advertisement
▼
Scroll to page 2
of
57
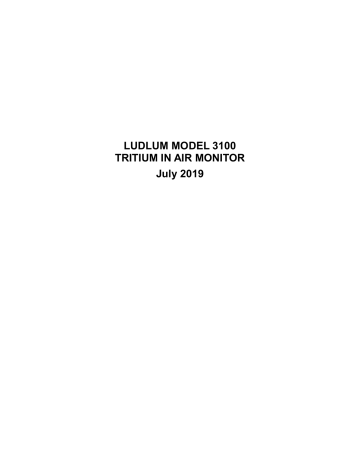
LUDLUM MODEL 3100 TRITIUM IN AIR MONITOR July 2019 LUDLUM MODEL 3100 TRITIUM IN AIR MONITOR July 2019 STATEMENT OF WARRANTY Ludlum Measurements, Inc. warrants the products covered in this manual to be free of defects due to workmanship, material, and design for a period of twelve months from the date of delivery. The calibration of a product is warranted to be within its specified accuracy limits at the time of shipment. In the event of instrument failure, notify Ludlum Measurements to determine if repair, recalibration, or replacement is required. This warranty excludes the replacement of photomultiplier tubes, G-M and proportional tubes, and scintillation crystals which are broken due to excessive physical abuse or used for purposes other than intended. There are no warranties, express or implied, including without limitation any implied warranty of merchantability or fitness, which extend beyond the description of the face there of. If the product does not perform as warranted herein, purchaser’s sole remedy shall be repair or replacement, at the option of Ludlum Measurements. In no event will Ludlum Measurements be liable for damages, lost revenue, lost wages, or any other incidental or consequential damages, arising from the purchase, use, or inability to use product. RETURN OF GOODS TO MANUFACTURER If equipment needs to be returned to Ludlum Measurements, Inc. for repair or calibration, please send to the address below. All shipments should include documentation containing return shipping address, customer name, telephone number, description of service requested, and all other necessary information. Your cooperation will expedite the return of your equipment. LUDLUM MEASUREMENTS, INC. ATTN: REPAIR DEPARTMENT 501 OAK STREET SWEETWATER, TX 79556 800-622-0828 325-235-5494 FAX 325-235-4672 TABLE OF CONTENTS Chapter Page LIST OF ILLUSTRATIONS ..................................................................................................................... iii LIST OF TABLES ...................................................................................................................................iv LIST OF APPENDICES ..........................................................................................................................iv SAFETY SUMMARY .............................................................................................................................. v 1 GENERAL INFORMATION AND SAFETY PRECAUTIONS .............................................................. 1-1 1.1 SAFETY CONSIDERATIONS ............................................................................................................. 1-1 1.1.1 Baseline Conditions ................................................................................................................ 1-1 1.1.2 Avoid Contact with Hazardous Live Parts .............................................................................. 1-1 1.1.3 Keep Out of Water .................................................................................................................. 1-1 1.2 INTRODUCTION ................................................................................................................................. 1-1 1.2.1 Purpose .................................................................................................................................. 1-4 1.2.2 Scope ...................................................................................................................................... 1-4 1.2.3 General Description ................................................................................................................ 1-4 1.3 EQUIPMENT INFORMATION ............................................................................................................. 1-4 1.3.1 Reference Data. ..................................................................................................................... 1-4 1.3.2 Equipment Supplied ............................................................................................................... 1-6 1.4 RECYCLING ........................................................................................................................................ 1-6 1.4.1 Recycling Materials. ............................................................................................................... 1-6 1.4.2 Labeling .................................................................................................................................. 1-6 2 OPERATION........................................................................................................................................ 2-1 2.1 INTRODUCTION ................................................................................................................................. 2-1 2.2 CONTROLS AND INDICATORS ......................................................................................................... 2-1 2.2.1 Description of Controls ........................................................................................................... 2-1 2.3 OPERATIONAL CHECK ..................................................................................................................... 2-4 2.3.1 Purpose .................................................................................................................................. 2-4 2.3.2 Battery Test/Installation .......................................................................................................... 2-4 2.3.3 Check Test.............................................................................................................................. 2-4 2.3.4 Instrument Test ....................................................................................................................... 2-5 2.4 MAINTENANCE ACTIONS ................................................................................................................. 2-7 2.4.1 Scheduled Maintenance ......................................................................................................... 2-7 2.4.2 Storage ................................................................................................................................... 2-7 2.4.3 Desiccant ................................................................................................................................ 2-8 2.4.4 Grease .................................................................................................................................... 2-8 3 SHIPPING AND TRANSPORTATION................................................................................................. 3-1 3.1 LITHIUM BATTERIES ......................................................................................................................... 3-1 4 FUNCTIONAL DESCRIPTION ............................................................................................................ 4-1 4.1 FUNCTIONAL DESCRIPTION ............................................................................................................ 4-1 4.2 OVERALL FUNCTIONAL DESCRIPTION .......................................................................................... 4-2 4.2.1 Handle and Tubing Assembly................................................................................................. 4-2 ii TABLE OF CONTENTS Continued Chapter Page 4.2.2 Filter ........................................................................................................................................ 4-2 4.2.3 Intake ...................................................................................................................................... 4-3 4.2.4 Mass Airflow Sensor ............................................................................................................... 4-3 4.2.5 In-line/Off-line Airflow Desiccant Switch ................................................................................. 4-3 4.2.6 Airflow Desiccant .................................................................................................................... 4-3 4.2.7 Tritium Detector Ion Chamber ................................................................................................ 4-3 4.2.8 Gamma Compensation Ion Chamber Detector ...................................................................... 4-3 4.2.9 Electrometer Board and Temperature Sensor ....................................................................... 4-3 4.2.10 Pump ...................................................................................................................................... 4-3 4.2.11 Power Supply.......................................................................................................................... 4-4 4.2.12 Primary AA Batteries .............................................................................................................. 4-4 4.2.13 Amplifier .................................................................................................................................. 4-4 4.2.14 Processor................................................................................................................................ 4-4 4.2.15 Pressure Sensor ..................................................................................................................... 4-4 4.2.16 Display .................................................................................................................................... 4-4 4.3 PUMP AND AIRFLOW SYSTEM ........................................................................................................ 4-4 4.4 RADIATION DETECTION ................................................................................................................... 4-5 4.4.1 Chambers ............................................................................................................................... 4-5 4.4.2 Electrometer ........................................................................................................................... 4-6 4.4.3 Main Board Radiation Signal Processing ............................................................................... 4-6 5 INSTALLATION ................................................................................................................................... 5-1 5.1 MOUNTING OPTIONS ........................................................................................................................ 5-1 5.1.1 Case Mount ............................................................................................................................ 5-1 5.1.2 Rack Mount............................................................................................................................. 5-2 6 SCHEDULED MAINTENANCE ........................................................................................................... 6-1 6.1 CLEANING .......................................................................................................................................... 6-1 6.1.1 Preparation ............................................................................................................................. 6-1 6.1.2 Clean with Care ...................................................................................................................... 6-1 6.2 BATTERY REPLACEMENT ................................................................................................................ 6-1 6.2.1 Remove Batteries ................................................................................................................... 6-1 6.2.2 Install Batteries Properly......................................................................................................... 6-2 6.3 REPLACING AIRFLOW DESICCANT................................................................................................. 6-2 6.3.1 Inspection and Removal ......................................................................................................... 6-2 6.3.2 Replacement/Rejuvenation .................................................................................................... 6-3 6.4 REPLACING ELECTROMETER DESICCANT ................................................................................... 6-3 6.4.1 Inspection and Removal ......................................................................................................... 6-3 6.4.2 Replacement/Rejuvenation .................................................................................................... 6-4 6.5 REPLACING PARTICULATE FILTER................................................................................................. 6-4 6.5.1 Particulate Filter Removal ...................................................................................................... 6-4 6.5.2 Particulate Filter Replacement ............................................................................................... 6-5 7 TROUBLESHOOTING ........................................................................................................................ 7-1 7.1 FAILURE DURING CHECK MODE ..................................................................................................... 7-1 7.1.1 Temperature ........................................................................................................................... 7-1 7.1.2 Pressure ................................................................................................................................. 7-1 7.1.3 HV+ ......................................................................................................................................... 7-1 7.1.4 HV- .......................................................................................................................................... 7-1 iii TABLE OF CONTENTS Continued Chapter 7.2 7.3 7.4 7.5 7.6 8 Page 7.1.5 Operational Check .................................................................................................................. 7-1 7.1.6 Problem Still Exists ................................................................................................................. 7-1 LOSS OF BIAS (CHAMBER) VOLTAGE ............................................................................................ 