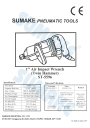
Sumake ST-5596 Owner's Manual
Add to My manuals8 Pages
Sumake ST-5596 is a powerful 1" impact wrench with a twin-hammer mechanism, delivering an impressive 1400 ft-lb of maximum torque and a free speed of 4000 r/min. It's designed for heavy-duty applications, such as loosening rusted bolts or tightening lug nuts on large vehicles.
The ST-5596 features a durable construction with a comfortable handle, making it easy to use for extended periods. Its 3/8" air inlet and 1/4" capacity bolt size make it compatible with a wide range of accessories and attachments.
With its exceptional power, versatility, and user-friendly design, the Sumake ST-5596 is an ideal tool for professionals and DIY enthusiasts alike.
advertisement
▼
Scroll to page 2
of
8
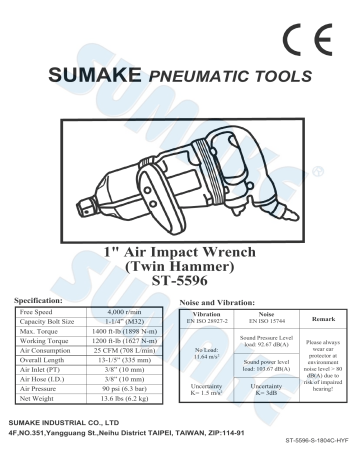
SUMAKE PNEUMATIC TOOLS 1" Air Impact Wrench (Twin Hammer) ST-5596 Specification: Free Speed Capacity Bolt Size Max. Torque Working Torque Air Consumption Overall Length Air Inlet (PT) Air Hose (I.D.) Air Pressure Net Weight Noise and Vibration: 4,000 r/min 1-1/4” (M32) 1400 ft-lb (1898 N-m) 1200 ft-lb (1627 N-m) 25 CFM (708 L/min) 13-1/5” (335 mm) 3/8” (10 mm) 3/8” (10 mm) 90 psi (6.3 bar) 13.6 lbs (6.2 kg) Vibration Noise EN ISO 28927-2 EN ISO 15744 Remark Sound Pressure Level load: 92.67 dB(A) No Load: 11.64 m/s² Sound power level load: 103.67 dB(A) Uncertainty K= 1.5 m/s² Uncertainty K= 3dB Please always wear ear protector at environment noise level > 80 dB(A) due to risk of impaired hearing! SUMAKE INDUSTRIAL CO., LTD 4F,NO.351,Yangguang St.,Neihu District TAIPEI, TAIWAN, ZIP:114-91 ST-5596-S-1804C-HYF EC DECLARATION OF CONFORMITY We: SUMAKE INDUSTRIAL CO., LTD. 4F, No. 351, Yangguang St., Neihu District, Taipei City, Taiwan declare in sole responsibility that the equipment Equipment: 1" AIR IMPACT WRENCH (TWIN-HAMMER) Model/ Serial No.:ST-5596 to which this declaration applies, complies with these normative documents: Machinery Directive: 2006/42/EC and conforms to the following EN standard, EN ISO 12100: 2010 EN ISO 11148-6:2012 Name and Signature/Position Date and Place 2013/6/28 Mike Su – Managing Director Taipei, Taiwan ST-5596-D-1401A-HYF Application: The impact wrench is designed to deliver high torque output with minimal exertion by the user, for the purpose of tightening or loosening nuts and bolts. Operation Method: 1. 2. 3. 4. Press the trigger for running and release to stop. Please be aware that the tool will stop rotation within few seconds. For safety reason, place the tool on the level plate or on hanger after use. You can adjust air flow by switch which indicated by several scales. The more air flow, the bigger torque output will be. Before use the tool, please check rotation direction; “F” indicates forward and “R” is reverse. Forward is defined as clockwise direction seen from the operator’s position. Only use sockets designed “for use with impact wrenches”. Hand tool sockets can break, creating a hazard from flying pieces. Always check sockets, retainers and drives regularly from wear or damage and replace when necessary. Common Troubleshooting: Event Appearance Air is coming from the exhaust valve Not operating No air coming from the exhaust valve Low revolution rate Low efficiency Motor running abnormal or unusual noises occur Motor keeps running Impact rate increases,torque rate decreases Trigger does not bounce back or does not bounce back correctly Trigger function normally Possible Cause Blades broken or worn out Ball bearing damaged Rusty motor or clogged with objects Hammer set broken Regulator is set at OFF No air flow Valve set damaged or broken Not enough air pressure Regulator/Reverse valve knob is not set properly Not enough lubrication, ball bearing, upper/lower end plate, cylinder, rotor, blade damaged Hammer set broken or worn out Trigger set has other objects stuck on it or the spring is broken, deformed or rusty Trigger O-ring worn out or valve set damaged or broken Solution Replace blades Replace ball bearing Disassemble and repair Disassemble and repair Adjust regulator Check air system and connections Disassemble and repair Check air pressure Adjust regulator/Reverse valve knob Lubricate or replace parts Replace hammer set Disassemble and repair Disassemble, repair and replace parts ST-5596(-6)-I-1403B-HY ST-5596(-6) 1" IMPACT WRENCH (W/6" ANVIL) (TWIN-HAMMER) PARTS LIST No. Parts No. 