Sick VISIC100SF - Gas adjustment kit Operating instructions
Add to My manuals30 Pages
SICK VISIC100SF - Gas adjustment kit is used to adjust the CO, NO and NO2 gas sensors used in the VISIC100SF. It is not applicable for other SICK devices. The adjustment tool has a display and operating elements, which include status LEDs, keypad, and an adjustment tool. It also has menus for navigation and settings, such as the start menu, menu tree, menu for nominal value/gas/unit, menu for error status, menu for measuring values, menu for display parameters, menu for installation and calibration, and menu for operating data and calibration.
advertisement
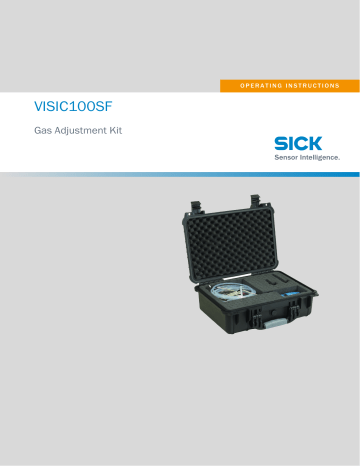
Title Page
VISIC100SF
Gas Adjustment Kit
MMMOPERATING INSTRUCTIONS MMMI
Described product
Product name: VISIC100SF Gas Adjustment Kit
Manufacturer
SICK AG
Erwin-Sick-Str. 1
79183 Waldkirch
Germany
Legal information
This work is protected by copyright. All rights derived from the copyright shall be reserved for SICK AG. Reproduction of this document or parts of this document is only permissible within the limits of the legal determination of Copyright Law.
Any modification, shortening or translation of this document is prohibited without the express written permission of SICK AG.
The trademarks stated in this document are the property of their respective owner.
© SICK AG. All rights reserved.
Original document
This document is an original document of SICK AG.
2 O P E R A T I N G I N S T R U C T I O N S | VISIC100SF 8027092/AE00/V1-0/2022-10 | SICK
Subject to change without notice
Contents
Contents
8027092/AE00/V1-0/2022-10 | SICK
Subject to change without notice
CONTENTS
Symbols and document conventions ............................................................. 5
Warning symbols ............................................................................ 5
Warning levels and signal words.................................................... 5
Information symbols ....................................................................... 6
Electrical safety............................................................................... 7
Dangerous substances................................................................... 8
Requirements for personnel qualification ..................................................... 8
Gas Adjustment Kit.......................................................................10
Transport, VISIC100SF Gas Adjustment Kit.................................................11
Storage, VISIC100SF Gas Adjustment Kit and accessories........................11
Transporting and storing test gases.............................................................11
Regulations applicable for VISC100SF........................................11
Securing loads ..............................................................................11
Valve protection ............................................................................11
No smoking allowed .....................................................................11
Hazard labels ................................................................................11
Ventilation .....................................................................................11
Transport document .....................................................................12
Vehicle equipment ........................................................................12
Other equipment...........................................................................12
Marking .........................................................................................12
Accident leaflet .............................................................................12
Training .........................................................................................12
Disposal.........................................................................................12
O P E R A T I N G I N S T R U C T I O N S | VISIC100SF 3
CONTENTS
Displays and operating elements ................................................................ 13
Adjustment tool ............................................................................ 13
Status LEDs .................................................................................. 13
Keypad .......................................................................................... 14
Status and malfunction messages .............................................................. 14
Menu - Installation and Calibration ............................................................. 17
MP Parameters............................................................................. 17
System Parameters ...................................................................... 17
Menu - Operating Data................................................................. 18
Menu - Calibration ........................................................................ 19
Adjust zero point....................................................... 19
Adjust sensitivity ....................................................... 20
Sequence and duration................................................................ 23
Connections between gas sensor and test gas cylinder ............ 23
Select gas type ............................................................................. 24
Performing zero point adjustment............................................... 25
Performing sensitivity adjustment............................................... 26
Final steps .................................................................................... 27
4 O P E R A T I N G I N S T R U C T I O N S | VISIC100SF 8027092/AE00/V1-0/2022-10 | SICK
Subject to change without notice
ABOUT THIS DOCUMENT 1
1
1.1
1.2
1.3
1.4
1.5
1.5.1
1.5.2
About this document
Function of this document
●
●
●
This document describes:
Adjusting the gas sensors
Transport and storage conditions for the VISIC100SF Gas Adjustment Kit
Important safety information for safe operation.
Scope of application
These Operating Instructions apply exclusively to the VISIC100SF Gas Adjustment Kit from
SICK for adjusting the CO, NO and NO
2
gas sensors used in the VISIC100SF.
They are not applicable for other SICK devices.
Target groups
This Manual is intended for persons qualified to perform an adjustment of the VISIC100SF gas sensors.
