advertisement
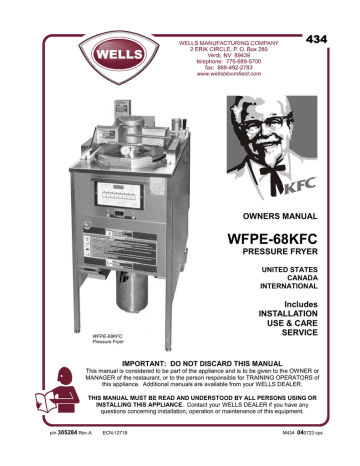
434
OWNERS MANUAL
WFPE-68KFC
PRESSURE FRYER
UNITED STATES
CANADA
INTERNATIONAL
Includes
INSTALLATION
USE & CARE
SERVICE
WFPE-68KFC
Pressure Fryer
IMPORTANT: DO NOT DISCARD THIS MANUAL
This manual is considered to be part of the appliance and is to be given to the OWNER or
MANAGER of the restaurant, or to the person responsible for TRAINING OPERATORS of this appliance. Additional manuals are available from your WELLS DEALER.
THIS MANUAL MUST BE READ AND UNDERSTOOD BY ALL PERSONS USING OR
INSTALLING THIS APPLIANCE. Contact your WELLS DEALER if you have any questions concerning installation, operation or maintenance of this equipment. p/n 305284 Rev.A ECN-12718 M434 04 0723 cps
LIMITED WARRANTY STATEMENT
GLOBAL WARRANTY STATEMENT for:
YUM! Restaurants International and YUM Brands Inc.
This WFPE-68KFC Pressure Fryer manufactured by Wells
Manufacturing Company exclusively for KFC is warranted against defects in materials and workmanship for a period of
two years from the date of original installation, except that; a. With respect to electronic controller, this material and
labor is limited to only one year after installation.
THE FOREGOING OBLIGATION IS EXPRESSLY GIVEN
IN LIEU OF ANY OTHER WARRANTIES, EXPRESSED OR
IMPLIED, INCLUDING ANY IMPLIED WARRANTY OF
MERCHANTABILITY OR FITNESS FOR A PARTICULAR
PURPOSE, WHICH ARE HEREBY EXCLUDED.
WELLS MANUFACTURING COMPANY, A DIVISION OF
CARRIER COMMERCIAL REFRIGERATION INC., SHALL
NOT BE LIABLE FOR INDIRECT, INCIDENTAL OR
CONSEQUENTIAL DAMAGES OR LOSSES FROM ANY
CAUSE WHATSOEVER.
This warranty is void if it is determined that upon inspection by an authorized service agency that the equipment has been modified, misused, misapplied, improperly installed, or damaged in transit or by fire, flood or act of God. It also does not apply if the serial nameplate has been removed or service is performed by unauthorized personnel. The prices charged by Wells for its products are based upon the limitations in this warranty. Seller’s obligation under this warranty is limited to the repair of defects without charge by
Wells’ factory authorized service agency or one of its sub-agencies. In addition to restrictions contained in this warranty, specific limitations are shown in the Service Policy and Procedure Guide. Please consult your classified telephone directory, your foodservice equipment dealer or for information and other details concerning warranty write to:
Service Parts Department
Wells Manufacturing Company
P.O. Box 280
Verdi, NV 89439
Phone (775) 689-5700 Fax: (775) 345-0569
SERVICE POLICY AND PROCEDURE GUIDE
ADDITIONAL WARRANTY EXCLUSIONS
1. Resetting the safety thermostats, circuit breakers, overload protector or fuse replacements unless warranted conditions are the cause.
2. All problems due to operation at voltages other than specified on equipment nameplates – conversion to correct voltage and phase are the customer’s responsibility.
3. All problems due to electrical connections not made in accordance with electrical code requirements and wiring diagrams supplied with the equipment.
4. Calibration of heat controls after the first sixty (60) days on original components. Replacement of items subject to normal wear to include such items as: knobs, light bulbs, baskets, grids, mechanical timers and thermocouples. Normal maintenance functions including lubrication, adjustments of airflow, thermostats, door mechanisms, microswitches, burners and pilot burners and replacement of fuses and indicating lights are not covered by warranty.
5. All fry pot welded in the field.
6.
Deterioration of aluminum vessels due to insertion of food product or use of abrasive cleaners not covered by warranty.
7. Full use, care and maintenance instructions are supplied with each machine. Those miscellaneous adjustments noted are customer responsibility. Proper attention will prolong the life of the machine.
8. Travel mileage is limited to sixty (60) miles from an
Authorized Service Agency or one of its sub-agencies.
9. All labor shall be performed during regular working hours. Overtime premium will be charged to the buyer.
10. All genuine Wells replacement parts are warranted for ninety (90) days from the date of purchase on nonwarranty equipment. This parts warranty is limited only to replacement of the defective part. Any use of non-
genuine Wells parts completely voids any warranty.
11. Installation, labor and job checkouts are not considered warranty.
12. Charges incurred by delays, waiting time or operating
restrictions that hinder the service technicians’ ability to
perform service are not covered by warranty.
This includes institutional and correctional facilities.
SHIPPING DAMAGE CLAIM PROCEDURE
NOTE: For your protection, please note that equipment in this shipment was carefully inspected and packaged by skilled personnel before leaving the factory. Upon acceptance of this shipment, the transportation company assumes full responsibility for its safe delivery.
IF SHIPMENT ARRIVES DAMAGED:
1.
VISIBLE LOSS OR DAMAGE: Be certain that any visible loss or damage is noted on the freight bill or express receipt, and that the note of loss or damage is signed by the delivery person.
2.
FILE CLAIM FOR DAMAGE IMMEDIATELY:
Regardless of the extent of the damage.
3.
CONCEALED LOSS OR DAMAGE: if damage is
unnoticed until the merchandise is unpacked, notify the
transportation company or carrier immediately, and file
“CONCEALED DAMAGE” claim with them. This
should be done within fifteen (15) days from the date
the delivery was made to you. Be sure to retain the
container for inspection.
Wells Manufacturing cannot assume liability for damage or loss incurred in transit. We will, however, at your request, supply you with the necessary documents to support your claim. xi
TABLE OF CONTENTS
GENERAL
WARRANTY xi
SPECIFICATIONS 1
FEATURES & OPERATING CONTROLS 2
AGENCY LISTING INFORMATION 3
PRECAUTIONS & GENERAL INFORMATION 4
INSTALLATION
UNPACKING, INSPECTION and SET-UP 6
ELECTRICAL INSTALLATION 7
USE AND CARE
FRYER OPERATION 8
CLEANING INSTRUCTIONS 11
SERVICE & REPAIR
TROUBLESHOOTING SUGGESTIONS 16
EXPLODED VIEWS & PARTS LIST 18
WIRING DIAGRAM 20
SERVICING INSTRUCTIONS 23
PARTS & SERVICE INFORMATION 33
CUSTOMER SERVICE DATA 33
Thank you for purchasing this
Wells Manufacturing Co.
Pressure Fryer
Proper installation, professional operation and consistent maintenance of this appliance will ensure that it gives you the very best performance and a long, economical service life.
This manual contains the information needed to properly install the fryer, to use and care for the fryer, and to service and repair the fryer in a manner which will ensure its optimum performance.
SPECIFICATIONS
MODEL
VOLTS
50/60 Hz
WATTS
AMPS 3ø
L1 L2 L3 N
AMPS
1ø
POWER SUPPLY
REQUIREMENTS
WFPE-68KFC
208V 3ø
240V
1ø or 3ø
10,500
10,500
29
25
29
25
29
25 n/a
ELECTRICAL n/a n/a
44
3-WIRE (L1, L2, L3) plus GND
Dedicated 50 amp 3ø circuit
8 ga. copper min. 90ºC
380-415V
3ø
10,500 14.6 14.6 14.6 0 n/a
1.5 mm
2
3 NAC
(L1, L2, L3, N) plus GND
Dedicated 25 amp 3ø circuit
copper min. 90ºC
IMPORTANT: This appliance must be installed in compliance with all applicable federal, state and
local codes and ordinances.
