- Home
- Domestic appliances
- Large home appliances
- Water heaters & boilers
- Lennox
- ML193DF045P36B
- User manual
advertisement
▼
Scroll to page 2
of
51
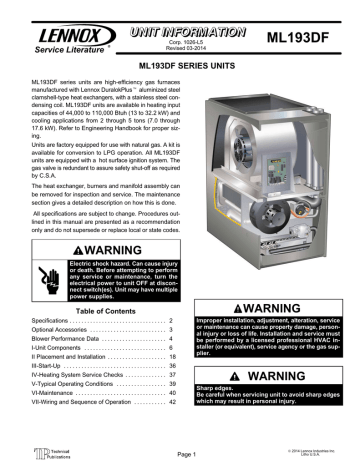
Corp. 1026-L5 Revised 03-2014 Service Literature ML193DF ML193DF SERIES UNITS ML193DF series units are high-efficiency gas furnaces manufactured with Lennox DuralokPlust aluminized steel clamshell-type heat exchangers, with a stainless steel con­ densing coil. ML193DF units are available in heating input capacities of 44,000 to 110,000 Btuh (13 to 32.2 kW) and cooling applications from 2 through 5 tons (7.0 through 17.6 kW). Refer to Engineering Handbook for proper siz­ ing. Units are factory equipped for use with natural gas. A kit is available for conversion to LPG operation. All ML193DF units are equipped with a hot surface ignition system. The gas valve is redundant to assure safety shut-off as required by C.S.A. The heat exchanger, burners and manifold assembly can be removed for inspection and service. The maintenance section gives a detailed description on how this is done. All specifications are subject to change. Procedures out­ lined in this manual are presented as a recommendation only and do not supersede or replace local or state codes. WARNING Electric shock hazard. Can cause injury or death. Before attempting to perform any service or maintenance, turn the electrical power to unit OFF at discon­ nect switch(es). Unit may have multiple power supplies. WARNING Table of Contents Improper installation, adjustment, alteration, service or maintenance can cause property damage, person­ al injury or loss of life. Installation and service must be performed by a licensed professional HVAC in­ staller (or equivalent), service agency or the gas sup­ plier. Specifications . . . . . . . . . . . . . . . . . . . . . . . . . . . . . . . . . 2 Optional Accessories . . . . . . . . . . . . . . . . . . . . . . . . . . 3 Blower Performance Data . . . . . . . . . . . . . . . . . . . . . . 4 I-Unit Components . . . . . . . . . . . . . . . . . . . . . . . . . . . . 6 II Placement and Installation . . . . . . . . . . . . . . . . . . . . 18 III-Start-Up . . . . . . . . . . . . . . . . . . . . . . . . . . . . . . . . . . . 36 WARNING IV-Heating System Service Checks . . . . . . . . . . . . . . 37 V-Typical Operating Conditions . . . . . . . . . . . . . . . . . 39 Sharp edges. Be careful when servicing unit to avoid sharp edges which may result in personal injury. VI-Maintenance . . . . . . . . . . . . . . . . . . . . . . . . . . . . . . . 40 VII-Wiring and Sequence of Operation . . . . . . . . . . . 42 Page 1 © 2014 Lennox Industries Inc. Litho U.S.A. SPECIFICATIONS Gas Heating Performance Model No. ML193DF045P36B ML193DF070P36B ML193DF090P48C ML193DF110P60C 93% 93% 93% 93% Input - Btuh 44,000 66,000 88,000 110,000 Output - Btuh 41,000 61,000 82,000 102,000 Temperature rise range - °F 25 - 55 50 - 80 40 - 70 50 - 80 3.5 / 10.0 3.5 / 10.0 3.5 / 10.0 3.5 / 10.0 High static - in. w.g. 0.50 0.50 0.50 0.50 Intake / Exhaust Pipe (PVC) 2/2 2/2 2/2 2/2 Gas pipe size IPS 1/2 1/2 1/2 1/2 Condensate Drain Trap (PVC pipe) - i.d. 1/2 1/2 1/2 1/2 with field supplied (PVC coupling) - o.d. 3/4 3/4 3/4 3/4 10 x 8 10 x 8 10 x 10 11 ½ x 10 1/3 1/3 1/2 1 Tons of add-on cooling 2.5 - 3 2.5 - 3 3-4 4-5 Air Volume Range - cfm 605 - 1615 560 - 1550 920 - 2145 1210 - 2410 1 AFUE Gas Manifold Pressure (in. w.g.) Nat. Gas / LPG/Propane Connections in. Indoor Blower Wheel nom. dia. x width - in. Motor output - hp Electrical Data Voltage 120 volts - 60 hertz - 1 phase Blower motor full load amps 6.1 6.1 8.2 11.5 Maximum overcurrent protection 15 15 15 15 124 129 147 162 Shipping Data lbs. - 1 package NOTE - Filters and provisions for mounting are not furnished and must be field provided. 1 Annual Fuel Utilization Efficiency based on DOE test procedures and according to FTC labeling regulations. Isolated combustion system rating for non-weatherized furnaces. Page 2 OPTIONAL ACCESSORIES - MUST BE ORDERED EXTRA “B” Width Models “C” Width Models 11M60 11M61 6 ft. 26K68 26K68 24 ft. 26K69 26K69 50 ft. 26K70 26K70 Fiberglass - 1/2 in. x 66 ft. 36G53 36G53 Aluminum foil - 2 in. x 60 ft. 16P89 16P89 51W18 51W18 65W80 65W80 51W07 51W08 (2) 20 x 20 x 1 (2) 20 x 20 x 1 51W03 51W03 71M80 69M29 --- 60L46 44W92 44W92 --- 44W93 CABINET ACCESSORIES Downflow Combustible Flooring Base CONDENSATE DRAIN KITS Condensate Drain Heat Cable Heat Cable Tape Crawl Space Vent Drain Kit CONTROLS Twinning Kit DOWNFLOW FILTER KITS Downflow Air Filter and Rack Kit No. and Size of filter - in. NIGHT SERVICE KITS Night Service Kit TERMINATION KITS See Installation Instructions for specific venting information. Termination Kits Direct Vent Applications Only Concentric US - 2 in. 3 in. Canada - 2 in. 3 in. Termination Kits Direct or Non-Direct vent Flush-Mount 2, 2-1/2 or 3 in. 51W11 51W11 Wall - Close Couple US - 2 in. 22G44 --- 3 in. 44J40 44J40 Wall - Close Couple WTK Canada - 2 in. 30G28 --- 3 in. 81J20 81J20 Roof 2 in. 15F75 Wall Ring Kit 2 in. 15F74 Roof Termination Flashing Kit - Direct or Non-Direct Vent Contains two flashings 15F75 3 44J41 15F74 44J41 Cleanable polyurethane frame type filter. Kits contain enough parts for two, non−direct vent installations. 3 Non-direct vent only. NOTE - Termination Kits 44W92, 44W93, 30G28, 81J20 are certified to ULC S636 standard for use in Canada only. 1 2 GAS HEAT ACCESSORIES Input all models High Altitude Pressure Switch Kit Natural Gas to LPG/Propane Kit LPG/Propane to Natural Gas Kit Natural Gas High Altitude Orifice Kit 4501 - 7500 ft. 7501 - 10,000 ft. 0 - 7500 ft. 0 - 7500 ft. 7501- 10,000 ft. 74W90 74W91 69W73 73W81 73W37 Page 3 BLOWER DATA ML193DF045XP36B PERFORMANCE (Less Filter) External Static Pressure in. w.g. ML193DF090XP48C PERFORMANCE (Less Filter) Air Volume / Watts at Various Blower Speeds High MediumHigh MediumLow Low cfm Watts cfm Watts cfm Watts cfm Watts External Static Pressure in. w.g. Air Volume / Watts at Various Blower Speeds High MediumHigh MediumLow Low cfm Watts cfm Watts cfm Watts cfm Watts 0.00 1615 650 1385 555 1205 465 1045 390 0.00 2075 800 1890 720 1625 645 1375 535 0.10 1605 640 1375 545 1195 455 1035 380 0.10 1995 755 1830 680 1590 615 1350 515 0.20 1500 620 1340 525 1165 445 1015 370 0.20 1910 715 1775 645 1575 580 1340 500 0.30 1450 590 1290 490 1125 420 975 365 0.30 1825 680 1705 610 1530 550 1325 485 0.40 1350 560 1235 480 1090 405 920 345 0.40 1730 645 1620 580 1475 525 1285 460 0.50 1300 545 1170 450 1035 380 875 335 0.50 1630 615 1530 545 1405 500 1240 440 0.60 1195 500 1095 425 840 320 0.60 1530 585 1450 525 1330 470 1175 420 990 365 0.70 1140 485 1020 400 895 345 780 300 0.70 1430 555 1340 485 1260 450 1095 390 0.80 1025 450 920 370 840 330 695 275 0.80 1300 525 1245 465 1145 415 1015 370 0.90 945 800 335 700 295 605 250 0.90 1185 495 435 ML193DF070XP36B PERFORMANCE (Less Filter) External Static Pressure in. w.g. MediumHigh MediumLow 430 1045 385 915 340 ML193DF110XP60C PERFORMANCE (Less Filter) Air Volume / Watts at Various Blower Speeds High 1110 Low cfm Watts cfm Watts cfm Watts cfm Watts External Static Pressure in. w.g. High MediumHigh MediumLow Low cfm Watts cfm Watts cfm Watts cfm Watts 0.00 1505 660 1310 570 1090 455 940 390 0.10 1480 625 1295 550 1070 435 935 365 0.10 2405 1385 2180 1070 1855 905 1555 730 0.20 1405 585 1255 515 1055 425 930 350 0.20 2285 1345 2120 1030 1850 865 1540 720 0.30 1355 580 1225 475 1045 405 900 330 0.30 2220 1315 2015 1005 1770 840 1535 705 0.40 1305 540 1165 470 1010 385 890 325 0.40 2185 1295 1950 955 1750 815 1530 685 0.50 1270 525 835 305 0.50 2045 1240 1830 925 1680 790 1500 660 1110 425 975 370 0.00 Air Volume / Watts at Various Blower Speeds 2410 1390 2190 1080 1860 910 1560 735 0.60 1175 500 1080 415 925 345 815 290 0.60 1965 1220 1710 890 1575 755 1445 640 0.70 1105 460 1000 395 855 320 745 270 0.70 1820 1165 1610 850 1495 720 1370 615 0.80 1040 440 925 365 790 300 670 250 0.80 1625 1155 1510 820 1400 695 1315 595 0.90 920 825 335 680 270 560 225 0.90 1455 1110 1390 790 1350 660 1210 565 400 Page 4 PARTS ARRANGEMENT CONTROL BOX (Includes integrated control, transformer and door switch) BAG ASSEMBLY BLOWER MOTOR (hidden) BLOWER ACCESS PANEL COMBUSTION AIR INDUCER BLOWER DECK PRIMARY LIMIT BURNER ACCESS PANEL COLD END HEADER BOX HEAT EXCHANGER GAS VALVE BURNER BOX ASSEMBLY (includes sensor, rollout switches and ignitor) FIGURE 1 Page 5 I-UNIT COMPONENTS WARNING ML193DF unit components are shown in figure 1. The combustion air inducer, gas valve and burners can be ac­ cessed by removing the burner access panel. The blower and control box can be accessed by removing the blower access door. Shock hazard. Disconnect power before servicing. Control is not field repairable. If control is inoperable, simply re­ place entire control. Can cause injury or death. Unsafe operation will result if repair is attempted. A-Control Box Components (Figure 2) Unit transformer (T1) and integrated ignition control (A92) are located in the control box. In addition, a door interlock switch (S51) is located in the control box. ML193DF Control Box INTEGRATED IGNITION CONTROL (A92) DOOR INTERLOCK SWITCH (S51) The ignition control system consists of an integrated con­ trol (figure 4) ignitor (figure 10) and sensor (figure 10). The integrated control and ignitor work in combination to en­ sure furnace ignition and ignitor durability. The integrated control, controls all maor furnace operations. The inte­ grated control also features two LED lights (DS1 red and DS2 green) for troubleshooting and two accessory termi­ nals rated at (1) one amp. The integrated control also fea­ tures a (3) amp fuse for overcurrent protection. Tables 1 and 2 show jack plug terminal designations. See table 3 for troubleshooting diagnostic codes. The 95 volt ignitor is made from a high strength, silicon nitride material that pro­ vides long life and trouble free maintenance. The inte­ grated control continuously monitors line voltage and maintains the ignitor power at a consistent level to provide proper lighting and maximum ignitor life. TABLE 1 4-Pin Terminal Designation TRANSFORMER (T1) PIN # FIGURE 2 FUNCTION 1 Combustion Air Inducer Line 2 3 4 Ignitor Line Combustion Air Inducer Neutral Ignitor Neutral TABLE 2 1. Transformer (T1) PIN # A transformer located in the control box provides power to the low voltage section of the unit. The transformers on all models are rated at 40VA with a 120V primary and 24V secondary. 2. Door Interlock Switch (S51) A door interlock switch rated 14A at 120VAC is located on the control box. The switch is wired in series with line volt­ age. When the blower door is removed the unit will shut down. 3. Integrated Ignition Control 100973 (A92) CAUTION Electrostatic discharge can affect elec­ tronic components. Take precautions to neutralize electrostatic charge by touching your hand and tools to metal prior to handling the control. 12-Pin Terminal Designations FUNCTION 1 High Limit Output 2 Not Used 3 24V Line 4 Not Used 5 Rollout Switch Out 6 24V Neutral 7 High Limit Input 8 Ground 9 Gas Valve Common 10 Pressure Switch In 11 Rollout Switch In 12 Gas Valve Out Electronic Ignition (See Figure 5) On a call for heat the integrated control monitors the com­ bustion air inducer prove switch. The integrated control will not begin the heating cycle if the prove switch is closed (bypassed). Once the prove switch is determined to be open, the combustion air inducer is energized. When the differen­ Page 6 tial in the prove switch is great enough, the prove switch closes and a 15-second pre-purge begins. If the prove switch is not proven within 2-1/2 minutes, the integrated control goes into Watchguard-Pressure Switch mode for a 5-minute re-set period. After the 15-second pre-purge period, the ignitor warms up for 20 seconds after which the gas valve opens for a 4-sec­ ond trial for ignition. The ignitor remains energized for the first 3 seconds during the 4 second trial. If ignition is not proved during the 4-second period, the integrated control will try four more times with an inter purge and warm-up time between trials of 35 seconds. After a total of five trials for ignition (including the initial trial), the integrated control goes into Watchguard-Flame Failure mode. After a 60-minute reset period, the integrated control will begin the ignition sequence again. The integrated control has an added feature of ignitor pow­ er regulation to maintain consistent lighting and longer igni­ tor life under all line voltage conditions. Fan Control The fan on time of 30 seconds is not adjustable. The fan off delay (amount of time that the blower operates after the heat demand has been satisfied) may be adjusted by changing the jumper position across the five pins on the integrated control. The unit is shipped with a factory fan off setting of 90 seconds. The fan off delay affects comfort and is adjustable to satisfy individual applications. Adjust the fan off delay to achieve a supply air temperature between 90° and 110°F at the moment that the blower is de-ener­ gized. Longer off delay settings provide lower return air temperatures; shorter settings provide higher return air temperatures. See figure 3. FAN‐OFF TIME IN SECONDS NO JUMPER To adjust fan-off timing, reposition jumper across pins to achieve desired setting. FIGURE 3 INTEGRATED CONTROL (Automatic Hot Surface Ignition System) HUM LINE XFMR EAC COOL HEAT PARK FLAME NEUTRALS TERMINAL DESIGNATIONS Humidifier (120VAC) Input (120VAC) Transformer (120VAC) Electronic Air Cleaner (120VAC) Blower - Cooling Speed (120VAC) Blower - Heating Speed (120VAC) Dead terminals to park alternate spd taps Flame sensor Neutral terminals (120VAC) 3 AMP, 32 VAC FUSE LED 1 LED 2 BLOWER OFF DELAY JUMPER FIGURE 4 Page 7 The integrated control is equipped with two LED lights for troubleshooting. The diagnostic codes are listed below in table 3. TABLE 3 DIAGNOSTIC CODES Make sure to Identify LED'S Correctly. LED #1 (Red) LED #2 (Green) DESCRIPTION SIMULTANEOUS SLOW FLASH SIMULTANEOUS SLOW FLASH Power on - Normal operation. Also signaled during cooling and continuous fan. SIMULTANEOUS FAST FLASH SIMULTANEOUS FAST FLASH Normal operation - signaled when heating demand initiated at thermostat. SLOW FLASH ON OFF SLOW FLASH Pressure prove switch open. OR: Blocked inlet/exhaust vent; OR: Pressure switch closed prior to activation of combustion air inducer. ALTERNATING SLOW FLASH ALTERNATING SLOW FLASH Watchguard 1 hour -- burners failed to ignite or lost flame 5 times during single heating demand. SLOW FLASH OFF ON SLOW FLASH ON ON Primary or secondary limit switch open. Limit must close within 3 minutes or unit goes into 1 hour Watchguard. Flame sensed without gas valve energized. Rollout switch open. OR: 12‐pin connector improperly attached. Circuit control failure or control wired incorrectly. ON OFF OFF ON FAST FLASH SLOW FLASH Main power polarity reversed. Switch line and neutral. SLOW FLASH FAST FLASH Low flame signal. Measures below 1.5 microamps. Replace flame sense rod. ALTERNATING FAST FLASH ALTERNATING FAST FLASH Improper main ground. OR: Line voltage below 90 volts. NOTE - Slow flash rate equals 1 Hz (one flash per second). Fast flash rate equals 3 Hz (three flashes per second). Minimum flame sense current = 0.5 microAmps. É É É ON OFF 15 Sec. Pre -Purge 20 sec. Ignitor Warmup *4 Sec.Trial for Ign. **Blower “On” Delay End of Heat Demand 5 SEC Blower Off Time ÉÉÉÉÉÉÉÉÉÉÉÉÉÉÉÉÉÉÉÉÉÉÉÉÉ ÉÉÉÉÉÉÉÉÉÉÉÉÉÉÉÉÉÉÉÉÉÉÉÉÉ ÉÉÉÉÉÉÉÉÉÉÉÉÉÉÉÉÉÉÉÉÉÉÉÉÉÉÉ ÉÉÉÉÉÉÉÉÉ ÉÉÉÉÉÉÉÉÉ ÉÉÉÉÉÉÉÉÉÉÉÉÉ ÉÉÉÉÉÉÉÉÉ ÉÉÉÉÉÉÉÉÉ Post Purge DEMAND CAI IGNITOR GAS VALVE INDOOR BLOWER *Ignitor will energize the first 3 seconds of the 4 second trial for ignition **Blower on time will be 45 seconds after gas valve is energized. Blower off time will depend on “OFF TIME” Setting. FIGURE 5 Page 8 TABLE 5 4. Integrated Ignition Control 103085 (A92) PIN # WARNING Shock hazard. Disconnect power before servicing. Control is not field repairable. If control is inoperable, simply re­ place entire control. Can cause injury or death. Unsafe operation will re­ sult if repair is attempted. The hot surface ignition control system consisting of an in­ tegrated control (figure 6 with control terminal designations in tables 4 and 5), flame sensor and ignitor (figure 10). The integrated control and ignitor work in combination to en­ sure furnace ignition and ignitor durability. The integrated control, controls all major furnace operations. The inte­ grated control also features a RED LED for troubleshooting and two accessory terminals rated at (1) one amp. See table 6 for troubleshooting diagnostic codes. The 120 volt ignitor is made from a high strength, silicon nitride material that provides long life and trouble free maintenance. 