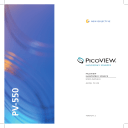
advertisement
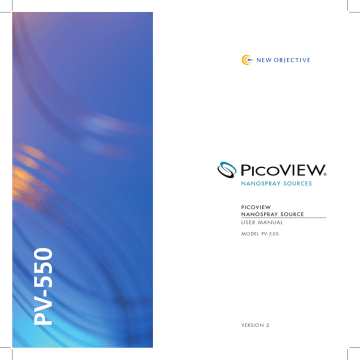
P I C O V I E W
N A N O S P R AY S O U R C E
U S E R M A N U A L
M O D E L P V - 5 5 0
V E R S I O N 2
2 Constitution Way
Woburn, Ma 01801-1023 USA
800 220 2998 US toll free
781 933 9560 phone
781 933 9564 fax www.newobjective.com
P I C O V I E W
N A N O S P R AY S O U R C E
USER M ANUAL
M O D E L P V - 5 5 0
V E R S I O N 2 . 0
X D - P V 5 5 0
© 2009 New Objective, Inc.
All rights reserved.
No portion of this document may be repurposed or reprinted without the prior written consent of New Objective, Inc.
Table of Contents
1 Read This first
Safety Considerations
1-1
1-1
Prior to Installation
Handling Fused-Silica Tubing
1-1
1-1
Tip Adjustment and/or Replacement 1-2
The Transfer Line
Contents & Components List
1-2
1-3
Trademarks
Limited Warranty
1-4
1-4
2 Applications
Continuous Infusion Nanospray
2-1
2-1
Nanospray Flow-Injection 2-1
Microspray Flow-Injection 2-2
Nanobore LC-MS Using a PicoFrit
®
Column 2-2
2-3 Nanobore LC-MS Using a PicoTip
® with a Separate Column
Capillary Bore LC
Supplying Voltage to the
Uncoated Tip Module (UTM)
2-3
2-4
TA b L E O f C O N T E N T S i
i i
TA b L E O f C O N T E N T S
3 Quick Guide
PicoView Components
3-1
3-1
Tip Modules 3-2
Digitally Controlled XYZ Positioning Stage 3-3
Imaging System
Injection Valves
3-3
3-3
4 Installing PicoView
®
Preparing the Mass Spectrometer
4-1
Placing the Mass Spectrometer into Standby Mode
4-1
Disconnecting the High-Voltage
Cable, Gas, and Sheath Liquid Lines
4-1
Removing the Ion Max™ Source 4-2
Mounting PicoView on the
Mass Spectrometer
Installing the Interface Flange
Attaching PicoView ® to the Interface flange
Installing the Imaging System
Mounting the Fiber Optic
Illuminator
Grounding Requirements
4-1
4-2
4-2
4-3
4-4
4-4
4-7
5 Setup
Cutting Fused Silica
Connectors & Fittings
Using the Coated Tip Module (CTM)
CTM in the Forward Position
Loading the MicroTight
®
Union
Attaching the CTM to the
Magnetic Stage Plate
Connecting High Voltage
Adjusting Tip Position
Using the Uncoated Tip Module (UTM)
Using PicoFrit
®
Columns
Removing a PicoFrit
®
Column from the FEP Sleeve
Attaching the UTM to the
Stage Plate in the Back Position
Loading the MicroTight ®
Union and Tip Holder
Supplying High Voltage
Plumbing the MicroTee
Loading the MicroTee into the UTM
Connecting High Voltage
Adjusting Tip Position
Uncoated Tip Module in the Forward Position
5-8
5-8
5-9
5-9
5-11
5-11
5-11
5-12
5-1
5-3
5-4
5-5
5-1
5-1
5-3
5-6
5-6
5-6
5-7
5-7
TA b L E O f C O N T E N T S i i i
i v
TA b L E O f C O N T E N T S
6 Techniques to Optimize
PicoView
®
Selecting the Right Type of Emitter
Choosing Tip Size and Coating Options
In-Line Filtration
Air Bubbles
Operating Parameters
Tip Position
Applied Voltage
Solvent Flow Rate
Electric Field Strength &
Flow Rate Interdependence
Voltage Tuning
Optimizing the Spray
Selecting a Flow Rate
Using the CTM
Using the UTM
Using the Imaging System
6-1
6-1
6-1
6-1
6-3
6-4
6-4
6-4
6-4
6-5
6-7
6-7
6-8
6-5
6-7
6-7
7 Mounting an Injection Valve
Mounting a Manual 6-Port Valve
Mounting a 10-Port Valco Valve
Components and Component Clamps
7-1
7-1
7-2
7-2
1 Read This first
Safet y Considerations
WARNING: Electrospray ionization involves the use of potentially lethal high-voltage electrical current. Observe all manufacturers’ safety recommendations in the use of such equipment. No equipment modifications should be made except by trained personnel using methods approved by the manufacturer in accordance with all safety requirements. Installation of equipment should be performed by qualified personnel in accordance with all applicable electrical codes.
Never use this product with defective, damaged, or faulty equipment. Serious injury or death could result.
SAFETY PRECAUTIONS: Only qualified personnel should use this product.
Provide a safe workplace equipped with all necessary safety equipment.
Prior to Installation
Follow all safety recommendations of the equipment manufacturer(s). All system voltages must be brought to ground potential and all high-voltage contacts disconnected from the inlet system before installation of the PicoView® system.
Inspect all equipment carefully prior to use. Any damaged, chipped, or cracked components should not be used and must be discarded or repaired.
handling fused-Silica Tubing
Handling of fused-silica or glass tubing and tips can result in serious personal injury, including eye and skin injury. Use safety glasses or goggles meeting ANSI Z87.1-1989 requirements, or the equivalent. Puncture- and chemical-resistant gloves should also be worn at all times.
1 R E A d T h I S f I R S T
1 - 1
1 - 2
1 R E A d T h I S f I R S T
Tip Adjustment and/or Replacement
Do not attempt to adjust or replace the tip unless the ESI high voltage and other applicable voltages are turned off and are at ground potential.
Reduce any applicable backing pressure (liquid, gas, etc.) to ambient before loosening ESI tip fittings and removing the fused-silica tip or transfer line from the coupling union. Prior to pressurization, make sure that components are tightened to specifications to prevent separation during use.
Failure to adhere to this warning could result in projectile-like expulsion of the tip from the coupling union, which could cause serious personal injury or damage to surrounding apparatus.
The Transfer Line
The transfer line connecting to either a tip module or the Micro Injection
Valve must not be made from an electrically conductive material. It must be fabricated from an electrically insulating material such as PEEK™ or fused silica. Otherwise, the operator may be exposed to potentially lethal voltage.
In systems where high voltage is applied directly to the ESI tip, the liquid sample inside the tip and transfer line tubing is also raised to a high voltage. To prevent exposure to potentially lethal voltages, a suitable ground point for the liquid inside the line must be provided.
Instructions for grounding are found in Section 4.4 on page 19.
Do not operate PicoView
®
without the external housing and lid in place.
WARNING: Do not defeat any mass spectrometer system software or hardware safety interlocks.
Contents and Components List
PicoView ® comes partially assembled, with system components contained in multiple boxes.
Model Number and Serial Number
Model Number:
Your Serial Number:
PV-550
110V | 220V - Plug-type:
Components Checklist
PicoView
®
base unit, translation stage, camera mount, housing, and lid
Magnetic stage mounting plate
Interface mounting flange
Accessories box
Uncoated Tip Module (UTM)
Coated Tip Module (CTM)
Tip holder
CCD camera
9” B/W monitor with cabling
Allen wrenches (metric & English)
Illuminator box with 150-watt illuminator
Fiber optic cable (in illuminator box)
Fiber optic adapter ring (in illuminator box)
Product literature
Inspected by: ________________
1 R E A d T h I S f I R S T
1 - 3
1 - 4
1 R E A d T h I S f I R S T
Trademarks
The following trademarks are found in this instruction manual:
Teflon is a registered trademark of E.I. du Pont de Nemours and Co.; LTQ,
Orbitrap, Deca XP Max, Deca XP Plus Max, and Xcalibur are trademarks or registered trademarks of Thermo Fisher Scientific; MicroTight and SealTight are trademarks or registered trademarks of Upchurch Scientific, Inc. a division of
IDEX Corporation; PEEK and PEEKsil are trademarks of Victrex plc; PicoView,
PicoView, PicoClear, PicoTip, PicoFrit, SilicaTip, TaperTip, GlassTip, and PicoTip
Powered are trademarks or registered trademarks of New Objective, Inc. All other trademarks are the properties of their respective companies.
Limited Warrant y
DISCLAIMER
Technical information contained in this publication is for reference purposes only and is subject to change without notice. The information is believed to be reliable and accurate; however, nothing set forth herein constitutes a warranty of any kind or nature. Given the variety of experimental conditions, New
Objective, Inc., cannot guarantee performance at a given flow rate; the best guide to tip selection and operation is empirical testing.
The user is solely responsible for complying with any patent(s) pertaining to applications or methods using the products described or mentioned in this manual.
New Objective, Inc., warrants this Product (PicoView
®
) to be free of defects in materials and workmanship for a period of one (1) year from the date of shipment. Any item believed to be defective within the meaning of the foregoing sentence shall be returned to New Objective, Inc., and, if found by us to be defective, shall be repaired or replaced with conforming Product of like kind.
Please note that a Return Merchandise Authorization Number (RMA) will be required. New Objective, Inc., will pay return freight on unsatisfactory items.
New Objective, Inc., shall have no other liability or obligation with respect to goods alleged to be defective. The foregoing shall constitute the sole and exclusive remedy, and New Objective, Inc.’s total liability for any and all losses and damages arising out of any cause whatsoever (whether such cause be based in contract, negligence, strict liability, other tort, or otherwise) shall in no event exceed the purchase price of the Product(s) in respect of which the cause rose.
New Objective, Inc., disclaims, and shall not be liable, in any event, for loss of profits, consequential or incidental damages, or punitive or exemplary damages in connection with the Product furnished hereunder.
