advertisement
▼
Scroll to page 2
of
82
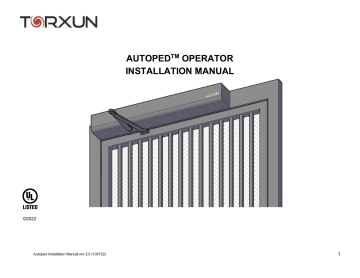
AUTOPEDTM OPERATOR INSTALLATION MANUAL ©2022 Autoped Installation Manual rev 2.0 (100722) 1 TORXUN reserves the right to make changes in the products described in this manual without notice and without obligation of TORXUN to notify any persons of any such revisions or changes. Additionally, TORXUN makes no representations or warranties with respect to this manual. This manual is copyrighted 2022 TORXUN Vehicle Access Systems, all rights reserved. No portion of this manual may be copied, reproduced, translated, or reduced to any electronic or digital medium without prior written consent from TORXUN. Autoped Installation Manual rev 2.0 (100722) 2 TABLE OF CONTENTS WELCOME LETTER FROM ART HIRD ……………………………………………………………………………………….…… 7 AUTOPED PARTS AND COMPONENTS………………………………………………………………………………….……….. 8 PARTS/COMPONENT LIST AND DESCRIPTIONS ………………………………………………………………………... 8 IMPORTANT INSTALLATION NOTES ……………………………………………………………………………………………... 9 A. AUTOPED CONVERSION: LEFT-HAND TO RIGHT-HAND (OR VICE VERSA) …………………………………… 9 B. AUTOPED ARM TYPES: PUSH ACTION (STANDARD ARM) OR PULL ACTION (TRACK ARM) ……………... 10 C. GENERAL REQUIREMENTS FOR INSTALLING THE AUTOPED …………………………………………………… 11 D. RECOMMENDED TOOLS FOR INSTALLATION ……………………………………………………………………….. 11 SECTION I. INSTALLING THE AUTOPED ON HEADERS 4” OR BIGGER ………………………………………………… 12 I.1 INSTALLATION: LEFT-HAND MOUNTED AUTOPED ………………………………………………………………… 13 I.2 INSTALLATION: RIGHT-HAND MOUNTED AUTOPED ………………………………………………………………. 14 SECTION II. INSTALLING THE AUTOPED ON HEADERS SMALLER THAN 4” …………………………………………... 15 II.1 INSTALLATION: LEFT-HAND MOUNTED AUTOPED ……………………………………………………………….. 16 II.2 INSTALLATION: RIGHT-HAND MOUNTED AUTOPED ……………………………………………………………… 17 SECTION III. INSTALLING THE STANDARD ARM ASSEMBLY (P/N: M10S.0028) ………………………………………... 18 III.1 INSTALLATION: STANDARD ARM ASSEMBLY………………………………………………………………..…..… 19 SECTION IV. INSTALLING THE TRACK ARM ASSEMBLY (P/N: M10S.0039) ……………………………………………... 22 IV.1 INSTALLATION: CONFIGURING THE AUTOPED FOR PULL ACTION ……………………….……………..…... 23 IV.2 INSTALLATION: TRACK ARM ASSEMBLY……………………………………………………………………..…….. 24 Autoped Installation Manual rev 2.0 (100722) 3 SECTION V. INSTALLING THE 3-FUNCTION ROCKER SWITCH (OR OPTIONAL KEY SWITCH) ……………………… 26 V.1 INSTALLATION: 3-FUNCTION ROCKER SWITCH .…………………………………………........…………………. 27 SECTION VI. CONNECTING THE AUTOPED TO AC POWER SOURCE ……………………………………………………. 29 VI.1 CONNECTING TO 115 VAC POWER SOURCE ……………………………………………………………………. 30 SECTION VII. INSTALLING THE OPTIONAL POSITIVE STOP (P/N: M10S.0040) …………………………………………. 31 VII.1 THE POSITIVE STOP KIT ………………………………………………………………………………………………. 32 VII.2 INSTALLING THE POSITIVE STOP …………………………………………………………………………………… 32 SECTION VIII. CLOSING-SPRING PRELOAD ……………………………………………………………………………….…... 34 VIII.1 ADJUSTING THE CLOSING - SPRING LOAD ..……………………………………………………………………… 35 SECTION IX. INSTALLING DOUBLE DOOR AND INTERLOCK SALLY PORT CONFIGURATIONS ………...………… 36 IX.1 SETUP SEQUENCE FOR DOUBLE DOOR/GATE OPERATION ………………………………..……………..…... 37 IX.2 SETUP SEQUENCE FOR INTERLOCK/SALLY PORT AIRLOCK ………………………………………………….. 39 SECTION X. INSTALLING ELECTRIC LOCKS, STRIKES AND SAFETY/ACCESS CONTROL DEVICES ………….…. 40 X.1 ELECTRIC LOCKS AND STRIKES SETUP …………………………………………………..………………………... 41 SECTION XI. QUICK START PROGRAMMING …………………………………………………………………………………. 42 XI.1 PROGRAMMING FLOW GUIDE CHART …………………………………………………..………………………... 43 XI.2 PROGRAMMING SEQUENCE FOR SINGLE DOOR/GATE OPERATION …………..……………………………. 41 XI.3 ADDITIONAL PROGRAMMING OPTIONS ……………………………………………..……………………………... 48 XI.4 FINAL ADJUSTMENTS AND COMPLIANCE TO ANSI 156.19 ……………………………...……………………… 48 XI.5 REATTACH CONTROL BOX COVER AND OPERATOR FRONT COVER………………………………………… 49 Autoped Installation Manual rev 2.0 (100722) 4 SECTION XII. MENUS AND PROGRAMMING …………………………………………………………………………………... 50 XII.1 MENU GLOSSARY ………..………………………...……………………………………….………………………….. 51 XII.2 CONTROL UNIT LED LIGHTS ……………...………………………………...…………….………………………….. 51 XII.3 LCD SCREEN GLOSSARY ……………………...…………………………………..….……………………………… 51 XII.4 CHART FOR MENUS AND WHAT THEY DO .…………………………………………….…………………………. 52 XII.5 PARAMETER MENU: SETTINGS FOR DOOR/GATE MOVEMENT ………………………………………..…...… 52 XII.6 CONFIGURATION MENU OPTIONS AND DEFINITIONS .………………………………………………………..... 55 XII.7 DOUBLE DOOR MENU CHART ………………………………………………………………...…………………..…. 56 XII.8 DIAGNOSTIC TABLE ……………………………………………………………………………………...…………….. 56 XII.9 REINIT MENU (RESET BACK TO FACTORY DEFAULT) ……………………………..……………...…..……..…. 57 XII.10 BLOCK/UNBLOCK MENU: LOCK KEYS ………………………………………………….……………….………... 57 XII.11 TEACH MENU ……...………………………………………………………………………….……………………...… 58 SECTION XIII. TROUBLE SHOOTING AND ERROR CHARTS ………………………………………………………………. 59 XIII.1 ERROR CODE DEFINITIONS ………………………………………………………………………………………… 60 SECTION XIV. TERMINAL CONNECTIONS AND WIRING SCHEMATICS ………………………………………………….. 65 XIV.1 TERMINAL CONNECTION CHART ………………………………………………………….……………………….. 66 XIV.2 WIRING SCHEMATIC DIAGRAMS ……………………………………………………….…………………………... 68 SECTION XV. SERVICE PARTS …………………………………………………………………………………………………… 77 XV.1 SERVICE PARTS/COMPONENTS VISUAL GUIDE ……….…….…………….……………………………………. 78 XV.2 STANDARD PARTS LIST …………………………………………..……………….………………………………….. 79 XV.3 OPTIONAL PARTS LIST ……………………………………………..……………….………………………………… 79 SECTION XVI. PRODUCT WARRANTY AND REGISTRATION ……………….………….…………………………………. 80 XVI.1 TORXUN LIMITED WARRANTY……………………………………………...………...……………………………... 81 XIV.2 PRODUCT REGISTRATION …………………………………………………………………….…………………….. 82 Autoped Installation Manual rev 2.0 (100722) 5 The above QR code will take you to a video demonstration of an AutoPed installation performed by Torxun. The video demonstrates a basic installation with a Standard Push Arm Assembly (P/N: M10S.0028). Autoped Installation Manual rev 2.0 (100722) 6 Welcome - thank you for your purchase! Our commitment to quality and innovation will become evident as you become familiar with the features, performance, and easy installation of this expertly engineered AutoPed heavy duty pedestrian swing Door/Gate operator. Some of its features are: o Fully outdoor rated o Built for continuous, heavy duty use for gates up to 250 lbs and 63” wide o UL 325 listed and designed to meet ANSI 156.19 low energy operated swinging door standards o A single model works for left and right-hand door/gates and push and pull applications Installers - I love you folks! I have been installing gate systems for decades. We have organized these instructions to keep things simple. This manual contains the instructions to install the AutoPed on a variety of header structures. You will find a “Quick Start Programming” in Section XI to get the AutoPed up and running its basic functions. When you need the AutoPed to perform its more complex functions and features, this manual provides you the additional “Menus and Programming” in Section XII. Throughout, we will point you right to the section to which you need to refer. Be safe! - think about your own safety during the installation. Also think about the safety of the public who will be using this automated gate for years to come. You NEED to be familiar with ANSI 156.19 standards. It is your responsibility to install and program the AutoPed to comply with these standards which include the velocity of the gate-in-motion, the force of the gate panel and the safety/warning labels. This manual will remind you of these responsibilities, but at the end of the day, you are the one in the field and are responsible for the publics’ safety! Options - some installations will require optional parts that you will need to order from your distributor to complete your installation. Refer to Section XV for AutoPed’s standard and optional parts components before you head out to install to confirm you have what you need. Owner/User - you are in for a treat! This operator is going to bring the satisfaction of automation to your property making residents and users happy that life has gotten just a little easier. Safety first! Please make sure that someone is responsible for daily checks of the gate system. For service, use only qualified and trained technicians. I want you to love this AutoPed Operator. I have been in this industry since 1976 and have never stopped trying to make products better. So let me know what you would like improved. .. AND what you appreciate. Art Hird, President Autoped Installation Manual rev 2.0 (100722) 7 AUTOPED OPERATOR STANDARD PARTS AND COMPONENTS Item Description 1 Enclosure - Front Cover 2 Enclosure - Rear Cover (Chassis) 3 Control Unit Cover - Front 4 Control Unit Cover - Rear 5 Control Unit 6 Motor-Gearbox Assembly 7 Assembly Plate 8 Spindle Extension; 20MM 9 Standard