advertisement
▼
Scroll to page 2
of
24
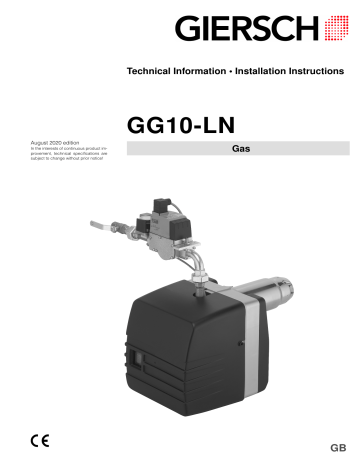
Technical Information • Installation Instructions GG10-LN August 2020 edition In the interests of continuous product improvement, technical specifications are subject to change without prior notice! Gas GB Contents Overview..............................................................................................................3 General information ............................................................................................................................... 3 Scope of supply and electrical ratings................................................................................................... 3 Operating instructions ........................................................................................................................... 3 Instruction of operating personnel ......................................................................................................... 3 Maintenance and customer service ....................................................................................................... 3 Key for code designation ....................................................................................................................... 4 Technical specifications ......................................................................................................................... 4 Installation............................................................................................................5 Installing the flange and burner .............................................................................................................. 5 Installing the gas ramp .......................................................................................................................... 5 Service position ...................................................................................................................................... 6 Connecting to the power supply ............................................................................................................ 7 Function ...............................................................................................................8 Control unit LME .................................................................................................................................... 8 Start-up ..............................................................................................................11 Air flow setting .................................................................................................................................... 11 Adjusting the mixing head ................................................................................................................... 11 Adjusting the ignition electrode ............................................................................................................ 12 Adjusting the gas ramps...................................................................................................................... 13 Adjustment tables................................................................................................................................ 15 Calculation principle for gas burner adjustment 17 Service instructions/dimensions ........................................................................19 19 19 19 20 21 22 23 24 24 E.04.99 • G. 17.08.20 Flame control using ionisation electrode ............................................................................................ Measuring the ionisation current ........................................................................................................ Servicing the air pressure monitor....................................................................................................... Circuit diagram GG10-LN ................................................................................................................... Exploded drawing................................................................................................................................ Spare parts list .................................................................................................................................... Declaration of conformity for the forced-air gas burner ....................................................................... Burner dimensions / boiler connection dimensions ............................................................................. Working ranges ................................................................................................................................... 