Primera 1200W, 1600B, 2000W Installation & Maintenance Manual
Add to my manuals
31 Pages
Primera 1200W is a powerful and efficient water heater designed to provide a constant supply of hot water for your home. With a capacity of 1200 watts, it can quickly heat water to the desired temperature and maintain it for extended periods. The Primera 1200W is equipped with advanced safety features, including a high-temperature limit control and freeze protection, ensuring safe and reliable operation. Its compact size and easy installation make it suitable for any home or business.
advertisement
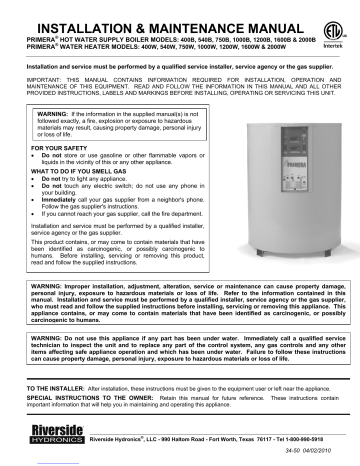
INSTALLATION & MAINTENANCE MANUAL
PRIMERA
PRIMERA
®
®
HOT WATER SUPPLY BOILER MODELS: 400B, 540B, 750B, 1000B, 1200B, 1600B & 2000B
WATER HEATER MODELS: 400W, 540W, 750W, 1000W, 1200W, 1600W & 2000W
Installation and service must be performed by a qualified service installer, service agency or the gas supplier.
IMPORTANT: THIS MANUAL CONTAINS INFORMATION REQUIRED FOR INSTALLATION, OPERATION AND
MAINTENANCE OF THIS EQUIPMENT. READ AND FOLLOW THE INFORMATION IN THIS MANUAL AND ALL OTHER
PROVIDED INSTRUCTIONS, LABELS AND MARKINGS BEFORE INSTALLING, OPERATING OR SERVICING THIS UNIT.
WARNING: If the information in the supplied manual(s) is not followed exactly, a fire, explosion or exposure to hazardous materials may result, causing property damage, personal injury or loss of life.
FOR YOUR SAFETY
Do not store or use gasoline or other flammable vapors or liquids in the vicinity of this or any other appliance.
WHAT TO DO IF YOU SMELL GAS
Do not try to light any appliance.
Do not touch any electric switch; do not use any phone in your building.
Immediately call your gas supplier from a neighbor's phone.
Follow the gas supplier's instructions.
If you cannot reach your gas supplier, call the fire department.
Installation and service must be performed by a qualified installer, service agency or the gas supplier.
This product contains, or may come to contain materials that have been identified as carcinogenic, or possibly carcinogenic to humans. Before installing, servicing or removing this product, read and follow the supplied instructions.
WARNING: Improper installation, adjustment, alteration, service or maintenance can cause property damage, personal injury, exposure to hazardous materials or loss of life. Refer to the information contained in this manual. Installation and service must be performed by a qualified installer, service agency or the gas supplier, who must read and follow the supplied instructions before installing, servicing or removing this appliance. This appliance contains, or may come to contain materials that have been identified as carcinogenic, or possibly carcinogenic to humans.
WARNING: Do not use this appliance if any part has been under water. Immediately call a qualified service technician to inspect the unit and to replace any part of the control system, any gas controls and any other items affecting safe appliance operation and which has been under water. Failure to follow these instructions can cause property damage, personal injury, exposure to hazardous materials or loss of life.
TO THE INSTALLER : After installation, these instructions must be given to the equipment user or left near the appliance.
SPECIAL INSTRUCTIONS TO THE OWNER: Retain this manual for future reference. These instructions contain important information that will help you in maintaining and operating this appliance.
Riverside Hydronics
®
, LLC - 990 Haltom Road - Fort Worth, Texas 76117 - Tel 1-800-990-5918
34-50 04/02/2010
TOPIC
CONTENTS
General Safety Warnings and Codes
Locations and Clearances
Electrical Requirements
Combustion and Ventilation Air
Venting
Outdoor Installation
Gas Supply and Piping
Water Connections and Pipe Size
Maintaining Proper Flow Rate/Temperature Rise
Required: Low Temperature Bypass Loop
Boiler Flow Rate Requirements
Circulator Pump Wiring
General Information
Temperature Setting
Operating Temperature Control
High Water Temperature Limit Control
Freeze Protection
Relief Valve
Water Flow Switch
Remote Connections - Terminal Strip
Boiler Management System (BMS) Connection
Sequence of Operation - Ignition Control
To Turn Gas Off To The Appliance
Lighting Instructions and Safety Warnings
Hot Surface Ignition System
Periodic Maintenance
Heating Boiler System Piping
Water Heater/Hot Water Supply Boiler Piping
Piping Schematics
PAGE
1
4
5
5
6
8
9
11
11
12
13
13
15
16
16
17
18
19
20
20
20
21
23
23
24-30
CHECKING EQUIPMENT BEFORE YOU INSTALL
Inspect the unit completely upon receipt from the freight carrier before signing the bill of lading.
Inspect the appliance and all accompanying parts for signs of impact or mishandling. Verify the total number of pieces shown on packing slips with those actually received. Contact the freight carrier immediately if any damage or shortage is detected.
WARRANTY
Factory warranty does not cover improper installation or operation, which rather than faulty equipment, is the primary cause of most operating problems. (See attached warranty for complete details)
Warranty exclusions include but are not limited to failure or malfunctions resulting from:
1. Failure to properly apply, install, operate, or maintain the appliance in accordance to printed instructions.
2. Abuse, alteration, accident, fire, flood and the like.
3. Sediment or lime buildup, freezing or any other conditions causing inadequate circulation.
4. Corrosive or contaminated atmosphere.
5. A water velocity flow rate exceeding or below the product design flow rate.
Important : This equipment is intended to operate in non-condensing conditions. Inlet water to the
º appliance must not drop below 130 F.
PRODUCT SAFETY INFORMATION
REFRACTORY CERAMIC FIBER PRODUCT WITH CRYSTALLINE SILICA
WARNING : This product contains crystalline silica, which has been identified by the International Agency for Research on Cancer (IARC) as carcinogenic to humans. This product also contains refractory ceramic fibers, which have been identified by the IARC as possibly carcinogenic to humans . Avoid breathing fiber particulates and dust.
RISKS :
Airborne fibrous insulation is a possible cancer hazard by inhalation.
Airborne crystalline silica may cause silicosis (lung disease) by inhalation.
May cause temporary irritation to eyes, skin, and respiratory tract.
PRECAUTIONARY MEASURES :
Minimize airborne fibers with engineering controls.
Use NIOSH/MSHA approved respirators as required (see MSDS).
Wear long sleeved, loose-fitting clothing, eye protection and gloves.
FIRST AID MEASURES : (If any of the irritations listed persists, seek medical attention)
Eyes:
Skin:
Flush with water.
Wash with soap and warm water.
Ingestion: Do not induce vomiting. Get medical attention if gastrointestinal symptoms develop.
Inhalation: Remove to fresh clean air.
WARNING: If you are unfamiliar with the safe handling of refractory ceramic fiber products, or if you wish additional information prior to beginning any disassembly of the water heater or boiler that might expose refractory ceramic fiber materials, contact: Unifrax Corporation, 2351 Whirlpool Street, Niagara Falls, NY 14305-2413, 1-800-322-2293.
IDENTIFICATION OF REFRACTORY CERAMIC FIBER MATERIALS (RCF): The combustion chamber top and bottom utilize
RCF material. (The RCF materials are located within the product and not generally exposed except during service, disassembly or assembly.)
2 34-50 04/02/2010
IMPORTANT SAFETY NOTE
It takes only 5 seconds of skin contact with 140°F water to cause a second degree burn! You must protect against high water temperatures at all lavatories, tubs, showers and other points of hot water contact.
Accidental scalding from high water temperatures is a greater risk in some types of installations. Some examples are:
HOMES FOR THE MENTALLY HANDICAPPED
HOMES FOR THE PHYSICALLY HANDICAPPED
HOSPITALS AND NURSING HOMES
ELDER CARE FACILITIES AND REST HOMES
ORPHANAGES AND CHILD CARE FACILITIES
OTHER INSTALLATIONS - WHERE RESPONSE TO CONTACT WITH HOT
WATER MAY BE SLOWER OR WHERE THE DANGER OF HOT WATER
CONTACT IS GREATER
Thermostatically controlled mixing valves must be used in the design of the potable hot water system.
Potable hot water should be tempered to no more than
110°F when used for bathing or other personal uses.
Good engineering practice mandates the use of thermostatically controlled mixing valves set at 120°F or less to keep the delivered water temperature below scalding temperatures.
3 34-50 04/02/2010
CODES
The equipment shall be installed in accordance with those installation regulations in force in the local area where the installation is to be made. These shall be carefully followed in all cases. Authorities having jurisdiction shall be consulted before installation is made. In the absence of such requirements, the installation shall conform to the latest edition of the National Fuel Gas Code, ANSI
Z223.1. Where required by the authority having jurisdiction, the installation must conform to American Society of Mechanical
Engineers Safety Code for Controls and Safety Devices for Automatically Fired Boilers, No. (CSD-1). All appliances conform to the latest edition of the ASME Boiler and Pressure Vessel Code, Section IV. Where required by the authority having jurisdiction, the installation must comply with the Canadian Association Code, CAN/CSA-B149.1 and/or B149.2 and/or local codes.