The foregoing limited warranty (i) shall be void as to any item of Product which is in any material respect altered by the user, and (ii) does not cover misuse of the
Product (for example, but not limited to, dropping or other mishandling of any components of PicoView, improper trimming of SilicaTips™, PicoFrit
®
Columns, or TaperTips™, damage caused by application of or exposure to excessive temperature, pressure, or voltage) or SilicaTip, PicoFrit, or TaperTip failure by reason of clogging.
The video monitor and camera are warranted to be free from defects in material or workmanship for a period of two (1) years from the date of purchase.
1 R E A d T h I S f I R S T
1 - 5
1 - 6
1 R E A d T h I S f I R S T
2 A P P L I C AT I O N S
2 Applications
PicoView
®
supports a variety of operating modes, ranging from continuous infusion at nanospray flow rates to gradient run nanobore LC-MS. The two tip modules (the coated tip module (CTM) and the uncoated tip module (UTM) included with the PicoView system afford the user the versatility to design experiments for a variety of flow rates and sensitivity requirements. With the open design and interchangeable modules, you can run the same analysis several different ways. This manual provides the most robust configurations for a given application. Following the schematic drawings, locate the desired application and the most effective PicoView configuration for that experimental design. See the referenced section for detailed directions on setting up PicoView. Techniques to optimize your spray, including how to select the best PicoTip® for your application, can be found in Section 6.
Continuous-Infusion Nanospray
Continuous infusion is the most straightforward method for sample introduction, with a syringe pump providing the solvent stream as illustrated in Figure
2.1. Sample is introduced directly from a syringe pump, at flow rates typically of 10–300 nL/min. The high voltage is applied through the coated tip module
(CTM) to the conductive coating on the PicoTip™. Coated SilicaTips™, a type of
PicoTip, are primarily used for ultra-low flow rate infusion (nanospray) to minimize electrolysis. Suggested tip sizes for continuous-infusion nanospray are 5–10
µm with a distal or standard coating. All coated tips should be handled with care, since mechanical abrasion can deteriorate the coatings. Use a pair of fine tweezers to handle the tips. Go to Section 5.3, “Coated Tip Module in the Forward
Position,” on page 23 for detailed instructions on setting up the CTM for continuous infusion.
Nanospray flow-Injection
Nanospray flow-injection entails injecting small volumes of sample into an established solvent stream, as depicted in Figure 2.2. An aliquot of sample (1–2 µL) is injected as a plug into the solvent stream through the micro injection valve sample loop. A syringe pump at flow rates of 10–300 nL/min is used to deliver the solvent stream that pushes the sample through the PicoTip. The flow-injection
Figure 2.1 Continuous-infusion nanospray
Figure 2.2 Nanospray flow-injection
2 - 1
2 - 2
2 A P P L I C AT I O N S
Figure 2.3: Microspray flow-injection
mode allows for smaller sample sizes than continuous infusion. This type of experiment is particularly useful for the rapid analysis of desalted samples. Voltage application for nanospray flow-injection is best accomplished using the coated tip module (CTM) in the forward position with conductively coated PicoTips.
SilicaTips in particular are recommended with either a distal-coating (those with
-D- in their item number) or standard coating (those with -CE- in their item number). Refer to Section 5 “Coated Tip Module in the Forward Position,” for detailed instructions on setting up the CTM for flow injection.
Microspray flow-Injection
Microspray flow-injection, as with nanospray flow-injection, entails injecting small volumes of sample into an established solvent, as diagrammed in Figure
2.3. The difference between the two is the flow rate. Nanospray flow rates are typically below 300 nL/min, whereas the higher microspray flow rates are typically between 0.5–5 µL/min. Sample is introduced as a plug into the solvent stream from an HPLC pump or syringe at flow rates of 400–5000 nL/min. The
Micro Injection Valve can be used for sample injection. Microspray flow-injection is particularly useful for the rapid analysis of desalted samples. Using a
TaperTip™, a type of PicoTip, voltage is applied through a liquid junction-style contact through either the uncoated tip module (UTM) in the back position or through the conductive coating (distal-coating style) when using the coated tip module (CTM) in the forward position. For the most robust setup, it is recommended to use uncoated TaperTips and the UTM in the back position. Suggested tip sizes for microspray flow-injection are 20 to 100 µm TaperTips. Refer to
Section 5, “Uncoated Tip Module in the Back Position,” or “Coated Tip Module in the Forward Position,” for detailed instructions on setting up the UTM or the
CTM for microspray flow-injection. Consult Technical Note TT-1, available on our web site (www.newobjective.com), to learn more about the use of TaperTips with microspray.
Nanobore LC-MS Using a Picofrit
®
Column
PicoView
®
is ideal for performing nanoscale LC-MS and LC-MS/MS using
PicoFrit
®
columns. PicoFrit columns, a type of PicoTip, are nanobore LC-MS chromatography columns with an integral tip, used at flow rates of 100–500 nL/min. In this configuration, the high voltage is applied to the back of the col-
2 A P P L I C AT I O N S umn through a liquid junction in the uncoated tip module (UTM) placed in the back position, as diagrammed in Figure 2.4. Solvent is delivered via an HPLC pump with a flow splitter. Suggested tip size is 15 µm with an uncoated PicoFrit column. Refer to Section 5, “Uncoated Tip Module in the Back Position,” for detailed instructions on setting up the UTM for a PicoFrit column.
Nanobore LC Using a PicoTip
®
with a Separate Column
PicoView ® can be used effectively for microscale LC-MS and LC-MS/MS. When running nanoscale separations it is best to use a PicoFrit
®
column, a combined emitter and a column, for increased sensitivity and decreased problems due to less plumbing. If experimental parameters do not allow use of a PicoFrit Column,
PicoView can accommodate a nanobore column connected to a PicoTip ® . New
Objective offers IntegraFrit™ c olumns designed specifically for this purpose. In this application it is recommended to use the SilicaTip type of PicoTip. Sample flows through the IntegraFrit, through the SilicaTip™, and into the mass spectrometer (Figure 2.5). Voltage is applied through a coated tip using the coated tip module (CTM) in the forward position. For a 75 µm ID column, the suggested tip size is 10 µm with a distal coated tip. Refer to Section 5, “Coated Tip Module in the Forward Position,” for detailed instructions on setting up the CTM for nanobore LC using a PicoTip connected to a column.
Capillar y bore LC
Capillary bore LC uses a column with a larger diameter than used in nanobore
LC. Capillary columns usually have an internal diameter of 100–320 µm and are suggested for use at flow rates of 200–1000 nL/min. Sample is introduced into a solvent stream through a capillary bore chromatography column, which is connected to a TaperTip™, a type of PicoTip
®
(Figure 2.6). Voltage is applied through a liquid junction in the uncoated tip module (UTM) placed in the forward position. Suggested tip size is 50 µm. Refer to Section 5, “Uncoated Tip Module in the Forward Position,” for detailed instructions on setting up the UTM for capillary bore LC using a TaperTip connected to a column.
Figure 2.4: Nanobore LC-MS using a
PicoFrit
®
Column
Figure 2.5: Nanobore LC using a
PicoTip
®
with a separate column
Figure 2.6: Capillary bore LC
2 - 3
2 - 4
2 A P P L I C AT I O N S
Figure 2.7 Assembled microtee used for making liquid-junction contact in the
PicoView UTM
Supplying Voltage to the Uncoated Tip Module
When using the UTM, high voltage is applied directly to the solvent stream in a liquid junction via a microtee made of PEEK™ polymer that contains an integral platinum electrode. Figure 2.7 shows the microee, which is easy to assemble and is ideal when using PicoFrit columns or other designs that require pre-column voltage contact. The microtee is unsuitable for low-volume post-column use, however, as it has an interior volume.
3 P I C O V I E W C O M P O N E N T S
3 Quick Guide
Components of PicoView
®
Figures 3.1A and B illustrate user-side and instrument-side views of PicoView
®
, showing the general layout of the components. The translation stage and stage plate comprise the PicoView hardware used for mounting and aligning tips with respect to the inlet on the mass spectrometer.
Flange Locking Lever
Interface Flange
CCD Camera
Optical Mount
Pan
Tilt
Focus
Fiber Optic Coupler
HV
Cable
Clip
Stage Plate
Y Adjustment
Translation Stage
X Adjustment
Universal
Valve Mount
(optional)
Grounding Clip
Component Clamps
(optional with mount)
Figure 3.1A User-side view of PicoView
®
Z Adjustment
3 - 1
3 - 2
3 P I C O V I E W C O M P O N E N T S
The optical stage, digital camera, and fiber optic illuminator make up the PicoView imaging hardware necessary for optimizing spray conditions. Complete descriptions of these components can be found later in this chapter.
Camera Mount
Illumination
Adjustment
Fiber Optic Bundle
Figure 3.1B Instrument-side view of PicoView
®
CCD Camera
Optic Tube
Slip Ring
Transparent Cover
Flange Locking
Levers
Objective Lens
Stage Plate
Fiber Optic
Coupler
Interface Flange
3 P I C O V I E W C O M P O N E N T S
Tip Modules
The two tip modules included with the PicoView
®
system afford the user the versatility to design experiments for a variety of flow rates and sensitivity requirements. The modules supply the high voltage for sample ionization through different junction styles, as dictated by the experimental design. The tip modules are mounted on the stage plate, and each module functions uniquely to accommodate different tip and column styles. The coated tip module (CTM) is depicted in Figure 3.2, and the uncoated tip module (UTM) in Figures 3.3A and B. Detailed descriptions for the experimental configuration of the tip modules are presented in
Section 5 “Setup”.
Coated Tip Module
The coated tip module (CTM), shown in Figure 3.2, connects the tip to the transfer line or column via a MicroTight ® union (Upchurch P/V/ P-720).
High voltage is provided to the coated tip using a conductive elastomer.
