advertisement
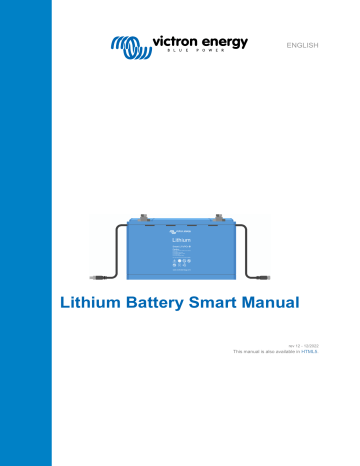
ENGLISH
Lithium Battery Smart Manual
rev 12 - 12/2022
This manual is also available in HTML5 .
Lithium Battery Smart Manual
Table of Contents
Lithium Battery Smart Manual
Lithium Battery Smart Manual
1. Safety precautions
• Observe these instructions and keep them located near the battery for future reference.
• The Material Safety Datasheet can be downloaded from the “Material Safety Datasheet menu” located on the Lithium Smart product page .
• Work on a lithium battery should be carried out by qualified personnel only.
1.1. General warnings
• While working on a li-ion battery wear protective eyeglasses and clothing.
• Any uncovered battery material such as electrolyte or powder on the skin or in the eyes must immediately be flushed with plenty of clean water. Then seek medical assistance. Spillages on clothing should be rinsed out with water.
• Explosion and fire hazard. The terminals of a li-ion battery are always live, therefore do not place metallic items or tools on top of a li-ion battery. Avoid short circuits, too deep discharges and too high charge currents. Use insulated tools. Do not wear any metallic items such as watches, bracelets, et cetera. In case of fire, you must use a type D foam or CO2 fire extinguisher.
• Do not open or dismantle the battery. Electrolyte is very corrosive. In normal working conditions contact with the electrolyte is impossible. If the battery casing is damaged do not touch the exposed electrolyte or powder because it is corrosive.
• Li-ion batteries are heavy. If involved in an accident they can become a projectile! Ensure adequate and secure mounting and always use suitable handling equipment for transportation.
• Handle with care because a li-ion battery is sensitive to mechanical shock.
• Do not use a damaged battery.
• Do not wet the battery.
1.2. Charge and discharge warnings
• Too deep discharges will seriously damage a li-ion battery and can even be dangerous. Therefore, use of an external safety relay is obligatory.
• Use only with a Victron Energy approved BMS.
• If charged after the Lithium Battery was discharged below the “Discharge cut-off voltage”, or when the
Lithium Battery is damaged or overcharged, the Lithium Battery can release a harmful mixture of gasses such as phosphate.
• The temperature range over which the battery can be charged is 5°C to 50°C. Charging the battery at temperatures outside this range may cause severe damage to the battery or reduce battery life expectancy.
• The temperature range over which the battery can be discharged is -20°C to 50°C. Discharging the battery at temperatures outside this range may cause severe damage to the battery or reduce battery life expectancy.
Page 1 Safety precautions
Lithium Battery Smart Manual
1.3. Transportation warnings
• The battery must be transported in its original or equivalent package and in an upright position. If the battery is in its package, use soft slings to avoid damage.
• Do not stand below a battery when it is hoisted.
• Never lift the battery at the terminals or the BMS communication cables, only lift the battery at the handles.
Batteries are tested according to UN Handbook of Tests and Criteria, part III, sub section 38.3 (ST/SG/AC.10/11/Rev.5).
For transport the batteries belong to the category UN3480, Class 9, Packaging Group II and have to be transported according to this regulation. This means that for land and sea transport (ADR, RID & IMDG) they have to be packed according to packaging instruction P903 and for air transport (IATA) according to packaging instruction P965. The original packaging complies with these instructions.
1.4. Disposal of lithium batteries
Do not throw a battery into fire.
Batteries must not be mixed with domestic or industrial waste.
Batteries marked with the recycling symbol must be processed via a recognized recycling agency. By agreement, they may be returned to the manufacturer.
Page 2 Safety precautions
Lithium Battery Smart Manual
2. Introduction
2.1. Lithium Battery Smart
Victron Energy Lithium Battery Smart batteries are Lithium Iron Phosphate (LiFePO4 or LFP) batteries available with a nominal voltage of 12.8V or 25.6V in various capacities. This is the safest of the mainstream lithium battery types. They can be connected in series, parallel and series/parallel so that a battery bank can be built for system voltages of 12V, 24V or 48V. Up to four 12.8V
batteries or two 25.6V batteries can be connected in series. A total of 20 batteries can be connected, resulting in energy storage of up to 84kWh in a 12V system or up to 102kWh in a 24V and 48V system.
A single LFP cell has a nominal voltage of 3.2V. A 12.8V battery consists of 4 cells connected in series and a 25.6V battery consists of 8 cells connected in series.
LFP is the chemistry of choice for very demanding applications. Some of its features are:
• High round trip efficiency.
• High energy density - More capacity with less weight and volume.
• High charge and discharge currents, enabling fast charging and discharging.
• Flexible charge voltages.
2.2. Lithium Battery Smart range
Here is a list of all Lithium Battery Smart models, which are available in a variety of capacities and voltages:
• LiFePO4 Battery 12,8V/50Ah Smart
• LiFePO4 Battery 12,8V/100Ah Smart
• LiFePO4 Battery 12,8V/160Ah Smart
• LiFePO4 Battery 12,8V/200Ah Smart
• LiFePO4 Battery 12,8V/330Ah Smart
• LiFePO4 battery 25,6V/100Ah Smart
• LiFePO4 battery 25,6V/200Ah Smart
For more information, like the datasheet, product photos, product drawings etc., also see the Lithium Battery Smart product page .
2.3. Battery management
The battery has an integrated Balancing, Temperature and Voltage control system (BTV). The BTV connects to an external
Battery Management System (BMS). In case of multiple batteries, the BTVs of several batteries are daisy chained and then connect to the BMS.
The BMS protects the battery cells against low and high cell voltages and against charging at too low or high temperatures.
This is how it works: The BTV monitors each individual battery cell. It balances the cell voltages and in case of high or low cell voltage, or in case of high or low cell temperature, it will generate an alarm signal. The alarm signal is received by the BMS and the BMS will turn off loads an/or chargers accordingly.
A Victron Energy BMS is essential for a correct operation of the lithium battery. The lithium battery is not allowed to be used without one. In addition to this you will also need to ensure that the BMS correctly controls all loads and charge sources that are connected to the battery.
The BMS is not included with the battery. It needs to be purchased separately. For more information on the different BMS types,
see chapter The BMS models [7] .
Page 3 Introduction
Lithium Battery Smart Manual
2.4. BMS extension cables
The battery is equipped with 50cm BMS communication cables. In case these cables are too short to reach the BMS, they can be extended by using the following BMS extension cables:
• M8 circular connector Male/Female 3 pole cable 1m (bag of 2)
• M8 circular connector Male/Female 3 pole cable 2m (bag of 2)
• M8 circular connector Male/Female 3 pole cable 3m (bag of 2)
• M8 circular connector Male/Female 3 pole cable 5m (bag of 2)
The BMS extension cables are not included with the battery. For more information see the BMS extension cable product page
2.5. The VictronConnect app
The battery is equipped with Bluetooth and uses this to communicate with the VictronConnect app.
The VictronConnect app can be used for:
• Monitoring the battery status
• Monitoring the battery voltage
• Monitoring the battery temperature
• To find out when the battery was last fully charged
• Monitoring the cell balancing status
• Monitoring the individual cell voltages
• To view or change the battery settings
• To update the battery firmware
The VictronConnect app can be downloaded from the respective app stores or from the Victron Energy website. For download links and information about the VictronConnect app see the VictronConnect app web page .
Page 4
The VictronConnect app
Introduction
Lithium Battery Smart Manual
3. System design and BMS functionality
This chapter describes how the battery interacts with the BMS and how the BMS interacts with loads and chargers to keep the battery protected. This information is essential for system design and to be able to choose the most suitable BMS for the system.
3.1. Maximum number of batteries in series, parallel or series/parallel configuration
As mentioned in the introduction, up to 20 Victron Lithium Battery Smart batteries in total can be used in a system, regardless of the Victron BMS used. This enables 12, 24 and 48V energy storage systems with up to 102kWh (84kWh for a 12V system), depending on the capacity used and the number of batteries. See the
Electrical installation chapter [17]
for installation details.
Check the table below to see how the maximum storage capacity can be achieved (using 12.8V/330Ah and 25.6V/200Ah batteries as an example):
System voltage
12V
24V
48V
12.8V/330Ah
20 in parallel
20 in 2S10P
20 in 4S5P
Nominal energy
84kWh
84kWh
84kWh
25.6V/200Ah na
20 in parallel
20 in 2S10P
Nominal energy na
102kWh
102kWh
3.2. The battery alarm signals and BMS actions
Cell voltages and battery temperature are monitored by the battery. If they are outside the normal range, an alarm is sent to the
BMS.
In order to protect the battery, the BMS will then turn off loads and/or chargers or generate a pre-alarm as soon as it has received the appropriate signal from the battery.
These are the possible battery warnings and alarms and the corresponding BMS actions:
Battery alarm signal
Low cell voltage pre-alarm warning
Low cell voltage alarm
High cell voltage alarm
Low battery temperature alarm
High battery temperature alarm
BMS action
The BMS generates a pre-alarm signal
The BMS turns loads off
The BMS turns chargers off
The BMS turns chargers off
The BMS turns chargers off
The battery communicates these alarms to the BMS via its BMS cables.
BMS
The BMS receives an alarm signal from a battery cell
If the system contains multiple batteries, all battery BMS cables are connected in series (daisy chained). The first and the last
BMS cable is connected to the BMS.
BMS
Page 5
The BMS receives an alarm signal from a cell in a multiple battery setup
System design and BMS functionality
Lithium Battery Smart Manual
There are two ways the BMS can control loads and chargers:
1. By sending an electrical or a digital on/off signal to the charger or load.
2. By physically connecting or disconnecting a load or a charge source from the battery. Either directly or by using a
BatteryProtect or Cyrix Li-ion relay .
All available BMS types for the lithium battery are based on either or both of these technologies. The BMS types and their functionality are briefly described in the next chapters.
Load or charger
OFF signal
BMS
The BMS sends an on/off signal to a load or charger
BMS
Load or charger
The BMS connects or disconnects from a load or charger
Page 6 System design and BMS functionality
Lithium Battery Smart Manual
3.3. The BMS models
There is a choice of 7 different BMS models that can be used with the Lithium Battery Smart. Below overview explains the differences between them and their typical application. See also the BMS Overview for additional info.
