- Home
- Do-It-Yourself tools
- Power tools
- Paint Sprayer
- Graco
- 308274E GM 1030 Air Spray Gun
- Owner's manual
advertisement
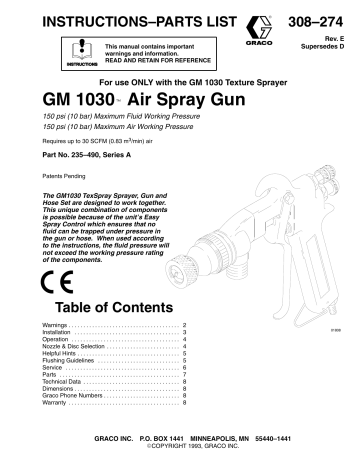
INSTRUCTIONS–PARTS LIST
This manual contains important warnings and information.
READ AND RETAIN FOR REFERENCE
For use ONLY with the GM 1030 Texture Sprayer
GM 1030 Air Spray Gun
150 psi (10 bar) Maximum Fluid Working Pressure
150 psi (10 bar) Maximum Air Working Pressure
Requires up to 30 SCFM (0.83 m 3 /min) air
Part No. 235–490, Series A
308–274
Rev. E
Supersedes D
Patents Pending
The GM1030 TexSpray Sprayer, Gun and
Hose Set are designed to work together.
This unique combination of components is possible because of the unit’s Easy
Spray Control which ensures that no fluid can be trapped under pressure in the gun or hose. When used according to the instructions, the fluid pressure will not exceed the working pressure rating of the components.
Table of Contents
Warnings
Installation
. . . . . . . . . . . . . . . . . . . . . . . . . . . . . . . . . . . . . .
. . . . . . . . . . . . . . . . . . . . . . . . . . . . . . . . . . . .
Operation . . . . . . . . . . . . . . . . . . . . . . . . . . . . . . . . . . . . .
Nozzle & Disc Selection . . . . . . . . . . . . . . . . . . . . . . . . .
Helpful Hints . . . . . . . . . . . . . . . . . . . . . . . . . . . . . . . . . . .
Flushing Guidelines . . . . . . . . . . . . . . . . . . . . . . . . . . . .
Service
Parts
. . . . . . . . . . . . . . . . . . . . . . . . . . . . . . . . . . . . . . .
. . . . . . . . . . . . . . . . . . . . . . . . . . . . . . . . . . . . . . . . .
Technical Data . . . . . . . . . . . . . . . . . . . . . . . . . . . . . . . . .
Dimensions . . . . . . . . . . . . . . . . . . . . . . . . . . . . . . . . . . . .
Graco Phone Numbers . . . . . . . . . . . . . . . . . . . . . . . . . .
Warranty . . . . . . . . . . . . . . . . . . . . . . . . . . . . . . . . . . . . . .
6
7
5
5
8
8
8
8
4
4
2
3
GRACO INC. P.O. BOX 1441 MINNEAPOLIS, MN 55440–1441
COPYRIGHT 1993, GRACO INC.
Warning Symbol
WARNING his symbol alerts you to the possibility of serious injury or death if you do not follow the instructions.
Symbols
Caution Symbol
CAUTION
This symbol alerts you to the possibility of damage to or destruction of equipment if you do not follow the instructions.
INSTRUCTIONS
EQUIPMENT MISUSE HAZARD
Equipment misuse can cause the equipment to rupture, malfunction or start unexpectedly and result in serious injury.
D This equipment is for professional use only.
D Read all instruction manuals, tags, and labels before operating the equipment.
D Use the equipment only for its intended purpose. If you are uncertain about the usage, call Graco
Technical Assistance at 1–800–543–0339.
D The TexSpray Gun and the GM 1030 TexSpray Sprayer is intended for use outside and with texture materials at low application pressures. If you are using the sprayer for any other application, including the high pressure pump accessory, GM 3012, you must provide complete system grounding, as explained in manual 308–127.
D The TexSpray Gun, P/N 235–490, is for use ONLY with the GM 1030 TexSpray system, P/N
231–300 which is specially designed so that the fluid pressure of the gun will not exceed the working pressure rating of the components.
