CHESTER Champion Mill 16VS Instruction Manual
Add to My manuals31 Pages
The CHESTER Champion Mill 16VS is a versatile machine designed for drilling, deep milling and face milling of small workpieces. It offers a range of features, including adjustable end stops for precise repeatability, a swiveling mill-drill head for various angles, and a built-in safety system with an emergency stop button. The machine is equipped with a MT2 spindle taper and a draw-in rod for secure tool mounting. With its compact size and robust construction, the CHESTER Champion Mill 16VS is ideal for small workshops, hobbyists, and educational applications.
advertisement
▼
Scroll to page 2
of
31
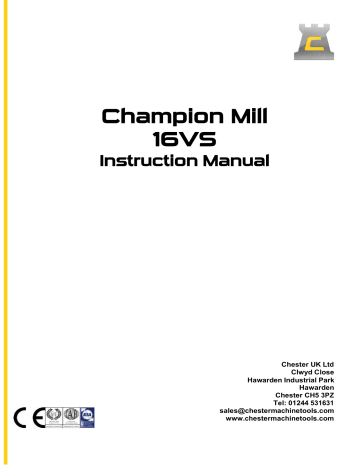
Champion Mill 16VS Instruction Manual Chester UK Ltd Clwyd Close Hawarden Industrial Park Hawarden Chester CH5 3PZ Tel: 01244 531631 [email protected] www.chestermachinetools.com 1. Safety 2. Technical Data 3. 3.1 3.2 3.3 3.4 3.5 3.6 Assembly and Connection Extent of supply Transport Storage Installation and assembly First use Operational accessories 4. 4.1 4.2 4.3 4.4 4.5 4.6 4.7 4.8 4.9 4.10 Operation Safety Controlling and indicating elements Starting the milling machine Inserting tools Changing the speed range Clamping workpieces Swiveling the mill-drill head Clamping levers End stops Installation on a lathe 5. 5.1 5.2 5.3 5.4 5.5 Maintenance Safety Inspection and maintenance Repair Spare parts Connecting Plan 6. 6.1 Anomalies Anomalies in the machine 7. Appendix 1.1 1.2 1.3 1.4 1.5 1.6 1.7 1.8 1.9 1.10 2 Safety warnings Proper use Possible dangers caused by the milling machine Qualification of personnel Safety devices Safety check Individual protection gear For your own safety during operation Disconnecting the machine and making it safe Using lifting equipment 1. Safety Purpose of this Machine: This machine has been designed for drilling, deep milling and face milling of small workpieces. If the operator intends to use this machine beyond its design, please contact the manufacturer or dealer before starting the operation. The Following Should be Obeyed before Operating Do not operate this machine before reading this manual thoroughly. Do not use this machine without professional training of drilling and milling operations. Do not operate this machine outside of its design parameters without first consulting the manufacturer or dealer. When operating this machine, make sure that every safety precaution is followed as indicated in this manual. 1.1 Safety warnings Special Warnings for this Machine Warning! There is a risk of the machine accidentally restarting after a power failure, make sure that all of the operation switches are in the off or neutral positions if the power is interrupted. Warning! Always wear approved eye protection when operating this machine. Correct Handling of this Machine The net weight of this machine is approximately 75kg, we recommend using the correct lifting equipment when moving this machine. If the operator has to handle the machine without lifting apparatus, make sure that you can comfortably lift this weight. Handle the machine with care and be aware of your surroundings to prevent accidents. 1.2 Proper use In the event of improper use the machine will • endanger personnel, • endanger the machine and other material property of the operator, • may affect proper operation of the machine This milling machine is designed and manufactured to be used for milling and drilling cold metals or other non-flammable materials that do not constitute a health hazard by using commercial milling and drilling tools. This machine must only be installed and operated in a dry and well-ventilated place. If the milling machine is used in any way other than described above, modified without authorization or operated with different process data, then it is being used improperly. We do not take any liability for damages caused by improper use. Any such modifications would also render the guarantee null and void. 3 It is also part of proper use that: • the maximum values for the machine are complied with • the operating manual is observed • inspection and maintenance instructions are observed 1.3 Possible dangers caused by the milling machine As the machine operates with • • • high revolutions rotating parts and tools electrical voltage and currents There is a residual risk with use. We have used construction resources and safety techniques to minimize the risk to health to personnel resulting from these hazards. If the machine is used and maintained by personnel who are not duly qualified, there may be a risk resulting from incorrect or unsuitable maintenance. All personnel involved in assembly, commissioning, operation and maintenance must • • be duly qualified, follow this operating manual Disconnect the machine whenever cleaning or maintenance work is being carried out. Warning! This machine may only be used with the safety devices activated. Disconnect the machine immediately whenever you detect a failure in the safety devices or when they are not fitted. All additional installations carried out by the operator must incorporate the prescribed safety devices. 