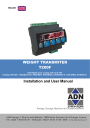
advertisement
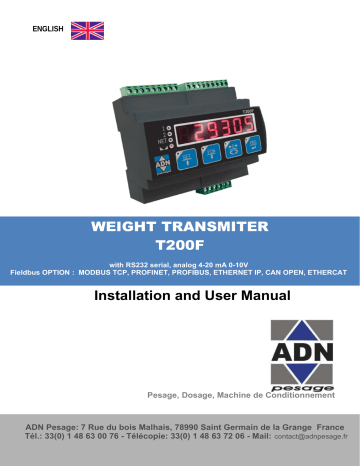
ENGLISH
WEIGHT TRANSMITER
T200F
with RS232 serial, analog 4-20 mA 0-10V
Fieldbus OPTION : MODBUS TCP, PROFINET, PROFIBUS, ETHERNET IP, CAN OPEN, ETHERCAT
Installation and User Manual
Pesage, Dosage, Machine de Conditionnement
ADN Pesage: 7 Rue du bois Malhais, 78990 Saint Germain de la Grange France
Tél.: 33(0) 1 48 63 00 76 - Télécopie: 33(0) 1 48 63 72 06 - Mail: [email protected]
ADN Pesage
TABLE OF CONTENTS
PRECAUTIONS ...........................................................................................…...Page
INTRODUCTION ........................................................................................…….Page
TECHNICAL FEATURES .................................................................................. Page
INSTALLATION ...........................................................................................….. Page
FRONT PANEL OF THE INSTRUMENT ......................................................….. Page 14
USING THE KEYBOARD ................................................................................. Page 15
INFO DISPLAY ............................................................................................… Page 18
2
3
5
6
OPERATING FUNCTIONS ............................................................................. Page 19
SETTING ....................................................................................................…. Page 23
DIAGRAM OF THE MENU .............................................................................. Page 27
CONFIGURATION PARAMETERS ................................................................. Page 28
CALIBRATION.............................................................................................…. Page 28
ANALOG PARAMETERS ................................................................................. Page 33
SERIAL PARAMETERS ...................................................................................... Page 35
INPUT/OUTPUT PARAMETERS ......................................................................... Page 44
WEIGHING PARAMETERS .............................................................................. Page 48
FILTER - SETTING FILTER PARAMETERS ...................................................... Page 50
SETTING FUNCTIONAL FEATURES .................................................................. Page 52
SET DATE AND TIME ...................................................................................... Page 55
UPLOAD/DOWNLOAD FUNCTION ................................................................ Page 56
ACCESS VIEWING ........................................................................................ Page
ALIBI MEMORY .............................................................................................. Page
57
58
SERIAL COMMUNICATION PROTOCOLS ........................................................ Page 59
FIELDBUS PROTOCOL .................................................................................... Page 71
TROUBLESHOOTING ..................................................................................... Page 84
Page 1
Transmetteur de pesage T200F : Manuel d’utilisation et d’installation
PRECAUTIONS
READ this manual BEFORE operating or servicing the instrument.
FOLLOW these instructions carefully.
KEEP this manual for future use.
WARNING
The purpose of this manual is to provide the operator with explanatory text and figures, the requirements and basic criteria for the installation and correct use of the instrument.
The installation, maintenance and repair should only be carried out by specialised personnel who have read and understood this manual. “Specialised personnel” means personnel who, because of their training and professional experience have been expressly authorised by the plant Safety Officer to carry out the installation.
Power the instrument with a voltage whose value is within the limits specified in the specifications.
The user is responsible for ensuring that the installation complies with the provisions in force.
Any attempt to dismantle or modify the instrument which is not expressly authorised will invalidate the warranty and will relieve
ADN Pesage from all liability.
Installation and maintenance of this instrument must be entrustedto qualified personnel only.
Be careful when performing inspections, tests and adjustments with the instrument on.
Perform the electrical connections with the instrument unplugged from the mains
Failure to observe these precautions may be dangerous.
DO NOT allow untrained personnel to work, clean, inspect, repairor alter this instrument.
Page 2
ADN Pesage
INTRODUCTION
The T200F is a weight transmitter to be combined with the load cells to detect the weight in every situation.
The module is easy to install and must be mounted on a 35 mm DIN rail or OMEGA bar. The weight, the status of the instrument, the setting parameters and any errors are all clearly shown on the display.
The 4 capacitive keys below the display permit easy use of these functions: ZERO-SETTING, TARE,
GROSS/NET switching, setting of the weight set-points, configuration, and both theoretical and real calibration.
The T200F uses the RS232 serial port with ASCII protocols, in order to be connected to a PC, PLC and remote units with a maximum distance of 15m, above which you must use the serial port RS422/
RS485 which also allows connection with the MODBUS RTU protocol up 32 addressable instruments.
Availability of the most widespread fieldbuses, as an alternative to port RS485, also makes it possible to interface the transmitter with any supervision device currently offered by the market.
There is also a USB 2.0 port for easy interfacing with the PC via a utility software which can be provided with it.
They are always 2 programmable weight set-points and control of the maximum weight value reached
(peak).
In addition you can have the analog output in current or voltage even with a FIELDBUS.
Available versions:
• T200F: weight transmitter with RS232 serial output, USB, RS485 and peak function. Supported protocols are Modbus RTU, continuous, slave and on demand. Two programmable set points, 2 inputs and Peak function.
• T200F/A: version with the analog output.
• T200F/PROFINET: weight transmitter with RS232 serial output, USB and PROFINET.
• T200F/ETHERNET IP:
• T200F/ETHERCAT:
• T200F/ETHERNET :
• T200F/PROFIBUS: weight transmitter with serial output RS232 and PROFIBUS.
• T200F/CANOPEN : weight transmitter with serial output RS232 and CANOPEN.
Page 3
Transmetteur de pesage T200F : Manuel d’utilisation et d’installation
IDENTIFICATION PLATE OF THE INSTRUMENT
Always cite this data when requesting information or instructions concerning the instrument, as well as the program number and version that are shown on the cover of the manual and on the display when the instrument is switched on.
ADN PESAGE
WARNINGS
The following procedures must be entrusted to qualified personnel.
All connections must be made with the instrument turned off.
Page 4
ADN Pesage
Power supply
Max. absorption
Isolation
Installation category
Operating temperature
Storage temperature
Weight display
Led
Keyboard
Overall dimensions
Assembly
Container material
Connections
Load cells power supply
Input sensitivity
Linearity
Temperature drift
Internal resolution
Displayed weight resolution
Measuring range
Weight acquisition frequency
Digital filter
Weight decimal number
Zero calibration and full scale
Logic outputs
Logic inputs
Serial port (n° 2)
Maximum cable length
Serial protocols
Baud rate
USB port device:
Analogue output (optional)
Analogue output calibration
Linearity
Thermal drift
Microcontroller:
Data storage
Fieldbus (alternative to RS485)
Regulatory Compliance
TECHNICAL FEATURES
12 ÷ 24 Vdc ± 15 %
5 W
Class II
Cat. II
-10°C ÷ +50°C (max humidity 85% without condensate)
-20°C ÷ +70°C
6 digit 7-segment red LEDs (h 14 mm)
4 3mm indicator LEDs
4 capacitive keys
106 mm x 63 mm x 110 mm (l x h x d)
On support for DIN profile or OMEGA bar
Self-extinguishing Noryl (UL 94 V1)
Removable terminal boards pitch 5.08.
5 Vcc/120 mA (max 8 cells x 350Ω in parallel) shortcircuit protected
0.02 μV min.
< 0.01% of full scale
< 0.001% of full scale / C°
24 bit
Up to 999,999 divisions on useful capacity
From –3,9 mV/V to +3,9 mV/V
12 Hz - 1000 Hz
Selectable 0,5 ÷50 Hz (up to 1000 Hz in manual) from 0 to 4 decimal digits
Automatic (theoretical) or executable from the keyboard.
2 optoinsulated (free contact) max 24Vdc / 100 mA ea.
2 optoinsulated 24 Vdc PNP (external power supply)
RS232C and RS422/485
15m (RS232C) and 1000m (RS422 and RS485)
ASCII, Modbus RTU
1200, 2400, 4800, 9600, 19200, 38400, 57600,
115200 selectable complies with USB 2.0; up to 12 Mbps speed optoinsulated 16 Bit
Voltage: 0÷5/10 V (R min10 K Ohm),
Current: 0/4÷20 mA (R max 300 Ohm)
From keyboard
< 0,02% FS
0,001% FS / °C
ARM Cortex M0+ to 32 bit, 256KB Flash reprogrammable on-board by USB.
64 Kbytes expandable up to 1024 Kbytes
PROFINET, ETHERNET IP, ETHERCAT, ETHERNET,
PROFIBUS, CANOPEN
EN61000-6-2, EN61000-6-3 , EN61010-1
EN45501
Page 5
Transmetteur de pesage T200F : Manuel d’utilisation et d’installation
INSTALLATION
GENERAL DATA
The T200F comprises a motherboard, to which various options can be added; the motherboard is housed in a plastic 35mm DIN rail mount enclosure.
The T200F should not be immersed in water, subjected to jets of water, and cleaned orwashed with solvents.
Do not expose to heat or direct sunlight.
Do not install the instrument near power equipment (motors, inverters, contactors, etc.) or anyhow equipment that does not comply with CE standards for electromagnetic compatibility.
The connection cable for the load cells must have a maximum length of 140mt/mm2.
The RS232 serial line must have a maximum length of 15 meters (standard EIA RS-232-C).
The recommendations given for connecting the individual devices must be adhered to.
OVERALL DIMENSIONS
ELECTRICAL INSTALLATION
62
45
106,3
35
90,5
Page 6
The transmitter T200F uses removable screw terminal boards with a pitch of 5.08 mm, for electrical connection. The load cell cable must be shielded and channelled away from power cables to prevent electromagnetic interference.
ADN Pesage
+EXC
-EXC
+SGN
-SGN
SHD
+EXC
-EXC
+SGN
-SGN
SHD
-EXC
+SGN
-SGN
SHD
+EXC
-EXC
+SGN
-SGN
SHD
3
4
5
1
2
+EXC
-EXC
+SGN
-SGN
SHD
3
4
1
2
5
+EXC
-EXC
+SGN
-SGN
SHD
4
5
2
3
-EXC
+SGN
-SGN
SHD
+SGN
-EXC
-SNS
+SNS
+EXC
SHD
5
6
7
2
3
4
3
4
1
2
5
+EXC
-EXC
+SGN
-SGN
SHD
The instrument is powered via terminals 22 and 23. The power cord must be channelled separately from the other cables.
The instrument is in insulation class II (double insulation) and there is no ground terminal provided, which is however necessary to
Make sure you have a valid ground connection.
Power supply voltage: 12÷24 Vcc ±15%, max 5W
LOAD CELL(S) CONNECTIONS
The cable of the cell(s) must be channelled separately, and not with
A maximum of 8 load cells of 350 ohm can be connected to the instrument in parallel. The supply voltage of the cells is 5 Vdc and has temporary short circuit protection.
The measuring range of the instrument permits the use of load cells with a sensitivity of up to 3.9 mV/V.
The cable of the load cells must be connected to terminals 11-18.
In the case of a 4-wire load cell cable, jumper the terminals 11 to
Connect the cell cable shield to terminal 10.
In the case of two or more load cells, use special junctionboxes
(CEM4/C or CSG4/C). The connection of these is shown below.
13
12
10
15
16
11
14
T200F
SIGN-
SIGN+
EXC-
SENSE-
SENSE+
EXC+
SHD
OUT1
OUT2
C OUT
IN1
IN2
C IN
7
8
9
4
5
6
1
2
3 mA+
V+
Ana-
+24V
22
23
+
-
24V
S.GND
RXD
TXD
21
20
19
Page 7
Transmetteur de pesage T200F : Manuel d’utilisation et d’installation
LOGIC INPUTS
The two logic inputs are opto-isolated.
The cable connected to the logic input should not be channelled withthe power cables.
Minimise the length of the connecting cables.
The function of the two inputs is selectable from Set-up:
The two functions are activated by connecting the 24 Vdc external power supply to the relative terminals as shown in the figure.
-
+
INPUT 1
INPUT 2
COM. INPUT
LOGIC OUTPUTS
The two opto-isolated relay outputs are of the type with normally open contacts.
The capacity of each contact is 24 Vdc, 100 mA max. The output connection cable does not have to be channelled with power cables. The connection should be as short as possible.
The environment where the equipment is installed can normally be subject to strong magnetic fields and electrical disturbances caused by the machinery present, therefore it is advisable to adopt the normal precautions in order to prevent them affecting the typical signals of an electronic precision apparatus. (filters on the remote control switches, diodes on the 24 VDC relays, etc.)
SERIAL COMMUNICATION
RS232:
The RS232 serial port is normally used for connections to PCs, printers and repeaters.
To make the serial connection, use a suitable shielded cable, making sure to ground the shield to just one of the two ends.
The cable must not be channelled with power cables; the maximumlength is 15 metres (EIA RS-232-C). In the case of a longer cable, use of the optional RS485 interface is required.
RS485:
The RS485 serial connection is of the 2-wire type, and allows you to connect up to 32 instruments to a single MASTER unit (PC, PLC etc.) by means of a shielded twisted cable, making sure to connect the shield to the ground of one of the two ends.
The cable should not be ducted with power cables.
NOTE: Links 6-7 and 4-9 are made within the instrument
(are used only for compatibility with the cables of the DAT
400.
5
9
4 6 9 7
1
6
RS422/485
N°32 units max
(1000m max)
Page 8
ADN Pesage mA+ (300 Ω max)
V+ (10 kΩ min)
Ana-
SHIELD
The transmitter provides an analogue output in current or voltage.
Analogue output in voltage: range from 0 to 10 Volt or from 0 to 5
Analogue output in current: range from 0 to 20 mA or from 4 to 20
Analog transmission can be sensitive to electromagnetic interference, it is therefore recommended that the cables are as short as possible and that they follow their own route.
To make the connection, use a suitable shielded cable, making sure to connect the shield to the ground in one of the two ends.
Caution: do not connect the analogue output to active devices.
USB DEVICE
( SPECIFICATION 2.0 COMPLIANT; FULL-SPEED 12 MBPS)
Use this communication port to directly interface a PC via a USB port.
Use a standard USB cable for the connection.
To connect the instrument via the USB device, you must install a driver on the PC which is suitable for the operating system used.
For installation please follow the specific instructions.
FIELDBUS CONNECTIONS
As an alternative to the RS485 serial port some of the most common fieldbuses are available. You can use a single fieldbus which must be specified when ordering.
ETHERNET CONNECTION
On the lower left part of the instrument there is a RJ45 connector for Ethernet.
Features:
Trasmission speed 10 Mbps
Network compatible with 10/100/1000 Base-T
TCP Ethernet protocols, Modbus/TCP, UDP, IP, ICMP, ARP
TCP server communication mode
LED indicators (2) Presence of Ethernet and communication/diagnostics line
Buffer size 256 bytes
Connection Time-out Min 30 seconds - Max 90 seconds
Link Time-out (cable disconnected) 30 seconds
Page 9
Transmetteur de pesage T200F : Manuel d’utilisation et d’installation
To connect to the MASTER, use a standard twisted pair Ethernet cable with RJ45 connector.
The RJ45 Ethernet connection cable has a variable maximum length, depending on the type of cable. A common Cat5 shielded cable can have a maximum length of about 180 m.
PIN DESCRIPTION
1 TX+
2
3
TX-
RX+
4
5 • You can connect the Ethernet communication port directly to the
PC, without having to go through other network devices (routers, switches, hubs, LAN-bridge or the like), but special RJ45 cables must be used, called “crossover.”
6
7
8
RX-
• Normally cables are the “direct” type and allow connection to network devices such as routers or hubs, but not direct connection to two PCs (even if there are currently network cards with auto-sensing technology, which recognize the type of cable and the type of connection, allowing direct PC-PC connections as well as using non cross-over cables).
1 2 3 4 5 6 7 8 1 2 3 4 5 6 7 8
• On side are diagrams of the two types of cables mentioned and their connection diagram.
8 6 7 4 5 3 1 2 7 8 5 6 3 4 1 2
ETHERNET / IP CONNECTION
Ethernet / IP is a real-time industrial protocol which is based on the
Ethernet network.
There are two RJ45 connectors to allow connection of multiple instruments in the same network.