Component, Controls and Connection Locations
(Locations May Vary)
LOCATION
These units are suitable for indoor installation and may be suitable for outdoor use with the addition of the optional outdoor venting kit.
1. Locate the unit so that if water connections should leak, water damage will not occur. When such locations are unavoidable, install a suitable drain pan, adequately drained, under the unit. Under no circumstances is the manufacturer responsible for water damage in connection with this unit, or any of its components. The manufacturer’s warranty does not include Water damage.
2. Protect associated electrical components and electrical connections from water (dripping, spraying, rain, etc.) during appliance operation and service.
3. Place the appliance on a level, non-combustible floor. Concrete over wood is not considered non-combustible.
4. Do not install on carpet or other combustible floor coverings.
5. Installation over a combustible floor: Units installed over a combustible floor MUST be provided with a base of hollow clay tile or concrete blocks from 8" to 12" thick and extending 24" beyond the sides. Place the blocks in line so that the holes line up horizontally to provide a clear passage through the blocks. Install 1/2” fireproof millboard with a 20-gage sheet metal cover over the block base. Center the unit on the base. Also follow this procedure if electrical conduit runs through the floor, and beneath the appliance. A field-installed base must meet all local fire and safety code requirements.
6. Outdoor models have special location and clearance requirements (See Outdoor Installation in the Venting section).
SERVICE CLEARANCES
Allow sufficient space to provide adequate clearances on all sides for service and inspection. It is recommended that
24” be provided at the top and front, 14” be provided at the rear and 8” at left and right sides of the appliance for service clearances. Optional equipment may increase the clearance requirements. See the “Combustion and
Ventilating Air” and “Venting” section for appliance vent and inlet air installation and clearance information. Allow sufficient space for installing and servicing connections such as water, gas, vent, combustion air, electrical, pump and other auxiliary equipment.
4 34-50 04/02/2010
CLEARANCES TO COMBUSTIBLE SURFACES
The appliance must not be installed on a combustible floor, on carpet, on other combustible floor coverings or on a non-combustible floor covering combustible material. Minimum 1” clearance must be provided from any appliance or venting surface to adjacent combustible construction.
ELECTRICAL REQUIREMENTS
This appliance is wired for 120-volt service. The appliance, when installed, must be electrically grounded in accordance with the requirements of the authority having jurisdiction or in the absence of such requirements, with the latest edition of the
National Electrical Code ANSI/NFPA No. 70. When the unit is installed in Canada, it must conform to the CAE C22.1,
Canadian Electrical Code, Part 1 and/or Local Electrical Codes.
AMPERAGE DRAW
Model
Total Amps @120VAC
(Includes Water Heater Pump Amp Draw.
Does not include optional boiler pump.)
Appliance Amp Draw @120VAC
(Does Not Include Pump Amp Draw)
Standard Pump Amp Draw @120VAC
(Amp draw for alternate pumps may differ)
Approximately 4
Approximately 4
Approximately 6
Approximately 6
Approximately 10
Approximately 10
Approximately 10
Approximately 10
Approximately 10
Approximately 10
Approximately 10
Approximately 10
Approximately 12
Approximately 2.1
(pump optional)
Approximately 2.1
Approximately 2.1
(pump optional)
Approximately 2.1
Approximately 8.2
(pump optional)
Approximately 8.2
Approximately 8.2
(pump optional)
Approximately 8.2
Approximately 8.2
(pump optional)
Approximately 8.2
Approximately 8.2
(pump optional)
Approximately 8.2
Approximately 11.2
(pump optional)
Approximately 12 Approximately 11.2
1. All wiring between the unit and field installed devices must be made with type T wire.
2. Line voltage wire exterior to the appliance must be enclosed in approved conduit or approved metal clad cable.
3. The appliance pump must be controlled by the provided intermittent pump control relay.
4. To avoid serious damage, DO NOT energize the unit until the system is full and water is flowing through the unit.
COMBUSTION AND VENTILATION AIR
Provisions for adequate combustion and ventilation air to the mechanical room must be in accordance with Section
5.3, Air for Combustion and Ventilation of the latest edition of the National Fuel Gas Code, ANSI Z223.1 and/or
CAN/CSA B149, Installation Codes or applicable provisions of the local building codes.
Equipment located in confined spaces requires two openings installed within 12” (300 m) from the top and bottom of the room to assure adequate combustion air and proper ventilation. The total input of all gas utilization equipment installed in the room must be used to determine the required minimum air volume needed for combustion, ventilation and dilution of flue gasses.
1. All Air From Outdoors: a. Each opening requires a minimum free area of 1 square inch per 4000 Btu/hr input if directly communicating with the outdoors or communicating to the outdoors through vertical ducts. b. Each opening requires a minimum free area of 1 square inch per 2000 Btu/hr input if communicating with the outdoors through horizontal ducts.
2. All Air From Inside The Building:
Each opening requires a minimum free area of 1 square inch per 1000 Btu/hr input, but not less than 100 square inches (0.06 m
2)
.
3. Combination Of Air From The Indoors And From The Outdoors:
Refer to National Fuel Gas Code, ANSI Z223.1 and/or CAN/CSA B149, Installation Codes or applicable provisions of the local building codes.
5 34-50 04/02/2010
NOTE : This unit may be installed with an optional remote air intake system which uses a make-up air duct to draw combustion air directly from outdoors. (See Vertical and Horizontal Remote Air Section).
WARNING – Adequate clean combustion air must be provided to the appliance. Under no circumstances should the appliance ever be under a negative pressure. Particular care should be taken when exhaust fans, compressors, air handling units, etc. may rob air from the appliance. The combustion air supply must be completely free of any chemical or fumes, which may be corrosive to the boiler. Some common chemical fumes to avoid are fluorocarbons and other halogenated compounds, most commonly present as refrigerants or solvents, such as Freon, trichloroethylene, perchlorethylene, chlorine, etc. These chemicals, when in contact with the equipment or when burned, form acids which quickly attack the tubes, flue collector, stack and other appliance and auxiliary equipment. The result of inadequate clean combustion air or negative pressure can be premature unwarranted product failure or unsafe operation producing carbon monoxide that could escape into the building. Exposure to carbon monoxide can lead to injury or death.
VENTING
For appliances connecting to gas vents or chimneys, vent installation must be in accordance with Part 7, "Venting of
Equipment," of the latest edition of the National Fuel Gas Code, ANSI Z223.1 or, in Canada, Section 7, “Venting
Systems and Air Supply for Appliances” of the latest edition of the CAN/CSA B149 Installation Codes, or applicable provisions of the local building codes.
Do not connect vent connectors serving appliances vented by natural draft to any portion of a mechanical draft system operating under positive pressure.
A barometric damper (draft control) is supplied for use on conventional vented installations. A properly installed and adjusted barometric damper helps stabilize draft and regulate high updraft. Conventional vented multiple unit installations with combined venting require barometric dampers to regulate draft at each unit. Adjust the barometric damper to 0.04 inches water column updraft, when used. Follow the barometric damper manufacturer’s installation instructions.
VENT AND COMBUSTION AIR CONNECTION SIZES (nominal sizes in inches)
MODELS VENT CONNECTION SIZE COMBUSTION AIR PIPE SIZE
400 6"
540 6"
6"
6"
750 8"
1000 8"
1200 10"
1600 12"
2000 12"
8"
8"
10"
12"
12"
Locate units as close as possible to chimney or gas vent. For conventionally vented installations, the connection from the vent to the stack or vent termination outside the building must be made with listed Type “B” double wall (or equivalent) vent connectors and must be direct as possible with no reduction in diameter.
Support horizontal portions of the venting system to prevent sagging. Horizontal runs must slope upwards not less than 1/4 inch per foot (21 mm/m) from the boiler to the vent terminal. Follow manufacturer’s instructions.
The Following Categories Apply To This Product For Venting Purposes:
Category I An appliance that operates with a non-positive vent static pressure and with a vent gas temperature that avoids excessive condensate production in the vent.
Category III An appliance that operates with a positive vent static pressure and with a vent gas temperature that avoids excessive condensate production in the vent.
VENTING OPTIONS
Gas vents and combustion air ducts connected to PRIMERA
®
products may terminate either above the roof surface or through the side wall. The product may also be equipped with an optional venting system suitable for outdoor installation.
Conventional Vertical Vent Termination (Category I)
The vent terminal should extend at least 3 ft (.09 m) above the highest point where it passes through the roof of a building and at least 2 ft (.06 m) higher than any portion of a building within a horizontal distance of 10 ft. (3.0 m).
6 34-50 04/02/2010
Through-the Wall Vent Termination (Category III)
The product uses the positive pressure generated by the burner system blower to push combustion products out of the vent. Vent materials may be a stainless steel suitable for exposure to condensate or shall be of the insulated type.
The vent system must be certified for use with an appliance requiring a Category III, pressurized vent system. Seal all joints and support horizontal lengths of vent as required by the vent manufacturer.
The sidewall vent length varies by unit size:
Sidewall vents on models 400, 540, 750 and 1000 may be up to Thirty Equivalent Feet (30') in length, plus the vent terminal. Sidewall vents on models 1200, 1600 and 2000 may be up to Fifty Equivalent Feet (50') in length, plus the vent terminal.
