Schneider Electric Loop CTRL -> A120 -> AKF, CLC12 V1.1 Configuration Guide
Add to my manuals
98 Pages
advertisement
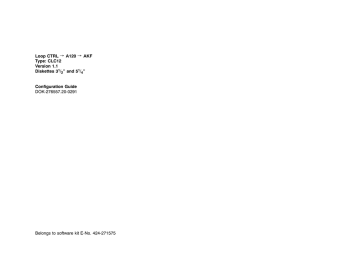
Loop CTRL → A120 → AKF
Type: CLC12
Version 1.1
Diskettes 3 1 /
2
” and 5 1 /
4
”
Configuration Guide
DOK-276557.20-0291
Belongs to software kit E-No. 424-271575
Overview
Notes
Table of Contents
Part I How to Proceed?
Part II Closed Loop Control Function Blocks
Part III Application
Part VII
Part VIII
Part IX
Part IV Appendix
Part V
Part VI
20
20
Notes
Table of Contents
20 v
vi
20
Notes
Application Note
Caution The relevant regulations must be observed for control applications involving safety requirements.
For reasons of safety and to ensure compliance with documented system data, repairs to components should be performed only by the manufacturer.
Training
AEG offers suitable training that provides further information concerning the system (see addresses).
Data, Illustrations, Alterations
Data and illustration are not binding. We reserve the right to alter our products in line with our policy of continuous product development. If you have any suggestions for improvements or amendments or have found errors in this publication, please notify us by using the form on the last page of this publication.
Addresses
The addresses of our Regional Sales Offices, Training Centers, Service and Engineering Sales Offices in Europe are given at the end of this publication.
20 vii
Copyright
All rights reserved. No part of this document may be reproduced or transmitted in any form or by any means, electronic or mechanical, including copying, processing or any information storage, without permission in writing by the AEG Aktiengesellschaft. You are not authorized to translate this document into any other language.
Trademarks
All terms used in this user manual to denote AEG products are trademarks of the AEG Aktiengesellschaft.
IBM, IBM-PC, IBM-XT and IBM-AT are registered trademarks of International
Business Machines Corporation.
Microsoft and MS-DOS are registered trademarks of Microsoft Corporation.
© 1990 AEG Aktiengesellschaft.
viii
20
Terminology
Note This symbol emphasizes very important facts.
Caution This symbol refers to frequently appearing error sources.
Warning This symbol points to sources of danger that may cause financial and health damages or may have other aggravating consequences.
Expert This symbol is used when a more detailed information is given, which is intended exclusively for experts (special training required). Skipping this information does not interfere with understanding the publication and does not restrict standard application of the product.
Path This symbol identifies the use of paths in software menus.
Figures are given in the spelling corresponding to international practice and approved by SI (Système International d‘ Unités).
I.e. a space between the thousands and the usage of a decimal point
(e.g.: 12 345.67).
20 ix
AKF
IL
FPF
DT1-part
FB
HVAC
NW
P-controller abbr. instruction list (IL), ladder diagram (LD), unction block diagram (FBD) instruction list fire protection flap real differential part of controller function block heating, ventilation and air conditioning network proportional-action controller
PI-controller
PID-controller
PADT
CLC-FB
<Alt>
<Del> proportional-plus-integral controller proportional-plus-integral-plus-derivative controller programming and debugging tool closed loop control function block
PC
I&C programmable controller central instrumentation and control
<Cr>, <Return> use carriage-return key
<Ctrl> use control-key use alternate-key use delete-key all three keys held down: warm restart x
20
Objectives
Present software and documentation can only be used together with softwarepackage Dolog AKF → A120.
This manual is designed for configuration of closed-loop control programs on
Modicon A120.
It contents information about installing the software on personal computer and the use of function blocks. The configuring of FBs (parameters, time etc.) will be described. As an introduction into the configuration of closed-loop control programs using CLC 12C software, the software kit contains an application example of heating, ventilation and air conditioning and the application of controlling an reacting-tank in process engineering.
Arrangement of This Guide
General This part contains the preface of the documents, describes the handling of install-disks and contains a detailed table of contents of this manual.
Part I Checklist for proceeding with present software kit.
Part II Requirements, installation and specification of closed-loop control function blocks.
Part III Installation and specification of application ‘I&C, HVAC’.
20 xi
Part IV Appendix
Addresses dresses
Publicatons Comment Form
Contain the adof the sales agencies at home and abroad.
Please use this form a lot, if you have any questions or corrections regarding the doumentation or software.
Related Documents
Software Kit
Dolog AKF → A120
Type: AKF12
E No 424-271521
Validity Note
This manual is assigned for software CLC12 version 1.1.
Translation of description DOK-275578.20.
xii
20
Handling 3
1
/
2
” Diskettes
No cleaning of diskettes.
Store diskettes in protective containers and boxes.
Temperature
Humidity
10 to 60 C
8 to 80%
Insert diskettes correctly.
No water on diskettes.
No heavy objects on diskettes.
No erasing on diskettes.
Diskettes tolerate no heat
(sunshine).
Label diskettes at the right spot.
Don’t move the metal slide.
No diskettes near magnetic fields.
No forcing diskettes into disk drive.
Always keep in mind
20 xiii
Handling 5
1
/
4
” Diskettes
No diskettes near magnetic fields.
Store diskettes in protective containers and boxes.
Label diskettes at the right spot.
No cleaning of diskettes.
No bending or folding of diskettes.
Temperature
Humidity
10 to 50 C
8 to 80%
Insert diskettes correctly.
No water on diskettes.
No heavy objects on diskettes.
xiv
No erasing on diskettes.
Diskettes tolerate no heat
(sunshine).
No paper clips on diskettes.
Touch only protected parts of diskettes.
No painted pencils for writing on diskettes.
No forcing diskettes into disk drive.
Always keep in mind
20
Table of Contents
20
Part I How to Proceed?
. . . . . . . . . . . . . . . . . . . . . . . .
1
Chapter 1 Checklist . . . . . . . . . . . . . . . . . . . . . . . . . . . . . . . . . . . . . . . . .
3
Part II Closed Loop Control Function Blocks . . . .
5
Chapter 1 Requirements . . . . . . . . . . . . . . . . . . . . . . . . . . . . . . . . . . . . .
7
Chapter 2 Installation of Function Blocks . . . . . . . . . . . . . . . . . . . .
9
Chapter 3 General Information about FBs . . . . . . . . . . . . . . . . . . .
11
3.1
Structure of FBs
3.2
. . . . . . . . . . . . . . . . . . . . . . . . . . . . . . . . . .
General Information about CLC-FBs . . . . . . . . . . . . . . . . .
FB305 PID1.16 PID controller with 16 bit fixed point arithmetics . . . . . . . . . . . . . . . . . . . . . . . . . . . . . . . . . . . . . . .
FB306 PID1.32 PID controller with 32 bit fixed point arithmetics . . . . . . . . . . . . . . . . . . . . . . . . . . . . . . . . . . . . . . .
12
13
15
21
FB310 ZR1 Two-position controller for A120
FB311 PDSR1 PD-step-action controller . . . . . . . . . . . . . .
31
. . . . . . . . . . . . . . . .
27 for A120
FB315 DR1 Three-position controller for A120
FB320 PBM1 Pulse-duration Modulator for . . . . . . . . . . . . . . .
41
. . . . . . . . . . . . . .
37
A120
Part III Application . . . . . . . . . . . . . . . . . . . . . . . . . . . . .
47
Chapter 1 Installation Application . . . . . . . . . . . . . . . . . . . . . . . . . . .
1.1
Installation of applications . . . . . . . . . . . . . . . . . . . . . . . . . .
1.1.1
Installation of application HVAC . . . . . . . . . . . . . . . . . . . . .
1.1.2
Installation of application REACT . . . . . . . . . . . . . . . . . . .
49
50
50
51
Table of Contents xv
Chapter 2 Applications . . . . . . . . . . . . . . . . . . . . . . . . . . . . . . . . . . . . .
53
2.1
Open Loop and Temperature Control of a Ventilation Sys-
2.1.1
2.1.2
tem in HVAC Techniques
Open Loop Control
. . . . . . . . . . . . . . . . . . . . . . . . . .
. . . . . . . . . . . . . . . . . . . . . . . . . . . . . . . .
Mixed air temperature control . . . . . . . . . . . . . . . . . . . . . . .
56
59
62
2.1.3
Room Temperature Control . . . . . . . . . . . . . . . . . . . . . . . . .
63
2.2
Closed Loop Control of a Reacting Tank in Process Engi-
2.2.1
neering . . . . . . . . . . . . . . . . . . . . . . . . . . . . . . . . . . . . . . . . . .
Sequence Control and Closed Loop Control . . . . . . . . . .
66
66
Part IV Appendix . . . . . . . . . . . . . . . . . . . . . . . . . . . . . .
69
Addresses . . . . . . . . . . . . . . . . . . . . . . . . . . . . . . . . . . . . . . .
71
Publications Comment Form . . . . . . . . . . . . . . . . . . . . .
81 xvi Table of Contents
20
Part I
How to Proceed?
20
1
2
20
20
Chapter 1
Checklist
The following list describes how to use this closed-loop control manual and how to handle the loop control software in the best way.
Checklist 3
Before using loop control function blocks take a look at the following checklist and note the software details in the corresponding chapters.
Get familiar with the conditions for using loop control software (part II, chapter
1).
Have you fullfilled the conditions of the first point?
Install the loop control function blocks (part II, chapter 2).
To check software operation, install one of the applications (part III, chapter1).
Start AKF program using the ‘AKF12’-command on your PADT (see also software kit ‘AKF12’).
With SeTup menu type the name of ‘PLant’ and ‘PC Station’ that you want to choose for applications (see also software kit ‘AKF12’).
