- No category
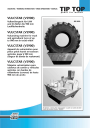
advertisement
▼
Scroll to page 2
of 62
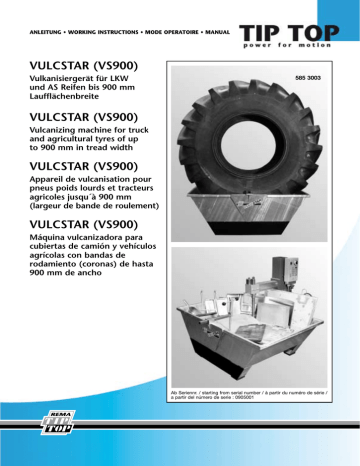
585 3003 VULCSTAR (VS900) Vulcanizing machine for truck and agricultural tyres of up to 900 mm in tread width Seite Table of contents page I. Introduction /general information�������������������������������� 2 II. Safety instructions ������������������������������������������������������ 4 III Technical data�������������������������������������������������������������� 6 IV. Description of the machine������������������������������������������ 8 V. Installation of the machine (before putting it into operation for the first time)������ 10 VI. Standard shipment���������������������������������������������������� 13 VII. Handling of the machine for tread repair������������������ 15 VIII. Handling of the machine for tread repair and building-up of tread pattern�������������������������������� 23 IX. Handling of the machine for sidewall repair�������������� 35 X. Curing time chart ������������������������������������������������������ 44 XI. Maintenance�������������������������������������������������������������� 46 XII. Trouble shooting�������������������������������������������������������� 49 Xlll. Accessories���������������������������������������������������������� 52/53 XlV. Exploded view ���������������������������������������������������������� 54 XV. Spare parts list���������������������������������������������������������� 56 I. Introduction/general Information •This manual explains the correct handling of the machine. It should be studied before the machine is put into operation for the first time, and read regularly when the machine is operated. •Whenever the machine is sold again, pass on this manual to the new owner. •The REMA TIP TOP VULCSTAR vulcanizing machine is designed for the vulcanization of an injury filled with uncured rubber on a light truck or agricultural tyre and the repair patch applied to it. The machine is also adapted to the working conditions, under which these operations are carried out. •For information about the preparation of injuries, refer to the separate REMA TIP TOP repair instructions. •Besides the explanations and safety instructions in this manual, the user/operator of the VULCSTAR machines has to take into account the precautions relating to the use of all technical devices. •All the information given in this manual refers only to the use of original REMA TIP TOP materials, accessories and spare parts. •We reserve the right to carry out modifications which we consider to be technically advantageous. •A proper repair requires not only the use of high quality repair materials and tools but also an appropriate working environment, for example: - good illumination - well-trained staff - periodical cleaning of the working place and the tools •© 2009 These instructions are copyright. Their reproduction (including reproduction through various photographic methods and storage by any electronic medium) is subject to the approval of REMA TIP TOP GmbH, 85586 Poing / Germany. Any commercial use of these instructions or any part of them is prohibited. page página II.a II.b II.a General safety instructions •Before putting the machine into operation, read the manual carefully step by step. Always observe the safety instructions! • Always keep the manual accessible to the operators. •When the machine has to be put out of service and to be disposed of, observe the relevant regulations on waste separation, recycling and the correct disposal of used parts. •The local air and electrical power supply must be equal to that stated on the machine data plate. If it is not equal to that stated on the machine data plate, do not plug the machine in! Have it connected by a qualified specialist! •Never exceed or change the settings etc. listed in this manual. •Allow only a qualified specialist to carry out any work on electric parts. •Make sure that the outside heating element is covered with enough granules. Risk of excessive heat build-up on the tyre surface. •Avoid rolling over cables! Risk arising from damaged cables! •Avoid any risk from electric cables etc.! Danger of stumbling! •Make sure that the tyre to be vulcanized is secured correctly. Use the appropriate supports and / or the REMA TIP TOP Tyre Support to prevent the tyre from tipping over or falling down. •Always check the Airpower-Bag and the heating system together with all the connection cables and air lines for damage, before putting the machine into operation! Risks due to electric tension and breakage of structural parts! •Immediately remove defective or damaged parts from the work place, and replace them by original REMA TIP TOP spare parts. Make sure that the machine cannot be put back into operation until it is repaired completely. •Keep your hands clear of the space between the tyre and the pressure-exerting parts while inflating the Airpower-Bag. Risk of injury due to entrapment. •Do not leave the machine unattended when it is operating. Observe the relevant measures for fire protection and the regulations regarding the use of electric heating systems. •Do not touch the heating elements and granules without protective gloves, when the machine is working or cooling down. Danger of burning! •Protect the machine/heating elements/Airpower-bags and the granules from moisture, sharp-edged objects, and dirt! Fire risk, risk of short-circuits! •Do not bend, fold or twist the heating mat or its cable; do not open the connectors! Risk of electric shock. •Do not open the control box. Allow only a qualified electrician to carry out any work on it. Risk due to electric tension! •Use the REMA TIP TOP VULCSTAR vulcanizing machine only for curing injuries filled with uncured rubber on tyres or other moulded rubber parts! •Deposit all objects only on the shelves designed for this purpose. Fire risk! •When using an extension lead, make sure that the cable diameter is sufficient. Always completely unwind cable drums. Fire risk! •Observe general safety instructions and the specific regulations for prevention of accidents from the employer´s liability insurance association. •Keep the machine in good working order by cleaning and servicing it regularly! •Make sure that the safe floor-load is not exceeded where the vulcanizing machine is located! (Machine weight plus weight of tyre: load = approx. 1000 kg/m²). II.b Safety instructions Airpower-Bag • Protect the Airpower-Bag from oil, solvents and acids. •Fill the Airpower-Bag only with compressed air free from oil. •Do not put the Airpower-Bag on hot, sharp-edged or pointed objects. •Use the Airpower-Bag only together with REMA TIP TOP vulcanizing machines. Do not use it as a lifting device etc. •The operating pressure must not exceed the maximum. Explosion hazard! •Do not change the pre-set pressure on the safety valve or damage it. •Use only original REMA TIP TOP pressure blocks for the transmission of pressure. •Always make sure that all locking pins and structural parts etc. are seated and secured correctly before inflating the AirpowerBag. II.a III. Technical data Betriebsspannung Power input Operating temperature Temperature control Curing time control Operating pressure Dimensions Weight Noise level Space requirement when in use basic model (heating system for granules), Inner heating mat basic model (heating system for granules) Inner heating mat heating system for granules Inner heating mat heating system for granules Inner heating mat mechanical timer Airpower-Bag size IV Airpower-Bag size VI Vibrator VULCSTAR (length x height x width) Heating system for granules Airpower-Bag size IV Airpower-Bag size VI standard shipment while the vibrator operates 230 V 230 V 2,2 kW max. 0,3 kW 190 °C +/- 10 °C / 375 °F +/- 50 °F 130 °C +/- 10 °C / 265 °F / +/- 50 °F temperature measured with thermocouple in the heating element, electronic control system and setting of desired value with automatic temperature limiting unit 0 - 6 hours with final cutoff of heating circuits 3 bar / 43 psi / safety valve 3.3 bar / 48 psi 2.5 bar / 36 psi / safety valve 2.8 bar / 41 psi 5 - 6 bar / 73 - 87 psi through pressure regulating flow control valve approx. 