2
4
5
8
1
3
6
7
10
9
11
13
5
12
3
4
6
9
7
8
PRIME
10
SPRAY
11
16
12
15
14
17
13 14 15 16 17 ti30321a
8
1 ON/OFF switch
2 Pressure control
3 Spray gun trigger
4 Turn control
5 Filter
6 Gauge
7 Prime/Pressure valves
8 Drain and siphon hoses
9 Battery compartment
10 Inverter circuit breakers
11 Pump
12 Trigger safety
13 Fuse
14 Charging port
15 Voltage meter
16 LED status center
17 Serial ID
3A4603A Operation, Repair, Parts
Battery and Charger
Battery and Charger
• The LineLazer ES 1000 is designed to work with one or two 12V 100 Ahr DEEP CYCLE Absorbent
Glass Mat (AGM) batteries. Maximum battery size is
13” x 9” x 7” (33cm x 23cm x 18cm).
• Battery Protection Features: Unit is designed to protect the battery by shutting down at 10.5V and not allowing charging to occur above 15.5V.
• Battery Operating Temperature: -4-140°F
(-20-60°C)
• Battery Charging Temperature: 14-140°F
(-10-60°C)
• Battery Storage Temperature: -4-140°F
(-20-60°C)
• Self Discharge: Lead acid batteries can self-discharge in as little as 3 months depending on storage temperatures. The hotter the storage temperature, the faster the self-discharge occurs. To prevent damage to the battery, it is important to keep the battery in a charged state.
• Battery Life: Battery recharge cycles depend on the depth of discharge per cycle. A battery that is discharged to 50% depth will get over twice as many cycles in its life compared to it being discharged to 100% depth each cycle.
Battery Disposal
Do not place batteries in the trash. Recycle batteries according to local regulations.
Battery Type and Charging Profiles
Graco recommends using a 12V 100 Ahr Absorbent
Glass Mat (AGM) DEEP CYCLE battery.The charger is set for this charging profile from the factory. If a different battery is used, the charging profile can be set at the
LED Status Center. The initial charge rate is 30 amps.
Only use batteries that allow an initial charge rate of 30 amps or higher.
Use a small flat head screw driver to turn the arrow to point at the number that correlates with the chosen battery.
0
1
2
3
4
5
6
7
8
9
BATTERY TYPE SELECTOR SETTINGS
Switch
Position Description Boost/Vdc Float/Vdc
14.0
14.1
14.6
Sealed Lead Acid 14.4
Open Lead Acid
Calcium
De-sulphation
13.7
13.4
13.7
13.6
14.4
14.8
13.8
13.3
15.1 13.6
15.5
(4 hours then Off) ti30488a
3A4603A Operation, Repair, Parts 9
Battery and Charger
Charging the Battery
Replace and charge battery only in well-ventilated area and away from flammable or combustible materials, including paints and solvents.
Use an extension cord with an undamaged ground contact. If an extension cord is necessary, use a 3-wire, 12
AWG (2.5 mm 2 ) minimum.
Batteries are fully charged when leaving the factory.
Due to self-discharging of the battery, charge battery before first use. It takes ~3 hours to charge a dead battery to 80%. It takes ~5 hours to charge a fully depleted battery (double these times for 2 battery unit).
1.
Place unit in dry, well-ventilated area and away from flammable or combustible materials, including paints and solvents.
2.
Ensure power switch is in OFF position.
3.
Plug charging cord into charging port on the unit.
Connect an extension cord, minimum 12AWG
(2.5mm
2
), to the charging cord and plug it into wall power.
ti30358a
4.
When power is connected the voltmeter will turn on and the charger will immediately begin charging.
User should be able to see voltmeter start to climb to indicate charging is occurring. ti30359a
5.
Battery will charge to 14.6-14.8 volts and then it will come back down to ~13.6 volts when fully charged.
ti30322a ti30360a
10 3A4603A Operation, Repair, Parts
Grounding Procedure
(AC Wall Power)
Grounding Procedure (AC Wall Power)
Do not place pail on a non-conductive surface such as paper or cardboard which interrupts grounding continuity.
This equipment must be grounded to reduce the risk of static sparking and electric shock. An electric shock or static spark can cause fumes to ignite or explode. An improper ground can cause electric shock. A good ground provides an escape wire for the electric current.
Position the striper so the wheels are on a true grounded surface. Not on pavement.
The plug must be plugged into an outlet that is properly installed and grounded in accordance with all local codes and ordinances.
Do not modify the plug provided; if it does not fit the outlet, have the proper outlet installed by a qualified electrician.
Always ground a metal pail: connect a ground wire to the pail. Clamp one end to the pail and the other end to a true earth ground such as a water pipe.
Power Requirements
• 100-120V units require 100-120 VAC, 50/60 Hz, 12 or 15A, 1 phase.
• 230V units require 230 VAC, 50/60 Hz, 7 or 9A, 1 phase.
ti24584a
To maintain ground continuity when sprayer is flushed or pressure is relieved: hold metal part of spray gun firmly to the side of a grounded metal pail then trigger gun.
Extension Cords
Use an extension cord with an undamaged ground contact. If an extension cord is necessary, use a 3-wire, 12
AWG (2.5 mm 2 ) minimum.
Pails
Solvent and oil-based fluids: follow local code. Use only conductive metal pails, placed on a grounded surface such as concrete.
ti24585a
3A4603A Operation, Repair, Parts 11
Grounding Procedure (Battery Power)
Grounding Procedure
(Battery Power)
Do not place pail on a non-conductive surface such as paper or cardboard which interrupts grounding continuity.
This equipment must be grounded to reduce the risk of static sparking. Static sparking can cause fumes to ignite or explode. Grounding provides an escape wire for the electric current.
1.
Position striper so that the tires are not on pavement.
2.
Striper is shipped with a grounding clamp.
Grounding clamp must attach to grounded object
(e.g., metal sign post).
Always ground a metal pail: connect a ground wire to the pail. Clamp one end to the pail and the other end to a true earth ground such as a water pipe.
ti27615a
Pails
Solvent and oil-based fluids: follow local code. Use only conductive metal pails, placed on a grounded surface such as concrete.
ti24584a
To maintain ground continuity when sprayer is flushed or pressure is relieved: hold metal part of spray gun firmly to the side of a grounded metal pail then trigger gun.
ti24585a
12 3A4603A Operation, Repair, Parts
Pressure Relief Procedure
Pressure Relief Procedure
3.
Turn pressure control to lowest setting. Trigger all guns to relieve pressure.
This equipment stays pressurized until pressure is manually relieved. To help prevent serious injury from pressurized fluid, such as skin injection, splashing fluid and moving parts, follow the Pressure Relief
Procedure when you stop dispensing and before cleaning, checking, or servicing the equipment.
1.
Perform Grounding Procedure if using flammable materials.
2.
Turn ON/OFF Switch to OFF . v
4.
Engage all gun trigger locks. Turn prime valve down. ti30323a ti30322a
5.
If you suspect the spray tip or hose is clogged or that pressure has not been fully relieved: a.
VERY SLOWLY loosen the tip guard retaining nut or the hose end coupling to relieve pressure gradually.
b.
Loosen the nut or coupling completely.
c.
Clear the obstruction in the hose or tip.
3A4603A Operation, Repair, Parts 13
Setup/Startup
Setup/Startup
5.
Turn On/OFF Switch to OFF .
1.
Perform
Pressure Relief Procedure , page 13 .
2.
Charge Battery
3.
Perform
Grounding Procedure (AC Wall Power) , page 11,
or Grounding Procedure (Battery
Power) , page 12, if using flammable materials.
4.
Fill throat packing nut with TSL to prevent premature packing wear. Do this daily or each time you spray.
a.
Place the TSL bottle nozzle into the top center opening in the grill at the front of the sprayer.
b.
Squeeze bottle to dispense enough TSL to fill the space between the pump rod and packing nut seal.
ti30322a
6.
If removed, install strainer.
ti27612a
7.
Turn prime valve down. Turn pressure control counterclockwise to lowest pressure.
ti24639a
NOTE: If running off wall power, plug cord into charging port. If using an extension cord, use a 3-wire, 12 AWG
(2.5mm
2
) minimum with an undamaged ground contact.
NOTE: Minimum hose size for proper sprayer operation is 1/4 in. x 50 ft for LL ES 1000.
8.
Place siphon tube set in grounded metal pail partially filled with flushing fluid. Attach ground wire to true earth ground. Use water to flush water-based paint and mineral spirits to flush oil-based paint and storage oil.