Pipe fittings reduce the maximum allowable sidewall vent length. See the “Vent Pipe Fitting Equivalent” table for each fitting installed in the sidewall vent.
Vent Pipe Size
90º Elbow
90º Long Radius Elbow
45º Elbow
VENT PIPE FITTINGS EQUIVALENT (in feet)
6"
11 feet
6 feet
5 feet
Do not use a barometric damper when sidewall venting.
8"
14 feet
8 feet
7 feet
10"
18 feet
12 feet
9 feet
12"
21 feet
14 feet
10 feet
The vent cap should terminate at least 3 feet (0.91 m) above any forced air inlet within 10 feet (3.05 m); 4 feet (1.22 m) below, 4 feet (1.22 m) horizontally from or 1 foot (0.3 m) above any door, window or gravity air inlet to the building; 1 foot (0.3 m) above grade; 1 foot (0.3m) above normal snow levels and shall terminate at least 7 feet (2.13 m) above grade when located adjacent to public walkways or gathering areas.
The vent terminal should not be installed closer than 3 feet (0.91 m) from an inside corner of an L-shaped structure.
CONVENTIONAL VENTING
THROUGH THE WALL VENTING
Vertical and Horizontal Remote Air
A vertical or horizontal remote air inlet system requires installation of an optional “Combustion Air Inlet Package” to duct combustion air from outdoors directly to the unit. The maximum length of field supplied single wall pipe, in equivalent feet is specified in the “Remote Combustion Air Inlet Package” table below.
Important: Each unit must have a dedicated remote combustion air duct. Combining multiple-unit remote air ducts into a common remote combustion air duct is not recommended.
The combustion air cap supplied with the optional remote combustion air inlet package MUST be used to adequately protect the combustion air inlet from wind and weather.
When the remote combustion air inlet and flue gas outlet are located on the same roof top surface, the cap must terminate at least 3 feet (0.91 m) lower than the flue gas outlet, if located within a 10 foot (3.05 m) radius.
For horizontal remote combustion air inlet only, locate the inlet in a wall with wind pressure similar to the wind pressure on the vent. Install the inlet cap at least one foot (0.3 m) above the rooftop or at least 18" above grade and at least one foot (0.3 m) above normal snow levels.
7 34-50 04/02/2010
Combustion air supplied from outdoors must be free of contaminants (See Combustion and Ventilation Air).
Remote Combustion Air Inlet Package
(Includes required inlet cap and necessary appliance connector. Reduce maximum vent length using the “Vent Pipe Fitting Equivalent” Table)
Unit Model
400
540
750 & 1000
1200
1600 & 2000
Use Part #
103336
103336
102406
103337
103338
Size
6"
6"
8"
10"
12"
Max Equivalent Length
100’ (30.48 m)
100’ (30.48 m)
100’ (30.48 m)
180’ (54.86 m)
180’ (54.86 m)
VERTICAL REMOTE AIR HORIZONTAL REMOTE AIR
Outdoor Installation
An optional “Outdoor vent Package” is required for units installed outdoors. This package includes an air intake top cover and vent materials for the most common outdoor installation.
WARNING: Outdoor models MUST be installed outdoors and MUST use the outdoor package supplied by the manufacturer as identified in the “Outdoor Package” table. All covers, doors and jacket panels must be properly installed to insure proper operation and prevent a hazardous condition. Unwarranted product damage, personal injury or death may result, if any of the outdoor package components are substituted, if an outdoor model is used indoors or if the covers, doors and jacket panels are not properly installed.
Outdoor Package
(Includes top mounted air intake system, rear mounted combustion products outlet system and pump rain shield.)
Unit Model Outdoor Package Option # Separate Kit Part #
400 25 103307
540 25 103307
750 25 103308
1000 25 103309
1200 25 103339
1600 25 103340
2000 25 103341
WARNING: Locate the unit according to the provided instructions to minimize deflection of high winds off adjacent walls, buildings or shrubbery, which can cause flue gas recirculation, and to minimize the opportunity for products of combustion to enter the building. Recirculation of flue gas (products of combustion drawn from the flue gas outlet into the combustion air inlet) can cause operational problems, premature unwarranted product failure, or unsafe operation producing carbon monoxide. Exposure to carbon monoxide can lead to injury or death.
Combustion air supply must be free of contaminants (See Combustion and Ventilation Air). Keep area clean and free of combustible and flammable materials. Maintain a minimum clearance of 3" to combustible surfaces and a minimum of 3" clearance to the air inlet. To avoid a blocked air inlet or blocked flue condition, keep the outdoor cap air inlet, flue outlet and drain slot clear of snow, ice, leaves, debris, etc.
The unit should be located at least 3 feet (0.19m) from any wall, vertical surface or inside corner of an L-shaped structure, to minimize the effect of adverse wind conditions on appliance performance. Do not install in locations where rain from building runoff drains will spill onto the unit.
8 34-50 04/02/2010
The combustion products outlet must be located at least 4 feet (1.22 m) below, 4 feet (1.22 m) horizontally from or 1 foot (0.3 m) above any door, window, walkway or gravity air inlet to the building. The outlet must be located at least 10 feet (3.05 m) away from any forced air inlet and at least 3 feet (0.91 m) outside any overhang.
The combustion air inlet on the unit top must be located at least one foot (0.30m) above grade and at least one foot
(0.30m) above normal snow levels.
Flue gas condensate can freeze on exterior walls or on the vent cap. Frozen condensate on the vent cap can result in a blocked flue condition. Some discoloration to exterior building or unit surfaces is expected. Protect adjacent brick or masonry surfaces with a rust resistant sheet metal plate.
A snow fence, screen or other provisions must be installed to prevent snow and ice accumulation around the appliance and its venting system.
GAS SUPPLY AND PIPING
OUTDOOR INSTALLATION
Verify that the type of gas specified on rating plate is supplied to the unit. This unit is orificed for operation up to 2000 feet altitude. Appliance btuh output derates 4% per 1000 feet above 2000 feet elevation. Consult Factory for installations above 2000 feet elevation.
Inlet Pressure: Measured at the inlet pressure tap located at the main gas cock. The inlet pressure must remain within the minimum and maximum values while the unit is at rest and while the unit is operating at maximum firing rate.
Manifold Pressure: Measure at the pressure tap on the downstream side of the final manual shutoff valve for each stage of operation. The rated manifold pressure for each stage appears on the data label located on the left side of the appliance jacket. Factory test pressures appear on a label affixed to the jacket inside the unit top and adjacent the combustion air inlet opening. Maximum manifold gas pressure must not exceed the value specified. Minimum value listed is for the purposes of input adjustment. The manifold pressure is preset at the factory and adjustment is not usually required. If adjustment is required, the burner must be firing at the minimum and/or full rate while the manifold pressure is adjusted.
SINGLE UNIT INSTALLATIONS SUGGESTED
GAS PIPE SIZE
BTU
INPUT
Distance from Meter (In feet)
0-50' 51-100' 101-200' 201-300' 301-500'
Inlet Pressure
Max. (Inches-Water Column)
Min. (Inches-Water Column)
Nat. Gas
10.5"
4.5"
LP
13"
11"
399,000 1 ¼” 1 ¼” 1½"
540,000 1 2"
1½" 2"
750,000 1½" 2"
2"
2" 2½"
1,000,000 2" 2" 2½" 2½"
1,200,000 2" 2½" 2½" 3”
2½"
3"
3"
3"
CONVERT FITTINGS TO EQUIVALENT STRAIGHT PIPE
Diameter Pipe
(inches)
Equivalent Length of Straight Pipe
(feet)
¾" 1" 1¼" 1½" 2" 3" 4" 5"
1,600,000 2½" 2½" 3” 3" 3½"
2,000,000 2½" 3" 3” 3½" 4"
Use the values in “Convert Fittings To Equivalent Straight Pipe” to add the equivalent straight pipe for each elbow or tee to obtain the total distance from the meter. Use this corrected total distance from the meter for determining the suggested pipe size in the “Single Unit Installation Suggested Gas Pipe Size” table.
Appliance Isolation During Gas Supply Piping Pressure Test
1. The appliance and its individual shutoff valve must be disconnected from the gas supply piping system during any pressure testing of that system at test pressures in excess of ½ PSI (3.5 kPa).
2. The appliance must be isolated from the gas supply piping system by closing its individual manual shutoff valve during any pressure testing of the gas supply piping system at test pressures equal to or less than ½ PSI (3.5 kPa).
3. The appliance and its gas connection must be leak-tested before placing it in operation.
9 34-50 04/02/2010
Gas Connection
1. Safe operation of unit requires adequate gas supply with the required static and dynamic (flow) pressures. Actual piping selection depends on many variables that must be carefully considered by the gas piping system designer. Do not select gas pipe sizes based only on the supplied tables. These tables are for use by the gas piping system designer as a reference in checking pipe size selections.
2. Gas pipe size may be larger than heater connection.
3. Installation of a union is suggested for ease of service.
4. Install a manual main gas shutoff valve, outside of the appliance gas connection and before the appliance gas valve, when Local Codes require.
5. A sediment trap (drip leg) MUST be provided in the inlet of the gas connection to the unit.
6. The appliance regulator and valve bias ports utilize vent limiters/are designed and must respond to pressure changes in the top cabinet, as opposed to atmospheric pressure. For proper operation, do not disconnect, alter, connect to atmosphere or relocate these gas valve and regulator bias ports or bias port tubing.