2 Overview Overview General information Installation of a gas-fired heating system must be performed in accordance with the applicable regulations and guidelines. It is therefore the duty of the installer to be familiar with all applicable regulations and requirements. Installation, start-up and maintenance must be performed with utmost care. The burner must not be operated in rooms with high levels of air humidity (laundry rooms), dust or corrosive vapours. The boiler room must be ventilated accordingly with ventilation air. The ENERTECH GG10-LN series of gas burners are suitable for burning natural gas or liquefied petroleum gas in accordance with DIN EN 437 and comply with the European Standard DIN EN 676. Scope of delivery and connection data Before installing the ENERTECH gas burner, please check the scope of delivery. Scope of delivery: Burner, sliding flange and gasket, 4 retaining screws, separate operating instructions, technical information, one 7-pin connector, gas ramp and gasket. Gas installation and commissioning are subject to the applicable national regulations, e.g. in Germany the Technical Regulations of the DVGW (DVGW-TRGI). The following must be observed for Switzerland: SVGW Gas Provisions G1, G3: Gas installation EKAS Form. 1942: Liquefied gas regulation, Part 2 Regulations of cantonal authorities (e. g. fire department regulations). The gas pipe must be designed to conform to the flow rate and the available gas flow pressure and routed with the lowest pressure loss over the shortest distance to the burner. The loss of gas pressure via the gas ramp and the burner, and the resistance on the fuel gas side of the heat generator must be less than the connection flow pressure. Caution ! Observe the through-flow direction of the gas ramp. Operating instructions The operating instructions together with this technical information leaflet must be displayed in a clearly visible position in the boiler room. It is essential to enter the address of the nearest customer service centre in the operating instructions. Instruction of operating personnel Faults are often caused by operator error. The operating personnel must be properly instructed in how the burner works. In the event of recurring faults, Customer Service should be notified. Maintenance and customer service E.04.99 • G. 17.08.20 The complete system should be checked once a year for correct functioning and leaks by a representative of the manufacturer or other suitably qualified person. We accept no liability for consequential damage in cases of incorrect installation or repair, the fitting of nongenuine parts or where the equipment has been used for purposes for which it was not intended. 3 Overview Key for code designation GG10/1-N-LN LowNox LowNox Erdgas LL+E Flüssiggas Natural gas LL +="-N"oder E = "-N", liquefied gas 3B/P =="F" "-F" Baugröße Burner type Burner series Baureihe Technical specifications Burner type Technical specifications Burner output Gas type GG10/1-LN GG10/2-LN 12 - 60 kW 20 - 90 kW Natural gas LL + E = "-N", liquefied gas 3B/P = "-F" Gas input pressure with MBC65 ½“ 65 mbar Gas input pressure MBC120 ¾“ 360 mbar Voltage 1 / N / PE ~ 50 Hz / 230 V Current consumption start max. / operation 1.9 A / 0.8 A Electric motor 90 Ignition transformer 35 mA; 8 kV rms. Control unit LME11 Weight 8 kg ≤ 59 dB(A) E.04.99 • G. 17.08.20 Noise emission 4 Installation Installation Mounting the flange and burner 1. Mount the flange base and gasket onto the boiler: - Observe "top" mounting position, - Tighten M8 screws including U-washer, - Place the flange top section (half shell) onto the burner tube. During the assembly procedure, ensure that the 0° display on the flange top aligns with the "top" display on the flange base. 2. Installing the burner: - To mount the burner, engage the burner housing in the retaining lugs by rotating it clockwise. - Tighten the clamping screw. Make sure that the conical nipple is inserted in the lower part of the flange correctly. 