Further detailed information
● VISIC100SF Operating Instructions
Symbols and document conventions
Warning symbols
Symbol Significance
Hazard (general)
Hazard through voltage
Hazard through acidic substances
Hazard through toxic substances
Hazard through noxious substances
Hazard for the environment/nature/organic life
Warning levels and signal words
DANGER:
Risk or hazardous situation which will result in severe personal injury or death
WARNING:
Risk or hazardous situation which could result in severe personal injury or death
8027092/AE00/V1-0/2022-10| SICK
Subject to change without notice
O P E R A T I N G I N S T R U C T I O N S | VISIC100SF 5
1 ABOUT THIS DOCUMENT
1.5.3
1.6
CAUTION:
Hazard or unsafe practice which could result in less severe or minor injuries
NOTICE:
Hazard which could result in property damage
Note:
Tips
Information symbols
Symbol Significance
Important technical information for this product
Important information on electric or electronic functions
Data integrity
SICK AG uses standardized data interfaces, such as standard IP technology, in its products.
The focus here is on product availability and features.
SICK AG always assumes the integrity and confidentiality of data and rights affected in connection with the use of the products are ensured by the customer.
In all cases, the customer is responsible for the implementation of safety measures suitable for the respective situation, e.g., network separation, firewalls, virus protection and patch management.
6 O P E R A T I N G I N S T R U C T I O N S | VISIC100SF 8027092/AE00/V1-0/2022-10| SICK
Subject to change without notice
FOR YOUR SAFETY 2
2
2.1
2.1.1
For your safety
Basic safety information
▸
Read and observe these Operating Instructions.
▸
Observe all safety information.
Correct use
▸
Only use the measuring device as described in “Intended use”. The manufacturer assumes no responsibility for any other use.
▸
Maintenance work should be performed as prescribed in this Manual.
▸
Do not perform any work or repairs on the measuring device not described in this
Manual.
▸
Do not remove, add or modify any components to or on the device unless described and specified in the official manufacturer information.
▸
Use only original spare parts and wear and tear parts from SICK.
Failure to observe these precautions could result in:
●
●
Voiding the manufacturer's warranty.
Causing the device to become dangerous.
Special local conditions
In addition to the information in these Operating Instructions, follow all local laws, technical rules and company-internal operating and installation directives applicable wherever the device is installed.
Retention of documents
These Operating Instructions:
▸
Must be available for reference.
▸
Must be conveyed to new owners.
Ensure the operational safety during all work on the device
The VISIC100SF is mainly used in combination with regulation and control technology.
▸
During all work on the device, ensure that this can not lead to hazards or hindrances for traffic.
Electrical safety
Hazard through electrical shock
●
●
There is a risk of electric shock when working on the measuring device with the voltage supply switched on.
● Before starting work on the measuring device, ensure the power supply can be switched off using a power isolating switch or circuit breaker in accordance with the valid standard.
Switch off the power supply before carrying out any work on the measuring device.
After completion of the work or for test purposes or adjustment, the power supply may only be activated again by authorized personnel complying with the safety regulations.
8027092/AE00/V1-0/2022-10| SICK
Subject to change without notice
O P E R A T I N G I N S T R U C T I O N S | VISIC100SF 7
2 FOR YOUR SAFETY
2.1.2
2.2
2.3
Dangerous substances
Hazard through acidic liquids
If the gas sensor is mechanically damaged, corrosive liquid may escape and cause serious injury.
●
●
Take appropriate protective measures for work (e.g., by wearing a safety mask, protective gloves and acid resistant clothes).
In case of contact with the skin or eyes, rinse the affected parts immediately with clear water and consult a doctor.
Hazard through escaping calibration gases
●
●
●
Incorrect handling of calibration gases can cause high concentrations above the workplace exposure limits to escape from the gas sensor into the ambient air and lead to poisoning.
Observe the Safety Datasheets of the calibration gases.
Ensure adequate ventilation.
Limit gassing time.
Intended use
The Gas Adjustment Kit serves to check and adjust the gas sensors in the VISIC100SF.
Requirements for personnel qualification
The device may only be operated by authorized persons who, based on their training on, and knowledge of the specific device, as well as knowledge of the relevant regulations can assess the tasks given and recognize the hazards involved.
8 O P E R A T I N G I N S T R U C T I O N S | VISIC100SF 8027092/AE00/V1-0/2022-10| SICK
Subject to change without notice
3
3.1
PRODUCT DESCRIPTION 3
Product description
Product identification
Product name
Manufacturer
Type plate
VISIC100SF Gas Adjustment Kit
SICK AG
Erwin-Sick-Str. 1 · 79183 Waldkirch · Germany
On the lid of the case, right bottom
Fig. 1: Type plate, Gas Adjustment Kit
Designation
Part number
Serial number
8027092/AE00/V1-0/2022-10| SICK
Subject to change without notice
O P E R A T I N G I N S T R U C T I O N S | VISIC100SF 9
3 PRODUCT DESCRIPTION
3.2
3.2.1
Layout and function
The Gas Adjustment Kit continuously checks the gas type and measuring range set for agreement with gas type and measuring range of the connected gas sensor and outputs an error if there is an inconsistency.