MULTIPLE UNIT INSTALLATIONS GAS PIPING SIZE CHART
Maximum Capacity of Pipe in Thousands of BTU’s per hour for gas pressures of 14 Inches Water Column (0.5
PSIG) or less and a pressure drop of 0.05 Inch Water Column (Based on NAT GAS, 1025BTU’s per Cubic Foot of Gas and 0.60 Specific Gravity).
Nominal Iron
Pipe Size,
Inches
3/4
1
1 1/4
1 1/2
Length of Pipe in Straight Feet
10 20 30 40 50 60 70 80 90 100 125 150 175 200
369 256 205 174 155 141 128 121 113 106 95 86 79 74
697 477 384 328 292 267 246 256 210 200 179 164 49 138
1400 974 789 677 595 543 502 472 441 410 369 333 308 287
2
2 1/2
3
4100 2820 2260 1950 1720 1560 1440 1330 1250 1180 1100 974 871 820
6460 4460 3610 3100 2720 2460 2310 2100 2000 1900 1700 1540 1400 1300
11200 7900 6400 5400 4870 4410 4000 3800 3540 3300 3000 2720 2500 2340
4
Gas Train and Controls Certification
NOTE: The gas train and controls assembly provided on this unit have been tested under the applicable American
National Standard to meet minimum safety and performance criteria such as safe lighting, combustion and safety shutdown operation.
Gas Control Trains
All model 400 and 540 gas control trains include a main gas cock located externally, a combination valve, a union which may or may not contain a factory installed orifice and a final manual shutoff valve with the manifold pressure tap on the side of the valve.
All model 750, 1000, 1200, 1600, and 2000 gas control trains include a main gas cock located externally, a proportionating valve, and a final manual shutoff valve with the manifold pressure tap on the side of the valve.
Caution : Do not adjust or remove any screws or bolts on gas train control components which are sealed with a red or blue colored compound. Doing so will void all approvals and warranties.
10 34-50 04/02/2010
WATER CONNECTIONS AND PIPE SIZE
Inlet and Outlet Connections
The inlet and outlet water connections to the unit are cupronickel and connect directly to the copper heat exchanger.
Use proper soldering/brazing attachment practices to make system and building connections. Twisting or bending loads on these connections may cause damage to the heat exchanger and are not covered by warranty. For ease of service, install unions on inlet and outlet of the unit. The connection to the unit marked “Inlet” on the header connects to the return from the system (water to be heated). The connection on the header marked “Outlet” connects to the supply side of the system (hot water out of the unit).
Copper piping connecting the PRIMERA
® cupronickel inlet and outlet to the circulating pump and the storage tank
(water heater) or main building heating loop (boiler) must be at least 2” diameter for models 399, 750, 1200 and 1600 and must be at least 2-1/2” diameter for models 1000 and 2000. (Note: 2” cupronickel or brass pipe and fittings may be used instead of 2-12” copper for models 1000 and 2000).
To facilitate connection of 2-1/2” copper pipe to the 2” cupronickel inlet and outlet connections, a quantity of two 2” x
2-1/2" increaser couplings are attached by a tie strap to the upper cupronickel outlet connection near the relief valve. If the circulator pump outlet is directly connected to the cupronickel inlet, the 2” x 2-1/2” increaser can be used as part of the connection of 2-1/2” copper pipe to the circulator pump inlet. If the pump is mounted remote from the cupronickel
PRIMERA
®
inlet, the increase from the 2” pump inlet and outlet must be made with brass or bronze fittings before connecting to the 2-1/2” copper pipe.
Improper use of smaller copper pipe sizes will cause increased back pressure and excessive water velocity. Increased water back pressure can cause the circulator pump to provide inadequate flow to maintain successful operation of the
PRIMERA
®
and excessive water velocity can cause pipe erosion which can lead to piping failure.
For PRIMERA
® heating boilers, black steel pipe (never use galvanize pipe or fittings) can be used instead of copper.
Number of Units
1
COMMON MINIMUM WATER MANIFOLD SIZE FOR MULTIPLE UNITS (USING TYPE-L COPPER)
Pipe sizing chart provides minimum pipe size for common manifold piping to insure adequate flow.
399,000 btuh
540,000 btuh
2"
750,000 btuh
2"
1,000,000 btuh
2½" (*) 2"
2 2" 3" 3½" 2½"
3 2½" 3½" 4" 3½"
2" 2½" (*)
3" 3½"
3½" 4"
* PRIMERA
®
boiler models 1000B and 2000B connections between the PRIMERA
® cupronickel inlet and outlet connections, the circulating pump and the main building heating loop can be made with 2” pipe if steel piping is used.
For other models and for multiple units, follow the manifold sizing in the chart.
MAINTAINING PROPER FLOW RATE / TEMPERATURE RISE
Important - To insure proper velocity through the heat exchanger, it is necessary to regulate the temperature rise across the heat exchanger from inlet to outlet. This must be done on initial installation and periodically rechecked. With the correct temperature rise across the heat exchanger, you may be assured of the proper velocity in the tubes. This will yield long life and economical operation from your appliance. Excessive lime build-up in the tubes is a result of too little velocity in the tubes. Too much velocity through the tubes or pipes causes excessive pitting or erosion in the tubes or pipes. Care should be taken to measure temperature rise and maintain a velocity as follows:
1. With the pump running and the PRIMERA
® boiler or water heater off (not firing), the inlet and outlet thermometers should read the same temperatures. If they do not, an adjustment must be made to your final calculation.
2. Turn the PRIMERA
® boiler or water heater full on (firing at maximum input) and allow a brief time for the outlet temperature to stabilize (about 5 to 10 seconds). Viewing both temperatures as quickly as possible, record the difference between the inlet and outlet temperatures. This difference is the “temperature rise.”
3. Compare this recorded temperature rise with the values shown in the “Required Temperature Rise” table below.
Should adjustment be needed, proceed as follows:
11 34-50 04/02/2010
REQUIRED TEMPERATURE RISE
Models
Temperature Rise (Outlet temp minus
Inlet temp) in degreesº F at Full Fire.
400 23°F
540 30°F
750 21°F
1000 23°F
1200 45°F
1600 45°F
2000 45°F
If the temperature rise is too high, then the water velocity is too low. Check the following:
1. Check for restrictions in the outlet of the heater.
2. Be sure all valves are open between the heater and the tank.
3. Check the pump to be sure it is running properly and that the pump motor is turning in the proper direction.
4. Be sure the circulation pipes between a single heater and the storage tank are not less than 2" (2-1/2” for models
1000 and 2000) diameter. Common manifold piping for multiple unit installations will require larger minimum pipe sizes to insure proper flow. See the Table titled “Common Minimum Water Manifold Size for Multiple Units.”
5. To prevent accidental change to the required temperature rise, remove and store the adjustment valve handle once the required temperature rise is obtained.
If the temperature rise is too low, then the water velocity is too high. Adjust as follows:
Slowly throttle the valve on the outlet side of the heater until the temperature rise is steady at the required temperature rise as noted in “Required Temperature Rise” Table.
REQUIRED: LOW TEMPERATURE BYPASS LOOP - INSTALLATION AND SETUP
Warning: Carefully follow the installation and setup instructions in this section to maintain a 130°F minimum
PRIMERA
® inlet water temperature. PRIMERA
® inlet water temperature below 130°F can result condensation that can cause heat exchanger corrosion or blockage. Operation at inlet water temperature below 130°F will void the warranty and may create hazardous conditions that result in property damage, personal injury, fire, explosion and creation of toxic carbon monoxide or death.
All PRIMERA
® water heater and boiler installations must maintain inlet water temperatures above 130°F to minimize the formation of condensate on the surface of the heat exchanger. A temperature adjustable bypass from the
PRIMERA
®
outlet piping to inlet piping is required to raise inlet water temperature to a minimum of 130°F before it enters the appliance (See piping schematics at rear of this manual):
In applications where low-temperature return water and outlet water temperature is predictable (fixed-rate), the bypass loop must include a properly adjusted manual flow metering device.
In applications with varying low-temperature return and varying outlet water temperatures (modulating), the bypass loop must include a fixed-temperature mixing valve at the inlet to constantly meter and mix outlet water with return water.
A Thermostatically Controlled Mixing Valve is an available option from Riverside Hydronics and is one of the most reliable and effective ways to maintain a minimum 130°F inlet water temperature on PRIMERA
® units
.
Caution - The maximum increase in inlet water temperature obtained by this manual bypass is limited, so this method may not be adequate to assure inlet water to the PRIMERA
®
is always above 130°F. See the chart below for additional information:
2-Inch Manual Bypass Pipe Size Is Recommended:
Manual Bypass size based on all copper construction with full port ball valve.
Maintain the required temperature rise for each model at all times.
If the bypass valve position is changed, readjust both the balancing valve and the bypass valve to result in the desired inlet water temperature and the required heat exchanger temperature rise from the PRIMERA
®
inlet to the outlet.