Refer to the previous page for connection notes and warnings.
Features:
10 and 100 Mbit operation, Full and Half Duplex
Modbus-TCP server
Up to 128 bytes of I / O fieldbus in every direction.
Page 10
ADN Pesage
PROFINET CONNECTION
The Profinet connector is RJ45, the same as the Ethernet interface.
There are two RJ45 connectors to allow connection of multiple instruments in the same network.
Refer to the previous page for connection notes and warnings.
Features:
PROFINET IO Real Time (RT) communications
Modbus-TCP server
Up to 128 bytes of I/O fieldbus in every direction.
ETHERCAT CONNECTION
EtherCAT is a real-time industrial protocol which is based on the
Ethernet network.
EhterCAT The protocol requires that the RJ45 connectors have the function of IN and OUT.
Putting more DAT1400 instruments in series, the MASTER will be connected to the IN connector of the first DAT1400, whose OUT connector will be connected to the IN connector of the next etc ...
Refer to the previous page for connection notes and warnings.
MAC ADDRESS IN INSTRUMENTS WITH INDUSTRIAL FIELDBUS
ETHERNET.
Instruments which install Hilscher modules with Industrial Ethernet
Protocol (Profinet, EthernetIP, EtherCAT, etc.) have a label under the connectors, as shown.
This label shows the MAC address of the module (red box), the identification number of the module (blue box) and a QR code that contains the MAC address. The latter can be read using a smartphone app for reading QR codes (eg. on Google Play store,
“QR Code Reader”).
Page 11
Transmetteur de pesage T200F : Manuel d’utilisation et d’installation
PROFIBUS DP CONNECTION
Pin
7
8
5
6
3
4
1
2
-
-
Signal
B line
RTS
GND Ground (isolated)
+ 5V Bus Output +5V termination (isolated)
-
A line
-
-RxD/-TxD, level RS485
9 -
Housing Cable shield
-
Description
-
-
+RxD/+TxD, level RS485
Request to send
Internally connected to protective earth according to Profibus specification
For connection to the Profibus Master, use a standard Profibus cable.
The typical impedance of the cable should be between 100 and
130 Ohms (f> 100 kHz). The cable capacity (measured between conductor and conductor) should be less than 60 pF / m and the minimum cable cross section should not be less than 0.22 mm2
In a Profibus-DP network, you can use either cable type A to type B cable, depending on the required performance. The following table summarizes the features of the cable to be used:
Specification
Impedance
Capacity
Resistance
Conductor cross section
Type A Cable from 135 to 165 ohm
(f = 3 – 20 MHz)
< 30 pF/m
< 110 ohm/km
> 0,34 mm 2
Type B Cable from 100 to 300 ohm
(f > 100 kHz)
-
< 60 pF/m
> 0,22 mm 2
The following table shows the maximum length of the wires line with cable type A and type B, function of the different communication speed required:
Baud rate
(kbit/s)
Cable A lenght
(m)
Cable B lenght
(m)
9.6
19.2
187.5
500 1500 3000 6000 12000
1200 1200 1000 400 200 100 100
1200 1200 600 200 -
100
-
For a reliable operation of the Fieldbus, should be used a line termination at both ends.
In the case of multiple T200F instruments, use the line termination at only one instrument.
For configuring the instrument, the GSD file is available (hms_1810.
gsd) that must be installed in the master.
9 6
Page 12
ADN Pesage
6
1
9
5
Pin
2
3
7
Signal
CAN_L
CAN_GND
CAN_H
Description
CAN low bus line
CAN high bus line
CANopen is an higher-layer communication protocols based on a
CAN seria bus system.
For the connection using a cable with a twisted pair differential and common return in accordance with ISO 11898. The length of the bus is limited by the speed of communication chosen according to
Bit Rate
1 Mbit/sec
500 Kbit/sec
250 Kbit/sec
125 Kbit/sec
<=50Kbit/sec
Max. Bus lenght
25 m
100 m
250 m
500 m
1000 m
The CAN line must have the resistance of 120Ω termination.
The reference CAN_GND must be connected to earth at one point of the line.
The cable can not be channeled with power cables.
For the configuration of the card is available ESD file that must be installed in the master.
Page 13
Transmetteur de pesage T200F : Manuel d’utilisation et d’installation
FRONT PANEL OF THE INSTRUMENT
The T200F has a 6-digit lit display, 4 status LEDs and four keys with corresponding LEDs for confirming pressing of the key.
In operating mode, the display shows the weight and the LEDs indicate the status of weight and thesetpoints.
The set-up parameters are easily accessed and modified using the three buttons on the front to select, edit, confirm and save the new settings.
DISPLAY
The 6-digit display normally shows the weight on the scale. According to the various programming procedures, the display is used for programming the parameters to be stored in the memory, i.e. the messages that indicate the type of operation in progress and, therefore, help the Operator to manage and program the instrument.
STAND-BY FUNCTION
The display can take on the stand-by mode, during which time the display brightness is reduced and the keypad is locked. All other functions of the instrument are up and running.
See the paragraph on the activation / deactivation of the stand-by mode.
LED INDICATORS
To the left of the display there are 4 LED indicators:
1 State of the logic output 1 (ON = closed contact OFF = open contact)
2 State of the logic output 2 (ON = closed contact OFF = open contact)
NET The displayed value is the net weight
> < indicates the condition of stable weight.
Next to each button is also a LED that indicates when the button is pressed.
Page 14
ADN Pesage
USING THE KEYPAD
The instrument is programmed and controlled via the capacitive keypad consisting of 4 keys, all with dual function. The selection of one of the two key functions is automatically established by the instruand whereas key is used to exit the menu or go back to the higher level.
You can also use the keyboard by sliding your finger from left to right and back again as with a regular smartphone.
SYMBOL DESCRIPTION
Short press on the single key. The corresponding LED will flash briefly
Long press on a single key. The corresponding LED will flash briefly and then lights up until released.
The red LED at each key signals its activation.
KEY
+ or
FUNCTIONS DURING WEIGHT DISPLAY
Access to the set points value programming menu
Display selection (gross weight, net weight).
(Press and hold) Weight / peak display selection
Resetting the displayed value (gross weight, net weight or peak).
Sending the weight string via the serial line.
(Press and hold) Access to quick set-up menu.
(Press for 3 sec) Access to set-up menu.
(Press for 6 sec) Access to set-up menu.
Page 15
Transmetteur de pesage T200F : Manuel d’utilisation et d’installation
KEY FUNCTION DURING THE PROGRAMMING MENU NAVIGATION
It selects the next menu.
It selects the previous menu.
KEY
It exits the programming menu or returns to the upper level.
It accesses the relative sub-menu or programming or confirms the selected parameter.
FUNCTION DURING SETTING OF THE NUMERICAL VALUES
It increases the value of the selected digit.
It decreases the value of the selected digit.
It selects the most-right digit.
It resets all the digits.
It ends composition and saves the value.
KEY
It exits without saving the changes.
FUNCTION WHILE SETTING SUGGESTED VALUES
It selects the next value.
It selects the previous value.
It confirms and stores the displayed value.
Pressing the key always results in a return to the previous menu.
Page 16
It exits without saving the changes.
ADN Pesage
KEYBOARD LOCKING/UNLOCKING FUNCTIONS
OPERATION
+
+
DESCRIPTION
Keyboard Lock - The keys are disabled until released. The display goes into low power mode. The instrument is locked by simultaneously pressing the ZERO + PRG keys for 5 seconds. By switching the instrument on and off the instrument automatically unlocks.
Keyboard Unlock - By simultaneously pressing the ZERO + PRG keys for
5 seconds, the keys are reactivated and the brightness of the display returns to standard.
EXITING THE CONFIGURATION MENU
Press the key
Keep the key pressed the weight display.
to return to the main menu. Press the key again . “StorE?”is displayed.
until the message “sEtUP” appears. Press the key. to return to
Page 17
Transmetteur de pesage T200F : Manuel d’utilisation et d’installation
INFO DISPLAY
PdAt01
When the instrument is switched ON, a display test is run followed by the identification code and then the version of the software, in that order. These codes are to be cited when requesting assistance
When is not in progress a programming procedure, the display shows the weight measured in kilograms.
Under certain conditions, the following messages are reported:
NOTIFICATION OF ERRORS
In operating mode, the following error codes may appear on the display.
Fixed message
P <picco> rENotE ϩϩϩϩϩϩ
Display of peak value.
Communication with “Optimation” PC utility software.
Overload. The load applied to the load cells exceeds by over 9 divisions the maximum capacity of the weighing system.
O-L
No CAL
No CoN
E-F.buS
Signal that the load cells are absent or outside of the measuring range mV/V.
Flashing message, alternating with the weight measured.
Calibration weight not performed)
Fieldbus network disconnected
Fieldbus interface absent or not working.
Page 18
ADN Pesage
OPERATING FUNCTIONS
Once calibrated, the display shows the current weight whenever it is switched on.
The following are the possible operations that can be carried out from the keyboard when viewing the weight of the instrument.
KEY OPERATION FUNCTION
Display of Gross Weight to Net Weight.
Display of the peak.
Net Weight being displayed: Auto-tare.
Gross Weight being displayed: Semi-Automatic zero.
Transmission of a string from serial (only protocol on-demand)
Set-Point function programming.
+
Or Entry into the Programming Menu
+
+
Keyboard Lock - The keys are disabled until released. The display goes into low power mode. The instrument is locked by simultaneously pressing the ZERO + PRG keys for 5 seconds. By switching the instrument on and off the instrument automatically unlocks.
Keyboard Unlock - By simultaneously pressing the ZERO + PRG keys for 5 seconds, the keys are reactivated and the brightness of the display returns to standard.
GROSS WEIGHT / NET WEIGHT DISPLAY
Press the key to toggle between the gross weight and the net weight and vice versa. The value displayed is signalled by the NET LED (lit: net weight). If the tare is not entered, the net weight is equal to the gross weight.
In the case of negative weight, the minus sign is shown before the digit.
RESETTING THE WEIGHT AND AUTO-TARE
These two functions are performed by the 0 key
Page 19
Transmetteur de pesage T200F : Manuel d’utilisation et d’installation
When the instrument is in the “Net” operating mode (“NET” LED on) the 0 key auto-tare function.
performs the
When the instrument is in the “Gross” operating mode (“NET” LED off) the 0 key gross weight resetting function.
performs the
ZERO SETTING
The reset command of the gross weight is used to correct for small zero shifts of the weighing system during normal operation.
Normally these zero shifts are due to thermal drifts or to residues of material that accumulate on the weighing system over the time.
To run the command, it is necessary for the instrument to be under “Gross” conditions (“NET” LED off) and for the deviation of the weight with respect to the zero of the scale (the one performed with the zero calibration procedure) does not exceed (in positive or negative) the number of divisions set in the
“0 BAND” parameter (within the PARAM menu).
The reset command of the gross weight is not executed if occurs even one of the following conditions:
• Unstable weight (with weight stability control enabled). In this case, the reset command takes effect only if the weight stabilises within 3 seconds or if the the weight stability control is disabled (“MO-
TION “ parameter equal to zero).
• Gross weight greater (in positive or negative) than the number of divisions set in the “0 BAND” parameter, when the auto-zero set-point is not programmed.
The zero obtained with the gross weight resetting operation is retained in memory even after the instrument is turned off.
The gross weight reset operation can be repeated several times, but the number of divisions reset to zero is added from time to time, so when the total exceeds the limit value set in parameter “0 BAND”, zero setting can no longer be executed. In this case, it is necessary to calibrate the Zero.
Any automatic zero parameter setting when switching on (AUTO 0) reduces (or clears, in the case of
“AUTO 0”> “0 BAND”) the range of action of the reset command.
AUTO-TARE
Auto-tare is possible in the following conditions:
• Instrument in “Net” conditions (“NET” LED on)
• Positive gross weight.
• Gross weight not exceeding maximum capacity.
• Stable weight.
• Unstable weight. In this condition 2 cases must be distinguished:
1. The weight stability control is enabled (the “MOTION” parameter (*) must be other than zero): the command executed while the weight is unstable only has an effect if the weight stabilizes within 3 seconds after the command was given.
2. The weight stability control is disabled (the “MOTION” parameter (*) is equal to zero): the executed command takes effect immediately, even with unstable weight.
(*) The operating modes of the “MOTION” parameter are described in the relevant paragraph.
The auto-tare is retained in memory even after the instrument is turned off.
Page 20
ADN Pesage
PEAK FUNCTION
The instrument continuously memorises the peak value of the gross weight.
This function is available only if the peak calculation function is enabled via the corresponding parameter in the set-up menu of the instrument. The peak display is shown by the letter P on the left of the display.
The peak value is detectedat the same frequency of acquisition of the weight (see table on filters). The peak value can also be used for the following functions:
FUNCTION
LOGIC OUTPUTS
SERIAL PORT
ANALOGUE OUPUT
DESCRIPTION
The set-points can be set to have the peak value as a reference. (See the procedure for setting operation of the logic outputs).
Acquisition of the peak value (peak hold) using the CONTIN, AUTO, DE-
MAND, and MODBUS SLAVE protocols.
The analogue ouput value can assume the peak value (peak hold). (See the analogue output configuration procedure).
FREEZING THE ACQUIRED WEIGHT
You can freeze the weight in the face of a variation of the logic inputs, if any of these is set in the
HOLD mode.
TEST FUNCTIONS - RS232 AND RS485
The test consists of sending the string received from its serial line (echo) and the display of the number of strings received and the number of characters received in the last string.
00C= 00
TEST FUNCTIONS - ANALOGUE OUTPUT TEST
Once in the test out function out. An , , the following message will appear:
out 0
out 0 where 0 indicates the output value (in current or voltage based on that selected) expressed as a % of the full scale.
You can change this value from 0 to 100, with an interval of 10%, by pressing the 0 key.
Press the SET key to exit the function.
INPUT / OUTPUT TEST FUNCTIONS
Once in the IN OUT test function, the following the logic inputs mode, as shown in the table:
1n 00
1n 00 will appear where 00 depends on
VALUE MEANING
00
01
10
11
No active input
Input 1 active
Input 2 active
Inputs 1 and 2 active
In the same menu you can enable or disable the outputs by repeatedly pressing the ZERO key.
The status of the two outputs is shown by the first 2 status LEDs.
Press the SET button to exit the function.
Page 21
Transmetteur de pesage T200F : Manuel d’utilisation et d’installation
PROGRAMMING THE WEIGHT SET-POINTS
The set-points are compared with the weight to drive the relative logic output. The comparison criterionis defined during set-up of the logic inputs/outputs (see the relevant section).
To access the Set points setting, press the SET key while viewing the weight
MENU MESSAGE DESCRIPTION TYPE DEFAULT RANGE IND.FIELDBUS
Set-point
SEtP. 1
SEtP. 2
Sets value of Set-point 1
Sets value of Set-point 2
Com.
Com.
0
0
0÷Capacity
0÷Capacity
201(MSB)
202(LSB)
203 (MSB)
204 (LSB)
The set-points are compared with the weight to drive the relative logic output. The comparison criteria is established in the set-point set-up procedure.
When the weight is not detectable or out of range, all the outputs are disabled (contact open or closed depending on the MODE; see the relevant chapter).
During the step of setting the set-points, both outputs are disabled. If the set-point value in the memory is 0, the relative output is never enabled, regardless of the set-up of the selected set-points.
WEIGHT ACQUISITION
The weight can be printed or sent to the serial port / fieldbus (depending on the setting of the communication ports), in the following ways:
• In automatic mode (in the event of selecting the “automatic” serial communication protocol).
• Through the instrument keyboard (pressing the PRG key, in the event of selecting the “on demand” serial communication protocol).
• From the external input (in the event of selecting the “on demand” serial communication protocol and the “data transmission on demand” operation selected on at least one input).
• Through the serial line (in the event of selecting the “slave” serial communication protocol), by sending the weighing execution command.
• Through the fieldbus, using the weighing execution command in the register command.
The following are the conditions for weight acquisition:
• Stable weight (or stabilised within 3 seconds from the command).
• Since the last acquisition carried out, the weight has undergone a change of at least 20 divisions
(weight difference).
• Gross weight equal or greater than the minimum weight (20 divisions) and less than the maximum capacity.
• Net weight not zero.
In METRIC operation, if the alibi memory is configured, the transaction is recorded. The net weight and the weight identification code are also stored in a memory register which can be read on a request from the fieldbus.