7-1 LOSS OF AIRFLOW ............................................................................................................................ 7-1 TEMPERATURE FAILURE ................................................................................................................. 7-2 LOW POWER ...................................................................................................................................... 7-2 LEAKS ................................................................................................................................................ 7-2 7.6.1 Can Assembly Leak Test........................................................................................................ 7-2 7.6.2 Identifying Can Assembly Leaks ............................................................................................ 7-3 7.6.3 Air Circuit Leak Test ............................................................................................................... 7-3 PARTS LIST ........................................................................................................................................ 8-1 APPENDIX A CALIBRATION..................................................................................................................A-1 A.1 CALIBRATION PROCEDURES ....................................................................................................A-2 A.1.1 Equipment Required ..................................................................................................................A-2 A.1.2 Initial Checks ..............................................................................................................................A-2 A.1.3 Computer Connection ................................................................................................................A-3 A.1.4 Setting the Board Offset and Pressure Calibration ....................................................................A-3 A.1.5 Airflow Calibration ......................................................................................................................A-4 A.1.6 Zeroing: Electrometer Offset ......................................................................................................A-4 A.1.7 Tritium Calibration ......................................................................................................................A-4 A.2 USE OF THE CL-1 TRITIUM CALIBRATOR ................................................................................A-5 A.2.1 Equipment Required ..................................................................................................................A-5 A.2.2 Unpacking ..................................................................................................................................A-5 A.2.3 Assemble Calibrator ...................................................................................................................A-5 A.2.4 Leak Check ................................................................................................................................A-6 A.2.5 Initial Procedure .........................................................................................................................A-6 A.2.6 Flushing ......................................................................................................................................A-6 A.2.7 Closed Loop Calibration .............................................................................................................A-7 A.2.8 Calculation of Response ............................................................................................................A-7 137 A.3 USE OF CS GAMMA CALIBRATION RANGE..........................................................................A-8 A.3.1 Equipment Required ..................................................................................................................A-9 A.3.2 Disabling the Gamma Compensation Chamber ........................................................................A-9 A.3.3 Placement of Model 3100 on the Gamma Range ......................................................................A-9 A.4 FINAL CALIBRATION STEPS ....................................................................................................A-10 LIST OF ILLUSTRATIONS Figure 1-1 1-2 1-3 1-4 2-1 2-2 2-3 2-4 iv Title Page Model 3100 ............................................................................................................................. 1-1 Front View Model 3100 ........................................................................................................... 1-2 Model 3100 Case with Mounting Brackets ............................................................................. 1-3 Model 3100 Inside Open Case ............................................................................................... 1-3 Identification of Controls ......................................................................................................... 2-1 Plugging in Power Cord .......................................................................................................... 2-4 Unplugging Power Cord ......................................................................................................... 2-4 First Check Display Screen .................................................................................................... 2-5 LIST OF ILLUSTRATIONS Continued 2-5 2-6 2-7 2-8 2-9 2-10 4-1 4-2 4-3 4-4 5-1 5-2 5-3 5-4 5-5 5-6 6-1 6-2 6-3 6-4 6-5 6-6 7-1 7-2 A-1 A-2 Check Test Screen Ok ........................................................................................................... 2-5 Check Test Screen Fail .......................................................................................................... 2-5 Internal Instrument Test Screen ............................................................................................. 2-6 External Instrument Test Screen ............................................................................................ 2-6 Sample Screen Display .......................................................................................................... 2-7 Prevent Moisture Build-up ...................................................................................................... 2-8 Functional Block Diagram ....................................................................................................... 4-1 Sniffer Handle ......................................................................................................................... 4-2 Particulate Filter ...................................................................................................................... 4-2 Air Flow Diagram .................................................................................................................... 4-5 Back of Case with Wall Mount ................................................................................................ 5-1 Front of Case with Wall Mount ............................................................................................... 5-1 Rack Mount Installation .......................................................................................................... 5-2 Rack Mount Dimensions ......................................................................................................... 5-2 Rotary Draw Latches Detail View BF ..................................................................................... 5-3 Rack Mount Safety Strap ........................................................................................................ 5-3 Battery Lid Removal ............................................................................................................... 6-1 Battery Compartment ............................................................................................................. 6-2 Battery Selection Switch ......................................................................................................... 6-2 Replacing the Airflow Desiccant ............................................................................................. 6-3 Electrometer Desiccant .......................................................................................................... 6-4 Particulate Filter Replacement ............................................................................................... 6-5 Loosening Air Hose ................................................................................................................ 7-2 Vacuum ................................................................................................................................... 7-2 Discharging Gamma Wall Voltage .........................................................................................A-9 Calibration Setup ..................................................................................................................A-10 LIST OF TABLES Number 1-1 1-2 1-3 8-1 8-2 8-3 A-1 Title Page Reference Data ...................................................................................................................... 1-4 Equipment Supplied ............................................................................................................... 1-6 Equipment Required but Not Supplied ................................................................................... 1-6 Parts Details for Model 3100 .................................................................................................. 8-1 Replaceable Parts for Model 3100 ......................................................................................... 8-1 List of Manufacturers .............................................................................................................. 8-2 Recommended Calibration Fields ........................................................................................A-10 LIST OF APPENDICES Appendix A Title Page CALIBRATION .......................................................................................................................A-1 v SAFETY SUMMARY This manual describes operations and organizational-level maintenance of the Model 3100, including the potential associated risks. The user must become completely familiar with the information in this manual and adhere to the procedures, recommendations, warnings and cautions for the safe use, maintenance and storage of this instrument. The following are general safety precautions and instructions that users must understand and apply during use of the Model 3100 to ensure personnel and equipment safety. Portions of this may be repeated elsewhere in this publication for emphasis. DO NOT SERVICE OR ADJUST ALONE! Under no circumstance should any person reach into or enter the enclosure for the purpose of servicing or adjusting the equipment, except in the presence of someone who is capable of rendering aid. RESUSCITATION Personnel working with or near high voltages should be familiar with modern methods if resuscitation. Such information may be obtained from the Bureau of Medicine and Surgery. WARNING, CAUTION AND NOTE STATEMENTS WARNING, CAUTION and NOTE statements have been strategically placed throughout this text prior to operating or maintenance procedures, practices, or conditions considered essential to the protection of personnel (WARNING) or equipment and property (CAUTION). A WARNING or CAUTION will appear each time a related step is repeated. Prior to operating or conducting maintenance on the Model 3100 the WARNINGS or CAUTIONS included in the text for that task will be reviewed and understood. WARNING Users shall conduct all radiation surveys in accordance with Federal and organizational guidelines to prevent hazardous exposure to external radiation sources and/or contamination. WARNING High voltage (115 VAC power and 75 VDC chamber bias) is present in this equipment, which can cause injury to operating or maintenance personnel. Observe the following safety precautions during troubleshooting or maintenance. vi Never disconnect or unsolder cables or components while power is turned on. Always shut off power when connecting test instruments to the equipment. Use one hand only when necessary to move oscilloscope or multimeter probe when power is turned on. Do not use test instruments known to be in poor condition. WARNING The walls of the each ion chamber are at opposite 75volt potentials. Do not contact either wall or its mounting hardware while equipment is operating. CAUTION Avoid immersing the Model 3100 in liquids or allowing spray or rainwater to collect around the instrument. vii CHAPTER 1 GENERAL INFORMATION AND SAFETY PRECAUTIONS 1.1 SAFETY CONSIDERATIONS. There are certain things to consider in order to safely operate the Model 3100 and avoid damaging the instrument and/or causing personal injury. See Safety Summary before the Table of Contents for some general warnings and instructions. 1.1.1 Baseline Conditions. a. Indoor or outdoor use. b. Temperature range of 32°F to 122°F (0°C to 50°C). c. Relative humidity (RH) of 40% to 90%. d. Pollution Degree 3 (Defined by IEC 644. See Table 1-1.), typical of industrial and construction sites. 1.1.2 Avoid Contact With Hazardous Live Parts. Normal operation of the instrument should always be performed with the instrument front panel attached to the instrument can assembly. The operator is warned to take the following precautions to avoid contact with internal hazardous live parts, should it be determined that the chassis needs to be separated from the instrument case. a. Turn the instrument power OFF, disconnect the power cord, and remove the batteries. b. Allow the instrument to sit for one minute before accessing internal components. 1.1.3 Keep Out of Water. This instrument meets the standards as specified by MIL-STD-810G Method 506 procedures I & III for moisture exposure, but it is not waterproof and should never be immersed in or used in standing water. See Table 1-1 for specifics. It is recommended that after operating in a wet or humid environment and the instrument has persistent readings above zero, the instrument be run in SAMPLE or PURGE mode (with AC power) with the desiccant switch set to in-line to ensure the air in the system is dry. 1.2 INTRODUCTION. This Technical Manual is applicable only to the Model 3100 (Figures 1-1 and 1-2), including the case (see Figures 1-3 and 1-4) and related accessories. This Technical manual contains specifications, descriptions of instrument operation and use, and procedures for user maintenance. Figure 1-1. Model 3100 1-1 Figure 1-2. Front View Model 3100. 