0° indicator Conical nipple top Flange top Flange base Mounting the gas ramp! Installing the gas ramp Installation position for vertical line Installation position for horizontal line as desired tilted up to max. 90° to left or right, not overhead Minimum distance to masonry 20 mm Installation position MBC-... Remove plastic protective plug. Mount the screw connections with enclosed seals. Observe the installation position. Check connecting point of gas ramp with non-corrosive foaming agent for leaks and vent the gas pipe. • When venting, use a hose to discharge the gas safely to the atmosphere. E.04.99 • G. 17.08.20 • • • • The gas supply line and gas assembly must not exert tensile, compression or torsional forces on the burner, since this can otherwise adversely affect operational safety. In Germany, observe DVGW-TRGI 1986/96 Section 7, TRF 1988, DIN 4756 and local regulations 5 Installation Service position E.04.99 • G. 17.08.20 Risk of injury by fan impeller on activation in service position. Release quick-release locks (4 x) and detach base plate.Place the keyhole openings in the base plate onto the socket head cap screws of the housing and lock them into place. 6 Installation Connect to power supply • • • Deenergise the system. Main switch "OFF". Check the polarity of all connectors. Connect the plug unit as indicated in the connection diagram. Lay the flexible control line so that the boiler door remains swivellable. Insert the coded cube connectors to the gas pressure monitor and to the solenoid valves and use a screw to fasten. If plug X11 is wired as shown the terminal diagram, check that the pins are correctly assigned.. Connect the 7-pin plug of the boiler controller (X11) to the black-brown socket on the burner (X12). The power cord of the 7-pin connecting plug X11 must be fused with a slow-acting fuse rated for max. 6.3 A or a quick-acting fuse rated for max. 10 A. • • • • Connection diagram Steckerteil X11 male adapter zum X11 Kessel to boiler Buchsenteil male adapter X12 X12 Brenner on burner am H11 N B4 P11 N S3 H13 T2 F21 Q1 N T1 PE PE L1 L1 N F11 F3 X11 X12 E.04.99 • G. 17.08.20 Legend: F11 External fuse 6.3 AT/max. 10AF F21 External temp. controller F3 Ext. safety temperature limiter Q1 Main heater switch H11 External pilot lamp H13 Ext. lamp for fault signals L1 Phase PE Protective earth P11 Operating hours counter N Neutral conductor 7 Function Function Function test of control box Danger of fatal injury from electric shocks! Disconnect electrical cable from power supply before carrying out any work on live parts! Troubleshooting may only be carried out by authorised and trained personnel! (Remote) Unlocking may only be carried out by an authorised specialist. Carry out the following checks after commissioning and maintenance of the burner. Burner start with interrupted lines to flame sensor: • Interrupt the line to the flame sensor and start the burner. At the end of the safety time, the control unit performs a failure shut-down after three repetitions. • Re-establish the connection. Burner operation with loss-of-flame simulation: • Turn the dial of the gas pressure monitor to the minimum value (see Page 13). • Start the burner. • Close the ball valve during operation. After loss of flame, the control unit performs a failure shut-down after three repetitions. • Turn the dial of the gas pressure monitor to the inital value. Burner operation with loss of air pressure: • Pull of the air hose at the "+" input of the air pressure monitor during operation. The control unit performs a failure shut-down. • Attach the air hose to the air pressure monitori again. E.04.99 • G. 17.08.20 Safety and switching functions If, at the end of the safety time, no flame forms, or there is a loss of flame during operation, a maximum of three repetitions can be carried out for each control circuit; otherwise a failure shut-down is performed. If a flame signal is given during the pre-ventilation phase, a failure shut-down will occur immediately. The position of the air pressure monitor is continuously checked. There can be no start-up if it is not in its neutral position. If the NO contact does not close or reopens during the pre-ventilation phase, a failure shutdown will occur. The air pressure monitor contact and the valves close if the air flow is insufficient during operation. The device goes into failure mode. 8 Function Display during commissioning Color code table for multi-color signal lamp Status Color code Color Waiting time (tw), other Waiting states ................................. OFF