- Industrial & lab equipment
- Welding System
- Spirax Sarco
- PC3000/PC3001 and PC4000/PC4001
- Installation and Maintenance Instructions
Spirax Sarco PC3000/PC3001 and PC4000/PC4001 Installation and Maintenance Instructions
Add to my manuals
20 Pages
Spirax Sarco PC3000/PC3001 and PC4000/PC4001 are pipeline connectors with integral piston valves that are either fully open or fully closed. They are not intended for throttling duties. Ideal for steam, air, or condensate/water applications, these products have a leaktight seal, thanks to a piston that moves actuated by a handwheel and a threaded spindle through two sealing rings with a lantern bush in between. The rising stem of the integral piston valves indicates the amount of valve opening, and the piston ensures a permanent seal during closing operation.
advertisement
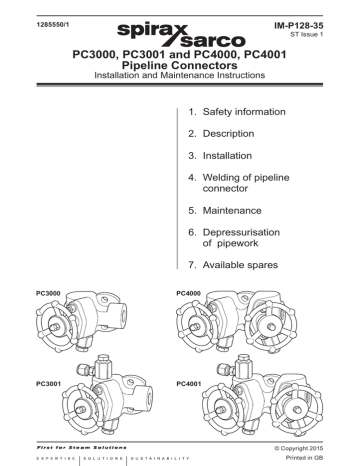
1285550/1
IM-P128-35
ST Issue 1
PC3000, PC3001 and PC4000, PC4001
Pipeline Connectors
PC3000
1. Safety information
2. Description
3. Installation
4. Welding of pipeline
connector
5. Maintenance
6. Depressurisation
of pipework
7. Available spares
PC4000
PC3001
IM-P128-35 ST Issue 1
PC4001
2
IM-P128-35 ST Issue 1
1. Safety information
Safe operation of these products can only be guaranteed if they are properly installed, commissioned, used and maintained by qualified personnel (see
Section 1.11) in compliance with the operating instructions. General installation and safety instructions for pipeline and plant construction, as well as the proper use of tools and safety equipment must also be complied with.
1.1 Intended use
Referring to the Installation and Maintenance Instructions, product markings and
Technical Information Sheet, check that the product is suitable for the intended use / application. These products comply with the requirements of the European
Pressure Equipment Directive 97 / 23 / EC and all fall within category 'SEP'. It should be noted that products within this category are required by the Directive not to carry the mark.
i) These products have been specifically designed for use on steam, air or condensate / water, which is in Group 2 of the above mentioned Pressure
Equipment Directive. The products' use on other fluids may be possible but, if this is contemplated, Spirax Sarco should be contacted to confirm the suitability of the product for the application being considered.
ii) Check material suitability, pressure and temperature and their maximum and minimum values. If the maximum operating limits of the product are lower than those of the system in which it is being fitted, or if malfunction of the product could result in a dangerous overpressure or overtemperature occurrence, ensure a safety device is included in the system to prevent such over-limit situations.
iii) Determine the correct installation situation and direction of fluid flow.
iv) Spirax Sarco products are not intended to withstand external stresses that may be induced by any system to which they are fitted. It is the responsibility of the installer to consider these stresses and take adequate precautions to minimise them.
v) Remove protection covers from all connections and protective film from all name-plates, where appropriate, before installation on steam or other high temperature applications.
1.2 Access
Ensure safe access and if necessary a safe working platform (suitably guarded) before attempting to work on the product. Arrange suitable lifting gear if required.
1.3 Lighting
Ensure adequate lighting, particularly where detailed or intricate work is required.
1.4 Hazardous liquids or gases in the pipeline
Consider what is in the pipeline or what may have been in the pipeline at some previous time. Consider: flammable materials, substances hazardous to health, extremes of temperature.
IM-P128-35 ST Issue 1 3
1.5 Hazardous environment around the product
Consider: explosion risk areas, lack of oxygen (e.g. tanks, pits), dangerous gases, extremes of temperature, hot surfaces, fire hazard (e.g. during welding), excessive noise, moving machinery.
1.6 The system
Consider the effect on the complete system of the work proposed. Will any proposed action (e.g. closing isolation valves, electrical isolation) put any other part of the system or any personnel at risk?