Print closed-loop control program using print menu ‘program list’ (see also software kit ‘AKF12’).
Get familiar to functionality of application using the program list and the manual‘s descriptions (see also software kit ‘AKF12’).
Edit your open loop program using ‘AKF12’ (see also software kit ‘AKF12’).
Copy the neecessary loop control Function Blocks to your actual plant using the ‘Special’ and ‘Copy Files’ commands (see also software kit ‘AKF12’).
Create your closed loop program under using the function blocks (see also part II).
The specific closed-loop control parts are now complete. Finally you can prepare the AKF program for loading it to the connect PC or return to other work on the given plant (AKF12, part ‘programming’, chap. ‘Programming Sequence’).
4 Checklist
20
Part II
Closed Loop Control
Function Blocks
20
5
6
20
Chapter 1
Requirements
This chapter enables you to perform closed loop control using
AKF software package Dolog AKF
→
A120 and the loop control software CLC 12.
20
Requirements 7
To guarantee proper operation of software ensure the following conditions:
IBM compatible programming and debugging tool (personal computer) with fixed disk drive and external-disk drive (3 1/2” or 5 1/4”) and with installed software Dolog AKF → A120 software conditions:
Kind of software
A120:
ALU 200 basic software
ALU 201 basic software
ALU 202 basic software
PADT:
Dolog AKF → A120 programming software
Loop CTRL → A120 →
Closed loop control FBs
AKF type
BSW 124
BSW 123
BSW 123
AKF12
CLC12 number
275121.00
275120.00
275120.00
E-Nr. 424-247197 version 2.0 or higher
E-Nr. 424-271575 version 1.0
Knowledge about project planning of the A120 using the software kit
Dolog AKF → A120
8 Requirements
20
Chapter 2
Installation of Function
Blocks
This chapter describes you how to copy closed loop control function blocks.
20
Installation of Function Blocks 9
The loop control function blocks (CLC-FBs) are equipped with AEG defined numbers. Nevertheless these numbers can be freely changed by the customer when copying function blocks from diskette to PC Station. To keep always best survey and to make survive activities less difficult, we recommend to use the same numbers or to commit function block numbers in your company.
Use the following procedure to copy FBs:
Step 1 Start AKF12 program
Step 2 Insert CLC12-diskette in your disk drive (e.g. A:\)
Step 3 You are in the Plant, entered during installation of AKF12
(e.g. ”C:\AKF12”)
Step 4 Select ”SeTup”, ”PC Station”, ”PC Station Name” in
AKF12 menu (e.g. ”CLC”)
Step 5 Select menu ”Special”, ”Copy Files”
Step 6 To specify source files type: A:\CLC12\*.* (note A:\ is the name of disk drive in which youve inserted the CLC12 diskette, eventually this drive can be B:\ )
Step 7 When entering the return key in the ”Target” line (empty line), the files on the inserted diskette will be copied into the PC station determined with SeTup (CLC12)
Menu entries for step 6 and step 7:
(parameter: /V)
Start Copying Files
SOurce: A:\CLC12\*.*
Target:
Parameter: /V
From this PC station the required FBs can be copied to the actual PC station containing the user program (the recommendation mentioned above is automatically kept when proceeding in this way).
For this Step 4 to Step 7 have to be repeated.
To Step 4: Type the name of PC station you want to work with.
To Step 6: ”Source” is the directory of PC station ”CLC”. Instead of *.* insert the number of required FB.
To Step 7: The selected PC station remains the target directory.
10 Installation of Function Blocks
20
Chapter 3
General Information about
FBs
20
General Information about FBs 11
3.1
Structure of FBs
Every function block consists of one operation and the necessary operands for executing the operation.
The operation determinates which function will be executed by the function block. The operand determinates which variable will be used when executing the operation.
Operation e.g. ZR1
Function Block
Operand actual operand assignable operand operand identifier
Parameter e.g. ER,X e.g. MW, M e.g. 2.3, 4.5
Condition
M...
M...
MW..
MW..
MW..
MW..
FB 310
ZR1
ER
ER
WE
XE
HYS
TA
YA
TM
VIM1
VIM2
VIW1
VIW2
MW..
T...
M...
M...
MW..
MW..
Note Only one FB is allowed in each network
Conditional- / unconditional FB call
The operation of every function block can be enabled with a ‘Conditional call’
(edit menu). Doing this causes AKF program to perform an additional FB marker input. Setting the conditional input enables FB operation, resetting the input turns the FB operation off. The output operands then will not be changed until the FB is reactivated. This allows for instances where output operands are shared with
12 General Information about FBs
20
further FBs in cases of process dependant operating modes (e.g. split-range control) - or simply to stop FB operation. The conditional input is next to the name of function block (here ZR1).
Conditional input e.g. E2.1
no conditional input
→ conditional call
→ unconditional call
The operand identifier determinates if it is e.g. an output variable (Q), Input variable (I), a marker byte (MB) etc. This information is demanded by Dolog AKF from the system. It is not possible to write a marker bit to places which are assigned for marker words. Wrong inputs will not be accepted (syntax check).
Valid characters of variables in Function Block Diagrams:
Condition conditional or unconditional call (enable) of function block
M...
MB..
for input/output value or marker with bit format for input/output value or marker with byte format
MW..
MD..
for input/output value or marker with word format for input/output value or marker with double word format
The points signify the required parameters
3.2
General Information about CLC-FBs
The Closed Loop Function Blocks of MODICON A120 can be copied into an existing PC station and used like regular FBs.
Inserting a Function Block into a Network causes the AKF program to prepare the finally program linkage with assignment of fundamental part of Function
Block code and additional the code for calling the FB in OB (see also FB descriptions). With every further insertion of the same Function Block only the call of the new FB is added to the code to be linked. The required program memory can be kept to a minimum in this way.
The Loop Control Function Blocks run without additional timing system using only timer controlled sampling. Therefore every CLC-FB gets one or more timer functions assigned at TMx variable. The sampling time, unless otherwise specified (see FB descriptions), should be determinated adapt to the conditions of
20
General Information about FBs 13
process loop. Usual values are 1/5 - 1/10 of loop control relevant system time constants.
The required memory allocation for internal variables, controller input- and output variables and controller parameters are completely assigned at the Controller
Function Block. There is no exceptional handling of data in the Data Block (DB) or consideration of restricted data areas.
The number of timer addresses used can be minimized by assigning the same timers to several function blocks in cases when the sampling time is determined as zero. (e.g. ZR1-, DR1 continuous operation or PID controller in P controller mode). Also the double words that have to be assigned to some controllers can be used commonly. They are only used for buffer storage.
In displaying A120 signals using ”Online List” it should be considered that variables identified as controllable (CE) will be overwritten for one program cycle with given list value after activating the transmit using the transmit command in the AKF menu. The controller outputs have storing characteristics and therefore should only be listed as viewable (no identifier). Identifying controller output variables as force variables should be avoided if regular and continual controller operation is to be guaranteed. (The fixing of output variables causes uncontrollable influence in FB operation)
14 General Information about FBs
20
FB305 PID1.16 PID controller with
16 bit fixed point arithmetic
1 Function
The closed loop control function block PID 1.16 is a freely parametrizable PID controller with 16 bit fixed point arithmetics. PID 1.16 has the following characteristics negative KP values possible (change of control direction)
D-, and I-part can separately and bumpless turned on/turned off
D-part with bumpless change over to system deviation or actual value
D-part part combined with 1st order lag element for controlled step response
(DT1)
Operation with anti windup reset (AWR)
Manual input with setpoint correction of integral part for bumpless return to automatic mode
Operating mode HALT for keeping the last value of controller output with setpoint correction of integral part
Dynamic HALT with positive edge trigger at DHLT-input during next FB cycle
Limiting of controller output to minimum/maximum value
Complete protection against arithmetic overflows; thus higher reliability
FB operating time less than 10 ms
20
PID1.16
15
2 Display
Condition
MW..
MW..
MW..
MW..
MW..
M...
M...
M...
MW..
MW..
MW..
M...
MW..
2.1
Funktion Block Symbol
FB 305
PID1.16
TN
TV
ED
TA
W
X
YH
YAO
YAU
HAND
HALT
DHLT
KP
Y
TM
VIM1
VIM2
VIW1
VIW2
VIW3
VIW4
VIW5
VIW6
VIW7
VIW8
MW..
T...
M...
M...
MW..
MW..
MW..
MW..
MW..
MW..
MW..
MW..
16 PID1.16
20
2.2
FB structure
Assignable parameter
TM
VIM1
VIM2
VIW1
VIW2
VIW3
VIW4
VIW5
VIW6
VIW7
VIW8
TV
ED
TA
Y
HALT
DHLT
KP
TN
PID1.16
W
X
YH
YAO
YAU
HAND
MW - addr.
MW - addr.
MW - addr.
MW - addr.
MW - addr.
M - addr.
M - addr.
M - addr.
MW - addr.
MW - addr.
MW - addr.
M - addr.
MW - addr.
MW - addr.
T - addr.
M - addr.
M - addr.
MW - addr.
MW - addr.
MW - addr.
MW - addr.
MW - addr.
MW - addr.
MW - addr.
MW - addr.
Meaning
Operation (Call) setpoint value actual value manual input maximum output value minimum output value operating mode HAND (priority over HALT) operating mode HALT dynamic HALT for next FB cycle controller gain integral-action time (in 0.1 s); TN < 0: I-part is turned off derivative-action time (in 0.1 s); TV < 0: D-part is turned off change over D-part (0 for KP
*
Xd, 1 for KP sampling time (in 0.1 s) manipulated variable (controller output)
*
-X) timer internal organization data (bit) internal organization data (bit) internal organization data (word) internal organization data (word) internal organization data (word) internal organization data (word) internal organization data (word) internal organization data (word) internal organization data (word) internal organization data (word)
20
PID1.16
17
Functtion Block
Figure 1 Controller design
18 PID1.16
20
3 Configuration
The function block can be copied from the source file (PADT or Diskette) to the target file of the selected PC station (ref. chapter LEERER MERKER).
