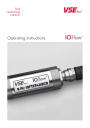
vse IO.flow Operating Instructions Manual
Add to My manuals25 Pages
The vse IO.flow is a compact IO-Link converter that seamlessly integrates VSE flow sensors into your existing IO Link systems. This module connects inline between your flow meter and evaluation system, converting the signal into a unit that is directly readable by your IO-Link master or PLC. With features like configurable signal filters, integrated calculation functions (unit conversion, linearization), data backup on power off, and support for device replacement, the IO.flow provides accurate and reliable flow measurement for a variety of applications.
advertisement
▼
Scroll to page 2
of
25
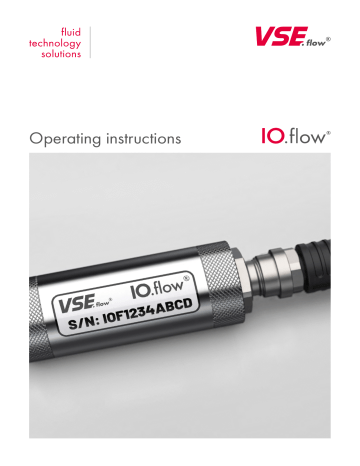
Operating instructions TABLE OF CONTENTS Page 1. Important information and legal notices. . . . . . . . . . . . . . . . . . . . . . . . . . . . . . . . 3 2. Features. . . . . . . . . . . . . . . . . . . . . . . . . . . . . . . . . . . . . . . . . . . . . . . . . . . . . . . . . . . . 4 3. Technical data. . . . . . . . . . . . . . . . . . . . . . . . . . . . . . . . . . . . . . . . . . . . . . . . . . . . . . . 4 Electrical operating conditions . . . . . . . . . . . . . . . . . . . . . . . . . . . . . . . . . . . . . . . . . . . . . . . . 4 Signal input specifications (flowmeter). . . . . . . . . . . . . . . . . . . . . . . . . . . . . . . . . . . . . . . . . . 5 IO-link specification. . . . . . . . . . . . . . . . . . . . . . . . . . . . . . . . . . . . . . . . . . . . . . . . . . . . . . . . . 5 Identification data of the device . . . . . . . . . . . . . . . . . . . . . . . . . . . . . . . . . . . . . . . . . . . . . . . 6 Mechanical properties. . . . . . . . . . . . . . . . . . . . . . . . . . . . . . . . . . . . . . . . . . . . . . . . . . . . . . . 6 4. Connection data. . . . . . . . . . . . . . . . . . . . . . . . . . . . . . . . . . . . . . . . . . . . . . . . . . . . . 7 5. Initial setup . . . . . . . . . . . . . . . . . . . . . . . . . . . . . . . . . . . . . . . . . . . . . . . . . . . . . . . . . 8 Example configuration. . . . . . . . . . . . . . . . . . . . . . . . . . . . . . . . . . . . . . . . . . . . . . . . . . . . . . . 9 Data-storage mechanism (device replacement) . . . . . . . . . . . . . . . . . . . . . . . . . . . . . . . . . . 9 6. Advanced features. . . . . . . . . . . . . . . . . . . . . . . . . . . . . . . . . . . . . . . . . . . . . . . . . . 10 Linearization . . . . . . . . . . . . . . . . . . . . . . . . . . . . . . . . . . . . . . . . . . . . . . . . . . . . . . . . . . . . . . 10 Frequency filter. . . . . . . . . . . . . . . . . . . . . . . . . . . . . . . . . . . . . . . . . . . . . . . . . . . . . . . . . . . . 11 Pulse filter function. . . . . . . . . . . . . . . . . . . . . . . . . . . . . . . . . . . . . . . . . . . . . . . . . . . . . . . . . . 11 Change of flow direction. . . . . . . . . . . . . . . . . . . . . . . . . . . . . . . . . . . . . . . . . . . . . . . . . . . . 11 Encoder properties – number of channels. . . . . . . . . . . . . . . . . . . . . . . . . . . . . . . . . . . . . . 12 Peak flowrate monitoring. . . . . . . . . . . . . . . . . . . . . . . . . . . . . . . . . . . . . . . . . . . . . . . . . . . . 12 7. Events. . . . . . . . . . . . . . . . . . . . . . . . . . . . . . . . . . . . . . . . . . . . . . . . . . . . . . . . . . . . . 12 Limits. . . . . . . . . . . . . . . . . . . . . . . . . . . . . . . . . . . . . . . . . . . . . . . . . . . . . . . . . . . . . . . . . . . . . 12 Flow monitoring. . . . . . . . . . . . . . . . . . . . . . . . . . . . . . . . . . . . . . . . . . . . . . . . . . . . . . . . . . . . 12 Standstill detection. . . . . . . . . . . . . . . . . . . . . . . . . . . . . . . . . . . . . . . . . . . . . . . . . . . . . . . . . 12 Negative flow detection. . . . . . . . . . . . . . . . . . . . . . . . . . . . . . . . . . . . . . . . . . . . . . . . . . . . . 13 Maintenance and diagnostic data . . . . . . . . . . . . . . . . . . . . . . . . . . . . . . . . . . . . . . . . . . . . 13 8. Errors . . . . . . . . . . . . . . . . . . . . . . . . . . . . . . . . . . . . . . . . . . . . . . . . . . . . . . . . . . . . . 14 9. Parameter description. . . . . . . . . . . . . . . . . . . . . . . . . . . . . . . . . . . . . . . . . . . . . . . 14 Process data structure. . . . . . . . . . . . . . . . . . . . . . . . . . . . . . . . . . . . . . . . . . . . . . . . . . . . . . . 14 Process data in . . . . . . . . . . . . . . . . . . . . . . . . . . . . . . . . . . . . . . . . . . . . . . . . . . . . . . . . . . . . 15 Process data out . . . . . . . . . . . . . . . . . . . . . . . . . . . . . . . . . . . . . . . . . . . . . . . . . . . . . . . . . . . 15 Device parameters . . . . . . . . . . . . . . . . . . . . . . . . . . . . . . . . . . . . . . . . . . . . . . . . . . . . . . . . . 16 System commands. . . . . . . . . . . . . . . . . . . . . . . . . . . . . . . . . . . . . . . . . . . . . . . . . . . . . . . . . . 22 10. Revision history . . . . . . . . . . . . . . . . . . . . . . . . . . . . . . . . . . . . . . . . . . . . . . . . . . . 23 11. Manufacturer declaration. . . . . . . . . . . . . . . . . . . . . . . . . . . . . . . . . . . . . . . . . . . 