12 34-50 04/02/2010
BOILER FLOW RATE REQUIREMENTS
Model
BOILER FLOW RATE REQUIREMENTS
AND FACTORY SUPPLIED* CIRCULATOR PUMP PERFORMANCE
Circulator Size (120V)
Design
HP Amp
Flow Rate
Draw
GPM
Temperature Rise at
Design Flow In
Degrees in °F
Maximum Foot Head of Circulator at Design Flow Rate
400 1/6 2.1
540 1/6 2.1
750 2/5 4.8
1000 3/4
1200 3/4
8.2
8.2
30
30
61
76
46
23
30
21
23
45
12
12
15
21
24
Foot Head Loss through PRIMERA at Design Flow Rate
8
8
10
12
18
1600 3/4 8.2
2000 1 11.2
61
76
45
45
23
28
18
19
* Pumps are supplied as standard equipment with PRIMERA
®
water heaters (Model W series). Pumps are not included as standard equipment for PRIMERA
®
boilers (Model B series), but may be selected from the optional equipment list. If a Cupronickel heat exchanger is supplied, pump specifications may change. Consult Riverside Hydronics.
CIRCULATOR PUMP WIRING
PRIMERA
® water heaters and boilers require a properly sized circulator pump. Whether factory or locally supplied, wire single-phase circulator pumps as shown below:
Important: Lubricate the pump to the manufacturer's recommendations. The warranty does not cover pump damage due to inadequate lubrication.
13 34-50 04/02/2010
Important For Hydronic Heating Applications:
1. Design flow rate is the maximum allowable and recommended flow through the heat exchanger on each individual boiler. This flow rate must not be varied on models 1200B, 1600B and 2000B. For all other models of PRIMERA
® boilers, system designers are strongly urged not to deviate from the design flow rate.
2. If connecting one or more PRIMERA
®
boilers to a heating loop that has variable flow rate pumping on the main circulator, consult Riverside Hydronics for recommendation on piping and flow rates.
3. Pumps supplied for hydronic heating applications may be cast iron, bronze or bronze fitted.
4. The System Designer must confirm proper sizing of the circulating pump by calculating total head loss through the primary loop piping, valves, fittings and the boiler at the boiler design flow rate.
Important For Water Heater Applications:
1. Design flow rate is the required flow rate for domestic water heating applications. Do not deviate above or below this flow rate, as erosion or scaling of the heat exchanger may result.
2. Chart information is acceptable for water hardness up to 16 grains (272 ppm). Otherwise, consult factory.
3. Maximum heater-to-tank recirculation piping length - When supplied from the factory with a standard pump, the pump sizing is based on the following number of tank to heater 2" (2-1/2” required for 1000W, 1000B, 2000W and
2000B) copper pipe recirculation loop fittings (for longer runs or more fittings, consult factory):
6 – 90 o
elbows (or 12 – 45 o
elbows) 2 - ball valves (full port type) for service shutoff and balancing
2 – bypass tees 1 - ball valves (full port type) and bypass piping
4 – unions 1 - cold domestic makeup water tee (if required)
Not more than 45 total feet of straight 2” (2-1/2” for models 1000 and 2000) pipe (DEDUCT 5 FEET from maximum allowable straight pipe in heater to tank circulating loop for every elbow and tee in excess of those shown above.)
4. If the PRIMERA
®
is ordered with the “No Pump” option, the System Designer must properly size an all bronze circulating pump by calculating the total head loss through the through the heater-to-tank piping, valves, fittings and water heater at the required water heater design flow rate.
Filling the Unit
1. Fill the system with water. To be sure that the unit is not “air bound,” open the relief valve. Leave the valve open until a steady flow of water is observed. Close valve and complete filling the system.
2. In hard water areas, water treatment should be used to reduce introduction of minerals into the system. Minerals in the water can collect in the tubes and cause noise during operation. Proper temperature rise must be maintained. Excessive buildup of minerals in the heat exchanger can cause a non-warrantable failure. Water must not be softened below a hardness of 2 grains, as water softened below this point becomes very aggressive and can cause a non-warrantable heat exchanger failure.
3. Make sure there are no system leaks. DO NOT use petroleum based stop-leak products. All system leaks must be repaired. The constant addition of make-up water to a closed loop boiler system can cause minerals to collect in the heat exchanger. Excessive buildup of minerals in the heat exchanger can cause a non-warrantable failure.
4. If freeze protection is required on a boiler connected to an indirect coil, DO NOT use undiluted or automotive type antifreeze. Use only hydronic system antifreeze, following the manufacturer’s instructions.
14 34-50 04/02/2010
GENERAL INFORMATION
Temperature Setting (For Domestic Hot Water Use)
This unit has an adjustable thermostat to control water temperature. The thermostat is factory pre-set at approximately
125
º
F. Households with small children or disabled individuals may require 120
º
F or lower temperature setting to reduce risk of scald injury. Some states may require a lower temperature setting. Check for local requirements governing the temperature setting. Remember, no water heating system will provide exact temperature at all times. Allow a few days of operation at this setting to determine the correct temperature setting consistent with your needs.
Note: (1) This water heater, when set at the lower temperature setting, is not capable of producing hot water of sufficient temperature for sanitizing purposes. (2) Higher stored water temperature increases the ability of the water heater to supply desired quantities of hot water; however it also increases the risk of scald injury.
This equipment is intended to operate in non-condensing condition. Incorrect piping of the cold water supply to the system may result in condensate formation on the heat exchanger, causing operational problems. Inlet water to the appliance must not drop below 130
º
F. See typical installation instructions for piping in low water temperature systems.
Higher water temperature into the appliance inlet reduces condensate formation. Damage caused by operating in condensing conditions is not covered by the Manufacturer’s warranty.
Operating Temperature Control
An adjustable digital operating control is located in the front control panel. To adjust the set to deliver the desired water temperature, press and release the Set 1 key on the face of the control. When set point adjustment is enabled, use the arrow keys to adjust the set point to the desired system temperature. Contact Riverside Hydronics to obtain expanded digital operating control information (form # 34-80) for more detailed instructions.
High Water Temperature Limit Control
Appliances are equipped with adjustable limit and high limit controls to control the maximum discharge water temperature. These controls are located inside the upper cabinet, on the right side of the main control panel and are accessed by removing the jacket top cover. The high limit control on boilers is of the manual reset type and may be reset by pressing any button on the TempTrac
®
control. The PRIMERA
®
(manual reset optional). Pressing the TempTrac
®
water heater high limit is of the auto reset type
to reset will not cause the control to reset until the water temperature has dropped below the set point of the manual reset high limit control.
Warning: Turn off all electrical service to the appliance when accessing the limit or high limit controls located inside the upper cabinet. The upper cabinet contains High Voltage wiring and terminals. If the electrical service is not turned off and these terminals are touched, a dangerous shock causing personal injury or loss of life could occur. Close and fasten the jacket top cover before restoring electrical service to the appliance.
Freeze Protection
Although these units are design certified for outdoor installations - such installations are not recommended in areas where the danger of freezing exists. Proper freeze protection must be provided for outdoor installations, units installed in unheated mechanical rooms or where temperatures may drop to the freezing point or lower. If freeze protection is not provided for the system, a low ambient temperature alarm is recommended for the mechanical room. Damage to the unit by freezing is not covered by the warranty.
1. Circulating water through the unit can help prevent freezing. If the system pump does not run continuously, a low temperature pump switch option is available to energize a circulator pump when low water temperatures are present.
2. Freeze protection for a boiler application can be provided by using hydronic system antifreeze, following the manufacturer’s instructions. DO NOT use undiluted or automotive type antifreeze. If the boiler is used as the energy source for an indirect coil type water heater, follow the indirect coil manufacturer’s instructions concerning the use of potable type antifreeze.
3. A snow fence, screen or other provisions must be installed to prevent snow and ice accumulation around the appliance and its venting system.
4. If for any reason the unit is to be shut off, you must: a. Shut off water supply. b. Drain the appliance, pump and piping completely.
5. A unit may contain water before or after installation for a variety of reasons. Drain all water through the lower inlet fitting on the appliance, and then drain the remaining water by removing the brass drain plug in the bottom of the heat exchanger. The drain plug is located between the floor and the bottom of the unit at the rear of the unit, below the water inlet connection, and can be removed with the use of a box wrench. The unit must be level for all water to drain.
15 34-50 04/02/2010
Cathodic Protection
In hot water systems utilizing cathodic protection, Hydrogen gas can be produced when the hot water system has not been used for a long period of time (generally two weeks or more).
Hydrogen gas is extremely flammable. To prevent the possibility of injury under these conditions, one of the hot water system faucets should be opened for several minutes before using any electrical device connected to the hot water system. If hydrogen is present, there will be an unusual sound such as air escaping through the pipe as the hot water begins to flow. Do not smoke, have open flames or turn electrical switches on or off near the faucet at the time it is open.
Relief Valve
PRIMERA
®
heating boilers are normally supplied with a pressure only relief valve(s) sized in accordance with the
ASME Boiler and Pressure Vessel Code, Section IV.
PRIMERA
®
water heaters and hot water supply boilers are normally supplied with a temperature and pressure relief valve(s) sized in accordance with ASME Boiler and Pressure Vessel Code, Section IV.
The relief valve(s) is installed in the hot water outlet. No valve or obstruction is to be placed between the relief valve, and the hot water outlet of the unit.
Caution : Do not install a reducing coupling, valve or other restriction in the relief valve(s) discharge line. The discharge line shall allow complete drainage of the valve and line. Relief valves should be manually operated at least once a year.
Warning: To prevent burns caused by hot water discharge and water damage, pipe the discharge from the relief valve to a suitable floor drain for disposal when relief occurs. Avoid contact with hot discharge water.