DIMENSIONS
Height: 38" (top of work surface)
47" (overall)
52-1/2" (top of operating lever swing)
Width: 20"
Depth: 33"
35-1/4" (including operating lever)
1
FEATURES & OPERATING CONTROLS
Fig. 1 Features and Operating Controls
2
FEATURES & OPERATING CONTROLS (continued)
Fig. 2 Electronic Controller
Fig. 3 Accessories and Tools
AGENCY LISTING INFORMATION
This appliance conforms to NSF Standard 4 for sanitation only if installed in accordance with the supplied Installation Instructions.
This appliance is and Listed under E6070.
STD 4
E6070 E6070
3
PRECAUTIONS AND GENERAL INFORMATION
DANGER:
BURN
HAZARD
Contact with hot shortening will cause severe injury or death. Wear protective gloves and clothing when operating or servicing this fryer.
DANGER:
BURN
HAZARD
Do not attempt to open the fryer lid until the pressure in the frypot has fallen to zero.
Opening the lid prematurely will result in the explosive release of hot shortening.
Contact with hot shortening will cause severe injury or death.
DANGER:
BURN
HAZARD
Do not attempt to open the fryer drain valve if the frypot is under pressure.
Opening the drain valve under pressure will result in the explosive release of hot shortening.
Contact with hot shortening will cause severe injury or death.
DANGER:
EXPLOSION
HAZARD
Failure to operate this pressure fryer as described in this manual can lead to explosion, severe injury and/ or death.
SAFE OPERATION OF THE PRESSURE FRYER
Contact with hot shortening will cause severe injury to unprotected skin and eyes. Extensive exposure to hot shortening can cause death.
Protect yourself from contact with hot shortening:
ALWAYS wear protective clothing when operating this pressure
fryer.
ALWAYS wear protective goggles, gloves and apron when
cleaning or servicing this pressure fryer.
Shortening under pressure can be very hazardous unless handled properly:
DO NOT attempt to operate this fryer without the LID O-RING and
COLLECTOR O-RING properly installed.
Do not operate this fryer if either of the LID O-RING or
COLLECTOR O-RING are damaged. A damaged O-ring will lead
to shortening leaks and/or spraying shortening.
Be sure the LID is seated in the frypot and the OPERATING
LEVER is turned fully COUNTERCLOCKWISE before starting a
cook cycle.
DO NOT attempt to turn the OPERATING LEVER until the
pressure in the frypot has fallen to zero.
DO NOT open the drain valve if the frypot is under pressure.
Opening the lid or drain valve with the fryer under pressure will
result in the explosive release of hot shortening.
Spilled shortening will cause a slip and fall hazard:
Add shortening, replenish the shortening, and service the fryer
carefully to avoid spills.
Clean up shortening spills promptly to avoid creating a slip and fall
hazard.
DO NOT allow water to contaminate the shortening. Water will
boil violently on contact with hot shortening, causing the hot
shortening to splatter.
DO NOT heat water in the fryer
DO NOT use boil-out method to clean the frypot.
DO NOT clean the frypot with water, water spray or steam
spray.
DO NOT use steel wool to clean any part of the fryer.
4
PRECAUTIONS AND GENERAL INFORMATION (continued)
WFPE-68KFC Pressure Fryer is intended for use in commercial establishments only.
This fryer is designed to prepare food for human consumption. No other use is recommended or authorized by the manufacturer or its agents. precautions, limitations and associated restrictions.
Operating instructions, warnings and labels must be read and understood by all persons using or installing this appliance.
Cleanliness of this fryer is essential to good sanitation. Read and follow all included cleaning instructions and schedules to ensure the safety of the food product.
DO NOT operate the fryer with faulty, loose or missing components.
DO NOT operate this fryer if the control panel is torn or damaged.
Contact a Wells Authorized Service Agent for repairs.
Disconnect this appliance from electrical power before performing any maintenance or servicing.
DO NOT pour water on, into or over any control, control panel or wiring.
DO NOT store flammable or combustible items (mops, paper, rags or chemicals) in, on or near the fryer.
This appliance is not jet-stream approved. Do not direct any water or steam jet at any part of this appliance. Do not use a jet stream to wash under the appliance.
The fryer is NOT a ladder. Never stand on the fryer to clean hood filters. Pull the fryer away from the wall and use a step stool or ladder.
DO NOT stand on, sit on or lean on the fryer.
DO NOT allow foreign objects such as closed containers, cigarette lighters or aerosol cans near the fryer or hot shortening. If dropped in hot shortening, such objects may explode.
DO NOT allow any foreign object near the fryer that can fall into the frypot and cause splashing or splattering of hot shortening.
Any procedure which requires the use of tools must be performed by a qualified technician.
This manual is considered to be a permanent part of the appliance.
This manual and all supplied instructions, diagrams, schematics, parts breakdown illustrations, notices and labels must remain with the appliance if it is sold or moved to another location.
This appliance is made in the USA. Unless otherwise noted, this appliance has American sizes on all hardware.
WARNING:
BURN
HAZARD
Do not attempt to operate this fryer without the LID O-RING properly installed.
Do not operate this fryer if the
LID O-RING or COLLECTOR
O-RING are damaged.
Hot oil may be released.
WARNING:
ELECTRIC
SHOCK HAZARD
All servicing requiring access to non-insulated electrical components must be performed by a factory authorized technician.
Do not open any access panel which requires the use of tools. Failure to follow this warning can result in severe electrical shock.
CAUTION:
Risk of
Damage
DO NOT connect or energize this appliance until all installation instructions are read and followed. Damage to the appliance will result if these instructions are not followed.
IMPORTANT:
The technical content of this manual, including any troubleshooting suggestions, parts breakdown illustrations, wiring diagrams, schematics, servicing instructions and/ or adjustment procedures, is intended for use by qualified technical
personnel only.
5
INSTALLATION
NOTE: DO NOT discard the carton or other packing materials until you have inspected the appliance for hidden damage and tested it for proper operation.
Refer to SHIPPING DAMAGE
CLAIM PROCEDURE on the inside front cover of this manual.
WARNING:
Risk of personal injury
Installation procedures must be performed by a qualified technician with full knowledge of all applicable electrical codes. Failure can result in personal injury and property damage.
UNPACKING & INSPECTION
Carefully remove the appliance from the carton. Remove all protective plastic film, packing materials and accessories from the appliance before connecting electrical power or otherwise performing any installation procedure.
Carefully read all instructions in this manual and the Installation
Instruction Sheet packed with the appliance before starting any installation.
Read all instructions in this manual carefully before starting installation of this fryer. READ AND UNDERSTAND ALL LABELS AND
DIAGRAMS ATTACHED TO THE FRYER.
Carefully account for all components and accessories before discarding packing materials.
1 ea Fryer Basket
1 ea Condensate Tray
1 ea Basket Drain Hook/Collector Lifting Tool
1 ea Frypot Stirring Tool
1 ea Collector
1 ea Displacement Tool
1 ea Cleaning Brush
2 ea Lid O-Ring
2 ea Collector O-Ring
1 ea Heat Transfer Plate
Store these components in a convenient place for later use:
SETUP
Verify that this fryer installation is in compliance with the specifications listed in this manual and with local code requirements. THIS IS THE
RESPONSIBILITY OF THE INSTALLER.
