- Home
- Do-It-Yourself tools
- Power tools
- Paint Sprayer
- Graco
- 313259F - Hopper or Hose Heat Circulation Kit
- Instructions
advertisement
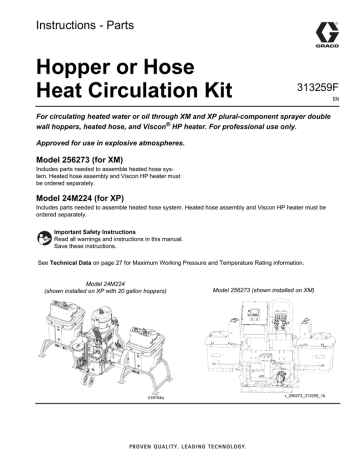
Instructions - Parts
Hopper or Hose
Heat Circulation Kit
313259F
EN
For circulating heated water or oil through XM and XP plural-component sprayer double wall hoppers, heated hose, and Viscon
®
HP heater. For professional use only.
Approved for use in explosive atmospheres.
Model 256273 (for XM)
Includes parts needed to assemble heated hose system. Heated hose assembly and Viscon HP heater must be ordered separately.
Model 24M224 (for XP)
Includes parts needed to assemble heated hose system. Heated hose assembly and Viscon HP heater must be ordered separately.
Important Safety Instructions
Read all warnings and instructions in this manual.
Save these instructions.
on page 27 for Maximum Working Pressure and Temperature Rating information.
Model 24M224
(shown installed on XP with 20 gallon hoppers)
Model 256273 (shown installed on XM)
r_256273_313259_1b ti19154a
2
Related Manuals
Contents
Related Manuals . . . . . . . . . . . . . . . . . . . . . . . . . . . 2
Warnings . . . . . . . . . . . . . . . . . . . . . . . . . . . . . . . . . 3
Heated Hopper or Hose Circulation Kit 256273 . . 5
Heated Hose Assembly . . . . . . . . . . . . . . . . . . . 5
Fluid Heater . . . . . . . . . . . . . . . . . . . . . . . . . . . . 6
Typical Installation . . . . . . . . . . . . . . . . . . . . . . . . . 8
Installation . . . . . . . . . . . . . . . . . . . . . . . . . . . . . . . 14
Grounding . . . . . . . . . . . . . . . . . . . . . . . . . . . . . 14
Tubing Lengths . . . . . . . . . . . . . . . . . . . . . . . . . 14
Install . . . . . . . . . . . . . . . . . . . . . . . . . . . . . . . . . 14
Setup . . . . . . . . . . . . . . . . . . . . . . . . . . . . . . . . . 17
Connecting Additional Hose Lengths . . . . . . . . 17
Operation . . . . . . . . . . . . . . . . . . . . . . . . . . . . . . . . 18
Maintenance . . . . . . . . . . . . . . . . . . . . . . . . . . . . . . 19
Troubleshooting . . . . . . . . . . . . . . . . . . . . . . . . . . 19
Parts . . . . . . . . . . . . . . . . . . . . . . . . . . . . . . . . . . . . 20
Technical Data . . . . . . . . . . . . . . . . . . . . . . . . . . . . 27
Graco Standard Warranty . . . . . . . . . . . . . . . . . . . 28
Graco Information . . . . . . . . . . . . . . . . . . . . . . . . 28
Related Manuals
Manual
312359 XM Operation
Description
313289 XM Repair
313292 XM OEM, Instructions-Parts
3A0420 XP Instructions-Parts
312747 Double Wall Hopper, Instructions-Parts
309524
308981
Viscon
®
HP Heater
Husky
™
716 Diaphragm Pump
313259F
Warnings
Warnings
The following warnings are for the setup, use, grounding, maintenance, and repair of this equipment. The exclamation point symbol alerts you to a general warning and the hazard symbol refers to procedure-specific risk. Refer back to these warnings. Additional, product-specific warnings may be found throughout the body of this manual where applicable.
FIRE AND EXPLOSION HAZARD
Flammable fumes, such as solvent and paint fumes, in
work area
can ignite or explode. To help prevent fire and explosion:
• Use equipment only in well ventilated area.
• Eliminate all ignition sources; such as pilot lights, cigarettes, portable electric lamps, and plastic drop cloths (potential static arc).
• Keep work area free of debris, including solvent, rags and gasoline.
• Do not plug or unplug power cords, or turn power or light switches on or off when flammable fumes are present.
• Ground all equipment in the work area. See
Grounding
instructions.
• Use only grounded hoses.
• Hold gun firmly to side of grounded pail when triggering into pail.
• If there is static sparking or you feel a shock,
stop operation immediately.
Do not use equipment until you identify and correct the problem.
• Keep a working fire extinguisher in the work area.
EQUIPMENT MISUSE HAZARD
Misuse can cause death or serious injury.
• Do not operate the unit when fatigued or under the influence of drugs or alcohol.
