advertisement
▼
Scroll to page 2
of
39
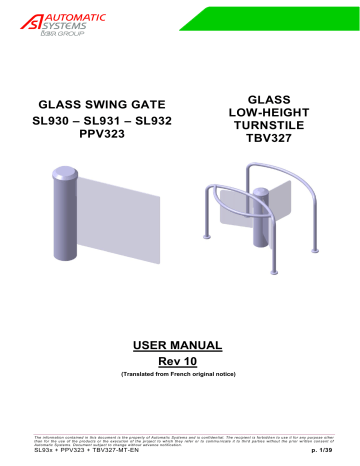
GLASS SWING GATE SL930 – SL931 – SL932 PPV323 GLASS LOW-HEIGHT TURNSTILE TBV327 USER MANUAL Rev 10 (Translated from French original notice) The informat ion conta ined in th is docu ment is the property of Automat ic Syst ems and is conf ident ial. The recip ient is forb idd en to use it for any purpose ot her than for the use of the products or the execut ion of the project to wh ich th ey refer or to commu nicate it to th ird parties without the pr ior wr itten conse nt of Automat ic Systems. Document sub ject to change without advance not if icat ion . SL93x + PPV323 + TBV327-MT-EN p. 1/39 Document changes Rev. Date Written 00 2006-12-12 MFy 01 2007-04-23 Mfy 02 2007-06-25 2010-06-11 Mfy 04 2010-07-01 Mfy 2010-07-02 RWK + JB Mfy 03 05 Checked Mfy RWK+HB+DL RH Subject Initial version - Page 15 (locking): “locked under voltage”. - Parameter 60°, 90°, rotating): add range and default value. - Input 2: “Pitch of encoder 80”. - Page 25 (point 3): “remove the screws (31)”. - Page 5 (1 point): “Folded and soldered stainless steel plate housing”. - Pages 11, 13, 15, 19: replace the terms “suction device” and “suction mechanism” by “hold magnet”. - Pages 15 & 34: translate electric diagrams in English. - Complete revision for adaptation to the modification realized on the equipment. - Tec. Spec: replace flow by opening time of the obstacles. - Non-return lock option for TBV only. - Installation: Last points of the Fixing procedure transferred to Electrical connections and Commissioning chapters. - Preventive maintenance: check power leakage and evacuation. st 06 2011-01-17 Mfy - SL932 added in: · Title p1, · Table ch.2.1, · Installation plan ch.3.2, · Spare parts ch.5.4, · EC certificate ch.7. 07 2012-01-09 Mfy - Ch. 2.1: MCBF, IP, CE, DAS added. 08 2012-10-03 Mfy - Parts related to PPV322 & TBV326 removed from spare parts. 09 2013-04-03 Mfy - Spare parts: conical coupling + references to illustrations added. - Ch. 5.10. adapted to software version v5.36. - Ch.5.11. added (Maintenance Interface). - Electrical diagrams adapted to CPU v16 + Power board v10. - Ch. 5.4. : update spare parts table. 10 2013-08-28 SLu YC + RWK The informat ion conta ined in th is docu ment is the property of Automat ic Syst ems and is conf ident ial. The recip ient is forb idd en to use it for any purpose ot her than for the use of the products or the execut ion of the project to wh ich th ey refer or to commu nicate it to th ird parties without the pr ior wr itten conse nt of Automat ic Systems. Document sub ject to change without advance not if icat ion . SL93x + PPV323 + TBV327-MT-EN p. 2/39 Table of Contents 1. SAFETY INSTRUCTIONS 4 2. DESCRIPTION 5 2.1. Technical Specifications 2.2. Location of the components 3. INSTALLATION 3.1. 3.2. 3.3. 3.4. 3.5. Storage Installation plans Fixing the equipment to the floor Electrical connections Commissioning 4. PRINCIPLE OF OPERATION 4.1. Locking 4.2. Position encoder 4.3. Safety 5. MAINTENANCE 5.1. Removing the housing 5.2. Turning the equipment ON/OFF 5.3. Preventive maintenance 5.4. Spare parts 5.5. Adjusting the locking sensor 5.6. Adjusting the obstacle closed point 5.7. Setting the movement limit stops (5, p6) 5.8. Fitting and adjusting the locking mechanism 5.9. Replacing an obstacle 5.10. Control unit menu (program v5.36) 5.11. Maintenance interface 5.11.1. Network communication settings 5.11.2. Login 5.11.3. Status 5.11.4. Identification 5.11.5. Commands 5.11.6. Network 5.11.7. Menu Configuration 5.12. Trouble shooting 5.13. Disposal / Destruction 5 6 7 7 8 11 12 13 14 15 16 16 17 17 18 18 19 20 21 21 22 25 26 29 29 29 30 30 30 31 31 32 33 6. ELECTRICAL DIAGRAMS 34 7. DECLARATION OF CONFORMITY 38 The informat ion conta ined in th is docu ment is the property of Automat ic Syst ems and is conf ident ial. The recip ient is forb idd en to use it for any purpose ot her than for the use of the products or the execut ion of the project to wh ich th ey refer or to commu nicate it to th ird parties without the pr ior wr itten conse nt of Automat ic Systems. Document sub ject to change without advance not if icat ion . SL93x + PPV323 + TBV327-MT-EN p. 3/39 1. SAFETY INSTRUCTIONS The SL93x, PPV323 and TBV327 gates and turnstiles are intended for the access control of users and cannot be otherwise used without risk for the user or for the integrity of the equipment. They are intended for light traffic applications (cf. technical specifications, ch.2.1. ) It is mandatory to let the equipment complete its opening and closing cycles automatically (without pushing the obstacle) to avoid untimely out of order. All operations on the equipment must be carried out by qualified personnel. Any unauthorized operation, or operation carried out by a technician not qualified on this product, voids the manufacturer’s guarantee automatically. Access to the mechanism must be limited to personnel aware of the electrical and mechanical risks that are incurred by negligent action. If possible, disconnect the electrical supply before opening the enclosure. Otherwise, turn the power off by means of the circuit breaker located on the power board (ch.5.2. ). WARNING: In both cases, wait 5 minutes before working inside the equipment (capacitors discharge)! Any internal element likely to be put under voltage or to move must be handled with caution. The equipment is configured in a minimal risk mode for its users. Any changes to the parameters must be carried out with full knowledge of the facts by qualified personnel and are not the responsibility of Automatic Systems. The informat ion conta ined in th is docu ment is the property of Automat ic Syst ems and is conf ident ial. The recip ient is forb idd en to use it for any purpose ot her than for the use of the products or the execut ion of the project to wh ich th ey refer or to commu nicate it to th ird parties without the pr ior wr itten conse nt of Automat ic Systems. Document sub ject to change without advance not if icat ion . SL93x + PPV323 + TBV327-MT-EN p. 4/39 2. DESCRIPTION 2.1. Technical Specifications AISI 304 stainless steel sheet