1 5596-01 2 5596-02 3 5596-03 4 5596-04 5 5596-05 6 5596-06 8 5596-08 9 5596-09 10 5596-10 11 5596-11 5596-12A 12 5596-12B 13 5596-13 14 5596-14 15 5596-15 16 5596-16 17 5596-17 18 5596-18 19 5596-19 20 5596-20 21 5596-21 22 5596-22 23 5596-23 24 5596-24 25 5596-25 26 5596-26 27 5596-27 28 5596-28 29 5596-29 30 5596-30 Description Hammer Housing Screw Seal Screw Washer Cap Screw Handle Anvil Bushing Socket Retainer O-Ring 1" Dr. Anvil [Incl. 10, 11] 6" Ext. 1" Dr. Anvil [Incl. 10, 11] Hammer Dog Hammer Cage Hammer Pin Gasket Ball Bearing Protective Nose Cover Valve Plug Housing Ass'y [Incl. 7, 52] Ball Bearing Oil Seal O-Ring Front End Plate Spring Pin Cylinder Rotor Rotor Blade Rear End Plate Spring Pin Q'ty 1 1 1 4 6 2 1 1 1 1 1 1 2 1 2 1 1 1 4 1 1 1 1 1 1 1 1 6 1 1 No. 31 32 33 34 35 36 37 38 39 40 41 43 44 45 46 47 48 49 51 53 54 55 58 62 63 64 65 66 67 Parts No. 5596-31 5596-32 5596-33 5596-34 5596-35 5596-36 5596-37 5596-38 5596-39 5596-40 5596-41 5596-43 5596-44 5596-45 5596-46 5596-47 5596-48 5596-49 5596-51 5596-53 5596-54 5596-55 5596-58 5596-62 5596-63 5596-64 5596-65 5596-66A 5596-66B 5596-67 Description Q'ty Ball Bearing 1 1 Retainer Ring Gasket 1 Protective Band 1 1 Rear Cover Ass'y [Incl. 42, 50] Cap Screw 4 1 Trigger Pin 2 1 O-Ring Valve Screw 1 Pin 1 O-Ring 2 Reverse Lever 1 Spring 1 Steel Ball 1 Washer 4 Reverse Switch 1 1 Spring Pin Valve Stem 1 Plug 1 Valve Seat 1 1 Valve Spring Oil Seal 1 Pin 1 Pin 1 Mesh Filter 1 3 Cap Screw Air Inlet Bushing (PT19) 1 Air Inlet Bushing (NPT18) 1 Hex Key 1 ST-5596(-6)-P-1505E-HY IMPACT WRENCH Original instructions SUMAKE Industrial Co. Ltd. Read all these safety instructions before operating this product and save these instructions. The tool has been manufactured in conformity with the instruction of EU machine directive. The EU mark will be considered void in the event of inexpert repairs, the use of non-original parts and in case of non-observance of the safety instructions in the user’s manual. Possible direct or indirect consequential damages are not the responsibility of SUMAKE Industrial co., Ltd. General safety rules: 1. 2. 3. 4. 5. 6. 7. 8. 9. 10. 11. 12. 13. 14. 15. 16. 17. 18. 19. 20. 21. 22. 23. 24. Watch the tool at all times when in use. People under the influence of alcohol or drugs are not allowed to use, repair or maintain the tool. Keep unqualified persons, children, etc. away from the tool. Keep work area clean and with sufficient daylight or artificial lighting. The work area on which the machine is used must be cleaned up. Disorder is a potential cause of accidents. Danger of explosion. Never use oxygen and combustible gas as an air supply for the tool which may be ignited by spark and cause fire or explosion. Never use gasoline or other flammable liquids to clean the tool. Do not use air tools in potentially explosive atmospheres such as in the presence of flammable liquids, cleaning solvents, fluid energy or stored gases. Do not expose air tools to rain. Do not use air tools in damp or wet locations. When a fault or failure is detected, the tool must immediately be disconnected from the air supply and returned for repair. When not in use, keep tools in a dry place, either locked up or in a high place, out of the reach of children. Do not force small air tools to do the job of a heavy –duty task. Do not use air tool for purpose of which was not intended. Wear suitable ear protection at environment noise level >80dB(A) and safety spectacles when using the tool. Always wear approved safety goggles if work in dusty. This also applies to other persons in the nearby vicinity. Do not wear loose clothing or jewelry. They can be caught in moving parts. Rubber gloves and non-skid foot wear are recommended when working outdoors. Wear protective hair covering to contain long hair. Keep proper footing and balance at all times. Use clamps or a vice to hold work-piece. It is safer than using your hand and free both hands to operate the air tool. When not use, before performing service or changing accessories, please disconnect tool from air compressor. Do not carry plugged in air tool with your finger on the switch trigger. Be sure switch is in the “OFF” position when connecting to air supply. Watch what you are doing. Use common sense, even unsafe situation or unbalanced positions, particularly when you are tired. Air powered tools can vibrate in use. Vibration, repetitive motions or