• Do not exceed the maximum working pressure or temperature rating of the lowest rated system component. See
Technical Data
in all equipment manuals.
• Use fluids and solvents that are compatible with equipment wetted parts. See
Technical Data
in all equipment manuals. Read fluid and solvent manufacturer’s warnings. For complete information about your material, request MSDS forms from distributor or retailer.
• Check equipment daily. Repair or replace worn or damaged parts immediately with genuine manufacturer’s replacement parts only.
• Do not alter or modify equipment.
• Use equipment only for its intended purpose. Call your distributor for information.
• Route hoses and cables away from traffic areas, sharp edges, moving parts, and hot surfaces.
• Do not kink or over bend hoses or use hoses to pull equipment.
• Keep children and animals away from work area.
• Comply with all applicable safety regulations.
ELECTRIC SHOCK HAZARD
Improper grounding, setup, or usage of the system can cause electric shock.
• Turn off and disconnect power cord before servicing equipment.
• Use only grounded electrical outlets.
• Use only 3-wire extension cords.
• Ensure ground prongs are intact on sprayer and extension cords.
• Do not expose to rain. Store indoors.
313259F 3
Warnings
SKIN INJECTION HAZARD
High-pressure fluid from gun, hose leaks, or ruptured components will pierce skin. This may look like just a cut, but it is a serious injury that can result in amputation.
Get immediate surgical treatment.
• Do not point gun at anyone or at any part of the body.
• Do not put your hand over the spray tip.
• Do not stop or deflect leaks with your hand, body, glove, or rag.
• Do not spray without tip guard and trigger guard installed.
• Engage trigger lock when not spraying.
• Follow
Pressure Relief Procedure
in this manual, when you stop spraying and before cleaning, checking, or servicing equipment.
BURN HAZARD
Equipment surfaces and fluid that’s heated can become very hot during operation. To avoid severe burns, do not touch hot fluid or equipment. Wait until equipment/fluid has cooled completely.
TOXIC FLUID OR FUMES HAZARD
Toxic fluids or fumes can cause serious injury or death if splashed in the eyes or on skin, inhaled, or swallowed.
• Read MSDS’s to know the specific hazards of the fluids you are using.
• Store hazardous fluid in approved containers, and dispose of it according to applicable guidelines.
• Always wear impervious gloves when spraying or cleaning equipment.
PERSONAL PROTECTIVE EQUIPMENT
You must wear appropriate protective equipment when operating, servicing, or when in the operating area of the equipment to help protect you from serious injury, including eye injury, inhalation of toxic fumes, burns, and hearing loss. This equipment includes but is not limited to:
• Protective eyewear
• Clothing and respirator as recommended by the fluid and solvent manufacturer
• Gloves
• Hearing protection
4 313259F
Heated Hopper or Hose Circulation Kit 256273
Heated Hopper or Hose Circulation Kit 256273
The kit described in this manual; includes all miscellaneous parts needed to assemble the system. There are three options for using circulation kit 256273:
• Circulate water through the heater and only the hop-
• Circulate water through the heater and only the
• Circulate water through the heater, hoppers, and
Heated Hose Assembly
Order separately a heated hose assembly that meets maximum pressure and hose diameter requirements. You can connect up to six 50 ft. (15.2 m) heated hose sections for a maximum total length of 300 ft. (91.4 m). See manual
309525.
A
B
A B
Single Hose Assembly
Single Hose Assemblies
Part No.,
Series
Maximum
Pressure Rating
psi (MPa, bar)
245840, D 5000 psi (34, 345)
245841, D 7250 psi (50, 500)
245842, D 5000 psi (34, 345)
245843, D 7250 psi (50, 500)
245844, D 5000 psi (34, 345)
245845, D 7250 psi (50, 500)
Hose Diameter
in. (mm)
1/4 (6.35)
1/4 (6.35)
3/8 (9.53)
3/8 (9.53)
1/2 (12.7)
1/2 (12.7)
C
Dual Hose Assembly
Thread A
npt(m)
1/4
1/4
3/8
3/8
1/2
1/2
Thread B
npsm(f)
1/4
1/4
3/8
3/8
1/2
1/2
Approvals
II 2 G
D
313259F 5
Heated Hopper or Hose Circulation Kit 256273
Dual Hose Assemblies
Part No.,
Series
248118, D
248119, D
Maximum
Pressure Rating
psi (MPa, bar)
Hose Diameter
in. (mm)
7250 psi (50, 500)
7250 psi (50, 500)
1/2 (12.7)
3/8 (9.53)
248120, D 7250 psi (50, 500) A = 1/2 (12.7)
B = 3/8 (9.53)
248121, D 7250 psi (50, 500) A = 3/8 (9.53)
B = 1/4 (6.35)
24M439, D 7250 psi (50, 500) A = 1/2 (12.7)
B = 1/4 (6.35)
24M440, D 5000 psi (34, 345) A = 3/8 (9.53)
B = 1/4 (6.35)
24M441, D 5000 psi (34, 345) 3/8 (9.53)
24M442, D 5000 psi (34, 345) A = 1/2 (12.7)
B = 1/4 (6.35)
24M443, D 5000 psi (34, 345) A = 1/2 (12.7)
B = 3/8 (9.53)
24M444, D 5000 psi (34, 345) 1/2 (12.7)
Thread
A
npt(m)
1/2
3/8
1/2
Thread
B
npsm(f)
1/2
3/8
1/2
3/8
1/2
3/8
3/8
1/2
1/2
1/2
3/8
1/2
3/8
3/8
1/2
1/2
1/2
Thread
C
npt(m)
1/2
3/8
3/8
1/4
1/4
1/4
3/8
1/4
3/8
1/2
1/4
3/8
1/4
3/8
1/2
Thread
D
npsm(f)
1/2
3/8
3/8
Approvals
1/4
1/4
II 2 G
Fluid Heater
Order separately a VISCON HP heater that meets local electrical and hazardous location requirements.