Air pressure switch waiting phase, Pre-ventilaton ................................. Yellow Ignition phase, ignition controlled Operation, flame OK Yellow flashing ................................. Operation, flame poor Green Green flashing External light on burner start Green-red Undervoltage Yellow-red Fault, alarm ...................................... Red Fault code output, see fault code table Red flashing Interface diagnostics Red flickering light E.04.99 • G. 17.08.20 Key: ......... Permanent OFF Red Yellow Green 9 Function Troubleshooting diagnostics After failure shutdown, the red signal lamp lights up permanently. In this state, the visual troubleshooting diagnostics can be activated according to the fault code table by actuating the unlocking key > 3 seconds. Actuate the unlocking key again for >3 seconds to activate the interface diagnostics. The interface diagnostics operates only when the unlocking key adapter AGK20… is not attached. If the interface diagnostics is activated unintentionally (indicated by a weak flickering of the signal lamp in red), it can be switched off again by actuatiing the unlocking key >3 seconds. The correct moment for switchover is signaled by a yellow light pulse. Fault code table Flashing code "red" Alarm at of the fault signal terminal 10 lamp (LED) Possible causes Flashes 2 x On No flame forms at the end of the safety time (TSA) - Defective or soiled fuel valves - Defective or soiled flame sensor - Poor burner setting, no fuel - Defective defekte ingnition device Flashes 3 x On Error air pressure monitor (LP) - Air pressure failure after specified time (t10) - Air pressure switch (LP) welded in idle position Flashes 4 x On External light on burner start Flashes 5 x On Time monitoring air pressure monitor (LP) - Air pressure monitor (LP) welded in working position - Fault during seal check (only in connection with leak check (LDU11..) Flashes 6 x On Free Flashes 7 x On Too frequent loss of flame during operation (repetition limit) - Defective or soiled fuel valves - Defective or soiled flame sensor - Defective burner setting Flashes 8 x On Free Flashes 9 x On Free Flashes 10 x Off Wiring fault or internal error, output contacts, other fault Flashes 14 x On CPI contact not closed The control outputs are deenergised during troubleshooting diagnostics. - The burner remains switched off, - The entrnal fault display remains deenergised - Fault signal alarm (AL) at terminal 10 according to fault code table. E.04.99 • G. 17.08.20 Unlock to exit the troubleshooting diagnostics and switch the burner on again. Press the unlocking key approx. 1 s (< 3 s). 10 Start-up Start-up The burner can be put into operation once the gas and electrical installation and assembly work has been completed. Air regulating sleeve The scale serves as an orientation aid to facilitate adjustment of the air quantity. Use a hexagon key (SW17) to modify the air quantity according to performance in accordance with the setting table (see page 15 ff). The values in the table of settings can be read off directly at the scale. If there is overpressure in the combustion chamber, set the value higher; if there is underpressure, the value must be reduced. Readjustment is necessary in any case on account of the type of plant. Air pressure sleeve position (dimension "A") After setting the combustion values, the air regulatig sleeve must be fixed with screw 1 to prevent misalignment. 1 Adjustment of the mixing head Set the position of the mixing head according to burner output in accordance with the setting table on page 15 ff. E.04.99 • G. 17.08.20 Mixing head position (dimension "B") 11 Start-up Adjusting the ignition electrode Ignition electrode Ionisation electrode The electrode is set at the factory. The dimensions are included for checking purposes. E.04.99 • G. 17.08.20 2.0 ±0,5 12 Start-up Setting the gas ramps Remove the gas flow cap on the gas ramp upwards prior to setting. The Allen key (2 mm) for setting is located in the cap. MBC65 ½“ MBC120 ¾“ Cap Cap MBC65 ½“ MBC120 ¾“ Measuring points pG - + pG + Measuring points pG + - pS pS - pG + - To measure the gas pressure, open the measuring points and connect the pressure gauge. pS = Starting gas pG = Gas pressure gauge Perform commissioning steps 1 bis 8 using the plant data analogous to the setting example. Exhaust gas values Natural gas LL+E O2 content CO2 content Liquefied gas propane 3P 3.5-5.0% 9-10% E.04.99 • G. 17.08.20 Setting the gas pressure monitor to Minimum (5 mbar at MBC65 ½“) 13 10.5-11.5% Start-up Adjustment example, GG10/1 to 30 kW, natural gas E: 1. Set the position of the mixing head to dimension "B" 5 mm (see Fig. p. 11, Setting the mixing head). 