- Industrial & lab equipment
- Measuring, testing & control
- Spirax Sarco
- UltraSonic Leak Detector LD-1
- Installation and Maintenance Instructions
Spirax Sarco UltraSonic Leak Detector LD-1 Installation and Maintenance Instructions
Add to my manuals
10 Pages
Spirax Sarco UltraSonic Leak Detector LD-1 is a sophisticated ultrasonic inspection system for locating steam trap issues, compressed air and vacuum leaks, refrigerant anomalies, evaluating valves and bearings, and predicting equipment failures. Its advanced digital controls and displays provide accurate and consistent readings. It features separate airborne and touchprobe sensors for versatility, adjustable volume and sensitivity, and a peak hold function for easy leak pinpointing. The LD-1 is powered by a 9V battery and comes with a headset for private listening.
advertisement
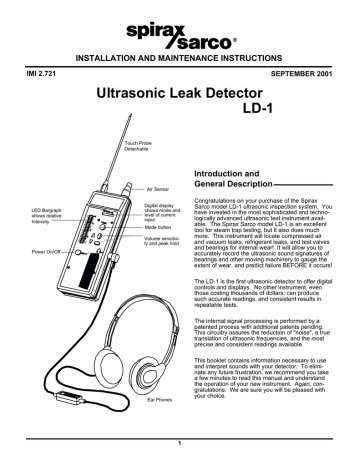
IMI 2.721
INSTALLATION AND MAINTENANCE INSTRUCTIONS
SEPTEMBER 2001
Ultrasonic Leak Detector
LD-1
LED Bargraph shows relative
Intensity
Power On/Off
Touch Probe
Detachable
Air Sensor
Digital display shows mode and level of current input
Mode button
Volume sensitivity and peak hold
Introduction and
General Description
Congratulations on your purchase of the Spirax
Sarco model LD-1 ultrasonic inspection system. You have invested in the most sophisticated and technologically advanced ultrasonic test instrument available. The Spirax Sarco model LD-1 is an excellent tool for steam trap testing, but it also does much more. This instrument will locate compressed air and vacuum leaks, refrigerant leaks, and test valves and bearings for internal wear! It will allow you to accurately record the ultrasonic sound signatures of bearings and other moving machinery to gauge the extent of wear, and predict failure BEFORE it occurs!
The LD-1 is the first ultrasonic detector to offer digital controls and displays. No other instrument, even those costing thousands of dollars, can produce such accurate readings, and consistent results in repeatable tests.
The internal signal processing is performed by a patented process with additional patents pending.
This circuitry assures the reduction of "noise", a true translation of ultrasonic frequencies, and the most precise and consistent readings available.
This booklet contains information necessary to use and interpret sounds with your detector. To eliminate any future frustration, we recommend you take a few minutes to read this manual and understand the operation of your new instrument. Again, congratulations. We are sure you will be pleased with your choice.
Ear Phones
1
Physical Description
The following describes the various controls, adjustments and features of the LD-1.
D
C
B
A
I H G
F
E
A. Airborne sensor: Detects external ultrasonic sound which travels through air vibration. Examples... pressurized gas leaks, vacuum leaks, external system noises. The sensor horn accepts various waveguides and attachments.
B. Touchprobe sensor: Detects internal system sounds. Examples... internal valve leaks, bearing wear, faulty steam traps.
C. Intensity display meter: Shows relative strength of detected signal in a bargraph format.
D. Power button: Turns the instrument on or off.
E. Alphanumeric Display (A.N.D.): Level/Mode Indicator, Displays active mode, current mode setting, and numeric intensity reading. Available mode options include; Air, Probe, Display, Volume, Sensitivity. This display also indicates when battery power is low (Display will read “Batt”).
F. Mode Select Button: Scrolls through mode options to be adjusted and/or selected.
G. UP Adjustment (
▲
): Increases setting or scrolls through options in a particular mode.
H. Down Adjustment (
▼
): Decreases setting or scrolls through options in a particular mode.
I. Headphone Jack: Insert Headphone connector.
2
Battery Installation
There is a sliding battery door located on the back of the LD-1.