Hazardous Location Heaters
Part No.
Series
VAC (50/60 Hz single phase) / Watts / Amps
245848 A 120 / 2300 / 19.2
245863 A 240 / 4000 / 16.7
245864
245862
246254
A
A
A
480 / 4000 / 8.30
200 / 4000 / 20.0
380 / 4000 / 10.5
Approvals
See heater manual 309524 for approvals.
Non-hazardous Location Heaters
Model No.
Series VAC (50/60 Hz single phase) / Watts / Amps
245867 A 120 / 2300 / 19.2
245868
245869
245870
246276
A
A
A
A
200 / 4000 / 20.0
240 / 4000 / 16.7
480 / 4000 / 8.30
380 / 4000 / 10.5
Approvals
See heater manual 309524 for approvals.
6 313259F
Heated Hopper or Hose Circulation Kit 256273
313259F 7
Typical Installation
Typical Installation
NOTE:
XM kit 256273 is shown in all typical installation illustrations. The general layout for XP Kit 24M224 is the same.
D
C
C
E
A
F
IG
. 1: Heat Only Hoppers Configuration
Key:
A Viscon HP Heater
B Husky diaphragm pump
C Hopper
D Frame
E Fluid circulation tubing
NOTE:
. 2 on page 9 for fluid schematic of heated fluid.
E
8
E
B r_256273_313259_1b
313259F
Typical Installation
AA
Back-Mounted Hoppers (BM)
AB
Table 1: Tubing Lengths
Section Tubing
AA
AB
AC
BA
BB
BC
CA
(BM) Hoppers in (mm)
1/2 in.
65 (1651)
51 (1295.4)
7 (177.8)
3/4 in.
40 (1016)
29 (736.6)
7 (177.8)
3/8 in.
21 (533.4)
(SM) Hoppers in (mm)
50 (1270)
35 (889)
4 (101.6)
36 (914.4)
17 (431.8)
7 (177.8)
21 (533.4)
BA
BA
AC
BC
CA
Side-Mounted Hoppers (SM)
BA
AA
CA
F
IG
. 2: Fluid schematic for only heating hoppers
AC
BB
BC
313259F
AB
9
Typical Installation
C
D
F
E
C
E
A
E
F
IG
. 3: Hoppers and Heated Hose Configuration
Key:
A Viscon HP Heater
B Husky diaphragm pump
C Hopper
D Frame
E Fluid circulation tubing
F Heated hose tee and elbow fittings (see heated hose
NOTE:
. 6 on page 13 for fluid schematic of heated
fluid.
10
B ti19227a
E
313259F
NOTE:
See page 9 for tubing lengths not shown in F
To Blue Tubing
To Red Tubing
27 in. (685.8 mm) 23 in. (584.2 mm)
Typical Installation
21 in. (533.4 mm)
Bottom View
ti19174a
F
IG
. 4: Fluid schematic for heating hoppers and heated hose
313259F
ti19175a
11
Typical Installation
H
F
D
A
F
IG
. 5: Heated Hose Only Configuration
Key:
A Viscon HP heater
B Husky diaphragm pump
C Hopper (not shown)
D Frame
E Fluid circulation tubing
F Heated hose tee and elbow fitting (to red tubing)
G Return hose tee and elbow fitting (from blue tubing)
H Recirculation valve
J Heated hose assembly (purchase separately)
K Overflow tank (used for only heated hose configuration)
NOTE:
. 6 on page 13 for fluid schematic of heated
fluid.
12
Heated Water Fluid Flow
G
F
G
F
H
G
E
K
J
B r_256273_313259_13a
313259F
Typical Installation
G
23 in.
(584.2 mm)
F
RED
BLUE
24 in.
(609.6 mm)
Single Hose Shown
38 in.
(965.2 mm)
F
IG
. 6: Fluid schematic for heated hose
313259F 13
Installation
Installation
Grounding
The equipment must be grounded. Grounding reduces the risk of static and electric shock by providing an escape wire for the electrical current due to static build up or in the event of a short circuit.