14 ti27613a
3A4603A Operation, Repair, Parts
9.
Turn ON/OFF Switch to ON:
Setup/Startup
13. Inspect fittings for leaks. If leaks occur, turn sprayer
OFF immediately. Perform
Pressure Relief Procedure , page 13. Tighten leaky fittings. Repeat
, steps 1 - 17. If no leaks, continue to trigger gun until system is thoroughly flushed. Proceed to step 18.
14. Place siphon tube in paint pails.
ti30324a
10. Turn pressure control to prime. Allow fluid to circulate for 15 seconds.
ti27613a
15. Trigger all guns again into a flushing fluid pail until paint appears. Assemble tips and guards.
ti30325a
11. Turn pressure down, turn prime valve horizontal.
Disengage gun trigger lock.
ti27774a
SwitchTip and Guard Assembly
ti27771a
12. Hold all guns against a grounded metal flushing pail.
Trigger guns and increase fluid pressure slowly until pump runs smoothly. Turn up as needed to prime/spray.
To avoid serious injury from skin injection do not put your hand in front of the spray tip when installing or removing the spray tip and tip guard.
1.
Engage trigger lock. Use end of SwitchTip to press
OneSeal into tip guard, with curve matching tip bore.
ti30349a
High-pressure spray is able to inject toxins into the body and cause serious bodily injury. Do not stop leaks with hand or rag.
ti27775a
2.
Insert SwitchTip in tip bore and firmly thread assembly onto gun.
3A4603A Operation, Repair, Parts ti27776a
15
Gun Placement
Gun Placement
Install Gun
1.
Insert guns into gun holder. Tighten clamps.
Another option can be to swing the gun out at an angle and rotate the tip guard. This results in better visibility for the user.
ti27777a
Position Gun
2.
Position gun: up/down, forward/reverse, left/right.
See Gun Positions Chart , page 17 for examples.
ti28130a
Select Guns
3.
Connect gun cables to left or right gun selector plates.
16
1
2 ti27780a a.
One gun: Disconnect one gun selector plate from trigger. ti27778a
NOTE: When striping above a curb, the mounting clamp can be rotated for clearance.
ti27781a b.
Both guns simultaneously: Adjust both gun selector plates to the same position. ti27782a c.
Solid-skip and skip-solid: Adjust solid-line gun to position 1 and skip-line to position 2. ti27782a ti28129a
3A4603A Operation, Repair, Parts
Gun Placement
Gun Positions Chart
1
5
4
3
2
6
7
3A4603A Operation, Repair, Parts
1 One line
2 One line up to 24 in. (61cm) wide
3 Two lines
4 One line or two lines to spray around obstacles
5 One gun curb
6 Two gun curb
7 Two lines or one line up to 24 in. (61 cm) wide ti27786a
17
Gun Placement
Gun Arm Mounts
This unit is equipped with front and rear gun arm mounts.
3.
Slide gun arm assembly into desired gun arm mounting slot.
ti27797a
4.
Tighten gun arm knob into gun arm mounting slot.
ti30326a
Change Gun Position
(Front and Back)
1.
Loosen gun arm knob and remove from gun arm mounting slot.
ti27798a
NOTICE
Make sure all hoses, cables, and wires are properly routed through brackets and do NOT rub on tire.
Contact with tire will result in damaged hoses, cables, and wires.
Change Gun Position
(Left and Right)
Removal
1.
Loosen vertical gun arm knob on gun arm mounting bar and remove.
ti27796c
2.
Slide gun arm assembly (including gun and hoses) out from gun arm mounting slot.
18 ti30327a ti30328a
2.
Extend mounting bar on opposite side of the machine.
ti30329a
3A4603A Operation, Repair, Parts
Installation
1.
Install vertical gun mount onto gun bar.
Gun Placement
Gun Cable Adjustment
Adjusting the gun cable will increase or decrease the gap between the trigger plate and the gun trigger. To adjust trigger gap, perform the steps below.
1.
Use wrench to loosen locking nut on cable adjuster.
ti30330a
NOTE: Make sure all hoses, cables, and wires are properly routed through brackets.
ti27884a
2.
Loosen or tighten adjuster until desired result is achieved. NOTE: More thread exposed means less gap between gun trigger and trigger plate.
3.
Use wrench to tighten locking nut on the adjuster.
3A4603A Operation, Repair, Parts 19
Gun Placement
Straight Line Adjustment
The front wheel is set to center the unit and allow the operator to form straight lines. Over time, the wheel may become misaligned and will need to be readjusted. To re-center the front wheel, perform the following steps:
1.
Loosen bolt on the front wheel bracket.
4.
Roll the striper. Repeat steps 2 and 3 until striper rolls straight. Tighten bolt on wheel alignment plate to lock the new wheel setting. ti27813a
Handle Bar Adjustment
ti27810a
2.
If striper arcs to the right, loosen left set screw and tighten right set screw for fine tune adjustment.
ti27811a
3.
If striper arcs to the left, loosen right set screw and tighten left set screw.
20 ti27812a ti27814a
3A4603A Operation, Repair, Parts
Paint Stripe Width
Paint Stripe Width
1.
Adjust gun up or down to change paint stripe width.
2.
Trigger gun and spray test pattern. Slowly adjust pressure to eliminate heavy edges. Use smaller tip size if pressure adjustment can not eliminate heavy edges.
ti30103a
Clearing Tip Clogs
ti30305a
.015
Spray Test Stripe
1.
Disengage trigger lock.
.025
1.
Release trigger. Engage gun trigger lock. Rotate
Uni-Tip. Disengage gun trigger lock and trigger gun to clear the clog.
ti30078a ti30306a
2.
Engage gun trigger lock, return Uni-Tip to original position, disengage gun trigger lock and continue spraying.
3A4603A Operation, Repair, Parts 21
Cleanup
Cleanup
1.
Perform
Pressure Relief Procedure , page 13.
2.
Remove guard and SwitchTip from all guns.
Fast Flush Drain Tube
6.
Remove fluid intake and drain tube from paint, wipe excess paint off outside.
TI3371A
3.
Unscrew cap, remove filter. Assemble without filter. ti24709a
7.
Place siphon tube set in grounded metal pail partially filled with flushing fluid. Use water for water base paint and mineral spirits for oil-based paint.
8.
To flush drain tube and pump turn prime valve down. ti6269a
4.
Clean filter, guard and SwitchTip in flushing fluid.
TI 33 75A
FLUSH
5.
Attach ground wire to true earth ground or plug unit into grounded outlet. ti24713a
9.
Turn pressure control to Fast Flush operate until the pump runs steady and flushing fluid appears in the waste pail.
ti24991a
22 3A4603A Operation, Repair, Parts
Fast Flush Hose and Gun
10. To flush airless hose and spray gun, turn prime valve horizontal.
11. Hold gun against waste pail. Disengage trigger lock.
Trigger gun and turn pressure control to Fast Flush operate until the pump runs steady and flushing fluid appears.
Cleanup
12. Stop triggering gun.
13. Fill pump with Pump Armor and reassemble filter, guard and SwitchTip.
14. Each time you spray and store, fill throat packing nut with TSL to decrease packing wear. ti24991a
3A4603A Operation, Repair, Parts 23
Maintenance
Maintenance
Routine maintenance is important to ensure proper operation of your sprayer. Maintenance includes performing routine actions which keep your sprayer in operation and prevents trouble in the future.
Activity
Inspect/clean sprayer filter, fluid inlet strainer, and gun filter.
Inspect motor shield vents for blockage.
Fill TSL by adding through TSL fill point.
Check sprayer stall.
Interval
Daily or each time you spray
Daily or each time you spray
Daily or each time you spray
Every 1000 gallons (3785 liters)
With sprayer gun NOT triggered, sprayer motor should stall and not restart until gun is triggered again.
If sprayer starts again with gun NOT triggered, inspect pump for internal/external leaks and check prime valve for leaks.
Throat packing adjustment
When pump packing begins to leak after extended use, tighten packing nut down until leakage stops or lessens. This allows approximately 100 gallons of additional operation before a repacking is required. Packing nut can be tightened without 0-ring removal.
As necessary based on usage
24 3A4603A Operation, Repair, Parts
Troubleshooting
Troubleshooting
Mechanical/Fluid Flow
1.
Follow Pressure Relief Procedure , page 13, before
checking or repairing.
2.
Check all possible problems and causes before disassembling the unit.
