advertisement
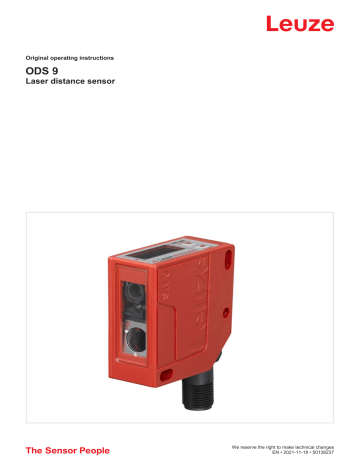
Original operating instructions
ODS 9
Laser distance sensor
We reserve the right to make technical changes
EN • 2021-11-18 • 50138237
© 2021
Leuze electronic GmbH + Co. KG
In der Braike 1
73277 Owen / Germany
Phone: +49 7021 573-0
Fax: +49 7021 573-199 www.leuze.com
Leuze electronic GmbH + Co. KG ODS 9 2
Table of contents
Leuze electronic GmbH + Co. KG ODS 9 3
Table of contents
Leuze electronic GmbH + Co. KG ODS 9 4
Table of contents
Leuze electronic GmbH + Co. KG ODS 9 5
About this document
1 About this document
1.1
Used symbols and signal words
Tab. 1.1: Warning symbols and signal words
Symbol indicating dangers to persons
Symbol indicating dangers from harmful laser radiation
NOTE
CAUTION
Signal word for property damage
Indicates dangers that may result in property damage if the measures for danger avoidance are not followed.
Signal word for minor injuries
Indicates dangers that may result in minor injury if the measures for danger avoidance are not followed.
Tab. 1.2: Other symbols
Symbol for tips
Text passages with this symbol provide you with further information.
Symbol for action steps
Text passages with this symbol instruct you to perform actions.
Symbol for action results
Text passages with this symbol describe the result of the preceding action.
Leuze electronic GmbH + Co. KG ODS 9 6
About this document
Tab. 1.3:
BG
DS
DSUpload
DTM
FDT
FE
IODD
Max.
Min.
NEC
ODS
OLED
PELV
Pt
SIO
SP
SSC
SSP
UL
Terms and abbreviations
B ack g round
Mode in which switching outputs react/switch when an object enters a set distance
D ata S torage
Data memory of the connected IO-Link master
D ata S torage Upload
Upload to the data memory of the connected IO-Link master
D evice T ype M anager
Software device manager of the sensor
F ield D evice T ool
Software frame for management of device managers (DTM)
F unctional e arth
IO D evice D escription
File with information on process data and device parameters
Max imum
Min imum
N ational E lectric C ode
O ptical D istance S ensor
Optical distance sensor
O rganic L ight E mitting D iode
Organic LED
P rotective E xtra L ow V oltage
Protective extra low voltage with reliable disconnection
P oin t
Switching point
S tandard IO mode
Signal transfer without IO-Link
S et p oint
Position at which the switching point is set
S witching S ignal C hannel
Abbreviation for the switching outputs acc. to Smart Sensor Profile
S mart S ensor P rofile
Profile acc. to IO-Link standard
U nderwriters L aboratories
Leuze electronic GmbH + Co. KG ODS 9 7
About this document
1.2
Important terms
Tab. 1.4: Important terms
Response time
(Response time)
Resolution
Warmup time
Output resolution
Also integration time or measurement time. Maximum length of time from the occurrence of an erratic change in distance to the steady state of the measurement value.
The response time depends on the set average calculation. Although the average calculation increases the response time, it also improves reproducibility.
Smallest representable change in measurement value, distance and speed.
Time the sensor needs in order to reach the operating temperature. An optimal measurement is only possible after the end of the warmup time.
The warmup time is approximately 20 minutes.
The output resolution describes how the measurement values are presented on the display and digital interfaces.
Time interval of measurement value updating at the interface.
Output time
(Output time)
Readiness delay The delay before start-up indicates the point in time when the first valid measurement can be obtained after switching on.
Data memory of the connected IO-Link master.
Data storage
IO-Link data storage
DSUpload
Accuracy
Light switching
Dark switching
Diffuse reflection
Reproducibility
Triangulation measurement principle
Data Storage Upload.
Upload to the data memory of the connected IO-Link master.
Maximum expected deviation of the measurement value between the determined and real distance value within the specified measurement range.
The behavior of the switching output if an object is within the taught/configured switching distance.
• Light switching: switching output active (high)
• Dark switching: switching output not active (low)
Return and/or degree of reflection of the radiated light. Observe the specifi-
cations regarding diffuse reflection (see chapter 12 "Technical data").
• 90 % is white
• 6 % is black
Also repeatability. Deviation of multiple measurement results relative to each other under identical conditions. Dependent on the measurement distance and the diffuse reflection of the measurement object.
The reproducibility can be considered as the measure of measurement value noise and is affected by the configuration of the response time.
Distance measuring procedure, which determines the distance of an object by the incidence angle of the light reflected from the object.
Leuze electronic GmbH + Co. KG ODS 9 8
Safety
2 Safety
This sensor was developed, manufactured and tested in line with the applicable safety standards. It corresponds to the state of the art.
2.1
Intended use
The device is designed as an optoelectronic sensor for the optical, contactless measurement of the distance to objects.
Areas of application
The laser distance sensor is designed for the following areas of application:
• Distance measurement
• Thickness measurement
• Positioning
• Diameter determination
• Fill level indicator
CAUTION
Observe intended use!
The protection of personnel and the device cannot be guaranteed if the device is operated in a manner not complying with its intended use.
Ä Only operate the device in accordance with its intended use.
Ä Leuze electronic GmbH + Co. KG is not liable for damages caused by improper use.
Ä Read these operating instructions before commissioning the device. Knowledge of the operating instructions is an element of proper use.
CAUTION
UL applications!
For UL applications, use is only permitted in Class 2 circuits in accordance with the NEC (National Electric Code).
NOTICE
Comply with conditions and regulations!
Ä Observe the locally applicable legal regulations and the rules of the employer's liability insurance association.
2.2
Foreseeable misuse
Any use other than that defined under "Intended use" or which goes beyond that use is considered improper use.
In particular, use of the device is not permitted in the following cases:
• in rooms with explosive atmospheres
• in circuits which are relevant to safety
• for medical purposes
NOTICE
Do not modify or otherwise interfere with the device!
Ä Do not carry out modifications or otherwise interfere with the device. The device must not be tampered with and must not be changed in any way.
Ä The device must not be opened. There are no user-serviceable parts inside.
Ä Repairs must only be performed by Leuze electronic GmbH + Co. KG.
Leuze electronic GmbH + Co. KG ODS 9 9
Safety
2.3
Competent persons
Connection, mounting, commissioning and adjustment of the device must only be carried out by competent persons.
Prerequisites for competent persons:
• They have a suitable technical education.
• They are familiar with the rules and regulations for occupational safety and safety at work.
• They are familiar with the operating instructions for the device.
• They have been instructed by the responsible person on the mounting and operation of the device.
Certified electricians
Electrical work must be carried out by a certified electrician.
Due to their technical training, knowledge and experience as well as their familiarity with relevant standards and regulations, certified electricians are able to perform work on electrical systems and independently detect possible dangers.
In Germany, certified electricians must fulfill the requirements of accident-prevention regulations DGUV
(German Social Accident Insurance) provision 3 (e.g. electrician foreman). In other countries, there are respective regulations that must be observed.
2.4
Disclaimer
Leuze electronic GmbH + Co. KG is not liable in the following cases:
• The device is not being used properly.
• Reasonably foreseeable misuse is not taken into account.
• Mounting and electrical connection are not properly performed.
• Changes (e.g., constructional) are made to the device.
Leuze electronic GmbH + Co. KG ODS 9 10
Safety
2.5
Laser safety notices
Laser class 1 (ODS9L1...)
ATTENTION
LASER RADIATION – CLASS 1 LASER PRODUCT
The device satisfies the requirements of IEC/EN 60825-1:2014 safety regulations for a product of laser class 1 and complies with 21 CFR 1040.10 except for conformance with IEC 60825-1
Ed. 3., as described in Laser Notice No. 56, dated May 8, 2019.
Ä Observe the applicable statutory and local laser protection regulations.
Ä The device must not be tampered with and must not be changed in any way.
There are no user-serviceable parts inside the device.
Repairs must only be performed by Leuze electronic GmbH + Co. KG.
Laser class 2 (ODS9L2...)
ATTENTION
LASER RADIATION – CLASS 2 LASER PRODUCT
Do not stare into beam!
The device satisfies the requirements of IEC/EN 60825-1:2014 safety regulations for a product of laser class 2 and complies with 21 CFR 1040.10 except for conformance with IEC 60825-1
Ed. 3., as described in Laser Notice No. 56, dated May 8, 2019.
Ä Never look directly into the laser beam, the laser aperture (1) or in the direction of reflected laser beams! If you look into the beam path over a longer time period, there is a risk of injury to the retina.
Ä Do not point the laser beam of the device at persons!
Ä Interrupt the laser beam using a non-transparent, non-reflective object if the laser beam is accidentally directed towards a person.
Ä When mounting and aligning the device, avoid reflections of the laser beam off reflective surfaces!
Ä CAUTION! Use of controls or adjustments or performance of procedures other than specified herein may result in hazardous light exposure.
Ä Observe the applicable statutory and local laser protection regulations.
Ä The device must not be tampered with and must not be changed in any way.
There are no user-serviceable parts inside the device.
Ä Repairs must only be performed by Leuze electronic GmbH + Co. KG.
Ä The laser radiation emitted from the sensor is collimated. The laser is operated in pulse
mode. Pulse power, pulse duration and wavelength see chapter 12 "Technical data".
Leuze electronic GmbH + Co. KG ODS 9 11
Safety
1
Fig. 2.1: Laser aperture
NOTICE
Affix laser information and warning signs!
Laser information and warning signs attached to the device. Also included with the device are self-adhesive laser warning and laser information signs (stick-on labels) in multiple languages.
Ä Affix the laser information sheet to the device in the language appropriate for the place of use.
When using the device in the US, use the stick-on label with the "Complies with
21 CFR 1040.10" notice.
Ä Affix the laser information and warning signs near the device if no signs are attached to the device (e.g. because the device is too small) or if the attached laser information and warning signs are concealed due to the installation position.
Affix the laser information and warning signs so that they are legible without exposing the reader to the laser radiation of the device or other optical radiation.
Leuze electronic GmbH + Co. KG ODS 9 12
Safety
50106507-06
LASERSTRAHLUNG
NICHT IN DEN STRAHL BLICKEN
Max. Leistung (peak):
Impulsdauer:
Wellenlänge:
LASER KLASSE 2
EN 60825-1:2014
1,8 mW
22 ms
650 nm
LASER RADIATION
DO NOT STARE INTO BEAM
Maximum Output (peak):
Pulse duration:
1.8 mW
22 ms
Wavelength: 650 nm
CLASS 2 LASER PRODUCT
EN 60825-1:2014
RADIAZIONE LASER
NON FISSARE IL FASCIO
Potenza max. (peak):
Durata dell'impulso:
1,8 mW
22 ms
Lunghezza d'onda: 650 nm
APARRECCHIO LASER DI CLASSE 2
EN 60825-1:2014
RAYONNEMENT LASER
NE PAS REGARDER DANS LE FAISCEAU
Puissance max. (crête):
Durée d`impulsion:
1,8 mW
22 ms
Longueur d`onde: 650 nm
APPAREIL À LASER DE CLASSE 2
EN 60825-1:2014
RADIACIÓN LÁSER
NO MIRAR FIJAMENTE AL HAZ
Potencia máx. (peak):
Duración del impulso:
1,8 mW
22 ms
Longitud de onda: 650 nm
PRODUCTO LÁSER DE CLASE 2
EN 60825-1:2014
Maximum Output (peak):
Pulse duration:
Wavelength:
1.8 mW
22 ms
650 nm
CLASS 2 LASER PRODUCT
Complies with 21 CFR 1040.10
RADIAÇÃO LASER
NÃO OLHAR FIXAMENTE O FEIXE
Potência máx. (peak):
Período de pulso:
1,8 mW
22 ms
Comprimento de onda: 650 nm
EQUIPAMENTO LASER CLASSE 2
EN 60825-1:2014
激光辐射
勿直视光束
最大输出(峰值):
脉冲持续时间:
波长:
2 类激光产品
IEC 60825-1:2014
1.8 mW
22 ms
650 nm
Fig. 2.2: Laser information and warning signs
Leuze electronic GmbH + Co. KG ODS 9 13
Device description
3 Device description
3.1
Device overview
3.1.1
General information
The laser distance sensor is an optical distance sensor that operates according to the triangulation measurement principle.
The sensor consists of the following components:
• Transmitter: laser spot
• Receiver
• White OLED display
• Control panel with control buttons
• Status LEDs
• Connection for connecting to the control: M12 connector
The sensor can be configured using display and control buttons.
With the Sensor Studio configuration software, the sensors can be configured via the IO-Link interface with a PC and the measurement values visualized. Stored parameter sets can be duplicated in other sensors.
The connection is made via the IO-Link USB master, which is available as an accessory.
2 3 4
1
5
6
7
5
6
7
1
2
3
4
Fig. 3.1:
Device housing
Status LEDs
Control buttons
Display
Transmitter
Receiver
Connection
Device construction
Leuze electronic GmbH + Co. KG ODS 9 14
Device description
3.1.2
Operating principle
Triangulation measurement principle
Distance measuring procedure, which determines the distance of an object by the incidence angle of the light reflected from the object.