housing. Internal frame protected with epoxy coating. Passage obstacle in clear toughened glass, thickness: 10 mm. Electrical supply: single phase, 230 VAC, 50 Hz (not to be connected to a floating network or to high-impedance earthed industrial distribution network). Consumption: 0.12 A in closed and locked position, 0.50 A when turning, 0.90 A while locking. Automatic obstacle unlocking on power failure. Variable speed controller ensures smooth obstacle movements. Obstacle position determined by encoder. Operating temperature: -20(*) to +60°C (*Thanks to the heat generated by the powered internal equipment). RH < 95%, without condensation. Minimum opening time of the obstacle (adjustable): 2.5 seconds. Net weight (kg): PPV323 SL930 1m SL930 1.2 m SL931 1.4 m SL931 1.7 m SL931 1.9 m SL932 0.9m TBV327 Column 62 62 62 77 77 77 62 77 Panels 17 19 24 29 36 40 17 3 x 8.4 Total 79 81 86 106 113 117 79 102 MCBF (Mean Cycles Between Failures), when respecting recommended maintenance: 1,000,000 cycles IP 51 EC compliant. DAS Certified (Powered Security Device) in accordance with Fire Safety NF S 61-937 standard Gates and turnstiles control pedestrian access in both directions. By definition, Direction A is the direction in which the controls are located on the right of the user (=> obstacle opening in the clockwise direction). Direction A = clockwise The informat ion conta ined in th is docu ment is the property of Automat ic Syst ems and is conf ident ial. The recip ient is forb idd en to use it for any purpose ot her than for the use of the products or the execut ion of the project to wh ich th ey refer or to commu nicate it to th ird parties without the pr ior wr itten conse nt of Automat ic Systems. Document sub ject to change without advance not if icat ion . SL93x + PPV323 + TBV327-MT-EN p. 5/39 2.2. Location of the components 3 13 1. Mounting base (attached to the floor) 2. Main chassis (= equipment without obstacle) 3. Obstacle (= glass panel) 4. Conical coupling of the rotor to the motor 5. Movement limit stop (not on TBV) 6. Variable speed controller 7. Locking system 8. Position encoder 9. Power supply board 10. Control board v16 (CPU) 12 4 (illustrated with optional IP module) 2 IP option 5 6 7 11. Regulated power supply 12. Obstacle support rotor 13. Additional support for high obstacle (for SL931 only) 14. Motor 15. Serial plate 14 8 15 (rear) 10 11 9 (rear) 1 The informat ion conta ined in th is docu ment is the property of Automat ic Syst ems and is conf ident ial. The recip ient is forb idd en to use it for any purpose ot her than for the use of the products or the execut ion of the project to wh ich th ey refer or to commu nicate it to th ird parties without the pr ior wr itten conse nt of Automat ic Systems. Document sub ject to change without advance not if icat ion . SL93x + PPV323 + TBV327-MT-EN p. 6/39 3. INSTALLATION The installation must be carried out in accordance with the safety instructions (p 4) and the installation plan (p3.2. ). 3.1. Storage Before installation, avoid all shocks to the equipment and place it in its original packing in a dry place, protected from dust, heat and bad weather. Storage temperature limits: -30 to +80°C The informat ion conta ined in th is docu ment is the property of Automat ic Syst ems and is conf ident ial. The recip ient is forb idd en to use it for any purpose ot her than for the use of the products or the execut ion of the project to wh ich th ey refer or to commu nicate it to th ird parties without the pr ior wr itten conse nt of Automat ic Systems. Document sub ject to change without advance not if icat ion . SL93x + PPV323 + TBV327-MT-EN p. 7/39 3.2. Installation plans The informat ion conta ined in th is docu ment is the property of Automat ic Syst ems and is conf ident ial. The recip ient is forb idd en to use it for any purpose ot her than for the use of the products or the execut ion of the project to wh ich th ey refer or to commu nicate it to th ird parties without the pr ior wr itten conse nt of Automat ic Systems. Document sub ject to change without advance not if icat ion . SL93x + PPV323 + TBV327-MT-EN p. 8/39 The informat ion conta ined in th is docu ment is the property of Automat ic Syst ems and is conf ident ial. The recip ient is forb idd en to use it for any purpose ot her than for the use of the products or the execut ion of the project to wh ich th ey refer or to commu nicate it to th ird parties without the pr ior wr itten conse nt of Automat ic Systems. Document sub ject to change without advance not if icat ion . SL93x + PPV323 + TBV327-MT-EN p. 9/39 The informat ion conta ined in th is docu ment is the property of Automat ic Syst ems and is conf ident ial. The recip ient is forb idd en to use it for any purpose ot her than for the use of the products or the execut ion of the project to wh ich th ey refer or to commu nicate it to th ird parties without the pr ior wr itten conse nt of Automat ic Systems. Document sub ject to change without advance not if icat ion . SL93x + PPV323 + TBV327-MT-EN p. 10/39 3.3. Fixing the equipment to the floor B C A 2 1 B C V A 1. Remove the 2 covers by removing the screws (50, p 25). 2. Unscrew the base (1, p 6) from the main chassis and secure it to the floor with the 3 expanding bolts supplied (Liebig B15/30 (A)). First drill 3 x 15 mm diameter holes to a depth of 85 mm. WARNING: It is essential to adapt the fastening hardware and the installation procedure to the environment and the nature of the floor on which the gate will be positioned. Installation must be validated by certified civil engineers. The gate must be fastened to the floor before it is made available to the users! Automatic Systems cannot be held responsible for any accident or damage to the gate due to the fact that the gate was not adequately fastened to the floor. 3. Position the main chassis (2, p 6) over the base (1), with the sticker COTE DU PASSAGE (=Passageway side) aligned as shown below, so that the control board (10, p 6) remains accessible. 4. Fit the obstacle(s) to the rotor (see ch.5.9. ). 5. Adjust the vertical alignment of the main chassis with the 3 bolts (B). 