24 With the publication of these operating instructions, all information from previous publications becomes invalid. VSE reserves the right to make changes and deviations. VSE accepts no liability for possible printing errors. Reproductions, including excerpts, are only permitted with the written consent of VSE. VSE reserves the right to make technical changes at any time. Status: 02/2023 3 1. IMPORTANT INFORMATION AND LEGAL NOTICES Dear customer, dear user, This operating instruction for the IO-Link converter „IO.flow® by VSE Volumentechnik GmbH (VSE) contains information required to properly install and commission the device for the intended purpose. Any installation, commissioning, operation, maintenance and testing may only be carried out by trained and authorized personnel. The operating instructions must be read and followed carefully to ensure a trouble-free, proper and safe operation of the device. In particular, the safety instructions are essential. These operating instructions must be kept safe and accessible for the authorized personnel at all times. At no time should contents of the operating instructions be removed. A missing manual or missing pages must be replaced immediately if lost. The operating instructions can be requested at any time from VSE or downloaded from our website www.vse-flow.com. The operating instructions must be passed on to each subsequent user of the IO-Link converter „IO.flow®“. This operating instruction is not subject to any modification service by VSE. VSE reserves the right to make technical changes at any time without notice. VSE makes no warranties, express or implied, with respect to commercial qualities and suitability for a particular purpose. VSE accepts no liability for damage and malfunctions resulting from operating errors, failure to observe these operating instructions, improper installation, commissioning or maintenance as well as improper use of the IO-Link converter „IO.flow®“. The opening of the IO-Link converter „IO.flow®“ is absolutely not permitted. After an unauthorized opening or rebuilding as well as after a single, incorrect connection of the flow circuits of the device, the warranty as well as the product liability by VSE expire. Operating manual–no.: E18-07-38-005 Vers. e 4 2. FEATURES The IO-Flow® Converter enables uncomplicated integration of all VSE flow sensors into IO Link systems. The signals of the preamplifier are measured by the module and converted into the desired unit so that they are available to the IO-Link master or the programmable logic controller (PLC) for direct further processing. The compact module is connected „in-line“ between the flow meter and the evaluation system. This means that it is integrated into the existing cabling with an additional M12 extension cable and thus repre- sents a signal converter. The IO-Link protocol enables simultaneous transmission of the process data volume and flow in the appropriate unit, together with diagnostic and statistical data. Parameters can be changed during operation or adapted to another flow sensor. In addition, integrated signal processing allows filtering and linearization of the volume sensor‘s measured values. Main features: • Accurate frequency measurement and volume counting • Configurable signal filters (dynamic / smoothed / precise) • I ntegrated calculation functions: • Unit conversion (pulses, volume, mass) • Linearization of flow and volume (20 linearization points) • Recording of statistical data for maintenance notifications • Data backup on power off •Configurable events for flow monitoring (limit values, invalid states) • Teach-in function for parameterization in the field • E rror messages • Support for data storage for easy exchange of devices • Two-channel SIO mode for quadrature signals (optional) 3. TECHNICAL DATA Electrical operating conditions Parameter Symbol Value Unit Notes Operating voltage Ub 18 – 30 V Unenn = 24 V Operating current IO-Link Mode Ib,IOL 15 mA at Ub = 24 V Operating current SIO-Mode Ib,SIO 5 mA at Ub = 24 V Max. ambient temperature Tmax 50 °C Burst (EN 61000-4-4) 2 kV Criterion A, 5/100 kHz ESD (EN 61000-4-2) ±4 / ±8 kV Criterion B, contact and air discharge Conducted immunity (EN 61000-4-6) 150 kHz - 80 MHz Criterion A, U0 =10V Radiated immunity EN 61000-4-3 80 Mhz - 6 GHz Criterion A, E0 =6-10V/m Radiated emissions EN 55016-2-3 30 MHz - 1 GHz Table 1: Operating conditions (electrical) 5 Signal input specifications (flowmeter) Parameter Symbol Value Unit Notes Operating voltage (flowmeter) UVS Ub V Same as operating voltage Ub Max. allowed current consumption (flowmeter) IVS,max < 200 mA Power supply dependent Maximum input frequency (IO-Link Mode) fmax,IO 125 kHz Maximum input frequency (SIO-Modus) fmax,SIO 250 kHz IO-Link Wakeup-Request only possible up to 25 kHz with activated SIO-Passthrough Measurement accuracy of frequency (lower range: 10 kHz) er,10k 0.013 0.005 0.014 % % % V_Filter = 2 V_Filter = 1 V_Filter = 0 Measurement accuracy of frequency (upper range: 100 kHz) er,100k 0.018 0.034 0.300 % % % V_Filter = 2 V_Filter = 1 V_Filter = 0 Settling time of frequency filter (V_Filter) trise 1000 350 10 ms V_Filter = 2 V_Filter = 1 V_Filter = 0 Table 2: Operating parameters (Signal input) IO-link specification The module uses a communication rate of 230,4 kBaud (COM3). The IODD is compatible with the specification version V1.1 and can be found in the download area of our homepage. www.vse-flow.com/en/downloads Parameter Value Manufacturer Name VSE Volumentechnik GmbH Manufacturer ID 1654 Device Name IO.flow Device ID 4900 HEX: 0x1324 Communication rate 230,4 kBaud COM3 Minimum cycle time 1 ms ISDU DataStorage Block Parameter supported Preoperate M-Seq. Type TYPE_1_V_8OD 8 byte OD