Advantages of the triangulation measurement principle:
• Short response times and, thus, high measurement rates
• High accuracy
3.1.3
Performance characteristics
The most important performance characteristic of the ODS 9 laser distance sensor:
• Measurement ranges:
50 mm … 1050 mm against objects (6 … 9% diffuse reflection)
• Analog current and voltage output (configurable)
Factory setting: current output
• OLED display and control buttons for configuration
• Configurable measurement range and measure mode
• Measurement value display in mm on OLED display
• IO-Link version 1.1
• Compliant with the "Smart Sensor Profile" specification
• Dual Channel: the IO-Link interface can be used in parallel with the other output functions.
• Communication interface RS 232/RS 485, depending on the device type
• Optional: multifunction input for deactivating the laser or for teaching the digital switching points (teachin)
Factory setting: input for deactivating the laser
• Optional: second switching output if the IO-Link interface is not used
For measurement against objects:
• Measurement range: 50 mm … max. 1050 mm, dependent on device type
• Measurement against diffusely reflective objects
• Reflection-independent distance information
• Applications:
• Distance measurement
• Contour determination
• Thickness measurement
• Positioning
• Diameter determination
• Sag determination
• Stack height measurement
• Loop measurement
3.1.4
Accessories
• Mounting systems for mounting on rods
• Connection cables
• IO-Link USB master set for connecting to a PC
• IO-Link master for cascading or integrating in a higher-level network
Leuze electronic GmbH + Co. KG ODS 9 15
Device description
3.2
Connection technology
For the electrical connection of the laser distance sensor, the following connection variants are available:
• M12 connector, 5-pin, turns 180°
3.3
Indicators and operational controls
The device housing is provided with the following indicators and operational controls:
• OLED display
• Two control buttons
• Green LED: operating state (PWR)
• Orange LED: switching output information (SSC)
1 2 3
4
3
4
1
2
Fig. 3.2:
Display
Orange LED (SSC1/SSC2)
Green LED (PWR)
Control buttons
Indicators and operational controls
3.3.1
LED indicators
Tab. 3.1:
LED
Green LED
PWR
Meaning of the LED indicators on the device housing
Orange LED
Switching output SSC1/
SSC2
Color, state
Green
Off
On
Off
Description
Sensor ready
No supply voltage
Object detected in the switching range
No object detected in the switching range
3.3.2
Control buttons
The sensor can be configured using display and control buttons. The display is controlled via the control buttons. You can make adjustments in the application via the control buttons.
• – Scroll through the functions
• – Enter button: select function, confirm/enter value
The and buttons have different functions depending on the operating situation. These functions are
Leuze electronic GmbH + Co. KG ODS 9 16
Device description
Navigating within the menus
Use the navigation button to move through the menu.
Activate the desired selection with the enter button .
The number of bars at the left edge of the display indicates the current menu level.
Selecting options
Set the desired option with the navigation button and the enter button .
Resetting to factory settings
Ä While switching on the supply voltage, press the enter button to reset the sensor configuration to the factory settings.
Ä Press the enter button again to reset all parameters to factory settings. All parameter settings made previously are permanently lost.
Press the navigation button to return to process mode without resetting the parameters.
NOTICE
You can also use the menu (see chapter 3.4 "Configuration / menu structure") or the
Sensor Studio
configuration software to reset to factory settings (see chapter 8 "Connecting to a PC
3.3.3
Display
The display changes depending on the current operating mode. The following display modes exist:
• Menu display
Press one of the two control buttons once or twice to access the menu display.
For information on operating via the menu, see chapter 3.4 "Configuration / menu structure" and the
configuration example (see chapter 3.5 "Configuration example").
• Process mode
After switching on the supply voltage and error-free initialization of the device, the green LED lights up continuously. The laser distance sensor is in process mode.
In process mode, the current measurement value is displayed in the display, e.g. "267 mm".
NOTICE
In the menu display, the selectable or editable values are shown with inverted text colors (black on white background).
If no key is pressed for approx. 6 minutes in the configuration menu, the device automatically returns to the process mode.
The sensor can be protected against unauthorized configuration change by activating the pass-
word query (see chapter 3.4.7 "Settings menu"). The password is permanently set to
165 . In addition, a complete button lock can be activated using the lock function (device access locks, bit 2) (see the table "Status displays on the display").
Leuze electronic GmbH + Co. KG ODS 9 17
Device description
Status displays in process mode
Tab. 3.2: Status displays on the display
Object distance in mm
No measurement value available, e.g. due to a weak or missing reception signal.
No object detected or reception signal too weak.
No object detected or reception signal too weak.
• Out of Range (+)
• Out of Range (-)
• +max
Sensor deactivated, laser switched off
• Via the input function (see chapter 3.4.1 "Input menu")
• Via the IO-Link command
The current measurement value is less than the lower limit value of the analog output distance.
The current measurement value is greater than the upper limit value of the analog output distance.
The measurement value has an offset and/or the gradient is falling (-1)
Lock function: Button lock activated via IO-Link (device access locks, bit 3)
The button lock can also be enabled and set using the configuration software Sensor Studio :
Configuration > Local operation
Leuze electronic GmbH + Co. KG ODS 9 18
Device description
3.3.4
Meaning of the display icons
The and buttons have different functions depending on the operating situation. These functions are displayed via icons at the right edge of the display.
Icon Position
First line
Second line
Function
By pressing the navigation button you select the next parameter within a menu level.
Symbolizes the respective, next menu level that you have not yet selected.
Second line
Second line
Second line
Second line
Second line
Press the enter button to exit the menu level or the menu.
Symbolizes the input mode.
The selected (highlighted) option field can be a fixed selection parameter or a multi-digit input field.
With a multi-digit input field, you can change the active digit cyclically using the navigation button and switch from one digit to the next using the enter button .
Note: If this icon does not appear, the local configuration lock is set via IO-Link
(index: 12, bit 2).
Confirmation of the selection.
This icon appears when you complete an option field with the enter button and the previously entered value is valid.
Pressing the enter button again saves and displays the change locally.
Reject the selection.
This icon is accessed from the previous icon (check mark) by pressing the navigation button .
Press the enter button to reject the current value or option parameter.
Return to selection.
This icon is accessed from the previous icon (cross) by pressing the navigation button .
This icon is also accessed if the value newly entered previously is outside the permissible value range, making correction of the entry necessary.
Press the enter button to reset the current value or option parameter and enter a new value or select a new option parameter.
3.4
Configuration / menu structure
The following chapters show the structure of all menu items. For each sensor model, only the actually available menu items are present for entering values or for selecting settings.
NOTICE
Use the navigation button to move through the menu.
Activate the desired selection with the enter button .
NOTICE
The number of bars at the left edge of the display indicates the current menu level.
Leuze electronic GmbH + Co. KG ODS 9 19
Device description
3.4.1
Input menu
The function of the switching input on pin 5 is set in the Input menu.
NOTICE
The Input menu is only available for sensors with multifunction input on pin 5 (ODS9…/ LAK -
…).
Level 1
Input
Level 2 Level 3
Teach
Deactivation
Activation
Description
Teach analog output and switching output
Switch off laser transmitter with +24 V on the switching input
Switch on laser transmitter with +24 V on the switching input
Default
Input_Mode Function of the switching input on pin 5 if the supply voltage is applied.
No_Function No input function active
X
Trigger_Rising The measurement value is only updated and output by an edge on input PIN 5.
Trigger_Falling
Important : Activation or deactivation using IO-Link commands or process data (PDOut) only has an effect if neither Deactivation nor Activation is set as the input function.
3.4.2
Output_SSC1 menu
The switching behavior of switching output SSC1 is set to pin 4 in the Output_SSC1 menu.
NOTICE
Designation "SSC" corresponds to designation "Q" previously used for switching outputs.
Leuze electronic GmbH + Co. KG ODS 9 20
Device description
Level 1 Level 2
Output_SSC1 SSC1_SP1_(dist.)
Level 3 Description
Upper switching point
Default
Depending on the device range:
• 100 mm: 75 mm
• 200 mm: 175 mm
• 450 mm: 250 mm
• 650 mm: 350 mm
• 1050 mm:
550 mm
SSC1_SP2_(near) Lower switching point 50 mm
Notice
: For the limit values of the measurement range for your sensor, see chapter 12
SSC1_Logic Behavior of the switching output if an object is within the taught/configured switching distance.
High_Active Switching output active (high) X
SSC1_Mode
Low_Active Switching output not active (low)
see chapter 7.1.2 "Setting the switching outputs"
One switching point on the object Single_Point
(Obj)
Window
Two_Point
Switching window Window
Two switching points on the object
Single_Point
(BG)
One switching point on the background (BG), also referred to as background-teach. Switching process for objects between background and sensor.
Deactivated Mode deactivated
SSC1_Hysteresis Hysteresis
X
10 mm
3.4.3
Output_SSC2 menu
• ODS9LA6: The switching behavior of switching output SSC2 is set to pin 5 in the Output_SSC2 menu.
• ODS9L6X: The switching behavior of switching output SSC2 is set to pin 2 in the Output_SSC2 menu.
NOTICE
Ä The Output_SSC2 can only be used for sensors with a second switching output SSC2.
Ä Designation "SSC" corresponds to designation "Q" previously used for switching outputs.
Leuze electronic GmbH + Co. KG ODS 9 21
Device description
Level 1 Level 2
Output_SSC2 SSC2_SP1_(dist)
Level 3 Description
Upper switching point
Default
Depending on the device range:
• 100 mm: 75 mm
• 200 mm: 175 mm
• 450 mm: 250 mm
• 650 mm: 350 mm
• 1050 mm:
550 mm
SSC2_SP2_(near) Lower switching point 50 mm
Notice
: For the limit values of the measurement range for your sensor, see chapter 12
SSC2_Logic Behavior of the switching output if an object is within the taught/configured switching distance.
High_Active Switching output active (high) X
SSC2_Mode
Low_Active Switching output not active (low)
see chapter 7.1.2 "Setting the switching outputs"
One switching point on the object Single_Point
(Obj)
Window
Two_Point
Switching window Window
Two switching points on the object
Single_Point
(BG)
One switching point on the background (BG), also referred to as background-teach. Switching process for objects between background and sensor.
Deactivated Mode deactivated
SSC2_Hysteresis Hysteresis
X
10 mm
Leuze electronic GmbH + Co. KG ODS 9 22
Device description
3.4.4
Analog_Output menu
The characteristic output curve of the analog output is set to pin 2 in the Analog Output menu.
NOTICE
The Analog Output menu is only available for sensors with analog output.
Analog output
Level 1 Level 2
Position_Max.Val.
Position_Min.Val.
Level 3 Default
Upper limit of the measurement range
50 mm
Notice
: For the limit values of the measurement range for your sensor, see chapter 12
Analog Range Current/voltage range of the analog output
4-20_mA X
1-10_V
0-10_V
Description
Distance measurement value for maximum voltage / maximum current
Distance measurement value for minimum voltage / minimum current
Spreading the characteristic output curve
You can spread the characteristic output curve of the analog output according to your requirements.
Ä Select the current or voltage range of the analog output.
Ä Set the distance measurement value that corresponds to the lower limit of the measurement range
(4 mA, 1 V, 0 V).
Ä Set the distance measurement value that corresponds to the upper limit of the measurement range
(20 mA, 10 V).
It is also possible to invert the working range of the analog output, i.e., the lower limit of the measurement range is set to a larger value than the upper limit. This creates a descending characteristic output curve.
3.4.5
Serial Menu
In the Serial menu, the function of the serial interface is set to pin 2 and pin 5.
NOTICE
The Serial is only available for sensors with a serial interface.
Leuze electronic GmbH + Co. KG ODS 9 23
Device description
Level 1
Serial
Level 2
Serial_Function
Level 3
ASCII
Description
Format of the measurement value output
Measurement value output corresponding to the device resolution
X
2 byte transfer
3 byte transfer
Default
14_Bit
16_Bit
24_Bit
Decimal
4 byte transfer
Transfer of the measurement value as decimal number
Remote_Control Remote control operation of the ODS via remote commands
Reserved
Note:
For the device resolution for your sensor see chapter 12 "Technical data".
Device_Address Address under which the ODS is addressed
1 0 … 14
Transmiss._Rate
2400_Baud
4800_Baud
Transmission rate of the serial interface
X 9600_Baud
19200_Baud
28800_Baud
38400_Baud
57600_Baud
115200_Baud
230400_Baud
Parity Transfer of parity bit
Stop_Bit
1
2
Termination_Byte
None
Odd
Even
Number of stop bits
If not equal to 0, the corresponding character is appended
X
X
0 … 255
Transmiss._Delay
Delay of data transmission in milliseconds
0
0 … 255 0
Leuze electronic GmbH + Co. KG ODS 9 24
Device description
3.4.6
Application menu
The measurement function of the sensor is set in the Application menu.
Level 1 Level 2 Level 3 Selection level 3
Application
Process_Settings
Description
Measurement value processing
Measurem._Mode
Standard Multi-purpose function for many measurement tasks
Precision Greater accuracy for less dynamic applications
Filter_Settings
Light_Suppression
Ambient light sensitivity
LightSupp r.Limit
2 … 32 Setting of the maximum number of measurements for preventing the sensor from measuring for too long if the light is too bright and, as a result, not outputting a measurement value.