3.1
Parametrization
The parametrization of PID 1.16 controller has no restrictions - Arithmetic overflows will be kept MAXINT limits the way that direction (sign) of substituted variable is the same as the direction of the unrepresentable, overshoot one (no undefined ‘saw-teeth’ effects). Controller operation without limited output value can be reached with regards to the overall arrangement of control loop.
Note :
Step changes in setpoint value will be amplified with a gain of 5 * KP at the instant of step change and are given out additional to the actual controller output value (once amplified by controller gain and four times by DT1-part, because of internal determination TV/T1 = 4).
The following course of the controller output value is essentially determined by the additional conditions of the control loop, mostly by system time constants.
The limiting of controller output in this connection, is in the main dependant on the course of the integral part, whose settling to an fixed value can only be done over the system loop.
Step changes in setpoint value can be (preferably in PI mode) transformed into a slower settling of the control loop, with bumpless change in controller output value, when simultaneous causing a positive edge trigger at DHLT input. In that case DHLT forces the controller to take over the normally occuring step change in the controller output into the integral part (one cycle). The former controller output value temporary remains as the output value. The following course of controller output value is essentially determinated by the changing of the integral part.
20
PID1.16
19
Table 1 Determination of sampling time
Controller
P
PI
PD
PID -
min
-
0 typ
-
< 0.2
*
TN
< 0.05
*
< 0.05
*
TV
TV -
-
-
max
3.2
FB operating times
Note The given operating times are valid when using ALU 202.
Operating times during sampling cycle:
Controller
P
PI
PD
PID normal
3.08 ms
5.06 ms
3.79 ms
5.41 ms
Operating times in other cycles: always 2.32
ms
AWR**
3.20 ms
4.25 ms
3.62 ms
4.46 ms mode
HAND
2.98 ms
4.02 ms
2.99 ms
4.03 ms
HALT
3.01 ms
4.03 ms
3.02 ms
4.94 ms
3.3
Program memory first FB-call in OB: 5 010 every further call: + 159
** if I part works
Byte*
Byte
* The given value represents worst case value and is valid when the Function
Block is the only one called in the OB. If however commands used in your closed loop control functions already exist in your program, only the additional program parts will cause an increase in the total linked program length (hence saving in program memory).
20 PID1.16
20
FB306 PID1.32 PID controller with
32 bit fixed point arithmetics
1 Function
The Closed Loop Control Function Block PID 1.16 is a freely parameterizable
PID controller with 16 bit fixed point arithmetics for input and output. The calculation of I- and DT1-part and the summing of the internal values for building the controller output signal are done with 32 bit accuracy.
negative KP values possible (change of control direction)
D-, and I-part can separately and bumplessly turned on/off
D-part with bumpless change over to system deviation or actual value
D-part part combined with 1st order lag element for controlled step response
(DT1)
Operation with anti windup reset (AWR)
Manual input with setpoint correction of integral part for bumpless return to automatic mode
Operating mode HALT for keeping the last value of controller output with setpoint correction of integral part
Dynamic HALT with positive edge trigger at DHLT-input during next FB cycle
Limiting of controller output to minimum/maximum value
Complete protection against arithmetic overflows; thus higher reliability
FB operating time less than 10 ms
20
PID1.32
21
2 Display
M...
MW..
MW..
MW..
M...
MW..
condition
MW..
MW..
MW..
MW..
MW..
M...
M...
FB 306
TN
TV
ED
TA
YAU
HAND
HALT
DHLT
KP
W
X
YH
YAO
PID1.32
Y
TM
VIM1
VIM2
VIW1
VIW2
VIW3
VIW4
VIW5
VIW6
VIW7
VIW8
VIW9
VID1
VID2
MW..
T...
M...
M...
MW..
MW..
MW..
MW..
MW..
MW..
MW..
MW..
MW..
MD..
MD..
22 PID1.32
20
2.1
FB structure
Assignable parameter
TM
VIM1
VIM2
VIW1
VIW2
VIW3
VIW4
VIW5
VIW6
VIW7
VIW8
VIW9
VID1
VID2
TV
ED
TA
Y
HALT
DHLT
KP
TN
PID1.32
W
X
YH
YAO
YAU
HAND
MW - addr.
MW - addr.
MW - addr.
MW - addr.
MW - addr.
M - addr.
M - addr.
M - addr.
MW - addr.
MW - addr.
MW - addr.
M - addr.
MW - addr.
MW - addr.
T - addr.
M - addr.
M - addr.
MW - addr.
MW - addr.
MW - addr.
MW - addr.
MW - addr.
MW - addr.
MW - addr.
MW - addr.
MW - addr.
MD - addr.
MD - addr.
Meaning
Operation (Call) setpoint value actual value manual input maximum output value minimum output value operating mode HAND (priority over HALT) operating mode HALT dynamic HALT for next FB cycle controller gain integral-action time (in 0.1 s); TN < 0: I-part is turned off derivative-action time (in 0.1 s); TV < 0: D-part is turned off change over D-part (0 for KP
*
Xd, 1 for KP sampling time (in 0.1 s) manipulated variable (controller output)
*
-X) timer internal organization data (bit) internal organization data (bit) internal organization data (word) internal organization data (word) internal organization data (word) internal organization data (word) internal organization data (word) internal organization data (word) internal organization data (word) internal organization data (word) internal organization data (word) internal organization data (double word) internal organization data (double word)
20
PID1.32
23
Figure 2 Controller design
24 PID1.32
20
3 Configuration
The function block can be copied from source file (PADT or Diskette) to the target file of the selected PC station (ref. chapter LEERER MERKER).
3.1
Parameterization
The parametrization of PID 1.16 controller has no restrictions - Arithmetic overflows will be kept within MAXINT limits the way that direction (sign) of substituted variable is the same as the direction of the unrepresentable, overshooten one
(no undefined ‘saw-teeth’ effects). Controller operation without limited output value can be reached with regards to the overall arrangement of control loop.
Note :
Step changes in setpoint value will be amplified with a gain of 5 * KP at the instant of step change and are given out additional to the actual controller output value (once amplified by controller gain and four times by DT1-part, because of internal determination TV/T1 = 4).
The following course of the controller output value is essentially determined by the additional conditions of the control loop, mostly by system time constants.
The limiting of controller output in this connection, is in the main dependant on the course of the integral part whose settling to an fixed value can only be done over the system loop.
Step changes in setpoint value can be (preferably in PI mode) transformed into a slower settling of the control loop, with bumpless change in controller output value, when simultaneousley causing a positive edge trigger at DHLT input. In that case DHLT forces the controller to take over the normally occuring step change in the controller output into the integral part (one cycle). The former controller output value temporary remains as the output value. The following course of controller output value is essentially determinated by the changing of the integral part.
20
PID1.32
25
Table 2 Determination of sampling time
Controller
P
PI
PD
PID -
min
-
0 typ
-
< 0.2
*
TN
< 0.05
*
< 0.05
*
TV
TV -
-
-
max
3.2
FB operating times
Note The given operating times are valid when using ALU 202.
Operating times during sampling cycle:
Controller
P
PI
PD
PID normal
3.43 ms
8.74 ms
3.79 ms
9.1
ms
Operating times in other cycles: always 2.56
ms
AWR
3.64 ms
6.42 ms
4.0
ms
6.78 ms mode
HAND
3.27 ms
6.29 ms
3.27 ms
6.29 ms
HALT
3.27 ms
8.7 ms
3.27 ms
8.73 ms
3.3
Program memory first FB-call in OB: 6 150 every further call: + 177
Byte*
Byte
* The given value represents worst case value and is valid when the function block is the only one called in OB. If however commands used in your closed loop control functions already exist in your program, only the additional program parts will cause an increase in the total linked program length (hence saving in program memory).
26 PID1.32
20
FB310 ZR1 Two-position controller for A120
1 Function
The Function Block ZR1 transforms an internally formed system deviation into a binary state for the output marker YA. If the absolute value of the system deviation (WE-XE) overranges by a half of the hysteresys value (HYS) the output will be set dependant (sign) on the deviation value.
Assigning hysteresis and sampling time
Continuous operation setting TA = 0
2 Display
2.1
Function block symbol
Condition
M...
M...
MW..
MW..
MW..
MW..
FB 310
ZR1
ER
EF
WE
XE
HYS
TA
YA
TM
VIM1
VIW1
VIW2
M...
T...
M...
MW..
MW..
20
ZR1 27
2.2
FB structure
Assignable parameter
ZR1
ER
EF
WE
XE
HYS
TA
YA
TM
VIM1
VIW1
VIW2
B - addr.
B - addr.
MW - addr.
MW - addr.
MW - addr.
MW - addr.
M - addr.
T - addr.
M - addr.
MW - addr.
MW - addr.
Meaning
Operation (Call) function block reset; ER = 1: reset of YA enable: EF = 0: freezes YA setpoint value actual value hysteresis sampling time (in 0.1 s); TA = 0 for continuous operation manipulated variable (controller output signal) timer internal organization data (bit) internal organization data (word) internal organization data (word)
HYS TM
TA
WE
Sampling Time
Xd
-t
XE
YA
HYS
1
Xd
YA
EF ER
Figure 3 controller design
28 ZR1
20
3 Configuration
The Function Block can be copied from source file (PADT or diskette) to the target file of selected PC station (ref. chapter LEERER MERKER).
3.1
Parameterization
The parameterization of ZR1 ensues with the assignment of the hysteresis and sampling times.