Turn the unit over so that the controls are facing the floor, and the sensor is facing away from your body.
At the opposite end from the sensors (the end closest to you) there is a sliding panel.
Apply minimal pressure to the center of the panel and slide it towards you exposing the battery compartment.
Install a new 9 volt battery noting the (+) and (-) positions which are indicated on the inner label.
If the display reads “Batt”, replace the battery.
Getting Started
OK, here it is. A quick overview of the Spirax Sarco
LD-1 written for those who will probably read nothing else. This will give you a basic understanding of the units operation and function, however we STRONG-
LY recommend that you read the complete manual.
Or, at the very least, continue to read the following section concerning the principles of operation.
Leak Detection
Use the airborne sensor for detecting pressurized gas leaks and vacuum leaks. Remember, leaks must be turbulent to detect ultrasonically.
1. Insert the headset jack into the plug on the side of the instrument (I.), and push the power button (D.).
2. Depress the mode select button (F.) until the alphanumeric display (A.N.D.) reads "AIR", then press the "
▲
" or "
▼
" to activate the airborne sensor
(A.). You will begin to hear a translation of any ultrasonic sound present in the test area, and the LED bargraph meter will display the strength of the corresponding signal. The highest LED will hold its place for 5 seconds before resetting its position. This will help guide you toward the leak, where the sound is most intense. The instrument always resets itself so that sensitivity is the active mode. If the LED bargraph meter is at maximum, reduce the sensitivity by simply pressing "
▼
" until it reads "10" or less, then continue. The A.N.D. will show the sensitivity as a digit between 0 and 255 prefixed by the letter "A" which identifies the airborne sensor being adjusted.
3. To adjust the volume, press the mode button once. The A.N.D reads "VOL". Then use the "
▲
" and "
▼
" buttons to make the adjustment. The alphanumeric display will read "V 000". Volume, as with all numerical values, has a range of 0 to 255.
4. Listen for the leak. A gas leak will sound like a harsh rushing noise, or high intensity hiss. This sound will increase as the instrument is drawn toward the leak point, and will clearly disappear as the sensor is turned away.
5. For more detailed information on specific applications, refer to page 8 of this manual.
BATTERY POWER NOTICE
Congratulations on the purchase of your new ultrasonic detector! This detector uses advanced digital technology and stores all instrument settings in its memory. The unit can be turned off and on again without having to reconfigure settings. In order to maintain this memory, the unit draws a small amount of battery power while in the off position.
If your instrument is to be stored for several days, or weeks between uses, you should remove the battery when stored to conserve battery power.
After installing a battery, it is important to turn the instrument on and off again. This resets the internal settings of the microprocessor.
Touchprobe Applications
Use the touchprobe to detect internally generated ultrasound. These applications include... steam traps, valves, and bearings.
1. Insert the metal touchprobe into its port (B.) on the nose of the LD-1. The probe should be snug so it can not rattle, however, do not overtighten.
Depress the mode select button (F.) until the display reads "Prob", then press the "
▲
" or "
▼
" to activate the touchprobe sensor.
2. Making a firm contact, touch the tip of the probe to the item being tested. Apply just enough pressure to make a good contact. You will hear a clear translation of the internally generated ultrasonic sound.
3. Listen for fluid leaks in valves, continuous flow or non-cycling in steam traps, and knocking or scraping in bearings.
4. The LD-1 always defaults back to Sensitivity as the active mode, therefore if your readings are off the scale simply press the "
▼
" to reduce the reading to within the range of the instrument. The
A.N.D. will display the active sensor and current sensitivity setting before it begins to make the adjustments.
5. To adjust the volume, press the mode button once. The A.N.D. reads "VOL". Then use the
"
▲
" and "
▼
" buttons to make the adjustment.
The alphanumeric display (A.N.D.) will read
"V000". Volume, as with all numerical values, has a range of 0 to 255.
6. When testing bearings or machinery vibration, record your sensitivity setting, and use the reading on the A.N.D. as a baseline for future readings. Now you can compare the wear patterns to future tests, and other similar equipment.
7. For more specific information on using the touchprobe, refer to page 5 of this manual.
WARNING: To insure a good contact, and accurate readings the touchprobe is sharp! Be careful not to injure yourself or others!