1-2 Figure 1-3. Model 3100 Case with Mounting Brackets Figure 1-4. Model 3100 Inside Open Case. 1.2.1 Purpose. The purpose of this manual is to provide information that will assist in the operation and user maintenance of the Model 3100 in all its modes of use. Failure to follow the procedures described herein may result in unsatisfactory performance of the equipment. 1-3 1.2.2 Scope. This manual covers operations, technical specifications, and user-level maintenance information required to support the Model 3100. This manual applies to all users of the Model 3100. For more advanced technical information, see the Model 3100 Technical Repair Standard manual. 1.2.3 General Description. The Model 3100 shown in Figure 1-1 is an instrument with a maintenance-free, long-life pump that pulls air through the 250 cc ionization chamber to measure the ionization caused by tritium gas (HT) and to measure air flow internally with a mass air flow sensor. A second internal chamber provides gamma compensation, allowing operation in higher gamma fields. The auto-ranging digital display provides clear indication of the current tritium concentration. The measurement of tritium in air normally measures both tritium gas, designated as HT, and tritiated water vapor, designated HTO. The Model 3100 contains an internal airflow desiccant compartment that can be switched in-line with the incoming airstream, drying the incoming air. The resulting measurement then is (ideally) of HT only. The IN-LINE airflow desiccant may also be used when purging the tritium chamber of adsorbed tritium. The core of the tritium detection is the electrometer chamber, using a state-ofthe-art, low-noise, temperature-compensated electrometer chip. This electrometer can reliably measure the femtoamperes of current resulting from ionization caused by tritium inside the chamber. The digital display provides feedback on the tritium concentration, as well as the status of several important conditions, such as temperature, pressure, power, airflow, chamber bias, and alarm or failure status. 1.3 EQUIPMENT INFORMATION. 1.3.1 Reference Data. Table 1-1 summarizes general information on the Model 3100. Table 1-1. Reference Data. DESCRIPTIVE INFORMATION Manufacturer (Mfr.) Ludlum Measurements Mfr. Part Number 48-4282-1 Mfr. Model Model 3100 Nomenclature Model 3100 SPECIFICATIONS Chamber Aluminum with powder coat finish Chamber Volume approximately 250 cm 1-4 3 Power Requirements 115 VAC 50/60 Hz input with 1.5 A circuit breaker, or 8 internal rechargeable NiMH AA cell batteries, or optional 8 internal nonrechargeable alkaline batteries Primary Battery Life Approximately 16 hours, with pump running continuously Table 1-1. Reference Data, continued. 3 Gamma Compensation Allows for tritium monitoring in up to 5 mR/hr (0.05 mSv/h) gamma fields Display Range 0-20,000 µCi/m (0 to 740 3 MBq/m ) Battery Dependence Calibration changes <5% within battery check limits Temperature 32 to 122 F (0 to 50 C) Humidity Range 40 - 90% RH maintaining response ±15% of reading at 40% RH and 71 °F (22 °C) Effective Range of Measurement From 1 to 10,000 µCi/m (0 3 to 370 MBq/m ) Minimum Detectable Activity (MDA) 2 µCi/m (0.074 MBq/m ) Off, Check, Measure, Sample (Pump On), and Purge Rugged, gasketed, (1) waterproof aluminum enclosure with external user-replaceable 0.2 µm PTFE particulate filter Response Time Approximately 60 seconds Linearity Reading within 20% of true value LCD Display 2.7 in. (6.9 cm) diagonal transflective backlit LCD housed inside the electronics enclosure Pollution Degree 3 (As defined by IEC 644, “Occurs when conductive pollution or dry nonconductive pollution becomes conductive due to condensation.”) Audio 75 ±5 dB at 2ft, at a frequency of 2500 Hz on alarm or failure conditions, may be acknowledged and then reset by operator using ACK / RESET button Output Sealed 9-pin D connector provides potential-free relay contacts for pump active (pins 6 &7) and alarm active (pins 8 & 9), contacts rated for 350V and 120 mA. Also has communication lines to connect to computer for calibration on pins 1-4. Dimensions Instrument: 7.9 x 6.3 x 11.8 in. (20 x 16 x 30 cm) (H x W x L) Weight Instrument: 9 lb (4 kg) with attached cables and tubing Mode Switch Positions Construction Case: 7.9 x 15.5 x 19.9 in. (20 x 40 x 51 cm) (H x W x L) o o 3 3 3 Case: 21 lb (9.5 kg) with detector, 20-ft hose, 35-ft power cord and manual Notes: (1) Lightly falling rain is defined as ¼ inch/hour for a period of 2 hours at 68 °F (20 °C). 1-5 1.3.2 Equipment Supplied. Table 1-2 summarizes the equipment supplied with the Model 3100 and Table 1-3 describes equipment needed but not provided by the manufacturer. Table 1-2. Equipment Supplied. Quantity Item Name Part Number Dimensions Weight 1 Model 3100 48-4282-1 7.9 x 6.3 x 11.8 in. (20 x 16 x 30 cm) (H x W x L) 9 lb (4 kg) with attached cables and tubing 1 Technical Manual Model 3100 Manual 0.5 lb (0.2 kg) 1 1 AC Power Cable Sniffing Hose, Handle 8520-069 21-8486, 4520-136 8.5 x 11 in. (21.6 x 37.9 cm) (H x L) 35 ft (11 m) long 20 ft (6 m) long, 0.25 in (0.64 cm) diameter 1 Case 4520-125 7.9 x 15.5 x 19.9 in. (20 x 40 x 51 cm) (H x W x L) 21 lb (9.5 kg) with contents 2.2 lb (1 kg) 1 lb (0.45 kg) Table 1-3. Equipment Required but Not Supplied. Category Calibration Battery Electrometer Desiccant Recommended Equipment Tritium Gas Calibrator CL-1 or equivalent No. 1 Phillips Screwdriver IP10 or T10 torx drive In-line Desiccant No. 6 Slotted Screwdriver Application Calibration Battery door removal Electrometer desiccant cover removal Desiccant window removal 1.4 RECYCLING. There are recyclable materials used in making the Model 3100. 1.4.1 Recycling Materials. These materials can be found in the Model 3100 and should be recycled separately. a. Batteries-NiMH (nickel-metal hydride), Li-Ion (non-rechargeable coin cells), and/or alkaline b. Circuit boards-fiberglass (FR-4) c. Glass-LCD d. Plastics e. Aluminum and stainless steel 1.4.2 Labeling. The crossed-out wheelie bin lets the consumer know the product is not to be mixed with unsorted waste when discarding. Each material must be separated. The symbol appears on the instrument case as such. 1-6 CHAPTER 2 OPERATION 2.1 INTRODUCTION. The Model 3100 is designed for use in applications where the presence or level of radioactive gas (tritium) must be determined. Radioactive gases, such as tritium, are low-energy beta emitters and must be brought inside the detector in order to obtain an accurate measurement of the level of radioactivity. The Model 3100 employs a flow-through type ionization (or ion) chamber and a small internal pump. Air from the surrounding atmosphere is drawn through the ion chamber, and the level of radioactivity is determined by a measurement of the ionization current occurring within the ion chamber. Another chamber, measuring the local gamma ionizations, is connected in parallel but with reverse voltage, in order to subtract out gamma background. The level of radioactivity in µCi/m3 ( or MBq/m3) of the air is displayed on a digital display. The digital display enables readings to be observed with scale levels of 102, 103, and 104 µCi/m3 of tritium in the air. Whenever the indicated activity exceeds either of the two user defined levels (Alert/Alarm), a latching, “beeping” audible alarm accompanied by the text “Alrm” on the display is energized. The alarm audio can be silenced by pressing the ACK/RESET button once. If the radiation activity decreases below the preset level, a second press of the ACK/RESET button will clear the “Alrm” text from the display. The Model 3100 may be powered either by eight AA-sized rechargeable nickel-metal-hydride NIMH batteries, or eight AA-sized alkaline batteries, or be powered by a mains power cord, connected at the back end of the instrument. The Model 3100 consists of the following sections: a tritium ion chamber, a gamma compensation chamber, an electrometer amplifier, range-dependent amplifier, microprocessor with A/D inputs, alarm, display, pump drive and pump, power supply, and battery charging circuits. The circuitry incorporates diagnostics enabling determination of the ability of the equipment to perform its intended function. Any failures are indicated by a latching steady audible alarm accompanied by a unique failure text on the display. In addition, a 20-foot sniffing hose is provided for monitoring remote locations that are difficult to access. The operator has access to the controls and indicators and is required to be familiar with their use and presentations during operation of the Model 3100 (See Figure 2-1). 2.2 CONTROLS AND INDICATORS. There are various controls and indicators users should make themselves familiar with prior to use. 2.2.1 Description of Controls. The controls are shown in Figure 2-1 and are described following the figure. 2-1 Figure 2-1. Identification of Controls. 2.2.1.1 Backlight Switch. This is a 295-degree rotary control that adjusts backlight intensity for minimum or maximum lighting contrast. 2.2.1.2 ACK/RESET Switch. Under alarm conditions, the first press of this button acknowledges (silences) the alarm audio, but maintains the “Alrm” text on the display. Once the radiation activity has decreased below the preset level, the second press resets the displayed alarm on the display. When in the CHECK mode, the ACK/RESET is used to toggle between the first check screen and the second check screen (see Section 2.2.1.4b). 2.2.1.3 Airflow Desiccant IN-LINE/OFF-LINE Switch. Located on the back side of the instrument, this toggle switch switches the desiccant in-line with the input airflow or allows the incoming airflow to bypass the airflow desiccant. 2.2.1.4 Mode Switch. This is a five-position rotary switch marked OFF, CHECK, MEASURE, SAMPLE (PUMP ON), and PURGE. 2-2 a. OFF means the unit is turned off. Note that in this position the internal batteries are not being recharged, even if the mains power cord is connected. b. The CHECK mode displays the results of several automatic measurement diagnostics. Diagnostic results that are within tolerance are marked with a check mark, while out-of-tolerance measurements or conditions are marked with the letter “X.” By pressing the ACK/RESET button, the second CHECK mode screen labeled “Check Test” will be activated. This mode is meant to check the electrometer and amplifier and provides a preset bias to the tritium chamber, generating a repeatable reading if internal voltages and the amplifier are working correctly. This preset bias may be disabled during calibration, if desired, so that an external gamma check source may be used instead to perform the same check. If so, then a gamma source is placed on the instrument can at the tritium detector to obtain a repeatable and consistent reading. c. The MEASURE mode allows the unit to measure already-sampled air inside the chamber, without the pump running. Note that the response time is approximately 60 seconds. This is the recommended mode to charge the internal batteries. d. The SAMPLE mode turns on the internal air pump and allows the unit to pull air through the tritium chamber while displaying the current measured tritium concentration. Note that the response time is approximately 60 seconds. High levels of tritium may cause the “Alrm” message to appear on the display, and for a loud “beeping” audio signal to be sounded. Low airflow levels (possibly caused by pinched tubing or a dirty particulate filter) will result in a "Fail Air" text on the display. e. The PURGE selection turns the air pump on and (when mains power is available) activates a heater in the tritium chamber to drive out tritium and/or moisture from the chamber. This mode is used whenever it is suspected that tritium has been adsorbed into the internal chamber walls, resulting in persistent high counts. This condition may occur especially when measuring high levels of tritium in a humid environment. Before starting the PURGE mode, the user should ensure that the air intake is sampling clean non-tritiated air. During the purging operation, it is also recommended to switch the airflow desiccant to IN-LINE so that dry air is entering the chamber. The PURGE mode will activate both the air pump and the internal heater, which has a thermostat set to limit the internal temperature to 149 °F (65 °C). The purge mode has a duration of 7200 seconds (2 hours) and countdown timer, shown on the display. The user should check after a purge cycle is complete and the instrument has returned to normal operation temperatures to see if the tritium level in the instrument has been reduced to normal levels. It may be necessary to repeat the purge cycle if the tritium level is still above normal. 2.2.1.5 Alarm Point Potentiometer. This flat screwdriver-adjustable 295-degree rotary potentiometer adjusts the tritium alarm threshold from 0 (OFF) to 10,000 µCi/m3or equivalent SI units (MBq/m3). Whenever this control is adjusted, the display screen temporarily switches to displaying the adjusted alarm point value. The alarm point value may only be set while CHECK mode is selected. As the potentiometer is rotated and the units are set to µCi/m3, the amount of change varies by 5 while the value is less than 100, varies by 50 when the value is between 100 and 1000, and varies by 500 when the value is greater than 1000. The pop-up alarm point screen MUST be allowed to close (approximately three seconds with no change) and return to the check screen in order to save the new alarm point value. When the instrument is set to utilize MBq/m3 units, the rate of change is equivalent to the same values in µCi/m3. Note: The software allows the user to establish a second non-latching alarm point labeled “Alert,” independent of the user-settable (screwdriver-adjustable) alarm point. 2.2.1.6 Circuit Breaker. Located on the back side of the instrument, this toggle switch, normally in the ON or up position, allows mains AC power from the power cord to power the instrument (automatically switching over from battery power) and recharges the internal AA batteries if needed. The circuit breaker protects the instrument and will disconnect the AC power if more than 2A is pulled by the instrument, and the toggle switch will automatically move to the OFF position. This switch may be used by the user as a power selector switch to disconnect AC power and force the primary AA batteries to supply power to the instrument. 