BMS type Voltage Typical application
SmallBMS
VE.Bus BMS V2
VE.Bus BMS
Lynx Smart BMS 500
Smart BMS CL
12/100
12, 24 or 48V
12, 24 or 48V
12, 24 or 48V
12, 24 or 48V
12V
Features
Controls loads and chargers via on/off signals.
Generates a pre-alarm signal.
Note: The smallBMS was previously named miniBMS.
Controls MultiPlus or Quattro via
VE.Bus.
Controls loads and chargers via on/off signals.
Generates a pre-alarm signal.
Remote On/Off terminals
Remote Panel port for communication with a GX device or DMC to control inverter/charger switch state (on/off/charger-only).
Auxiliary power input and output terminals to power a GX device.
Controls MultiPlus or Quattro via
VE.Bus.
Controls loads and chargers via on/off signals.
Generates a pre-alarm signal.
Controls loads and chargers via on/off signals.
Can control inverter/chargers, solar chargers and select AC chargers via DVCC.
Generates a pre-alarm signal.
500A contactor to disconnect system positive.
Battery monitor.
Bluetooth.
Can connect to a GX device via
VE.Can.
Remote On/Off/Standby via
VictronConnect app or a GX device.
Installed in system positive and negative.
Instant readout via Bluetooth
100A dedicated alternator port.
Controls loads and chargers via on/off signals.
Generates a pre-alarm signal.
Bluetooth.
Installed in system positive.
Small systems without inverter/ chargers.
Systems with inverter/chargers.
Systems with inverter/chargers.
Larger systems with digital integration or when a built-in safety relay is needed.
Also systems with inverter/chargers if GX device is present.
Relatively small systems with an alternator.
Page 7 System design and BMS functionality
Lithium Battery Smart Manual
BMS type
Smart BMS 12/200
BMS 12/200
Voltage
12V
12V
Features
200A dedicated alternator port.
200A dedicated DC system port.
Controls loads and chargers via on/off signals.
Generates a pre-alarm signal.
Bluetooth.
Installed in system positive.
200A dedicated alternator port.
200A dedicated load and charger port.
Installed in the system negative. Be aware that in many systems this is not ideal.
Typical application
Relatively small systems with an alternator and DC loads.
Relatively small systems with an alternator and DC loads but without inverter/charger.
Note: This BMS is end of life, use a Smart BMS CL 12/100 or Smart
BMS 12/200 instead.
3.3.1. The Small BMS
The smallBMS is equipped with a “load disconnect”, a “charge disconnect” and a pre-alarm contact.
• In the event of low cell voltage, the smallBMS will send a “load disconnect” signal to turn the load(s) off.
• Prior to turning the load off, it will send a pre-alarm signal indicating imminent low cell voltage.
• In the event of high cell voltage or low or high battery temperature, the smallBMS will send a “charge disconnect” signal to turn the charger(s) off.
For more information see the smallBMS product page .
Load
Charger
SmallBMS
The smallBMS
The smallBMS controls loads and chargers via “load disconnect” and “charge disconnect” signals
3.3.2. The VE.Bus BMS V2
The VE.Bus BMS V2 is the next generation of the VE.Bus Battery Management System (BMS). It is designed to interface with and protect Victron Lithium Battery Smart in systems that have Victron inverters or inverter/chargers that have VE.Bus
communication and offers new features such as auxiliary power in- and output ports for powering a GX device, remote on/off ports and communication with GX devices.
Just like the smallBMS, it also features a “load disconnect”, a “charge disconnect” and a "pre-alarm" contact.
• In the event of low cell voltage, the VE.Bus BMS V2 will send a “load disconnect” signal to turn off the load(s) and will also disable inverting of the inverter/charger via VE.Bus communication.
• Prior to turning loads off, it will send a pre-alarm signal warning of imminent low cell voltage.
• In the event of a high cell voltage or high/low battery temperature, the VE.Bus BMS V2 will send a “charge disconnect” signal to turn the charger(s) off and it will also disable the charger of the inverter/charger.
A mains detector and a short RJ45 UTP cable ship together with the VE.Bus BMS V2. These are needed for mains detection once the inverter/charger has been turned off by the BMS.
Page 8 System design and BMS functionality
Lithium Battery Smart Manual
The mains detector is not needed for the MultiPlus-II or Quattro-II series of inverter/chargers.
For more information see the VE.Bus BMS V2 manual which can be found on the VE.Bus BMS product page .
VE.Bus BMS V2, VE.Bus BMS Mains detector and RJ45
UTP cable
The VE.Bus BMS V2 will turn loads and chargers off via
“load disconnect”, and “charge disconnect” and controls the inverter/charger
3.3.3. The VE.Bus BMS
The VE.Bus BMS is used in a system that also contains one or multiple Victron Energy inverter/chargers. The VE.Bus BMS directly communicates via the VE.Bus with the inverter/chargers. Just like the smallBMS, it also features a “load disconnect”, a
“charge disconnect” and a "pre-alarm" contact.
• In the event of low cell voltage, the VE.Bus BMS will send a “load disconnect” signal to turn off the load(s) and it will also turn the inverter of the inverter/charger off.
• Prior to turning loads off, it will send a pre-alarm signal warning of imminent low cell voltage.
• In the event of a high cell voltage or high/low battery temperature, the VE.Bus BMS will send a “charge disconnect” signal to turn the charger(s) off and it will also turn the charger of the inverter/charger off.
A mains detector and a short RJ45 UTP cable ship together with the VE.Bus BMS. These are needed for mains detection once the inverter/charger has been turned off by the BMS.
The mains detector is not needed for the MultiPlus-II or Quattro-II series of inverter/chargers.
For more information see the VE.Bus BMS manual which can be found on the VE.Bus BMS product page .
VE.Bus BMS, V.Bus BMS mains detector and RJ45 UTP cable
The VE.Bus BMS will turn loads and chargers off via
“load disconnect”, and “charge disconnect” and controls the inverter/charger
Page 9 System design and BMS functionality
Lithium Battery Smart Manual
3.3.4. The Lynx Smart BMS
The Lynx Smart BMS is used in medium to large systems that contain DC loads and AC loads via inverters or inverter/chargers, for example on yachts or in recreational vehicles. This BMS is equipped with a contactor that disconnects the DC system, a “load disconnect”, a “charge disconnect”, a "pre-alarm" contact and a battery monitor. In addition to this it can be connected to a GX device and control Victron Energy equipment via DVCC.
• In the event of low cell voltage, the Lynx Smart BMS will send a “load disconnect” signal to turn the load(s) off.
• Prior to turning a load off, it will send a pre-alarm signal indicating imminent low cell voltage.
• In the event of high cell voltage or low/high battery temperature, the BMS will send a “charge disconnect” signal to turn the charger(s) off.
• If the batteries are even further discharged (or overcharged), the contactor will open, effectively disconnecting the DC system to protect the batteries.
The Lynx smart BMS
The Lynx Smart BMS will turn loads and chargers off via “load disconnect”, and “charge disconnect” signals and controls the inverter/charger via a GX device. Should the battery be discharged even further, the BMS will disconnect the battery from the DC system.
3.3.5. The Smart BMS CL 12/100
The Smart BMS CL 12/100 is equipped with a “load disconnect”, a “charge disconnect” and a "pre-alarm" contact. The BMS also features a dedicated alternator port that will "current limit" the alternator current. It can be set for a variety of currents all the way up to 100A.
• In the event of low cell voltage, the Smart BMS CL 12/100 will send a “load disconnect” signal to turn the load(s) off.
• Prior to turning the load off it will send a pre-alarm signal indicating imminent low cell voltage.
• In the event of high cell voltage or low/high battery temperature, the Smart BMS CL 12/100 will send a “charge disconnect” signal to turn the charger(s) off.
• The alternator port controls and current limits the alternator.
For more information see the Smart BMS CL 12/100 product page .
Alternator
Smart BMS CL 12/100
Load
Charger
The Smart BMS CL 12/100
The Smart BMS CL 12/100 will turn loads and chargers off via “load disconnect“ and “charge disconnect“ signals. It also controls and limits the alternator
Page 10 System design and BMS functionality
Lithium Battery Smart Manual
3.3.6. The Smart BMS 12/200
The Smart BMS 12/200 is equipped with a “load disconnect”, a “charge disconnect” and a "pre-alarm" contact. The BMS also features a dedicated alternator and system port. The alternator port will "current limit" the alternator current. It can be set for a variety of currents all the way up to 100A. The system port is used to connect the DC system and can be used for both charging and discharging the battery.
• In the event of low cell voltage, the Smart BMS 12/200 will send a “load disconnect” signal to turn the load(s) off and will disconnect the load/charger port.
• Prior to turning the load off it will send a pre-alarm signal indicating imminent low cell voltage.
• In the event of high cell voltage or low/high battery temperature, the Smart BMS 12/200 will send a “charge disconnect” signal to turn the charger(s) off.
• The alternator port controls and current limits the alternator.
Load
Charger
Smart BMS 12/200
Alternator
DC system
The Smart BMS 12/200
The Smart BMS12/200 will disconnect loads and chargers or turn loads and chargers off via “load disconnect“ and
“charge disconnect“ signals. It also controls and limits the alternator.
Page 11 System design and BMS functionality
Lithium Battery Smart Manual
3.4. The pre-alarm signal
The purpose of the pre-alarm is to warn the user that the BMS is about to turn off the loads because the battery is getting too empty. For example; you would want an early warning that loads are going to be turned off while manoeuvring your boat, or if lights are turned off when it is dark. We recommend connecting the pre-alarm to a clearly visible or audible alarm device. When the pre-alarm is raised the user can turn on a charger to prevent the DC system from shutting down.
Switching behaviour
In case of an imminent under voltage shutdown, the pre-alarm output of the BMS will switch on. In case the voltage continues to decrease, the loads are switched off (load disconnect) and at the same time the pre-alarm output will switch off again. In case the voltage rises again (operator has enabled a charger or has reduced the load) the pre-alarm output will switch off, once the lowest cell voltage has risen above 3.2V.
The BTV ensures a minimum delay of 30 seconds between enabling the pre-alarm and the load-disconnect. This delay is to allow the user a minimal amount of time to prevent the shutdown.
3.5. Charging from an alternator
Compared to lead acid batteries, lithium batteries have a very low internal resistance. They will accept a higher charge current than lead acid batteries. Because of this, special care must be taken when lithium batteries are charged from an alternator.