4-Pin Terminal Designation PIN # FUNCTION 1 Combustion Air Inducer Line 2 3 4 Ignitor Line Combustion Air Inducer Neutral Ignitor Neutral 1 High Limit Output 2 Sensor 3 24V Line 4 Not Used 5 Rollout Switch Out 6 24V Neutral 7 High Limit Input 8 Ground 9 Gas Valve Common 10 Pressure Switch In 11 Rollout Switch In 12 Gas Valve Out TABLE 6 Electronic Ignition (Figure 7) On a call for heat the integrated control monitors the com­ bustion air inducer pressure switch. The control will not be­ gin the heating cycle if the pressure switch is closed (bypassed). Once the pressure switch is determined to be open, the combustion air inducer is energized. When the differential in the pressure switch is great enough, the pres­ sure switch closes and a 15-second pre-purge begins. If the pressure switch is not proven within 2-1/2 minutes, the integrated control goes into Watchguard-Pressure Switch mode for a 5-minute re-set period. After the 15-second pre-purge period, the ignitor warms up for 20 seconds after which the gas valve opens for a 4-sec­ ond trial for ignition. The ignitor remains energized for the first 3 seconds of the trial for ignition. If ignition is not proved during the trial for ignition, the integrated control will try four more times with an inter purge and warm-up time between trials of 30 seconds. After a total of five trials for ignition (in­ cluding the initial trial), the integrated control goes into Watchguard-Flame Failure mode. After a 60-minute reset period, the integrated control will begin the ignition se­ quence again. TABLE 4 12-Pin Terminal Designations FUNCTION DIAGNOSTIC CODES LED Status DESCRIPTION LED Off No power to control or control harware fault detected. LED On Normal operation. 1 Flash Flame present with gas vavle de-energized. 2 Flashes Pressure switch closed with combustion air inducer de-energized. 3 Flashes Pressure switch open with combus­ tion air inducer energized. 4 Flashes Primary limit switch open. 5 Flashes Rollout switch open. 6 Flashes Pressure switch cycle lockout. 7 Flashes Lockout, burners fail to light. 8 Flashes Lockout, buners lost flame too many times. 9 Flashes Line voltage polarity incorrect. Note - This control is equipped with a push button switch for diagnostic code recall. The control stores the last 5 fault codes in non-volatile memory. The most recent fault code is flashed first, the oldest fault code is flashed last. There is a 2 second pause between codes. When the push button switch is pressed for less than 5 seconds, the control will flash the stored fault codes when the switch is released. The fault code history may be cleared by pressing the push button switch for more than 5 seconds. Page 9 INTEGRATED CONTROL (Automatic Hot Surface Ignition System) HUM LINE XFMR EAC COOL HEAT PARK CONT NEUTRALS TWIN TERMINAL DESIGNATIONS Humidifier (120VAC) Input (120VAC) Transformer (120VAC) Indoor Air Qality Accessory Air Cleaner (120VAC) Blower - Cooling Speed (120VAC) Blower - Heating Speed (120VAC) Dead terminals to park alternate spd taps Continuous blower Neutral terminals (120VAC) Twinning Terminal (24VAC) LED PUSH BUTTON TWIN FIGURE 6 ÉÉ ÉÉ ON OFF DEMAND CAI IGNITOR GAS VALVE INDOOR BLOWER ELECTRONIC IGNITION 1 35 15 69 39 5 SEC ÉÉÉÉÉÉÉÉÉÉÉÉÉÉÉÉÉÉÉÉÉÉÉÉ ÉÉÉÉÉÉÉÉÉÉÉÉÉÉÉÉÉÉÉÉÉÉÉÉ ÉÉÉÉÉÉÉÉÉÉÉÉÉÉÉÉÉÉÉÉÉÉÉÉÉÉ ÉÉÉÉÉÉÉÉÉÉÉÉÉÉÉÉÉÉÉÉÉÉÉÉÉÉ ÉÉÉÉÉÉÉÉÉÉ ÉÉÉÉÉÉÉÉÉÉÉÉÉ ÉÉÉÉÉÉÉÉÉÉÉÉÉ ÉÉÉÉÉÉÉÉÉ ÉÉÉÉÉÉÉÉÉ Pre -Purge Ignitor Warm-up Trial for Ignition Blower “On”* Delay Post Purge *Blower on time will be 30 seconds after flame is sensed. Blower off time will depend on “OFF TIME” Setting. FIGURE 7 Page 10 Fan Time Control Heating Fan On Time The fan on time of 30 seconds is not adjustable. Heating Fan Off Time Fan off time (time that the blower operates after the heat demand has been satisfied) can be adjusted by moving the jumper to a different setting. The unit is shipped with a fac­ tory fan off setting of 120 seconds. For customized comfort, monitor the supply air temperature once the heat demand is satisfied. Note the supply air temperature at the instant the blower is de-energized. Adjust the fan-off delay to achieve a supply air temperature between 90° - 110° at the instant the blower is de-ener­ gized. (Longer delay times allow for lower air temperature, shorter delay times allow for higher air temperature). See figure 8. Cooling Fan On Time The fan on time is 2 seconds and is not adjustable. Cooling Fan Off Time The control has a 60 second fan off delay after cooling de­ mand has been met. This delay is factory set and not ad­ justable. Twinning 2 ML193DF Furnaces Integrated control 103085 is equipped with a provision to ”twin” (interconnect) two(2) adjacent furnaces with a com­ mon plenum such that they operate as one (1) large unit. When twinned, the circulating blower speeds are synchro­ nized between the furnaces. If either furnace has a need to run the blower, both furnaces will run the blower on the same speed. The cooling speed has highest priority, fol­ lowed by heating speed and fan speed. Field installation of twinning consists of connecting wires between the ”C” and ”Twin” terminals of the two controls. The 24 VAC secondary of the two systems must be in phase. All thermostat connections are made to one control only. Figure 9 show wiring for two-stage and single stage thermostats. The twinned furnace without thermostat connections is to have the call for heat supplied by an external 24VAC isola­ tion relay to prevent its rollout switch from being bypassed by the other twinned furnace. The coil of the isolation relay connects from the thermostat ”W” to 24 VAC common. The contacts of the relay connect ”R” to ”W” on the non-thermo­ stat twin. HEAT FAN‐OFF TIME IN SECONDS NO JUMPER To adjust fan-off timing, reposition jumper across pins to achieve desired setting. 180 Second off Time 60 90 120 180 120 Second off Time 60 90 120 180 90 Second off Time 60 90 120 180 60 90 120 180 60 Second off Time FIGURE 8 Page 11 FIELD WIRING FOR TWINNING THE ML193DF TWO-STAGE THERMOSTAT TWIN R SINGLE STAGE THERMOSTAT R R TWIN 1 Y TWIN 1 Y Y Y Call For Fan Call For Fan G Call For 2nd StageHeat R Call For Cool Call For Cool Call For 1st Stage Heat TWIN G G G Call For Heat W W1 W2 W W C C TWIN TWIN ISOLATION RELAY ISOLATION RELAY R R TWIN 2 TWIN 2 Y Y G G W W C C FIGURE 9 Page 12 NOTE - The ML193DF furnace contains electronic components that are polarity sensitive. Make sure that the furnace is wired correctly and is properly grounded. B-Heating Components Combustion air inducer (B6), primary limit control (S10), SureLight ignitor, burners, flame rollout switch (S47), gas valve (GV1), combustion air prove switch (S18), and clam­ shell heat exchangers are located in the heating compart­ ment. The heating compartment can be accessed by re­ moving the burner access panel. 1. Ignitor (Figure 10) ML193DF units use a mini-nitride ignitor made from a pro­ prietary ceramic material. Ignitor longevity is enhanced by controlling the voltage to the ignitor. Units equipped with control 103085 have a 120V ignitor. Units equipped with control 100973 have a 95V ignitor. See figure 11 and table 7 for resistance and voltage checks. 2. Flame Sensor (Figure 10) 3. Flame Rollout Switches (Figure 10) Flame rollout switches S47 are SPST N.C. high tempera­ ture limits located on the top left and bottom right of the front buner box plate. S47 is wired to the burner ignition control A92. When either of the switches sense flame rollout (indi­ cating a blockage in the combustion passages), the flame rollout switch trips, and the ignition control immediately closes the gas valve. Switch S47 in all ML193DF units is factory preset to open at 250_F + 12_F (121_C + 6.7_C) on a temperature rise. All flame rollout switches are manual reset. A flame sensor is located on the left side of the burner sup­ port. The sensor is mounted on the bottom burner box plate and the tip protrudes into the flame envelope of the leftmost burner. The sensor can be removed for service with­ out removing any part of the burners. During operation, flame is sensed by current passed through the flame and sensing electrode. The ignition control allows the gas valve to remain open as long as flame signal is sensed. ML193DF Burner Box Assembly IGNITOR BURNERS ROLLOUT SWITCHES FRONT BURNER BOX PLATE SENSOR GAS VALVE FIGURE 10 Page 13 IGNITOR CHECKS Control 103085 100973 TABLE 7 Ohms Voltage + 10% 39 to 70 120 24 to 47 95 Test 1 Multi−Meter (set to ohms) Integrated Control Detail Test 1 Check ignitor circuit for correct resistance. Remove 4-pin plug from control. Check ohms reading across terminals 2 and 4. See table 7. If value is correct, this is the only test needed. If the reading on the meter is not correct, (0 or infinity) then a second test is needed. Test 2 Check ignitor for correct resistance. Seperate the 2-pin jack-plug near the manifold and check resistance of ignitor at the plug. See table 7. If the reading is correct, then the problem is with the wiring between the jack-plug and the control. If reading is not correct, the issue is the ignitor. Multi−Meter (set to ohms) Test 2 Integrated Control Detail Multi−Meter (set to VAC) Test 3 Integrated Control Detail Test 3 Check ignitor for correct voltage Insert meter probes into terminals 2 and 4 (use small diameter probes in order not to damage plug). Check voltage during 20 second ignitor warm up period. See table 7. If voltage reads below these values, check for correct supply voltage to furnace. FIGURE 11 Page 14 4. Primary Limit Control (Figure 12) Primary limit (S10) used on ML193DF units is located in the heating vestibule panel. When excess heat is sensed in the heat exchanger, the limit will open. Once the limit opens, the furnace control energizes the supply air blower and deenergizes the gas valve. The limit automatically resets when unit temperature returns to normal. The switch is fac­ tory set and cannot be adjusted. For limit replacement re­ move wires from limit terminals and rotate limit switch 90 degrees. Slowly remove from the vestibule panel. Install replacement limit with same care. burner input. See table 8 for orifice size. The burner is sup­ ported by the orifice and will easily slide off for service. A flame retention ring in the end of each burner maintains correct flame length and shape and keeps the flame from lifting off the burner head. TABLE 8 Gas Orifice Size Unit Fuel Orifice Size All Natural 0.0625 All L.P./Propane 0.034 Primary Limit Location and Heat Exchanger Burner Detail Top Vie­ w SENSOR IGNITOR ORIFICES FIGURE 13 7. Gas Valve (GV1) Install limit face down FIGURE 12 5. Heat Exchanger (Figure 12) ML193DF units use an aluminized steel primary and stain­ less steel secondary heat exchanger assembly. Heat is transferred to the air stream from all surfaces of the heat exchanger. The shape of the heat exchanger ensures maximum efficiency. The combustion air inducer pulls fresh air through the burn­ er box. This air is mixed with gas in the burners. The gas / air mixture is then burned at the entrance of each clam­ shell. Combustion gases are then pulled through the pri­ mary and secondary heat exchangers and exhausted out the exhaust vent pipe. 6. Burners (Figure 13) The ML193DF uses an internally redundant to valve to as­ sure safety shut‐off. If the gas valve must be replaced, the same type valve must be used. 24VAC terminals and gas control switch are located on top of the valve. All terminals on the gas valve are connected to wires from the ignition control. 