Filter for ascertaining and suppressing outliers
Default
X
32
Filter_Type
None X
Averaging Floating average calculation taking 2 … 99 measurements into account
The response time increases with the number of measurements.
Spike_Su ppression
Average_Count
Blocked central value filtering across buffer sizes from 5 … 99 measurements
Number of measurements used in averaging 10
Spike_Supp.Count
10
Spike_Supp.Depth
Raw
Number of measurements used in outlier suppression
Adjustable filter depth for outlier suppression
Averages approx. 75 % of the central measurement values
X
Medium Averages approx. 50 % of the central measurement values
Fine Averages approx. 25 % of the central measurement values
Distance calibration Dist.Correction
Offset
Gradient
Rising
Falling
Preset_Position
Preset_Calc.
Inactive
Execute
0 mm
X
0 mm
X
Leuze electronic GmbH + Co. KG ODS 9 25
Device description
Measurement value processing and filtering is set according to the given requirements and the application via the display or using the Sensor Studio configuration software.
By changing the measurement value processing or filtering, the response time and accuracy can be increased.
NOTICE
A higher response time presupposes the possibility of measuring an object for a longer period.
Measurement value processing
Processing settings > Measure mode > Standard/Precision/Ambient light
Tab. 3.3: Measurement value processing
Standard
Precision
Ambient light
Accuracy
+
+ +
+
Measurement time / reload
+
- -
- -
Ambient light
+
+
+ +
Varying diffuse reflection
+
+
0
Filter
Filter settings > Filter type > Averaging/outlier suppression
A floating average value is calculated over the number of set measurement values.
The measurement value noise decreases, i.e., measurement value fluctuations become smaller.
If the measurement value changes erratically, the output value moves linearly from the old measurement value to the new measurement value over n measurements.
The higher the number of measurements is set, the higher the response time of the sensor. With dynamic applications, averaging should be set to a very low number of measurement values or switched off altogether.
The time of measurement value updating is not affected by the filtering.
Outlier suppression
Filter settings > Degree of suppression > Coarse/Medium/Strong
Measurement results with excessively high or low measurement values (referred to as "outliers" or
"spikes") are suppressed or rejected according to the set filter depth.
• The user sets the number of measurements via the display or using the configuration software Sensor Studio .
• The sensor performs the set number of measurements on the object, e.g. 100 measurements.
Due to physical reasons, the measurement results are not all the same. The measurement values have a scatter which corresponds to a normal distribution comprising a large number of similar measurement values and a small number of excessively high or low measurement values (outliers, spikes).
Leuze electronic GmbH + Co. KG ODS 9 26
Device description
The suppression or rejection of the measurement value outliers is configured in the following levels using the filter depth:
• Coarse: A large number of measurement values which do not occur with a high frequency are suppressed or rejected.
• Falling on one side: 12 %
• Used center area, averaged: 76 %
Fig. 3.3: Coarse filter depth
• Medium
• Falling on one side: 24 %
• Used center area, averaged: 52 %
Fig. 3.4: Medium filter depth
Leuze electronic GmbH + Co. KG ODS 9 27
Device description
• Strong
• Falling on one side: 36 %
• Used center area, averaged: 28 %
Fig. 3.5: Strong filter depth
NOTICE
In the case of dynamic applications with erratic changes in measurement distance, it is recommended to filter by setting the response time.
Distance calibration "Distance correction"
Under the Distance correction menu item, you can influence the output of the measured distance value.
Gradient
If the gradient is changed from rising to falling , the measurement values decrease as the distance from the object to the sensor increases. The distance information is output inverted.
NOTICE
Negative measurement values may result if the gradient is reversed.
Offset and Preset
Deviations that arise while mounting and attaching the sensor can be compensated for with the entries for the Offset and Preset parameters.
NOTICE
Negative measurement values may occur if an offset is set.
The offset/preset calculation is available as a teach function. The assignment of the teach time frame can
be read out via IO-Link (see chapter 7 "Starting up the device").
Specify offset and preset
Under the Application > Dist.Correction
menu item, you can influence the output of the measured distance value. The Offset and Preset parameters are used for correcting the measurement value by a fixed amount.
Leuze electronic GmbH + Co. KG ODS 9 28
Device description
Deviations that arise while mounting and attaching the sensor can be compensated for with the entries for the Offset and Preset parameters.
• For the Offset parameter, a fixed value and sign are specified.
• For the Preset parameter, a nominal measurement value is specified; a measurement is then performed using an object located at the desired nominal distance. The Offset parameter is changed as a result of this measurement.
NOTICE
If the calculation of the Offset parameter results in negative measurement values, zero is output at the interface and on the display.
Setting the offset
Ä Enter an offset value via the display:
Application > Dist.Correction > Offset
ð The set offset value is added to the measured distance value of the sensor.
Example:
• Measurement value of the ODS 9: 1,500 mm
• Entry offset-value: -100 mm
• Output on the display and at the interface: 1400 mm
Preset presetting
Ä Enter a Preset value via the display or using the Sensor Studio configuration software ( IO-Link ):
Application > Distance correction > Preset position
Ä Position an object at the desired preset distance.
Ä Perform the preset measurement:
Application > Distance correction > Preset calculation > Execute
ð The offset value is automatically calculated from the measurement value and nominal measurement value (preset value) and entered as the offset in the configuration.
Example:
• Entry: preset value 350 mm
• Object distance: 300 mm in front of the sensor
Trigger preset measurement
Distance correction > Preset calculation > Execute
An offset of +50 mm is automatically calculated and stored in the configuration.
• Object distance: 300 mm
Output to display and interface: 350 mm
• Object distance: 400 mm
Output to display and interface: 450 mm
Leuze electronic GmbH + Co. KG ODS 9 29
Device description
3.4.7
Settings menu
You can set the display language and call up information about the sensor in the Settings menu.
Level 1
Settings
Level 2
Language
Display
English
Deutsch
Auto
Off
On
Level 3
Auto_Off
Description Default
Setting of the display language
Note : If the display language is changed, this change only becomes effective when the sensor is restarted.
Display language English X
Display language German
Display settings
After pressing a control button, the display is set to full brightness for approx. one minute.
The display is then dimmed slightly for five minutes and then dimmed considerably.
X
The display (measurement value display) is automatically switched off after approx.
six minutes.
No measurement value display – the display is only active in the menu after pressing a control button.
The display (measurement value display) is always at full brightness.
Factory_Settings
Inactive
Execute
Password_Lock
Info
Reset to factory settings
The sensor is not reset to factory settings.
X
The sensor is reset to factory settings.
Locks access to the menu with the fixed password 165
Inactive
Active
X Inactive
Activated
Exit_behaviour Exit the configuration settings
Report_to_DS After making a change in the menu, the change is taken over in the data memory after returning to measurement operation. The
DSUpload flag is set.
The "Data Storage" (DS) parameter memory is updated.
X
Only_local_changes
The change is only temporary or local on the device or no data memory is used.
The DSUpload flag is cleared.
Information on the sensor
Leuze part number of the sensor Part_No.
Serial_No.
Firmware_Revision
Sensor serial number
Firmware version
Leuze electronic GmbH + Co. KG ODS 9 30
Device description
3.4.8
Ending configuration
With IO-Link data storage, the behavior upon ending the configuration settings can be changed in the following ways in the Settings menu.
Tab. 3.4: Settings > Exit behavior
Menu item
Report to DS
(Report to DS)
Only local changes
(only local changes)
Use
Changes in the menu are taken over in the data memory after returning to measurement operation. The DSUpload flag is set.
Display of the menu item
A change was performed and the data memory updated.
The change is only temporary or local on the device or no data memory is used. The DSUpload flag is cleared.
A change was made only locally on the device.
Central storage of configuration data
If the configuration setting is ended with subsequent adoption of the data in the data memory of a connected IO-Link master, the sensor does not need to be newly configured if a device is changed.
The sensor adopts the configuration from the data memory of the connected IO-Link master, provided that the IO-Link master is capable of doing this and enabled accordingly.
Timeout
If the configuration setting is ended due to a timeout, the previously made changes are always reported by default to the data memory (Data Storage, DS). If an IO-Link master is connected, the changes are transferred to its data memory. The status of the DSUpload flag is not changed.
If the DSUpload flag is not set and the changes are only stored locally, after reconnection the change is overwritten by the configuration which is stored in the data memory of the connected IO-Link master.
NOTICE
If the sensor is not operated via an IO-Link master, these settings do not need to be made.
3.5
Configuration example
To illustrate menu operation, the setting of the lower switching point of switching output SSC1 to 100 mm is explained as an example.
Ä In process mode, press a control button to activate the menu display.
Input
Output SSC1
Ä Press the navigation button .
ð The display shows "Output SSC1" in the upper menu line.
Output SSC1
Output
Ä Press the enter button to select Output SSC1.
SSC1 SP1 (dist.)
00250 mm
Leuze electronic GmbH + Co. KG ODS 9 31
Device description
Ä Press the navigation button once.
ð The display shows "SSC1 SP2 (near)" in the upper menu line.
SSC1 SP2 (near)
00050 mm
Ä Press the enter button to set the lower switching point.
ð The first digit of the switching point value is displayed with inverted colors.
SSC1 SP2 (near)
0 0050 mm
Ä Press the enter button twice until the hundreds digit is inverted.
SSC1 SP2 (near).
00 0 50 mm
Ä Press the navigation button as many times as necessary to set the desired value “1”.
SSC1 SP2 (near)
00 1 50 mm
Ä Press the enter button to accept the set value.
Ä Repeat the setting for digit 5 until the complete value “00100” is set.
Press the enter button to move to the units digit.
SSC1 SP2 (near)
0010 0 mm
After pressing the enter button again, the icon appears in the lower right part of the display.
• The icon indicates that the next time the enter button is pressed, the set value will be accepted.
• You can change the function of the enter button by pressing the navigation button several times.
The following icons are displayed in succession:
• : re-edit value
• : reject value
Ä Press the enter button to accept the set value 00100.
ð "SSC1 SP2 (near)" is displayed inverted in the display.
The newly set value “00100 mm”, which is stored in non-volatile memory, appears in the display.
SSC1 SP2 (near)
00100 mm
Ä Press the navigation button repeatedly until the ← icon appears in the upper menu line.
←
SSC1 SP1 (dist.)
Leuze electronic GmbH + Co. KG ODS 9 32
Device description
Ä Press the enter button to access the next-higher menu level.
Output SSC2
Analog output
Ä Press the enter button to exit the menu display and access process mode.
225 mm
Quick exit
If you do not wish to make any further configuration settings, you can exit the menu via Quick exit and return to process mode.
NOTICE
The DSUpload upload flag is always set on quick exit. This means that parameter changes are passed on to the connected IO-Link master.
Ä Press and hold down the enter button for at least 5 s – until the "Exit menu" message appears on the display.
Ä Confirm with the enter button .
Leuze electronic GmbH + Co. KG ODS 9 33
Applications
4 Applications
The laser distance sensor is designed for the following areas of application:
• Distance measurement
• Thickness measurement
• Positioning
• Diameter determination
• Fill level indicator
4.1
Wood width measurement
Fig. 4.1: Application example: wood width measurement
Leuze electronic GmbH + Co. KG ODS 9 34
Applications
4.2
Assembly inspection
Fig. 4.2: Application example: assembly inspection
Leuze electronic GmbH + Co. KG ODS 9 35
Mounting
5 Mounting
The sensor can be mounted in the following ways:
• Mount using a mounting system
• BTU 300M-D10: mounting on rod Ø 10 mm
• BTU 300M-D12: mounting on rod Ø 12 mm
• BTU 300M-D14: mounting on rod Ø 14 mm
NOTICE
Observe during mounting!
Ä Make certain that the required environmental conditions (humidity, temperature) are maintained.
Ä Make certain that the optics cover of the sensor is not soiled, e.g., by leaking fluids, abrasion from boxes or residues from packaging material.
Ä When mounting behind a cover: Make certain that the cutout in the cover is at least as large as the lens cover of the sensor. Correct measurement cannot otherwise be ensured.
5.1
Mounting with mounting system
Ä Mount the mounting system on the rod (system-side).
Ä Mount the sensor on the mounting system with M4 fastening screws (not included in delivery contents).
Max. tightening torque of the fastening screws: 1.4 Nm
Leuze electronic GmbH + Co. KG ODS 9 36
Electrical connection
6 Electrical connection
6.1
Overview
The assignment of the electrical connections is dependent on the type of sensor that is used. The type designation of the sensor is specified on the name plate.
CAUTION
Safety notices!
Ä Before connecting the device, be sure that the supply voltage agrees with the value printed on the name plate.
Ä Only allow competent persons to perform the electrical connection.
Ä Ensure that the functional earth (FE) is connected correctly.
Fault-free operation is only guaranteed if the functional earth is connected properly.
Ä If faults cannot be rectified, take the sensor out of operation. Protect the sensor from accidentally being started.
NOTICE
Protective Extra Low Voltage (PELV)!
The device is designed in accordance with protection class III for supply with PELV (Protective
Extra-Low Voltage).
NOTICE
Ä For all connections (connection cable, interconnection cable, etc.), use only the cables listed
in the accessories (see chapter 13.2 "Accessories – cables and connectors").
Ä Use shielded cables when using the analog interface. You can thereby prevent interference caused by electromagnetic fields.