Dangers might include isolation of vents or protective devices or the rendering ineffective of controls or alarms. Ensure isolation valves are opened and closed progressively to avoid system shocks.
1.7 Pressure systems
Before attempting any maintenance of pipeline connectors, ensure that any pressure is isolated and safely vented to atmospheric pressure before attempting any maintenance programme. This is easily achieved by use of the Spirax Sarco depressurisation valves fitted to the assembly (see Section 1.7.1 below and
Section 6). Do not assume that the system is depressurised even when a pressure gauge indicates zero.
1.7.1 Blowdown and depressurisation valves
Blowdown and depressurisation valves are generally used to depressurise a system / vessel prior to maintenance or removal. Do not assume that the system has depressurised even if a pressure guage indicates zero. Consider the direction of the depressurised flow and ensure that this will not cause a hazard to yourself or others.
1.8 Temperature
Allow time for temperature to normalise after isolation to avoid the danger of burns and consider whether protective clothing (including safety glasses) is required.
1.9 Isolation
Consider whether closing isolating valves will put any other part of the system or personnel at risk. Dangers might include; isolation of vents, protective devices or alarms. Ensure isolation valves are turned on and off in a gradual way to avoid system shocks.
1.10 Tools and consumables
Before operating valves ensure that you have the correct tools available. Please see reference table for relevant tooling and the correct torque settings prior to attempting and maintenance.
1.10 Protective clothing
Consider whether you and / or others in the vicinity require any protective clothing to protect against the hazards of, for example, chemicals, high / low temperature, radiation, noise, falling objects, and dangers to eyes and face.
4
IM-P128-35 ST Issue 1
1.11 Permits to work
All work must be carried out or be supervised by a suitably competent person.
Installation and operating personnel should be trained in the correct use of the product according to the Installation and Maintenance Instructions.
Where a formal 'permit to work' system is in force it must be complied with. Where there is no such system, it is recommended that a responsible person should know what work is going on and, where necessary, arrange to have an assistant whose primary responsibility is safety.
Post 'warning notices' if necessary.
1.12 Handling
Manual handling of large and / or heavy products may present a risk of injury. Lifting, pushing, pulling, carrying or supporting a load by bodily force can cause injury particularly to the back. You are advised to assess the risks taking into account the task, the individual, the load and the working environment and use the appropriate handling method depending on the circumstances of the work being done.
1.13 Residual hazards
In normal use the external surface of the product may be very hot. If used at the maximum permitted operating conditions the surface temperature may reach temperatures in excess of 425°C (797°F).
Many products are not self-draining. Take due care when dismantling or removing the product from an installation (refer to 'Maintenance instructions').
1.14 Freezing
Provision must be made to protect products which are not self-draining against frost damage in environments where they may be exposed to temperatures below freezing point.
1.15 Disposal
Unless otherwise stated in the Installation and Maintenance Instructions, this product is recyclable and no ecological hazard is anticipated with its disposal providing due care is taken.
1.16 Returning products
Customers and stockists are reminded that under EC Health, Safety and Environment
Law, when returning products to Spirax Sarco they must provide information on any hazards and the precautions to be taken due to contamination residues or mechanical damage which may present a health, safety or environmental risk. This information must be provided in writing including Health and Safety data sheets relating to any substances identified as hazardous or potentially hazardous.
IM-P128-35 ST Issue 1 5
2. Description
2.1 General
Pipeline connectors PC3000, PC3001 and PC4000, PC4001 have integral piston valves.
A leaktight seal in the piston valve is obtained by a piston, operated by a handwheel and a threaded spindle, moving through two sealing rings separated by a lantern bush. With the piston fully retracted and held only by the upper sealing ring (ensuring no leak path to the environment) the valve is open. With the piston fully inserted and held also by the lower sealing ring (ensuring no leak path between the valve inlet and outlet), the valve is closed. The lantern bush allows flow through the valve whilst maintaining separation between the two sealing rings. Consequently the valve is soft seated, with contact between the piston and rings assured by the stud bolts and the special patented material / composition of the sealing rings (laminated graphite / stainless steel) compensating pressure and temperature variations.