2. pS , pG and dimension"A" remain unchanged. 3. Start the burner. 4. To achieve the desired performance (30 kW in this case), pG and dimension "A" must be changed gradually from the factory setting. Set pG to approx. 5.1 mbar and dimension "A" to approx. 35°. 5. Turn pS up (left) to 19 mm 6. Start the burner again and correct the settings if necessary. 7. Close the measuring points 8. Check the gas pressure controller after start-up. Close the ball valve slowly. Close the ball valve slowly, the burner must switch off without triggering a fault. MBC120 ¾“ MBC65 ½“ pG pS pS pG The setting screw pG does not have a stop. To restore the factory settings for a modified gas ramp, you must observe the following: GG10/2-LN with MBC-120 1 Turn pG 10 x left 2 pS 18 mm 2 pS 18 mm 3 Dimension "A" 24° 3 Dimension "A" 35° 4 Start the burner 4 Start the burner 5 Set pG to 2.3 mbar 5 Set pG to 3.9 mbar E.04.99 • G. 17.08.20 GG10/1-LN with MBC-65 1 Turn pG 10 x left 14 Start-up Adjustment tables The values given in the tables are only guide values for start-up. The system settings required in each case must be redefined if values such as boiler output, calorific value and altitude deviate. A correction is required in any case. On first commissioning and after each adjustment, a combustion check must be carried out. GG10/1-N-LN Burne r output Boiler output η= 92% [kW] 12 Natural gas LL: Hi,n = 9.3 [kWh/m3] Mixing head Position Dimension "B" [mm] Gas nozzle pressure pG Starting gas pS Gas flow rate [kW] Air regulating sleeve Position Dimension "A" [°] [mbar] [mm] [m3/h] 11 10 5 1.0 16 1.3 15 14 18 5 1.7 18 1.7 20* 18 24 5 3.0 18 2.2 25 23 29 5 4.6 18 2.8 30 28 35 5 6.6 19 3.3 41 38 66 5 11.6 22 4.5 45 41 72 5 14.0 22 5.0 40 37 45 0 8.1 22 4.4 51 47 64 0 12.6 22 5.7 60 55 125 0 16.0 22 6.7 GG10/1-N-LN Burner output Boiler output η= 92% [kW] 12 Natural gas E: Hi,n = 10.4 [kWh/m3] Mixing head Position Dimension "B" [mm] Gas nozzle pressure pG Starting gas pS Gas flow rate [kW] Air regulating sleeve Position Dimension "A" [°] [mbar] [mm] [m3/h] 11 10 5 0.8 16 1.2 15 14 18 5 1.3 18 1.5 20* 18 24 5 2.3 18 2.0 25 23 29 5 3.5 18 2.5 30 28 35 5 5.1 19 3.0 41 38 66 5 8.9 22 4.1 45 41 72 5 10.8 22 4.5 40 37 45 0 6.2 22 4.0 51 47 64 0 9.7 22 5.1 60 55 125 0 12.3 22 5.9 Liquid gas: Hi,n = 25.89 [kWh/m3] E.04.99 • G. 17.08.20 GG10/1-F-LN Burner output Boiler output η= 92% Mixing head Position Dimension "B" [mm] Gas nozzle pressure pG Starting gas pS Gas flow rate [kW] Air regulating sleeve Position Dimension "A" [°] [kW] [mbar] [mm] [m3/h] 16 15 18 5 1.0 16 0.6 24* 22 29 5 2.3 18 1.0 30 28 35 2 2.7 19 1.2 35 32 45 2 3.7 20 1.4 40 37 45 0 3.9 22 1.6 50 46 60 0 6.0 22 2.0 65 60 125 0 10.0 22 2.6 * Factory setting 15 Start-up Natural gas LL: Hi,n = 9.3 [kWh/m3] GG10/2-N-LN Burner output Boiler output η= 92% Mixing head Position Dimension "B" [mm] Gas nozzle pressure pG Starting gas pS Gas flow rate [kW] Air regulating sleeve Position Dimension "A" [°] [kW] [mbar] [mm] [m3/h] 21 19 22 5 1.2 16 2.3 35* 32 35 5 3.9 18 3.9 50 46 51 5 7.6 18 5.5 36 33 31 2 2.8 18 4.0 50 46 40 2 5.1 20 5.5 65 60 55 2 8.3 20 7.2 65 60 60 0 8.0 22 7.2 80 74 80 0 11.4 22 8.9 90 83 125 0 15.4 22 10.0 Natural gas E: Hi,n = 10.4 [kWh/m3] GG10/2-N-LN Burner output Boiler output η= 92% Mixing head Position Dimension "B" [mm] Gas nozzle pressure pG Starting gas pS Gas flow rate [kW] Air regulating sleeve Position Dimension "A" [°] [kW] [mbar] [mm] [m3/h] 21 19 22 5 0.9 16 2.1 35* 32 35 5 3.0 18 3.5 50 46 51 5 5.8 18 5.0 36 33 31 2 2.2 18 3.6 50 46 40 2 3.9 20 5.0 65 60 55 2 6.4 20 6.4 65 60 60 0 6.1 22 6.4 80 74 80 0 8.8 22 7.9 90 83 125 0 11.8 22 8.9 GG10/2-F-LN Burner output Boier output η= 92% [kW] Liquid gas: Hi,n = 25.89 [kWh/m3] Mixing head Position Dimension "B" [mm] Gas nozzle pressure pG Starting gas pS Gas flow rate [kW] Air regulating sleeve Position Dimension "A" [°] [mbar] [mm] [m3/h] 22 20 21 5 1.0 18 0.9 35* 32 36 5 2.8 18 1.4 40 37 33 2 2.8 20 1.6 65 60 55 2 7.2 20 2.6 75 69 702 0 8.7 22 3.0 85 78 100 0 10.5 22 3.4 95 87 125 0 13.2 22 3.8 E.04.99 • G. 17.08.20 * Factory setting 16 Start-up Calculation principle for gas burner