Operate M-Seq. Type TYPE_2_V_2OD 9 byte PDin, 1 byte PDout, 2 byte OD M-Seq. Capability 43 HEX: 0x2B SIO-Mode 2-channel passthrough mode (dependent on V_SIO-Passthrough) Pin 2: QA/Pin 4: QB Table 3: IODD operating parameters for IO.flow® Notes HEX: 0x0676 ® Identification data of the device If the device is paired/parametrized with a specific flowmeter, there is a separate label on the back of the device housing. This label contains the serial number and type of the paired flowmeter. Each IO.flow ® converter is equipped with a unique serial number according to the scheme IO********. It can be found as a lasered marking on the device’s housing and in digital form in the parameter V_SerialNumber (Index 0x15). Additionally, the manufacturing date of the device is stored in the read-only parameter V_MfgDate (0x4F). Figure 1: Parameter label for the paired flowmeter Mechanical properties 88,5 60,4 S/N: IOF1234ABCD SW18 M12x1 (female) Ø25 6 M12x1 (male) Parameter Symbol Value Unit Length (total) lges 88.5 mm Length (main body) lmain 60.4 mm Diameter d 25 mm Weight m 68 g Protection against liquid penetration waterproof Table 4: Mechanical properties 1 Performed test: Device immersed in water (50 cm depth) for 30 min. No traces of liquid inside the device. Notes With mated connectors1 4. CONNECTION DATA 7 The two 4-pin connectors are compatible with any existing cabling and enable simple installation of the IO-Link module. Both shielded and unshielded cables are suitable as connection cables. Signal input side (Quadrature signal) Signal output side (IO-Link) 2 2 1 1 IO-FLOW 3 M12 MALE 4 4 1 +24 V (brown). 2 QA (white) . 3 4 M12 FEMALE 3 0 V (blue). C/Q/QB (black) . Figure 2: Connector specifications and cable assignment The signal output side uses a male M12 connector and connects to the IO-Link master. On the signal input side there is a female M12 connector which usually connects to a flowmeter or other device with pulse signal output. In SIO-mode the pin assignment is identical on both connectors. The supply voltage, which is connected to pins 1 and 3 of the male connector, is passed through to the same pins of the female connector. In IO-Link mode, pin 4 represents the communication line and pin 2 is pulled to 0 V. 8 5. INITIAL SETUP Figure 3: Schematic overview of the IO-Link system with a VSE flowmeter and IO.flow ® The male connector of the device is usually connected to the IO-Link master via a M12 extension cable (male/female). On the signal input side, the preamplifier of the flowmeter is connected with another extension cable to the female connector. The maximum cable length for either side must be below 20 m. Note The IO.flow ® converter is unshielded per IO-Link specification. For this reason, the connected flowmeter must be grounded via the hydraulic piping or using the earth terminal of the flowmeter. At start-up, the device works in SIO-mode, in which both quadrature signals of the flowmeter are passed through to the IO-Link side (if SIOPassthrough is activated, see page 19). A wake-up request from the IO-Link master switches the device to IO-Link mode. Using the IODD (Download → page 5) the device can be added to the master’s configuration software, where parameters can be adjusted and process data can be read. Before using the device, certain parameters must be set. The setting values depend on the specific flowmeter which is connected on the signal input side. If a flowmeter is purchased together with an IO.flow ® converter, the pairing process and configuration can be done by VSE. The following table lists the parameters that are checked for validity. Relevant parameters should be set when commissioning the device. 9 The “param error” flag in the process input data will be cleared when a valid configuration is detected. After a successful configuration of these parameters, the device status changes to “Device is operating properly”. Parameter Index (HEX) Unit Requirement V_KFactor 0x45 Imp/l KFactor ≥ 1 (V_Unit=Hz) KFactor > 1 (V_Unit≠Hz) V_IPF 0x46 V_Qmax 0x5A V_Lin_enable 0x63 IPF > 0 Qmax > 0 (V_Unit≠Hz) l/min Linenable > 0, but no lin.-points set Table 5: Parameters with validity check Example configuration If the IO.flow® converter is purchased together with a flowmeter, the initial setup is performed by VSE and all necessary parameters regarding the paired flowmeter are already pre-set. In case of a separate purchase for retrofitting existing systems, the parametrization is usually carried out by the customer using an existing IO-Link master. An example configuration is shown in the following table: Parameter Description Value V_FM-SN Flowmeter serial number 060 / 24 / 110 V_FM-Type Flowmeter type VS 0,1/16 GPO 12V-42R11/X V_CalDate Flowmeter calibration date 21.06.2022 12:00:00 V_Unit Process data unit 1 (volume / unit: litre) V_KFactor Calibration factor (K-Factor) 160 000 Imp/l V_IPF Interpolation factor 16 V_Qmax Maximum allowed flowrate 10 l/min V_EncProp Number of input channels 0 (2-channel flowmeter) Table 6: Example configuration for a VSE VS 0,1 Data-storage mechanism (device replacement) If data storage is activated, all parameters that are not affected by the connected flowmeter are backed up in the IO-Link master. In the event of a flowmeter defect, a seamless device replacement is thus possible without manual reconfiguration. This also enables device replacement with a different type of flow meter. All application-specific settings such as filter, unit and limit values are restored. After connecting a new converter to the IO-Link master, the data storage download is started, and the device is ready for use again. 