To safely connect an alternator, use one of these options:
• Make sure that the alternator current rating is at least twice the battery capacity rating. For example; a 400A alternator can be safely connected to a 200Ah battery.
• Use an alternator equipped with a temperature controlled alternator regulator. This prevents the alternator from overheating.
• Use a current-limiting device like a DC-DC charger or a DC-DC converter between the alternator and the starter battery.
• Use a BMS with an alternator port with built-in current limiting, such as the Smart BMS CL 12/100 or the Smart BMS 12/200.
For more information on charging lithium batteries with an alternator, see the Alternator lithium charging blog and video .
60A 200A
100Ah 100Ah
Regulator with temperature sensor
100Ah
Alternator charging
60A
Current limiting device
100Ah
Page 12 System design and BMS functionality
Lithium Battery Smart Manual
3.6. Battery monitoring
The common battery parameters, such as the battery voltage, battery temperature and cell voltages can be monitored via
Bluetooth using the VictronConnect app. However, state of charge monitoring is not built into the battery. To monitor state of charge use the Lynx Smart BMS or add a battery monitor such as a BMV or a SmartShunt to the system.
If a battery monitor is used together with a lithium battery, adjust the following two settings:
• Set the charge efficiency to 99%
• Set the Peukert exponent to 1.05
For more information on battery monitors see the Battery monitor product page .
When a battery monitor is added to the system it matters how the battery monitor is powered. There are two options:
• Power the battery monitor from the load disconnect terminal of the BMS:
This is the prefered method. The battery cannot get accidentally discharged by the battery monitor. When the battery voltage is low and the BMS disconnects the loads, the battery monitor will also stop working. Once the battery is sufficiently charged, the battery monitor will automatically power back up. The battery monitor memory is nonvolatile, this means that the battery monitor will keep its settings and history data when it is re-powered.
The battery monitor power wire is connected to the BMS
• Power the battery monitor directly from the battery:
This is not the preferred method, as it is only suitable for battery monitors with a low self consumption such as the BMV-712 or the
SmartShunt and the battery bank has to be larger than 200Ah. In a large battery bank, the battery monitor self consumption is less significant.
If using this method, be aware that the battery monitor is not controlled by the BMS and that the battery monitor will continue to drain energy from the battery, even after the BMS has turned the loads off. The battery monitor can potentially totally discharge (and damage) the battery.
The battery monitor power wire is connected to the battery
Page 13 System design and BMS functionality
Lithium Battery Smart Manual
4. Installation
4.1. Preparation
4.1.1. What's in the box
Unpacking and handling the battery
Take care when unpacking the battery. Batteries are heavy. Do not lift the battery by its terminals or by its BMS cables. The
chapter.
Familiarise yourself with the battery. The battery terminals, on the top of the battery, have indicators for correct polarity: a “+” symbol for the positive and a “-” symbol for the negative terminal.
The battery has two BMS cables. These cables are used for communication with the BMS. One cable has a male 3-pole connector and the other has a female 3-pole connector. Depending on the battery model, the BMS cables are located on one side of the battery or on two opposite sides of the battery.
Pay attention to the location of the BMS cables when handling the battery. The BMS cables can easily get damaged.
Top view and side views showing battery terminals (+ and -), BMS cables (A) and carry handles (B)
4.1.2. Download and install the VictronConnect app
The VictronConnect app is used to monitor the battery, change battery settings and update firmware.
Download the VictronConnect app for Android, iOS or macOS from their respective app stores. For more information about the app see the VictronConnect product page .
The VictronConnect app communicates with the battery via Bluetooth
4.1.3. Update the battery firmware
Before the battery is going to be used, it is important to check if the battery has the most up to date firmware. The firmware can be checked and updated with the VictronConnect app. Also make sure you have the latest VictronConnect version. This ensures that the latest battery firmware version is available.
The VictronConnect app might ask, on first connection, to update firmware. If this is the case, let it perform a firmware update. If it did not automatically update, check if the firmware is already up to date using the following procedure:
1. Connect to the battery.
2. Click on the settings symbol to go to the Settings page.
3. Click on the option symbol to go to the Product info.
4. Check if you are running the latest firmware and look for the text: “This is the latest version”.
Page 14 Installation
Lithium Battery Smart Manual
5. If the battery does not have the most up to date firmware, perform a firmware update.
Updating battery firmware
4.1.4. Charge batteries before use
If multiple batteries are going to be connected in series or in series/parallel, each individual battery needs to be fully charged before all batteries are interconnected.
How to charge batteries before use
Always use a BMS controlled charger when individually charging lithium batteries.
Initial charge procedure:
1. Connect each individual battery to a charger or to an inverter/charger and to a BMS (and repeat for every other battery).
2. Refer to the BMS manual on how to set the BMS up.
3. Set the charger to the charge profile as indicated in below table.
4. Ensure that the battery, the BMS and the charger are communicating with each other. Check this by disconnecting one of the battery BMS cables from the BMS and verify that the charger turns off. Then reconnect the BMS cable and verify that the charger turns back on.
5. Turn the charger on and check that the charger is charging the battery.
6. Note that during charging, the charger might repeatedly be turned off, and then on again by the BMS should there be an imbalance between the battery cells. This will manifest as follows: The charger will be on for a short period of time, then the charger will be off for a few minutes and then on again for a short time and so on. This might be repeated many times. This is nothing to be worried about and is part of the charge process. If the cells are balanced, the charger will not be turned off until the battery is fully charged.
7. The battery is fully charged when the battery charger has reached the float stage and the VictronConnect app battery cell status is "balanced". In case the battery cell status is "unknown" or "imbalanced", then the battery charger needs to be restarted multiple times until the battery cell status is "balanced".
Page 15 Installation
Lithium Battery Smart Manual
BMS
Initial charge using a BMS
Charger or inverter/charger settings for initial charge with a BMS (these are the same as the normal charge settings):
Battery model
Recommended charger settings
Charge profile Absorption voltage Absorption time Float voltage
12.8V - 50Ah
12.8V - 60Ah
12.8V - 100Ah
12.8V - 160Ah
12.8V - 200Ah
12.8V - 300Ah
12.8V - 330Ah
25.6V - 100Ah
25.6V - 200Ah
Max. charge current
30A
30A
50A
80A
100A
150A
150A
50A
100A
Lithium, fixed
Lithium, fixed
Lithium, fixed
Lithium, fixed
Lithium, fixed
Lithium, fixed
Lithium, fixed
Lithium, fixed
Lithium, fixed
14.2V
14.2V
14.2V
14.2V
14.2V
14.2V
14.2V
28.4V
28.4V
2h
2h
2h
2h
2h
2h
2h
2h
2h
13.5V
13.5V
13.5V
13.5V
13.5V
13.5V
13.5V
27.0V
27.0V
Why charge batteries before use
Lithium batteries are only approximately 50% charged when shipped from the factory. This is a transportation safety requirement.
But due to differences in transportation routes and warehousing, the batteries do not all have the same state of charge by the time they are installed.
The battery cell balancing system is only able to correct small differences in state of charge from one battery to another. A large imbalance, as can be the case with new batteries, will not be corrected. Please note that this type of imbalance, a different state of charge between batteries, is a different type of imbalance than if the cells within the battery are imbalanced.
Charging the batteries before use is not needed for a single battery or for individual batteries connected in parallel (none connected in series).
Page 16 Installation
Lithium Battery Smart Manual
4.2. Physical installation
4.2.1. Mounting
Mounting must meet the following requirements:
1. The battery must be mounted in an upright position.
2. The battery is only suitable for indoor use and needs to be located in a dry location.
3. Batteries are heavy. When moving the battery into its destined location, use suitable handling equipment for transportation.
4. Ensure adequate and secure mounting as the battery can become a projectile if involved in an accident.
5. Batteries produce a certain amount of heat when they are charged or discharged. Keep a 20mm space on each side of the battery for ventilation purposes.
4.3. Electrical installation
4.3.1. Connecting battery cables
The positive terminal is indicated by a “+” (plus) symbol and the negative terminal is indicated by a “-“ (minus) symbol.
Observe the battery polarity when connecting the battery terminals to a DC system or to other batteries. Take care not to short circuit the battery terminals.
Connect the cables as indicated in the diagram on the right:
1. Bolt
2. Spring washer
3. Washer
4. Cable lug
5. Battery terminal
Battery terminals
Battery cable connection
When tightening the bolts, use the correct torque, as indicated in below table, and use insulated tools that match the bolt's spanner size.
Thread Torque Battery model
12.8V - 50Ah
12.8V - 60Ah
12.8V - 100Ah
12.8V - 160Ah
12.8V - 200Ah
12.8V - 300Ah
12.8V - 330Ah
25.6V - 100Ah
25.6V - 200Ah
M8
M8
M8
M8
M8
M10
M10
M8
M8
10Nm
10Nm
10Nm
14Nm
14Nm
20Nm
20Nm
10Nm
14Nm
Cable cross sectional area and fuse ratings
Use battery cables with a cross sectional area that matches the currents that can be expected in the battery system.
Batteries can produce very large currents; it is therefore necessary that all electrical connections to a battery are fused.
The battery fuse rating has to match the current rating of the battery cable that has been used. Both the battery cable and the fuse have to also match the expected maximum system currents.
For more information on cable cross sectional area, fuse types and fuse ratings see the Wiring Unlimited book .
Page 17 Installation
Lithium Battery Smart Manual
The battery maximum discharge rating is indicated in the table below. The system current and therefore also the fuse rating should not exceed this current rating. The fuse has to match the lowest current rating, being the cable current rating, the battery current rating or the system current rating.
Battery model
12.8V - 50Ah
12.8V - 60Ah
12.8V - 100Ah
12.8V - 160Ah
12.8V - 200Ah
12.8V - 300Ah
12.8V - 330Ah
25.6V - 100Ah
25.6V - 200Ah
Maximum current rating
100A
120A
200A
320A
400A
600A
660A
200A
400A
Connecting a single battery
• Fuse the battery on the positive side.
• Connect the battery to the DC system.
DC system
Single battery
Connecting multiple batteries in series
• Each individual battery needs to have been fully charged.
• Connect a maximum of four 12.8V batteries or a maximum of two
25.6V batteries in series.
• Connect the negative to the positive of the next battery.
• Fuse the series string on the positive side.
• Connect the battery bank to the system.
Connecting multiple batteries in parallel
• A total of 20 batteries can be connected in parallel.
• Fuse each battery on the positive side.
• Connect the DC system cables diagonally to ensure an equal current path through each battery.