adjustment The values given in the tables are setting values for start-up. The necessary system adjustment must be newly determined in each case. General: The calorific value (Hi,n) of fuel gases is generally specified for the normal state (0°C, 1013 mbar). Natural gas E Hi,n = 10.4 kWh/m3 Natural gas LL Hi,n = 9.3 kWh/m3 Liquefied gas PB Hi,n = 25.89 kWh/m3 Gas meters measure the volume of gas in the operational state. Gas flow determination: To allow the heat generator load to be adjusted correctly, the gas flow rate must be determined in advance. Example: Height above sea level Atmospheric pressure B (according to table) Gas pressure PG at meter Gas temperature ϑG Boiler rating Qn Efficiency ηK (assumed) Calorific value Hi,n 230 m 989 mbar 20 mbar 16°C 30 kW 92% 10.4 kWh/m3 Gas flow in standard state (Vn)1 3 Qn m 30kW Vn = -------------------- = ---------------------------------------- = 3, 1 ------η k × H i, n kWh h 0, 92 × 10, 4 ----------m3 Gas flow in operating state (V B) 3 m -----3 , 1 3 Vn h m VB = ------ = ----------------- = 3, 3 ------f 0, 94 h Conversion factor (f) B+P 273 f = --------------G × -------------------1013 273 + ϑG Annual average air pressure Average geodetic altitude of the from supply region above sea level [m] to E.04.99 • G. 17.08.20 Annual average of air pressure 1 51 101 151 201 251 301 351 401 451 501 551 601 651 701 50 100 150 200 250 300 350 400 450 500 550 600 650 700 750 (mbar) 1016 1013 1007 1001 995 989 983 977 971 965 959 953 947 942 936 930 0 Legend: Qn = boiler output [kW] ηK = efficienc [%] Hi,n = lower standard calorific value [kWh/m3] f = conversion factor B= atmospheric pressure [mbar] pG = gas pressure at gas meter [mbar] ϑG = gas temperature at gas meter [°C] 17 Start-up Flow measurement Determining flow duration at gas meter.. Calculated flow duration in seconds tspec for a flow volume of 200 litres (corresponding to 0.2 m3) for the example given above is:: VB = 3.3 m3/h s 3 3s 3s 0, 2m × 3600 --- 720m --- 720m --h h h - = -------------------- = ------------------- = 218s t soll = ------------------------------------3 3 3 m m m V B -----3, 3 -----V B -----h h h Gas flow setting Measures Greater than calculated flow duration tset Increase gas flow Less than calculated flow duration tset Reduce gas flow Equal to calculated flow duration tset Gas flow achieved E.04.99 • G. 17.08.20 Measured flow duration in seconds [s] 18 Service instructions/dimensions Service instructions/dimensions Flame control using ionisation electrode If an AC current is applied between the burner and the ionisation rod, a DC current flows due to the rectifying effect of the flame. This ionisation current forms the flame signal and is amplified and passed to control box. A flame cannot be faked because the rectifying effect no longer works if there is a short-circuit between the sensor electrode and the burner. Measuring the ionisation current The ionisation current must be measured during burner start-up and maintenance or after a fault indication in the control box. This done by disconnecting the plug in the ionisation cable and connecting it to the ionisation measuring cable. The measurement must be carried out directly after post-ignition during the safety time! The ionisation current must be at least 1.5 µA. Values below 1.5 µA will result in unreliable operation or produce a fault. In this case, clean the inside of the ionisation rod and the burner tube. Bend ionisation rod if necessary. The ionisation rod must be replaced if defective. If necessary, reverse polarity on ignition transformer. Check the cable for moisture and dry it if necessary. Servicing the air pressure monitor • Detach the silicone connecting hose and clean, check the switching function. • Replace the air pressure monitor if switching function is no longer working properly. To do so: • Switch off the burner voltage Disconnect (7-oin connector X11). • Unscrew the cover. • Disconnect the electrical connectors. • Release the retaining screws on motor. • Reassemble in the reverse order.. "P1" marks the pressure measuring connection for the silicone hose! E.04.99 • G. 17.08.20 P1 19 Service instructions/dimensions Circuit diagram GG10-LN with LME Boiler controller Burner SP_1-860 Gas ramp B2 Ionisation electrode F11 External fuse 6.3 AT/max. 10AF F21 External temp. controller F3 Safety temperature limiter F4 Air pressure monitor F51 Gass pressure monitor H11 External