Operation
The integral piston valves should be either fully open or fully closed. They are not intended for throttling duties. The rising stem of the integral piston valves provides an indication of the amount of valve opening.
During closing operation the piston ensures a permanent seal by means of the handwheel.
Therefore during service never remove the handwheel from the threaded bonnet. Due to the large sealing area of the piston valve, it is not necessary to use a valve key to ensure leaktight shut-off.
During opening operation the piston is stopped when the valve is fully open as its top touches the inside of the bonnet.
Operation of the handwheel should always be light.
-
Only when the flow is already cut off do the two cylindrical seating surfaces (lower sealing
-
The piston is always held by at least one ring ensuring no vibration during opening and
-
closing.
The piston is protected against erosive corrosive actions and depositing of foreign matter
when the valve is completely open, being totally retracted through the upper sealing ring.
Standards
These products fully comply with the requirements of the European Pressure Equipment
Directive 97 / 23 / EC.
Certification
These products are available with certification to EN 10204 3.1. Note: All certification / inspection requirements must be stated at the time of order placement. For other certification contact
Spirax Sarco.
Note:
For further product specific data see the following Technical Information Sheets:
- TI-P128-33 for the PC4000 and PC4001
- TI-P128-34 for the PC3000 and PC3001
2.2
Sizes and pipe connections
DN15 and DN20 condensate inlet / outlet connections are available with screwed BSP or
NPT and as a socket weld connection to ASME B16.11 class 3000. Drainage and venting connections have an M18 thread as standard.
Flanged versions are also available upon request. Please contact Spirax Sarco for further details.
6
IM-P128-35 ST Issue 1
PC3000
Upstream trap vent valve with integral strainer screen
Piston isolation valve
*
Please note that the line drain outlet is shown out of position for clarity and that the line drain pipework is to be supplied by the customer.
*
PC3001
Line drainage valve
Piston isolation valve
PC4000
Upstream trap vent valve with integral strainer screen
Upstream trap vent valve with integral strainer screen
2 x Piston isolation valves
Downstream trap depressurisation valve
*
PC4001
Line drainage valve
2 x Piston isolation valves
Fig. 1
IM-P128-35 ST Issue 1
Upstream trap vent valve with integral strainer screen
Downstream trap depressurisation valve
7
2.3 Pressure / temperature limits
(ISO 6552)
Pressure psi g
Steam saturation curve
Pressure bar g
The product must not be used in this region or beyond the parameter of the PMA or TMA of the relative end connection - See notes below.
Notes:
1. If flange connections are fitted then these will limit the maximum and minimum design conditions of the pipeline connector.
2. The maximum operating limits of the complete assembly will be dictated by the steam trap of choice. Reference the specific steam trap technical information sheet for its
'Pressure / temperature limits'.
Body design condition
PMA Maximum allowable pressure
TMA Maximum allowable temperature
Minimum allowable temperature
99.3 bar g @ 38 °C
425
°C @ 56 bar g
-40 °C
62 bar g @ 279 °C
TMO Maximum operating temperature 425 °C @ 56 bar g
Minimum operating temperature -40 °C
Designed for a maximum cold hydraulic test pressure of: 150 bar g
ASME 600
1 440 psi g @ 100 °F
797
°F @ 812 psi g
-40 °F
899 psi g @ 534 °F
797 °F @ 812 psi g
-40 °F
2 175 psi g
8
IM-P128-35 ST Issue 1
3. Installation
Note: Please read 'Safety information', Section 1, before commissioning.
3.1 General
There are two criteria which must be satisfied to ensure that the swivel connector trap will operate correctly and ensure effective condensate removal:
-
The pipeline connector shall be installed with the flow in the direction of the arrow on the connector body. Flow can be horizontal (either direction), vertical or inclined.
-
The connection face for the swivel connector steam trap must always be in the vertical plane.
Ensure that there is sufficient access to the handwheel to allow proper operation.
After installation it is recommended that the pipeline connector is insulated to minimise radiated heat losses and to protect personnel from burns risk.
Note: some trap types should not be insulated.
The PC and trap are joined by a high integrity gasketed joint. It is important that no damage is caused, e.g. by weld, weld splatter, knocks, etc. to the trap gasket face.