• Take care that cross sectional area of the system cable is equal to the cross sectional area of the string cable times the number of strings.
• Fuse the positive main cable going to the battery bank.
• Connect the battery bank to the DC system.
• For more information on how to construct a parallel battery bank see the Wiring Unlimited book .
DC system
Multiple batteries in series
DC system
Multiple batteries in parallel
Page 18 Installation
Lithium Battery Smart Manual
Connecting multiple batteries in series/parallel
• Connect a maximum of 20 batteries in a parallel/series combination.
• Each individual battery needs to have been fully charged.
• Fuse each series string on the positive side.
• Do not interconnect midpoints or other between string points
• Connect the system cables diagonally to ensure an equal current path through each battery string.
• Take care that cross sectional area of the system cable is equal to the cross sectional area of the string cable, times the number of strings.
• Fuse the positive main cable going to the battery bank.
• Connect the battery bank to the DC system.
DC system
Multiple batteries in series/parallel
Do not interconnect midpoints or other between string points
Battery banks consisting of different batteries
When constructing a battery bank, ideally all batteries should be of the same capacity, age and model. However, there are situations where this is not possible, such as when capacity need to be expanded by adding more batteries, or when a single battery in a battery bank needs to be replaced. In these cases, follow the guidelines in the table below.
Parallel
Battery bank type Different capacities allowed?
Yes
Series
Series/parallel - within a series string
Series/parallel - in case a whole series string is replaced or added
1) All batteries must have the same capacity rating and the same part number
2) The age difference should not exceed 3 years
No 1)
No 1)
Yes
Different ages allowed?
Yes
Yes 2)
Yes 2)
Yes
Background information:
When batteries with different capacities, or a big age difference (old batteries have a reduced capacity), are connected in series, an imbalance will occur between the batteries. This imbalance will increase over time and causes a reduction of the overall battery capacity. In theory, the battery with the smallest capacity will determine the overall capacity of a series battery string. But in reality, the imbalance will reduce the overall battery bank capacity even further. For example, if a 50Ah battery is connected in series with a 100Ah battery, the overall string capacity is 50Ah. But over time the batteries become imbalanced, and when the imbalance has become, let's say, 10Ah, the overall battery capacity will be 50Ah-10Ah = 40Ah. The cells of the fullest battery will have an overvoltage during charging, while they are not able to send the excess voltage to the other battery cells. The BMS will constantly interfere, and this results in that the emptiest battery is being discharged too far and the fullest battery is being overcharged.
Adding a Battery Balancer to a series string will reduce imbalance.
4.3.2. Connect the BMS
Each battery has two BMS cables with an M8 male and M8 female connector that need to be connected to the BMS.
Page 19
BMS cables on either side or on one side
Female and male BMS connector
Connected BMS connectors
Installation
Lithium Battery Smart Manual
How to connect the cables:
• For a single battery, connect both BMS cables directly to the BMS.
• For a battery bank consisting of multiple batteries, interconnect each battery (daisy chain) and connect the first and last BMS cable to the BMS. The batteries can be interconnected in any order.
• If the BMS is too far away for the cables to reach, use the optional extension cables. The BMS extension cables are available as a pair and come in a variety of lengths. For more information see the BMS extension cable product page .
BMS
Single battery BMS connection
4.4. Configuration
Two battery BMS connection (with optional extension cables) Multiple battery BMS connection
4.4.1. Battery settings
The default settings in the battery are suitable for almost all applications. There is no need to change these settings unless the application requires very specific conditions.
If settings need to be changed, use the VictronConnect app. To access the settings, click on the settings symbol .
VictronConnect battery settings
Allowed-To-Discharge cell voltage
This is the lowest battery cell voltage, at which discharging the battery is disallowed.
A lithium battery cell will be damaged if the cell voltage drops too low. As soon as one of the cells reaches the "Allowed-To-
Discharge" voltage, the BMS will disable all loads by sending a signal to the load or to the load disconnection device.
The default value is 2.80V, the range is 2.60V to 2.80V.
We recommend not to change this setting. The only scenario where a lower setting might be applicable is in emergency systems, where it could be a requirement to discharge the battery as far as possible and therefore sacrificing part of the battery's overall lifetime.
Page 20 Installation
Lithium Battery Smart Manual
If the "Allowed-To-Discharge" cell voltage is set to a low value, there will be less reserve capacity than when it is set at a higher value, for example:
• At 2.8V cell voltage there is approximately 3% remaining capacity in the battery.
• At 2.6V there is about 1% remaining capacity in the battery.
More reserve capacity is important. When there is less reserve capacity, the battery will need to be recharged almost straight away after a low voltage shutdown has occurred. If the battery is not recharged, it will further discharge due to self-discharge and quicker reach the point where one or more cells are damaged due to low cell voltage. This will lead to a permanent reduction of battery capacity and/or lifetime.
Cell under voltage pre-alarm threshold
When the cell voltage drops below this threshold, a pre-alarm signal is sent to the BMS. The purpose of the pre-alarm is to warn
The default value is 3.10 V and the range is 2.80V to 3.15V.
If the pre-alarm threshold is set at a higher voltage, the warning will come earlier than when it is set at a lower voltage. An earlier warning will give the user more time to take action and avert the imminent shutdown. In any case, there is at least a minimum of
30 seconds between pre-alarm and system shutdown.
Allowed-To-Charge minimum temperature
This setting defines the lowest temperature at which the BMS allows battery charging. A lithium battery cell will sustain permanent damage when it is charged at temperatures below 5°C.
The default value is 5°C and the range is -20°C to +20°C.
Setting this temperature below 5°C will void the warranty.
Battery temperature offset
This setting can be used to set an offset to improve the accuracy of the battery temperature measurement.
The default value is 0°C and the range is -10°C to +10°C.
Battery model
12.8V -
50Ah
12.8V -
60Ah
12.8V -
100Ah
12.8V -
160Ah
12.8V -
200Ah
12.8V -
300Ah
12.8V -
330Ah
25.6V -
100Ah
25.6V -
200Ah
4.4.2. Charger settings
Set all charge sources to the following charge parameters:
Recommended charge current
30A
30A
50A
80A
100A
150A
150A
50A
100A
Max.
charge current
Recommended charger settings
Charge profile
Absorption voltage
100A
120A
Lithium, fixed
Lithium, fixed
14.2V
14.2V
200A
320A
400A
Lithium, fixed
Lithium, fixed
Lithium, fixed
14.2V
14.2V
14.2V
600A
400A
200A
400A
Lithium, fixed
Lithium, fixed
Lithium, fixed
Lithium, fixed
14.2V
14.2V
28.4V
28.4V
Absorption time
2h
2h
2h
2h
2h
2h
2h
2h
2h
Float voltage
13.5V
13.5V
13.5V
13.5V
13.5V
13.5V
13.5V
27.0V
27.0V
* Storage stage is not per se needed for a lithium battery, but if the charger has a storage mode, set it at the same as the float voltage.
Storage voltage *
13.5V
13.5V
13.5V
13.5V
13.5V
13.5V
13.5V
27.0V
27.0V
Page 21 Installation
Lithium Battery Smart Manual
4.5. Commissioning
Once all connections have been made, the system wiring needs to be checked, the system needs to be powered up and the BMS functionality needs to be checked. Follow this checklist:
Check polarity of all battery cables.
Check cross sectional area of all battery cables.
Check if all battery cable lugs have been crimped correctly.
Check if all battery cable connections are tight (don’t exceed maximum torque).
Tug slightly on each battery cable and see if the connections are tight.
Check all BMS cable connections and make sure the connector screw rings are screwed all the way down.
Connect with VictronConnect to each battery.
Check if each battery has the most up to date firmware.
Check if each battery has the same settings.
Connect the system positive and negative DC cable to the battery (or battery bank).
Check the string fuse(s) rating (if applicable).
Place the string fuse(s) (if applicable).
Check the main fuse rating.
Place the main fuse.
Check if all battery charge sources have been set to the correct charge settings.
Turn on all battery chargers and all loads.
Check if the BMS is powered up.
Disconnect a random BMS cable and verify that the BMS is turning off all charge sources and all loads.
Reconnect the BMS cable and check if all charge sources and loads turn back on.
Page 22 Installation
Lithium Battery Smart Manual
5. Operation
5.1. Battery care
Once the battery is in operation, it is important to take proper care of the battery to maximise its lifetime.
These are the basic guidelines:
• Prevent total battery discharge at all times.
• Familiarize yourself with the pre-alarm feature and act when pre-alarm is active to prevent a system shutdown.
• If the pre-alarm is active or if the BMS has disabled the loads, make sure that the batteries are recharged as soon as possible.
Minimise the time the batteries spend in a far discharged state as much as possible.
• The batteries must spend at least 2 hours in absorption charge mode each month to ensure sufficient time in balancing mode.
• When leaving the system unattended for some time, make sure to either keep the batteries charged during that time, or make sure the batteries are (almost) full and then disconnect the DC system from the battery.
5.2. Monitoring
The VictronConnect app can be used to monitor the battery via Bluetooth in two ways:
1. Via a connected Bluetooth link to the battery: requires pairing between the mobile device and the battery.
2. Via Instant readout: show the most relevant data of the battery in the product list page via Bluetooth without having to establish connection.
Paired Bluetooth connection
When connected to the battery via VictronConnect app, it will show the following parameters:
• Battery status
• Battery voltage
• Battery temperature
• Time since last full battery charge
• Cell balance status
• Individual cell voltage
In case of an alarm, an alarm message will be shown in the VictronConnect app. Please note that alarm messages can only be seen or received when the VictronConnect app is actively connected to the battery and the phone or tablet is showing the battery screen. The app is not active in the background nor when the screen is off.
Page 23 Operation
Lithium Battery Smart Manual
Monitoring the battery via the VictronConnect app
Instant readout
Instant readout via Bluetooth offers the advantage that the most important data is shown instantly in the VictronConnect app
(together with data of other devices that are compatible), without having to connect directly to the battery. In addition, it offers a better range than a regular connection.
Instant readout is disabled by default and can be enabled in the product info page. See also chapter Instant readout in the
VictronConnect manual .
Instant readout will show the following parameters:
• Battery voltage and temperature
• Cell balance status
• Highest, average and lowest cell voltage
Page 24 Operation
Lithium Battery Smart Manual
Live data via Instant readout
5.3. Battery charging and discharging
This chapter describes the charging, discharging and cell balancing process in more detail for those who are interested in the technical background.