6. ADVANCED FEATURES Linearization Error (%) Precision (%) Flowrate (ml/min) Figure 4: Typical error curve of a positive displacement flowmeter at low fluid viscosity Every flowmeter based on the positive displacement principle has a Kfactor which represents its resolution in the unit of pulses per litre. However, mechanical tolerances, wear and operating conditions, such as low fluid viscosity, mean that this K-factor is not constant over the entire flow range. This can result in measurement errors if not taken care of. To quantify these deviations, a flowmeter can be calibrated. The results of the calibration can then be used to eliminate the device-specific deviations using a linearization table. Using this mathematical correction, the measurement error gets eliminated which leads to a higher measurement quality over the entire measuring range. By entering the linearization data into the IO.flow converter and enabling it via the parameter V_Lin_enable, the measured flow and volume values will be output as corrected process data values. Depending on the available calibration data, two modes of linearization can be selected (K-Factor or Flowrate). The linearization table supports up to twenty entries. All intermediate values will be linearly interpolated. Name Index Data type Value = 0 Value = 1 Value = 2 V_Lin_enable 0x63 SingleValue Linearization disabled (gray) f-K table (green) f-Q table Linearization table X Subindex 1 .. 20 Contains X-coordinates of the linearization points. This is the measured frequency value that serves as a reference for the corresponding Y-coordinate. Unit in Hz. Linearisierungstabelle Y Subindex 1 .. 20 Contains Y-coordinates of the linearization points. Each coordinate represents the frequency dependent process value of the attached flowmeter. Depending on the table type it can contain K-factors or the actual flowrate values. f-K-Linearization: Unit in pulses per litre f-Q-Linearization: Unit in litre per minute Flowrate 10 Frequency Figure 5: Linearization principle 11 Frequency filter Using the parameter V_Filter the measurement can be adapted to the desired accuracy and dynamic requirements. A high filter setting of “2” is set as the default value to ensure the highest possible measurement accuracy. Using a low filter setting, highly dynamic flow phenomena, such as sudden flow peaks, can be detected and measured. The filter properties are further specified in Table 2. Pulse filter function Wait Time Process data value (IO-Link) 123.4 l/ min 0 l/ min 0 l/ min 123.4 l/ min Figure 6: Functionality of the pulse filter function Oscillations in fluid systems are characterized by cyclic forward and backward movement in the liquid domain (→ Pulsation), which is also detected by the flowmeter and converted into proportional pulse signals and edge sequences. Depending on the application, oscillations or vibrations can occur during standstill or discontinuous flows. The pulses generated during the oscillation phase can be incorrectly interpreted by the downstream evaluation unit or controller as a high flow peak, which can lead to wrong measurements, if not evaluated correctly. The pulse filter function of the IO.flow converter continuously monitors the output pulses during rapid forward and backward movement of the gears or rotors of the flowmeter. On a direction change, the signals at the channel outputs are suppressed and internally buffered until the flowmeter position is back at the position where the filter action started (see Figure 6). This leads to a steady standstill signal even though the flow is pulsating without losing signal information. Change of flow direction If the displayed flow value is negative although the actual flow direction is positive, the sign of the frequency measurement and pulse counter can be reversed with the parameter V_DirectionInvert. With the parameter V_Impfilter_Enabled the user can set the maximum buffer size for pulses in the negative direction. A value of “1” corresponds to one gear tooth volume. A whole gear revolution is a value of 20 for the average number of teeth on VSE flowmeters. The so called “preferred direction” is the flow direction where no filtering occurs and are forwarded to the process data directly. If the set buffer size of the pulse filter is exceeded while running in the nonpreferred direction, the preferred direction is switched over and the measured value is output again. Simultaneously the counter function adds the suppressed volume to the counter, so that no volume information is lost on a direction change. To inform the user about an exceeded buffer count, the IO-Link event 0x1816 gets triggered. If this event occurs too often in the application, it is advisable to increase the buffer size of the filter. 12 Encoder properties – number of channels The V_EncProp parameter is used to set whether the signal evaluation of the flowmeter signals is single-channel or dual-channel. In singlechannel mode, a pulse signal is expected on pin 2 (white wire) or pin 4 (black wire). In this case there is no direction detection, and the measurement resolution of the volume is reduced to a quarter of the resolution of the two-channel measurement. Furthermore, other features such as negative flow detection and the pulse filter function will no longer function. Pulsation in the liquid domain at standstill can lead to an unwanted increase in the measured volume in this mode, as each signal edge is added up. Peak flowrate monitoring For diagnostic purposes, the peak flowrate value is stored in the parameter V_QPeak. If the flowrate during operation is higher than the nominal flowrate V_Qmax of the flowmeter, this can lead to a mechanical overload and damage to the device. In this case, the IOLink event 0x8C20 is triggered. Zeroing the value is done with the help of a system command (see page 22). 