Arm Assembly 10 3-Function Rocker Switch 11 Mounting Template Assembly Plate Mounting 12 Screws Motor-Gearbox Assembly 13 Mounting Screws 14 Control Unit Mounting Screws Autoped Installation Manual rev 2.0 (100722) Qty 1 1 1 1 1 1 set 1 set 1 1 1 set 1 6 4 2 8 IMPORTANT INSTALLATION NOTES A. CONVERSION: LEFT-HAND INSTALLATION TO RIGHT-HAND INSTALLATION (or vice versa) The AutoPed operator can be used in a left-hand or right-hand, push or pull door/gate system application without need for conversion adapters or modification. To change the Hand of the Operator Installation: • Remove the motor-drive assembly attached to the assembly plate from the chassis by removing the six (6) M6x12 bolts; Fig 1 • Rotate the assembly plate with the motor-drive clockwise or counter-clockwise to facilitate either left- or – right-hand installation. • Chassis is neutral, Orientation is the same for left- or right- hand installation • Left-hand operator installation: Control unit is to the left of the motor-drive • Right-hand operator installation: Control unit is to the right of the motor-drive Fig I.1 Changing Operator Installation: Left-hand to Right-hand or vice versa Autoped Installation Manual rev 2.0 (100722) 9 B. AUTOPED ARM TYPES: PUSH ACTION (STANDARD ARM); PULL ACTION (TRACK ARM) B.1 Push Action – Standard Arm Assembly; P/N M10S.0028 If the required operation is “push open” the Door/Gate, the AutoPed is fitted with a Standard Arm; Fig B.1 Note that in this configuration, the door hinge is located on the side of the door frame opposite the location of the AutoPed. When the AutoPed is energized, the Standard Arm “pushes” to swing the door or gate open away from the AutoPed. Fig B.1 Standard Arm B.2 Pull Action – Track Arm Assembly; P/N M10S.0039 If the required operation is to “pull open” the Door/Gate, the AutoPed is fitted with the Track Arm; Fig B.2 Note that in this configuration, the door hinge and the AutoPed are both located on the same side of the door frame. When the AutoPed is energized, the Track Arm “pulls” to swing the door or gate open from under the AutoPed. Fig B.2 Track Arm Autoped Installation Manual rev 2.0 (100722) 10 C. GENERAL REQUIREMENTS FOR INSTALLING THE AUTOPED 1. Important: The AutoPed requires that the Door/Gate rest against some type of actual stop in the closed position. The unit will selfcheck the closed limits by attempting to close past the closed limit. If the unit does not sense the resistance of a stop, a locking device, or a door jamb, etc., the AutoPed will go into a soft shutdown. 2. The AutoPed cannot be installed on a Double acting door: a door that swings both in and out. 3. TORXUN recommends installing the AutoPed on Door/Gate headers measuring four inches (4”) or more in height. 4. For installation on headers less than four inches (4”) in height, TORXUN requires the use of the StiffenerPlate or equivalent to add rigidity to the installation of the operator; refer to Sections II.1 and II.2. D. RECOMMENDED TOOLS FOR INSTALLATION • • • • • • • • • • • • • • • Hammer Center punch set Portable power drill and bits (1/16”, 1/8”) Micro flat head screwdriver Flat head screwdriver ( 2mm) Philips head screwdriver #1 3mm Allen key 5mm Allen key 6mm Allen key Wire stripper Level gauge Wire nuts 22~14 gauge Masking tape Ladder or step stool Zip ties Autoped Installation Manual rev 2.0 (100722) 11 SECTION I INSTALLING THE AUTOPED ON HEADERS 4” OR BIGGER Autoped Installation Manual rev 2.0 (100722) 12 I.1 INSTALLATION: LEFT-HAND MOUNTED AUTOPED ON HEADERS 4” OR BIGGER STEP 1 Use left-hand side of Mounting Template STEP 4 Drill 1/16” pilot holes on header through Template STEP 5 Mount1 operator Chassis directly to header STEP 2 Align arrow to inside corner of left hinge jamb and bottom of header STEP 6 Mount2 Motor-Drive assembly to operator Chassis STEP 3 Center-punch mounting holes through Template STEP 7 Proceed to Section III or IV to continue installation of the swing arm assembly 1 2 Autoped Installation Manual rev 2.0 (100722) Type, size and material of fastener by installer Use Screw M6 x 1.0 x 12 included in kit 13 I.2 INSTALLATION: RIGHT-HAND MOUNTED AUTOPED ON HEADERS 4” OR BIGGER STEP 1 Use right-hand side of Mounting Template STEP 4 Drill 1/16” pilot holes on header through Template STEP 5 Mount3 operator Chassis directly to header STEP 2 Align arrow to inside corner of right hinge jamb and bottom of header STEP 6 Mount4 Motor-Drive assembly to operator Chassis STEP 3 Center-punch mounting holes through Template STEP 7 Proceed to Section III or IV to continue installation of the swing arm assembly 3 4 Autoped Installation Manual rev 2.0 (100722) Type, size and material of fastener by installer Use Screw M6 x 1.0 x 12 included in kit 14 SECTION II INSTALLING THE AUTOPED ON HEADERS SMALLER THAN 4” For installation of the AutoPed on headers less than four inches (4”) in height, TORXUN requires the use of the StiffenerPlate (P/N: M10S.011) or its equivalent to add rigidity to the installation of the operator. Autoped Installation Manual rev 2.0 (100722) 15 II.1 INSTALLATION: LEFT-HAND MOUNTED AUTOPED ON HEADERS LESS THAN 4” STEP 1 Put up the StiffenerPlate on the header STEP 4 Drill 1/16” pilot holes 1,2,3 STEP 5 Fasten5 StiffenerPlate through holes 1,2,3 STEP 6 Mount6 operator Chassis to StiffenerPlate STEP 2 Align the StiffenerPlate to the corner of the left hinge jamb and bottom of header; marked “X” on the drawing STEP 7 Mount7 Motor-Drive assembly to operator Chassis STEP 3 Center-punch pilot holes 1,2,3 STEP 8 Proceed to Section III or IV to continue installation of the swing arm assembly 5 Type, size, and material of fasteners by installer Use screws NF 7/16 x 20 x 3/4 included in kit to mount 7 Use screws M6 x 1.0 x 12 included in kit to mount 6 Autoped Installation Manual rev 2.0 (100722) 16 II.2 INSTALLATION: RIGHT-HAND MOUNTED AUTOPED ON HEADERS LESS THAN 4” STEP 1 Put up the StiffenerPlate on the header STEP 4 Drill 1/16” pilot holes 1,2,3 STEP 5 Fasten8 StiffenerPlate through holes 1,2,3 STEP 6 Mount9 operator Chassis to StiffenerPlate STEP 2 Align the StiffenerPlate to the corner of the right hinge jamb and bottom of header; marked “X” on the drawing STEP 7 Mount10 Motor-Drive assembly to operator Chassis STEP 3 Center-punch pilot holes 1,2,3 STEP 8 Proceed to Section III or IV to continue installation of the swing arm assembly 8 Type, size, and material of fasteners by installer Use screws NF 7/16 x 20 x 3/4 included in kit to mount 10 Use screws M6 x 1.0 x 12 included in kit to mount 9 Autoped Installation Manual rev 2.0 (100722) 17 SECTION III INSTALLING THE STANDARD ARM ASSEMBLY (PUSH ACTION OPERATION) P/N: M10S.0028 Autoped Installation Manual rev 2.0 (100722) 18 III.1 INSTALLATION: STANDARD ARM ASSEMBLY STEP 1 Assemble the Standard Arm Assembly STEP 2 Insert Standard Arm assembly with 20MM standard Extension Spindle to the Operator Gear Box NOTE: 30mm (M10S.0018) and 50mm (M10S.0055) Spindle Extension are available as optional parts ordered separately. If needed, it may be used instead of the 20mm to lower further the Standard Arm assembly to accommodate wider clearance/gap between bottom of AutoPed operator and top of Arm Shoe. Autoped Installation Manual rev 2.0 (100722) 19 STEP 3 Sit the Arm Shoe squarely on the face of the Door/Gate frame (or panel) STEP 4 For a left-hand mounted AutoPed, place centerline of Arm Shoe 4” to the right of the centerline of spindle. For a right-hand mounted AutoPed, place centerline of Arm Shoe 4” to the left of the centerline of spindle. NOTE: Make sure the Standard Arm is inserted to the Gear Box snugly and installed level. Autoped Installation Manual rev 2.0 (100722) 20 STEP 5 Use Arm Shoe mounting holes as template; mark the holes and center-punch through Door/Gate frame STEP 6 Drill 1/16” pilot holes on the center marks STEP 7 Use the appropriate fasteners11 to mount the Arm Shoe on the Door/Gate panel STEP 8 Loosen lock screws on Standard Arm assembly; adjust length of arm to form 90º between Standard Arm and Door/Gate panel STEP 9 Tighten the spindle bolt, mounting screws, set screws on the Arm Shoe and Standard Arm assembly respectively to complete the installation. STEP 10 Proceed to Section V to install the Rocker Switch (or Key Switch). 