24V applied to the terminals opens the valve. Inlet and outlet pressure taps are located on the valve. A manifold adjustment screw is also located on the valve. An LPG changeover kit is available. MANIFOLD PRESSURE ADJUSTMENT SCREW (under barbed fitting) All units use inshot burners. Burners are factory set and do not require adjustment. Burners can be removed as an as­ sembly for service. Burner maintenance and service is de­ tailed in the MAINTENANCE section of this manual. Each burner uses an orifice which is precisely matched to the Page 15 Gas Valve MANIFOLD PRESSURE OUTLET PORT INLET PRESSURE PORT FIGURE 14 8. Combustion Air Inducer (B6) & Cold End Header Box Pressure Switch All ML193DF units use a combustion air inducer to move air through the burners and heat exchanger during heating op­ eration. The blower uses a shaded pole 120VAC motor. The motor operates during all heating operation and is con­ trolled by burner ignition control A3. Blower operates con­ tinuously while there is a call for heat. The burner ignition control will not proceed with the ignition sequence until combustion air inducer operation is sensed by the proving switches. The CAI is installed on the cold end header box. The cold end header box is a single piece made of hard plastic. The box has an internal channel where the combustion air in­ ducer creates negative pressure at unit start up. The chan­ nel contains an orifice used to regulate flow created by the CAI. The box has pressure taps for the CAI pressure switch hoses. The pressure switch measure the pressure across the CAI orifice or difference in the channel and the box. If replacement is necessary the gaskets used to seal the box to the vestibule panel and the CAI to the box, must also be replaced. TABLE 9 ML193DF Unit C.A.I. Orifice Size -045 0.618 -070 0.891 -090 1.031 -110 1.297 9. Combustion Air Pressure Switch (Figure 15) ML193DF series units are equipped with a differential pres­ sure switch located on the cold end header box. The switches monitor across the CAI orifice to insure proper flow through the heat exchanger. The switch is a SPST N.O. prove switch electrically con­ nected to the integrated control. The purpose of the switch is to prevent burner operation if the combustion air inducer is not moving enough air for proper combustion. 24VAC TERMINALS BRACKET TAP TAP FIGURE 15 On start‐up, the switch senses that the combustion air in­ ducer is operating. It closes a circuit to the ignition control when the difference in pressure across the CAI orifice ex­ ceeds a non-adjustable factory setting. If the switch does not successfully sense the required differential, the switch cannot close and the furnace cannot operate. If the flue or air inlet become obstructed during operation, the switch senses a loss of pressure differential and opens the circuit to the ignition control. If the condensate line is blocked, wa­ ter will back up into the header box and reduce the pressure differential across the switch. The prove switch opens if the differential drops below the set point. See table 10. Checks of pressure differential can aid in troubleshooting. When measuring the pressure differential, readings should be taken at the pressure switch. See figure 16. Lack of dif­ ferential usually indicates problems in the intake or exhaust piping, but may indicate problems in the heat exchanger, condensing coil, header boxes, combustion inducer or oth­ er components. TABLE 10 Altitude ft 4501 0 - 4500 7501 - 10000 ML193DF 7500 Set Point SetPoint Set Point -045 -070 -090 -110 -0.65 -0.60 *Set point is factory set and non-adjustable Page 16 -0.55 Measuring Pressure Differential RED TUBING NEGATIVE BLACK TUBING POSITIVE 12- Remove thermostat demand and allow unit to cycle off. Install a tee in the negative (-) line (red tubing) and a tee in the positive (+) line (black tubing) running from the pressure switch to the cold end header box. 3 - Install a manometer with hose from the negative (-) side of the manometer to the tee installed in the negative (-) line and with hose from the positive (+) side of the manometer to the tee in the positive (+) line. NOTE - Both sides of the cold end header box are negative. How­ ever the (+) port reads less negative pressure than the (-) port. 4- Operate unit and observe manometer reading. Readings will change as heat exchanger warms. a. Take one reading immediately after start‐up. b. Take a second reading after unit has reached steady state (approximately 5 minutes). This will be the pressure differential. The pressure differential should be greater than those listed in table 10. 5- Remove thermostat demand and allow to cycle off. 6- Remove manometer and tee's. Reinstall combustion air sensing hoses to the pressure switch. FIGURE 16 C-Blower Compartment 1.Blower Motor (B3) and Capacitor (C4) Blower motor (B3) and capacitor (C4), are located in the blower compartment. The blower compartment can be ac­ cessed by removing the blower access panel. All ML193DF units use single-phase direct-drive blower motors. All motors are 120V permanent split capacitor mo­ tors to ensure maximum efficiency. See SPECIFI­ CATIONS table at the front of this manual for more detail. See motor nameplate for capacitor ratings. Blower Motor Housing BOLTS MOTOR CAPACITOR To Remove Blower From Unit: Disconnect Power, Remove Control Box, Remove Bolts and Unplug Motor Wires From Control Board. Then Slide Out Front of Unit. FIGURE 17 Page 17 II-PLACEMENT AND INSTALLATION IMPORTANT Pipe & Fittings Specifications All pipe, fittings, primer and solvent cement must conform with American National Standard Institute and the Ameri­ can Society for Testing and Materials (ANSI/ASTM) stan­ dards. The solvent shall be free flowing and contain no lumps, undissolved particles or any foreign matter that ad­ versely affects the joint strength or chemical resistance of the cement. The cement shall show no gelation, stratifica­ tion, or separation that cannot be removed by stirring. Re­ fer to the table 11 below for approved piping and fitting ma­ terials. CAUTION Solvent cements for plastic pipe are flammable liq­ uids and should be kept away from all sources of ignition. Do not use excessive amounts of solvent cement when making joints. Good ventilation should be maintained to reduce fire hazard and to minimize breathing of solvent vapors. Avoid contact of ce­ ment with skin and eyes. TABLE 11 PIPING AND FITTINGS SPECIFICATIONS Schedule 40 PVC (Pipe) Schedule 40 PVC (Cellular Core Pipe) D1785 F891 Schedule 40 PVC (Fittings) D2466 Schedule 40 CPVC (Pipe) F441 Schedule 40 CPVC (Fittings) F438 SDR-21 PVC or SDR-26 PVC (Pipe) SDR-21 CPVC or SDR-26 CPVC (Pipe) Schedule 40 ABS Cellular Core DWV (Pipe) F442 F628 D1527 Schedule 40 ABS (Fittings) D2468 ABS-DWV (Drain Waste & Vent) (Pipe & Fittings) D2661 PVC-DWV (Drain Waste & Vent) Pipe & Fittings) D2665 PVC & CPVC Primer PVC Solvent Cement CPVC Solvent Cement ABS Solvent Cement ASTM SPECIFICATION F656 D2564 F493 D2235 PVC/CPVC/ABS All Purpose Cement For Fittings & Pipe of the same material D2564, D2235, F493 ABS to PVC or CPVC Transition Solvent Cement D3138 CANADA PIPE & FITTING & SOLVENT CEMENT PVC & CPVC Pipe and Fittings PVC & CPVC Solvent Cement Use PVC primer and solvent cement or ABS solvent ce­ ment meeting ASTM specifications, refer to Table 11. As an alternate, use all purpose cement, to bond ABS, PVC, or CPVC pipe when using fittings and pipe made of the same materials. Use transition solvent cement when bonding ABS to either PVC or CPVC. Low temperature solvent cement is recommended during cooler weather. Metal or plastic strapping may be used for vent pipe hangers. Uniformly apply a liberal coat of PVC primer for PVC or use a clean dry cloth for ABS to clean in­ side socket surface of fitting and male end of pipe to depth of fitting socket. Canadian Applications Only - Pipe, fittings, primer and solvent cement used to vent (exhaust) this appliance must be certified to ULC S636 and supplied by a single manufacturer as part of an approved vent (exhaust) sys­ tem. In addition, the first three feet of vent pipe from the fur­ nace flue collar must be accessible for inspection. D2241 Schedule 40 ABS (Pipe) PRIMER & SOLVENT CEMENT ML193DF exhaust and intake connections are made of PVC. Use PVC primer and solvent cement when using PVC vent pipe. When using ABS vent pipe, use transitional solvent cement to make connections to the PVC fittings in the unit. MARKING ULCS636 ABS to PVC or CPVC Transition Cement POLYPROPYLENE VENTING SYSTEM PolyPro by Duravent ULC-S636 Page 18 TABLE 12 OUTDOOR TERMINATION USAGE* STANDARD Input Size 045 070 090 110 Vent Pipe Dia. in. Flush­ Mount Kit Wall Kit CONCENTRIC Wall Ring Kit 2 inch 1-1/2 inch 2 inch 71M80 (US) 444W92 (CA) 69M29 (US) 444W92 (CA) 3 inch 2 inch 3 inch 51W11 (US) 51W12 (CA) 22G44 (US) 430G28 (CA) 44J40 (US) 481J20 (CA) 15F74 2 3YES YES 1YES 1YES 5YES 2YES 2-1/2 3YES YES 1YES 1YES 5YES 2YES 3 3YES YES 1YES 1YES 5YES 2YES 2 3YES YES 1YES 1YES 5YES 2YES 2-1/2 3YES YES 1YES 1YES 5YES 2YES 3 3YES YES 1YES 1YES 5YES 2YES 2 3YES YES YES 5YES YES YES 2-1/2 3YES YES YES 5YES YES YES 3 3YES YES YES 5YES YES YES 2 YES YES YES 5YES YES YES 2-1/2 YES YES 5YES YES YES 3 YES YES 5YES YES YES Field Fabricated 60L46 (US) (CA) 444W93 NOTE - Standard Terminations do not include any vent pipe or elbows external to the structure. Any vent pipe or elbows external to the structure must be included in total vent length calculations. See vent length tables. * Kits must be properly installed according to kit instructions. 1Requires field-provided outdoor 1-1/2” exhaust accelerator. 2Concentric kits 71M80 and 44W92 include 1-1/2” outdoor accelerator, when used with 045 and 070 input models. 3 Flush mount kit 51W11 and 51W12 includes 1-1/2 in. outdoor exhaust accelerator, required when used with 045, 070 and 090 input models. 4 Termination kits 30G28, 44W92, 4493 and 81J20 are certified to ULC S636 for use in Canada only. 5 See table 17 for vent accelerator requirements. Page 19 Venting Practices Joint Cementing Procedure All cementing of joints should be done according to the specifications outlined in ASTM D 2855. Piping Suspension Guidelines SCHEDULE 40 PVC - 5' all other pipe* - 3' NOTE - A sheet metal screw may be used to secure the intake pipe to the connector, if desired. Use a drill or self tapping screw to make a pilot hole. DANGER * See table 11 for allowable pipe. DANGER OF EXPLOSION! Fumes from PVC glue may ignite during system check. Allow fumes to dissipate for at least 5 minutes before placing unit into operation. NOTE - Isolate piping at the point where it exits the outside wall or roof in order to prevent transmission of vibration to the structure. Wall Thickness Guidelines 24” maximum 3/4” minimum 1 - Measure and cut vent pipe to desired length. 2 - Debur and chamfer end of pipe, removing any ridges or rough edges. If end is not chamfered, edge of pipe may remove cement from fitting socket and result in a leaking joint. 3 - Clean and dry surfaces to be joined. 4 - Test fit joint and mark depth of fitting on outside of pipe. 5 - Uniformly apply a liberal coat of PVC primer for PVC or use a clean dry cloth for ABS to clean inside socket surface of fitting and male end of pipe to depth of fitting socket. 6 - Promptly apply solvent cement to end of pipe and in­ side socket surface of fitting. Cement should be ap­ plied lightly but uniformly to inside of socket. Take care to keep excess cement out of socket. Apply second coat to end of pipe. NOTE - Time is critical at this stage. Do not allow prim­ er to dry before applying cement. 7 - Immediately after applying last coat of cement to pipe, and while both inside socket surface and end of pipe are wet with cement, forcefully insert end of pipe into socket until it bottoms out. Turn PVC pipe 1/4 turn dur­ ing assembly (but not after pipe is fully inserted) to dis­ tribute cement evenly. DO NOT turn ABS or cellular core pipe. NOTE - Assembly should be completed within 20 sec­ onds after last application of cement. Hammer blows should not be used when inserting pipe. 8 - After assembly, wipe excess cement from pipe at end of fitting socket. A properly made joint will show a bead around its entire perimeter. Any gaps may indicate an improper assembly due to insufficient solvent. 9 - Handle joints carefully until completely set. inside Wall FIGURE 18 CHIMNEY OR GAS VENT (Check sizing for water heater only) FURNACE (Replaced by ML193) REPLACING FURNACE THAT WAS PART OF A COMMON VENT SYSTEM WATER HEATER OPENINGS (To Adjacent Room) If an ML193DF furnace replaces a furnace which was com­ monly vented with another gas appliance, the size of the ex­ isting vent pipe for that gas appliance must be checked. Without the heat of the original furnace flue products, the existing vent pipe is probably oversized for the single water heater or other appliance. The vent should be checked for proper draw with the remaining appliance. FIGURE 19 Page 20 outside 1. In areas where piping penetrates joists or interior walls, hole must be large enough to allow clearance on all sides of pipe through center of hole using a hanger. 2. When furnace is installed in a residence where unit is shut down for an extended period of time, such as a vacation home, make provisions for draining conden­ sate collection trap and lines. Exhaust Piping (Figures 21 and 22) Route piping to outside of structure. Continue with installa­ tion following instructions given in piping termination sec­ tion. The ML193DF can be installed as either a Non-Direct Vent or a Direct Vent gas central furnace. NOTE - In Direct Vent installations, combustion air is taken from outdoors and flue gases are discharged outdoors. In Non-Direct Vent installations, combustion air is taken from indoors or ventilated attic or crawlspace and flue gases are discharged outdoors. Intake and exhaust pipe sizing -- Size pipe according to tables 13 and 14. Count all elbows inside and outside the home. Table 13 lists the minimum vent pipe lengths per­ mitted. Table 14 lists the maximum pipe lengths permitted. TABLE 13 MINIMUM VENT PIPE LENGTHS CAUTION Do not discharge exhaust into an existing stack or stack that also serves another gas appliance. If verti­ cal discharge through an existing unused stack is re­ quired, insert PVC pipe inside the stack until the end is even with the top or outlet end of the metal stack. CAUTION The exhaust vent pipe operates under positive pres­ sure and must be completely sealed to prevent leak­ age of combustion products into the living space. Vent Piping Guidelines NOTE - Lennox has approved the use of DuraVent ® manu­ factured vent pipe and terminations as an option to PVC. When using the PolyPro ® by DuraVent venting system the vent pipe requirements stated in the unit installation in­ struction – minimum & maximum vent lengths, termination clearances, etc. – apply and must be followed. Follow the instructions provided with PoyPro by DuraVent venting system for assembly or if requirements are more restrict­ ive. The PolyPro by Duravent venting system must also fol­ low the uninsulated and unconditioned space criteria listed in table 16. ML193DF MODEL MIN. VENT LENGTH* 045, 070, 090, 110 15 ft. or 5 ft plus 2 elbows or 10 ft plus 1 elbow *Any approved termination may be added to the minimum length listed. Regardless of the diameter of pipe used, the standard roof and wall terminations described in section Exhaust Piping Terminations should be used. Exhaust vent termination pipe is sized to optimize the velocity of the exhaust gas as it exits the termination. Refer to table 17. In some applications which permit the use of several differ­ ent sizes of vent pipe, a combination vent pipe may be used. Contact Lennox' Application Department for assis­ tance in sizing vent pipe in these applications. IMPORTANT Do not use screens or perforated metal in exhaust or intake terminations. Doing so will cause freeze-ups and may block the terminations. Use the following steps to correctly size vent pipe diameter. Page 21 Piping Size Process 1 2 3 What is the furnace capacity? 