6.2
Pin assignment
Pin assignment ODS9L2.8/LAK-…-M12
Analog OUT
Fig. 6.1: Pin assignment
Pin Designation
1 18-30 V DC +
2 Analog OUT
3
4
5
GND
IN
Assignment
Supply voltage
Configurable analog output
• Current: 4 mA … 20 mA
• Voltage: 1 V … 10 V, 0 V … 10 V
Factory setting: Current
Functional earth
IO-Link / switching output 1, push-pull
Function of the switching input
Leuze electronic GmbH + Co. KG ODS 9 37
Electrical connection
Pin assignment ODS9L2.8/L6X-…-M12
Fig. 6.2:
4
5
2
3
Pin assignment
Pin Designation
1 18-30 V DC +
GND don’t connect
Assignment
Supply voltage
Switching output 2, push-pull
Functional earth
IO-Link / switching output 1, push-pull don’t connect
Pin assignment ODS9L2.8/LA6-…-M12
Analog OUT
Fig. 6.3:
Pin Designation
1
2
Pin assignment
18-30 V DC +
Analog OUT
3
4
5
GND
Pin assignment ODS9L2.8/LFH-…-M12
Assignment
Supply voltage
Configurable analog output
• Current: 4 mA … 20 mA
• Voltage: 1 V … 10 V, 0 V … 10 V
Factory setting: Current
Functional earth
IO-Link / switching output 1, push-pull
Switching output 2, push-pull
Fig. 6.4: Pin assignment
4
5
2
3
Pin Designation
1 18-30 V DC +
RxD
GND
TxD
Assignment
Supply voltage
Signal RxD of the RS 232 serial interface
Functional earth
IO-Link / switching output 1, push-pull
Signal TxD of the RS 232 serial interface
Leuze electronic GmbH + Co. KG ODS 9 38
Electrical connection
Pin assignment ODS9L2.8/LQZ-…-M12
Fig. 6.5: Pin assignment
3
4
Pin Designation
1
2
18-30 V DC +
D –
GND
5 D +
Assignment
Supply voltage
Signal D – of the RS 485 serial interface
Functional earth
Switching output
Signal D + of the RS 485 serial interface
Leuze electronic GmbH + Co. KG ODS 9 39
Starting up the device
7 Starting up the device
7.1
Teaching and configuring output functions
7.1.1
Setting the analog output
The sensors are equipped with an analog output with linear response within the respective measurement range.
Above and below the measurement range linearity is not obtained. If a signal is present, the output values can be used to determine whether the measurement range is exceeded or not met.
In order to achieve the highest resolution possible, set the range of the analog output as small as the application allows. The characteristic output curve can be configured as rising or falling, e.g. for fill level applications.
The output can be switched to current or voltage with the following ranges:
• 4 … 20 mA
• 1 … 10 V
• 0 … 10 V
To configure the analog output, the two distance values Position Min. Val.
and Position Max. Val.
are specified at which the respective minimum or maximum analog value is output.
Measurement range C is assigned ex works (see figure), e.g., 50 … 100 mm for device types -100 .
I [mA]
≈ 21
20
U [V]
≈ 10.5
10
ODS9L…/LA…-M12
C
A B
B D E
4
1
1
0
F
0
0
0
0
0
≈ 45
≈ 45
≈ 45
≈ 45
≈ 45
50
50
50
50
50
100
200
450
650
105
210
470
680
1050 1100
≈ 650
≈ 650
≈ 650
≈ 1000
≈ 1500
D
E
F
A
B
C
Fig. 7.1:
Area not defined
Linearity not defined
Measurement range
Object present
No object detected (characteristic curve behavior configurable via IO-Link)
Measurement distance
Characteristic curve of analog output ODS9L…/LA…-M12
Setting the analog output
You can set the characteristic output curve for the analog output as follows:
• Directly changing the parameters:
• Via the Sensor Studio
configuration software (see chapter 8 "Connecting to a PC – Sensor Studio").
Leuze electronic GmbH + Co. KG ODS 9 40
Starting up the device
• Teach-in / teach:
• Via IO-Link (see chapter 7.1.5 "Teaching the output functions via the IO-Link system commands"),
especially using the Sensor Studio
configuration software (see chapter 8 "Connecting to a PC –
• Via the multifunction input with set Teach
input function (see chapter 7.1.4 "Teaching the output functions via the multifunction input").
7.1.2
Setting the switching outputs
All sensors are equipped with at least one SSC1 switching output. LA6 model sensors are provided with a second SSC2 switching output.
For each switching output you can configure the following parameters:
• Upper and lower switching point
• Switching hysteresis
• Switching logic
• Light switching (high active)
• Dark switching (low active)
• Switching point mode
NOTICE
The output state in the hysteresis area is not uniquely defined!
The output state in the hysteresis area is dependent on the previous situation.
If the output in the hysteresis area is permanently set to high active , a short detection failure (no signal, e.g., due to a target that is marginally dark) results in a change to permanently low active
(dark switching).
3 3
ON
1
OFF
ON
2
OFF
4
1
2
3
4
Light switching
Dark switching
Hysteresis
Measurement distance
Fig. 7.2: Switching output configuration
Leuze electronic GmbH + Co. KG ODS 9 41
Starting up the device
NOTICE
For sensor models with multifunction input, there is only one physically present switching output that can be taught in.
Configuring switching point modes
The following switching point modes can also be configured. These are structured according to the switching profiles of the Smart Sensor Profile specification.
• SinglePoint Object mode (SinglePt Obj): single switching point taught on an object
• Window: window mode
• TwoPoint: two-point mode
• SinglePoint Background mode (SinglePt BG): single switching point taught against a background
SinglePoint Object mode (SinglePt Obj)
When teaching setpoint SP1 before of after, the object (Obj) is targeted, i.e., with SP1, the SSC is still active. The SSC becomes inactive only after SP1.
3 3
5
4
2 1
1
6
1
2
3
4
5
6
Setpoint SP1
Measurement range minimum
Hysteresis
Signal response
Sensor/SSC
Reserve if >0
Fig. 7.3: SinglePoint Object switching point mode
• Only setpoint SP1 (not SP2) is used for calculating the switching edges. The lower switching edges are always at the lower limit value.
• Reserve and hysteresis run from the upper switching point into the distance, so that the switching output has reliably (i.e., with reserve) switched on after the teach event (provided it is light switching high active ).
Leuze electronic GmbH + Co. KG ODS 9 42
Starting up the device
Window – window mode
Teach point is midway between the equidistantly shifted setpoints S2 (near) and SP1 (far)
4
3 3
5
2
3
4
5
1
2
6
7
Setpoint SP1 (far)
Setpoint SP2 (near)
Hysteresis
Teach point
Sensor/SSC
Signal response
Window
Fig. 7.4: Switching point mode window
• Hysteresis runs to the outside.
• Reserve is not used.
7
1
6
Leuze electronic GmbH + Co. KG ODS 9 43
Starting up the device
TwoPoint – two-point mode
• Closer than setpoint SP2, the output is set to high active (as with the Single Point modes).
• The "far" hysteresis area lies between setpoint SP2 and setpoint SP1; the Hysteresis parameter is not used here.
• After setpoint SP1, the output is set to low active .
3
4
5
6
7 2 1
3
4
1
2
5
6
7
Fig. 7.5:
Setpoint SP1
Setpoint SP2
Hysteresis "near"
Hysteresis "far"
Sensor/SSC
Signal response
Measurement range minimum
TwoPoint switching point mode
NOTICE
The Hysteresis parameter is used for the switch-on/switch-off edges at the start of the measurement range.
Ä If setpoint SP2 is too close to the switch-on edge, the assigned switching edge is shifted into the distance by the distance of the Hysteresis parameter.
Ä If, afterwards, setpoint SP1 is closer than the shifted edge, the edge assigned to setpoint
SP1 is placed on the shifted SP2 edge. The two far switching edges then decrease together.
NOTICE
The output state in the hysteresis area is not uniquely defined!
The output state in the hysteresis area is dependent on the previous situation.
If the output in the hysteresis area is permanently set to high active , a short detection failure (no signal, e.g., due to a target that is marginally dark) results in a change to permanently low active
(dark switching).
Leuze electronic GmbH + Co. KG ODS 9 44
Starting up the device
SinglePoint Background mode (SinglePt BG)
When teaching setpoint SP1 before of after, the background (BG) is targeted, i.e., with setpoint SP1, the
SSC must no longer be active. The SSC is only active before setpoint SP1.
3 3
5
4
2 1
6
1
3
4
5
6
1
2
Setpoint SP1
Measurement range minimum
Hysteresis
Signal response
Sensor/SSC
Reserve if >0
Fig. 7.6: SinglePoint BG switching point mode
• Only setpoint SP1 (not SP2) is used for calculating the switching edges. The lower switching edges are always at the lower limit value.
• Reserve and hysteresis run from the upper switching point into the near range, so that the switching output has reliably (i.e., with reserve) switched off after the teach event (provided it is light switching high active ).
Leuze electronic GmbH + Co. KG ODS 9 45
Starting up the device
7.1.3
Teach-in / teach
Teaching offers the possibility to adjust certain parameters based on the current measurement situation.
Focus here is primarily on settings that affect the output functions, i.e., analog output and the switching output(s).
The teaching action is triggered in the following ways:
• Via the multifunction input when setting the input function to Teach
(see chapter 7.1.4 "Teaching the output functions via the multifunction input")
• Special teach via the device menu (OLED display and control buttons)
When completed, each successful teach returns a so-called teach point (TP), which is formed by averaging multiple individual measurements.
• Prerequisite for successfully teaching is a minimum number of valid measurement values. Objects that are marginally dark and/or distant objects can increase the teach time.
• The teachable areas are limited by model.
• A teach point may only be located within the measurement range described in the table in order for an assignment to the respective, likewise limited parameters to be possible.
Device
(Device)
Outside of the operating range (-)
(Out of Range
(-))
Operating range [mm]
(measurement value shown on the display)
Outside of the operating range
(+)
(Out of
Range(+))
Limited accuracy
Measuring range Limited accuracy
…-100-…
…-200-…
…-450-…
…-650-…
…-1050-…
Directly underneath
47.00
47.00
47.0
47.0
47.0
50.00
50.00
50.0
50.0
50.0
100.00
200.00
450.0
650.0
1050
110.00
220.00
500.00
700.00
1100
Directly above
7.1.4
Teaching the output functions via the multifunction input
NOTICE
The information in this chapter only applies for devices that are equipped with a multifunction input on pin 5 (ODS9…/ LAK -…).
To teach, a teach signal is applied to the multifunction input (pin 5). The duration of the teach signal (low level on the teach input) determines the teach-in function.
T
+24V
0V t
T Duration of the teach signal
Fig. 7.7: Plot of the teach signal
To teach, proceed as follows:
Ä In the Configuration menu, activate the input function Teach (Default)
Input > Input mode > Teach
Leuze electronic GmbH + Co. KG ODS 9 46
Starting up the device
Ä Position the measurement object at the desired distance.
NOTICE
The teachable area must be located within the measurement range of the sensor.
Ä Apply the teach signal to the multifunction input (pin 5).
• The duration T of the low level at the teach input determines the teach-in function.
• The teach functions assigned to the time frames are preset and can be queried via IO-Link.
Tab. 7.1: Default assignment of the teach functions
Duration T [ms] Teach function
20 … 80 Object teach of switching output SSC1
120 … 180
220 … 280
320 … 380
Window teach (Window) of switching output SSC1
Analog teach of the distance value for the smallest analog value
(4 mA, 1 V, 0 V) on pin 2
Analog teach of the distance value for the largest analog value
(20 mA, 10 V) on pin 2
420 … 480
520 … 580
620 … 680
720 … 780
820 … 880
920 … 980
1020 … 1080
Preset-Offset calculation: determination of an offset value so that the preset Preset value is output as measurement value.
Background-Teach_SSC1
Setpoint 1-Teach SP1_SSC1
Setpoint 2-Teach SP2_SSC1
Alternative setpoint 1-Teach SP1a_SSC1
Logic of SSC1 to 0 "light switching" Light_SSC1
Logic of SSC1 to 1 "dark switching" Dark_SSC1
1120 … 1180 Toggle logic of SSC1 "light/dark switching"
Corresponding IO-Link object :
Index 140, teach level assignment (Wire Function Array)
Function no.
14
15
6
7
8
16
12
13
17
19
20
18
Ä Detection and averaging of measurement values for forming the teach point TP begins with the rising edge of the input signal.
The parameter or parameters assigned to the time frame for the teach signal is/are updated based on the teach point.
NOTICE
Ä With the preset assignment of the teach functions, teaching can only be performed via the multifunction input in SinglePoint Object
mode (see chapter 7.1.2 "Setting the switching outputs").
Only the upper setpoint SP1 is then shifted, so that the targeted object is just detected
(switching output triggered). More distant objects are no longer detected.
Ä
Ä Alternatively, the assignment table assignments can also be changed or expanded for applicative optimization.
NOTICE
A complete process data map of all function indices can be generated via the IODD file. You can find the IODD file on the Internet at www.leuze.com
.
Leuze electronic GmbH + Co. KG ODS 9 47
Starting up the device
Ä In the following cases, perform two successive teach actions:
• Analog output: teach the two positions for start and end of the analog value range
• Switching output: individually teach setpoints SP1 and SP2 in Window or Two-Point mode
Ä Ensure that the taught values are taken over correctly, for example by checking the corresponding entries in the configuration menu.
7.1.5
Teaching the output functions via the IO-Link system commands
functions.