1.
Remove grounding screw on diaphragm pump (3) and tighten ring terminal on grounding cable (15) under ground screw.
15
Tubing Lengths
The length of tubing (4, 16, 29) is determined by the hopper mounting configuration and heating choices.
Reference the fluid schematic, from the configurations listed below, to find the tubing lengths.
•
•
•
Heating hoppers and hoses. See F
Cut tubing to length specified in fluid schematics.
1.
Use tubing cutter to cut tubing (4) squarely to desired lengths.
NOTE: To ensure a leak-proof seal, apply PTFE tape on all npt threads.
2.
Insert tubing through the back of the nut in each of the plastic fittings (7) until the tube stops. Tighten the nut hand tight, then tighten it to 1-1/2 to 2 turns with a wrench.
Y r_256273_313259_9
2.
Loosen grounding lug locknut (W) on back of control box. Insert ground wire end (Y) into lug slot and tighten locknut securely.
Install
1.
XM Kit 256273 only:
Mount bracket (1) on XM frame (D) using screws (5).
5
Y
W r_256273_313259_10
1
D r_256273_313259_5
2.
XP Kit 24M224 only:
Mount brackets (101, 102) on
XP frame (D) using plates (105), screws (134), nuts (133).
134
134
101
102
D
105
105
133 ti19176a
133
14 313259F
Installation
3.
XM Kit 256273 only:
Remove 3/4 npt plugs from the end of the diaphragm pump fluid manifold and place in center.
4.
For only heating hoppers or heating hoppers and heated hose:
Install tube fitting (31) in fluid inlet. See F
IG
. 7.
5.
For heating heated hose only (see F
IG
. 7):
a.
Install elbow (32), mounting fitting (23), o-ring
(22) and 1.5 gallon reservoir tank (21) on diaphragm pump fluid inlet. b.
XM Kit 256273 only:
Connect elbow fitting (7) to mounting fitting (23).
6.
Install bushing (12) and elbow tube fitting (17) to diaphragm pump fluid outlet. See F
IG
. 7.
7.
Mount diaphragm pump to bracket.
XM Kit 256273 only:
Use four screws (2) to mount pump (3) on mounting bracket. See F
IG
. 7.
XP Kit 24M224 only:
Use nuts (135) to mount pump (3) to threads on mounting bracket. See F
IG
.
7.
8.
Connect air regulator assembly.
XM Kit 256273 only:
Connect nipple (10), air regulator/gauge (9), and fitting (19) to pump (3). See F
IG
.
7.
XP Kit 24M224 only:
Connect elbow (137), nipple (10), air regulator/gauge (9), elbow (136), and fitting (19) to pump (3).
9.
Remove plug on system air control supply and connect fitting (19) in place of the plug. Connect hose
(27) between fitting (19) on 100 psi (0.7 MPa, 7 bar)
XM air supply and fitting (19) on the air regulator/gauge (9). See F
IG
. 7. Refer to Husky 716 manual 308981 if needed.
NOTE:
The air regulator (9) controls pump pressure.
XM: Heated Hose Only XM: All Others
21
22
23
7
33
32
XP: Heated Hose Only
17
12
12
17
21
22
23
7
33
134
105
133
135
F
IG
. 7: Diaphragm Pump Installation
ti19229a
19
9
10
3
137 10 9
136,19,27
32
XP: All Others
12
17 ti19155a
134
105
133
19
12
17
2
9
10
3
31
137 10 9 136,19,27
135 31 ti19173a
313259F 15
Installation
10. Slide Viscon HP heater (A) into slots on frame.
Tighten bolts to secure to frame.
XP Kit 24M224
A
XM Kit 256273
All wiring must be done by a qualified electrician. See
A ti19156a r_256273_313259_7
11.
For heating hoppers or heating hoppers and heated hose:
install fitting (18) and elbow (17) in the heater’s fluid inlet facing away from the system.
Install elbow (7) in heater outlet facing the back of the system.
13. Wire Viscon HP heater (B) to your voltage supply.
Follow wiring procedure in the Viscon HP manual
309524.
14. If heating hoppers:
a.
Remove bottom plug (P) from hopper (C).
b.
XP Kit 24M224 only:
Install nipple (33) and coupling (139) into bottom of hopper. See
c.
Install elbows (32) and fittings (31). d.
Repeat for second hopper.
7
XM shown
C
P
17
18 r_256273_313259_16a
F
IG
. 8
12.
For heating heated hose only:
connect elbow fitting (17) to heater fluid inlet facing the back of the system. Install elbow (7) in the heater outlet facing upward.
F
IG
. 9
17 r_256273_313259_17a
7 11
P
31
32 r_256273_313259_8
15. Remove side plug (P) used for fluid inlet.
16. Replace plug with bushing (11) and elbow fitting (7).
17. Cut tubing (4, 16, 29). See
NOTE:
Fitting nuts may need retightening as the system reaches normal operating temperatures.