The hysteresis defines the operating points of the controller. Outside the hysteresis the system deviation causes ZR1 to switch the output depending on the sign of the deviation. Inside the hysteresis area ZR1 operates like a dead zone with stored output.
To select the sampling time is an option that can be done to synchronize ZR1 with other controllers. If synchronizing is not necessary the Function Blocks can be enabled to work in every program cycle by setting sampling time TA=0.
3.2
Reset of Function Block
ER = 1 reset of output marker YA.
EF = 0 no change in output marker condition even when the system deviation or controller parameters are changing.
3.3
FB operating times
Note The given operating times are valid when using ALU 202.
Operating conditions :
ER = 1
EF = 0
0.52 ms
0.47 ms
ER = 0, EF = 1 1.5 ms
20
ZR1 29
3.4
Program memory first FB-call in OB: 1 596 every further call: + 75
Byte*
Byte
* The given value represents worst case value and is valid when the function block is the only one called in OB. If however commands used in your closed loop control functions already exist in your program, only the additional program parts will cause an increase in the total linked program length (hence saving in program memory).
30 ZR1
20
FB311 PDSR1 PD-step-action controller for A120
1 Function
The Function Block PDSR1 consists of a three-position controller hysteresis and a 1st order lag feedback loop. The internal coupling of 1st order lag element from controller output to the input summing point approaches controller characteristics of those in continuously sampling PD controllers (supposing relatively high system- and actuator time constants for efficient filtering of switched output signal). When connected with an integral actuator (e.g. control valve) the actuator/controller combination has PI characteristics. The parameterization is simplified by the direct assignment of the actuator-action time (nominal value of the valve) and the required parameters KP and TN. The determination of feedbackand hysteresis value is done by the controller itself.
Parameterization of controller gain, integral action time, actuator action time and scaling value
Internal determination of feedback- and hysteresis values
Accommodation of the controller operation to the process conditions by the use of the scaling value KSN
20
PDSR1 31
2 Display
2.1
Function block symbol
Condition
M...
M...
MW..
MW..
MW..
MW..
MW..
MW..
FB 311
ER
EF
WE
XE
KP
TN
TS
KSN
PDSR1
YP
YN
TM1
VIM1
VIW1
VIW2
VIW3
VIW4
VID1
VID2
MW..
MW..
T...
M...
MW..
MW..
MW..
MW..
MD..
MD..
2.2
FB structure
Assignable parameter
TM1
VIM1
VIW1
VIW2
VIW3
VIW4
VID1
VID2
XE
KP
TN
TS
PDSR1
ER
EF
WE
KSN
YP
YN
B - addr
B - addr
MW - addr
MW - addr
MW - addr
MW - addr
MW - addr
MW - addr
M - addr
M - addr
T - addr
M - addr
MW - addr
MW - addr
MW - addr
MW - addr
MD - addr
MD - addr
Meaning
Operation (Call) function block reset; ER = 1: reset of YA enable: EF = 0: freezes YP, YN setpoint value actual value controller gain integral-action time (in s) nominal actuating time of integral actuator (in s) scaled process gain controller output for positive directed actuating controller output for negative directed actuating timer internal organization data (bit) internal organization data (word) internal organization data (word) internal organization data (word) internal organization data (word) internal organization data (double word) internal organization data (double word)
32 PDSR1
20
WE
XE
KSN
2.3
FB structure
ER
EF
TM1
Function Block
Control
--
KR HYS UZ
KR
TA = 100 ms
YP
--
YN
Xd
UZ HYS
Conversion
TN
K = 1
KSN
Y
KP TN TS
Figure 4 Controller design
YP
YN
20
PDSR1 33
3 Configuration
The Function Block can be copied from the source file (PADT or diskette) to the target file of the selected PC station (ref. chapter LEERER MERKER).
3.1
Parameterization
The parameterization of PDSR1 is carried out by the assignment of the controller gain, integral-action time, the nominal actuating time of integral actuator and the scaled process gain.
The gain of the 1st order lag feedback element is a function of scaled process gain KSN. Therefore KSN has to be determinated in relation to input scaling of controller setpoint- and actual value. For instance - a theoretical temperature range of +/-400 o C that refers to +/- 4000 integer value (e.g. scaling an input voltage signal of ADU204 ) results an input scaling of 10/ o C. If the maximum difference in process temperature (actual value between the states - shut down valve and widely opened valve- ) results to KS = 200 o C the scaled process gain is given to KSN = 2000.
The scaling accommodates the switching of the controller outputs to the appropriate switching of an integer value for feedback circuitry. In this way the transposition of the given parameters will be guaranteed and the handling of control loop can be done close to that of continuously operating loops.
To keep the developing controller attributes close to the determinated parameters the following values have to be selected:
Parameter
KP
TN
TS min
1
120
30 type
-
> 4
*
TS
< TN/4 max
-
(s)
(s)
The hysteresis determines the controller sensitivity and is internally calculated the way:
HYS = KSN / (KP
*
TS)
34 PDSR1
20
When the scaling setpoint- and actual value to a function of twice the process gain (exampled above) the resolution error reaches at the most 1.66 %. If the user determination of integer range (not the scaling, hence KSN = constant) this is defined otherwise, the resolution changes while the absolute error remains the same.
3.2
Reset of Function Block
ER = 1 reset of output markers YP and YN.
EF = 0 no change in condition of output markers even when the system deviation or controller parameters are changing.
3.3
FB operating times
Note The given operating times are valid when using ALU 202.
Operating conditions:
ER = 1
EF = 0
0.76 ms
0.67 ms
ER = 0, EF = 1 7.0
ms
3.4
Program memory first FB-call in OB: 3 903 every further call: + 117
Byte*
Byte
* The given value represents worst case value and is valid when the function block is the only one called in OB. If however commands used in your closed loop control functions already exist in your program, only the additional program parts will cause an increase in the total linked program length (hence saving in program memory).
20
PDSR1 35
FB315 DR1 Three-position controller for A120
1 Function
The Function Block DR1 transforms an internally formed system deviation into binary states for output markers YP and YN. If the absolute value of the system deviation (WE-XE) overranges by half of the hysteresys value (HYS) which is shifted by dead band (UZ), the output will be set dependant (sign) on the deviation value (if positive - YP, if negative - YN). If system deviation falls below the value marked by the inner edge of appropriate hysteresis loop the marker will be reset. Overlapping of hysteresis loops can be done up to HYS = 2
*
UZ
Assigning hysteresis, dead band and sampling time
Operation up to HYS = 2
*
UZ possible
Continuous operation setting TA = 0
2 Display
2.1
Function block symbol
Condition
M...
M...
MW..
MW..
MW..
MW..
MW..
ER
EF
WE
XE
HYS
UZ
TA
FB 315
DR1
YP
YN
TM
VIM1
VIW1
VIW2
M...
M...
T...
M...
MW..
MW..
20
DR1 37
2.2
FB structure
Assignable parameter
DR1
ER
EF
WE
XE
HYS
UZ
TA
YA
TM
VIM1
VIW1
VIW2
B - addr.
B - addr.
MW - addr.
MW - addr.
MW - addr.
MW - addr.
MW - addr.
M - addr.
T - addr.
M - addr.
MW - addr.
MW - addr.
Meaning
Operation (Call) function block reset; ER = 1: reset of YA enable: EF = 0: freezes YA setpoint value actual value hysteresis dead band sampling time (in 0.1 s); TA = 0 for continuous operation manipulated variable (controller output signal) timer internal organization data (bit) internal organization data (word) internal organization data (word)
TM
TA
WE
Cycle time
--
Xd t
XE
UZ HYS
YP
YA
YN
UZ
HYS
Xd pos.
neg.
YP
YN
ER
Figure 5 controller design
EF
38 DR1
20
3 Configuration
The Function Block can be copied from the source file (PADT or diskette) to the target file of the selected PC station (ref. chapter LEERER MERKER).
3.1
Parameterization
The parameterization of Function Block ensues with assignement of hysteresis, dead band and sampling time. The hysteresis defines the operating points of the controller. Outside the hysteresis the system deviation causes DR1 to switch the appropriate output depending on the sign of the deviation. Inside the hysteresis area DR1 keeps the current output states as long as deviation does not overrange (underrange) the corresponding operating point (if high state - falling edge of hysteresis, if low state - rising edge of hysteresis). The separation of the deviation area for the use of two controller outputs allows the design of loop controls with separate control actions (split-range control, e.g. heating and cooling). The select sampling time TA is optional and can be used to synchronize DR1 with other controllers. If synchronization is not necessary the Function Blocks can be enabled to work in every program cycle by setting sampling time TA=0.
3.2
Reset of Function Block
ER = 1 reset of output markers YP and YN.
EF = 0 no change in condition of output markers even when the system deviation or controller parameters are changing.
3.3
FB operating times
Note The given operating times are valid when using ALU 202.
Operating conditions :
ER = 1
EF = 0
0.6 ms
0.53 ms
ER = 0, EF = 1 1.2 ms
20
DR1 39
3.4
Program memory first FB-call in OB: 1 623 every further call: + 87
Byte*
Byte
* The given value represents worst case value and is valid when the function block is the only one called in OB. If however commands used in your closed loop control functions already exist in your program, only the additional program parts will cause an increase in the total linked program length (hence saving in program memory).
40 DR1
20
FB320 PBM1 Pulse-duration Modulator for
A120
1 Function
Function Block PBM1 transforms an input signal, related to the given limiting value (OBGR), into a periodical pulse string with proportionally modulated pulsewidth. The Function Block can be used as a P-controller (input WE, XE) and even as a transformer for continual signals (input WE with XE = 0) e.g. PID controller output connected to PBM1 for operating a two-point actuator of controllable system.
Assign of sampling time, absolute input value causing permanent output signal and minimum/maximum pulse-width
Transformation of negative values (YN)
2 Display
2.1
Function block symbol
Condition
M...