1.4 Qualification of personnel This manual is addressed to • operators, • users, • maintenance staff The warning notes therefore refer to both operation and maintenance of the milling machine. Always disconnect the machine plug from the electrical power supply. This will prevent it from being used by unauthorized personnel. All personnel involved in assembly, commissioning, operation and maintenance must • be duly qualified, • follow this operating manual 4 In the event of improper use • there may be a risk to personnel, • there may be a risk to the machine and other material property, • the proper operation of the machine may be affected 1.5 Safety devices Use the milling machine only with properly functioning safety devices. Stop the machine if there is a failure in the safety device or if it is not functioning for any reason. If a device has not been activated or has failed, the milling machine must only be used when • the cause of failure has been removed • it has been verified that there is no resulting danger for personnel or objects Warning! If you bypass, remove or override a safety device in any way, you are endangering yourself any other personnel working with the milling machine. The possible consequences are • damage as a result of components or parts of components flying off at high speed. • contact with rotating parts, • fatal electrocution The milling machine includes the following safety devices: • a self-locking emergency stop button • a protective cover at the drill-mill head Emergency stop button The emergency stop button switches the machine off. Open the cover of the emergency stop button in order to switch the machine on again. Protective cover The drill-mill head is fitted with a protective cover. Warning! Remove the protective cover after the mains plug of the machine has been pulled. 1.6 Safety check Check the milling machine regularly • at the beginning of each shift, • once a week, • after every maintenance and repair operation 5 General Check Equipment Protective covers Labels, markings Check Mounted, firmly bolted and not damaged Installed and legible OK Functional Test Equipment Emergency Stop Check When the Emergency Stop button is activated, the machine should switch off automatically. A restart will not be possible until the Emergency Stop button has been unlocked and the On switch has been activated. OK 1.7 Individual protection gear For certain work individual protection gear is required. Protect your face and eyes. During all work and specifically work during which your face and eyes are exposed to hazards, a safety helmet with facial protection should be worn. Use protective gloves when handling pieces with sharp edges. Wear safety shoes when you position, dismantle or transport heavy components. Use ear protection if the noise level (inmission) in the workplace exceeds 80 dB (A). Before starting work, make sure that the prescribed individual protection gear is available at the workplace. Caution! Dirty or contaminated individual protection gear can cause disease. Clean it after each use and once a week. 1.8 For your own safety during operation Warning! Before activating the machine, double check that it will not endanger other people or cause damage to equipment. Avoid unsafe working practices: • • • • • • • • 6 The instructions in this manual must be observed during assembly, handling, maintenance and repair. Use protective goggles Turn off the machine before measuring the workpiece. Do not work on the machine if your concentration is reduced, for example, because you are taking medication. Stay on the machine until all rotating parts have come to a halt. Use the prescribed protection gear. Make sure to wear a well-fitting work suit and a hairnet, if necessary. Do not use protective gloves during drilling or milling work. Unplug the shockproof plug from the mains before changing the tool. • • • Use suitable devices to remove drilling and milling chips. Make sure your work does not endanger