The CTM mounted in the forward position is the module of choice for performing continuous-infusion nanospray and microscale flow-injection experiments at ultra-low flow rates. It can also be used with commercial nanobore columns as well as with static, or offline, nanospray emitters.
Uncoated Tip Module
Within the uncoated tip module (UTM), the transfer line connects to the emitter via a modified microtee or through a zero dead volume titanium union. High voltage is applied to the liquid junction via either the platinum electrode in the microtee or through the body of a zero dead volume titanium union. Refer to Section2, “Supplying Voltage” to learn which electrode is best for your application. The UTM can operate in modes analogous to the CTM, but it is most effectively utilized with microspray flow rates for nanobore chromatography. The UTM can be mounted on the stage in the forward (Figure 3.3A) or the back (Figure 3.3B) positions.
In the back position, the UTM provides an optimal interface for PicoFrit columns to afford purification, concentration, and separation of analytes at high sensitivity. Mounted in the front position, the UTM can connect
mounting screw mounting screw mounting screw cover screw cover screw
Figure 3.2: Coated tip module (CTM) mounted in the forward position cover screw
Figure 3.3A: Uncoated tip module (UTM) mounted in the forward position
Figure 3.3B: Uncoated tip Module (UTM) mounted in the back position with tip holder forward
3 - 3
3 - 4
3 P I C O V I E W C O M P O N E N T S
Figure 3.4 MS inlet and spray as seen through PicoView imaging system
an uncoated PicoTip
®
to a nano- or capillary bore LC column.
Turn off or disconnect all power prior to performing any service on PicoView or any devices attached to it to avoid potentially lethal electrical voltages.
Always use chemical- and puncture-resistant gloves and ANSI-approved safety glasses when handling fused-silica tubing.
digitally-Controlled XYZ Positioning Stage
Precise alignment of the tip is accomplished using the PicoView ® PV
Acquire™ software and the actuated X, Y, and Z translation stage. The translation stage moves the stage plate, on which a tip module is mounted. Consult the provided PicoView PV Acquire Software Manual for more information regarding the stage operation and specifications.
Imaging System
The imaging system allows the user to quickly and efficiently optimize the electrospray conditions by providing direct observation of the character of the spray. The system includes a high-resolution CCD camera and an objective lens. Alignment of the imaging system is accomplished using the Focus, Tilt, and Pan adjustment screws of the optical stage (refer to Figure 3.1A).
Injection Valves
A micro injection valve typically serves as the inlet for sample introduction to PicoView
®
. The sample is loaded into a sample loop using an injection port adapter or a syringe directly connected to the sample inlet port. Sample and solvent from an HPLC pump or syringe are transferred to a tip module and subsequently to a column or tip. Please refer to the instructions particular to your valve for information on its setup and use, as PicoView can accommodate many different valves. Section
7 “Mounting an Injection Valve” illustrates how to mount a valve on the
PicoView universal valve mount.
4 Installing PicoView
®
Preparing the Mass Spectrometer
Before installing PicoView
®
, the mass spectrometer must be put into standby mode and the standard Ion Max™ source must be removed.
Placing the Mass Spectrometer into Standby Mode
Use the following procedure to put the mass spectrometer into standby mode
(refer to the LTQ™ operator manual provided by Thermo Finnigan for additional details).
1. Wait until data acquisition, if any, is complete.
2. Turn off the flow of sample solution, if any, from the LC or syringe pump to the Ion Max™ source.
3) From the Tune Plus window, choose Control from the menu bar, then either choose Standby or click the On/Standby button to put the MS detector in standby. The sheath gas flow will automatically be set to 20 units, and the system LED on the front panel of the MS detector will be illuminated orange.
Disconnecting the High-Voltage Cable, Gas, and Sheath Liquid Lines from the
Ion Max™
1. Disconnect the high-voltage cable from the connector labeled “HV” on the
ESI probe. To disconnect the cable, turn the locking ring on the cable counterclockwise and carefully remove.
2. Disconnect the sample transfer line from the grounded transfer line fitting on the ESI flange.
3. Disconnect the sheath gas line and fitting from the inlet labeled “Sheath
Gas” on the ESI probe by turning the blue fitting counterclockwise until the line and the fitting pull free from the probe.
4. Disconnect the auxiliary gas line and fitting from the inlet labeled “Aux Gas” on the ESI probe by turning the green fitting counterclockwise until the line and the fitting pull free from the probe.
4 I N S TA L L I N G P I C O V I E W
4 - 1
4 - 2
4 I N S TA L L I N G P I C O V I E W
Approx.
30 mm
Slip ring
Figure 4.1 The optical tube should extend approximately 30 mm below the slip ring.
5) If the sheath liquid line is attached to the ESI probe, disconnect the line and its fitting from the inlet labeled “Sheath Liquid” on the ESI probe by turning the fitting counterclockwise until the line and the fitting pull free from the probe.
Removing the Ion Max™ Source
1. Rotate the Ion Source Housing Locking Levers to unlock the Ion Max™ source from the MS detector face plate.
2. Gently pull the source towards you and away from the mass spectrometer.
3. Store the Ion Max™ source in its original foam storage container for protection.
Assembling the PicoView
®
Imaging System
The PicoView ® imaging system consists of an optical stage for fine positioning of the camera, a slip ring through which the optical tube is inserted, the optical tube, a CCD camera, a fiber optic illuminator, and a lens. Installation of the imaging system involves attaching a lens and the CCD camera (or optional eyepiece) to the optical tube. The optional Hauppauge USB Live Video Capture enables observation of the live spray directly on the system computer screen, the video monitor, or both. Contact New Objective for more information.
During assembly, avoid getting fingerprints on the imaging system lenses.
Connecting the Optical Tube and Lens
1. Locate the optical tube and the 9/64 Allen wrench in the accessories kit.
Using the Allen wrench, loosen the slip ring (refer to Figure 4.1). With the threaded end of the optical tube pointing up, slide the optical tube through the slip ring so that approximately 30 mm extends below.
2. Tighten the fastener using the Allen wrench. Take care to not over tighten.
3. Select the low-power lens from the accessories box.
4. Screw the (male) threaded end of the lens onto the mating (female) thread on the instrument-side end of the optical tube. Turn the lens counterclockwise until it is finger-tight (see Figure 3.1A).
4 I N S TA L L I N G P I C O V I E W
Attaching the High-Resolution CCD Camera
1. The CCD camera and illuminator are shipped in containers separate from
PicoView. Remove the CCD camera from its box and remove the protective end cap from the camera.
2. Place the optical end of the CCD camera flush with the user end of the optical tube.
3. While supporting the CCD camera with one hand, screw the threaded nut of the CCD camera clockwise onto the threads on the user end of the optical tube until the CCD camera nut is finger-tight.
4. While supporting the CCD camera with one hand, loosen the optical tube fastener at the top of the slip ring using a 9/64 Allen wrench. Rotate the optical tube until the CCD camera is aligned horizontally, then tighten the optical tube fastener to hold the CCD camera in place.
Adjusting Camera Gain and Gamma
For optimal imaging the CCD camera’s gain setting needs to be in the auto (A) position, and the gamma control needs to be turned on. The rotary gain switch has three settings: auto (A), fixed (F), and manual (M). The gamma setting (γ) is controlled with a dip switch, and has on and off positions. Both switches are located on the rear of the camera housing just below the video out connector.
Proper camera settings are shown in Figure 4.2. If your camera settings are correct no action needs to be taken.
1. Using a jeweler’s screwdriver or similar instrument, rotate the (brown) gain control switch clockwise until the slot points to the “A” position.
2. Using the same screwdriver, slide the gamma control to the right into the
“ON” position.
Figure 4.2 CCD camera gain switch set to automatic
4 - 3
4 - 4
4 I N S TA L L I N G P I C O V I E W
Guide pins
Figure 4.3 Attach brackets to source mounting flange
Figure 4.4 LTQ™ Interface Flange mounted on the LTQ
Interface Flange levers locked in place
Figure 4.5 LTQ™ Interface Flange locked on the LTQ
Figure 4.6 PicoView mounted on the
LTQ™ Interface Flange
Mounting PicoView
®
Installing the LTQ Interface Flange
The LTQ™ Interface Flange is used to secure the instrument-end of PicoView to the LTQ inlet block on the front of the mass spectrometer.
1. Locate the LTQ™ Interface Flange
2. Make sure that the Flange locking levers are open (pointing towards the user, away from the MS detector).
3. Align the two guide pin holes at the base of the Interface Flange with the guide pins on the face of the MS detector and gently push the Interface
Flange onto the detector face plate. Ensure that the the Interface Flange is flush against the front of the face plate (Figure 4.4).
4. Rotate the Flange locking levers 90º inward towards the inlet of the mass spectrometer to lock the Flange into place (Figure 4.5).
Attaching PicoView
®
to the LTQ™ Interface Flange
1. Carefully align the PicoView base onto the slide base of the Interface Flange.
2. With the PicoView mounted on the Interface Flange (see Figure 4.6), gently slide the assembly toward the MS detector face plate.
Mounting the Fiber Optic Illuminator
To install the fiber optic illumination, pull the PioView source away from the instrument housing. The optical fiber provides the intense, no-heat illumination necessary for the CCD camera.
1. Locate the fiber optic bundle, bundle adapter, and power cord from the illuminator box.
2. Remove the plastic sleeve from each end of the fiber optic bundle.
3. Slip one end of the fiber optic bundle through the opening on the right side of the PicoView housing and into the back end of the fiber optic coupler. The coupler holds a lens which focuses the illumination on the nanospray emitter and can be adjusted to accommodate for tip position using the Illumination
Adjustment knob (see Figure 3.1B).
4 I N S TA L L I N G P I C O V I E W
4. With the fiber optic bundle securely placed within the coupler, lock the bundle in position using the thumb screw. Do not over tighten. (Figure 4.7)
5. Insert the bundle adapter and the other end of the fiber optic bundle into the illuminator faceplate. Tighten the set screw to finger-tight. Figure 4.8 shows the assembled fiber optic bundle and mount.