M...
MW..
MW..
MW..
MW..
MW..
MW..
FB 320
ER
EF
WE
XE
OBGR
TTK
TMAX
TMIN
PBM1
YP
YN
TM1
TM2
VIM1
VIM2
VIM3
VIM4
VIW1
VIW2
VID1
VID2
M...
M...
T...
T...
M...
M...
M...
M...
MW..
MW..
MD..
MD..
20
PBM1 41
2.2
FB structure
Assignable parameter
PBM1
ER
EF
WE
XE
OBGR
TTK
TMAX
TMIN
YP
YN
TM1
TM2
VIM1
VIM2
VIM3
VIM4
VIW1
VIW2
VID1
VID2
B - addr.
B - addr.
MW - addr.
MW - addr.
MW - addr.
MW - addr.
MW - addr.
MW - addr.
M - addr.
M - addr.
T - addr.
T - addr.
M - addr.
M - addr.
M - addr.
M - addr.
MW - addr.
MW - addr.
MD - addr.
MD - addr.
Meaning
Operation (Call) function block reset; ER = 1: reset of YA enable: EF = 0: freezes YA setpoint value actual value limiting value (absolute) sampling time (in s) maximum pulse time (in s) minimum pulse time (in s) output signal for positive directed actuation output signal for negative directed actuation
1st timer
2nd timer internal organization data (bit) internal organization data (bit) internal organization data (bit) internal organization data (bit) internal organization data (word) internal organization data (word) internal organization data (double word) internal organization data (double word)
3 Configuration
The Function Block can be copied from the source file (PADT or diskette) to the target file of selected PC station (ref. chapter LEERER MERKER).
42 PBM1
20
3.1
Parameterization
The parameterization of PBM1 ensues with assignment of the limiting value, the sampling time and minimum/maximum pulse-width.
TTK determines the sampling time in which the actuating pulses are periodically given out to the controller outputs YP or YN. The actual pulse-width and thereby the averaged proportionality ym of the actuating pulses are dependant on the relation of the input value (system deviation or setpoint) to the limiting value
(OBGR).
Tp =
WE -- XE
OBGR
* TTK ym =
WE -- XE
OBGR
* 100%
If the pulse-width underranges the given value TMIN the controller outputs are turned to low.
If pulse-width overranges the given value TMAX, the pulse-width will be limited to TMAX. Both measures ensure correct opeation between the modulator and the characteristics of a given actuator.
When assigning TMIN = 0 and TMAX = TTK the pulse-width is not restricted this way.
Note To keep the developing controller attributes as close to the determinated parameters the following values should be selected:
Parameter
OBGR
TTK
TMAX
TMIN min
-
0
-
10
20 type max
-
--
< TTK
< TMAX -
-
--
3200 (s)
PBM1 43
3.2
Reset of Function Block
ER = 1 reset of output markers YP and YN.
EF = 0 no change in condition of output markers even when the system deviation or controller parameters are changing.
3.3
FB operating times
Note The given operating times are valid when using ALU 202.
Operating conditions :
ER = 1
EF = 0
0.83 ms
0.73 ms
ER = 0, EF = 1 > 1.5 ms (3.45 ms maximum)
3.4
Program memory first FB-call in OB: 3 309 every further call: + 129
Byte*
Byte
* The given value represents worst case value and is valid when the function block is the only one called in OB. If however commands used in your closed loop control functions already exist in your program, only the additional program parts will cause an increase in the total linked program length (hence saving in program memory).
44 PBM1
20
smallest impulse time
Ti
TTK free controller range transient impulse length
Tp
Output signal = 0 when Tp < TMIN
Output signal when
Tp > TMAX
TMAX
Figure 6 Clock grid and pulse-shaping t t
EF = 1
EF = 1 t possible clockgrid t
Output
20
PBM1 45
Tp at VP
-- Xd
TTK
OBGR
T MIN
T MAX
TTK
--Tp at YN
Figure 7 Transfer characteristics
T MIN
T MAX
OBGR
Xd
46 PBM1
20
Part III
Application
20
47
48
20
Chapter 1
Installation Application
This chapter tells you how to copy the applications of the AKF12
Closed Loop Control.
20
Installation Application 49
1.1
Installation of applications
The enclosed diskette contains two applications as example of close loop control using AKF12.
1.1.1
Installation of application HVAC
Application of heating ventilation and air conditioning : ”HVAC”
Use the following procedure with the application:
Step1 Start AKF12 program
Step2 Insert CLC12-diskette in your disk drive (e.g. A:\)
Step3 You are in the Plant, entered during installation of AKF12
(e.g. ”C:\AKF12”)
Step4 Enter in the the AKF12 menu the station ”HVAC” under
”SeTup”, ”PC Station”, ”PC Station Name”
Step5 Select menu ”Special”, ”Copy Files”
Step6 To specify source files type: A:\CLC12\*.* (note A:\ is the name of disk drive in which youve inserted the CLC12 diskette, eventually this drive can be B:\ )
Step7 When entering the return key in the ”Target” line (empty line), the files on the inserted diskette will be copied into the PC station determined with SeTup (CLC12)
Menu entries for step 6 and step 7:
(parameter: /V)
Start Copying Files
SOurce: A:\CLC12\*.*
Target:
Parameter: /V
Now you can take a look at the PC station ”HVAC”.
50 Installation Application
20
1.1.2
Installation of application REACT
Application of a reacting tank in process engineering: ”REACT”
Use the following procedure with the application:
Step1 Start AKF12 program
Step2 Insert CLC12-diskette in your disk drive (e.g. A:\)
Step3 You are in the Plant, entered during installation of AKF12
(e.g. ”C:\AKF12”)
Step4 Enter in the the AKF12 menu the station ”REACT” under
”SeTup”, ”PC Station”, ”PC Station Name”
Step5 Select menu ”Special”, ”Copy Files”
Step6 To specify source files type: A:\CLC12\*.* (note A:\ is the name of disk drive in which youve inserted the CLC12 diskette, eventually this drive can be B:\ )
Step7 When entering the return key in the ”Target” line (empty line), the files on the inserted diskette will be copied into the PC station determined with SeTup (CLC12)
Menu entries for step 6 and step 7:
(parameter: /V)
Start Copying Files
SOurce: A:\CLC12\*.*
Target:
Parameter: /V
Now you can take a look at the PC station ”REACT”. For a better understanding of the operation, in addition with the line comments available in IL mode, please notice the network comments of NW1 in OB and the comments in NW2 of the additional FBs.
20
Installation Application 51
52 Installation Application
20
Chapter 2
Applications
20
Applications 53
Instrumentation and control technology - Heating, Ventilation and Air Conditioning technology (HVAC)
The application originates from the production automation of chemical plants
(batch process) including the additional building services automation. Open loopand Closed Loop Control is respectively realized using Modicon A120 (ALU 202) central unit with I/O modules placed on basic rack and expansion subrack
(ANSI). The networking to Modicon A350 central controller ensues with Modnet 1/SFB (1N procedure). In addition with visual display processor VIP101 and a directly connected operator panel the arrangement represents an example for central instrumentation and control technology (I&C) used for HVAC. The ”reacting-tank in process engineering” is achieved with the training board Modicon
ET722. The board simulates level and temperature of a reacting tank by combined digital and analogue simulations.
The following application contains only the CLC-part ”HVAC” of the original PC station, because this part may be similar to some other applications in process engineering. The open loop part is too dependant on the handling characteristics of non CLC process appliances (like fans or flaps) or activities (like operating and monitoring of process). The open loop function therefore is only briefly described.
54 Applications
20
DEP
DEP
DEP
DEP
DAP
216
216
216
216
216
01
05
01
216 DAP
KOS2
DNP2
ALU2
204 ADU
02
05
216
216
DNP2
ALU2
DAP
DEP
106 DEA
VIP101
BIK151
Figure 8 Application ”I&C techniques, HVAC techniques”
20
Applications 55
2.1
Open Loop and Temperature Control of a
Ventilation System in HVAC Techniques
The process scheme is represented in Figure 9 and Figure 10. The CLC part described in chapter LEERER MERKER is located in PC station HVAC on the enclosed diskette (please read network comments and hints in NW1 of OB1).
For better understanding of the technology the essential open loop functions for operating the process will be described in the following.
56 Applications
20
Figure 9 HVAC air conditioning
20
Applications 57
Figure 10 HVAC air distribution
58 Applications
20
2.1.1
Open Loop Control
In the automatic mode the system is turned on with ‘I&C-remote’ key, located on the operating and monitoring module MAB64. The following operating modes can be additionally activated from there and from VIP101
I&C Day/On
Supply air fan M1
Exhaust air fan M2
Exhaust air fan M4
Exhaust air fan M11
2nd speed
2nd speed
1st speed
1st speed
Night/Off low fan speed
Supply air fan M1 1st speed
Exhaust air fan M2
Exhaust air fan M4
Exhaust air fan M11
1st speed
OFF
OFF
Remote Control
If EXair fans M4 and M11 are in turned on state (2nd speed) the SUair fan M1 runs with 3rd speed. If EXair fans M4 or M11 and 2 from 4 laboratory tables are activated also the SUair fan M1 is running with 3rd speed. If 3 from 4 laboratory tables are in active state the SUair fan (M1) also runs with 3rd speed. With the
FBs assigned for testing area I and II the corresponding EXair fans M4 and M11 will be changed to 2nd speed.
20
Applications 59
Exhaust Air Fans
The EXair fans (M6/M9) for the solvent boxes (LSM) are continuously operating.
The EXair fan for the adjoining rooms (M12) is turned on by the light switch and turned off with time delay after turning off the light.
The EXair fan for WC and showers is activated by the light switch (with time delay) when using WC or by humidity sensor (hygrostat) when using the shower cabins. When using only one room the fan runs with 1st speed. When using both rooms the EXair fan runs with 2nd speed.