11 Type, size, and material of fasteners by installer Autoped Installation Manual rev 2.0 (100722) 21 SECTION IV INSTALLING THE TRACK ARM ASSEMBLY (PULL ACTION OPERATION) P/N: M10S.0039 Autoped Installation Manual rev 2.0 (100722) 22 IV.1 INSTALLATION: CONFIGURING THE AUTOPED FOR PULL ACTION The AutoPed is shipped out wired for a “push action” operation; Fig IV.1 Switch the AutoPed to “pull action” by following the steps below: 1. Remove the AutoPed’s Front Cover to expose the motor and wiring 2. Disconnect the orange pair of wire connector from the Motor input wire connector (with red and black wires) by pressing down on the lock tab on the connectors and pulling the connectors apart; see orange arrow in Fig IV.1 3. Push the plastic connector of the green pair of wires into the Motor input wire connector, see green arrow in Fig IV.2 4. The AutoPed is now configured for Pull action operation. Fig IV.1 Push action configuration Motor Input Wires Autoped Installation Manual rev 2.0 (100722) Fig IV.2 Pull action configuration Motor Input Wires 23 IV.2 INSTALLATION: TRACK ARM ASSEMBLY NOTE: • Use the Track Arm with a standard 20mm Spindle Extension. • If the 20mm Spindle Extension is not sufficient to extend the Track Arm down to the Door/Gate frame, use the optional 30mm or 50mm extensions • Make sure that the swing of the Track Arm clears the top of the gate frame by at least 1/2” and that the Door/Gate swing is unobstructed by the Track Arm assembly STEP 3 Align the AutoPed Chassis to the Hinge Centerline Fig IV.3 Track Arm Assembly STEP 1 Assemble the Track Arm to the AutoPed STEP 4 Move the AutoPed up or down (↕) until bottom of Track Arm clears the top of the Door/Gate frame by a minimum gap of ½” throughout the top of the Gate Frame STEP 2 Place the AutoPed up onto the Header Autoped Installation Manual rev 2.0 (100722) 24 STEP 5 Mark the mounting holes of the Chassis on the Header STEP 6 Take down the Chassis with the assemblies STEP 7 Drill pilot holes for Chassis mounting on the Header STEP 10 Perform the following check: a. Manually open and close the Door/Gate to check for a smooth and unobstructed swing of the Door/Gate panel. b. Check that the Slider piece glides smoothly inside the Track Guide. STEP 8 Mount12 the Chassis with assemblies on the Header STEP 11 Replace the left and right endcaps of the Track Guide. STEP 12 Proceed to Section V to install the Rocker Switch (or Key Switch). NOTE: All the preceding installation steps also apply to a Right-hand mounted operator. Note that the measure of 4” in Step 9 will be on the opposite side of the illustration for a Right-hand install. STEP 9 Mount the Track Guide on the Door/Gate Frame • Insert the Slide Piece in the Track Guide • Place the Track Guide on the Door/Gate Frame • Move the end of the Track Guide about 4” from the Slide Piece, (see illustration above) 12 Type, size, and material of fasteners by installer Autoped Installation Manual rev 2.0 (100722) 25 SECTION V INSTALLING THE 3-FUNCTION ROCKER SWITCH (OR OPTIONAL KEY SWITCH, P/N: M10S.0083) Autoped Installation Manual rev 2.0 (100722) 26 V.1 INSTALLATION: 3-FUNCTION ROCKER SWITCH (see next section for the optional Key Switch) Provided with your operator is a 3-function switch that switches the operator and door/gate function to one of three modes: a. Manual mode – door/gate has no automation; gate can be manually operated by pushing or pulling b. Normal mode – door/gate opens and closes automatically based on activation inputs and programming c. Hold mode – door/gate opens and stays open allowing for continuous access NOTE: The Switch can be installed at the bottom left or right of the AutoPed operator; knockouts are provided at both ends STEP 1 Choose and punch out one knockout at the bottom of the AutoPed chassis (NOTE: The following illustrations show the use of the left knockout) STEP 2 Feed the switch wires through the knockout Autoped Installation Manual rev 2.0 (100722) STEP 3 Sit the switch body squarely on the chassis STEP 4 Feed the switch wires through the rubber grommet; connect to Block X110 as shown in drawing below; (see schematic circuit in Fig 1.7b in the following page) 27 NOTE: Optional 3-Function Key Switch (P/N M10S.0083) For more secure applications, an alternate to the Rocker Switch is the Key Switch, an option that can be purchased from TORXUN distributors. The Key Switch has the same 3-Function feature as the Rocker Arm Switch and has a spring-loaded cap/cover to protect the key cylinder. ⚠ When installing the key switch on a pull application gate; be aware of the clearance between the top of the gate panel and the switch with a key in it. It is possible for the gate panel to strike the key while opening. Install the Key Switch in the same way the Rocker Switch is installed; see Section V.1, p.27 Installation: 3-Function Rocker Switch. Fig V.1a 3-Function Key Switch Fig V.1b Rocker or Key Switch Schematic Autoped Installation Manual rev 2.0 (100722) 28 SECTION VI CONNECTING THE AUTOPED TO AC POWER SOURCE (115 VAC) Autoped Installation Manual rev 2.0 (100722) 29 VI.1 CONNECTING TO 115 VAC POWER SOURCE NOTE: The Chassis has Wire Access Holes on either end to feed through a 115 VAC supply line Do not cut into the operator front cover or chassis. Use only the cut-outs provided to route wirings. STEP 4 Connect the 115 VAC wires to the Power Connector STEP 1 Shut off 115 VAC power to Operator STEP 2 Pull out Power Connector from Control Unit STEP 5 Use wire nut to connect Line Ground and Green Pigtail wires together STEP 3 Feed the 115 VAC line through a Wire Access Hole Use only water tight conduit connections STEP 6 Plug Power Connector back to Control Unit; turn AC power back on Autoped Installation Manual rev 2.0 (100722) 30 SECTION VII INSTALLING THE OPTIONAL POSITIVE STOP (P/N M10S.0040) TORXUN requires a physical stop (wall, fence, floor stop or similar) to prevent the door/gate from opening beyond 105 degrees. Without it, the AUTOPED may be damaged by being forced into an over-open position. The internal positive stop is an alternative solution for locations without aggressive wind loads. Autoped Installation Manual rev 2.0 (100722) 31 VII.1 OPTIONAL POSITIVE STOP KIT (P/N M10S.0040) NOTE: Depending on the function of the operator, push or pull, you may have to change the location of the positive stop cam to the other mounting hole. You want to use the positive stop cam mounting location closest to the rotation of the gear box. VII.2 INSTALLATION: OPTIONAL POSITIVE STOP STEP 1 Swing Door/Gate to desired opening; keep the door in open position. STEP 3 Install the Positive Stop Cam Bracket and Cam; use the two stainless steel M6x3 bolts included in the kit STEP 2 Remove top two bolts on the Gear Box mounting plate Autoped Installation Manual rev 2.0 (100722) 32 STEP 4 Gather the Spindle bolt, Positive Stop Clamp & Spindle STEP 5 Assemble the Stop Clamp and Spindle together STEP 6 Insert Clamp and Spindle assembly to the Gearbox IMPORTANT NOTE ON STEP 6 Make sure that the Stop Clamp* and Stop Spindle* are flush with each other when assembled (see drawing above*). Place the Stop Clamp so that its rounded vertical face (contact point) is almost contacting the Positive Stop Cam at full open. STEP 7 Insert the Spindle Bolt to the Positive Stop Clamp* and Stop Spindle*; tighten to fasten the assembly to the Gearbox. Autoped Installation Manual rev 2.0 (100722) 33 SECTION VIII CLOSING-SPRING PRELOAD The spring tension may need to be adjusted to regulate the closing pressure of the door or gate panel. Make these adjustments when the door or gate panel does not fully close or slams when closing. Autoped Installation Manual rev 2.0 (100722) 34 VIII.1 ADJUSTING THE CLOSING-SPRING PRELOAD The AutoPed operator is equipped with a closing spring that aids in the closure of the gate/door and to keep closing speeds while the gate/door is in manual mode. When power to the operator is cut or turned off, the closing spring will allow the Door/Gate to close in a controlled manner, fully latching the door lock system. The tension of the spring regulates the amount of pressure the door requires to be pushed open. Preload adjustment is done by turning the Adjusting Screw. By default, distance X between top of head of Adjusting Screw and spring bracket is: X = 1-1/32 inch (26 mm) Autoped Installation Manual rev 2.0 (100722) 35 SECTION IX INSTALLING DOUBLE DOOR AND INTERLOCK SALLY PORT CONFIGURATIONS Autoped Installation Manual rev 2.0 (100722) 36 IX.1 SETUP SEQUENCE FOR DOUBLE DOOR/GATE OPERATION IMPORTANT NOTE: The AutoPed must be initially programed for basic functions before it can be setup for Double Door/Gate Operation. Refer to Section XI: Quick Start Programming for this purpose. Warning: The default setting of the AutoPed is "Low Energy." The AutoPed is ONLY approved and warranted for Low Energy, ANSI 156.19 applications. It is the responsibility of the installing party to adhere to ANSI 156.19 standards when completing the AutoPed installation. Use of the AutoPed for Full Energy applications is PROHIBITED. TORXUN IS NOT RESPONSIBLE FOR LIABILITY ASSOCIATED WITH FULL ENERGY APPLICATIONS. The AutoPed is capable of being linked to another AutoPed unit and working in tandem with that other unit. The two operators must be physically