Only in FREE operation and print executed by key or ester-no input, the weighing is permitted even with the gross weight less than the minimum weight or with the net weight at zero.
CALIBRATION JUMPER
In the event of metrological use, the enabling to the setting of the metric parameters can be done with the internal bridge towards the board.
Page 22
ADN Pesage
SETTING
GENERAL DATA
All functions of the T200F are activated and modified by accessing a simple setup menu, shown on the next page. All settings that are selected or activated remain in the memory even after the transmitter has been switched off.
The T200F is preconfigured with a default setting. The following pages shows the “Default” values of each parameter.
With the first field installation some parameters have to be changed in order to obtain a correct indication of the displayed weight (Theoretical calibration).
This may be required when you first purchase the T200F.
The settings of the setup menu can be changed using the keys on the front or the “OPTIMATION”utility software provided.
KEY FUNCTION WHILE MAIN MENU PROGRAMMING
It selects the next menu.
It selects the previous menu.
KEY
It exits the programming menu or returns to the upper level.
It accesses the relative sub-menu or programming or confirms the selected parameter.
FUNCTION WHILE SETTING SUGGESTED VALUES
It selects the next value.
It selects the previous value.
It confirms and stores the displayed value.
KEY FUNCTION WHILE SETTING NUMERIC VALUES
It increases the value of the flashing digit.
It decreases the value of the flashing digit.
It goes to the next digit.
It confirms and stores the displayed value.
Page 23
Transmetteur de pesage T200F : Manuel d’utilisation et d’installation
CHANGING AND ENTERING THE PARAMETERS:
The procedure for accessing the menu depends on the operating mode selected: FREE or METRIC.
MENU ACCESS IN FREE OPERATION MODE.
In the event of FREE operation all instrument parameters can be changed by the operator.
MENU ACCESS IN METRIC OPERATION MODE.
In the event of METRIC operation programming of weighing parameters and the weight calibration settings are only permitted to personnel authorised by law, through password-protected access.
For this procedure you need the password table.
1d
0000
Cod..000
0000
To access the menu the operator’s identification code is requested. The “ID” timed message is displayed and then you are prompted to enter the code.
Enter the identification code of the operator who has authorised access, corresponding with the number of the password table and confirm with PRG. If the value 0000 is confirmed or if the procedure is cancelled with the ZERO key access to the menu parameters will be limited (you will not be able to access the programming of the weighing parameters and the calibration settings of the weight).
The display shows a 3 digit number randomly selected. Locate on the table the corresponding password (4 digits) and press PRG to access the password setting.
Enter the password obtained from the table and confirm with the PRG key. If 0000 is confirmed or if the procedure is cancelled with the ZERO key access to the menu parameters will be limited (you will not be able to access the programming of the weighing parameters and the calibration settings of the weight).
Page 24
Each authorised personnel access is recorded in the memory which contains the last 5 accesses.
Turn on the instrument with the bridge for enabling calibration in the CALIBRATION position in order to go directly to the programming menu (when the calibration bridge is on, you cannot exit the programming menu).
1nfo will appear on the display. Use the arrow keys until the menu appears where you want to group the instrument parameters in a number of main menus.
The first to appear is that of 1nfo that allows you to view the information for instrument identification and configuration.
The second menu is that of tEst concerning procedures for functional testing of the instrument.
The third is that of SEtup which allows you to program the parameters which determine the operation of the instrument
ADN Pesage
To access the setup menu, press the PRG key and then the SET key and hold them down simultaneously for 3 seconds or press and hold the PRG key for at least 6 seconds .
Access by confirming your choice with the PRG key.
MESSAGE NAME
1nFo
Information
tEst
Test
SEtuP
Setup
DESCRIPTION
Parameter menu can be viewed for identification of the instrument and its configuration.
Menu of test procedures for operation of the instrument hardware.
Menu of programmable parameters which determine the operation of the instrument
INFO MENU
MENU MESSAGE NAME DESCRIPTION TYPE
Cod. FN
Firmware code Indication of installed Firmware code Vis.
rEL. FN
Firmware revision Indication of revision of the Firmware installed Vis.
F.SCALE
Full scale of the instrument
F. bUS
Fieldbus present
Indicates the full scale set
Indicates the type of Fieldbus configured
Vis.
Vis.
Addr.
Fieldbus address menu item is displayed only in the RS485 configurations.
Vis.
1nFo
1P
SubnEt.
oUt.. An
NENory
Fieldbus IP address menu item is displayed only in the ETHERNET, Vis.
PROFINET and ETHERNET/IP configurations.
Subnet Mask
Fieldbus
Analog Output
Configuration
Optional Memory
Configuration menu item is displayed only in the ETHERNET, Vis.
PROFINET and ETHERNET/IP configurations.
Indicates the presence and type of analogue output (Not present - Unipolar - Bipolar)
Indicates the presence and type of memory
(None - Alibi memory - μSD card)
Vis.
Vis.
In the case of PROFINET field bus: the parameters IP address and Subnet Mask are programmable by PLC and are updated in this menu only when the instrument is switched on. Following a change in these parameters from the PLC, the instrument must be switched off and on again to display the correct value.
It is important to remember that even if you set the parameters IP address and subnet mask in Temporary mode, these parameters are not automatically updated in the instrument. Moreover, when the instrument is switched off and then on again, these parameters will all be set to 0.0.0.0.
Page 25
Transmetteur de pesage T200F : Manuel d’utilisation et d’installation
TEST MENU
MENU MESSAGE
tESt
NAME DESCRIPTION
S1GnAL
H1 rES.
PSuppL.
Cell signal
Resolution x10
Power supply voltage
Display of the signal in mV/V in input to the instrument
Display of the weight with a resolution 10 times greater than that set
Display of the supply voltage measured by the instrument
NENory
1n oUt.
rS 232 rS 485 oUt.. An
Test of the memory
(Only with configured memory)
Automatic operation test of the additional memory
I/O test
Test RS232
Test RS485
Analogue output test
I/O test with simultaneous display of inputs and outputs (See specific description)
Transmission and receipt test (See specific description)
Transmission and receipt test (See specific description)
Test procedure with manual activation of the output value (See specific description)
TYPE
Vis.
Vis.
Vis.
Test.
Test.
Test.
Test.
Test.
SETUP MENU
MENU
SEtuP
SUB MENU NAME
CAL1br.
Calibration Settings (*)
AnALoG
Analog output settings (Only with analog output configured)
CoN.Por..
Serial ports and fieldbus settings
1n-oUt.
Logic Output and Input settings
PArAN
Weighing meteorological parameter settings
F1LtEr
Filter Settings
FUnCt
Functional Features settings
CLock
(**)
uPL.dow
Upload/Download function of saved setup data
accEss
Showing the last 5 accesses of the Authorized Staff (***)
ali.NEN
Aliby memory consultation (***)
(*) These menu items are displayed only when operating in FREE mode or if accessed using the password of authorised personnel (if operating in METRIC mode).
(**) This menu is displayed only in case of hardware with calendar clock.
(***) This menu items are only displayed when operating in METRIC mode.
On exiting the setup menu, if changes were made to the parameters, the message StorE , is displayed which is confirmed with PRG
Page 26
ADN Pesage
DIAGRAM OF THE MENU
Page 27
Transmetteur de pesage T200F : Manuel d’utilisation et d’installation
CONFIGURATION PARAMETERS
All the parameters that can be set are described in the following pages. At the end of each parameter description, where present, the fieldbus address corresponding to the parameter is shown. If the parameter is the selectable type, the value to be entered in the register for the desired selection is shown between “[ ]”.
CALIBRATION MENU
Access to this menu is only allowed when operating in FREE mode or when operating in METRIC with access using the password of authorised personnel.
rESoLU
DIVISION VALUE [1101÷1102]
Value of a single division, expressed in kg. The ratio between the capacity of the system and the division valuerepresents the resolution of the system (number of divisions).
Following the change of the division value, if the maximum capacity is not changed, calibration of the weight is corrected automatically.
Values that can be selected:
0.0001 - 0.0002 - 0.0005
0.001 - 0.002 - 0.005
0.01 - 0.02 - 0.05
0.1 - 0.2 - 0.5
1 -2 - 5
10 - 20 - 50
Default: 1
L.C. CAP.
CAPACITY OF THE LOAD CELLS [1103-1104]
It defines the value corresponding to the sum of the rated capacity values of the load cells expressed in kg. In the case of systems with only one load cell and “N” fixed supports, enter the capacity value of the cell for the total number of supports. This figure represents the full scale value of the weighing system. Following the change of the parameter value, the theoretical weight value is recalculated.
Values: from 1 to 999999
Default: 0
L.C. SEn..
SENSITIVITY OF THE LOAD CELLS [1105]
Set the value corresponding to the average sensitivity of the loadcells, in mV / V. The instrument accepts values between 0.0 and 4 mV / V. If no value if programmed, 2mV/V is set by default.
Following the change of the sensitivity value, the theoretical weight value is recalculated.
Values: from 0.0000 to 4.0000 mV/V
Default: 2.0000
Page 28
ADN Pesage
SySt.FS
CAPACITY OF THE WEIGHING SYSTEM [1301-1302]
Programming the useful capacity (net) of the weighing system.
Values: from 0 to Load Cell Capacity
Default: 0
dEAd L.
FIXED TARE OF WEIGHING SYSTEM [1106-1107]
Programming the fixed tare value of the weighing system
Values: from 0 to Capacity Value
Default: 00000
CAL.tyP
SELECTING THE CALIBRATION TYPE
Selecting the calibration type. On confirmation one of the following procedures is started.
dEAd W
DEAD WEIGHT TYPE CALIBRATION [501÷503]
Zero Calibration and Full Scale up to 5 linearisation points using Sample weights.
tAbLE
TABLE TYPE CALIBRATION [1151÷1172]
Allows you to manually program up to 5 calibration points. The values corresponding to those resulting from the linearisation procedure with sample weights. In this way you can copy the calibration values made with sample weights.
PARAMETERS DISPLAYED ONLY DURING METRIC OPERATION
G-CAL
CALIBRATION LOCATION GRAVITY [1108-1109]
Programming of the force of gravity of the location where the calibration takes place.
Values: from 9.77000 to 9.84000
Default: 0
G-uSE
GRAVITY OF LOCATION OF USE [1110-1111]
Programming of the force of gravity of the location where the instrument will be used.
Values: from 9.77000 to 9.840000
Default: 0
Page 29
Transmetteur de pesage T200F : Manuel d’utilisation et d’installation
CONFIGURATION/CALIBRATION EXAMPLE
Set the parameters listed above to perform theoretical calibration of the Full Scale of the T200F. This procedure must be completed with calibration of the zero-point as described later on. The procedure ensures good precision of the system (maximum error <1% FS) when there are no mechanical problems.
When you change the rESOLU selection, calibration of the full-scale is automatically recalculated. Selections incompatible with the calibration parameters or with the calibration value saved in the memory are not accepted.
A tank must be weighed, of an unladen weight of 750 Kg and capacity 1000 litres, containing a product with specific weight 1.3 Kg/dm3 the weight of which needs to be read with a display resolution 0.2 Kg.
Before proceeding with configuration it is required to ensure the load cells are connected correctly to the unit and the tank is empty, the parameters may then be set.
Use:
3 load cells 1000 Kg capacity
Sensitivity respectively 2.0015, 2.0008 and 1.9998 mV/V (average value = 2.0007 mV/V)
Set the following figures in configuration parameters:
SySt.FS
= 1500
dEAd L.
= 0
rESoLU
= 0.2
Ensure the value read in parameter S1GNAL of the menu TEST corresponds to the tare weight of the system according to the following proportion:
3000:2.0007=750:X
Where X is the value of the signal expressed in mV/V corresponding to the theoretical value of the empty tank weight- The value should be about 0.5 mV/V
At this stage one may proceed with calibration described in the following paragraph or exit the configuration menu saving the data entered.
The instrument should indicate the value corresponding to the unladen tank weight (e.g. 756.8).
It is possible to enter the configuration menu again and enter the value of the weight read in parameter dEad L and enter 756.8
Exit the configuration menu again after saving the data.
For greater precision arrange sample weights or pre-weighed material on a certified scale and proceed with calibration as described in the following paragraph.
Page 30
ADN Pesage
CALIBRATION OF SAMPLE WEIGHTS
The calibration procedure described below should be carried out using sample weights and/or a sample product pre-weighed on a weighing system.
Before proceeding with calibration of the full scale, always perform zero calibration.
During the calibration phase, the weight is shown on the display in alternation with the text CAL.
WARNING: Switching off the instrument without exiting the set-up menu cancels any changes made during the programming process.
N.B. If linearity errors are shown after calibration, verify that theweighed structure is completely free of mechanical constraints.
ZERO CALIBRATION
Perform this operation with the scale unloaded (including the fixedtare), and when the weight is stable.
The zero value of the system is set by pressing the key 0.
The weight displayed is reset and the display shows CAL and 0. in alternation. This operation can be repeated at will.
CALIBRATION OF THE FULL SCALE
Before calibration, put the sample weight on the scale and wait for stabilisation; the display shows a weight value.
To correct the displayed weight press the SET key. All the digits to 0 appears on the display with the the first digit on the left flashing. Using the arrow keys, enter the actual weight loaded on the scale starting with the first flashing digit. Move to the next digit by pressing PRG. Pressing the PRG key to confirm the last digit (far right) corrects the weight. SAVE and then CAL are shown in alternation to the actual weight value entered on the display.
If the set value is higher than the resolution offered by the instrument,the weight is not accepted and an error message appears on the display for a few seconds.
This procedure can be repeated.
Press and hold the PRG key to return to the CaL1br... menu.
LINEARISATION PROCEDURE
Sample weights linearisation: (SET key long press) Up to 5 linearisation points are possible on positive scale. The progression of linearisation points is displayed alternately to the current weight. Press the SET key to set the sample weight value loaded and stabilised. On confirmation you go to the next point. If
0 is set the value is not saved. To end the procedure press and hold the PRG key. It is possible to save a number of points less than 5.
The calibration operations can always be repeated.
When programming the sample weight, values greater than the full scale, or lower than the previous point, or when the weight is not stable, are not accepted. If the entered value is accepted, the next step is shown, otherwise still the same.
The linearisation points are automatically reset by any change of the theoretical calibration data or if a full-scale calibration is performed.
Page 31
Transmetteur de pesage T200F : Manuel d’utilisation et d’installation
TABLE CALIBRATION
It allows you to manually program up to five calibration points, in addition to zero. The values corresponding to those resulting from the linearisation procedure with sample weights. This way you can view the values automatically determined with this procedure or modify and program them in accordance with predetermined values.
BELOW MENUMESSAGGIO NAME DESCRIPTION TYPE
tAbLE
0 S1G.
P1 JAL.
P1 S1G.
P2 JAL.
P2 S1G.
P3 JAL.
P3 S1G.
P4 JAL.
P4 S1G.
P5 JAL.
P5 S1G.
GEt 0
Zero signal
Weight point 1
Signal point 1
Weight point 2
Signal point 2
Weight point 3
Signal point 3
Weight point 4
Signal point 4
Weight point 5
Signal point 5
Acquire the
Zero Signal
Signal value in mV / V corresponding to the zero scale
Weight value corresponding to the 1st calibration point
Signal value in mV/V corresponding to the
1st calibration point
Weight value corresponding to the 2nd calibration point
Com.
Com.
Com.
Com.
Signal value in mV/V corresponding to the
2nd calibration point
Weight value corresponding to the 3rd calibration point
Signal point 4 Signal value in mV/V corresponding to the 4th calibration point
Com.
Com.
Signal value in mV/V corresponding to the
3rd calibration point
Weight point 4 Weight value corresponding to the 4th calibration point
Com.
Com.
Com.
Weight point 5 Weight value corresponding to the 5th calibration point
Com.
Signal point 5 Signal value in mV/V corresponding to the 5th calibration point
Com.
Acquisition function of the signal corresponding to the zero scale expressed in mV/V
The programmed to zero are not considered. The calibration data sheet is automatically cancelled when a new theoretical calibration is carried out or with sample weights.
After the execution of the zero signal acquisition function, using key, the signals in the table are recalculated. At each signal value an offset is added, obtained from the difference between the new acquired zero signal and the old zero signal value.