Gas Adjustment Kit
Fig. 2: Contents, Gas Adjustment Kit
1
2
3
Designation
Hose (marked blue/orange),
3 m for nitrogen monoxide (NO) and nitrogen dioxide (NO
2
)
Hose, transparent (marked pink),
3 m for carbon monoxide (CO) and synthetic air
Accessories: 2 × hose adapters and transition pieces,
2 × replacement seals (O-rings) for tapping valves
4 Stainless steel sampling valve (marked blue) for NO and NO
2
, flow rate: 0.5 l/min
5 Brass sampling valve (marked pink) for CO and synthetic air, flow rate: 0.5 l/min
6 Adjustment tool
Operating Instructions
Note:
It is assumed that the test gases are provided by the customer.
Calibration gas data, see “Test gases”, page 28
.
10 O P E R A T I N G I N S T R U C T I O N S | VISIC100SF 8027092/AE00/V1-0/2022-10| SICK
Subject to change without notice
TRANSPORT AND STORAGE 4
4
4.1
4.2
4.3
4.3.1
4.3.2
4.3.3
4.3.4
4.3.5
4.3.6
Transport and storage
Transport, VISIC100SF Gas Adjustment Kit
No special regulations must be observed when transporting and storing the Gas
Adjustment Kit. The standard SICK AG regulations are applicable.
Storage, VISIC100SF Gas Adjustment Kit and accessories
Always store the contents of the Service case in the Service case.
Transporting and storing test gases
The following Sections describe the general obligations when transporting and storing test gases or test gas cylinder for the VISIC100SF Gas Adjustment Kit.
Regulations applicable for VISC100SF
●
●
●
The dangerous goods amount in the vehicle must NOT exceed 1000 ADR (Accord européen relatif au transport international des merchandises dangereuses par route) points.
The test gases or test gas cylinders may only be transported to the place of use to carry out measurements, repairs or maintenance work, i.e. no supply trips!
Also observe the respective local regulations!
Securing loads
The load must always be secured adequately, also during transport in private vehicles.
●
●
●
Lashing straps
Clamping bars
Wedges etc.
Secure the load so that pieces being transported cannot change direction and therefore not damage the load. The test gases or test gas cylinders may only be transported in the intended bags.
Valve protection
The closing valves must be protected against damage (e.g. by protective caps, valve protection collars, protective boxes, etc.).
No smoking allowed
Open fire or light is forbidden during loading work, in the proximity of the transport pieces and other vehicles as well as in the vehicles.
Hazard labels
Hazard labels must be affixed to the test gas cylinders. The code is required in the bottom corner of the hazard label.
Ventilation
No special ventilation is required when the limit values
8027092/AE00/V1-0/2022-10| SICK
Subject to change without notice
O P E R A T I N G I N S T R U C T I O N S | VISIC100SF 11
4 TRANSPORT AND STORAGE
4.3.7
4.3.8
4.3.9
4.3.10
4.3.11
4.3.12
4.3.13
Transport document
Note:
▸
Always carry the transport document.
The transport document is not required in Germany in compliance with Exception 18
GGAV when:
●
●
●
Gases are not transferred to third parties
No special agreement is applied
A proof of quantity (e.g. delivery bill) is available
Vehicle equipment
Not required when carrying a maximum of 340 liters of specified CO test gas cylinders or
880 liters of specified NO test gas cylinders or 4290 liters of specified NO
2 cylinders.
test gas
Other equipment
Not required.
Marking
Not required.
Accident leaflet
Not required.
Training
All persons involved in transporting dangerous goods (e.g. driver, loader, consignor, consignee, filler, transporter) must have received appropriate training.
Disposal
Test gas cylinders that are not emptied must be returned to the supplier and the supplier is responsible for their disposal.
12 O P E R A T I N G I N S T R U C T I O N S | VISIC100SF 8027092/AE00/V1-0/2022-10| SICK
Subject to change without notice
OPERATION 5
5
5.1
5.2
5.2.1
Operation
Operating concept
The complete operation and configuration is performed using the control keys and the LC display.
Displays and operating elements
Adjustment tool
1110
SICK AG
CO ppm
5.2.2
Designation
1 Status LEDs
2 LC display
3 Control keys
Status LEDs
●
●
The status LEDs indicate the operating status.
Green: Ready for operation
Yellow: Malfunction
8027092/AE00/V1-0/2022-10| SICK
Subject to change without notice
O P E R A T I N G I N S T R U C T I O N S | VISIC100SF 13
5.4
5.5
5 OPERATION
5.2.3
Keypad
Key
5.3
Designation
ESC key
Confirm key
Arrow up
Arrow down
Arrow left
Arrow right
●
●
●
●
●
●
●
●
●
●
Function
Terminate program
Query whether value should be saved
Return to previous menu level
●
Select submenu
End value input
Store parameter
Navigating within a menu level
Change value
Navigating within a menu level
Change value
Change cursor position
● Change cursor position
Navigating and setting
Press key
and
and
and
Action
Open menu.
Move cursor to position segment to be changed.
Use to set the desired parameter or setpoint.
End value input.
Change other parameters in the same menu.
End value input.
Save changed value?
Yes and return to next higher menu or
No and return to next higher menu.
Old value is not overwritten.
Status and malfunction messages
Possible status and malfunction messages are described in the respective Menu Section.
Measuring point
The term measuring point (MP) refers to a gas sensor connected to the VISIC100SF.
For a sensor with digital communication, the display shows
DP = Digital Measuring Point.