D Do not exceed the maximum working pressure of the lowest rated system component. This gun has a 150 psi (10 bar) maximum fluid working pressure at a 125 psi (9 bar) maximum incoming air pressure.
D Do not alter or modify this equipment. Use only genuine Graco parts and accessories.
D Check equipment daily. Repair or replace worn or damaged parts immediately.
D Do not lift pressurized equipment.
D Route the hoses away from the traffic areas, sharp edges, moving parts, and hot surfaces. Do not expose Graco hoses to temperatures above 180 _ F (82 _ C) or below –40 _ F (–40 _ C).
D Do not use the hoses to pull the equipment.
D The material hose must have a spring guard at the end which is installed at the outlet of the automatic pressure drain valve. The spring guard helps protect the hose from stress and strain which could cause the hose to rupture.
D Use fluids or solvents that are compatible with the equipment wetted parts. See the Technical
Data section of all the equipment manuals. Read the fluid and solvent manufacturer’s warnings.
D Do not use 1,1,1-trichloroethane, methylene chloride, other halogenated hydrocarbon solvents or fluids containing such solvents in this equipment, which contains aluminum and/or zinc parts.
Such use could result in a serious chemical reaction, with the possibility of explosion, which could cause death, serious injury and/or substantial property damage.
D Comply with all applicable local, state and national fire, electrical and other safety regulations.
D Wear ear protection when operating this equipment. See Sound Data in TECHNICAL DATA .
TOXIC FLUID HAZARD
Hazardous fluids or toxic fumes can cause a serious injury or death if the fluid is swallowed or splashed in the eyes or on the skin or if the fumes are inhaled.
Know the specific hazards of the fluid you are using.
Store hazardous fluid in an approved container. Dispose hazardous fluid according to all local, state and national guidelines.
Wear appropriate clothing, gloves, eyewear and respirator.
MOVING PARTS HAZARD
Moving parts or parts that start unexpectedly can pinch or amputate fingers or cause other serious injury.
Keep clear of any moving parts, such as the connecting link and pin of the pump, when starting or operating or checking the equipment.
Installation
How the Gun and Sprayer Work Together
This gun is designed for use only with the GM 1030
Texture Sprayer. Refer to the sprayer manual for a detailed explanation of how the sprayer’s Easy Spray
Control is controlled by the gun. The following information is a summary.
2. See page 5 for disc and nozzle recommendations. Install the disc (2) and nozzle (5) on the gun as shown in Fig. 1. Tighten the retaining rings (1 and 3) snugly, but do not use a wrench.
3. Refer to the GM1030 sprayer manual for how to start and prime the sprayer.
11
The gun will not operate if the Easy Spray Control is in the OFF/RELIEVE PRESSURE mode.
When the Easy Spray Control is in the SPRAY/
FILL HOSE mode, fully triggering the gun starts the pump. Releasing the gun trigger stops the pump and opens the sprayer’s Automatic Pressure Drain
Valve which relieves the system pressure. This automatic pressure relief and the special TexSpray hoses and pump design eliminates blasts of material when the gun is triggered and eliminates “spray pulsing” to ensure consistent atomization.
Setup
1. Connect the air and material hoses to the gun and tighten securely.
2
Fig. 1
1
4
3
5
20
Operation
WARNING
EQUIPMENT MISUSE HAZARD
In the GM 1030 Texture Sprayer, the fluid pressure is relieved automatically when
INSTRUCTIONS the gun trigger is released. However , to further reduce the risk of injury, including injury from moving parts, always follow the Pressure Relief
Procedure when you are not spraying and before checking or adjusting the system.
TIP: More fluid flow = more air, and less fluid = less air.
4. If you cannot get a good spray pattern, try adjusting the air regulator pressure or try another spray disc and nozzle combination.
To Prevent Material Surge at the Beginning of a Spray Pattern
Pressure Relief Procedure
1. Turn the Easy Spray Control to OFF.
2. Turn the engine stop lever to OFF.
1.
Always trigger the gun fully.
If the gun is triggered partially, which only triggers the air portion of the system, the pump will start and pressurize the hoses. Then, when you complete the triggering action, you will get a blast of unatomized material.