anyone. Clamp the workpiece tightly before activating the machine. In the description of work on the drilling-milling machine we highlight the dangers specific to that work. 1.9 Disconnecting the machine and making it safe Pull the main plug before beginning any maintenance or repair work. Using lifting equipment Warning! Use of unstable lifting equipment and load-suspension devices that break under load can cause very serious injuries or even death. Check that the lifting equipment and load-suspension devices are of sufficient load capacity and in perfect condition. Observe the rules for preventing accidents issued by your association for the prevention of occupational accidents and safety in the workplace or other inspection authorities. Tighten loads properly. Never walk under suspended loads! 7 2. Technical Data The following information gives the dimensions and weight and is the manufacturer’s authorized machine data. Engine power consumption Drilling capacity End Milling capacity Face Milling capacity Working radius Spindle taper Spindle stroke Headstock tilt Cross travel Longitudinal travel Vertical travel Table size Spindle speeds T slot size Motor Dimensions Net Weight 240V / 50Hz / 600W 16mm 16mm 52mm 175mm MT2 52mm ±90º 160mm 440mm 200mm 500 x 140mm 50-2500rpm 10mm 600W (0.8hp) 520 x 550 x 800mm 75kg Emissions The noise level (emission) of the drilling-milling machine ranges below 78 dB(A). If the drillingmilling machine is installed in an area where various machines are in operation, the acoustic influence (inmission) on the user of the drilling-milling machine may exceed 85 dB(A) in the working area. We recommend the use of soundproofing and ear protection. Remember that the duration of the noise pollution, the type and characteristics of the work area and operation of other machines influence the noise level in the working area. 8 3. Assembly and Connection The drilling-milling machine comes pre-assembled. 3.1 Extent of supply When the drilling-milling machine is delivered, check immediately that the machine has not been damaged during transport and that all components are included. Also check that no fastening screws have come loose. Compare the parts supplied with the information on the packaging list. 3.2 Transport Warning! Machine parts falling off forklift trucks or other transport vehicles could cause very serious or even fata injuries. Follow the instructions and information on the transport case: • Centers of gravity, • Suspension points, • Weights, • Means of transport to be used, • Prescribed shipping position. Use of unstable lifting equipment and load-suspension devices that break under load can cause very serious injury or even death. Check that the lifting and load-suspension gear has sufficient load capacity and that it is in perfect condition. Observe the rules for preventing accidents. Holds the load properly. Never walk under suspended loads. 3.3 Storage Improper storage may cause important parts to be damaged or destroyed. Store packed or unpacked parts only under the intended environmental conditions. Consult Chester UK if the machine or accessories have to be stored for a period of over three months or under different environmental conditions than those given here. 3.4 Installation and assembly The work area for operation, maintenance and repair work must not be hindered. The mains plug of the drilling-milling machine must be freely accessible. Proceed with extreme caution when lifting, installing and assembling the machine. Danger of crushing and overturning. • • 9 Secure the load-suspension device around the drill-mill head. Use a lifting sling for this purpose. Clamp all the clamping levers at the machine before lifting it. • Make sure that no add-on pieces or varnished parts are damaged due to the load-suspension. • Check the horizontal orientation of the base of the machine with a spirit level. • Check that the foundation has sufficient floorload capacity and rigidity. Insufficient rigidity of the foundation leads to the superposition of vibrations between the drillingmilling machine and the foundation (natural frequency of components). Insufficient rigidity of the entire milling machine assembly also rapidly causes the machine to reach critical speeds, with unpleasant vibrations, leading to bad milling results. • • Position the drilling-milling machine on the intended foundation. Attach the drilling-milling machine using the provided recesses in the machine base. 3.5 First use Cleaning and lubricating. Remove the anticorrosive agent applied on the drilling-milling machine for transport and storage purposes. We recommend the use of kerosene. Do not use any solvents, thinners or other cleaning agents which could corrode the varnish on the drilling-milling machine. Follow the specifications of the manufacturer of the cleaning agent. Cleaning the machine. Lubricate all bright machine parts with non-corrosive lubricating oil. Grease the machine according to the lubrication chart. Check smooth running of all spindles. Connect the electrical power cable (shockproof plug). 