3
Principle of Operation
The principle of operation of the LD-1 is based on the turbulent flow of fluids and gases. Turbulent flow has a high content of ultrasound. This is sound which is above the human hearing range, but can be heard with the LD-1, and traced to its source.
Imagine air leaking from a tire. Because this is such a large leak, your ear can detect this sound, however your ear hears only about 1/3 of the actual spectrum of sound which exists. The sound of small leaks is mostly ultrasonic which your ear can not detect.
It is important to remember this example... A piece of straight tubing connected to a gas supply and left free to exhaust into the atmosphere will not generate sound if the volume of gas through it is such that turbulence does not take place.
Yet for that same flow, an opening as small as
0.005 of an inch could generate enough sound to be heard several feet away.
For a leak to happen there must be an opening in the system that carries a gas or fluid. Normally, these openings are not clean smooth holes, but passages through cracks with many jagged edges and internal chambers. Fluid or gas escaping through an "orifice" like this, is forced into turbulence, random circularlike motions. Inside a tube where a gas may be flowing, the flow is normally laminar which means that a given layer of gas does not mix with layers above it or below it. This condition happens in a straight long tube when the velocity of the fluid is not high. A gas leaking out of a straight and long tube will not generate as much sound as if it were leaking out of a small crack because the flow is not turbulent.
The intensity of sound generated at a leak is a very complex function of the viscosity, the temperature, the speed the fluid is moving, the Raynolds number, the pressure differential across the leak, and the physical dimensions and characteristics of the orifice. This is why it is possible for a smaller leak to generate more sound than a larger one.
What this all means...
The LD-1 detects ultrasound NOT refrigerant or the presence of a specific gas. It is NOT a sniffer.
Because of this fact, the LD-1 can function in areas where heavy wind or a concentration of fumes renders other detectors useless.
The unique touchprobe system in the LD-1, is an excellent means for detecting turbulent internal flow in situations such as leaks in valves, steam traps, and pump cavitation.
WARNING: Ultrasonic detectors will not indicate a leak if there is no turbulent flow producing sound when you check it. If you suspect a toxic gas, natural gas, or other combustible gas leak, and do not detect it with the LD-1, do not assume that it does not exist as it may not be turbulent.
Use another method as verification that there is no leaking gas present.
Operation
To use the system, plug the headphones into the jack on the right side of the instrument ( I ).
Depress the "on/off" button (D.) once to turn the unit on (depress it again to turn the unit off).
Depending on whether you are in contact or airborne mode, you will immediately begin to hear the translated ultrasonic signal from either the airborne sensor
(A.), or the touchprobe sensor (B.).
Using the Modes
The LD-1 uses a simple method of select and adjust.
Press the "Mode" button to select the parameter you wish to change, then use the Up and Down arrows
(G. & H.) to make the adjustment. The LD-1 offers modes in the following order...
Volume
➞
Display
➞
Air
➞
Probe
➞
Oper.
("
▲
" and "
▼
") ("
▲
" or "
▼
" to active) (Continuous,
Peak Hold, or Off)
Setting the Sensitivity:
The LD-1 always defaults back to sensitivity as the active mode. This means that after any other adjustment has been made, it will hold the setting in memory, and reset itself so that "
▲
" and "
▼
" adjust sensitivity.
Pressing the "
▲
" and "
▼
" arrows will adjust the sensitivity while in either the Airborne or Touchprobe mode. The prefix on the A.N.D. indicates the active mode being changed. For example, the display will read "A 000" to show that you are adjusting the airborne sensors sensitivity, or "P 000" to indicate that you are adjusting the sensitivity of the touchprobe sensor.
Setting the Volume:
While using either the Airborne or Touchprobe mode, pressing the "MODE" button once will put the LD-1 in the Volume Adjust Mode. The alphanumeric display will read "Vol" as long as the MODE button is pressed. When released it will show "V000" indicating the current volume setting. Use the "
▲
" and "
▼
" buttons to make the adjustment. You will hear the volume change as the display changes from "V 000" to "V 255" (the "V" prefix indicates that volume is the current mode being adjusted).