1200 x 1100 x 1600 mm approx. 500 x 700 mm (effective surface area of heating element) approx. 300 x 470 mm approx. 400 x 470 mm approx. 700 kg (including 350 kg of granules) minimum safe floor-load required where the machine is located together with tyre of maximum size: 1000 kg/m² max 80 db A approx. 1600 x 1600 mm (length x width) / area: approx. 2,6 m² We reserve the right to carry out modifications which we consider to be technically advantageous. Dimensions Dimensiones IV. Description of the machine The following main targets have been set for the development of the REMA TIP TOP VULCSTAR vulcanizing machine: maximum flexibility, easy handling, easy maintenance and unlimited suitability for any present and future sizes and shapes of tyres The REMA TIP TOP Vulcstar 900 is a further development from Vulcstar 700, and has been designed in response to the constantly changing tyre sizes / aspect ratios in the tyre industry. The machine Vulcstar 900 now makes it easy to repair agricultural tyres of up to 850 mm in tread width. Repair area up to 850 mm in the tread , up to 520 mm in the sidewall. With accessories from VS 700 (not in standard shipment, available as options, see spare parts list), the application area of the VS 900 vulcanizing machine can be extended to include injuries to the tread, sidewall and shoulder of tyres starting from 295/80 R22.5. These targets have been reached with the use of a pressure system which is flexible and can be adapted to suit any contour and shape of a tyre. The pressure system is convincingly simple and reliable, and does not require a large stock of contour plates or time-consuming refinishing work on the repair area. Thus, lugs on agricultural tyres can be built up with uncured rubber in their original size and shape and then be cured in the vulcanizing machine without any change of shape or contour, so that it is virtually unnecessary to spend a lot of time on filling the voids between the lugs with pressure equalizing pads etc.. – Less post-cure buffing and refinishing work! In addition, REMA TIP TOP repair patches are easy to cure with the Vulcstar machine, whether laminated with MTR Rubber (if this is required) or applied with Special Cement BL, HR Solution or MTR-Solution. Lieferumfang / standard shipment / livraison standard / volumen de suministro estándar Laufflächenreparatur / tread repair / réparation bande de roulement / reparación en la banda de rodamiento V. 10 V. Installation of the machine (before putting it into operation for the first time Several preparations have to be made upon delivery, before putting the REMA TIP TOP VULCSTAR machine into operation for the first time. •Choose the place where the machine should be in­stalled, provide the necessary access; make sure that there is enough space for work, and that the safe floor-load is not exceeded where the vulcanizing machine is located! (load: approx. 1000 kg/m²). •Check whether the shipment is complete and in good condition. •Move the REMA TIP TOP VULCSTAR vulcanizing machine to the appropriate place using the appropriate lifting device (e.g. fork lift truck). •Make sure that the machine is secured correctly and stands on an even surface, far enough from other machines, walls etc. •Remove the packing and check whether the pressure bed is dry and clean. •Fill about 2 thirds of the pressure bed gradually with original REMA TIP TOP granules (approx. 10 bags) and distribute them evenly. Safety instruction: Use only dry granules! •Put the heating element on the surface of the granules, with the connection cable towards the rear of the vulcanizing machine, then put another two sacks of granules into the pressure bed, distributing them evenly. The heating element must be covered with an approx. 5 - 6 cm thick layer of granules. Put the enclosed accessories on the appropriate tool shelves, and mount the lower front panel. •Then connect the VULCSTAR machine to the local mains and compressed air supply. The indicator lamp for mains power supply illuminates. Safety instruction: The local air and electrical power supply must be equal to that stated on the machine data plate. If it is not equal to that stated on the machine data plate, do not plug the machine in! Have it connected by a qualified specialist! Then put the machine into operation by setting the timer to 15 minutes. Thus check whether the heating system and the control box work correctly. The indicator lamp for the operation of the heating system is on during the previously set curing time. -A t the end of the previously set curing time, the heating system switches off automatically. At this moment, a significant increase in temperature should be noted on the surface of the granules. Safety instruction: Use protective gloves! Danger of burning! - If the indicator lamp for the operation of the heating system does not illuminate, check whether the fuse and the mains power supply are appropriate and work correctly. If no defect is found, disconnect the machine from the mains. Have the machine checked by a qualified electrician. If the previously set time has not elapsed on the timer or if the machine has not switched off automatically at the end of the previously set time, disconnect the machine from the mains, and have it checked by a REMA TIP TOP technician. •If no defects have been found during the a.m. trial service, the machine is ready for normal operation. V. 11 5 6 7 2 4 8 16 3 14 15 13 19 20 12 17 18 22 14 23 11 Abb./fig./esq. 6.1 28 27 30 29 34 35 31 32 36 26 Abb./fig./esq. 6.2 37 39 38 49 44 41 42 45 40 43 51 46 47 50 48 Abb./fig./esq. 6.3 12 VI. Standard shipment 1*Vulcstar control box including heating element for pressure granules 2 Pressure bed 3 Front panel (can be demounted for transport) 4*pressure granules, (14 sacks, each 25 kg) 5Upper pressure unit with vertical adjustment 6 Cross arm (can be adjusted) 7Supporting point for vertical adjustment of pressure unit 8 Tool shelves 9Machine feet with rubber pads (non shown) 10Vibrator, Pressure regulating flow control valve 6 bar/87 psi (non shown) 11 Spatula for pressure granules 12socket adapter set: socket adapter casing, pressure spindle with guide bushing and special locking pin 13* Airpower-Bag IV and Vl 14pressure blocks L 2 / L 3 and S2/S3 15Pressure plate for agricultural tyres AS 1 16Pressure plate for agricultural tyres AS 2 17 Pressure block AS 2 18Counter pressure plates GD 1 and GD 2 19counter-pressure bar with spindle / extension of counter-pressure bar 20Tubular socket wrench for pressure spindle 21Locking pin (20 mm diameter) for frame 22Height adjusting lever for upper pressure unit 23 shovel for granules 24 bucket for granules 25 diamond-shaped tool tray Options 26* Vulcstar inner heating mat ll, lV 27* Airpower-Bag Il 28 pressure block, L1 / S1 29 (Pneumatic) wrench with adapter 30 tyre support 31pressure clamp for shoulder and sidewall repairs 32 Pressure bar (40 mm diameter) 33shearing pins (10 pcs not visible), for pressure bar 34Locking pin for sidewall pressure clamp 35Locking pin (12 mm diameter) for pressure bar 36Adapter for sidewall pressure clamp / T-piece Control box for electrical / pneumatic system 37 Timer 0 - 6 hours 38 Fuse holder, 10 A 39 Mains switch 40 Indicator lamp for mains power supply 41 Indicator lamp for heating element for pressure granules (heating element ON) 42 Indicator lamp for inner heating mat (inner heating mat ON) 43 Indicator lamp for overheating cutout ON 44 Connector for inner heating mat 45 Connection cable for heating element for pressure granules 46 Mains cable 47 Fitting for compressed air supply 48 Pneumatic hand lever valve for vibrator 49 FI fault current breaker 50 EWO air fittings for tools 51 Mains supply connector The parts marked with an asterisk *) are wear parts, for which no guarantee claim based on any legal provisions whatsoever can be accepted. VI. Volumen de suministro 13 Abb./fig./esq. 7.1 Abb./fig./esq. 7.2 Abb./fig./esq. 7.4 14 VII.Handling of the machine for tread repairs to truck, and agricultural tyres The handling of the machine is shown on a truck tyre tread injury which has been prepared according to the onestage system des­cribed in the current REMA TIP TOP repair instructions. 