EXITING THE CALIBRATION MENU
To exit the CAL1b press the menu key , press until the text storE? appears on the display.
Press PRG to save calibration and exit the setup menu.
It is possible to clear the zero and full scale calibrations.
+
Page 32
delete zero calibration.
+
delete the full scale calibration.
ADN Pesage
ANALOG - ANALOG OUTPUT PARAMETERS (OPTIONAL) rAnGE..
ANALOG OUTPUT RANGE [1506]
Select the analogue output range.
Selectable setting:
0÷10 Vdc [0]
0÷5 Vdc [1]
4÷20 mA [2]
0÷20 mA [3]
Default: 0÷10 Vdc
NodE..
ANALOG OUTPUT OPERATION MODE [1505]
Selection of the value to be associated to the analogue output, corresponding to the net weight, gross weight or peak value.
Selectable setting:
NET [0]
GROSS [1]
PEAK [2]
HOLD [3]
Default: NET
An 0..
ANALOG OUTPUT ZERO VALUE [1501-1502]
Analogue value to be subtracted referred to the full scale of the analogue output.
An FS..
FULL SCALE [1503-1504]
It is the weight corresponding to the analog output full scale.
Value settable from 0 to Capacity
Default: Capacity
0 AdJ..
ZERO OFFSET REGULATION
Measure the analogue output value with a multimeter to perform the zero (0) calibration.
Use the keys
Press key
and to regulate the analogue output. Press and hold the key for rapid change.
to go back to the ANALOG menu.
Page 33
Transmetteur de pesage T200F : Manuel d’utilisation et d’installation
FS.AdJ..
FULL SCALE OFFSET REGULATION
Measure the analogue output value with a multimeter to perform the full scale (FS) calibration.
Use the keys and to regulate the analogue output. Hold the key for a quick change.
Press key to go back to the ANALOG menu.
This procedure is available to the user for adjustment, for each selectable range. In the case of a full reset of the setup memory (PC Configurator), they are restored values to the factory calibration.SERIAL
Page 34
ADN Pesage
SERIAL COMMUNICATIONS PARAMETERS
This menu makes it possible to configure the COM1 and COM2 serial ports and the communication parameters. The instrument has two independent serial ports:
COM1 always with interface RS232 ; COM2 can be fitted with either of the following interfaces:
RS485, ETHERCAT, ETHERNET, ETHERNET IP, PROFINET.
C1 Nod..
RS232 OUPUT MODE
Selecting the value transmitted on output RS 232.
Values that can be selected: nEt
GroSS
PEAk
Default: nEt
C1Prot...
COM1 PROTOCOL
It defines how to use the RS232 serial port:
Values that can be selected:
None: Serial communication OFF
Contin: Continuous transmission of the weight string. It can be used, for example, to drive a weight repeater. See details in the relevant section.
on deM: When the Operator presses the relative button on the front or uses Input 2, a weight string is sent. The command is acceptedif the weight is stable. Between two consecutive transmissions, variation of the weight must be at least equal to 20 divisions.
Autom: A weight string is sent automatically when theweight stabilises at a value above the minimum weight (20 divisions).
Slave: ASCII protocol. See details in the relevant section.
Print: When the operator presses the key on the front or by Input, a weight string is transferred. The command is accepted if the weight is stable. Between two successive transmissions, the weight must have a variation of at least 20 divisions.
Default: Slave
Page 35
Transmetteur de pesage T200F : Manuel d’utilisation et d’installation
C1baud.
COM1 BAUD RATE
Defines the baud rate of serial port RS232.
The value must be set at the same value as PC/PLC or remote display.
Values that can be selected:
1200
2400
4800
9600
19200
38400
57600
115200
Default: 9600
C1ForN
COM1 PROTOCOL
Type of frame. For the SLAVE protocol you cannot select 7-bit data format (E-7-1 e O-7-1):
Values that can be selected: n-8-1 n-8-2
E-7-2
E-8-1 o-7-2 o-8-1
Default: n-8-1
Page 36
ADN Pesage
COM 2 PARAMETERS WHEN PRESENT RS485
C2 Nod..
COM2 OUTPUT MODE
Selecting the value transmitted on output RS 485.
Values that can be selected: nEt
GroSS
PEAk
Default: nEt
C2Prot...
COM2 PROTOCOL
It defines how to use the RS485 serial port:
Values that can be selected:
None: Serial communication OFF
Contin: Continuous transmission of the weight string. It can be used, for example, to drive a weight repeater. See details in the relevant section.
on deM: When the operator presses the relevant front key or via Input 2, a weight string is transmitted. The command is accepted if the weight is stable. Between two subsequent transmissions the weight must undergo a variation of 20 divisions.
Autom: A weight string is sent automatically when theweight stabilises at a value above the minimum weight (20 divisions). Variation of the weight between two consecutive transmissions must be at least
20 divisions.
Slave: ASCII protocol. See details in the relevant section.
Modbus: MODBUS RTU Protocol See details in the relevant section.
Default: Slave
C2baud.
COM2 BAUD RATE
Defines the baud rate of serial port RS485.
The value must be set at the same value as PC/PLC or remote display.
Values that can be selected:
1200
2400
4800
9600
19200
38400
57600
115200
Default: 9600
Page 37
Transmetteur de pesage T200F : Manuel d’utilisation et d’installation
C2ForN
COM2 PROTOCOL
Type of frame. For the SLAVE or MODBUS protocol you cannot select 7-bit data format (E-7-1 e O-7-1):
Values that can be selected: n-8-1 n-8-2
E-7-2
E-8-1 o-7-2 o-8-1
Default: n-8-1
C2Addr.
COM2 ADDRESS
Communication address of the serial port:
Values from 1 to 32
Default: 1
Page 38
ADN Pesage
COM 2 PARAMETERS WHEN PROFINET / ETHERCAT IS PRESENT
En.FbuS.
FIELDBUS ENABLING
Enabling PROFINET / ETHERCAT fieldbus, if OFF error messages concerning FIELDBUS communication are never displayed:
Values that can be selected:
OFF
ON
Default: OFF
InP.rEG..
INPUT AREA DIMENSION
Input area dimension for fieldbus (value expressed in Bytes).
Values that can be selected:
32, 64, 96, 128
Default: 128
oUt.rEG..
OUTPUT AREA DIMENSION
Output area dimension for fieldbus (value expressed in Bytes).
Values that can be selected:
32, 64, 96, 128
Default: 128
In case of PROFINET fieldbus, the XML configuration file “GSDML-V2.3-HILSCHER-NIC 50-RE PNS 32-
20160122.xml” is provided. The size of the input and output areas set in the PLC (possible selections:
32, 64, 96 or 128 bytes) must correspond to the size of the input and output areas selected in the instrument (parameters “INP.REG.” and “OUT .REG.“).
The instruments are supplied with the parameter “Profinet Name” not configured and IP address set at 0.0.0.0.
In case of ETHERCAT fieldbus: the devices will be connected with ring type (according to EtherCAT specification), refer to the installation manual for the use of INPUT and OUTPUT ports.
4 different XML configuration fileare provided:
“Hilscher NIC 50-RE V2.2 ECS Byte.xml 32” (32 bytes Input Area, 32 bytes of Output area).
“Hilscher NIC 50-RE V2.2 ECS 64 Byte.xml” (64 bytes Input Area, 64 bytes of Output area).
“Hilscher NIC 50-RE V2.2 ECS Byte.xml 96” (96 bytes Input Area, 96 bytes of Output area).
“Hilscher NIC 50-RE V2.2 ECS 128 Byte.xml” (128 bytes Input Area, 128 bytes of Output area).
In the PLC must be imported the file that matches the size of the input and output areas selected in the instrument (for example, if the instrument is set to InP.rEG.=128 and oUt.rEG.=128, the PLC has to be imported file “Hilscher NIC 50-RE V2.2 ECS 128 Byte.xml”). It could be import multiple files with different size, but in this case you can not run the automatic search function and configuration of the devices on the network.
Page 39
Transmetteur de pesage T200F : Manuel d’utilisation et d’installation
PARAMETERS COM 2 WHEN ETHERNET IP IS PRESENT
En.FbuS.
FIELDBUS ENABLING
Enabling ETHERNET IP fieldbus, if OFF error messages concerning Fieldbus communication are never displayed:
Values that can be selected:
OFF
ON
Default: OFF
1P
IP ADDRESS
ETHERNET IP protocol address
Values from 0.0.0.0 to 255.255.255.255
Default: 0.0.0.0
SubnEt
SUBNET MASK
ETHERNET IP protocol Subnet Mask.
Values from 0.0.0.0 to 255.255.255.255
Default: 0.0.0.0
InP.rEG..
INPUT AREA DIMENSION
Input area dimension for fieldbus (value expressed in Bytes).
Values that can be selected:
32, 64, 96, 128
Default: 128
oUt.rEG..
OUTPUT AREA DIMENSION
Output area dimension for fieldbus (value expressed in Bytes).
Values that can be selected:
32, 64, 96, 128
Default: 128
In the case of IP ETHERNET fieldbus, the EDS configuration file “HILSCHER NIC 50-RE EIS V1.1.EDS” is provided. The size of the input and output areas set in the PLC (possible selections: 32, 64, 96 or 128 bytes) must correspond to the size of the input and output areas selected in the instrument (parameters
“INP.REG.” and “OUT .REG.“).
Page 40
ADN Pesage
COM 2 PARAMETERS WHEN ETHERNET IS PRESENT
1P
IP ADDRESS
ETHERNET protocol IP address
Values from 0.0.0.0 to 255.255.255.255
Default: 192.168.0.201
SubnEt
SUBNET MASK
ETHERNET protocol Subnet Mask.
Values from 0.0.0.0 to 255.255.255.255
Default: 255.255.255.0
GatE
GATEWAY
ETHERNET protocol gateway.
Values from 0.0.0.0 to 255.255.255.255
Default: 192.168.0.1
Port
PORT
Communication port for ETHERNET protocol.
Values from 1 to 65535
Default: 1800
Eth.Pro..
ETHERNET COMMUNICATION PROTOCOL
Selecting communication type for Ethernet protocol.
Values that can be selected:
None: Serial communication OFF
Contin: Continuous transmission of the weight string. It can be used, for example, to drive a weight repeater. See details in the relevant section.
on deM: When the Operator presses the relative button on the front or uses Input 2, a weight string is sent. The command is acceptedif the weight is stable. Between two consecutive transmissions, variation of the weight must be at least equal to 20 divisions.
Autom: A weight string is sent automatically when theweight stabilises at a value above the minimum weight (20 divisions).
Slave: ASCII protocol. See details in the relevant section.
Modbus: Modbus TCP protocol.
Default: Slave
Page 41
Transmetteur de pesage T200F : Manuel d’utilisation et d’installation
COM 2 PARAMETERS WHEN PROFIBUS DP IS PRESENT
En.FbuS.
FIELDBUS ENABLING
Enabling PROFIBUS DP fieldbus, if OFF error messages concerning Fieldbus communication are never displayed:
Values that can be selected:
OFF
ON
Default: OFF
Addr.Pr
PROFIBUS ADDRESS
Programming the address used in the PROFIBUS protocol.
Values: from 0 to 126
Default: 01
InP.rEG..
INPUT AREA DIMENSION
Input area dimension for fieldbus (value expressed in Bytes).
Values that can be selected:
32, 64, 96, 128
Default: 128
oUt.rEG..
OUTPUT AREA DIMENSION
Output area dimension for fieldbus (value expressed in Bytes).
Values that can be selected:
32, 64, 96, 128
Default: 128
In the case of PROFIBUS fieldbus, the GSD configuration file “hms_1810.gsd” is provided. The size of the input and output areas set in the PLC (possible selections: 32, 64, 96 or 128 bytes) must correspond to the size of the input and output areas selected in the instrument (parameters “INP.REG.” and “OUT
.REG.“).
Page 42
ADN Pesage
COM 2 PARAMETERS WHEN CANOPEN IS PRESENT
En.FbuS.
FIELDBUS ENABLING
Enabling CANOPEN fieldbus, if OFF error messages concerning Fieldbus communication are never displayed:
Values that can be selected:
OFF
ON
Default: OFF
Addr.Co
CANOPEN ADDRESS
Programming the address used in the CANOPEN protocol.
Values: from 0 to 126
Default: 1
Baud.Co..
CANOPEN BAUD RATE
Defines the baud rate of the Canopen protocol.
The value must be set to the same value as the PC / PLC.
Values that can be selected (expressed in Kbit/sec.):
10
20
50
125
250
500
1000
Default: 20
Page 43
Transmetteur de pesage T200F : Manuel d’utilisation et d’installation
INPUT/OUTPUT PARAMETERS
FUn.1n.1
INPUT 1 FUNCTION
Selecting the function associated with input 1. [1401]
Values that can be selected:
Zero: It calibrates to zero. [0]
Tare: It executes the automatic tare. [1]
Del.Tar: It cancels the tare. [2]
Peak: Reset of the peal function. [3]
Hold: Holds Acquired Weight. [4]
Send: Data transmission on demand. [5]
Log: Activates the datalogger function. [6]
Default: Zero
FUn.1n.2
INPUT 2 FUNCTION
Selecting the function associated with input 2. [1402]
Values that can be selected:
Zero: It calibrates to zero. [0]
Tare: It executes the automatic tare. [1]
Del.Tar: It cancels the tare. [2]
Peak: Reset of the peal function. [3]
Hold: Holds Acquired Weight. [4]
Send: Data transmission on demand. [5]
Log: Activates the datalogger function. [6]
Default: Zero
NodE 1
SET-POINT 1 OPERATING MODE
Select in sequence 4 operating criteria of set-point 1: [1403]
Comparison with net weight, with gross weight or with peak. In the latter case the comparison is carried out with the last acquired peak value, even when the peak function is not active.
NET The relay output is active in Net Weight mode. [0]
GROSS The relay output is active in Gross Weight mode. [1]
PEAK The relay output is active in Peak mode. [2]
PROCESS The relay output is active when the instrument is working normally. [3]
Default: GROSS
Page 44
ADN Pesage
Selecting the output status if normally open or closed: [1404] n. oPEn. Relay 1 is normally open. [0] n.CLoSE Relay 1 is normally closed. [1]
Defaul: n. oPEn.
Select if positive or negative values have to be compared. [1405]
PoSIt.. The output is operative with positive weight. [0] nEGAt. The output is operative with negative weight. [1]
ALL: The output is operative both with positive and negative weight. [2]
Default: PoSIt
Select whether only stable weight values are to be compared or also unstable: [1406] norMAL Output 1 is active with unstable weight. [0]
StAbLE The output is active with stable weight. [1]
Default: norMAL
HySt. 1
SET-POINT 1 HYSTERESIS [1407]
Hysteresis value with respect to the set-point
Value: from 0 to Capacity
Default: 2
t1NEr1
SET-POINT 1 TIMING [1408]
Value of time, in tenths of a second, during which, when the weight value set is exceeded, the output associated with set-point 1 remains enabled.
After this time, even if the weight value is still above the set-point, theoutput is automatically disabled.
The function is not active with programmed time equal to zero.
Values: from 000 to 999
Default: 0
dELAy1
SET-POINT 1 DELAY [1409]
Value of time, in tenths of a second, after which, when the set weight value is exceeded, the output associated with set-point 1 is enabled.
The function is not active with programmed time equal to zero
Values: from 000 to 999
Default: 0
Page 45
Transmetteur de pesage T200F : Manuel d’utilisation et d’installation
NodE 2
SET-POINT 2 OPERATING MODE
Select in sequence 4 operating criteria of set-point 2: [1410]
Comparison with net weight, with gross weight or with peak. In the latter case the comparison is carried out with the last acquired peak value, even when the peak function is not active.
NET The relay output is active in Net Weight mode. [0]
GROSS The relay output is active in Gross Weight mode. [1]
PEAK The relay output is active in Peak mode. [2]
PROCESS The relay output is active when the instrument is working normally. [3]
Default: GROSS
Selecting the output status if normally open or closed: [1411] n. oPEn. Relay 2 is normally open. [0] n.CLoSE Relay 2 is normally closed. [1]
Defaul: n. oPEn.
