- Home
- Home security & automation
- Gate Opener
- HySecurity
- Apollo 1500 Linear Actuator System (816 arm & 636 Control Board)
- Reference manual
HySecurity Apollo 1500 Linear Actuator System (816 arm & 636 Control Board) Reference manual
Add to My manuals50 Pages
advertisement
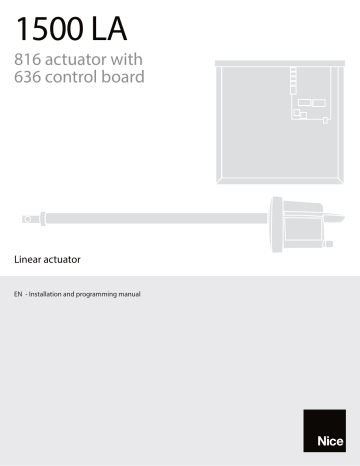
1500 LA
816 actuator with
636 control board
Linear actuator
EN - Installation and programming manual
1500 LA
Installation and Programming Manual
TABLE OF CONTENTS
LIST OF INSTRUCTIONS................................................................................. 2
SECTION 1: CBOX636 & 816 LA OVERVIEW........................................... 3
1.1 636 CONTROL BOARD FEATURES.....................................................3
SECTION 2: CBOX636 PARTS IDENTIFICATION..................................... 5
SECTION 3: SAFETY AND UL325 USAGE CLASSES.............................. 5
SECTION 4: INSTALLATION SAFETY..........................................................11
SECTION 5: TOOLS & MATERIALS NEEDED............................................11
5.1 TOOLS REQUIRED..................................................................................11
5.2 RECOMMENDED BATTERY SPECIFICATIONS .........................11
SECTION 6: ACTUATOR MECHANICAL INSTALLATION.....................12
SECTION 7: CBOX636 INSTALLATION......................................................19
SECTION 8: 816 ACTUATOR AND BATTERY CONNECTIONS ....... 21
SECTION 9: BATTERY CHARGING OPTIONS: AC & SOLAR.............. 25
9.1 120VAC ELECTRICAL WIRING AND SAFETY ................................ 25
9.2 HIGH VOLTAGE WIRE GAUGE REQUIREMENTS........................... 26
9.3 AC-TO-DC CHARGER CONNECTIONS............................................ 26
9.4 SOLAR PANEL CONNECTIONS.......................................................... 27
9.5 SETTING OPEN/CLOSE LIMITS.......................................................... 29
9.6 RECEIVER/TRANSMITTER INSTALLATION & PROGRAMMING.... 31
SECTION 10: 636 CONTROL BOARD FEATURES.................................. 34
10.1 EMERGENCY BYPASS CONNECTOR........................................... 34
10.2 PROGRAM DIP SWITCHES............................................................ 35
10.3 ADJUSTMENTS, SWITCHES, & FUSES........................................ 36
10.4 ACCESSORY CONNECTORS.......................................................... 37
10.5 ACTUATOR INPUT CONNECTORS.............................................. 38
SECTION 11: APPENDIX............................................................................... 39
11.1 CALCULATING SOLAR REQUIREMENTS.................................. 39
11.2 MAINTENANCE SCHEDULE........................................................ 40
11.3 SYSTEM TROUBLESHOOTING..................................................... 41
11.4 INSTALLATION CHECKLIST.......................................................... 42
11.5 PART DRAWINGS............................................................................. 43
SECTION 12: WARRANTY............................................................................. 48
LIST OF INSTRUCTIONS
INSTRUCTION 1A:
INSTALL PIVOT ARM TO GATE: PULL-TO-OPEN .................... 12
INSTRUCTION 1B:
INSTALL PIVOT ARM TO GATE: PUSH-TO-OPEN .................. 13
INSTRUCTION 2:
MOUNT ACTUATOR TO PIVOT ARM ............................................. 14
INSTRUCTION 3:
AFFIX GATE BRACKET TO ACTUATOR ARM ............................... 15
INSTRUCTION 4:
POSITION GATE BRACKET ON GATE .......................................... 16
INSTRUCTION 5:
AFFIX GATE BRACKET TO GATE .................................................. 17
INSTRUCTION 6:
MOUNT CONTROL BOX ..................................................................18
INSTRUCTION 7:
RUN ACTUATOR CABLE(S) TO CONTROL BOX ........................... 19
INSTRUCTION 8A:
CONNECT ACTUATOR(S) TO 636 BOARD: PULL-TO-OPEN ..... 21
INSTRUCTION 8B:
CONNECT ACTUATOR(S) TO 636 BOARD: PUSH-TO-OPEN .... 22
INSTRUCTION 9:
ATTACH WARNING SIGNS TO GATE ............................................ 23
INSTRUCTION 10:
CONNECT AC-DC CHARGER TO BATTERY ............................... 25
INSTRUCTION 11A:
SOLAR PANEL CONNECTIONS: 10-20 WATTS ........................ 26
INSTRUCTION 11B:
SOLAR PANEL CONNECTIONS: 30 WATTS & ABOVE .............. 26
INSTRUCTION 12A:
SETTING MASTER GATE OPEN/CLOSE LIMITS ...................... 27
INSTRUCTION 12B:
SETTING SLAVE GATE OPEN/CLOSE LIMITS .......................... 28
INSTRUCTION 13:
INSTALL 318N RECEIVER & TRANSMITTER ............................... 29
INSTRUCTION 14:
PROGRAMMING TRANSMITTERS FOR 318N ............................ 30
INSTRUCTION 15:
DELETING SINGLE TRANSMITTER FROM MEMORY ................ 31
INSTRUCTION 16:
DELETING ALL TRANSMITTERS FROM MEMORY ..................... 31
INSTRUCTION 17:
USING EMERGENCY BYPASS CONNECTOR ............................. 32
INSTRUCTION 18:
CALCULATING SOLAR REQUIREMENTS..................................... 37 support.hysecurity.com
1500 LA Installation and Programming
1500 LA
Installation and Programming Manual
SECTION 1: 1500 SYSTEM OVERVIEW
Congratulations on selecting a Nice 1500 LA Series gate operator using the 636 control board and 816 LA actuator. With proper selection, system design, installation and maintenance this operator should provide years of reliable operation.
EXTREMELY IMPORTANT!
Anyone who installs, assists with installation or otherwise facilitates the installation in any manner should thoroughly read and understand this manual in its entirety before any attempt is made to actually begin the installation process.
1.1 636 CONTROL BOARD FEATURES
The 636 control board off ers the following features:
•
Simple installation and confi guration
•
Dual gate capable
•
Low power consumption for longer battery life in solar confi gurations
•
Voltage output (+12VDC) connectors to power various added accessories
•
Emergency bypass connector
•
Settings for timer to close, sensitivity, gate reversal after timeout, close timer, and open, stop, close controls
•
LEDs for confi guration and troubleshooting
•
Accepts 318N receiver for remote control operation
1500 LA Installation and Programming
MX4725 Rev. C ©2022
1500 LA
Installation and Programming Manual
OPERATOR KIT
OPERATING VOLTAGE
STANDBY CURRENT
ACCESSORY POWER
POWER SOURCES
OPEN/CLOSE TIME (TO 90°)
TEMPERATURE RATING
GATE WEIGHT MAXIMUM
GATE LENGTH MAXIMUM
USER CONTROLS
CONTROL BOX DIMENSIONS (inches)
ACCESSORY INPUTS
REMOTE CONTROL
CBOX636 SPECIFICATIONS
Single Gate: CBOX636 and 816-1
Dual Gate: CBOX636, 816-1, and 816-2
12 VDC
10 mA
12 VDC
12VDC battery (and optional solar panel for charging)
14 - 16 (gate dependant)
-4º to 122º F (-20º to 50º C)
600 lbs. (272 kg)
16 feet (5 meters)
636 control board
18x18x8
3x Step-by-Step Inputs, 2x Edge Sensor,
Shadow, Safety, Fee Exit, Emergency Bypass
Nice 318N Receiver, 2-Chan., 433.92 MHz, 63 Code Memory
DRIVE
GATE LENGTH MAX.
GATE WEIGHT MAX
OPEN/CLOSE TIME (TO 90°)
816 LA ACTUATOR SPECIFICATIONS
Electromechanical
16 ft (5 m ) leaf
600 lb (272 kg)
14 - 16 seconds (adjustable)
TEMPERATURE RATING
OPERATING VOLTAGE
ACTUATOR DIMENSIONS
USER CONTROLS
LISTED TO UL325
-4º to 122º F (-20º to 50º C)
12VDC
42” retracted - 66” extended
636, 936, or 1050 control board
936 & 1050 Control Boards: Usage Class I, II,
816 LA ACTUATOR PARTS LIST
PART#
816-1
816-2 (DUAL GATE ONLY)
1116
10025215
1125
• 816-1 - ACTUATOR WITH 12’ HARNESS
• 816-2 - ACTUATOR WITH 42’ HARNESS
DESCRIPTION
ACTUATOR WITH 12 FOOT HARNESS
ACTUATOR WITH 42 FOOT HARNESS
PIVOT ARM
GATE BRACKET
ACTUATOR BOLT KIT
ACTUATOR
BOLT KIT
(P/N 1125)
QTY
1
1
1
1
1 support.hysecurity.com
PIVOT ARM (P/N 1116)
GATE BRACKET,
BLACK
(P/N 10025215)
1500 LA Installation and Programming
1500 LA
Installation and Programming Manual
SECTION 2: 1500 LA PARTS IDENTIFICATION
1500 LA PARTS LIST
PART# DESCRIPTION
CBOX636 1500 Series Control Box with 636 Control Board
318N
2-Channel Receiver, 433.92 MHz, 63 Code
Memory
ABF/A
273C
Antenna for 318N Receiver
Gate Warning Signs
75500019 Cable Ties (for Warning Signs)
QTY
1
1
1
2
4
GATE OPERATOR CONTROL BOX
(P/N CBOX636)
2-CHANNEL
RECEIVER
(P/N 318N)
RECEIVER ANTENNA
(P/N ABF/A)
WARNING SIGNS
(P/N 273C)
CABLE TIES (P/N 75500019)
(FOR WARNING SIGNS)
SECTION 3: SAFETY AND UL325 USAGE CLASSES
The UL325 standard covers gate operators. Within this safety standard several Usage Classes are described that defi ne diff erent types of installations where gate operators can be applied. Some operators are restricted in their usage application. All Nice USA operators are approved for use in all four UL325 Usage Classes. Appropriate
Usage Classes are shown in the specifi cations.
CLASS I RESIDENTIAL GATE OPERATOR
Intended for use in a location of one to four single family dwellings or a parking area associated with one to four single family dwellings.