045, 070, 090 or 110? Which style termination being used? Standard or concentric? See table 12. NOTE - It is acceptable to use any pipe size which fits within the guidelines allowed in table 14. NOTE - All horizontal runs of exhaust pipe must slope back toward unit. A minimum of 1/4” (6mm) drop for each 12” (305mm) of horizontal run is mandatory for drainage. NOTE - Exhaust pipe MUST be glued to furnace exhaust fittings. NOTE - Exhaust piping should be checked carefully to make sure there are no sags or low spots. Which needs most elbows? Intake or exhaust? How many elbows? 4 Count all elbows inside and outside house. 5 Desired pipe size? 2”, 2-1/2”, 3” 6 What is the altitude of the furnace installation? 7 Use table 14 or 15 to find max intake or exhaust pipe length. Includes all vent pipe and elbows inside and outside the house. FIGURE 20 Page 22 TABLE 14 Maximum Allowable Intake or Exhaust Vent Length in Feet *Size intake and exhaust pipe length separately. Values in table are for Intake OR Exhaust, not combined total. Both Intake and Exhaust must be same pipe size. NOTE - Additional vent pipe and elbows used to terminate the vent pipe outside the structure must be included in the total vent length calculation. Standard Termination at Elevation 0 - 10,000 ft. 2” Pipe 2-1/2” Pipe Number Of 90° Elbows Used 045 070 090 1 61 46 2 56 3 Model 3” Pipe Model 110 Model 045 070 090 24 100 80 41 19 95 51 36 14 4 46 31 5 41 26 6 36 21 7 31 16 8 26 11 9 21 10 16 n/a n/a n/a 110 045 070 090 110 43 127 127 108 108 75 38 122 122 103 103 90 70 33 117 117 98 98 85 65 28 112 112 93 93 80 60 23 107 107 88 88 75 55 18 102 102 83 83 70 50 13 97 97 78 78 65 45 92 92 73 73 60 40 87 87 68 68 55 35 82 82 63 63 n/a n/a Concentric Termination Elevation 0 - 10,000 ft. 2” Pipe 2-1/2” Pipe Model Model Number Of 90° Elbows Used 045 070 090 1 53 38 2 48 33 3 43 28 4 38 5 Model 045 070 090 22 90 70 17 85 65 12 80 23 33 18 6 28 13 7 23 8 18 9 13 10 n/a 110 n/a n/a n/a 3” Pipe 110 045 070 090 110 39 111 111 104 104 34 106 106 99 99 60 29 101 101 94 94 75 55 24 96 96 89 89 70 50 19 91 91 84 84 65 45 14 86 86 79 79 60 40 81 81 74 74 55 35 76 76 69 69 50 30 71 71 64 64 45 25 66 66 59 59 n/a n/a TABLE 15 Maximum Allowable Exhaust Vent Lengths With Furnace Installed in a Closet or Basement Using Ventilated Attic or Crawl Space For Intake Air in Feet NOTE - Additional vent pipe and elbows used to terminate the vent pipe outside the structure must be included in the total vent length calculation. Standard Termination at Elevation 0 - 10,000 ft. 2” Pipe 2-1/2” Pipe Number Of 90° Elbows Used 045 070 090 1 51 36 2 46 3 Model 3” Pipe Model Model 045 070 090 045 070 14 85 65 090 110 28 107 107 88 31 9 80 88 60 23 102 102 83 41 26 4 83 75 55 18 97 97 78 78 4 36 5 31 21 70 50 13 92 92 73 73 16 65 45 8 87 87 68 6 26 11 68 60 40 3 82 82 63 7 21 6 63 55 35 77 77 58 8 16 1 58 50 30 72 72 53 9 11 53 45 25 67 67 48 10 6 48 40 20 62 62 43 43 n/a 110 n/a n/a Page 23 n/a 110 n/a TYPICAL EXHAUST PIPE CONNECTIONS Pipe size determined in table 14. 2” 2” 2” 2” 2” or 3” TRANSITION *2” DO NOT transition from smaller to larger pipe size in horizontal runs of exhaust pipe. INTAKE EXHAUST TOP VIEW * When transitioning up in pipe size, use the shortest length of 2” PVC pipe possible. NOTE − Exhaust pipe and intake pipe must be the same diameter. FIGURE 21 TYPICAL INTAKE PIPE CONNECTIONS Pipe size determined in table 14. 2” 2” 2” 2” 2” or TRANSITION 3” *2” 3” *2” TRANSITION *2” INTAKE EXHAUST TOP VIEW * When transitioning up in pipe size, use the shortest length of 2” PVC pipe possible. NOTE − Intake pipe and exhaust pipe must be the same diameter. FIGURE 22 Follow the next two steps when installing the unit in Direct Vent applications, where combustion air is taken from The ML193DF furnace may be installed in either direct outdoors and flue gases are discharged outdoors. The vent or non-direct vent applications. In non-direct vent provided air intake screen must not be used in direct applications, when intake air will be drawn into the furnace vent applications (outdoors). from the surrounding space, the indoor air quality must be Intake Piping considered. Guidelines listed in Combustion, Dilution and Ventilation Air section must be followed. 1 - Use cement to secure the intake pipe to the inlet air connector. Page 24 2 - Route piping to outside of structure. Continue with installation following instructions given in general guide lines for piping terminations and intake and ex­ haust piping terminations for direct vent sections. Re­ fer to table 14 for pipe sizes. EQUIPMENT IN CONFINED SPACE (Inlet Air from Ventilated Attic and Outlet Air to Outside) Ventilation Louvers Inlet Air (Minimum 12 in.(305mm) Above attic floor) Roof Terminated Exhaust Pipe TYPICAL AIR INTAKE PIPE CONNECTIONS NON−DIRECT VENT APPLICATIONS *Intake Debris Screen (Provided) AIR INTAKE SCREEN (Provided) Furnace * See table 15 for maximum vent lengths NOTE-The inlet and outlet air openings shall each have a free area of at least one square inch per 4,000 Btu (645mm 2 per 1.17kW) per hour of the total input rating of all equipment in the enclosure. FIGURE 24 EQUIPMENT IN CONFINED SPACE (Inlet Air from Ventilated Crawlspace and Outlet Air to Outside) Roof Terminated Exhaust Pipe NOTE - Air intake screen and elbow may be rotated, so that screen may be positioned to face forward or to either side. FIGURE 23 Follow the next two steps when installing the unit in Non‐ Direct Vent applications where combustion air is taken from indoors and flue gases are discharged outdoors. Ventilation Louvers (Crawl space) 1 - Use field-provided materials and the factory-provided air intake screen to route the intake piping as shown in figure 23. Maintain a minimum clearance of 3” (76mm) around the air intake opening. The air intake opening (with the protective screen) should always be directed forward, or sideways. 2 - If intake air is drawn from a ventilated attic (figure 24) or ventilated crawlspace (figure 25) the exhaust vent length must not exceed those listed in table 15. If 3” di­ ameter pipe is used, reduce to 2” diameter pipe at the termination point to accommodate the debris screen. 3 - Use cement to secure the intake pipe to the connector, if desired. CAUTION If this unit is being installed in an application with combustion air coming in from a space serviced by an exhaust fan, power exhaust fan, or other device which may create a negative pressure in the space, take care when sizing the inlet air opening. The in­ let air opening must be sized to accommodate the maximum volume of exhausted air as well as the maximum volume of combustion air required for all gas appliances serviced by this space. Furnace Coupling or 3 in. to 2 in. Transition (Field Provided) Inlet Air (Minimum 12 in.(305mm) Above crawl space floor) *Intake Debris Screen Provided) * See table 15 for maximum vent lengths NOTE-The inlet and outlet air openings shall each have a free area of at least one square inch per 4,000 Btu (645mm 2 per 1.17kW) per hour of the total input rating of all equipment in the enclosure. FIGURE 25 General Guidelines for Vent Terminations In Non‐Direct Vent applications, combustion air is taken from indoors and the flue gases are discharged to the out­ doors. The ML193DF is then classified as a non‐direct vent, Category IV gas furnace. In Direct Vent applications, combustion air is taken from outdoors and the flue gases are discharged to the out­ doors. The ML193DF is then classified as a direct vent, Category IV gas furnace. In both Non‐Direct Vent and Direct Vent applications, the vent termination is limited by local building codes. In the ab­ sence of local codes, refer to the current National Fuel Gas Code ANSI Z223-1/NFPA 54 in U.S.A., and current CSAB149 Natural Gas and Propane Installation Codes in Can­ ada for details. Page 25 closed areas that are not exposed to the outdoor ambient temperature and are above 32 degrees F (0°C) are to be considered conditioned spaces. Position termination according to location given in figure 27 or 28. In addition, position termination so it is free from any obstructions and 12” above the average snow accumula­ tion. At vent termination, care must be taken to maintain protective coatings over building materials (prolonged exposure to exhaust condensate can destroy protective coatings). It is recommended that the exhaust outlet not be located within 6 feet (1.8m) of a condensing unit because the condensate can damage the painted coating. NOTE - See table 16 for maximum allowed exhaust pipe length without insulation in unconditioned space during winter design temperatures below 32°F (0°C). If required exhaust pipe should be insulated with 1/2” (13mm) Arma­ flex or equivalent. In extreme cold climate areas, 3/4” (19mm) Armaflex or equivalent may be necessary. Insula­ tion must be protected from deterioration. Armaflex with UV protection is permissable. Basements or other en­ IMPORTANT Do not use screens or perforated metal in exhaust terminations. Doing so will cause freeze-ups and may block the terminations. IMPORTANT For Canadian Installations Only: In accordance to CSA International B149 installation codes, the minimum allowed distance between the combustion air intake inlet and the exhaust outlet of other appliances shall not be less than 12 inches (305mm). TABLE 16 Maximum Allowable Exhaust Vent Pipe Length (in ft.) Without Insulation In Unconditioned Space For Winter Design Temperatures Single - Stage High Efficiency Furnace Winter Design Temperatures1 °F (°C) 32 to 21 (0 to -6) 20 to 1 (-7 to -17) 0 to -20 (-18 to -29) Vent Pipe Diameter 2 in. 2-1/2 in. 3 in. 2 in 2-1/2 in. 3 in. 2 in. 2-1/2 in. 3 in. 045 PVC 26 18 14 16 12 9 10 8 4 070 2PP 24 N/A 12 15 N/A 8 9 N/A 3 2PP PVC 44 32 26 28 20 16 20 14 10 41 N/A 23 26 N/A 14 18 N/A 8 Unit Input Size 090 2PP PVC 44 44 50 N/A 38 33 40 37 30 N/A 26 23 30 28 20 N/A 16 14 110 PVC 24 58 55 24 44 32 24 32 26 1Refer 135 2PP 24 N/A 49 24 N/A 28 24 N/A 23 PVC N/A N/A 60 N/A N/A 40 N/A N/A 30 2PP N/A N/A 53 N/A N/A 35 N/A N/A 26 to 99% Minimum Design Temperature table provided in the current edition of the ASHRAE Fundamentals Handbook. vent pipe (PP) NOTE - Maximum uninsulated vent lengths listed may include the termination(vent pipe exterior to the structure) and cannot exceed 5 linear feet or the maximum allowable intake or exhaust vent length listed in table 14 or 15 which ever is less. NOTE - If insulation is required in an unconditioned space, it must be located on the pipe closest to the furnace. See figure26. 2 Poly-Propylene Conditioned Space Pipe Insulation Conditioned Space Unconditioned Space FIGURE 26 Page 26 Exhaust Pipe Intake Pipe VENT TERMINATION CLEARANCES FOR NON-DIRECT VENT INSTALLATIONS IN THE USA AND CANADA INSIDE CORNER DETAIL G H A D E B L Fixed Closed Operable F B B C I Fixed Closed Operable M B K J A B AREA WHERE TERMINAL IS NOT PERMITTED AIR SUPPLY INLET VENT TERMINAL US Installations1 A= Clearance above grade, veranda, porch, deck or balcony B= Clearance to window or door that may be opened C= Clearance to permanently closed window D= Vertical clearance to ventilated soffit located above the terminal within a horizontal distance of 2 feet (610 mm) from the center line of the terminal E= Clearance to unventilated soffit F= Clearance to outside corner G= 12 inches (305mm) or 12 in. (305mm) above average snow accumulation. 4 feet (1.2 m) below or to side of opening; 1 foot (30cm) above opening Canadian Installations2 12 inches (305mm) or 12 in. (305mm) above average snow accumulation. 6 inches (152mm) for appliances <10,000 Btuh (3kw), 12 inches (305mm) for appliances > 10,000 Btuh (3kw) and <100,000 Btuh (30kw), 36 inches (.9m) for appliances > 100,000 Btuh (30kw) * 12” * 12” * Equal to or greater than soffit depth. * Equal to or greater than soffit depth. * Equal to or greater than soffit depth. * No minimum to outside corner * Clearance to inside corner * Equal to or greater than soffit depth. * No minimum to outside corner * H= Clearance to each side of center line ex­ tended above meter / regulator assembly * 3 feet (.9m) within a height 15 feet (4.5m) above the meter / regulator assembly 3 feet (.9m) within a height 15 feet (4.5m) above the meter / regulator assembly I= Clearance to service regulator vent outlet Clearance to non-mechanical air supply inlet to building or the com­ bustion air inlet to any other ap­ pliance * 3 feet (.9m) 3 feet (.9m) J= K= L= M= 4 feet (1.2 m) below or to side of opening; 1 foot (30 cm) above opening Clearance to mechanical air sup­ ply inlet Clearance above paved sidewalk or paved driveway located on public property Clearance under veranda, porch, deck or balcony 3 feet (.9m) above if within 10 feet (3m) horizontally 7 feet (2.1m)† 7 feet (2.1m)† *12 inches (305mm)‡ 1 In 2 In accordance with the current ANSI Z223.1/NFPA 54 Natural Fuel Gas Code accordance with the current CSA B149.1, Natural Gas and Propane Installation Code † A vent shall not terminate directly above a sidewalk or paved driveway that is located between two single family dwellings and serves both dwellings. ‡ Permitted only if veranda, porch, deck or balcony is fully open on a minimum of two sides beneath the floor. Lennox recommends avoiding this location if possible. FIGURE 27 Page 27 6 inches (152mm) for appliances <10,000 Btuh (3kw), 12 inches (305mm) for appliances > 10,000 Btuh (3kw) and <100,000 Btuh (30kw), 36 inches (.9m) for appliances > 100,000 Btuh (30kw) 6 feet (1.8m) 12 inches (305mm)‡ *For clearances not specified in ANSI Z223.1/NFPA 54 or CSA B149.1, clearance will be in accordance with local installation codes and the requirements of the gas supplier and these instal­ lation instructions.” VENT TERMINATION CLEARANCES FOR DIRECT VENT INSTALLATIONS IN THE USA AND CANADA INSIDE CORNER DETAIL G H A D E B L Fixed Closed Operable F B B C I Fixed Closed Operable M B A K J B AREA WHERE TERMINAL IS NOT PERMITTED AIR SUPPLY INLET VENT TERMINAL US Installations1 A= Clearance above grade, veranda, porch, deck or balcony B= Clearance to window or door that may be opened C= Clearance to permanently closed window D= Vertical clearance to ventilated soffit located above the terminal within a horizontal distance of 2 feet (610mm) from the center line of the terminal E= Clearance to unventilated soffit F= Clearance to outside corner G= Clearance to inside corner H= Clearance to each side of center line ex­ tended above meter / regulator assembly I= Clearance to service regulator vent outlet Clearance to non-mechanical air supply inlet to building or the com­ bustion air inlet to any other ap­ pliance J= K= L= Clearance to mechanical air sup­ ply inlet Clearance above paved sidewalk or paved driveway located on public property 12 inches (305mm) or 12 in. (305mm) above average snow accumulation. 