Setup the fryer only on a firm, level, non-combustible surface. Verify local codes for requirements. Concrete, tile, terrazzo or metal surfaces are recommended. Metal over combustible material may not meet code for non-combustible surfaces.
Verify that the unit sits firmly ON BOTH LEGS AND BOTH WHEELS.
With a spirit level, check that the appliance is level front-to-back and side-to-side. With the adjustable legs, adjust as required to level the appliance. Both legs must be adjusted to firmly contact the floor in order to prevent tipping.
Some locations require the fryer to be secured to prevent tipping or rolling. It is the responsibility of the installer to meet this requirement.
DO NOT store flammable or combustible items (mops, paper, rags or chemicals) in, on or near the fryer.
6
INSTALLATION (continued)
ELECTRICAL INSTALLATION
Refer to the nameplate on the appliance to verify the ELECTRICAL
SERVICE POWER. Voltage and phase must match the nameplate specifications, and available electrical service amperage must meet or exceed the specifications listed on page 1. Incoming wiring must comply with National Electrical Code or International specifications.
UNITED STATES & CANADA
This appliance requires a dedicated 50 amp, 3-phase circuit. Wiring must be at least 8 ga. copper suitable for a minimum of 90ºC. Wiring must be installed with a suitable strain relief (provided by electrical contactor).
INTERNATIONAL
This appliance requires a dedicated 25 amp, 3-phase circuit (L1, L2,
L3, N plus ground). Wiring must be at least 1.5 mm
2
copper suitable for a minimum of 90ºC. Wiring must be installed with a suitable strain relief (provided by electrical contactor).
Remove the RIGHT SIDE PANEL. Route supply wiring from the
FEED-THRU on the lower rear panel, then to the terminal block.
Incoming electrical supply is connected to the L1, L2 and L3 (and N for international) terminals of the TERMINAL BLOCK.
The chassis-mounted GROUND LUG must be connected to earth ground.
Verify that all connections are tight.
CAUTION:
SHOCK HAZARD
Removal of any exterior panel will result in exposed electrical circuits. Electrical connection must be performed by a
qualified technician only.
Use care whenever working around exposed electrical circuits.
IMPORTANT:
Contact a licensed electrician to install and connect electrical power to the fryer.
IMPORTANT:
Damage due to being connected to the wrong voltage or phase is NOT covered by warranty.
CAUTION:
SHOCK HAZARD
Failure to connect the chassis ground to a suitable earth ground will result in a potential shock hazard.
Fig. 4 Terminal Block Location and Wiring
7
OPERATION
DANGER:
BURN
HAZARD
Contact with hot shortening will cause severe injury or death. Wear protective gloves and clothing when operating this fryer.
CAUTION
SHOCK HAZARD
If you experience an electrical shock from the fryer:
IMMEDIATELY disconnect the fryer at the circuit breaker and contact an
AUTHORIZED WELLS
SERVICE AGENT for repairs.
GENERAL GUIDELINES
ALWAYS be sure the pressure gauge reads "0" before turning the operating lever clockwise.
ALWAYS be sure the
LID O-RING is in good condition and properly installed.
*IMPORTANT:
Collector MUST be Wellstype collector with collapsible handle welded to the bottom.
ALWAYS be sure the
COLLECTOR O-RING is in good condition and properly installed.
DAILY START-UP
Remove the DEAD WEIGHT COVER.
Verify that the DEAD WEIGHT is in place
and that the vent holes are clean and free
from obstructions. Be sure the gasket is in
position, then latch the cover in place.
Be sure the EXHAUST VENT is free from
obstructions.
Open the FRYPOT LID. Turn the operating lever fully clockwise.
Slide pivot tube forward until it drops into the indents in the rods.
Slide the lid and yoke assembly to the rear until the lid pivot is in
the pivot tube.
Using the LID HANDLE, lift the front of the lid and yoke until it
rests on the REAR SUPPORT in the raised position.
Lubricate a freshly cleaned LID O-RING with a thin coating of
vegetable oil, then install the o-ring in the groove in the lid. Set the
lid and yoke assembly back onto the glides.
Lift the pivot tube slightly and slide it to the rear of the fryer.
Be sure the frypot is clean, and all breading and crumbs have been
brushed from between the heating elements.
Lubricate a freshly cleaned COLLECTOR O-RING with a thin
coating of vegetable oil, then install the o-ring in the groove in the
COLLECTOR*. Fully insert the COLLECTOR ASSEMBLY into the
opening in the bottom of the FRYPOT. DO NOT install the HEAT
TRANSFER PLATE at this time.
Check the DRAIN VALVE.
Make sure the valve is fully
closed.
Be sure the CONDENSATE TRAY
is empty and properly installed.
8
ADD SHORTENING
Pack 68 lbs (31 kg) of solid shortening into the
frypot. If using liquid shortening, fill frypot to
LOWER OIL LEVEL line. Be sure the heating
elements are completely covered with shortening.
Connect the fryer to electric power by turning on
the circuit breaker. Press the POWER SWITCH
ON. The POWER LIGHT will glow.
Press EXIT COOL, then press 2, 4 or 6-head
MENU KEY (first product to be cooked) The
digital readout will display "LO" while the fryer is
in the shortening melt cycle.
With the FRYPOT STIRRING TOOL, stir the
shortening. Push the stirring tool through the
shortening to the bottom of the collector as the
shortening heats, until all shortening is melted.
Be sure the heating elements are covered with
shortening at all times. Stir until all shortening
is melted.
All shortening in the collector must be completely
melted. Stir into the collector until all shortening is
visibly melted, and at least 5 minutes thereafter.
Using the hook of the BASKET/COLLECTOR
REMOVAL TOOL, lower the HEAT TRANSFER
PLATE into the bottom of the collector.
When the digital readout displays droP, and the
HEAT LIGHT begins to cycle, check the shortening level.
The level must be up to the UPPER OIL LEVEL line scribed into
the frypot above the elements.
Add shortening if necessary.
If overfilled, dip out excess shortening using a saucepan. Use
the excess shortening later as add-back.
Stir the shortening in the frypot thoroughly at least once before
cooking. Do not stir the collector once the heat transfer plate is in
place.
LOAD FRYER BASKET
Using established procedures,
load the FRYER BASKET.
Suspend the fryer basket over the
frypot using the BASKET DRAIN
HOOK.
OPERATION (continued)
DANGER:
BURN
HAZARD
Contact with hot shortening will cause severe injury or death. Wear protective gloves and clothing when operating this fryer.
CAUTION:
FIRE HAZARD,
EQUIPMENT
DAMAGE
The heating elements must be covered with shortening before the fryer is energized, and at all times during the shortening melt cycle and fryer operation. Serious equipment damage and possible fire will result if the elements are dry-fired.
GENERAL GUIDELINES
ALWAYS be sure the drain valve is closed before filling the frypot.
ALWAYS check the fryer leveling before operating.
Shortening should be at the same distance from the rim all the way around the frypot.
ALWAYS use the basket drain hook to raise / lower the fryer basket into / out of the frypot.
ALWAYS use two hands to manipulate the drain hook.
9
OPERATION (continued)
DANGER:
BURN
HAZARD
Contact with hot shortening will cause severe injury or death. Wear protective gloves and clothing when operating this fryer.
CAUTION:
FIRE HAZARD
EQUIPMENT
DAMAGE
The heating elements must be covered with shortening before the fryer is energized, and at all times during the shortening melt cycle and fryer operation. Serious equipment damage and possible fire will result if the elements are dryfired.
To cancel a cook cycle, press and hold the active menu key for 3 seconds.
GENERAL GUIDELINES
ALWAYS be sure the lid o-ring is in place before closing the frypot cover.
ALWAYS be sure the operating lever is turned fully counterclockwise before starting a cook cycle.
ALWAYS be sure the pressure gauge reads "0" before turning the operating lever clockwise.