2.2.1.7 AC Power Cord. The AC power cord connects to the receptacle on the back of the instrument. To connect the power cord, align the AC plug with the receptacle, and push firmly in. See Figure 2-2. A slight click may be heard from the locking mechanism. To disconnect the power cord, pull back on the blue housing while holding the cord grip, as shown in Figure 2-3. Failure to pull back on the blue housing properly may result in breakage of the internal locking mechanism inside the AC plug. If this happens, the AC power cord will still function, but not be securely held in place. 2-3 Figure 2-2. Plugging in Power Cord Figure 2-3. Unplugging Power Cord. 2.2.1.8 Relays Connector. Located on the back side of the instrument, this 9-pin “D” connector provides access to dry contacts for two internal relays. These two relays are form “A” relays, supplying contacts for the POWERED and “Alrm” functions. These contacts, rated for 350 V and up to 120 mA of current, can be used to provide remote indication that the internal air pump is powered and/or that the alarm or failure mode is active. 2.3 OPERATIONAL CHECK. 2.3.1 Purpose. To assure proper operation of the instrument between calibrations and periods of non-use, an instrument operational check should be performed daily or prior to each use. This check should include battery test and instrument test. Obtain a reference reading with a check source at the time of initial calibration for use in confirming proper instrument operation. In each case, ensure a proper reading on each scale. If the instrument fails to read within 20% of a reference reading, it should be sent to a calibration facility for recalibration. 2.3.2 Battery Test/Installation. The unit may be operated from the connected AC power cord or from internal batteries. The batteries, if used, should be checked each time the instrument is turned on. See Section 6.2 for the correct procedure to replace the batteries. 2.3.3 Check Test. When the unit is deployed, the first check is to rotate the main rotary switch from OFF to CHECK. The unit powers up and temporarily shows the Ludlum logo. This screen also shows the firmware version number, the alert and alarm setpoints, and the number of hours that the pump has run. All internal relays become active for 3 seconds immediately after power-up, so connected devices should be able to see this test. The screen then displays a diagnostics screen that shows several key parameters and status measurements. Any measurement outside of normal operating bounds will be marked with an “X” on the display. If battery power is too low for operation, the user may operate with the connected mains power cord. Otherwise, the user should ensure that the main power cord is connected, and leave the unit on and charging for several hours prior to use. Note that charging happens in the SAMPLE, MEASURE, and PURGE modes only, and is indicated by the lightning bolt icon next to the battery icon. 2-4 Figure 2-4. First Check Display Screen. 2.3.4 Instrument Test. To assure proper operation of the instrument between calibrations and periods of non-use, the following instrument operational check should be performed daily or prior to use. This test takes less than 60 seconds to complete. Rotate the main rotary knob to the CHECK position. When the first screen (Figure 2-4) is shown, after the pump has shut off (this takes about 8 seconds), press the ACK/RESET button. The second CHECK mode screen, labeled “Check Test,” will then be shown. Two possibilities exist for this test – internal electronic-only test or external source test. For more instructions on how to set up this function, please refer to the Model 3100 software manual. Note: If the airflow has not reached the minimum accepted value before the ACK/RESET button is pressed, the “Fail Air” audible alarm will turn on without the status message being displayed. Pressing the ACK/RESET button to silence the audible alarm will exit the “Check Test” screen. Note: If the “Check Test” value is greater than the alert or alarm values, the audible alarms will be activated without the accompanying text being displayed. Note: At the end of the 60 seconds, the instrument will display one of two screens, depicted in either Figure 2-5 or 2-6. Figure 2-5. Check Test Screen Ok. a. Figure 2-6. Check Test Screen Fail. INTERNAL-A preset bias and the resulting reading may be defined at calibration in order to give a consistent reference reading during the CHECK operation. This reading tests the electronics and amplifier and will generate a repeatable reading if the circuits are functioning properly. If the instrument fails to read within 20% of a proper reading within 60 seconds, it should be sent to a calibration facility for recalibration. See Figure 2-7 for an example of an internal test screen. 2-5 Figure 2-7. Internal Instrument Test Screen. b. EXTERNAL-If desired, an external gamma source can be used during the operational check. In this case, a reference reading with a gamma check source should be obtained at the time of initial calibration or as soon as possible for use in confirming proper instrument operation. The user should place the gamma check source over the dimple on the side of the instrument enclosure marking the center of the tritium chamber. If the instrument fails to read within 20% of a proper reading within 30 seconds, it should be sent to a calibration facility for recalibration. See Figure 2-8 for an example of an external test screen. Figure 2-8. External Instrument Test Screen. c. 2-6 Rotate the rotary switch to the SAMPLE position, to display the following screen (see Figure 2-9), as an example. The following example screen shows the current tritium concentration in bold in the middle of the screen, the temperature, pressure, and power status on the top line, the current airflow in the lower right, and fail indications in the lower left. Ensure that the status of the airflow is NORMAL in the lower left of the screen. A ”Fail Air” warning is given any time the airflow is too low, likely resulting from either a clogged particulate filter or kinked air hoses on the IN or OUT side of the instrument. Replace the particulate filter as described in Section 6.5, or troubleshoot as described in Section 7. Figure 2-9. Sample Display Screen. 2.4 MAINTENANCE ACTIONS.There are several maintenance actions suggested below to help with the continued proper working of the Model 3100. 2.4.1 Scheduled Maintenance. Maintenance and verification activities will increase confidence and extend the usable life of the instrument, and are recommended at the intervals suggested below. 2.4.1.1 Daily When In Use. The operational tests described in Section 2.3 shall be conducted daily or prior to instrument use. The operational tests verify power, chamber bias, high voltage, temperature, pressure, airflow, and include either an electronic or radiological check on the tritium detector. The airflow desiccant, if used, should also be visually checked prior to use. 2.4.1.2 Quarterly. The Model 3100 shall be visually inspected, including airflow and electrometer desiccant condition checks, and cleaned when necessary and at least quarterly, per Section 6.3 and 6.4. 2.4.1.3 Calibration. Instrument response shall be calibrated yearly at a calibration facility. Users shall turn in the Model 3100 within a month of the labeled calibration due date to their servicing calibration facility. See Appendix A for the calibration procedure. 2.4.2 Storage. The instrument and accessories used with the instrument have certain storage requirements, as listed below. 2.4.2.1 Remove Batteries. The AA-size batteries may be removed any time the instrument is placed into storage. Battery leakage may cause corrosion on the battery contacts, which must be scraped off and/or washed using a solution made from lemon juice or diluted vinegar, and mixed 50% with water. 2.4.2.2 Fresh Desiccant. The instrument should be stored with a fresh desiccant in the airflow desiccant chamber to prevent moisture from condensing and freezing on the pump diaphragm. This should not damage the pump, but it will prevent it from operating at temperatures near freezing. It is recommended that after operating in a wet or humid environment and the instrument has persistent readings above zero, the instrument should be run in SAMPLE or PURGE mode (with AC power) with the desiccant switch set to IN-LINE to ensure the air in the system is dry. 2.4.2.3 Humidity. If the instrument is stored in an area with high humidity, rapid changes in temperature should be avoided to reduce the chance of condensation. A storage cabinet with a light bulb inside is one means of keeping the instrument in a slightly warmer-than-ambient temperature environment in order to prevent problems from rapid changes in temperature and humidity. In order to prevent moisture or humidity build-up inside the instrument, any time that the instrument is in storage or not in use, the vinyl hose should be connected to the inlet valve on one side and to the outlet valve on the other. See Figure 2-10. 2-7 Figure 2-10. Prevent Moisture Build-up CAUTION Although this instrument will operate at very high ambient temperatures, battery seal failure may occur at temperatures as low as 100 °F (37 °C). Should battery seal failure occur, corrosion on the battery contacts may appear and battery chemicals may damage interior components. 2.4.3 Desiccant. An airflow desiccant is provided to optionally dry the incoming air in the tritium chamber. A switch on the instrument places this desiccant “IN-LINE” or “OFF-LINE” to the incoming airflow. A clear window is provided to view the desiccant. An electrometer desiccant is also used internally to ensure dryness of the electrometer board and gamma chamber. A small window is provided internally to view the desiccant. If either desiccant remains blue, when visually checked, it can then absorb moisture from the airstream. If the desiccant becomes pink, it should be replaced. See Section 6.3 and 6.4 for the procedures to replace the desiccant. The pink desiccant can be re-used once it is heated to dry off the moisture. See Section 6.3.2 or 6.4.2 on rejuvenation. WARNING The silica used may cause irritation to the skin if handled directly. Please take necessary precautions to avoid long-term physical contact with the silica. Should handling of the product be required, avoid rubbing your eyes or placing your hands in or around your mouth, as the silica may also cause an irritation of the digestive tract. Wash hands with mild soap and water after handling. 2.4.4 Grease. In order for the instrument to remain watertight, dielectric silicone grease must be applied to the front-panel gasket. Anytime the instrument front panel is opened, grease should be reapplied in the front-panel gasket slot. 2-8 CHAPTER 3 SHIPPING AND TRANSPORTATION 3.1 LITHIUM BATTERIES. The Model 3100 contains two lithium metal (non-rechargeable) batteries. WARNING Although the lithium content is low, some precautions and labeling may be required to ship on commercial transportation. The Ludlum part number for the lithium batteries is 2536-273. These batteries have been tested and passed per the UN Manual of Tests and Criteria, sixth revised edition, sub-section 38.3. This report is available upon request from Ludlum Measurements, Inc. Each battery is made of 25 “coin” cells (Panasonic CR1220), with a total of 0.25 g of lithium content in each battery. The two batteries are mounted securely inside the instrument and have a combined lithium content of 0.50 g. 3-1 CHAPTER 4 FUNCTIONAL DESCRIPTION 4.1 FUNCTIONAL DESCRIPTION. The Model 3100 is intended for continuous measurement of tritium activity concentration in the ambient atmosphere. Tritium, which is a low-energy beta emitter, must be brought inside the detector in order to be detected. The instrument employs a pump and a flow-through pneumatic system to circulate ambient air through the otherwise sealed ion chamber detector. The level of activity is determined by measuring the ionization occurring within the chamber. The level of radioactivity in microcuries per cubic meter of air is shown on the digital display. Three ranges provide full-scale levels of 102, 103, and 104 µCi/m3 of tritium in the air. An audible alarm can be preset so that the user is notified when the alarm level is exceeded, and must be manually reset whenever triggered. The instrument is shown in block diagram in Figure 4-1. The unit consists of an inlet filter, tritium detector, gamma compensation ion chamber, an electrometer amplifier, a range-dependent amplifier, display, alarm circuit, pump drive and pump, power supply, and battery charging circuits. See overall description following the diagram. Figure 4-1. Functional Block Diagram. 4-1 4.2 OVERALL FUNCTIONAL DESCRIPTION. The following information describes the overall functions of the Model 3100. 4.2.1 Handle and Tubing Assembly. Air to be measured for tritium is brought to the instrument via a sniffer handle/wand (Figure 4-2) and 20 feet of tubing. This handle is convenient to hold in order for the user to direct the input to a particular location. The handle and tubing assembly is connected to the particulate filter. Figure 4-2. Sniffer Handle. 4.2.2 Filter. The particulate filter’s function is to filter incoming air (see Figure 4-3), capturing dust or other particles that might disturb the tritium measurement. The filter is normally connected to the intake nozzle on the instrument and to the incoming wand and tubing assembly. The filter may become clogged over time, restricting the airflow, and need to be replaced. It is secured in place by a black elastic strap. See Section 6.5 for replacement instructions. Figure 4-3. Particulate Filter. 4-2 4.2.3 Intake. The brass intake nozzle is located on the front, left end of the instrument, and is designed to fit 0.25inch tubing. Under most applications, the vinyl tubing connected here connects to the particulate filter mounted on the front of the instrument and conducts the air inside the instrument. 4.2.4 Mass Airflow Sensor. The flow of air into the instrument is measured by a mass airflow sensor connected internally to the intake nozzle. The mass airflow sensor produces an analog voltage that the main board measures and converts to an airflow in L/min (liters of air per minute). The mass airflow sensor is connected to the in-line/offline desiccant switch. 