Locking the PicoView
®
Housing to the Mounting Brackets
1. Close the transparent top cover on the PicoView® source.
2. With the PicoView mounted on the Interface Flange base, gently slide the assembly toward the face plate of the LTQ™. A groove located at the top left of the Flange will lock the cover down when the source is is pushed firmly against the flange and interlock switch. (Figure 4.9)
3. Make sure the lower portion of the mounting brackets line up with the associated latches mounted on the base of the PicoView source (Figure 4.10).
If they do not, check to make sure PicoView is properly mounted on the
Interface Flange slide base. Adjustment of the base may be necessary (see
Section 4.3.2.
4. To lock the PicoView in place, fasten the two latches on the bottom of the
PicoView base and gently lock them into place (Figure 4.10).
Connecting the PicoView
®
Imaging System
1. Remove the monitor from its shipping carton and place it in a convenient viewing area.
2. Plug the power cord for the monitor into an electrical outlet (preferably one protected by a suitable surge protector). Connect the video cable from the monitor to the BNC video out jack on the high-resolution CCD camera.
3. Connect the camera power supply to the high-resolution CCD camera
(Figure 4.11). Plug the other end of the cable into an electrical outlet (again, preferably one with a suitable surge protector).
Connecting the Optional Hauppauge USB Live Video Capture
1. Locate the BNC cable supplied with the Hauppauge system. Using a BNC-
RCA adapter, plug the BNC cable into the video output connection on the
Figure 4.7 When locking the fiber optic bundle in place, do not overtighten thumb screw
Figure 4.8 Fiber optic bundle properly installed
Cover locked
Figure 4.9 Source pushed firmly against flange
Figure 4.10 Brackets should line up with latches
4 - 5
4 - 6
4 I N S TA L L I N G P I C O V I E W
Figure 4.11 Connect the power cable to the camera
Figure 4.12 Exterior view of assembled
PicoView
Happague USB
Live Video
Capture
Module
PicoView
CCD Camera
Figure 4.13 Video out from CCD camera to video in connection on monitor. Video out from monitor goes to Live Video
Capture module.
back of the monitor.
2. Use a BNC-RCA adapter to connect the BNC cable to the Hauppauge USB
Live Video Capture module. USB Live can be directly connected to your computer’s USB port. Refer to Figure 4.13 for cabling diagram.
3. Refer to Happauge instructions for installing the imaging software.
Turning on the Power to the Mass Spectrometer
From the Tune Plus window, choose Control from the menu bar; then either choose Standby or click the On/Standby button to turn on the MS detector. The sheath gas flow will automatically be set to 20 units, and the system LED on the front panel of the MS detector will be illuminated green.
Turning Off the Sheath Gas
The LTQ™ source recognition feature will automatically disengage the sheath gas when it recognizes that a nanospray source has been attached.
Adjusting the Camera Position
Optimized operation of PicoView involves adjustments of both the camera and the tip positions. Upon installation, the imaging system should only require fine adjustment. However, some course adjustment may be necessary if the lens is changed.
Fine Adjustment
Using your fingertips to move the fine adjustment knobs, you can adjust the camera position to optimally image the tip and spray pattern during operation. If a tip is not currently loaded in the PicoView source, you may use the inlet of the mass spectrometer to adjust the imagainf system. The locations of the fine tuning knobs are indicated in Figure 3.1A.
1. Move the Tilt knob up and down until the inlet is visible. At this point the inlet image will likely be very fuzzy and require focusing. Using the Tilt knob, center the inlet on the monitor (or as viewed using the optional eyepiece).
2. Adjust the Focus knob until the inlet comes into focus.
3. Move the Pan knob left or right to center the inlet.
4 I N S TA L L I N G P I C O V I E W
Coarse Adjustment of the Camera Body
NOTE: Only perform coarse adjustment if the fine adjustments on the optical mount and the stage plate will not allow adequate imaging of the tip.
1. Using a 9/64 Allen wrench, loosen the optical tube fastener at the top of the slip ringholding the optical tube.
2. Looking at the monitor, slowly slide the optical tube through the slip ring until the inlet is visible and in focus. The inlet will appear on the monitor as a polished metal surface at the top of the field of view (see Figure 3.5).
3. Tighten the screw on the optical tube slip ring to hold the optical tube in place.
4. Use the fine adjustment method above to focus the image of the inlet further.
Grounding Requirements
In systems where high voltage is applied directly to the ESI tip, the liquid sample inside the tip and transfer line tubing are also raised to high voltage. To prevent exposure to potentially lethal voltages, a suitable ground point for the liquid inside the line must be provided. It is best not to position the ground too close to the tip. Two recommended methods for grounding the source are described.
Grounding Through a Union
The ground union (Figure 4.13) is a stainless steel low dead volume union.
During operation, this union is placed in the grounding clip on the housing of the PicoView, situated just under the valve mount.
To ground a sample:
1. Locate the ground union in the PicoView accessories box.
2. Remove the nut and ferrule from one side of the union by turning the fitting counterclockwise.
3. Thread fused-silica through a green SealTight™ adapter sleeve. Carefully cleave the end of the tubing.
4. Insert the sheathed tubing and fitting into the ground union receptacle.
Finger-tighten the fitting by turning clockwise, making sure the tubing is firmly seated into the bottom of the fitting. (Figure 4.14)
Figure 4.13 The grounding clip
Figure 4.14 Grounding union in place
4 - 7
4 - 8
4 I N S TA L L I N G P I C O V I E W
CTM
Figure 4.15A Optimal location for grounding union for continuous-flow microspray or nanospray
UTM
Figure 4.15B Optimal location for grounding union for nanobore chromatography with a PicoFrit™ column
Repeat steps 1–3 for the tubing leading from the installed tip module. Complete descriptions of the tip modules can be found in Section 5.
Grounding Guidelines with the CTM or UTM
For the highest level of safety it is recommended that the grounding union be spliced into the plumbing between the Micro Injection Valve and the CTM or
UTM, as shown in Figure 4.15A. This configuration is recommended for continuous-flow microspray or nanospray operation. With nanobore chromatography, however, the interior volume of the union may deteriorate chromatographic peak shape. In this event, the optimal place for the grounding union is between the injection valve and the HPLC or syringe pump (Figure 4.15B).
If your mobile phase contains a high concentration of TFA or formic acid, the electrical conductivity of the liquid may rise to the point where the electrospray power supply is partially shorted to ground. If this occurs, it becomes impossible for a stable spray to form because the voltage at the end of the tip is too low, and the total spray current displayed on your monitor will read abnormally high (in the multi-microamp range). This can only be corrected by reducing the conductivity of the mobile phase or by replacing the tubing between the ground point and the tip module. The new splice should be of longer length, of smaller inside diameter, or both. Good performance can be obtained with a 25–30 cm length of fused silica of either 20 or 50 µm ID.
Grounding to a Syringe Needle or HPLC
If the syringe pump is being used to deliver solvent to PicoView, use an insulated wire with alligator clips on each end for grounding. Clip one end to the stainless steel syringe needle. Clip the other end to a ground point such as the loop on the injection valve located on the front panel of the mass spectrometer.
If an HPLC is being used to deliver solvent to PicoView, please refer to the manufacturer’s directions for grounding the pump.
WARNING: Transfer lines connected to either the tip module or the micro injection valve must not be made from an electrically conductive material such as steel or PEEKsil™. These transfer lines must be fabricated from an electrically insulating material such as PEEK™ or fused silica. Otherwise, the operator may be exposed to potentially lethal voltage.
CAUTION: Do not attempt to use the injection valve as a grounding point.
The interior of the valve is fabricated from ceramic materials and is electrically insulating; therefore, a proper ground will not result.
4 I N S TA L L I N G P I C O V I E W
4 - 9
4 - 1 0
4 I N S TA L L I N G P I C O V I E W
5 S E T U P
5 Setup
Cut ting fused Silica
Proper cleaving of the fused-silica tubing is critical for achieving optimal performance in nanospray applications. A flat, smooth cut is essential for maintaining low dead volume connections. Cleaving is best accomplished with a high-quality diamond chip scribe, available from many chromatography supply houses.
New Objective carries a high-quality scribe as part of a nanospray tool kit (stock number TIP-KIT). Inexpensive carbide or ceramic scribing tools are not recommended, since they generally result in poor-quality (i.e., ragged) cleaved ends, generating fine particles that lead to clogging.
1. Place the tubing to be cut on a clean, flat surface and position the cleaving tool blade perpendicular to the tubing bore, as illustrated in Figure 5.2
2. Press down with a gentle force. DO NOT saw or move the blade laterally; simply nick the surface of the polyimide coating to score the fused silica.
(Figure 5.2 inset)
3. Pull gently on the tubing along its axis; it should easily separate at the point of scoring. If it does not, repeat the procedure with slightly more force. Be careful not to force the blade through the tubing, as this will create a ragged end.
Be sure to pull the tubing apart, do not bend the tubing to induce a snap.
This will produce a burr along the tubing face and result in less-than-optimal connections.
4. It is best to check the cleaved tubing ends for particle contamination prior to use.
This is most effectively done using a light microscope at 100x magnification.
Connectors
Making leak-free connections is important for limiting sample loss and for reducing turbulent flow. PicoView
®
comes with two different systems of microconnectors for plumbing fused silica to the various fittings. Assembling the connectors is covered in detail later in this section. The two different connector systems differ by size and are not interchangeable. The MicroTight ® system is used with the microtee and MicroTight
®
unions in the CTM and UTM tip modules and
A B
Figure 5.1 (A) Close-up views of standard diamond-chip scribe (90º), and
(B) high-performance diamond- bladed scribe (60º)
B C
Figure 5.2 (A) Improper cutting angle (B) Align cleaving tool blade perpendicular to tubing (C) Press down gently, scoring tubing (D) Too much downward pressure will crush tubing, producing particles that can cause tubing to clog
Figure 5.3 Typical cleave using diamond scribe.