7.1 Switch the machine off by setting the mains switch to - 0 -. (fig. 7.1) Safety instruction: Work on electric parts, only when the machine is switched off. Risk due to electric tension! 7.2 Remove the heating element from the granule filling; then using a spatula, adapt the surface of the granulate roughly to the diameter of the tyre. (fig. 7.2) Safety instruction: Hold the heating element only by its holding loop to remove it from the granule filling. Risk of damage to the heating element. Use protective gloves! Danger of burning! 7.3 Put the heating element on the granules, with its cable outlet towards the rear of the vulcanizing machine. Then cover it completely with granules. (fig. 7.3) Layer of granules on heating element: sidewall repairs: 2 - 3 cm tread / shoulder: depth of tread pattern + 3 - 4 cm Safety instruction: use protective gloves! Danger of burning! 7.4 We recommend drawing auxiliary lines (cross) on the outside of the tyre as far as the bead in order to make it easier to centre the tyre in the VULCSTAR vulcanizing ma­chine. Move the tyre to the vulcanizing machine and position the repair area covered with heat resistant foil, as shown on the fig. 7.4. Note: Make sure that the skive is filled completely, without any air entrapment. Avoid air entrapment by filling the skive evenly and by evenly stitching on the skive filling. Safety instruction: Always observe the relevant regulations for prevention of accidents (e.g. the German UVV regulations), when changing the position of the tyre. 15 Abb./fig./esq. 7.5 Abb./fig./esq. 7.6a Abb./fig./esq. 7.6b Abb./fig./esq. 7.7a 16 Abb./fig./esq. 7.7b 7.5 Then tip the tyre forwards into the pressure bed so as to centre the repair area over the heating element in the granule filling. (fig. 7.5) Now, the tyre stands upright in the middle of the vulcanizing machine. Build up granules evenly around the tyre, making sure that the outside heating element is always covered with granules. This will ensure an even distribution of heat over the whole repair area. Attention: Standard tyres in sizes such as 295/80 R22.5 must be accurately positioned in the centre of the pressure bed. Otherwise, it may be difficult to adjust the cross-arm and the counterpressure plate GD 1/2. 7.6 If inner heating mats are available (option), select the one which fits the repair patch applied. Powder both sides of the selected inner heating mat with talcum. The heating mat has to cover the whole repair patch (together with any cushion gum applied to it) plus an at least 15 - 20 mm-wide area around the (laminated) patch. Now, powder the repair area with talcum, and centre the inner heating mat onto the repair area, with its cable outlet towards the rear of the vulcanizing machine. (fig. 7.6a and 7.6b) Safety instruction: always check the inner heating mat for visible defects or damage, before use! Immediately remove defective parts and replace them by original REMA TIP TOP spare parts. 7.7 Select the Airpower-Bag which fits the selected inner heating mat and the repair patch applied. Powder the selected Airpower-Bag with talcum. The Airpower-Bag has to cover the repair patch (together with any cushion gum applied to it) plus an approx. 15 mm – wide area around them. Now, centre the Airpower-Bag onto the inner heating mat / the repair patch powdered with talcum. The compressed air connector of the Airpower-Bag has to face in the axial direction. (fig. 7.7a and 7.7b) Note: If the Airpower-Bag and the inner heating mat are regularly powdered with talcum, they will last much longer, and the repair will be more stable. Safety instruction: Always check the Airpower-Bag and the inner heating mat for defects or damage before use. Immediately remove defective parts and replace them by original REMA TIP TOP spare parts. 17 Abb./fig./esq. 7.8a Abb./fig./esq. 7.8b Abb./fig./esq. 7.8c Abb./fig./esq. 7.9 Abb./fig./esq. 7.10a 18 Abb./fig./esq. 7.10b 7.8 If necessary, adjust the upper pres­ sure unit to the required height using the height adjusting device. Then insert the locking pin again. (fig. 7.8a) Move the cross-arm forward, until the recess for the pressure spindle is centred over the repair area. Then, fit the socket adapter casing on the cross-arm. Secure the socket adapter casing with the special locking pin. Then centre the required pressure block onto the airpower bag. Insert the guide bushing for the pressure spindle in the matching socket on the pressure block. Insert the pressure spindle in the guide bushing, and tighten the spindle with your hands. Finally, make sure again that all these elements are centred exactly over the (fig. 7.8b and 7.8c) repair area. Safety instruction: Check all parts for any defects or damage! Immediately remove defective parts and replace them by original REMA TIP TOP spare parts. Always insert the locking pins and check whether they are seated correctly. The pressure spindle must be tightened only with your hands, in order to prevent the pressure block on the centre of the repair patch/airpower bag from building up mechanical pressure. The optimum distribution of equal pressure over the repair patch must be ensured by an air cushion which is built up while inflating the airpower-bag. 7.9.Screw the valve core of the AirpowerBag in; then inflate the Airpower-Bag up to 1.0 bar / 15 psi, using a tyre inflator, thus locking the pressure sys(fig 7.9) tem. Safety instruction: Inflate the Air­powerBag only with compressed air free from oil! Re-check whether all the locking pins are seated correctly. 7.10 Open the hand lever valve and let the vibrator operate for approx. 45 - 60 seconds. Thus the granules are compacted, filling the voids and providing a contour that snugly fits the tyre and ensures optimum distribution of heat. If the granule layer under the repair area becomes too thin during this process, push granules towards the tyre using the spatula. (fig. 7.10a and 7.10b) After this time, close the hand lever valve again, and check again whether all pressure exerting parts and locking elements are seated precisely. If the position of pressure exerting parts has to be changed, release the pressure in the Airpower-Bag, and repeat the operations described from no .7.8 onwards. Safety instruction: The vibrator generates high-frequency vibrations. Do not put any fragile parts / objects on the machine. Use the vibrator only together with the original pressure regulating flow control valve. Risk of excessive stress and increased noise level. 19 Abb./fig./esq. 7.11 Abb./fig./esq. 7.12a Abb./fig./esq. 7.12b Abb./fig./esq. 7.13 Abb./fig./esq. 7.14 20 7.11 Increase the pressure in the Airpower-Bag up to 3 bar / 43 psi for truck tyres (up to 2.5 bar / 36 psi for agricultural tyres), and remove the tyre inflator. Check the valve of the Airpower-Bag for air tightness, then close the valve with the valve cap. (fig. 7.11) Do not use the vibrator any longer until the end of the curing process! Safety instruction: Fill the Airpower– Bag only with compressed air free from oil. 7.12 Select the appropriate curing time according to the chart X. (see page 44). Switch the vulcanizing machine on by setting the mains switch to I. Wind up the timer with one complete revolution, then reset it to the required curing time. (fig. 7.12a and 7.12b) Safety instruction: Do not leave the machine unattended when it is operating. Observe the relevant measures for fire protection and the regulations regarding the use of electric heating systems. Never use the machine with humid granules! Risks due to electric current and formation of steam. 