10 4. Operation 4.1 Safety Use the drilling-milling machine only under the following conditions. • • • • The machine is in proper working order The machine is used as prescribed The operating manual is followed All safety devices are installed and activated All anomalies should be eliminated immediately. Stop the drilling-milling machine immediately in the event of any anomaly in operation and make sure it cannot be started up accidentally or without authorization. 4.2 Controlling and indicating elements 11 4.3 Starting the milling machine By pressing the green button, the machine is switched on. By pressing the red button, the machine is switched off. The electrical system controls the speed with a ramp to the set value. Wait a little while before you continue with the feed when milling or drilling. 4.4 Inserting tools The mill head is equipped with an MT2 seat and a M10 draw-in rod. When milling operations are performed the cone seat must always be fixed to the draw-in rod. All cone connections with the taper bore of the work spindle without using the draw-in rod is not allowed for milling operations. The cone connector should be released by the lateral pressure. Injuries by parts flying off. In the work spindle you may only use tool holding fixtures and clamping tools with morse taper MK2 and internal screw thread M10 for an interlocking fixture. Reducing bushes is not allowed. • • • • • • • • Remove the cover. There is no need to disassemble the motor cover completely. Clean the conical seat in the mill head. Clean the taper mandrel of your tool. Press the mandrel taper with some push into the seat. If the taper mandrel does not hold by itself, either the taper mandrel or the taper bore of the work spindle are not clean or free of grease. Use the draw-in tool supplied with the machine - Hexagon socket spanner for draw-in rod - Hexagon socket spanner for draw-in nut Screw the draw-in rod approx. 15 turns into the taper of your tool Tighten the draw-in nut Follow the same steps in reverse order to extract the tool from the machine. Use of collet chucks When using collet chucks for the reception of milling tools, a higher operation tolerance is possible. The exchange of the collet chucks for a smaller or larger end mill cutter is performed simply and rapidly and the disassembly of the complete tool is not required. The work spindle is equipped with a surface for the hold-up with a fork wrench to unfasten the swivel nut of the collet chuck retainer. The collet chuck is pressed into the ring of the swivel nut and must hold there by itself. By fastening the swivel nut on the tool the milling cutter is clamped. Make sure that the correct collet chuck is used for each milling cutter diameter, so that the milling cutter may be fastened securely and firmly. 12 Direct clamping into the work spindle Tools or collet chucks with a MT2 shank may be clamped directly into the work spindle. For mounting these tools, proceed as described in ‘inserting tool’ on page 13. Make sure that the tool is clamped with the draw-in rod. 4.5 Changing the speed range Wait until the machine has come to a complete halt before changing the speed using the gear switch. • Turn the gear switch in the position ‘H’ for a speed range of 200 – 3000 min • Turn the gear switch into the position ‘L’ for a speed range of 100 – 1500 min • Adjust the speed with the potentiometer Selecting the speed For milling operations, the essential factor is the selection of the correct speed. The speed determines the cutting speed of the cutting edges which cut the material. By selecting the correct cutting speed, the service life of the tool is increased and the working result is optimized. The optimum cutting speed mainly depends on the material and on the material of the tool. With tools (milling cutters) made of hard metal or ceramic insert it is possible to work with higher speeds than with tools made of high-alloy high speed steel (HSS). You will achieve the correct cutting speed by selecting the correct speed. For the correct cutting speed for your