Problem
Control board status light is blinking or the light is off and there is power to the sprayer.
Pump output is low
What to Check
If check is OK, go to next check
What to Do
When check is not OK, refer to this column
Fault condition exists.
Spray tip worn.
Spray tip clogged.
Determine fault correction from page 27.
Follow
Pressure Relief Procedure , page 13.
Follow
Pressure Relief Procedure , page 13, then replace tip. See separate
gun or tip manual.
Follow
Pressure Relief Procedure , page 13. Check and clean spray tip.
Refill and reprime pump.
Remove and clean, then reinstall.
Paint supply.
Intake strainer clogged.
Intake valve ball and piston ball are not seating properly.
Remove intake valve and clean. Check balls and seats for nicks; replace if necessary. See pump manual. Strain paint before using to remove particles that could clog pump.
Clean filter.
Fluid filter or tip filter is clogged or dirty.
Prime valve leaking.
Follow
Pressure Relief Procedure , page 13, then repair prime valve.
Service pump. See pump manual.
Verify pump does not continue to stroke when gun trigger is released.
(Prime valve not leaking.)
Leaking around throat packing nut which may indicate worn or damaged packings.
Pump rod damage.
Replace packings. See pump manual.
Also check piston valve seat for hardened paint or nicks and replace if necessary. Tighten packing nut/wet-cup.
Repair pump. See pump manual.
Low stall pressure.
Turn pressure knob fully clockwise. Make sure pressure control knob is properly installed to allow full clockwise position. If problem persists, replace pressure transducer.
Piston packings are worn or damaged. Replace packings. See pump manual.
O-ring in pump is worn or damaged.
Replace o-ring. See pump manual.
Intake valve ball is packed with material.
Large pressure drop in hose with heavy materials.
Clean intake valve. See pump manual.
Reduce overall length of hose.
Check extension cord for correct size. See Extension Cords , page 11.
3A4603A Operation, Repair, Parts 25
Troubleshooting
Problem
Motor runs but pump does not stroke
Excessive paint leakage into throat packing nut
Fluid is spitting from gun
Pump is difficult to prime
Sprayer operates for 5 to 10 minutes then stops
What to Check
If check is OK, go to next check
What to Do
When check is not OK, refer to this column
Connecting rod assembly damaged.
Replace connecting rod assembly. See pump manual.
Gears or drive housing damaged.
Inspect drive housing assembly and gears for damage and replace if necessary.
Throat packing nut is loose.
Remove throat packing nut spacer.
Tighten throat packing nut just enough to stop leakage.
Replace packings. See pump manual.
Throat packings are worn or damaged.
Displacement rod is worn or damaged.
Air in pump or hose.
Replace rod. See pump manual.
Spray tip is partially clogged.
Fluid supply is low or empty.
Check and tighten all fluid connections.
Cycle pump as slowly as possible during priming.
Clear tip.
Air in pump or hose.
Refill fluid supply. Prime pump. See pump manual. Check fluid supply often to prevent running pump dry.
Check and tighten all fluid connections.
Cycle pump as slowly as possible during priming.
Intake valve is leaking.
Pump packings are worn.
Paint is too thick.
Clean intake valve. Be sure ball seat is not nicked or worn and that ball seats well. Reassemble valve.
Replace pump packings. See pump manual.
Thin the paint according to supplier recommendations.
Pump packing nut too tight. When pump packing nut is too tight the packings on the pump rod restrict pump action and overloads the motor.
Loosen pump packing nut. Check for leaks around throat. If necessary, replace pump packings. See Pump manual.
26 3A4603A Operation, Repair, Parts
Troubleshooting
Electrical
Symptom: Sprayer does not run, stops running, or will not shut off.
Perform
Pressure Relief Procedure , page 13.
1.
Turn the ON/OFF switch OFF wait 30 seconds and then turn power back ON again (this ensures sprayer is in normal run mode).
2.
Turn pressure control knob clockwise 1/2 turn.
Keep clear of electrical and moving parts during troubleshooting procedures. To avoid electrical shock hazards when covers are removed for troubleshooting, wait 7 seconds after disconnecting power cord for stored electricity to dissipate.
3.
Remove control box cover to view control board status light. To determine which code (or any other code besides voltage supply) refer to the control board status light. Turn the ON/OFF switch OFF , remove the control cover then turn power back ON .
Observe the status light. Blinking LED total count equals the error code (for example: two blinks equals CODE 02).
Error Code Messages
CODE
02
03
05
06
MESSAGE
HIGH PRESSURE DETECTED -
RELIEVE PRESSURE
PRESSURE TRANSDUCER NOT
DETECTED
MOTOR NOT SPINNING
MOTOR OVERHEATED
ACTION
Check for clogs. Use only Graco spray hoses, use a minimum of 50ft/15m.
Check transducer connection.
Check for mechanical failure and check motor connections. Material may be too thick, thin material.
Turn sprayer OFF. Check motor connections. Check shroud vents for blockage. Sprayer may take up to an hour to cool.
Problem
Sprayer does not run at all
AND
Control board status light never lights
Sprayer does not shut off
AND
Control board status light blinks 2 times repeatedly
What to Check
Control board.
How to check
Replace control board.
3A4603A Operation, Repair, Parts 27
Troubleshooting
Problem
Sprayer does not run at all
AND
Control board status light blinks 2 times repeatedly
Sprayer does not run at all
AND
Control board status light blinks 3 times repeatedly
What to Check How to check
Check transducer or transducer connections
Make sure there is no pressure in the system (see
Pressure Relief Procedure , page 13). Check fluid path
for clogs, such as clogged filter.
Use airless paint spray hose with no metal braid. A small hose or metal braid hose may result in high-pressure spikes.
Turn ON/OFF switch OFF and disconnect power to sprayer by unplugging power cord and disconnecting battery.
Check transducer and connections to control board.
Disconnect transducer from control board socket. Check that transducer and control board contacts are clean and secure.
Reconnect transducer to control board socket. Connect power, turn ON/OFF switch ON and control knob
1/2 turn clockwise. If sprayer does not run properly, turn
ON/OFF switch OFF and go to next step.
Install new transducer. Connect power, turn ON/OFF switch ON and control knob 1/2 turn clockwise. Replace control board if sprayer does not run properly.
Check transducer or transducer connections (control board is not detecting a pressure signal).
Turn ON/OFF switch OFF and disconnect power to sprayer by unplugging power cord and disconnecting battery.
Check transducer and connections to control board.
Disconnect transducer from control board socket. Check to see if transducer and control board contacts are clean and secure.
Reconnect transducer to control board socket. Connect power, turn ON/OFF switch ON and control knob to 1/2 turn clockwise. If sprayer does not run, turn ON/OFF switch OFF and go to next step.
Connect a confirmed working transducer to control board socket.
Turn ON/OFF switch ON and control knob to 1/2 turn clockwise. If sprayer runs, install new transducer.
Replace control board if sprayer does not run.
Check transducer resistance with an ohmmeter (less than 9k ohm between red and black wires and 3-6k ohm between green and yellow wires).
28 3A4603A Operation, Repair, Parts
Troubleshooting
Problem
Sprayer does not run at all
AND
Control board status light blinks 5 times repeatedly
What to Check How to check
Control is commanding motor to run but motor shaft does not rotate. Possibly locked rotor condition, an open connection exists between motor and control, there is a problem with motor or control board, or motor amp draw is excessive.
1.
Remove pump and try to run sprayer. If motor runs, check for locked or frozen pump or drive train.
If sprayer does not run, continue to step 2.
2.
Turn ON/OFF switch OFF and disconnect power to sprayer by unplugging power cord and disconnecting battery.
3.
Disconnect motor connector(s) from control board socket(s). Check that motor connector and control board contacts are clean and secure. If contacts are clean and secure, continue to step 4.
4.
Set sprayer to OFF and spin motor fan 1/2 turn.
Restart sprayer. If sprayer runs replace control board. If sprayer does not run, continue to step 5.
5.
Perform Spin Test: Test at large 4-pin motor field connector. Disconnect fluid pump from sprayer.
Test motor by placing a jumper across pins 1 & 2.
Rotate motor fan at about 2 revolutions per second. A cogging resistance to motion should be felt at the fan. The motor should be replaced if no resistance is felt. Repeat for pin combinations 1 & 3 and 2 & 3.
Pin 4 (the green wire) is not used in this test. If all spin test is positive, continue to step 6.