Select if positive or negative values have to be compared. [1412]
PoSIt.. The output is operative with positive weight. [0] nEGAt. The output is operative with negative weight. [1]
ALL: The output is operative both with positive and negative weight. [2]
Default: PoSIt
Select whether only stable weight values are to be compared or also unstable: [1413] norMAL Output 2 is active with unstable weight. [0]
StAbLE Output 2 is active with stable weight. [1]
Default: norMAL
HySt. 2
SET-POINT 2 HYSTERESIS [1414]
Hysteresis value with respect to the set-point
Value: from 0 to Capacity
Default: 2
t1NEr2
SET-POINT 2 TIMING [1415]
Value of time, in tenths of a second, during which, when the weight value set is exceeded, the output associated with set-point 2 remains enabled.
After this time, even if the weight value is still above the set-point, theoutput is automatically disabled.
The function is not active with programmed time equal to zero.
Values: from 000 to 999
Default: 0
Page 46
ADN Pesage
dELAy2
SET-POINT 2 DELAY [1416]
Value of time, in tenths of a second, after which, when the set weight value is exceeded, the output associated with set-point 2 is enabled.
The function is not active with programmed time equal to zero
Values: from 000 to 999
Default: 0
Page 47
Transmetteur de pesage T200F : Manuel d’utilisation et d’installation
WEIGHING PARAMETERS
The parameters in this menu permit adjustment of the times for acquisition and updating of the display and manual or automatic resetting by the transmitter.
uSE
INSTRUMENT OPERATION
Selecting the operation of the instrument. In case of a change from FREE operation to METRIC operation, to confirm the setting authentication is required through the password of authorised personnel.
Value Variation
Free
Trade
Default: Free
Free operation. [0]
METRIC instrument operation. [1]
Not1on
STABILITY OF WEIGHT [1303]
This parameter defines the number of divisions needed to consider the weight stable.
A high number of divisions allows the transmitter to quickly detect stability of the weight, which is needed when executing tare and print commands.
Value
0
1
2
3
4
Default: 2
Variation
Weight always stable
Stability determined quickly
Stability determined with medium parameters
Stability determined accurately
Stability determined with the highest accuracy
AUto-0
AUTOZERO WHEN SWITCHING ON [1304-1305]
This parameter defines the value of maximum weight that can be reset when the instrument is switched on.
This operation corresponds to zero calibration of the system andis executed only if the weight is stable and below the set value.
Value: from 0 to Capacity.
Default: 0
Page 48
ADN Pesage
0-trAC
ZERO TRACKING [1306]
This function allows you to perform temporary zero calibration compensating for the temperature drift of the weight.
Switching off the transmitter automatically restores the previous zero calibration.
The maximum weight that can be reset by this parameter is 2% of the capacity of the system.
To disable this function, set the value 0.
Value
0
1
2
3
4
Default: 0
Variation
Control excluded
0.5 div/sec
1 div/sec
2 div/sec
3 div/sec
0-bAnd
ZERO BAND [1307]
This parameter defines the number of divisions that can be reset by pressing the zero button on the front or the associated Input.
Values: from 0 to 200.
Default: 100
Page 49
Transmetteur de pesage T200F : Manuel d’utilisation et d’installation
FILTER - SETTING FILTER PARAMETERS d1G.bAn.
WEIGHT FILTER VALUE [1201]
This parameter adjusts not only the refresh rate of the display, but specially the serial and analogue output. The maximum refresh rate of the display is limited to 25 Hz
High filter values speed up the weight update.
Low values of the filter slow down the weight update.
Factor
(Hz)
Settling
Time
(mS)
ADC Freq
(Hz)
N readings
Monotony
Time (mS)
Oscillation time (mS)
Oscillation range (div)
MANUAL [0]
50 [1]
25 [2]
10 [3]
5 [4]
2 [5]
1,25 [6]
1 [7]
0,7 [8]
0,5 [9]
20
40
100
200
500
800
1000
1500
2000
Selectable
250
100
50
50
50
12,5
12,5
12,5
12,5
25
10
12
19
25
Settable
5
5
5
10
Settable
20
40
80
100
250
300
400
500
600
Settable
4000
3000
2500
2000
1500
1500
1500
1200
1000
Settable
10
12
16
20
25
25
25
30
30
Default: 2 Hz
The following parameters are visible and therefore can be set, only if the parameter selection is MANUAL.
C. rAtE.
ADC SPEED [1202]
With this parameter, the frequency of weight acquisition is adjusted. If the parameter changes to values higher than 12.5 Hz, the weight must be stable. In case of instability the instrument will immediately indicate an error message.
Selectable Values:
12,5 [0]
50 [1]
100 [2]
250 [3]
1000 [4]
AJErAG.
NUMBER OF READINGS ON AVERAGE [1203]
With this parameter you set the number of readings that the filter will use to establish the average weight value.
Values: from 0 to 50.
Page 50
ADN Pesage
Nonot.
MONOTONY TIME [1204
Parameter used to stabilize the weight when continuous variation of the last digit is detected. Normally used in case of resolution of the weight exceeding 10,000 divisions or with low sensitivity of the input signal. Value expressed in mS.
Values: from 0 to 999.
t.oSC1L..
OSCILLATIONS TIME [1205]
Parameter used in conjunction with oscillation Range to reduce the lens weight changes and repetitive typical in lifting systems. Enter the value of the oscillation time expressed in mS.
Values: from 0 to 999.
r.oSC1L.
OSCILLATIONS RANGE [1206]
As for the parameter Oscillation time, used to reduce the oscillations. Enter the value of the oscillation expressed in weight divisions.
Values: from 0 to 99.
Page 51
Transmetteur de pesage T200F : Manuel d’utilisation et d’installation
SETTING FUNCTIONAL FEATURES
Std. by.
STAND BY [1001]
Idle time beyond which the instrument automatically assumes a low brightness status and keypad lock.
0 = deactivated function.
Values: from 0 to 999.
Default: 0
LoCk.
KEYPAD LOCK [1002]
Set of 4 binary values that correspond to the 4 keys.
0 —> key not locked
1—> key locked
(e.g. 0101 corresponds to locking the 2nd and 4th key).
Values from 0000 to 1111.
Default: 0000
P1n.Cod..
PASSWORD SETTING [1003]
If programmed, to access the programming menu you must enter the password. In the event of subsequent accesses it is no longer necessary to type the password until the stand-by intervenes or the instrument is powered off.
Values from 0 to 9999.
Default: 0000 (no Pasword)
PEAk.
PEAK FUNCTION [1004]
Allows the peak function to be available or not and refers it to the net or gross weight.
If the application does not provide this feature you can disable it.
Selectable setting:
NONE [0]
NET [1]
GROSS [2]
Default: NONE
Page 52
ADN Pesage
DISPLAYED PARAMETERS ONLY IF OPTIONAL MEMORY INSTALLED
dAt.LoG.
DATALOGGER [1005]
Allows you to save the weight and I/O status in the optional memory in Excel format. The logging can be a single measurement or a continuous series of measurements from the start of storage (max 1000 measurements). The memory can contain a maximum of 60000 records, after which the oldest records are overwritten.
Selectable setting:
NONE [0]
SINGLE [1]
CONTIN. [2]
Default: NONE
LoG.trG.
TRIGGER DATALOGGER [1006]
If the datalogger is enabled, select whether storage is done manually (by button or input), or on activation of output 1 or 2. To start storing by key, press and hold the SET button. Storage can be interrupted at any time by pressing the ZERO key.
Selectable setting:
MANUAL [0]
OUT1 [1]
OUT2 [2]
Default: MANUAL
LoG.FrQ.
DATALOGGER FREQUENCY [1007]
If the datalogger is enabled, select the storage frequency of data (datalogger). The maximum frequency corresponds to that of weight acquisition (maximum frequency 250 Hz).
Selectable setting:
10 MIN. [0]
5 MIN. [1]
1 MIN. [2]
10 SEC. [3]
5 SEC. [4]
2 SEC. [5]
1 HZ [6]
5 HZ [7]
10 HZ [8]
HIGH [9]
Default: 10 MIN.
Page 53
Transmetteur de pesage T200F : Manuel d’utilisation et d’installation
LoGdnL.
DOWNLOAD LOG
Log download function, the records are transmitted through the USB key of the instrument. This function can be interrupted at any time by pressing the ZERO key.
At the end of the transmission you are prompted to delete the log, confirm by pressing PRG or cancel by pressing the ZERO weight key.
LoGErS.
LOG DELETION
Log delete function, confirm with the PRG key or cancel with the ZERO key.
NOTE: In the download function of the log the records are transmitted in the followings format
(starting from the oldest record):
<Tempo>; <Gross>; <Net>; <Peak>; <Inputs>; <Outputs> CR LF
Or in case of Date and Time option
<Date> ; <Time> ; <Lordo> ; <Netto> ; <Picco> ; <Ingressi> ; <Uscite> CR LF
Where:
Tempo: field consists of six ASCII characters with the value of the recording time justified to the right
(value in seconds from 0 to 999999, without insignificant zeros) If the LOG function is configured to store a single record at a time, this field is always 0.
Date: field consists of eight ASCII characters with the value of the recording date, in the format “dd/ mm/yy”.
Time: field consists of eight ASCII characters with the value of the recording time, in the format
“hh:mm:ss”.
Gross Net Peak: fields consisting of 8 ASCII characters with the weight value justified to the right
(without insignificant zeroes, with decimal points and negative signs).
Inputs: two ASCII characters, “0” (30h, input disabled) or “1” (31h, input enabled). Which indicate the status of input 1 and the status of input 2.
Outputs: two ASCII characters, ‘’0’’ (30h, ouput disabled) or ‘’1’’ (31h, output enabled). Which indicate the status of output 1 and the status of output 2.
Page 54
ADN Pesage
SET DATE AND TIME
This menu is shown only with clock hardware installed.
dAtE
SET DATE
Parameter for the adjustment of the current date
Format of selectable value: dd.mm.yy dd from 01 to 31 mm from 01 to 12 yy from 00 to 99
Default: actual date
t1NE
SET TIME
Parameter for the adjustment of the current time
Format of selectable value: hh:mm hh from 00 to 23 mm from 00 to 59
Default: actual time
Page 55
Transmetteur de pesage T200F : Manuel d’utilisation et d’installation
UPLOAD/DOWNLOAD FUNCTION
The TESTER 1008 must be connected to the serial COM1 (RS232) of the instrument.
This feature allows you to download or upload the setup configuration and calibration data stored in the instrument.
• Download function: The instrument setup parameters are stored in a file.
• Upload function: the instrument is configured with the setup parameters read from a file.
To use these functions it is necessary to activate the procedure ( “receive” files or “transmit file”) in
1008 TESTER instrument.
Page 56
ADN Pesage
ACCESS VIEWING
This menu only appears in case of METRIC functioning.
SUB MENU MESSAGGE NAME
ACCEss
ACC-01
Access 01
ACC-02
Access 02
ACC-03
Access 03
ACC-04
Access 04
ACC-05
Access 05
DESCRIZIPTION
Procedure for wiewing last access of authorized personnel.
Procedure for wiewing last but one access of authorized personnel.
Procedure for wiewing last but two access of authorized personnel.
Procedure for wiewing last but three access of authorized personnel.
Procedure for wiewing last but four access of authorized personnel.
TYPE
Spc
Spc
Spc
Spc
Spc
PROCEDURE FOR ACCES VIEWING
Press PRG to enter: you will see the operator code used to access the programming of the instrument and the sequential number of accesses as indicated below:
1d.0000
The display shows the ID code used for access (the password table). In the case where access is made through calibration jumper, it displays the identification code 0000.
Press the PRG key to continue with the visualization of the progressive access number.
Pr.0000
The display shows the sequence number of access (this value is incremented at each access and is never reset). Press the PRG key to exit the access viewing procedure.
Page 57
Transmetteur de pesage T200F : Manuel d’utilisation et d’installation
ALIBI MEMORY CONSULTATION
This menu only appears in case of METRIC functioning.
SUB MENU MESSAGGE NAME
ALi.NEN
SEE.NEN.
Aliby memory consultation
DESCRIZIPTION
Procedure for consulting weigh stored in aliby memory.
TYPE RANGE
Spc 0÷959999
In case of METRIC functioning and with aliby memory enabled:
• Each executed weigh is stored in the aliby memory.
• For each weighing it is associated an identification code, with value range from 0 to 959999
• The identification code of the weighing is transmitted to the serial port at the time of weighing.
ALIBI MEMORY CONSULTATION PROCEDURE
000000
Enter the ID code of the weighing and confirm with the PRG key.
0.000
The display shows the weight associated with the required identification code. Press the ZERO key to exit the consultation procedure of the alibi memory.
no Cod.
If the required identification code is not present in the alibi memory, a timed message “NO CODE” is showed.
Page 58
ADN Pesage
SERIAL COMMUNICATION PROTOCOLS
CONTINUOUS, AUTOMATIC AND MANUAL ASCII PROTOCOLS
The continuous transmission is carried out at the refresh rate of the weight, consistent with the serial transmission baud rate. In case of communication on the ethernet port, the continuous transmission frequency is limited to 12.5 Hz.
In case of FREE mode, the string is transmitted with Continuous, On Demand and Automatic protocols:
STX <status> <weight> ETX <chksum> EOT
In case of METRIC mode, the string is transmitted with On Demand and Automatic protocols:
STX <status> <weight> Weighing ID ETX <chksum> EOT
Where:
STX (start of text) = 0x02h
ETX (end of text) = 0x03h
EOT (end of transmission) = 0x04.
<status> = character encoded as per the following table (bit = 1 if condition TRUE):
Bit 7
0
Bit 6
0
Bit 5
1
Bit 4
1
Bit 3
Tare
Entered
Bit 2
Zero band
Bit 1
Stable weight
Bit 0
Centre zero
<weight> = field consisting of 8 ASCII characters with the weight value justified to the right (without insignificant zeroes, with decimal points and negative signs).
The weight value transmitted may be the net weight, the gross weight or the peak value, depending on the transmitted data selected (parameter MODE) in the configuration menu of the serial communication ports (see related paragraph).
In conditions of overweight the field assumes the value: “^^^^^^^^”.
In conditions of underweight greater than 999999, the field assumes the value: “_ _ _ _ _ _ _ _”.
In conditions of weight reading error the field assumes the value: “ O-L ”.
<weighing ID> = field consisting of seven ASCII characters with the identifier code of the weight justified to the right (without insignificant zeros).
<chksum> = checksum of the string data. It is calculated by performing the exclusive OR (XOR) of all the characters between STX (or from <Addr>) and ETX, with the exclusion of the latter two; the result of the XOR is broken up into 2 characters considering the upper 4 bits (first character) and the lower
4 bits (second character) separately; the2 characters obtained are then ASCII encoded;
(example: XOR = 5Dh; <csum> = “5Dh” i.e. 35h and 44h).
In the case of automatic and manual communication protocols, between 2 successive transmissions the weight must have a variation of at least 20 divisions.
Page 59
Transmetteur de pesage T200F : Manuel d’utilisation et d’installation
SLAVE TRANSMISSION PROTOCOL
LIST OF THE CONTROLS AVAILABLE:
1. Request for the net and gross weight and current peak.
2. Execution weghing command
3. Autotare command
4. Zero command
5. Peak reset command
6. Programming two weight setpoints
7. Requesting the programmed setpoints.
8. Logic output activation
9. Request Input status
10. Command of setpoints storage in permanent memory.
11. Change in net weight.
12. Change in gross weight.
13. DeleteTare command.
14. Request for Net weight.
15. Request for Gross weight.
The unit connected to the instrument (typically a personal computer) acts as a MASTER and is the only unit that can start a process of communication.
The process of communication must be made by the transmission of a string by the MASTER, followed by a reply from the SLAVE concerned.
CONTROLS FORMAT DESCRIPTION:
The double quotes enclose constant characters (observe upper and lower case); the < and > symbols contain variable numeric fields. The <addr> is the instrument identification. In case of communication on the RS485 port, is obtained by adding 80h to the instrument’s address value (for example with address 3 <addr> = 80h + 03h = 83h). In case of communication on the RS232 port, the <addr> must always be equal to 81h, or, in case of communication on the Ethernet port, the <addr> must always be equal to FFh
1.REQUEST FOR THE NET AND GROSS WEIGHT AND CURRENT PEAK
Master: <Addr> “N” EOT
DAT 400: “N” <Addr> <status> <net> <gross> <peak> ETX <chksum> EOT
2 EXECUTION WEIGHIN COMMAND
This command is only available in case of METRIC operation. The possible use conditions are:
• Stable weight.