ALWAYS use the basket drain hook to raise / lower the fryer basket into / out of the frypot.
ALWAYS use two hands to manipulate the drain hook.
FRYER OPERATION
Press the EXIT COOL key. When the digital readout displays
droP, lower the fryer basket into the frypot. Lower slowly to avoid
foaming. Remove and properly store the drain hook.
Slide the lid and yoke forward. When it is over the frypot, turn the
operating lever fully counterclockwise. This lowers the lid into the
frypot.
Press the desired menu (2, 4 or 6 head) key. The active menu
indicator will glow. And the timer will count down the cook time.
While there is pressure in the frypot, the operating lever is locked in
the down position.
Pressure will build during the cook cycle. At the end of the cook
cycle, pressure in the frypot is released, the audible signal sounds,
and the digital display reads donE.
When the pressure gauge drops to zero, raise the lid by turning the
operating lever counterclockwise (which releases the lid lock), then
fully clockwise to raise the lid.
Slide the lid and yoke assembly toward the rear until it clears the
frypot. Using the basket drain hook, lift the fryer basket out of the
frypot and hook on the front edge of the fryer frame. Suspend the
fryer basket over the frypot to drain.
Once drained, remove basket with drain hook. Product is ready for
any additional processing prior to serving.
10
CLEANING INSTRUCTIONS
PROCEDURE: Cleaning During Operation
PRECAUTIONS: Wear protective goggles, gloves, and apron
FREQUENCY: As required, approximately every 3 - 6 loads
TOOLS: Frypot Stirring Tool
Hi-Temperature Brush
Breading will build up at the oil line. This breading must be removed from the cooking zone to prevent leaving burned specks on product.
Also, the elements must be kept free of breading crumbs and other cooking debris to ensure optimum operation.
1. Remove the fryer basket from the fryer. Using the blade of the
FRYPOT STIRRING TOOL, scrape the built-up breading from the
oil line.
2.
Using a hi-temperature brush, brush all breading and other cooking debris from the face of the heating elements, and from between the elements, element retainers and the frypot.
IMPORTANT: Be careful when cleaning around the temperature
probe and hi-limit thermobulb. Damage to either component will
put the fryer out of service.
3. Using a hi-temperature brush, push all breading and crumbs into
the collector.
4. Check the shortening level. Add shortening as required to bring the
level between the MIN OIL and MAX OIL lines.
5. Using the FRYPOT STIRRING TOOL, stir the frypot until all
shortening is melted. DO NOT stir into the collector.
6. Raise LID AND YOKE assembly (see page 8). Clean bottom of lid
then carefully return lid & yoke to horizontal position.
7. Check CONDENSATE TRAY. Empty if necessary and reinstall.
8. Properly store tools.
Procedure is complete
DANGER:
BURN
HAZARD
Contact with hot shortening will cause severe injury or death. Wear protective gloves and clothing when cleaning this fryer during operation.
Clean Breading from Oil Line
Clean Heating Elements
11
CLEANING INSTRUCTIONS (continued)
DANGER:
BURN
HAZARD
Contact with hot shortening will cause severe injury or death. Wear protective gloves and clothing when changing shortening.
FRYER MUST NOT BE
PRESSURIZED WHEN
PERFORMING THIS
PROCEDURE
CAUTION:
BURN HAZARD
Open the valve slowly to avoid splashing hot shortening.
CAUTION:
BURN HAZARD
The drained shortening and the container are hot and can cause burns.
CAUTION:
SLIPPING
HAZARD
Avoid spilling shortening on the floor. Clean up all spills immediately to prevent creating a slip and fall hazard.
IMPORTANT:
The displacement tool is to be used to force shortening up to the drain opening.
DO NOT use the displacement tool to bail or transport shortening.
PROCEDURE: Drain or Replace Shortening
PRECAUTIONS: Disconnect fryer from electric power
Wear protective goggles, gloves, and apron
FREQUENCY: As required, shortening to be filtered or replaced
TOOLS: Basket / Collector Tool, Displacement Tool
Container for Shortening
1.
Disconnect fryer from electric power.
Frypot lid must be in the open position.
Remove fryer basket from fryer.
2. Position an appropriate container or
approved shortening filtration system
under the drain valve. Open the drain
valve and drain frypot shortening into
the container.
3. Using the BASKET / COLLECTOR TOOL, remove the HEAT
TRANSFER PLATE from the COLLECTOR.
4. Using the DISPLACEMENT TOOL, force as much shortening as
possible to drain into the container.
Follow established procedures for handling used shortening.
Empty the collector (see page 13), or clean the fryer (see page 13).
Procedure is complete
12
CLEANING INSTRUCTIONS (continued)
PROCEDURE: Daily Cleaning
PRECAUTIONS: Disconnect fryer from electric power
Drain shortening. Allow fryer to cool
Wear protective goggles, gloves, and apron
FREQUENCY: Daily
TOOLS: Basket / Collector Tool, Frypot Stirring Tool,
Clean Cloth or Sponge, Nylon Brush
1.
Disconnect fryer from electric power. Remove fryer basket from fryer. Drain shortening (see page 12).
2. Using the BASKET / COLLECTOR TOOL, lift the
COLLECTOR from the frypot. Empty collector
contents per established procedures. Hold the
collector by the HANDLE on the bottom when
emptying.
3. Place a stockpot under frypot to catch all
breading and oil drips. Using a nylon brush, clean
all breading and crumbs from frypot.
4.
Clean components by wiping with a clean cloth:
DO NOT use caustic cleaners.
DO NOT use steel wool.
DO NOT use soap.
DO NOT spray with water or steam.
Raise LID AND YOKE assembly (see page 8).
Carefully remove LID O-RING, then turn OPERATING LEVER
fully counterclockwise. Clean lid and yoke. Install a freshly
cleaned o-ring before operating fryer. Turn operating lever fully
clockwise.
Clean cabinet and counter top. Do not pour water on, into or over
the control panel.
Set yoke and lid assembly back into the horizontal position.
Disassemble DEAD WEIGHT ASSEMBLY (see page 8). Clean all
internal components, then reassemble.
Remove COLLECTOR O-RING from COLLECTOR. Clean
collector. Install a freshly cleaned o-ring. Set collector back into
frypot.
Empty and clean CONDENSATE TRAY. Reinstall in fryer.
Clean HEAT TRANSFER PLATE. Set aside.
Clean fryer baskets, brushes, collector lifting tool, frypot stirring tool
and displacement tool.
Clean lid and collector o-rings. Store o-rings in a shallow pan of
water in a refrigerator until ready for the next use cycle.
5. Close lid. Properly store tools.
Procedure is complete
DANGER:
BURN
HAZARD
Contact with hot shortening will cause severe injury or death. Wear protective gloves and clothing when cleaning this fryer during operation.
CAUTION:
SLIPPING
HAZARD
Avoid spilling shortening on the floor. Clean up all spills immediately to prevent creating a slip and fall hazard.
CAUTION:
HOT OIL
SPLATTER
HAZARD
DO NOT clean the frypot with commercial boil-out products.
DO NOT clean with water or steam spray. Water will boil violently causing splatter when the shortening reaches temperature.
IMPORTANT:
Clean components with a clean towel or sponge Scrub with a soft bristle brush only if necessary to remove food particles.
NOTE: The following may safely be cleaned in a dishwasher:
Collector, heat transfer plate, fryer basket, condensate tray, tools.
IMPORTANT:
Be sure all components are completely dry. Water will boil violently on contact with hot oil, causing hot oil to splatter.
13
CLEANING INSTRUCTIONS (continued)
DANGER:
BURN
HAZARD
Contact with hot shortening will cause severe injury or death. Wear protective gloves and clothing when cleaning this fryer during operation.