1 In 12 inches (305mm) or 12 in. (305mm) above average snow accumulation. 6 inches (152mm) for appliances <10,000 6 inches (152mm) for appliances <10,000 Btuh (3kw), 9 inches (228mm) for ap­ Btuh (3kw), 12 inches (305mm) for pliances > 10,000 Btuh (3kw) and <50,000 appliances > 10,000 Btuh (3kw) and Btuh (15 kw), 12 inches (305mm) for ap­ <100,000 Btuh (30kw), 36 inches (.9m) pliances > 50,000 Btuh (15kw) for appliances > 100,000 Btuh (30kw) * 12” * 12” * Equal to or greater than soffit depth * Equal to or greater than soffit depth * No minimum to outside corner * * 3 feet (.9m) * Equal to or greater than soffit depth * Equal to or greater than soffit depth * No minimum to outside corner * 3 feet (.9m) within a height 15 feet (4.5m) above the meter / regulator assembly 3 feet (.9m) within a height 15 feet (4.5m) above the meter / regulator assembly 3 feet (.9m) 6 inches (152mm) for appliances <10,000 6 inches (152mm) for appliances <10,000 Btuh (3kw), 9 inches (228mm) for ap­ Btuh (3kw), 12 inches (305mm) for pliances > 10,000 Btuh (3kw) and <50,000 appliances > 10,000 Btuh (3kw) and Btuh (15 kw), 12 inches (305mm) for ap­ <100,000 Btuh (30kw), 36 inches (.9m) pliances > 50,000 Btuh (15kw) for appliances > 100,000 Btuh (30kw) 3 feet (.9m) above if within 10 feet 6 feet (1.8m) (3m) horizontally 7 feet (2.1m)† * 7 feet (2.1m) M = Clearance under veranda, porch, deck or balcony 2 In Canadian Installations2 *12 inches (305mm)‡ accordance with the current ANSI Z223.1/NFPA 54 Natural Fuel Gas Code accordance with the current CSA B149.1, Natural Gas and Propane Installation Code † A vent shall not terminate directly above a sidewalk or paved driveway that is located between two single family dwellings and serves both dwellings. ‡ Permitted only if veranda, porch, deck or balcony is fully open on a minimum of two sides beneath the floor. Lennox recommends avoiding this location if possible. FIGURE 28 Page 28 12 inches (305mm)‡ *For clearances not specified in ANSI Z223.1/NFPA 54 or CSA B149.1, clearance will be in accordance with local installation codes and the requirements of the gas supplier and these installation instructions.” Details of Intake and Exhaust Piping Terminations for Direct Vent Installations NOTE - In Direct Vent installations, combustion air is taken from outdoors and flue gases are discharged to outdoors. NOTE - Flue gas may be slightly acidic and may adversely affect some building materials. If any vent termination is used and the flue gasses may impinge on the building ma­ terial, a corrosion-resistant shield (minimum 24 inches square) should be used to protect the wall surface. If the optional tee is used, the protective shield is recommended. The shield should be constructed using wood, plastic, sheet metal or other suitable material. All seams, joints, cracks, etc. in the affected area should be sealed using an appropriate sealant. See figure 36. Intake and exhaust pipes may be routed either horizontally through an outside wall or vertically through the roof. In at­ tic or closet installations, vertical termination through the roof is preferred. Figures 31 through 37 show typical ter­ minations. 1. Intake and exhaust terminations are not required to be in the same pressure zone. You may exit the intake on one side of the structure and the exhaust on another side (figure 29). You may exit the exhaust out the roof and the intake out the side of the structure (figure 30). 2. Intake and exhaust pipes should be placed as close together as possible at termination end (refer to il­ lustrations). Maximum separation is 3” (76mm) on roof terminations and 6” (152mm) on side wall termina­ tions. NOTE - When venting in different pressure zones, the maximum separation requirement of intake and ex­ haust pipe DOES NOT apply. 3. On roof terminations, the intake piping should termi­ nate straight down using two 90° elbows (See figure 31). 4. Exhaust piping must terminate straight out or up as shown. A reducer may be required on the exhaust pip­ ing at the point where it exits the structure to improve the velocity of exhaust away from the intake piping. See table 17. TABLE 17 NOTE - Care must be taken to avoid recirculation of exhaust back into intake pipe. Exiting Exhaust and Intake Vent (different pressure zones) Exhaust Pipe FIGURE 29 Exiting Exhaust and Intake Vent (different pressure zones) Roof Terminated Exhaust Pipe Exhaust Pipe Size Termination Pipe Size *045 and *070 *090 110 2” (51mm), 2-1/2” (64mm), 3” (76mm) 3” (76mm) 1-1/2” (38mm) 2” (51mm) 2” (51mm) Inlet Air (Minimum 12 in. 305 MM) above grade or snow accumulation Furnace FIGURE 30 Inches(mm) EXHAUST PIPE TERMINATION SIZE REDUCTION ML193 MODEL Inlet Air (Minimum 12 in. 305 MM) above grade or snow accumulation Furnace 3”(76mm) MAX. SIZE TERMINATION PIPE PER TABLE 17. UNCONDITIONED ATTIC SPACE 8” (203mm) MIN *ML193DF-045, -070 and -090 units with the flush-mount termination must use the 1-1/2”accelerator supplied with the kit. 1/2” (13mm) FOAM INSULATION IN UNCONDITIONED SPACE 12” (305mm) ABOVE AVERAGE SNOW ACCUMULATION 5. On field-supplied terminations for side wall exit, ex­ haust piping may extend a maximum of 12 inches (305mm) for 2” PVC and 20 inches (508mm) for 3” (76mm) PVC beyond the outside wall. Intake piping should be as short as possible. See figure 36. 6. On field supplied terminations, a minimum distance between the end of the exhaust pipe and the end of the intake pipe without a termination elbow is 8” and a minimum distance of 6” with a termination elbow. See figure 36. Page 29 3” (76mm) OR 2” (51mm) PVC PROVIDE SUPPORT FOR INTAKE AND EXHAUST LINES DIRECT VENT ROOF TERMINATION KIT (15F75 or 44J41) FIGURE 31 7. If intake and exhaust piping must be run up a side wall to position above snow accumulation or other ob­ structions, piping must be supported. At least one bracket must be used within 6” from the top of the el­ bow and then every 24” (610mm) as shown in figure 36, to prevent any movement in any direction. When exhaust and intake piping must be run up an outside wall, the exhaust piping must be terminated with pipe sized per table 17.The intake piping may be equipped with a 90° elbow turndown. Using turndown will add 5 feet (1.5m) to the equivalent length of the pipe. 8. A multiple furnace installation may use a group of up to four terminations assembled together horizontally, as shown in figure 34. EXHAUST VENT INTAKE AIR 18” MAX. (457mm) INTAKE Minimum Above Average Snow Accumulation 12” (305mm) Min. above grade or average snow ac­ INTAKE cumulation. AIR Inches (mm) Side View optional intake elbow OPTIONAL VENT TERMINATION FOR MULTIPLE UNIT INSTALLATION OF DIRECT VENT WALL TERMINATION KIT (30G28 or 81J20) FIGURE 34 2” EXTENSION FOR 2” PVC PIPE1” EXTENSION FOR 3” PVC PIPE FLASHING (Not Furnished) FURNACE EXHAUST PIPE 4'' FURNACE INTAKE PIPE SHEET METAL STRAP (Clamp and sheet metal strap must be field installed to support the weight of the termination kit.) GLUE EXHAUST END FLUSH INTO TERMINATION CLAMP FIELD-PROVIDED REDUCER MAY BE REQUIRED TO ADAPT LARGER VENT PIPE SIZE TO TERMINATION FLAT SIDE FLUSH-MOUNT SIDE WALL TERMINATION 51W11 (US) or 51W12 (Canada) FIGURE 35 FIGURE 32 FIELD-PROVIDED REDUCER MAY BE REQUIRED TO ADAPT LARGER VENT PIPE SIZE TO TERMINA­ TION OUTSIDE WALL EXHAUST AIR 1-1/2” (38mm) accelerator provided on 71M80 & 44W92 kits for ML193DF045P36B- & 070P36B INTAKE AIR EXHAUST AIR CLAMP (Not Furnished) 1-1/2” ACCELERATOR (all -45, -070 and -090 units) DIRECT VENT CONCENTRIC ROOFTOP TERMINATION 71M80, 69M29 or 60L46 (US) 41W92 or 41W93 (Canada) INTAKE AIR Front View EXHAUST VENT 1-1/2” (38mm) accelerator provided on 71M80 & 44W92 kits for ML193DF045P36B- & 070P36B 12” (305mm) 12” (305mm) 5-1/2” (140mm) 5” (127mm) INTAKE 12” (305mm) Min. AIR above grade or average snow ac­ cumulation. GRADE DIRECT VENT CONCENTRIC WALL TERMINATION 71M80, 69M29 or 60L46 (US) 41W92 or 41W93 (Canada) FIGURE 33 Page 30 FIELD FABRICATED WALL TERMINATION NOTE − FIELD−PROVIDED REDUCER MAY BE REQUIRED TO ADAPT LARGER VENT PIPE SIZE TO TERMINATION 2” (51mm) 3” (76mm) Vent Pipe Vent Pipe D D B Intake Elbow C1 A B C2 A STRAIGHT APPPLICATION A− Minimum clearance above grade or average snow accumulation 12” (305 mm) 12” (305 mm) B− Maximum horizontal separation between intake and exhaust 6” (152 mm) 6” (152 mm) C1 -Minimum from end of exhaust to inlet of intake 8” (203 mm) 8” (203 mm) C2 -Minimum from end of exhaust to inlet of intake 6” (152 mm) 6” (152 mm) D− Maximum exhaust pipe length 20” (508 mm) 12” (305 mm) E− Maximum wall support distance from top of each 6” (152 mm) pipe (intake/exhaust) * WALL SUPPORT D D E E B B A C1 EXTENDED APPLICATION A C2 6” (152 mm) See venting table 14 for maximum venting lengths with this arrangement. * Use wall support every 24” (610 mm). Use two wall supports if extension is greater than 24” (610 mm) but less than 48” (1219 mm). NOTE − One wall support must be within 6” (152 mm) from top of each pipe (intake and exhaust) to prevent movement in any direction. ALTERNATE TERMINATIONS (TEE & FORTY−FIVE DEGREE ELBOWS ONLY) B D B Exhaust D 1 C C 2 Intake Elbow A 3 1 E Intake B B− Horizontal separation between intake and exhaust C− Minimum from end of exhaust to inlet of intake A Front View of Intake and Exhaust D A− Clearance above grade or average snow accumulation D− Exhaust pipe length 2” (51MM) Vent Pipe 3” (76MM) Vent Pipe 12” (305 mm) Min. 12” (305 mm) Min. 6” (152 mm) Min. 6” (152 mm) Min. 24” (610 mm) Max. 24” (610 mm) Max. 9” (227 mm) Min. 9” (227 mm) Min. 12” (305 mm) Min. 12” (305 mm) Min. 16” (405 mm) Max. 20” (508 mm) Max. E− Wall support distance from top of each pipe 6” (152 mm) Max. (intake/exhaust) 6” (152 mm) Max. Exhaust 12” C 2 A 1 The exhaust termination tee should be connected to the 2” or 3” PVC flue pipe as shown in the illustration. Do not use an accelerator in applications that include an exhaust termination tee. The accelerator is not required. 2 As required. Flue gas may be acidic and may adversely affect some building materials. If a side wall vent termination is used and flue gases will impinge on the building materials, a corrosion−resistant shield (24 inches square) should be used to protect the wall surface. If optional tee is used, the protective shield is recommended. The shield should be constructed using wood, sheet metal or other suitable material. All seams, joints, cracks, etc. in affected area, should be sealed using an appropriate sealant. 3 Exhaust pipe 45° elbow can be rotated to the side away from the combustion air inlet to direct exhaust away from adjacent property. The exhaust must never be directed toward the combustion air inlet. FIGURE 36 Page 31 2. On field supplied terminations for side wall exit, ex­ haust piping may extend a maximum of 12 inches (305mm) for 2” PVC and 20 inches (508mm) for 3” (76mm) PVC beyond the outside wall. ML193DF DIRECT VENT APPLICATION STRAIGHT-CUT OR USING EXISTING CHIMNEY ANGLE-CUT IN DIRECTION OF ROOF SLOPE * 8” - 12” (203mm - 305mm) Minimum 12” (305MM) above chimney top plate or average snow accumulation 3” - 8” (76mm203mm) EXHAUST VENT 1/2” (13mm) WEATHERPROOF INSULATION 3. If exhaust piping must be run up a side wall to position above snow accumulation or other obstructions, pip­ ing must be supported every 24 inches (610mm). When exhaust piping must be run up an outside wall, any reduction in exhaust pipe size must be done after the final elbow. 4. Distance between exhaust pipe terminations on mul­ tiple furnaces must meet local codes. SHOULDER OF FITTINGS PROVIDE SUPPORT OF PIPE ON TOP PLATE INTAKE PIPE INSULATION (optional) SHEET METAL TOP PLATE ALTERNATE INTAKE PIPE 3” - 8” (76mm203mm) INSULATE TO FORM SEAL EXTERIOR PORTION OF CHIMNEY ML193DF NON-DIRECT VENT APPLICATION USING EXISTING CHIMNEY *SIZE TERMINATION PIPE PER TABLE 17. STRAIGHT-CUT OR ANGLE-CUT IN DIRECTION OF ROOF SLOPE SIZE TERMINATION PIPE PER TABLE 17. NOTE - Do not discharge exhaust gases directly into any chimney or vent stack. If ver­ tical discharge through an existing unused chimney or stack is required, insert piping inside chimney until the pipe open end is above top of chimney and terminate as illus­ trated. In any exterior portion of chimney, the exhaust vent must be insulated. FIGURE 37 Details of Exhaust Piping Terminations for Non‐Direct Vent Applications Exhaust pipes may be routed either horizontally through an outside wall or vertically through the roof. In attic or closet installations, vertical termination through the roof is pre­ ferred. Figures 38 through 39 show typical terminations. 1. Exhaust piping must terminate straight out or up as shown. The termination pipe must be sized as listed in table 17.The specified pipe size ensures proper ve­ locity required to move the exhaust gases away from the building. 12” (305mm) ABOVE AVE. SNOW ACCUMULATION 3” - 8” (76mm203mm) Minimum 12” (305MM) above chimney top plate or average snow accumulation SHOULDER OF FITTINGS PROVIDE SUPPORT OF PIPE ON TOP PLATE SHEET METAL TOP PLATE INSULATE TO FORM SEAL 3” - 8” (76mm203mm) EXTERIOR PORTION OF CHIMNEY NOTE - Do not discharge exhaust gases directly into any chimney or vent stack. If ver­ tical discharge through an existing unused chimney or stack is required, insert piping inside chimney until the pipe open end is above top of chimney and terminate as illus­ trated. In any exterior portion of chimney, the exhaust vent must be insulated. SIZE TERMINATION PIPE PER TABLE 17. FIGURE 39 1/2” (13mm) FOAM INSULATION 3” (76mm) OR 2” (51mm) PVC EXHAUST VENT 1/2” (13mm) WEATHERPROOF INSULATION UNCONDITIONED ATTIC SPACE PROVIDE SUPPORT FOR EXHAUST LINES NON-DIRECT VENT ROOF TERMINATION KIT (15F75 or 44J41) FIGURE 38 Page 32 Condensate Piping This unit is designed for either right‐ or left‐side exit of con­ densate piping. Refer to figures 40 and 42 for condensate trap locations. NOTE - If necessary the condensate trap may be installed up to 5’ away from the furnace. Use PVC pipe to connect trap to furnace condensate outlet. Piping from furnace must slope down a minimum of 1/4” per ft. toward trap. CONDENSATE TRAP AND PLUG LOCATIONS 4 - Install drain trap using appropriate PVC fittings, glue all joints. Glue the provided drain trap as shown in fig­ ures 46 and 47. Route the condensate line to an open drain. 