7. EVENTS Limits Using the limit value function, events can be triggered by the IO.flow device when the process data values (volume and flowrate) fall below or exceed predefined limit values. If the corresponding parameter va- lue is ≠ 0, the limit event is activated. The event remains active as long as the condition is fulfilled. Name Event Code Hex Event Code Dec Type Duration Volume Notify 1 (≥) 0x1810 6160 Notification Appear/Disappear 0 Volume Notify 2 (≤) 0x1811 6161 Notification Appear/Disappear 0 Flowrate Notify 1 (≥) 0x1814 6164 Notification Appear/Disappear 0 Flowrate Notify 2 (≤) 0x1815 6165 Notification Appear/Disappear 0 Device Status Table 7: Events for limit values Flow monitoring The IO.flow® converter has various functions to detect unusual flow events to trigger an IO-Link event. If it makes sense to use these events depends on the specific application. The standstill detection (V_Standstilldetection_Enabled) generates a permanent event as long as the measured flowrate is zero. The parameter V_WaitTime controls the delay time in milliseconds after which the measured value of the flow is set to zero if no more pulse edges are measured. It can be set between 100 ms and 10000 ms. For example, clogging or a defect of the flowmeter can be detected in the application, if a flow standstill is very unlikely due to other sensor readings in the system (pressure sensors, pump speed). Standstill detection This function triggers an event as soon as the flowmeter stops measuring pulses (depending on the V_WaitTime parameter setting). It remains active for the entire duration of the standstill. The negative flow detection (V_NegativeDirectionDetection) generates an event if the sign of the flow value is negative, for example if a flow in negative direction takes place. If the output of the event is inverted, the parameter V_DirectionInvert can be used to change the counting direction and thus swap the polarity of the event. This event can be used, for example, to detect unwanted reverse flows in the fluid system. If the pulse filter function is activated (V_Impfilter_Enabled > 0), a continuous flow against the preferred direction of the filter leads to a change of the preferred direction and a notification event is generated. If this event occurs too often, the oscillation in the fluid is greater than the set filtered number of teeth and the value of the V_Impfilter_Enabled parameter should be increased. 13 Negative flow detection The negative flow detection triggers an event if the flow direction is negative. It can be used to detect unwanted backflow in the application. Name Event Code Hex Event Code Dec Type Duration Standstill 0x1812 6162 Notification Appear/Disappear 0 Direction negative 0x1813 6163 Notification Appear/Disappear 0 Pulse filter overrun 0x1816 6166 Notification Single Shot 0 Device Status Table 8: Events for flow monitoring Maintenance and diagnostic data In the Diagnostic data menu, maintenance intervals can be set, after which a permanent event is triggered. Two characteristic values for the wear of the device can be used for this purpose: The parameter V_TotalVolume stores the totalized volume which has flown through the flowmeter in litres (only works after successful parametrization of the device). If, for example, a highly abrasive fluid is measured, an event can be triggered after a predefined volume V_TotalVolNotify, to indicate that a maintenance should soon be scheduled to prevent flowmeter failure or an impaired measurement quality. A second maintenance-relevant characteristic value are the total operating hours of flowmeter with active flow. The parameter V_OPHours stores a TimeSpan, which is incremented every second if the flowrate V_Flow is ≠ 0. Using the parameter V_OpHoursNotify the timespan is defined after which the event appears. Name Event Code Hex Event Code Dec Type Duration Operating hours exceeded 0x1820 6176 Warning Appear/Disappear 1 Total volume exceeded 0x1821 6177 Warning Appear/Disappear 1 Table 9: Other events Device Status 14 8. ERRORS Name Event Code Hex Event Code Dec Type Duration Device Status TEMPERATURE_FAULT_EVENT 0x4000 16384 Error Appear/Disappear 4 NVM_ERROR_EVENT 0x5011 20497 Error One Shot 4 PARAM_ERROR_EVENT 0x6320 25376 Warning Appear/Disappear 3 MEASUREMENT_RANGE_EXCEEDED 0x8C20 35872 Warning Appear/Disappear 2 NO_MALFUNCTION_EVENT 0x0000 0 Notification Appear/Disappear 0 Table 10: Error codes NO_MALFUNCTION_EVENT PARAM_ERROR_EVENT After the device has been started, this event is triggered as the result of a successful device self-test. Incorrect or incomplete parameterization can prevent this event from occurring at start-up. The parameter settings of the device are incomplete or invalid. After resetting to factory settings, this error is active by default. The parameters that influence the device status and this error are listed in Table 5. TEMPERATURE_FAULT_EVENT MEASUREMENT_RANGE_EXCEEDED The temperature of the IO.flow® converter is too high. Causes for this error may be external heat sources, overvoltage or internal heating due to a short circuit. Please check the wiring and supply voltage. The current flowrate has exceeded the flow limit V_Qmax of the flowmeter. To avoid damage to the flowmeter, reduce the flowrate. This error message can also occur with short flow/pressure peaks. NVM_ERROR_EVENT If this event occurs, the stored parameters could not be loaded from the remanent data memory (EEPROM) and all parameter changes are lost. The default values are loaded. 