Circulating Pump of Supply Air Heater
The circulating pump M3 is activated when the heater valve is opened and turned off when the heater valve is shut.
Frost Protection
If the outside temperature sinks below the protection value of 5 o C the fans (M1,
M2, M4 and M11) are turned off. In this turned-off mode of the ventilation system the circulating pump is activated without respect to the key positions. The heater valve is opened and the cooler valve is shut.
Filter Maintenance Signal
The differential pressure switches S1 and S4 signalize polluted filters which have to be exchanged if the increasing differential pressure overranges given limits.
V-belt Control
The differential pressure switches S2, S3, S5 and S6 are controlling the differential pressure of the respecting fans. When a V-belt is broken the differential pressure vanishes, the respecting fan is turned off and the ventilation system signalizes a failure in process.
Fire Protecting Flap (FPF)
The Fire protecting flaps are shut by fusible links in the case of fire or fire hazard. The appropriate process units (SUair fans, EXair fans) are turned off.
60 Applications
20
Smoke Ventilation
The appliances for exhausting smoke are installed according to the regulations of the fire department. In this ventilation system the activating of ‘smoke ventilation’ mode sets SUair fan to run with 3rd speed and the EXair fans M2, M4 and
M11 to run with 2nd speed. With manual control ‘Man/On’ at the switchgear cubicle the EXair fans can be turned on if required. The fire protecting flaps have to be opened before activating the smoke ventilation.
Signalling
The operating state of every system unit is displayed by the control module LED:
Ready steady light
Failure - blinking light
If one single system unit has failed the system is turned off automatically (by PC program). The display lamps then turn off and the lamp corresponding to the failured unit starts blinking. After repair the ventilation system has to be turned into
‘automatic’ mode (acknowledge). All failure signals are collected in a special failure module. In this module the unit failures are signalling by blinking LEDs. The failure can be acknowledged with ”Ackn. failure” key. After proceeding in this way the blinking LEDs are turning to a steady light. This light is finally extinquished when the failed unit is repaired or exchanged by a new one.
Manual Control
Every drive (fan, circulating pump) can be activated separately in its different speeds by the corresponding keys of control module.
20
Applications 61
2.1.2
Mixed air temperature control
Application: Ventilation- and air conditioning systems in which...
for save of heating energy the mixed air temperature is kept constant a minimum supply of outside air is to guarantee for save of cooling energy the supply of outside air is to minimize to a given limit.
with change between summer- and winter mode the system has to be controlled by outside- and exhaust air temperature.
Function
The sensors B1, B2 and B3 measure the temperature of the outside air, mixed air and exhaust air. The P-controller (N1) compares the determinated setpoint value with the actual value of mixed air.
In cases of deviation, the actuating signal of P-controller output (N1) changes the flap positions in a way that system deviation can be compensated. The CLC-
FB prevents the underrange of the determinated limiting value, for ensuring a minimum supply of outside air.
Closed Loop Control
Simultaneously with increasing outside air temperature the corresponding outside air flap opens. If the outside air temperature reaches the mixed air temperature setpoint, the outside air flap is opened wide and the mixed air flap is shut.
If the EXair temperature rises above the determined limit, the outside air flap is driven to minimum supply of outside air and the mixed air flap is opened.
In this case for the purpose of energy saving, it is more suitable to use mixed air enthalpy instead of mixed air temperature for control (not realized here).
With this pre-connected mixed air temperature control the influence on the process by disturbing changes in outside air temperature can be efficently compensated. That means the difference between the outside air temperature in summer
62 Applications
20
and the outside air temperature in winter is reduced to the smaller one between the mixed air temperatures. The following SUair system loop thereby is less burdened.
2.1.3
Room Temperature Control
Application
For systems with constant room temperature in winter time and a steadily increasing of room temperature in summer time (as a function of outside air temperature) e.g. bureaus, hotels, administration buildings, schools, theaters, laboratories etc.
Function
Sensor B1 measures the outside air temperature, sensor B3 measures SUair temperature and sensor B4 measures room temperature. The PPI-cascade control unit (N 2) includes the secondary control loop with PI-controller for SUair temperature control, this compensates for most of the disturbances to the system loop. The primary control loop with P-controller for room temperature control determines the setpoint value for the secondary control loop. With an increasing room temperature the setpoint for the SUair control decreases vice versa.
The cascade control unit N 2 compares the given setpoint value with the appropriate actual value. In cases of deviation the controller output (N 2) changes to compensation. The output signal of cascade control unit (N 2) operates sequentially with the actuators of the air heater and air cooler. For the purpose of energy saving and because of physiological reasons the room temperature should be increased relative to the rise of the outside air temperature (DIN 1946, part 2 ref. Figure 11). To accomplish this demand the outside air temperature is applied to control unit N 2. To prevent the possibility of unhealthy draughts the system operation is determined in such a way that the SUair setpoint values are only valid within given limits. The limiting values therefore are set in the control unit.
20
Applications 63
Closed Loop Control Function
With the rise of room temperature the heater valve drives to direction ”Shut” and sequentially the cooler valve drives to direction ”Open”. If room temperature is too low, the cooler valve drives to direction ”Shut” and sequentially the heater valve to direction ”Open”.
oC
26
24
22
22 24 26
Outside air temp.
28
υ a
30 oC 32
Figure 11 Setpoint value for room temperature vs. outside air temperature
The results of loop control operation are shown in Figure 12 and Figure 13.
Figure 12 shows the reaction of the process where there is a step function change in outside air temperature. This disturbance change has no significance in practice but is done here to evaluate the control quality. Figure 13 shows the settling of the control loop after a system failure. In this test the system air loop itself was opened (EXair temperature = constant). The process settling after reactivation of circulating pump is similar to the settling caused by step change in outside air temperature. The disturbance, however is compensated more quickly because of the cancelled system meshing.
64 Applications
20
TIME:
240.0 s
PER
PARTING
LINE
T_SUPPLY_AIR
→
20 min/partition
T_ROOM
SUP_POS
SUP_NEG
T_SUPPLY_AIR 27.2095
T_ROOM 24.6506
Figure 12 Loop control reaction after abrupt change in outside air temperature
TIME:
240.0 s
PER
PARTING
LINE
T_SUPPLY_AIR
T_ROOM
SUP_POS
SUP_NEG
T_SUPPLY_AIR 20.3987
T_ROOM 22.3079
Figure 13 Settling of control loop after system failure (temporary failure of circulating pump)
20
Applications 65
2.2
Closed Loop Control of a Reacting Tank in Process Engineering
The process scheme is represented in Figure 14. The software described in chapter LEERER MERKER is located in PC station REACT on the enclosed diskette (please note network comments and hints in NW1 of OB1).
2.2.1
Sequence Control and Closed Loop Control
By controlled enabling of every function block, the AKF program realizes batch processing with fixed clock grid (ref. NW comment NW3, FB999 resp. NW2,
FB1). The time sequences are: filling of tank to give setpoint value heating to given setpoint value cooling to fixed setpoint value clearing of tank
On the enabling the level controller the reacting tank starts filling to the given setpoint value. (The actual value is read as analogue value from the input module.) The assigned two-position controllers operate as limit monitors. Disturbances caused by opening of 2nd inlet valve leads to an earlier attainment of the setpoint and to an earlier turn-off of the controller operated valve V2. Overfilling is not compensated for additional emptying of the tank, because the tank contents should not be taken out before the heating and cooling periods are complete. If the setpoint level can not be reached in the given sequence time, the following batch is carried out with a small quantity of product tank level.
After locking the level controller, the three-position temperature controller is activated with its first temperature setpoint value. (The actual value is read as an analog value from input module.) The temperature control is performed as a split-range control for both of the setpoint values. The control inlet valve AV2 of the heating system (here operated binary) is opened together with drain valve
V5 for heating. For cooling the tank the valves V3 and V4 are opened. Hysteresis and dead band of controller are selecting way that there is no need for cool-
66 Applications
20
ing pulses during the heating period and no need for heating pulses during the cooling period. If setpoint temperature can not be reached in a given sequence time, the following batch is carried out with a reduced temperature of the tank contents.
By changing over to the second, internally determined temperature setpoint (in
FB1), the cooling period begins. If the setpoint temperature cannot be reached in the given sequence time, the chemical product is discharged with its temperature reached up to that time.
The time for discharging the tank is calculated in such a way that the complete clearing is guaranteed.
20
Applications 67
PA
H
V1
M
M
3~
V2
T
PB
AV
2
H C
V3
AV1
V4
PC
Figure 14 Reacting tank in process engineering
V5
68 Applications
20
Part IV
Appendix
20
69
70
20
Addresses
24
Addresses 71
Regional Sales Modicon - Addresses of Technical Sales Offices
Regional Sales Offices Addresses
Hamburg Stadthausbrücke 9
2000 Hamburg 36
Kiel
Bremen
Bremerhaven
Berlin
Hannover
Bielefeld
Braunschweig
Dortmund
Münster
Nordhorn
Osnabrück
Siegen
Seekoppelweg 7
2300 Kiel 1
Stresemannstraße 29
2800 Bremen 11
Löningstr. 6
2850 Bremerhaven
Hohenzollerndamm
1000 Berlin 33
Max-Müller-Straße 50-56
3000 Hannover 1
Schillersstraße 44
4800 Bielefeld
Campestraße 7
3300 Braunschweig
Rheinlanddamm
4600 Dortmund 1
Friedrich-Ebert-Straße 7
4400 Münster
Ootmarsumer Weg 8
4460 Nordhorn
Pferdestraße 23
4500 Osnabrück
Sandstraße 173
5900 Siegen 1
Representat.
Blunck
Schultze
Rehfeldt
Freese
Döring
Modersitzki
Schmidt, G.