CLASS III INDUSTRIAL/LIMITED ACCESS GATE
OPERATOR
Intended for use in an industrial location or building such as factories or loading docks or other locations not intended to service general public.
CLASS II COMMERCIAL/GENERAL ACCESS GATE
OPERATOR
I n t e n d e d fo r u s e i n a commercial location or building such as a multifamily housing units (five or more single family units) hotels, garages, retail stores or other buildings servicing general public.
CLASS IV RESTRICTED ACCESS GATE OPERATOR
Intended for use in guarded i n d u s t r i a l l o c a t i o n s o r buildings such as an airport s e c u r i t y a re a o r o t h e r restricted access location, not servicing general public, in which access is monitored by security personnel or via closed circuitry.
1500 LA Installation and Programming
MX4725 Rev. C ©2022
1500 LA
Installation and Programming Manual
IMPORTANT!
• The gate operator installation is NOT a “do-it-yourself” project. Contract a qualified gate operator installation company to install this system to ensure a safe and reliable installation.
• It is the responsibility of the property owner to ensure the installer is qualified to carry out the installation in a safe and professional manner.
• Consult local government agencies for latest rules and regulations to satisfy licensing, codes or regulations for automated gate system design and installation.
UL325 USAGE CLASSES
The UL325 standard covers gate operators. Within this safety standard several Usage Classes are described that defi ne diff erent types of installations where gate operators can be applied. Some operators are restricted in their usage application. All Nice USA operators are approved for use in all four UL325 Usage Classes. Appropriate Usage Classes are shown in the Specifi cations.
SAFETY, WARNINGS, AND CAUTIONS
A gate operator is only a component in a gate system. The other parts of the gate system can include:
• the gate
• the external entrapment sensors
• access controls
• vehicle detectors
To have a gate system that provides safety, security, and reliable operation it is essential these components operate together as a system. It is the responsibility of the system designer and/or installer to ensure any safety or operational issues have been addressed.
DANGER!
TO REDUCE THE RISK OF SEVERE INJURY, DEATH,
OR PROPERT Y DAMAGE READ AND FOLLOW ALL
SAFETY INSTRUCTIONS. SAVE THESE INSTRUCTIONS!
CLASS I RESIDENTIAL GATE OPERATOR: Intended for use in a location of one to four single family dwellings or a parking area associated with one to four single family dwellings.
C L A S S I I C O M M E R C I A L / G E N E R A L A C C E S S G AT E
OPERATOR: Intended for use in a commercial location or building such as a multi-family housing units (fi ve or more single family units) hotels, garages, retail stores or other buildings servicing general public.
C L A S S I I I I N D U S T R I A L / L I M I T E D A C C E S S G AT E
OPERATOR: Intended for use in an industrial location or building such as factories or loading docks or other locations not intended to service general public.
C L A S S I V R E S T R I C T E D ACC E S S G AT E O P E R ATO R :
Intended for use in guarded industrial locations or buildings such as an airport security area or other restricted access location, not servicing general public, in which access is monitored by security personnel or via closed circuitry.
VEHICULAR TRAFFIC ONLY
This automatic gate operator is not designed nor is it intended for pedestrian traffi c. Vehicular gate operators must by their nature be powerful to function reliably. This power can cause injury or death. Accordingly, direct all pedestrian traffi c to a separate walk-through gate.
•
Never let children operate or play with gate controls. Keep the remote control away from children.
•
Always keep people and objects away from the gate. No one should cross the path of the moving gate.
•
Test the gate operator monthly. Gate must reverse on contact with a rigid object or stop when an object activates the non-contact sensors. After adjusting the force or the limit of travel, retest the gate operator. Failure to adjust and retest the gate operator properly can increase the risk of injury or death.
•
Use the emergency release only when gate is not moving.
•
Keep gates properly maintained. Read the user’s manual.
Have a qualifi ed service person make repairs to gate hardware.
•
The entrance is for vehicles only. Pedestrians must use separate entrance.
• Save these instructions.
GATE INSTALLATION REQUIREMENTS
Install this gate operator only when:
• The operator is appropriate for the construction of the gate and the usage Class of the gate;
• All openings of a horizontal slide gate are guarded or screened from the bottom of the gate to a minimum of
1.83 meters (6 feet) above the ground to prevent a 57.2 mm (2-1/4 inches) diameter sphere from passing through the openings anywhere in the gate, and the portion of the adjacent fence that the gate covers in the open position;
• All exposed pinch points are eliminated or guarded;
• Guarding is supplied for exposed rollers); support.hysecurity.com
1500 LA Installation and Programming
1500 LA
Installation and Programming Manual
PEDESTRIAN TRAFFIC
The operator is intended for installation only on gates used for vehicles. Pedestrians must be supplied with a separate access opening. The pedestrian access opening shall be designed to promote pedestrian usage. Locate the gate such that persons will not come in contact with the vehicular gate during the entire path of travel of the vehicular gate.
GATE CLEARANCES
The gate must be installed in a location so that enough clearance is supplied between the gate and adjacent structures when opening and closing to reduce entrapment risk. Swinging gates shall not open into public access areas.
GATE CONDITION
The gate must be properly installed and work freely in both directions prior to gate operator installation. Don’t change operator force sensitivity settings to compensate for an improperly installed, improperly functioning, or damaged gate.
GATE CONTROL ACCESS
Permanently mounted controls intended for user activation must be located at least 1.83 m (6 ft) away from any moving part of the gate and where the user is prevented from reaching over, under, around or through the gate to operate the controls. Exception: Emergency access controls only accessible by authorized personnel (e.g. fire, police, EMS) may be placed at any location in the line-of-sight of the gate.
STOP/START BUTTON LOCATION
The Stop and/or Reset button must be located in the lineof-sight of the gate. Activation of the reset control shall not cause the operator to start.
WARNING SIGNS
A minimum of two (2) WARNING SIGNS shall be installed, in the area of the gate. Each placard is to be visible by persons located on the side of the gate on which the placard is installed.
PHOTO EYE SENSORS
For gate operators using a non-contact sensor (Photo Eye):
• See instructions on the placement of non-contact sensors for each type of application.
• Care shall be exercised to reduce the risk of nuisance tripping, such as when a vehicle, trips the sensor while the gate is still moving, and....
• One or more non-contact sensors shall be located where the risk of entrapment or obstruction exists, such as the perimeter reachable by a moving gate or barrier.
CONTACT SENSORS (EDGE)
For a gate operator utilizing a contact sensor (Edge):
• One or more contact sensors shall be located where entrapment or obstruction risks exists, such as at the leading edge, trailing edge, and post-mounted both inside and outside of a vehicular horizontal slide gate.
• A hardwired contact sensor shall be located and its wiring arranged so that the communication between the sensor and the gate operator is not subjected to mechanical damage.
• A wireless device such as one that transmits radio frequency
(RF) signals to the gate operator for entrapment protection functions shall be located where the transmission of the signals are not obstructed or impeded by building structures, natural landscaping or similar obstruction. A wireless device shall function under the intended end-use conditions.
• One or more contact sensors shall be located on the inside and outside leading edge of a swing gate. Additionally, if the bottom edge of a swing gate is greater than 152 mm
(6 in) but less than 406 mm (16 in) above the ground at any point in its arc of travel, one or more contact sensors shall be located on the bottom edge.
USE OF VEHICLE DETECTORS
Use of vehicle detectors (loop detectors) is strongly encouraged to prevent damage to vehicles caused by gates closing on them. This is not considered to be a safety item as vehicle detectors cannot provide protection to pedestrians. In some situations, photoelectric devices may be used as vehicle detectors, but should be wired accordingly.
GATE CONSTRUCTION & SAFETY
Gate construction plays a very important role in ensuring the safety of any automated gate system. The standard for gate construction is ASTM F2200. Below are key areas to address safety in gate design. For complete information consult the standard. Copies of the standard are available at: https://www.astm.org/Standards/F2200.htm
Another source of information is available from DASMA, the
Door and Access System Manufacturer’s Association. The
Association publishes Technical Data Sheets, one of which concerns ASTM F2200. For more information, see: h t t p : / / w w w . d a s m a . c o m / P D F / P u b l i c a t i o n s /
TechDataSheets/OperatorElectronics/TDS370.pdf
1500 LA Installation and Programming
MX4725 Rev. C ©2022
1500 LA
Installation and Programming Manual
GENERAL GATE CONSTRUCTION REQUIREMENTS:
GATE TYPES
Gates shall be constructed in accordance with the provisions given for the appropriate gate type listed. Refer to ASTM
F2200 for additional gate types.
DETACHED GATES
Gates shall be designed, constructed and installed to not fall over more than 45 degrees from the vertical plane, when a gate is detached from the supporting hardware.
GATE BOTTOM EDGE
Gates shall have smooth bottom edges, with vertical bottom edged protrusions not exceeding 0.50 inch (12.7 mm) when other than the exceptions listed ASTM F2200.
BARBED WIRE/TAPE HEIGHT
The minimum height for barbed wire shall not be less than
6 ft. (1.83 m) above grade. The minimum height for barbed tape shall not be less than 8 ft. (2.44 m) above grade.
EXISTING GATE LATCHES
An existing gate latch shall be disabled when a manually operated gate is retrofitted
GATE LATCH RESTRICTIONS
A gate latch shall not be installed on an automatically operated gate.
GATE PROTRUSIONS
Protrusions shall not be permitted on any gate. Consult
ASTM F2200 for exceptions.
GRAVITY AND GATE MOVEMENT
Gates shall be designed, constructed and installed such that their movement shall not be initiated by gravity when an automatic operator is disconnected.
PEDESTRIAN GATES
For pedestrian access in the vicinity of an automated vehicular gate, a separate pedestrian gate shall be provided.
The pedestrian gate shall be installed in a location such that a pedestrian shall not come in contact with a moving vehicular access gate. A pedestrian gate shall not be incorporated into an automated vehicular gate panel.
UPGRADING NON-AUTOMATIC GATES
Any non-automated gate that is to be automated shall be upgraded to conform to the provisions of this specifi cation.
PEDESTRIAN AND NON-AUTOMATIC GATES
This specification shall not apply to gates generally used for pedestrian access and to vehicular gates not to be automated.
UPGRADING EXISTING AUTOMATED GATES
Any existing automated gate, when the operator requires replacement, shall be upgraded to conform to the provisions of this specifi cation in eff ect at that time.