Note: Volume and sensitivity are not the same.
Volume adjusts the loudness of the signal in the headset. Sensitivity adjusts the meters reaction to the incoming signal.
Selecting the Sensor:
Press the "MODE" button three times. The alphanumeric display will read "Air". The instrument will wait
3 seconds after releasing the MODE button for you to press the "
▲
" or "
▼
" button which locks in the sensor selection. If you press the "MODE" button again, the alphanumeric display will read "Prb", and wait 3 seconds for you to press the "
▲
" or "
▼
" button to lock in Probe as your sensor selection.
4
Adjusting the Display:
The alphanumeric display offers three viewing options. Continuous, Peak, and Off. Press the
"MODE" button twice. The display will read "Disp".
Then by pressing the "
▲
" or "
▼
" buttons it will scroll through the display options which are as follows...
"Cont" = Continuous, the A.N.D. will show the level of the signal in real time. "Peak" = Peak Hold, the
A.N.D. will hold the highest reading for 5 seconds.
"Off" = Turns the alphanumeric display off (with the exception of the "-"). Since this display is not necessary for most airborne applications, turning it off can save a substantial amount of battery.
NOTE: The adjustments you have just made are now in memory, and will remain there until they are changed or if the battery is removed.
"Hidden" MODE Options
There are other features that the "MODE" button can be used for.
1. Checking the serial #... While the unit is powered OFF, hold down the "MODE" button. Now turn the unit on while holding down the "MODE" button. The LD-1 will show its serial number in the alphanumeric display.
2. Calibration... The instrument is field calibratable when a calibrator is purchased. There is detailed operational information available by pressing certain combinations of buttons.
OTHER IMPORTANT TIPS
This unit offers BOTH sensitivity AND volume adustments. By adjusting these two parameters independantly, you can “zoom” into signals more effectively in the presence of background noise interference.
If you can see the meter reacting to signals but cannot hear anything, you need to go into the “VOL” mode to increase the volume. Remember there is also a volume limiter on the headset. Be sure this is set high enough to hear the signal.
If you can hear a signal, but see no indication on the meter you may ust need to increase the sensitivity. If the signal gets too loud in the headset, turn down the volume either on the instrument, or on the headset adjustment.
If the bargraph meter is working, but you only see a dash on the alphanumeric display, it means that display is turned off. Go into “disp” mode and change its setting.
For details on adjusting the modes, review the
“Operation” section of the manual.
5
Applications Overview
Touchprobe Applications
(Internal sounds, bearings, valves, steam traps).
Ultrasound not only travels through air but solid materials as well. The touchprobe sensor (B.) is used to detect abnormal system sounds which are internally generated. Such sounds include abnormal flow in piping, valves, and steam traps. Other applications include the detection of friction or increased wear in bearings, motors and gears.
Warning: To insure a good contact, and accurate readings the touchprobe is sharp! Be careful not to injure yourself or others!
The Test:
To test steam traps you will use the touchprobe sensor (B.). Press the "MODE" button (F.) until the display reads "Prbe", then press "
▲
" or "
▼
" to activate the touchprobe sensor.
Making a firm contact, touch the end of the probe to the steam trap being tested. Apply just enough pressure to make a good contact, but do not push too hard! You will hear a clear translation of the internally generated ultrasonic sound. If the trap sounds appear to be masked by other system sounds, reduce the sensitivity, and touch just upstream and downstream from the trap to verify that what you hear is only the steam trap being tested.
1. Before testing any trap, the following information should be determined so readings from the unit can be properly interpreted:
A. Type of Trap (Thermo-Dynamic, Inverted
Bucket, Thermostatic, etc.)
B. Working Steam Pressure (15, 30, 150 psi, etc.)
C . Trap Application Type and expected condensate load. (Main Drip, tracer, radiator, process, etc.)
Knowing the above, you will be able to predict the type and sound level that you should be receiving and will help to set sensitivity level.
Practice to gain testing skills on both good and leaking traps used in your plant. You will find that condensate flow produces less ultrasound than does steam leaking through a trap orifice.