Teaching the analog output via IO-Link system commands
To configure the analog output, the two distance values Position Min. Val.
and Position Max. Val.
are taught at which the respective minimum or maximum analog value is output.
Value hex / dec
0xC3 / 195
Command
Teach Analog Min
Description
0xC4 / 196 Teach Analog Max
System command: AnalogRangeMin=TP
Teaches the distance value to which the lower analog limit value (4 mA, 1 V, 0 V) is assigned
( Position Min. Val .).
Teaches the distance value to which the upper analog limit value (20 mA, 10 V) is assigned ( Position Max. Val .).
Teaching-in the switching outputs via IO-Link system commands
The teach-in functions are compliant with the Smart Sensor Profile specification. Manufacturer-specific extensions are included with two of the three teach-in functions.
NOTICE
Detailed descriptions of the teach-in processes can be found in the Smart Sensor Profile specification: http://www.io-link.com/share/Downloads/Smart-Sensor-Profile/IOL-Smart-Sensor-Profile-2ndEd_V10_Mar2017.pdf
Procedure:
Ä The so-called "setpoint" (1 and/or 2) is taught.
Ä In the second step, the corresponding switching function is defined.
This means that setpoint "SP" is not yet the same as switching point "SSC". Via the switching function / switching mode defined in the second step, the setpoints with the corresponding hystereses become switching points.
If, for example, teaching is performed in Window mode, both setpoints (SP1 and SP2) are taught while retaining the distance to one another.
Leuze electronic GmbH + Co. KG ODS 9 48
Starting up the device
Tab. 7.2:
Value hex / dec
0x41 / 65
0x42 / 66
0x4B / 75
0x4C / 76
IO-Link system commands for teaching the switching point modes
Command Description
Teach SP1
IOL_USERCMD_SSP_TEACH_SP1
TP
1: Setpoint SP1
TP: Teachpoint 1
Teach SP2
IOL_USERCMD_SSP_TEACH_SP2
TP
2: Setpoint SP2
TP: Teachpoint 2
Custom Teach: window
IOL_USERCMD_SSP_CUS-
TOMTEACH_WINDOW
1
3
2
1: Setpoint SP1
2: Setpoint SP2
3: WindowWidth
TP: Teachpoint
TP
Custom Teach: SP1a
IOL_USERCMD_SSP_CUS-
TOMTEACH_SP1a
=
1
1
2
3
2
Teaching the far or upper setpoint (SP1): Determine teachpoint 1 for setpoint 1
First select the target (switching point) via command TI select (Index 0x3A = 58):
• 0 = SSC1 (default)
• 1 = SSC1
• 2 = SSC2
• 255 = all together
Teaching the nearby or lower setpoint (SP2):
Determine teachpoint 2 for setpoint 2
First select the target (switching point) via command TI select (Index 0x3A = 58):
• 0 = SSC1 (default)
• 1 = SSC1
• 2 = SSC2
• 255 = all together
Manufacturer-specific teaching of both setpoints SP1 and SP2 together:
• Retaining the distance between one another
• Centered around the teach point (TP) newly determined during the teach event
First select the target (switching point) via command TI select (Index 0x3A = 58):
• 0 = SSC1 (default)
• 1 = SSC1
• 2 = SSC2
• 255 = all together
Exception :
If WindowWidth is not equal to 0, its contents are used instead of the previous distance between the setpoints (SP2-SP1).
WindowWidth is a manufacturer-specific extension that is defined additionally for each
SSC (Switching Signal Channel or switching output).
Manufacturer-specific teaching of manufacturer-specific setpoint SP1a. Setpoint SP1a is used instead of SP1 when resetting from
Window teach mode to the two SinglePoint teach modes provided its content is not equal to 0.
Teaching the offset value via IO-Link system commands
Value hex / dec
0xD4 / 212
Command
Teach Preset to Offset
Description
At the time the calculation is performed, the offset is corrected so that the nominal value stored under Preset is output.
Leuze electronic GmbH + Co. KG ODS 9 49
Starting up the device
7.2
Setting measurement value processing and filtering
Ä
Set the measure mode using the display and the control buttons (Application menu item; see chapter
3.4.6 "Application menu") or using the
Sensor Studio
configuration software (see chapter 8 "Connecting to a PC – Sensor Studio").
• Standard
Multi-purpose mode (factory setting)
• Precision
Higher accuracy for measurement tasks with lower dynamics requirements
• Ambient light
For measurements in which increased ambient light occurs.
• Less dynamic
• Increased response times
7.3
Reset to factory settings
Sensor Studio
configuration software (see chapter 8 "Connecting to a PC –
To reset the sensor via the OLED display and keyboard, proceed as follows:
Ä Switch off the voltage supply or disconnect the sensor from the voltage supply.
Ä Press the enter button and hold down the button.
Ä Switch on the voltage supply or connect the sensor to the voltage supply.
• The LEDs for PWR and switching output flash.
Ä Press the enter button again.
ð The sensor restarts, reset to the factory settings.
7.4
IO-Link interface
7.4.1
Overview
The sensors are equipped with an IO-Link 1.1 interface for configuration and measurement data output.
• The sensor transfers data packets in the TYPE_2_V process data format.
• The process data length is 32 bits. Eight status bits, eight scale bits and 16 measurement value bits are transferred. On the control-side, you can only use the measurement value bits.
• Of the eight possible control input bits, bit 0 is available for deactivation (control signal Transducer Disable ).
• The sensor cyclically transfers (minCycleTime = 0.5 ms) data packets at a baud rate of 230.4 kBaud
(COM3).
• The process data and parameters along with the corresponding system commands are described in the
IO Device Description (IODD file).
Ä Download the IODD file from the Internet ( www.leuze.com
).
Ä Unpack the ZIP archive to a separate directory. The supplementary HTML files contain a description in tabular form in German and English.
• You can configure the sensor using the Sensor Studio
configuration software (see chapter 8 "Connecting to a PC – Sensor Studio").
Leuze electronic GmbH + Co. KG ODS 9 50
Starting up the device
IO-Link system commands
Value hex / dec
0x41 / 65
0x42 / 66
0x4B / 75
0x4C / 76
0x80 / 128
0x82 / 130
0xA0 / 160
0xA1 / 161
0xB0 / 176
0xB1 / 177
0xB2 / 178
0xC3 / 195
0xC4 / 196
0xD4 / 212
Command Description
Teach SP1
Teach SP2
Custom Teach: window
Custom Teach: SP1a
Teach the far setpoint.
Teach the near setpoint.
Teach both setpoints.
Teach the alternative far setpoint.
Device Reset
Restore Factory Settings
(Factory Reset)
ClearDsUploadFlag
Restart operating software.
Reset non-volatile user settings to factory settings.
ParamDownloadStore
Teach Analog Max
Teach Preset to Offset
Delete the DsUpload flag.
Delete identifier "Accept sensor configuration in master" again.
Counterpart to command 0xA1 ParamDownload-
Store.
After reconnecting, the sensor configuration is again overwritten by the configuration in the data storage of the master.
Set the DsUpload flag.
End sensor configuration to indicate acceptance in data storage (set DsUpload flag) and, if applicable, trigger data storage via event.
Activation HighPrio Activation of the sensor (laser or measurement on) with higher priority than the Transducer Disable bit in PDout.
If activate or deactivate was selected as the input function, the input has priority over all other requirements.
Deactivation HighPrio Deactivation of the sensor (laser or measurement on) with higher priority than the Transducer
Disable bit in PDout.
If activate or deactivate was selected as the input function, the input has priority over all other requirements.
ActivationDeactivation Std-
Prio
Resetting of priority to 176 or 177. Transducer
Disable in PDout is effective again.
Only input functionalities have a higher priority.
Teach Analog Min Teaching of distance of minimum analog output value (AnalogRangeMin).
Teaching of distance of maximum analog output value (AnalogRangeMax).
Teaching of offset to achieve predefined preset value (Offset=Preset TP).
Leuze electronic GmbH + Co. KG ODS 9 51
Starting up the device
7.4.2
IO-Link process data
Process data format
• Profile: SSP4 (Mixed Measuring Sensor, Switching Measuring Sensor, Disable function)
• M-sequence TYPE_2_V
• PDIn (Sensor -> Master): 32 bits (PDI32.INT16_INT8, 8 status bits, 8 scale bits, 16 measurement value bits)
• PDOut (Master -> Sensor): 8 control input bits (PDO8.BOOL1)
Status bits
Tab. 7.3:
Bit
Value
Status bits
7
T
6
0
5
W
4
S
3
M
2
0
1
SSC2
0
SSC1
0
M
S
SSC1
SSC2
T
W
Reserved, unassigned bits (bit 2 and bit 6) are 0; initialization state is also 0
1: measurement operation
0: during start-up, teaching, deactivation
1: signal OK, reception signal is sufficient for measurement value output
Internally calculated switching states
1: Active
Toggle bit; toggles after a measurement value change due to a trigger edge
1: warning; e.g., weak reception signal
During measurement operation, the measurement value is susceptible to interference. The cause for the warning can be read out in ExtStatus Bit2:4.
Scale bits
Resolution and scaling:
• Measurement value*10 Scale [m]
• Standard resolution (Std): 0xFC = -4 (1/10 mm)
• High resolution (HR): 0xFB = -5 (1/100 mm)
Tab. 7.4:
15
Scale bits
14 13 12 11 10 9 8
Measurement values
16-bit measurement value: distance to the object – between lower and upper limit of the measurement range – in mm. Maximum -32000 … +32000.
31 30 29 28 27 26 25 24 23 22 21 20 19 18 17 16
Special values:
• No measurement values (No Measurement Data): 32764
• Upper limit of the measurement range exceeded (Out of Range (+)): 32760
• Lower limit of the measurement range exceeded (Out of Range (-)): -32760
Leuze electronic GmbH + Co. KG ODS 9 52
Starting up the device
Control inputs
Tab. 7.5:
Bit
Value
Di
R
Control input bits
7
R
6
R
5
R
Control signal Transducer Disable .
1: Deactivation of the laser
Reserved
4
R
3
R
2
R
1
R
0
Di
7.5
Serial interface
The ODS9L….8/LFH and ODS9L….8/LQZ sensors are equipped with one switching output and one serial interface, which is implemented either as an RS 232 interface (ODS9L….8/LFH) or as an RS 485
(ODS9L…8/LQZ) interface. The transmission rate can be set to between 2400 baud and 230 kbaud. For configuration and service purposes, the devices with a serial interface have an IO-Link interface on pin 4
(see chapter 7.4 "IO-Link interface").
Serial transmission is performed initially with 1 start bit, 8 data bits and 1 stop bit without parity. The port parameters can be adjusted via the menu or via IO-Link.
• ASCII measurement value
(6 bytes)
• 14-bit measurement value
(2 bytes, ODS 96 compatible)
• 16-bit measurement value
(3 bytes, ODSL 30 compatible)
• 24 bit measurement value
(4 bytes, measurement value + status byte)
• Decimal measurement value
• Remote control operation
7.5.1
Measurement value output for various transmission types
Object distance
No evaluable reception signal
Below measurement range
Within measurement range
Above measurement range
Device error
Measurement value output
65535 (signal too weak)
Distance value (linearity undefined)
Linear distance value
Distance value (linearity undefined)
65334 (signal error)
65333 (laser error)
Leuze electronic GmbH + Co. KG ODS 9 53
Starting up the device
Measurement value ASCII transmission
Transmission format: MMMMM<CR>
MMMMM or
= 5-digit measurement value in 0.1 mm (with 0.1 mm output resolution)
= 5-digit measurement value in 0.01 mm (with 0.01 mm output resolution)
<CR> = ASCII character "Carriage Return" (x0D)
Measurement value = 14 bit
Output resolution 0.01 mm / 0.1 mm (type‑dependent)
A: Low byte (bit 0=0) B: High byte (bit 0=1)
7
A
0
0
7
B
0
1
Measurement value = 16 bit
Output resolution 0.01 mm / 0.1 mm (type‑dependent)
A: Low byte (bit 0=0, bit 1=0) B: Middle byte (bit 0=1, bit 1=0) C: High byte (bit 0=0, bit 1=1)
7
0
A
0
0
7
0
B
0
1
7 x x
C
0
1 0
Measurement value = 24 bit
Output resolution 0.01 mm / 0.1 mm (type‑dependent)
A: Low byte (bit 0=0, bit 1=0) B: Middle byte 1 (bit 0=1, bit 1=0) C: Middle byte 2 (bit 0=0, bit 1=1)
D: High byte (bit 0=1, bit 1=1) M bit: Measurement value bit S bit: Status bit
A B
7 0
0 0
7 0
0 1
7
C
0
1 0
7
D
0
1 1
Decimal measurement value
Transmission format: (-)MMMMM<CR>
(-) = Minus character with negative value
MMMMM
<CR>
= Measurement value (length depends on output resolution and value)
= "Carriage Return"
Remote control operation
ASCII transfer of the measurement value on request and control of the ODS
4 digits (4 bytes) or 5 digits (5 bytes).
Fig. 7.8: Serial transmission formats ODS 9
Leuze electronic GmbH + Co. KG ODS 9 54
Starting up the device
7.5.2
Commands for remote control operation
For remote-control operation ( Serial > Com Function > Remote control ), a device address can be set between 0 and 14 ( Serial > Node Address ). In this operating mode, the ODS 9 sensor with serial interface only responds to commands from the control. The following control commands are available:
Measurement value query, 4 digits
Command
Sensor response
Byte no.