VEHICULAR HORIZONTAL SLIDE GATE REQUIREMENTS:
CLASS I, II AND III VEHICULAR HORIZONTAL SLIDE GATES:
The following provisions shall apply to Class I, Class II and Class
III vehicular horizontal slide gates:
Exposed Rollers
All weight bearing exposed rollers 8 feet (2.44 m), or less, above grade shall be guarded or covered
Guarding or Screening Gate Openings
All openings shall be designed, guarded, or screened from the bottom of the gate to the top of the gate or a minimum of 72 inch (1.83 m) above grade, whichever is less, to prevent a 2 1/4 inch (57 mm) diameter sphere from passing through the openings anywhere in the gate, and in that portion of the adjacent fence that the gate covers in the open position. The gate panel shall include the entire section of the moving gate, including any back frame or counterbalance portion of the gate.
Gaps Between Gate Frames and Other Objects
A gap, measured in the horizontal plane parallel to the roadway, between a fixed stationary object nearest the roadway (such as a gate support post) and the gate frame when the gate is in either the fully open position or the fully closed position, shall not exceed 2 1/4 inch (57 mm). Exception: All other fixed stationary objects greater than 16 inch (406 mm) from the gate frame shall not be required to comply with this section.
Class I, Class II and Class III Gate Stops
Positive stops shall be required to limit travel to the designed fully open and fully closed positions. These stops shall be installed at either the top of the gate, or at the bottom of the gate where such stops shall horizontally or vertically project no more than is required to perform their intended function.
Gate Lateral Stability
All gates shall be designed with sufficient lateral stability to assure that the gate will enter a receiver guide. Consult ASTM
F2200 for details on various gate panel types.
CLASS IV VEHICULAR HORIZONTAL SLIDE GATES:
The following provisions shall apply to Class IV vehicular horizontal slide gates:
Guarded or Covered Rollers
All weight bearing exposed rollers 8 feet (2.44 m), or less, above grade shall be guarded or covered.
support.hysecurity.com
1500 LA Installation and Programming
Class IV Gate Stops
Positive stops shall be required to limit travel to the designed fully open and fully closed positions. These stops shall be installed at either the top of the gate, or at the bottom of the gate where such stops shall horizontally or vertically project no more than is required to perform their intended function.
CLASS I, II, AND III HORIZONTAL SWING GATES:
The following provisions shall apply to Class I, Class II, and
Class III horizontal swing gates:
Avoiding Entrapment Areas
Gates shall be designed, constructed and installed so as not to create an entrapment area between the gate and the supporting structure or other fixed object when the gate moves toward the fully open position, subject to the following provisions.
Open Gate Size Restrictions
The width of an object (such as a wall, pillar or column) covered by a swing gate when in the open position shall not exceed 4 inch (102 mm), measured from the centerline of the pivot point of the gate. Exception: For a gate that is not in compliance with this provision, the defined area shall be subject to the entrapment protection provisions of UL 325.
Open Gate Minimum Distance to Objects
Except for the zone specified in Open Gate Size Restriction
(above) the distance between a fixed object such as a wall, pillar or column, and a swing gate when in the open position shall not be less than 16 inch (406 mm). Exception: For a gate that is not in compliance with this provision, the defined area shall be subject to the entrapment protection provisions of
UL 325.
Class IV Installations
Class IV vehicular horizontal swing gates shall be designed, constructed and installed in accordance with security related parameters specific to the application in question.
MAINTENANCE OF GATE SYSTEMS
To keep your automated gate system performing both safely and reliably it is important to ensure that the components of that system are functioning properly. At least monthly:
GATE TRAVEL TESTING
Disconnect the gate operator and manually move the gate through its range of travel. Note any squeaks from rollers or hinges or areas of binding. The gate should travel smoothly and quietly throughout its range. If it does not, contact a gate professional to correct the problem.
SAFETY DEVICE TESTING
1500 LA
Installation and Programming Manual
Reconnect gate operator and perform the following tests:
PHOTO EYE BLOCKAGE TEST
With the gate opening, block any photo eyes and/or depress any safety edges used to protect the open direction. The gate should stop, or, stop and reverse.
EDGE CONTACT TEST
With the gate closing, block any photo eyes and/or depress any safety edges used to protect the close direction. The gate should stop, or, stop and reverse.
OBSTRUCTION TEST - OPENING
Using a suitable obstruction in the path of the gate (a solid, immovable object), run the gate in the open direction until it contacts the obstruction. The gate should stop and reverse.
ENTRAPMENT PROTECTION
The UL325 standard for gate operators requires a minimum of two independent entrapment protection means for each entrapment zone. An entrapment zone is defi ned as follows:
For slide gates, any locations between a moving gate and a counter opposing edge or surface where entrapment is possible up to a height of 6 ft. (1.83 m) above grade. Such locations occur if at any point in travel if the gap between a moving gate and the fixed counter opposing edges or surfaces is less than 16 inch (406 mm).
For swing gates, locations between a moving gate or moving, exposed operator components and a counter opposing edge or surface where entrapment is possible up to 6 feet
(1.83m) above grade. Such locations occur if during any point in travel: a. The gap between the bottom of a moving gate and the ground is greater than 4 inch (101.6 mm) and less than
16 inch (406 mm); or b. The distance between the center line of the pivot and the end of the wall, pillar, or column to which it is mounted when in the open or closed position exceeds 4 inch (101.6 mm). Any other gap between a moving gate and fi xed counter opposing edges or surfaces or other fi xed objects is less than 16 inch (406 mm) (examples are walls, curbs, berms or other immovable objects).
c. Potential entrapment zones may be identified before installation for swing gates, but there may be other entrapment zones presented by the actual installation and adjacent structures or landscape that must be protected as well. All Nice gate operators feature an Inherent Entrapment System (IES) (UL325 Type A) that monitors the force on the gate during travel. This system protects in both the open and close direction
1500 LA Installation and Programming
MX4725 Rev. C ©2022
1500 LA
Installation and Programming Manual and reverses on contact with an obstruction. This IES system serves as one of the means of entrapment protection.
External sensors must be used to protect against entrapment at each location where an entrapment zone exists. The minimum number of external sensors required to enable automatic operation of the swing gate is one sensor in the close direction
(provided the gate in the open direction presents no risk of entrapment.)
The gate operator tests for the presence of at least one functioning sensor, and if not found, the operator will only run using continuous pressure on an Open/Close button, either on the controller, or an external device.
SENSORS AND ACCESSORIES
Instructions have been provided for installation of the photo eye transmitter/receiver pair per UL325 requirements, but there are other sensors that should be used to avoid entrapment scenarios.
• Non-contact and contact sensors must be installed individually or in combination with each other to provide external entrapment protection.
• Care should be exercised to reduce the risk of nuisance tripping, such as when a vehicle trips the sensor while the gate is still moving, and one or more non-contact sensors shall be located where the risk of entrapment or obstruction exists, such as the perimeter reachable by a moving gate or barrier.
• A hardwired contact sensor shall be located and its wiring arranged so that the communication between the sensor and the gate operator is not subjected to mechanical damage.
• A wireless contact sensor such as one that transmits radio frequency (RF) signals to the gate operator for entrapment protection functions shall be located where the transmission of the signals are not obstructed or impeded by building structures, natural landscaping or similar obstruction.
support.hysecurity.com
1500 LA Installation and Programming
1500 LA
Installation and Programming Manual
SECTION 4: INSTALLATION SAFETY
IMPORTANT!
•
The gate operator installation is NOT a “do-it-yourself” project. Contract a qualified gate operator
•
Property owner is responsible to ensure installer is qualifi ed to make a safe and professional installation.
• regulations that regulate automated gate system design and installation.
•
The gate being modifi ed should be level and plumb and the gate should open easily and evenly.
•
Nice swing gate systems are NOT intended for installation on an incline.
CAUTION!
•
Disconnect power at the control panel before making any electric service power connections.
•
Be aware of all moving parts and avoid close proximity to any pinch points.
SECTION 5: TOOLS & MATERIALS NEEDED
5.1 TOOLS REQUIRED
Below is a list of tools and materials necessary for installation of the actuator and control box:
•
Welder, unless optional bolt-on pivot arm (P/N 446) is used.
•
Basic hand tools (screwdrivers, wrenches, pliers, etc..)
•
Bubble Level (for ensuring pivot arm and actuator are level).
•
Framing square (for determining pivot arm location)
• Wire cutters/strippers
•
Drill and assorted size bits
•
Hardware for mounting control box
•
Electrical conduits, grommets, asphalt patch, etc. as needed
5.2 RECOMMENDED BATTERY SPECIFICATIONS
The following are required to install and program the CBOX636:
•
12VDC battery to power the control board
•
An AC-to-DC fully automatic charger and/or solar panel to charge the battery.
Nice off ers AC-to-DC converters and solar panel solutions for charging 12VDC batteries. Recommended battery specifi cations are as follows:
RECOMMENDED 12VDC BATTERY SPECIFICATIONS
12 Volt DC Output
Sealed lead acid starter battery
Terminal posts on top (not sides)
35 AMP hours or larger for AC charging applications
70 AMP hours or larger for Solar charging applications & Longer Backup
1500 LA Installation and Programming
MX4725 Rev. C ©2022
1500 LA
Installation and Programming Manual
SECTION 6:
ACTUATOR MECHANICAL INSTALLATION
1A
INSTALL PIVOT ARM TO GATE: PULL-TO-OPEN
1.
Securely mount the pivot arm to the hinge post (IMAGE 1A-1).
2.
If necessary, cut pivot arm for correct placement of the actuator mounting hole. Measurements are taken from the center of pivot of the gate hinge.
3. It is strongly recommended to weld the pivot arm to the hinge post.
NOTE:
Welding is much preferred but Nice off ers an optional bolt-on pivot arm
(P/N 446) for when welding is not possible.
CAUTION!
NEVER WELD PARTS TO THE GATE OR POSTS WHEN THE CONTROL BOARD IS
POWERED TO AVOID IRREPAIRABLE DAMAGE TO THE CIRCUIT BOARD!
HINGE POST
CENTER OF HINGE
HINGE POST
CENTER OF HINGE
GATE CLOSED
6”
13”
PIVOT ARM
DIRECTION OF OPENING
TOP VIEW
CENTER LINE OF
ATTACHMENT POINT
FOR GATE BRACKET
PIVOT ARM
13”
6”
1/2”
PIVOT ARM
HINGE POST support.hysecurity.com
LEFT SIDE VERTICAL VIEW
IMAGE 1A-1: "PULL TO OPEN" PIVOT ARM INSTALLATION
1500 LA Installation and Programming
1500 LA
Installation and Programming Manual
1B
INSTALL PIVOT ARM TO GATE: PUSH-TO-OPEN
1.
Securely mount the pivot arm to the hinge post (IMAGE 1B-1).
2.