connected with a CAN-Bus at terminal X117 to function as double doors; Fig IX.1 STEP 1 Move the joystick up or down to scroll through the menu selections until you get to Double Door. • Press the joystick in to select the Double Door section and you will get DoubleD on the screen. • Toggle the joystick left or right to select if the operator will be designated as one of the following: Master A, Master B, Slave A, Slave B. • An activation of the slave door will open both, while and activation of the master will only open the master. • Wire all activation devices to the slave operator so that both units will activate from a single input device. STEP 2 Wire between Master and Slave/Secondary Operators • Wire the AutoPed Master A to Slave A. Run the wire between terminal X117 on each control board. (See Fig XIV.2g, p.76 Wiring Fig IX.1 Double Door In Tandem Autoped Installation Manual rev 2.0 (100722) 37 Schematics, and Section XII.7, p.56 for programming information) • When the CANbus connection is made between the AutoPed controllers, the master is identified by a small black (m) and the slave by a small black (s) on their respective LCD’s. • If a CANbus connection does not exist, the master is identified by a small white (m) and the slave by a small white (s). STEP 3 Vo • Using the joystick, toggle down to VO (opening speed) and set the desired opening speed STEP 4 AoSeq • Using the joystick in the Master Operator, toggle down to AoSeq. • AoSeq is the delay angle of the Master before the Slave/Secondary begins its opening sequence. For example, if you set AoSeq to 20° then the slave operator's gate will wait until the master gate breaks the 20° mark then it will start to open. STEP 5 TDelay • If an electric lock is installed on the gate system, the choice TDelay will function the same way that it would in the normal programming sequence and adjust the amount of time that the gate delays before moving to allow time for the lock to release. For this set up, refer to TDelay in Table VII.6 of Sec VII Menus and Programming STEP 6 AcSeq • Using the joystick on the Slave operator, select AcSeq. AcSeq is the delay for the master closing sequence. The default AcSeq setting is 0 degrees. This will work the same way that AoSeq does, allowing a set degree of closure to happen before the master gate starts movement. Autoped Installation Manual rev 2.0 (100722) 38 IX.2 SETUP SEQUENCE FOR INTERLOCK/SALLY PORT/AIRLOCK IMPORTANT NOTE: The AutoPed must be initially programed for basic functions before it can be setup for Interlock/Sally Port Operation. Refer to Section XI: Quick Start Programming for this purpose. The gates can be spaced apart from each other and connected to each other via a CAN BUS connection to create an interlocking system similar to an air lock or sallyport, Fig IX.2. When Gate A gets an open command, it will block out any inputs to Gate B until Gate A is fully closed. The same is true for Gate B. When Gate B is opened, Gate A will not be able to open until Gate B is fully closed. STEP 1 CAN BUS wire between gate A and gate B Operators • Wire the AutoPed in gate A to the AutoPed in gate B. Run the CAN BUS wire between terminal X117 on each control board; (see item X117 in Section XIV Terminal Connections and Wiring Schematics on p.67 ) STEP 2 InterL • Enter the DoubleD menu • Make sure that DoubleD is off in the Double Door menu. • Using the joystick toggle down to InterL o Set one control unit to side A and the other to side B • With the two control units set to interlock A and B respectively, they will work independent of each other but not allow input commands to be activated on one gate until the other has completed its cycle Fig IX.2 Interlock/Sally Port Autoped Installation Manual rev 2.0 (100722) 39 SECTION X SETTING UP ELECTRIC LOCKS AND STRIKES Autoped Installation Manual rev 2.0 (100722) 40 X.1 ELECTRIC LOCKS AND STRIKES SETUP For wiring of the locks and strikes, see Fig XIV.2d (1, 2), and Fig XIV.2e (1, 2) in Section XIV Terminal Connections and Wiring Schematics, p.71, p.73. When setting up an electric lock, all the needed settings can be found in the configuration menu of the AutoPed controller. The following are the settings that you will need. NOTE: When setting up fail safe and fail secure locks, the difference is in the wiring of the locks not the settings. The settings will apply to all electric locks and strikes including mag locks. STEP 1 Click the joystick next to the LCD screen in to enter the menus section. STEP 2 Using the joystick, toggle down to the Config menu. STEP 3 Press the joystick in to access the configuration section. STEP 4 Using the joystick, toggle down to the section “Unlock” • Set unlock to Permanent; refer to Section XII.6 on p.55 for additional information STEP 5 Using the joystick, toggle down to EL – Fb (Electric Lock - Feedback) • Set EL-Fb to N.C.; refer to Section XII.6 on p.55 for additional information STEP 6 Using the joystick, toggle down to LockAu (Lock Automatic) • Set LockAu to lock; refer to Section XII.6 on p.55 for additional information STEP 7 Using the joystick, toggle down to LockEx (Local Exit) • Set LockEx to lock; refer to Section XII.6 on p.55 for additional information STEP 8 Using the joystick, toggle down to LockMa (Lock Manual) STEP 9 Set LockMa (Lock Manual) to lock; refer to Section XII.6 on p.55 for additional information Autoped Installation Manual rev 2.0 (100722) 41 SECTION XI QUICK START PROGRAMMING NOTE 1: If using Track Arm for pull action operation, make sure the AutoPed is converted for pull action; see Section IV.2, p.23 NOTE 2: Remember to select SLI-PL when initializing the programming of the operator; see Step 3 of Sec XI.2, p.45 Autoped Installation Manual rev 2.0 (100722) 42 XI.1 PROGRAMMING FLOW GUIDE CHART Anytime an item in the “Parameter” menu is changed, the E10 code will appear and a “Teach” cycle becomes necessary Autoped Installation Manual rev 2.0 (100722) 43 XI.2 PROGRAMMING SEQUENCE FOR SINGLE DOOR/GATE OPERATION ⚠ Following are the basic programming steps for the AUTOPED operator. Complete these 12 steps before addressing advanced programming requirements. Warning: The default setting of the AutoPed is "Low Energy." The AutoPed is ONLY approved and warranted for Low Energy, ANSI 156.19 applications. It is the responsibility of the installing party to adhere to ANSI 156.19 standards when completing the AutoPed installation. Use of the AutoPed for Full Energy applications is PROHIBITED. TORXUN IS NOT RESPONSIBLE FOR LIABILITY ASSOCIATED WITH FULL ENERGY APPLICATIONS. Once power has been supplied or reconnected to the control unit, indicator lights will flash, and the LCD display will light up with the current software version. Locate the LCD display window and the joystick adjacent to it. The joystick (encircled in red; Fig II.2) can be moved: Up (↑), Down (↓), Left (←), Right (→) and pressed in to accept the selected command. The following procedures will get the AUTOPED operational with basic programming. The control unit is password protected; Fig XI.2b. When you get to the “password” screen: o The password is three nudges to the left on the joystick ←,←,← o Then three nudges to the right on the joystick. →,→,→ Fig XI.2a Joystick Fig XI.2b Password Screen STEP 1: Screen Orientation The words “Press Down” will appear on the LCD screen. The text will alternate between being right side up and upside down. Nudge the joystick down (↓) to set the screen orientation upright. NOTE: The downward movement of the joystick is in relation to the installer, not the text on the screen. The screen will set its orientation based on the downward nudge of the joystick. Autoped Installation Manual rev 2.0 (100722) 44 STEP 2: Region Selection o Press the joystick in and then either left or right (←,→) to select “Region US (USA)” STEP 3: Rod o Select the appropriate arm assembly type: o STD-PH (Standard Push Arm) o NOTE: When using the standard push arm, use the orange wire connectors. When using the optional Track Arm Assembly, use the green wire connections. o SLI-PL (optional track arm pulling configuration) P/N: M10S.0039 o SLI-PH (optional track arm pushing configuration) P/N: M10S.0039 o ⚠ WIN-PH, DIR-PH, DIR-PL, OHC-PH, OHC-PL will not be used! ⚠ o Press the toggle in to select the appropriate arm type STEP 4: dAxis o The D Axis is the distance from the chassis mounted to the header to the centerline of the hinge spindle. Measure this distance on the door/gate. o Toggle left and right to get the correct number in inches and press the joystick in to confirm the selection. Autoped Installation Manual rev 2.0 (100722) 45 STEP 5: Ao o Ao is the angle of opening. o The default selection is 95°, toggle left or right to select the desired angle of opening then press the