5 - Figure 44 shows the furnace and evaporator coil using a separate drain. If necessary, the condensate line from the furnace and evaporator coil can drain togeth­ er. See figures 45 and 43. The field provided vent must be a minimum 1” to a maximum 2” length above the condensate drain outlet connection. NOTE - If necessary the condensate trap may be installed up to 5 feet away from the furnace. Piping from furnace must slope down a minimum of 1/4” per ft. toward trap. NOTE - Appropriately sized tubing and barbed fitting may be used for condensate drain. Attach to the drain on the trap using a hose clamp. See figure 41. Trap (same on right side) 1-1/2 in. Field Provided Drain Components Plug (same on left side) Elbow Barbed Fitting Tubing Hose Clamp FIGURE 41 FIGURE 40 1 - Determine which side condensate piping will exit the unit, location of trap, field-provided fittings and length of PVC pipe required to reach available drain. 2 - For furnaces with a 1/2” drain connection use a 3/8 al­ len wrench and remove plug (figure 40) from the cold end header box at the appropriate location on the side of the unit. Install field-provided 1/2 NPT male fitting into cold end header box. For furnaces with a 3/4” drain connection use a large flat head screw driver or a 1/2” drive socket extension and remove plug. Install provided 3/4 NPT street elbow fitting into cold end header box. Use Teflon tape or appropriate pipe dope. 3 - Install the cap over the clean out opening at the base of the trap. Secure with clamp. See figures 46 and 47. 6 - If unit will be started immediately upon completion of installation, prime trap per procedure outlined in Unit Start-Up section. Condensate line must slope downward away from the trap to drain. If drain level is above condensate trap, condensate pump must be used. Condensate drain line should be routed within the conditioned space to avoid freezing of condensate and blockage of drain line. If this is not possible, a heat cable kit may be used on the condensate trap and line. Heat cable kit is avail­ able from Lennox in various lengths; 6 ft. (1.8m) - kit no. 26K68; 24 ft. (7.3m) - kit no. 26K69; and 50 ft. (15.2m) - kit no. 26K70. Page 33 CAUTION Do not use copper tubing or existing copper condensate lines for drain line. CONDENSATE TRAP LOCATION (shown with right side exit of condensation) ML193DF with Evaporator Coil Using a Separate Drain Field Provided Vent 1” min. 2” max. above condensate drain. Trap can be installed a maxi­ mum of 5ft. from furnace (*PVC only) Field Provided Vent 1” min. 2” max. above condensate drain. Condensate Drain Connection 1” min. 2” max. 5’ max. Evaporator Drain Line (vent required) Drain to drain *Piping from furnace must slope down a minimum 1/4” per ft. toward trap FIGURE 42 FIGURE 44 IMPORTANT When combining the furnace and evaporator coil drains together, the A/C condensate drain outlet must be vented to relieve pressure in or­ der for the furnace pressure switch to operate properly. Condensate Trap With Optional Overflow Switch From Evaporator Coil Field Provided Vent 1” min. 2” max. above condensate drain. ML193DF with Evaporator Coil Using a Common Drain Field Provided Vent 1” min. 2” max. above condensate drain. FurnaceCondensate Drain Connection Optional Condensate Drain Connection Evaporator Drain Line (vent required) FIGURE 43 FIGURE 45 Page 34 TRAP / DRAIN ASSEMBLY USING 1/2” PVC OR 3/4” PVC COLD END HEADER BOX WITH 3/4” DRAIN CONNECTION Optional Condensate Drain Connection Adapter 3/4 inch slip X 3/4 inch mpt (not furnished) 90° Street Elbow 3/4 inch PVC (not furnished) Adapter 3/4 inch slip X 3/4 inch mpt (not furnished) Condensate Drain Connection In Unit 90° Street Elbow 3/4 inch PVC ( furnished) 1 (25 mm) Min. 2 (50 mm) Max. Above Top Of Condensate Drain Connection In Unit Vent Condensate Drain Connection In Unit 5 Feet Maximum 90° Elbow 3/4 inch PVC (Not Furnished) To Trap Optional DrainPiping FromTrap 3/4 inch PVC Pipe (Not Furnished) 1/2 inch PVC Pipe (Not Furnished) Coupling 3/4 inch slip X slip (Not Furnished) Drain Assembly for 1/2 inch Drain Pipe 1/2 inch PVC Pipe (Not Furnished) Drain Trap Assembly (Furnished) 90° Elbow 1/2 inch PVC (Not Furnished) To Drain Drain Assembly for 3/4 inch Drain Pipe Drain Trap Clean Out 90° Elbow 3/4 inch PVC (Not Furnished) 90° Elbow 3/4 inch PVC (Not Furnished) To Coupling 3/4 inch slip X slip Drain (Not Furnished) To Drain DrainTrap Assembly with 1/2 inch Piping 1 (25 mm) Min. 2 (50 mm) Max. Above Top Of Condensate Drain Connection In Unit DrainTrap Assembly (Furnished) Vent 1 (25 mm) Min. 2 (50 mm) Max. Above Top Of Condensate Drain Connection In Unit Vent 3/4 inch 1/2 inch 7 (178) DrainTrap Assembly with 3/4 inch Piping Condensate Drain Connection In Unit Condensate Drain Connection In Unit To Drain To Drain FIGURE 46 Page 35 TRAP / DRAIN ASSEMBLY USING 1/2” PVC OR 3/4” PVC Optional Condensate Drain Connection Adapter 1/2 inch slip X 1/2 inch mpt (Not Furnished) 90° Street Elbow 1/2 inch PVC (Not Furnished) 1 (25 mm) Min. 2 (50 mm) Max. Above Top Of Condensate Drain Connection In Unit Condensate Drain Connection In Unit 90° Street Elbow 1/2 inch PVC (Furnished) Adapter 1/2 inch slip X 1/2 inch mpt (Not Furnished) Condensate Drain Connection In Unit Vent 5 Feet Maximum 90° Elbow 1/2 inch PVC (Not Furnished) To Trap Optional Drain Piping From Trap 1/2 inch PVC Pipe (Not Furnished) 1/2 inch PVC Pipe (Not Furnished) Coupling 1/2 inch slip X slip (Not Furnished) Drain Assembly for 1/2 inch Drain Pipe 1/2 inch PVC Pipe (Not Furnished) Drain Trap Assembly (Furnished) 90° Elbow 1/2 inch PVC (Not Furnished) To Drain Drain Assembly for 3/4 inch Drain Pipe Drain Trap Clean Out 90° Elbow 3/4 inch PVC (Not Furnished) To Drain 90° Elbow 3/4 inch PVC (Not Furnished) Drain Trap Assembly with 3/4 inch Piping To Coupling 3/4 inch slip X slip Drain (Not Furnished) Drain Trap Assembly with 1/2 inch Piping 1 (25 mm) Min. 2 (50 mm) Max. Above Top Of Condensate Drain Connection In Unit Drain Trap Assembly (Furnished) Vent 1 (25 mm) Min. 2 (50 mm) Max. Above Top Of Condensate Drain Connection In Unit Vent 3/4 inch 1/2 inch 7 (178) Drain Trap Assembly with 3/4 inch Piping Condensate Drain Connection In Unit Condensate Drain Connection In Unit To Drain To Drain FIGURE 47 Page 36 III-START‐UP A-Preliminary and Seasonal Checks 1 - Inspect electrical wiring, both field and factory installed for loose connections. Tighten as required. 2 - Check voltage at disconnect switch. Voltage must be within range listed on the nameplate. If not, consult the power company and have voltage condition corrected before starting unit. 3 - Inspect condition of condensate traps and drain as­ sembly. Disassemble and clean seasonally. B-Heating Start‐Up BEFORE LIGHTING the unit, smell all around the furnace area for gas. Be sure to smell next to the floor because some gas is heavier than air and will settle on the floor. The gas valve on the ML193DF is equipped with a gas con­ trol switch. Use only your hand to move the switch. Never use tools. If the the switch will not move by hand, replace the valve. Do not try to repair it. Force or attempted repair may result in a fire or explosion. Placing the furnace into operation: ML193DF units are equipped with a SureLight ignition sys­ tem. Do not attempt to manually light burners on this fur­ nace. Each time the thermostat calls for heat, the burners will automatically light The ignitor does not get hot when there is no call for heat on units with SureLightt ignition system. Priming Condensate Trap The condensate trap should be primed with water prior to start-up to ensure proper condensate drainage. Either pour 10 fl. oz. (300 ml) of water into the trap, or follow these steps to prime the trap: 1 - Follow the lighting instructions to place the unit into op­ eration. 2 - Set the thermostat to initiate a heating demand. 3 - Allow the burners to fire for approximately 3 minutes. 4 - Adjust the thermostat to deactivate the heating de­ mand. 5 - Wait for the combustion air inducer to stop. Set the thermostat to initiate a heating demand and again al­ low the burners to fire for approximately 3 minutes. 6 - Adjust the thermostat to deactivate the heating de­ mand and again wait for the combustion air inducer to stop. At this point, the trap should be primed with suffi­ cient water to ensure proper condensate drain opera­ tion. WARNING If you do not follow these instructions exactly, a fire or explosion may result causing property damage, personal injury or death. Gas Valve Operation (Figure 48) 1 - STOP! Read the safety information at the beginning of this section. 2 - Set the thermostat to the lowest setting. 3 - Turn off all electrical power to the unit. 4 - This furnace is equipped with an ignition device which automatically lights the burners. Do not try to light the burners by hand. 5 - Remove the upper access panel. 6 - Move gas valve switch to OFF. See figure 48. 7 - Wait five minutes to clear out any gas. If you then smell gas, STOP! Immediately call your gas supplier from a neighbor's phone. Follow the gas supplier's instruc­ tions. If you do not smell gas go to next step. 8 - Move gas valve switch to ON. See figure 48. MANIFOLD PRESSURE ADJUSTMENT SCREW (under barbed fitting) MANIFOLD PRESSURE OUTLET INLET PRESSURE PORT GAS VALVE SHOWN IN ON POSITION FIGURE 48 9 - Replace the upper access panel. 10- Turn on all electrical power to to the unit. 11- Set the thermostat to desired setting. NOTE - When unit is initially started, steps 1 through 11 may need to be repeated to purge air from gas line. 12- If the appliance will not operate, follow the instructions “Turning Off Gas to Unit” and call your service techni­ cian or gas supplier. Turning Off Gas to Unit 1 - Set the thermostat to the lowest setting. 2 - Turn off all electrical power to the unit if service is to be performed. 3 - Remove the upper access panel. 4 - Move gas valve switch to OFF. 5 - Replace the upper access panel. Failure To Operate If the unit fails to operate, check the following: 1 - Is the thermostat calling for heat? 2 - Are access panels securely in place? 3 - Is the main disconnect switch closed? 4 - Is there a blown fuse or tripped breaker? 5 - Is the filter dirty or plugged? Dirty or plugged filters will cause the limit control to shut the unit off. 6 - Is gas turned on at the meter? 7 - Is the manual main shut‐off valve open? 8 - Is the internal manual shut‐off valve open? 9 - Is the unit ignition system in lockout? If the unit locks out again, inspect the unit for blockages. Page 37 available through Lennox under part number 31B2001. See Corp. 8411-L10, for further details. IV-HEATING SYSTEM SERVICE CHECKS A-C.S.A. Certification All units are C.S.A. design certified without modifications. Refer to the ML193DF Operation and Installation Instruc­ tion Manual Information. WARNING Do not use matches, candles, flame or any other source of ignition to check for gas leaks. B-Gas Piping CAUTION D-Testing Gas Supply Pressure If a flexible gas connector is required or allowed by the authority that has jurisdiction, black iron pipe shall be installed at the gas valve and extend outside the furnace cabinet. The flexible connector can then be added between the black iron pipe and the gas supply line. Gas supply piping should not allow more than 0.5”W.C. drop in pressure between gas meter and unit. Supply gas pipe must not be smaller than unit gas connection. Compounds used on gas piping threaded joints should be resistant to action of liquefied petroleum gases. C-Testing Gas Piping IMPORTANT In case emergency shutdown is required, turn off the main shut‐off valve and disconnect the main power to unit. These controls should be properly labeled by the installer. When pressure testing gas lines, the gas valve must be dis­ connected and isolated. Gas valves can be damaged if subjected to more than 0.5psig (14” W.C.). See figure 49. MANUAL MAIN SHUT-OFF VALVE WILL NOT HOLD NORMAL TEST PRESSURE 1/8” N.P.T. PLUGGED TAP FURNACE ISOLATE GAS VALVE CAP FIGURE 49 When checking piping connections for gas leaks, use pre­ ferred means. Kitchen detergents can cause harmful cor­ rosion on various metals used in gas piping. Use of a spe­ cialty Gas Leak Detector is strongly recommended. It is When testing supply gas pressure, use the 1/8” N.P.T. plugged tap or pressure post located on the gas valve to facilitate test gauge connection. See figure 48. Check gas line pressure with unit firing at maximum rate. Low pres­ sure may result in erratic operation or underfire. High pres­ sure can result in permanent damage to gas valve or over­ fire. On multiple unit installations, each unit should be checked separately, with and without units operating. Supply pres­ sure must fall within range listed in table 19. E-Check Manifold Pressure After line pressure has been checked and adjusted, check manifold pressure. Move pressure gauge to outlet pres­ sure tap located on unit gas valve (GV1). Checks of manifold pressure are made as verification of proper regulator adjustment. IMPORTANT For safety, connect a shut‐off valve between the manometer and the gas tap to permit shut off of gas pressure to the manometer. 1 - Remove the threaded plug from the outlet side of the gas valve and install a field-provided barbed fitting. Connect to a manometer to measure manifold pres­ sure. 2 - Start unit and allow 5 minutes for unit to reach steady state. 