If necessary, cut pivot arm for correct placement of the actuator mounting hole. Measurements are taken from the center of pivot of the gate hinge.
3. It is strongly recommended to weld the pivot arm to the hinge post.
NOTE:
Welding is much preferred but Nice off ers an optional bolt-on pivot arm
(P/N 446) for when welding is not possible.
CAUTION!
NEVER WELD PARTS TO THE GATE OR POSTS WHEN THE CONTROL BOARD IS
POWERED TO AVOID IRREPAIRABLE DAMAGE TO THE CIRCUIT BOARD!
DIRECTION OF OPENING
HINGE POST
CENTER OF HINGE
HINGE POST
CENTER OF HINGE
GATE CLOSED
6”
11”
PIVOT ARM
HINGE POST
TOP VIEW
11”
PIVOT ARM
6”
CENTER LINE OF
ATTACHMENT POINT
FOR GATE BRACKET
1/2”
PIVOT ARM
LEFT SIDE VERTICAL VIEW
IMAGE 1B-1: "PUSH TO OPEN" PIVOT ARM INSTALLATION
1500 LA Installation and Programming
MX4725 Rev. C ©2022
1500 LA
Installation and Programming Manual
2
MOUNT ACTUATOR TO PIVOT ARM
1.
Mount the actuator to the pivot arm as shown (IMAGE 2-1). Note that the washer goes above the actuator fl ange.
2.
Tighten the lock nut to prevent movement or shifting when the actuator is running. This will also prevent excessive “bounce” or “wobble” when the gate stops moving.
BOLT
WASHER
PIVOT
ARM
LOCK
NUT
ACTUATOR
IMAGE 2-1: ACTUATOR INSTALLATION support.hysecurity.com
1500 LA Installation and Programming
1500 LA
Installation and Programming Manual
3
AFFIX GATE BRACKET TO ACTUATOR ARM
If security is of the utmost importance then the bracket may be connected to the actuator arm using the
1/2” x 3” bolt, washer, and lock nut (IMAGE 3-1).
However, to enable quick manual opening of the gate in case of power failure, it is recommended to use the quick release hitch pin with R-clip (IMAGE 3-2).
1/2” WASHER
1/2”x 3” BOLT
GATE
BRACKET
ACTUATOR
ARM
1/2” LOCK NUT
IMAGE 3-1: GATE BRACKET TO ACTUATOR USING BOLT, WASHER, & NUT
HITCH PIN
HOLE FOR R-CLIP
R-CLIP (INSERT INTO HITCH
PIN HOLE)
IMAGE 3-2: GATE BRACKET TO ACTUATOR USING HITCH PIN AND R-CLIP
1500 LA Installation and Programming
MX4725 Rev. C ©2022
1500 LA
Installation and Programming Manual
3: AFFIX GATE BRACKET TO ACTUATOR ARM (CONT.)
1/2”x 3” BOLT
1/2” WASHER
GATE BRACKET
ACTUATOR
ARM
1/2” LOCK NUT
IMAGE 3-3: GATE BRACKET WITH BOLT, WASHER, NUT
HITCH PIN
GATE BRACKET
ACTUATOR
ARM
R-CLIP
IMAGE 3-4: GATE BRACKET WITH HITCH PIN AND R-CLIP support.hysecurity.com
1500 LA Installation and Programming
1500 LA
Installation and Programming Manual
4
POSITION GATE BRACKET ON GATE
1.
Place gate in: a) OPEN position for PULL-TO-OPEN confi guration (IMAGE 4-1).
b) CLOSED position for PUSH-TO-OPEN confi gurations ( IMAGE 4-2).
2.
With actuator arm fully retracted, rotate entire actuator on the pivot arm around until the gate bracket attached to the actuator is positioned on a supporting structure of gate.
3.
Mark position of gate bracket on gate or clamp into position.
NOTES:
• Do not attach gate bracket to gate pickets. Attach only to structural supports.
• If unsure of exact bracket location, tack weld or clamp until gate can be tested.
GATE OPEN
GATE BRACKET
LOCATION
ACTUATOR
(RETRACTED)
PIVOT ARM
PIVOT ARM
IMAGE 4-1: GATE BRACKET LOCATION (PULL-TO-OPEN)
ACTUATOR
(RETRACTED) GATE BRACKET
LOCATION
GATE
CLOSED
WALL
IMAGE 4-2: GATE BRACKET LOCATION (PUSH-TO-OPEN)
1500 LA Installation and Programming
MX4725 Rev. C ©2022
1500 LA
Installation and Programming Manual
5
AFFIX GATE BRACKET TO GATE
1.
Weld the gate bracket to the gate supporting structure (IMAGE 5-1).
CAUTION!
NEVER WELD PARTS TO THE GATE OR POSTS WHEN THE CONTROL BOARD IS
POWERED TO AVOID IRREPAIRABLE DAMAGE TO THE CIRCUIT BOARD!
GATE BRACKET
CENTERLINE
ACTUATOR
ARM
WELD
1/2”
1/2” FROM
SURFACE OF PIVOT
ARM, SEE INST. 1A & 1B
GATE BRACKET
IMAGE 5-1: GATE BRACKET WELDED TO GATE
IMPORTANT! Ensure bracket centerline is 1/2” above the top of the pivot arm.
2.
If welding is not possible, drill two holes to match bracket and affi x with two 3/8”x2.5” screws and 3/8” nuts included in the kit (IMAGE 5-2).
GATE BRACKET
3/8”x2.5” HEX BOLT (x2)
3/8” NUT (x2)
IMAGE 5-2: GATE BRACKET AND HARDWARE
IMPORTANT!
Use a bubble level to assure after mounting that actuator is level and plumb.
support.hysecurity.com
1500 LA Installation and Programming
1500 LA
Installation and Programming Manual
SECTION 7: CBOX636 INSTALLATION
6
MOUNT CONTROL BOX
1. Mount control box on same side as primary actuator (for dual gate systems, same side as the actuator with shorter harness) and at least six feet away from pivot arm (IMAGE 6-1).
2. Set battery inside of control box with terminals toward the front.
6 FOO
MINIMUM LOCATE
BATTERY HERE
CONTROL
BOX
NOTES:
Mounting holes and hardware for the control box are NOT included.
Drill holes as needed and use hardware capable of supporting the weight of the control box with the battery included.
PIVOT ARM
LOCATION
GATE
IMAGE 6-1: CONTROL BOX MOUNTING LOCATION
NOTE:
IMAGE 6-1 shows a typical install. The control box may be installed on either side of the wall depending on which direction the gate opens or where a person monitoring the gate will be located.
CAUTION!
DO NOT MOUNT THE CONTROL BOX WHERE THE PERSON USING THE PUSH BUTTON
ON SIDE OF BOX CAN COME IN CONTACT WITH THE GATE!
1500 LA Installation and Programming
MX4725 Rev. C ©2022
1500 LA
Installation and Programming Manual
7
RUN ACTUATOR CABLE(S) TO CONTROL BOX
Run the cable of the actuator closest to the control box through a hole (with rubber grommet) drilled in the bottom on the control box. If necessary, entry may be made elsewhere on the control box.
If a dual gate installation:
1.
Dig a trench across the driveway deep enough to accommodate the longer harness cable from the actuator farthest from the control box.
2.
Run the cable through an appropriate conduit and lay this in the trench.
3.
Cover the trench and use asphalt patch if needed.
4.
Run the 2nd cable into a hole (with rubber grommet) into the bottom of the control box.
NOTE:
Ensure the cable(s) reaches into the control box suffi ciently to reach the MOTOR inputs on the control board. support.hysecurity.com
1500 LA Installation and Programming
1500 LA
Installation and Programming Manual
SECTION 8: ACTUATOR WIRING & CONNECTIONS
There are two actuator input connectors on the 636 control board, MASTER and SLAVE. The MASTER connector is used for single gate systems, and the SLAVE is used when a second actuator is used for a dual gate confi guration.
For a single gate system, the unused SLAVE connector is populated by a connector with jumpers (FIGURE 8-1).
Pull-to-Open (Standard) and Push-to-Open confi gurations use diff erent wiring in the actuator harness/connector to reverse limit detection (PINS 1 & 2) and motor direction (PINS 3 & 4).
NOTE:
Refer to INSTRUCTION 2B for instructions for rewiring connector for Push-To-Open confi gurations.
7
5
3
1
8
6
4
2
7
5
3
1
8
6
4
2
SLAVE INPUT
(WITH JUMPERED
CONNECTOR)
MASTER INPUT
SLAVE MASTER
FIGURE 8-1: ACTUATOR CONNECTORS
NOTE:
The unused SLAVE connector is populated with jumpered connector for single gate system, as shown in
FIGURE 8-1. This jumpered connector is removed if the SLAVE connector is used for a second actuator.
PIN
ACTUATOR WIRING
(PULL-TO-OPEN)
FUNCTION
1 ORANGE Open Limit Input
2 WHITE
Close Limit Input
3
COLOR
BLACK
Motor -
4
5
RED
GREEN
Motor +
Limit Switch Common
6
7
8
BLACK
RED
---
BLUE
N/C
Battery Negative
Battery Positive
Encoder
PIN
ACTUATOR WIRING
(PUSH-TO-OPEN)
FUNCTION
1 WHITE Close Limit Input
2 ORANGE
Open Limit Input
3
COLOR
RED
Motor +
4
5
6
BLACK
GREEN
---
Motor -
Limit Switch Common
N/C
7
8
BLACK
RED
BLUE
Battery Negative
Battery Positive
Encoder
1500 LA Installation and Programming
MX4725 Rev. C ©2022
1500 LA
Installation and Programming Manual
8.1
816 ACTUATOR CABLE HARNESS AND BATTERY CONNECTIONS
The 816 actuator cable harness is shipped with connector and battery leads already installed for connecting to the 636 control board
and battery for PULL-TO-OPEN systems. For PUSH-TO-OPEN confi gurations, it is necessary to rewire the actuator connector (see INSTRUCTION 8B).
BATTERY
LUGS
ACTUATOR CONNECTOR
FIGURE 8-2: 816 EXISTING CONNECTOR & BATTERY LEADS ON 816 ACTUATOR CABLE
CURRENT SENSE DEL
TIMER TO CL
AY
OSE OPT.
SLAVE DISABLE
MASTER DISABLE
MAX RUN TIMER OPT .