0
Sensor address
0x00 to
0x0E
" * "
(0x2A)
-
1
ASCII address tens
-
2 ones
-
3
-
4
-
5
-
6
ASCII distance measurement value
1000's
The response time of the sensor is maximum 15 ms.
100's tens ones
Measurement value query, 5 digits
Command
Sensor response
"
Byte no.
0
" * "
(0x2A)
* "
(0x2A)
1
ASCII address"0
…
9","A…
D"
ASCII address"0
…
9","A…
D"
2
"M"
(0x4D)
3
"#"
(0x23)
-
4
-
5
ASCII distance measurement value
10000's 1000's
The response time of the sensor is maximum 15 ms.
100's tens
-
6 ones
-
-
7
"#"
(0x23)
7
Status
-
-
-
8
8
"#"
(0x23)
Execute preset measurement
Command
Sensor response
Byte no.
0
" * "
(0x2A)
1
ASCII address"0
…
9","A…
D"
" * "
(0x2A)
ASCII address"0
…
9","A…
D"
2
"P"
(0x52)
Status
3
"#"
(0x23)
"#"
(0x23)
-
-
4
-
-
5
The response time of the sensor is maximum 2 s.
Detailed information on Preset/Offset: see chapter 3.4.6 "Application menu"
-
-
6
-
-
7
-
-
8
Leuze electronic GmbH + Co. KG ODS 9 55
Starting up the device
Activate sensor
Command
Sensor response
"
Byte no.
0 1
" * "
(0x2A)
* "
(0x2A)
ASCII address"0
…
9","A…
D"
ASCII address"0
…
9","A…
D"
2
"A"
(0x41)
Status
3
"#"
(0x23)
"#"
(0x23)
The response time of the sensor is maximum 15 ms.
-
-
4
Deactivate sensor
Command
Sensor response
"
Byte no.
0 1
" * "
(0x2A)
* "
(0x2A)
ASCII address"0
…
9","A…
D"
ASCII address"0
…
9","A…
D"
2
"D"
(0x44)
Status
3
"#"
(0x23)
"#"
(0x23)
The response time of the sensor is maximum 15 ms.
-
-
4
Activate/deactivate sensor via the transducer disable bit
Command
Sensor response
Byte no.
0
" * "
(0x2A)
1
ASCII address"0
…
9","A…
D"
" * "
(0x2A)
ASCII address"0
…
9","A…
D"
2
"I"
(0x49)
Status
3
"#"
(0x23)
"#"
(0x23)
The response time of the sensor is maximum 15 ms.
-
-
4
-
-
-
-
5
-
5
-
5
-
-
-
-
6
-
7
-
-
-
-
6
-
7
-
6
-
7
-
-
-
-
8
-
8
-
8
Leuze electronic GmbH + Co. KG ODS 9 56
Starting up the device
5
4
3
2
Status byte (bitwise processing)
Bit no.
7 (MSB)
6
1
0 (LSB)
Meaning
0 (reserved)
0: OK
1: other error (e.g. no measurement possible or preset unsuccessful)
1
0 (reserved)
0 (reserved)
0: sensor activated
1: sensor deactivated
0: signal OK
1: no or too low signal
0: laser OK
1: laser interference
7.5.3
Termination of data lines
The ODS9L….8/LQZ sensor features a combined transmitter and receiver component that can transmit serial data according to the RS 485 standard.
This standard defines some basic rules that should be followed in order to achieve the most reliable data transmission:
• The data lines A and B (which correspond to the pins Tx+ and Tx-) are connected to a characteristic impedance of Z
0
≈ 120 Ω via a 2-wire twisted pair cable.
• The top and end of the data line are terminated with a 120 Ω resistor. The ODS9L….8/LQZ sensor does not have an internal bus termination.
• The RS 485 bus participants are wired in a linear bus topology, i.e., the data line is fed from one bus participant to the next. Stub cables are to be avoided or to be kept as short as possible.
• The RS 485 specification assumes an inactive potential difference of UAB ≥ 200 mV between the data lines. A bus termination in the form of a voltage divider should be implemented in order to maintain this level. Usually, it is connected to the RS 485 coupling module of the control. If the coupling module does not include a bus termination with voltage divider, the following circuit may be used.
+24 V
A (Tx+)
15 k Ω
B (Tx-)
470 Ω
1,5 k Ω
Fig. 7.23: Voltage divider for the RS 485 bus termination
Leuze electronic GmbH + Co. KG ODS 9 57
Starting up the device
NOTICE
Make sure that the bus bias level (UAB ≥ 200 mV) is observed.
The RS 485 specification permits transmission rates in the megabit range for up to 32 participants. The
ODS9L….8/LQZ is designed for a typical data rate of 9,600 baud, 2,400 baud… 230 kBaud can be configured. In practice, this means that the strict requirements regarding the bus termination and the cabling are
"softened" for a few bus participants.
7.5.4
Operation on the fieldbus and Ethernet
ODS9L….8/L sensors can be connected to fieldbuses or Ethernet using the IO-Link masters from the
Leuze product range (see chapter 13.3.2 "Accessories – IO-Link master").
Leuze electronic GmbH + Co. KG ODS 9 58
Connecting to a PC – Sensor Studio
8 Connecting to a PC – Sensor Studio
The Sensor Studio configuration software – in combination with an IO-Link USB master – provides a graphical user interface for the operation, configuration and diagnosis of sensors with IO-Link configuration interface (IO-Link devices), independent of the selected process interface.
Each IO-Link device is described by a corresponding IO Device Description (IODD file). After importing the
IODD file into the configuration software, the IO-Link device connected to the IO-Link USB master can be operated, configured and checked – conveniently and in multiple languages. An IO-Link device that is not connected to the PC can be configured offline.
Configurations can be saved and reopened as projects for transferring back to the IO-Link device at a later time.
NOTICE
Only use the Sensor Studio configuration software for products manufactured by Leuze .
The Sensor Studio configuration software is offered in the following languages: German, English, French, Italian and Spanish.
The FDT frame application of the Sensor Studio supports all languages; all languages may not be supported in the IO-Link device DTM (Device Type Manager).
The Sensor Studio configuration software is designed according to the FDT/DTM concept:
• You make the individual configuration settings for the sensor in the Device Type Manager (DTM).
• The individual DTM configurations of a project can be called up via the frame application of the Field
Device Tool (FDT).
• Communication DTM: IO-Link USB master
• Device DTM: I/O-Link Device/IODD for ODS 9
NOTICE
Configuration changes only via the control!
Ä Always perform the configuration for process mode via the control and, if applicable, the interface.
In process mode, only the configuration conveyed via the control is active. The configuration changes made via Sensor Studio are only active in process mode if they were previously transmitted 1:1 to the control.
Procedure for the installation of the software and hardware:
Ä Install the Sensor Studio configuration software on the PC.
Ä Install the driver for the IO-Link USB master on the PC.
Ä Connect the IO-Link USB master to the PC.
Ä Connect the OSD 9 (IO-Link device) to the IO-Link USB master.
Ä Install IO-Link device DTM with IODD file for ODS 9 in the Sensor Studio FDT frame.
Leuze electronic GmbH + Co. KG ODS 9 59
Connecting to a PC – Sensor Studio
8.1
System requirements
To use the Sensor Studio configuration software, you need a PC or laptop with the following specifications:
Tab. 8.1: System requirements for Sensor Studio installation
Operating system
Computer
Graphics card
Windows 7 or higher
• Processor type: 1 GHz or higher
• USB interface
• CD-ROM drive
• Main memory
• 1 GB RAM (32-bit operating system)
• 2 GB RAM (64-bit operating system)
• Keyboard and mouse or touchpad
DirectX 9 graphic device with WDDM 1.0 or higher driver
Additionally required capacity for Sensor Studio and
IO-Link device DTM
350 MB hard drive memory
64 MB main memory
NOTICE
Administrator privileges on the PC are necessary for installing Sensor Studio .
8.2
Installing Sensor Studio configuration software and IO-Link USB master
NOTICE
The installation files of the Sensor Studio configuration software must be downloaded from the
Internet at www.leuze.com.
For subsequent updates, you can find the most recent version of the installation software on the
Internet at www.leuze.com
.
8.2.1
Downloading configuration software
Ä Call up the Leuze home page: www.leuze.com
Ä Enter the type designation or part number of the device as the search term.
Ä The configuration software can be found on the product page for the device under the Downloads tab.
NOTICE
On delivery, the device is configured for HID operation (Human Interface Device). The device can thereby be operated directly via the Windows application.
Leuze electronic GmbH + Co. KG ODS 9 60
Connecting to a PC – Sensor Studio
8.2.2
Installing the Sensor Studio FDT frame
NOTICE
First install the software!
Ä Do not yet connect the IO-Link USB master to the PC.
First install the software.
NOTICE
If FDT frame software is already installed on your PC, you do not need the Sensor Studio installation.
You can install the communication DTM (IO-Link USB master) and the device DTM (IO-Link device ODS 9) in the existing FDT frame.
Ä Start your PC with administrator privileges and log on.
Ä Download the Sensor Studio configuration software from the Internet: www.leuze.com
> Products
> Measuring sensors > Optical distance sensors > ODS 9 > (Device model) > Downloads > Software/driver
Ä Copy the file into a suitable folder on your hard drive and unpack the zip file.
Ä Start the SensorStudioSetup.exe
file and follow the instructions on the screen.
ð The installation wizard installs the software and places a shortcut on the desktop ( ).
8.2.3
Installing drivers for IO-Link USB master
Ä Select the IO-Link USB Master installation option and follow the instruction on the screen.
ð The installation wizard installs the software and places a shortcut on the desktop ( ).
Leuze electronic GmbH + Co. KG ODS 9 61
Connecting to a PC – Sensor Studio
8.2.4
Connecting IO-Link USB master to the PC
Ä Connect the IO-Link USB master to the plug-in power supply unit or the mains supply.
NOTICE
Included in the delivery contents of the IO-Link USB master is a USB interconnection cable for connecting the PC to the IO-Link USB master as well as a plug-in power supply unit and a short description.
The mains supply of the IO-Link USB master via the plug-in power supply unit is only activated if
IO-Link USB master and PC are connected via the USB interconnection cable.
Ä Connect the PC to the IO-Link USB master.
2
3
1
1
2
3
IO-Link USB master
Plug-in power supply unit
PC
Fig. 8.1: PC connection via the IO-Link USB master
ð The wizard for searching for new hardware starts and installs the driver for the IO-Link USB master on the PC.
8.2.5
Connecting IO-Link USB master to the sensor
Prerequisites:
• IO-Link USB master and PC are connected via the USB interconnection cable.
• IO-Link USB master is connected to the mains supply with the plug-in power supply unit.
NOTICE
Connect the plug-in power supply unit for IO-Link USB master!
Ä To connect the sensor, the plug-in power supply unit must be connected to the IO-Link USB master and the mains supply.
The voltage supply via the USB interface of the PC is permissible only for IO-devices with a current consumption of up to 40 mA at 24 V.
NOTICE
Included in the delivery contents of the IO-Link USB master is a USB interconnection cable for connecting the PC to the IO-Link USB master as well as a plug-in power supply unit and a short description.
The mains supply of the IO-Link USB master via the plug-in power supply unit is only activated if
IO-Link USB master and PC are connected via the USB interconnection cable.
Ä Connect the IO-Link USB master to the M12 connection of the sensor via an interconnection cable.
The interconnection cable is not included in the delivery contents and must be ordered separately if
needed (see chapter 13.3.1 "Accessories – PC connection").
Leuze electronic GmbH + Co. KG ODS 9 62
Connecting to a PC – Sensor Studio
8.2.6
Installing the DTM and IODD
Prerequisites:
• The sensor is connected to the PC via the IO-Link USB master.
• FDT frame and driver for IO-Link USB master are installed on the PC.
Ä Select the IO-Link device DTM (User Interface) installation option and follow the instructions on the screen.
ð The installation wizard installs the DTM and the IO Device Description (IODD) for the sensor.
NOTICE
DTM and IODD for all IO-Link devices currently available from Leuze are installed.
8.2.7
Importing device descriptions
Proceed as follows to manually add device descriptions (DTM and IODD):
Ä Unpack the downloaded ZIP file (e.g. Leuze_ODS9-20180209-IODD1.1.zip
) to a suitable directory on your hard drive, e.g. ODS9-20180209-IODD1.1
.
Ä Copy the directory ODS9-20180209-IODD1.1
to the following directory:
C:\ProgramData\Leuze\IO-Link Device DTM\IO-Link DDs
Ä Open the Sensor Studio configuration software. If a project is already open, close it using the menu command File > New .
Ä Update the DTM general catalog: Tools > DTM catalog management :
Click the [Find installed DTMs] button.
Mark the required DTMs in the Known DTMS list and move them to the Current DTM catalog list ([>] button). You need at least the DTM for the used sensor and the communication DTM IO-
Link USB Master 2.0.
Ä Click [OK] to exit DTM catalog management.
8.3
Starting the Sensor Studio configuration software
Prerequisites:
• The Sensor Studio
Ä Start the Sensor Studio configuration software by double-clicking the Sensor Studio icon ( ).
ð The mode selection of the project wizard is displayed
Ä Select the Device selection without communication connection (offline) configuration mode and click on [Next].
ð The Project Wizard displays the device selection list of the configurable devices.
Leuze electronic GmbH + Co. KG ODS 9 63
Connecting to a PC – Sensor Studio
Fig. 8.2: Device selection
NOTICE
The figure shows a similar sensor.