9. PARAMETER DESCRIPTION Process data structure For this IO-Link device, both process input and output data are provided. The process data structure is shown in the following figure. The total length of the data packet is 72 bit / 9 byte. In addition to flow rate and volume, the device status and the status of the defined limit values are transmitted as process values. For process data output a data packet of 8 bit / 1 byte is used. The volume reset function will only be active if the process output data is valid. 15 Process data in Name Subindex Datatype Bit length Offset V_Flow 1 Float32T 32 0 Description Rights Process data: Flowrate value RO Name Subindex Datatype Bit length Offset V_Volume 2 Float32T 32 32 Description Rights Process data: Volume value RO Name Subindex V_FlowNotifyFlag13 3 Datatype Bit length BooleanT 1 Offset 64 Description Value: 0 Value: 1 Rights FlowNotify1 Event Status Event not active Event active RO Name Subindex Datatype Bit length Offset V_FlowNotifyFlag2 4 BooleanT 1 65 Description Value: 0 Value: 1 Rights FlowNotify2 Event Status Event not active Event active Name Subindex Datatype Bit length RO Offset V_VolNotifyFlag1 5 BooleanT 1 66 Description Value: 0 Value: 1 Rights VolumeNotify1 Event Status Event not active Event active RO Name Subindex Datatype Bit length Offset V_VolNotifyFlag2 6 BooleanT 1 67 Description Value: 0 Value: 1 Rights VolumeNotify2 Event Status Event not active Event active RO Name Subindex Datatype Bit length Offset ParamError 7 BooleanT 1 68 Description Value: 0 Value: 1 Rights ParamError Event Status Event not active Event active Name Subindex Datatype Bit length RO Offset DeviceStatus 8 UIntegerT 3 69 Description Value range Rights IO-Link Device Status2 0 Device is operating properly 1 Maintenance-Required 2 Out-of-Specification 3 Functional-Check 4 Failure RO Process data out 2 Name Subindex Datatype Bit length Offset V_Volume_Reset 0 BooleanT 1 0 Description Value range Rights Sets the process variable V_Volume to zero if desired false: V_Volume not reset true: V_Volume reset to zero RW see IOL_Interface-Spec_10002_V113_ Jun19 → B.2.20.1 Device Status 16 Device parameters In this chapter all device parameters are described. This includes the name, data type, bit width, storage type and write rights of the respective parameter. The "storage" field describes whether the parameter is backed up to the master by the data storage functionality. IDENTIFICATION VSE specific data Name Index Subindex Datatype Default value Length V_VendorName 0x0010 - StringT VSE Volumentechnik GmbH 64 characters Description Storage Rights Manufacturer name - RO Name Index Subindex Datatype Default value Length V_VendorText 0x0011 - StringT High precision flow measurement technology 64 characters Description Storage Rights Manufacturer Text - RO IO.flow® Name Index Subindex Datatype Default value Length V_ProductName 0x0012 - StringT IO.flow 64 characters Description Storage Rights Product name - RO Name Index Subindex Datatype Default value Length V_ProductText 0x0014 - StringT Signal Converter from quadrature to IO Link 64 characters Description Storage Rights Product Text - RO Name Index Subindex Datatype Default value Length V_SerialNumber 0x0015 - StringT IO*** 16 characters Description Storage Rights Serial number – Unique manufacturer-specific ID of the device - RO Name Index Subindex Datatype Default value Length V_Hardware Revision 0x0016 - StringT R* 64 characters Description Storage Rights Hardware revision of the device - RO Name Index Subindex Datatype Default value Length V_Firmware Revision 0x0017 - StringT IOF-FW-V* 64 characters Description Storage Rights Firmware revision of the device - RO Name Index Subindex Datatype Default value Length V_MfgDate 0x004F - TimeT - 64 bit Description Storage Rights Manufacturing date of the IO.flow ® converter at VSE - RO 17 Information of the paired flowmeter Name Index Subindex Datatype Default value Length V_FM-SN 0x0051 - StringT - 16 characters Description Storage Rights Serial number of the paired flowmeter - RW Name Index Subindex Datatype Default value Length V_FM-Type 0x0052 - StringT - 32 characters Description Storage Rights Type of the paired flowmeter (same as flowmeter’s type plate) - RW Name Index Subindex Datatype Default value Length V_CalDate 0x0050 - TimeT - 64 bit Description Storage Rights Date of the last flowmeter calibration - RW Common profile Name Index Subindex Datatype Default value Length V_Application-SpecificTag 0x0018 - StringT *** 32 characters Description Storage Rights Application specific tag - RW Name Index Subindex Datatype Default value Length V_Location-Tag 0x001A - StringT *** 32 characters Description Storage Rights Location tag - RW Name Index Subindex Datatype Default value Length V_Function-Tag 0x0019 - StringT *** 32 characters Description Storage Rights Function tag - RW 18 PARAMETER Process-settings Name Index