CAUTION:
HOT OIL
SPLATTERING
HAZARD
DO NOT use water to clean lid. Water can contaminate the shortening, causing violent splattering of hot oil.
IMPORTANT:
Yoke and lid assembly weighs approximately 70 lbs.
Use appropriate lifting procedures.
IMPORTANT:
Clean components with a clean towel or sponge Scrub with a soft bristle brush only if necessary to remove food particles.
PROCEDURE: Clean Lid and Yoke Assembly
PRECAUTIONS: Wear protective gloves and apron
Lid Assembly is heavy! Use caution lifting.
FREQUENCY: Weekly or As Needed
TOOLS: Clean Towels or Sponge, Soft Bristle Brush
1. Open the FRYPOT LID. Turn the operating lever fully clockwise.
Slide pivot tube forward until it drops into the indents in the rods.
Slide the lid and yoke assembly to the rear until the lid pivots in the
pivot tube.
Using the LID HANDLE, lift the front of the lid and yoke until it
rests on the REAR SUPPORT.
2.
Remove lid o-ring from groove. Wipe o-ring clean, then store in water in the refrigerator.
3. Wipe bottom of lid until clean. Be sure o-ring groove is clean and
free from shortening build-up.
4. Lower lid to horizontal position. Slide pivot tube fully to the rear.
5. Turn operating lever fully counterclockwise to raise yoke assembly.
Wipe all components until clean. Be sure area at base of piston is
free from shortening build-up.
6. Turn operating lever fully clockwise. Raise lid to vertical position as
in step 1.
7. Lubricate fresh lid o-ring with clean vegetable oil and install in lid
o-ring groove. Lower lid to horizontal position. Slide pivot tube fully
to the rear.
Procedure is complete
14
CLEANING INSTRUCTIONS (continued)
PROCEDURE: Clean Pivot Tube and Slide Rods
PRECAUTIONS: Wear protective gloves and apron
FREQUENCY: Monthly or As Needed
4.
TOOLS: Clean Towels or sponge, Bottle Brush
Flat Blade Screwdriver
1. Lower lid into the frypot. Unlatch and remove dead weight cover.
2. Loosen screws in right and left rod mounting blocks. Work slide
rods to the rear until they are clear of the front mounting blocks.
3.
Free pivot tube from slide rods. Pivot tube may be cleaned in the dishwasher. Use a bottle brush to clean the inside of the pivot tube guides.
Work slide rods out of the rod mounting blocks. Slide rods may be
cleaned in the dishwasher. Scrub with a soft bristle brush only if
necessary to remove food particles from indents.
5. Reinsert slide rods into mounting blocks. Install pivot tube on slide
rods.
6. Reinstall slide rods in front mounting blocks. Tighten screws in rod
mounting blocks. Test pivot rod for proper operation.
Procedure is complete
DANGER:
BURN
HAZARD
Contact with hot shortening will cause severe injury or death. Wear protective gloves and clothing when cleaning this fryer during operation.
NOTE: The following may safely be cleaned in the dishwasher:
Pivot Tube
Slide Rods
IMPORTANT:
Be sure all components are completely dry before reinstalling. Water will boil violently on contact with hot oil, causing hot oil to splatter.
SUGGESTION:
When reinstalling, engage pivot tube guides in slide rod indents prior to tightening screws in order to ensure proper alignment.
15
TROUBLESHOOTING SUGGESTIONS
Problem
No power to fryer
Possible Cause Suggested Remedy
Fryer unplugged or circuit breaker off or tripped
Connect fryer to power
Reset circuit breaker
Power switch off or damaged
Blown fuse
Press power switch to ON
Replace power switch
Correct cause of fuse failure
Replace fuse
Allow to cool, reset safety No power -
"service" light lit
Hi-limit safety tripped
Hi-limit safety trips often Thermobulb contaminated with crumbs Clean hi-limit thermobulb
Temp sensor contaminated with crumbs Clean temperature sensor probe
Temp sensor or wiring damaged Check wiring for damage, repair as req'd.
Replace temperature sensor probe
Hi-limit safety or thermobulb damaged Replace hi-limit safety
Fryer does not heat
"power" light lit
"heat" light lit
"service" light not lit
Fryer does not heat
"power" light lit
"heat" light not lit
"service" light not lit
Fryer will not build pressure
24v relay R1 damaged (welded contacts)
Controller damaged
Replace relay R1
If relay R1 remains energized at all oil temps, replace controller
Wiring damage (elements, contactors) Check wiring for damage, repair as req'd.
Damaged E-Safe relay Replace E-Safe relay
Damaged back-up contactor
Temp sensor or wiring damaged
Relay R3 or wiring damage
24v relay R1 or wiring damaged
24v transformer damaged
Controller damaged
Replace back-up contactor
Check wiring for damage, repair as req'd.
Replace temperature sensor probe
Check wiring for damage, repair as req'd.
Replace relay R3
Replace relay R1
Replace transformer
If no 24v to R1 when calling for heat , replace controller
Insufficient moisture in product
Lid o-ring damaged or missing
Dead weight damaged or dirty
Pressure relief body damaged or dirty
Relief pin bent or dirty
Pressure relief valve damaged
Cook only authorized product
Replace lid o-ring
Clean dead weight, replace if req'd.
Clean pressure relief body, replace if req'd.
Clean relief pin, replace as req'd.
Replace pressure relief valve
Pressure gauge damaged
Solenoid damaged
Connecting link or cotter pin damaged Replace connecting link and cotter pins
Pressure hose damaged Replace pressure hose
24V relay R2 or wiring damaged
Replace pressure gauge
Replace solenoid
Controller damaged
Check wiring for damage, repair as req'd.
Replace relay R1
If no 24v to R2 during pressure phase of cook cycle, replace controller
16
TROUBLESHOOTING SUGGESTIONS (continued)
Problem
Fryer slow to heat / recover
Possible Cause
Heating elements dirty
One or more damaged elements
Controller works only intermittently
Insufficient ventilation
Cooling fan damaged or dirty
Suggested Remedy
Clean elements and frypot
Replace defective heating elements
Be sure area under fryer remains clear
Clean or replace cooling fan
Replace transformer 24v transformer damaged
Damaged controller
Cannot lower lid Pivot tube engaged
Lid not centered over frypot
Lid o-ring not properly installed
If internal temperature and 24v supply OK, replace controller. Be sure cooling fan is operating
Be sure pivot tube is disengaged from pivot bracket at back of lid
Position lid & yoke properly
Properly install o-ring
Cannot raise lid
No reading or incorrect reading on pressure gauge
Piston and/or yoke damaged or dirty
Pressure not bled off
Disassemble, thoroughly clean yoke & lid
Repair or replace as required
Lid cannot be raised until all pressure has been relieved from frypot
Improper procedure for opening
Lid has cocked in frypot
After all pressure has been relieved, turn operating lever fully counterclockwise to release cam pawl, then fully clockwise to raise lid.
Tap front and back of lid while attempting to move operating lever both directions
Properly install o-ring Lid hard to raise or lower Lid o-ring not properly installed
Excess water and grease vented from exhaust
Steam vents from pressure relief cover
Frypot leaks at collector
Piston and/or yoke damaged or dirty
Muffler full of condensate and shortening
Latches not properly engaged
Gasket missing or damaged
Pressure relief cover damaged
Collector o-ring missing or damaged
Collector o-ring improperly installed
Disassemble, thoroughly clean yoke & lid
Repair or replace as required
Remove and clean muffler. Be sure drain line is clear.
Engage extended fingers of latches fully in slots, then turn twist latch handle 180º clockwise
Replace gasket
Replace pressure relief cover
Replace o-ring
Properly install o-ring
Collector damaged Replace collector
Fryer basket will not lower fully into frypot
Excessive built up of crumbs in frypot Clean frypot, empty collector
Bracket for hi-limit thermobulb damaged Repair or replace thermobulb bracket.