Nummensen
Meinecke
Rauen
Veltrup
Herforth
Siepker
Rautland
Pötter
Herforth
Helmer
Mertens
Herforth
Langbein
Gerstmann
Mieske
Marquart
Mücke
Döhrmann
Geiss
Lange
Sperling
Döhrmann
Mücke
Mieske
Marquart
Biermann
Engels
Hansen
Herforth
Benighaus
Jerke
Kottenstede
Herforth
Phone No.
(0 40) 34 98-0
(04 31) 6896-0
(04 21) 44 94-0
(04 71) 49 32-0
(030) 8 28-0
(05 11) 63 04-0
(05 11) 63 04-0
(05 11) 63 04-0
(02 31) 12 00-0
(02 51) 53 06-0
(02 31) 12 00-0
(0 59 21) 50 45
(02 31) 12 00-0
(05 41) 5 84 92-0
(02 31) 12 00-0
(02 71) 47 55
(02 31) 12 00-0
-
370
332
272
344
420
288
491
108
116
115
491
-
470
470
227
2947
2942
-
-
-
-
-
470
227
-
-
491
23
28
26
491
-
-
491
Ext.
280
244
233
233
291
72 Addresses
24
Regional Sales Offices Addresses
Essen Kruppstraße 6
4300 Essen 1
Düsseldorf
Köln
Wiesenstraße 21
4000 Düsseldorf 11
Oskar-Jäger-Straße 125-143
5000 Köln 30
Aachen
Koblenz
Frankfurt
Gießen
Kassel
Grüner Weg 22/24
5100 Aachen 1
Rheinstraße 17
5400 Koblenz 1
Mainzer Landstraße 351-367
6000 Frankfurt 1
Schanzenstraße 1 - 5
6300 Gießen 1
Lilienthalstraße 150
3500 Kassel
Mainz
Mannheim
Karlsruhe
Saarbrücken
Stuttgart
Freiburg
Fischtorplatz 14
6500 Mainz 1
N7, 5 - 6 Kunststraße
6800 Mannheim 1
Neureuter Straße 5/7
7500 Karlsruhe 21
Mainzer Straße 176
6600 Saarbrücken 3
Dornierstraße 7
7030 Böblingen-Hulb
Tullstraße 84
7800 Freiburg 1
Roos
Tödtemann
Trosch
Hadamik
Emmerich
Dünkel
Keilmann
Cramer
Wittemeier
Specht
Müller-Veit
Hensel
Schulz
Lanzet
Jüngling
Reinhard
Braun
Eisele
Göhringer
Heim
Diessl
Liersch
Pfalzgraf
Höhne
Gutmann
Representat.
Vomhof
Fraenz
Jansen
Fr. Kytzia
Appel
Steiner
Henkel
Goebel
Eich
Häring
Fr. Schäfer
Gilleßen
Kamps
Sander
Phone No.
(02 01) 2 44-1
(02 11) 50 80-01
(02 21) 54 91-0
(02 41) 1 08-0
(02 61) 3 94-0
(069) 75 07-0
(06 41) 7 06-0
(05 61) 5 02-0
(0 61 31) 2 06-0
(06 21) 2 97-1
(07 21) 59 69-0
(06 81) 81 03-0
(0 70 31) 66 68-1
(07 61) 51 01-1
221
216
281
229
2820
2823
2825
2828
2824
-
-
238
444
336
393
276
248
210
651
652
214
214
213
236
585
Ext.
642
687
672
616
125
133
227
334
537
465
536
378
364
360
24
Addresses 73
Regional Sales Offices Addresses
München Arnulfstraße 205
8000 München 19
Augsburg
Kempten
Nürnberg
Würzburg
Regensburg
Bayreuth
Raiffeisenstraße 13
8900 Augsburg 41
Kronenstraße 21
8960 Kempten 1
Muggenhofer Straße 135
8500 Nürnberg 80
Gneisenaustraße 20
8700 Würzburg 1
Bukarester Straße 12
8400 Regensburg 1
Opernstraße 24-26
8580 Bayreuth 2
Representat.
Detzner
Hart
Ulmann
Dups
Rautenstrauß
Demharter
Bestler
Albrecht
Ankenbrand
Dötsch
Will
Mayerhofer
Söder
Balling
Markert
Moldan
Giglberger
Strobel
Phone No.
(089) 13 05-0
(08 21) 79 03-0
(08 31) 2 40 49
(09 11) 3 23-0
(09 31) 7 20 41
(09 41) 79 66-0
(09 21) 88 03-0
-
-
-
-
2630
2650
2520
2520
179
26
Ext.
620
615
289
667
558
-
132
130
74 Addresses
24
Contact Addresses
Publications
AEG Aktiengesellschaft
Automatisierungstechnik
Verkaufsförderung/Werbung
Steinheimer Straße 117
6453 Seligenstadt
Telefon 0 61 82/81-25 60
Training Center
AEG Aktiengesellschaft
Trainingszentrum
Außenstelle Mauergasse 3
6453 Seligenstadt
Telefon 0 61 82/81-22 68
Repairs
AEG Aktiengesellschaft
Automatisierungstechnik
Reparaturabteilung
Steinheimer Straße 117
6453 Seligenstadt
Herr Wombacher,
Telefon 0 61 82/81-22 30
Herr Feid,
Telefon 0 61 82/81-24 03
Service
Central:
AEG Aktiengesellschaft
Anlagenmontage
Automatisierungstechnik
Herr Joachim Hirschmann
Goldsteinstraße 238
6000 Frankfurt 71
Telefon 0 69/66 99-2 35
Telexelektron mont 413 705
AEG Aktiengesellschaft
Anlagenmontage
Herr Karl-Josef Reuter
Goldsteinstraße 238
6000 Frankfurt 71
Telefon 0 69/66 99-2 33
Sales Offices:
AEG Aktiengesellschaft
Anlagenmontage
Inbetriebsetzung und Service
Stützpunkt Konstanz
Herr Werner Oligmüller
Bückelstraße 1-5
7750 Konstanz
Telefon 0 75 31/86-27 20
AEG Aktiengesellschaft
Anlagenmontage
Inbetriebsetzung und Service
Stützpunkt Frankfurt
Herr Max Kummer
Lyoner Straße 19
6000 Frankfurt-Niederrad
Telefon 0 69/66 46 78*
0 69/6 69 92 43
0 69/6 69 93 72
AEG Aktiengesellschaft
Anlagenmontage
Inbetriebnahme und Service
Stützpunkt Stuttgart
Herr Knut Seyerle
Dornierstraße 7
7030 Böblingen-Hulb
Telefon 0 70 31/66 68-203
0 70 31/66 68-201*
AEG Aktiengesellschaft
Anlagenmontage
Inbetriebnahme und Service
Stützpunkt München
Herr Helmut Serfas
Arnulfstraße 199
8000 München 19
Telefon 0 89/13 05-5 98*
0 89/13 05-5 99
AEG Aktiengesellschaft
Anlagenmontage
Technischer Dienst
Stützpunkt Berlin
Herr Heinz Rudolf
Hohenzollerndamm 150
1000 Berlin 33
Außendienst Prozeßtechnik
Telefon 0 30/8 28-21 68
0 30/8 28-27 62*
AEG Aktiengesellschaft
Automatisierungstechnik
Technischer Dienst
Stützpunkt Hannover
Herr Wilhelm Stömpel
Max-Müller-Straße 50-56
3000 Hannover 1
Telefon 05 11/63 04-4 44
AEG Aktiengesellschaft
Automatisierungstechnik
Technischer Dienst
Stützpunkt Hamburg
Herr Jan-Helmut Peters
Holstenkamp 42
2000 Hamburg 54
Telefon 0 40/8 53 95-3 28
0 40/8 53 95-2 49*
AEG Aktiengesellschaft
Automatisierungstechnik
Technischer Dienst
Stützpunkt Essen
Herr Horst Lohmann
Teilungsweg 28
4300 Essen 1
Telefon 02 01/31 94-2 02*
Telex elektron essen 875 849
AEG Aktiengesellschaft
Automatisierungstechnik
MODICON Europa
Service München
Herr Dieter Schödel
Tegernseer Landstr, 161
8000 München 90
Telefon 089/69777-0
* phone recorder
24
Addresses 75
Technical Offices and Sales Points of AEG in the
Federal Republic of Germanyand Berlin (West)
Aachen
Grüner Weg 22/24
D-5100 Aachen
Tel. (02 41) 1 08-0
Augsburg
Raiffeisenstraße 13
D-8900 Augsburg-Lechhausen
Tel. (08 21) 79 03-130
Bayreuth
Opernstraße 24/26
D-8580 Bayreuth 2
Tel. (09 21) 2 20 21
Berlin
Hohenzollerndamm 150
D-1000 Berlin 33
Tel. (0 30) 8 28-1
Bielefeld
Schillerstraße 44
D-4800 Bielefeld 1
Tel. (05 21) 8 05-0
Braunschweig
Campestraße 7
D-3300 Braunschweig
Tel. (05 31) 70 02-0
Bremen
Stresemannstraße 29
D-2800 Bremen 1
Tel. (04 21) 44 94-0
Bremerhaven
Löningstraße 6
D-2850 Bremerhaven*
Tel. (04 71) 4 93 20
Dortmund
Rheinlanddamm
D-4600 Dortmund 1
Tel. (02 31) 12 00-1
Düsseldorf
Wiesenstraße 21
D-4000 Düsseldorf 11
Tel. (02 11) 50 80-01
Essen
Kruppstraße 6
D-4300 Essen 1
Tel. (02 01) 2 44-1
Frankfurt
Mainzer Landstr. 351-367
D-6000 Frankfurt 1
Tel. (0 69) 75 07-0
Freiburg
Tullastraße 84