joystick in to confirm the selection. o ⚠ If a physical stop such as a bollard, wall, or cleat is NOT in place to stop the Gate/Door, the use of the Physical Stop Kit is required. P/N: M10S.0040 STEP 6: LowEn o This is the type of function in which the AutoPed will operate. o The default is “LowEn on”. o Keep the operator in LowEn on and press the joystick in to confirm the selection. o The operator is intended to be used in LowEn mode which complies with the ANSI 156.19 standards o ⚠ Warning: The default setting of the AutoPed is "Low Energy." The AutoPed is approved and warranted only for Low Energy, ANSI 156.19 applications. It is the responsibility of the installing party to adhere to ANSI 156.19 standards when completing the AutoPed installation. Use of the AutoPed for Full Energy applications is PROHIBITED. TORXUN is not responsible for liability associated with FULL ENERGY applications. STEP 7: Width o Measure the gate leaf from outside edge to outside edge and use the toggle left or right to select the correct width in inches of the gate leaf. Press the joystick in to confirm the selection. o ⚠ UL 325 approves the gate width up to 63” STEP 8: Weight o Calculate the approximate weight of the gate leaf. o Use the joystick either left or right to select the approximate weight in pounds (lbs) of the gate leaf o Press the joystick in to confirm the selection. o ⚠ UL 325 approves the operator for weights up to 250lbs STEP 9: Vo o Vo controls the velocity/speed at which the gate opens. o The default setting is 9, nudge joystick left and right to select the desired speed, press the joystick in to confirm the selection; i.e.. In LowEn ON mode, the selection Autoped Installation Manual rev 2.0 (100722) 46 maximum is 9. ⚠ TORXUN recommends setting Vo between 1-3 for initial set up. Once the operation of the gate is confirmed, then the desired speed can be finalized in compliance with ANSI 156.19. ⚠ STEP 10: Vc o Vc controls the Velocity/speed at which the gate closes. o Default is set to 9, use the joystick left and right to select the desired speed. Press the joystick in to confirm the selection; i.e. In LowEn ON mode, the selection maximum is 9 ⚠ TORXUN recommends setting Vc between 1-3 for the initial set up. Once the operation of the gate is confirmed, then the desired speed can be finalized in compliance with ANSI 156.19 ⚠ STEP 11: Invers o Using the joystick left and right, set Invers to “OFF”. Press the joystick in to confirm the selection. o Invers refers to configuring the Door/Gate to open when power is lost. In such rare applications the gate will default (spring) to open and operate to close. ⚠ ATTENTION: At this point, clear the area of any persons or objects in the path of the gate to avoid injuries or damages. Proceed to the next step once the path of the gate is clear. ⚠ STEP 12: Teach o Press the joystick in to move to the next selection. o “Teach ok?” will appear on the screen o Press the joystick in again and you will hear beeping as well as see a ten (10) second countdown on the screen. o Once the countdown ends, the gate will open, pause, and then close while beeping. If no errors occur, the LCD display will display “Done!” with “E11” underneath it. o E11 requires the operator to be run through one more full Open and Close cycle via activation command to confirm the settings. Autoped Installation Manual rev 2.0 (100722) 47 XI.3 ADDITIONAL PROGRAMMING OPTIONS Before completing the installation, install any additional hardware or make further programming adjustments. These may include: a. Push and Go (when the gate is pushed open a programmable set of degrees, the AutoPed will take over and open the gate the rest of the way; Section VII.7 APuGO in the Configuration Menu). b. Internal Physical Stop Kit P/N: M10S.0040 (a mechanical option which prevents the gate from being forced beyond 105 degrees to protect the AutoPed operator; see Section VII Installing the Optional Positive Stop c. Closing Spring Preload (adjust the pressure of the door/gate closure to overcome the gate slamming or not fully latching); see Section VIII Adjusting The Closing Spring Load. d. Programming for Double Door system; refer to Section IX. e. Programming for the Interlock Sally Port; refer to Section IX. XI.4 FINAL ADJUSTMENTS AND COMPLIANCE TO ANSI 156.19 Make final adjustments to the controller programming and gate operation. ANSI 156.19 is a safety standard that protects pedestrians when using a low energy automatic door/gate. The AutoPed is designed so that each installation can comply with this standard. ⚠ IMPORTANT It is the responsibility of the INSTALLER to adjust the AutoPed so that the gate operates in compliance with ANSI 156.19. Each gate is different so adjustments must be made on a gate-by-gate basis. Refer to the ANSI 156.19 standards for the tables that prescribe: • The speed/velocity of the opening and closing of gate being installed based on its width and weight. Speed is adjusted in the Vo and Vc settings in the Parameters menu. • The force of the gate when opening and closing. Force is adjusted in the Fo and Fc settings in the Parameters menu. • Use a Door Pressure Gauge tool to properly calibrate the force (pressure) of the opening and closing of the gate panel; Fig XI.4 • Signage – Attach signage(s) to Door/Gate and activation switches as specified by ANSI 156.19 Fig XI.4 Typical Door Pressure Gauge Tool (refer to Vendor’s Instructions on use) Autoped Installation Manual rev 2.0 (100722) 48 XI.5 REATTACH THE CONTROL BOX AND OPERATOR FRONT COVER a. Reattach front plastic cover of Control Box After the unit has been cycled a few times and your ANSI checklist has been completed, reattach the plastic cover onto the control unit. Align the gaskets into the cut outs so that they sit flush. Tighten the two provided screws into the threaded sections of the control board. Give the cover a slight tug to make sure that it is secured properly. ⚠ Do not over tighten the cover. ⚠ Make sure that the grommets are completely seated in the cut outs on both ends and sealed properly within the groove. b. Reattach the operator Front Cover There are two knock outs on the Front Cover that will correspond with the arm coming from the gearbox. Remove the appropriate knock out for the location of the arm and slide the front cover onto the operator. Secure the front cover to the chassis with the four (4) thumb screws. Tighten the thumb screws by hand until the front cover is secured to the chassis. Autoped Installation Manual rev 2.0 (100722) 49 SECTION XII MENUS AND PROGRAMMING Autoped Installation Manual rev 2.0 (100722) 50 XII.1 MENU GLOSSARY Display OEO OEI KEY SES PRE SER SEF EMY-IN PUGO Description Exterior activation sensor (exterior activation signal) Interior activation sensor (interior activation signal) Activation device (external switch activation signal, key switch, card reader, etc.) Swing side Door/Gate mounted sensor (swing side safety signal) Header mounted sensor on swing side Push side door mounted sensor (approach side safety signal) Door mounted sensor for obstacle detection Emergency open input (emergency input signal) Push and go XII.2 CONTROL UNIT LED LIGHTS LED SOK OE active SE active Error E-lock relay LED description and color indications Description System ok Opening devise Safety devise Error E-lock relay Indicator Green flashing Blue=active Yellow=active Red White XII.3 LCD SCREEN GLOSSARY Display <REF?> < ?? > >< >##< <<>> <> >><< == Autoped Installation Manual rev 2.0 (100722) Description Waits for reference switch Unknown: position of the gate is unknown to the operator Closed Closed and locked Opening Open Closing Stopping 51 XII.4 CHART FOR MENUS AND WHAT THEY DO Menu Title PARAMETER CONFIG DOUBLE DOOR DIAGNOSTICS ERROR ACTIVE Description Sets the parameters for swing Door/Gate movements Configuration: sets the configuration of the AutoPed control features and functions Sets the closing sequence and interlock function for double door applications Diagnostic tools that display the status of various inputs ❖ Displays pending active errors ❖ A0 indicates the latest active error ❖ Displays all active errors that were detected and then corrected or not corrected. ❖ H0 indicates the latest active error Reinitialization resets settings back to factory default Locks/unlocks joystick Start the software upgrade process from a USB stick ❖ Programs the initial setup, finds errors (if any) ❖ Programs a new setup procedure when necessary HISTORY ERROR REINT BLOCK? UPDATE SW TEACH XII.5 PARAMETER MENU: SETTINGS FOR DOOR/GATE MOVEMENT Device Region Unit type Low Energy Default US US Vo Vc TOEx Low energy Low energy Low energy 9 9 5s 0-9 0-9 3-60s TKey Low energy 5s 3-180s TPuGo Low energy 3s 3-180s TDelay Low energy .2s 0.0-4.0s FDelay Low energy Off Off-7.0A Autoped Installation Manual rev 2.0 (100722) Value Description US- united states Software version decided by UL standards Velocity of opening 9=fastest, 0=slowest Velocity of closing 9= fastest, 0= slowest Sets the hold open time for the OEO or OEI input commands. ANSI 156.19 for low energy: TOEx must be no less than 5 seconds. ❖ TKey sets the hold open time resulting from an activation signal from a device (referred to as KEY) on terminal X102 ❖ With TOEx and TKey, you can set a different hold open time for different activation devices by using different terminals Determines how long the Door/Gate stays open when activated by the push and go feature. Tdelay sets the amount of time the door hesitates to allow the lock to release before opening. Fdelay is a temporary “hold closed” force applied to the door to keep it closed while the electric lock is released. This parameter sets the amount of force applied. FDelay is only active if TDelay setting is greater than 0. 