16 313259F
Installation
Setup
For heating hoppers only:
See fluid schematic on page 9 and parts on page 21.
NOTE: To ensure a leak-proof seal, use PTFE tape on all pipe thread connections.
1.
Connect A and B fluid hoses to shutoff check valve outlets (H).
2.
Connect elbow fitting (17) in pump outlet (3) and elbow fitting (17) on heater inlet (A) with tubing (16).
3.
Connect fitting (7) in the heater fluid outlet (A) and tee fitting (13) with tubing (4). Connect tee fitting (13) and fittings (7) in the hopper side ports with tubing (4).
4.
Connect fittings (31) to elbow in bottom outlet of hoppers and tee fitting (30) with tubing (29). Connect tee fitting (30) and the pump (3) inlet fitting (31) with tubing (29).
For heating heated hose only:
See fluid schematic on page 13 and parts on page 22.
1.
Connect A and B fluid hoses to shutoff check valve fluid outlets (H).
2.
Connect elbow fitting (17) in pump outlet (3) and elbow fitting (17) on heater inlet (A) with tubing (16).
3.
Connect fitting (7) in the heater fluid outlet (A) and tee fitting (13) with tubing (4).
4.
Connect tee fitting (42) and elbow fitting (41) to recirculation inlets and outlet connections of the
5.
Connect elbow fitting (7) to 1-1/2 gallon tank manifold (23) with tubing (4).
For heating hoppers and heated hose:
See fluid schematic on page 11 and parts on page 20.
1.
Connect A and B fluid hoses to shutoff check valve outlets (H).
2.
Connect elbow fitting (17) in pump outlet (3) and elbow fitting (17) on heater inlet (A) with tubing (16).
3.
Connect fitting (7) in the heater fluid outlet (A) and tee fitting (13) to hose circulation inlet with tubing (4).
4.
Connect tee fitting (13) from hose circulation return to tee fitting (13) with tubing (4).
5.
Connect tee fitting (13) and fittings (7) in the hopper side ports with tubing (4).
6.
Connect fittings (31) to elbow in bottom outlet of hoppers and tee fitting (30) with tubing (29). Connect tee fitting (30) and the pump (3) inlet fitting (31) with tubing (29).
Hopper Inlet or
1-1/2 gallon tank manifold
Blue hose connections
Heater Outlet
ti19230a
Red hose connections
F
IG
. 10: Recirculation Inlet and Outlet Connections
Connecting Additional Hose
Lengths
Up to six 50 ft (15.2 m) sections of heated hose can be attached for a maximum total length of 300 ft (91.4 m).
1.
Remove plastic u-turn fittings at the end of the heated hose assembly.
2.
Connect the next length of hose, using union fittings supplied with the hose.
3.
Tubes are color coded. Connect like colors.
NOTICE
To prevent cross-contamination, ensure you connect
“A” side fluid hose to “A” side fluid hose on additional heated hose.
313259F 17
Operation
Operation
1.
Select fluid to use for heating circulation.
• 50% water and 50% ethylene glycol mixture is recommended for fastest heat-up time and prevention of algae build-up regardless of ambient temperature.
• Oil can be used but heat-up time will increase and the hopper fill level must be decreased.
See item 2.
NOTE:
Detailed diaphragm pump operating instructions are in the Husky 716 diaphragm pump manual 308981.
2.
Fill Heating Fluid
in double wall hopper (C) outer cavity. See manual 312747 for instructions.
NOTICE
Do not plug top ports. Always have venting fittings installed to prevent outer cavity pressurization.
Failure to do so may cause leakage into spray material.
3.
Set the flow rate of the circulation fluid by adjusting the pump’s air regulator (9) until the pump cycles about 50 cycles/min. Do not use a higher flow rate as doing so will decrease system heating performance and pump life. Never exceed the hose’s
95 psi (0.6 MPa, 6.6 bar) maximum working pressure rating.
4.
Adjust the heater thermostat to the desired circulation temperature. The setting at the heater output thermometer should be about 10° F (6° C) higher than the desired paint temperature. Never exceed the hose’s 140° F (60° C) maximum temperature rating.See Viscon HP heater manual 309524 for instructions.
NOTE:
If the hose is not being used for more than one hour, shut off Viscon HP heater and pump to lengthen heater life.
NOTICE
If oil is the heating fluid selected, the maximum oil level must be 3 in. (76.2 mm) below the hopper side port level. A higher fluid level may cause the oil to overflow during initial pump and heater startup.
NOTE:
If using heated hose: each 50 ft. (15.2 m) heated hose section holds approximately 1.25 gal. (4.7 liters) of fluid.
18 313259F
Maintenance
Maintenance
• Check double wall hopper heating fluid level monthly. Add fluid as needed.
•
Do not overfill when using oil.
See overfilling
• Follow pump maintenance instructions in Husky 716 diaphragm pump manual 308981.
• Follow heater maintenance instructions in Viscon
HP manual 309524.