Hence care must be taken when installing the PC into the pipework. It is recommended that the trap is installed immediately the PC is in the pipework. Alternatively, the trap can be joined to the PC prior to installation.
3.2 Welding into pipeline of socket weld variants
(Refer to Section 4)
A universal weld procedure covering the requirements of different National and International
Standards and practices is difficult to provide - specifically regarding the welding procedure, welding conditions (run number, consumable size, current, voltage, polarity), storage of consumables and make / type of consumables due to the abundance of appropriate consumable suppliers.
Therefore, this is only advice based on British Standards to be used for guidance on the essential requirements of welding socket weld pipeline connectors into the pipeline.
It is intended that the PC3000 and PC3001 pipeline connectors should only be used on systems where the steam trap discharges directly to atmosphere. If there is any backpressure a separate downstream isolation valve and depressurisation valve should be considered.
The PC4000 and PC4001 pipeline connectors are recommended for all applications in a closed system.
IM-P128-35 ST Issue 1 9
4. Welding of pipeline connector
Note: This is only advice based on British Standards.
The welding of pipeline connector DN15 and DN20 socket weld to pipe DN15 and DN20 schedule 80
Parent material(s)
Description
PC300_ and PC400_ - Austenitic stainless steel with minimum tensile strength up to and including 485 N/mm ².
Pipe - Carbon steel with minimum tensile strength up to and including 430 N / mm ².
Parent material(s) dimensions
DN15
PC Pipe
Specification(s)
ASTM A182 F304L (PC300_ and PC400_)
ASTM A106 Gr B (Pipe)
PC
DN20
Thickness (mm)
8.85
3.73
5.50
O / D (mm)
39.00
21.30
39.00
Pipe is to BS 1600 Schedule 80
Joint type
Socket joint to ASME B16.11 Class 3000 lb (This is equivalent to BS 3799)
Pipe
3.91
26.70
Welding process(es)
Manual Metal Arc (MMA)
Welding position(s)
All: site welded
Weld preparation
Dimensioned sketch
Diametrical clearance 1.0 mm maximum t
PC
1.5 mm approximately
Pipe
Ref.- BS 2633 : 1987 : Section 3.1 and Fig. 9
10
IM-P128-35 ST Issue 1
Welding consumables
Filler material: -
Composition - Low C: 23% Cr: 12% Ni:
Specification - BS 2926: 1984: 23-12 L BR
Shielding gas / flux:
Not applicable
Method of preparation and cleaning
Socket : As supplied and wire brushed.
Pipe : Mechanically cut and wire brushed.
Additional information
1. Fit-up using tack welds.
Parent material temperature
Preheat temperature
Only required when ambient is below 5
°C then
'warm to touch'
Interpass temperature
Not applicable
Post-weld heat treatment
None required
Run sequence and completed weld dimensions
Sketch
This edge is not to be completely melted away
1.4t minimum
PC
Pipe
Ref.- BS 806 : 1990 : Section 4 : Clause 4.7.3
IM-P128-35 ST Issue 1 11
5. Maintenance
Note: Before actioning any maintenance, read 'Safety information', Section 1.
5.1 Introduction
All work must be carried out by a suitably competent person. Before starting work ensure that suitable tools are available.
Use only Spirax Sarco replacement parts.
5.2 Maintenance in service
After the pipeline connector is first put into service or after a change of sealing rings, the bonnet nuts ( 4) should be lightly tightened with the valve in the closed position. Ensure that the bonnet ( 2) is driven down straight during tightening and that care is taken with the handwheel operation.
This operation is to be repeated should any trace of leakage develop. If perfect sealing cannot be achieved in this way, repack the valve following the procedure below.
The handwheel can be unscrewed from the piston valve assembly following the removal of the top nut and domed lock-nut, (item 11).
A washer is located under these nuts and also one between the the handwheel and valve bonnet. During reassembly ensure that these are refitted in the correct locations, by using a suitable anti-seize compound applied to the washers and applying the recommended torque to the nuts - See Table 1, page 19.
The top nut and domed lock-nut (item 11) should be locked together by unscrewing the top nut by an 1/8
th
of a turn whilst maintaining the position of the domed lock-nut.