Examine thermobulb for damage.
One or more element clamps damaged Repair or replace element clamps
Examine elements for damage
Gauge orifice dirty Remove gauge and clean
Damaged pressure gauge Replace gauge
17
EXPLODED VIEW & PARTS LIST
18
ITEM
1
2
4
5
6
8
9
29
30
31
32
25
26
27
28
33
34
21
22
23
24
17
18
19
20
14
15
16
10
11
12
13
39
40
41
42
35
36
37
38
43
44
45
PART NUMBERS IN <BRACKETS> ARE FOR REFERENCE ONLY
505365
<305203>
<305383>
<305384>
505382
505439
505381
<305254>
505307
506134
<305406>
505308
506152
<305389>
<305398>
<305192>
<305366>
505306
PART NO
505297
506157
506130
506149
506150
506167
506036
505483
505451
505433
505218
<305400>
505972
505289
506158
<305373>
505449
506135
<305174>
<305425>
<305178>
<305164>
505362
505361
505387
505167
<305235>
505426
DESCRIPTION
PROBE, TEMPERATURE
CLAMP, HI-LIMIT THERMOBULB
THERMO, HI-LIMIT SAFETY
ELEMENT, 240V 3500W
ELEMENT, 208V 3500W
CLAMP, HEATING ELEMENT
VALVE, FRYPOT DRAIN
DEAD WEIGHT 9 PSI
DEAD WEIGHT 11 PSI
DEAD WEIGHT 12 PSI
GASKET, DEAD WEIGHT COVER
ASSEMBLY, DEAD WEIGHT CAGE
SUPPORT BLOCK, BASKET HOOK
COVER, DEAD WEIGHT
GLIDE, LID
PISTON, LID
GAUGE, PRESSURE 0-15 PSI
LID
O-RING, LID
CAP, YOKE
CAM PLATE
ASSEMBLY, YOKE
HANDLE, OPERATING LEVER
TUBE, PRESSURE RELIEF VENT
VALVE, PRESSURE RELIEF
ADAPTER, PRESSURE RELIEF VALVE
ASSEMBLY, LID SUPPORT
MOUNTING BLOCK, LEFT
MOUNTING BLOCK, RIGHT
SLIDE ROD
PIVOT TUBE
MOUNTING BLOCK, ROD
ASSEMBLY, EXHAUST VENT
CLAMP, EXHAUST TUBE
TUBE, EXHAUST MUFFLER INLET
TUBE, EXHAUST MUFFLER OUTLET
LID, EXHAUST MUFFLER
GASKET, EXHAUST MUFFLER
MUFFLER, EXHAUST
BRACKET, PIVOT
PIVOT PIN
CLIP, RETAINING
PIN, PRESSURE RELIEF
BUSHING
COVER, MOUNTING BRACKET
SOLENOID, PRESSURE RELIEF
57
58
59
60
61
53
54
55
56
49
50
51
52
ITEM
46
47
48
62
63
83
84
85
75
80
81
82
71
72
73
74
64
65
66
67
86
87
88
90
T1
T2
T3
T5
T6
KIT
EXPLODED VIEW & PARTS LIST (continued)
506080
<306083>
<306082>
506078
<305231>
<305270>
<305212>
<305229>
506183
57780
50131
60310
505413
505309
22888
23080
<306081>
505295
50516
505280
63880
505504
503655
506161
505419
504892
57779
PART NO
<305234>
<305361>
<305388>
<305236>
<48689>
505798
51157
<305227>
54871
54769
<305378>
22891
23079
22887
22885
22886
22892
22943
DESCRIPTION
BRACKET, SOLENOID MOUNTING
PIN, RETAINING
PIVOT ARM
CONNECTING ROD
STRAIN RELIEF, WATER-TIGHT
RELAY, 24V
LIGHT, INDICATING RED
SWITCH, 240V DPST LIGHTED
LIGHT, INDICATING AMBER
CONTROLLER F.A.S.T. EM99
RELAY, 240V
TRANSFORMER, 240V PRI 24V SEC
FAN, 240V
FOOT ADJUSTABLE
CASTER NON-SWIVEL
RELAY, 240V E-SAFE
CONTACTOR 208V
CONTACTOR 240V
TERMINAL BLOCK 3P
TERMINAL BLOCK 4P
ASSEMBLY, COLLECTOR
O-RING, COLLECTOR
HEAT TRANSFER PLATE
TRAY, CONDENSATE
ASSEMBLY, ADAPTER, 1/2 MPT x HOSE
FLEX HOSE
ADAPTER, 1/2 FPT x HOSE FLARE
NIPPLE 1/2MPT CLOSE
SWITCH GUARD
ASSEMBLY, FRAME
PANEL, SIDE
PANEL, FRONT UPPER, CONTROL
PANEL, FRONT LOWER
PANEL, REAR
O-RING, DEAD WEIGHT PIN
SHELF, ELECTRICAL
FUSE, SC-10 10A 300V (pk 4)
FUSE HOLDER, HPG-EE 10A 240V
ASSEMBLY, FRYPOT
BASKET, CHICKEN COOKING 6-HEAD
BASKET, CHICKEN COOKING 4-HEAD
TOOL, DISPLACEMENT
BASKET DRAIN HOOK / COLL. REMOVAL TOOL
TOOL, STIRRING
BRUSH
INCL. ITEMS T2 thru T6
19
WIRING DIAGRAM
20
21
WIRING DIAGRAM (continued)
WIRING DIAGRAM (continued)
22
CABINET COMPONENTS
A. Removable Components
The following major components may be removed without the use
of service tools:
Lid and Yoke Assembly
Condensate Tray
Collector and Heat Transfer Plate (use the Collector Lifting Tool)
Dead Weight Cover and Dead Weight
Remove the Muffler by loosening the four hose clamps that secure
the exhaust tubing. Work the tubing off of the vent tubes, then lift
the muffler out of the cabinet.
B. Access Panels
Remove the following panels by removing two screws at the
bottom, then sliding the panel out of the channel in the frame:
Lower Front Panel
Right Side and Left Side Panels
Upper Rear Panel
After removing the Lower Front Panel, remove two screws at the
bottom of the Upper Front Panel and slide it out of the frame.
Disconnect the controller connectors in the front electrical
compartment.
The Electrical Shelf is held by two screws at the bottom, and slides
out to the limit of the wiring.
SERVICING INSTRUCTIONS
WARNING
Electric Shock
Hazard
Disconnect from electrical power before removing any panel or cover.
CAUTION
BURN
HAZARD
Allow fryer to cool. Be sure all pressure is relieved before proceeding.
TOOLS REQUIRED:
#2 Phillips Screwdriver
Container to hold fasteners
IMPORTANT:
Yoke and lid assembly weighs approximately 70 lbs.
Use appropriate lifting procedures.
23
SERVICING INSTRUCTIONS (continued)
WARNING
Electric Shock
Hazard
Disconnect from electrical power before removing any panel or cover.
CAUTION
BURN
HAZARD
Allow fryer to cool. Be sure all pressure is relieved before proceeding.
TOOLS REQUIRED:
#2 Phillips Screwdriver
Flat blade screwdriver
Container to hold fasteners
CHASSIS ELECTRICAL COMPONENTS
A. Access
Remove RIGHT SIDE PANEL
Remove LOWER FRONT PANEL then UPPER FRONT PANEL.
Note wiring connections to control panel, switches and indicators.
Disconnect wiring and set upper front panel aside.
B. Components
Note location of wiring connections, then disconnect wires from
component. Detach component from chassis.