5.3.1. Charging
Lithium batteries are easier to charge than lead-acid batteries. The charge voltage may vary anywhere from 14V to 15V for a
12.8V lithium battery and 28V to 30V for a 25.6V lithium battery, as long as no cell is subjected to more than 4.2V. Lithium batteries will become permanent damaged if they are over-charged.
Should a cell reach 4.2V, all charge into that cell will be dissipated as heat. However, this is impossible on a properly installed system.
We recommend 14.2V (28.4V) as the absorption voltage, but if you want to change it, we advise keeping it between 14.0V (28V) and 14.4V 28.8V). Float voltage should always be 13.5V (27V).
Because of the flexibility in charge voltages, up to 20 batteries can be connected in parallel without much problems. No damage will occur if there are small differences in individual battery voltages because of varying cable resistances or internal battery resistances.
Once the absorption stage has been finalised, the battery charger goes into float.
The storage stage is not per se needed for a lithium battery, but if the charger has a storage mode, set the storage voltage at the same value as the float voltage.
We recommend a charge current of 0.5C. This means that if the battery is completely empty, it will take 2 hours to charge the battery. A charge rate of 0.5C for a 100Ah battery is 50A charge current. The maximum charge current is 2C, for a 100Ah battery this is 200A. This will charge the battery in half an hour. But be aware that the batteries will produce more heat when high charge currents are used. More ventilation space is needed around the batteries and depending on the installation, hot air extraction or forced air cooling might be needed.
Page 25 Operation
Lithium Battery Smart Manual
Lithium battery charge graph
The BMS will turn off all charge sources as soon as a battery cell voltage reaches 3.75V or if the battery temperature drops below
5°C or increases above 75°C. This means that all charge sources that are connected to the lithium battery must be controlled by the BMS.
Please note that the maximum battery operating temperature is still 50 degrees Celsius. A higher "charging not allowed" temperature limit of 75 degrees Celsius has been chosen, because the internal temperature measurement can be higher during balancing while the cell temperature is still within the operating range.
5.3.2. Cell balancing
The battery consists of lithium cells that are connected in series. The 12.8V battery has 4 and the 25.6V battery has 8 cells in series.
Why is cell balancing needed
Though carefully selected during the production process, the cells in the battery are not 100% identical. Therefore, when cycled, some cells will be charged or discharged earlier than the other cells. If the cells are not regularly balanced these differences will increase over time.
The same happens in a lead-acid battery, but there the cells self-correct without the need for cell balancing electronics because a small current will continue to flow even after one or more cells are fully charged. This current helps to fully charge the other cells that are lagging behind, thus equalising the charge state of all cells. The current through a lithium cell however, when fully charged, is almost zero. Lagging cells will not be charged further unless they receive "help" with this from cell balancing electronics.
Cells do not get damaged if they have different balance levels, but the imbalance will manifest itself in a (temporary) battery capacity reduction.
How does cell balancing work
The battery has built-in "active" and "passive" cell balancing. This ensures that all cells will be balanced. Each cell voltage is monitored and if required, energy will be moved from the cell(s) with the highest voltage to the cells with a lower voltage. This process will continue until all cell voltages are within 0.01V of each other.
When does cell balancing take place
The cell balancing process starts when the first cell has reached 3.3V. This depends on the level of imbalance. In case of a severely imbalanced battery, balancing can start at a lower voltage.
The cell balancing process generally takes place when the cell voltages are 3.50V. This can happen only during the absorption charge stage, as during this stage the charge voltage (14.2V or 28.4V) is high enough to allow the cells to reach a high enough voltage so the smaller cell differences can be corrected.
The cell balancing process is nearing completion when all cells have reached a voltage of 3.55V and the charge current has dropped below 1.5A. Balancing is complete when the charge voltage has dropped even further.
How to ensure that the battery remains balanced
A 2-hour fixed absorption period is recommended for lithium batteries, so that there is enough time for cell balancing to take place. It is important to regularly fully charge the battery. This so that the battery spends enough time in the absorption stage. A
Page 26 Operation
Lithium Battery Smart Manual full charge once a month should be sufficient. However, there are some applications where the battery cells will become quicker unbalanced than usual. This is the case when the system is intensively used or if the battery bank consists of multiple batteries in series. To ensure a well balanced battery, a weekly full charge is required for:
• Systems with a battery bank that contains batteries that are connected in series.
• Systems that are charged/discharged every day or a few times per week.
• Systems that have high discharge currents.
• Systems that have short charge periods or low charge voltages.
It is not possible to speed up the cell balancing process
Please note that a higher charge voltage will not speed up the cell balancing process. The cells are charged by current and not by voltage. Feeding current into a cell will cause the voltage to increase over time, but this is a fixed process. Applying more voltage will not speed this process up. In addition to this, the balancing speed is determined by the maximum current rating (1.8A) of the active and the passive balancing circuits.
How to monitor cell balancing status
Use the VictronConnect app to monitor the balance status of the battery. The app will indicate 4 balancing stages, being:
• Unknown - The battery is used for the first time or has not been charged for 30 days.
Charge the battery to let it determine possible cell imbalance. More precisely, the cell imbalance status will be detected as soon as the battery voltage is above 13.8V (27.2V). The cell balance status resets to unknown in case the battery has not been charged for the past month.
• Balancing - The balancing process is taking place.
The battery is currently balancing its internal cells. The cell status will show "Balanced" when completed.
• Balanced - All cells are balanced.
This is the optimal battery status. All battery cells are balanced and will be charged/discharged evenly.
• Imbalance - The balancing process was not completed the last time the battery was charged, or there is a voltage difference of more than 0.1V between the battery cells.
The battery cells must be re-balanced. Do this by fully charge the batteries. In case of severe imbalance it might be necessary to manually restart the charger several times. This is needed because balancing can only take place during the absorption stage and balancing will stop as soon as the charger has reached the float stage.
For more information on these 4 stages, click the information text, located below the cell status listing, and a pop-up window will open up with an explanation of each stage.
Cell balancing information. From left to right: unknown, balancing, balanced and imbalance.
The app also indicates the number of days since the last full battery charge. If the full charge was more than 30 days ago, it will indicate "unknown". This means that the battery has not received its recommended monthly charge.
Page 27 Operation
Lithium Battery Smart Manual
5.3.3. Discharging
Nearly the whole available battery capacity can be used, with exception of the approximate last 3% of remaining capacity. Lithium batteries will become permanently damaged if they are discharged too deeply.
Lithium batteries can be discharged with high currents. The maximum discharge rate of the lithium battery is 2C. For a 100Ah battery this means a 200A discharge current. This current will discharge the battery in half an hour. However, we recommend not to discharge above a 1C rate. A 1C rate means that the battery is discharged in 1 hour. For a 100Ah battery this is a discharge current of 100A.
When using a higher discharge rate, the battery will produce more heat than when a low discharge rate is used. More ventilation space is needed around the batteries and depending on the installation, hot air extraction or forced air cooling might be needed.
Also, some cells might reach the low voltage threshold quicker than the other cells. This can be because of a combination of heat and ageing.
To be able to tell if a battery is too deeply discharged you will need to look at the individual cell voltages. As the battery is being discharged, the cell voltage drops. This is indicated in below discharge graph. When the battery is almost empty, the voltage will drop faster. This is the sign that the battery is almost empty. This happens at around a cell voltage of 2.80V to 2.60V. Further discharge needs to be prevented, otherwise the battery will get damaged. So as soon as one of the cells has reached this voltage the BMS will disable all DC loads.
The under voltage shutdown threshold is configurable, if it is set to a higher voltage the reserve capacity is greater than if it is set at a lower voltage. It is set by default at 2.8V and the range is 2.6V to 2.8V.
Discharge graph showing cell voltage at various depths of discharge for different discharge rates
The BMS will turn off all loads as soon as a battery cell voltage drops below the low voltage threshold.
Although a BMS is used, there are still a few possible scenarios where the battery can be damaged due to over discharge. This can occur if small loads, such as: alarm systems, relays, standby current of certain loads, back current drain of battery chargers or charge regulators, slowly discharge the battery when the system is not in use. In addition to this, the battery itself also has a small amount of self-discharge.
In case of any doubt about possible residual current draw, isolate the battery when the system is not in use. Do this by opening the battery switch, by pulling the battery fuse(s) or by disconnecting the battery positive cable.
A residual discharge current is especially dangerous if the system has been discharged completely and a low cell voltage shutdown has occurred. At 2.8V cell voltage there is approximately 3% remaining capacity and at 2.6V there is about 1% remaining capacity.
After shutdown due to low cell voltage, a capacity reserve of 1% corresponds with 1Ah left in a 100Ah capacity battery. The battery will be damaged if the remaining capacity reserve is drawn from the battery. A residual current of 10mA for example may damage a 100Ah battery if the system is left in discharged state during more than 4 days (100 hours).
If all cells are 2.8V, this means that the battery terminal voltage is 11.2V (22.4V) and if all cells are 2.6V the battery terminal voltage is 10.4V (20.8V). Be aware that the BMS will turn the loads off as soon as one cell drops below the low voltage threshold.
This might not necessarily correspond with the battery terminal voltage. So, if investigating low voltage scenarios, always use the
VictronConnect app to look at the actual cell voltages and do not just rely on the battery terminal voltage.
5.3.4. Cell under voltage pre-alarm
The battery sends a signal to the BMS in case of imminent cell under voltage. This is used by the BMS to generate a pre-alarm signal. This signal will give an advanced warning that the BMS is about to generate a “load disconnect” signal and that the loads are going to be turned off. This happens at a default cell voltage of 3.10V and the range is 2.80V to 3.15V.
Page 28 Operation
Lithium Battery Smart Manual
Please note that older batteries might not support pre-alarm.
5.4. Warnings, alarms and errors
Cell under voltage warning (pre-alarm)
The voltage of one or more cells is becoming too low and has dropped below the pre-alarm setting. To remedy this warning, recharge the battery as soon as possible.
Under voltage alarm
The voltage of one or more cells is too low and discharging has been disabled. To remedy this warning, recharge the battery as soon as possible.
Under voltage alarm
Over voltage alarm
The voltage of one or more cells has become too high. Immediately disable all chargers and contact the system installer to check that all chargers are properly controlled by the “charge disconnect” contact on the BMS. When properly controlled, a high voltage situation is not possible, as the BMS disconnects all chargers well before raising the high voltage alarm.
Under temperature alarm
The battery has reached its low temperature threshold and charging is disabled.
Over temperature alarm
The battery has reached its high temperature threshold and charging is disabled.