How to Adjust the Spray Pattern
1. Be sure the Air Control Valve (11) is turned in fully to prevent air from mixing with the fluid. Note that the air will exit the rear of the gun.
2. While triggering the gun, adjust the engine RPM to determine fluid flow and pressure. A good starting point is to adjust the fluid flow until you have an 8 in. (20 cm) stream.
3. Holding the gun 18 to 30 in (0.5 to 1.0 m) from a test surface, test the spray pattern while turning out the gun’s Air Control Valve (11) which allows the air to atomize the fluid. Adjust the Air Control
Valve to obtain the desired spray pattern.
2.
When you release the gun trigger , allow the material to completely depressurize before triggering the gun again.
Failure to do this will result in spraying some unatomized material, and may cause material to back up into the gun air passages and block air flow. Longer hoses and heavier material may take several seconds longer to depressurize.
As you test the spray pattern, also determine how long it takes to depressurize the system and keep that in mind as you are working.
Fluid Nozzle and Spray Disc Selection
Three spray discs and nozzles are supplied with the sprayer. The nozzles are numbered 1, 2 or 3 – the larger the number the more scfm is required. These parts can be interchanged to produce a pattern suitable for each job. Use the chart below to help determine the right combination for your application.
Material Fluid
Nozzle
Elastomerics
Simulated Accoustical
Splatter Coat* and
Knockdown
Orange Peel
#3
#2
#1
#2
Fine
1/8”
1/8”
1/4” or 3/8”
1/8” or 1/4”
* When spraying interior splatter coat with heavy
(unthinned or slightly thinned) drywall mud and the desired flow rate is 1 gpm or less, we recommend using the accessory 2 gpm pump, Model 235–965.
Spray Discs (by aggregate size)
Medium
1/4”
1/4” n/a
Coarse
1/4” or 3/8”
1/4” or 3/8” n/a n/a n/a
Extra Coarse
3/8”
3/8” n/a n/a
Helpful Hints
A spraying distance of 18 to 30 in (0.5 to 1.0 m) is recommended for most applications.
Keep the gun triggered and moving as much as possible.
To spray a small, confined area, you may be able to restrict the spray pattern sufficiently by restricting the gun’s air. For further adjustment, reduce the engine RPM.
Set the gun’s trigger bail (20) to hold the trigger open and reduce operator fatigue on large surface areas.
Check the material consistency periodically.
The material may thicken as it sits and slow down production. Check and thin the material as needed to maintain proper consistency.
When releasing the trigger wait until the system pressure is fully relieved before triggering the gun again to eliminate a blast of unatomized material.
If fluid from the gun is pulsing and you are spraying thin material, install an accessory Flow
Restrictor, P/N 190–109 to restrict the flow of fluid to the gun. Install as shown in Fig. 2.
Simulated acoustic material with polystyrene texture compresses easily so the system pressure builds up more slowly.
When spraying elastomerics, maintain a wet edge, spray vertical passes followed by horizontal passes. Then hold the gun further away and “dust” the area to blend in the pattern.
To spray ceilings as high as 9 to 12 ft (3 to 4 m) without using stilts or scaffolding, use a higher engine RPM and open the gun’s Air Adjustment
Valve more to project the material onto the ceiling, and increase the regulator air pressure.
Fig. 2
E
04628
Flushing
1. Setup – prepare a pail of warm, soapy water or solvent. Turn the gun’s Air Control Valve all the way in. Start the engine with the sprayer’s Easy
Spray Control in the OFF mode.
2. Turn the Easy Spray Control to SPRAY .
4. Release the trigger – pressure will be relieved automatically.
5. Turn the Easy Spray control to PRIME .
6. Circulate the flushing fluid through the pump, siphon hose and drain hose until well flushed.
3. Trigger the gun. Direct the spray material into a waste container until the flushing fluid appears.
Now direct the flushing fluid into the flushing pail, secure the trigger bail to keep the gun triggered and circulate the fluid until the gun and hose are thoroughly flushed.