10
3, 4 + 5
6 2
1
Fig. 2 View showing valve internals
Washer
Top nut
Domed lock-nut
Fig. 3
12
11 Washer
IM-P128-35 ST Issue 1
5.3 Preparation of valve dismantling
If performing maintenance whilst the pipework is hot, wear appropriate protective clothing.
Carefully remove insulation if fitted. It is not necessary to remove the steam trap prior to dismantling the valve.
5.4 Dismantling the valve:
-
Using the handwheel ( 10), fully open the valve.
-
Remove the bonnet nuts ( 4) and washers (5) from studs (3).
-
Carefully turn the handwheel in the closing direction to lift the bonnet ( 2).
-
Rotate the bonnet ( 2) to ensure that the flange bolt holes are misaligned with the studs (3).
-
Turn the handwheel in the opening direction to release the piston ( 6) from the upper and lower sealing rings ( 8 and 9) and so release piston / bonnet sub-assembly from the pipeline connector body ( 1).
-
Examine the piston ( 6) for signs of scoring, corrosion etc. which could affect perfect tightness of the valve.
-
Check other parts for wear / damage and replace if necessary.
Extractor tool
5.5 Repacking the valve:
-
With the valve dismantled, insert the valve internals extractor tool through the upper and lower sealing rings ( 8 and 9) and lantern bush ( 7).
-
Firmly tap to ensure that the tool bottoms out in the bore and with a quarter turn of the handle carefully remove the two sealing rings ( 8 and 9) and the lantern bush (7).
-
Thoroughly clean the sealing rings housing and all the internals.
-
Fit new lower sealing ring ( 9), lantern bush
( 7) and upper sealing ring (8), ensuring they fit perfectly. ( Note: The lower and upper sealing rings are the same.)
-
Apply a thin layer of graphite based grease to threads only (not to internals and piston).
Fig. 4
Plan view of the pipeline connector
illustrating the valve internals extractor tool
IM-P128-35 ST Issue 1 13
5.6 Reassembling the valve
- See Figure 5
:
-
Take the piston valve sub assembly ( 6), lightly inserting it into the pipeline connector body
( 1) and applying an even downwards force using the bonnet assembly (2) over the studs.
-
Fit the belleville washers ( 5) and nuts (4) and evenly tighten the bonnet assembly (2) down to a torque of 12 Nm (8.9 lbf ft).
-
The valve handwheel can now be reinstalled as per the instructions in Section 5.2, paying particular attention to the placement of the washers and torque figures.
-
At this point the backlash of the valve should be tested ensuring it is not more than ¼ of a turn and that the securing nuts do not turn with the handwheel.
5.7 Replacement of steam traps and depressurisation of pipeline
-
See Section 6.
1
4
5
2
6 Studs
Fig. 5
14
IM-P128-35 ST Issue 1
6. Depressurisation of pipework
6.1 Operation of line drainage and depressurisation valves:
The line drain and depressurisation valves are fitted to the PC300_ / PC400_ series of pipeline connectors to provide safe and reliable venting / bypassing of the steam trap.
BDV2 Always fitted to upstream trap vent connections, to ensure a safe downward discharge.
For further details on the operation of BDV valves see TI-P600-01 and IM-P600-02.
Note: It is important to ensure that the discharge from all pressurised systems are directed to a safe position and that correct safety precautions are taken when operating the valves.
(See Section 1,'Safety information').
6.2 To remove / replace a steam trap fitted to:
PC3000 and PC3001 pipeline connectors:
-
Close the upstream isolation valve ( A).
-
Open the line drain valve ( B) to keep the steam line drained.
-
If fitted on a system which does not discharge directly to atmosphere, ensure that any downstream pressure is isolated and depressurised before continuing. A PC400_ connector should be considered.
-
If fitted open the trap vent valve ( C) to relieve pressure.
-
After removal of the plastic protector (on new traps) replace the steam trap and tighten the bolts to the recommended torque of 33 Nm (24.3 lbf ft).
-
Close the blowdown / line drain valves ( B) and (C) and then slowly open valve (A) checking for leaks.