uncomfortable positions may be harmful to your hands or arms. Stop using any tool if discomfort, tingling feeling or pain occurs. Seek medical advice before resuming use. For multiple hazards, read and understand the safety instructions before installing, operating, repairing, maintaining, changing accessories on, or working near the assembly power tool for threaded fasteners. Failure to do so can result in serious bodily injury. Only qualified and trained operators should install, adjust or use the assembly power tool for threaded fasteners. Do not modify this assembly power tool for threaded fasteners. Modifications can reduce the effectiveness of safety measures and increase the risks to the operator. Do not discard the safety instructions; give them to the operator. Tools shall be inspected periodically to verify that the ratings and markings required by this part of EN ISO 11148 are legibly marked on the tool. The employer/user shall contact the manufacturer to obtain replacement marking labels when necessary. Safety precautions for projectile hazards 1. Failure of the workpiece, of accessories or even of the inserted tool itself can generate high-velocity projectiles. 2. Always wear impact-resistant eye protection during the operation of the assembly power tool for threaded fasteners. The grade of protection required should be assessed for each use. 3. Ensure that the workpiece is securely fixed. Safety precautions for entanglement hazards 1. Entanglement hazards can result in choking, scalping and/or lacerations if loose clothing, personal jewellery, neckware, hair or gloves are not kept away from the tool and accessories. 2. Gloves can become entangled with the rotating drive, causing severed or broken fingers. 3. Rotating drive sockets and drive extensions can easily entangle rubber-coated or metal-reinforced gloves. 4. Do not wear loose-fitting gloves or gloves with cut or frayed fingers. 5. Never hold the drive, socket or drive extension. 6. Keep hands away from rotating drives. Safety precautions for operating hazards 1. The use of the tool can expose the operator's hands to hazards including crushing, impacts, cuts and abrasions and heat. Wear suitable gloves to protect hands. 2. Operators and maintenance personnel shall be physically able to handle the bulk, weight and power of the tool. 3. Hold the tool correctly; be ready to counteract normal or sudden movements and have both hands available. 4. Maintain a balanced body position and secure footing. 5. Release the start-and-stop device in the case of an interruption of the energy supply. 6. Use only lubricants recommended by the manufacturer. 7. Do not use in confined spaces and beware of crushing hands between tool and workpiece, especially when unscrewing. Safety precautions for repetitive motions hazards 1. When using a power tool, the operator can experience discomfort in the hands, arms, shoulders, neck, or other parts of the body. 2. While using an assembly power tool for threaded fasteners, the operator should adopt a comfortable posture whilst maintaining secure footing and avoiding awkward or off-balanced postures. The operator should change posture during extended tasks, which can help avoid discomfort and fatigue. 1 3. If the operator experiences symptoms such as persistent or recurring discomfort, pain, throbbing, aching, tingling, numbness, burning sensations or stiffness, these warning signs should not be ignored. The operator should tell the employer and consult a qualified health professional. Safety precautions for accessory hazards 1. Disconnect the assembly power tool for threaded fasteners from the energy supply before changing the inserted tool or accessory. 2. Do not touch sockets or accessories during impacting, as this increases the risk of cuts, burns or vibration injuries. 3. Use only sizes and types of accessories and consumables that are recommended by the assembly power tool for threaded fasteners manufacturer. 4. Use only impact-wrench-rated sockets in good condition, as poor condition or hand sockets and accessories used with impact wrenches can shatter and become a projectile. Safety precautions for workplace hazards 1. Slips, trips and falls are major causes of workplace injury. Be aware of slippery surfaces caused by the use of the tool and also of trip hazards caused by the air line or hydraulic hose. 2. Proceed with care in unfamiliar surroundings. Hidden hazards, such as electricity or other utility lines, can exist. 