tool and for the material to be cut you may refer to the following standard values or a table reference book. The required speed is calculated as follows: 13 Standard values for cutting speeds [m/min] with high speed steel and hard metal in conventional milling. Tool Steel Peripheral and side milling cutters Relived form cutters Inserted tooth cutter with SS Inserted tooth cutter with HM Grey cast iron 10-25mm 10-22mm Age-hardened AI Alloy 150-350mm 15-24mm 15-30mm 100-200mm 10-20mm 12-25mm 30-100mm 150-250mm 200-300mm 300-400mm The results are in the following standard values for speeds in dependence of the milling cutter diameter, cutter type and material. Tool diameter Peripheral and side milling cutters 35mm 40mm 45mm 50mm 55mm 60mm 65mm Tool diameter Form cutters 4 5 6 8 10 12 14 16 Steel 10-25m/min Grey cast iron 10-22m/min Age hardened AI alloy 150-350m/min 91-227 80-199 71-177 64-159 58-145 53-133 49-122 91-200 80-175 71-156 64-140 58-127 53-117 49-108 1365-3185 1195-2790 1062-2470 955-2230 870-2027 795-1860 735-1715 Spindle Speed [min -1] Grey cast iron 10-20 m/min Spindle Speed [min -1] Age hardened AI alloy 150-250 m/min 1194-1911 955-1529 796-1274 597-955 478-764 398-637 341-546 299-478 796-1592 637-1274 531-1062 398-796 318-637 265-531 227-455 199-398 11900-19000 9550-15900 7900-13200 5900-9900 4700-7900 3900-6600 3400-5600 2900-4900 Steel 15-24 m/min Spindle Speed [min -1] Friction during the cutting process causes high temperatures at the cutting edge of the tool. The tool should be cooled during the milling process. Cooling the tool with a suitable cooling lubricant ensures better working results and a longer edge life of the cutting tool. Use a water soluble and non-pollutant emulsion as a cooling agent. This can be acquired from authorized distributors. Make sure that the cooling agent is properly retrieved. Respect the environment when disposing of any lubricants and cooling agents. Follow the manufacturer’s disposal instructions. 14 4.6 Clamping workpieces Caution! Injury by flying off parts The workpiece is always to be fixed by a machine vice, jaw chuck or by another appropriate clamping tool such as clamping claws. 4.7 Swiveling the mill-drill head The mill-drill head may be swiveled to the left. Caution! The drill head may tilt to the right or the left on it’s own after loosening a screw. Proceed with extreme caution when loosening the clamping joints. • • • Loosen or unscrew the nut of the guide screw. Hold the drill-mill head. Loosen the clamping screw. Swivel the mill-drill head into the desired position. Retighten the guide and clamping screw. 4.8 Clamping levers The machine is equipped with clamping levers and screws for the respective movement axes. Use the clamping levers for locking the position of the axes during drilling or milling operations. 4.9 End stops adjustable end stops. The cross table is fitted with two Use the end stops for limiting the travel in order to guarantee the exact repeatability when manufacturing various technical components. 15 4.10 Installation on a lathe The mill head with column can be mounted on a lathe. For fastening an adapter is required. The adapter needs to be fixed to the engine bed. It is not possible to fix it to the lathe slide. The adapter is dimensioned in a way that the middle of the lathe chuck should be reached with the center of the milling spindle (alignment headstock – lathe chuck). Due to the manufacturing tolerances of castings and the manufacturing tolerances of two different machines it is however not possible to reach the exact center, the adapter may be too long or short. If required, the adapter is to be milled off or equipped with dummy sheets. When using sheets the complete surface is to be filled. In order to reduce the support expenditure of the column with milling head during the orientation we recommend you disassemble the milling head off the column. Unscrew the locking screw (safety screw) position 266. Disassemble the milling head off the column by completely loosening the clamping screw and the lead screw and stripping off the milling head. Control the orientation (90° angle horizonal and vertical) of the column with the reference planes on the engine bed of the lathe. In order to prevent you from having to reorient the milling head when altering later on, we recommend you to provide the column and the adapter as well as the engine bed with alignment pins. If required, pin the column together with the cross table before disassembling the column. It is recommended to use hardened straight pins according to