5 - 1
5 - 2
5 S E T U P with the tip holder. The SealTight™ system is used to connect fused silica to any standard 1/16” port, such as the grounding union. Each union uses specific ferrules, nuts, and sleeves to seat the fused silica. Do not use a MicroTight sleeve with a SealTight™ fitting and vice versa. Table 5.1 lists the different locations of connectors within PicoView
®
and describes which ferrules and nuts are used. All of the listed components are found in the PicoView accessory box. Replacement unions, ferrules, nuts, and sleeves should be ordered directly from Upchurch
Scientific (www.upchurch.com). The corresponding Upchurch part numbers are provided.
Connectors
Upchurch P/N
Connector
P-720
N/A
P-720
Used in...
CTM union
UTM (microtee)
UTM (ZDV)
Tip holder union
Grounding union
Injection port adapter
System
MicroTight
®
MicroTight
®
SealTight™
MicroTight
®
SealTight™
MicroTight
®
Upchurch P/N
Ferrule Nut
Combined F-125
F-172 P-416
F-192 F-194
Combined F-125
F-192 F-194
F-152 P-416
Sleeves are used within unions to ensure a reliable connection. As with the ferrules and nuts, it is very important to use the appropriate sleeve for the connection system. The table on page 5-3 lists the different sleeves supplied with PicoView and their applications.
Always use MicroTight
®
sleeves with MicroTight
®
unions and SealTight™ sleeves with
1/16” diameter fittings.
Sleeves
System
MicroTight
®
MicroTight
SealTight™
®
Sleeve
Color
Blue
SealTight™ Blue
Green
Upchurch
Part No.
F-183x
Green F-185x
F-240
F-242
Sleeve OD
(inches)
0.025
0.025
1/16
1/16
Sleeve
ID (µm)
280
395
280
395
Connector
CTM, UTM, Tip holder
CTM, UTM, Tip holder
ZDV, Grounding union
ZDV, Grounding union
The sleeve ID should be approximately equal to the tubing OD. Other sleeve sizes are available from Upchurch Scientific. 380 µm ID sleeves are compatible with New Objective
SilicaTips.
Always select proper ferrules, nuts, and sleeves for the union. Mismatching of union components will result in spaces with dead volume or a leaky seal.
Always cleave the fused silica, either tubing or the back end of a Pico-
Tip™, after pushing it through a sleeve. The fused silica will collect dirt and particles that were in the sleeve, which, if left in the fused silica, may cause clogs downstream. Cleaving the fused silica will help prevent particle contamination.
Coated Tip Module in the for ward Position
This section provides instructions on connecting standard-length 5 cm distal or standard coated PicoTips ® to a transfer line or capillary column. “PicoTip” refers to any of New Objective’s high-quality tips for electrospray ionization, such as
SilicaTips™, PicoFrits ® , and TaperTips™.
Take care when tightening the MicroTight
®
fittings, making sure to only tighten enough to prevent leaks from occurring. Due to the delicate nature of some fused-silica tubing, it is possible to damage the tubing if the fittings are overtightened.
5 S E T U P
5 - 3
5 - 4
5 S E T U P
Figure 5.4 MicroTight
®
union, gauge plug, and compression fittings
Figure 5.5 MicroTight
®
union with gauge plug and compression assembly ready to load
Figure 5.6 MicroTight
®
union with gauge plug and compression assembly loaded
Figure 5.7 Union, compression fitting, and MicroTight
®
sleeve cut to 14 mm
Loading the MicroTight
®
Union
1. Remove the MicroTight ® union (Upchurch P/N P-720) from the PicoView ® accessories box. Unscrew and remove the compression fittings from both ends of the union.
2. Screw the white gauge plug finger-tight on to one end of the union. Thread the fused-silica transfer line through a green MicroTight sleeve. The appropriate sleeve size is 0.002–0.003 inches greater than the OD of the capillary tubing. Use the green MicroTight sleeves with 360 µm OD tubing. After the transfer line passes through a green sleeve, thread it through one of the compression fittings. Figure 5.5 shows the union loaded with the white gauge plug on the right and fused-silica tubing threaded through a tubing sleeve and a compression fitting. Cleave the end of the tubing and slip it into the union until both the tubing and the sleeve ends seat against the gauge plug inside the union. Screw the compression fitting finger-tight into the union, as shown in Figure 5.6.
3. Remove the gauge plug and return it to the PicoView accessory box.
4. Carefully trim a new green MicroTight sleeve to a length of approximately 14 mm, as shown in Figure 5.7. The shorter sleeve will allow the coating on the
PicoTip
®
to contact the conductive elastomer inside the CTM.
5. Choose a PicoTip from the assortment sent with PicoView. Although either coating style, the standard coating (-CE-) or the distal coating (-D-), will work, if flow rates permit, the distal coating is recommended due to its immunity to arcing.
6. Insert the back, or distal, end of the PicoTip through the trimmed sleeve and through the other compression fitting. When properly installed, the tip end should extend 15–20 mm past the end of the fitting when it is tight. This will afford optimal positioning of the PicoTip within the adjustment range of the stage plate. Using a ruler, measure and note the distance the tip extends from the fitting. Remove the fitting/sleeve/PicoTip assembly and carefully trim the back end of the PicoTip so the extension of the tip beyond the fitting is 15–20 mm. Cleave the remaining portion from the back end of the PicoTip. See
“Cutting Fused Silica” earlier in this section for cleaving instructions.
7. After trimming, reinsert the assembly into the union, seat the PicoTip and sleeve against the transfer line or column tubing, and tighten the compression fitting finger-tight. Pull gently on the tubing to ensure the connection is tight. Figure 5.9 depicts the fully assembled union.
5 S E T U P
Always use chemical- and puncture-resistant gloves and ASNI-approved safety glasses when handling fused-silica tubing.
Loading the Coated Tip Module
1. Remove the CTM from the PicoView
®
components box. Disassemble the
CTM by unscrewing and removing the cover screw.
2. Lower the assembled MicroTight
®
union and PicoTip
®
into the cavity in the base of the CTM, as shown in Figure 5.10.
The PicoTip must make direct contact with the conductive elastomer inside the cover of the CTM.
3. Replace the top of the CTM. Replace the cover screw through the hole in the top and align it with the mating hole in the base. Be careful not to touch the tip of the emitter to any surface.
A
B
Figure 5.8 PicoTip™ in fitting, before (A) and after (B) trimming to length
Attaching the CTM to the Stage Plate in the Forward Position
Proper orientation of the CTM in the forward position is illustrated in Figure 5.9.
The stage plate is configured like an optical breadboard to provide the user with the greatest versatility in tip placement. The best camera view will be provided when the tip is approximately perpendicular to the camera axis, at a 45º angle with respect to the inlet.
It is very easy at this point to break the tip. Be careful not to touch the tip to any surface.
1. Unlock and slide the PicoView unit from the mass spectrometer and open the cover.
2. Remove the magnetic stage plate from the unit by grasping the plate firmly and pulling upward.
3. Set the CTM into the front positioning groove on the stage plate. Align the mounting slot on the CTM base with a corresponding tapped hole on the stage plate. Refer to Figure 5.9 as necessary.
4. Insert the stage mounting screw through the mounting slot on the CTM base and thread it into the threaded hole on the stage plate, as shown in Figure
5.9. Tighten the screw.
Figure 5.9 A fully assembled MicroTight
® union
Figure 5.10 MicroTight
®
union inserted in the CTM base
5 - 5
5 - 6
5 S E T U P
mounting screw front position groove cover screw
Figure 5.11 CTM in the forward position
Figure 5.12 CTM assembly on the stage plate
The CTM can be mounted so that the PicoTip™ is pointing directly at the entrance of the inlet. This alignment is less desirable because the imaging system cannot adequately image the tip at that angle. There is no apparent loss in sensitivity when spraying at a moderate angle with respect to the inlet.
Connecting High Voltage
If the CTM is mounted so that the PicoTip
®
is directly pointing at the entrance of the inlet, thread the high-voltage cable through the opening in the rear of the housing.
1. Connect the cable by inserting it into the cable jack and turning the locking ring clockwise until it is tight.
2. Place the magnetic stage back onto the XYZ stage as shown in Figure 5.12.
Adjusting the Tip Position
Carefully slide the source into operating position while observing the tip position.
If it looks like the tip may contact the inlet, use the Y-axis actuator manual knob control (Figure 3.1A) or the PicoView
®
Acquire™ Stage Control panel to adjust the Y-axis to prevent contact. When certain that contact will not occur, lock the bracket latches on the PicoView base, securing it to the source mounting flange.
By visual inspection, adjust the stage plate position using either the manual knob controls (see Figure 3.1A) or through the PicoView Acquire Stage Control panel until the tip is approximately 2–5 mm from the mass spectrometer inlet. Focus the camera using the focus knob on the optical stage (see Figure 3.1A). Instead of focusing on the inlet, focus on the tip, which may appear as a fuzzy line prior to fine focusing. Do not let the tip contact the inlet.
Uncoated Tip Module in the back Position: Long PicoTips
The uncoated tip module uses a microtee to supply high voltage. When using
PicoView with long PicoTips, such as PicoFrits or uncoated TaperTips, a tip holder is needed to anchor and position the tip toward the inlet. This orientation is accomplished using a MicroTight
®
union within the tip holder.
5 S E T U P
Using PicoFrit® Columns
PicoView ® is ideal for performing nanoscale LC-MS and LC-MS/MS using
PicoFrit
®
columns. In this configuration, the high voltage is applied to the back of the column through a liquid junction in the uncoated tip module. The PicoFrit column is packaged as a loop, as shown in Figure 5.13, to keep both ends of the column at the same pressure during storage and shipping. Do not remove either the orange-colored PEEK™ sleeve or the snug-fitting FEP (Teflon
®
) tubing holding the ends of the loop together until the column is being prepared for installation and use.