6. Tighten the 3 locknuts (C) to secure the main chassis to the base (tightening torque: 43 Nm). 7. Cut the cable tie securing the locking mechanism (7, p 6). The informat ion conta ined in th is docu ment is the property of Automat ic Syst ems and is conf ident ial. The recip ient is forb idd en to use it for any purpose ot her than for the use of the products or the execut ion of the project to wh ich th ey refer or to commu nicate it to th ird parties without the pr ior wr itten conse nt of Automat ic Systems. Document sub ject to change without advance not if icat ion . SL93x + PPV323 + TBV327-MT-EN p. 11/39 3.4. Electrical connections WARNING: The operations must be undertaken in accordance with the safety warnings, ch.1. In particular, the mains must be shut down before any of the work described below is begun. Connections must be executed in accordance with the wiring diagrams provided inside the equipment, which remain the reference. Type of cable Connections 3G2.5² Electrical power supply of each equipment (230 V single phase + ground + differential breaker 30 mA min for each equipment). WARNING: High leakage current. => Connection to the ground imperative with a 1-mm² cable before connecting the mains. => Do not connect several equipments to the same differential breaker. Δ 30 mA Δ 30 mA 230 VAC - 50 Hz 2.5² If the gates are powered through long cables, ensure the equipotential bonding between the gates forming a bank by connecting them with a 1mm² ground wire. 0.75² Connect the Emergency command (Fire) if desired. Refer to the electrical diagrams. 0.75² Connect the opening commands and eventual Inputs/Outputs. Refer to the electrical diagrams. The informat ion conta ined in th is docu ment is the property of Automat ic Syst ems and is conf ident ial. The recip ient is forb idd en to use it for any purpose ot her than for the use of the products or the execut ion of the project to wh ich th ey refer or to commu nicate it to th ird parties without the pr ior wr itten conse nt of Automat ic Systems. Document sub ject to change without advance not if icat ion . SL93x + PPV323 + TBV327-MT-EN p. 12/39 3.5. Commissioning 1. Adjust the obstacle opening angle in the clockwise and anti-clockwise directions by adjusting the mechanical stops (ch.5.7. ). 2. Switch ON the equipment. The obstacle will move, seeking its starting point (closed position), then it locks. 3. Start the CONFIG AUTO menu (Note: the obstacles must be fitted): Press the Menu button, Press the > button until CONFIG AUTO is displayed, Press OK to start the procedure The equipment seeks the mechanical stops in both directions at slow speed and accelerates. 4. Check the locking by pushing the obstacle. 5. Give a clockwise opening command. 6. Give a counter-clockwise opening command. 7. Trigger a FIRE command (open the Fire contact on the power board, see electric diagrams) and check if the obstacle opens (the opening direction is adjustable, cf. ch.5.10. ). 8. Turn off the power and check that the obstacle unlocks. 9. Replace the covers. The informat ion conta ined in th is docu ment is the property of Automat ic Syst ems and is conf ident ial. The recip ient is forb idd en to use it for any purpose ot her than for the use of the products or the execut ion of the project to wh ich th ey refer or to commu nicate it to th ird parties without the pr ior wr itten conse nt of Automat ic Systems. Document sub ject to change without advance not if icat ion . SL93x + PPV323 + TBV327-MT-EN p. 13/39 4. PRINCIPLE OF OPERATION The references in this chapter refer to the illustrations on ch.2.2. The Swing Gates and Turnstiles (named hereafter "Gates") are bidirectional pivoting access control units that allow passage in both directions. They have a steel central column (2) fixed to the floor containing the control board (10) and the drive unit. The central column is equipped with 1 or 3 glass obstacles (3). The gate is unlocked by an external command (pushbutton, card readers, etc.). According to the selected mode, the obstacle then starts to turn automatically (in the authorized direction of passage) or on light pressure. The movement of the obstacle is transmitted by a geared motor driven by a variable speed controller (6), which allows the opening and closing speed to be adjusted. The opening angle can be adjusted in both directions and 2 mechanical stops maintain the obstacles open. The direction of rotation and the position of the obstacle are determined by a position encoder (8). The obstacle stays open for a period set by a parameter and then closes again automatically. Movement sequence: The obstacle opens from the starting point (= passage closed) at the selected speed. From the B RAKING A NGLE (set by the program according to the selected speed and the obstacle inertia), the obstacle decelerates to complete its movement against the mechanical stop. The obstacle registers a stopping time (set by parameter) in the open position. The obstacle is maintained at low power against the limit stop. The obstacle closes at the selected speed. From the B RAKING A NGLE , the obstacle decelerates to complete its movement. When the obstacle reaches its closed position, the lock is engaged. Closed (= 0°) Dir. B Dir. A Braking angle for closing opening angle A way Opening angle B way Braking angle for opening O PENING ANGLE A WAY S TOP T IME D ELAY Angle parameters The parameters are the same for clockwise and counter-clockwise opening directions. The informat ion conta ined in th is docu ment is the property of Automat ic Syst ems and is conf ident ial. The recip ient is forb idd en to use it for any purpose ot her than for the use of the products or the execut ion of the project to wh ich th ey refer or to commu nicate it to th ird parties without the pr ior wr itten conse nt of Automat ic Systems. Document sub ject to change without advance not if icat ion . SL93x + PPV323 + TBV327-MT-EN p. 14/39 4.1. Locking The locking mechanism (70) is activated by an electromagnet (71) with positive security (locked under voltage). When the obstacle approaches its closed position, the locking sensor (75) is activated by detection of a vane (76). The electromagnet then moves the lock into hole (77a) of plate (77), locking the rotor (12). Locking is maintained by the electrical circuit between the hold magnet (72) and the contact plate (73). The Fire Detection signal on the power board (see wiring diagrams) opens the obstacle in the selected direction and allows free passage. 