52 TLock Low energy 0.5s 0.0-4.0s Flock Low energy 2.0A Off-7.0A FSlam Low energy Off Off-10 FWind Low energy Off Off Open Close Both Fo Low energy 9 0-9 Fc Low energy 9 0-9 Foh Fch Low energy Low energy 4 0.0A 0-9 0.0A-3.5A LowEn Low energy On On Width Low energy 48in 30-63in Weight Ao Low energy Low energy 100~250lbs 100-550lbs 95° 20°-190° Autoped Installation Manual rev 2.0 (100722) Sets amount of time Door/Gate panel will press against lock to engage it. Sets amount of force applied to the Door/Gate panel to engage the lock at the closed position. It is only active if TLock setting is greater than 0. Accelerating function (Force Slam). For example: when a Door/Gate panel needs to be forced shut due to a latch or heavy seals. ❖ Wind load detection optimized for exterior doors/gate panels ❖ Assuming that a gust of wind is not a hard obstacle which will stop the door, the motor current will rise “slowly.” In this case the AutoPed control unit will supply additional power to continue the door movement. ❖ When FWind is turned ON, TORXUN strongly recommends the use of Door/Gate panel mounted sensors to stop or reopen the door if an obstacle is detected during the door cycle ❖ Opening force (force open) when an obstacle is detected during open/close cycle or both ❖ In standard mode obstacle detection cannot be switched on/off. It can be adjusted with parameters for “Fo”=force opening and “Fc”=force close. To make obstacle detection least sensitive, set both parameters on 9. To make obstacle detection most sensitive, set both parameters on 0. (Caution, this can allow the drive to react to slight changes in wind) Hold open force (force hold open) ❖ Interlocking force (force close hold) automatically programs Flock and FDelay if these settings are set at 0. ❖ If there is no electric lock and the interlocking force Fch is not adjusted, error 14/02 will be displayed as a warning after the teach 1 procedure and the Door/Gate will endlessly reopen. Door/Gate panel is low energy in both directions. Door/Gate panel is activated by a knowing act. Width of the Door/Gate panel from edge to edge. ⚠UL approval for maximum width of 63” ⚠ Weight of the Door/Gate panel. ⚠UL approval for 250lbs⚠ Opening angle of the door (angle open) Teach must be activated after this setting has been changed 53 Rod Full and low STD-PH Rod Low energy STD-PH Inverse Low energy Off dAxis Low energy 7in Autoped Installation Manual rev 2.0 (100722) STD-PH Outswing Push function using Standard Arm assembly arm and Motor cable connector: X=orange Arm-Shoe SLI-PL Inswing arm Pull function using Track Arm assembly with track (P/N: M10S0039) and roller Motor cable connector: Y=Green SLI-PH Outswing Push function using Track Arm assembly with inswing (P/N: M10S0039) track and Motor cable connector: X=orange roller ❖ If panic breakout latch is installed and the motor is plugged in backwards or the wrong arms are chosen during programming, there is a possibility the Door/Gate panel can burst open unexpectedly towards the installer once TEACH mode is initiated. ❖ Teach must be activated after this setting has been changed. OffIn case of a power failure/error, the Door/Gate panel is opened by spring power On from any position (unless it has been locked). The position of the motor connector is reversed on the standard drive unit. Teach must be activated after this setting has been changed. 2Distance between center line of the door hinge spindle(s) and the mounting 25in surface of the operating assembly. dAxis is an approximate value. Depending on the installation situation, dAxis may have to be estimated. Teach must be activated after this setting has been changed. 54 XII.6 CONFIGURATION MENU OPTIONS AND DEFINITIONS Device APuGO ASES Off 95° Default Off, 2°-10° 45°-95° ASER 0° 0°-60° SESClo Inactive Active Inactive EMY-IN CL-SPR OExSTp Unit type Off CL-SPR STOP OPEN CL-MOT Off OEI OEO KEY RADIO UNLOCK PERMAN EL-FB Off IMPULS PERMAN Lock AU UNLOCK Off N.O. N.C. UNLOCK/LOCK LockEX LOCK UNLOCK/LOCK LockMA UNLOCK UNLOCK/LOCK Autoped Installation Manual rev 2.0 (100722) Description Triggering angle for Push and Go (angle Push and Go) Lock out angle: Angle at which the swing side Door/Gate panel mounted sensor is ignored just before open/ If Ao is changed, ASES is automatically set to Ao. Lock out angle: angle at which push side of the Door/Gate panel sensor is ignored just before closing. Sensor mounted on swing side of Door/Gate is activated or inactivated during closing cycle Configuration of the emergency terminal (break contact switch) Spring close (standard application) Stops Door/Gate panel closing/opening Opens the Door/Gate panel Motor close (inverse application) N/A ❖ Used to set one of the activation “values” to “sequential” mode. Opening devise ❖ Sequential mode is used to hold the door open until a inside second activation is received. Opening devise ❖ One activation opens the Door/Gate panel, and a outside second activation is needed to close the Door/Gate Key opening panel. devise N/A When the Door/Gate panel is first opened: momentarily unlocks the electric lock When the Door/Gate panel is first opened: Permanently unlocks the electric lock. Electric lock status feedback Open if unlocked (-); closed if locked (+) Open if locked (+); closed if unlocked (-) ❖ Sets the condition of the lock when in automatic mode. ❖ Only visible when Unlock is set to PERMAN. ❖ Sets the condition of the lock when in EXIT mode. ❖ Only visible when Unlock is set to PERMAN ❖ Sets the condition of the lock when in MANUAL mode. ❖ Only visible when Unlock is set to PERMAN 55 LcdDir MovCon Pre Sen OExMAN 0 OFF N.C. ON 0-1 OFF/ON Off/N.C./N.O. OFF/ON Orientation of the display (LCD direction) Endurance test Open/Close (moving continuous) Swing side presence sensor output logic ❖ On enables activation to reopen the door during the closing cycle of a manual opening. ❖ OExMAN only if APuGo is turned OFF XII.7 DOUBLE DOOR MENU CHART Device DoubleD Off Default AoSeq 20° Value Off MastrA SlaveA MastrB SlaveB 0-110° AcSeq 20° 0-110° InterL Off ILAuto Active ILExit Active ILNigt Active Off SideA SideB Inacti Active Inacti Active Inacti Active Description Closing sequence role and interlocking side Current delay angle for opening sequence control (only visible if DoubleD is active) Current delay angle for closing sequence control (only visible if DubleD is active) Interlocking door system where one door will only receive open commands once the other is closed Interlock mode Operating mode AUTOMATIC (only visible in InterL is active) Interlock mode operating mode EXIT (only visible if InterL is active) Interlock mode Operating mode Night (only visible in InterL is active) XII.8 DIAGNOSTIC TABLE Devise K-I-O-R-S-P-E Description (K) Key (I) OEI (Interior Activation Sensor) (O) OEO (Exterior Activation Sensor) (R) SER (Push Side Door Mounted Sensor) (S) SES (Swing side door mounted sensor) (P) Swing side header mounted presence Autoped Installation Manual rev 2.0 (100722) Value (+) Active (-) Inactive (Read only and cannot be changed) 56 -0.0A ; 0° X.YA/Z° Simulate Key E-Lock PG Version SW Version UL Version HW Version Cycles RO R1 FP RP sensor (E) EMY-IN (Emergency Open Input) Displays motor current and the swing door opening angle (Example: 2.1A ; 65°) Displays the actual current used by the motor and the current angle of the door/ gate panel. Key command that opens the door panel by pressing OK L- Display status of the lock FB- Display input El-FB. Press OK to activate the electric locking device Packaged software Version of software Software changed due to UL specifications Version of logic PCB Total number of openings the gate has performed. Display what the Door/Gate panel is doing (R0) Relay print with address 0 (R1) N/A (FP) N/A (RP) N/A (L+) locked (L-) Unlocked (FB+) Locked (FB-) Unlocked (-) Identified and ready for operation (+) Neither identified nor registered (a) Defective or error (x) Removed XII.9 REINIT MENU (RESET BACK TO FACTORY DEFAULT) Device FACTORY RESET PARAM RESET CONFIG RESET DOUBLE RESET Description All settings that were programmed into the control will be reset to factory defaults Resets/sets all motion parameters back to the default values (inclusive opening angle, rod assemblies, invers and dAxis) Resets all configuration settings back to the default values Resets simultaneous pair settings and airlock settings back to the default values XII.10 BLOCK/UNBLOCK MENU: LOCK KEYS Menu Block? UBLOC? BlockD Description To lock the joystick Press ok for 2 seconds The display shows temporarily BLOC! To unlock the joystick Press ok for 2 seconds The display shows temporarily UBLOC When the joystick is blocked, the “home display” shows BLOCKD if the joystick is operated! Autoped Installation Manual rev 2.0 (100722) 57 XII.11 TEACH MENU Device TEACH OK? Description Programs the setup procedure within the AutoPed controller. Autoped Installation Manual rev 2.0 (100722) 58 SECTION XIII TROUBLE SHOOTING AND ERROR CHARTS Autoped Installation Manual rev 2.0 (100722) 59 XIII.1 ERROR CODE DEFINITION A F H W A0 Drive unit deactivates itself during a certain period: manual operating mode or stopping position Fatal error Manual operating mode with restarting attempt Warning A(active error); (0) most recent error Error No E1 01 02 03 04 05 06 E2 07 08 09 10 11 12 13 02 E3 01 02 Description Encoder Motor Current Latch check (cushioning) Cause Channel A lost Channel B lost Channel A+B lost Short Circuit A+B Malfunctions Motor Cable incorrectly plugged in No signal channel A No signal channel B No signal channel A+B Short Circuit A+B Malfunctions Malfunctions Encoder not connected Current too high Current too low Jumper missing Test failed once Test failed twice Damping defective Opening beyond range of operator Autoped Installation Manual rev 2.0 (100722) Elimination • • • • check: o o o Encoder Connection Motor Cable If jumper is inserted on x106 Direction of motor rotation does not match swing side of door Door is blocked Check: o Motor cable o Confirm jumper is inserted on x106 Switch the drive unit to Manual operating mode. Carefully check if the door closes in a cushioned manner. • If not: replace hardware • If yes: check/correct the friction of the Door/Gate and the pre-stressing of the closing spring Checking time During Run Reaction H Prior to Start-up H During Encoder Test H Prior to Start up During Test H H Always Prior to start up H H Prior to closing cycle (after startup) W F (Drive unit is functioning Buzzer Active) 60 Error No E4 01 Description Reference switch 02 03 04 Cause Range of operator detected in the Open Position Not detected in the Closed Position Not detected in the closed Position Not detected in the open position in “INVERS” mode • • • • E5 00 Power limitation Control overload Maximum power is restricted • • E10 01 Full teach required 02 E11 01 02 Half teach required (opening) Half teach required (closing) Elimination Check: o The connection o Switching the point of the reference switch Reference switch must be activated in closed position (switch contact to open) Before start (teach) door must be in open position Reference switch must be activated in open position (switch contact open) Checking time Open position Prior to the first setup run A Check/correct: o Friction of the Door/Gate o Pre-load of closing spring Ensure maximum door weight is not exceeded Permanent A H W Parameter Ao, Rod, Invers or dAxis was changed Carry out a learn cycle Minimum opening angle has not been achieved Check the locking/ electric lock Upon changing the drive unit configuration During teach Parameter Vo changed Carry out a complete and unhindered opening cycle Upon changing the speed parameters Parameter Vc or ForceSlam changed Carry out a complete and unhindered closing cycle Autoped Installation Manual rev 2.0 (100722) Reaction F H 61 Error No E14 01 Description Locking/Electr ic lock Cause The Door/Gate got caught in the locking/electric lock The inverted operation has no locking, or the interlocking force Fch has not been programmed Elimination Check the function of the locking/electric lock Program/increase the interlocking force Fch Checking Time When opening from a closed position At the end of the teach procedure Reaction H Obstacle during opening Obstacle during closing Too many successive obstacles have occurred • • • Permanent H, A Restart after 60 seconds Temperature Temperature on output level has reached 178°F Allow the unit to cool down Permanent A Drive unit functions with reduced power A Drive unit has stopped A 02 E15 01 02 E16 01 02 E20 01 Temperature on output level has reached 196°F SER test (Swing side safety) 02 E21 01 02 Examine the installation Remove the obstacle Move the Door/Gate to the target position SES test (Push side safety) SER test signal unsuccessful SER short circuit to the earth. Check the cabling of the sensor or the jumper SER too slow SER reacts too slowly. Check the cabling for the sensor. Check for polarity reversal/test signal. Prior to closing SES test signal unsuccessful Prior to opening SES too slow Autoped Installation Manual rev 2.0 (100722) SES short circuit to the earth. Check the cabling of the sensor or the jumper. SES reacts too slowly. Check the cabling of the sensor. Check for polarity reversal/test signal. W E20-01 and E20-02 together, no line in between, like E21 A 62 Error No E22 01 Description EMY-IN test (emergency input) Cause EMY-IN input on 24v E30 01 02 03 30v error 30v too low 30v too high Error upon switching on E31 01 02 24v general Error upon switching on Over-resp, under-voltage E32 01 24v safety Over-resp, under voltage E33 01 24v E-lock Error: over-resp under voltage Premonition: over-resp under voltage Over resp under voltage 02 02 E34 01 24v CAN E60 00 10 20 30 Malfunction Elimination Check the jumper NOT. Check the cabling of the NOT Restart the control unit SW update necessary Main’s failure, overload motor. Check 115vac line. Replace hardware Checking time Permanent Overload, short circuit of the 24v inputs (without electric lock, safety sensors) Overload, short circuit safety sensors Overload, short circuit electric lock After power up permanent Reaction H After power up Permanent A After power up A (restart after 10 seconds) W Overload, short circuit external power supply CAN Relay PCB 0 Relay PCB 1 Radio PCB Fire Protection E50 01- System error E51 99 E52 Optional PCB has been removed, its address changed or became defective Check if the option is provided. If defective: replace or remove from configuration. Permanent W W W A Unexpected hardware or software event Permanent W or H or F E70 XX CAN bus setting CAN address XX existing twice Switch the drive unit Off/On. Carry out a Factory Reset, Carry out a software update, inform the manufacturer Correctly define the role of the closing sequence or the interlock function Permanent W E71 01 CAN connection No CAN connection Plug in, check, or replace the CAN cable Check if all the CAN participants are switched on Permanent W Autoped Installation Manual rev 2.0 (100722) 63 Error No E80 01 02 E81 01 02 Description Continuous routine MCU routine Cause Malfunction Elimination ----Power down then power up ----Power down then power up Checking time Permanent E82 01 02 Dynamic routine Damping test failed ----Power down then power up Motor current test failed ----1. Power down then power up again 2. If problem is not resolved, turn the “ForceSlam potentiometer adjuster” fully counterclockwise. 