• Since the last executed weigh, the weight has undergone a change of at least 20 divisions (delta weight).
• Gross weight equal to or greater than the minimum weight (minimum of 20 divisions) and less than the maximum capacity.
• Net weight not null. Between two successive requests, the weight must have a variation of 20 divisions; if the weight is unstable the command is not executed.
Page 60
ADN Pesage
Master: <Addr> “P” EOT
T200F: <Addr> “P” <status> <weight> <ID weight> ETX <chksum> EOT or <Addr> NAK EOT
3 AUTO-TARE COMMAND
Master: <Addr> “A” EOT
T200F: <Addr> “A” ACK EOT or <Addr> NAK EOT
4. SEMI-AUTOMATIC ZERO COMMAND
Master: <Addr> “Z” EOT
T200F: <Addr> “Z” ACK EOT or <Addr> NAK EOT
5. PEAK VALUE RESET COMMAND
Master: <Addr> “X” EOT
T200F: <Addr> “X” ACK EOT or <Addr> NAK EOT
6. PROGRAMMING TWO WEIGHT SET-POINTS
Master: <Addr> “S” <s1> <s2> ETX <csum> EOT
T200F: <Addr> “S” ACK EOT or <Addr> NAK EOT
7. REQUESTING PROGRAMMED SET-POINTS
Master: <Addr> “R” EOT
T200F: <Addr> “R” <s1> <s2> ETX <csum> EOT or <Addr> NAK EOT
8. ACTIVATION OF LOGIC OUTPUTS.
Master: <Addr> “U” <outputs> EOT
T200F: <Addr> “U” ACK EOT or <Addr> NAK EOT
9. STATUS REQUEST OF LOGIC INPUTS
Master: <Addr> “I” EOT
T200F: <Addr> “I” <inputs> ETX <csum> EOT or <Addr> NAK EOT
10. COMMAND FOR STORING SET-POINTS IN THE PERMANENT MEMORY.
Master: <Addr> “E” EOT
T200F: <Addr> “E” ACK EOT or <Addr> NAK EOT
In the case of a communication error or a command that is not recognised, T200F responds with the following string:
T200F: <Addr> NAK EOT
<s1> and <s2>: formatted as weight field.
<outputs> and <inputs>: single ASCII character encoded as per the following table (bit = 1 if input/ output enabled).
BIT 7 BIT 6 BIT 5 BIT 4 BIT 3 BIT 2
0 0 1 1 0 0
BIT 1
Input 2 / output 2
BIT 0
Input 1 / output 1
11. CHANGE FROM GROSS TO NET WEIGHT
Master: <Addr> “CN” EOT
T200F: <Addr> “C” ACK EOT or <Addr> NAK EOT
Page 61
Transmetteur de pesage T200F : Manuel d’utilisation et d’installation
12. CHANGE FROM NET TO GROSS WEIGHT
Master: <Addr> “CL” EOT
T200F: <Addr> “C” ACK EOT or <Addr> NAK EOT
13. DELETE TARE COMMAND
MASTER: <Addr> “DT” EOT
T200F: <Addr> “D” ACK EOT or <Addr> NAK EOT
14. REQUEST FOR NET WEIGHT (used for repeater program PDAT06)
MASTER: <Addr> “W” “N” EOT
T200F: <Addr> “W” <rip status> <net> ETX <csum> EOT or <Addr> NAK EOT
15. REQUEST FOR GROSS WEIGHT (used for repeater program PDAT06)
MASTER: <Addr> “W” “G” EOT
T200F: <Addr> “W” <rip status> <gross> ETX <csum> EOT or <Addr> NAK EOT where:
<rip status>: character encoded as per the following table (bit = 1 in case of true condiction).
Bit 7
0
Bit 6
0
Bit 5
1
Bit 4
1
Bit 3
Displayed weight
0 = net
1 = gross
Bit 2
Zero band
Bit 1
Stable weight
Bit 0
Zero center
<net> <gross> = field consisting of 8 ASCII characters with the net and gross weight value justified to the right (without insignificant zeroes, with decimal points and negative signs).
In overweight conditions the field assumes the value: “^^^^^^^^”.
In conditions of underweight (negative weight greather of 999999), the field assumes the value: “_ _ _ _”.
Under weight reading error conditions, the field assumes the value: “ O-L ”.
Page 62
ADN Pesage
PRINTER PROTOCOL
Data transmission protocol to Plus Printer
Printing can be started by pressing a key (see section FUNCTION OPERATIONAL) or by input (see paragraph SETTING I/O).
Here is an example of printer.
216/06/16
Net
Gross
Tare
Peak
Code 212456
15:32
209.0 kg
211.5 kg
2.5 kg
268.5 kg
• Date is printed only in case of hardware with time clock.
• The peak value is only printed if the peak function is enabled.
• The identification code of the weighing is printed only in case of METRIC operation and alibi memory configured.
The conditions to printing are:
• Stable weight (or stabilized within 3 seconds from command).
• Since the last executed weigh, the weight has undergone a change of at least 20 divisions (delta weight).
• Gross weight equal to or greater than the minimum weight (20 divisions) and less than the maximum capacity.
• Net weight not null.
Only in case of FREE functioning, printing is permitted even with gross weight less than the minimum weight or with zero net weight.
Page 63
Transmetteur de pesage T200F : Manuel d’utilisation et d’installation
MODBUS RTU PROTOCOL
The addresses set out in the tables follow the standard routing specified in the reference guide of Modicom
PI-MBUS-300 an extract of which is provided below to help the user communicate with the instrument.
“All data addresses in Modbus messages are referenced to zero. The first occurrence of a data item is addressed as item number zero. For example:
The coil known as ‘coil 1’ in a programmable controller is addressed as coil 0000 in the data address field of a Modbus message.
Coil 127 decimal is addressed as coil 007E hex (126 decimal).
Holding register 40001 is addressed as register 0000 in the data address field of the message. The function code field already specifies a ‘holding register’ operation. Therefore the ‘4XXXX’ reference is implicit.”
To confirm a new value entered in E2prom, run the MAKE – BACKUP function. If this function is not performed, by switching off, the T200F, the value before the change will be restored.
Unless otherwise specified, the numerical values (such as addresses, codes and data) are expressed as decimal values.
The MODBUS RTU protocol is available only on COM2 RS485.
HANDLING OF COMMUNICATION ERRORS
The CRC (Cyclic Redundancy Check) is carried out to check the communication strings. In the case of a communication error, the slave does not respond with a string. The master must consider a timeout for receipt of the response. If it does not receive a response, a communication error has occurred
HANDLING OF RECEIVED DATA ERRORS
In the case of a string that has been received correctly but cannot be executed, the slave responds with an EXCEPTIONRESPONSE as indicated in the table below.
CODE
1
2
3
DESCRIPTION
ILLEGAL FUNCTION (The function is not valid or not supported)
ILLEGAL DATA ADDRESS (The address of the specified data is not available)
ILLEGAL DATA VALUE (The values of the received data are invalid)
FUNCTIONS SUPPORTED:
FUNCTION
01
02
03
04
DESCRIPTION
READ COIL STATUS (Reading the status of the logic outputs)
READ INPUT STATUS (Reading the status of the logic inputs)
READ HOLDING REGISTERS (Reading the programmable registers)
READ INPUT REGISTERS (Reading the “read only” registers”)
05
06
15
16
FORCE SINGLE COIL (Writing the status of each output)
PRESET SINGLE REGISTER (Writing a programmable register)
FORCE MULTIPLE COILS (Multiple writing of outputs)
PRESET MULTIPLE REGISTERS (Multiple writing of registers)
Funct + 80h EXCEPTION RESPONSE
Page 64
ADN Pesage
LIST OF THE MODBUS PROTOCOL HOLDING REGISTERS
The instrument parameters that can be read or programmed via the communication interfaces available on the instrument, depending on the hardware configuration, are listed in the following table.
R type registers are readable while W type are writeable.
In case of Modbus TCP protocol, the address of the instrument (the “Unit Identifier” field) must always be FFh.
If a fieldbus is used (different from the Modbus), only the R or R/W registers will be in the input area and only the W or R/W registers will be in the output area.
The registers are 16 bit in size.
1103
1104
1105
1106
1107
1108
1109
1003
1004
1005
1006
1007
1101
1102
0203
0204
0501
0502
0503
1001
1002
0009
0101
0102
0103
0104
0201
0202
Address Holding Register
0001 Status Register
0002
0003
0004
0005
0006
0007
0008
Gross weight (MSB)
Gross weight (LSB)
Net weight (MSB)
Net weight (LSB)
Peak (MSB)
Peak (LSB)
Digital Inputs
Digital Outputs
Weighted Net weight (MSB)
Weighted Net weight (LSB)
Weight code (MSB)
Weight code (LSB)
Set-Point 1 (MSB)
Set-Point 1 (LSB)
Set-Point 2 (MSB)
Set-Point 2 (LSB)
Data Register (MSB)
Data Register (LSB)
Command Register
Stand-by function
Keypad Lock function
Password function
Peak function
Data-Logger function
Data-Logger Trigger
Data-Logger function
Weight division value (*)
Decimals (*)
Capacity of load cells (MSB) (*)
Capacity of load cells (LSB) (*)
Sensitivity of load cells (*)
Fixed Tare (MSB) (*)
Fixed Tare (LSB) (*)
Gravity Calibration (MSB) (*)
Gravity Calibration (LSB) (*)
R
R
R
R
R
R
R
R/W Notes
R See relevant table.
INT value. - Most significant word
INT. value - Less significant word
INT. value - Most significant word
INT. value - Less significant word
INT. value - Most significant word
INT. value - Less significant word
See relevant table
R
R
R
R
INT. value - Most significant word
INT. value - Less significant word
R
INT. value - Most significant word
INT. value - Less significant word
R/W INT. value - Most significant word
R/W INT. value - Less significant word
R/W INT. value - Most significant word
R/W INT. value - Less significant word
W
W
INT. value - Most significant word (See relevant table)
INT. value - Least significant word (See relevant table)
W See relevant table.
R/W INT. value
R/W See relevant table
R/W INT. value
R/W See correspondence on page 47
R/W See correspondence on page 48
R/W See correspondence on page 48
R/W See correspondence on page 48
R/W
See relevant table.
R/W
R/W INT. value - Most significant word
R/W INT. value - Less significant word
R/W INT. value
R/W INT. value - Most significant word
R/W INT. value - Less significant word
R/W INT. value - Most significant word
R/W INT. value - Less significant word
Page 65
Transmetteur de pesage T200F : Manuel d’utilisation et d’installation
1401
1402
1403
1404
1405
1406
1407
1408
1409
1302
1303
1304
1305
1306
1307
1308
1201
1202
1203
1204
1205
1206
1301
1166
1167
1168
1169
1170
1171
1172
1158
1159
1160
1161
1162
1163
1164
1165
1110
1111
1151
1152
1153
1154
1155
1156
1157
Zero tracking (*)
Resettable Divisions (MSB) (*)
Resettable Divisions (LSB) (*)
Input 1 function
Input 2 function
Output mode 1— Function
Output mode 1— Logic
Output mode1— Polarity
Output mode 1— Stability
Hysteresis output 1
Timing output 1
Delay output 1
Gravity zone of use (MSB) (*)
Gravity zone of use (LSB) (*)
Cal. table Zero signal (MSB) (*)
Cal. table Zero signal LSB) (*)
Cal. table P1 signal (MSB) (*)
Cal. table P1 signal (LSB) (*)
Cal. table P2 signal (MSB) (*)
Cal. table P2 signal (LSB) (*)
Cal. table P3 signal (MSB) (*)
Cal. table P3 signal (LSB) (*)
Cal. table P4 signal (MSB) (*)
Cal. table P4 signal (LSB) (*)
Cal. table P5 signal (MSB) (*)
Cal. table P5 signal (LSB) (*)
Cal. table P1 value (MSB) (*)
Cal. table P1 value (LSB) (*)
Cal. table P2 value (MSB) (*)
Cal. table P2 value (LSB) (*)
Cal. table P3 value (MSB) (*)
Cal. table P3 value (LSB) (*)
Cal. table P4 value (MSB) (*)
Cal. table P4 value (LSB) (*)
Cal. table P5 value(MSB) (*)
Cal. table P5 value (LSB) (*)
Filter factor
Output rate ADC
Number of readings on average
Monotony Time
Oscillations Time
Oscillations Range
Full Scale (MSB) (*)
Full Scale (LSB) (*)
Weight stability (*)
R/W INT. value - Most significant word
R/W INT. value - Less significant word
R/W INT. value - Most significant word
R/W INT. value - Less significant word
R/W INT. value - Most significant word
R/W INT. value - Less significant word
R/W INT. value - Most significant word
R/W INT. value - Less significant word
R/W INT. value - Most significant word
R/W INT. value - Less significant word
R/W INT. value - Most significant word
R/W INT. value - Less significant word
R/W INT. value - Most significant word
R/W INT. value - Less significant word
R/W INT. value - Most significant word
R/W INT. value - Less significant word
R/W INT. value - Most significant word
R/W INT. value - Less significant word
R/W INT. value - Most significant word
R/W INT. value - Less significant word
R/W INT. value - Most significant word
R/W INT. value - Less significant word
R/W INT. value - Most significant word
R/W INT. value - Less significant word
R/W See correspondence on page 48
R/W See correspondence on page 48
R/W INT. value
R/W INT. value
R/W INT. value
R/W INT. value
R/W INT. value - Most significant word
R/W INT. value - Less significant word
R/W See correspondence on page 46
R/W See correspondence on page 47
R/W INT. value - Most significant word
R/W INT. value - Less significant word
R/W See correspondence on page 43
R/W See correspondence on page 43
R/W See correspondence on page 43
R/W See correspondence on page 43
R/W See correspondence on page 44
R/W See correspondence on page 44
R/W Valore INT.
R/W Valore INT.
R/W Valore INT.
Page 66
ADN Pesage
1410
1411
1412
1413
1414
1415
1416
1501
1502
1503
1504
1505
1506
1507
1508
2000
2100
Output mode 2—F unction
Output mode 2— Logic
Output mode 2— Polarity
Output mode 2 — Stability
Hysteresis output 2
Timing output 2
Delay output 2
Analogue Tare (MSB
Analogue Tare (LSB)
R/W See correspondence on page 44
R/W See correspondence on page 45
R/W See correspondence on page 45
R/W See correspondence on page 45
R/W INT. value
R/W INT. value
R/W INT. value
R/W INT. value - Most significant word
R/W INT. value - Less significant word
Analogue Full Scale (MSB
Analogue Full Scale (LSB)
R/W INT. value - Most significant word
R/W INT. value - Less significant word
Analogue Output Mode R/W See correspondence on page 35
Analogue Output Range
Regulation of analogue zero
Regulation of analogue full scale
Monitor register
R/W See correspondence on page 35
R/W
R/W
W
INT. value Analogue output zero points, to end the regulation procedure it is necessary to send the data storage command to the permanent memory in the Command Register.
INT. value Analogue output full scale points, to end the regulation procedure it is necessary to send the data storage command to the permanent memory in the command register.
The programmed value is automatically copied in the Monitor
Register R (2100).
Monitor register R
(*) These registers can only be modified in FREE mode or if in METRIC mode with a calibration bridge enabled.
TABLE A - REGISTER STATUS CODING
BIT
Description Setup (***)
BIT
Description
15
7
Not calibrated
14
Weight difference
6
Weight error
13
Output 2 Output 1 Input 2
5
Over-load
12
4
Underload
11
3
Tare entered
TABLE B - KEYPAD LOCK CODING
BIT
Description
15÷4 3 2 1 0
Not used SET Key FUN Key 0 Key PRG Key
10
Input 1
2
Zero band
ATTENTION: the bits from 15 to 4 are not managed and are always equal to 0.
TABLE C - INPUTS/OUTPUTS CODING
BIT 15÷2 1 0
Description Not used IN/OUT 2 Active IN/OUT 1 Active
9
Run
Backup
1
Stable weight
8
Hold function
0
Zero centre
ATTENTION: the bits from 15 to 4 are not managed and are always equal to 0.