7.13 At the end of the previously set curing time, the heating system is automatically cut off by the timer. Switch the vulcanizing machine off by setting the mains switch to - 0 -. Completely release the pressure in the Airpower-Bag by removing the valve core, then remove the pressure-exerting parts. (fig 7.13) Safety instructions: Use protective gloves! Danger of burning due to hot granules / hot parts! Deposit all the parts on the tool shelves designed for this purpose! Risks due to falling parts! 7.14 Remove the tyre from the vulcanizing machine. Using a brush, remove any granules from the tyre. Then check whether the repair area has been correctly vulcanized. Do not speed up the cooling-down process of the repair area using water, compressed air etc. (fig. 7.14) 7.15 If necessary, finish-buff the outside of the repair area after the vulcanization and complete cooling of the repair 21 Abb./fig./esq. 8.2 Abb./fig./esq. 8.3 Abb./fig./esq. 8.4 22 Abb./fig./esq. 8.5 VIII. Handling of the machine for tread repairs to agricultural tyres and for building-up tread patterns This chapter shows how to use the machine for building-up a tread lug, and for curing a tread injury which has been prepared according to the one-stage system described in the current REMA TIP TOP repair instructions. Select the repair patch which fits the tyre and injury size, according to the repair chart; apply the patch according to the one-stage system described in the current REMA TIP TOP repair instructions. 8.1 Skive filling / building-up tread lugs Fill the skive according to the onestage system described in the repair instructions. To speed up skive filling, we recommend the use of our REMA TIP TOP - Extruder – Normal (ref.no. 517 7505) together with the MTR Extruder Rope Rubber (ref. no. 516 1016). Shape the lug with uncured rubber in its original size and contour. (fig. 8.1) Note: During skive filling / tread lug building, you should regularly stitch on the extruded portions of rope rubber with a thin roller-stitcher. Use Thermopress MTR – Solution /Rub­ ber only together with REMA TIP TOP vulcanizing machines or in retreading systems at operating temperatures of at least 100 °C (212 °F). 8.2 Trim any uneven spots and adapt them to the original contour, using an offset knife (ref.no. 595 2139). (fig. 8.2) 8.3 In order to avoid the granules sticking to the skive filling, coat the surface of the skive filling with Thermopress MTR Solution (drying time 1 - 2 minutes), and cover the skive filling with heat resistant foil (ref.no. 517 6977). (fig. 8.3) 8.4 Switch the machine off by setting the mains switch to - 0 -. (fig. 8.4) Safety instruction: Work on electric parts, only when the machine is switched off. Risk due to electric tension! 8.5 Remove the heating element from the granule filling; then using a spatula, adapt the surface of the granulate roughly to the diameter of the tyre. (fig. 8.5) Safety instruction: Hold the heating element only by its holding loop to remove it from the granule filling. Risk of damage to the heating element. Use protective gloves! Danger of burning! 23 radial Abb./fig./esq. 8.7 Abb./fig./esq. 8.9 24 8.6 Put the heating element on the granules, with its cable outlet towards the rear of the vulcanizing machine. Then cover it completely with granules. (fig. 8.6) Layer of granules on heating element sidewall repairs: 2 - 3 cm tread / shoulder: depth of tread pattern + 3 - 4 cm 8.7 To cure sidewall or shoulder repairs with large repair patches applied, put the heating element on the granules, with its cable outlet towards the rear of the vulcanizing machine (heating element in radial direction). Then cover it com­pletely with granules as described in section 8.6. (fig. 8.7) Safety instruction: use protective gloves! Danger of burning! 8.8 We recommend drawing auxiliary lines (cross) on the outside of the tyre as far as the bead in order to make it easier to centre the tyre in the VULCSTAR vulcanizing ma­chine. Then introduce the counter pressure bar. Note: Once the tyre has been positioned in the machine, it is no longer possible to introduce the counter pressure bar! 8.9 Move the tyre to the vulcanizing machine and position the repair area covered with heat resistantfoil, as shown on the fig. 8.9. Tyres with a section width not exceeding 520 mm can be positioned by tipping them over the wall of the pressure bed. Tyres wider than 520 mm must be positioned using lifting equipment (repair stand/ fork lift truck). Note: Make sure that the skive is filled completely, without any air entrapment. Avoid air entrapment by filling the skive evenly and by evenly stitching on the skive filling. When positioning the tyre in the machine, make sure that the pressure granules which cover the heating element for pressure granules are not dispersed or shifted away, leaving little or no depth of granulate to take up the tyre profile or shape. Safety instruction: Always observe the relevant regulations for prevention of accidents (e.g. the German UVV regulations), when changing the position of the tyre. Abb./fig./esq. 8.10 Abb./fig./esq. 8.10a Abb./fig./esq. 8.10b Abb./fig./esq. 8.11a 26 Abb./fig./esq. 8.11b 8.10 Then lift the tyre/tip the tyre forwards into the pressure bed so as to centre the repair area over the heating element in the granule filling. (fig. 8.10a) Now, the tyre stands upright in the middle of the vulcanizing machine. Build up granules evenly around the tyre, making sure that the outside heating element is always covered with granules. This will ensure an even distribution of heat over the whole repair area. (fig. 8.10b) 8.10.a When the tyre is safely positioned in the pressure bed, open the hand lever valve, and let the vibrator operate. Prior to this operation, do not apply pressure to the repair area using the airpower bag. (fig.8.15a page 30) Let the tyre compress the granules only with its own weight until it stops sinking in. (Attention: The tread lugs should be at least 2 - 3 cm away from the heating element for pressure granules in order to avoid burning damage to the tyre!) In order to ensure that there are enough pressure granules around the tread lugs, use the spatula to compensate for any loss of granules flowing away. (fig. 8.15b page 30) 8.11 If inner heating mats are available (option), select the one which fits the repair patch applied. Powder both sides of the selected inner heating mat with talcum. The heating mat has to cover the whole repair patch (together with any cushion gum applied to it) plus an at least 15 - 20 mm-wide area around the (laminated) patch. Now, powder the repair area with talcum, and centre the inner heating mat onto the repair area, with its cable outlet towards the rear of the vulcanizing machine. (fig. 8.11a and 8.11b) Note: If the two-way repair system is used, the pressure plate for agricultural tyres should be used to stabilize the repair area and to avoid deformation to the tread lugs. Safety instruction: always check the inner heating mat for visible defects or damage, before use! Immediately remove defective parts and replace them by original REMA TIP TOP spare parts. 27 Abb./fig./esq. 8.12a Abb./fig./esq. 8.12b Abb./fig./esq. 8.13a Abb./fig./esq. 8.13b Abb./fig./esq. 8.13c 28 8.12 Select the Airpower-Bag which fits the selected inner heating mat and the repair patch applied. Powder the selected Airpower-Bag with talcum. The Airpower-Bag has to cover the repair patch (together with any cushion gum applied to it) plus an approx. 