The number following is always 1 because the adjustment tool can only address one sensor.
14 O P E R A T I N G I N S T R U C T I O N S | VISIC100SF 8027092/AE00/V1-0/2022-10| SICK
Subject to change without notice
6
6.1
6.2
6.3
MENUS 6
Menus
Start menu
Display
1110
SICK AG
CO ppm
●
●
Display of the company name and by default the CO sensor.
The adjustment tool automatically tries to communicate with a CO sensor.
Menu tree
Menu level
Nom./Gas/Unit
Error Status
Measuring Values
Display Parameters
Software Version
Serial Number
Language
LCD Function
Installation & Calibration
MP Parameters
System Parameters
Operation Data
Calibration
DP1
Zero DP1
Test gas
Explanation
Select gas type
Display malfunction
Display measured values
Display parameters
Display software version
Display serial number
Select language
Test hardware function
Read out and change measuring point and system parameters, perform adjustment
Read out measuring point parameters
Read out or change system parameters
Read out gas sensor operating data
Adjust gas sensor: Zero point and sensitivity
Select measuring point
Adjust zero point
Set test gas concentration
Menu - Nom./Gas/Unit
Function: Set gas type
Display
Nom./Gas/Unit
1110 CO
Symbol
1110
CO ppm ppm
Description
Type number of the gas sensor used and the gas type
Gas type formula
Unit
Table 1: Gas types and measuring ranges
Type
1110
1129
1130
Gas type
Carbon monoxide
Nitrogen monoxide
Nitrogen dioxide
Formula
CO
NO
NO
2
Measuring range
0–300/0–200
0–100
0–5
Unit ppm ppm ppm
8027092/AE00/V1-0/2022-10| SICK
Subject to change without notice
O P E R A T I N G I N S T R U C T I O N S | VISIC100SF 15
6 MENUS
6.4
6.5
6.6
Menu - Error status
Function: Display current error message
●
●
●
Display
Status LED is yellow.
The currently pending error is displayed.
The malfunction message is acknowledged automatically when the malfunction is cleared.
Menu - Measuring Values
Function: Display measured value characteristics and messages
Display
Symbol
DP1
CO ppm
51.0 l
#
Comm.Error
Underrange
Overrange
Warm-Up
Time
Description
Measuring point number
Gas type formula
Unit
Function
Digital measuring point
Gas type display
Measured value (example)
Maintenance information
Malfunction measuring point
Monitoring measuring range
I = Current measured value (actual value) of the gas concentration
Gas sensor maintenance required (maintenance date exceeded)
Communication malfunction, gas sensor
↔
Adjustment tool
Measuring signal < permissible range (< zero point –
6%)
Measuring signal > permissible range (> measuring range end value +6%)
Warm-up time Warm-up time of gas sensor active
Menu - Display Parameters
●
●
Function: Display and change parameters
General and non-safety relevant parameters are stored.
The change can be made in operating mode.
●
●
●
Display Parameters
●
Software version
Serial number of the adjustment tool
Language: Select language
– German (factory setting)
– English
– USA English
– French
– Italian
LCD function: Test LCD hardware.
– All LEDs light up for approx. 2 seconds.
– Backlight is yellow.
– All points are displayed on the LED.
16 O P E R A T I N G I N S T R U C T I O N S | VISIC100SF 8027092/AE00/V1-0/2022-10| SICK
Subject to change without notice
MENUS 6
6.7
6.7.1
6.7.2
Menu - Installation and Calibration
Note: Changed parameters must be read back to check for correctness!
MP Parameters
Function: Display measuring point parameters
Display
Displays the measuring range of the active measuring point
Procedure:
1 Menu: Installation & Calibration
→
MP Parameter
→
DP1
→
Open Nom/Gas/Unit.
2 Press Down arrow key and display the measuring range.
System Parameters
Function: Display system parameters
●
●
System Parameters
System information: Serial number
Power-on time
Power-on time
Gas sensors require a warm-up time until the measurement process reaches a stable state. During this warm-up time, the sensor signal can lead to the unwanted triggering of a pseudo alarm. Therefore, the power-on time is started after switching on the voltage or voltage recovery. During this time, the sensor outputs “Warm-up time” instead of the measured value.
The factory-set power-on time is 5 min. and can only be read out.
8027092/AE00/V1-0/2022-10| SICK
Subject to change without notice
O P E R A T I N G I N S T R U C T I O N S | VISIC100SF 17
6 MENUS
6.7.3
Menu - Operating Data
Function: Read out operating data of the gas sensor
Display operating data
Symbol
Software Version
Days of Operation
Gas Conc. Counter
●
●
Description
Current software version
Number of current operating days
Gas concentration counter*
Unit. 10% of measuring range per day
Days of Operation expected
Min. Temperature
Max. Temperature
●
●
●
●
Expected lifetime of the gas sensor.
Is continuously recalculated based on adjustments and concentration counter
Display of the lowest measured temperature (start value = 70°C)
Will be updated only after 7 days when restarting
●
●
Display of the highest temperature value measured on the device
(start value = -34°C)
Will be updated only after 7 days when restarting
Display of the tool number used for the last access.