Page 67
Transmetteur de pesage T200F : Manuel d’utilisation et d’installation
TABLE D - DECIMALS AND DIVISION VALUE CODING
ADDRESS
1104
1105
DESCRIPTION
Division value
Number of decimals
ACCEPTED VALUES
1 - 2 - 5 - 10 - 20 - 50
0 - 1 - 2 - 3 - 4
TABLE E - DATA REGISTER / COMMAND REGISTER CODING
REGISTER
VALUE
COMMAND REGISTER FUNCTION
0x0001 Semiautomatic zero
0x0002 Auto-tare
0x0003 Peak Reset
0x0004 Zero calibration (**)
0x0005 Full scale calibration (**)
0x0006 Analogue Test
0x0007 Saving the data in the permanent memory
0x000A Run command.
0x000B Change from gross to net
0x000C Change from net to gross
0x000D
Acquisition of the zero signal (calibration table)
0x3FFF Enabling Output Data Area (*)
FUNCTION DATA REGISTER
Sample weight value in MSB and LSB
Value between 0 and 100 at intervals of 10 LSB
(*) The instrument parameters managed in the Fieldbus Output Data Area are not changed until this command is sent. When the instrument is switched on the Output Data area is completely reset, the master fieldbus must read the parameter values from the Input Data Area and copy them in the relevant registers of the Output Data Area, then it must send the enable command in the Command
Register. Otherwise all parameters managed in the Output Data area would be reset when switched on.
(**) Function only available in FREE mode or if in METRIC mode with a calibration jumper enabled.
(***) The instrument is undergoing configuration (TRUE flag during access to the SETUP menu of the instrument or during connection with PC “Optimation” software).
EXAMPLES
ZERO CALIBRATION
In condiction of stable and unloaded scale write hexadecimal value 0004 in Command Register (0503).
To permanentely store in the memory the new Zero value, write hexadecimal value 0007 in Command
Register (0503).
FULL SCALE CALIBRATION
Put a sample weight on the scale, i.e 1256 kg.
Write in Data Register (0501 and 0502) the hex value of the sample weight: 04E8.
Write to the Command Register (0503), the hexadecimal value 0005.
You can write at the same time the Comand Register and Data Register using the multiple registers function.
To permanentely store in the memory the new value, write hexadecimal value 0007 in Command
Register (0503).
Page 68
ADN Pesage
INSTRUMENT RESPONSE TIMES
The instrument, to satisfy most requests, uses a variable time in accordance with the programming of the instrument parameters and the type of request as per table:
Update frequency of measurements
Analogue output update frequency
Fieldbus memory area reading and update update frequency.
Update frequency of logic outputs.
12,5 Hz
12,5 Hz
125 Hz
50 Hz
50 Hz
125 Hz
100 Hz
100 Hz
125 Hz
250 Hz
250 Hz
125 Hz
1000 Hz
1000 Hz
125 Hz
Status and weight acquisition cycle from
Modbus RTU (*)
12,5 Hz 50 Hz 100 Hz 250 Hz 1000 Hz 𝒇𝒇𝒇𝒇𝒇𝒇𝒇𝒇 =
𝟏𝟏 𝒏𝒏𝒏𝒏𝒏𝒏𝒏𝒏𝒏𝒏 +
𝟏𝟏𝟏𝟏𝒃𝒃𝒃𝒃𝒃𝒃𝒃𝒃
+
∗
,
𝟖𝟖
𝟎𝟎 𝟎𝟎𝟎𝟎𝟎𝟎
Status and weight acquisition cycle from
ASC11 protocol (*) 𝒇𝒇𝒇𝒇𝒇𝒇𝒇𝒇 =
𝟏𝟏
+ 𝒃𝒃𝒃𝒃𝒃𝒃𝒃𝒃
𝟖𝟖 ∗ 𝟏𝟏𝟏𝟏
(*) nchar = sum of characters which make up the request string of the master (Query) and the response string of the T200F (Response).
Example of status request, net weight and gross weight (5 registers) at baud rate = 115,2 kbit/sec:
1 / (((8 + 15 + 8) * 10) / 115200) + 0,004) = 149 Hz
Exceptions are:
• the Backup E2prom command (max time = 350mSec.)
• writing of the registers of Cells capacity, Cells sensitivity, Net weight, System tare, Filter (max time
= 550mSec).
Page 69
Transmetteur de pesage T200F : Manuel d’utilisation et d’installation
USE OF SERIAL APPLICATIONS VIA THE USB PORT
PC software “OPTIMATION” allows:
• total configuration of all the setup parameters;
• testing of the different hardware sections;
• consultation of the instrument documentation
• updating of instrument firmware
• storage over time of the weight values acquired by the instrument using the Datalogger function;
• saving and loading of the configuration parameters of the instrument on file.
Page 70
ADN Pesage
FIELDBUS PROTOCOL
The following table lists the registers of the input area (produced from the instrument and read by the master), common to all PROFIBUS, PROFINET, ETHERCAT, ETHERNET/IP fieldbuses.
The registers are 16 bit in size. The input area is updated at a fixed frequency of 150 Hz (80 Hz in case of PROFIBUS).
The size of the output area configured in the master fieldbus must match the size configured in the instrument.
35-36
37-38
39-40
41-42
43-44
45-46
47-48
19-20
21-22
23-24
25-26
27-28
29-30
31-32
33-34
1-2
3-4
5-6
7-8
9-10
11-12
13-14
15-16
17-18
49-50
51-52
53-54
55-56
57-58
59-60
61-62
63-64
65-66
67-68
INPUT DATA AREA
Byte
21
22
23
17
18
19
20
13
14
15
16
9
10
11
12
7
8
5
6
3
4
1
2
Register address
0
28
29
30
24
25
26
27
31
32
33
INPUT AREA REGISTER
Status Register
Gross weight (MSB)
Gross weight (LSB)
Net weight (MSB)
Net weight (LSB)
Peak (MSB)
Peak (LSB)
Digital Inputs
Digital Outputs
Monitor register
Net weight weighing (MSB)
Net weight weighing (LSB)
Code weighing (MSB)
Code weighing (LSB)
Set-Point 1 (MSB)
Set-Point 1 (LSB)
Set-Point 2 (MSB)
Set-Point 2 (LSB)
Capacity of load cells (MSB)
Capacity of load cells (LSB)
Sensitivity of load cells
Weight division value
Decimals
Fixed Tare (MSB)
Fixed Tare (LSB)
Stand-by function
Keypad Lock function
Password function
Peak function
Data-Logger function
Data-Logger Trigger
Data-Logger function
Filter factor
Output rate ADC
Notes
See relevant table.
INT. value - Most significant word
INT. value - Less significant word
INT. value - Most significant word
INT. value - Less significant word
INT. value - Most significant word
INT. value - Less significant word
See relevant table.
This value corresponds to the same register in the output area.
INT. value - Most significant word
INT. value - Less significant word
INT. value - Most significant word
INT. value - Less significant word
INT. value - Most significant word
INT. value - Less significant word
INT. value - Most significant word
INT. value - Less significant word
INT. value - Most significant word
INT. value - Less significant word
INT. value
See relevant table.
See relevant table.
INT. value - Most significant word
INT. value - Less significant word
INT. value
See relevant table.
INT. value
See correspondence on page 50
See correspondence on page 51
See correspondence on page 51
See correspondence on page 51
See correspondence on page 48
See correspondence on page 48
Page 71
Transmetteur de pesage T200F : Manuel d’utilisation et d’installation
69-70
71-72
73-74
75-76
77-78
79-80
81-82
83-84
85-86 42
87-88
89-90
91-92
93-94
95-96
97-98
99-100
101-102 50
103-104 51
105-106 52
46
47
48
49
43
44
45
107-108 53
109-110 54
111-112 55
113-114 56
115-116 57
117-118 58
119-120 59
121-122 60
123-124 61
125-126 62
127-128 63
34
35
36
37
38
39
40
41
Number of readings on average
Monotony Time
Oscillations Time
Oscillations Range
Full Scale (MSB)
Full Scale (LSB)
Weight stability
Auto zero when switching on
(MSB)
Auto zero when switching on
(LSB)
Zero tracking
Input 1 function
Input 2 function
Input 1 mode —Function
Input 1 mode —Logic
Input 1 mode —Polarity
Input 1 mode —Stability
Hysteresis input 1
Timing input 1
Delay input 1
Input 2 mode —Function
Input 2 mode —Logic
Input 2 mode —Polarity
Input 2 mode —Stability
Hysteresis input 2
Timing input 2
Delay input 2
Analogue Fixed Tare (MSB)
Analogue Fixed Tare (LSB)
Analogue Full Scale (MSB)
Analogue Full Scale (LSB)
INT. value
INT. value
INT. value
INT. value
INT. value - Most significant word
INT. value - Less significant word
See correspondence on page 46
INT. value - Most significant word
INT. value - Less significant word
See correspondence on page 47
See correspondence on page 43
See correspondence on page 43
See correspondence on page 43
See correspondence on page 43
See correspondence on page 44
See correspondence on page 44
INT. value
INT. value
INT. value
See correspondence on page 44
See correspondence on page 45
See correspondence on page 45
See correspondence on page 45
INT. value
INT. value
INT. value
INT. value - Most significant word
INT. value - Less significant word
INT. value - Most significant word
INT. value - Less significant word
READING EXAMPLE
To read the gross weight on the T200F it is needed to read the addresses from 3 to 6 of the Input
Area.
To read the net weight is needed to read the addresses from 7 to 10 of the Input Area.
When the display shows the gross weight value of 12351 in the corresponding bytes there will be:
Hex
Byte 3
00
Byte 4
00
Byte 5
30
Byte 6
3F
Page 72
ADN Pesage
The following table lists the registers of the output area (written by the master and acquired by the instrument), common to all PROFIBUS, PROFINET, ETHERCAT, ETHERNET / IP Fieldbuses.
The registers are 16 bit in size. The registers written by the master in the output area, are read by the instrument at a fixed frequency of 150 Hz. (80 Hz in case of PROFIBUS)
The size of the output area configured in the master fieldbus must match the size configured in the instrument.
OUTPUT DATA AREA
Byte
Register address
OUTPUT AREA REGISTER
43-44
45-46
47-48
49-50
51-52
53-54
55-56
29-30
31-32
33-34
35-36
37-38
39-40
41-42
15-16
17-18
19-20
21-22
23-24
25-26
27-28
1-2
3-4
5-6
7-8
9-10
11-12
13-14
57-58
59-60
61-62
63-64
65-66
67-68
69-70
71-72
73-74
75-76
25
26
27
21
22
23
24
18
19
20
14
15
16
17
11
12
13
7
8
9
10
4
5
6
2
3
0
1
32
33
34
35
36
28
29
30
31
37
Note
Command Register
Data Register (MSB)
Data Register (LSB)
Monitor register
Set-Point 1 (MSB)
Set-Point 1 (LSB)
Set-Point 2 (MSB)
Set-Point 2 (LSB)
Capacity of load cells (MSB)
Capacity of load cells (LSB)
Sensitivity of load cells
Weight division value
Decimals
Fixed Tare (MSB)
See relevant table.
INT. value - Most significant word (See Table)
INT. value - Least significant word (See Table)
This value corresponds to the same register in the input area.
INT. value - Most significant word
INT. value - Less significant word
INT. value - Most significant word
INT. value - Less significant word
INT. value - Most significant word
INT. value - Less significant word
INT. value
See relevant table.
See relevant table.
INT. value - Most significant word
Fixed Tare (LSB)
Stand-by function
Keypad Lock function
Password function
Peak function
Data-Logger function
Data-Logger Trigger
INT. value - Less significant word
INT. value
See relevant table.
INT. value
See correspondence on page 50
See correspondence on page 51
See correspondence on page 51
Data-Logger function
Filter factor
See correspondence on page 51
See correspondence on page 48
Output rate ADC See correspondence on page 48
Number of readings on average INT. value
Monotony Time
Oscillations Time
Oscillations Range
INT. value
INT. value
INT. value
Full Scale (MSB)
Full Scale (LSB)
INT. value - Most significant word
INT. value - Less significant word
Weight stability See correspondence on page 46
Auto zero when switching on (MSB) INT. value - Most significant word
Auto zero when switching on (LSB) INT. value - Less significant word
Zero tracking See correspondence on page 47
Resettable Divisions (key >0<) INT. value
Input 1 function See correspondence on page 43
Input 2 function See correspondence on page 43
Input 1 mode —Function See correspondence on page 43
Page 73
Transmetteur de pesage T200F : Manuel d’utilisation et d’installation
77-78
79-80
81-82
83-84
85-86
87-88
89-90
91-92
93-94
95-96
97-98
47
48
99-100 49
101-102 50
103-104 51
105-106 52
107-108 53
109-110 54
111-112 55
113-114 56
38
39
44
45
46
40
41
42
43
Input 1 mode —Logic
Input 1 mode —Polarity
Input 1 mode —Stability
Hysteresis input 1
Timing input 1
Delay input 1
Input 2 mode —Function
Input 2 mode —Logic
Input 2 mode —Polarity
Input 2 mode —Stability
Hysteresis input 2
Timing input 2
Delay input 2
Analogue Fixed Tare (MSB)
Analogue Fixed Tare (LSB)
Analogue Full Scale (MSB)
Analogue Full Scale (LSB)
Analogue Output Mode
Analogue Output Range
See correspondence on page 43
See correspondence on page 44
See correspondence on page 44
INT. value
INT. value
INT. value
See correspondence on page 44
See correspondence on page 45
See correspondence on page 45
See correspondence on page 45
INT. value
INT. value
INT. value
INT. value - Most significant word
INT. value - Less significant word
INT. value - Most significant word
INT. value - Less significant word
See correspondence on page 35
See correspondence on page 35
(*) These registers can only be modified in FREE mode or if in METRIC mode with a calibration bridge enabled.
WRITING EXAMPLES
To write the set-up parameters following the example:
In the bytes 1-2 (Command Register) write value Hex 3FFF. This value opens the writing area of the
T200F.
Example: to change the default values of the T200F like the Capacity of the load cells, the Sensitivity and Division value to 15000, 2.9965 and 2:
Capacity Byte 17 Byte 18 Byte 19 Byte 20
Hex
Dec
00 00
15000
3A 98
Sensitivity Byte 21 Byte 22
Hex 75 0D
Dec 29965
Division Byte 23 Byte 24
Hex 00 0D
Dec 13
Save the data by writing the value Hex 7 in Command Register.
N.B. The T200F does not accept writing of the same values already written.
To perform Zero and FS Calibration it is not needed to abilitate the internal Writing Area of the DAT
1400.
Zero Calibration:
Whit empty system put Hex 4 in Command Register (bytes 1-2). The new Zero value is stored.
Page 74
ADN Pesage
Full Scale Calibration:
Put a know weight on the system and write its value in the Data Register (from byte 3 to 6). Put value
Hex 5 in Command Register. The weight value will be displayed.
Page 75
Transmetteur de pesage T200F : Manuel d’utilisation et d’installation
CANOPEN - DESCRIPTION
The protocol supports the CiA DS301 “communication profile area”.
Network Management (NMT) manages Pre-Operational, Operational, Stopped, Reset and Reset Communication states with its protocols.
The Heartbeat protocol is supported, setted by default at 1 second, and can be switched off by programming at 0 the intervention time. (Index = 1017h).
The Emergency Message Management intervenes when the following events occur or cease:
• Fault Sensor (code = 5030h according to CiA DS404) when the load cell signal is not detected due to failure or incorrect connection or failure of the hardware of the instrument.
• Sensor Calibration (code = 6310h based on CiA DS404), when no weight calibration was performed.
• Input Overload (code = F001h according to CiA DS404), when the load cell signal is out of the instrument reading range.
Two transmission PDO’s are handled with the following transmission types:
• Synchronous acyclic (00h): The data is transmitted in response to the SYNC signal only if the data has been updated with respect to the previous transmission.
• Synchronous cyclic (01h): The data is transmitted in response to the SYNC signal even though it has not been updated yet.
• Asynchronous (FFh): This is the default operation that involves the transmission of the PDO to a predetermined frequency programmable in communication parameters (default = 0, transmission disabled).
The PDO1 is mapped to transmit the following values (updated at 125 Hz frequency):
• Gross weight (Index = 2001h), formatted as 32-bit Signed.
• Net weight (Index = 2002h), formatted as 32-bit Signed.
The PDO2 is mapped to transmit the following values (updated at 125 Hz frequency):
• Peak (index = 2003h), formatted as 32-bit Signed.
• Status Register (index = 2000h), formatted as 16-bit Signed.
• Digital input (index = 2004h), formatted as 8-bit Unsigned.