UE
TIMER TO CLOSE VALUE
T
TIMER
O CL OSE
CURRENT
SENSITIVIT Y
_
NEGATIVE
(BLACK)
+
POSITIVE
(RED)
M ASTER
OPEN
M ASTER
CLOSE
SL AVE
OPEN
SL VE
CL OSE
BATTERY
MASTER INPUT
CONNECTOR
EMER
MOMENT AR
PASS
Y USE ONL Y
TO ACTUATOR
RED
BLACK
FIGURE 8-3: BATTERY CONNECTION FROM ACTUATOR HARNESS (SINGLE GATE SHOWN)
NOTES:
•
For dual gate systems, once the primary actuator harness battery leads are connected to the battery, it is not necessary to connect the battery leads of the secondary actuator cable harness.
•
The actuator closest to the control box (with shortest actuator harness), is connected to the MASTER
(MOTOR 1) connector on the control board.
•
The actuator farthest from the control box (longest harness) is connected to the SLAVE (MOTOR 2) connector.
•
Note that wiring connections are diff erent for Pull-to-Open and Push-to-Open installations.
support.hysecurity.com
1500 LA Installation and Programming
1500 LA
Installation and Programming Manual
8A
ACTUATOR CONNECTIONS: PULL-TO-OPEN
1. Locate the MASTER and SLAVE input connectors on the 636 control board per FIGURE 8-1.
2.
Plug the primary actuator harness connector into the MASTER connector on the 636 control board
(IMAGE 8A-1).
3.
Connect the two battery lugs of the primary actuator cable from the actuator harness(es) to the battery; red to positive (+) and black to negative (-).
4.
For dual gate confi gurations, remove the existing jumpered connector from the SLAVE connector, then plug the secondary actuator (with longer harness) into the SLAVE connector. Do not use the battery cables from the secondary actuator cable, as the primary actuator cable battery cables have already been connected in Step 3.
_
+
BLACK
GREEN
BLACK
ORG
BLACK
GREEN
BLACK
ORG
7
5
3
1
MASTER
7
5
3
1
8
6
4
2
BLUE
RED
YELLOW
RED
WHITE
IMAGE 8A-1: SINGLE GATE - PULL-TO-OPEN WIRING
SLAVE
8
6
4
2
BLUE
RED
YELLOW
RED
WHITE
BLACK
GREEN
BLACK
ORG
MASTER
7
5
3
1
8
6
4
2
IMAGE 8A-1: DUAL GATE - PULL-TO-OPEN WIRING
BLUE
RED
YELLOW
RED
WHITE
1500 LA Installation and Programming
MX4725 Rev. C ©2022
1500 LA
Installation and Programming Manual
8B
ACTUATOR CONNECTIONS: PUSH-TO-OPEN
PUSH-TO-OPEN confi gurations require that the actuator connectors be rewired as follows:
1.
Reverse wires on pins 1 and 2 (orange & white, limit switch wires), IMAGE 8B-1.
2.
Reverse wires on pins 3 and 4 (black & red, motor wires), IMAGE 8B-1.
NOTE: See next page for tips on rewiring the Tyco connector.
BLACK
PULL-TO-OPEN (EXISTING)
7 8
BLUE
RED
GREEN 5 6 YELLOW
BLACK
ORG
3
1
4
2
RED
WHITE
BLACK
PUSH-TO-OPEN (REWIRED)
7 8
BLUE
RED
GREEN 5 6 YELLOW
RED
WHITE
3
1
4
2
BLACK
ORG
IMAGE 8B-1: HARNESS REWIRING FOR PUSH-TO-OPEN INSTALLATIONS
3. Locate the MASTER and SLAVE input connectors on the 636 control board per FIGURE 8-2.
4.
Plug the primary (shorter harness) actuator connector into the MASTER connector on the 636 control board.
5.
For dual gate confi gurations, remove the existing jumpered connector from the SLAVE connector, then plug the secondary actuator (longer harness) into the SLAVE connector.
6.
Connect the two battery lugs from the MASTER actuator harness to the battery; red to positive (+) and
SLAVE MASTER
BLACK 7 8
BLUE
RED BLACK 7 8
BLUE
RED
GREEN 5 6 YELLOW GREEN 5 6 YELLOW
RED
WHITE
3
1
4
2
BLACK
ORG
RED
WHITE
3
1
4
2
BLACK
ORG
IMAGE 8B-2: DUAL GATE - PUSH-TO-OPEN WIRING
1500 LA Installation and Programming support.hysecurity.com
1500 LA
Installation and Programming Manual
TIPS: REWIRING TYCO CONNECTORS
Switch wires by removing the pin/wire from Tyco connector and reinserting into new position using a very small screwdriver or the Tyco extraction tool (TE P/N 305183, follow manufacturers instructions). To use a small screwdriver instead of the extraction tool, see below:
TYCO PIN EXTRACTION/INSERTION TOOL
1.
Change wires by inserting small screwdriver into the front of connector next to the pin/wire as shown below, pushing in tab on pin, then pulling pin/wire from rear of connector. After reinserting into new position, tab should snap into place and hold the wire pin in place.
TAB (PUSH DOWN)
PULL WIRE PIN SMALL SCREWDRIVER
CONNECTOR
SHELL
REMOVING PIN/WIRE WITH SMALL SCREWDRIVER (SIDE VIEW)
9
ATTACH WARNING SIGNS TO GATE
1.
Place the warning signs (IMAGE 9-1) on outside and inside of gate in high visibility locations (eye height) to warn of entrapment dangers. If signs cannot be attached to gate, ensure they are as visible as possible to pedestrians and anyone operating the gate.
2.
Use two tie wraps per sign, or alternative means, to securely affi x signs to the gate.
IMAGE 9-1: GATE ENTRAPMENT WARNING SIGN
1500 LA Installation and Programming
MX4725 Rev. C ©2022
1500 LA
Installation and Programming Manual
SECTION 9:
BATTERY CHARGING OPTIONS: AC & SOLAR
The control board is powered once the actuator(s) harness battery wires are connected to the 12 VDC battery
(see INSTRUCTIONS 8A and 8B), but the battery itself must be recharged using either a battery charging device or solar panel(s).
• If AC electrical power will be run to the control box to allow the use of an AC-DC charger to recharge the battery, refer to wiring and safety information below. See INSTRUCTION 10 for AC-DC charger information.
• If solar panels are used, refer to INSTRUCTIONS 11A and 11B.
9.1 120VAC ELECTRICAL WIRING AND SAFETY
CAUTION!
DO NOT WIRE AC POWER TO
THE CONTROL BOARD! THE
CONTROL BOARD OPERATES ON
DC POWER ONLY!
DANGER!
TO REDUCE THE RISK OF SEVERE
INJURY AND DEATH FOLLOW ALL
SAFETY PROCEDURES!
DANGER!
DO NOT WIRE AC MAINS
POWER TO METAL CONTROL
BOX WITHOUT EARTH GROUND
CONNECTION!
•
Disconnect power to the gate operator by manually opening its dedicated circuit breaker before making any mechanical or electrical adjustments.
•
Use a 20 amp dedicated circuit breaker for each installed gate operator.
•
Open dedicated circuit breaker supplying power to gate operator before a new installation or making any modifi cations to an existing installation of this gate operator.
•
All wiring connections must be made by a qualifi ed individual.
• Run individual circuits in separate U.L. Listed conduits.
Do not combine high voltage (120vac) power wiring and low voltage (+12vdc to +24vdc) control wiring in the same conduits.
IF AC POWER IS BEING RUN INTO THE CONTROL
BOX FOR CONVERSION TO DC,
IT IS RECOMMENDED
THAT THE GATE OPERATOR SYSTEM SHOULD BE
GROUNDED THROUGH THE EARTH GROUND IN
THE AC MAINS WIRING SYSTEM (GREEN WIRE).
This ground connection will prevent dangerous currents from appearing on the metal control box, the actuator, or the gate itself.
Nice recommends an 8 foot copper rod driven all the way into the ground with a copper clamp and 12ga copper wire minimum.
Connect ground wire to the control box by drilling a hole in the control box, removing the powder coating around the hole, and bonding the copper ground wire to that area with a bolt.
support.hysecurity.com
1500 LA Installation and Programming
1500 LA
Installation and Programming Manual
9.2
HIGH VOLTAGE WIRE GAUGE REQUIREMENTS
Use Table 9-1, below, to determine high voltage wire size requirements. Distance shown in the chart is measured from the operator to the power source. If power wiring is greater than the maximum distance shown, a service feeder is recommended. When large gauge wire is used, a separate junction box must be installed for the operator connection.
Wire table is based on stranded copper wire. Wire run calculations are based on a 110 VAC power source with a 3% voltage drop on the power line, plus an additional 10% reduction in distance to allow for other electrical losses in the system.
110V/AWG GAUGE
MAX RUN
TABLE 9-1: MAXIMUM RUN PER WIRE GAUGE
14
180 FT
(54.8m)
12
280 FT
(85.3m)
10
460 FT
(140m)
8
700 FT
(213.3m)
6
1150 FT
(350.5m)
4
1800 FT
(548.6m)
9.3
AC-TO-DC CHARGER CONNECTIONS
Nice off ers an AC-DC battery charger (P/N 404c) as shown in IMAGE 10-1. If using a diff erent charger, refer to the manufacturers instructions for installation.
10
CONNECT AC-DC CHARGER TO BATTERY
1.
Attach the battery cables from the charger (IMAGE 4-1) to the battery terminals; red to positive (+) and black to negative (-).
2.
Plug the charger into an appropriate AC source (see previous page for AC power safety warnings).
IMAGE 10-1: AC-TO-DC BATTERY CHARGER (P/N 404C)
1500 LA Installation and Programming
MX4725 Rev. C ©2022
1500 LA
Installation and Programming Manual
9.4 SOLAR PANEL CONNECTIONS
11A
SOLAR PANEL CONNECTION - UP TO 10W
Any solar panel rated at 10W (watts) or smaller, may be installed directly to the battery as follows:
1.
Assemble solar panel mounting bracket and panel with included hardware.
2.
Locate solar panel out of shadows of surrounding buildings, walls, etc. and orient to collect the maximum sunlight energy throughout the year. In the northern hemisphere, mount panels at upward angle of about
45 degrees with panel oriented south. In the southern hemisphere orient the panel to face north.
3.
Connect battery lugs directly to the battery (red wire to positive and black wire to negative).
NOTE:
For all solar panels rated above 10 Watts, an external charge regulator must be used. Nice off ers a regulator (P/N SG-4) for this purpose. See INSTRUCTION 11B for installation instructions for the SG-4 regulator.
support.hysecurity.com
1500 LA Installation and Programming
1500 LA
Installation and Programming Manual
11B
SOLAR PANEL CONNECTION - ABOVE 10 WATTS
Solar panels rated above 10W must
be connected to a charge regulator, which in turn then connects to the battery to enable battery charging. Nice off ers a regulator (P/N SG-4) for this purpose. For other regulators, follow the manufacturers instructions. Connect any solar panel above 10W using the SG-4 regulator as follows:
1.