Settings data lost error
To remedy this, go to the settings page and reset settings to factory defaults.
If this error is not resolved after a settings reset, contact your Victron Energy dealer or distributor and ask for this issue to be escalated to Victron Energy, as this error should never happen. Please include battery serial number and firmware version.
Hardware failure error
This error is generated in the following circumstances:
1. Software fault. This can be potentially fixed by restarting the microcontroller. The
Communication error or hardware failure [35]
chapter explains how to do this.
2. One (or more) cells are very deeply discharged or are defective. Check the battery terminal voltage. If the battery terminal
voltage is too low, refer to the Battery very low terminal voltage [33]
chapter what to do next.
Page 29 Operation
Lithium Battery Smart Manual
Number
A-SL9
A-SL15
A-SL22
A-SL11
W-SL12
E-SL24
E-SL1
E-SL2
E-SL9
E-SL10
E-SL119
3. The internal circuit board has a hardware fault. To resolve this, contact your Victron Energy dealer or distributor.
before contacting your Victron Energy dealer or distributor. This to rule out the first two possible causes of this error. Do not just assume that the error is caused by a hardware failure.
Other errors
In case of any of these alerts or errors, contact your dealer or distributor to resolve this situation:
• Balancer failure error
• Internal communication failure error
• Overlapped voltage error
• Balancer update error
Overview of all warnings, alarms and errors:
Error
Error
Error
Error
Error
Type
Alarm
Alarm
Alarm
Alarm
Warning
Error
Description
Overvoltage alarm ( Cell voltage > 3.95V )
Over temperature alarm ( Temp > 75°C )
Under temperature alarm ( Temp < temperature setting )
Under voltage alarm ( Cell voltage < setting minimum voltage )
Under voltage warning (Cell voltage < pre-alarm setting )
Hardware failure
Balancer failure
Internal communication failure
Overlapped voltage error
Balancer update error
Settings data lost
Page 30 Operation
Lithium Battery Smart Manual
6. Troubleshooting, support and warranty
Consult this chapter in case of unexpected battery behaviour or if you suspect a battery fault.
The troubleshooting and support process is to first consult the common battery issues as described in this chapter. Should this fail to resolve the issue, follow the advice in the technical support paragraph.
6.1. Troubleshooting
6.1.1. VictronConnect issues
Cannot connect with the VictronConnect app to the battery
It is highly unlikely that the Bluetooth interface is faulty. Check these possible causes before seeking support:
• Is the product a "Smart" product? Non-Smart products do not support Bluetooth.
• Is the battery voltage still high enough? The Bluetooth module is turned off as a precaution as soon as the battery terminal voltage drops below 8V or when one of the cells drop below 2V. The Bluetooth module will power up again once the battery is charged. When recharging the battery after a low voltage event, use the low voltage charge procedure as described in paragraph: “Battery very low terminal voltage”.
• Is there already another phone or tablet connected to the product? Only one phone or tablet can be connected at any given time. Make sure no other devices are connected and try again.
• Are you close enough to the product? In open space the maximum distance is about 20 meters.
• Are you using the Windows version of the VictronConnect app? The Windows version cannot use Bluetooth. Use an Android, iOS or macOS device instead.
• Has Bluetooth been disabled in the battery product settings?
IMPORTANT : Disabling Bluetooth is an irreversible process. Once Bluetooth has been disabled, it can never be re-enabled.
• Does the VictronConnect app have an issue? Try to connect to another Victron Energy product, does this work? If that also does not work, then there probably is an issue with the phone or tablet. Refer to the troubleshooting section of the
VictronConnect manual .
PIN code lost
If you have lost the PIN code, you will need to reset the PIN code to its default PIN code. This is done in the VictronConnect app.
• Navigate to the device list of the VictronConnect app. Click on the option symbol next to the product listing.
• A new window will open which allows you to reset the PIN code back to its default: 000000.
• Enter the batteries unique PUK code as printed on the product information sticker on the product.
• More information and specific instructions can be found in the VictronConnect manual .
Interrupted firmware update
This is recoverable, just try to update the firmware again.
6.1.2. Battery issues
Cell imbalance
How to recognize cell imbalance
• The BMS frequently disables the charger
This is an indication that the battery is imbalanced. The charger will never be disabled by the BMS if the battery is well balanced. Even when fully charged, the BMS will leave the charger enabled.
• The battery capacity seems to be less than before
If the BMS is disabling loads much sooner than it used to do, even while the overall battery voltage still looks OK, this is an indication that the battery is imbalanced.
• There is a noticeable difference between the individual cell voltages during absorption stage
When the charger is in the absorption stage, all cell voltages should be equal and between 3.50V and 3.60V. If this is not the case, this is an indication that the battery is imbalanced.
Page 31 Troubleshooting, support and warranty
Lithium Battery Smart Manual
• A cell slowly drops in voltage when the battery is not used
This is not imbalance, although it might look like it. A typical example of this is when the battery cells initially all have equal voltages, but when the battery is not used after a day or so, one of the cells has dropped 0.1 to 0.2V below the other cells. This cannot be fixed by rebalancing and the cell is considered to be defective.
How to recover an imbalanced battery
• Charge the battery using a charger that is configured for lithium and is controlled by the BMS.
• Be aware that cell balancing only takes place during the absorption stage. It will be necessary to manually restart the charger each time the charger has gone to float. Rebalancing can take a long time (up to a few days) and it will require many manual charger restarts.
• Be aware that during cell balancing it might look like nothing is happening. The cell voltages can remain the same for a long time and the lithium BMS will repeatedly turn the charger on and off. This is all normal.
• Balancing is taking place when the charge current is at or above 1.8A or when the BMS has temporarily disabled the charger.
• Balancing is almost finished when the charge current drops below 1.5A and the cell voltages are close to 3.55V.
• The rebalancing process is complete when the charge current has dropped even further, and all cells are 3.55V.
Be 100% sure that the charger is controlled by the BMS, dangerous cell overvoltage can occur if it is not.
Check this by monitoring the cell voltages using the VictronConnect app. The voltage of the fully charged cells will slowly creep up until 3.7V has been reached. At this point the BMS will disable the charger and the cell voltages will drop again. This process will continuously repeat until balance is restored.
Background information on cell balancing
What causes cell imbalance or a variation in cell voltages:
• The battery has not spent enough time in the absorption charge stage.
This can, for example, happen in a system where there is not enough solar power to fully charge the battery, or in systems where the generator is not running long or often enough. During normal operation of a lithium battery, small difference between cell voltages occur all the time. These are caused by slight differences between the internal resistance and self-discharge rates of each cell. The absorption charge stage fixes these small differences. We recommend a minimum absorption time of 2 hours per month for lightly operated systems, such as backup or UPS applications and 4 to 8 hours per month for heavy used (off-grid type) systems.
• The battery charger never reaches the storage (or float) stage.
The storage (or float) stage follows the absorption stage. During this stage, the charge voltage drops to 13.5V and the battery can be considered full. If the charger never enters this stage, it might be a sign that the absorption stage has not been completed (see previous point). The charger should be allowed to reach this stage at least once a month. This is also needed for battery monitor SoC (state of charge) synchronization.
• The battery has been discharged too deeply.
During a very deep discharge, one or more cells in the battery can drop well below their low voltage thresholds. The battery might be recoverable by rebalancing, but there is also a realistic chance that one or more cells are defective, and that rebalancing will not be successful. Consider the cell to be defective. This is not covered by warranty.
• The battery is old and is near to its maximum cycle life.
When the battery is close to its maximum cycle life, one or more battery cells will start to deteriorate, and the cell voltage will be lower than the other cell voltages. This is not imbalance, although it might look like it is. This cannot be fixed by rebalancing.
Consider the cell defective. This is not covered by warranty.
• The battery has a defective battery cell.
A cell can become defective after a very deep discharge, when it is at the end of its cycle life or because of a manufacturing fault. A defective cell is not unbalance (although it might look like it is). It cannot be fixed by rebalancing. Consider the cell defective. Very deep discharge and end of cycle life are not covered by warranty.
Calculation example of time required to restore a heavily imbalanced battery:
For this example, imagine a 12.8V, 200Ah battery with one heavily undercharged (discharged) cell.
A 12.8V battery contains 4 cells, each is 3.2V. And they are connected in series. Hence, 3.2 x 4 = 12.8V. Just like the battery, each cell has a capacity of 200Ah.
Let's say that the imbalanced cell is only at 50% of its capacity, while the other cells are fully charged. To restore the balance, the rebalancing process will need to add 100Ah to that cell.
The balancing current, which is a given fact, as per the specifications of the battery, is 1.8A. It will take at least 100/1.8 = 55 hours to rebalance the cell.
Page 32 Troubleshooting, support and warranty
Lithium Battery Smart Manual
Balancing only takes place when the charger is in the absorption stage. If a 2-hour lithium charge algorithm is used, the charger will need to be manually restarted 55/2=27 times during the rebalancing process. If the charger is not restarted immediately, the balancing process will be delayed, and this will add to the total balancing time.
A tip for Victron Energy distributors and professional users: To avoid having to restart the charger continuously, use the following trick. Set the float voltage at 14.2, this will have the same effect as the absorption stage. Also make sure to disable the storage stage, and/or set that to 14.2V as well. Or alternatively set the absorption time to a very long time. What matters is that the charger maintains a continuous 14.2V charge voltage during the rebalancing process. After the battery has been rebalanced, make sure to set the charger back to the normal lithium charge algorithm. Never leave a charger connected like this in a running system. Keeping the battery at such a high voltage will decrease the lifetime of the battery.
Less capacity than expected
If the battery capacity is less than its rated capacity these are the possible reasons for that:
• The battery has a cell imbalance, causing premature low voltage alarms, which in turn causes the BMS to turn loads off. Please refer to paragraph “Charge battery before use”.
• The battery is old and is near its maximum cycle life. Check how long the system has been in operation, check how many cycles the battery has gone through and to what average depth of discharge the battery has been discharged? A way to find this information is to look at the history of a battery monitor (if available).
• The battery bas been discharged too far and one or more cells in the battery are permanently damaged. These bad cells will have a low cell voltage faster than the other cells and this will cause the BMS to turn loads off prematurely. Has the battery perhaps been through a very deep discharge event?
Battery very low terminal voltage
If the battery has been discharged too far, the voltage will fall well below 12V (24V). If the battery has a voltage of less than 10V
(20V) or if one of the battery cells has a cell voltage below 2.5V, the battery will have permanent damage. This will invalidate the warranty. The lower the battery or cell voltage is, the bigger the damage to the battery will be.