Optional Relief Valve
PRIMERA
® water heaters certified to ANSI Z21.13 (for hot water supply boilers) may be supplied with an optional pressure only relief valve(s). When a heater equipped with this optional pressure only relief valve is piped to a separate storage vessel, the storage vessel must have a properly installed temperature and pressure relief valve which complies with the Standard for Relief Valves and Automatic Gas Shutoff Devices for Hot Water Supply Systems, ANSI
Z21.22.
Thermal Expansion
A relief valve that discharges periodically may be due to thermal expansion in a closed system, such as water heaters or hot water supply boilers installed in a system closed by components, such as a backflow preventer or check valve in the cold water supply or a closed boiler heating loop. These systems must be provided with means to control expansion. Contact a boiler or plumbing professional to resolve this situation. Do not plug the relief valve.
Water Flow Switch
Units are equipped with a factory installed water flow switch in the discharge piping. A minimum of 30 GPM (20 GPM for model 400 and 540) is required to “turn on” (make) the flow switch and start burner operation. The water flow switch meets code requirements for a low-water cut off device on boilers requiring forced circulation for operation. Low water cutoffs are designed for use on tank type equipment with defined water levels and are not appropriate for use on equipment, such as the PRIMERA
®
., that require forced circulation to operate.
16 34-50 04/02/2010
REMOTE CONNECTIONS - TERMINAL STRIP
A terminal strip for the remote connection is located behind the control panel and is accessed by removing the top pan.
Terminals A1-A2 and P1-P2 are functional only when the PRIMERA
®
is equipped with the factory installed option required to activate the terminals. Terminals R1-R2, C1-C2 and T1-T2 are standard pre-wired functions on all
PRIMERA
®
products. The following describes the functions of each of these terminals and the factory-installed options required to activate the terminals. Disconnect electrical power before accessing the terminal strip.
R1
R2
R1-R2. Used to activate /de-activate boiler from remote master control. *
Terminals are wired to a relay in a remote Boiler Management or Energy
Management System. When relay closes, circuit from R1 to R2 is completed and boiler controls are enabled. Boiler ships from factory with jumper between terminals Remove jumper when connecting to a remote boiler controller.
Options required: none (see note)
A1
A2
A1-A2: Used to activate a remote alarm signaling shutdown of combustion control
Provides a maximum 10 amp relay contact closure when flame safeguard terminates combustion due to tripping any of the following: air proving switch, high limit switch, low water flow switch or flame sensor.
Options required: Option 23 (supplies relay)
P1
P2
P1-P2: Activates remote equipment and requires confirmation signal back to boiler
Provides a maximum 10 amp relay contact closure to activate a remote device, such as mechanical room air louvers, draft inducer or power venter. The remote device must send return signal via proving switch to confirming proper operation to terminals C1-C2, prior to boiler being able to energize.
Options required: Option 20 (supplies relay)
C1
C1-C2: Used for proving operation of remote device.
Terminals are wired to a proving switch on a remote device such as a power venter. When relay closes, circuit from C1 to C2 is completed and boiler controls are enabled. Boiler ships form the factory with jumper between terminals.
Options required: None (see note)
C2
T1
T2
T1-T2: Used for external 2-stage or modulation control *
To connect external control to a two-stage PRIMERA, remove the factory installed jumper connecting terminals T1-T2, then connect the external control signal to terminals T1 and T2. To connect external control to a modulating PRIMERA, disconnect and cap the blue wire connected to terminal T2 and connect the external modulating signal to terminals T1 (positive) and T2 (negative).
Options required: None.
* For detailed information on connecting PRIMERA
®
to a multiple boiler controller, refer to supplemental installation manual number 34-400.5. This document is available online at www.riversidehydronics.com.
Note: Do not use single strand bell wire for remote field connections to terminals R1-R2 and C1-C2. Use only multi-strand copper wire. See table below for wire length and gauge:
Wire Gauge
Maximum Length
18 GA
30 FT
16GA
50 FT
14 GA
75 FT
12 GA
100 FT
17 34-50 04/02/2010
BOILER MANAGEMENT SYSTEM (BMS) CONNECTION
Connections for BMS control are made to the terminal strip located on rear of PRIMERA control box.
The terminal strip is accessed by removing the PRIMERA top pan.
Refer to above picture for all applications
If BMS is to provide remote on/off control only:
1. Remove the jumper connecting terminals R1 and R2
2. Connect the BMS output leads for the enable/disable function to terminals R1 and R2
3. Leave all other wires in their initial positions
If BMS provides STAGE-FIRING control: (Models 400B)
1. Remove the jumper connecting terminals R1 and R2
2. Connect the BMS first stage leads to terminals R1 and R2 (no polarity)
3. Connect the BMS second stage leads to terminals T1 and T2 (no polarity)
4. On the TempTrac Control, move parameter St1 up to its maximum setting of 180°F. This setting effectively takes the TempTrac out of the way and allows complete control by the BMS system
5. Leave all other wires in their initial positions
NOTE: BMS must call for both first and second stage operation before firing cycle will be initiated. Afterward,
BMS can cycle between low and high fire.
If BMS provides MODULATION control through a 4 to 20 milliamp or 0 to 10 volt signal:
1. Remove the jumper connecting terminals R1 and R2
2. Connect the BMS output leads for the enable/disable function to terminals R1 and R2 (no polarity)
3. Remove blue wire from terminal T1 and cap the end with a wire nut. Secure the loose wire
4. Connect the BMS variable signal output leads to terminals T1 and T2 (T1 is positive, T2 is negative)
5. On the TempTrac Control, move parameter St1 up to its maximum setting of 180°F. This setting
effectively takes the TempTrac out of the way and allows complete control by the BMS system
6. If the BMS supplies a 0 to 10 volt signal, the resistor connecting terminals 1 and 3. For milliamp signal, resistor must remain in place
7. Leave all other wires in their initial positions
In all cases, the BMS must sense temperature on the building’s hydronic distribution loop upstream of the
PRIMERA boilers. No attempt should be made to control the PRIMERA boilers by sensing temperature downstream of the boilers.
18 34-50 04/02/2010
SEQUENCE OF OPERATION - IGNITION CONTROL
1. POWER-UP
Power is applied to the full time 24 volt input. The microprocessor will start a self-check routine of about five seconds. After this delay, the LED will come on and the control is ready to start a new call for heat.
For Manual Reset Button Models Only
Models of the 35-67 with non-volatile lockout (manual reset button), the microprocessor will check memory to determine if the control should remain in lockout.
Lockout Present: The lockout indicator output will turn on, and the LED will repeatedly flash three times. To reset the control, push the Reset Button.
Not in Lockout: The control is ready to start a new call for heat.
2. CALL FOR HEAT
The thermostat is turned on. The combustion fan relay will turn on.
Proof of Pressure Switch: The control will look for a signal from the pressure switch, indicating that the fan has come on.
Pre-Purge Delay: When the pressure switch signal is seen, the pre-purge delay will start. The pre-purge indicator output will turn on.
3. HEAT-UP
After the pre-purge delay, power will be applied to the hot surface ignition element. The pre-purge indicator will turn off.
Current Proving: The 35-67 will monitor the current through the ignition element. When the current reaches a pre-determined level, the LED will flash once.
Dwell Time: From the point when the current has been proven, there will be a delay called dwell time. Dwell time assures that the ignition element has sufficient time to reach ignition temperature.
4. IGNITION
When dwell time is completed, the gas valve will open. The ignition element will turn off 2 seconds before the end of the ignition period.
No Flame:
Single Trial for Ignition Models - The control will go to post-purge, and then lockout.
Three Trials for Ignition Models - The control will make two additional purge/heat-up/ignition cycles. If a flame is not proven, the control will go to post-purge, and then lockout.
Flame is Proven:
The gas valve will remain on beyond the normal ignition period. This continues as long as signals are present for the flame, thermostat and pressure switch.
Post-Purge: After all ignition cycles are complete, the control will enter post-purge. The combustion fan will remain on.
Lockout: After post-purge is complete, the combustion fan will turn off. The Lockout Indicator output will turn on.
The LED will repeatedly flash three times.
5. LOSS OF FLAME SIGNAL
The gas valve will turn off. Depending on the model chosen:
Single Trial for Ignition Models - A new trial for ignition cycle will start.
Three Trials for Ignition Models - Three new ignition cycles will start.
CONTROL PANEL INDICATING LIGHTS
The control panel has an ON/OFF power switch with indicating light and five (5) indicating lights to show operation and control sensed malfunctions.
OPERATING CONTROL INDICATING LIGHTS
Indicating Lights FUNCTION
Call for Heat
Lockout
Flame
Blower
Water Flow
Operating control has enabled the burner control to begin the ignition sequence.
Ignition module unable to properly prove ignition.
Burner is operating
Blower is running
Water flow rate meets the minimum threshold of the flow switch
19 34-50 04/02/2010
TO TURN OFF GAS TO APPLIANCE
1. Turn off all electric power to the appliance if service is to be performed.
2. Locate manual gas shutoff valve by looking where the gas pipe enters
the appliance and follow the gas line away from the appliance jacket until you reach
the manual gas shutoff valve.
3. Turn the gas off by rotating the gas valve handle 90 degrees to aim across the pipe.
(The gas valve is on when the handle is parallel to the gas pipe).
LIGHTING INSTRUCTIONS (For Your Safety Read before Operating)
Manual Gas Valve (Cock)
Warning: If you do not follow these instructions exactly, a fire or explosion may result causing property damage, personal injury or loss of life.