Crackling or sputtering flow is associated with condensate flashing in the low pressure area downstream of the orifice. Leaking steam or gas generates a constant amount of ultrasound but there will always be some condensate mixed in.
2 . Trap types: All traps should be checked with probe firmly touching the trap outlet area or pipe. Readings must not be taken while the probe is moving.
A . T h e r m o - D y n a m i c : The disc trap has a blast dis-
charge and cycles on and off. The ultrasonic tester will give a 0, then 100% reading on this trap so low sensitivity setting is normally recommended. A properly sized trap in good working order will discharge between 1-10 cycles/minute. A trap which operates 20 or more cycles/minute should be inspected for dirt or wear. A continuous discharge means the trap is either severely worn, is subject to high back pressure, or dirt is preventing the disc from closing off.
B. Inverted Bucket: The discharge pattern is usually
semi-cyclical. On medium to heavy loads, the trap will have a definite on/off cycle. The ultrasonic tester reading will be a sweeping motion, back and forth. Light loads will change the discharge pattern to a modulating low flow and the ultrasonic tester will give a low continuous reading. When the trap is malfunctioning, the sonic readout will be a full 100% reading for blowthrough and an erratic on/off type operation for lost prime failure.
C. Float & Thermostatic: The discharge pattern of
this trap is a continuously modulating flow. We must first determine the type of application; process or light load condition. If the condensate load is light such as found on main drips and tracers, sound levels would be normally low and would give a low level continuous readout. A high readout would mean that some part of the trap has failed. When testing, be aware that this type of trap has
t w o
orifices; the main orifice located below the normal condensate level, and the thermostatic air vent at the top in the steam s p a c e .
In normal operation on process equipment such as heat exchangers and air handlers, the flow will be continuous and at a high sound level. For the ultrasonic test to be accurate, the load must be removed or lightened to allow the trap to shut or throttle back considerably.
Readings should be compared at high and low loads. To reduce the load, the air flow on a coil should be shut off; on a heat exchanger, the liquid flow turned off or a blowdown valve before the trap opened to reduce the load. In any case, the trap should shut off or throttle back to a point where a good test can be made. When load has been reduced or cut off, the ultrasound reading should be very low or at zero level if the orifice is tightly closed.
D . Thermostatic/Radiator Trap: These traps are often
on low pressure and the usual discharge pattern is a dribbling type action. The load on convectors and radiators is normally low and should give a very low or zero readout when the unit is on and operating.
Since thermostatic traps are wide open when cold, the trap can be tested for both opening and closing by turning off the steam supply to the trap and allowing the trap to cool. When trap is cool, open steam valve while sonic probe is on trap outlet. Trap discharge should start wide open, then quickly shut.
This test proves full function of the trap and should be used if normal test proves inconclusive.
E . Thermostatic/General Purpose Trap: E l e m e n t
design and filling contained will vary, but generally this trap dribbles on light load and modulates on heavy loads but can also cycle on/off. Main drips and tracers where loads are light should give a low readout and cycle on/off. On most process use, the trap will tend to modulate or sometimes cycle.
For testing, the same procedure given above for process on Float & Thermostatic traps should be used. Closing the trap off and letting it cool will open the valve fully. When turning the trap back on, the trap will blast full open, the trap should shut down within a minute’s time. The ultrasonic tester will be able to indicate both full flow and shutoff condition. This method should be used if the reading that is normally given off by the trap is unclear as to whether it is good or leaking steam.
F . Bimetallic Trap: Bimetal traps do not respond to
load change as fast as other types and the discharge pattern is normally modulating and tends to dribble. Bimetal traps are usually found on drips, tracers and light load applications, so discharge would normally be continuous with a low sound level. Draining condensate ahead of the trap should shut it off, and ultrasound levels should drop to zero.
Bearings and Moving Machinery
The most common mechanical failure is a broken or seized bearing. However this type of failure normally does not happen instantly. When the bearing begins to fail, the sound that it makes changes. These changes occur in the ultrasonic range and can be detected with the LD-1 by touching the bearing housing with the touchprobe and listening for abnormal sounds. Periodic preventive maintenance tests can prevent major disasters in both the machinery and down time.
Note: Large industrial processing plants check criti-
cal moving machinery (bearings) on a routine basis.