15 mm – wide area around them. Now, centre the Airpower-Bag onto the inner heating mat / the repair patch powdered with talcum. The compressed air connector of the Airpower-Bag has to face in the axial direction. (fig. 8.12a and 8.12b) Note: If the Airpower-Bag and the inner heating mat are regularly powdered with talcum, they will last much longer, and the repair will be more stable. Safety instruction: Always check the Airpower-Bag and the inner heating mat for defects or damage before use. Immediately remove defective parts and replace them by original REMA TIP TOP spare parts. 8.13 If necessary, adjust the upper pres­sure unit to the required height using the height adjusting device. Then insert the locking pin again. (fig. 8.13a) Move the cross-arm forward, until the recess for the pressure spindle is centred over the repair area. Then, fit the socket adapter casing on the cross-arm. Secure the socket adapter casing with the special locking pin. Then centre the required pressure block onto the airpower bag. Insert the guide bushing in the matching socket on the pressure block. Then, secure the guide bushing in the cross-arm with the locking pin. Finally, make sure again that all these elements are centred exactly over the repair area. (fig. 8.13b and 8.13c) Safety instruction: Check all parts for any defects or damage! Immediately remove defective parts and replace them by original REMA TIP TOP spare parts. Always insert the locking pins and check whether they are seated correctly. The pressure spindle must be tightened only with your hands, in order to prevent the pressure block on the centre of the repair patch/airpower bag from building up mechanical pressure. The optimum distribution of pressure over the top side of the repair patch must be ensured by an air cushion which is built up while inflating the airpower-bag. 29 Abb./fig./esq. 8.14 Abb./fig./esq. 8.15a Abb./fig./esq. 8.15b Abb./fig./esq. 8.16 30 Abb./fig./esq. 8.17 8.14 Screw the valve core of the Airpower-Bag in; then inflate the Airpower-Bag up to 2.0 bar / 30 psi, using a tyre inflator, thus securing the pressure system. (fig 8.14) Safety instruction: Inflate the AirpowerBag only with compressed air free from oil! Re-check whether all the locking pins are seated correctly. Check again whether all pressure exerting parts and locking elements are seated precisely. If the position of pressure exerting parts has to be changed, release the pressure in the airpower bag, and repeat the operations described from no. 8.13. 8.15 Open the hand lever valve and let the vibrator operate for approx. 45 - 60 seconds. Thus the granules are compacted, filling the voids and providing a contour that snugly fits the tyre and ensures optimum distribution of heat. If the granule layer under the repair area becomes too thin during this process, push granules towards the tyre using the spatula. (fig. 8.15a and 8.15b) After this time, close the hand lever valve again, and check again whether all pressure exerting parts and locking elements are seated precisely. If the position of pressure exerting parts has to be changed, release the pressure in the Airpower-Bag, and repeat the operations described from no .8.13 onwards. Safety instruction: The vibrator generates high-frequency vibrations. Do not put any fragile parts / objects on the machine. Use the vibrator only together with the original pressure regulating flow control valve. Risk of excessive stress and increased noise level. 8.16 Select the appropriate counterpressure plate (distance between the tyre and the edge of the pressure bed). Position it near the tyre (distance: approx. 1 cm), and secure it using the pressure spindle. Generate enough pressure using the pneumatic wrench or the tubular socket wrench. (fig. 8.16) Safety instruction: Use a counter-pressure plate to ensure that the required parts snugly fit the surface of the skive, if the tyre section width makes this possible. 8.17 Increase the pressure in the Airpower-Bag up to 2.5 bar / 36 psi, and remove the tyre inflator. Check the valve of the Airpower-Bag for air tightness, then close the valve with the valve cap. (fig. 8.17) Do not use the vibrator any longer until the end of the curing process! Safety instruction: Fill the Airpower– Bag only with compressed air free from oil. Abb./fig./esq. 8.18b Abb./fig./esq. 8.19 Abb./fig./esq. 8.20a Abb./fig./esq. 8.20b Abb./fig./esq. 8.21 32 8.18 Select the appropriate curing time according to the chart X. (see page 44). Switch the vulcanizing machine on by setting the mains switch to - I -. Wind up the timer with one complete revolution, then reset it to the required curing time. (fig. 8.18a and 8.18b) Safety instruction: Do not leave the machine unattended when it is operating. Observe the relevant measures for fire protection and the regulations regarding the use of electric heating systems. Never use the machine with humid granules! Risks due to electric current and formation of steam. 8.19 At the end of the previously set curing time, the heating system is automatically cut off by the timer. Switch the vulcanizing machine off by setting the mains switch to - 0 -. Completely release the pressure in the Airpower-Bag by removing the valve core, then remove the pressure-exerting parts. (fig 8.19) Safety instructions: Use protective gloves! Danger of burning due to hot granules / hot parts! Deposit all the parts on the tool shelves designed for this purpose! Risks due to falling parts! 8.20 Remove the tyre from the vulcanizing machine. Using a brush, remove any granules from the tyre. Then check whether the repair area has been correctly vulcanized. Do not speed up the cooling-down process of the repair area using water, compressed air etc. (fig. 8.20a and 8.20b) 8.21 If necessary, finish-buff the outside of the repair area after the vulcanization and complete cooling of the repair. Use finish buffer (ref.no. 595 5552). (fig. 8.21) Caution: use safety eye goggles! 33 Abb./fig./esq. 9.2 Abb./fig./esq. 9.1 axial Abb./fig./esq. 9.3 radial Abb./fig./esq. 9.4 Abb./fig./esq. 9.5 Abb./fig./esq. 9.6 34 IX. Handling of the machine for sidewall repairs to truck, and agricultural tyres The handling is shown on a sidewall injury which has been prepared according to the one-stage system described in the current REMA TIP TOP repair instructions. Attention! In order to be able to repair standard truck tyres (in sizes such as 305/70 R22.5), several parts from the attached list of accessories must be ordered, as these parts are not included in the standard shipment of the machine. 9.1 Switch the machine off by setting the mains switch to - 0 -. (fig. 9.1) Safety instruction: Work on electric parts, only when the machine is switched off. Risk due to electric current! 9.2 Remove the heating element from the granule filling; then using a spatula, adapt the surface of the pressure granulate roughly to the diameter of the tyre. (fig. 9.2) Safety instruction: Hold the heating element only by its holding loop to remove it from the granule filling. Risk of damage to the heating element. Use protective gloves! Danger of burning! 9.3.Put the heating element on the granules, with its cable outlet towards the rear of the vulcanizing machine (heating element in axial direction. (fig. 9.3) Then cover it completely with granules: Layer of granules on heating element sidewall repairs: 2 - 3 cm tread / shoulder: depth of tread pattern + 3 - 4 cm 9.4.To cure sidewall or shoulder re­pairs with large repair patches applied, put the heating element on the granules, with its cable outlet towards the rear of the vulcanizing machine (heating element in radial direction, fig. 9.4). Then cover it completely with granules as described in section 9.3. Safety instruction: Use protective gloves! Danger of burning! 9.5 We recommend drawing auxiliary lines (cross) on the outside of the tyre as far as the bead in order to make it easier to centre the tyre in the VULCSTAR vulcanizing ma­chine. Move the tyre to the vulcanizing machine and position the repair area as shown on the fig. 9.5. 