A. This appliance does not have a pilot. It is equipped with an ignition device that automatically lights the burner.
DO try to light the burner by hand.
B. BEFORE OPERATING, smell around the appliance area for gas. Be sure to smell next to the floor because some gas is heavier than air and will settle to the floor.
What To Do If You Smell Gas
Do not try to light any appliance.
Do not touch any electric switch; do not use any phone in your building.
Immediately call your gas supplier from a neighbor’s phone. Follow the gas supplier’s instructions.
If you cannot reach your gas supplier, call the fire department.
C. Use only your hand to turn the gas control lever. Never use tools. If the lever will not turn by hand, don’t try to repair it, call a qualified service technician. Force or attempted repair may result in a fire or explosion.
D. Do not use this appliance if any part has been under water. Immediately call a qualified service technician to inspect the appliance and to replace any part of the control system and any gas control that has been under water.
Lighting Instructions
1. STOP!
Read the safety information.
2. Turn manual gas cock clockwise to the “ON” position.
3. Wait five (5) minutes to clear out any gas. If you smell gas, STOP!
Follow "B" in the safety information. If you don't smell gas go on to the next step.
4. Turn On all electrical power to the appliance.
5. Lift and raise the plastic control access panel at the front of the unit.
6. Press rocker switch to “ON” position.
7. Adjust thermostat to obtain a call for heat.
8. The automatic ignition device will light the burners. DO NOT try to light the burner by hand.
9. Replace control access panel.
10. If the appliance will not operate, follow the instructions "To Turn Off Gas to Appliance" and call your service technician or gas supplier.
Test Ignition System Shutoff Device
After placing the appliance in operation, the ignition system safety shutoff device must be tested.
To conduct this test:
1. Locate the manual valve on the large gas pipe entering the blower.
2. While the unit is firing at full rate, turn gas off to the burner by closing this manual valve.
3. When the burner loses flame, the ignition system safety shutoff device should de-energize the main gas valve.
4. After successful testing, reopen the manual valve, reset the ignition safety shutoff device (if necessary) and verify normal appliance operation.
HOT SURFACE IGNITION SYSTEM
Warning: The hot surface gas igniter (HSI/glow bar) and the hot surface ignition module are not repairable and when faulty must be replaced with a new, factory specified replacement part. The ignition characteristics of this Riverside Hydronics
®
specified hot surface gas igniter and hot surface ignition module are unique and replacements are only available from Riverside Hydronics
®
or a Riverside Hydronics
®
authorized representative. Any modification, attempts to repair, or part substitution will invalidate the warranty and may create hazardous conditions that result in property damage, personal injury, fire, explosion, toxic gases or death.
20 34-50 04/02/2010
PERIODIC MAINTENANCE
Listed below are items that must be checked to insure safe reliable operations. Maintenance must be performed by a qualified service or maintenance provider. Verify proper operation after servicing.
Warning: When servicing the controls, use exact, Factory authorized, replacement parts and label all wires prior to disconnection. Verify proper operation after servicing. Incorrect parts substitution and wiring errors can cause damage, improper operation, fire, carbon monoxide and other unexpected and unsafe conditions that could result in fire, injury or death.
1. Examine the appliance and venting system at least once a year. Check more often in first year to determine inspection interval. Check all joints and pipe connections for tightness, corrosion or deterioration. Clean screens in the venting air intake system as required. Have the entire system, including, but not limited to, the burner, heat exchanger and venting system, periodically inspected by a qualified service agency.
2. Using the view port, located on the blower base, visually check main burner flames at each start up after long shutdown periods or at least every six months. a. Normal Flame: A normal flame is blue, without yellow tips or flame lifting. b. Yellow Tip: Yellow tip can be caused by blockage or partial obstruction of airflow to the burner. c. Yellow Flames: Yellow flames can be caused by blockage of primary airflow to the burner or excess gas input. This condition MUST be corrected immediately. d. Lifting Flames: Lifting flames can be caused by over firing the burner(s) or excessive primary air. e. Glowing Burner Media: Glowing burner media can be caused by a blocked air or burner condition resulting in a reduced firing rate.
3. Exposure to Dusty or Dirty Combustion Air: An appliance installed in a dust or dirt contaminated atmosphere will require cleaning of the burners on a 3 to 6 month schedule or more often, based on severity of contamination.
Contaminants can be drawn in with the combustion air. If an air filter box is used to remove dust or dirt, be certain it does not restrict free airflow into the appliance and that the filters are periodically cleaned. Inadequate combustion air or non-combustible particulate matter such as dust, dirt, dryer lint, concrete dust, dry wall dust or the like can block burner ports and cause unsafe operation and a non-warrantable failure. To inspect and clean the burner, a qualified serviceman or installer should use the procedures described in item 5 & 6 below.
4. Heat Exchanger Inspection and Cleaning: Any sign of soot on the heat exchanger or in the flue indicates the need for increased inspection frequency and possible cleaning. Properly installed and adjusted units seldom need heat exchanger cleaning. If a blocking amount of soot has formed or is forming, the heat exchanger must be cleaned and soot-causing problem corrected. (The most common causes are restricted combustion air or excessive gas.)
A blocked heat exchanger can cause unsafe operation and will reduce efficiency. To inspect and clean the heat exchanger, a qualified serviceman or installer should use the procedures described in item 5 & 6 below.
5. All gaskets on disassembled components must be replaced on reassembly with exact, Factory Authorized, replacement parts only. Gasket kits are available from your Riverside Hydronics
®
Representative or by contacting
Riverside Hydronics
®
, LLC.
6. Burner and/or Heat Exchanger Inspection and Cleaning Procedure: a. Write notes and/or take pictures during this process to aid in correct reassembly. b. Turn off main power to unit. c. Turn off gas supply. d. Remove the top access pan. e. For models 400, 540, 750 and 1000, disconnect the main manual gas cock from the gas train. f. For models 1200, 1600 and 2000, remove screws to disconnect the water outlet and gas supply escutcheon plates and the combustion air supply pipe (if connected). Then remove screws and open upper latch to release and remove the service half of the upper enclosure. g. Remove the hot surface igniter and set safely aside (Do not touch the black heating surface of the igniter, as oils from your hand can cause early failure. Take care during removal and reassembly, as the black heating element is very easy to break when not installed.) disconnecting wires.
21 34-50 04/02/2010
i. Tag to identify then disconnect wires to the gas valve, blower, pressure switches, etc., as required to remove the blower and gas train assembly. j. Disconnect, lift and remove the blower and gas train assembly from the unit bulkhead, exposing the burner. k. Carefully remove burner, gaskets and Mica sight glass. l. If the inner screen of the burner is blocked with dust or dirt, it must be carefully cleaned with soap and water. A garden hose with nozzle spraying through the outer burner surface toward the inside of the burner is helpful.
Do not brush or scrub the burner surface as this can cause permanent damage to the burner material. m. Looking through the burner opening in the bulkhead, check the heat exchanger surface for sooting (part of scheduled maintenance). If a blocking amount of soot is present, the heat exchanger must be cleaned and soot-causing problem corrected. n. Remove soot from heat exchanger with a medium stiff bristle brush and use a vacuum to remove loose soot from surfaces and inner chamber, as necessary. Take care not to damage the heat exchanger fins and do not brush or otherwise disturb the insulation above and below the copper heat exchanger. If further cleaning or if additional access is required contact Riverside Hydronics
®
Customer Service for assistance. o. Replace all gaskets exposed during disassembly (see item 5 above). p. To reassemble the unit, maintain the following sequence: 1. Clean the bulkhead gasket surface; 2. Install one fiberglass burner gasket, aligning gaskets and bulkhead openings; 3. Insert burner through gasket into bulkhead; 4. Install Mica sight glass over bolts and covering the round sight glass opening; 5. Install second fiberglass burner gasket over the burner and Mica sight glass, matching the gasket and bulkhead openings; 6.
Carefully reattach the blower and gas train assembly over the burner and gaskets; 7. Continue to reassemble in reverse order. q. Cycle unit and test to verify all safety and operating controls are properly functioning and the combustion chamber is free of leaks.
7. Combustion Air Blower: Check and lubricate the combustion air blower motor on models 750 thru 2000 according to the motor manufacturer’s instructions. Some blower motors are permanently lubricated and do not have lubrication ports. Lubricate with non-detergent SAE 20 oil every 6 months. Clean the blower and blower motor as required when installed in a dust or dirt contaminated location.
8. Inspect low water cutoffs and relief valves for proper operation at every six months, or more often if indicated by inspection.
9. Water Circulating Pump: Inspect the pump every 6 months and lubricate according to the manufacturer’s instructions. (Most Riverside Hydronics
®
pumps are permanently lubricated and do not have lubrication ports.
10. Keep appliance area clear and free from combustible materials, gasoline and other flammable vapors and liquids.
11. Check frequently to be sure the flow of combustion and ventilation air is unobstructed to the boiler.
12. This unit uses a transformer to supply a low voltage control circuit. The voltage on the secondary side should be 24 to 28 VAC, when measured with a voltmeter.
13. All models have a 6 AMP fuse provided on the secondary side of the transformer. A blown fuse indicates a short in the 24VAC controls that must be corrected.
14. All replacement parts are available through your Riverside Hydronics
®
Dealer or directly from the Factory at the address and telephone number located on the first and last page of this manual.