Assemble solar panel mounting bracket and panel with included hardware.
2.
Locate solar panel out of shadows of surrounding buildings, walls, etc. and orient to collect the maximum sunlight energy throughout the year. In the northern hemisphere, mount panels at upward angle of about
45 degrees with panel oriented south. In the southern hemisphere orient the panel to face north.
3.
Drill two holes into a vertical surface in the CBOX chassis matching the two mounting tabs on the regulator. Mount the SG-4 with appropriate hardware to fi x it in place.
CAUTION! Do not attach wires to battery until until STEP 5.
4. Connect:
•
Solar panel RED wire to regulator YELLOW wire.
•
Solar panel BLACK wire to either
regulator BLACK wire.
•
Battery cable RED wire (positive) to regulator RED wire.
•
Battery cable BLACK wire (negative) to other regulator BLACK wire.
5.
Attach both battery lugs to the battery (red to positive and black to negative).
NOTES:
•
Wire-to-wire connections may use wire nuts, crimp caps, or butt connectors, as long as the connections are secure .
•
It is permissible to cut off 8” to 10” (or so) of the solar panel wires (with battery lugs) in order to use for attaching the regulator to the battery.
•
The SG-4 prevents reverse current leakage at night, so a blocking diode is not required in the system.
•
A negative earth ground at the battery is recommended for most eff ective lightning protection.
•
The SG-4 can be mounted outdoors, but do not expose to ambient temperatures above 140˚F (60˚C).
•
Ensure that water is able drain from inside the case if it becomes wet.
SOLAR PANEL
RED
BLACK
SOLAR
+
YELLOW
S O L A R C O N T R O L L E R
RATED 4.5A 12V
Made in Sing apore
SOLAR
–
BLACK
BATTERY BATTERY
12 V
–
BLACK
12 V
+
RED
RED
BLACK
NEG
-
POS
+
BATTERY
IMAGE 11B-1: P/N SG-4 SOLAR PANEL REGULATOR WIRING
1500 LA Installation and Programming
MX4725 Rev. C ©2022
1500 LA
Installation and Programming Manual
9.5 SETTING OPEN/CLOSE LIMITS
12A
SETTING MASTER GATE OPEN/CLOSE LIMITS
REMOVE LIMIT
SWITCH END CAPS
EXTEND LIMIT
SCREW
RETRACT
LIMIT SCREW
IMAGE 12A-1: 816 ACTUATOR LIMIT SWITCH LOCATIONS
636
CONTROL
BOARD
OPEN/STOP/CLOSE
GATE BUTTON
CONTROL BOX
(SIDE PANEL REMOVED)
IMAGE 12A-2: OPEN/STOP/CLOSE BUTTON LOCATION ON CBOX636 (SIDE VIEW)
DETAIL
LED ENABLE BUTTON support.hysecurity.com
MASTER OPEN LIMIT LED
MASTER CLOSE LIMIT LED
SLAVE OPEN LIMIT LED
SLAVE CLOSE LIMIT LED
IMAGE 12A-3: OPEN/CLOSE LIMIT LEDS ON 636 CONTROL BOARD
(Continued)
1500 LA Installation and Programming
1500 LA
Installation and Programming Manual
12A: SET MASTER GATE OPEN/CLOSE LIMITS (CONT.)
(Continued)
After connection of actuator and battery leads, the gate should now open or close when the black button on the control box (see FIGURE 12A-2) is pressed.
NOTE:
For dual gate installations, leave the SLAVE actuator disconnected until after the MASTER actuator has been limit adjusted. See INSTRUCTION 6B for SLAVE adjustment instructions.
1.
Remove the cap(s) from the limit screws on the actuator (IMAGE 12A-1).
2.
With the gate in the closed position depress the LED ENABLE button on 636 board (IMAGE 12A-3).
You should see the MASTER CLOSE limit LED illuminate.
3.
Using the black button on the side of the control box (IMAGE 12A-2), cycle the operator to the open position. If the actuator does not stop before reaching the fully open position depress the black button to stop the motor in the desired open position.
4.
Adjust the retract (pull to open) or extend (push to open) limit as shown on previous page. Turn the limit screw until the MASTER OPEN limit LED illuminates (while holding the LED enable button).
•
EXTEND more: Turn the limit screw counterclockwise
•
EXTEND less: Turn the limit screw clockwise
•
RETRACT more: Turn the limit screw clockwise
•
RETRACT less: Turn the limit screw counterclockwise
5.
If installing a dual gate system, proceed to INSTRUCTION 12B. If installing a single gate confi guration, proceed to INSTRUCTION 13.
12B
SETTING SLAVE GATE OPEN/CLOSE LIMITS
1.
After following instructions in INSTRUCTION 12A for adjusting limit switch of the MASTER actuator, follow the steps below to set the SLAVE gate actuator.
2.
Once the MASTER gate actuator is set, disconnect it from board and plug the SLAVE gate harness into the MASTER side of the circuit board.
3.
Follow the same steps to set the limit for the SLAVE as done for the MASTER actuator.
4.
Once both actuators are set, plug the MASTER gate actuator into the master connector on the board and SLAVE gate actuator into the slave connector on the board.
5. Proceed to INSTRUCTION 13.
1500 LA Installation and Programming
MX4725 Rev. C ©2022
1500 LA
Installation and Programming Manual
9.6 RECEIVER/TRANSMITTER INSTALLATION & PROGRAMMING
13
INSTALL 318N RECEIVER AND ANTENNA
IMAGE 13-1: 318N RECEIVER
1.
Install the 318N radio receiver (IMAGE 13-1) inside the control box (hardware not included), ensuring that receiver harness is able to reach the 636 control board.
2.
Refer to IMAGE 13-2 and remove the empty connector at J1.
3.
Plug the radio harness connector into the vacant J1 connector (IMAGE13-2).
TO J1
TIMER TO CLOSE
TIMER TO CL OSE OPT.
AVE DISABLE
MAX RUN TIMER OPT
MAX RUN TIMER VAL
“STOP” CI
OSE OPT.
SLAVE DISABLE
MASTER DISABLE
A
T
TIMER
O CL OSE
CURRENT
SENSITIVIT Y
HARNESS FROM 318N
RADIO RECEIVER
M
CLOSE
SL AVE
SL
CL
A VE
OSE
EMER GENC
MOMENT
Y BY
Y USE ONLY Y
IMAGE 13-2: 318N RECEIVER TO 636 CONTROL BOARD CONNECTION
4.
Remove connector from antenna cable with small screwdriver, mount antenna outside control box, route cable into control box, strip/twist both wire & shielding, then install shield into terminal
1 and wire into terminal 2 of receiver terminal strip, as shown in IMAGE 13-3.
318N RECEIVER TERMINAL STRIP
12VDC
318N
318N WIRE HARNESS TO 636
WIRE COLOR 636
TERM. 1 RED 12VDC
RELAY 2
TERM. 2
TERM. 3
BLACK
GREEN
GND
ANTENNA TERM. 4 BLUE or WHITE INPUT
RELAY 1
IMAGE 13-3: 318N RECEIVER TERMINAL WIRING AND FUNCTIONS
NOTE:
To control another gate or device in close proximity using the second relay, connect wires from activation terminals of second operator or device to terminals 5 and 6 of the 318N receiver. support.hysecurity.com
1500 LA Installation and Programming
1500 LA
Installation and Programming Manual
14
PROGRAMMING TRANSMITTERS FOR 318N
1.
Remove receiver cover by squeezing the top two tabs and lifting off cover (IMAGE 14-1).
IMAGE 14-1: REMOVE 318N RECEIVER COVER
2. Press and release the
Yellow Learn Button on the receiver (IMAGE 14-2).
RED LED YELLOW LEARN BUTTON
IMAGE 14-2: 318N LEARN BUTTON AND LED LOCATIONS
3.
The red LED next to the learn button will turn on and stay on for 5 seconds.
4.
While the red LED of the receiver is on, press and hold either button on your 2 button transmitter until the LED on the receiver turns off .
5.
When the red LED on the receiver turns off , release the transmitter button and immediately press and release the same transmitter button again.
6.
The red LED on the receiver will fl ash 3 times indicating the transmitter is programmed.
7.
Repeat these steps for programming additional transmitters.
8.
By default, after programming the transmitter(s), button 1 will control relay 1 and button 2 will control relay 2.
1500 LA Installation and Programming
MX4725 Rev. C ©2022
1500 LA
Installation and Programming Manual
15
DELETING SINGLE TRANSMITTER FROM MEMORY
1.
Press and hold the yellow learn button (IMAGE 14-2) for 3 seconds.
2.
When the LED turns off , release the yellow button.
3.
Press and hold either transmitter button (of the transmitter to be deleted) until the LED turns off , release the transmitters button and immediately press the same button again.
4.
The LED fl ashes 1 time to confi rm the transmitter has been deleted.
16
DELETING ALL TRANSMITTERS FROM MEMORY
1.
Press and hold the yellow learn button of the receiver (IMAGE 14-2), the LED will turn on and after 3 seconds turn off , then start to fl ash.
2.
Release the yellow button on exactly the 3rd fl ash.
3.
As soon as the LED turns back on, press the yellow learn button and release as soon as the LED turns back off .
support.hysecurity.com
1500 LA Installation and Programming
1500 LA
Installation and Programming Manual
SECTION 10: 636 CONTROL BOARD FEATURES
10.1 EMERGENCY BYPASS CONNECTOR
17
USING THE EMERGENCY BYPASS CONNECTOR
The emergency bypass connector is used to open the gate(s) even if the control box open/close gate button is locked. Instructions for use are as follows:
1.
Unplug the motor harness from the Master (or Slave) Connector and momentarily insert into the
Emergency Bypass Connector to open the gate.
NOTE:
Using the emergency bypass connector only applies motor power to the actuator(s) to open the gate(s), with no limit function, closing function, or other setting options.
2.
Make sure to unplug the connector from the emergency bypass before the gate fully opens and binds.
3.
In the event the motor is not disconnected quickly enough, the blue 15 amp fuse (see IMAGE 17-
1) will protect the circuit board from damage and should be replaced when the original problem is fi xed.
EMERGENCY BYPASS FUSE
EMERGENCY BYPASS
CONNECTOR
IMAGE 17-1: EMERGENCY BYPASS CONNECTOR AND FUSE LOCATIONS
1500 LA Installation and Programming
MX4725 Rev. C ©2022
1500 LA
Installation and Programming Manual
10.2
636 CONTROL BOARD CONTROLS, SWITCHES, & FUSES
12 VDC
ACCESSORY
FUSES: 3A
EMERGENCY
BYPASS
FUSE: 15A
DIP SWITCH (SETTINGS)
See next page.