3. If the problem still is not resolved, replace the faulty control and or motor operator. After power down then every 24hrs when Door/Gate is closing Test occurs at the door closed position E83 01 02 Static routine Autoped Installation Manual rev 2.0 (100722) Before: opening Door/Gate Closing Door/Gate Reaction W F W F W F W F 64 SECTION XIV TERMINAL CONNECTIONS AND WIRING SCHEMATICS Autoped Installation Manual rev 2.0 (100722) 65 XIV.1 TERMINAL CONNECTION CHART Terminal Description X101 Opening command outside (OEO) X101 Opening command inside (OEI) X102 Key Operated Switch X103 X104 Plug in connection to the Power Supply Unit Programmable Emergency Close or Open or Stop X105 Safety Devise Stop X106 X107 Jumper Safety Devise Reverse X108 Electric Lock X110 External Program Selector (three position Rocker Switch or Optional Key Switch P/N: M10S.0100) used to activate preprogrammed options Autoped Installation Manual rev 2.0 (100722) Connector 8 9 10 11 12 13 1 2 3 N/A 4 5 14 15 16 17 N/A 18 19 20 21 27 28 29 30 31 32 SA SL SO SM SW SG Description 24VDC OEO GND 24VDC OEI GND 24VDC KEY GND N/A EmA EmB SE 24V SE Stop SE Test GND N/A SE 24V SE Rev SE Test GND EL 24V GND EL-COM EL-NO EL-NC EL-Fb Auto Locked Hold Open Manual One Way GND 66 Terminal Description X111 Present Sensor (Sensor is only checked before the door moves) X113 X114 X115 X116 Connection to the Encoder Power/Program Selector Switch Serial Port Connection to the Relay PCB Board X117 Can Bus (for dual door installation) X118 USB/Service Autoped Installation Manual rev 2.0 (100722) Connector PU PI PO PG N/A N/A N/A N/A Description Programmable I/O Voltage Programmable Input Programmable Output GND N/A N/A N/A N/A CG CL CH N/A GND CAN Low CAN High N/A 67 XIV.2 WIRING SCHEMATIC DIAGRAMS Fig X.2a 3-Function Switch Wiring Diagram (Rocker Arm and Key type switches) Autoped Installation Manual rev 2.0 (100722) 68 Fig XIV.2b Non-Powered Activation Devices Autoped Installation Manual rev 2.0 (100722) 69 Fig XIV.2c Powered Activation Devices NOTE: Do not exceed 2A 24V draw from the Board. TORXUN recommends one board powered accessory only. Others should be powered by independent power supplies. Autoped Installation Manual rev 2.0 (100722) 70 Fig XIV.2d Locking Devices Powered by the AutoPed Operator 1. FAIL SECURE: Powered by Control Board Configuration Settings: Unlock : Permanent EL-FB (Electric Lock - Feedback : N.C. LockAu (Lock Automatic) : Lock LockEx (Lock Exit): Lock LockMa (Lock Manual) : Lock NOTE: Do not exceed 2A 24V draw from the Board. TORXUN recommends one board powered accessory only. Others should be powered by independent power supplies Autoped Installation Manual rev 2.0 (100722) 71 2. FAIL SAFE: Powered by Control Board Configuration Settings: Unlock : Permanent EL-FB (Electric Lock – Feedback) : N.C. LockAu (Lock Automatic) : Lock LockEx (Lock Exit): Lock LockMa (Lock Manual) : Lock NOTE: Do not exceed 2A 24V draw from the Board. TORXUN recommends one board powered accessory only. Others should be powered by independent power supplies Autoped Installation Manual rev 2.0 (100722) 72 Fig XIV.2e Locking Devices Powered by Another Source (not powered by AutoPed Operator) 1. FAIL SECURE: Powered by External Source Power to Lock: 24 VDC, 800 mA Max Configuration Settings: Unlock : Permanent EL-FB (Electric Lock – Feedback): N.C. LockAu (Lock Automatic): Lock LockEx (Lock Exit): Lock LockMa (Lock Manual): Lock SECTION XV SERVICE PARTS Autoped Installation Manual rev 2.0 (100722) 73 2. FAIL SAFE: Powered by External Source Power to Lock: 24 VDC, 800 mA Max Configuration Settings: Unlock : Permanent EL-FB (Electric Lock – Feedback): N.C. LockAu (Lock Automatic): Lock LockEx (Lock Exit): Lock LockMa (Lock Manual): Lock Autoped Installation Manual rev 2.0 (100722) 74 Fig XIV.2f Secured Activation Devices Autoped Installation Manual rev 2.0 (100722) 75 Fig XIV.2g Wiring for Double Door/Gate System Autoped Installation Manual rev 2.0 (100722) 76 SECTION XV SERVICE PARTS Autoped Installation Manual rev 2.0 (100722) 77 XV.1 SERVICE PARTS/COMPONENTS VISUAL GUIDE Autoped Installation Manual rev 2.0 (100722) 78 XV.2 STANDARD PARTS LIST ITEM# TORXUN PART NUMBER DESCRIPTION QTY 1 M10S.0001 REV A ENCLOSURE - FRONT COVER 1 2 M10S.0001 REV A ENCLOSURE - CHASSIS 1 3 M10S.0020 CONTROL UNIT FRONT COVER 1 4 M10S.0019 CONTROL UNIT REAR COVER 1 5 M10S.0022 CONTROL UNIT 1 6 M10S.0021 MOTOR-GEARBOX ASSEMBLY 1 7 M10S.0010 MOUNTING PLATE 1 8 M10S.0017 SPINDLE EXTENSION 20MM 1 9 M10S.0028 STANDARD SWING ARM ASSY 1 10 M10S.0092 3-FUNCTION ROCKER SWITCH 1 11 M10S.0034 PAPER MOUNTING TEMPLATE 1 12 M10S.0056 M6 -1 x12 (fastens mounting plate to chassis) 6 13 M10S.0026 M6 -1 x 18 (fastens gearbox to mounting plate) 4 14 M10S.0027 M4 x 10 (fastens control unit box to mounting plate) 2 XV.3 OPTIONAL PARTS LIST ITEM# TORXUN PART NUMBER DESCRIPTION QTY S1 M10S.0011 STIFFENERPLATE 1 S2 M10S.0040 POSITIVE STOP KIT 1 S3 M10S.0018 EXTENSION SPINDLE 30MM 1 S4 M10S.0055 EXTENSION SPINDLE 50MM 1 S5 M10S.0039 TRACK ARM ASSEMBLY 1 S6 M10S.0083 3-FUNCTION KEY SWITCH WITH SAFETY COVER S7 9700.0001 DOOR PRESSURE GAUGE TOOL S8 9750-0004, 9750-0006, 9750-0008 RADIO FREQUENCY ANTENNA KIT Autoped Installation Manual rev 2.0 (100722) 1 SET 1 1 SET 79 SECTION XVI PRODUCT WARRANTY AND REGISTRATION Autoped Installation Manual rev 2.0 (100722) 80 XVI.1. TORXUN LIMITED WARRANTY To the original purchaser only: TORXUN Vehicle Access Technologies, (hereafter referred to as TORXUN) warrants, for one (1) year from the date of invoice, the gate operator systems and other related systems and equipment manufactured by, and distributed by TORXUN, to be free from defects in material and workmanship under normal use and service for which it was intended provided it has been properly installed and operated. TORXUN’s obligations under this warranty shall be limited to the repair or exchange of any part or parts manufactured by and distributed by TORXUN. Defective products must be returned to TORXUN, freight prepaid by purchaser, within the warranty period. Items returned will be repaired or replaced, at TORXUN’s option, upon an examination of the product by TORXUN, which discloses, to the satisfaction of TORXUN, that the item is defective. TORXUN will return the warranted item freight prepaid. The products manufactured by TORXUN and distributed by TORXUN are not warranted to meet the specific requirements, if any, of safety codes of any state, municipality, or other jurisdiction, and TORXUN does not assume any risk or liability whatsoever resulting from the use thereof, whether used singly or in combination with other machines or apparatus. Any products and parts not manufactured by TORXUN and distributed by TORXUN, will carry only the warranty, if any, of the manufacturer. This warranty shall not apply to any products or parts thereof which have been repaired or altered, without TORXUN’s written consent, outside of TORXUN’s workshop, or altered in any way so as, in the judgment of TORXUN, to affect adversely the stability or reliability of the product(s) or has been subject to misuse, negligence or accident, or has not been operated in accordance with TORXUN’s instructions or has been operated under conditions more severe than, or otherwise exceeding, those set forth in the specifications for such product(s). TORXUN shall not be liable for any loss or damage whatsoever resulting, directly or indirectly, from the use or loss of use of the product(s). Without limiting the foregoing, this exclusion from liability embraces a purchaser’s expenses for downtime or for making up downtime, damages for which the purchaser may be liable to other persons, damages to property, and injury to or death of any persons. TORXUN neither assumes nor authorizes any person to assume for them any other liability in connection with the sale or use of the products of TORXUN. The warranty herein- above set forth shall not be deemed to cover maintenance parts, including, but not limited to, hydraulic oil, filters, batteries, or the like. No agreement to replace or repair shall constitute an admission by TORXUN of any legal responsibility to effect such replacement, to make such repair, or otherwise. This limited warranty extends only to wholesale customers who buy directly through TORXUN’s normal distribution channels. TORXUN does not warrant its products to end consumers. Consumers must inquire from their selling dealer as to the nature and extent of that dealer’s warranty, if any. This warranty is expressly in lieu of all other warranties expressed or implied including the warranties of merchantability and fitness for use. This warranty shall not apply to products or any part thereof which have been subject to accident, negligence, alteration, abuse, or misuse or if damage was due to improper installation or use of improper power source, or if damage was caused by fire, flood, lightning, electrical power surge, explosion, wind storm, hail, aircraft or vehicles, vandalism, riot or civil commotion, or acts of God. Autoped Installation Manual rev 2.0 (100722) 81 XVI.2 PRODUCT REGISTRATION Date Today:_______________ End User Location & Information Installer Information First Name, Last Name Company Name Company/ Association First Name, Last Name Street Address Street Address City City State State Zip Code Zip Code Telephone Telephone Email Address Email Address Product Information Operator and Gate Use Model Name/ Number [ ] Residential [ ] Commercial/ Multi-Family Serial Number [ ] Restricted Access Facility [ ] Parking Spaces Inside Garage Purchase Date Installation Date Distributor’s Name Distributor’s City Fax or Email this completed form to: TORXUN ™ 50 Sloan Court Tracy, CA 95304 Fax: 888-492-4283 Email: [email protected] Autoped/GS033120 Autoped Installation Manual rev 2.0 (100722) 82
advertisement
Related manuals
advertisement