Troubleshooting
Problem
Fluid fittings leaking.
Hose not heating to desired temperature.
Loose fittings.
Cause
Diaphragm flow rate set too high.
Problem with Viscon HP heater.
Diaphragm pump not operating correctly.
Oil overflowing out vented hopper side fill port during startup.
Hopper not reaching set temperature when heating fluid hose first.
Oil level higher than 3 in. (76.2 mm) below fill port at room temperature and at rest.
Temperature loss in heated hose is too much for the heater capacity to compensate for.
Air and heating fluid splatter is exiting hopper vented fitting.
Diaphragm in Husky 716 diaphragm pump is cracked.
Solution
Tighten fittings after system reaches desired temperature.
Decrease diaphragm pump flow rate to 50 cycles/min.
See troubleshooting in Viscon HP heater manual 309524.
See troubleshooting in Husky 716 diaphragm pump manual 308981.
Lower oil level to 3 in. (76.2) below hopper fill port.
Allow longer heating time. Insulate heated hose bundle.
Replace pump diaphragm. See manual 308981 for parts.
313259F 19
Parts
Parts
256273, XM Heated Hopper or Hose Circulation Kit
For heating hoppers and heated hose
To Blue Tubing
To Red Tubing
41, 42
1
4
4
1
41, 42
1
7, 11
32, 31
1
4
1
13
4
1
29
7, 11
30
29
1
32, 31
2
29
1
20
1
16
1
Cut tubing to length. See table on page 9.
2
Heater and Diaphragm Pump (3) Connections
ti19231a
313259F
Parts
For only heating hoppers
Back-Mounted Hoppers (BM)
7, 11 7, 11
32, 31
1
4
32, 31
7, 11
4
1
1
Cut tubing to length. See table on page 9.
2
313259F
1
29
1
4
13
30
29
1
1
32, 31
4
1
29
1
7
2
16
1
Side-Mounted Hoppers (SM)
12, 17
32, 31
1
29
13
30 29
1
1
4
7
16
1
4
1
2
7, 11
21
Parts
Heater and Diaphragm Pump (3) Connections
5
4
8
13
For heating heated hose only
21
17
8
22
18
4
7
16
9
8
13
17
12
1
7
23
33
32
15
3
10
5 ti19232a
19
For heating hoppers or hoppers and heated hose only
27
19
17
12
19
9
10
3
5
31
2
5
22 313259F
Parts
Ref.
Part Description
Qty
.
1
2
3
4
5
7
9
10
11
12
13
30
31
32
33
41
42
256196 PLATE, mounting
100333 SCREW, cap, hex; 1/4-20 x 1/2 in.
(13 mm)
D53288 PUMP, 716, Husky
054139 TUBE, nylon, flexible, 1/2 in. (13 mm) OD; 17 ft (5.2 m)
112395 SCREW, cap, flng hd
126898 FITTING, elbow; 1/2 npt(m) x 1/2 in. (13 mm) OD tube
110147 REGULATOR, air, 1/4 npt
156971 FITTING, nipple, short; 1/4-18 npt
124070 BUSHING, pipe; 1 npt(m) x 1/2 npt(f)
C19683 BUSHING, reducing; 3/4(m) x 3/8(f) 1
17E117 FITTING, tee; 1/2 in. (13 mm) OD 1
1
1
2
4
5
1
1
1
4
15
16
17 tube
119402 CABLE, coiled, ground
054134 TUBE, nylon; 3 ft (914 mm); 3/8 in.
(9.5 mm)
17E118 FITTING, elbow, male; 3/8-18 npt x
3/8 OD tube
122275 FITTING, coupling, reducing; 3/8 x 18
19
1/2
162453 FITTING, nipple; 1/4 npt(m) x 1/4 nps(m)
21* 188787 HOPPER, 1.5 gallon
22* 104938 O-RING
23* 15B338 FITTING, reservoir, mounting
27
29
212005 HOSE, coupled; 6 ft (1.8 m)
054929 TUBE, nylon, flexible; 3/4 in. (19 mm) OD, 8 ft (2.4 m)
17H050 FITTING, union tee, 3/4 in tube
17H051 FITTING, connector, male; 3/4 npt(m) x 3/4 OD tube
124042 FITTING, elbow, street; 3/4 npt(m) x 3/4 in.(f)
175013 FITTING, nipple 3/4
126896 FITTING, elbow, tube x nptf
126895 FITTING, tee, tube x tube x nptm
1
3
1
1
2
1
2
3
1
2
2
1
1
1
1
1
* Only used for circulating heated fluid through heated hose.
Viscon HP heater is not included with this kit (purchase separately).
Heated hose assembly is not included with this kit
(purchase separately).
313259F 23
Parts
24M224, XP Heated Hopper or Hose Circulation Kit
11 7, 4 41, 42 13 30
33
32
134
21
22
23
33
139
32
31
29
135
102
105
133
17
12
137
10
9
136
19, 27
15
17 18 7, 16
101
134
105
133 ti19157a
24 313259F
Parts
To Blue Tubing
Hose Identification
4
4
29
To Red Tubing
4
4
29
29
16 ti19174a
1
Cut tubing to length. See table on page 9.