4.2.5 In-line/Off-line Airflow Desiccant Switch. The in-line/off-line airflow desiccant switch is located on the back end of the instrument, and is connected to the incoming air through the mass airflow sensor. The function of the in-line/off-line airflow desiccant switch is to divert the incoming air through the instrument’s desiccant chamber when in the in-line (down) position. When off-line (or up) position, the incoming air bypasses the desiccant chamber and enters the chamber directly. 4.2.6 Airflow Desiccant. The airflow desiccant chamber is mounted on the back of the instrument, and serves to dry the incoming air whenever the desiccant switch is in the in-line position. The desiccant used is a color-indicating silica gel that is blue when the desiccant is able to absorb moisture, and pink when it is saturated with moisture. The color of the desiccant may be seen through the window on the back end of the instrument. See Section 6.3 on replacement of the desiccant. Dry air exits this chamber and enters the tritium chamber. 4.2.7 Tritium Detector Ion Chamber. Incoming air from the desiccant chamber or from the mass airflow sensor (depending on the position of the in-line/off-line desiccant switch) enters the tritium ionization chamber. The polarization voltage applied to the tritium chamber causes a low-level current to flow when ionization occurs in the ion chamber detector. The magnitude of this current is directly proportional to the level of tritium present in the air being monitored. The mark on the instrument can closest to the back of the instrument identifies the center of the tritium chamber. Note that ionization of the air being monitored can also be produced by either a radioactive contaminant in the air or by the action of a background gamma radiation incident to the tritium detector. Since it is the purpose of this unit to measure the concentration of tritium in the air, the contribution made by gamma background must be subtracted. This subtraction is accomplished by means of the gamma compensation ion chamber detector. 4.2.8 Gamma Compensation Ion Chamber Detector. The gamma compensation ion chamber detector is equal in size and shape to the tritium detector but is isolated from the air being monitored. It will only react to gamma radiation. The mark on the instrument can closest to the front of the instrument identifies the center of the gamma chamber. The current produced by this detector is electrically subtracted from the tritium chamber’s current by the electrometer board, which provides an output voltage proportional to the tritium level only. 4.2.9 Electrometer Board and Temperature Sensor. The electrometer board is mounted to the gamma and tritium chambers and is connected to the electrodes of both chambers. The signal produced by the detector is an extremely low DC current in the order of femtoamperes that is applied to the electrometer, which converts the lowlevel DC current into a DC voltage to send to the amplifier on the main board. The electrometer board also has a temperature sensor that produces an analog voltage. This analog voltage is measured by the microprocessor on the main board. The electrometer board has a gasketed lid with a window to view the desiccant. To work effectively, the electrometer board must be kept clean and dry. 4.2.10 Pump. The pump draws incoming air through the instrument and through the tritium ion chamber detector. The air passes through the pump and is then exhausted from the equipment by the OUT nozzle back into the area being monitored or to a designated location. The pump used to draw air into the tritium chamber is a relay-driven positive displacement pump. It is powered by the pump drive circuit, consisting of a transistor switch and switching power supply. 4-3 4.2.11 Power Supply. The equipment is capable of operating from 115 VAC 50/60 Hz power or from internal AA-sized batteries. Input AC power passes through a circuit breaker and is applied to a power supply board that regulates it to a constant +12 VDC supply. While the instrument is operating with AC power applied, the internal batteries, if low, may be recharged with a constant (approximately 200 mA) circuit. The +12 VDC regulated voltage provides input power to the main board, which produces 5 VDC and several other voltages. The power supply also has a relay to activate the tritium chamber heater when in the PURGE mode, as well as signal relays that provide contacts for remote indication of alarm and sampling conditions. 4.2.12 Primary AA Batteries. The instrument may be operated from internal AA batteries, mounted in a battery compartment at the bottom of the instrument. See Section 6.2 for replacement of these batteries. Nickel-metal hydride (NIMH) or alkaline batteries may be used. Note that the battery compartment does also contain a selfresetting fuse (a positive temperature coefficient resistor) designed to protect the batteries from short circuits. The batteries can be either rechargeable or non-rechargeable. Ensure the selector switch is switched to the correct type. 4.2.13 Amplifier. The output of the electrometer is applied to the range-dependent amplifier on the main board for current amplification to input to the A/D converter of the microprocessor. This amplifier provides three levels of gain, adjusted by the microprocessor for the three ranges of measurement from 0-100 µCi/m3, 100-1000 µCi/m3, or 1000 to 10,000 µCi/m3 (or Bq/m3 equivalent). The microprocessor uses the serial communications lines SDI and SCL to communicate with the transflective LCD (liquid crystal display). 4.2.14 Processor. The processor is located on the main board and is responsible for handling all the inputs and outputs of the instrument. The instrument’s firmware is stored in flash memory on the processor. The processor also has variables and parameters that may be adjusted via software. Inputs to the processor include analog voltages representing temperature, pressure, chamber bias, and the amplified electrometer signal. The outputs include a pulse-width-modulated (PWM) output for an electrometer offset, as well as digital outputs to turn on the internal heater and the airflow pump. 4.2.15 Pressure Sensor. The pressure sensor is located on the main board and produces an analog voltage related to the atmospheric pressure. This voltage is measured and utilized by the microprocessor to make compensations for the variation in air density. 4.2.16 Display. The display, located on the front panel, supplies status and measurement information to the user. The tritium concentration level, which can be displayed in µCi/m3 or Bq/m3, is displayed in a large font. Other information, like current temperature or pressure, is less prominent. The display has a backlight, controlled by a 295degree rotary control on the front panel. The display is controlled by a serial interface by the microprocessor. 4.3 PUMP AND AIR FLOW SYSTEM. The air flow system is shown in Figure 4-4. Air is drawn into the instrument through the input particulate filter. The air then moves to the mass airflow sensor and then to the airflow DESICCANT SWITCH. When the switch is in the IN-LINE position, the air flows through the desiccant chamber, which dries the air. When the switch is in the OFFLINE position, the air bypasses the desiccant chamber and goes straight to the tritium ion chamber. The tritium ion chamber detector is where the ionization, occurring while the air containing tritium is in the detector, is collected as ionization current. This current is proportional to the tritium level in the chamber. If the gamma background radiation is compensated for, this tritium chamber current is exactly proportional to the tritium (or other radioactive gas contamination present in the air stream). The air is then removed through the pump and then to the OUT outlet. The pump operates on a regulated direct current voltage provided by the power supply on the main board. 4-4 Figure 4-4. Air Flow Diagram. 4.4 RADIATION DETECTION. The Model 3100 has two ionization chambers – one to measure tritium and the other to subtract out background interference from the tritium measurement. These two chambers are mounted into the bottom of the instrument can, which has marks on the outside to identify the center of each chamber. The mark on the instrument can closest to the front of the instrument identifies the center of the gamma chamber. The mark on the instrument can closest to the back of the instrument identifies the center of the tritium chamber. The chambers are mounted together on an aluminum plate, with the electrometer circuit board mounted on the top of the plate. These two chambers and the associated electrometer board (commonly called an electrometer) are the basis for the radiation detector of Model 3100. 4.4.1 Chambers. The cylindrical chamber housings, approximately 250 cc in volume, are constructed from drawn aluminum and are powder-coated black on the outside wall. Chamber wall thickness is 0.032 in. (0.081 cm). The wall of the tritium chamber, which is electrically isolated, is maintained at approximately -75 VDC, while the wall of the gamma chamber, which is also electrically isolated, is maintained at approximately +75 VDC. The center electrodes of both chambers are connected electrically together at the electrometer board. Since gamma background affects both chambers, this parallel subtracting arrangement provides the gamma compensation so that the resulting electrometer signal is due solely by the additional ionization within the tritium chamber. The electrodes of both ionization chambers are connected to the electrometer board input and are maintained at guard potential by the electrometer. For air (at standard temperature and pressure: 22 °C and sea level), the average energy W to ionize a single ion pair is 34 eV/ion pair. The expected ionization current per µCi (37,000 disintegrations per second) of tritium (identified as “I” in the following equation) in the chamber, given a W of 34 eV in air, the charge of an electron equaling 1.60207 x 10-19 C, and an average beta tritium energy of 5.65 keV (assuming negligible wall losses since the maximum range in air of tritium is approximately 5 mm) is: I = (5.65x103 eV) x (37,000 disintegrations per second) x (1.60207 x 10 -19 C) / 34 eV 4-5 I = 9.9 x 10-13 coulombs/sec I = 0.99 pA ( per µCi of tritium) 4.4.2 Electrometer. The electrometer consists of summed electrodes providing a net signal to the input of a guarded trans-impedance amplifier with a feedback resistor that provides a short time constant. A short time constant means that the chamber reacts quickly. Large spikes in the output data are caused by radon or other alpha emitters, which have approximately 1000 times the energy of the tritium beta particle (5.5 MeV vs 5.65 keV). These spikes are filtered out in firmware, without affecting the tritium signal, using a proprietary algorithm. Given a chamber volume is 250 cm3, and that the current is measured with a feedback resistor of 500 Gohm (=500x109 ohms), then the resulting voltage output of the electrometer V, per microcurie/m 3 is: V = (0.99 x 10-12) (250 x 10-6)(500 x 109) = 0.124 mV per µCi/m3 The voltage output of the electrometer board is then connected to the main board for further processing. 4.4.3 Main Board Radiation Signal Processing. 4.4.3.1 Amplifier Range Change. The microprocessor on the main board controls the amplification of the electrometer signal. The Model 3100 is auto-ranging so the user doesn’t have to switch a range control as the radiation level changes, but internally, the microprocessor controls three ranges to properly adjust the amplifier gain. The microprocessor starts in the X1 range, which covers from 1 to 100 µCi/m3 (0.037 to 3.7 MBq/m3). When the chamber reaches 100 µCi/m3 (3.7 MBq/m3), the output of the electrometer is 12.4 mV relative to guard potential, and the gain on the main board is switched to the X10 range. When the chamber reaches 1000 µCi/m3 (37 MBq/m3), the output of the electrometer reaches 124 mV relative to guard potential, and the gain on the main board is switched to the X100 range. The top calibrated reading is 10,000 µCi/m3 (370 MBq/m3) when the output of the electrometer reaches 1240 mV relative to guard potential. 4.4.3.2 Offset Adjustment. The electrometer operational amplifier (op amp) will have some offset voltage. An internal calibration control on the main board marked OFF provides an offset voltage that can be adjusted during calibration to null out the electrometer offset voltage. 4.4.3.3 Analog-To-Digital Input. The voltage from the amplifier section of the main board then enters the analog-to-digital (A/D) input of the microprocessor. The microprocessor samples and measures this voltage input every 200 milliseconds. It compares this input to the 2.5 V reference voltage and digitizes the result. The microprocessor uses proprietary digital filters to average the results and then converts the readings into the calibrated displayed reading. 4-6 CHAPTER 5 INSTALLATION 5.1 MOUNTING OPTIONS. Although the Model 3100 is a typical portable, handheld instrument, LMI offers two options for mounting it – a case mount and a rack mount. 5.1.1 Case Mount. As shown in Figure 5-1, attach mounting plates with screws to the case. These plates are supplied with the instrument. Figure 5-1. Back of Case with Wall Mount. Figure 5-2. Front of Case with Wall Mount. 5-1 5.1.2 Rack Mount. This option, as shown in Figures 5-3 and 5-4, is optional. Figure 5-3. Rack Mount Installation. Figure 5-4. Rack Mount Dimensions. 5-2 a. Latch the four rotary draw latches located on the rack mount to the catches on the side of the instrument as shown in Figure 5-5. b. Swing out the handles on the bottom to rotary draw latches on the instrument, but do not turn them to unlatch them. c. Attach the safety strap on the rack mount through the opening in the latch handle as shown in Figure 5-6. Figure 5-5. Rotary Draw Latches Detail View BF. Figure 5-6. Rack Mount Safety Strap. 5-3 CHAPTER 6 SCHEDULED MAINTENANCE 6.1 CLEANING. Cleaning the Model 3100 is important in keeping it in working order and in helping the instrument last. The following is the procedure for cleaning the instrument. 6.1.1 Preparation. Shut the instrument down properly before cleaning. a. Turn the MODE SWITCH to OFF. b. Disconnect the AC power cord if attached. 6.1.2 Clean With Care. CAUTION Do not immerse the instrument in any liquid. Gently wipe all exposed surfaces with a damp cloth, using only water as a wetting agent. Allow instrument to dry thoroughly before reuse. 