There are some important considerations in the handling and use of PicoFrit columns that make them very different from any other chromatography columns on the market today. PicoFrit columns are fabricated from 360 µm OD, polyimidecoated, fused-silica tubing. The column has a specially tapered tip with an integral high-porosity frit. Behind the frit is the packed chromatography bed. There is no frit at the back end of the bed, only unpacked fused-silica tubing. Mobile phase flow must always be directed toward the tip. Reversing the flow may result in partial or complete unpacking of the chromatography bed.
The column is shipped filled with methanol and needs to be conditioned with an appropriate mobile phase for your gradient. Since there is no distal frit, the distal end of the column bed may loosen with time; this is not a problem, as the bed will repack when the column is pressurized.
The label attached to the opaque orange PEEK sleeve that slides along the length of the column. The arrow on the label points toward the tip end.
The tip end may also be identified by the charred section of polyimide coating just prior to the tapered region of the tip.
Removing a PicoFrit
®
Column from the FEP Sleeve
Care must be taken to properly remove the column from the clear FEP (Teflon) sleeve to prevent damaging the fragile tip and frit. Use the free-sliding orange PEEK sleeve–assisted by gravity–to push the clear FEP sleeve off the fused-silica tubing without damaging the tip.
1. Remove the distal end of the column from the FEP sleeve by either pulling it free of the sleeve or (preferably) by cleaving the fused-silica tubing near the terminus.
Figure 5.13 PicoFrit
®
column packaged for shipping
Figure 5.14 Pushing the PEEK™ sleeve against the FEP sleeve
Figure 5.15 Pushing the FEP sleeve off the tip end of a PicoFrit™ column
5 - 7
5 - 8
5 S E T U P
Figure 5.16 UTM aand tip holder bases attached to stage plate
UTM mounting holes
Rear position groove
Tip holder mounting
holes front positioning groove
Figure 5.17 Location of mounting holes for attaching the uncoated tip module and the tip holder
Figure 5.18 PicoFrit
®
column loaded into MicroTight union
2. Slide the PEEK sleeve toward the tip end until it butts up against the FEP sleeve, as in Figure 5.14.
3. Orient the FEP sleeve vertically, with the tip facing toward the floor. This way, when the FEP sleeve slides free, it will fall toward the ground without damaging the tip.
4. Carefully push the PEEK sleeve against the FEP sleeve until the FEP sleeve falls off, as shown in Figure 5.15. This may or may not take a LOT of force. You will have to move the PEEK sleeve about 3–5 mm. Grasp the column in one hand while pushing the sleeve off with the other hand.
5. Once the FEP sleeve falls away, remove the PEEK sleeve by sliding it over the back end. Do not let the PEEK sleeve slide off the tip end as this will damage the tip.
Retain the column label for identification purposes.
Attaching the UTM to the Stage Plate in the Back Position
Figure 5.16 illustrates proper orientation of the tip holder and the UTM. The stage plate is configured like an optical breadboard to provide the user with the greatest versatility in tip placement.
1. Unlock the PicoView base from the interface flange, slide the source away from the mass spectrometer and lift open the cover.
2. Remove the magnetic stage plate from the unit by grasping the plate firmly and pulling upward.
3. Set the UTM in the rear positioning groove on the stage plate and align the mounting slot on the UTM base with the corresponding tapped holes on the stage plate. Refer to Figures 5.16 and 5.17.
4. Insert the mounting screw through the mounting slot on the UTM base and thread it into an appropriate threaded hole on the stage plate, as shown in
Figures 5.16 and 5.17 and tighten.
Loading the MicroTight ® Union
1. A MicroTight
®
union within the tip holder is used as a pass through to position the tip toward the inlet. Locate the union in the PicoView ® accessories box.
5 S E T U P
2. Unscrew and remove the compression fittings from the end of the union.
Thread the distal end of the PicoFrit
®
through a green MicroTight sleeve and through a MicroTight fitting. Gently screw the fitting into the union, but do not tighten. Push the distal end of the PicoFrit all the way through the union.
The PicoFrit should freely move within the union.
3. When properly installed into the MicroTight union, the tip end should extend
15–20 mm past the end of the fitting when it is tight. This will afford optimal positioning of the tip within the adjustment range of the stage plate. Using a ruler, measure and note the distance the tip extends from the fitting. Gently move the PicoFrit until the tip extends 15–20 mm past the end of the fitting.
Finger-tighten the compression fitting to hold the tip in place. Figure 5.18 shows a correctly loaded union.
Installing the MicroTight
® Union into the Tip Holder
It is very easy at this point to break the tip. Take care not to touch the tip to any surface.
1. Being careful not to put mechanical stress on the fused-silica tubing, insert the MicroTight union into the recessed area of the tip holder cover. Press gently until the union snaps into place (Figure 5.19).
2. Place the top of the tip holder with the loaded union over the base. Replace the cover screw through the hole in the top and thread it through the mating hole in the holder base. Tighten.
Supplying High Voltage
The uncoated tip module uses a modified microtee to supply the high voltage at the liquid junction. This modified microtee has an integrated platinum wire that makes connection with the liquid sample at the point that the two pieces of fused-silica tubing are joined in the union.
Plumbing the Modified Microtee
1. The modified microtee joins the transfer line to the PicoTip ® and supplies the high voltage. Remove the microtee from the PicoView
®
accessory box.
Orient the microtee as shown in Figure 5.20 so that the platinum electrode
Figure 5.19 Union installed in the tip holder
Figure 5.20 Union installed in the tip holder
Do not adjust end cap!
Inlet
Figure 5.21 microtee with sleeves
Outlet
5 - 9
5 - 1 0
5 S E T U P
Figure 5.22 Fitting nut, MicroFerrule, and sleeve threaded by PicoTip
A B
Figure 5.23 Assemble the nut, ferrule, sleeve, and PicoTip (A) and secure the finger-tight into the microtee (B)
A B
Figure 5.24 (A) Assemble the nut, ferrule, sleeve, and transfer line and (B) secure into the microtee
is facing away from the user and the setscrews are visible. Unscrew the nuts and remove the black ferrules from the posts of the microtee.
Do not loosen the setscrews or remove the electrode cap, as this may damage the electrode. The solvent will not become charged and an electrospray will not form. Altering will void warranty.
2. Thread the end of the PicoTip tubing through a green MicroTight sleeve
(Upchurch P/N F-185), which is used for assembly with 360 µm OD tubing.
Make sure the PicoTip does not extend past the tubing sleeve end that will be inserted into the microtee. Thread the sleeved PicoTip through the fitting nut and a black MicroFerrule, as shown in Figure 5.22.
3. Cleave the end of the PicoTip after the tubing is threaded through the sleeve, nut, and ferrule. Instructions for cleaving fused silica may be found in Section
5.1 on page 21. Slip the end of the tubing through the right post of the microtee, as viewed in Figure 5.23A, until the tubing and sleeve seat against the bottom ledge inside the post, as shown in Figure 5.23B. Screw the nut finger-tight onto the microtee.
4. Insert the distal end of the fused-silica transfer line through a green MicroTight sleeve, then through the nut and the black MicroFerrule, as shown in Figure
5.24A. Carefully trim the end of the transfer line. After trimming, insert the assembly back into the microtee, seat the transfer line, ferrule, and sleeve against the PicoTip, and finger-tighten the nut, as shown in Figure 5.24B.
Gently pull on the tubing ends to ensure the connection is tight. Check for leaks by running solvent through the tubing at the expected operating pressure. Leaks will be apparent if solvent collects at the exposed ends of the sleeves.
5 S E T U P
Loading the Assembled Microtee into the UTM
1. Lower the assembled microtee into the cavity in the base of the UTM (see
Figure 5.28). The setscrews on the black cap should be visible when the microtee is properly in place.
2. Replace the UTM module top. Place the cover screw through the hole in the module top and align it with the mating hole in the module base and tighten.
Figure 5.28 shows properly mounted UTM and tip holder.
Alignment of the UTM cover is critical. Misalignment of cover may damage the internal spring contact mechanism. make sure cover is correctly aligned with base before applying pressure and securing cover.
Connecting the High Voltage
Run the high-voltage cable from the mass spectrometer through the opening in the rear housing. Connect the cable by pushing it into the cable jack and turning the locking ring clockwise until it is tight.
Adjusting the Tip Position
By visual inspection, adjust the stage plate position using the manual knob controls (see Figure 3.1A) until the tip is approximately 2–5 mm from the mass spectrometer inlet. Focus the camera using the focus knob on the optical stage (see
Figure 3.1A). By focusing on the inlet and then bringing the tip into focus by adjusting the stage position, you are assured that the tip is vertically in line with the inlet.
Figure 5.25 Plumbed microtee loaded in the UTM
Figure 5.26 UTM mounted in rear position with tip holder
5 - 1 1
5 - 1 2
5 S E T U P
mounting screw cover screw
Figure 5.28 UTM mounted in the forward position on the stage plate
UTM mounting holes
Rear position groove
Tip holder mounting
holes front positioning groove
Figure 5.29 Location of mounting holes for attaching the uncoated tip module and the tip holder
Uncoated Tip Module in the for ward Position
The UTM can be used with uncoated PicoTips in the forward position for continuous infusion, as shown in Figure 5.28. This configuration minimizes transfer volumes by accommodating a short PicoFrit column (5 cm or shorter) or an uncoated PicoTip. In this arrangement, as with the UTM in the back position, high voltage is applied directly to the solvent stream in a liquid junction via an electrode. The uncoated tip module uses a special microtee to supply the high voltage.
Loading the UTM is identical for use in either the forward or back positions. See page 5-9 for instructions on loading the UTM.
Attaching the UTM to the Stage Plate in the Forward Position
The stage plate is configured like an optical breadboard to provide the user with the greatest versatility in tip placement. The best camera view will be provided when the tip is approximately perpendicular to the camera axis.
1. Unlock and slide the PicoView unit away from the mass spectrometer and open the cover.
2. Remove the magnetic stage plate from the unit by grasping the plate firmly and pulling upward.
It is very easy at this point to break the tip. Be careful not to touch the tip to any surface.