3. The assembly power tool for threaded fasteners is not intended for use in potentially explosive atmospheres and is not insulated against coming into contact with electric power. 4. Make sure there are no electrical cables, gas pipes, etc., that can cause a hazard if damaged by use of the tool. Safety precautions for dust and fume hazards 1. Dust and fumes generated when using assembly power tools for threaded fasteners can cause ill health (for example, cancer, birth defects, asthma and/or dermatitis); risk assessment and implementation of appropriate controls for these hazards are essential. 2. Risk assessment should include dust created by the use of the tool and the potential for disturbing existing dust. 3. Direct the exhaust so as to minimize disturbance of dust in a dust-filled environment. 4. Where dust or fumes are created, the priority shall be to control them at the point of emission. 5. All integral features or accessories for the collection, extraction or suppression of airborne dust or fumes should be correctly used and maintained in accordance with the manufacturer's instructions. 6. Use respiratory protection in accordance with employer's instructions and as required by occupational health and safety regulations. Safety precautions for noise hazards 1. Unprotected exposure to high noise levels can cause permanent, disabling, hearing loss and other problems, such as tinnitus (ringing, buzzing, whistling or humming in the ears). 2. Risk assessment and implementation of appropriate controls for these hazards are essential. 3. Appropriate controls to reduce the risk may include actions such as damping materials to prevent workpieces from “ringing”. 4. Use hearing protection in accordance with employer's instructions and as required by occupational health and safety regulations. 5. Operate and maintain the assembly power tool for threaded fasteners as recommended in the instruction handbook, to prevent an unnecessary increase in noise levels. 6. If the assembly power tool for threaded fasteners has a silencer, always ensure it is in place and in good working order when the assembly power tool for threaded fasteners is operating. 7. Select, maintain and replace the consumable/inserted tool as recommended in the instruction handbook, to prevent an unnecessary increase in noise. Safety precautions for vibration hazards 1. 2. 3. 4. Exposure to vibration can cause disabling damage to the nerves and blood supply of the hands and arms. Keep the hands away from the sockets. Wear warm clothing when working in cold conditions and keep your hands warm and dry. If you experience numbness, tingling, pain or whitening of the skin in your fingers or hands, stop using the assembly power tool for threaded fasteners, tell your employer and consult a physician. 5. Operate and maintain the assembly power tool for threaded fasteners as recommended in the instruction handbook, to prevent an unnecessary increase in vibration levels. 6. Do not use worn or ill-fitting sockets or extensions, as this is likely to cause a substantial increase in vibration. 7. Select, maintain and replace the consumable/inserted tool as recommended in the instruction handbook, to prevent an unnecessary increase in vibration levels. 8. Sleeve fittings should be used where practicable. 9. Support the weight of the tool in a stand, tensioner or balancer, if possible. 10. Hold the tool with a light but safe grip, taking account of the required hand reaction forces, because the risk from vibration is generally greater when the grip force is higher. Additional safety instructions for pneumatic power tools 1. Always shut off air supply, drain hose of air pressure and disconnect tool from air supply when not in use, before changing accessories or when making repairs. 2. Never direct air at yourself or anyone else. 3. Whipping hoses can cause severe injury. Always check for damaged or loose hoses and fittings. 4. Cold air shall be directed away from the hands. 5. Do not use quick-disconnect couplings at tool inlet for impact and air-hydraulic impulse wrenches. Use hardened steel (or material with comparable shock resistance) threaded hose fittings. 6. Whenever universal twist couplings (claw couplings) are used, lock pins shall be installed and whipcheck safety cables shall be used to safeguard against possible hose-to-tool and hose-and-hose connection failure. 