ACCESSORY INPUT LEDS
TIMER TO CLOSE ADJUSTMENT
CURRENT SENSITIVITY
LED ENABLE BUTTON
Enables LEDs for limit setting and troubleshooting (must be depressed to observe LEDs).
OPEN/CLOSE LIMIT LEDS
(when lit)
MASTER OPEN = Primary OPEN limit.
MASTER CLOSE = Primary CLOSE limit.
SLAVE OPEN = Secondary OPEN limit.
SLAVE CLOSE = Secondary CLOSE limit.
NOTE:
In single gate confi gurations, a jumpered connector is installed at the
SLAVE connector, which will cause both
SLAVE LEDs to light up when the LED
ENABLE BUTTON is pressed.
12 VDC
ACCESSORY
FUSE: 3A
FIGURE 10-1: 636 CONTROL BOARD CONTROLS, SWITCHES, & FUSES
TIMER TO CLOSE ADJUSTMENT
Rotate clockwise to increase time before gate closes, and counter-clockwise to decrease time before gate closes. If program switch #3 is on, the gate must activate the open limit switch in order for the timer to close to operate.
CURRENT SENSITIVITY
Rotate clockwise to decrease sensitivity (more force) and counter-clockwise to increase sensitivity (less force).
WARNING:
The current sensitivity should be adjusted to prevent injury in the event of someone being entrapped in the gate. This feature should be periodically tested to assure proper operation. Refer to SAFETY
PRECAUTIONS in SECTION 3.
ACCESSORY INPUT LEDS
A lit red LED to the right of an accessory input indicates that the accessory is connected and functioning.
support.hysecurity.com
1500 LA Installation and Programming
1500 LA
Installation and Programming Manual
10.3
DIP SWITCH SETTINGS
FACTORY
SETTINGS
DIP SWITCH SETTINGS
1 - TIMER TO CLOSE - Automatically closes gate
• ON - Close timer enabled
• OFF - Close timer disabled (FACTORY)
OFF
OFF
2 - CURRENT SENSITIVITY OPTION - Delays current sensing from start up
• ON - 4 second delay
• OFF - 2 second delay (FACTORY)
ON
OFF
OFF
OFF
ON
ON
OFF
3 - TIMER TO CLOSE OPTION
•
ON - timer to close works only when open limit switch is activated
(FACTORY)
•
OFF - timer to close works from any open gate position
4 - SLAVE DISABLE
•
ON - disables slave side of dual board
•
OFF - enables slave side of dual board (FACTORY)
5 - MASTER DISABLE
•
ON - disables master side of dual board
•
OFF - Enables master side of dual board (FACTORY)
6 - MAXIMUM RUN TIMER OPTION
•
ON - stops and reverses gate if run timer times out before closing
•
OFF - stops gate if run timer times out before closing (FACTORY)
7 - MAXIMUM RUN TIMER VALUE
• ON - 40 seconds (FACTORY)
• OFF -20 seconds
8 - TIMER TO CLOSE VALUE
• ON - 20 to 70 seconds (adjustable) (FACTORY)
• OFF - 10 to 35 seconds (adjustable)
9 - OPEN, STOP, CLOSE CONTROL ENABLE
•
ON - allows for open, stop, close unit (optional) to operate gate
•
OFF - normal operation (If 9 is on, terminals 4 & 5 must be normally closed for proper operation.) (FACTORY)
1500 LA Installation and Programming
MX4725 Rev. C ©2022
1500 LA
Installation and Programming Manual
10.4 ACCESSORY CONNECTORS
A number of accessory inputs are provided on the 636 control board as shown below:
GND
GND
INP
INP
12V
GND - Supplied Battery Ground
J1 INPUT - Step by Step activation
12V - Supplied battery voltage (protected with 3AMP fuse)
GND
INP
12V
GND - Supplied Battery Ground
J2 INPUT - Step by Step activation
12V - Supplied battery voltage (protected with 3AMP fuse)
3
4
5
1
2
6
7
EDGE
EDGE
GND
GND
STOP
CLOSE
OPEN
EDGE - Reverse edge input. Stop and reverse gate if closing, resets close timer if gate open.
EDGE - Reverse edge input. Stop and reverse gate if closing, resets close timer if gate open.
GND - Supplied Battery Ground
GND - Supplied Battery Ground
STOP - Stop input from a 3 button station
CLOSE - Close input from a 3 button station
OPEN - Open input from a 3 button station
10
11
12
8
9
13
14
GND
GND
GND - Supplied Battery Ground
GND - Supplied Battery Ground
FREE EXIT FREE EXIT - Opens gate if closed, stops and reverses gate if closing, resets close timer if gate is open.
GND
SHADOW
GND
SAFETY
GND - Supplied Battery Ground
SHADOW - Resets close timer when gate is open (also referred to as under gate loop)
GND - Supplied Battery Ground
SAFETY - Resets close timer if gate is open, stops and reverses if gate is closing.
Does not open a closed gate.
support.hysecurity.com
1500 LA Installation and Programming
1500 LA
Installation and Programming Manual
SECTION 11: APPENDIX
11.1 CALCULATING SOLAR REQUIREMENTS
18
CALCULATING SOLAR REQUIREMENTS
1.
Estimate gate traffi c measured in open/close cycles per the
Watt/Cycle Chart
below and refer to the notes.
DAILY CYCLES
5 Watt Solar Panel
10 Watt Solar Panel
SOLAR PANEL WATT/CYCLE CHART
15 Watt Solar Panel
(requires regulator)
20 Watt solar Panel
(requires regulator)
30 Watt Solar Panel
(requires regulator)
40 Watt
Solar Panel (requires regulator)
1.5 Amp
Battery Charger
10 Amp
Battery Charger
1-10 1-20 1-30 1-40 1-60 1-80
80+ x x x x x x x x
NOTES:
• The Solar Panel Watt/Cycle Chart is only a guide. Other gate operator confi gurations may reduce or increase the daily power usage.
•
For all solar panels rated above 10 Watts, an external charge regulator must be used.
•
For dual gate operators, double the amount of required solar wattage.
•
If a standard electrical outlet is not available for trickle charging, a licensed electrician will be required for proper electrical hookup.
2.
Estimate the amount of sunlight available per the
Solar Map at right.
3.
Use the solar wattage c a l c u l a t o r f o u n d o n t h e H y S e c u r i t y w e b s i t e a t h t t p s : / / s u p p o r t . h y s e c u r i t y.
c o m / h c / e n - u s / articles/360057403914 to determine battery and solar panel size needed to serve the installation in question.
1500 LA Installation and Programming
MX4725 Rev. C ©2022
1500 LA
Installation and Programming Manual
11.2
MAINTENANCE SCHEDULE
MAINTENANCE SCHEDULE
Maintenance Action
BATTERY
EMERGENCY
BYPASS
Check the batteries for any leakage or loose connections. It is recommended that batteries be replaced every two years.
Check emergency bypass function for proper operation. See SECTION 10.1 for more information.
GATE
Inspect for damage.
LOOP(S)
Check vehicular reverse and shadow loops for proper operation.
MOUNTING
HARDWARE
Check screws and nuts.
PHOTO
EYES
Use a hand held cylinder (approx. 2” [5cm] diameter and 12” [30cm] in length) and pass between photo eye line of sight. Pass cylinder through line of sight near transmitter, pass cylinder through line of sight near receiver, pass cylinder through line of sight halfway between transmitter and receiver. Gate should stop and reverse on detection.
Check for humidity, oxidation, and foreign bodies (such as insects) and remove from chassis. Clean housings and front plate. Do not use alcohol, benzene, abrasives or other cleaning products. Use only a slightly dampened soft cloth to clean transmissive panels or lenses.
6
Months
x x x x
Annually
x x x x x x support.hysecurity.com
1500 LA Installation and Programming
1500 LA
Installation and Programming Manual
11.3
SYSTEM TROUBLESHOOTING
Problem
Gate opens a short distance, then stops and reverses.
SYSTEM TROUBLESHOOTING
Possible Solution
•
Check the UL/Edge input on the gate controller.
•
Ensure limit LEDs are functioning properly.
•
Check for obstructions.
•
Adjust Force Settings.
Gate opens but will not close.
•
Check the input LEDs. Any ON will hold the gate open and indicates a problem with a keying device. Exception is “STOP”.
•
Check limit LEDs. Check limits for failures. Replace as necessary.
•
Check the loop detectors. Any activated safety devices can hold the gate open and indicates a problem with the loop detector or ground loop.
Gate opens by itself.
Check accessory inputs and clear them as necessary.
636 status LEDs will not light up.
Check battery voltage and replace if necessary.
Gate moves in direction opposite expected.
Reverse the actuators Red and Black motor wires connected to the 636 control board.
Open limit LED glows when gate is closed, and close limit LED glows when gate is open.
Reverse the actuators Orange and White encoder wires connected to the
636 control board.
1500 LA Installation and Programming
MX4725 Rev. C ©2022
1500 LA
Installation and Programming Manual
11.4
INSTALLATION CHECKLIST
•
The installer and customer must each ensure that all of the following actions have been completed.
•
Left box is for installer check off and the right box is for customer check off .
INSTALLATION CHECKLIST
� �
The gate has been checked to make sure it is level and moves freely in both directions.
� �
Potential pinch areas have been guarded so as to be inaccessible.
� �
� �
If pedestrian traffi c is expected, a separate pedestrian gate has been installed, a minimum of seven feet from the gate. The customer has been informed that all pedestrian traffi c must use the pedestrian gate.
� � Warning signs have been installed on each side of the gate in highly visible locations. The customer has been informed that these signs must remain at all times.
� �
There are no controls installed within 6 feet of the gate.
The installer has properly adjusted the obstruction sensing feature and has tested the gate to make sure that the gate stops and reverses a short distance with minimal resistance applied (Approximately
40 lbs. on a swing gate, at the end of the gate.
� �
� �
� �
The installer has instructed the customer in the proper use of the gate operator and reviewed all of the operational functions, obstruction sensing devices, warning beeper and reset, etc.
The installer has instructed the customer in the proper way of disconnecting the operator. Manual disconnect must never be used while the gate is in motion. The power must be turned off and battery disconnected before disengaging the operator.
The installer has reviewed all safety instructions with the customer, and has left the safety instructions and owner’s manual for their reference.
� � The installer has answered any questions the customer has regarding the operation of the gate operator and gate operator safety precautions.
� � The installer has explained to the customer that a regular maintenance schedule for both the gate and the gate operator is recommended.