7. If you are going to store the sprayer, set the sprayer’s Easy Spray Control to OFF/RELIEVE PRES-
SURE , turn the engine switch off, and remove the spark plug cable.
1
2
3
4
WARNING
To reduce the risk of a serious injury due to the sprayer starting unexpectedly, always shut off the engine and disconnect the spark plug before performing any checks or service.
Service
If air is leaking around the air valve
1. Follow the Pressure Relief Procedure.
2. Remove the trigger (24).
3. Unscrew the packing nut (31). Grasp the seat (29) and pull it out. Remove the remaining parts.
Air valve
Fluid valve
Fluid inlet
Air inlet 1
4. Check for worn or damaged parts and replace as necessary. Lubricate all packings, o–rings and moving parts and reassemble the gun. Tighten the packing nut (31) just enough to prevent leaking, but don’t over compress the packings.
2
3
Fig. 3 4
01809
NOTE: Refer to the Parts Drawing on page 7 during the repair.
If air is not flowing to nozzle
1. Follow the Pressure Relief Procedure.
2. Remove the disk and nozzle assembly.
3. Remove the trigger (24).
4. Unscrew the air control valve (11) and clean.
5. Use a 3/8 in. hex key wrench to unscrew the head bolt (10).
6. Unscrew the spring and valve guide (15). Remove the gasket (17) and o–ring (16).
7. Unscrew the packing nut (31).
8. Grasp the valve stem (27) and pull it out the front of the gun.
9. Clean and inspect all parts. Replace worn or damaged parts.
10. Lubricate all packings, o–rings and moving parts.
Reassemble the gun. Tighten the packing nut (31) just enough to prevent leaking, but don’t over compress the packings.
Parts
9
1
2
3
8
4
5
6
7
31
30
16
29
28
27
26
25
10
11
13
12
20
21
22
23
18
17
16
15
19
24
14
01829
1
2
3
4
5
8
9
6
7
10
11
12
13
14
Model 235–490, Series A
Includes items 1 to 31
Ref
No.
Part No.
Description Qty
188–354 RETAINING NUT
SPRAY TIP DISKS (all sizes included)
235–579 1/8” orifice
235–580 1/4” orifice
235–581 3/8” orifice
160–225 LOCKRING, nozzle
188–353 HOUSING ADAPTER
GUN NOZZLE (all sizes included)
188–428 Size 1
188–429 Size 2
188–430 Size 3
188–447 VALVE STEM
111–967 QUAD RING PACKING
188–445 HEAD
160–217 PIVOT PIN
160–233 BOLT
235–741 AIR CONTROL VALVE KIT
160–231 SCREW, fluid valve regulating
111–966 SPRING, fluid valve
160–227 PUSH ROD, fluid valve
1
1
1
1
1
1
1
1
1
1
1
1
1
1
1
1
1
1
Ref
No.
19
20
21
22
23
24
15
16
17
18
25
26
27
28
29
30
31
Part No.
Description
160–232 GUIDE, spring and valve
156–082 O–RING
150–925 GASKET, copper
203–953 LOCKSCREW, trigger
188–446 GUN BODY
160–215 TRIGGER LATCH
160–222 AIR INLET ADAPTER, 3/8 npsm
154–741 O–RING
161–274 PLUG
160–239 TRIGGER
161–319 SPRING, air valve
177–139 POPPET, valve
169–943 AIR VALVE STEM
160–910 WASHER
160–229 AIR VALVE SEAT
160–240 PACKING, air valve stem
160–228 PACKING NUT, air valve stem
Qty
1
1
1
1
1
1
1
1
1
2
1
1
1
1
1
1
1
Keep these spare parts on hand to reduce down time.
Technical Data
Maximum Fluid Working Pressure
Maximum Air Working Pressure
Air Requirements . . . . . . . . . . . . .
. . . 150 psi (10 bar)
. . . . . . . 125 psi (9 bar)
30 scfm (0.84 m 3 /min)
Fluid Inlet Size
Air Inlet Size
. . . . . . . . . . . . . . . . . . . . . . . . .
. . . . . . . . . . . . . . . . . . . . . . . . .