GRN BLU R BLK
STEP 1:
STEP 2:
GRN BLU R BLK
STEP 3:
GRN BLU R BLK
3A4603A Operation, Repair, Parts 29
Troubleshooting
Problem What to Check How to check
6.
Perform Field Short Test: Test at large 4-pin motor field connector. There should not be continuity from pin 4, the ground wire, and any of the remaining
3 pins. If motor field connector tests fail, replace motor.
7.
Check Motor Thermal Switch: Unplug thermal wires. Set meter to ohms. Meter should read 100k ohms.
1-3 ohms
-
Sprayer does not run at all
AND
Control board status light blinks 6 times repeatedly
Basic electrical problems
Motor is hot or there is a fault in the motor thermal device.
8.
Reconnect motor connector(s) to control board socket(s). Connect power, turn ON/OFF switch ON and control knob to 1/2 turn clockwise. If motor does not run, replace control board.
Allow sprayer to cool. If sprayer runs when cool, correct cause of overheating. Keep sprayer in cooler location with good ventilation. Make sure motor air intake is not blocked. If sprayer still does not run, replace motor.
NOTE: Motor must be cooled down for the test.
1.
Check thermal device connector (yellow wires) at control board.
Motor leads are securely fastened and properly mated
2.
Disconnect thermal device connector from control board socket. Make sure contacts are clean and secure. Measure resistance of the thermal device. If reading is not correct, replace motor.
Check Motor Thermal Switch: Unplug thermal wires.
Set meter to ohms. Meter should read 100k ohms.
3.
Reconnect thermal device connector to control board socket. Connect power, turn sprayer ON and control knob 1/2 turn clockwise. If sprayer does not run, replace control board.
Replace loose terminals; crimp to leads. Be sure terminal are firmly connected.
Motor armature commutator for burn spots, gouges or extreme roughness.
Clean circuit board terminals. Securely reconnect leads.
Remove motor and have motor shop resurface commutator if possible.
Inverter will not turn on during initial power up.
Batteries are not connected, loose battery-side connections
Check the batteries and cable connections. Check DC fuse and breaker.
Low battery voltage below 10V Charge the battery with external charger (not charger on board the unit).
30 3A4603A Operation, Repair, Parts
Troubleshooting
Problem What to Check How to check
No AC output voltage and indicator lights ON.
AC output voltage is low and the inverter turns loads OFF in a short time.
Charger is inoperative and unit will not accept AC.
Output circuit breaker tripped
Low battery
Charger is supplying a lower charger rate.
Check circuit breaker and reset if necessary, page 35.
Check the condition of the batteries and recharge if possible.
AC voltage has dropped out-of-tolerance
Check the AC voltage for proper voltage and frequency.
Charger controls are improperly set.
Refer to the section on adjusting the “Charger Rate”
Low AC input voltage.
Loose battery or AC input connections.
Source qualified AC power.
Check all DC / AC connections.
3A4603A Operation, Repair, Parts 31
Troubleshooting
Sprayer Will Not Run
(See following page for steps)
Remove Control box cover.
Turn sprayer ON. Observe control board status light on control board (see page 27).
No Light
Once Normal Operation
Light on continuously
Control board
Commanding motor to run
Flashing
See Code section for further troubleshooting
See Step 1. Do you have over 100 VAC
(220 VAC for 230v units)?
YE S
NO
Troubleshoot Inverter
See page 35.
See Step 2. Is there
Continuity through the thermal switch wires?
YE S
See Step 3.
Does the motor run?
YE S
Replace the potentiometer.
NO
If motor is hot, let cool and retest. If Step 2 still shows no continuity, replace motor. The motor has a defective thermal device.
NO
Connect a test transducer to the board.
Does the motor run?
YE S
Replace the transducer
NO
Replace the control board
ti30335a
32 3A4603A Operation, Repair, Parts
Troubleshooting
S
tep 1:
Plug Power cord in and turn switch ON. Connect probes to control board. Turn meter to
AC Volts.
S
tep 2:
Check motor thermal switch.
Unplug yellow wires. Meter should read 100 ohms.
NOTE: Motor should be cool during reading.
110-120 AC
V
100 ohms
-
Yellow Thermistor
Wires to motor
-
Blue
Brown
+
-
Green
Power
Cord
S
tep 4:
Connect probes to positive and negative posts on inverter.
S
tep 3:
Disconnect potentiometer.
Plug power cord in and turn switch ON.
Control Board
To Potentiometer
S
tep 5:
Connect jumper across pins
1 and 2
-
V ti30331a
3A4603A Operation, Repair, Parts 33
Troubleshooting
Sprayer Will Not Shut Off
1.
Perform
Pressure Relief Procedure , page 13.
Leave prime valve open (down) and turn ON/OFF switch OFF .
Troubleshooting Procedure
Plumb pressure gauge into paint hose, plug sprayer in, and turn power switch ON.
Does sprayer reach or exceed its maximum pressure?
NO
2.
Remove control box cover so the control board status light can be viewed if available.
Mechanical problem:
See the proper fluid pump manual for the sprayer for further troubleshooting procedures.
YE
S
Is the control board status light on?
YE
S
Unplug the transducer from control board.
Does motor stop running?
YE
S
Bad transducer.
Replace and test with a new one.
NO
NO
Replace the control board.
Replace the control board.
ti24731a
34 3A4603A Operation, Repair, Parts
Troubleshooting
Inverter
The inverter has 2 circuit breakers, and an LED Status
Center that communicates inverter operation status.
See chart below for different functions, alarms, and fault modes.
S
tatus Center
BATTERY
TYPE
POWER
SAVER
OVER
LOAD
8
7
9
0
6
1 2
4 5
1 2
$
OVER
TEMP
3
UNIT
ALARM
4
FLOAT
CHG
5
FAST
CHG
6
INVERTER
MODE
7
LINE
MODE
8
Indication & Fault finding chart
S tatus L.E.D.s Function
Charge function
Inverter mode
Alarms
Fault mode
Constant current charge
Constant voltage charge
Float
Standby
Inverter on
Battery low voltage
Battery high voltage
Over load (inverter mode)
Over temp (inverter mode)
Over temp (line mode)
Over charge
Fan lock
Battery high voltage
Inverter mode overload
Over temperature
1 2 3 4 5 6 7 8
on
Flash on on on on on on on on on on on on on on on on on on on on on on on on on on
Alarm beep 0.5s
every 5 s beep 0.5s
every 5 s beep 0.5s
every 5 s beep 0.5s
every 5 s beep 0.5s
every 5 s beep 0.5s
every 5 s beep continuous beep continuous beep continuous beep continuous
3A4603A Operation, Repair, Parts 35
Troubleshooting
Sprayer does not have 100 VAC
(220 VAC for 230V units)
Troubleshooting Procedure:
Sprayer doesn t have 100VAC
Remove front shroud on unit to access DC power connections on inverter.
Remove paint bucket tray to access fuse and battery.
Remove inverter access panels to see circuit breakers and status center lights.
Do not plug unit into wall power.
See Step 4 on page 33.
Do you have
10.0 volts or higher?
YE S
Turn on power switch.
Does light 7 illuminate on power center?
NO
Is Fuse blown?
YE S
NO
Replace fuse and ensure no battery cables are shorted.
Tighten all battery cable connections.
YE
Reset circuit
Check output voltage circuit breaker.
Is it in tripped
OFF position?
S
breaker.
NO
YE
Check wiring connections from inverter to sprayer.
If all wiring is good replace inverter control boards.
See Manual 3A4746.
S NO
YE S
See Step 4 on page 33.
Do you have 10.0 volts or higher?
Check wiring connections from ON/Off switch to inverter. Turn on power switch. Does light 7 illuminate on power center?
NO
NO
Trickle charge the battery with an external charger or replace battery
Problem fixed.
YE S
Problem fixed.
Does switch have continuity for both poles in ON position?
YE S
Does light 7 illuminate on power center?
NO
Replace switch.
YE S NO
Check wiring for intermittent connection.
Replace inverter control boards.
See Manual 3A4746.
ti30337a
36 3A4603A Operation, Repair, Parts
Troubleshooting
Battery Will Not Charge
Troubleshooting Procedure:
Remove front shroud on unit to access DC power connections on inverter.
Remove paint bucket tray to access fuse and battery.
Remove inverter access panels to see circuit breakers and status center lights.
See Step 4 on page 33.
Do you have
10.0 volts or higher?
YE S
NO
Is Fuse blown?
NO
YE S
Replace fuse.