6.2 BATTERY REPLACEMENT. Turn the MODE switch to OFF, and disconnect the AC power cord if attached before replacing the batteries. 6.2.1 Remove Batteries. Open the battery lid by removing the screws (Figure 6-1). Remove the 8 NIMH AA batteries from the compartment (see Figure 6-2). Figure 6-1. Battery Lid Removal 6-1 6.2.2 Install Batteries Properly. Install 8 NIMH AA batteries into the compartment (see Figure 6-2), taking care to orient all batteries correctly. Note the (+) and (-) marks inside the battery holder. Match the battery polarity to these marks. Figure 6-2. Battery Compartment. Insert all batteries to match these marks. The center post of each battery is positive. Note that batteries are placed in the battery compartment in alternating directions. Ensure the battery selection switch (Figure 6-3) is in the correct position for rechargeable or non-rechargeable batteries. Figure 6-3. Battery Selection Switch Reinstall the battery lid by tightening all the screws around the perimeter of the battery lid. 6.3 REPLACING AIRFLOW DESICCANT. In the event the desiccant needs to be inspected and/or replaced, perform the following procedure. 6.3.1 Inspection and Removal. Visually inspect the desiccant. A clear window is provided to view the desiccant. 6-2 a. If the desiccant is all blue, then it is dry and in working order and can absorb moisture from the air stream, when the airflow toggle switch is set to IN-LINE. b. If the desiccant is pink, remove the clear lid using the two thumbscrews, empty out the desiccant, and replace it with a fresh blue desiccant. 6.3.2 Replacement/Rejuvenation. The pink (wet) desiccant may be replaced with a blue (dry) desiccant or may be rejuvenated as follows: a. Rejuvenate the desiccant by: (1) Placing the pink desiccant in an oven at 240 °F (115 °C) for three hours, or (2) Placing the pink desiccant in a microwave oven on the high setting for 20 seconds. (3) If water vapor is apparent, wipe off the water and heat for another 20 seconds. Repeat this step until the box and desiccant appear dry and blue in color. b. Once the desiccant is replaced or rejuvenated, reinstall the clear lid with the two thumbscrews. See Figure 6-4. Tighten until hand tight, do not use a screwdriver. Figure 6-4. Replacing the Airflow Desiccant. Note: Overfilling the compartment with desiccant material may prevent air flow. The lid should not be off for prolonged periods. The instrument SHALL NOT be operated without the lid or with a damaged lid. c. Verify that airflow is ok with the desiccant switch in the IN-LINE position. 6.4 REPLACING ELECTROMETER DESICCANT. In the event the desiccant needs to be inspected and/or replaced, perform the following procedure. 6.4.1 Inspection and Removal. Turn the rotary Mode knob to OFF and remove the power cord if applicable. Open the instrument using the four rotary draw latches on the sides of the instrument and carefully lay the front panel over so that the electrometer section is visible. Visually inspect the desiccant. A clear window in the electrometer lid is provided to view the desiccant. 6-3 a. If the desiccant is all blue, then it is in working order and will protect the sensitive electrometer electronics from moisture. b. If the desiccant is pink, carefully remove the electrometer lid using the four screws and replace the desiccant packs with new or rejuvenated desiccant packs. Note: It is recommended to remove HV bias batteries and discharge chamber wall voltages (using HV bias battery slug), and to disconnect the electrometer board ribbon cable before removing electrometer lid. CAUTION Be careful not to touch the electrometer board with your bare hand. Oils from your skin can cause electrical leakage, resulting in erratic readings. 6.4.2 Replacement/Rejuvenation. The pink (wet) desiccant may be replaced with fresh desiccant packs or rejuvenated as follows: a. Rejuvenate the desiccant by: (1) Placing the pink desiccant in an Erlenmeyer flask in a microwave oven on the high setting for a maximum of 20 seconds. Then allow to cool for a minimum of 60 seconds. (2) If water vapor is apparent, wipe off the water and heat for 20 seconds. Repeat these steps until no water vapor is seen. b. Once the desiccant is replaced or rejuvenated, replace the electrometer lid using the four screws. See Figure 6-5. Figure 6-5. Electrometer Desiccant. 6.5 REPLACING PARTICULATE FILTER. The particulate filter is user-replaceable and is located at the front of the instrument. Under normal use, it will gradually become clogged with trapped particles and limit the airflow. In the event the particulate filter at the front of the instrument needs to be inspected and/or replaced, perform the following procedure. (See Figure 6-6.) 6.5.1 Particulate Filter Removal. Turn the rotary Mode knob to OFF and remove the power cord if applicable. Disconnect the short airline connected to the top of the particulate filter. Disconnect the T-strap at the top of the 6-4 instrument that secures the particulate filter. Pull the particulate filter out and disconnect the hose located at the bottom of the filter. The particulate filter is now removed from the instrument. 6.5.2 Particulate Filter Replacement. Reconnect the input airline, if used, at the bottom of the particulate filter, and insert the particulate filter down into its housing. Reconnect the T-strap to secure the particulate filter, ensuring that the T-strap is run between the filter nozzle and the filter bracket. Reconnect the short airline previously connected to the top of the particulate filter. Plastic (“zip”) ties may be used to secure the airlines. See Figure 6-6. Figure 6-6. Particulate Filter Replacement. 6-5 CHAPTER 7 TROUBLESHOOTING 7.1 FAILURE DURING CHECK MODE. A FAIL or “X” on the display when the Mode switch is in the CHECK position can be caused by a number of different problems. Note that this section contains information for procedures for both user (organizational level) and repair (intermediate level) personnel. 7.1.1 Temperature. If the internal operating temperature goes outside the normal operating range of the instrument (from 32 to 122 oF {0 to 50 °C}), and this temperature is not obviously caused by environmental conditions, an adjustment of the instrument by a technician may be required. 7.1.2 Pressure. If the internal pressure goes outside the normal operating range of the instrument (from 76 to 120 kPa), and this pressure is not obviously caused by environmental conditions, an adjustment of the instrument by a technician may be required. 7.1.3 HV+. If the internal positive high voltage (used to bias the internal gamma chamber) goes outside the normal operating range of the instrument (from 50 to 100 VDC), a replacement of this internal battery by a technician may be required. 7.1.4 HV-. If the internal negative high voltage (used to bias the internal tritium chamber) goes outside the normal operating range of the instrument (from -50 to -100 VDC), a replacement of this internal battery by a technician may be required. 7.1.5 Operational Check. The operational check may be performed electronically or with an external gamma source. In either case, a failure to measure the correct value within 20% may result. If an external gamma source is being used, ensure that it is the correct source and that the placement of the source is correct per Section 2.3.4. If this action does not result in a correct reading, repair by a technician may be required. 7.1.6 Problem Still Exists. If after performing the operational check, and/or battery replacement (as appropriate) the instrument still exhibits an improper reading, the problem is most likely electrical in nature and service by a technician may be required 7.2 LOSS OF BIAS (CHAMBER) VOLTAGE. If during power on, or whenever the CHECK position of the Mode switch is chosen, the words “Fail HV Pos” (positive) or “Fail HV Neg” (negative) show on the display, then it is likely that one or both lithium coin cell batteries is old or weak. Replacement of these internal batteries by a technician may be required. 7.3 LOSS OF AIRFLOW. If a minimum airflow of 0.8 L/min is not maintained, a message on the display will warn of “Fail Air.” Low airflow is most commonly the result of a clogged particulate filter. The particulate filter should be replaced immediately, or the instrument response time may be longer than desired. If replacing the particulate filter does not clear the “Fail Air” message, then some other airflow restriction may be present. Check the IN and OUT hose connections to see if the restriction can be pinpointed and corrected. It is also possible that the airflow desiccant window does not have a good seal. Remove the window and inspect the gasket beneath to ensure nothing has compromised it. 7-1 7.4 TEMPERATURE FAILURE. If the temperature reading on the display begins to flash, then the measured temperature is beyond the operating temperature range of the instrument. To restore proper operation, reduce or increase the temperature as necessary. If this message is seen in error, then it is possible that the temperature sensor, located on the electrometer board, has failed and should be replaced by a technician. 7.5 LOW POWER. If the message "Low Batt" is shown on the display, then it is likely that the primary batteries need to be replaced or recharged. Ensure that when replacing batteries (Section 6.2), the battery selection switch (Figure 6-3) is in the correct position for rechargeable or non-rechargeable batteries. Alternatively, operation is possible if the 115 VAC power cord is properly connected into a source of 115 VAC power. If operation is not restored by this action, also ensure that the circuit breaker on the back of the instrument is not toggled to the OFF (down) position. 7.6 LEAKS. Perform the can assembly and the air circuit leak tests if a leak is suspected. The leak test procedure for the Model 3100 ensures that the air circuit is functioning properly and water ingress will be limited to ensure compliance with MIL-STD-810G Method 506 Procedures I and III. 7.6.1 Can Assembly Leak Test. a. Open the front panel of the Model 3100 by loosening the four latches. b. Loosen an air hose fitting from the desiccant switch. See Figure 7-1. Figure 7-1. Loosening Air Hose. c. Apply grease to the front-panel gasket as required. d. Close the front panel by securing all four latches tightly. e. Attach the handheld vacuum pump to the OUT port located under the air filter. See Figure 7-2. f. Plug the IN port. See Figure 7-2. Figure 7-2. Vacuum. 7-2 g. Apply a vacuum of -5 inches Hg. h. If the vacuum is held, proceed to Air Circuit Leak Test, Section 7.6.3. i. If the vacuum is not held, identify and repair leaks. 7.6.2 Identifying Can Assembly Leaks. a. Open the front panel of the Model 3100 by loosening the four latches. b. Loosen an air hose fitting from the desiccant switch. See Figure 7-1. c. Apply grease to the front-panel gasket as required. d. Close the front panel by securing all four latches lightly. e. Attach the handheld air pump (electronic pump such as the one in the Model 3100 may be used with caution) to the OUT port located under the air filter. See Figure 7-2. f. Plug the IN port. g. Apply air pressure. h. Water test options: (1) Dunk the unit under water while applying pressure in order to locate air bubbles. (2) Spray the unit with soapy water/bubbles while applying pressure to identify leaks. Note: The desiccant door will likely leak when applying pressure above 1 psi. Continue to look for other leaks. 7.6.3 Air Circuit Leak Test. a. Open the front panel of the Model 3100 by loosening the four latches. b. Ensure all air hoses are properly connected. Note: The desiccant switch hoses may have been loosened during the Model 3100 can leak test. c. While the front panel is open, attach the vacuum pump to the OUT port located under the air filter. See Figure 7-2. d. Plug the IN port. See Figure 7-2. e. Apply a vacuum of -5 inches Hg. f. Verify that the vacuum is holding before proceeding. g. If the vacuum will not hold, identify and repair the leak. Repeat the air circuit leak test before proceeding. 7-3 CHAPTER 8 PARTS LIST Table 8-1. Parts Details for Model 3100. The Model 3100 Tritium-In-Air Monitor comes in a case with its accessories. Part Number Manufacturer CAGE Code Reference Number Model 3100 48-4282-1 Ludlum 23609 Figure 1-1 In-air tritium monitor, including accessories Model 3100 Case Assembly 4520-125 Ludlum 23609 Figure 1-2 Case with foam inserts and bulkhead mount Sniffer Hose 21-8486 McMasterCarr Supply 39428 Figure 4-4 20 ft (6.1m) of 1/4 inch PVC clear tubing Sniffer Handle 4520-136 Ludlum 23609 Figure 4-2 Handle with grip attached to tubing AC Power Cable 8520-069 Ludlum 23609 Figure 4-2 35 ft (11 m) long power cord Item Description Table 8-2. Replaceable Parts for Model 3100. Other replaceable parts referenced in this manual include: Item Part Number Manufacturer CAGE Code Reference Number Description Batteries 21-8844 Duracell 90303 Figure 6-2 NIMH AA batteries Desiccant 03-6017, 03-6120 Multisorb 22627 Figure 6-5 1g, 1.5g desiccants in electrometer Desiccant 03-6016 Sorbent Systems, IMPAK Figure 6-4 Bulk desiccant in desiccant box Figure 6-6 0.2 micron PTFE filter in polypropylene housing Particulate Filter 7520-133 1WRS2 Ludlum 23609 8-1 Table 8-3. List of Manufacturers. 