9.6 Then tip the tyre forwards into the pressure bed so as to centre the repair area over the heating element in the granule filling. (fig. 9.6) Safety instruction: When changing the position of the tyre, always make sure that it is secured correctly! Observe the relevant regulations for prevention of accidents (e.g. the German UVV regulations), 35 Abb./fig./esq. 9.7a Abb./fig./esq. 9.7b Abb./fig./esq. 9.8a Abb./fig./esq. 9.8b Abb./fig./esq. 9.9a 36 Abb./fig./esq. 9.9b 9.7 The tyre is inclined in the vulcanizing machine, the inclination depending on the position of the repair patch Build up granules evenly around the tyre, making sure that the outside heating element is always covered with granules. This will ensure an even distribution of heat over the whole repair area. (fig. 9.7a and 9.7b) Safety instruction: Prevent the al­ready inclined tyre from tipping over. If necessary, use the tyre support (ref. no. 585 3159) for this purpose. 9.8 If inner heating mats are available (option), select the one which fits the repair patch applied. Powder both sides of the selected inner heating mat with talcum. Powder both sides of the selected inner heating mat with talcum. The heating mat has to cover the whole repair patch (together with any cushion gum applied to it) plus an at least 15 - 20 mm-wide area around the (laminated) patch. Now, powder the repair area with talcum, and centre the inner heating mat onto the repair area, with its cable outlet towards the rear of the vulcanizing machine. (fig. 9.8a and 9.8b) Safety instruction: always check the inner heating mat for visible defects or damage, before use! Immediately remove a damaged heating mat and replace it by the original spare part. 9.9 Select the Airpower-Bag which fits the selected inner heating mat and the repair patch applied. Powder the selected Airpower-Bag with talcum. The Airpower-Bag has to cover the repair patch (together with any cushion gum applied to it) plus an approx. 15 mm – wide area around them. Now, centre the Airpower-Bag onto the inner heating mat / the repair patch powdered with talcum. The compressed air connector of the Airpower-Bag has to face in the radial direction. (fig. 9.9a and 9.9b) Note: For sidewall repairs, the valves of the Airpower Bag always have to protrude over the bead. If the Airpower-Bag and the inner heating mat are regularly powdered with talcum, they will last much longer, and the repair will be more stable. Safety instruction: Always check the Airpower-Bag for defects or damage before use. Immediately remove a defective Air­ power-Bag and replace it by the original spare part. 37 Abb./fig./esq. 9.10a Abb./fig./esq. 9.10b Abb./fig./esq. 9.10c Abb./fig./esq. 9.11 Abb./fig./esq. 9.12 38 9.10 If necessary, adjust the upper pressure unit to the required height using the height adjusting device. Then insert the locking pin again. (fig. 9.10a) Move the cross-arm forwards, until the recess for the pressure clamp is centred over the repair area. Then, fit the pressure clamp on the crossarm. Secure the pressure clamp with the special locking pin. Note: Keep the distance between the airpower bag and the pressure clamp as short as possible in order to prevent the excessive inflation of the airpower bag. (fig 9.10b and 9.10c) Safety instruction: Check all parts for any defects or damage! Immediately remove defective parts and replace them by original REMA TIP TOP spare parts. Always insert the locking pins and check whether they are seated correctly. The optimum distribution of pressure over the top side of the repair patch must be ensured by an air cushion which is built up while inflating the airpower-bag. 9.11 S crew the valve core of the Air­ power-Bag in; then inflate the Air­ power-Bag up to 1.0 bar / 15 psi, using a tyre inflator, thus locking the pressure system. (fig. 9.11) Safety instruction: Inflate the Air­powerBag only with compressed air free from oil! 9.12 O pen the hand lever valve and let the vibrator operate for approx. 45 - 60 seconds. Thus the granules are compacted, filling the voids and providing a contour that snugly fits the tyre and ensures optimum distribution of heat. If the granule layer under the repair area becomes too thin during this process, push granules towards the tyre using the spatula. (fig. 9.12) After this time, close the hand lever valve again, and check again whether all pressure exerting parts and locking elements are seated precisely. If the position of pressure exerting parts has to be changed, release the pressure in the AirpowerBag, and repeat the operations described from no. 9.8 onwards. Safety instruction: The vibrator generates high-frequency vibrations. Do not put any fragile parts / objects on the machine. Use the vibrator only together with the original pressure regulating flow control valve. Risk of excessive stress and increased noise level. 39 Abb./fig./esq. 9.13a Abb./fig./esq. 9.13b Abb./fig./esq. 9.14 Abb./fig./esq. 9.15a Abb./fig./esq. 9.15b Abb./fig./esq. 9.16 40 9.13 Select a counter pressure plate depending on the distance between the bead and the machine frame. Install the counter pressure bar with the pressure spindle. Position the counter pressure plate near the bead, and secure it with the pressure spindle. Gene­rate enough pressure using the pneumatic wrench or the tubular socket wrench. (fig. 9.13a and b) Safety instruction: The counter pressure plate is essential to provide a contour that snugly fits the tyre and optimizes the flow of the skive filling rubber. 9.14 Increase the pressure in the Airpower-Bag up to 3 bar / 43 psi (size II and IV) 2.5 bar / 36 psi (size VI) and remove the tyre inflator. Check the valve of the AirpowerBag for air tightness, then close the valve with the valve cap. (fig. 9.14) Do not use the vibrator any longer until the end of the curing process. Safety instruction: Fill the Air­power– Bag only with compressed air free from oil. 9.15 Select the appropriate curing time according to the chart X. (see page 44). Switch the vulcanizing machine on by setting the mains switch (28) to - I -. Wind up the timer with one complete revolution (26), then reset it to the required curing time. (fig. 9.15a and 9.15b) Safety instruction: Do not leave the machine unattended when it is operating. Observe the relevant measures for fire protection and the regulations regarding the use of electric heating systems. Never use the machine with humid granules! Risks due to electric current and formation of steam. 9.16 At the end of the previously set curing time, the heating system is automatically cut off by the timer. Switch the vulcanizing machine off by setting the mains switch to - 0 -. Completely release the pressure in the Airpower-Bag by removing the valve core, then remove the pressure-exerting parts. (fig. 9.16) Safety instructions: Use protective gloves! Danger of burning due to hot pressure granules / hot parts! Deposit all the parts on the tool shelves designed for this purpose! Risks due to falling parts! 41 Abb./fig./esq. 9.17 42 9.17 Remove the tyre from the vulcanizing machine. Using a brush, remove any pressure granules from the tyre. Then check whether the repair area has been correctly vulcanized. Do not speed up the cooling-down process of the repair area using water, compressed air etc. (fig. 9.17) 9.18 If necessary, finish-buff the outside of the repair area after the vulcanization and complete cooling of the repair. Caution: Use safety eye goggles. 