77 77 77a 77b 69 70 68 73 72 71 76 75 69 NON-RETURN OPTION (for TBV model only*): During the opening in one direction, if the obstacle is forced to open in the other direction, the electromagnet (68) moves the non-return lock (69) into hole (77b) of plate (77), locking the rotor (12). The correct movement continues as soon as this reverse force is removed (without putting the equipment out of service). (*) This option is not available on SL93x because the flow direction is not controlled . The informat ion conta ined in th is docu ment is the property of Automat ic Syst ems and is conf ident ial. The recip ient is forb idd en to use it for any purpose ot her than for the use of the products or the execut ion of the project to wh ich th ey refer or to commu nicate it to th ird parties without the pr ior wr itten conse nt of Automat ic Systems. Document sub ject to change without advance not if icat ion . SL93x + PPV323 + TBV327-MT-EN p. 15/39 4.2. Position encoder The direction of rotation and the position of the obstacle are determined by a position encoder (80), consisting of a vaned disk that turns with the motor shaft and passes through 2 sensors (81 and 82). This encoder does not need any adjustment. 80 81 82 4.3. Safety During rotation, if the obstacle encounters an obstruction limiting its movement, it will make several attempts to complete the current movement, after which the motor will be powered off automatically if the resistance is still present (see parameter NUMBER OF W ARNINGS, ch.5.10. ). As long as the opening command is maintained, the obstacle will not close. When a second opening command is received in the same direction while the obstacle is closing, it will re-open immediately. When an Emergency command (FIRE) is received, the gate opens automatically (the direction of opening is set by parameter DIR. EMERGE. OPENING, ch.5.10. ). When there is a power failure, the gate is unlocked automatically and can then be opened manually. The informat ion conta ined in th is docu ment is the property of Automat ic Syst ems and is conf ident ial. The recip ient is forb idd en to use it for any purpose ot her than for the use of the products or the execut ion of the project to wh ich th ey refer or to commu nicate it to th ird parties without the pr ior wr itten conse nt of Automat ic Systems. Document sub ject to change without advance not if icat ion . SL93x + PPV323 + TBV327-MT-EN p. 16/39 5. MAINTENANCE WARNING: The adjustment operations must be carried out in accordance with the safety instructions (p 4). 5.1. Removing the housing 1. Remove all the screws (50). 2. Remove both elements of the housing. 50 The informat ion conta ined in th is docu ment is the property of Automat ic Syst ems and is conf ident ial. The recip ient is forb idd en to use it for any purpose ot her than for the use of the products or the execut ion of the project to wh ich th ey refer or to commu nicate it to th ird parties without the pr ior wr itten conse nt of Automat ic Systems. Document sub ject to change without advance not if icat ion . SL93x + PPV323 + TBV327-MT-EN p. 17/39 5.2. Turning the equipment ON/OFF ON OFF 5.3. Preventive maintenance Every 100,000 operations, or every 6 months, whichever comes first, check the following points: The security of all components (attachment to the floor, obstacle, motor, conical coupling (4, p 6), etc.). The state of the ground cable on the rotor (Fig. A). Fig. A: connection of the rotor to the ground The control signals. The opening and closing speeds. The obstacle opening and closing angles and positions. The activation of the locking mechanism in the closed position. The unlocking in case of a power outage. The obstacle opening in case of an emergency command (opening of the Fire contact on the power board, see electric diagrams). Any output signals to optional peripheral equipment. Clean the stainless steel surfaces and glasses by means of an appropriate product. Every 800,000 operations, replace the locking mechanism (ch.5.8. ). The informat ion conta ined in th is docu ment is the property of Automat ic Syst ems and is conf ident ial. The recip ient is forb idd en to use it for any purpose ot her than for the use of the products or the execut ion of the project to wh ich th ey refer or to commu nicate it to th ird parties without the pr ior wr itten conse nt of Automat ic Systems. Document sub ject to change without advance not if icat ion . SL93x + PPV323 + TBV327-MT-EN p. 18/39 5.4. Spare parts DESIGNATION Conical coupling (4, p6) Contact plate (73, p 15) CPU board (10, p6) Electromagnet (71, p 15) Frequency inverter 230V Frequency inverter 230V (6, p 6) Hall-effect sensor (75, p15 & 82, p16) Holder electromagnet (72, p 15) Locking assembly (p 22) Locking disc (77, p 15) Long lock in aluminum (21, p22) Mobile obstacle 1030 x 850 mm Mobile obstacle 1230 x 850 mm Mobile obstacle 1530 x 850 mm Mobile obstacle 1730 x 850 mm Mobile obstacle 480 x 640 mm Mobile obstacle 640 x 950 mm Mobile obstacle 830 x 850 mm Motor assembly with encoder (14 + 8, p6) Motor assembly with encoder (14 + 8, p6) Non-return lock (69, p15) Obstacle mobile 740 x 850 mm Optocoupler on CPU board Power supply board V3 (9, p 6) Power supply board V5 (9, p 6) Short lock in stainless steel (21, p22) Stabilized Power supply (11, p 6) Stainless steel cover Stainless steel cover (cut-out) Stainless steel cover (cut-out) Stainless steel cover (cut-out) Stainless steel cover (straight) Stainless steel cover (straight) Stainless steel cover (straight) Stainless steel top cover Stainless steel top cover CODE VALIDITY PPV323 SL930 SL931 SL932 TBV327 0/6980/816 0/6982/071 E/6980/530 E/6980/540 0/6982/066 E/6980/538 E/6980/531 E/6980/520 E/6980/542 0/6980/583 0/6982/068 OBV-E07047 OBV-E07050 OBV-E07030 OBV-E07049 OBV-E07054 