� � The installer has given any keys for the control box to the customer and explained how to manually open the gate in the event of a loss of power.
support.hysecurity.com
1500 LA Installation and Programming
1500 LA
Installation and Programming Manual
11.5 PART DRAWINGS
2 8.3
22 18.
1500 LA Installation and Programming
MX4725 Rev. C ©2022
1500 LA
Installation and Programming Manual support.hysecurity.com
1500 LA Installation and Programming
4 5.7
1500 LA
Installation and Programming Manual
8 7.3
4.0
66 Ø1.
1500 LA Installation and Programming
MX4725 Rev. C ©2022
1500 LA
Installation and Programming Manual support.hysecurity.com
1500 LA Installation and Programming
1500 LA
Installation and Programming Manual
1500 LA Installation and Programming
MX4725 Rev. C ©2022
1500 LA
Installation and Programming Manual
SECTION 12: WARRANTY
1. Warranty.
HySecurity Gate, Inc. (“HySecurity”) warrants that at the �me of sale each
HySecuritybranded product that it sells will, in all material respects, conform to its then applicable specifica�on and will be free from defects in material and manufacture.
The following addi�onal dura�onal warran�es apply to HySecurity products, depending on whether (1) the product is purchased through an authorized
HySecurity distributor and (2) whether a �mely and complete product registra�on is submited to HySecurity.
It is therefore important that you register your product with HySecurity, online at www.hysecurity.com/warranty , within the 60-day period described below.
1(a) HySecurity Products Purchased Through Authorized Distributors and Properly
Registered
For any gate operator product that is purchased from an authorized HySecurity distributor (this excludes product purchased through internet resellers or any distributor not authorized by HySecurity), if the product registra�on is completed by the Dealer/Installer or End User within 60 days of the date of purchase, the following wa rranty terms will apply. HySecurity warrants that the product will remain serviceable for the following periods: a) Hydraulic industrial gate operator hydraulics, controls, and mechanical components: Five Years or 500,000 gate cycles (whichever occurs first) a�er the date of installa�on, b) Hydraulic wedge operator hydraulics and controls: Five Years or 500,000 cycles
(whichever occurs first) a�er the date of installa�on. Wedge mechanical components: Two Years a�er the date of installa�on, c) Electromechanical pad-mounted Slide and Swing operators: Five Years or
500,000 cycles (whichever occurs first) a�er the date of installa�on, except single family residen�al usage, where the warranty term shall be Seven Years a�er the d ate the product was shipped from HySecurity, d) Electromechanical linear actuator Swing operators: Two Years a�er the date of installa�on , e) Electromechanical surface mount wedge operator electronics: Two Years or
500,000 gate cycles (whichever occurs first), a�er the date of installa�on, f) Electromechanical Barrier Arm Operators: Two years or 1,000,000 gate cycles
(whichever occurs first) a�er the date of installa�on, provided that the preceding Five Year warranty period in (a), (b) , and (c) will n ot extend beyond seven years from the date that the product was shipped from
HySecurity, and the Two Year warranty period in (b), (d) , (e), and (f ) will not extend beyond four years from the date that the product was shipped from HySecurity.
The preceding warranty dura�ons do not apply to the products or components described below ( g-j), which have a shorter warranty period : g) Hydraulic gate operator drive wheels , including XtremeDrive™ wheels and rack:
Two Years from date of installa�on.
h) AC and DC power supplies, chargers , and inverters and HyNet™ Gateway: Two
Years from date of installa�on, except bateries.
i) Bateries: One Year from date of shipment from HySecurity.
j) Components subject to normal wear including, but not limited to, chains, belts, idler wheels, sprockets and fuses: One Year from date of installa�on.
1(b) HySecurity Products Not Purchased Through an Authorized Distributor or Not
Properly Registered within 60 Days
For any product that is not purchased from an authorized HySecurity distributor or for which the product registra�on was not completed by the Dealer/Installer/End
User within sixty (60) days of the date of purchase, the following warranty will apply:
HySecurity warrants that the product will remain serviceable for the following periods, which begin on the date that the product was shipped from HySecurity: a) All gate operators: One Year or 100,000 gate cycles , whichever comes first.
b) AC and DC power supplies, chargers , or inverters: One Year.
c) HyNet™ Gateway: One Year.
d) Hydraulic gate operator drive wheels: One Year.
1(c) Replacement Parts
HySecurity warrants that replacement parts (whether new or recondi�oned) will remain serviceable for One Year from the date that the part was shipped from
HySecurity or the remaining period of the Gate Operator warranty, whichever is longer.
1(d) Limita�ons and Exclusions Applicable to Each of the Preceding Warran�es.
The preceding warran�es shall not apply to equipment that has been (1) installed, maintained, or used improperly or contrary to instruc�ons; (2) subjected to negligence, accident, vandalism, or damaged by severe weather, wind, flood, fire,
HySecurity Warranty D0317 Revised 032919
WARRANTY
6705 S 209 th St, Ste 101
Kent, WA 98032
800-321-9947 www.hysecurity.com
terrorism or war; or (3) damaged through improper opera�on, maintenance, storage or abnormal or extraordinary use or abuse. Any modifica�on made to products will void the warranty unless the modifica�ons are approved in wri�ng by HySecurity in advance of the change (this exclusion does not apply to normal installa�on of approved accessories and/or protec�ve devices or sensors). It is the responsibility of the Distributor, Dealer/Installer, or End User to ensure that the so�ware version in the product is maintained to the latest revision level.
The preceding warran�es do not extend to accessories when those items carry another manufacturer’s name plate and they are not a part of the base model.
HySecurity disclaims all warran�es for such accessory components, which carry only the original warranty, if any, of their original manufacturer. HySecurity hereby assigns its rights under such manufacturer warran�es —to the extent that such rights are assignable — to Buyer.
The se warran�es extend to HySecurity’s Distributors, to the Dealer/Installer, and to the first End User of the product following installa�on. They do not extend to subsequent purchasers.
2. Exclusion of Other Warran�es.
The warran�es contained in Sec�on 1 are the exclusive warran�es given by
HySecurity and supersede any prior, contrary or addi�onal representa�ons, whether oral or writen. Any prior or extrinsic representa�ons or agreements are discharged or nullified. HYSECURITY HEREBY DISCLAIMS AND EXCLUDES ALL OTHER
WARRANTIES— WHETHER EXPRESS, IMPLIED, OR STATUTORY — INCLUDING ANY
WARRANTY OF MERCHANTABILITY , ANY WARRANTY OF FITNESS FOR A
PARTICULAR PURPOSE , ANY LIABILITY FOR INFRINGEMENT, AND ANY WARRANTIES
OTHERWISE ARISING FROM COURSE OF DEALING, COURSE OF PERFORMANCE, OR
USAGE OF TRADE.
3. Buyer’s Exclusive Remedies for Any Nonconformity.
If a HySecurity product fails to conform to the warran�es in Sec�on 1, Buyer must no�fy and order replacement parts from the Distributor through which the produ ct was purchased within a reasonable �me and in no event more than thirty (30) days a�er the discovery of the nonconformity. HySecurity will inves�gate and, in the event of a breach, will provide, within a reasonable period of �me, one of the following:
(1) repair or replacement of any nonconforming products or components or
(2) refund of the price upon return of the nonconforming items. HySecurity reserves the right to supply used or recondi�oned material for all warranty claims. HySecurity will not be considered to be in breach of or default under this Warranty because of any failure to perform due to condi�ons beyond its reasonable control, including any force majeure. This warranty does not cover any incidental expenses, including fines or penal�es, temporary security, labor, shipping, travel �me or standby �me that are incurred for inspec�on or replacement of any nonconforming items. As a condi�on of warranty coverage, warranty claims must be submited in accordance with the procedures describ ed on the HySecurity form, “RMA Procedures.”
THE REMEDY SELECTED BY HYSECURITY IN ACCORDANCE WITH THIS PARAGRAPH
SHALL BE THE EXCLUSIVE AND SOLE REMEDY OF BUYER FOR ANY BREACH OF
WARRANTY.
4. Exclusion of Consequen�al and Incidental Damages.
HYSECURITY SHALL NOT BE LIABLE FOR ANY INCIDENTAL, SPECIAL, OR
CONSEQUENTIAL DAMAGES, WHETHER RESULTING FROM NONDELIVERY OR FROM
THE USE, MISUSE, OR INABILITY TO USE THE PRODUCT OR FROM DEFECTS IN THE
PRODUCT OR FROM HYSECURITY’S OWN NEGLIGENCE. This exclusion applies regardless of whether such damages are sought for breach of warranty, breach of contract, negligence, or strict liability. This exclusion does not apply to claims for bodily injury or death.
5. Severability.
If any provision of this warranty i s found to be invalid or unenforceable, then the remainder shall have full force and effect.
6. Proprietary Rights.
HySecurity retains and reserves all right, �tle, and interest in the intellectual property rights of its products, including any accompanying proprietary so�ware. No ownership of any intellectual property rights in the products or accompanying so�ware is transferred to Distributor, Dealer/Installer , or End User.
7. Applicable Law.
This warranty will be interpreted, construed, and enforced in all respects in accordance with the laws of the State of Washington, without reference to its choice of law principles. The U.N. Conven�on on Contracts for the Interna�onal Sale of
Goods will not apply to this warranty.
Page 1 of 1 support.hysecurity.com
1500 LA Installation and Programming
1500 LA
Installation and Programming Manual
(Page intentionally blank)
1500 LA Installation and Programming
MX4725 Rev. C ©2022
NAME
Curtis Harvey
Curtis Harvey
1500 LA
Installation and Programming Manual
DOCUMENT REVISIONS
DESCRIPTION OF CHANGE
Rev-B: Revised wattage ranges/instructions for solar panel to battery
& inverter wiring, rebranded, replaced cover, upated warranty, revised solar calc page, and updated fonts.
Rev-C: Changed DIP Switch illustration on page 37 to show Dip
Switch 1 as OFF (not ON) to match text per DCR 331.
INSTALLATION INFORMATION AND SIGN-OFFS
DATE
11/23/2021
11/30/2022
Installation Acceptance
Address where opener is located
Installer name, number and address
End user name and telephone number
Contact Information:
Visit https://hysecurity.com/technical-support/
for installation manuals, replacement part instructions, part diagrams and more.Qualifi ed HySecurity distributors are experienced and trained to assist in resolving installation problems. For the name of a qualifi ed distributor near you, call HySecurity at 800-321-
9947. *Before contacting your distributor or HySecurity Technical Support, obtain the serial number of your operator.
support.hysecurity.com
1500 LA Installation and Programming
advertisement
Related manuals
advertisement