8-2 CAGE Code Name and Address 23609 Ludlum Measurements, Inc. 501 Oak Street Sweetwater, TX 39428 McMaster-Car Supply Company 600 North County Line Elmhurst, IL 60126 90303 Duracell Duracell Berkshire Corporate Park Bethel, CT 06801 22627 Multisorb Technologies 325 Harlem Rd. Buffalo, NY 14224 1WRS2 IMPAK Corporation 13700 S. Broadway Los Angeles, CA 90061 APPENDIX A CALIBRATION Section Page A.1 CALIBRATION PROCEDURES ....................................................................................................A-2 A.1.1 Equipment Required ............................................................................................................A-2 A.1.2 Initial Checks .......................................................................................................................A-2 A.1.3 Computer Connection ..........................................................................................................A-3 A.1.4 Setting the Board Offset and Pressure Calibration..............................................................A-3 A.1.5 Airflow Calibration ................................................................................................................A-4 A.1.6 Zeroing: Electrometer Offset................................................................................................A-4 A.1.7 Tritium Calibration................................................................................................................A-4 A.2 USE OF THE CL-1 TRITIUM CALIBRATOR ................................................................................A-5 A.2.1 Equipment Required ............................................................................................................A-5 A.2.2 Unpacking ............................................................................................................................A-5 A.2.3 Assemble Calibrator ............................................................................................................A-5 A.2.4 Leak Check ..........................................................................................................................A-6 A.2.5 Initial Procedure ...................................................................................................................A-6 A.2.6 Flushing ...............................................................................................................................A-6 A.2.7 Closed Loop Calibration ......................................................................................................A-7 A.2.8 Calculation of Response .....................................................................................................A-7 A.3 USE OF 137 CS GAMMA CALIBRATION RANGE..........................................................................A-8 A.3.1 Equipment Required ............................................................................................................A-9 A.3.2 Disabling the Gamma Compensation Chamber ..................................................................A-9 A.3.3 Placement of Model 3100 on Gamma Range .....................................................................A-9 A.4 FINAL CALIBRATION STEPS ....................................................................................................A-10 A-1 A.1 CALIBRATION PROCEDURES. All instruments used in the calibration of the Model 3100 must be calibrated by standards traceable to the National Institute of Standards and Technology and must have a current calibration label attached. Calibration for the Model 3100 involves calibrating the pressure, the airflow, tritium calibration, and check source reading of the instrument. A.1.1 Equipment Required. LMI can provide the following items: a. Model 3100 calibration software (part # 1370-090) b. RS-232 9-pin D to phone plug adapter cable (part # 8303-1038) c. Connector RJ11 inline coupler (part # 2313770) d. Model 9-4 pressure calibration kit (part # 4293-675) e. Calibrated air flowmeter (part # 2313771) f. Gamma +HV battery replacement “slug” (part # 7520-152) The other required equipment items include: g. A 137Cs source capable of exposure rates of 0.25 mR/hr to 25 mR/hr, if using the gamma calibration method, OR a Model CL-1 Tritium Calibrator with traceable tritium gas cylinder attached h. Weather station or barometer to measure current temperature and atmospheric pressure i. Low background area (≤ 10 µR/hr) A.1.2 Initial Checks. If any calibration procedure cannot be completed satisfactorily, the instrument shall be tagged and removed for proper disposition. A-2 a. Check the condition of both the external and internal desiccants. Replace if necessary. Use only fresh or revitalized desiccants. Refer to the proper section in the manual for replacement procedures. If replacements are made, wait at least 24 hours before continuing calibration process. b. Perform mechanical checks and visual inspections to ensure that the switches, buttons, seals, and other mechanical devices function properly and that no obvious defects are present. Turn the desiccant switch on the back panel to OFF-LINE. c. Turn the instrument on, rotating the mode switch to the CHECK position. Verify the audio is activated briefly, and record the firmware number from the initial screen. d. From the CHECK display, verify battery voltage and/or +12 VDC voltage from mains voltage. Ensure that mains power measures +12 VDC or above when the mains cord is plugged in and the circuit breaker is in the active or up position. If using rechargeable batteries, ensure that they are above +10 VDC, or charge overnight and check again. If using non-rechargeable batteries, ensure that battery voltage is above +10 VDC. e. Verify also, from the CHECK display, that both the HV+ and HV- (the two bias batteries) are reading at ±50 to 100 V or above. Replace the HV bias batteries if necessary, waiting an hour after battery replacement to ensure stable operation before continuing. f. Perform Air Circuit Leak Test. See Section 7.6. g. Ensure that the airflow is OK (typically between 1.0 and 2.0 L/min). Low airflow is typically caused by either a kinked hose, a clogged particulate filter, an over-full in-line desiccant box, or the desiccant box door not sealed properly. Straighten or replace the hose, replace the filter as necessary to restore normal airflow, remove excess desiccant material, tighten desiccant door, or remove debris from desiccant door seal. h. While in CHECK Mode, rotate the alarm point potentiometer completely counter-clockwise to zero. When the alarm potentiometer is changed, a pop-up alarm point screen shows the setpoint value. The pop-up alarm point screen MUST be allowed to close (approximately three seconds with no change) and return to the check screen in order to save the new alarm point value. i. If the check screen shows a failure condition, and then fix the condition highlighted on the screen before continuing. If the check screen shows OK, rotate the MODE switch to the MEASURE position. A.1.3 Computer Connection. a. Assuming the interface software has been previously loaded on your PC, connect the USB-to-serial adapter to the test the computer; next connect the other end of the calibration cable to the Model 3100 9-pin “D” connector. Refer to the software manual for further information. b. Pull up the Model 3100 software program on the computer. The first thing you should see when the program loads will be a selector box. Choose the “Model 3100” as the instrument choice. The second screen will be a small dialogue box entitled, Select Device Serial Number, in front of the main program screen. This refers to the USB adapter, which is now plugged into the USB port of your computer. c. Confirm that the serial number displayed in the software matches the instrument’s serial number. If it does not, correct it. (If correcting the instrument serial number is not necessary, skip the remainder of this section and proceed to the Section A.1.4 Pressure Calibration to continue.) d. Once the serial number is corrected, tab over to the next field to get to the Update button on the lower right-hand corner to turn pink. Press the Update button to save the correction just made. e. Do a Ctrl + R (press the Ctrl key followed by the R key) to reload all data. This is to confirm that the correction just made to the serial number has been saved correctly. A.1.4 Setting the Board ADC Offset and Pressure Calibration. a. The following steps b. through m. may be skipped if the unit has been previously calibrated and no repairs have been made. b. From the computer, enter the BOARD ADC VALUE into the Board ADC Offset box. This shall be less than 0.050. If the BOARD ADC VALUE is greater than 0.050, repeat step A.1.2.h. c. Obtain the current atmospheric pressure reading. If the pressure reading is in “inHg” (inches of mercury), convert the pressure reading from inHg to kPa by multiplying the pressure reading by 3.3864. (Example: If the pressure reading on a weather station reads 27.67 inHg, multiply this by 3.3864 to get 93.701688. The number to use in this example is 93.70.) d. The Pressure Calibration button must be selected. Before pressing it, open the Model 3100 can by turning the four latches. Locate a small black surface mount component at the top edge of the circuit board. This is called the “pressure sensor.” Take the vacuum pump hose and attach it to this part. Note: Take special care that you do not pull or cause the vacuum line to slip off of this component. If it comes off during the next set of steps, you will have to start your pressure calibration over again in order to do it correctly. e. Squeeze the trigger slowly until you drive the needle on the vacuum pump gauge to -10 inches of mercury (10 inHg). If you do go past the -10 value, slightly pull on the release valve until you either settle back over -10 or slightly under where you can increase by pulling on the trigger. A-3 f. Once the gauge is showing -10 inHg vacuum, click on the Pressure Calibration button. A dialogue box will appear to enter Low Pressure Value in kPa. This value is calculated by subtracting 33.86 from the current atmospheric pressure obtained in the first step of this section. g. Once the Low Pressure Value has been entered, select the Take Voltage Readings button. h. The Voltage readings will populate in the window (ensure that these values are fluctuating near the displayed average voltage reading.) Once the status bar has completed, press the ACCEPT button in lower right corner of the dialogue box. Two possible problems indicated by non-fluctuating values could be a loss of communication between the software and instrument or a loss of vacuum. i. The next dialogue box will appear to enter High Pressure Value. Remove the vacuum pump from the pressure sensor before proceeding. Then select the Take Voltage Readings button. j. The voltage readings will populate in the window (ensure that these values are moving around the average.) Once the status bar has completed, press the ACCEPT button in the lower right corner of the dialogue box. k. The next dialogue box will appear as a reminder to update the new calculated pressure values. Press OK. l. The UPDATE button on the main window must be selected to save the new Pressure Calibration Slope and Offset. A.1.5 Airflow Calibration. This step in calibration is optional and is recommended for new instruments or whenever airflow miscalibration is suspected. a. Connect a calibrated airflow meter to the input (the port labeled IN) of the Model 3100. b. Operate the instrument in SAMPLE mode, and compare readings from the external flowmeter to the Model 3100 displayed value. c. If there is a significant difference between the two readings, adjust the Airflow Cal Constant value on the Pressure/AirFlow tab of the software until the two readings match. Note: Since this instrument utilizes a diaphragm pump, airflow readings taken from the outlet (port labeled OUT) of the Model 3100 may be incorrect. A.1.6 Zeroing: Electrometer Offset. a. Adjust the Electrometer Offset value in software in order to change the background display value to 0 µCi/m3. This value shall be between 2.000 and 2.100 b. If using the Electrometer Calibration Wizard, target a filtered ADC average as close as possible to zero without being a positive value. Note: It is recommended to confirm that the instrument is zeroed correctly by enabling streaming. Streaming through the software is recommended since the data shown has better resolution. The instrument readings should be less than 1.000 µCi/m3, but occasionally greater than 0.000 µCi/m3. A.1.7 Tritium Calibration. The Model 3100 calibration software is used to adjust the calibration constants for each of the three tritium ranges – from 1to 100 µCi/m3, from 100 to 1000 µCi/m3, and from 1000 to 10,000 µCi/m3. These three Calibration Constants are found on the 3H Calibration tab of the software. a. A-4 There are four calibration methods for calibration of the tritium readout on the Model 3100. 1. Three point tritium calibration is recommended by ANSI 42.30 (2002), and for the Model 3100, requires three tritium gas concentration levels of approximately 25 µCi/m3, 500 µCi/m3, and 7500 µCi/m3. Using this method, the calibration constant is adjusted to correct the displayed tritium concentration value of the Model 3100 at each of the three ranges. See Section A.2 Use of the CL1 Tritium Gas Calibrator. 2. Single point calibration is easier, requiring a single tritium gas concentration value. A calibration constant is adjusted at this one concentration point to correct the displayed tritium concentration value of the Model 3100. Using this method, all three ranges are set to the same calibration constant. See Section A.2 Use of the CL-1 Tritium Gas Calibrator. 3. Three point gamma calibration uses an open-air 137Cs calibration range. This calibration method uses a manufacturer-determined gamma equivalence value to determine gamma fields to establish known readings in the middle of each range. Using this method, a calibration constant is adjusted to correct the displayed tritium concentration value of the Model 3100 at each of the three ranges. In this mode, the gamma compensation chamber is disabled by substituting the calibration kit’s gamma +HV replacement “slug” in place of the gamma +HV battery. See Section A.3 Use of a Cs-137 Gamma Calibration Range. 4. Single point gamma calibration uses an open-air 137Cs calibration range. This calibration uses a manufacturer-determined gamma equivalence value to determine a gamma field to establish a known reading. A calibration constant is adjusted at this one concentration point to correct the displayed tritium concentration value of the Model 3100. In this mode, the gamma compensation chamber is disabled by substituting the calibration kit’s gamma +HV replacement “slug” in place of the gamma +HV battery. Using this method, all three ranges are set to the same calibration constant. See Section A.3 Use of a Cs-137 Gamma Calibration Range. A.2 USE OF THE CL-1 TRITIUM GAS CALIBRATOR. A.2.1 Equipment Required. a. Becton Dickinson Cl-1 Tritium Calibrator or equivalent traceable tritium gas injection device. A.2.2 Unpacking. a. b. The calibrator is shipped disassembled (in accordance with government regulations) into three main parts. 1. Gas cylinder containing approximately 60 liters of tritiated methane at approximately 1600 PSIG. 2. Lecture bottle regulator and adaptor fittings. 