Last Tool No.
Number of Calibr.
Sensitivity
Maintenance Days last
Days of operation Last
Number of adjustments performed
Sensitivity of the sensor at the last adjustment to new sensor
Remaining maintenance days due before the last adjustment
Number of operating days since last adjustment (fixed value)
Maintenance Days Currently Current remaining days until next maintenance date (down counter)
Max. Current Value Maximum measured current value of the gas sensor
Procedure:
1 Menu: Installation & Calibration
→
Open Operating Data.
>>> Operating data are read in.
>>> “Please wait...” is displayed during reading in.
>>> Read-in not successful: Display returns to the previous menu item.
>>> Read-in successful: First subordinate menu item is displayed.
2 Press “Down arrow”to display the following menu items.
18 O P E R A T I N G I N S T R U C T I O N S | VISIC100SF 8027092/AE00/V1-0/2022-10| SICK
Subject to change without notice
MENUS 6
6.7.4
6.7.4.1
Menu - Calibration
Function: Adjust zero point and sensitivity
Adjust zero point
Display
Symbol
Zero
□
Current value too small
Current value too high
Current value unstable
Internal error
Description
Zero point adjustment
Zero point adjustment finished, zero point offset saved
Electrochemical cell defective, replace gas sensor.
Wrong gas for zero point adjustment (actual current value > 10% of measuring range)
Displayed as long as the deviation between two measuring cycles
(100 ms) is > 3%.
Goes off automatically when sensor signal becomes stable.
Displayed when the adjustment is not possible, e.g. in case of serious errors. Exchange gas sensor.
Procedure
see “Perform adjustment”, page 23
8027092/AE00/V1-0/2022-10| SICK
Subject to change without notice
O P E R A T I N G I N S T R U C T I O N S | VISIC100SF 19
6 MENUS
6.7.4.2
Adjust sensitivity
Display
Symbol
Test gas XX.x ppm
Gain
□
Current Value too small
Current value too high
Test gas too small
Test gas too high
Actual value unstable
Time too short
Sensitivity <
Internal error
Description
Set the test gas concentration
Sensitivity adjustment
Sensitivity adjustment finished, sensitivity offset saved
No test gas or incorrect test gas at the sensor
Test gas concentration > entered value.
Internal error. Exchange gas sensor.
Set test gas concentration must be within 30% and 90% of the measuring range.
●
●
●
●
●
●
Displayed as long as the deviation between two measuring cycles
(100 ms) is > 3%.
Goes out automatically when sensor signal becomes stable.
Message “Actual value unstable” starts internal timer (10-20 s).
The text is displayed when the timer has expired and the actual value is still unstable.
The process starts again.
If the value is stable, the actual value is displayed again and the adjustment process is continued.
There is an internal error when the cycle repeats several times.
The adjustment procedure must be canceled and the gas sensor replaced.
Sensitivity of the gas sensor < 30%, adjustment no longer possible.
Exchange gas sensor.
Internal error that cannot be corrected. Exchange gas sensor.
Procedure
see “Perform adjustment”, page 23
20 O P E R A T I N G I N S T R U C T I O N S | VISIC100SF 8027092/AE00/V1-0/2022-10| SICK
Subject to change without notice
7
7.1
7.2
ADJUSTMENT 7
Adjustment
An electrochemical process always leads to a loss of sensitivity over time. Therefore, an adjustment of the zero point and the sensitivity is necessary at regular intervals.
Safety
WARNING: Hazard by voltage.
Live parts are accessible when the device is open!
▸
Only use suitable, insulated tools.
WARNING: Hazard by corrosive liquids
If the gas sensor is mechanically damaged, corrosive liquid may escape and cause serious injury.
▸
Take appropriate protective measures for work (e.g., by wearing a safety mask, protective gloves and acid resistant clothes).
▸
In case of contact with the skin or eyes, rinse the affected parts immediately with clear water and consult a doctor.
▸
Dispose of damaged gas sensors immediately.
WARNING: Health hazard due to defective gas cylinders
The use of defective test gas cylinders for adjusting the electrochemical cells can lead to accidents and health hazards.
▸
Do not use expired test gas cylinders.
▸
When handling pressure vessels, observe the required safety regulations.
WARNING: Hazard through escaping calibration gases
Incorrect handling of calibration gases can cause high concentrations above the occupational exposure limits to escape from the gas sensor into the ambient air and lead to poisoning.
▸
Observe the Safety Datasheets of the calibration gases.
▸
Ensure adequate ventilation.
▸
Limit gassing time.
Materials and tools required
●
●
●
●
●
●
●
Gas Adjustment Kit
VISIC100SF with gas sensors
Test gas cylinder with synthetic air (21% O
2
Test gas cylinder with test gas:
, 79% N
2
) for zero point adjustment
– For CO/NO in the range 30-90% of the measuring range for sensitivity adjustment
– For NO
2
: 30% measuring range end value up to 6 ppm
Test gas CO /NO/NO
2
Allen key, SW4
Special pliers/universal tool for cable glands
8027092/AE00/V1-0/2022-10| SICK
Subject to change without notice
O P E R A T I N G I N S T R U C T I O N S | VISIC100SF 21
7 ADJUSTMENT
7.3
Preparation
NOTICE:
Risk of destruction of electronic components by electrostatic discharge (ESD)
When touching electronic assemblies, there is a risk of the assembly being destroyed by electrical equipotential bonding.