3. Set the UTM into the front positioning groove on the stage plate and align the mounting slot on the UTM base with a corresponding tapped hole on the stage plate. Refer to Figure 5.31 for positioning.
4. Insert the mounting screw through the mounting slot on the UTM base and thread it into a threaded hole on the stage plate and tighten the screw.
Connecting the High Voltage
Thread the high-voltage cable from the mass spectrometer through the opening in the left side of the housing. Connect the cable by pushing it into the cable jack and turning the locking ring clockwise until it is tight.
Adjusting the Tip Position
By visual inspection, adjust the stage plate position using either the manual knob controls (see Figure 3.1A) or through the PicoView
®
Acquire™ Stage Control panel until the tip is approximately 2–5 mm from the mass spectrometer inlet.
Focus the camera using the focus knob on the optical stage (see Figure 3.1A).
Refer to Section 6 for information on optimizing the spray.
5 S E T U P
5 - 1 3
5 - 1 4
5 S E T U P
6 Techniques to Optimize PicoView
®
This section provides techniques to assure successful use of PicoView
®
, along with hints on ways to optimize the spray to consistently generate high-quality data. Also discussed are the interdependent parameters involved in creating stable electrospray.
6 T E C h N I Q U E S T O O P T I M I Z E P I C O V I E W
Selecting a PicoTip
®
Low flow rate ESI (under 1 µL/min) differs substantially from conventional ESI in that signal levels in the mass spectrometer are more sensitive to solvent composition, flow stability, and applied voltage. It may take a little time to learn how to obtain consistent results at low flow rates. A little patience and practice early on can pay off greatly in terms of success.
An effective way to begin working at low flow rates is by starting with larger (15–
30 µm) ID tips and using flow rates at the higher end of the recommended range of operation for a given tip style. Once you are comfortable working at a certain level of performance, you can more easily switch to emitters with smaller diameters and operate at lower flow rates. “PicoTip
®
” refers to any of New Objective’s high-quality tips for electrospray ionization, such as SilicaTips™, PicoFrits
®
, and
TaperTips™. TaperTips are used for higher flow rate applications and may be a good starting point when learning to work with nanospray. Once basic performance levels are established, you can switch to SilicaTips with smaller tip sizes.
For highly aqueous mobile phases, however, tip sizes of 10–15 µm and smaller are recommended.
Choosing a Tip Size and Coating St yle
New Objective SilicaTips are available in sizes from 2 µm ID to 30 µm ID, in three different coating styles: standard (-CE-), distal (-D-), and uncoated (-N-).
Coated PicoTips have a special enhanced conductive multilayer coating (U.S.
Patent 5,788,166) that provides for excellent electrochemical stability and durability against ESI solvent exposure. All coated tips should be handled with care, since mechanical abrasion can deteriorate the coatings. Use a pair of fine tweezers to handle the tips.
6 - 1
6 - 2
6 T E C h N I Q U E S T O O P T I M I Z E P I C O V I E W
Coated tips are typically employed for the lowest flow rate applications requiring the highest degree of performance from the system. For lowest flow rate experiments, the standard (-CE-) coating is recommended, but it may be subject to damage from arcing at high voltage. The use of distal (-D-) coated tips is encouraged due to their immunity to arcing. Use uncoated (-N-) PicoTips when a liquid junction is required, typically for nanoscale flow injection applications or when using LC columns larger than 100 µm ID. The choice of tip size and coating style will be influenced by the desired flow and application (continuous-flow nanospray, capillary LC, CE interfacing, etc.). See Section 2 on page 5 for assistance in choosing tip size and coating style based on the desired application. Since the size of the Taylor cone grows with flow rate, it is proportional to tip size. Use
Table 6.1 as a guide in choosing the proper tip size.
Follow the flowrate guidelines in Table 6.2 to obtain the best results. Smaller diameter tips will operate best at the lower end of the flow rate range, and larger diameter tips require higher flow rates to establish a stable spray (see Table 6.1).
Recommended Flow Rate Ranges for Different Tip IDs
SilicaTip™
Tip ID (µm)
5
8
10
15
30
Flow Rate*
(nL/min)
20–200
50–300
100–350
150–500
300–1000
TaperTip™
Tip ID (µm)
20
75
100
-
-
Flow Rate*
(nL/min)
200–500
300–2000
400–3000
-
-
* Approximate range of flow rates over which the tips will generate a stable electrospray plume without sheath gas assistance. Actual performance may differ due to variations in experimental parameters (mobile phase composition, applied voltage, etc.).
Recommended Flow Rate Ranges for Different Coating Styles
Tip Coating
Standard (-CE-) Coated
Distal (-D-) Coated
Uncoated (-N-)
Recommended Flow Rate Range*
10 nL/min. – 250 nL/min.
100 nL/min. – 5 µL/min.
100 nL/min. – 5 µL/min.
* Operable flow rate is a function of tip size.
In-Line filtration
Loss of spray due to clogging by fine particles is the most common cause of tip failure. Installing an in-line filter in the solvent transfer line is highly recommended to minimize this problem, even if using HPLC-grade solvents.
6 T E C h N I Q U E S T O O P T I M I Z E P I C O V I E W
Air bubbles
Air bubbles in an emitter have three different possible origins. The first is a leaky
HPLC fitting. A fitting, even if under high pressure, will leak air into the system if liquid is leaking out. Small leaks, even those in which no liquid is visible, can admit significant quantities of air into the system. Be sure to tighten fittings properly.
The second possible origin of air bubbles is outgassing of the mobile phase. If gasses are forced into the mobile phase at high pressure, air bubbles will form as the mobile phase exists the column. The use of strictly degassed solvents is strongly recommended. If you are connecting a SilicaTip™ or a TaperTip™ to the outlet of a conventional LC column, air bubbles from outgassing can adversely affect the stability of the electrospray, especially at lower flow rates. Using a smaller tip size can also reduce this effect since the increase in back pressure generated by the tapered restriction can significantly reduce bubble formation.
You may end up using a smaller tip than your required flow rate would suggest, but stability will improve.
The third possible cause is outgassing due to electrolysis of mobile phase at the high-voltage electrode. Since the electrode is at a high potential there are always re-dox reactions occurring on its surface. Air bubbles may form at the liquid junction interface in the UTM as a result of electrolysis; the use of higher flow rates, however, tends to minimize the effects of air bubbles. These relatively higher flow rates used with the UTM match well with the flow rate requirements of most LC delivery systems. If air bubbles persist and you believe they are due to electrolysis, the most effective way to completely eliminate the phenomenon is to switch to a pre-column high-voltage contact with the UTM in combination with a PicoFrit column. The even backpressure gradient created by the column will eliminate air bubble formation due to electrolysis. If a post-column set-up must be used, fewer air bubbles are produced when using the CTM equipped with coated PicoTips
®
. The use of distal coated (-D-) PicoTips is recommended due to their immunity to arcing at higher voltages.
6 - 3
6 - 4
6 T E C h N I Q U E S T O O P T I M I Z E P I C O V I E W
Operating Parameters
Parameters that require optimization for stable electrospray are the position of the tip with respect to the heated inlet, the applied voltage, and the flow rate.
Tip Position
The transfer of ions created in the electrospray process is maximized when the flow rate is minimized and when the tip is positioned closest to the mass spectrometer inlet. The optimal gap between the tip and the inlet varies from 0.5 mm to 5 mm. Too close and the tip may arc; too far away and the electric field strength drops to a point where the Taylor cone collapses.
Tuning becomes somewhat difficult at distances less than 0.5 mm due to the large effect on the spray pattern of relatively small changes in voltage. Most tips can be used at distances of 2–5 mm with a minimal loss in ion current (under 10 percent). For the majority of operating conditions, a distance of 1–2 mm appears to be an optimal compromise between sensitivity and ease of tuning.
Applied Voltage
Applied voltage is perhaps the most important parameter for stable, efficient operation. Never use a “turn on” voltage above 500 volts unless stable ESI has been previously established. Direct application of a high voltage (e.g., 2.0 kV) can cause a corona discharge or an arc between the tip and inlet. This can destroy the conductive coating, disrupt the fine structure of the tip, and cause the formation of air bubbles within the tip. Once stable operation has been achieved, however, the voltage can be turned on and off at the same level with no fear of arcing, provided no other operating parameters have changed.
Solvent Flow Rate
The optimal flow rate of solvent delivered by PicoView depends on the tubing inner diameter, the tip size and the applied voltage. A flow rate too low or too high may result in an unstable spray pattern.
Using a flow rate that is too low leads to large fluctuations in the ion current.
Ion current will likely drop to zero periodically, even frequently. To improve the
spray quality, raise the flow rate by 25 percent and look for an improvement in signal and spray stability.
Using a flow rate that is too high is generally not as problematic; ion current will fluctuate but will probably not drop to zero. General chemical noise may increase, and the quality of the mass spectra may be diminished. To minimize the ion current fluctuations, reduce the flow rate by 25 percent and look for improvements in signal stability. Raising the applied voltage can sometimes compensate for a flow rate that is too high, provided the voltage is not above the threshold for corona discharge.
6 T E C h N I Q U E S T O O P T I M I Z E P I C O V I E W
Electric Field Strength and Flow Rate Interdependence
In low-flow ESI, it is important to recognize the interdependence of flow rate and the applied electric field. The optimal value of the flow rate is altered when a parameter is changed that affects the “strength” of the electric field (e.g., the size of the tip, the distance from the tip to the heated capillary inlet, or the applied voltage).
For a given tip size, stable ESI can occur over a wide range of flow rates but only over a narrow range of field strength (100 volts or less). Raising the flow rate requires a higher field strength, and vice versa.
In the static nano-electrospray mode, where there is no external flow source, the system is self-regulating in that the electric field actually dictates its own optimal flow rate.