Ä Select the connected sensor according to the configuration in the device selection and click on [Next].
ð The device manager (DTM) of the connected sensor starts with the offline view for the Sensor Studio configuration project.
Ä Establish the online connection to the connected sensor.
In the Sensor Studio FDT frame, click on the [Establish connection with device] button ( ).
In the Sensor Studio FDT frame, click on the [Online parameters] button ( ).
ð The IO-Link USB master synchronizes with the connected sensor and the current configuration data and measurement data are displayed in the device manager (DTM).
Leuze electronic GmbH + Co. KG ODS 9 64
Connecting to a PC – Sensor Studio
Fig. 8.3: Configuration project: Sensor Studio device manager (DTM)
NOTICE
The figure shows a similar sensor.
Ä The menus of the Sensor Studio device manager (DTM) can be used to change or read out the configuration or process data of the connected sensor.
The user interface of the Sensor Studio device manager (DTM) is largely self-explanatory.
The online help system provides information on the menu items and adjustment parameters.
Select the Help menu item in the menu [?]
8.4
Short description of the Sensor Studio configuration software
This chapter contains information and explanations on the individual menu items and adjustment parameters of the Sensor Studio configuration software and the device manager (DTM) for the laser distance sensor.
NOTICE
This chapter does not include a complete description of the Sensor Studio configuration software.
Complete information on the FDT frame menu and on the functions in the device manager
(DTM) can be found in the online help system.
The device manager (DTM) of the Sensor Studio configuration software has the following main menus and functions:
• IDENTIFICATION
(see chapter 8.4.2 "IDENTIFICATION function")
• CONFIGURATION
(see chapter 8.4.3 "CONFIGURATION function")
• PROCESS
(see chapter 8.4.4 "PROCESS function")
• DIAGNOSIS
(see chapter 8.4.5 "DIAGNOSIS function")
NOTICE
The online help system displays information on the menu items and adjustment parameters for each function. Select the Help menu item in the menu [?].
Leuze electronic GmbH + Co. KG ODS 9 65
Connecting to a PC – Sensor Studio
8.4.1
FDT frame menu
NOTICE
You can find complete information on the FDT frame menu in the online help system. Select the
Help menu item in the menu [?].
8.4.2
IDENTIFICATION function
Fig. 8.4: IDENTIFICATION function
NOTICE
The figure shows a similar sensor.
• Device information, e.g., designation, order no., serial number, etc.
• Information on the IO-Link parameters of the connected sensor, e.g., Device ID, cycle time, etc.
• Assignment of the teach-in functions to the power levels defined by the duration of the teach signal
Optional for devices with input (see chapter 7.1 "Teaching and configuring output functions", )
• Technical description of the connected sensor
• Data sheet of the connected sensor
Leuze electronic GmbH + Co. KG ODS 9 66
Connecting to a PC – Sensor Studio
8.4.3
CONFIGURATION function
Fig. 8.5: CONFIGURATION function
NOTICE
The figure shows a similar sensor.
• Configuration of measure mode
• Configuration of analog output functions
• Configuration of digital switching inputs/outputs
• Configuration of local control
• Configuration of data storage
• Configuration of serial interface
Deactivation property
This function is used to determine whether, when the sensor is deactivated, the most recent measurement value to be output is frozen or whether the sensor does not output a measurement value at all. The switching outputs which are dependent on the measurement value, and an analog output (if present) behave according to the output measurement value.
• Frozen: The most recent measurement value to be output is frozen (default).
Fig. 8.6: Display: Measurement value frozen in the case of deactivation
• No Signal: No measurement value is output
Leuze electronic GmbH + Co. KG ODS 9 67
Connecting to a PC – Sensor Studio
Fig. 8.7: Display: No measurement value in the case of deactivation
Input function: Activating/deactivating sensor via switching input
The following options are available:
• Activation: Voltage on the multifunction input activates the sensor
• Deactivation: Voltage on the multifunction input deactivates the sensor
• No function
• Teach
• Trigger rising
• Trigger falling
NOTICE
If you select the Activation or Deactivation input functions, the functions via IO-Link have no effect ( Transducer Disable and the associated system commands).
Data storage
The current status of the DSUpload (Data Storage Upload) flag stored in the non-volatile memory of the sensor is displayed, provided that cyclical updating is active.
The following functions for changing the DSUpload flag are available:
• Set DSUpload Flag : Local configuration changes at the sensor remain saved when an IO-Link master is connected, and are transferred to the IO-Link master.
• Clear DSUpload Flag : Local configuration changes at the sensor are overwritten when an IO-Link master is connected.
Local configuration lock
This button is used to disable the sensor. Operation via the OLED display and keyboard is only possible after deactivation of the lock via IO-Link or using the configuration software Sensor Studio .
Leuze electronic GmbH + Co. KG ODS 9 68
Connecting to a PC – Sensor Studio
8.4.4
PROCESS function
NOTICE
The figures show a similar sensor.
Fig. 8.8: PROCESS function
• Visualization of the distance value and the states of the digital output signals.
Text-based display of the current values:
Fig. 8.9: PROCESS function – distance value and status
Leuze electronic GmbH + Co. KG ODS 9 69
Connecting to a PC – Sensor Studio
• Graphical display of the recorded measurement values, including the history:
Fig. 8.10: PROCESS function – display of the measurement values
Fig. 8.11: PROCESS function – display of the measurement values
Leuze electronic GmbH + Co. KG ODS 9 70
Connecting to a PC – Sensor Studio
8.4.5
DIAGNOSIS function
Fig. 8.12: DIAGNOSIS function
NOTICE
The figure shows a similar sensor.
• Information on the current device status
• Restart or reset of the device to factory settings
• User commands
• Set or clear the DSUpload flag
Set DSUpload Flag : Local configuration changes at the sensor remain saved when an IO-Link master is connected, and are transferred to the IO-Link master.
Clear DSUpload Flag : Local configuration changes at the sensor are overwritten when an IO-Link master is connected.
• Activate or deactivate the sensor
8.4.6
Exiting Sensor Studio
After completing the configuration settings, close the Sensor Studio configuration software.
Ä Exit the program via File > Exit .
Ä Save the configuration settings as a configuration project on the PC.
You can open the configuration project again at later time via File > Open or via the Sensor Studio project wizard ( ).
Leuze electronic GmbH + Co. KG ODS 9 71
Troubleshooting
9 Troubleshooting
9.1
What to do in case of failure?
sist in checking the proper function and troubleshooting.
In case of error, you can determine the error from the LEDs and the indicators on the display. With the error message you can determine the cause of the error and initiate measures to rectify it.
Ä Switch off the system and leave it switched off.
Ä Analyze the cause of the error using the operation indicators, the error messages and with the help of the Sensor Studio configuration software, DIAGNOSTICS menu, and rectify the error.
NOTICE
Contact Leuze subsidiary/customer service.
Ä If you are unable to rectify a fault, contact the Leuze branch responsible for you or call the
Leuze customer service (see chapter 11 "Service and support").
9.2
LED indicators
Tab. 9.1: Green LED – causes and measures
Error display
Off
Possible cause
• No supply voltage connected to the sensor
• Hardware error
Measures
• Check supply voltage
• Contact Leuze customer service (see chapter 11 "Service and support")
Tab. 9.2: Orange LED – causes and measures
Error display
Off
Possible cause
No object detected in the switching range
Measures
Position object in the configured switching range
9.3
Indicators in the display
Tab. 9.3:
Display
Display indicators – causes and measures
Possible cause
Warning message, e.g., weak reception signal
No object detected or reception signal too weak
Measures
Optimize object alignment
Position object in the measurement range
Signal failure
Sensor defective
If the icon is displayed continuously: contact
Leuze customer service (see chapter 11 "Service and support")
The current measurement value is less than the lower limit of the analog output distance
Change the setting for the lower limit of the
measurement range (see chapter 3.4.4 "Analog_Output menu")
The current measurement value is greater than the upper limit of the analog output distance
Change the setting for the upper limit of the
measurement range (see chapter 3.4.4 "Analog_Output menu")
Leuze electronic GmbH + Co. KG ODS 9 72
Care, maintenance and disposal
10 Care, maintenance and disposal
10.1
Cleaning
If there is dust on the device:
Ä Clean the device with a soft cloth; use a cleaning agent (commercially available glass cleaner) if necessary.
NOTICE
Do not use aggressive cleaning agents!
Ä Do not use aggressive cleaning agents such as thinner or acetone for cleaning the device.
Use of improper cleaning agents can damage the lens cover.
10.2
Servicing
The device does not normally require any maintenance by the operator.
Repairs to the device must only be carried out by the manufacturer.
Ä
10.3
Disposing
Ä For disposal observe the applicable national regulations regarding electronic components.
Leuze electronic GmbH + Co. KG ODS 9 73
Service and support
11 Service and support
Service hotline
You can find the contact information for the hotline in your country on our website www.leuze.com
under
Contact & Support .
Repair service and returns
Defective devices are repaired in our service centers competently and quickly. We offer you an extensive service packet to keep any system downtimes to a minimum. Our service center requires the following information:
• Your customer number
• Product description or part description
• Serial number and batch number
• Reason for requesting support together with a description
Please register the merchandise concerned. Simply register return of the merchandise on our website www.leuze.com
under Contact & Support > Repair Service & Returns .
To ensure quick and easy processing of your request, we will send you a returns order with the returns address in digital form.
What to do should servicing be required?
NOTICE
Please use this chapter as a master copy should servicing be required!
Ä Enter the contact information and fax this form together with your service order to the fax number given below.
Customer data (please complete)
Device type:
Serial number:
Firmware:
Display messages
Status of LEDs:
Error description:
Company:
Contact person/department:
Phone (direct dial):
Fax:
Street/No:
ZIP code/City:
Country:
Leuze Service fax number:
+49 7021 573-199
Leuze electronic GmbH + Co. KG ODS 9 74
Technical data
12 Technical data
12.1
Measurement data
Tab. 12.1: Measurement ranges
ODS9…-100…
ODS9…-200…
ODS9…-450…
ODS9…-650…
ODS9…-1050…
50 mm … 100 mm
50 mm … 200 mm
50 mm … 450 mm
50 mm … 650 mm
50 mm … 1050 mm
6 % … 90 % diffuse reflection
Measurement against diffusely reflective objects
Tab. 12.2: Accuracy
Resolution ODS9…-100…
ODS9…-200…
ODS9…-450…
ODS9…-650…
ODS9…-1050…
Temperature deviation
(in % of measurement value)
Accuracy
(in % of measurement value)
ODS9…-100…
ODS9…-200…
ODS9…-450…
ODS9…-650…
ODS9…-1050…
• Diffuse reflection: 6 % … 90 %
• Measure mode: Standard
• At 20 °C after warmup time of 20 minutes
0.01 mm
0.01 mm of 50 mm … 100 mm
0.1 mm of 100 mm … 200 mm
0.1 mm
0.1 mm
0.1 mm
≤ ±0.02 %/K
±0.5 %
±0.5 % of 50 mm … 100 mm
±1 % of 100 mm … 200 mm
±1 %
±1 %
±1.5% of 200 mm … 1000 mm
Leuze electronic GmbH + Co. KG ODS 9 75
Technical data
1
PP
PP
\
PP
[
\
2
2 mm y
0,25 mm
D
200 mm x y
3
6,5 mm
4,5 mm y
0,5 mm a
450 mm 650 mm y a
A x y
Gray area
1
2
3
Larger measurement distances
Fig. 12.1:
Measurement range
Measurement distance
Maximum measurement error (+/-)
Permissible measurement deviation
Accuracy up to 100 mm, a = 0.5% of the measurement value
Accuracy up to 200 mm, a = 1% of the measurement value
Accuracy up to 450 mm and 650 mm, a = 1% of the measurement value
Accuracy up to 1050 mm, a = 1.5% of the measurement value
ODS 9 measurement accuracy
Leuze electronic GmbH + Co. KG ODS 9 x
76
Technical data
Tab. 12.3: Reproducibility
3 sigma
Diffuse reflection
Reproducibility available
12.2
Optical data
Tab. 12.4: Optical data
Light source
ODS9…-100/-200/-450/-650…: 0.15 mm
ODS9…-1050…: 0.6 mm
6 % … 90 %
At 20 °C after warmup time of 20 minutes
Wavelength
Pulse duration
Max. output power (peak)
Light spot
Laser diode
ODS9L1: Laser class 1 acc. to IEC 60825-1:2014
ODS9L2: Laser class 2 acc. to IEC 60825-1:2014
650 nm (red, visible)
22 ms
ODS9L1...: 0.78 mW
ODS9L2...: 1.8 mW approx. 1 mm x 1 mm
12.3
Indicators and operational controls
Tab. 12.5: Indicators/operational controls
Display
Keyboard
LEDs on the control panel
OLED display
Two buttons
PWR: status LED, green
SSC: LED for object detection/switching output, orange
Leuze electronic GmbH + Co. KG ODS 9 77
Technical data
12.4
Electrical data
Tab. 12.6: Electrical equipment
Operating voltage U
B
Supply voltage
Residual ripple
Open-circuit current
Switching output
Signal voltage high/low
Analog output
ODS9L1.8/LA…
IO-Link
18 V … 30 V DC incl. residual ripple
≤ 15 % of U
B
≤ 50 mA
Push-pull switching output
NOTE!
The push-pull switching outputs must not be connected in parallel.