Subindex Datatype Default value Min Max V_Unit 0x0042 - UInt16T 0 0 2 Description Storage Rights Unit of the process data (0: pulses, 1: volume, 2: mass) Yes RW Name Index Subindex Datatype Default value Min Max V_KFactor 0x0045 - Float32T 1.0 1.0 +∞ Description Unit Storage Rights Calibration factor (K-Factor) of the connected flowmeter in consideration of the IPF Imp/l - RW Name Index Subindex Datatype Default value Min Max V_IPF 0x0046 - UInt16T 1 1 65535 Description Storage Rights Interpolation factor (IPF) of the connected flowmeter - RW Name Index Subindex Datatype Default value Min Max V_Qmax 0x005A - Float32T 0.0 0.0 +∞ Description Unit Storage Rights Maximum allowed flowrate of the flowmeter (see datasheet) – Useful to detect flow peaks that are out of specification l/min - RW Name Index Subindex Datatype Default value Min Max V_Density 0x0047 - Float32T 1000.0 0.0 +∞ Description Unit Storage Rights Fluid density for mass flow calculation kg/m³ Yes RW Teach-functions Name Index Subindex Datatype Default value Min Max V_VolumeNotify1 0x005B - Float32T 0 -∞ +∞ Description Unit Storage Rights Volume ≥ Volume limit 1 (0: Disabled) l/min Yes RW Name Index Subindex Datatype Default value Min Max V_VolumeNotify2 0x005C - Float32T 0 -∞ +∞ Description Unit Storage Rights Volume ≤ Volume limit 2 (0: Disabled) l/min Yes RW Name Index Subindex Datatype Default value Min Max V_FlowNotify1 0x005F - Float32T 0 -∞ +∞ Description Unit Storage Rights Flowrate ≥ Flowrate limit 1 (0: Disabled) l/min Yes RW Name Index Subindex Datatype Default value Min Max V_FlowNotify2 0x0060 - Float32T 0 -∞ +∞ Description Unit Storage Rights Flowrate ≤ Flowrate limit 2 (0: Disabled) l/min Yes RW 19 Functions Name Index Storage Datatype Default value Length V_EncProp 0x004B - UIntegerT 0 (2-channel flowmeter) 8 bit Description Value range Rights Number of flowmeter channels 2-channel evaluation 1: 1-channel eval. (Pin 2) 2: 1-channel eval. (Pin 4) RW Name Index Storage Datatype Default value Length V_Filter 0x004D Yes UIntegerT 2 (High precision) 8 bit Description Value range Rights Filter dynamic / accuracy 0: Dynamic response (Medium precision) 1: Smooth response (Medium precision) 2: Heavily filtered response (High precision) RW Name Index Subindex Datatype Default value Min Max V_WaitTime 0x004E - UInt16T 500 100 10000 Description Unit Storage Rights Wait time – Time to pass without input pulses after which the frequency measurement value is set to zero ms Yes RW Name Index V_DirectionInvert 0x0044 Storage Datatype Default value Storage Yes BoolT false Yes Description Value: true Value: false Rights Invert direction of input signals Direction inverted Direction not inverted RW Name Index Subindex Datatype Default value Min Max V_ImpfilterEnabled 0x0048 - UInt8T 0 0 255 Description Storage Rights Pulse filter function – Number of buffered pulses/teeth (0: Disabled) Yes RW Name Index Storage Datatype Default value Storage V_Standstill detectionEnabled 0x0049 Yes BoolT false Yes Description Value: true Value: false Rights Standstill detection Enabled Disabled RW Name Index Storage Datatype Default value Storage V_Negative DirectionDetection 0x004A Yes BoolT false Yes Description Value: true Value: false Rights Negative flow direction detection Enabled Disabled RW Name Index Storage Datatype Default value Storage V_SIO-Passthrough 0x0059 Yes BoolT false Yes Description Value: true Value: false Rights Passthrough mode for quadrature signals (IO-Link-WUR only for f<25 kHz) Enabled Disabled RW 20 Name Index Subindex Datatype Default value Min Max V_Lin_enable 0x0063 - UInt8T 0 0 2 Description Storage Rights Enabling and choosing the linearization mode for volume and flowrate: 0: Disabled 1: Frequency/K-Factor-Table 2: Flowrate/K-Factor-Table - RW Linearization table Name Index Subindizes Datatype Elemente Min Max V_Lin_X 0x0064 1 .. 20 Array of Float32T 20 -∞ +∞ Description Storage Rights X-Values of the linearization table – dependent on the selected table type: V_Lin_enable=1: Frequency values of the flowmeter V_Lin_enable=2: Flowrate values of the flowmeter - RW Name Index Subindizes Datatype Elemente Min Max V_Lin_Y 0x0078 1 .. 20 Array of Float32T 20 -∞ +∞ Description Storage Rights Y-Values of the linearization table → K-Factors of the flowmeter - RW OBSERVATION Process data (unit: selectable) Name Index Subindex Datatype Default value V_Flow 0x0040 - Float32T 0 Description Unit Storage Rights Current flowrate value in selected unit Hz l/min kg/min - RO Name Index Subindex Datatype Default value V_Volume 0x0041 - Float32T 0 Description Unit Storage Rights Current volume in selected unit pulses litres kilogram - RO 21 Statistical data Name V_TotalVolume 3 Index Subindex Datatype Default value Min Max 0x0056 - Float32T 0 0 +∞ Description Unit Storage Rights Totalized volume counter (sums up positive and negative volume) litres - RO Name V_OPHours 3 Index Subindex Datatype Default value Length 0x0057 - TimeT 00:00:00.000 64 bit Description Storage Rights Operating hour counter with active flow - RO Name V_QPeak 3 Index Subindex Datatype Default value Min Max 0x004C - Float32T 0.0 0.0 +∞ Description Unit Storage Rights Highest measured flow value (peak value) l/min - RO DIAGNOSIS Diagnosis data 3 Name Note V_TotalVolume Description see Observation → Statistical data Name Index Subindex Datatype Default value V_TotalVolNotify 0x0062 - Float32T 0 Description Storage Rights Event on exceeded total volume (0: Disabled) Yes RW Name