SPECIAL DESIGN APPLICATIONS
The boiler, when used in connection with a refrigeration system, must be installed so the chilled medium is piped in parallel with the boiler with appropriate valves to prevent the chilled medium from entering the boiler.
The boiler piping system of the hot water boiler (when connected to heating coils located in air handling units where they may be exposed to refrigerated air circulation) must be equipped with flow control valves or other automatic means to prevent gravity circulation of the boiler water during the cooling cycle.
22 34-50 04/02/2010
HEATING BOILER SYSTEM PIPING:
Primary-Secondary Piping
For highest reliability and temperature accuracy, plumb PRIMERA
®
boilers to the building’s heating water circulating loop using a primary-secondary piping system (see figure 1.) By definition, a primary-secondary piping system uses separate circulating pumps for each loop. This arrangement assures that flow through the building’s heating loop will not cause flow through the boiler piping, and that the boiler loop flows only when the boiler loop circulator is energized.
Remote Thermowell (for TempTrac sensor)
A single-probe thermowell ships with each PRIMERA
®
boiler. For boiler applications, this thermowell must be located in the secondary loop upstream of the boiler’s primary /secondary loop connection. A ¾-inch NPT female fitting with a depth clearance of
3 inches is required for installation. This factory-supplied single-probe thermowell (or optional four-probe well) is required for the sensor to operate properly. Obtain good thermal contact between the sensing bulb and the well using heat conductive paste designed for this purpose. The sensing bulb wire can extend approximately twenty feet. This wire can be spliced to extend up to
200 feet.
Replacement thermowell part numbers: 102560 (single-probe well) and 102561 (four-probe well).
IMPORTANT: Relocating the Operating Temperature Probe
®
PRIMERA boilers and water heaters ship from the factory with the primary sensing probe (thermister) for the operating temperature control installed in a thermowell in the inlet plumbing of the unit. The sensor must be located here initially to assist in setting up the required temperature rise/flow rate for the appliance (see Water Velocity Control, page 18).
After the proper flow rate through each boiler/water heater is established, relocate the sensor to the remote thermowell.
The only exceptions to moving the primary sensing probe(s):
1. Boiler applications where the primary circulator (pump controlling flow through the boiler) runs continuously. (not suggested or recommended because of increased off cycle energy loss).
2. Boiler applications where staging or modulation control for each PRIMERA
®
is provided by a remote multiple boiler controller; where 2-stage burners are controlled by two separate energize/de-energize signals or where modulating burners are controlled by a variable voltage or milliamp signal.
NOTE: If the multiple boiler controller provides only a single “on/off” signal to each boiler and the onboard TempTrac control stages or modulates the burners, the probe must be relocated to the secondary loop as described above. If there is any uncertainty about the control of the boilers, the installing contractor should provide a sufficient number of ¾-inch female NPT fittings in the secondary loop as described above.
DOMESTIC WATER HEATER AND HOT WATER SUPPLY BOILER PIPING (Service Water Heating):
Important: Do Not install as an instantaneous heater. The unit must be piped to a storage tank (see figure 3).
When Using PRIMERA
®
Water Heating Models In Potable Water Heating Systems :
Do not use water piping, fittings, valves, pumps or other components which are not compatible with potable water.
Do not connect the heater to any heating system or components using non-potable water.
Do not add boiler treatment or any chemicals to the system piping.
Do not use solder containing lead in the potable water lines.
Remote Thermowell (for TempTrac sensor)
A single-probe thermowell ships with each PRIMERA
®
heater. For water heating applications, this thermowell must be located in the storage tank. A ¾-inch NPT female fitting is required for installation. This factory-supplied single-probe thermowell (or optional four-probe well) is required for the sensor to operate properly. Obtain good thermal contact between the sensing bulb and the well using heat conductive paste designed for this purpose. The sensing bulb wire can extend approximately twenty feet. This wire can be spliced to extend up to 200 feet.
Replacement thermowell part numbers: 102560 (single-probe well) and 102561 (four-probe well).
IMPORTANT: Relocating the Operating Temperature Probe
PRIMERA
®
boilers and water heaters ship from the factory with the primary sensing probe (thermister) for the operating temperature control installed in a thermowell in the inlet plumbing of the unit. The sensor must be located here initially to assist in setting up the required temperature rise/flow rate for the appliance (see Water Velocity Control, page 18).
After the proper flow rate through each boiler/water heater is established, relocate the sensor to the remote thermowell in the storage tank. The only exception to moving the primary sensing probe(s) is a water heater application where the primary circulator (pump controlling flow through the water heater) runs continuously. This method of operation is not suggested or recommended.
23 34-50 04/02/2010
24 34-50 04/02/2010
Return temperature to the boiler must be = 130°F
Piping Schematic for Multiple PRIMERA® Boilers - Primary-Secondary
Circulator (confirm proper sizing)
Full Port Isolation Ball Valve
Swing Check Valve
Union
Pressure relief valve. Pipe to drain with no restrictions or valves.
When low temperature bypass is used, boiler flow rate is adjusted using the valve upstream of the bypass.
Notes:
1. Piping shared by multiple PRIMERA boilers, must be sized for the total anticipated flow at a maximum of velocity recommended for the piping material used.
2. Pump sizing must be confirmed for the required boiler flow rate (gpm) against the head loss of the boiler and the boiler piping circuit to and from the building loop connection point.
3. Low temperature bypass from hot outlet of boiler to cold inlet is required if return water to the boiler is expected to drop below 130°F. A thermostatic mixing valve (part no.104348)
4. is recommended if the bypass is installed. Pipe diameter of bypass is 2 inch.
A multiple boiler lead-lag control is recommended on all multiple boiler installations. If multiple boiler control is not used, operating probe from each boiler must be relocated to the indicated loop sensor location after initial boiler delta T and flow rate setup.
5. Refer to individual boiler installation manuals for more details.
Air Separator
PRIMERA
3
PRIMERA
2
PRIMERA
1
Building Supply
Exp.
Tank
Makeup Line
Continuous flow is required. Use a continuous loop or employ 3-way valves adequate to maintain minimum flow
Low
Temperature
Bypass with Valve.
(see note 3)
Minimum static pressure of 15 psi required in the primary boiler loop at all times. Multiple
Boiler
Control
Loop Sensor
B
A
Primary-secondary piping interface.
Maximum of 4 pipe diameters from point A to B is recommended.
IMPORTANT :
Flow through the building loop must always be
125% of the flow required by all boilers firing at any given time. Special attention to boiler sequencing is required if VFD is used on the building loop.
Building Return
25 34-50 04/02/2010
26 34-50 04/02/2010
27 34-50 04/02/2010
28 34-50 04/02/2010
Piping Schematic for Two PRIMERA® Water Heaters and Two Storage Tanks
Circulator (confirm proper sizing)
Full Port Isolation Ball Valve
Swing Check Valve
Union
Temperature and Pressure Relief Valve
Operating Probes
Notes:
1. All piping to the storage tanks must be balanced; this include cold inlet, hot outlet to the building and the piping to and from the water heater main headers.
2. Piping shared by multiple PRIMERA heaters, must be sized for the total anticipated flow of approximately 6 feet per second as required for type L copper.
3. Pump sizing must be confirmed for the required heater flow rate (gpm) against the head loss of the water heater-to-tank piping, as well as the water heater itself.
4. Low temperature bypass from hot outlet to the cold inlet is required on each heater.
5. Operating probes are moved to storage tank after water heater flow rate setup.
3/4" fitting required and multiple-probe thermowell (part no. 102561).
6. Pipe all temperature and pressure relief valves to drain with no restrictions or valves.
7. Refer to heater installation manual (form 34-50) for more details.
Return temperature to the water heater must be = 130°F
Low Temperature
Bypass with Valve.
Size bypass piping and valve for 2 inches
2.5" dia. for models 1000W and 2000W.
All other models 2" dia.
PRIMERA
2
Main Header Sizing for Two Heaters
Models
400W / 540W
750W
1000W
1200W
Total GPM Min. Pipe Size
60
122
152
92
2" dia.
3" dia.
3.5" dia.
2.5" dia.
1600W
2000W
122
152
3" dia.
3.5" dia.
PRIMERA
1
Use the outlet piping isolation valve to set water heater Δ T and flow rate.
NOTE: Pipe size from this T to each storage tank can be reduced from the main header size, but doing so limits the number of heaters that can operate if one of the tanks is valved off for maintenance.
Size pipe for a velocity of 6 feet per second at the anticipated flow rate.
29
Storage
Tank 1
Storage
Tank 2
Hot Outlet
Exp.
Tank
Cold Inlet
Building Return
34-50 04/02/2010
30 34-50 04/02/2010
31 34-50 04/02/2010
advertisement
* Your assessment is very important for improving the workof artificial intelligence, which forms the content of this project
Key Features
- 1200 watts of heating power for fast and efficient water heating
- High-temperature limit control for safety and peace of mind
- Freeze protection to prevent damage in cold weather
- Compact size for easy installation in any space
- Advanced safety features for reliable operation
Related manuals
Frequently Answers and Questions
What is the capacity of the Primera 1200W?
Does the Primera 1200W have a high-temperature limit control?
Does the Primera 1200W have freeze protection?
Is the Primera 1200W difficult to install?
Are there any advanced safety features on the Primera 1200W?
advertisement