3/4 npt(m)
3/8 npsm(m)
Wetted Parts . . . . . . . . . . . Aluminum, Stainless Steel,
Steel, Viton ,Delrin
Sound Data (gun only):
Sound Pressure Level
Sound Power Level
. . . . . . . . . . . . . . . . . .
. . . . . . . . . . . . . . . . . . .
96dB(A)*
104dB(A)*
* Spraying simulated acoustical texture under typical conditions as specified by the material manufacturer.
Viton and Delrin are registered trademarks of the
Company
Dimensions
Weight (dry, without packaging)
Height
. . . . . . . .
. . . . . . . . . . . . . . . . . . . . . . . . . .
34 oz (980 g)
A: 8.9” (226 mm)
Length
Width
. . . . . . . . . . . . . . . . . . . . . . . . . .
. . . . . . . . . . . . . . . . . . . . . . . . . . . .
B: 9.0” (229 mm)
C: 1.6” (41 mm)
B
A
Graco Phone
Numbers
C
TO PLACE AN ORDER , contact your Graco distributor, or call this number to identify the distributor closest to you: 1–800–328–0211 Toll Free
Manual
Change Summary
FOR TECHNICAL ASSIST ANCE, service repair information or assistance regarding the application of
Graco equipment: 1–800–543–0339 Toll Free
Added CE mark to cover, Sound Data to Technical Data and ear protection warning to Warnings on page 2.
The Graco Warranty and Disclaimers
WARRANTY
Graco warrants all equipment manufactured by it and bearing its name to be free from defects in material and workmanship on the date of sale by an authorized Graco distributor to the original purchaser for use. As purchaser’s sole remedy for breach of this warranty, Graco will, for a period of twelve months from the date of sale, repair or replace any part of the equipment proven defective. This warranty applies only when the equipment is installed, operated and maintained in accordance with Graco’s written recommendations.
This warranty does not cover, and Graco shall not be liable for, any malfunction, damage or wear caused by faulty installation, misapplication, abrasion, corrosion, inadequate or improper maintenance, negligence, accident, tampering, or substitution of non–Graco component parts. Nor shall Graco be liable for malfunction, damage or wear caused by the incompatibility with Graco equipment of structures, accessories, equipment or materials not supplied by Graco, or the improper design, manufacture, installation, operation or maintenance of structures, accessories, equipment or materials not supplied by Graco.
This warranty is conditioned upon the prepaid return of the equipment claimed to be defective to an authorized Graco distributor for verification of the claim. If the claimed defect is verified, Graco will repair or replace free of charge any defective parts. The equipment will be returned to the original purchaser transportation prepaid. If inspection of the equipment does not disclose any defect in material or workmanship, repairs will be made at a reasonable charge, which charges may include the costs of parts, labor and transportation.
DISCLAIMERS AND LIMITATIONS
The terms of this warranty constitute purchaser’s sole and exclusive remedy and are in lieu of any other warranties (express or implied), including warranty of merchantability or warranty of fitness for a particular purpose , and of any non–contractual liabilities, including product liabilities, based on negligence or strict liability. Every form of liability for direct, special or consequential damages or loss is expressly excluded and denied. In no case shall Graco’s liability exceed the amount of the purchase price.
Any action for breach of warranty must be brought within two (2) years of the date of sale.
EQUIPMENT NOT COVERED BY GRACO WARRANTY
Graco makes no warranty, and disclaims all implied warranties of merchantability and fitness for a particular purpose , with respect to accessories, equipment, materials, or components sold but not manufactured by Graco. These items sold, but not manufactured by Graco (such as electric motor, switches, hose, etc.) are subject to the warranty, if any, of their manufacturer.
Graco will provide purchaser with reasonable assistance in making any claim for breach of these warranties.
Sales Offices: Atlanta, Chicago, Detroit, Los Angeles
Foreign Offices: Belgium; Canada; England; Korea; Switzerland; France; Germany; Hong Kong; Japan
GRACO INC. P.O. BOX 1441 MINNEAPOLIS, MN 55440–1441
PRINTED IN U.S.A. 308–274 2/93 Revised May 1995
advertisement
* Your assessment is very important for improving the workof artificial intelligence, which forms the content of this project