OBV-E07052 OBV-E07014 0/6982/065 E/6980/541 0/6980/658 E/0875/023 E/6980/539 E/6980/537 0/6982/064 0/6982/069 E/6980/536 0/6980/542 0/6980/545 CRA-E01122 0/6980/547 0/6980/546 CRA-E01124 0/6980/548 0/6980/549 CRA-E01107 > 01/2007 > 01/2007 > 01/2007 > 01/2007 > 12/2008 < 12/2008 > 01/2007 > 01/2007 > 01/2007 > 01/2007 < 08/2008 > 01/2007 > 01/2007 > 01/2007 > 01/2007 > 01/2007 > 01/2007 > 01/2007 > 12/2008 < 12/2008 > 01/2007 >01/2007 > 01/2007 < 10/2009 > 10/2009 > 08/2008 > 01/2007 > 01/2007 < 01/2007 > 01/2007 > 01/2007 < 01/2007 > 01/2007 > 01/2007 < 01/2007 > 01/2007 x x x x x x x x x x x x x x x x x x x x x x x x x x x x x x x x x x x x x x x x x x x x x x x x x x x x x x x x x x x x x x x x x x x x x x x x x x x x x x x x x x x x x x x x x x x x x x x x x x x x x x x x x x x x x x x x x x x x x x x x x x x x The informat ion conta ined in th is docu ment is the property of Automat ic Syst ems and is conf ident ial. The recip ient is forb idd en to use it for any purpose ot her than for the use of the products or the execut ion of the project to wh ich th ey refer or to commu nicate it to th ird parties without the pr ior wr itten conse nt of Automat ic Systems. Document sub ject to change without advance not if icat ion . SL93x + PPV323 + TBV327-MT-EN p. 19/39 5.5. Adjusting the locking sensor Locking holes 12 70 78 75 76 79 1. Unlock the obstacle by switching off the power or selecting programming mode. 2. Turn rotor (12) until one of the 3 locking holes is in front of lock (70). 3. In that position, the sensor (75) must detect one of the vanes (76). If necessary, adjust the vane and/or the vane support ring (79). 4. For the TBV327, repeat the procedure for the 2 remaining locking holes. The informat ion conta ined in th is docu ment is the property of Automat ic Syst ems and is conf ident ial. The recip ient is forb idd en to use it for any purpose ot her than for the use of the products or the execut ion of the project to wh ich th ey refer or to commu nicate it to th ird parties without the pr ior wr itten conse nt of Automat ic Systems. Document sub ject to change without advance not if icat ion . SL93x + PPV323 + TBV327-MT-EN p. 20/39 5.6. Adjusting the obstacle closed point 1. Close and lock the obstacle. E 2. Loosen the 6 screws (D) on the conical coupling (4, p6) for 3 mm. D 3. Tighten the 3 screws (E) in the upper ring so that the 2 parts of the coupling are separated. Note: if the screws (E) are not supplied, use 3 screws (D). 4. Move the obstacle to its closed position. 5. Unscrew the 3 screws (E) and tighten the other 6 (D). 5.7. Setting the movement limit stops (5, p6) Note: there are no stops for the TBV327turnstile! Note: Check that the obstacle operating angle allowed by the stops is greater than the angle set by the OPENING ANGLE CLOCKWISE and OPENING ANGLE ANTI-CLOCKWISE parameters (ch.5.10. ). 1. Switch off the power. 2. Loosen screw (41) on cams (40) and (43). 3. Bring the obstacle to the desired position in one opening direction. Bring cam (40) against stop (42), then position the cam 3 mm back from the stop and tighten screw (41). 4. Adjust the second cam (43) in the same way for the other opening direction. 5. Start an AUTOMATIC SETUP in the control unit (ch.5.10. ) 42 40 41 43 The informat ion conta ined in th is docu ment is the property of Automat ic Syst ems and is conf ident ial. The recip ient is forb idd en to use it for any purpose ot her than for the use of the products or the execut ion of the project to wh ich th ey refer or to commu nicate it to th ird parties without the pr ior wr itten conse nt of Automat ic Systems. Document sub ject to change without advance not if icat ion . SL93x + PPV323 + TBV327-MT-EN p. 21/39 5.8. Fitting and adjusting the locking mechanism a. Slacken the lock-nut (36) and screw the lock (21) completely onto the threaded rod (22), 21 b. Unscrew 4 turns. a b 22 36 Unscrew the sleeve (23), pass the rod through the plate and tighten the sleeve. 23 Turn the obstacle rotor (12), p6 so that the lock (21) lines up with a locking hole (cf. ch.5.5. ). 24 Turn the sleeve (23) until it is 9 mm above the plate level and lock it with nut (24). 9 mm Screw completely the lock (21). Slightly tighten nut (25) to hold the spacer (26). Firmly tighten nut (27) against nut (25) to lock the plate (28) in position. 27 28 25 26 The informat ion conta ined in th is docu ment is the property of Automat ic Syst ems and is conf ident ial. The recip ient is forb idd en to use it for any purpose ot her than for the use of the products or the execut ion of the project to wh ich th ey refer or to commu nicate it to th ird parties without the pr ior wr itten conse nt of Automat ic Systems. Document sub ject to change without advance not if icat ion . SL93x + PPV323 + TBV327-MT-EN p. 22/39 Fit the electromagnet assembly to plate (28) by means of screw (29). 29 Put the fixing screws (30) in place, without tightening them. 30 31 Push in the electromagnet core (31) to bring the centre shaft (32) in contact with the stop (33). 32 33 The informat ion conta ined in th is docu ment is the property of Automat ic Syst ems and is conf ident ial. The recip ient is forb idd en to use it for any purpose ot her than for the use of the products or the execut ion of the project to wh ich th ey refer or to commu nicate it to th ird parties without the pr ior wr itten conse nt of Automat ic Systems. Document sub ject to change without advance not if icat ion . SL93x + PPV323 + TBV327-MT-EN p. 23/39 With the obstacle in its locked position (lock 21 engaged into a hole), the contact plate (34) must lie on the hold magnet (35). Check that the electro-magnet core (31) does not touch the steel frame; if so, move the complete lock assembly away from the frame. Fix the lock assembly to the plate by tightening screws (30). In the locked position (activate the lock by pushing core (31) and not contact plate (34)!), adjust the lock (21) until it is as far as possible into the hole: the contact plate (34) must smoothly lie on hold magnet (35), without forcing. If not the case, adjust the hold magnet support height by means of the screws (38). Check the same adjustment for the 2 remaining locking holes. 