DIN 6325 in 8mm or 10mm and a fitting tolerance zone m6. (zB. DIN 6325-8 m6 x 30). These alignment pins have a round cap on one side which facilitates pinning together the parts. When assembled the boring holes must be pilot-drilled to 0.2mm smaller and then rubbed with a reamer also when assembled. Ideally, use a new twist drill with a diameter of 7,8mm for alignment pins of 8mm. 16 5. Maintenance In this section you’ll find important information about • Inspection • Maintenance • Repair The diagram below shows which of these headings each task falls under: Properly performed regular maintenance is essential for safe operation, faulty-free operation, a long service life of the milling machine, and the quality of products that you manufacture. Installation and equipment from other manufacturers must also be in optimum condition. 5.1 Safety The consequences of incorrect maintenance and repair work may include: • Serious injury to personnel working on the milling machine • Damage to the milling machine Only qualified personnel should carry out maintenance and repair work on the milling machine. Only carry out work on the milling machine if it has been unplugged from the mains power supply, then pull the plug out. Restarting Before restarting the machine run a safety check. Before disconnecting the machine check that there is no danger for personnel and that the machine is undamaged. 17 5.2 Inspection and Maintenance The type and extent of wear depends on individual usage and service conditions. For this reason, all the intervals are only valid for the following authorized conditions: Interval Start of work After each maintenance or repair operation Start of work After each maintenance or repair operation Weekly Where? What? How? Drilling-Milling Machine Safety check Safety check Dovetail sideways Lubricate Lubricate all sideways Cross-table Lubricate Lubricate all blank steel parts. Use acid-free oil, for example engine oil An increased clearance in the spindles of the cross-table can be reduced by re-adjusting the spindle nuts. See spare parts drawing 1. The spindle nuts are re-adjusted by reducing the flank of screw thread of the spindle nut with an adjusting screw. By re-adjusting you can assure smooth running of the toolpath, otherwise the wear by friction between spindle nut/spindle would increase considerably. Swivel the mill-drill head to the right by 90°. Every six months Geared mill-drill Grease Detach the cover plate on the head rear side. Lubricate the gear wheels The spindle bearing arrangement is permanently lubricated. No new lubrication is necessary. As required Spindle nuts Re-adjust 5.3 Repair Any maintenance work may only be carried out by a specialized company or by a duly trained personnel. Any maintenance work on electrical equipment may only be carried out specialized electrical staff. For any repair work get assistance from our technical service team. Chester UK Ltd does not take any responsibility nor does it guarantee against damage and operating anomalies resulting from failure to observe this manual. For repairs only use faulty free and suitable tools, original spare parts or parts authorized by Chester UK Ltd. 18 19 Spare parts list 1 Pos. 1 2 3 4 5 6 7 8 9 10 11 12 Designation Turnsignal bearing blocked mill head Locking screw M6 x 16 Washer Spring washer 8 Hexagon socket screw M8 x 25 Nut M12 x 40 Spring washer 12 Washer 12 Screw Washer 10 Spring washer 10 Nut M10 Article No 03336116 1 Qty 1 Pos. 40 03338116 2 2 42 03338116 3 03338116 4 03338116 5 2 6 2 43 44 03338116 6 03338116 7 03338116 8 03338116 9 03338116 10 03338116 11 03338116 12 1 5 1 1 1 1 1 48 49 50 51 13 Guidance item 03338116 13 1 52 14 15 Brass pin Clamping lever DM6 x 16 Slotted head screw Gib 03338116 14 03338116 15 5 3 53 54 03338116 16 03338116 17 1 1 56 03338116 18 03338116 19 1 12 57 58 20 21 22 Angle scale Hexagon socket screw M5 x 10 Bellows Nut M5 Fixing of bellows 03338116 20 03338116 21 03338116 22 1 2 1 59 60 61 23 Rubber chip cover 03338116 23 1 62 24 Gib 03338116 24 1 63 25 26 27 03338116 25 03338116 26 03338116 27 2 1 1 64 65 66 28 Nut M16 x 1.5 Bearing 51203 Tapered toothed wheel Feather key 4 x 16 03338116 28 2 67 29 Spindle Z-axis 03338116 29 1 68 30 Spindle nut Z-axis 03338116 30 1 69 31 32 33 Washer 5 Cover cap Hexagon socket screw M8 x 20 Cover plate column 03338116 31 03338116 32 03338116 33 4 1 4 70 71 72 03338116 34 1 73 Bearing cover Hexagon socket screw M5 x 12 Scale ring Handwheel 03338116 35 03338116 36 1 7 74 75 03338116 37 03338116 38 1 1 76 77 16 17 18 19 34 35 36 37 38 20 Designation