Many firms have spent tens of thousands of dollars on vibration analysis instrumentation to help detect these hidden problems. Because of its high frequency capabilities many other companies use ultrasonic detection as an alternative, or even a complement to this equipment.
While vibration analyzers work in the lower Hertz frequency range, the LD-1 detects sound in the kilohertz range which is much higher. When a bearing begins to fail, changes occur in the ultrasonic (kilohertz) range before they can be detected with traditional vibration monitoring equipment.
Bearings... The First Test
The first test is very important! This is the reading that all future tests will be based on.
With some experience you will be able to compare two similar bearings and identify the sound of a good bearing from a worn one by just using your ear.
When several months pass between tests, however, it is very important to log your results.
To take a reading on a mechanical system, such as a bearing or gear box, you must use the touchprobe attachment. Touch the end of the probe to the outer housing of the gear box or bearing, making a good contact. Do not press very hard at any given point when collecting data. Use just enough force to keep the tip of the probe in place, and try to be consistent with the amount of pressure you use. It is often effective to use only the weight of the LD-1 itself to hold the tip in place.
6
Adjust the sensitivity so that the intensity meter reads less than half. This gives you room on the display for future readings.
As the bearing wears the ultrasonic sound intensity will increase. Future readings can indicate the extent of this wear.
When testing a bearing or other moving machinery it is important to ...
1. Record your volume and sensitivity settings.
2. Record the level on the alphanumeric display.
3. Record or mark the test point where the level was taken.
By recording these things you have the most accurate and repeatable test possible. Although the sound of a moving machine member may fluctuate, the LD-1’s built in peak hold feature will allow you to assign a number to the sound level emanating from the item being tested. Use this number to compare to future tests.
Charting your results
Ultrasound will be produced differently for all types of systems. It may be strong on one side of a bearing shaft, and weak on the other, depending upon the unique wear patterns. Therefore it is very important to mark the test point, so that future readings can be taken from the exact same position. Doing the same test with the sensitivity set differently can completely change the results, therefore it is extremely important to keep track of the instruments settings for future tests to be valid.
Keep this information in your files, or tagged on the equipment itself. When returning to the same equipment, perhaps several months or even years later, you have the information you need to make a decision as to the degree of wear in a particular piece of equipment.
It is worth while to show this information to your customers. Letting them know what is going on will help build your reputation, credibility, and make you more profits in the process. Maintenance agreements are much easier to sell when they include LD-1 testing.
More scheduled repairs and less emergency repairs keeps your business under control, as well as your clients temper.
Vibration
Vibration, misalignment, or moving machinery which is not properly balanced can be deadly to a system.
These things can cause leaks, and excessive wear bringing the life of any system to an early demise.
All these problems have a common warning signal; increased ultrasonic energy. This ultrasonic energy is generated from the friction associated with these problems, and can be detected with the LD-1. With experience, you will know what readings are good, and which are bad for the most common types of equipment you work on.
Example: If you are responsible for maintaining the
A/C units in a large residential area such as an apartment complex, where all residences use the same cooling unit. After testing a sample of compressors, you soon will be able to easily determine what readings are normal or abnormal for a particular model.
Reminder: To insure success be consistent... If you
test compressor mounts, for example, test the same place, at the same sensitivity setting.
It is a good idea (although not necessary) to test units when they are new, and keep your own records of what is acceptable for a new piece of equipment.
You may want to show your customers the measures you take to insure an accurate indication of the health of their system. The customer should also be happy to know that this test will show the early warning signs of system failure.
See the previous page on Charting your results.
WARNING
Be careful when working around rotating machinery.
The headphones will dampen much of the sound which may cause you to forget that the machine is moving. Use care, common sense, and be alert at all times. Make certain the cord from the headphones is out of the way of any moving machine member.
7
Other Applications
Use your imagination. The LD-1 is probably one of the most versatile test instruments you can own.
Keep in mind that ultrasonic sound is generally produced by Friction, Arcing, and Turbulence (F A T).
Therefore any pressurized gas, moving machine, or electrical system can be tested.
