advertisement
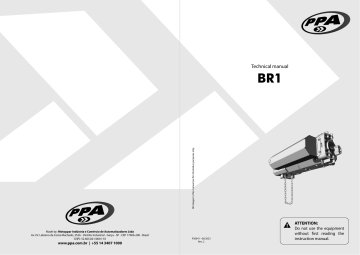
Technical manual
BR1
Made by: Motoppar Indústria e Comércio de Automatizadores Ltda
Av. Dr. Labieno da Costa Machado, 3526 - Distrito Industrial - Garça - SP - CEP 17406-200 - Brasil
CNPJ: 52.605.821/0001-55 www.ppa.com.br | +55 14 3407 1000
P30641 - 06/2023
Rev. 2
ATTENTION:
Do not use the equipment without first reading the instruction manual.
2
INDEX
IMPORTANT SAFETY INSTRUCTIONS ........................................................................................ 3
TECHNICAL CHARACTERISTICS .................................................................................................. 4
TOOLS NEEDED FOR INSTALLATION ........................................................................................ 5
ELECTRICAL INSTALLATION ........................................................................................................ 5
GATE CARE BEFORE OPERATION ............................................................................................... 7
INSTALLATION AND FIXING THE OPERATOR ......................................................................... 7
ADJUSTMENT OF THE ANALOG LIMIT SWITCH ..................................................................12
SAFETY ITEMS ................................................................................................................................14
MAINTENANCE ...............................................................................................................................15
IMPORTANT SAFETY INSTRUCTIONS
Recommendation:
For the installation of the equipment, it is important that the specialized PPA installer follows all the instructions mentioned in this technical manual and in the user manual .
Armed with the user manual , the installer must present all the information, uses and safety items of the equipment to the user.
Before using the operator, read and strictly follow all instructions contained in this manual.
-Before installing the operator, make sure that the local electrical network is compatible with that required on the equipment identification label;
-Do not turn on the mains until the installation/maintenance is completed.
Make the electrical connections of the board always with the mains disconnected;
-After installation, make sure that the gate parts do not extend along the paths and public walkway;
-It is mandatory to use total shutdown devices in the operator installation.
3
4
TECHNICAL CHARACTERISTICS
OPERATOR
MODEL
RATED VOLTAGE
NOMINAL FREQUENCY
RATED POWER
ENGINE ROTATION
NOMINAL CHAIN
REDUCTION
LINEAR SPEED
MANEUVERS
DEGREE OF PROTECTION
STREAMING
TEMPERATURE RANGE
INSULATION TYPE
LIMIT SWITCH
MAXIMUM GATE MASS
MAXIMUM DIMENSION OF THE
GATE
BR1-300
Roll-up door
Single phase
220 VCA
60 HZ
480 W
1740 RPM
3,0 A
1:200
6 m/min
6 cycles/day
IPX4 chain
-5°C /+50°C
Class B, 130°C
Analog
300 kg (~661lb)
Blade #24: (Door height) x (Door width) x 10 = 300 Kg (~661lb)
Blade #22: (Door Height) x (Door Width) x 13 = 300 Kg (~661lb)
OPERATOR
MODEL
RATED VOLTAGE
NOMINAL FREQUENCY
RATED POWER
ENGINE ROTATION
NOMINAL CHAIN
REDUCTION
LINEAR SPEED
MANEUVERS
DEGREE OF PROTECTION
STREAMING
TEMPERATURE RANGE
INSULATION TYPE
LIMIT SWITCH
MAXIMUM GATE MASS
MAXIMUM DIMENSION OF THE
GATE
BR1-500
Roll-up door
Single phase
220 VCA
60 HZ
605 W
1740 RPM
4,0 A
1:200
6 m/min
6 cycles/day
IPX4
Chain
-5°C / + 50°C
Class B, 130°C
Analog
500 Kg (~1102 lb)
Blade #24: (Door height) x (Door width) x 10 = 500 Kg (~1102 lb)
Blade #22: (Door Height) x (Door Width) x 13 = 500 Kg (~1102 lb)
TOOLS NEEDED FOR INSTALLATION
Below are some tools needed to install the operator:
PLIERS HANKSAW CANNON KEY SCREWDRIVER FIXED KEY
LADDER SQUARE DRILL PENCIL SANDERS
SOLDERING MACHINE HAMMER LEVEL TAPE
ELECTRICAL INSTALLATION
For the electrical installation, the network must contain the following characteristics:
- 220 V electrical network;
-Have 5 A circuit breakers in the electric power distribution box;
- 3/4” diameter conduits between the electrical distribution box and the total shutdown device;
-3/4” diameter conduit between the total shutdown device and the point operator connection;
- 1/2” diameter conduits for external and optional pushbuttons;
-1/2” diameter conduit for safety photocells (optional).
5
6
- The cable for the fixed wiring must comply with NBR NM 247-3;
- The power supply conductor of a product for internal use must be a flexible cable 3 x 0.75 mm²; 500 V, according to the NBR standard
NM 247-5;
- The power supply conductor of a product for external use must be a flexible cable 3 x 0.75 mm²; 500V, according to the IEC standard
60245-57.
Mandatory that the earth terminal be connected to the power cable network grounding.
IMPORTANT
The device must be powered via a residual current device (DR) with a rated residual operating current exceeding 30 mA.
GATE CARE BEFORE OPERATION
Before applying the operator to the gate, some procedures must be taken:
-Check if the operator supports the weight of the door leaf;
-Check the mechanical conditions, if there are no impediments to the opening and closing of the door;
-Remove any equipment not necessary for the operation of the device, such as locks, ropes, chains, tools, among others;
-In the case of installation of pushbuttons (fixed control optional), install at a height of at least 1.5 m from the floor, within sight of the door and away from moving parts;
- Fix the risk of crushing warning, available in the operator kit, in visible places or close to the pushbutton (fixed control);
-Check the manual release chain, if it is located at least 1.5 m high from the floor;
-The gate must have a resistant structure and, as far as possible, non-deformable.