If the voltage has dropped below 8V, the battery will not communicate via Bluetooth anymore. The Bluetooth module is turned off when the battery terminal voltage drops below 8V or if a cell voltage drops below 2V.
You can try to recover the battery by using the below low voltage recharge procedure. Be aware that this is not a guaranteed process, recovery might be unsuccessful and there is a realistic chance that the battery has permanent cell damage resulting in a moderate to severe capacity loss after the battery has been recovered.
Charge procedure for recovery after low voltage event:
This recovery charge procedure is performed on an individual battery. If the system contains multiple batteries, repeat this procedure for each individual battery.
This process can be risky. A supervisor must be present at all times.
• Set a charger or power supply to 13.8V (27.6V).
• In case any of the cell voltages is below 2.0V, charge the battery with 0.1A until the voltage of the lowest cell increases to 2.5V.
A supervisor must monitor the battery and stop the charger as soon as the battery is getting hot or is bulging. If this is the case the battery is unrecoverable damaged.
• Once the voltage of the lowest cell has increased above 2.5V, increase the charge current to 0.1C. For a 100Ah battery this is a charge current of 10A.
• Connect the battery to a BMS and ensure that the BMS has control over the battery charger.
• Make note of the initial battery terminal voltage and battery cell voltages.
• Start the charger.
• The BMS might turn the charger off, then on again for a short time and then off again. This can occur many times over and is normal behaviour in case there is a significant cell imbalance.
• Make note of the voltages at regular intervals.
• The cell voltages should increase during the first part of the charge process. If the voltage of any of the cells does not increase in the first half hour, consider the battery as unrecoverable and abort the charge procedure.
• Check the battery temperature at regular intervals. If you see a sharp increase of temperature, consider the battery as unrecoverable and abort the charge procedure.
Page 33 Troubleshooting, support and warranty
Lithium Battery Smart Manual
• Once the battery has reached 13.8V (27.6) increase the charge voltage to 14.2V (28.4V) and increase the charge current to
0.5C. For a 100Ah battery this is a charge current of 50A.
• The cell voltages will increase more slowly, this is normal during the middle part of the charge process.
• Leave the charger connected for 6 hours.
• Check the cell voltages, they should all be within 0.1V of each other. If one or more cells has a much bigger voltage difference, consider the battery as damaged.
• Let the battery rest for a few hours.
• Check the voltage of the battery. It should comfortably sit above 12.8V (25.6V) like 13.2V (26.4V) or higher. And the cell voltages should still be within 0.1V of each other.
• Let the battery rest for 24 hours.
• Measure the voltages again. If the battery voltage is below 12.8V (25.6V) or if there is a noticeable cell imbalance, the battery is unrecoverable damaged.
Battery is close to end of cycle life or has been misused
As a battery ages, its capacity will reduce and eventually one or more battery cells will become faulty. Battery age is related to how many charge/discharge cycles the battery has been through.
The battery can also have a reduced capacity or faulty cells if the battery has been misused, for example when the battery was discharged too far.
To determine what could have caused a battery issue, start by checking the battery history by looking at the history of a battery monitor or a Lynx Smart BMS.
VictronConnect battery history
To check if the battery is close to its cycle life:
• Find out how many charge/discharge cycles the battery has been subjected to. Battery lifetime is related to the number of cycles.
• How deep has the battery been discharged on average? The battery will last for less cycles if deeply discharged, compared to more cycles if discharged less deep.
• For more info on the life cycle see chapter
To check if the battery has been misused:
• Is the BMS connected and functional? Not using the battery with a Victron Energy approved BMS voids the warranty.
Page 34 Troubleshooting, support and warranty
Lithium Battery Smart Manual
• Is there mechanical damage to the battery, its terminals or the BMS cables? Mechanical damage voids the warranty.
• Has the battery been mounted upright? The battery can only be used in an upright position.
• Check the “allowed to charge minimum temperature” setting in VictronConnect? Also check if the battery temperature offset has not been set to an unrealistic value. Charging the battery below 5°C voids the warranty.
• Is the battery wet? The battery is not waterproof and is not suitable for outdoor use.
• Is there an indication that the battery has been totally discharged? Look at the battery monitor settings or VRM. Inspect the deepest discharge, minimum battery voltage and number of full discharges in the battery monitor. Total and very deep discharge voids the warranty.
• Is there an indication the battery has been charged with a too high voltage? Check the maximum battery voltage and the high voltage alarms in the battery monitor.
• How many synchronisations were there? Each time the battery is fully charged, the battery monitor will synchronise. This can be used to check if the battery is receiving a regular full charge.
• What was the time since last full charge? The battery needs to be at least fully charged once a month.
Communication error or hardware failure
In case of a communication error or a hardware failure a microcontroller restart might fix the issue.
To perform a microcontroller restart, do the following:
• In the VictronConnect app go to the battery.
• Go to the battery settings by clicking on the settings symbol in the top right hand corner.
• Go to product info by clicking on the option symbol in the top right hand corner.
• Click on "RESTART" text in the "Controller" listing.
If this procedure was unable to resolve the error, please contact your Victron Energy dealer or distributor.
Microcontroller restart
6.1.3. BMS issues
The BMS frequently disables the battery charger
A well-balanced battery does not disable the charger, even when the batteries are fully charged. But when the BMS frequently disables the charger, this is an indication of cell imbalance.
Page 35 Troubleshooting, support and warranty
Lithium Battery Smart Manual
In case of moderate or large cell imbalance it is an expected behaviour that BMS frequently disables the battery charger. This is the mechanism behind this behaviour:
As soon as one cell reaches 3.75V the BMS disables the charger. Whilst the charger is disabled the cell balancing process still continues, moving energy from the highest cell into adjacent cells. The highest cell voltage will drop, and once it has fallen below
3.6V the charger will be enabled again. This cycling typically takes between one and three minutes. The voltage of the highest cell will rise again quickly (this can be in a matter of seconds) after which, the charger will be disabled again, and so forth. This does not indicate a problem with the battery or the cells. It will continue with this behaviour until all cells are fully charged and balanced. This process might take several hours. It depends on the level of imbalance. In case of serious imbalance this process can take up to 12 hours. Balancing will continue throughout this process and balancing even takes place when the charger is disabled. The continued enabling and disabling of the charger can appear strange but rest assured that there is no problem. The
BMS is merely protecting the cells from over voltage.
The BMS is prematurely turning chargers off
This could be because of a cell imbalance. One cell in the battery has a cell voltage above 3.75V. Check the cell voltages of all the batteries that are connected to the BMS.
The BMS is prematurely turning loads off
This could be because of a cell imbalance.
If a cell has a cell voltage below the "Allowed to Discharge" setting in the battery the BMS will turn the load off. The "Allowed to
Discharge" level can be set between 2.6V and 2.8V. The default is 2.8V.
Check the cell voltages of all the batteries that are connected to the BMS using the VictronConnect app. Also check if all batteries have the same "Allowed to Discharge" settings.
Once the loads have been turned off due to low cell voltage, the cell voltage of all cells needs to be 3.2V or higher before the
BMS will turn the loads back on.
The pre-alarm setting is missing in VictronConnect
Pre-alarm is only available if the battery supports it. The current battery models all support it, but older batteries do not have the hardware necessary for the pre-alarm feature.
BMS is displaying alarm while all cell voltages are within range
A possible cause is a loose or damaged BMS cable or connector. Check all BMS cables and their connections.
First rule out that the cell voltages and temperature of all connected batteries are in range. If they are all in range, then follow one of the following procedures.
Also consider that once there has been a cell under voltage alarm, the cell voltage of all cells need to be increased to 3.2V before the battery clears the under voltage alarm.
A way to rule out if a fault is originating from a faulty BMS or from a faulty battery, is to check the BMS using one of the following
BMS test procedures:
Single battery and BMS check:
• Disconnect both BMS cables from the BMS.
• Connect a single BMS extension cable between both BMS cable connectors. The BMS cable should be connected in a loop, as in below diagram. The loop tricks the BMS in thinking that there is a battery connected without any alarms.
• If the alarm is still active after the loop has been placed, the BMS is faulty.
• If the BMS has cleared the alarm after the loop has been placed the battery is faulty and the BMS is not faulty.
Page 36
Testing a Lynx Smart BMS by connecting a single BMS extension cable to both BMS cable connections
Troubleshooting, support and warranty
Lithium Battery Smart Manual
Testing a Small BMS by connecting a single BMS extension cable to both BMS cable connections
Multiple batteries and BMS check:
• Bypass one of the batteries by disconnecting both its BMS cables
• Connect the BMS cables of the neighbouring batteries (or battery and BMS) to each other, effectively bypassing the battery.
• Check if the BMS has cleared its alarm.
• If the alarm has not been cleared, repeat this for the next battery.
• If the alarm is still active after all batteries have been bypassed, the BMS is faulty.
• If the BMS cleared its alarm when a particular battery was bypassed, that particular battery is faulty.
BMS
Eliminating a BMS error by bypassing a suspect battery
How to test if the BMS is functional
To test if the BMS is functional, disconnect one of the battery BMS cables and see if the BMS will go into alarm mode.
BMS
Check BMS functionality by deliberately loosening a BMS cable
6.2. Technical support
For technical support contact the point of purchase. If the point of purchase is unknown, refer to the Victron Energy Support web page .
6.3. Warranty
This product has a 3-year limited warranty. This limited warranty covers defects in materials and workmanship in this product and lasts for three years from the date of original purchase of this product. To claim warranty the customer must return the product together with the receipt of purchase to the point of purchase.
This limited warranty does not cover damage, deterioration or malfunction resulting from alteration, modification, improper or unreasonable use or misuse, neglect, exposure to excess moisture, fire, improper packing, lightning, power surges, or other acts of nature.
This limited warranty does not cover damage, deterioration or malfunction resulting from repairs attempted by anyone unauthorized by Victron Energy to make such repairs.
Non-compliance with the instructions in this manual will render the warranty void.
Victron Energy is not liable for any consequential damages arising from the use of this product. The maximum liability of Victron
Energy under this limited warranty shall not exceed the actual purchase price of the product.