Electrical Arcing
A jump in electrical current or Arc, will make a popping, frying, or buzzing noise in the ultrasonic range.
The LD-1 can be used to locate electrical failures which are causing a decline in power quality. Use to test circuit breakers, buss bars, relays, corrosion in contacts, or poor insulation.
Warning
Be careful, and use common sense around electrical currents. Keep in mind the nose of the LD-1 is metal, use the plastic waveguide, and keep at a safe distance!
Fan Belts
You may be familiar with the sound of a loose fan belt in a car. Early warning of such wear is indicated by a similar sound in the ultrasonic range.
Ductwork
Leaking ducts can be a significant source of energy loss. The LD-1 can be used to identify the sound of air leaking from a pressurized duct system.
Pneumatics and Hydraulics
Leaks are quite common in pneumatic systems (controls, hoses, tools, fittings). Listen for the rushing sound of the leak!
Large hydraulic leaks are obviously easy to see, but small ones can often be difficult. The LD-1 will allow you to hear these leaks with ease! Internal leaks in hydraulic cylinders can be detected using the touchprobe. When testing for external hydraulic leaks use the yellow waveguide to protect any fluid from entering the sensor.
Applications Overview
1. Airborne Applications (External sounds)
The Airborne sensor (A.) is used to detect soundwaves which travel to the LD-1 through the air. The most common airborne application is for leak detection.
External Leaks
When searching for leaks with the LD-1, remember you are listening for the turbulent flow of the gas as it exits the leak orifice (refer back to "Principles of
Operation" for a more detailed explanation). The LD-
1 is capable of hearing leaks from over fifty feet away, but it is best to hold the instrument as close to the test area as safely possible.
Stand a few feet from the suspected leak area, and reduce the sensitivity until only the first one or two lights are lit on the LED bargraph meter. Check around fittings, flanges and all other suspected areas. If at anytime the display is at maximum due to background noise in the area, reduce the sensitivity
(and volume if necessary) and continue searching.
The sound in the headset, and the bar graph meter will increase as the unit is drawn closer to the leak.
Using the yellow flexible waveguide will help reduce background noise interference and also make the units sensitivity more directional allowing you to pinpoint the precise location of the leak.
In the case of larger leaks which may over concentrate "sniffer" type leak detectors. Try removing the waveguide and increasing the sensitivity. Then sweep the instrument over the entire unit. Leaks may be where you least suspect them, and the LD-1 may very likely detect something even from a greater distance.
Too Much Background Noise???
The LD-1 detects a narrow band of ultrasonic sound, therefore although there may appear to be overwhelming background noise, the sound may not be within the detection range of the LD-1. Notice that you can yell directly into the sensor and your voice will not be translated in the headset.
The LD-1’s patented circuitry is capable of reproducing the sound signature of the signal it detects. This means that the sound you hear is closely related to the actual sound. It is an actual translation, not an electronically synthesized tone, or "beep".
Leaks sound like a "hiss" or rushing sound, while compressors "chatter" a rhythmical mechanical pattern. Fans should not produce any wind noise detectable by the LD-1, although the fan motor may produce a "buzz" or "hum".
Example: Mechanical vibrations sound very different from leak sounds. Shake a set of keys, then take a short quick breath through your nose. Listening to both sounds through the LD-1 is a good example of how the direct translation process of the LD-1 helps you to distinguish the difference between the two signals.
Practice listening to different components of your system, this will help you to identify the sound of a leak from other normal operational sounds.
8
Methods of reducing background noise interference.
Placing the flexible wave guide onto the airborne sensor will make the reception of the LD-1 more directional. This helps shield the sensor from competing sounds entering from other directions. Cupping your hand around the end of the wave guide will also help to reduce the background noise.
Reducing the sensitivity will suppress the effect background noise has on the display, and also in the headset. This will help make the leak sound more identifiable.
The most interfering background sounds come from areas of high turbulence within a pipe. This can be where high velocity flow changes direction, or is restricted such as within a partially closed valve.
These situations will produce a high frequency hiss which is very similar to the sound of the leak. Use the standard methods for reducing background noise. If you are still unsuccessful, shut the system down.
Although the pressure may be somewhat reduced, it should still be sufficient for leak testing.