INSTALLATION AND FIXING THE
OPERATOR
Before installing the operator, remove all unnecessary cables and disable any equipment or systems connected to the electrical network.
To install the equipment, follow the steps below:
7
1st Step: It is recommended to fix a rigid structure (bracket, not included in the kit) for each side where the door roller bearings will be installed, as shown in the image:
FRENCH HAND
8
Note: Perform the alignment using a level.
2nd Step: Position the header and bearing, along with the door tube in the bracket already installed, as shown in the image:
DOOR TUBE
PILLOW
BLOCK
FOREPART
Note: Use spot welding to fix the head and bearing, make the alignment using the level and as soon as it is level, make a weld bead for better fixing of the positioned components.
3rd Step: Position the Operator BR1 on the forepart fixing screws, aligning the hexagonal output shaft on the pinion, which is also located on the headstock.
Check the image below:
OPERATOR BR1
FIXING
SCREWS HEX AXLE +
PINION
Note: Tighten the screws well and check if the chain remains taut after the
Operator is fixed.
9
10
4th Step: The board is located on the front of the operator. Connect the operator
BR1 harnesses and peripherals to the terminals of the board, according to the table below:
Operator / Peripherals
Capacitor
3 way engine harness
2 way electromagnetic brake harness socket harness
3-way limit switch harness
Open button ( )
Stop button ( )
Close button ( )
Photocell
Rollity Pop Board
CAP
CM AB FC
FEL
R S
FCAC
UP (BT3)
STOP (BT1)
DOWN (BT2)
PHOTO
GND
STOP (BT1)
DOWN (BT2)
UP (BT3)
FCAC
PHOTO
CAP
FC
AB
CM
FEL
R S
5th Step: Centrally fix the blades and the sill to the door tube, as shown in the following image:
1. First assemble 8 profiles to fix the door tube with screws spaced 500 mm apart;
2. Then fit and fix the rest of the blades, including the threshold at the end, as shown in the image below.
SPACED SELF-DRILL-
ING SCREWS
BLADES
THRESHOLD
11
6th Step: Fix the side guides so that the door blades move inside them, see in the image below:
2nd Step: With the door closed, press the lock to release access to the pulley and turn until the micro switch is activated, as shown in the image:
MICRO SWITCH
12
SIDE GUIDES
Note: After fixing the side guides, turn on the Operator BR1 to check the correct operation, both opening and closing.
ADJUSTMENT OF THE ANALOG LIMIT
SWITCH
:
1st Step: Remove the cover of the limit switch box to gain access to the adjustment:
LIMIT SWITCH COVER
LOCK WHEEL
Note: Turn on the operator ( ), if the door does not start to open, repeat the procedure, but placing the other pulley on the other micro switch and take the first pulley to the middle of the course.
3rd Step: With the door open (after turning on Operator BR1 to test the first limit switch, stop ( ) operator BR1 until just before opening the door, press the lock again to release access to the other pulley and turn until it activates the second micro switch, as shown in the image:
SECOND MICRO SWITCH
SECOND WHEEL
13
14
4th Step: With the two limit switches adjusted, do the opening and closing test.
Press the DOWN button ( ) to close the door, after it is completely closed, press the UP button ( ) to open the door and wait for it to open completely. There is also the STOP ( ), option, which works both to stop the door from opening and to stop the door from closing.
SAFETY ITEMS
It is recommended to use a photocell (for doors up to 10 meters), as exemplified in the image below:
It is also recommended to install the Anti-Fall Device, which prevents the door leaf from falling in cases of poor structural installation or unnatural wear of door components. This safety device must be installed on the opposite side of Operator
BR1. As shown in the image below:
ATTENTION
It is not allowed the transit of the people or vehicles during the operation of the automator both in opening and closing, even with safety devices installed.
COMMAND BOARD:
Check the label attached to the product
(according to the model on the side) which is the automation center. After that, consult the control unit manual that is available for download at www.ppa.com.br
and make all the connections and configurations.
Batch:
Code:
Model:
Reduction:
Technology:
Voltage:
Board:
Size:
Mounting:
Housing:
Gear:
MAINTENANCE
In the table below, some PROBLEMS will be mentioned — DEFECTS, PROBABLE
CAUSES AND CORRECTIONS — that may occur in your Operator. Before any maintenance, it is necessary to completely disconnect the electrical network.
DEFECTS
Motor does not start / does not move
Motor blocked
Electronic board does not accept command
Motor only turns to one side
PROBABLE CAUSES
A) Power off
B) Fuse open / blown
C) Locked gate
D) Limit switch with defective
A) Inverted motor connection
B) Locked gate or operator
A) Fuse blown
B) Mains disconnected (power supply)
C) Defect in the discharged remote control
D) Transmitter range (remote control)
A) Inverted motor wires
B) Inverted limit switch system
C) Defect in the command board
CORRECTIONS
A) Make sure the mains is connected correctly
B) Replace the fuse with the same specification
C) Make sure there is no object blocking the gate operation
D) Replace the limit switch system
(analog and/or digital)
A) Check the motor wires
B) Put in manual mode and check separately
A) Replace the fuse
B) Turn on the mains (power supply)
C) Check and change battery
D) Check the position of the receiver antenna and, if necessary, reposition it to ensure range
A) Check the motor connection
B) Invert the limit switch connector
(analog and/or digital)
C) Replace the command board
15
advertisement
Related manuals
advertisement