▸
Make sure you have the same electric potential as the subassembly (e.g. by grounding) before touching the subassembly.
NOTICE:
Entering a too high test gas concentration on the adjustment tool can lead to incorrect adjustment of the electrochemical cell.
▸
Ensure the correct test gas concentration is used depending on the gas concentration,
NOTICE:
The warm-up phase for the gas sensors takes 5 minutes.
▸
Do not interrupt the connection to the gas sensors or the voltage supply of the
VISIC100SF when opening it.
The 5-minute warm-up phase of the gas sensors will otherwise restart.
Running-in time and warm-up time
Gas sensor
CO
NO
NO
2
Running-in time
(hrs.)
24
24
24
5
5
Warm-up time
(min.)
5
Flow rate
(ml/min.)
500
500
500
Exposure time
(sec.)
120
120
180
Procedure
1 Open the VISIC100SF enclosure:
▸
Unscrew the two screws on the enclosure cover with the SW4 hex key.
▸
Remove the enclosure cover on the front side of the device.
▸
Unscrew the four screws of the measuring unit.
▸
Hang the measuring unit in using the hinge fixture and swivel it downwards.
2 Set the VISIC100SF to Maintenance mode.
3 Observe the running-in and warm-up time for the gas sensors.
22 O P E R A T I N G I N S T R U C T I O N S | VISIC100SF 8027092/AE00/V1-0/2022-10| SICK
Subject to change without notice
ADJUSTMENT 7
7.4
7.4.1
7.4.2
Perform adjustment
Sequence and duration
Sequence:
1 Zero point adjustment
2 Sensitivity adjustment
The sequence cannot be changed.
Duration: 3 ... 10 minutes.
The gas sensor terminates the adjustment mode automatically after a certain period of inactivity (typically 10 minutes).
Connections between gas sensor and test gas cylinder
To obtain reliable results during adjustment, make sure the hoses and sampling valves are used correctly. All parts are marked accordingly:
For CO and synthetic air (parts are marked in pink):
– Hose, transparent
– Hose adapter
– Transition piece for tapping valve
– Brass tapping valve, flow rate: 0.5 l/min
For NO and NO
2
(parts are marked blue/orange):
– Hose
– Hose adapter
– Transition piece for tapping valve
– Stainless steel tapping valve, marked blue, flow rate: 0.5 l/min
NOTICE:
Only use undamaged sealing rings on the tapping valves.
8027092/AE00/V1-0/2022-10| SICK
Subject to change without notice
O P E R A T I N G I N S T R U C T I O N S | VISIC100SF 23
7 ADJUSTMENT
7.4.3
Select gas type
Procedure
1 Place the adjustment tool on the interface on the board.
2 Switch the adjustment tool on.
>>> The Start menu appears on the display.
3 On the adjustment tool: Press “Confirm”.
>>> Menu: Nom./Gas/Unit opens.
4
5 End the input with “Confirm”.
6 Press “ESC”.
>>> Value is saved.
24 O P E R A T I N G I N S T R U C T I O N S | VISIC100SF 8027092/AE00/V1-0/2022-10| SICK
Subject to change without notice
ADJUSTMENT 7
7.4.4
Performing zero point adjustment
Procedure
1 Screw the hose adapter for synthetic air (marked pink) into the thread under the sensor to be calibrated.
2 Attach the hose for synthetic air (marked pink) to the hose adapter.
3 Screw the closed sampling valve (marked pink) onto the test gas cylinder with synthetic air.
4 Connect the corresponding transition piece (marked pink) to the tapping valve.
5 Connect the open end of the hose to the transition piece.
6 On the calibration tool: Menu: “Confirm”
→
Installation & Calibration
→
Calibrate
→
DP1
→
Open zero.
7 Press “Confirm”.
>>> Current actual value is displayed.
8 Open the sampling valve for feeding the test gas.
Note:
The flow rate is set to a fixed value of 0.5 l/min for all gases.
9 Press “Confirm” to start the adjustment procedure.
>>> New zero offset is calculated.
>>> During the calculation, an underscore runs from left to right in the 2nd line.
>>> The actual value drops to “0”.
10 When the actual value is stable, press “Confirm” and finish calculation of the value.
>>> “Save“ appears.
>>> After successful saving, a square is briefly displayed on the right.
>>> Zero point adjustment is finished. New zero point offset is saved.
>>> Display automatically changes to the display of the current actual value (new zero point).
11 Press “ESC”.
12 Close the gas sampling valve to stop the gas sampling.
13 Pull the hose off the hose adapter.
14 Remove the hose adapter.
Possible malfunction messages
see “Adjust zero point”, page 19
8027092/AE00/V1-0/2022-10| SICK
Subject to change without notice
O P E R A T I N G I N S T R U C T I O N S | VISIC100SF 25
7 ADJUSTMENT
7.4.5
Performing sensitivity adjustment
The sensitivity adjustment is started when the zero point adjustment has been completed.