Plug in wall power to charging port. Does light 6 and 8 illuminate on power center?
Tighten all battery cable connections.
Check wiring from charging socket to relay board and from relay board to inverter.
Does light 6 and 8 illuminate on power center?
NO YE S
See Step 4 on page 33.
Do you have 10.0 volts or higher?
Check charger circuit breaker. Is it in tripped position?
NO YE S
YE S
Problem fixed.
YE S
NO
See Step 5 on page
33. Put a jumper wire across inverter input.
Does light 6 and 8 illuminate?
Reset circuit breaker.
Check wiring for any shorts
NO
NO
YE S
Trickle charge the battery with an external charger
or replace battery.
Check battery selector by status center. Is it set to position 3?
Problem fixed.
NO YE S
Set to position 3.
Are all power wires securely assembled to inverter?
Replace inverter control boards.
See Manual
3A4746.
Replace relay board. See parts list.
YE S NO
Replace inverter control boards.
See Manual 3A4746.
Assemble wires.
ti30338a
3A4603A Operation, Repair, Parts 37
Parts Drawing - LineLazer ES 1000
Parts Drawing - LineLazer ES 1000
1
Torque to 17-23 ft-lbs
(23.0-31.1 N·m)
2
Torque to 190-210 in-lbs
(21.4-23.7 N·m)
3
Torque to 18-22 in-lbs
(2.0-2.4 N·m)
4
Torque to 23-27 ft-lbs
(31.1-36.6 N·m)
5
Torque to 45-55 ft-lbs
(61.0-74.5 N·m)
104
157
6
41
5
50
3
114
259 306 302
307
305
304
303
113
124
48
158
6
312
296
137
163
301
300 305
114
3
40
27
69
6
43
1
94
325
111
70
312
42
4
10
14
11
13
9
21
16
254
4
93
2
43
1
1
6 6
26
17 7
31 1
20
18
19
38
162 ti30462a
3A4603A Operation, Repair, Parts
Parts List
Parts List
Ref. Part Description
42
43
48
50
27
31
40
41
69
70
93
19
20
21
26
14
16
17
18
9
10
11
13
6
7
1
4
17N763 FRAME, linestriper
108851 WASHER, plain
101566 NUT, lock
193405 AXLE
198891 BRACKET
198930 ROD, brake
198931 BEARING
195134 SPACER, ball, guide
113961 SCREW, cap, hex hd
111040 NUT, lock, insert, nylock, 5/16
111020 WHEEL, pneumatic
112405 NUT, lock
112825 WASHER, belleville
114648 CAP, dust
125205 NUT, lock, nylon, 3/8-16
17P800 BUMPER
17P831 PAD, non-slip, no step
114982 SCREW, cap, flng hd
24Y665 FRAME, handle upright
15F576 BRACE, right
15F577 BRACE, left
128977 SCREW, cap, btn hd, 3/8 x 1
17J125 BRACKET, slide
17J136 SCREW, hex, flange head
17P305 PLATE, bucket holder
17N536 HOLDER, bucket
125112 SCREW, cap, btn hd, 5/16 x 1
Qty
2
4
1
2
1
1
1
6
1
2
2
5
2
6
2
2
3
1
4
1
1
1
1
12
1
1
4
Ref. Part Description
94 129601 SCREW, cap, btn hd, 3/8 x 1.25
104 17N451 CONTROL, assembly, LL ES
111 867517 SCREW, hex head, 3/8-16 x 3.5”
113 17J135 COVER, control
137 278723 GASKET, pail
124 249080 HOSE, cpld, 1/4” x 50’
157 114271 STRAP, retaining
158 108471 KNOB, pronged
162 115077 PAIL, plastic
163 24U241 KIT, pail cover
254 17K396 LABEL, safety
259 17N740 LABEL, tool box
296 17K379 LABEL, console
300 17K235 BRACKET, access door
301 17K236 HINGE, access door
302 17K291 DOOR, access, painted
303 17K309 MAGNET, square
304 107070 SCREW, mach, flh
305 109466 NUT, lock, hex
306 17K320 KNOB, ribbed
307 112925 SCREW, cap
312 16W408 KNOB, t-handle, 1/4-20 thd stud
325 17K584 LABEL, wire cutout
Replacement Danger and Warning labels, tags, and cards are available at no cost.
Qty
1
1
1
1
1
1
1
1
1
1
1
1
4
1
4
1
1
4
2
4
1
2
2
3A4603A Operation, Repair, Parts 39
Parts Drawing - LineLazer ES 1000
Parts Drawing - LineLazer ES 1000
86
2
101
88
257
2 101
255
5 608
609
607
600
658
601
4
92
201 612
1 606
46
52
97
99
5
98 2
603
45
72
71
107
610
3
611
613
25
602
604
605
1
Torque to 140-160 in-lbs
(15.8-18.1 N·m)
2
Torque to 30-35 in-lbs
(3.4-4.0 N·m)
3
Hammer tight
4
Torque to 9-11 in-lbs
(1.0-1.2 N·m)
5
Torque to 20-25 in-lbs
(2.3-2.8 N·m)
103
1
606
87
85
253
102 2
250
125 127
123
2 98
71
138
139
72
96
95
21
153
100
130
164 ti30486a
40 3A4603A Operation, Repair, Parts
Parts List
Parts List
Ref. Part Description
91
92
95
96
85
86
87
88
46
52
71
72
5
21
25
45
17P496 COVER, inverter
125205 NUT, lock, nylon, 3/8-16
24R702 MOTOR, electric
129604 GROMMET, rubber
17N444 GROMMET
278204 CLIP, drain line
17P506 GASKET, access port
17P497 COVER, access port
17C541 COVER, front
15G449 SHIELD, motor
17C483 COVER, PC pro pump rod
15G447 PLUG, shield
17N989 WIRE, jumper, 18 awg, white
125220 CLAMP, cushion, support
114064 PLUG, inlet
15W998 SCREW, mach
97
98
129627 SPACER, nylon
108795 SCREW, mach
99 111193 SCREW, cap
100 117493 SCREW, mach, hex washer hd
101 117501 SCREW, mach, slot hex wash hd
102 127914 SCREW, mach, slot hex wash hd
103 17P888 GUIDE, hose
107 110996 NUT, hex, flange head
123 16X071 TUBE, drain line
125 248008 HOSE, cpld, 1/4” x 44”
126 15F624 NUT, cable, gun
127 196180 BUSHING
130 17M772 HOSE, suction
Qty
1
1
4
3
1
4
1
4
2
1
1
1
1
1
2
1
1
1
1
1
1
2
2
1
1
1
2
1
1
Ref. Part Description
137 278723 GASKET, pail
138 115099 WASHER, garden
139 117559 O-RING
153 17N217 HOSE, coupled
164 187651 STRAINER, 3/4-16 unf
201 107254 SCREW, thd forming
250 17N730 LABEL, front, bottom
253 17N729 LABEL, front, brand
255 195793 LABEL, warning
257 17N731 LABEL, side
600 15D088 FAN, motor
601 115477 SCREW, mach
602 243980 GEAR, reducer
603 287002 GEAR, crankshaft
604 180131 BEARING, thrust
605 24W625 HOUSING, drive
606 117493 SCREW, mach
607a 17N562 BOX, control, 120V
607b 17N558 BOX, control, 230V
608 117501 SCREW, mach
609 277229 COVER, control
610 17C490 ROD, connecting
611 24Z731 PUMP, displacement
612 17C964 LABEL, smart control
613 16H137 O-RING
Qty
1
1
1
1
1
1
1
1
1
1
1
5
2
1
1
1
1
1
1
1
1
1
4
7
1
Replacement Danger and Warning labels, tags, and cards are available at no cost.