43 X. Curing time chart (All the information given refers only to the use of original REMA TIP TOP materials and ambient temperatures of at least +15 °C / 59 °F) Caution: In case of sidewall repairs to truck tyres with a height/width ratio of under 75% and a narrow radius (e.g. 305 / 70 R 22.5), inner heating mats may prevent the correct positioning of the pressure blocks. In this case, precisely fitting the pressure block S 1or S 2 on the tyre contour and centring it onto the injury is more important than using an inner heating mat. without inner heating system with inner heating system with SPEED inner heating system Truck and agricultural tyres in case of tread and shoulder repairs 3,5 hours Truck and agricultural tyre sidewall repairs 2,5 hours 2,0 hours 1,3 hours In general all rubber-only or penetrating injuries with or without repair patches, or repairs to lugs in the tread and shoulder area of agricultural tyres max. tyre thickness in mm x 5 mins. (e.g. 25 mm x 5 mins. = 125 mins.) 3,0 hours1,5 hours max. tyre thickness in mm x 5 mins. - 30 mins. (e.g. 25 mm x 5 Min. - 30 mins. = 95 mins.) max. tyre thickness in mm x 3 mins. (e.g. 25 mm x 3 mins. = 75 mins.) These recommended curing times refer only to the use of a cold vulcanizing machine. Within a series of curing processes carried out at intervals no longer than 30 minutes, you can reduce the curing times given in the above chart by 20 minutes from the second curing process onwards. This rule will also be applicable, if the pressure granules are pre-heated separately for 60 minutes, that is without any tyre placed in the vulcanizing machine. At ambient temperatures ranging between 0 °C / 32 °F to +15°C / 59 °F, the curing times given in the above chart have to be extended by 20 minutes. Note: In order to cure laminated (cushion-backed) repair patches (except for those with SV Blue Bonding Rubber) or uncured rubber patches, we recommend using an inner heating mat. If no inner heating mat is used, extend the curing times specified, by 60 minutes respectively. 44 3,0 horas1,5 horas 2,5 horas 2,0 horas 1,3 horas Grosor máximo del neumático en mm x 5 min (p. ej.: 25 mm x 5 min = 125 min) 45 Material 1 x monatlich Universalöl Airpower - Bag Formgranulat REMA TIP TOP Formgranulat XI. Maintenance As the REMA TIP TOP Vulcstar machines are very reliable, thanks to their construction and the high quality of their parts and materials, they have long intervals between servicing. For safety and warranty reasons, damaged machine parts should immediately be replaced by original REMA TIP TOP spare parts. Any work on electric components as well as any work which exceeds maintenance work has to be carried out only by a qualified specialist. Maintenance schedule Machine part Type of maintenance work Required material Sliding surfaces of the cross-arm Clean and slightly lubricate them Once every month Universal oil Check for tightness and damage Airpower - Bag Check the safety valve Visually check for damage Locking pins Screw links Check, tighten loose screws, if necessary Compressed air supply Drain the water separator in the air line Pressure granules Remove foreign bodies; compensate for loss of granules, if necessary 46 Every time the machine is put into operation A month after putting the machine into operation for the first time, then: once every three months Periodically Immediately remove damaged parts, and replace them by original REMA TIP TOP spare parts Granulat granulat REMA TIP TOP Materiales 1 vez por mes Aceite universal Airpower - Bag Pernos de seguridad Granulado regularmente Granulado REMA TIP TOP 47 48 Nur original- REMA TIP TOP Reparaturmaterial und - MTR-Rubber verwenden XII. Trouble shooting Trouble Possible reason The mains switch does not illuminate The machine has not been switched on Switch the machine on by means of the mains switch No mains power supply Restore the electric power supply Defective fuse Replace the fuse The time set does not elapse on the timer face Defective timer Replace the part by original REMA TIP TOP spare part The heating element in the granules does not heat up No mains power supply See “possible solution - mains switch” The inner heating mat does not heat up Timer not set Set the timer to the required curing time Defective timer Replace the part by original REMA TIP TOP spare part Defective heating element or control box Remove the parts and replace them by the respective original REMA TIP TOP spare parts. Send the old parts to REMA TIP TOP for inspection The mains switch does not illuminate See “possible solution – mains switch” Timer not set Set the timer to the required curing time Defective timer Replace the part by the original REMA TIP TOP spare part Defective inner heating mat or control box Replace the inner heating mat by the original REMA TIP TOP spare part Remove the control box together with the pressure granule heating system and replace them by the original REMA TIP TOP spare parts. Send the old parts to REMA TIP TOP for inspection Evidence of insufficient curing pressure on the tyre outside/sidewall The layer of granules between the heating element and the tyre is too thin The vibrator has not worked long enough to provide sufficient density of the granules The vibrator has worked too long, thus causing too large a quantity of granules to flow away from the repair area Evidence of insufficient curing pressure on the tyre inside Repair area not vulcanized enough Make sure that the layer of granules on the heating element is thick enough. See item 7.3 page 15 Put the vibrator into operation and let it operate for approx. 45 - 60 seconds according to this manual item 7.10, page 19 Use only REMA TIP TOP granules Air entrapment in the skive filling Fill the skive carefully and stitch on thoroughly No counter pressure plate The counter pressure plate is essential to provide a contour that snugly fits the tyre Make sure of sufficient pressure (Tubular socket wrench, pneumatic wrench) Wrong counter-pressure plate selected Select the largest possible counter-pressure plate and position it near the bead After the compacting of the granules, the pressure in the Airpower-Bag has not been increased After compacting the granules, increase the pressure in the Airpower-Bag up to 3 bar / 43 psi or 2.5 bar / 36 psi The inner heating mat selected is too small The inner heating mat has to cover the repair patch all around. Use the right size! The Airpower-Bag selected is too small The Airpower-Bag has to cover the repair patch all around. Use the right size! The Airpower-Bag does not exert enough pressure Check the operating pressure (3 bar / 43 psi or 2.5 bar /36 psi) in the Airpower-Bag Insufficient counter-pressure put on the tyre outside Check whether the repair area is correctly positioned in the pressure granules and whether there are enough granules under the repair area Curing time too short Observe or determine the curing times according to this manual The required temperature has not been reached within the previously set curing time The layer of pressure granules between the heating element and the tyre is too thick, or the heating element is too far away from the tyre At ambient temperatures below +15 °C/ 59 °F, extend the curing time accordingly The repair material/skive filling used vulcanizes too slowly Use only original REMA TIP TOP repair material and REMA TIP TOP MTR Rubber Too high mechanical pressure on Airpower-Bag Tighten the pressure spindle only with your hands. Inflate the Airpower-Bag up to 1 bar 49 Vulcanisation insuffisante Granulat inapproprié Pression insuffisante Membrane gonflable Airpower-Bag choisie trop petite 50 El temporizador no finaliza No se ha dado cuerda al temporizador No se ha dado cuerda al temporizador La almohadilla eléctrica interior no se calienta 51 Xlll. Zubehör / Accessories / Accessoires / Accesorios Pos. 1 2 3 4 5 6 7 8 9 10 11 12 Pos. Ref. No. 1 2 3 4 5 6 7 8 9 10 11 12 585 3159 585 3290 585 3173 585 1807 585 3142 585 3269 585 3056 585 3087 517 6946 585 3018 585 3025 585 3276 tyre support Adapter for sidewall pressure clamp / T-piece Pressure bar (40 mm diameter), complete (Pneumatic) wrench with adapter pressure clamp for shoulder and sidewall repairs Locking pin for sidewall pressure clamp Pressure block L 1 Pressure block S 1 Airpower Bag size II approx 300 x 320 mm Vulcstar