D-7800 Freiburg
Tel. (07 61) 51 01-1
Gießen
Schanzenstraße 1-5
D-6300 Gießen
Tel. (06 41) 7 06-212
Hamburg
Stadthausbrücke 9
D-2000 Hamburg 36
Tel. (0 40) 34 98-0
Hannover
Max-Müller-Straße 50-60
D-3000 Hannover 1
Tel. (05 11) 63 04-0
Heilbronn
Weinsberger Straße 18
D-7100 Heilbronn*
Tel. (0 71 31) 6 16-0
Karlsruhe
Neureuther Straße 5-7
D-7500 Karlsruhe 21
Tel. (07 21) 59 69-0
Kassel
Lilienthalstraße 150
D-3500 Kassel-Bettenhausen
Tel. (05 61) 5 02-1
Kempten
Kronenstraße 21
D-8960 Kempten*
Tel. (08 31) 2 40 49
Kiel
Seekoppelweg 7
D-2300 Kiel 1
Tel. (04 31) 68 96-0
Koblenz
Rheinstraße 17
D-5400 Koblenz
Tel. (02 61) 3 94-0
Köln
Oskar-Jäger-Str. 125-143
D-5000 Köln 30
Tel. (02 21) 54 91-0
Mainz
Fischtorplatz 14
D-6500 Mainz 1
Tel. (0 61 31) 2 06-0
Mannheim
N 7, 5-6, Kunststraße
D-6800 Mannheim 1
Tel. (06 21) 2 97-1
München
Arnulfstraße 205
D-8000 München 19
Tel. (0 89) 13 05-0
Münster
Friedrich-Ebert-Straße 7
D-4400 Münster
Tel. (02 51) 53 06-0
Nordhorn
Ootmarsumer Weg 8
D-4460 Nordhorn*
Tel. (0 59 21) 50 45/60 50
Nürnberg
Gutenstetter Straße 12
D-8500 Nürnberg 60
Tel. (09 11) 65 97-0
Osnabrück
Pferdestraße 23
D-4500 Osnabrück*
Tel. (05 41) 5 84 92-0
* Sales Point
76 Addresses
24
Ravensburg
Henri-Dunant-Straße 6
D-7980 Ravensburg*
Tel. (07 51) 95 58
Regensburg
Bukarester Straße 12
D-8400 Regensburg 1
Tel. (09 41) 79 66-0
Saarbrücken
Mainzer Straße 176
D-6600 Saarbrücken 3
Tel. (06 81) 81 03-1
Siegen
Sandstraße 173
D-5900 Siegen 1
Tel. (02 71) 47 55
Böblingen
Dornierstraße 7
D-7030 Böblingen-Hulb
Tel. (0 70 31) 66 68-1
Ulm
Neue Straße 113-115
D-7900 Ulm*
Tel. (07 31) 1 72-0
Wesel
Delogstraße 2
D-4320 Wesel*
Tel. (02 81) 2 50 91
Wilhelmshaven
Zedeliusstraße 28
D-2940 Wilhelmshaven*
Tel. (0 44 21) 3 48 60
Würzburg
Gneisenaustraße 20
D-8700 Würzburg 1
Tel. (09 31) 7 20 41
* Sales Point
24
Addresses 77
Austria
AEG Austria GmbH.
Brünner Str. 52
A-1211 Vienna
Tel. (222) 2 77 11-0
MODICON Handelsgesellschaft mbH.
Brünner Str. 52
A-1211 Vienna
Tel. (222) 2 77 11-65 04
AEG Austria GmbH.
Bildgasse 8-10
A-6851 Dornbirn
Tel. (5572) 6 36 12
Asperngasse 2
A-8020 Graz
Tel. (316) 57 25 70-0
Amraser Str. 118
A-6020 Innsbruck
Tel. (5222) 49 21 50
Rosentalerstraße 189
A-9023 Klagenfurt
Tel. (463) 28 27 00
Bachstr. 75
A-5023 Salzburg
Tel. (662) 7 45 01
Europaplatz 6/2
A-3100 St. Pölten
Tel. (2742) 6 76 46
Rubensstr. 40
A-4050 Traun
Tel. (732) 8 30 31
Belgium
S.A. belge - Belgische N.V. AEG
Rue de Stalle 65
B-1180 Brussels
Tel. (2) 3 70 06 11
S.A. belge - Belgische N.V. AEG
Automatisierungstechnik
Bisschoppenhoflaan 637
B-2100 Antwerp (Deurne)
Tel. (3) 3 26 01 70
78 Addresses
Subsidiaries, Representatives and MODICON Distributors of AEG in Europe
Czechoslovakia
MEDIA
Strakonicka 510
CS-1500 Prague 5
Tel. (2) 54 53 46...49
Denmark
AEG Dansk Aktieselskab
Roskildevej 8-10
DK-2620 Albertslund
Tel. (42) 64 85 22
Finland
Säköliikkeiden Oy
Sähkömetsä
SF-01301 Vantaa 30
Tel. (0) 83 81
OY E. Sarlin AB
Automation
Kaivokselantie 3-5, Vantaa
SF-00101 Helsinki
Tel. (0) 53 50 22
France
AEG Modicon Automation S.N.C.
Rue Einstein, ZI Vaux le Pénil
F-77015 Melun Cédex
Tel. (1) 64 37 15 10
MODICON France S.A.R.L.
Rue Michael Faraday
F-78180 Montigny Le Bretonneux
Tel. (1) 34 60 61 01
Great Britain
AEG (UK) Ltd.- Eng. Division
Eskdale Road, Berkshire
GB-Winnersh RG 11 5 PF
Tel. (734) 69 83 30
MODICON Electronics Ltd.
6 Beechwood
Chineham Business Park
GB-Basingstoke,
Hants RG 24 OWA
Tel. (256) 84 31 84
Greece
AEG Hellas A.E.
Florinis Str. 15
GR-18346 Moschaton (Athens)
Tel. (1 ) 4 89 21 11
Hungary
MERCATOR S.A.R.L.
Thököly ut 156
H-1145 Budapest, XIV
Tel. (1) 63 03 55
Iceland
Braedurnier Ormsson H/F
Lágmúla 9
IS-108 Reykjavik
Tel. (1) 3 88 20
Ireland
Process Control & Automation
Systems Ltd.
Strawhall Industrial Estate
IRL-Carlow
Tel. (503) 4 23 77
Italy
AEG Italiana S.p.A.
Via Stephenson, 94
I-20157 Milan
Tel. (2) 3 32 12-1
MODICON Italiana S.r.L.
Via Stephenson, 94
I-20157 Milan
Tel. (2) 3 32 12-1
Elettronucleonica S.p.A.
Piazza de Angeli 7
I-20146 Milan
Tel. (2) 49 82 451
Luxembourg
AEG Luxembourg S.à.r.L.
2, Rue Albert Borschette
L-1246 Luxembourg-Kirchberg
Tel. 43 88 81
24
Netherlands
AEG Nederland N.V.
Aletta Jacobslaan 7
NL-1066 BP Amsterdam
Tel. (20) 5 10 59 11
MODICON B.V.
Haarlemmerstraatweg 113
NL-1165 MK Halfweg (N.H.)
Tel. (2907) 70 41
Norway
AEG Norge A/S
Stanseveien 6
N-0902 Oslo 9
Tel. (2) 16 11 11
Solberg & Andersen a/s
Brynsveien 5
N-0611 Oslo 6
Tel. (2) 65 70 00
Poland
UNITEX S.A.
UI. Stawki 2/31
PL-00950 Warsaw
Tel. (22) 39 82 32
Portugal
AEG Portuguesa S.A.
Rua João Saraiva 4/6
P-1799 Lisbon
Tel. (1) 89 11 71
Romania
AEG Liaison Office Bukarest
Str. Sevastopol No.13-17,Ap. 404
RO-78118 Bucharest
Tel. (0) 59 20 22
Soviet Union
AEG Liaison Office Moskow
Pokrovskij Boulevard 4/17
Korpus 3, 1. Etage
SU-101000 Moskow
Tel. (095) 2 08 54 13
Spain
AEG Ibérica de Electricidad S.A.
c/Principe de Vergara, 112
E-28002 Madrid
Tel. (1) 2 62 76 00
Sweden
AEG Svenska AB
Svetsarvägen 6
S-17127 Solna
Tel. (8) 89 85 65
Switzerland
Elektron AG
Riedhofstraße 11
CH-8804 Au ZH
Tel. (1) 7 81 01 11
GSY Industrieautomation AG
Biberiststr. 24
CH-4501 Solothurn
Tel. (65) 21 81 21
Turkey
AEG Genel Elektrik T.A.S.
Yildiz Posta
Irfan Bastúg Cad. No. 1
Timlo Is Hani, Kat. 3-6
TR-80280 Esentepe/Istanbul
Tel. (1) 1 74 58 10...17
Yugoslavia
INTEREXPORT
27. Marta 69/XII
YU-11000 Belgrade
Tel. (11) 62 00 55
24
Addresses 79
80 Addresses
24
From
Company
Name
Street
City
Phone
AEG Aktiengesellschaft
Fachbereich Automatisierungstechnik
MODICON Europa / Abt. A91 M22
Postfach 1162
D-6453 Seligenstadt
Publications Comment Form
We are constantly striving to improve the contents and usability of our technical documents. If you have any suggestions for improvement, please let us know and mail this form to us.
Name:
Automation Device:
Progr. Device (PADT):
E-No. 424-
Version:
Factory No.
GSW-/Firmware-Version:
MS-DOS-Version:
Graphic Module:
23
81
Suggestions for improvement
Software-Product:
Product Documentation:
Thank you for your help.
82
23
advertisement
* Your assessment is very important for improving the workof artificial intelligence, which forms the content of this project
Related manuals
advertisement