Reassemble in reverse order
24
SERVICING INSTRUCTIONS (continued)
CONTROL PANEL COMPONENTS
A. Access
Remove LOWER FRONT PANEL. Remove screws holding
UPPER FRONT PANEL to cabinet.
B. Controller
Disconnect two connectors from electrical compartment. Note
orientation of connectors.
Remove two screws holding controller to panel.
C. Indicator Lights
Disconnect wiring from light.
Collapse mounting tabs on light body. Withdraw light through front
of panel.
D. Power Switch
Note position of wires on switch. Disconnect wires.
Collapse mounting tabs on switch body. Withdraw switch with
switch guard through front of panel.
Reassemble in reverse order. Be careful that no wires are pinched when reinstalling upper front panel.
WARNING
Electric Shock
Hazard
Disconnect from electrical power before removing any panel or cover.
TOOLS REQUIRED:
#2 Phillips Screwdriver
Needle Nose Pliers
Container to hold fasteners
25
SERVICING INSTRUCTIONS (continued)
YOKE AND LID ASSEMBLY
CAUTION
BURN
HAZARD
Allow fryer to cool. Be sure all pressure is relieved before proceeding.
TOOLS REQUIRED:
#2 & #3 Phillips Screwdrivers
Flat Blade Screwdriver
Screw Starter
7/16" Box End Wrench or
Hex Socket
1/2" & 1" Open End
Wrenches
Container to hold
Fasteners
IMPORTANT:
Yoke and lid assembly weighs approximately 70 lbs.
Use appropriate lifting procedures.
ASSEMBLY & TORQUE
SPECS:
Piston Assy to Lid
Loctite™246
Lockwasher (35486)
75 in.-lbs
Cam Plate to Piston Assy
Loctite™246
Lockwasher (35486)
75 in.-lbs
A. Access
Turn operating lever fully clockwise. Slide yoke and lid assembly to
the rear until it clears the blocks. Assembly may be lifted off, or
work may be performed in place.
IMPORTANT: Yoke and lid assembly weighs approximately 70 lbs.
Use appropriate lifting procedures.
B. Yoke Assembly
Remove two screws from CAP.
Remove three inside screws/lock washers holding CAM PLATE.
Lift YOKE ASSEMBLY off of LID AND PISTON ASSEMBLY.
Glides: Remove two screws holding glides to yoke.
No other field operations can be performed on the yoke assembly.
C. Lid and Piston Assembly
O-RING may be worked out of the groove in the lid. Lubricate
o-ring with clean vegetable oil before reinstalling.
Remove four screws/lock washers holding piston to lid.
Reassemble in reverse order
Remove four screws holding LID REAR SUPPORT/PIVOT to lid.
Unscrew PRESSURE RELIEF TUBE from PRESSURE RELIEF
VALVE. Unscrew PRESSURE RELIEF and PRESSURE GAUGE
from lid. Unscrew ADAPTER from PRESSURE RELIEF VALVE.
To reinstall, lightly coat male threads with hi-temperature silicone
sealant.
Reassemble in reverse order.
Lubricate cam with food-grade grease before installing cam plate
and cap.
When reassembling lid & piston to yoke, support lid and piston on
a suitable 1" high object to ease installation of cam plate.
Be sure lid is assembled to yoke with the pressure gauge on the
operating lever side.
26
SERVICING INSTRUCTIONS (continued)
MOUNTING BLOCKS AND ASSOCIATED COMPONENTS
A. Access
Turn operating lever fully clockwise and slide lid and yoke assembly
to rear until it clears the blocks. Lift lid and yoke off of fryer.
IMPORTANT: Yoke and lid assembly weighs approximately 70 lbs.
Use appropriate lifting procedures.
Remove LEFT SIDE PANEL, RIGHT SIDE PANEL and UPPER
REAR PANEL.
B. Pivot Tube and Guide Rods
Loosen screws in top of ROD MOUNTING BLOCKS. Slide GUIDE
RODS to the rear. Slide PIVOT ROD forward until it clears the
GUIDE RODS.
To reinstall, be sure guide rods are properly oriented with the flat
ends toward the rear and the locating notch “up”. Pivot tube must
be positioned on the guide rods with the ears “up” and the handle
on the right side. After installation, test pivot rod for smooth
operation, to be sure it locates securely into the notches, and that it
is easily moved from the notches.
C. Mounting Blocks
Remove five bolts from each mounting block. Note that mounting
blocks may be attached with sealant to cabinet top.
To reinstall, be sure mounting blocks are oriented with the smooth
side toward the outside, and the notched upper flange toward the
rear. Apply a thin bead of food-grade silicone sealant to the bottom
of the mounting block before installing.
D. Basket Hook Support Block
Remove two bolts from support block. Note that support block may
be attached with sealant to cabinet top.
To reinstall, be sure support block is oriented with the smooth
side toward the frypot. Apply a thin bead of food-grade silicone
sealant to the bottom of the block before installing.
CAUTION
BURN
HAZARD
Allow fryer to cool. Be sure all pressure is relieved before proceeding.
TOOLS REQUIRED:
3/8" & 3/4" Sockets w/ 4" extension
Container to hold fasteners
Food-Grade Silicone Sealant
IMPORTANT:
Yoke and lid assembly weighs approximately 70 lbs.
Use appropriate lifting procedures.
ASSEMBLY & TORQUE
SPECS:
Mounting Blocks
Loctite™246
80 ft.-lbs
Basket Hook Block
Loctite™246
Lockwasher (37500)
20 ft.-lbs
27
SERVICING INSTRUCTIONS (continued)
WARNING
Electric Shock
Hazard
Disconnect from electrical power before removing any panel or cover.
CAUTION
BURN
HAZARD
Drain oil and allow fryer to cool before proceeding
TOOLS REQUIRED:
#2 Phillips Screwdriver
Assorted open wrenches from 3/8" to 15/16"
Molex™ connector tool
Container to hold fasteners
IMPORTANT:
Tighten fittings only enough to prevent leaks.
Over tightening is not necessary.
ASSEMBLY & TORQUE
SPECS:
Temperature Probe
25 ft.-lbs
Compression Nut
35 ft.-lbs
Hi-Limit Thermostat
25 ft.-lbs
Compression Nut
35 ft.-lbs
Element
Element Clamp
23 in.-lbs
Bulkhead Fitting
30 ft.-lbs
Terminal Nut, Inner
8 in.-lbs
Terminal Nut, Outer
30 in.-lbs
Terminal Locknut
30 in.-lbs
FRYPOT ELECTRICAL COMPONENTS
A. Access
Remove LOWER FRONT PANEL then UPPER FRONT PANEL.
Note wiring connections to control panel, switches and indicators.
Disconnect wiring and set upper front panel aside.
Carefully remove insulation from around frypot electrical terminals.
B. Temperature Probe
Disconnect temperature probe connector. Work pins out of
connector with Molex™ tool.
Remove nut and o-ring (interior of frypot). Withdraw probe and
fitting from frypot.
Remove compression nut and ferrule, then remove probe from
fitting.
Reassemble in reverse order.
Be sure frypot surfaces are clean before reassembly.
Use a fresh fiber washer and o-ring.
Be sure connector pins are fully
seated in connector.
F. REPLACE HI-LIMIT THERMOSTAT
Disconnect wiring from old hi-limit
thermostat.
Remove old hi-limit probe from frypot.
Remove and discard old hi-limit
thermostat and bulkhead fitting.
Mount new hi-limit thermostat bracket
to cabinet. Be sure green ground
wire is attached to one of the bracket
screws.
28
SERVICING INSTRUCTIONS (continued)
FRYPOT ELECTRICAL COMPONENTS (continued)
Clean frypot at bulkhead fitting.
Apply hi-temp sealant around hole
THERMOBULB
for bulkhead fitting.
Slide probe through compression
nut, ferrule and fitting, then insert
probe into frypot.