Counternut Ball bearing 6001-2RZ Shaft Feather key 4x12 Article No 03338116 40 Qty 4 2 03338116 44 1 2 Column Scale-Z axis Tapered pin A5x25 Hexagon socket screw M6 x 16 Bearing block cross table left x-axis Seal Milling table 03338116 45 03338116 49 03338116 50 03338116 51 1 1 1 8 03338116 52 1 03338116 53 03338116 54 2 1 Bearing block cross table left x-axis Handle M6 x 63 Handwheel 03338116 56 1 03338116 57 03338116 58 3 3 Scale ring Bearing 51200 Hexagon socket screw M6 x 10 Bush of top layer limit stop X-axis Rectangular nut (sliding block) Scale X-axis Spindle X-axis Spindle nut X-axis 03338116 59 03338116 60 03338116 61 3 5 2 03338116 62 2 03338116 63 1 03338116 64 03338116 65 03338116 66 1 1 1 Hexagon socket screw M4 x 20 Guidance of cross table Limit stop of top layer x-axis Gib Spindle nut Y-axis Gib 03338116 67 4 03338116 68 1 03338116 69 1 03338116 70 03338116 71 03338116 72 1 1 1 Hexagon socket screw M6 x 25 Bearing block Spindle Y-axis 03338116 73 2 03338116 74 03338116 75 1 1 Machine stand Hexagon socket screw M12 x 90 03338116 76 03338116 77 1 4 21 Spare parts list 2 Pos. Designation 203 Tension spring 2.5 x 28 x 110-3 Circlip 45 0 3338116 203 1 0 3338116 204 1 Ball bearing 52092RZ Toothed wheel (Z60/Z80) Bearing 7007AC 0 3338116 205 1 0 3338116 206 1 0 3338116 207 1 Circlip 15 Toothed wheel (Z46) Circlip 32 0 3338116 208 0 3338116 209 201 201 204 205 Position disc Bush Article No 0 3338116 201 0 3338116 202 Qty 1 1 Pos. 239 240 Designation Cover Countersink head screw M4 x 8 Article No 0 3338116 239 0 3338116 240 Qty 1 6 243 Spring piece 0 3338116 243 2 1 1 246 247 Spindle Spindle nut 0 3338116 246 0 3338116 247 1 1 0 3338116 210 2 248 0 3338116 248 2 0 3338116 211 2 249 0 3338116 249 1 0 3338116 212 1 250 O-ring 58x2.85 0 3338116 250 1 213 214 215 Ball bearing 600Z2RZ Toothed wheel (Z42/Z62) Primary shaft Feather key 5 x 50 Feather key C5 x 12 Ball bearing 7005AC/P5 Spindle sleeve 0 3338116 213 0 3338116 214 0 3338116 215 1 1 1 251 Tightening nut 0 3338116 251 1 216 Gearshift fork 0 3338116 216 1 217 218 Arm of gearshift fork Screw M5 x 8 0 3338116 217 0 3338116 218 1 1 255 Handle lever 0 3338116 252 3 219 Cover cap of drawin rod Engine cover Motor 0 3338116 219 1 257 0 3338116 257 1 0 3338116 220 0 3338116 221 1 1 258 Hub star knob pinhole infeed Scale ring star knob 0 3338116 258 1 Hexagon socket screw M4 x 8 Washer 4 Hexagon socket screw M6 x 14 Pin A5 x 25 0 3338116 222 6 260 0 3338116 260 3 0 3338116 223 0 3338116 224 6 6 261 Hexagon socket screw M4 x 10 Cover panel 0 3338116 261 1 0 3338116 225 2 Washer 6 Milling head casing cover Hexagon socket screw M5 x 12 C-Circlip 10 Motor toothed wheel (Z25) Feather key C4 x 16 Type plate 0 3338116 226 0 3338116 227 6 1 264 265 Feather key 4 x 12 Low face pinion 0 3338116 264 0 3338116 265 1 1 0 3338116 228 6 266 0 3338116 266 1 0 3338116 229 0 3338116 230 1 1 267 268 Locking screw M6 x 20 Indicator Locking screw M8 x 8 0 3338116 267 0 3338116 268 1 1 0 3338116 231 0 3338116 232 1 1 269 270 271 0 3338116 269 0 3338116 270 0 3338116 271 1 1 1 0 3338116 272 1 273 274 Spring 0.8 x 5 x 25-3 Steel ball 6.5 Rotary selector switch gear 12 x 50 Locking screw M5 x 16 Speed label Retainer disc 0 3338116 273 0 3338116 274 1 1 275 Selector shaft 0 3338116 275 1 206 207 208 209 210 211 212 220 221 222 223 224 225 226 227 228 229 230 231 232 272 236 237 238 22 Clamping lever DM8 x 20 Brass pin Housing of milling head 0 3338116 236 1 0 3338116 237 0 3338116 238 1 1 5.5 Connecting plan Spare parts list for electrical system Designation Control board Fine-wire fuse 23 Article No 0 3338116 301 0 3338116 302 Qty. 1 1 Designation Motor Emergency stop on/off Potentiometer Article No 0 3338116 303 0 3338116 304 Qty. 1 1 0 3338116 305 1 6. Anomalies 6.1 Anomalies in the machine Anomaly The machine does not start Tool burn Cause/Possible effects • Defective fuse • • • • Impossible to insert holding taper into spindle sleeve Motor won’t start Working spindle rattling on rough workpiece • • • Remove dirt, grease or oil from the internal conical surface of the spindle sleeve or holding taper Morse taper is incorrect size Defective fuse • • • • • Climb milling machine not possible under the current operating conditions Clamping levers of the movement axes not tightened Loose collet chuck, loose drill chuck, loose draw-in rod Tool blunt Workpiece loose • Excessive slack in bearing • • Spindle shaft worn or worn out • • Working spindle goes up and down • • • • 24 Incorrect speed The chips have not been removed from the hole Blunt tool Operating without cooling Solution • Have it checked by authorized personnel • Select different speed, feed may be too high • Retract tool more frequently • Sharpen and replace tool • Use cooling agent • Clean surfaces well. Keep surfaces free of grease Use M10 taper Have it checked by authorized personnel Perform conventional milling machining • Tighten clamping levers • Check, retighten • • Sharpen or replace tool Secure the workpiece properly Re-adjust bearing clearance or replace bearing. Replace pos. 246 and 251 of spare parts list 2 Re-adjust bearing clearance or replace bearing pos. 248 spare parts list 2 7. Appendix 7.1 Copyright This document is copyright. All derived rights are also reversed, especially those of translation, re-impression, use of figures, broadcast, reproduction by photo-mechanical or similar means, and recording in data processing systems, whether partial or total. The company reverse the right to make technical alterations without prior notice. 7.2 Terminology/Glossary Term Cross table Taper mandrel Workpiece Draw-in rod Drill chuck Collet chuck Drill-mill head Spindle sleeve Milling sleeve Drilling table Taper Mandrel Spindle sleeve lever Quick action drill chuck Workpiece Tool 25 Explanation Bearing surface, clamping surface for the workpiece with X and Y axis travel. Taper of the tool seat, taper of the bit or the drill chuck. Piece to be milled, drilled or machined. Threaded bar for fastening the taper mandrel in the spindle sleeve. Device for the holding bit. Holding fixture for end mill cutters. Upper part of the drilling-milling machine. Hollow shaft in which the milling spindle turns. Shaft activated by the motor. Bearing surface, clamping surface. Cone of the bit or mill chuck. Manual control for activating the bit. Manually tighten able bit holding fixture. Piece to be turned or machined. Milling cutter, drill bit, countersink etc… 7.3 Product follow up We are required to perform a follow-up service for our products which extends beyond shipment. We would be grateful if you could send us the following information: • • • 26 Modified settings Experiences with the milling machine, which could be important to other users. Repeated failings 7.4 EC Declaration of Conformity 27 8. Index A Anomalies …………………………………………………………………………………….. 24 Appendix …………………………………………………………………………………….. 25 Assembly and connection …………………………………………………………………… 9 C Classification of hazards ……………………………………………………………………… 3 Connecting plans ………………………………………………………………………………23 D Declaration of conformity …………………………………………………………………….. 27 Dimensions …………………………………………………………………………………….. 8 E Emergency stop button ………………………………………………………………………… 5 Emissions ………………………………………………………………………………………... 8 Environmental conditions ………………………………………………………………………. 8 F First use ………………………………………………………………………………………….. 9 I Individual protection gear……………………………………………………………………….. 6 Installation and assembly ………………………………………………………………………. 9 Installation drawing ………………………………………………………………………………10 M Maintenance ………………………………………………………………………………………17 O Operating material ……………………………………………………………………………….. 8 Operation …………………………………………………………………………………………. 11 P Product follow up ………………………………………………………………………………… 26 Proper use ………………………………………………………………………………………… 3 Protective cover …………………………………………………………………………………... 5 S Safety check ……………………………………………………………………………………… 5 Safety devices ……………………………………………………………………………………. 5 Safety during operation ………………………………………………………………………….. 6 Spare parts list ………………………………………………………………………………. 20-22 Spindle seat ………………………………………………………………………………………. 8 Standard values cutting speeds ……………………………………………………………….. 14 Starting the machine ……………………………………………………………………………..12 Storage ……………………………………………………………………………………………. 9 Swiveling the mill-drill head ……………………………………………………………………. 15 T Technical data ……………………………………………………………………………………. 8 Transport ………………………………………………………………………………………….. 9 U Using lifting equipment …………………………………………………………………………... 6 28 29 30 31
advertisement
Key Features
- Drilling, deep & face milling
- Swivelling head
- Adjustable end stops
- MT2 taper
- Emergency stop
- Compact size
Related manuals
Frequently Answers and Questions
What is the drilling capacity of the CHESTER Champion Mill 16VS?
The drilling capacity is 16mm.
What type of spindle taper does the CHESTER Champion Mill 16VS use?
It uses an MT2 spindle taper.
What are the recommended safety precautions when operating the CHESTER Champion Mill 16VS?
Always wear approved eye protection, use the machine only with properly functioning safety devices, and disconnect the machine before maintenance or repair work.