3 - While waiting for the unit to stabilize, observe the flame. Flame should be stable and should not lift from burner. Natural gas should burn blue. 4 - After allowing unit to stabilize for 5 minutes, record manifold pressure and compare to value given in table 19. NOTE - Shut unit off and remove manometer as soon as an accurate reading has been obtained. Take care to remove barbed fitting and replace threaded plug. Page 38 F- Proper Gas Flow (Approximate) G- Proper Combustion Gas Flow (Approximate) Furnace should operate at least 15 minutes with correct manifold pressure and gas flow rate before checking com­ bustions. Take sample beyond the flue outlet and compare to table 20. TABLE 18 GAS METER CLOCKING CHART Seconds for One Revolution Natural LP ML193 Unit 1 cu ft 2 cu ft 1 cu ft 2 cu ft Dial Dial Dial DIAL -045 80 160 200 400 -070 55 110 136 272 -090 41 82 102 204 -110 33 66 82 164 Natural-1000 btu/cu ft TABLE 20 ML193 Unit -045 -070 -090 -110 LP-2500 btu/cu ft Pressure in.wg. Nat. Gas All sizes L.P. Gas All sizes 8.6 - 9.3 NOTE - In Canada, certification for installations at eleva­ tions over 4500 feet (1372 m) is the jurisdiction of local au­ thorities. ML193DF-1 through -6 units require no manifold pressure adjustments for operation at altitudes up to 10,000 feet (3048 m) above sea level. However, -7 units and later in­ stalled at altitude of 4501 - 10,000 feet (1373 to 3048m) re­ quire a pressure switch change which can be ordered sep­ arately and manifold de-rate. See table 19 or table 21 for manifold pressures at varying altitudes. Table 22 lists con­ version kit and pressure switch requirements at varying al­ titudes. The combustion air pressure switch is factory-set and re­ quires no adjustment. Supply Pressure in.wg. Manifold 7.2 - 7.9 H- High Altitude TABLE 19 Manifold and Supply Pressure (Outlet) inches w.c. At All Altitudes For -1 Through -6 Units Model Input Sizes CO2% For L.P. The carbon monoxide reading should not exceed 50 ppm. NOTE - To obtain accurate reading, shut off all other gas appliances connected to meter. Furnace should operate at least 5 minutes before checking gas flow. Determine time in seconds for two revolutions of gas through the meter. (Two revolutions assures a more accurate time). Divide by two and compare to time in table 18. If manifold pressure matches table 19 and rate is incor­ rect, check gas orifices for proper size and restriction. Re­ move temporary gas meter if installed. Fuel CO2% For Nat Min. Max. 3.5 4.5 13.0 10.0 11.0 13.0 TABLE 21 Manifold and Supply Line Pressure 0-10,000ft. For -7 Units and Later Manifold Pressure in. wg. ML193 Unit All Sizes Gas Supply Line Pressure in. w.g. 0 - 10000 ft. 0-4500 ft. 4501-5500 ft. 5501-6500 ft. 6501 7500ft. 7501 - 10000ft. Natural 3.5 3.3 3.2 3.1 3.5 4.5 13.0 LP/propane 10.0 9.4 9.1 8.9 10.0 11.0 13.0 NOTE - A natural to L.P. propane gas changeover kit is necessary to convert this unit. Refer to the changeover kit installation instruction for the conversion procedure. TABLE 22 Conversion Kit and Pressure Switch Requirements at Varying Altitudes ML193 Unit -045 -070 -090 -110 Natural to LP/Propane High Altitude Natural Burner Ori­ fice Kit LP/Propane to Natural 0 - 7500 ft (0 - 2286m) 7501 - 10,000 ft (2286 - 3038m) 0 - 7500 ft (0 - 2286m) 4501 - 7500 ft (1373 - 2286m) 7501 -10,000 ft (2286 - 3048m) *69W73 73W37 *73W81 93W87 93W88 High Altitude Pressure Switch * Conversion requires installation of a gas valve manifold spring which is provided with the gas conversion kit. Pressure switch is factory set. No adjustment necessary. All models use the factory-installed pressure switch from 0-4500 feet (0-1370 m). Page 39 I-Flame Signal V-TYPICAL OPERATING CHARACTERISTICS A transducer (Part #78H5401 available from Lennox Re­ pair Parts) is required to measure flame signal if meter used will not read a low micro amp signal. Seefigure50. The transducer converts microamps to volts on a 1:1 con­ version. Flame signal is shown in table 23. A digital readout meter must be used. The transducer plugs into most me­ ters. A-Blower Operation and Adjustment 1 - Blower operation is dependent on thermostat control system. 2 - Generally, blower operation is set at thermostat sub­ base fan switch. With fan switch in ON position, blower operates continuously. With fan switch in AUTO posi­ tion, blower cycles with demand or runs continuously while heating or cooling circuit cycles. 3 - Depending on the type of indoor thermostat, blower and entire unit will be off when the system switch is in OFF position. B-Temperature Rise Temperature rise depends on unit input, blower speed, blower horsepower and static pressure as marked on the unit rating plate. The blower speed must be set for unit op­ eration within the range of “TEMP. RISE °F” listed on the unit rating plate. To Measure Temperature Rise: TABLE 23 Normal Flame Signal 1.50 Microamps Low Flame Signal 1.40 Microamps Drop Out Signal = 0.50 Microamps To Measure Flame Signal: 1 - Set the volt meter to the DC voltage scale. Insert trans­ ducer into the VDC and common inputs. Observe cor­ rect polarities. Failure to do so results in negative (-) values. 2 - Turn off supply voltage to control. 3 - Disconnect ignition control flame sensor wire from the flame sensor. 4 - Connect (-) lead of the transducer to flame sensor. 5 - Connect (+) lead of transducer to the ignition control sensor wire. 6 - Turn supply voltage on and close thermostat contacts to cycle system. 7 - When main burners are in operation for two minutes, take reading. Remember 1 DC volt = 1 DC microamp. NOTE-MUST USE DIGITAL METER SET DIAL TO MEASURE VDC (+) (+) TO IGNITION CONTROL SENSOR WIRE (-) (-) TO FLAME SENSOR FIGURE 50 TRANSDUCER PART #78H5401 RED COLLAR INDICATES POSITIVE LEAD 1 - Place plenum thermometers in the supply and return air plenums. Locate supply air thermometer in the first horizontal run of the plenum where it will not pick up ra­ diant heat from the heat exchanger. 2 - Set thermostat for heat call. Unit must operate on sec­ ond-stage heat. 3 - After plenum thermometers have reached their high­ est and steadiest readings, subtract the two readings. The difference should be in the range listed on the unit rating plate. If the temperature is too low, decrease blower speed. If temperature is too high, first check the firing rate. Provided the firing rate is acceptable, in­ crease blower speed to reduce temperature. C-External Static Pressure 1 - Tap locations shown in figure 51. STATIC PRESSURE 2 - Punch a 1/4” diameter hole TEST in supply and return air ple­ nums. Insert manometer filter hose flush with inside edge of hole or insulation. Seal coil around the hose with perma­ gum. Connect the zero end of the manometer to the dis­ FIGURE 50 charge (supply) side of the system. On ducted sys­ tems, connect the other end of manometer to the return duct as above. 3 - With only the blower motor running and the evaporator coil dry, observe the manometer reading. Adjust blow­ er motor speed to deliver the air desired according to the job requirements. 4 - External static pressure drop must not be more than 0.8” W.C. in the heating mode and must not exceed 1.0” W.C in the cooling mode. 5 - Seal the hole when the check is complete. To change existing heat tap, turn off power then switch out speed tap with tap connected to ”PARK” . See unit diagram for blower motor tap colors for each speed. Page 40 TABLE 24 VI-MAINTENANCE WARNING Furnace Cabinet Width Filter Size 17-1/2” 16 x 25 x 1 (1) 21” ELECTRICAL SHOCK, FIRE, OR EXPLOSION HAZARD. Failure to follow safety warnings exactly could result in dangerous operation, serious injury, death or property damage. Improper servicing could result in dangerous opera­ tion, serious injury, death, or property damage. Before servicing, disconnect all electrical power to furnace. When servicing controls, label all wires prior to dis­ connecting. Take care to reconnect wires correctly. Verify proper operation after servicing. At the beginning of each heating season, system should be checked as follows by a qualified service technician: Blower Check the blower wheel for debris and clean if necessary. The blower motors are prelubricated for extended bearing life. No further lubrication is needed. WARNING The blower access panel must be securely in place when the blower and burners are operating. Gas fumes, which could contain carbon monoxide, can be drawn into living space resulting in personal inju­ ry or death. Exhaust and air intake pipes Check the exhaust and air intake pipes and all connections for tightness and to make sure there is no blockage. NOTE - After any heavy snow, ice or frozen fog event the furnace vent pipes may become restricted. Always check the vent system and remove any snow or ice that may be obstructing the plastic intake or exhaust pipes. Electrical 1 - Check all wiring for loose connections. 2 - Check for the correct voltage at the furnace (furnace operating). Correct voltage is 120VAC + 10% 3 - Check amp-draw on the blower motor with blower ac­ cess panel in place. Motor Nameplate__________Actual__________ Winterizing and Condensate Trap Care 1 - Turn off power to the furnace. 2 - Have a shallow pan ready to empty condensate water. 3 - Remove the clean out cap from the condensate trap and empty water. Inspect the trap then reinstall the clean out cap. Condensate Hose Screen (Figure 52) Check the condensate hose screen for blockage and clean if necessary. 1 - Turn off power to the unit. 2 - Remove hose from cold end header box. Twist and pull screen to remove. 3 - Inspect screen and rinse with tap water if needed. 4 - Reinstall screen and turn on power to unit. Filters Condensate Hose Screen All air filters are installed external to the unit. Filters should be inspected monthly. Clean or replace the filters when necessary to ensure proper furnace operation. Table 24 lists recommended filter sizes. IMPORTANT If a high­efficiency filter is being installed as part of this system to ensure better indoor air quality, the fil­ ter must be properly sized. High­efficiency filters have a higher static pressure drop than standard­ef­ ficiency glass/foam filters. If the pressure drop is too great, system capacity and performance may be re­ duced. The pressure drop may also cause the limit to trip more frequently during the winter and the indoor coil to freeze in the summer, resulting in an increase in the number of service calls. Before using any filter with this system, check the specifications provided by the filter manufacturer against the data given in the appropriate Lennox Product Specifications bulletin. Additional informa­ tion is provided in Service and Application Note ACC­00­2 (August 2000). Hose FIGURE 52 Cleaning Heat Exchanger If cleaning the heat exchanger becomes necessary, follow the below procedures and refer to figure 1 when disassem­ bling unit. Use papers or protective covering in front of fur­ nace while removing heat exchanger assembly. 1 - Turn off electrical and gas supplies to the furnace. 2 - Remove the furnace access panels. 3 - Disconnect the 2 wires from the gas valve. 4 - Remove gas supply line connected to gas valve. Re­ move gas valve/manifold assembly. 5 - Remove sensor wire from sensor. Disconnect 2‐pin plug from the ignitor. Page 41 6 - Disconnect wires from flame roll-out switches. 7 - Loosen clamps at vent elbow. Disconnect condensate drain tubing from flue collar. and remove the vent el­ bow. 8 - Remove four burner box screws at the vestibule panel and remove burner box. Set burner box assembly aside. NOTE - If necessary, clean burners at this time. Follow procedures outlined in Burner Cleaning section. 9 - Mark and disconnect all combustion air pressure tub­ ing from cold end header collector box. 10 - Mark and remove wires from pressure switches. Re­ move pressure switches. Keep tubing attached to pressure switches. 11 - Disconnect the plug from the combustion air inducer. Remove two screws which secure combustion air in­ ducer to collector box. Remove combustion air induc­ er assembly. Remove ground wire from vest panel. 12 - Remove electrical junction box from the side of the fur­ nace. 13 - Mark and disconnect any remaining wiring to heating compartment components. Disengage strain relief bushing and pull wiring and bushing through the hole in the blower deck. 14 - Remove the primary limit from the vestibule panel. 15 - Remove two screws from the front cabinet flange at the blower deck. Spread cabinet sides slightly to allow clearance for removal of heat exchanger. 16 - Remove screws along vestibule sides and bottom which secure vestibule panel and heat exchanger as­ sembly to cabinet. Remove two screws from blower rail which secure bottom heat exchanger flange. Re­ move heat exchanger from furnace cabinet. 17 - Back wash heat exchanger with soapy water solution or steam. If steam is used it must be below 275°F (135°C) . 18 - Thoroughly rinse and drain the heat exchanger. Soap solutions can be corrosive. Take care to rinse entire assembly. 19 - Reinstall heat exchanger into cabinet making sure that the clamshells of the heat exchanger assembly are resting on the support located at the rear of the cabi­ net. Remove the indoor blower to view this area through the blower opening. 20 - Re‐secure the supporting screws along the vestibule sides and bottom to the cabinet. Reinstall blower and mounting screws. 21 - Reinstall cabinet screws on front flange at blower deck. 22 - Reinstall the primary limit on the vestibule panel. 23 - Route heating component wiring through hole in blow­ er deck and reinsert strain relief bushing. 24 - Reinstall electrical junction box. 25 - Reinstall the combustion air inducer. Reconnect the combustion air inducer to the wire harness. 26 - Reinstall pressure switches and reconnect pressure switch wiring. 27 - Carefully connect combustion air pressure switch hos­ ing from pressure switches to proper stubs on cold end header collector box. 28 - Reinstall condensate trap. 29 - Reconnect exhaust piping and exhaust drain tubing. 30 - Reinstall burner box assembly in vestibule area. 31 - Reconnect flame roll-out switch wires. 32 - Reconnect sensor wire and reconnect 2-pin plug from ignitor. 33 - Secure burner box assembly to vestibule panel using four existing screws. Make sure burners line up in center of burner ports. 34 - Reinstall gas valve manifold assembly. Reconnect gas supply line to gas valve. 35 - Reconnect 2 wires to gas valve. 36 - Replace the blower compartment access panel. 37 - Refer to instruction on verifying gas and electrical con­ nections when re-establishing supplies. 38 - Follow lighting instructions to light and operate fur­ nace for 5 minutes to ensure that heat exchanger is clean and dry and that furnace is operating properly. 39 - Replace heating compartment access panel. Cleaning the Burner Assembly 1 - Turn off electrical and gas power supplies to furnace. Remove upper and lower furnace access panels. 2 - Disconnect the 2-pin plug from the gas valve. 3 - Remove the burner box cover. 4 - Disconnect the gas supply line from the gas valve. Re­ move gas valve/manifold assembly. 5 - Mark and disconnect sensor wire from the sensor. Dis­ connect 2‐pin plug from the ignitor at the burner box. 6 - Remove four screws which secure burner box assem­ bly to vest panel. Remove burner box from the unit. 7 - Use the soft brush attachment on a vacuum cleaner to gently clean the face of the burners. Visually inspect the inside of the burners and crossovers for any block­ age caused by foreign matter. Remove any blockage. 