2
Heater and Diaphragm Pump (3) Connections
Ref Part Description
3
4
7
9
D53288 PUMP, 716, husky
054139 TUBE, nylon, round
126898 FITTING, elbow
110147 REGULATOR, air, 1/4 in. npt, with gauge
10 156971 FITTING, nipple, short
11 100380 BUSHING, pipe
12 C19683 BUSHING, reducing
13 17E117 FITTING, tee, tube
15 119402 CABLE, coiled
16 054134 TUBE, nylon
17 17E118 FITTING, elbow, male
18 122275 FITTING, coupling, reducing
19 162453 FITTING, 1/4 npsm x 1/4 npt
21* 188787 HOPPER, 1.5 gallon
22* 104938 PACKING, o-ring
23* 15B338 FITTING, reservoir mounting
27 212005 HOSE, coupled, 6 ft
29 054929 TUBE, nylon, round, 0.75 OD
30 17H050 FITTING, tee, 0.75 tube
31 17H051 FITTING, 0.75 npt to 0.75 tube
32 124042 FITTING, elbow, 0.75 street, brass
33 175013 NIPPLE, pipe
41 126896 FITTING, elbow, tube x nptf
42 126895 FITTING, tee, tube x tube x nptm
101 24N445 BRACKET, heater, heated hose
102 24N446 BRACKET, pump, heated hose
105 24N447 BRACKET, base, heated hose
133 113981 NUT, lock, high tensile
134 123443 SCREW, cap, flange head
135 115942 NUT, hex, flange head
136 111763 FITTING, elbow, 1/4 npt
137 155541 FITTING, swivel, 90 degree
139 16P292 COUPLING, pipe, 3/4 npt, female x female
140 114958 STRAP, tie
Qty
1
20
5
1
20
4
1
8
8
2
2
1
2
2
1
3
2
3
3
14
1
1
1
1
1
1
2
3
2
3
1
1
2
1
* Only used for circulating heated fluid through heated hose.
Viscon HP heater is not included with this kit (purchase separately).
Heated hose assembly is not included with this kit
(purchase separately).
313259F 25
Parts
Heated Hose Replacement Parts
Fitting*
104 (red)
Material Hose
103*
105 (blue)
110
111
101*
102*
Part
248118
248119
248120
248121
24M439
24M440
24M441
24M442
24M443
24M444
“A”
MATERIAL
Hose
H75050
H73850
H75050
H73850
H75050
H53850
H53850
H55050
H55050
H55050
EA
1
1
1
1
1
1
1
1
1
1
“A” Fitting*
158491
156849
158491
156849
158491
156849
156849
158491
158491
158491
EA
Ref Part Description
101* 126898 FITTING, elbow, 1/2 in. x 1/2-14 npt male threads
102* 126896 FITTING, elbow, 1/2 in. x 1/2-14 npt female threads
103* 126894 FITTING, union, 1/2 in. x 1/2 in.
104 16X027 TUBE, red, 1/2 in. OD, 50 foot length
105 16X028 TUBE, blue, 1/2 in. OD, 50 foot length
110 16T136 INSULATION, 50 foot length
111 16T138 JACKET, scuff, 50 foot length
Qty
2
2
2
1
2
2
1
* Included in Connector Kit 16U666.
1
1
1
1
1
1
1
1
1
1
“B”
MATERIAL
Hose
H75050
H73850
H73850
H72550
H72550
H52550
H53850
H52550
H53850
H55050
EA
1
1
1
1
1
1
1
1
1
1
“B” Fitting* EA
158491
156849
156849
156971
156971
156971
156849
156971
156849
158491
1
1
1
1
1
1
1
1
1
1
26 313259F
Technical Data
Maximum Working Pressure
High Pressure Fluid Hose . . . . . . . . . . . . . . . . . . . . . See
Heated Fluid Circulation Components . . . . . . . . . . . . 95 psi (0.6 MPa, 6.6 bar)
Maximum Temperature Rating . . . . . . . . . . . . . . . . . . . . . 140° F (60° C)
Wetted Parts
High Pressure Fluid Hose . . . . . . . . . . . . . . . . . . . . . Nylon, Zinc-Plated Carbon Steel
Heated Fluid Circulation Tubing. . . . . . . . . . . . . . . . . Nylon
Heated Fluid Circulation Fittings . . . . . . . . . . . . . . . . Aluminum, Brass, Zinc-Plated Carbon Steel
Reservoir Tank. . . . . . . . . . . . . . . . . . . . . . . . . . . . . . Low Density Polyethylene
Heated Hose Weight (50 ft. section) . . . . . . . . . . . . . . . . Dry: 31 lb (14.1 kg)
Wet: 41 lb (18.6 kg)
Technical Data
313259F 27
Graco Standard Warranty
Graco warrants all equipment referenced in this document which is manufactured by Graco and bearing its name to be free from defects in material and workmanship on the date of sale to the original purchaser for use. With the exception of any special, extended, or limited warranty published by Graco, Graco will, for a period of twelve months from the date of sale, repair or replace any part of the equipment determined by
Graco to be defective. This warranty applies only when the equipment is installed, operated and maintained in accordance with Graco’s written recommendations.