inner heating mat II 230 V approx 200 x 380 mm Vulcstar inner heating mat IV 230 V approx 310 x 475 mm Locking pin (12 mm diameter) for pressure bar Pos. Réf. 1 2 3 4 5 6 7 8 9 10 11 12 585 3159 585 3290 585 3173 585 1807 585 3142 585 3269 585 3056 585 3087 517 6946 585 3018 585 3025 585 3276 Pos. № Ref. 1 2 3 4 5 6 7 8 9 10 11 12 52 Xlll. Zubehör / Accessories / Accessoires / Accesorios 7 9 8 4 1 11 6 12 3 5 2 10 53 XIV. Explosionszeichnung / Exploded view / Vue éclatée / Despiece 21 22 13 17 25 12 26 36 1 14 24 41 32 37 10 31 9 34 19 28 27 23 15 44 16 1 44 35 20 40 6 54 7 1 2 3 4 5 6 7 8 9 10 11 12 13 14 15 16 17 18 19 20 21 22 23 24 25 26 27 28 29 30 31 32 33 34 35 36 37 38 39 40 41 42 43 44 45 55 XV. Spare Parts List Vulcstar / Vulcstar accessories Ref. No. 585 3003 Pos. Ref. No. Description 1 2 3 4 5 6 7 8 9 10 11 12 13 14 15 16 17 18 19 20 21 22 23 24 25 26 27 28 29 30 31 32 33 34 35 36 37 38 39 40 41 42 43 44 45 585 3049 * Vulcstar control box including heating element for pressure granules, approx 500 x 700 mm 585 3032 * pressure granules, (14 sacks, each 25 kg) 585 3018 * Vulcstar inner heating mat II, 230 V, approx 200 x 380 mm 585 3025 * Vulcstar inner heating mat IV, 230 V, approx 310 x 475 mm 517 6946 * Airpower Bag size II, approx 300 x 320 mm 517 6939 * Airpower Bag size IV, approx 300 x 470 mm 517 6757 * Airpower Bag size VI, approx 400 x 470 mm 585 3056 Pressure block L 1 585 3063 Pressure block L 2 585 3070 Pressure block L 3 585 3087 Pressure block S 1 585 3094 Pressure block S 2 585 3104 Pressure block S 3 585 3135 Pressure plate for agricultural tyres AS 1 585 3111 Counter-pressure plate GD 1 585 3128 Counter-pressure plate GD 2 585 3142 pressure clamp for shoulder and sidewall repairs 585 3173 Pressure bar (40 mm diameter), complete 585 7825 Tubular socket wrench for pressure spindle 540 0052 Set of 4 rubber pads, approx 100 x 100 x 30 mm 585 3180 * Mains cable 585 3197 Mains supply connector 585 3207 * Vibrator with fastening screws 585 3214 Hand lever valve 585 3221 Mains switch 585 3238 Timer 0 - 6 hours 585 3245 Pressure regulating flow control valve 6 bar / 87 psi 585 3252 * counter-pressure bar with spindle / extension of counter-pressure bar 585 3269 Locking pin for sidewall pressure clamp 585 3276 Locking pin (12 mm diameter) for pressure bar 585 3283 Locking pin (20 mm diameter) for frame 557 8434 Safety pin for locking pin (20 mm diameter) 585 3290 Adapter for sidewall pressure clamp / T-piece 585 3440 Height adjusting lever 585 3166 Spatula for pressure granules 585 3317 Fuse-holder 10 A (with cap) 585 1807 * (Pneumatic) wrench with adapter 585 3430 *socket adapter set: socket adapter casing, pressure spindle with guide bushing and special locking pin 585 3470 adapter 585 3136 Pressure plate for agricultural tyres AS 2 585 3095 Pressure block AS 2 585 3540 shovel for granules 585 3550 bucket for granules 22 liters (4x) 585 3416 diamond-shaped tool tray, 600 x 145 x 8 mm, 4x 585 3159 tyre support Safety instruction. Allow only a qualified specialist to carry out any work on electric parts! The parts marked with an asterisk *) are wear parts, for which no liability based on any legal regulations whatsoever can be accepted. 56 Réf. 1 2 3 4 5 6 7 8 9 10 11 12 13 14 15 16 17 18 19 20 21 22 23 24 25 26 27 28 29 30 31 32 33 34 35 36 37 38 39 40 41 42 43 44 45 57 № Ref. 1 2 3 4 5 6 7 8 9 10 11 12 13 14 15 16 17 18 19 20 21 22 23 24 25 26 27 28 29 30 31 32 33 34 35 36 37 38 39 40 41 42 43 44 45 58 Anschlussplan - Wiring diagram - Schéma des connexions - Esquema de conexiones Anschlussplan für den Anschluss von Vulcstar 2001 Geräten an ein 115 V Netz (USA) Sicherheitshinweis: Arbeiten an stromführenden Bauteilen nur von einem Fachmann durchführen lassen! Wiring diagram for connecting Vulcstar 2001 to 115 Volt USA-mains supply Security remarks: The wiring has to be done only by a qualified electrician! Schéma des connexions pour Vulcstar - version 2001 pour le branchement sur l´alimentation secteur 115 Volts (Etats Unis). Consigne de sécurité : Il faut que le branchement ne soit fait que par un électricien qualifié. Esquema de conexiones Vulcstar 2001 para la conexión a la red eléctrica 115 voltios (EE.UU.) Instrucción de seguridad: ¡La conexión debe ser llevada a cabo únicamente por un electricista autorizado! Wenn dieses Messergebnis erreicht wur­ de bitte nach nebenstehendem Schaltbild anschließen. When this measuring result has been attained, connect according to the wiring diagram opposite. Lorsque ce résultat de mesure est indiqué, faites le branchement conformément au schéma ci-contre. Una vez conseguido este resultado de me­dición, conecte el aparato según el es­quema de conexiones al lado. Starting from serial number/ab Seriennr./à partir du numéro de série/ a partir del número de serie : 01-039-002 59 Air Power Bag Anwendungshinweise / Instructions for use / Notice d´utilisation / Nota de utlilización Typ / Type Type / Tipo Air Power Bag II 517 6946 Air Power Bag IV 517 6939 Air Power Bag VI 517 6757 300 mm x 320 mm 300 mm x 470 mm 400 mm x 470 mm max. 3 bar / 43 psi max. 3 bar / 43 psi max. 2,5 bar / 36 psi Air Power Bag 1. Use for tread repairs - The Air Power Bag has to cover the repair patch sufficiently, - with its air connector valve facing in the running direction. (see fig.1) Abb. / Fig. / Esquema 1 2. Use for sidewall and shoulder repairs: - The Air Power Bag has to cover the repair patch sufficiently. - Make sure that the air connector valve protrudes over the bead. (see fig.2) richtig Correct Correct CORRECTO Air Power Bag II Air Power Bag IV Air Power Bag VI 2. Ventil wird geknickt / The valve is twisted. / Le raccord d´air est plié. / La válvula de conexión se dobla. Abb. / Fig. / Esquema 2 Die Ventile des Air Power Bag müssen über den Wulst hinausragen! Ein Abknicken der Ventile führt zur Beschädigung des Air Power Bag. The valves of the Air Power Bag have to protrude over the bead. Twisting the valves causes damage to the Air Power Bag. La valve et la soupape de la membrane gonflable Airpower-Bag doivent dépasser du talon. Toute déformation de la valve et de la soupape occasionnera des dommages de la membrane gonflable. La válvula de conexión así como la válvula de sobrepresión del colchón neumático Air Power Bag tienen que solapar el talón. Todo tipo de deformación de dichas válvulas causará deterioros en el colchón neumático. 60 Air Power Bag • • • • • • • • • • • Air Power Bag Use the Air Power Bag only together with the VULCSTAR and TRUCKMASTER vulcanizing machines. Do not use it as a lifting device etc. Always check the Air Power Bag for damage before use. Always position the Air Power Bag with the vulcanette/ logo facing upwards. Use only original REMA TIP TOP pressure blocks for the transmission of pressure. Always make sure that all locking pins are seated and secured correctly on the vulcanizing machine/the pressure units before inflating the Airpower-Bag. Fill the Airpower Bag only with compressed air free from oil. The maximum operating pressure must not be exceeded. (For information about the right operating pressure for the repair, refer to the user´s manual of the vulcanizing machine.) Do not change the pre-set pressure on the safety valve or damage it. Protect the Airpower-Bag from oil, grease, solvents and acids. Do not put the Airpower-Bag on hot, sharp-edged or pointed objects. Observe the general safety regulations and the regulations for prevention of accidents. • • • • • • • • • • • • • • • • • • • • • • • • • • • • • • • • • 61 Printed in Germany Vll.09 581 1190 REMA TIP TOP GmbH Gruber Straße 63 85586 Poing / Germany 62 Tel.: +49 8121 707-322 Fax: +49 8121 707-349 www.rema-tiptop.com
advertisement
* Your assessment is very important for improving the workof artificial intelligence, which forms the content of this project
Related manuals
advertisement
Languages
Only pages of the document in English were displayed