34 frame 35 31 36 Fix the lock (21) by firmly tightening nut (36). Fit the return spring (37). 37 Adjust the centering of contact plate (34) with respect to hold magnet (35) by carefully bending the contact plate’s arm. 34 35 38 Connect the red cable to the contact plate exactly as shown in the picture. The cable must be not snag during the movement of contact plate (34). The informat ion conta ined in th is docu ment is the property of Automat ic Syst ems and is conf ident ial. The recip ient is forb idd en to use it for any purpose ot her than for the use of the products or the execut ion of the project to wh ich th ey refer or to commu nicate it to th ird parties without the pr ior wr itten conse nt of Automat ic Systems. Document sub ject to change without advance not if icat ion . SL93x + PPV323 + TBV327-MT-EN p. 24/39 5.9. Replacing an obstacle 1. Remove the 2 parts of the housing by unscrewing the screws (50). 2. Hold the glass plate. 3. Remove the screws (51) maintaining the glass on its support. 4. Remove the clamp (52). 5. Remove the glass plate. 6. Remove the spacers (53) from the holes in the glass plate that has been removed and fit them to the new glass plate. 7. Attach the new glass plate in the reverse order. Do not forget the cork gaskets between metal and glass. The glass edge must be parallel to the frame. Tightening torque: 45 Nm min. 52 53 51 50 Align parallel with the frame The informat ion conta ined in th is docu ment is the property of Automat ic Syst ems and is conf ident ial. The recip ient is forb idd en to use it for any purpose ot her than for the use of the products or the execut ion of the project to wh ich th ey refer or to commu nicate it to th ird parties without the pr ior wr itten conse nt of Automat ic Systems. Document sub ject to change without advance not if icat ion . SL93x + PPV323 + TBV327-MT-EN p. 25/39 5.10. Control unit menu (program v5.36) The 3 pushbuttons correspond to the text on the display. When not in the menu, buttons < and > start a clockwise and counter-clockwise rotation of the obstacle. When powering on the gate, the software versions are displayed for a few seconds, then the following parameters: - Position of the obstacle with regard to its closed position. - Serial n° of the CPU board, alternating with the IP address of the board if the IP interface option is fitted. - The obstacle rotation speed. - Any error messages ( ch.5.12. ) Enter the menu by pressing the center button (MENU) => the obstacle unlocks. Note: do not enter the menu before the serial n° is displayed. This would lose the customized configuration and return to the factory settings. Move in the various sections by means of button >. Choose one parameter of a series by means of button CHG. Modify the parameter value by means of buttons < and >. The modifications validation is automatic. Exit the menu via QUIT section of the menu or by pressing the button > for at least 3 s. Parameter Description PRODUCT TYPE Select the equipment model (cf. serial plate 15, ch.2.2. ): - PPV 323 - TBV 327 - SL930 - SL931 - SL932 - Unknown Note: to be recognized by the Smart n' Slim monitoring panel, all models must be declared as SL930. The informat ion conta ined in th is docu ment is the property of Automat ic Syst ems and is conf ident ial. The recip ient is forb idd en to use it for any purpose ot her than for the use of the products or the execut ion of the project to wh ich th ey refer or to commu nicate it to th ird parties without the pr ior wr itten conse nt of Automat ic Systems. Document sub ject to change without advance not if icat ion . SL93x + PPV323 + TBV327-MT-EN p. 26/39 Parameter Description PUSH AND GO No: a passage authorization unlocks the obstacle and its rotation is driven by the motor. Yes: the passage authorization unlocks the obstacle. Its rotation must be started manually, the motor assisting for the complete opening. The obstacle locks again automatically if it has not been opened after 6 seconds (not adjustable). The AUTH MEMORISATION parameter is not active if PUSH AND GO is set to Yes. AUTONM./MASTER/ SLAVE Autonomous normal operation Master/ Slave only with IP option AUTH. MEMORISATION Number of opening requests saved while the preceding movement is still in progress. The stack of opening requests in one direction is always cleared before accepting opening requests in the opposite direction. (TBV only) OPENING ANGLE A WAY (PPV only) Fine adjustment of the maximum opening angle in the clockwise direction (A direction), measured during the automatic configuration (AUTOMATIC SETUP section). This adjustment may be necessary according to obstacle’s height. Note: adjust the limit stops after modifying this parameter (ch.5.7. ). OPENING ANGLE B WAY (PPV only) Fine adjustment of the maximum opening angle in the counterclockwise direction (B direction), measured during the automatic configuration (AUTOMATIC SETUP section). This adjustment may be necessary according to obstacle’s height. Note: adjust the limit stops after modifying this parameter (ch.5.7. ). TIME DELAY AFTER CMD Time delay between an opening command (badge, pushbutton, etc.) and the actual unlocking (0 to 100 seconds). STOP TIME DELAY (PPV only) Stop time in the open position before closing (0 to 100 s). BRAKING ANGLE Angle from which the obstacle speed decreases (cf. ch.4. ). Note: do not change this value, calculated during the automatic configuration (AUTOMATIC SETUP section) according to the obstacle dimensions and inertia. DIR.EMERGE.OPENING (PPV only) Direction of obstacle opening on an Emergency (FIRE) command (ch.4.3. ): clockwise (A) or counter-clockwise (B) ROTATION SPEED Adjustment of the obstacle’s opening and closing speed (5 to 40, 22 by default). Note: proceed to an AUTOMATIC SETUP after each modification of this parameter! NUMBER OF WARNING Number of successive attempts to complete the opening or closing movement, before the equipment is put out of service and the error message is displayed and a signal is sent to the CPU output. LANGUAGE Menu language selection: French / English. FUNCTIONAL TEST Continuous