3. Calibrator base plate. Unpack each part and inspect them for damage. A.2.3 Assemble Calibrator. a. Remove the cap plugs from the regulator connector and outlet valve connector of the regulator. Inspect and clean the regulator connector, if necessary, to ensure that the sealing O-ring is in place. Inspect and clean the outlet valve connector also, if necessary. b. Remove the threaded dust plug from the gas cylinder and inspect and clean the sealing surface, if necessary. c. Adjust pressure by slowly turning the outlet pressure adjust knob clockwise to approximately 15 PSIG on the outlet pressure gauge. A-5 d. Carefully slide the gas cylinder and regulator into the gas cylinder holder on the calibrator base plate. It may be necessary to loosen the cylinder-locking screw. Line up the outlet valve connector with its mating fitting on the calibrator base plate. Remove and discard the three caps on the base plate tubing. e. Hand-tighten the outlet valve connector. Tighten the cylinder-locking screw and finish tightening the outlet valve connecter with a wrench. f. Connect the two lengths of plastic tubing supplied to the inlet and outlet of the calibrator. A.2.4 Leak Check. a. Close metering outlet valve and open both metering inlet valve and regulator outlet valve. b. Apply pressure to regulator by opening lecture bottle valve. c. Adjust pressure by slowly turning the outlet pressure adjust knob clockwise to approximately 15 PSIG on the outlet pressure gauge. d. Close the lecture bottle valve to isolate tubing from the gas supply. If the system is leaking, the cylinder pressure gauge will slowly drop. e. A tight system should lose less than 50 psi on the cylinder pressure gauge in one hour. f. If tubing is leaking, determine whether the leak is in the regulator part or in the metering volume and associated valves. g. Having determined the portion which is leaking, tighten appropriate connections and retest. Note: The calibrator is a precision instrument capable of accurate, reproducible results. Operation is simple, but erroneous results can be obtained if an incorrect technique is used. Before proceeding further, note that the bellowssealed valves on either side of the metering volume have Teflon seals, which close with a small amount of pressure. CAUTION The valves may be damaged by the use of excess pressure when closing them. Note: Before injecting tritium gas into the instrument’s chamber, air must be flushed from the calibrator. A.2.5 Initial Procedure. The procedure need only be done the first time the cylinder is connecting to the regulator. a. Open the lecture bottle valve momentarily, reclosing tightly. b. Open the metering outlet and inlet valves, as well as the regulator outlet valve. Turn the regulator outlet pressure adjust knob clockwise until the cylinder pressure gauge drops to 0. c. Close the metering inlet and outlet valves and back off the outlet pressure adjust knob. A.2.6 Flushing. The metering volume should always be flushed before performing a calibration. A-6 a. Check to see if the metering inlet and outlet valves are closed, the regulator outlet valve is open, and the outlet pressure adjust knob is backed off counterclockwise until it is loose. b. Momentarily open and reclose the lecture bottle valve, admitting as to the regulator and causing the cylinder pressure gauge to indicate. c. Turn the outlet pressure adjust knob clockwise until the outlet pressure gauge reads about 20 psi. d. Momentarily open and reclose metering inlet valve. e. Momentarily open and reclose metering outlet valve, flushing the metering volume. f. Repeat steps “d” and “e” if required. The calibrator is now ready for use. A.2.7 Closed Loop Calibration. a. Connect the calibrator outlet hose to the outlet of the instrument and turn on its air pump. b. If the cylinder pressure gauge shows any pressure reading, there is enough gas contained in the regulator to proceed with the next step. If not, momentarily open and close the lecture bottle valve so that this gauge reads upscale. c. Open metering inlet valve. Metering outlet valve should be closed. d. Turn the outlet pressure adjust knob slowly clockwise, watching the reading on the outlet pressure gauge. e. When the outlet pressure gauge reads the desired injection pressure (typically 20 or 30 psi), close the metering inlet valve. f. Connect the inlet hose to the inlet connector on the instrument. g. Open the metering outlet valve for between two and four seconds, and then reclose it firmly. Longer or shorter times will lead to incorrect results. h. In the above step, a known aliquot of gas was injected into the chamber. To inject a second aliquot, repeat Steps “c” to “f” above. Any number of aliquots may be injected with the instrument reading increasing proportionately. In closed-loop calibration, the activity enters the chamber rapidly but is then redistributed throughout the volume of the instrument and calibrator gas system. Since the bulk of the volume is in the tritium ion chamber, the scale reading will rise (spike), then drop, and then level off to a constant value independent of time constants or pumping speeds. The indicated scale reading depends solely upon the system volume and the pressure in the aliquot as described in the next section. A.2.8 Calculation of Response. Using the technique described in the previous section, the 11 mL metering volume is always kept filled with tritiated methane. When the outlet pressure gauge reads 20 psi and the metering inlet valve is open, the actual methane pressure in the metering volume is 35 psia. With the metering inlet valve closed and metering outlet valve opened momentarily, the methane pressure in the metering volume is now 15 psia. This means the mass of methane injected can be calculated from the pressure differential (35-15 psia), which is equal to the scale reading of the outlet pressure gauge. It is very important to open the metering outlet valve for only 2 to 4 seconds. A longer opening time allows the residual 15 psia of pure methane in the metering volume to mix with the air stream flowing into the calibrator tubing, eventually distributing this extra gas throughout the system volume. The instrument scale reading will then correspond to injection of 35 psi of gas using the formula below. Although this technique can be used, we do not recommend it since it is slower and somewhat less reproducible. A.2.8.1 Formula. The response can be calculated using: v = metering volume (11.0 mL in the CL-l) V = total volume of instrument plus calibrator (in mL) P = gauge pressure of gas in metering volume (psig) (i.e., reading of outlet pressure gauge) A = original specific activity of gas in lecture bottle (µCi/liter at 25 °C and 14.7 psia) n = number of aliquots injected d = tritium decay since cylinder calibration (see below) A-7 T = ambient temperature (°C) The volume of gas injected = P 298 nv · ∙ ml 14.7 273+𝑇 Hence, activity injected = P 298 nv · ∙ · dA x 10-3 µCi 14.7 273+𝑇 So tritium concentration = P 298 dA nv · ∙ · µCi /m3 14.7 273+𝑇 V For the case where v = 11.0 mL and T = 25 °C, this becomes: nPdA Tritium concentration = 0.75 µCi/m3 V The value of V is the sum of: a. the inside gas volume of the Model 3100 (254 mL); b. plus the volume of connecting tubing between the calibrator and the Model 3100 (48 inches of ¼ inch ID tubing is 39 mL); c. plus the volume of tubing in the CL-1 calibrator (37 mL). Thus, the total value of V, assuming a total of 48 inches of ¼ inch ID tubing is used to connect the gas calibrator to the Model 3100, is 330 mL. Since tritium decays with a 12.26 year half-life, the specific activity of the cylinder gradually decreases. Be sure to get a current specific activity of the cylinder using the following formula: Given that: d = decay factor HL = half-life (12.26 years for tritium) T = years elapsed since original specific activity d = e-(0.693 xT / HL) A.2.8.2 Example of Decay Calculation. What is the decay factor of a tritium gas cylinder calibrated a year ago? d = e(-0.693 x 1 / 12.26) d = 0.945 A.2 8.3 Example of Tritium Concentration Calculation. Given that a tritium gas cylinder with a concentration of 45 x 10 3 µCi/m3, calibrated a year ago, with a gauge pressure of 60 psi, what is the concentration of tritium gas with a single injection into a total volume of 330 mL at 25 °C and sea level? d = 0.945 (as calculated above) V = 330 mL v = 11 mL Tritium concentration = 11mL/14.7psi*60 psi*0.945*45 x 10 3 µCi/m3 /330mL, = 5786 µCi/m3 Note: If using a dilution method to obtain lower reading after final aliquot, the Model 3100 shall be placed in MEASURE Mode during valve manipulation. 137 A.3 USE OF A CS GAMMA CALIBRATION RANGE. A 137Cs gamma range can be used to calibrate the tritium readings of the Model 3100. The use of a gamma range can simplify the calibration, avoiding the complications of using tritium gas. A-8 A.3.1 Equipment Required a. 137 Cs gamma calibration range, NIST-traceable capable of producing a uniform gamma field from 0.15 to 60 mR/hr (if doing the three-point calibration), or a single point within this range if doing the singlepoint calibration method. Note: The gamma equivalence value for the Model 3100 was determined by calibrating multiple instruments using NIST-traceable tritium gas concentrations. Once calibrated, the gamma compensation chambers were disabled by replacing the +75 V HV gamma bias battery with an aluminum slug of the same size. The units were then exposed to a uniform field from a NIST-traceable 137Cs gamma source, and an equivalence established: 1 mR/hr 137Cs = 177.6 µCi/m3. So, for a three-point calibration, the following gamma fields could be used: 0.25 mR/hr = 44 µCi/m3 2.5 mR/hr = 444 µCi/m3 25 mR/hr = 4440 µCi/m3 A.3.2 Disabling the Gamma Compensation Chamber. Before starting on the gamma range, the following procedure should be used to disable the gamma compensation chamber. a. Turn the Model 3100 instrument to OFF, rotate the four quarter-turn latches, and open the instrument. b. Using a flat-blade screwdriver, remove the battery marked “+HV Gamma” from its holder. Be careful not to short both ends of the battery together. It is good practice to put the battery into a small plastic bag. c. Replace the battery with the aluminum substitute “slug” (LMI # 7520-152). This action disables the gamma compensation on the instrument, making the instrument sensitive to gamma fields once the voltage from the bias battery has been completely discharged. This could take several hours. d. Wait a minimum of 1 hour for settling time before continuing. Ensure the gamma wall voltage is fully discharged by shorting one of the two vinyl-covered screws near the HV bias batteries to the detector plate as pictured below. Figure A-1. Discharging Gamma Wall Voltage. e. Turn the instrument back ON and verify proper operation. Note that you will get a warning about the lack of +HV, but this can be ignored during this procedure. A.3.3 Placement of Model 3100 on the Gamma Range. Place the instrument on the gamma range with the front of the Model 3100 facing the gamma source (see Figure A-2). The dimple on the side of the can closest to the A-9 back end of the instrument marks the center of the tritium chamber for alignment purposes. To ensure a uniform gamma field, the instrument shall be at least 28 inches away from the radiation source. Gamma Source Gamma Dimple Tritium Dimple Figure A-2. Calibration Setup. a. Record the background reading (which may be elevated since gamma compensation is disabled). b. Expose the Model 3100 to the desired uniform gamma field using the dimple marks on the “can” to center the chamber. Note that the response time of the instrument is approximately one minute. If the instrument does not read the correct value after one minute has elapsed, increase or decrease the calibration constant for the appropriate range as needed until the correct value is reached. See Table A1 for recommended calibration fields. “Cal” indicates the recommended point for adjusting the calibration constant, while “Ref” indicates where the reference reading is taken to confirm linearity. Table A-1. Recommended Calibration Fields. 137 Cs µSv/h (mR/hr) 600 (56.4) 450 (42.3) 150 (14.1) 45 (4.23) 30 (2.28) 4.5 (0.42) 1.5 (0.14) Tritium µCi/m3 Equivalence 9967 7475 2492 748 498 75 25 Range/Test During effective range of measurement X 100 Cal X 100 Ref X 10 Cal X 10 Ref X 1 Cal X 1 Ref Note: Be sure to account for background reading when performing calibration. To calculate calibration constants: (Expected Reading/ Net Reading) * Existing Calibration Constant = New Calibration Constant. c. The calibration software contains a calibration wizard to ease calibration. See the Model 3100 calibration software manual for more detailed instructions. d. Repeat calibration steps for the remaining range multipliers, or if doing a single point calibration, copy the calibration constant found to the other two ranges. A.4 FINAL CALIBRATION STEPS. If the 137Cs range calibration method was used to calibrate the tritium reading, turn off the instrument and replace the +HV gamma bias battery, making sure to insert it into the holder correctly. Close the instrument and turn it back ON. Verify that the +HV measurement in the check screen has a check-mark beside it. Wait a minimum of four hours settling time to continue. A-10 a. b. Review the parameters and settings and make sure that they are saved inside the instrument. There are two parameters that should be reviewed at this point: 1. Alert: this parameter establishes a fixed alarm point, independent of the user-settable alarm point. If not desired, a set point of 0 disables this feature. 2. Check Source Mode and Target Reading: The check source test is typically used on a daily or as-used basis, and can be either internal, or one can use an external check source. Choose either external or internal, and then enter the target reading you expect the source to cause. When the test is performed, the check should cause a reading within 20% of the target reading, or else the word FAIL will be displayed. See Section 2.3.4 for more detailed instructions. Print your parameters by one of two methods: 1. Go to Parameters at the top of the program screen and click there to get the drop-down menu to locate and select Print Parameters. 2. Simply press the Ctrl and P keys to print. c. Before closing the software program, take note of the firmware number located immediately to the left of the Update key at the bottom right corner of the program screen. This number should be documented in the comments section of the certificate of calibration. d. Document all readings on an appropriate calibration form. Include a printout of parameters along with the calibration certificate. A-11
advertisement
Related manuals
advertisement