7. Do not exceed the maximum air pressure stated on the tool. 8. For torque-control and continuous-rotation tools, the air pressure has a safety critical effect on performance. Therefore, requirements for length and diameter of the hose shall be specified. 9. Never carry an air tool by the hose. 2 General preparation and connection: 1. 2. 3. 4. 5. 6. 7. When using brand-new air hose or air pipe. Blow and clean the inside of air hose or pipe before installation. Keep inside of air hose or air pipe clean to prevent airdrop problem caused by the lots of drain and dust accumulated and possibly make the inside diameter smaller in the long use. Before connecting the air hose, apply 4 to 5 drops of SAE#10-20 spindle oil at the air inlet. Also, every 3 to 4 hours of operation, oiling is necessary. Twist Teflon thread tape to ensure a proper seal air inlet. Then tighten the air coupler into air tool. The supplied compressed air must be clean and dry, with the appropriate oil mist. Use an air treatment unit; filter, regulator and lubricator. Please refer Fig.1 illustration shows the correct mode of connection to the air supply system which will increase the efficiency and useful life of the tool. The quick connect coupling and hose must have sufficient air flow capacity. We recommend an air hose with a diameter of 10mm (3/8”). To ensure a good performance. The operation pressure at the compressed air inlet should not exceed 6.2bar (90psi) (unless indicated otherwise). Higher operating pressures may cause damaged or excessive wear. Operating pressures below 5.3bar may cause pressure or power loss. Risk of injury 1. 2. 3. 4. 5. 6. Compressed air can inflict serious injuries. Therefore never point the air hose at another person or yourself. Shut – off the air supply and disconnect the tool in case: ➢ You want to change or replace accessories. ➢ You want to clean, repair or maintain the tool. ➢ The tool is not going to use for some times. Check compressed air hose before use. If it is damaged, broken, torn, or deformed, the hose is not to be connected to the tool. Always check the pneumatic couplings before using the tool. If they show signs of damage, fracture, cracking or excessive corrosion, the respective tool or the air hose is not to be used. Use only qualified adapters and connectors, In case of wear they are to be replaced immediately. Only use air pipes that are fit for the use at maximum pressure. Maintenance instruction: 1. Dry the filter (fig1) and the air inlet of the tool. 2. Lubricate the quick connect coupling to prevent blocking. 3. Air tool require lubrication throughout the life of the tool. The air motor and bearing uses compressed air to start the tool. The moisture in compressed air will rust the air motor; you must lubricate the motor daily. 4. Avoid storing the tool in a location subject to high humidity. If the tool is left as it is used, the residual moisture inside the tool can cause rust. 5. Before storage, lubricate tool and run it for a few seconds. 6. Regular inspection of spindles, threads, and clamping devices in respect of wear and tolerances for location of abrasive products. 7. If the tool is too seriously damage to be used anymore, recycle raw material instead of disposing as waste. The machine, accessories and packaging should be sorted for environmental-friendly recycling. Check with your local authority or retailer for recycling advice. 3 IMPACT WRENCH-I-2013-04A
advertisement
Key Features
- 1400 ft-lb maximum torque for demanding tasks
- Twin-hammer mechanism for increased power and efficiency
- 4000 r/min free speed for fast and effortless operation
- 3/8" air inlet and 1/4" capacity bolt size for compatibility with various accessories
- Durable construction and comfortable handle for extended use
- Lightweight at 13.6 lbs for easy handling
- Forward and reverse rotation for versatility
Related manuals
Frequently Answers and Questions
What is the maximum torque output of the ST-5596?
1400 ft-lb
What is the free speed of the ST-5596?
4000 r/min
What size air hose is required for the ST-5596?
3/8" (10 mm)
What is the recommended air pressure for the ST-5596?
90 psi (6.3 bar)
What is the maximum bolt size that the ST-5596 can handle?
1-1/4" (M32)
Does the ST-5596 have a forward and reverse rotation?
Yes
What is the net weight of the ST-5596?
13.6 lbs (6.2 kg)
advertisement