clockwise and anti-clockwise opening cycles. Exit the mode by pressing on the STOP button. The informat ion conta ined in th is docu ment is the property of Automat ic Syst ems and is conf ident ial. The recip ient is forb idd en to use it for any purpose ot her than for the use of the products or the execut ion of the project to wh ich th ey refer or to commu nicate it to th ird parties without the pr ior wr itten conse nt of Automat ic Systems. Document sub ject to change without advance not if icat ion . SL93x + PPV323 + TBV327-MT-EN p. 27/39 Parameter Description AUTOMATIC SETUP Automatic configuration of the BRAKING ANGLE, according to the ROTATION SPEED set and the obstacle inertia. PRESS OK TO QUIT AND SAVE SETUP Leave programming mode and return to the main screen. MANUFACTURER RESET Loading of the default values for the menu and the variable speed controller parameters. BACKLASH Display of the mechanical play of the motor coupling, as measured during the AUTOMATIC SETUP procedure. The informat ion conta ined in th is docu ment is the property of Automat ic Syst ems and is conf ident ial. The recip ient is forb idd en to use it for any purpose ot her than for the use of the products or the execut ion of the project to wh ich th ey refer or to commu nicate it to th ird parties without the pr ior wr itten conse nt of Automat ic Systems. Document sub ject to change without advance not if icat ion . SL93x + PPV323 + TBV327-MT-EN p. 28/39 5.11. Maintenance interface 5.11.1. Network communication settings Note: a basic knowledge of networks is necessary. 1. Switch the power on the gate (ch.5.2. ). 2. Connect a PC to the RJ45 connector of the CPU board by means of an Ethernet patch cable. 3. Set the PC communication parameters: On the web browser, deactivate the Network communication mode via Proxy server. Set the PC IP address to be in the same range as the gate's address, displayed on the CPU (192.168.0.85 by default). 4. In the PC web browser, type the gate's IP address. 5.11.2. Login User: admin Password: as Note: the menu language is adjustable through Configuration section. The informat ion conta ined in th is docu ment is the property of Automat ic Syst ems and is conf ident ial. The recip ient is forb idd en to use it for any purpose ot her than for the use of the products or the execut ion of the project to wh ich th ey refer or to commu nicate it to th ird parties without the pr ior wr itten conse nt of Automat ic Systems. Document sub ject to change without advance not if icat ion . SL93x + PPV323 + TBV327-MT-EN p. 29/39 5.11.3. Status Status of the obstacle Last major defect registered Last minor defect registered Mechanical play of the motor coupling Mechanical play of the motor coupling (pitch) Number of major/minor defects since the last reset Number of openings in clockwise direction (A) or counter-clockwise (B) since the last reset Reset of 1 of the 4 counters above Same counters as above, without reset 5.11.4. Identification Indicate the type of gate see serial number or installation drawing Note: if the gate is connected to the Smart n' Slim monitoring panel, select AS-SL930 Enter the desired reference for the gate Save the modifications 5.11.5. Commands This screen allows testing the following inputs: Closing: closing and locking the obstacle Emergency opening: opening of the obstacle. Opening in direction A (clockwise) / B (counterclockwise): opening of the obstacle in the A or B direction. The informat ion conta ined in th is docu ment is the property of Automat ic Syst ems and is conf ident ial. The recip ient is forb idd en to use it for any purpose ot her than for the use of the products or the execut ion of the project to wh ich th ey refer or to commu nicate it to th ird parties without the pr ior wr itten conse nt of Automat ic Systems. Document sub ject to change without advance not if icat ion . SL93x + PPV323 + TBV327-MT-EN p. 30/39 5.11.6. Network Modification of the gate's IP address (cf. ch.5.11.1. ) to adapt it to a new network. These parameters must be authorized by the network manager! Note: the gate's IP address is displayed on the CPU when powering it on Validation of the modifications 5.11.7. Menu Configuration This section is a copy of the CPU parameters (cf. ch.5.10. ). The last change in the maintenance interface or the CPU prevails. The informat ion conta ined in th is docu ment is the property of Automat ic Syst ems and is conf ident ial. The recip ient is forb idd en to use it for any purpose ot her than for the use of the products or the execut ion of the project to wh ich th ey refer or to commu nicate it to th ird parties without the pr ior wr itten conse nt of Automat ic Systems. Document sub ject to change without advance not if icat ion . SL93x + PPV323 + TBV327-MT-EN p. 31/39 5.12. Trouble shooting Refer to error messages of the control unit. SYMPTOM No power Buzzer + Error message on the CPU display The obstacle does not move CAUSE / REMEDY Check that the equipment is connected to the power supply as specified (ch.2.1. ) and that the mains switch is ON (ch.5.2. ). Defect detected: - Holding: the contact plate (73, p15) is not in contact with hold magnet (72, p15). - Origin: the obstacle did not find the locking position sensor (= the origin point corresponding to its closed position). - Obstruction: the obstacle did not complete its opening or closing movement. - Mech. stop: the obstacle rotation passed beyond the mechanical stop position, as memorized during the AUTOMATIC SETUP procedure. Check the speed and opening angles (ch.5.10. ). These must be smaller than the angles allowed by the mechanical stops. - Mot. drive com: communication fault with the variable speed controller. - Lock fever: fuse failed on the lock electro magnet. - Emergency opening: Emergency (FIRE) opening active on the power supply board. Note: The error is reset by an opening command or an Emergency opening command. Check if the gate has detected a defect (see error messages here above). Check that ambient temperature is within the required range (ch.2.1. ). Check the power supply, the state of the circuit breaker and the fuses, and