Page 37 Troubleshooting, support and warranty
Lithium Battery Smart Manual
7. Technical data
VOLTAGE AND CAPACITY
Battery model LFP-
Smart
12,8/
50
Nominal voltage
12.8
V
Nominal capacity
@ 25°C*
Nominal capacity
@ 0°C*
Nominal capacity
@ -20°C*
Nominal energy @
25°C*
*Discharge current ≤1C
50Ah
40Ah
25Ah
640
Wh
48Ah
30Ah
768
Wh
12,8/
60
12.8
V
60Ah
12,8/
100
12.8
V
100A h
80Ah
50Ah
1280
Wh
2,8/1
60
12.8
V
160A h
130A h
80Ah
2048
Wh
12,8/
200
12.8
V
200A h
160A h
100A h
2560
Wh
12,8/
300
12.8
V
300A h
240A h
150A h
3840
Wh
12,8/
330
12.8
V
330A h
260A h
160A h
4220
Wh
25,6/
100
25.6
V
100A h
80Ah
50Ah
2560
Wh
25,6/
200
25.6
V
200A h
160A h
100A h
5120
Wh
25,6/
200a
25.6
V
200A h
160A h
100A h
5120
Wh
CYCLE LIFE (capacity ≥ 80% of nominal)
80% DoD
70% DoD
50% DoD
100A 120A
2500 cycles
3000 cycles
5000 cycles
200A
DISCHARGE
320A 400A 600A 400A 200A 400A 400A
Maximum continuous discharge current
Recommended continuous discharge current
End of discharge voltage
≤50A
11.2
V
≤60A
11.2
V
≤100
A
11.2
V
≤160
A
11.2
V
≤200
A
11.2
V
≤300
A
11.2
V
≤300
A
11.2
V
≤100
A
22.4
V
≤200
A
22.4
V
≤200
A
22.4
V
OPERATING CONDITIONS
Operating temperature
Storage temperature
Humidity (noncondensing)
Protection class
CHARGE
Charge voltage
Float voltage
Maximum charge current
Recommended charge current
Discharge: -20°C to +50°C Charge: +5°C to +50°C
-45°C to +70°C
Max. 95%
IP 22
100A
≤30A
120A
Between 14V/28V and 14.4V/28.8V (14.2V/28.4V recommended)
13.5V/27V
200A 320A 400A 600A 400A 200A 400A
≤30A ≤50A ≤80A ≤100
A
≤150
A
≤150
A
≤50A ≤100
A
400A
≤100
A
Page 38 Technical data
Lithium Battery Smart Manual
OTHER
Max storage time @
25°C*
BMS connection
Power connection
(threaded inserts)
Dimensions (h x w x d) mm
Weight
* When fully charged
M8
199 x
188 x147
7kg
M8
239 x
286 x
132
12kg
1 year
Male + female cable with M8 circular 3 pole connector, length 50cm
M8
197 x
321 x
152
14kg
M8
237 x
321 x
152
18kg
M8
237 x
321 x
152
20kg
M10
347 x
425 x
274
51kg
M10
265 x
359 x
206
30kg
M8
197 x
650 x
163
28kg
M8
317 x
631 x
208
56kg
M8
237 x
650 x
163
39kg
Page 39 Technical data
Lithium Battery Smart Manual
8. Appendix
8.1. Initial charge procedure without BMS
If, for a specific reason, the initial charge procedure needs to be performed without a BMS, this is the procedure for it. Please note that this is not something we recommend because this process can be risky. A supervisor must be present, who will need to watch their phone continuously for hours as the battery cell voltages must be checked continuously to safeguard that the voltage of the highest cell never exceeds 4V.
Charging without BMS is not the preferred method. It can be risky, and a supervisor must be present at all times.
These are the charger or inverter/charger settings when the battery is charged without a BMS:
Battery model
Recommended charger settings when performing an initial charge without a BMS
WARNING: Use these settings only during the initial charge process
Max.
charge current
Charge profile
Absorption voltage
Absorption time Float voltage
20A
30A
Lithium, fixed
Lithium, fixed
13.8V
13.8V
12h
12h
14.2V
14.2V
12.8V - 60Ah
12.8V -
100Ah
12.8V -
160Ah
12.8V -
200Ah
12.8V -
300Ah
25.6V -
200Ah
50A
60A
100A
60A
Lithium, fixed
Lithium, fixed
Lithium, fixed
Lithium, fixed
13.8V
13.8V
13.8V
27.0V
12h
12h
12h
12h
14.2V
14.2V
14.2V
27.6V
Storage voltage
13.5V
13.5V
13.5V
13.5V
13.5V
27.0V
Initial charge without using a BMS
Charge procedure:
• Use a battery charger that is suitable for Li-ion, such as a BluePower charger.
• Set the charger to the charge profile as indicated in above table.
• The supervisor connects with the VictronConnect app to the battery.
• The supervisor monitors the individual cell voltages at all times.
• The supervisor interrupts the battery charge process immediately should a battery cell voltage exceeds 4 Volt.
Page 40 Appendix
Lithium Battery Smart Manual
• The process is complete when all cell voltages are between 3.5V and 3.6V
8.2. Micro-controller power-cycle procedure
Note that when the system is installed and operated correctly, it will never be necessary to carry out this procedure. Carrying out this procedure is only necessary when the battery has been discharged far too deeply. And even then, only sometimes. Before opening the battery, carefully follow below instructions, to make sure this procedure is needed. Only use this procedure as a last resort, after all other troubleshooting options have been exhausted!
This procedure involves opening the battery cover and temporary disconnecting the positive terminal of the battery's internal circuit board. It should only be performed by Victron Energy dealers or distributors, technicians or professional users. If in doubt about performing this procedure consult your Victron Energy dealer or distributor.
Introduction and when to use this procedure:
After a battery has been discharged far too deep, ie. terminal voltages below 8V for a 12V model and 16V for a 24V model, a
. Read that chapter carefully. After such a too deep discharge, it can happen that the microcontroller does not power up correctly. This chapter explains how to fix that by power cycling the micro-controller. Before opening the battery, first carefully follow below instructions to make sure that it's necessary.
Note, that when installed and operated correctly, batteries will never be discharged to that level. Make sure to understand why it happened, and amend the installation and/or the operation of the system accordingly.
Lastly, be informed that this chapter is added to the manual for the benefit of installers and technically qualified users – to help to recover from such a situation without having to ship the battery out for repair. This does not at all mean that it is required to carry out this procedure yourself. The Victron service points and repair centres are happy to carry out the procedure when that is preferred. And, again, do note that once discharged as deeply as described here (cell voltages below 2V), the battery will be damaged and its usable capacity will, at best, have been reduced. And in the worst case the battery needs to be replaced.
How to recognise a stuck microcontroller:
First, make sure the system is within operational parameters:
• The battery needs to be charged and the battery voltage above 13V (26V).
• The battery temperature needs to be above the low temperature cut-off (default is 5°C or 41°F).
• The BMS cables between the battery and the BMS need to be connected and in good working condition.
Now, verify that the BMS still signals loads and chargers to disconnect. This table details how to do that for all available BMS-es:
The BMS is not allowing loads and chargers to operate when:
SmallBMS The blue "Load On" LED is off and the red "Temp or OVP" LED is on.
VE.Bus BMS
Lynx Smart BMS
The red LED is on, the blue LED is off and the MultiPlus/Quattro LED is on.
In VictronConnect (or a GX device IO tab) both the "Allow-to-charge" and the "Allow-to-discharge" parameters are disabled.
Smart BMS CL 12/100
Smart BMS 12/200
BMS 12/200
The yellow and orange LEDs are off.
The yellow and orange LEDs are off.
The "charge" and "output on" LEDs are off
Lastly, check that the battery is not visible in the VictronConnect device list. If the battery shows, the micro-controller is running normally and a power cycling is not required.
Micro-controller reset procedure:
• Opening the battery will expose 12Vdc (or 24Vdc) voltages that can not be isolated.
• Always use insulated tools when working on batteries.
• Prevent short circuits between the battery terminals, the battery cell terminals, the cell busbars and/or the internal circuit board. There is no fuse protection.
Page 41 Appendix
4
Page 42
1
2
Lithium Battery Smart Manual
Tools needed:
• Nylon or rubber hammer
• Scraper, chisel or flat screwdriver
• Insulated torque socket wrench M10 (electrical tape can be used to insulate the socket and part of the wrench)
• Electrical tape
• Remove the battery terminal wiring.
• Remove the terminal hex nuts.
3
• Carefully loosen or break open the lid. This can be done with a scraper, flat screwdriver or chisel.
When it creaks, it comes loose. Then continue a bit further until the lid is completely loose.
• Remove the top cover.
Appendix
7
8
5
6
Lithium Battery Smart Manual
• Insulate the negative busbar terminal located next to the positive battery terminal. Do this by covering the busbar with electrical tape. See red tape in the image on the left.
The electrical tape is a precaution to prevent a possible short-circuit between the positive battery terminal and the negative busbar.
• Loosen and remove the bolt that holds the positive circuit board wire cable lug.
• Leave the positive circuit board cable lug disconnected for a few seconds.
• Reinstall the positive circuit board cable lug and the bolt.
• Fasten the bolt using a 10Nm torque.
• Remove the electrical tape.
Page 43 Appendix
9
10
Lithium Battery Smart Manual
• Put the cover back on the battery.
• Reinstall the terminal hex nuts.
• Reinstall the battery terminal wiring.
• Check if the BMS is now allowing loads and chargers to connect to the battery.
• Check to see if the battery appears in the device list of the VictronConnect app*.
If the BMS is allowing loads and chargers, the procedure was successful.
* Note that if the battery does not appear in the device list, this can be because Bluetooth has been disabled. See the
chapter for more information.
Page 44 Appendix
advertisement
* Your assessment is very important for improving the workof artificial intelligence, which forms the content of this project
Related manuals
advertisement
Table of contents
- 18 How to charge batteries before use
- 19 Why charge batteries before use
- 20 Cable cross sectional area and fuse ratings
- 21 Connecting a single battery
- 21 Connecting multiple batteries in series
- 21 Connecting multiple batteries in parallel
- 22 Connecting multiple batteries in series/parallel
- 22 Battery banks consisting of different batteries
- 23 Allowed-To-Discharge cell voltage
- 24 Cell under voltage pre-alarm threshold
- 24 Allowed-To-Charge minimum temperature
- 24 Battery temperature offset
- 34 Cell imbalance
- 36 Less capacity than expected
- 36 Battery very low terminal voltage
- 37 Battery is close to end of cycle life or has been misused
- 38 Communication error or hardware failure
- 38 The BMS frequently disables the battery charger
- 39 The BMS is prematurely turning chargers off
- 39 The BMS is prematurely turning loads off
- 39 The pre-alarm setting is missing in VictronConnect
- 39 BMS is displaying alarm while all cell voltages are within range
- 40 How to test if the BMS is functional