Note V_OPHours Description siehe Beobachtung / Statistik Name Index Subindex Datatype V_OPHoursNotify 0x0061 - TimeSpanT Default value Description Storage Rights Event on exceeded operating hours with flow (0: Disabled) Yes RW Name Index Subindex Datatype Default value V_ErrorCount 0x0020 - UInt16T 0 Description Storage Rights Number of occurred errors of the technology specific application since the last start-up or reset of the device - RW Name Note V_QPeak Description see Observation → Statistical data Automatic data store on device shutdown 22 Device status Name Index Subindex Datatype Default value Min Max V_DeviceStatus 0x0024 - UIntegerT 0 (Device OK) 0 4 Description Storage Rights Display of the status of the device and diagnostics - RO Name Index Subindex Datatype Element count V_DetailedDeviceStatus 0x0025 1 .. 64 Array of OctetStringT 64 Description Storage Rights List of all currently pending events of the device - RO SYSTEM COMMANDS Data resets System Commands are used to reset the statistical data recorded by the device. Various buttons are provided for this purpose in the Diagnosis → Reset buttons menu. System Command (Button) HEX Reset: total volume 0xA4 Reset: operating hours 0xA5 Reset: peak flowrate value 0xA6 Reset: volume 0xA7 Restore factory settings 0x82 Application reset 0x81 Reset total volume Restore factory settings The total volume counter (V_TotalVolume) will be reset to a value of zero. This function resets the device to factory/default settings. All saved parameter values will be lost. After completion, the device will be restarted. Reset operating hours Application reset The operating hour counter (V_OPHours) will be reset to a value of zero. Reset peak flowrate value All parameters except those used for IO-Link device identification (e.g., application/location tag) are reset to the default values. No restart will be performed. The value of the highest measured flowrate value (V_QPeak) will be reset to a value of zero. Reset volume The process value of the volume (V_Volume) will be reset to a value of zero. Teach functionality To perform a fast and easy setup of limit values, there are four buttons in the menu Parameter → Limits. When the buttons are pressed, the current process value is saved (→ “teached”) to the corresponding limit value parameter. This way, the limit values can be set in the real-world application. System Command (Button) HEX Teach: Volume event 1 0xA0 Teach: Volume event 2 0xA2 Teach: Flowrate event 1 0xA1 Teach: Flowrate event 2 0xA3 23 10 REVISION HISTORY Revision Date Changes - 12.01.2022 Preliminary version a 21.06.2022 Changes for Firmware revision V1.2 b 03.08.2022 Figure updates, new parameter V_SIO_Passthrough, Measured precision values, Firmware revision V1.7 c 29.08.2022 English version, design fixes, figure updates d 19.09.2022 EMC data update, correction of V_Density, PDout addition, Firmware revision V1.9 e 20.10.2022 Change of data storage parameters, Addition of application reset, Change of ParamError-Flag behaviour, PDout validity, Icon/Logo Changes, Manufacturer Declaration 24 11. MANUFACTURER DECLARATION MANUFACTURER'S DECLARATION OF CONFORMITY We: VSE Volumentechnik GmbH Hönnestraße 49 D-58809 Neuenrade declare under our own responsibility that the product(s): IO.flow ® (IO-Link Device) to which this declaration refers conform to: IO-Link Interface and System Specification, V1.1 .3, June 2019 ( NOTE 1,2 ) IO Device Description, V1.1.3, January 2021 IO-Link Common Profile Specification, V1.1, Dec. 2021 The conformity tests are documented in the test reports: TID-20220907-01_VSE_1654_4900_EMC Test Report.pdf TID-20220905-01_VSE_1654_4900_IO-Link PhysicalLayer Test Report.pdf Protocol_Test_Report_IO.flow_Nov22.pdf Issued at Authorized signatory Name: Axel Vedder Title: Managing Director Signature: Reproduction and all distribution without written authorization prohibited NOTE 1 Relevant Test specification is V1.1.3, January 2021 NOTE 2 Additional validity in Package 2020 and Corrigendum IO-Link Manufacturer Declaration VSE IO.flow® MD-Version: V1.1.3 / 2022-01 Page 1/1 Phone +49 (0) 23 94 / 6 16-30 [email protected] www.vse-flow.com E18-07-38-005 Vers. e 02/23 www.plakart.de VSE Volumentechnik GmbH Hönnestraße 49 58809 Neuenrade / Germany
advertisement
Key Features
- IO-Link communication
- Signal conversion
- Data backup
- Device replacement
- Linearization
- Signal filtering
- Pulse filter function
- Flow direction change support
- Peak flowrate monitoring
- Event triggers
Related manuals
Frequently Answers and Questions
How do I connect the IO.flow to my flowmeter and IO-Link master?
Use M12 extension cables to connect the IO.flow's female connector to the flowmeter and its male connector to the IO-Link master. Ensure both cables are less than 20 meters long.
What are the different types of signal filters available?
The IO.flow offers three filter levels: "dynamic" for fast response, "smoothed" for reduced noise, and "precise" for maximum accuracy. Select the appropriate filter based on your application's needs.
Can I change the measurement unit for flow and volume?
Yes, you can configure the output unit using the V_Unit parameter. Choose between pulses, volume, and mass depending on your requirements.
How do I perform a device replacement with a new IO.flow?
If data storage is enabled, the IO-Link master will backup all relevant parameters. Connect the new IO.flow and start the data storage download to restore the configuration.