3A4603A Operation, Repair, Parts 41
Parts Drawing - LineLazer ES 1000
Parts Drawing - LineLazer ES 1000
114
117
256
22
76
78
114
2
* †
12
1
614
201
49
47
81
3
89
615
616
617
618
617
1
Torque to 8-10 ft-lbs
(10.8-13.6 N·m)
62
42
112
32 see pg. 50 ti30463a
3A4603A Operation, Repair, Parts
Parts List
Parts List
Ref. Part Description Qty
22
32
44
47
2a* 17N508 INVERTER, power supply, 120V
2b† 17N509 INVERTER, power supply, 230V
3
12
17N448 BATTERY
113796 SCREW, flanged, hex hd
49
62
16A390 NUT, hex, flanged
113469 SCREW, cap, hex hd
17N921 BOX, voltage meter, 120V
17N816 HOLDER, fuse
17N815 FUSE, 200, amp
CORD, power
17N760 US
17R033 AUSTRALIA
76
78
17R034 CEE 7/7
17R035 SWITZERLAND
17R036 DENMARK
17R037 ITALY
17M321 CABLE, red, dia .625 x 3 ft
17M323 CABLE, black, dia .625 x 3.5 ft
81
89 w/ cover
17M322 CABLE, red, dia .625 x 2 ft w/ cover
129629 STRAP, retaining
112 102040 NUT, lock, hex
114 128978 SCREW, mach, slot hex wash hd
117 17P562 COVER, front, LL ES
1
1
1
6
8
1
1
1
1
2
2
1
1
1
6
1
1
Ref. Part Description Qty
201 107257 SCREW, hhd forming
256 17P202 LABEL, logo
614 129545 COVER, black
615 129546 COVER, red
616 108768 SCREW
617 104572 WASHER, lock
618 108788 WASHER, flat
620a 17R015 PANEL, box, meter, voltage, 120V
620b 17N929 PANEL, box, meter, voltage, 230V
621 17N638 METER, volt, digital
622a 25M487 KIT, repair, bear, relay, 120V
622b 25M489 KIT, repair, bear, relay, 230V
623 104714 SCREW, mach, pnh
624a 114064 PLUG, inlet
624b 129649 FILTER, inlet
625a 15W998 SCREW, mach, torix
625b 119912 SCREW, mach, phillips
626a 17N659 LABEL, battery, 120V AC
626b 17N753 LABEL, battery, 230V AC 1
627 129510 FASTENER, threaded hex standoff 2
628* 129696 SCREW, pan head, phillips
2
1
2
4
1
2
2
1
1
2
1
1
2
2
1
1
1
1
1
* Included in 120V Control Board Repair Kit 24Z803
† Included in 230V Control Board Repair Kit 24Z804
3A4603A Operation, Repair, Parts 43
Parts Drawing - LineLazer ES 1000
Parts Drawing - LineLazer ES 1000
44
33
16
20
18
19
495
497
496 498
6
495
500 494
493
3 18
19
36
28
15 2
29
31
1
483
499
38
484
485
4
487
488 5
489
490
19
35
292
491
492
33
34 ti30464a
53
56
1
Torque to 17-23 ft-lbs
(23.0-31.1N·m)
2
Torque to 190-210 in-lbs
(21.4-23.7 N·m)
3
Torque to 23-27 ft-lbs
(31.1-36.6 N·m)
4
Torque to 60-80 in-lbs
(6.7-9.0 N·m)
5
6
7
Torque to 17-23 ft-lbs
(23.0-31.1 N·m)
Torque to 35-45 ft-lbs
(47.4-61.0 N·m)
Torque to 365-385 in-lbs
(41.2-43.4 N·m)
55
54
2
57
8
284
60
59
172 6
282
66 65
63
61
7
67
68
284
51
64 ti30467a
3A4603A Operation, Repair, Parts
Parts List
Parts List
Swivel Wheel Assembly
Ref. Part Description
6*
8
15
16
101566 NUT, lock
196179 FITTING, elbow, street
112960 SCREW, cap, flng hd
111040 NUT, lock, insert, nylock, 5/16
18*‡ 112405 NUT, lock
19*‡ 112825 WASHER, belleville
20*‡ 114648 CAP, dust
28‡ 15F910 BRACKET, cable
29
31
240991 BRACKET, caster, front
114982 SCREW, cap, flng hd
33*‡ 193658 SPACER, seal
34* 114549 WHEEL, pneumatic
35* 113471 SCREW, cap, hex hd
36‡ 114632 CABLE
38‡ 114802 STOP, wire
292*‡ 17H489 LABEL, disk adjustment
483* ‡ 114548 BEARING, bronze
484* ‡ 110754 SCREW, cap, sch
485* ‡ 193662 STOP, wedge
487* ‡ 15J603 SPACER, round
488* ‡ 120476 BOLT, shoulder
489* ‡ 17H486 DISK, adjuster, assembly
490* ‡ 17G762 SCREW, disk adjuster
491* ‡ 113962 WASHER
492* ‡ 114681 SCREW, cap, hex hd
493* ‡ 17H485 FORK
494* ‡ 113484 SEAL, grease
495* ‡ 113485 BEARING, cup/cone
496* ‡ 112776 WASHER, plain
497* ‡ 181818 KNOB, pronged
498* ‡ 193661 JAW
499* ‡ 15G952 CASTER
500* ‡ 108483 SCREW, shoulder
* Included in Swivel Wheel Repair Kit 240719
‡ Included in Swivel Wheel Repair Kit 241105
Qty
1
1
1
1
1
2
1
1
1
1
2
1
1
1
2
1
1
1
1
1
2
2
1
1
2
1
1
2
4
2
2
2
1
Filter
Ref. Part Description
56
57
59
60
51
53
54
55
17K166 MANIFOLD, filter
15C765 CAP, filter
15C766 TUBE, diffusion
243984 FILTER, fluid
117285 PACKING, o-ring
111801 SCREW, cap, hex hd
111457 PACKING, o-ring
15G331 PLUG, pipe
61† 287879 VALVE, drain, assy
63† 114708 SPRING, compression
64 196181 FITTING, nipple
65† 15G563 HANDLE, valve
66† 116424 NUT, cap
67† 193709 SEAT, valve
68† 193710 SEAL, seat valve
172 17R281 TRANSDUCER
282 868015 GAUGE, pressure, 0-5000 psi
284 196177 ADAPTER, nipple
† Included in Prime Valve Repair Kit 245103
Qty
1
1
1
1
1
2
1
1
1
1
1
1
1
2
1
1
1
1
3A4603A Operation, Repair, Parts 45
Parts Drawing - LineLazer ES 1000
Parts Drawing - LineLazer ES 1000
6
121
118
116
407
409
2
408
158
1
Torque to 17-23 ft-lbs
(23.0-31.1 N·m)
2
Torque to 145-155 in-lbs
(16.3-17.5 N·m)
116
1
31
39
122
410
128
159
119
504
411
412
115
119
420
419
151
120
417
418
112
501
416
415
414 413 ti30465a
136
134
133 131
134
126
105
46
132
133 135
287 ti30466a
3A4603A Operation, Repair, Parts
Parts List
Parts List
Gun Holder and Arm
Ref. Part Description
6
31
101566 NUT, lock
114982 SCREW, cap, flng hd
39 17N447 BRACKET, gun arm
112 102040 NUT, lock, hex
115 17J407 ARM, extension, bar, weldment
116 17J424 BAR, heigh adjustment, assy
118 24Y645 KIT, clamp
119 287882 BAR, gun holder
120 15F208 CABLE, gun
121 188135 GUIDE, cable
122 235457 GUN, flex, basic
128 16P136 LABEL, safety, warning, iso
151 119648 SCREW, mach, trshd
158 108471 KNOG, pronged
159 111145 KNOB, pronged
407 17J139 BAR, gun, height, adjustment
408 17J153 BRACKET, gun, holder
409 113428 SCREW, mach, hex hd
410 243161 GUARD
411‡ 15F750 KNOB, holder, gun
412 17J575 FASTENER
413‡ 15F216 HOLDER, gun
414‡ 119664 BEARING, sleeve
415 15F209 STUD, pull, trigger
416 17J576 SPACER
417 15F211 STUD, cable
418 15F214 ACTUATOR, lever
419 119647 SCREW, cap, socket
420 17J145 ARM, holder, gun
501 15F213 BRACKET, cable
504 LL5317 STRIPING TIP
LL5319 STRIPING TIP
Replacement Danger and Warning labels, tags, and cards are available at no cost.