Voltage Tuning Procedure
1. For a continuous-infusion experiment, prepare a standard sample and load
100–200 µL into a 250 µL syringe. Peptide and protein standards should be prepared at 1 µM in a suitable solvent system, such as 1:1 0.5% acetic acid:methanol. Secure the syringe to the mass spectrometer syringe pump using the syringe holder. Ground the needle with an alligator clip as described in “Grounding to a Syringe Needle or HPLC,” on page 4-10.
2. Lock PicoView to the mass spectrometer using the mounting brackets. Make sure the vacuum LED is illuminated green.
3. Turn on the mass spectrometer by accessing the Tune Plus window, choos-
6 - 5
6 - 6
6 T E C h N I Q U E S T O O P T I M I Z E P I C O V I E W ing Control from the menu bar, and selecting On; alternatively, click the On/
Standby button.
4. In the Tune Plus window, click the API Source button and set the initial ESI
Voltage to 500 volts.
5. In the Tune Plus window, set the solvent flow rate by clicking the Syringe
Pump icon, choosing On next to Flow Control, then typing in the desired flow rate next to the Flow Rate parameter. If the CTM is being used, the flow rate should be set between 50 nL/min and 250 nL/min. If the UTM is employed, the flow rate should be set to a value greater than 100 nL/min. Under
Type, highlight the Hamilton button, and under Volume (µL), type “250.”
Click Apply.
6. You may observe the ESI current in the Tune Plus window on the mass spectrometer. Access the Graph window by clicking the Display Graph View icon. Click the Tune icon, select the Manual tab, and click the ESI Spray
Current button. Click Start.
7. Look on the imaging system monitor to see if solvent is flowing through, forming a droplet at the tip. If it is, increase the voltage in 100-volt increments until ESI current is observed in the Tune Plus window. If solvent is not flowing, try increasing the flow rate setting until a solvent droplet comes into view. If a solvent droplet does not appear, a clog may have formed. If necessary, change tips.
8. If signal is unstable, increase the voltage in 50-volt increments and look for improvements in signal stability.
9. If the ion current does not stabilize, optimal field strength has been exceeded. Lower the voltage 200 volts below the point at which current was first observed, then raise the voltage in 50-volt increments.
10. The flow rate should be adjusted if stable ESI current cannot be achieved.
11. If no signal is observed, turn off the applied voltage and look for droplet formation at the tip to visually verify solvent flow-through. If a clog has formed, change the tip.
Do not be concerned if the applied voltage required to generate an electrospray is greater than that normally required for nano-electrospray methods (e.g., nano-
ESI may only require 600 volts for proper operation, while PicoTip® operation using a 15 µm ID may require 2 kV or more). The applied voltage should still be well below that required for conventional ESI. Voltages above 4 kV are generally considered excessive with most PicoTips. A corona discharge may occur if
the applied voltage is too high, even when the distance between the tip and the heated capillary is large (greater than 5 mm).
6 T E C h N I Q U E S T O O P T I M I Z E P I C O V I E W
Optimizing the Spray
PicoView is ready for use once the tip or column is in position, fluid transfer has been established, and electrical contact has been made. Bringing the system to stable ESI conditions will involve adjusting the solvent flow rate and the ESI spray voltage and using the imaging system to visualize the resulting spray pattern.
Selecting a flow Rate
Using the Coated Tip Module
The CTM is most effective at flow rates below 250 nL/min when used with
SilicaTips and above 500nL/min with TaperTips. The user will need to empirically determine the best flow rate based on specific sample conditions and PicoTip placement. Use the lowest possible flow rate to generate a stable electrospray when low sample volumes and/or extremely dilute samples are analyzed. When the pumping element is a syringe pump, a 10–100 µL syringe is recommended.
To set the flow rate using the syringe pump, open the Tune Plus window and access the syringe pump parameters by choosing Setup from the menu bar. Select either
Syringe Pump or click the Syringe Pump icon. Choose the appropriate syringe from the pull-down menu. Set the flow rate to 0.250 µL/min and click Apply. Once spray is established, decrease the flow rate while adjusting the voltage and tip position, if necessary, until a stable spray is established at the desired flow rate.
Using the Uncoated Tip Module
The UTM is used most effectively at flow rates above 100 nL/min using PicoFrit
® columns at flow rates ranging between 150 and 350 nL/min. The user will need to empirically determine the best flow rate for each specific experimental design.
When using a syringe pump for delivery, a 100–250 µl syringe is recommended.
To set the flow rate using a syringe pump, open the Tune Plus window and access the syringe pump parameters by choosing Setup from the menu bar. Select
6 - 7
6 T E C h N I Q U E S T O O P T I M I Z E P I C O V I E W either Syringe Pump or click the Syringe Pump icon. Choose the appropriate syringe from the pull-down menu. Set the flow rate to approximately 0.350 µL/min and click Apply. Once the spray is established, decrease the flow rate while adjusting the voltage and tip position (if necessary) until a stable spray is established at the desired flow rate.
Using the Imaging System to Optimize the Spray
The superior imaging capabilities of PicoView ® allow the user to fine tune the electrospray and easily optimize the distance/ voltage/flow rate parameters. The figures below depict characteristics of unstable and stable spray patterns.
If the applied voltage is slightly low, an unstable spray will form with droplets forming periodically at the tip. This stream of large droplets normally seen under these conditions is not ideal (Figures 6.1 through 6.4) and will result in poor and unstable ion signal for the mass spectrometer. This spray mode is most commonly seen in gradient chromatography during highly aqueous portions of the gradient. Tuned correctly, the spray will stabilize as the gradient becomes more organic. Typically, the spray should be optimized at 30% organic.
Figure 6.1 850V
Drops stick to tip
Figure 6.2 950V
Droplet stream
Figure 6.3 1150V
Droplet stream and spray
Figure 6.4 1400V
Droplet stream and spray
6 - 8
Figure 6.5 1800V
Perfectly tuned spray
Figure 6.6 1900V
Acceptable spray
Figure 6.7 2200V
Multiple sprays formed
Figure 6.8 2800V
Mulitple sprays formed
When the voltage is correct, a stable fine spray will form, as shown in Figure 6.5, and the best-quality data, given the experimental conditions, will be generated.
If the voltage is too high, multiple jets can form around the tip, as shown in
Figures 6.7 and 6.8. Decrease the voltage until a stable spray is formed.
Throughout an experiment, periodically check the imaging system monitor to confirm that the spray is stable. Clogs can form in the tip during infusion, causing the spray to fail. Changes in the organic composition of the solvent gradient may affect the solvent flow rate during micro-LC applications, and it may become necessary to adjust the position of the tip to maintain an optimal spray. It is generally not necessary to change any of the other parameters.
It may take some time to master electrospray at low flow rates. With careful tuning, PicoView can be used to generate consistent, high-quality data for a variety of chemical and biochemical applications.
6 T E C h N I Q U E S T O O P T I M I Z E P I C O V I E W
6 - 9
6 - 1 0
6 T E C h N I Q U E S T O O P T I M I Z E P I C O V I E W
7 M O U N T I N G I N j E C T I O N VA LV E S
7 Mounting an Injection Valve
PicoView’s optional universal valve mount has been designed to accommodate a variety of valve sizes (6 or 10 port) and from different vendors. A brief set of instructions are listed below showing the mounting of two popular valve styles: the Upchurch manual micro-injection valve and the actuated Valco valve.
Contact New Objective for more information on adding the universal valve mount to you PicoView.
Mounting an Upchurch
®
6-Por t Manual Valve
1. An adaptor backing plate is used to mount the manual Upchurch
®
valve–or similer manual injection valve–to PicoView. It can be found in the accessories kit. To fasten the plate, first place the valve with the port side on the table and the handle pointing away from you. Attach the plate as shown in
Figure 7.1 using the two 8-32 cap screws with an allen wrench.
2. Attach the backing plate with the Upchurch valve to the universal valve mount (refer to Figure 3.1) using the two 6-32 cap screws as shown in Figure
7.2 and 7.3. Make sure the valve ports face the opening in the housing.
Figure 7.1 Upchurch valves require the included backplate be attached prior to mounting
Figure 7.2 Attach the backplate to the mount using two mounting screws
Figure 7.3 Properly mounted Upchurch valve
7 - 1
7 M O U N T I N G I N j E C T I O N VA LV E S
Figure 7.4 Attach the Valco valve directly to the mount using two mounting screws, as shown
Mounting a 10-Por t Automatic Valco
®
Valve
The Valco valves can be attached directly onto the PicoView ® valve mount. The two holes on the valve mount directly match two 8-32 threaded holes on the face of the Valco valve. Using two 8-32 cap screws, fasten the Valco valve to the valve mount as shown in Figure 7.4. Make sure the valve ports face the opening in the housing.
Components and Component Clamps
PicoView
®
has four (4) component clamps that have been designed to hold an injection adapter (included in the accessories kit), columns or unions that may be required in your experiment. The thumb screws in the component clamps will gently hold items in place. Alternately, these clamps can be removed and set aside when they are not needed.
Figure 7.5 Properly mounted Valco valve
Figure 7.6 Component clamps with injection adapter and an IntegraFrit™ trap column
7 - 2
Figure 7.7 Micro injection adapter with mounting nut
7 M O U N T I N G I N j E C T I O N VA LV E S
7 - 3
7 - 4
7 M O U N T I N G I N j E C T I O N VA LV E S
T E C h N I C A L S U P P O R T
Contact New Objective
For Technical Support questions, for your PicoView ® or regarding columns, fittings, valves, etc., please contact the New Objective Customer Solutions Group.
Hours:
Email:
Telephone:
Fax:
Postal Mail:
Monday - Friday, 9 a.m. - 5 p.m. ET
+1 781 933 9560
1 888 220 2998 U.S. Toll Free
+1 781 933 9564
New Objective, Inc.
2 Constitution Way
Woburn, MA 01801-1023 USA
XD-PV550 Rev 2
2 Constitution Way
Woburn, MA 01801-1023
888 220 2998 Sales
781 933 9560 Tel
781 933 9564 Fax www.newobjective.com
advertisement
Related manuals
advertisement