This warranty does not cover, and Graco shall not be liable for general wear and tear, or any malfunction, damage or wear caused by faulty installation, misapplication, abrasion, corrosion, inadequate or improper maintenance, negligence, accident, tampering, or substitution of non-Graco component parts. Nor shall Graco be liable for malfunction, damage or wear caused by the incompatibility of Graco equipment with structures, accessories, equipment or materials not supplied by Graco, or the improper design, manufacture, installation, operation or maintenance of structures, accessories, equipment or materials not supplied by Graco.
This warranty is conditioned upon the prepaid return of the equipment claimed to be defective to an authorized Graco distributor for verification of the claimed defect. If the claimed defect is verified, Graco will repair or replace free of charge any defective parts. The equipment will be returned to the original purchaser transportation prepaid. If inspection of the equipment does not disclose any defect in material or workmanship, repairs will be made at a reasonable charge, which charges may include the costs of parts, labor, and transportation.
THIS WARRANTY IS EXCLUSIVE, AND IS IN LIEU OF ANY OTHER WARRANTIES, EXPRESS OR IMPLIED, INCLUDING BUT NOT
LIMITED TO WARRANTY OF MERCHANTABILITY OR WARRANTY OF FITNESS FOR A PARTICULAR PURPOSE
.
Graco’s sole obligation and buyer’s sole remedy for any breach of warranty shall be as set forth above. The buyer agrees that no other remedy
(including, but not limited to, incidental or consequential damages for lost profits, lost sales, injury to person or property, or any other incidental or consequential loss) shall be available. Any action for breach of warranty must be brought within two (2) years of the date of sale.
GRACO MAKES NO WARRANTY, AND DISCLAIMS ALL IMPLIED WARRANTIES OF MERCHANTABILITY AND FITNESS FOR A
PARTICULAR PURPOSE, IN CONNECTION WITH ACCESSORIES, EQUIPMENT, MATERIALS OR COMPONENTS SOLD BUT NOT
MANUFACTURED BY GRACO
. These items sold, but not manufactured by Graco (such as electric motors, switches, hose, etc.), are subject to the warranty, if any, of their manufacturer. Graco will provide purchaser with reasonable assistance in making any claim for breach of these warranties.
In no event will Graco be liable for indirect, incidental, special or consequential damages resulting from Graco supplying equipment hereunder, or the furnishing, performance, or use of any products or other goods sold hereto, whether due to a breach of contract, breach of warranty, the negligence of Graco, or otherwise.
FOR GRACO CANADA CUSTOMERS
The Parties acknowledge that they have required that the present document, as well as all documents, notices and legal proceedings entered into, given or instituted pursuant hereto or relating directly or indirectly hereto, be drawn up in English. Les parties reconnaissent avoir convenu que la rédaction du présente document sera en Anglais, ainsi que tous documents, avis et procédures judiciaires exécutés, donnés ou intentés, à la suite de ou en rapport, directement ou indirectement, avec les procédures concernées.
Graco Information
For the latest information about Graco products, visit
www.graco.com
.
For patent information, see
www.graco.com/patents .
TO PLACE AN ORDER, contact your Graco distributor or call to identify the nearest distributor.
Phone: 612-623-6921 or Toll Free: 1-800-328-0211 Fax: 612-378-3505
All written and visual data contained in this document reflects the latest product information available at the time of publication.
Graco reserves the right to make changes at any time without notice.
Original instructions. This manual contains English. MM 313259
Graco Headquarters:
Minneapolis
International Offices:
Belgium, China, Japan, Korea
GRACO INC. AND SUBSIDIARIES • P.O. BOX 1441 • MINNEAPOLIS MN 55440-1441 • USA
Copyright 2009, Graco Inc. All Graco manufacturing locations are registered to ISO 9001.
www.graco.com
Revision F, December 2015
advertisement
* Your assessment is very important for improving the workof artificial intelligence, which forms the content of this project
Related manuals
advertisement
Table of contents
- 2 Related Manuals
- 3 Warnings
- 5 Heated Hopper or Hose Circulation Kit 256273
- 5 Heated Hose Assembly
- 6 Fluid Heater
- 8 Typical Installation
- 14 Installation
- 14 Grounding
- 14 Tubing Lengths
- 14 Install
- 17 Setup
- 17 Connecting Additional Hose Lengths
- 18 Operation
- 19 Maintenance
- 19 Troubleshooting
- 20 Parts
- 27 Technical Data
- 28 Graco Standard Warranty
- 28 Graco Information