‡ Included in Gun Holder Repair Kit 287569
Qty
1
1
1
1
1
2
1
1
1
1
1
1
1
1
1
1
1
1
1
1
1
3
1
1
1
1
1
1
1
3
2
2
Gun Trigger
Ref. Part Description
105 114659 GRIP, handle
126 15F624 NUT, cable, gun
131 198896 BLOCK, mounting
132 245676 HANDLE
133 198895 PLATE, lever, pivot
134 111017 BEARING, flange
135 116941 SCREW, shoulder
136 129476 NUT, lock w/ nylon insert
287 128803 SCREW, thd forming, hex washer
Qty
1
1
2
2
1
1
1
2
2
3A4603A Operation, Repair, Parts 47
Parts Drawing - LineLazer ES 1000
Parts Drawing - LineLazer ES 1000
1
Torque to 18-22 in-lbs
(2.0-2.4 N·m)
2
Torque to 28-32 in-lbs
(3.1-3.6 N·m)
3
Torque to 45-55 ft-lbs
(61.0-74.5 N·m)
515
3
50
510
508
505
520
525
520
509
507 2
58
325
506
201
521
106
1
503
502
108
36
1
114 109
114
1
105
146
299 ti30487a
48 3A4603A Operation, Repair, Parts
Parts List
Parts List
5
Ref. Part Description
36
50
114632 CABLE
17J136 SCREW, hex, flange hd
58 113491 CLAMP, wire
105 114659 GRIP, handle
106 237686 GROUNDING, clip
108 194310 LEVEL, actuator
109 17J123 PLATE, cover
114 128978 SCREW, mach, slot hex wash hd
146 120151 PLUG, tube
299 17K310 PLUG, button
325 17K584 LABEL, wire cutout
501 24Y642 PLATE, control, Weldment
Qty
1
8
1
1
1
1
1
4
1
1
2
1
Ref. Part Description
502 17N443 POTENTIOMETER
503 198650 SPACER, shaft
505 17J126 BRACKET, shroud
506 17N419 BRACKET, switch
507 102040 NUT, lock, hex
508 15C973 GASKET
509 17N416 LABEL, control
510 116167 KNOB, potentiometer
515 24Y641 BAR, handle
520 17N435 INDICATOR, LED, panel mount
521 17N418 SWITCH, toggle
525 195428 BOOT, toggle
Qty
1
1
4
1
1
1
1
1
1
1
1
1
3A4603A Operation, Repair, Parts 49
Voltage Meter Box, 120V
Voltage Meter Box, 120V
1 623
622a
3
628
627 1
620a
1
Torque to 8-11 in-lbs
(0.9-1.2 N·m)
2
Torque to 10-15 in-lbs
(1.1-1.7 N·m)
3
Torque to 2-4 in-lbs
(0.2-0.4 N·m)
624a
626a
621
2 625a
Voltage Meter Box, 230V
1 623
622b
3
628
1 627
624b
620b
1
Torque to 8-11 in-lbs
(0.9-1.2 N·m)
2
Torque to 10-15 in-lbs
(1.1-1.7 N·m)
3
Torque to 2-4 in-lbs
(0.2-0.4 N·m)
626b
621
625b
2 ti30491a
50 3A4603A Operation, Repair, Parts
Parts List
Parts List
Voltage Meter Box, 120V
Ref. Part Description Qty
620a 17R015 PANEL, box, meter, voltage, 120V
621 17N638 METER, volt, digital
622a 25M487 KIT, repair, bear, relay, 120V
623 104714 SCREW, mach, pnh
624a 114064 PLUG, inlet
625a 15W998 SCREW, mach, torix
626a 17N659 LABEL, battery, 120V AC 1
627 129510 FASTENER, threaded hex standoff 2
628 129696 SCREW, pan head, phillips
1
2
2
1
2
1
1
Voltage Meter Box, 230V
Ref. Part Description Qty
620b 17N929 PANEL, box, meter, voltage, 230V
621 17N638 METER, volt, digital
622b 25M489 KIT, repair, bear, relay, 230V
623 104714 SCREW, mach, pnh
624b 129649 FILTER, inlet
625b 119912 SCREW, mach, phillips
626b 17N753 LABEL, battery, 230V AC 1
627 129510 FASTENER, threaded hex standoff 2
628 129696 SCREW, pan head, phillips
1
2
2
1
2
1
1
3A4603A Operation, Repair, Parts 51
Control Box, 120V
Control Box, 120V
1
Torque to 20-25 in-lbs
(2.3-2.8 N·m)
2
Torque to 12±2 in-lbs
(1.4 ± 2 N·m)
3
Torque to 30-35 in-lbs
(3.4-3.9 N·m)
650a
655 2
608
657
661
658
653 1
654 3
652 3
609
Control Box, 230V
1
Torque to 20-25 in-lbs
(2.3-2.8 N·m)
2
Torque to 12±2 in-lbs
(1.4 ± 2 N·m)
3
Torque to 30-35 in-lbs
(3.4-3.9 N·m)
650b
657
661
658
651
651 ti30522a
609
2
660
655
659
654
3
1
656
652
3
608
653
52 ti30524a
3A4603A Operation, Repair, Parts
Parts List
Parts List
Control Box, 120V
Ref. Part Description Qty
608 117501 SCREW, mach, slot hex wash hd
609 277229 COVER, control
650a 25M490 BOX, control board, 120V , includes
651, 652, 653, 654, 655, 657, 658
651 15G562 BUSHING, control box
652 120405 SCREW, mach, hex washer hd
653 120165 SCREW, mach, phillips, pan hd
654 123850 SCREW, tapping, slot hex wash hd 1
655 120406 SCREW, mach, hex, wash hd 1
657 16Y457 PLUG, molded
658 17N560 PLUG
661 17N559 BOX, control 1
1
1
1
2
1
4
1
1
Control Box, 230V
Ref. Part Description Qty
608 117501 SCREW, mach, slot hex wash hd
609 277229 COVER, control
650b 25M491 BOX, control board, 230V, includes
651, 652, 653, 654, 655, 656, 657,
658, 659, 660
651 15G562 BUSHING, control box
652 120405 SCREW, mach, hex washer hd
653 120165 SCREW, mach, phillips, pan hd
654 123850 SCREW, tapping, slot hex wash hd 1
655 120406 SCREW, mach, hex, wash hd 1
656 128038 SCREW, mach, hex wash
657 16Y457 PLUG, molded
2
1
1
2
1
658 17N560 PLUG
660 17P859 WIRE, jumper
661 17N559 BOX, control
1
1
1
4
1
1
3A4603A Operation, Repair, Parts 53
Wiring Diagram
54 ti30550a
3A4603A Operation, Repair, Parts
RED WIRE
Wiring Diagram
3A4603A Operation, Repair, Parts ti30551a
55
Control Board Wiring Diagram
Control Board Wiring Diagram
110/120V
MOTOR
Black
To Power
Plug
Green
Potentiometer
J12
J11
Pressure
Transducer
ti30332a
56 3A4603A Operation, Repair, Parts
Control Board Wiring Diagram
230V
NOTICE
Heat from inductor coil of filter board may destroy wire insulation that comes in contact with it. Exposed wires could cause shorts and component damage. Bundle and tie loose wires so none lay in contact with inductor coil on the filter board.
MOTOR
To Power
Plug
Blue Brown
Green
Black
Blue
J12
J11
Potentiometer
Pressure
Transducer ti30333a
3A4603A Operation, Repair, Parts 57
Technical Specifications
Technical Specifications
Dimensions
Height (with handle bar down)
Width
Length (with platform down)
Weight (dry - no paint)
Noise (dBa)
Sound Power per ISO 3741:
Sound Pressure per ISO 3741:
Vibration (m/s
2
) (8 hours daily exposure)
Right-hand (per ISO 5349)
Left-hand (per ISO 5349)
Maximum Delivery
Maximum Tip Size
1 gun
Inlet paint strainer
Outlet paint strainer
Pump inlet size
Pump outlet size
Maximum working pressure
Battery
LineLazer ES 1000 with 1 battery
U.S.
Unpackaged - 44.5 in.
Packaged - 53.0 in.
Unpackaged - 34.25 in.
Packaged - 39.0 in.
Unpackaged - 68.75 in.
Packaged - 75.0 in.
Unpackaged - 340 lbs
Packaged - 437 lbs
89.8 dBA
85.3 dBA
1.85
0.90
Metric
Unpackaged - 113.03 cm
Packaged - 134.62 cm
Unpackaged - 86.99 cm
Packaged - 99.06 cm
Unpackaged - 174.63 cm
Packaged - 190.5 cm
Unpackaged - 154 kg
Packaged - 198 kg
0.6 gpm 2.3 lpm
.025
16 mesh
60 mesh
1190 micron
297 micron
1 in. NSPM (m)
1/4 NPT (f)
3300 psi 228 bar, 22.8 MPa
12V, 100Ah, AGM, Deep cycle
Wetted Parts: PTFE, Nylon, polyurethane, V-Max,
UHMWPE, fluoroelastomer, acetal, leather, tungsten carbide, stainless steel, chrome plating, nickel-plated carbon steel, ceramic
58 3A4603A Operation, Repair, Parts
Electrical Specifications
Minimum Start Voltage
Low Battery Alarm
Low Battery Trip
High Voltage Alarm & Fault
High DC Input Recovery
Low Battery Voltage Recovery
Idle Consumption-Search Mode
Charge
Input Voltage Range
Input Frequency Range
Output Voltage
Charger Breaker Rating (230Vac)
Charger Breaker Rating (120Vac)
Max Charger Rate
Over Charge Protection
Battery Type
Gel U.S.A.