NOTICE:
Use correct hoses, hose adapters, sampling valves and transition pieces for the respective gas sensor:
▸
CO: Marked pink
▸
NO and NO
2
: Marked blue/orange
Procedure
1 Screw the hose adapter for the corresponding test gas into the thread under the sensor to be calibrated.
2 Attach the hose for the corresponding test gas to the hose adapter.
3 Screw the closed sampling valve onto the test gas cylinder containing the test gas.
4 Connect the appropriate adapter to the tapping valve.
5 Connect the open end of the hose to the transition piece.
6 On the adjustment tool: Menu item: “DP1” appears
7 On the adjustment tool: Press “Down arrow” to menu item:
Test gas
→
Enter test gas concentration
8 Enter the test gas concentration using the “Arrow” keys.
9 Press “Confirm”.
10 Press “Arrow down”.
>>> Menu: Gain DP1 is displayed.
11 Open the sampling valve to feed the test gas. Hose connection of the hose adapter must point vertically downwards.
Note:
The flow is automatically regulated to a constant value.
● 0.5 l/min for synthetic air and CO, NO and NO
2
12 Press “Confirm”.
>>> Current actual value and sensitivity value from the last adjustment are displayed.
13 Press “Confirm” to start the adjustment procedure.
>>> New sensitivity value is calculated.
>>> During the calculation, an underscore runs from left to right in the 2nd line.
>>> The actual value adjusts to the entered test gas concentration.
>>> The sensitivity is also recalculated.
14 When the actual value is stable, press “Confirm” and finish calculation of the value.
>>> “Save” appears.
>>> After successful saving, a square is briefly displayed on the right.
>>> Sensitivity adjustment is finished. New zero point offset is saved.
>>> Display automatically changes to the display of the current actual value (new zero point).
15 Close the gas sampling valve to stop the gas sampling.
16 Pull the hose off the hose adapter.
17 Remove the hose adapter.
Possible malfunction messages
see “Adjust sensitivity”, page 20
26 O P E R A T I N G I N S T R U C T I O N S | VISIC100SF 8027092/AE00/V1-0/2022-10| SICK
Subject to change without notice
7.4.6
Final steps
1 Switch off the adjustment tool and remove it from the board.
2 VISIC100SF: Set maintenance mode to inactive.
3 Close the measuring unit and fasten it with the 4 screws.
4 Replace the housing cover and tighten it with the two screws.
ADJUSTMENT 7
8027092/AE00/V1-0/2022-10| SICK
Subject to change without notice
O P E R A T I N G I N S T R U C T I O N S | VISIC100SF 27
8 TECHNICAL DATA
8
8.1
Technical data
Test gases
For gas sensor CO
Zero point
Gas
Synthetic air
Formula
0
2
Sensitivity
Gas
Carbon monoxide
Formula
CO
For gas sensor NO
Zero point
Gas
Synthetic air
Formula
0
2
Sensitivity
Gas Formula
Nitrogen monoxide NO
For gas sensor NO
2
Zero point
Gas
Synthetic air
Formula
0
2
Sensitivity
Gas
Nitrogen dioxide
Formula
NO
2
Concentration
20.9%
Concentration
180 ppm
(160 ... 200 ppm)
Accuracy
< ± 2%
Concentration
20.9%
Concentration
60 ppm
(50 ... 70 ppm)
Concentration
20.9%
Concentration
5 ppm
Accuracy
< ± 2%
Accuracy
< ± 2%
Accuracy
< ± 2%
Accuracy
< ± 2%
Accuracy
5%
Rest
Nitrogen N
2
Rest
Nitrogen N
2
Rest
Nitrogen N
2
Rest
Nitrogen
Rest
Nitrogen N
2
Rest
Synthetic air
Note:
The flow volumes for CO, NO and NO
2
are set fixed using the valves.