pilot lamp H13 Ext. lamp for fault signals M1 Burner motor P11 Ext. operating hours counter Q1 Main heater switch S1 Control unit LME T3 Ignition transformer X11 Plug for boiler controller X12 Socket for burner X52 Socket for gas pressure monitor (grey) X62 Socket for solenoid valves (black) X51,X61 Gas ramp connection Y1 Solenoid valve Y3 Safety solenoid valve E.04.99 • G. 17.08.20 Colour code: bl = blue br = brown rt = red sw = black ws = white 20 Service instructions/dimensions E.04.99 • G. 17.08.20 ZBZ_1-758 Exploded drawing 21 Service instructions/dimensions Spare parts list Seq. No. Designation 1 Gas mixer head GG10/1-N-LN, complete, with baffle plate and electrode VE Order no. 1 47-90-25313 1 Gas mixer head GG10/2-N-LN, complete, with baffle plate and electrode 1 47-90-25314 1 Gas mixer head GG10/1-F-LN, complete, with baffle plate and electrode 1 47-90-25315 1 Gas mixer head GG10/2-F-LN, complete, with baffle plate and electrode 1 47-90-25316 2 Ignition electrode 1 47-90-25296 3 Ignition cable with angled plug 1 47-90-24835 3 Ignition cable with angled plug 100 mm extended 1 47-90-26740 3.1 Ionisation cable with socket unit 1 44-90-20634 3.1 Ionisation cable with socket unit 100 mm extended 1 47-90-26328 4 Silicon hose 10 x 1 x 80 lg. 1 47-90-22466 5 Adapter plate with gas connection, complete 1 47-90-29045 5 Adapter plate with gas connection, complete 100 mm extended 1 47-90-29045-01 6 Intake channel insulation insert 1 47-90-22161 7 Airflow rectifier 1 47-90-22489-01 8 Guide ring 1 47-90-26918 9 Air regulatig sleeve with scale 1 47-90-21777 10 Spring lid with foeam rubber seal 1 47-90-29049 11 Motor 90 W 1 31-90-11582 12 Fastening ring for air pressure monitor 1 47-90-25249 13 Air pressure monitor 1 47-90-25290 14 Control unit LME11 1 47-90-29190 15 Control unit base GG10 LME11 1 47-90-29467 16 Ignition transformer 1 47-90-24469 19 Pre-assembled base plate 1 47-90-25287 20 Pinion 1 47-90-21884 21 7-pin socket with cable 1 47-90-22072 22 Ventilator wheel Ø133 x 52 1 47-90-21729 24 Filler insulation 1 47-90-22105 23 Inlet nozzle item 1 1 47-90-21774-01 25 Housing, complete with suction silencer 1 47-90-21770 26 Intake damper cpl. 1 47-90-21771 27.1 Burner tube GG10/1-LN 1 47-90-24757 27.2 Burner tube GG10/2-LN 1 47-90-24758 27.2 Burner tube GG10/2-LN 100 mm extended 1 47-90-24758-01 Assembly kit Enertech flange 90 mm 1 47-90-25126 28 O-ring ID 110 x 4 1 47-90-25242 29 - Flange seal 152 x 152 mm 1 47-90-24429 30 Burner cover, complete with reset button 1 47-90-21765-01 31 Rectangular spring 1 47-90-26966 Interference-suppression button, short 1 47-90-21767 - Working ranges 2 x Ø4,5 1 47-90-25129 - Transformer earthing cable 1 47-90-25289 E.04.99 • G. 17.08.20 32 22 Service instructions/dimensions Declaration of conformity for the forced-air gas burner Declaration of Conformity for Gas Burners We, Enertech GmbH, Adjutantenkamp 18 in D-58675 Hemer declare under our responsibility that gas burner type GG10/... is conform with the regulations of these directives MD2006/42/EG EMC2014/30/EU GAD 2016/426/EU LVD2014/35/EU RoHS 2011/65/EU DIN EN 676 and is marked with: CE-0085 Hemer, 16.01.2018 i.V. Wendel Sales director Rebbe Technical management E.04.99 • G. 17.08.20 ppa. 23 Burner dimensions / boiler connecting dimensions (all dimensions are in mm) GG10/1-LN GG10/1-N-LN 180 160 225 ± 10 45° M8 226 90 59 150 31 45° min Ø90 Ø150 145 min. 302 37 173 GG10/2-LN GG10/2-N-LN 1,0 GG10/1-LN 0,8 0,6 0,4 0,2 0 0 2 0 4 0 6 0 8 0 100 B r e n nBurner e r l e i s tcapacity ung [kW ] [kW] Furnace resistance [mbar] Feuerraumwiderstand [mbar] Feuerraumwiderstand [mbar] Furnace resistance [mbar] Working ranges 1,0 GG10/2-LN 0,8 Mixer unit "close" Mixer unit "open" 0,6 0,4 0,2 0 0 2 0 4 0 6 0 8 0 100 B r e n Burner n e r l e i s capacity tung [kW ] [kW] All information in this technical documentation as well as the drawings, photos and technical descriptions made available by us remain the property of GIERSCH and may not be duplicated without our prior written permission. Right reserved to effect modifications. Enertech GmbH • Brenner und Heizsysteme Adjutantenkamp 18 • D-58675 Hemer • Telephone 02372/965-0 • Telefax 02372/61240 Email: [email protected] • Internet: http://www.giersch.de G. 17.08.20 • 08-2020 • Art. No. 70-17-58250-GB • Printed in Germany • Enertech GmbH Working ranges acc. to DIN EN 676. The working ranges are referred to 15°C and 1013 mbar.
advertisement