Recording overall system noise.
Use the LD-1 to record sound levels of compressor noise, fan vibration, fan belts, motors, and even noisy ducts.
The overall sound level of a system can be recorded and compared to previous and future readings. If a system owner is complaining about increased noise coming from certain equipment, this can be verified if previous LD-1 readings were taken.
Although the LD-1 will only record the ultrasonic range of a noisy system, this part of the sound will increase in proportion to the sonic part the customer is hearing and complaining about.
Taking a baseline reading.
When taking a reading of overall noise level, begin by reducing the sensitivity until the bargraph reads slightly less than 1/2, (approximately 6). This will give you room on the display for future readings.
IMPORTANT: Record the sensitivity and volume set-
ting, the numeric level reading on the display (E.), and the position from which the reading was taken. This will be your baseline for future tests.
Care and Service
The LD-1 is constructed of durable, impact resistant
ABS, however it is also a precision electronic test instrument which should be handled with care and respect. We suggest you follow these simple instructions to insure many years of reliable performance.
• If you find yourself working in damp areas or the instrument is exposed to oils, or chemical agents that corrode, make sure that you wipe it clean with a soft cloth and window cleaner. Be very gentle around the front of the instrument so that the sensor is not damaged. Periodically, use an automotive polish on the case to bring back its original luster.
• Keep both sensor openings free of dirt, oils, moisture, or any other foreign substances. Use the yellow waveguide to protect the airborne sensor when using the unit in harsh environments.
• When performing touchprobe applications, do not use excessive pressure on the item being tested.
Bent probes or cracked sensor housings are considered abuse, and will not be covered under warranty.
• Keep the instrument stored in its protective carrying case when not in use.
• Your LD-1 comes with a high quality, industrial grade 9volt battery. However, all batteries have the possibility of leaks. Remove the battery if the unit is not to be used for longer periods of time.
Calibration
The LD-1 detector was designed in a way to minimize the need for regular calibrations. It is constructed with components of very tight tolerances, and do not age rapidly. If there is a need to know for sure that the instrument is consistent with manufacturer specifications, or if you suspect a problem, we will perform the calibration at a fixed cost. Call the factory for current calibration costs.
If you need service, return the instrument, postage
paid and insured, to:
Spirax Sarco
1150 Northpoint Blvd.
Blythewood, SC 29016
(803) 714-2000
Please include your name, company name, return address, and a brief note describing the problem.
9
Warranty & Service Repair
The LD-1 is warranted for 1 year to be free of manufacturing defects adversely affecting performance, and unconditionally for 30 days. Should an instrument fail within the 1 year warranty period, the unit will be repaired or replaced provided in the opinion of the factory, the instrument has not been tampered with or abused.
If defective, return to the factory for repair and re-calibration. Maximum liability of Spirax Sarco shall be limited to replacement of unsatisfactory product.
Recommendations and product information are believed to be accurate, but the furnishing of it does not constitute the making of a good process warranty of Seller.
Spirax Sarco warrants that this product conforms to the Product Description contained in this literature.
Spirax Sarco makes no other warranty, whether expressed or implied, including warranties of merchantability or of fitness for a particular purpose or application. No statements or recommendations contained herein are to be construed as inducements to infringe any relevant patent, now or hereafter in existence. Spirax Sarco neither assumes nor authorizes any representatives or other person to assume for it any obligation of liability other than such as expressly set forth herein.
Under no circumstances shall Spirax Sarco be liable for incidental, consequential or other damages from any alleged negligence, breach of warranty, strict liability or any other theory, arising out of the use or handling of this product.
If a fresh battery does not cure a failure, carefully pack the instrument and contact Spirax Sarco
Returned Material Department for shipping instructions.
For any additional information you may require, contact:
Spirax Sarco Applications Engineering Department
Toll Free 1-800-833-3246
SPIRAX SARCO, INC. • 1150 NORTHPOINT BLVD. • BLYTHEWOOD, SC 29016
PHONE 803-714-2000 • FAX 803-714-2200
advertisement
* Your assessment is very important for improving the workof artificial intelligence, which forms the content of this project
Related manuals
advertisement