the voltage delivered by the gate's power supply (24VDC). Check if the variable speed controller is defective (refer to the error code on the VSC). Check the hold magnet (72, ch.4.1. ) power supply (broken cable, …). Check the conical coupling (see ch.5.6. ). The obstacle does not lock in closed position Check the power supply (see here above). Check if the lock is powered and enters into the rotor hole (ch.4.1. ). Check the electromagnet contact plate wire. Check the variable speed controller power supply. Check for a mechanical obstruction of the movement. The obstacle remains open Check that the clockwise/counter-clockwise opening commands are not maintained. Check that the evacuation contact is closed (ch.3.4. ). The informat ion conta ined in th is docu ment is the property of Automat ic Syst ems and is conf ident ial. The recip ient is forb idd en to use it for any purpose ot her than for the use of the products or the execut ion of the project to wh ich th ey refer or to commu nicate it to th ird parties without the pr ior wr itten conse nt of Automat ic Systems. Document sub ject to change without advance not if icat ion . SL93x + PPV323 + TBV327-MT-EN p. 32/39 5.13. Disposal / Destruction If the equipment is not used for an extended period, it should be stored in a dry place, protected from heat and bad weather conditions. When the equipment is retired from service, dispose of the various components through the appropriate channels (metal parts, electronic components, etc.) according to the regulations in force in the country concerned. The informat ion conta ined in th is docu ment is the property of Automat ic Syst ems and is conf ident ial. The recip ient is forb idd en to use it for any purpose ot her than for the use of the products or the execut ion of the project to wh ich th ey refer or to commu nicate it to th ird parties without the pr ior wr itten conse nt of Automat ic Systems. Document sub ject to change without advance not if icat ion . SL93x + PPV323 + TBV327-MT-EN p. 33/39 6. ELECTRICAL DIAGRAMS MOTOR GROUND U V W VARIABLE SPEED CONTROLLER Output+24 Vdc 220V Ground 220V Emergency command 24/48 Vdc (*) Ground (*) +R -R SG +S -S SC S5 S4 S3 S2 S1 Shunt the connectors if the Emergency command ground is not used contact plate Hold magnet Jumper to the right for 24 Vdc Jumper to the right for 48 Vdc thermal fuse - Electromagnet Max absorbed Power: 1W Non return lock ( option ) Voltage Dry contacts 24 Vdc or 48 Vdc see above Locking position sensor LINE 10 / 2012 NEUTRAL Motor encoder sensors CPU : V16 Ground connector PWR board: V10 MAINS 220V AC HOUSING The informat ion conta ined in th is docu ment is the property of Automat ic Syst ems and is conf ident ial. The recip ient is forb idd en to use it for any purpose ot her than for the use of the products or the execut ion of the project to wh ich th ey refer or to commu nicate it to th ird parties without the pr ior wr itten conse nt of Automat ic Systems. Document sub ject to change without advance not if icat ion . SL93x + PPV323 + TBV327-MT-EN p. 34/39 The informat ion conta ined in th is docu ment is the property of Automat ic Syst ems and is conf ident ial. The recip ient is forb idd en to use it for any purpose ot her than for the use of the products or the execut ion of the project to wh ich th ey refer or to commu nicate it to th ird parties without the pr ior wr itten conse nt of Automat ic Systems. Document sub ject to change without advance not if icat ion . SL93x + PPV323 + TBV327-MT-EN p. 35/39 GATE OPEN (except for emergency cmd) DEFECT DETECTED CLOSED & LOCKED GATE (except for emergency cmd) 07 08 09 10 11 12 13 14 15 16 17 18 RS 485 COUNTERCLOCKWISE opening request CLOCKWISE opening request The informat ion conta ined in th is docu ment is the property of Automat ic Syst ems and is conf ident ial. The recip ient is forb idd en to use it for any purpose ot her than for the use of the products or the execut ion of the project to wh ich th ey refer or to commu nicate it to th ird parties without the pr ior wr itten conse nt of Automat ic Systems. Document sub ject to change without advance not if icat ion . SL93x + PPV323 + TBV327-MT-EN p. 36/39 DOUBLE GATES Entry In the case of 2 gates that must open simultaneously, one opens in the clockwise direction and the other in the anti-clockwise direction, and vice versa. Gate Gate B A Note: The opening request inputs must be connected as described below. Note that the clockwise input on one gate is connected to the counter-clockwise input on the other: GATE A CLOCKWISE opening COUNTERCLOCKWISE opening GATE B The informat ion conta ined in th is docu ment is the property of Automat ic Syst ems and is conf ident ial. The recip ient is forb idd en to use it for any purpose ot her than for the use of the products or the execut ion of the project to wh ich th ey refer or to commu nicate it to th ird parties without the pr ior wr itten conse nt of Automat ic Systems. Document sub ject to change without advance not if icat ion . SL93x + PPV323 + TBV327-MT-EN p. 37/39 7. DECLARATION OF CONFORMITY The informat ion conta ined in th is docu ment is the property of Automat ic Syst ems and is conf ident ial. The recip ient is forb idd en to use it for any purpose ot her than for the use of the products or the execut ion of the project to wh ich th ey refer or to commu nicate it to th ird parties without the pr ior wr itten conse nt of Automat ic Systems. Document sub ject to change without advance not if icat ion . SL93x + PPV323 + TBV327-MT-EN p. 38/39 AUTOMATIC SYSTEMS BELGIUM - HQ Email: [email protected] Tel.: +32.10.23 02 11 Fax: +32.10.23 02 02 The informat ion conta ined in th is docu ment is the property of Automat ic Syst ems and is conf ident ial. The recip ient is forb idd en to use it for any purpose ot her than for the use of the products or the execut ion of the project to wh ich th ey refer or to commu nicate it to th ird parties without the pr ior wr itten conse nt of Automat ic Systems. Document sub ject to change without advance not if icat ion . SL93x + PPV323 + TBV327-MT-EN p. 39/39
advertisement
Related manuals
advertisement