Slide green fiber washer, belleville
washer (with bell toward frypot) and
nut over probe. Assemble all
components of bulkhead fitting
ELEMENT
CLAMP
APPLY
HI-TEMP
SEALANT
TEMP PROBE
NUT
BELLEVILLE
WASHER
(NOTE: BELL
TOWARD
FRYPOT)
FIBER WASHER
finger-tight.
Push probe back through bulkhead
FITTING
FERRULE
COMPRESSION NUT
fitting until bend in probe contacts
fitting nut.
Gently contour free end of probe to
FRYPOT
match curvature of element.
Assemble clamp approximately
3 inches from free end of probe. Be
sure clamp captures two loops of the element, then tighten screw.
Tighten bulkhead fitting to frypot. Torque to 25 ft-lb.
Tighten compression nut. Torque to 35 ft-lb.
Be sure glass sleeving completely covers exposed portion of probe
on outside of frypot.
Reconnect wiring.
D. Heating Elements
Disassemble hi-limit thermobulb clamp. Carefully position
thermobulb out of the way.
Remove screws from bottom of element clamps, then remove
clamps.
Disconnect wiring from heating elements. Disassemble bulkhead
fittings and withdraw elements from frypot in the following order:
Top heating element
Middle heating element
Bottom heating element
Reassemble in reverse order
Be sure frypot surfaces are clean before reassembly.
Use fresh o-rings.
Be sure ceramic spacer is properly installed before connecting
wiring.
Be sure all three elements are firmly held by the element
clamps.
Be sure hi-limit thermobulb is firmly held by the bulb clamp.
WARNING
Electric Shock
Hazard
Disconnect from electrical power before removing any panel or cover.
CAUTION
BURN
HAZARD
Drain oil and allow fryer to cool before proceeding
TOOLS REQUIRED:
#2 Phillips Screwdriver
Assorted open wrenches from 3/8" to 15/16"
Container to hold fasteners
IMPORTANT:
Tighten fittings only enough to prevent leaks.
Over tightening is not necessary.
Wells recommends that if any element must be replaced, all three elements be replaced at the same time.
29
SERVICING INSTRUCTIONS (continued)
WARNING
Electric Shock
Hazard
Disconnect from electrical power before removing any panel or cover.
CAUTION
BURN
HAZARD
Allow fryer to cool. Be sure all pressure is relieved before proceeding.
TOOLS REQUIRED:
7/16" Nut Driver
1" Open End Wrench
Container to hold fasteners
Food-Grade Silicone Sealant
DEAD WEIGHT ASSEMBLY
A. Access
Remove RIGHT SIDE PANEL, LEFT SIDE PANEL and UPPER
REAR PANEL.
B. Pressure Relief Components
Unlatch DEAD WEIGHT COVER and lift off.
DEAD WEIGHT lifts straight out of the CAGE.
The GASKET may be lifted out of the BODY ASSEMBLY
C. Body Assembly
Remove PIVOT ARM and RELIEF PIN (see page 31).
Disconnect PRESSURE HOSE ASSEMBLY from BODY.
Be careful that the hose does nor twist or kink.
Remove four nuts holding body assembly to cabinet. Remove
body. Note that body may be attached with sealant to cabinet top.
Reassemble in reverse order.
When reinstalling relief pin, do not over tighten retaining plate
screws. Relief pin must be free to drop of its own weight.
Be sure to seal body to cabinet top with a thin bead of food-grade
silicone sealant.
30
SOLENOID AND RELATED COMPONENTS
SERVICING INSTRUCTIONS (continued)
WARNING
Electric Shock
Hazard
Disconnect from electrical power before removing any panel or cover.
TOOLS REQUIRED:
#2 Phillips Screwdriver
Needle Nose Pliers
Container to hold fasteners
A. Access
Remove RIGHT SIDE PANEL and UPPER REAR PANEL.
B. Pivot Arm
Remove cotter pin from lower portion of CONNECTING ROD.
While supporting the assembly, remove four nuts holding PIVOT
ARM and BRACKET to cabinet. Lower carefully. Be sure to
withdraw RELIEF PIN from pressure relief body and store safely.
Remove RETAINING PIN. Withdraw PIVOT. Be sure to capture
PIVOT BUSHING.
C. Solenoid
Remove three screws holding MOUNTING BRACKET COVER to
mounting bracket. Remove cover.
Disconnect wiring from SOLENOID.
Remove cotter pin from upper portion of CONNECTING ROD.
Remove four nuts holding solenoid to mounting bracket. Remove
solenoid from bracket.
Disassemble STRAIN RELIEF from mounting bracket only if
replacing wiring.
Reassemble in reverse order. Replace cotter pins if worn or damaged.
31
SERVICING INSTRUCTIONS (continued)
WARNING
Electric Shock
Hazard
Disconnect from electrical power before removing any panel or cover.
CAUTION
BURN
HAZARD
Allow fryer to cool. Be sure all pressure is relieved before proceeding.
TOOLS REQUIRED:
Flat Blade Screwdriver
7/16" Nut Driver
Container to hold fasteners
Food-Grade Silicone Sealant
MUFFLER COMPONENTS
A. Access
Remove UPPER REAR
PANEL.
B. Exhaust Hoses
Loosen CLAMPS. Work
hose up upper vent fitting
until hose clears vent filling
on muffler. Move end of
hose to the side, then work
hose off of upper fitting.
C. Muffler Assembly
Remove both exhaust hoses
per above, Lift muffler until
drain pipe clears cabinet,
then remove muffler from
cabinet toward rear.
Remove 10 nuts holding lid
to muffler. Remove lid
assembly.
GASKET lifts off.
D. Exhaust Vent
Remove four nuts holding VENT to cabinet. Remove vent. Note
that vent may be attached with sealant to cabinet top.
Reassemble in reverse order. Be sure to seal vent to cabinet top with a thin bead of food-grade silicone sealant.
32
ACCESSORIES & OPTIONAL COMPONENTS
DESCRIPTION PART NO.
BASKET, 6-HEAD 22891
BASKET, 4-HEAD 23079
BASKET DRAIN HOOK/
COLLECTOR REMOVAL TOOL 22885
STIRRING TOOL 22886
DISPLACEMENT TOOL 22887
HEAT TRANSFER PLATE 22888
CLEANING BRUSH 22892
TRAY, CONDENSATE 23080
SELECTED SERVICE PARTS
DESCRIPTION PART NO.
O-RING, LID 506201
O-RING, COLLECTOR 506202
DEADWEIGHT, 9 PSI 505435
DEADWEIGHT, 11 PSI 505451
DEADWEIGHT, 12 PSI 505433
PARTS & SERVICE
IMPORTANT: Use only factory authorized service parts and replacement
filters.
For factory authorized service, or to order factory authorized replacement parts, contact your Wells authorized service agency, or call:
Wells Manufacturing Co.
2 Erik Circle
P. O. Box 280
Verdi, NV 89439 phone: (775) 689-5700 fax: (888) 492-2783
(Service Parts Dept.)
Service Parts Department can supply you with the name and telephone number of the WELLS
AUTHORIZED SERVICE
AGENCY nearest you.
CUSTOMER SERVICE DATA
please have this information available if calling for service
RESTAURANT _____________________________ LOCATION _____________
INSTALLATION DATE ________________________ TECHNICIAN ___________
SERVICE COMPANY ________________________________________________
ADDRESS ___________________________ STATE ______ ZIP__________
TELEPHONE NUMBER (_____)_____-_________
EQUIPMENT MODEL NO. _______________
EQUIPMENT SERIAL NO. _______________
VOLTAGE: (check one) 208 3Ø 240 1Ø 240 3Ø 380-415 3Ø
33
CREATED FOR
BY
advertisement
Related manuals
advertisement