-
If no leaks are detected open valve ( A) completely.
PC3000
A
A. Upstream isolation
B. Upstream line drain (with integral strainer)
C. Steam trap vent
D. Downstream isolation
E. Downstream trap test
C
PC3001
B
A
B
Fig. 6
IM-P128-35 ST Issue 1 15
6.3 To remove / replace a steam trap fitted to:
PC4000 and PC4001 pipeline connectors:
-
Close the upstream and downstream isolation valves ( A) and (D).
-
Open the line drain valve ( B) to keep the upstream line drained.
-
If fitted open the trap vent valve ( C) and trap test valve (E) to relieve pressure.
-
After removal of the plastic protector (on new traps), replace the steam trap ensuring the
gasket and gasket faces are clean, tighten the bolts to the recommended torque of
33 Nm (24.3 lbf ft).
-
Close valves ( C) and (E) and the close line drain valve (B).
-
Open valve ( D) fully, then slowly open valve (A) checking for leaks.
-
If no leaks are detected open valve ( A) completely.
PC4000
A
D
B
C
A. Upstream isolation
B. Upstream line drain (with integral strainer)
C. Steam trap vent
D. Downstream isolation
E. Downstream trap test
A
E
PC4001
D
Fig. 7 B
E
6.4 Steam trap testing
The depressurisation valve ( E) (on PC4000 series only) can be used for steam trap testing.
Open the valve screw and observe the discharge from the valve to ensure correct operation of the steam trap When observation is complete close the screw and tighten to the recommended torque.
16
IM-P128-35 ST Issue 1
6.5 Strainer screen replacement
-
Identify the upstream drain where the strainer screen is fitted, valve ( B).
-
Isolate the live steam supply through the closure of valve ( A).
-
Drain any residue pressure through opening valve ( B) and where fitted and if required open valve ( C) to keep the upstream line drained.
-
It is now possible to remove valve ( B) and replace the integral strainer screen, ensuring correct fitment into the valve body.
-
Upon refitting use a new graphite gasket and ensure the micro grooved gasket face is clean and undamaged.
-
The upstream drain valve ( B) can now be tightened to the recommended torque:
74 - 78 N m (55 - 58 lbf ft).
C
A
Fig. 8
IM-P128-35 ST Issue 1
B
Please note when isolating the unit for strainer screen replacement drain any residue pressure through opening valve ( B) DO NOT break open the upstream drain until
it has been drained.
17
7. Available spares
Spare parts
Please note that the available spare parts are the same for the PC300_ and PC400_ pipeline connectors. The spare parts available are shown in heavy outline. Parts drawn in broken line are not supplied as spares. For ease of replacement an extractor tool is available for removing the sealing rings.
Available spares
Sealing ring set
Piston valve assembly
Piston valve sub-assembly
Extractor tool
PC depressurisation valve and gasket
PC line drain valve and gasket
Strainer screen and gasket (packet of 3)
Valve gasket set (packet of 10)
PC depressurisation valve, gasket and strainer
8 and 9
2, 4, 5, 6, 7, 8, 9, 10, 11 and 12
6, 7, 8 and 9
See Figure 3 on page 13
14
15
22 and 23
22
14, 21 and 22
How to order spares
Always order spares by using the description given in the column headed 'Available spares' and state type and size of equipment.
Examples:
1 off Sealing ring set for an integral piston valve on a PC3000 pipeline connector having
DN15 socket weld connections.
or
1 off Sealing ring set for an integral piston valve on a PC4000 pipeline connector having
DN15 socket weld connections.
4
5
2
10
11
12
12
Fig. 9
18
IM-P128-35 ST Issue 1
Table 1 Recommended tightening torques
Item or mm
4
11
14 and 15
14
10
24
" x 18 UNC
M6
M18
N m
12
12
74 - 78
lbf ft
8.9
8.9
55 - 58
PC4001 shown
6
8
7
9
21
22
15
22
*
*
*
The bolts are supplied with the steam trap of choice.
14
IM-P128-35 ST Issue 1 19
20
IM-P128-35 ST Issue 1
advertisement
* Your assessment is very important for improving the workof artificial intelligence, which forms the content of this project
Related manuals
advertisement