≥ (U
B
- 2 V) / ≤ 2 V
• Voltage
1 V … 10 V / 0 V … 10 V
R
L
≥ 2 kΩ
• Current (factory setting)
4 mA … 20 mA, R
L
≤ 500 Ω
COM3 (230.4 kBaud), Vers. 1.1
min. cycle time: 0.5 ms
SIO is supported
9,600 baud (factory setting, baud rate configurable) Serial interface
RS 232 / RS 485
12.5
Mechanical data
Tab. 12.7: Mechanical data
Housing
Optics cover
Weight
Connection type
Plastic
Glass, ODS9Lx.8/xxx.P: plastic
85 g
M12 connector, turnable by 90°
12.6
Environmental data
Tab. 12.8: Environmental data
Ambient temperature (operation)
Ambient temperature (storage)
Protective circuit
VDE protection class
Degree of protection with correctly screwed-on M12 connector
Standards applied
-20 °C … +50 °C
-30 °C … +70 °C
Transient protection
Polarity reversal protection
Short circuit protection for all outputs
III
IP67
IEC 60947-5-2
Leuze electronic GmbH + Co. KG ODS 9 78
Technical data
12.7
Dimensioned drawings
A
B
C
D
E
F
G
H
J
All dimensions in mm
Reference edge for the measurement
Optical axis
M12 connector, turnable by 90°
Receiver
Transmitter
Display
Yellow LED – switching output state
Green LED – operating state
Control buttons
Fig. 12.2: Dimensioned drawing ODS 9 with M12 connector
Leuze electronic GmbH + Co. KG ODS 9 79
Technical data
12.8
Dimensioned drawings: Accessories
all dimensions in mm
Fig. 12.3: Dimensioned drawing mounting system BTU 300M-D10/D12/D14 all dimensions in mm
Fig. 12.4: Dimensioned drawing mounting bracket BT 300M.5
Leuze electronic GmbH + Co. KG ODS 9 80
Order guide and accessories
13 Order guide and accessories
13.1
Type overview ODS 9
Optical distance sensors, measurement against object
NOTICE
The types given in the overview below can change or be supplemented with further models.
NOTICE
If the IO-Link interface is not used, all device models are equipped with a switching output on pin 4.
50136953
50137824
50137823
50137822
50137821
50138326
50138327
50138328
Tab. 13.1: Type overview ODS 9
Part no.
50137820
Part designation
ODS9L2.8/LAK-100-M12
50137819 ODS9L2.8/LAK-200-M12
50137818
50137817
50146971
50137816
50137815
50137813
ODS9L2.8/LAK-450-M12
ODS9L2.8/LAK-650-M12
ODS9L1.8/LAK-1050-M12
ODS9L2.8/LA6-100-M12
ODS9L2.8/LA6-200-M12
ODS9L2.8/LA6-450-M12
ODS9L2.8/LA6-650-M12
ODS9L2.8/L6X-100-M12
ODS9L2.8/L6X-200-M12
ODS9L2.8/L6X-450-M12
ODS9L2.8/L6X-650-M12
ODS9L2.8/LFH-100-M12
ODS9L2.8/LFH-450-M12
ODS9L2.8/LQZ-100-M12
Leuze electronic GmbH + Co. KG ODS 9
Description
100 mm max. measurement distance, IO-Link interface, analog output, multifunction input
200 mm max. measurement distance, IO-Link interface, analog output, multifunction input
450 mm max. measurement distance, IO-Link interface, analog output, multifunction input
650 mm max. measurement distance, IO-Link interface, analog output, multifunction input
1050 mm max. measurement distance, IO-Link interface, analog output, multifunction input
100 mm max. measurement distance, IO-Link interface, analog output, second multifunction input
200 mm max. measurement distance, IO-Link interface, analog output, second multifunction input
450 mm max. measurement distance, IO-Link interface, analog output, second multifunction input
650 mm max. measurement distance, IO-Link interface, analog output, second multifunction input
100 mm max. measurement distance, IO-Link interface, switching output
200 mm max. measurement distance, IO-Link interface, switching output
450 mm max. measurement distance, IO-Link interface, switching output
650 mm max. measurement distance, IO-Link interface, switching output
100 mm max. measurement distance, IO-Link interface, serial interface RS 232
450 mm max. measurement distance, IO-Link interface, serial interface RS 232
100 mm max. measurement distance, IO-Link interface, serial interface RS 485
81
Order guide and accessories
Part no.
50138329
50138330
50141322
Part designation
ODS9L2.8/LQZ-450-M12
ODS9L2.8/LQZ-650-M12
ODS9L1.8/LAK-450-M12
Description
450 mm max. measurement distance, IO-Link interface, serial interface RS 485
650 mm max. measurement distance, IO-Link interface, serial interface RS 485
450 mm max. measurement distance, IO-Link interface, switching output
13.2
Accessories – cables and connectors
NOTICE
Ä To avoid electromagnetic interference, use shielded connection cables when using the analog output.
Tab. 13.2: Cables and connectors
Part no.
50020501
Part designation
KD 095-5A
50020502 KD 095-5
50132077
50133842
50133855
KD U-M12-5A-V1-020
KD U-M12-5W-V1-020
KD S-M12-5A-V1-020
50132079
50133802
50133856
KD U-M12-5A-V1-050
KD U-M12-5W-V1-050
KD S-M12-5A-V1-050
50132080
50133803
50133857
KD U-M12-5A-V1-100
KD U-M12-5W-V1-100
KD S-M12-5A-V1-100
50130692 KD U-M12-4W-P1-020
50130728 KD S-M12-4W-P1-020
50133839 KD U-M12-5A-P1-020
Leuze electronic GmbH + Co. KG ODS 9
Description
M12 connector (cable socket), user-configurable, 5pin, axial
M12 connector (cable socket), user-configurable, 5pin, angled
Connection cable with M12 connector on one end,
5-pin, M12, axial, length 2 m, PVC sheathing
Connection cable with M12 connector on one end,
5-pin, M12, angled, length 2 m, PVC sheathing
Shielded connection cable with M12 connector on one end, 5-pin, M12, axial, length 2 m, PVC sheathing
Connection cable with M12 connector on one end,
5-pin, M12, axial, length 5 m, PVC sheathing
Connection cable with M12 connector on one end,
5-pin, M12, angled, length 5 m, PVC sheathing
Shielded connection cable with M12 connector on one end, 5-pin, M12, axial, length 5 m, PVC sheathing
Connection cable with M12 connector on one end,
5-pin, M12, axial, length 10 m, PVC sheathing
Connection cable with M12 connector on one end,
5-pin, M12, angled, length 10 m, PVC sheathing
Shielded connection cable with M12 connector on one end, 5-pin, M12, axial, length 10 m, PVC sheathing
PUR connection cable with M12 connector on one end, 4-pin, M12, angled, length 2 m
Only for devices ODS9…/L6X…
Shielded PUR connection cable with M12 connector on one end, 4-pin, M12, angled, length 2 m
Only for devices ODS9…/L6X…
PUR connection cable with M12 connector on one end, 5-pin, M12, axial, length 2 m
82
Order guide and accessories
Part no.
50132536
50133859
50133862
50133841
50133860
50115049
Part designation
KD U-M12-5W-P1-020
KD S-M12-5A-P1-020
KD S-M12-5W-P1-020
KD U-M12-5A-P1-050
KD S-M12-5W-P1-050
K-DS M12A-MA-5P-3m-S-PUR
Description
PUR connection cable with M12 connector on one end, 5-pin, M12, angled, length 2 m
Shielded PUR connection cable with M12 connector on one end, 5-pin, M12, axial, length 2 m
Shielded PUR connection cable with M12 connector on one end, 5-pin, M12, angled, length 2 m
PUR connection cable with M12 connector on one end, 5-pin, M12, axial, length 5 m
Shielded PUR connection cable with M12 connector on one end, 5-pin, M12, axial, length 5 m
PUR connection cable with RS232 to MA 2xxi modular connection units, M12 connector on one end, 5pin, A-coded, axial, 2nd connection JST ZHR, 12pin, length 3 m
13.3
Other accessories
Tab. 13.3: Other accessories
Part no.
50117251
50117252
50117253
50118543
Part designation
BTU 300M-D14
BTU 300M-D12
BTU 300M-D10
BT 300M.5
Description
Mounting system for mounting on rods Ø 14 mm
Mounting system for mounting on rods Ø 12 mm
Mounting system for mounting on rods Ø 10 mm
Mounting bracket
13.3.1 Accessories – PC connection
Tab. 13.4: Accessories - PC connection configuration
Part no.
Part designation
IO-Link USB master V2.0
50121098
50110126
Description
SET MD12-US2-IL1.1 + accessories IO-Link USB master V2.0
Plug-in power supply unit (24 V/24 W) with international adapters
High-speed USB 2.0 connection cable; USB A to
Mini-USB
Data carrier with software, drivers and documentation
K-DS M12A-M12A-4P-2m-PVC Interconnection cable with M12 connector on both ends, 4-pin, M12, axial, length 2 m, PVC sheathing
Leuze electronic GmbH + Co. KG ODS 9 83
Order guide and accessories
13.3.2 Accessories – IO-Link master
Tab. 13.5: Accessories – IO-Link master
Part no.
50131482
Part designation
MD748i-11-42/L5-2222
50131483 MD248i-12-8K/L4-2R2K
50131484 MD758i-11-42/L5-2222
50131485 MD258i-12-8K/L4-2R2K
Description
IO-Link master
Interfaces: PROFINET
IO-Link master for top-hat rail mounting in switch cabinet
Interfaces: PROFINET
IO-Link master
Interfaces: EtherNet/IP, Modbus TCP
IO-Link master for top-hat rail mounting in switch cabinet
Interfaces: EtherNet/IP, Modbus TCP
Leuze electronic GmbH + Co. KG ODS 9 84
EC Declaration of Conformity
14 EC Declaration of Conformity
The optical distance sensor systems of the ODS 9 series were developed and manufactured in accordance with the applicable European standards and directives.
The manufacturer of the product, Leuze electronic GmbH + Co. KG in D-73277 Owen, possesses a certified quality assurance system in accordance with ISO 9001.
Leuze electronic GmbH + Co. KG ODS 9 85
advertisement
Related manuals
advertisement
Table of contents
- 6 About this document
- 6 Used symbols and signal words
- 8 Important terms
- 9 Safety
- 9 Intended use
- 9 Foreseeable misuse
- 10 Competent persons
- 10 Disclaimer
- 11 Laser safety notices
- 14 Device description
- 14 Device overview
- 14 General information
- 15 Operating principle
- 15 Performance characteristics
- 15 Accessories
- 16 Connection technology
- 16 Indicators and operational controls
- 16 LED indicators
- 16 Control buttons
- 17 Display
- 19 Meaning of the display icons
- 19 Configuration / menu structure
- 20 Input menu
- 20 Output_SSC1 menu
- 21 Output_SSC2 menu
- 23 Analog_Output menu
- 23 Serial Menu
- 25 Application menu
- 30 Settings menu
- 31 Ending configuration
- 31 Configuration example
- 34 Applications
- 34 Wood width measurement
- 35 Assembly inspection
- 36 Mounting
- 36 Mounting with mounting system
- 37 Electrical connection
- 37 Overview
- 37 Pin assignment
- 40 Starting up the device
- 40 Teaching and configuring output functions
- 40 Setting the analog output
- 41 Setting the switching outputs
- 46 Teach-in / teach
- 46 Teaching the output functions via the multifunction input
- 48 Teaching the output functions via the IO-Link system commands
- 50 Setting measurement value processing and filtering
- 50 Reset to factory settings
- 50 IO-Link interface
- 50 Overview
- 52 IO-Link process data
- 53 Serial interface
- 53 Measurement value output for various transmission types
- 55 Commands for remote control operation
- 57 Termination of data lines
- 58 Operation on the fieldbus and Ethernet
- 59 Connecting to a PC – Sensor Studio
- 60 System requirements
- 60 Installing Sensor Studio configuration software and IO-Link USB master
- 60 Downloading configuration software
- 61 Installing the Sensor Studio FDT frame
- 61 Installing drivers for IO-Link USB master
- 62 Connecting IO-Link USB master to the PC
- 62 Connecting IO-Link USB master to the sensor
- 63 Installing the DTM and IODD
- 63 Importing device descriptions
- 63 Starting the Sensor Studio configuration software
- 65 Short description of the Sensor Studio configuration software
- 66 FDT frame menu
- 66 IDENTIFICATION function
- 67 CONFIGURATION function
- 69 PROCESS function
- 71 DIAGNOSIS function
- 71 Exiting Sensor Studio
- 72 Troubleshooting
- 72 What to do in case of failure?
- 72 LED indicators
- 72 Indicators in the display
- 73 Care, maintenance and disposal
- 73 10.1 Cleaning
- 73 10.2 Servicing
- 73 10.3 Disposing
- 74 Service and support
- 75 Technical data
- 75 12.1 Measurement data
- 77 12.2 Optical data
- 77 12.3 Indicators and operational controls
- 78 12.4 Electrical data
- 78 12.5 Mechanical data
- 78 12.6 Environmental data
- 79 12.7 Dimensioned drawings
- 80 12.8 Dimensioned drawings: Accessories
- 81 Order guide and accessories
- 81 13.1 Type overview ODS
- 82 13.2 Accessories – cables and connectors
- 83 13.3 Other accessories
- 83 Accessories – PC connection
- 84 Accessories – IO-Link master
- 85 EC Declaration of Conformity