A.G.M 1
A.G.M 2
Sealed Lead Acid
Gel Euro
Open Lead Acid
Calcium
De-sulphation
Bypass & Protection
Nominal Voltage
Low Voltage Trip
Low Voltage re engage
High Voltage Trip
High Voltage re engage
Max Input AC Voltage
Nominal Input Frequency
Low Freq Trip
Low Freq re engage
High Freq Trip
High Freq re engage
Output Short circuit protection
Bypass Breaker Rating (230Vac)
Bypass Breaker Rating (120Vac)
Electrical Specifications
LineLazer ES 1000
DC Input
Nominal Input Voltage 12.0Vdc
10.0Vdc
11.0Vdc
10.5Vdc
16.0Vdc
15.5Vdc
13.0Vdc
60W
100~135VAC / 194~243 VAC;
50/60Hz
Depends on battery type (see chart below)
10A
20A
30 amps
15.7V for 12Vdc
Fast Vdc
14.0
14.1
14.6
14.4
14.4
14.8
15.1
Float Vdc
13.7
13.4
13.7
13.6
13.8
13.3
13.6
15.5 for 4 hrs
120Vac
90V±4%
100V±4%
140V±4%
230Vac
184V±4%
194V±4%
253V±4%
135V±4%
150VAC
50Hz or 60Hz (Auto detect)
Wide: 40±0.3Hz for 50Hz/60Hz
243V±4%
270VAC
Wide: 45±0.3Hz for 50Hz/60Hz
Wide: No up limit for 50Hz/60Hz
Wide: No up limit for 50Hz/60Hz
Circuit Breaker
20A
30A
3A4603A Operation, Repair, Parts 59
Graco Standard Warranty
Graco warrants all equipment referenced in this document which is manufactured by Graco and bearing its name to be free from defects in material and workmanship on the date of sale to the original purchaser for use. With the exception of any special, extended, or limited warranty published by Graco, Graco will, for a period of twelve months from the date of sale, repair or replace any part of the equipment determined by
Graco to be defective. This warranty applies only when the equipment is installed, operated and maintained in accordance with Graco’s written recommendations.
This warranty does not cover, and Graco shall not be liable for general wear and tear, or any malfunction, damage or wear caused by faulty installation, misapplication, abrasion, corrosion, inadequate or improper maintenance, negligence, accident, tampering, or substitution of non-Graco component parts. Nor shall Graco be liable for malfunction, damage or wear caused by the incompatibility of Graco equipment with structures, accessories, equipment or materials not supplied by Graco, or the improper design, manufacture, installation, operation or maintenance of structures, accessories, equipment or materials not supplied by Graco.
This warranty is conditioned upon the prepaid return of the equipment claimed to be defective to an authorized Graco distributor for verification of the claimed defect. If the claimed defect is verified, Graco will repair or replace free of charge any defective parts. The equipment will be returned to the original purchaser transportation prepaid. If inspection of the equipment does not disclose any defect in material or workmanship, repairs will be made at a reasonable charge, which charges may include the costs of parts, labor, and transportation.
THIS WARRANTY IS EXCLUSIVE, AND IS IN LIEU OF ANY OTHER WARRANTIES, EXPRESS OR IMPLIED, INCLUDING BUT NOT
LIMITED TO WARRANTY OF MERCHANTABILITY OR WARRANTY OF FITNESS FOR A PARTICULAR PURPOSE .
Graco’s sole obligation and buyer’s sole remedy for any breach of warranty shall be as set forth above. The buyer agrees that no other remedy
(including, but not limited to, incidental or consequential damages for lost profits, lost sales, injury to person or property, or any other incidental or consequential loss) shall be available. Any action for breach of warranty must be brought within two (2) years of the date of sale.
GRACO MAKES NO WARRANTY, AND DISCLAIMS ALL IMPLIED WARRANTIES OF MERCHANTABILITY AND FITNESS FOR A
PARTICULAR PURPOSE, IN CONNECTION WITH ACCESSORIES, EQUIPMENT, MATERIALS OR COMPONENTS SOLD BUT NOT
MANUFACTURED BY GRACO . These items sold, but not manufactured by Graco (such as electric motors, switches, hose, etc.), are subject to the warranty, if any, of their manufacturer. Graco will provide purchaser with reasonable assistance in making any claim for breach of these warranties.
In no event will Graco be liable for indirect, incidental, special or consequential damages resulting from Graco supplying equipment hereunder, or the furnishing, performance, or use of any products or other goods sold hereto, whether due to a breach of contract, breach of warranty, the negligence of Graco, or otherwise.
Graco Information
For the latest information about Graco products, visit www.graco.com
.
For patent information, see www.graco.com/patents .
TO PLACE AN ORDER, contact your Graco distributor or call 1-800-690-2894 to identify the nearest distributor.
All written and visual data contained in this document reflects the latest product information available at the time of publication.
Graco reserves the right to make changes at any time without notice.
Original instructions.
This manual contains English. MM 3A4603
Graco Headquarters: Minneapolis
International Offices: Belgium, China, Japan, Korea
GRACO INC. AND SUBSIDIARIES • P.O. BOX 1441 • MINNEAPOLIS MN 55440-1441 • USA
Copyright 2016, Graco Inc. All Graco manufacturing locations are registered to ISO 9001.
www.graco.com
Revision A , December 2016
advertisement
* Your assessment is very important for improving the workof artificial intelligence, which forms the content of this project
Related manuals
advertisement
Table of contents
- 3 Warnings
- 7 Tip Selection
- 8 Component Identification (ES 1000)
- 9 Battery and Charger
- 9 Battery Disposal
- 9 Battery Type and Charging Profiles
- 10 Charging the Battery
- 11 (AC Wall Power)
- 11 Power Requirements
- 11 Extension Cords
- 11 Pails
- 12 (Battery Power)
- 12 Pails
- 13 Pressure Relief Procedure
- 14 Setup/Startup
- 15 SwitchTip and Guard Assembly
- 16 Gun Placement
- 16 Install Gun
- 16 Position Gun
- 16 Select Guns
- 17 Gun Positions Chart
- 18 Gun Arm Mounts
- 18 (Front and Back)
- 18 (Left and Right)
- 19 Installation
- 19 Gun Cable Adjustment
- 20 Straight Line Adjustment
- 20 Handle Bar Adjustment
- 21 Paint Stripe Width
- 21 Spray Test Stripe
- 21 Clearing Tip Clogs
- 22 Cleanup
- 22 Fast Flush Drain Tube
- 23 Fast Flush Hose and Gun
- 24 Maintenance
- 25 Troubleshooting
- 25 Mechanical/Fluid Flow
- 27 Electrical
- 32 Sprayer Will Not Run
- 34 Sprayer Will Not Shut Off
- 35 Inverter
- 36 units)
- 37 Battery Will Not Charge
- 38 Parts Drawing - LineLazer ES
- 39 Parts List
- 40 Parts Drawing - LineLazer ES
- 41 Parts List
- 42 Parts Drawing - LineLazer ES
- 43 Parts List
- 44 Parts Drawing - LineLazer ES
- 45 Parts List
- 45 Swivel Wheel Assembly
- 45 Filter
- 46 Parts Drawing - LineLazer ES
- 47 Parts List
- 47 Gun Holder and Arm
- 47 Gun Trigger
- 48 Parts Drawing - LineLazer ES
- 49 Parts List
- 50 Voltage Meter Box, 120V
- 50 Voltage Meter Box, 230V
- 51 Parts List
- 51 Voltage Meter Box, 120V
- 51 Voltage Meter Box, 230V
- 52 Control Box, 120V
- 52 Control Box, 230V
- 53 Parts List
- 53 Control Box, 120V
- 53 Control Box, 230V
- 54 Wiring Diagram
- 56 Control Board Wiring Diagram
- 56 110/120V
- 58 Technical Specifications
- 59 Electrical Specifications
- 60 Graco Standard Warranty