28 O P E R A T I N G I N S T R U C T I O N S | VISIC100SF 8027092/AE00/V1-0/2022-10| SICK
Subject to change without notice
TECHNICAL DATA 8
Recommended sizes of the test gas packs
Typical gas fill volume (liter)
Cylinder bottle size (liter)
Pressure (bar)
Dimensions (mm)
Empty weight (kg)
Valve outlet
34
0.9
34
Height
Width
281
74
0.56
5/8"
18 UNF
C10
58
1.6
34
359
90
1.11
5/8"
18 UNF
C10
110
1.6
68
359
90
1.11
5/8"
18 UNF
C10
8027092/AE00/V1-0/2022-10| SICK
Subject to change without notice
O P E R A T I N G I N S T R U C T I O N S | VISIC100SF 29
Australia
Phone +61 (3) 9457 0600
1800 33 48 02 – tollfree
E-Mail [email protected]
Austria
Phone +43 (0) 2236 62288-0
E-Mail [email protected]
Belgium/Luxembourg
Phone +32 (0) 2 466 55 66
E-Mail [email protected]
Brazil
Phone +55 11 3215-4900
E-Mail [email protected]
Canada
Phone +1 905.771.1444
E-Mail [email protected]
Czech Republic
Phone +420 234 719 500
E-Mail [email protected]
Chile
Phone +56 (2) 2274 7430
E-Mail [email protected]
China
Phone +86 20 2882 3600
E-Mail [email protected]
Denmark
Phone +45 45 82 64 00
E-Mail [email protected]
Finland
Phone +358-9-25 15 800
E-Mail [email protected]
France
Phone +33 1 64 62 35 00
E-Mail [email protected]
Germany
Phone +49 (0) 2 11 53 010
E-Mail [email protected]
Greece
Phone +30 210 6825100
E-Mail [email protected]
Hong Kong
Phone +852 2153 6300
E-Mail [email protected]
Hungary
Phone +36 1 371 2680
E-Mail [email protected]
India
Phone +91-22-6119 8900
E-Mail [email protected]
Israel
Phone +972 97110 11
E-Mail [email protected]
Italy
Phone +39 02 27 43 41
E-Mail [email protected]
Japan
Phone +81 3 5309 2112
E-Mail [email protected]
Malaysia
Phone +603-8080 7425
E-Mail [email protected]
Mexico
Phone +52 (472) 748 9451
E-Mail [email protected]
Netherlands
Phone +31 (0) 30 229 25 44
E-Mail [email protected]
New Zealand
Phone +64 9 415 0459
0800 222 278 – tollfree
E-Mail [email protected]
Norway
Phone +47 67 81 50 00
E-Mail [email protected]
Poland
Phone +48 22 539 41 00
E-Mail [email protected]
Romania
Phone +40 356-17 11 20
E-Mail [email protected]
Russia
Phone +7 495 283 09 90
E-Mail [email protected]
Singapore
Phone +65 6744 3732
E-Mail [email protected]
Detailed addresses and further locations at www.sick.com
Slovakia
Phone +421 482 901 201
E-Mail [email protected]
Slovenia
Phone +386 591 78849
E-Mail [email protected]
South Africa
Phone +27 10 060 0550
E-Mail [email protected]
South Korea
Phone +82 2 786 6321/4
E-Mail [email protected]
Spain
Phone +34 93 480 31 00
E-Mail [email protected]
Sweden
Phone +46 10 110 10 00
E-Mail [email protected]
Switzerland
Phone +41 41 619 29 39
E-Mail [email protected]
Taiwan
Phone +886-2-2375-6288
E-Mail [email protected]
Thailand
Phone +66 2 645 0009
E-Mail [email protected]
Turkey
Phone +90 (216) 528 50 00
E-Mail [email protected]
United Arab Emirates
Phone +971 (0) 4 88 65 878
E-Mail [email protected]
United Kingdom
Phone +44 (0)17278 31121
E-Mail [email protected]
USA
Phone +1 800.325.7425
E-Mail [email protected]
Vietnam
Phone +65 6744 3732
E-Mail [email protected]
6,&.$* _ :DOGNLUFK _ *HUPDQ\ _ ZZZVLFNFRP
advertisement
Related manuals
advertisement
Table of contents
- 5 About this document
- 5 Function of this document
- 5 Scope of application
- 5 Target groups
- 5 Further detailed information
- 5 Symbols and document conventions
- 5 Warning symbols
- 5 Warning levels and signal words
- 6 Information symbols
- 6 Data integrity
- 7 For your safety
- 7 Basic safety information
- 7 Electrical safety
- 8 Dangerous substances
- 8 Intended use
- 8 Requirements for personnel qualification
- 9 Product description
- 9 Product identification
- 10 Layout and function
- 10 Gas Adjustment Kit
- 11 Transport and storage
- 11 Transport, VISIC100SF Gas Adjustment Kit
- 11 Storage, VISIC100SF Gas Adjustment Kit and accessories
- 11 Transporting and storing test gases
- 11 Regulations applicable for VISC100SF
- 11 Securing loads
- 11 Valve protection
- 11 No smoking allowed
- 11 Hazard labels
- 11 Ventilation
- 12 Transport document
- 12 Vehicle equipment
- 12 Other equipment
- 12 Marking
- 12 Accident leaflet
- 12 Training
- 12 Disposal
- 13 Operation
- 13 Operating concept
- 13 Displays and operating elements
- 13 Adjustment tool
- 13 Status LEDs
- 14 Keypad
- 14 Navigating and setting
- 14 Status and malfunction messages
- 14 Measuring point
- 15 Menus
- 15 Start menu
- 15 Menu tree
- 15 Menu - Nom./Gas/Unit
- 16 Menu - Error status
- 16 Menu - Measuring Values
- 16 Menu - Display Parameters
- 17 Menu - Installation and Calibration
- 17 MP Parameters
- 17 System Parameters
- 18 Menu - Operating Data
- 19 Menu - Calibration
- 19 Adjust zero point
- 20 Adjust sensitivity
- 21 Adjustment
- 21 Safety
- 21 Materials and tools required
- 22 Preparation
- 23 Perform adjustment
- 23 Sequence and duration
- 23 Connections between gas sensor and test gas cylinder
- 24 Select gas type
- 25 Performing zero point adjustment
- 26 Performing sensitivity adjustment
- 27 Final steps
- 28 Technical data
- 28 Test gases