8 - Reconnect the sensor wire and reconnect the 2-pin plug to the ignitor wiring harness. 9 - Reinstall the burner box assembly using the existing four screws. Make sure that the burners line up in the center of the burner ports. 10 - Reinstall the gas valve manifold assembly. Reconnect the gas supply line to the gas valve. Reinstall the burn­ er box cover. 11 - Reconnect 2-pin plug to gas valve. 12 - Replace the blower compartment access panel. 13 - Refer to instruction on verifying gas and electrical con­ nections when re-establishing supplies. 14 - Follow lighting instructions to light and operate fur­ nace for 5 minutes to ensure that heat exchanger is clean and dry and that furnace is operating properly. 15 - Replace heating compartment access panel. Page 42 VII-WIRING DIAGRAM AND SEQUENCE OF OPERATION ML193DF With Integrated Control 100973 1 - When there is a call for heat, W1 of the thermostat en­ ergizes W of the furnace control with 24VAC. 2 - S10 primary limit switch and S47 rollout switch are closed. Call for heat can continue. 3 - The integrated contol (A92) energizes combustion air inducer B6. Combustion air inducer runs until S18 combustion air prove switch closes (switch must close within 2-1/2 minutes or control goes into 5 minute Watchguard Pressure Switch delay). Once S18 closes, a 15-second pre-purge follows. 4 - The integrated control (A92) energizes ignitor. A 20-second warm-up period begins. 5 - Gas valve opens for a 4-second trial for ignition 6 - Flame is sensed, gas valve remains open for the heat call. 7 - After 30-second delay, the integrated control (A92) energizes indoor blower B3. 8 - When heat demand is satisfied, W1 of the indoor ther­ mostat de-energizes W of the integrated control which de-energizes the gas valve. Combustion air inducer B6 continues a 5-second post-purge period, and in­ door blower B3 completes a selected OFF time delay. Page 43 Sequence of Operation Flow Chart - Integrated Control 100973 HEATING SEQUENCE OF OPERATION ABNORMAL HEATING MODE NORMAL HEATING MODE POWER ON GAS VALVE OFF. COMBUSTION AIR INDUCER OFF. INDOOR BLOWER DELAY OFF. LED #1 ON LED #2 ON (RESET CONTROL BY TURNING MAIN POWER OFF.) NO CONTROL SELF-CHECK OKAY? YES NO POLARITY REVERSED. LED #1 -- FAST FLASH LED #2 -- SLOW FLASH NO IMPROPER GROUND. LED #1 -- ALTERNATING FAST FLASH LED #2 -- ALTERNATING FAST FLASH IS POLARITY CORRECT? YES IS THERE A PROPER GROUND? YES NO LEDs SIGNAL FAST ALTERNATING FLASH. CONTROL WILL NOT RESPOND TO A CALL FOR HEATING UNTIL VOLTAGE RISES ABOVE 95 VOLTS. IS VOLTAGE ABOVE 90 VOLTS? YES ROLLOUT SWITCH CLOSED? GAS VALVE OFF. COMBUSTION AIR INDUCER ON. INDOOR BLOWER ON. LED #1 -- ON. LED #2 -- SLOW FLASH. SEQUENCE HOLDS UNTIL ROLLOUT SWITCH CLOSES AND POWER IS RESET OR T'STAT IS INTERRUPTED FOR MINIMUM OF 1 SECOND. NO YES BURNER OFF? GAS VALVE OFF. COMBUSTION AIR INDUCER ON. INDOOR BLOWER ON HEATING SPEED. LED #1 -- SLOW FLASH LED #2 -- OFF NO (Flame sensed without gas valve energized) YES NO NORMAL OPERATION: LED #1 -- SLOW FLASH LED #2 -- SLOW FLASH YES THERMOSTAT CALLS FOR HEAT: LED #1 -- FAST FLASH LED #2 -- FAST FLASH NO YES COMBUSTION AIR INDUCER OFF. INDOOR BLOWER ON LED #1 SLOW FLASH RATE LED #2 -- ON PRIMARY LIMIT SWITCH. CLOSED? YES NO IS COMBUSTION AIR PRESSURE SWITCH OPEN? YES GAS VALVE OFF. COMBUSTION AIR INDUCER OFF. INDOOR BLOWER OFF WITH DELAY. LED #1 OFF LED #2 SLOW FLASH (Sequence holds until pressure switch opens or thermostat resets control.) IS COMBUSTION AIR INDUCER ENERGIZED? YES HAS COMBUSTION AIR PRESSURE SWITCH CLOSED IN 2.5 MINUTES? NO YES CONTINUED NEXT PAGE Page 44 PRESSURE SWITCH IS IN WATCHGUARD MODE. GAS VALVE OFF. COMBUSTION AIR INDUCER OFF. INDOOR BLOWER OFF WITH DELAY. LED #1 -- OFF. LED #2 -- SLOW FLASH. IS 5‐MINUTE RESET PERIOD COMPLETE? YES HEATING SEQUENCE CONTINUED NORMAL HEATING MODE ABNORMAL HEATING MODE 15‐SECOND COMBUSTION AIR INDUCER PREPURGE INITIATED BY CLOSED PRESSURE SWITCH. YES NO IS VOLTAGE ABOVE 90 VOLTS? IGNITOR WARM‐UP -- 20 SECONDS. YES NO YES 4‐SECOND TRIAL FOR IGNITION. GAS VALVE OPENS. IGNITOR ENERGIZED FOR FIRST 3 SECONDS OF THE TRIAL. YES FLAME STABILIZATION PERIOD. 4 SECONDS LEDS SIGNAL ALTERNATING FAST FLASH UNTIL VOLTAGE IS ABOVE 95 VOLTS, THEN RESTARTS HEATING SEQUENCE. GAS VALVE OFF. COMBUSTION AIR INDUCER ON. INDOOR BLOWER OFF. NO HAS CONTROL FAILED TO SENSE FLAME FOR FIVE CONSECUTIVE TRIES DURING A SINGLE HEAT DEMAND? FLAME RECTIFICATION CURRENT CHECK. CAN FLAME BE PROVEN WITHIN 4 SECONDS AFTER GAS VALVE OPENS? (0.5 microamps) NO YES WATCHGUARD MODE. GAS VALVE OFF. COMBUSTION AIR INDUCER OFF. INDOOR BLOWER OFF WITH DELAY LEDs SIGNAL WATCHGUARD FAILURE CODE. IS 60‐MINUTE RESET PERIOD COMPLETE? YES YES NO NO HAS CONTROL RESET IGNITION SEQUENCE FOUR TIMES? FLAME PRESENT? YES YES LIMIT SWITCH WATCHGUARD MODE. GAS VALVE, COMB. AIR INDUCER AND INDOOR BLOW­ ER OFF. LEDs SIGNAL LIMIT SWITCH OPEN UNTIL MAIN POWER IS INTERRUPTED OR GAS VALVE DE-ENERGIZED. T'STAT IS CYCLED COMBUSTION AIR INDUCER DE-ENERGIZED. OFF/ON FOR 1 SEC. NO INDOOR BLOWER ON UNTIL SWITCH CLOSES. MINIMUM. 60-MIN­ LED #1 -- SLOW FLASH. LED #2 -- ON. UTE WATCHGUARD IS LIMIT SWITCH CLOSED? PERIOD STARTS AT YES TIME LIMIT CLOSES. IS 60-MIN. PERIOD YES HAS PRIMARY / SECONDARY COMPLETE? LIMIT RESET TIME NO FLAME SIGNAL 1.5 MICROAMPS OR GREATER? YES INDOOR BLOWER ON AFTER 30-SECOND DELAY YES PRIMARY AND SECONDARY LIMIT SWITCHES CLOSED? YES LOW FLAME SIGNAL (Does not affect operation of control) LED #1 -- SLOW FLASH LED #2 -- FAST FLASH EXCEEDED 3 MINUTES? NO NO ROLLOUT SWITCH CLOSED? YES COMBUSTION AIR PRESSURE SWITCH CLOSED? YES THERMOSTAT DEMAND SATISFIED. YES LED #1 & #2 SIMULTANEOUS SLOW FLASHES. YES COMB. AIR INDUCER CONTINUES 5‐SECOND POST PURGE AFTER T'STAT DEMAND IS SATISFIED. INDOOR AIR BLOWER COMPLETES SELECTED “OFF” DELAY BEFORE SHUTTING OFF. NO GAS VALVE POWER OFF. COMBUSTION AIR INDUCER POWER ON. INDOOR BLOWER ON LED #1 -- ON. LED #2 -- SLOW FLASH. SEQUENCE HOLDS UNTIL ROLLOUT SWITCH IS RESET AND MAIN POWER IS INTERRUPTED OR THERMOSTAT IS CYCLED OFF/ON FOR 1 SEC. MINIMUM. HAS PRESSURE SWITCH OPENED 5 1 HR TIMES IN THE SAME HEAT DEMAND? PRESSURE SWITCH YES NO WATCHGUARD GAS VALVE DE-ENERGIZED. MODE COMBUSTION AIR INDUCER ON. INDOOR BLOWER OFF WITH DELAY LED #1 -- OFF. LED #2 -- SLOW FLASH. HAS CAB SWITCH CLOSED IN 2.5 MINUTES? NO 5‐MINUTE PRESSURE SWITCH WATCHGUARD MODE. Page 45 COOLING SEQUENCE OF OPERATION NORMAL COOLING MODE ABNORMAL COOLING MODE POWER ON IGNITION CONTROL MAIN POWER ON. NO CONTROL SELF DIAGNOSTIC CHECK. IS CONTROL OPERATING NORMALLY? GAS VALVE OFF. COMBUSTION AIR INDUCER OFF. INDOOR BLOWER OFF WITH NORMAL DELAY. SIGNAL CIRCUIT CONTROL FAILURE AT LED. INTERRUPT MAIN POWER TO RESET CONTROL. YES NO IS THERE A PROPER GROUND? YES NO IS POLARITY CORRECT? YES SIGNAL IMPROPER GROUND AT LED. CONTROL WILL CONTINUE TO CALL FOR COOLING IN THIS CONDITION. SIGNAL POLARITY REVERSED AT LED. CONTROL WILL CONTINUE TO CALL FOR COOLING IN THIS CONDITION. NO LED SIGNALS LOW VOLTAGE. CONTROL WILL CONTINUE TO CALL FOR COOLING IN THIS CONDITION. IS VOLTAGE ABOVE 90 VOLTS? YES NO ROLLOUT SWITCH MONITORED CONTINUOUSLY. IS ROLLOUT SWITCH CLOSED? YES LED: SLOW FLASH RATE REMAINS UNCHANGED THROUGHOUT COOLING CYCLE. THERMOSTAT CALLS FOR COOLING. COMPRESSOR CONTACTOR AND SYSTEM FAN ENERGIZED WITH 2‐SECOND DELAY (COOLING SPEED). EAC TERM. ENERGIZED. THERMOSTAT OPENS. COMPRESSOR OFF. SYSTEM FAN AND EAC TERM. OFF WITH 45‐SECOND DELAY. Page 46 GAS VALVE OFF. COMBUSTION AIR INDUCER ON. INDOOR BLOWER ON. SIGNAL ROLL‐OUT SWITCH OPEN AT LED. SEQUENCE HOLDS UNTIL ROLLOUT SWITCH CLOSES AND MAIN POWER IS INTERRUPTED OR THERMOSTAT IS CYCLED OFF/ON FOR 1 SEC. MINIMUM. CONTINUOUS HEAT SPEED FAN SEQUENCE OF OPERATION LED: SLOW FLASH RATE REMAINS UNCHANGED THROUGHOUT SEQUENCE. MANUAL FAN SELECTION MADE AT THERMOSTAT. CONTROL (G) ENERGIZES SYSTEM FAN AT HEAT SPEED. EAC TERMINAL IS ENERGIZED. THERMOSTAT CALLS FOR HEAT (W). YES NO THERMOSTAT CALLS FOR COOLING. YES SYSTEM FAN SWITCHED TO COOL SPEED. EAC TERM. REMAINS ON. NO HUM TERM. ENERGIZES WITH COMB. AIR INDUCER. SYSTEM FAN REMAINS ON HEATING SPEED. THERMOSTAT OPENS. HUM TERM. DE-ENERGIZES WITH COMB. AIR INDUCER THERMOSTAT OPENS. MANUAL FAN SELECTION MADE AT THERMOSTAT. CONTROL (G) ENERGIZES SYSTEM FAN AT HEAT SPEED. EAC TERM. ENERGIZED. Page 47 SYSTEM FAN REMAINS ON HEATING SPEED. ML193DF With Integrated Control 103085 1 - When there is a call for heat, W1 of the thermostat en­ ergizes W of the furnace control with 24VAC. 2 - S10 primary limit switch and S47 rollout switch are closed. Call for heat can continue. 3 - The integrated control (A92) energizes combustion air inducer B6. Combustion air inducer runs until S18 combustion air prove switch closes (switch must close within 2-1/2 minutes or control goes into 5 minute Watchguard Pressure Switch delay). Once S18 closes, a 15-second pre-purge follows. 4 - The integrated control (A92) energizes ignitor. A 20-second warm-up period begins. 5 - Gas valve opens for a 4-second trial for ignition 6 - Flame is sensed, gas valve remains open for the heat call. 7 - After 30-second delay, the integrated control (A92) energizes indoor blower B3. 8 - When heat demand is satisfied, W1 of the indoor ther­ mostat de-energizes W of the integrated control which de-energizes the gas valve. Combustion air inducer B6 continues a 5-second post-purge period, and in­ door blower B3 completes a selected OFF time delay. Page 48 Sequence of Operation Flow Chart - Integrated Control 103085 HEATING SEQUENCE OF OPERATION ABNORMAL HEATING MODE NORMAL HEATING MODE POWER ON GAS VALVE OFF. COMBUSTION AIR INDUCER OFF. INDOOR BLOWER DELAY OFF. LED: OFF NO CONTROL SELF-CHECK OKAY? YES NO POLARITY REVERSED. LED: 9 FLASHES IS POLARITY CORRECT? YES IMPROPER GROUND. LED: OFF CONTROL WILL NOT RESPOND TO CALL FOR HEAT UNTIL PROPER GROUND. NO IS THERE A PROPER GROUND? YES NO LED: ON STEADY IGNITOR WILL GLOW DIMLY BUT WILL NOT LIGHT IS VOLTAGE ABOVE 90 VOLTS? YES ROLLOUT SWITCH CLOSED? GAS VALVE OFF. COMBUSTION AIR INDUCER ON. INDOOR BLOWER ON. LED: 5 FLASHES SEQUENCE HOLDS UNTIL ROLLOUT SWITCH CLOSES AND POWER IS RESET OR T'STAT IS INTERRUPTED FOR MINIMUM OF 1 SECOND. NO YES BURNER OFF? GAS VALVE OFF. COMBUSTION AIR INDUCER ON. INDOOR BLOWER ON HEATING SPEED. LED: 1 FLASH NO (Contiuous Flame Check) YES NO NORMAL OPERATION: LED: STEADY ON YES COMBUSTION AIR INDUCER OFF. INDOOR BLOWER ON LED: 4 FLASHES THERMOSTAT CALLS FOR HEAT: LED: STEADY ON YES NO PRIMARY AND SECONDARY LIMIT SWITCH. CLOSED? YES NO IS COMBUSTION AIR PRESSURE SWITCH OPEN? YES IS COMBUSTION AIR INDUCER ENERGIZED? YES HAS COMBUSTION AIR PRESSURE SWITCH CLOSED IN 2.5 MINUTES? NO YES CONTINUED NEXT PAGE Page 49 GAS VALVE OFF. COMBUSTION AIR INDUCER OFF. INDOOR BLOWER OFF WITH DELAY. LED: 2 FLASHES (Sequence holds until pressure switch opens or thermostat resets control.) PRESSURE SWITCH IS IN WATCHGUARD MODE. GAS VALVE OFF. COMBUSTION AIR INDUCER OFF. INDOOR BLOWER OFF WITH DELAY. LED: 3 FLASHES IS 5‐MINUTE RESET PERIOD COMPLETE? YES HEATING SEQUENCE CONTINUED NORMAL HEATING MODE ABNORMAL HEATING MODE 15‐SECOND COMBUSTION AIR INDUCER PREPURGE INITIATED BY CLOSED PRESSURE SWITCH. YES NO IS VOLTAGE ABOVE 90 VOLTS? IGNITOR WARM‐UP -- 20 SECONDS. YES NO YES 4‐SECOND TRIAL FOR IGNITION. GAS VALVE OPENS. LED: ON STEADY UNTIL VOLTAGE IS ABOVE 95 VOLTS, THEN RESTARTS HEATING SEQUENCE. GAS VALVE OFF. COMBUSTION AIR INDUCER ON. INDOOR BLOWER OFF. NO HAS CONTROL FAILED TO SENSE FLAME FOR FIVE CONSECUTIVE TRIES DURING A SINGLE HEAT DEMAND? YES FLAME STABILIZATION PERIOD. 4 SECONDS FLAME RECTIFICATION CURRENT CHECK. CAN FLAME BE PROVEN WITHIN 4 SECONDS AFTER GAS VALVE OPENS? NO YES WATCHGUARD MODE. GAS VALVE OFF. COMBUSTION AIR INDUCER OFF. INDOOR BLOWER OFF WITH DELAY LED: 7 FLASHES WATCHGUARD FAILURE CODE. IS 60‐MINUTE RESET PERIOD COMPLETE? YES YES NO NO HAS CONTROL RESET IGNITION SEQUENCE FOUR TIMES? FLAME PRESENT? YES NO FLAME SIGNAL 1.5 MICROAMPS OR GREATER? YES INDOOR BLOWER ON AFTER 30-SECOND DELAY GAS VALVE DE-ENERGIZED. COMBUSTION AIR INDUCER DE-ENERGIZED. INDOOR BLOWER ON UNTIL SWITCH CLOSES. LED: 4 FLASHES IS LIMIT SWITCH CLOSED? YES PRIMARY AND SECONDARY LIMIT SWITCHES CLOSED? LOW FLAME SIGNAL (Does not affect operation of control) LED: ON STEADY NO YES NO YES 5 MINUTE WATCHGUARD MODE. HAS LIMIT SWITCHED CLOSED AFTER 5 MINUTES? NO NO ROLLOUT SWITCH CLOSED? YES COMBUSTION AIR PRESSURE SWITCH CLOSED? YES THERMOSTAT DEMAND SATISFIED. YES LED: ON STEADY YES COMB. AIR INDUCER CONTINUES 15‐SECOND POST PURGE AFTER T'STAT DEMAND IS SATISFIED. INDOOR AIR BLOWER COMPLETES SELECTED “OFF” DELAY BEFORE SHUTTING OFF. NO YES GAS VALVE POWER OFF. COMBUSTION AIR INDUCER POWER ON AFTER 15 SECOND DELAY. INDOOR BLOWER ON LED: 5 FLASHES SEQUENCE HOLDS UNTIL ROLLOUT SWITCH IS RESET AND MAIN POWER IS INTERRUPTED OR THERMOSTAT IS CYCLED OFF/ON FOR 1 SEC. MINIMUM. HAS PRESSURE SWITCH OPENED 5 TIMES IN THE SAME HEAT DEMAND? NO GAS VALVE DE-ENERGIZED. COMBUSTION AIR INDUCER ON. INDOOR BLOWER OFF WITH DELAY LED: 6 FLASHES 5 MINUTE PRESSURE SWITCH WATCHGUARD MODE. Page 50 1 HR PRESSURE SWITCH YES WATCHGUARD MODE COOLING SEQUENCE OF OPERATION NORMAL COOLING MODE ABNORMAL COOLING MODE POWER ON IGNITION CONTROL MAIN POWER ON. LED: ON STEADY NO CONTROL SELF DIAGNOSTIC CHECK. IS CONTROL OPERATING NORMALLY? GAS VALVE OFF. COMBUSTION AIR INDUCER OFF. INDOOR BLOWER OFF WITH NORMAL DELAY. LED: OFF INTERRUPT MAIN POWER TO RESET CONTROL. YES NO IS THERE A PROPER GROUND? LED: ON STEADY CONTROL WILL CONTINUE TO CALL FOR COOLING IN THIS CONDITION. YES NO IS POLARITY CORRECT? LED: 9 FLASHES CONTROL WILL CONTINUE TO CALL FOR COOLING IN THIS CONDITION. YES NO LED: ON STEADY. CONTROL WILL CONTINUE TO CALL FOR COOLING IN THIS CONDITION. IS VOLTAGE ABOVE 90 VOLTS? YES LED: ON STEADY. REMAINS UNCHANGED THROUGHOUT COOLING CYCLE. THERMOSTAT CALLS FOR COOLING. COMPRESSOR CONTACTOR AND SYSTEM FAN ENERGIZED WITH 2‐SECOND DELAY (COOLING SPEED). EAC TERM. ENERGIZED. THERMOSTAT OPENS. COMPRESSOR OFF. SYSTEM FAN AND EAC TERM. OFF WITH 60‐SECOND DELAY. CONTINUOUS FAN SEQUENCE OF OPERATION LED: ON STEADY MANUAL FAN SELECTION MADE AT THERMOSTAT. CONTROL (G) ENERGIZES SYSTEM FAN ON CONTINUOUS BLOWER SPEED. EAC TERMINAL IS ENERGIZED. THERMOSTAT CALLS FOR HEAT (W). YES NO SYSTEM FAN SWITCHES TO HEATING SPEED. THERMOSTAT CALLS FOR COOLING. YES SYSTEM FAN SWITCHED TO COOL SPEED. EAC TERM. REMAINS ON. HUM TERM. ENERGIZES WITH COMB. AIR INDUCER. NO THERMOSTAT OPENS. HUM TERM. DE-ENERGIZES WITH COMB. AIR INDUCER THERMOSTAT OPENS. MANUAL FAN SELECTION MADE AT THERMOSTAT. CONTROL (G) ENERGIZES SYSTEM FAN ON CONTINUOUS BLOWER SPEED. Page 51 SYSTEM FAN SWITCHES TO CONTINUOUS BLOWER SPEED .
advertisement