• Output (index = 2005h), formatted as 8-bit Unsigned.
Page 76
ADN Pesage
NMT
Error Log
Boot-up
Range ID nodo
CANopen bit-rates
Numero di PDO
Modalità PDO
Mappatura PDO
Emergency message
Numero di SDO
Sync
Time stamp
Funzioni aggiuntive
Application layer
Frameworks supportati
Profili supportati
Certificato
SPECIFICATION
NMT slave
Heartbeat producer
Yes
1 - 127
10 – 1000 kbit/sec
1 TPDO
Event-triggered (timer)
Synchronous (cyclic)
Synchronous (acyclic)
Si (6 obj/PDO)
Si (Producer)
1 SDO server (“expedited” and “segmented” transferred)
No SDO client
Sync producer: no
Sync counter: no
-
No
-
CiA 301 V 4.0.2
-
No
Page 77
Transmetteur de pesage T200F : Manuel d’utilisation et d’installation
CANOPEN - OBJECT DICTIONARY - COMMUNICATION PROFILE AREA
GENERIC PARAMETERS
Index Sub-Index Name Description
1000h 0
1001h 0
1005h 0
0
1
1010h
2
3
1011h
1014h
1017h
1018h
0
1
2
3
0
0
2
3
0
1
DEV_TYPE
ERR_REG
Device type information (*)
Error log
U32
U8
COB_ID SYNC COB_ID Sync message (80h)
Sub-index number(4)
Store all parameters (**)
STORE_PAR
U32
U8
U32
Store communication parameters (**) U32
Store application parameters (**) U32
RESTORE_PAR
COB_ID EMCY
HBT_TIME
OBJ_ID
Sub-index number(4)
Restore default parameters (***)
U8
U32
Restore communication parameters
(***)
U32
Restore application parameters (***) U32
COB_ID Emergency message
(80+Node_ID)
Heartbeat time (expressed in ms, default 1000 mS)
Sub-index number (4)
ID Vendor
Product code
Version number
U32
U16
U8
U32
U32
U32
(*) 00070194h (according to CiA DS404 for mesurement device).
(**) 65766173h (‘a’,’v’,’e’,’s’).
(***) 64616F6Ch (‘d’,’a’,’o’,’l’).
Type Attribute
R
R
R/W
R
R/W
R/W
R/W
R
R/W
R/W
R/W
R
R/W
CONST
CONST
CONST
CONST
SDO SERVER PARAMETERS
Index Sub-Index
0
1200h
1
Name
SDO_PAR
2
Description
SDO record number(2)
COB_ID Client->Server (rx)
( = 600h + Node_ID )
COB_ID Server->Client (tx)
( = 580h + Node_ID )
Type Attribute
U8
U32
U32
R
R
R
Page 78
ADN Pesage
T_PDO COMMUNICATION PARAMETERS
Index Sub-Index Name Description Type Attribute
1800h
0
1
2
3
4
5
AI_T_PDO_CPAR
Sub-index number(5)
COB_ID used from PDO
(180h + Node_ID )
Transmission type PDO (*)
Inhibition time (0)
Reserved
U8
U32
U8
U16
U8
Event timer (expressed in ms, default
8 ms)
U16
R
R
R
R/W
R/W
R/W
(*) PDO Transmission type:
00h = synchronous acyclic (PDO is transmitted following the receipt of SYNC, but only if a new measurement has been acquired).
01h = synchronous cyclic (PDO is always transmitted after receiving SYNC).
FFh = asynchronous (default) (PDO is periodically transmitted according to the set time, setting “event timer” to zero, transmission is disabled).
Other types of transmission provided by the CIA DS-301 are not supported.
T_PDO MAPPING PARAMETERS
Index Sub-Index Name Description
1A00h
0
1
2
T_PDO_MPAR1
Number of “application objects” mapped in the PDO (2)
Applic.Obj.map 1 (*)
Applic.Obj.map 2 (*)
Below is the sub-index structure from 1h to 6h.
Byte: MSB
Index (16 bit)
(*) The following default values are defined:
LSB sub-index (8 bit) object lenghtr (8 bit)
• Sub-index 0 = 6h.
• Sub-index 1 = 2001 0120h ( Index = 2001h, sub-index 01, 32 bit lenght).
• Sub-index 2 = 2002 0120h ( Index = 2002h, sub-index 01, 32 bit lenght).
Type
U8
U32
U32
Attribute
R
R
R
Page 79
Transmetteur de pesage T200F : Manuel d’utilisation et d’installation
T_PDO COMMUNICATION PARAMETERS
Index Sub-Index Name Description Type Attribute
1801h
0
1
2
3
4
5
AI_T_PDO_CPAR2
Sub-index number(5)
COB_ID used from PDO
(180h + Node_ID )
Transmission type PDO (*)
Inhibition time (0)
Reserved
U8
U32
U8
U16
U8
Event timer (expressed in ms, default
8 ms)
U16
R
R
R
R/W
R/W
R/W
(*) PDO Transmission type:
00h = synchronous acyclic (PDO is transmitted following the receipt of SYNC, but only if a new measurement has been acquired).
01h = synchronous cyclic (PDO is always transmitted after receiving SYNC).
FFh = asynchronous (default) (PDO is periodically transmitted according to the set time, setting “event timer” to zero, transmission is disabled).
Other types of transmission provided by the CIA DS-301 are not supported.
T_PDO MAPPING PARAMETERS
Index Sub-Index Name Description
1A01h
0
1
2
3
4
T_PDO_MPAR2
Number of “application objects” mapped in the PDO (2)
Applic.Obj.map 1 (*)
Applic.Obj.map 2 (*)
Applic.Obj.map 3 (*)
Applic.Obj.map 4 (*)
Below is the sub-index structure from 1h to 6h.
Type
U8
U32
U32
U32
U32
Byte: MSB
Index (16 bit)
(*) The following default values are defined:
LSB sub-index (8 bit) object lenghtr (8 bit)
• Sub-index 0 = 6h.
• Sub-index 1 = 2003 0120h ( Index = 2003h, sub-index 01, 32 bit lenght).
• Sub-index 2 = 2000 0110h ( Index = 2000h, sub-index 01, 16 bit lenght).
• Sub-index 1 = 2004 0120h ( Index = 2004h, sub-index 01, 8 bit lenght).
• Sub-index 2 = 2005 0120h ( Index = 2005h, sub-index 01, 8 bit lenght).
Attribute
R
R
R
R
R
Page 80
ADN
Pesage
PARAMETERS DEFINED BY THE MANUFACTURER
Index Sub-Index
2000h
2001h
2002h
2003h
2004h
2005h
2006h
2007h
2008h
2009h
200Ah
200Bh
200Ch
200Dh
200Eh
200Fh
2010h
1
0
1
0
1
0
1
0
1
0
1
0
1
0
1
0
1
0
1
0
1
0
1
0
1
0
1
0
1
0
1
0
1
0
UD_IN
Name
UD_STATUS
UD_LORDO
UD_NETTO
UD_PICCO
UD_OUT
UD_COMMAND
UD_DATA
UD_MONITOR_R
UD_MONITOR_W
UD_W_VAL
UD_W_CODE
UD_SET_1
UD_SET_2
UD_PORTATA
UD_SENS
UD_DIV
Description
Sub-index number(1)
Status Register
Sub-index number(1)
Gross weight
Sub-index number(1)
Net weight
Sub-index number(1)
Peak
Sub-index number(1)
Digital input
Sub-index number(1)
Digital output
Sub-index number(1)
Command Register
Sub-index number(1)
Data Register
Sub-index number(1)
Monitor Register (reading)
Sub-index number(1)
Monitor Register (writing)
Sub-index number(1)
Net weight weighing
Sub-index number(1)
Weighing code
Sub-index number(1)
Set-Point 1
Sub-index number(1)
Set-Point 2
Sub-index number(1)
Load cells capacity
Sub-index number(1)
Load cells sensitivity
Sub-index number(1)
Weight division value
Type Attribute
S32
U8
U16
U8
U8
U8
S32
U8
S32
U8
U8
U16
U8
U16
U8
S32
U8
S32
U8
U8
U16
U8
U32
U8
S32
U8
U8
U8
U8
U16
U8
S32
U8
S32
R/W
R
R/W
R
R/W
R
R/W
R
R/W
R
R
R
R
R
R
R
W
R
R
R
R/W
R
R/W
R
R
R
R
R
R
R
R
R
R/W
R
Page 81
Transmetteur de pesage T200F : Manuel d’utilisation et d’installation
Index Sub-IndexName
2011h
2012h
2013h
2014h
2015h
2016h
2017h
2018h
2019h
201Ah
201Bh
201Ch
201Dh
201Eh
201Fh
2020h
2021h
0
1
0
1
0
1
0
1
1
0
1
0
1
0
1
0
1
0
1
1
0
1
0
0
1
0
1
0
1
0
1
0
1
0
UD_DEC
UD_TARA_F
UD_STAND_B
UD_BLOCCO_T
UD_PASS
UD_PICCO
UD_LOG
UD_FILT
UD_RATE
UD_N_MEDIA
UD_T_MON
UD_T_OSC
UD_R_OSC
UD_FS
UD_STAB
UD_AUTO_Z
UD_INS_Z
Description Type Attribute
Sub-index number (1)
Decimal
Sub-index number (1)
Fixed tare
Sub-index number (1)
Stand by function
Sub-index number (1)
Keypad lock function
Sub-index number (1)
Password function
Sub-index number (1)
Peak function
Sub-index number (1)
Datalogger function
Sub-index number (1)
Filter factor
Sub-index number (1)
Output rate ADC
U8
U8
U8
Sub-index number (1) U8
Number of readings on averageU8
Sub-index number (1) U8
Monotony Time
Sub-index number (1)
Oscillations Time
Sub-index number (1)
Oscillations Range
Sub-index number (1)
Full Scale
Sub-index number (1)
Weight stability
Sub-index number (1)
U8
U8
Auto zero when switching on S32
Sub-index number (1) U8
Zero tracking U8
U16
U8
U16
U8
U8
U8
S32
U8
U8
U16
U8
U8
U8
U8
U8
U8
U8
U8
S32
U8
U16
U8
U8
R/W
R
R/W
R
R/W
R
R/W
R
R/W
R
R/W
R
R/W
R/W
R
R/W
R
R/W
R
R
R/W
R
R/W
R
R/W
R
R
R/W
R
R/W
R
R/W
R
R/W
Page 82
ADN
Pesage
Index Sub-IndexName
2022h
2023h
2024h
2025h
2026h
2027h
2028h
2029h
202Ah
202Bh
202Ch
202Dh
202Eh
202Fh
2030h
2031h
2032h
2033h
2034h
2035h
0
1
0
1
0
1
0
1
0
1
0
1
0
1
1
0
1
0
0
1
0
1
0
1
0
1
0
1
0
1
0
1
1
0
1
0
0
1
0
1
UD_FUN_IN1
UD_FUN_IN2
UD_FUN_OUT1
UD_LOG_OUT1
UD_POL_OUT1
UD_STAB_OUT1
UD_IST_OUT1
UD_T_OUT1
UD_R_OUT1
UD_FUN_OUT2
UD_LOG_OUT2
UD_POL_OUT2
UD_STAB_OUT2
UD_IST_OUT2
UD_T_OUT2
UD_R_OUT2
UD_ANA_T
UD_ANA_FS
UD_ANA_M
UD_ANA_R
Description
Sub-index number (1)
Input 1 function
Sub-index number (1)
Input 2 function
Sub-index number (1)
Output mode 1— Function
Sub-index number (1)
Output mode 1— Logic
Sub-index number (1)
Output mode1— Polarity
Sub-index number (1)
Output mode 1— Stability
Sub-index number (1)
Hysteresis input 1
Sub-index number (1)
Timing input 1
Sub-index number (1)
Delay input 1
Sub-index number (1)
Output mode 2— Function
Sub-index number (1)
Output mode 2— Logic
Sub-index number (1)
Output mode 2— Polarity
Sub-index number (1)
Output mode 2— Stability
Sub-index number (1)
Hysteresis input 2
Sub-index number (1)
Timing input 2
Sub-index number (1)
Delay input 2
Sub-index number (1)
Analogue Fixed Tare
Sub-index number (1)
Analogue Full Scale
Sub-index number (1)
Analogue Output Mode
Sub-index number (1)
Analog output range
Tipo Attributo
U8
U8
U8
U8
U8
U8
S32
U8
U16
U8
U16
U8
U8
U8
U8
U8
U8
U8
U8
S32
U8
U8
U8
U8
U8
U8
U8
U8
U8
U8
U8
U8
U8
U16
U8
U16
U8
S32
U8
S32
R/W
R
R/W
R
R/W
R
R/W
R
R/W
R
R/W
R
R/W
R
R
R/W
R
R/W
R
R/W
R
R
R/W
R
R/W
R
R/W
R
R/W
R/W
R
R/W
R
R/W
R
R/W
R
R/W
R
R/W
Page 83
Transmetteur de pesage T200F : Manuel d’utilisation et d’installation
TROUBLESHOOTING
PROBLEM POSSIBLE CAUSE SOLUTION
The display shows the
O-L message
The weight cannot be detected because the cell is not available or has been connected incorrectly.
The hyphen is shown in the top display.
Check the connections of the cells.
The acquired weight cannot be shown because it exceeds the available five digits or is greater than the capacity of the cells.
Configure setup parameters that are compatible with system features
The number of decimal places is wrong.
Incorrect division value selected.
Select the correct division value inthe main menu.
switched off
Weight display is frozen
The load cell is not functioning properly or has not been properly connected
Power up the instrument with the correct supply voltage
Use a multimeter and measure 5Vdc between EXC+ and EXC- and a lower value between SENSE+ and
SENSE- (greater are the distance between the instrument and the load cells and lower will be the SENSE voltage) and check the variation in millivolt between SGN+ and SGN- when loading or unloading the load cells
Inputs and / or outputs does not work properly
The serial communication does not work properly.
The semi-automatic zero-setting function does not work.
The semi-automatic tare function does not work.
Wiring or Software Setup Errors
Installation has been completed properly. Selection of operation of theserial interface is incorrect.
Use the I / O Test Function to verify the correct operation of inputs and outputs and verify the settings of the specific program
Check the connections as describedin the installation manual.
Select the settings as appropriate.
The gross weight exceeds the action limit of semi-automatic zero-setting.
The weight doesn’t stabilise.
To re-establish the zero, calibrate the weight.
Wait for the weight to stabilise or adjust the weight filter parameter.
The gross weight is negative orexceeds the maximum capacity.
The weight doesn’t stabilise.
Check the gross weight.
Wait for the weight to stabilise or adjust the weight filter parameter.
Page 84
ADN Pesage
We
EU Declaration of conformity (DoC)
ADN Pesage
7 Rue du Bois Malhais
F-78640 St-Germain-De-La-Grange
FRANCE
declare that the DoC issued under our sole responsibility and belongs to the following product:
Apparatus model/Product:
Type:
T200F
Weighing instrument
The object of the declaration described above used as indicated in the installation manual and use, is in conformity with the relevant Union harmonisation legislation:
Directive EMC 2014/30/EU Electromagnetic Compatibility
The following harmonized standards and technical specification have been applied:
EN 61000-6-2:2005
EN 61000-6-3:2007 + A1 2011
Directive LVD 2014/35/EU Low Voltage Directive
The following harmonized standards and technical specification have been applied:
EN 61010-1:2011
Directive EMC 2014/32/EU Measuring Instruments
The following harmonized standards and technical specification have been applied:
EN 45501:2015
Signed for end on behalf of:
Concorezzo: 16/01/2019
Page 85
Weight indicator MS100
PRODUCT RANGE
Weight procesor MS300
Lite weight indicator T16F
Junction box for load cell
load cell and mounting kit
Process transmiter T200F
ADN Pesage: 7 Rue du bois Malhais, 78990 Saint Germain de la Grange France
Tél.: 33(0) 1 48 63 00 76 - Télécopie: 33(0) 1 48 63 72 06 - Mail: [email protected]
Transmetteur de pesage T200F : Manuel d’utilisation et d’installation
ADN Pesage: 7 Rue du bois Malhais, 78990 Saint Germain de la Grange France
Tél.: 33(0) 1 48 63 00 76 - Télécopie: 33(0) 1 48 63 72 06 - Mail: [email protected]
advertisement
Related manuals
advertisement