advertisement
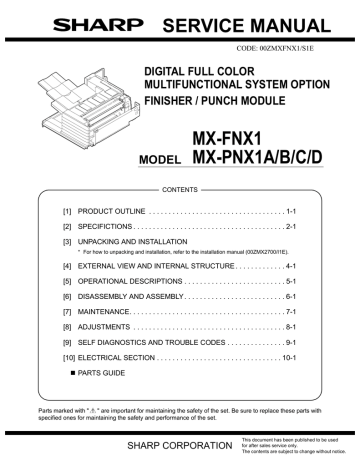
1. Circuit descriptions
A. MX-FNX1
(1) General
This circuit controls transport, alignment (bundle alignment), staple, and exit of paper discharged from the main unit.
This circuit is composed of sensors, switches, the circuit which processes signals from the main unit, the circuit which drives motors and solenoids, the CPU, and its peripheral circuits.
(2) Circuit descriptions a. Communication circuit
Service Manual
The tray intermediate lower limit sensor (FMLLD) employs the photo interrupter in which the light emitting diode and the photo transistor are integrated.
The lower limit is detected by interruption of lights with the light-shielding plate.
Signals are inputted to the multiplexer (IC14-14pin) through the noise filter of R12 and C2.
The logic of the signal inputted to the CPU is L for the tray intermediate position.
R2 is the current-limiting resistor of the light emitting diode. R7 is the load resistor of the sensor.
3) Tray lower limit sensor (FLLD)
The tray lower limit sensor (FLLD) employs the photo interrupter in which the light emitting diode and the photo transistor are integrated.
The lower limit is detected by interruption of lights with the light-shielding plate.
Signals are inputted to the multiplexer (IC14-15pin) through the noise filter of R13 and C3.
The logic of the signal inputted to the CPU is L for the tray lower limit position.
R3 is the current-limiting resistor of the light emitting diode. R8 is the load resistor of the sensor.
Tray paper empty sensor (FBED)
This circuit is the communication circuit with the main unit.
TxD and DTR are data to be sent from the main unit to the inner finisher. RxD and DSR are data to be sent from the inner finisher to the main unit. The reset signal from the main unit is inputted to
RESET.
b. Sensor input circuit
Tray upper limit sensor (FULD)
4) Tray paper empty sensor (FBED)
The tray empty sensor (FBED) employs the photo interrupter in which the light emitting diode and the photo transistor are integrated.
Paper empty is detected by interruption of lights with the levertype actuator.
Signals are inputted to the CPU (IC10-74pin) through the noise filter of R14 and C4.
The logic of the signal inputted to the CPU is L when paper is loaded to the tray, and H for paper empty.
R4 is the current-limiting resistor of the light emitting diode. R9 is the load resistor of the sensor.
Paper surface detection sensor 1
(FSLD1)
Paper surface detection sensor 2
(FSLD2)
Tray intermediate lower limit sensor
(FMLLD)
Tray lower limit sensor (FLLD)
1) Tray upper limit sensor (FULD)
The tray upper limit sensor (FULD) employs the photo interrupter in which the light emitting diode and the photo transistor are integrated.
The upper limit is detected by interruption of lights with the light-shielding plate.
Signals are inputted to the multiplexer (IC14-13pin) through the noise filter of R11 and C1.
The logic of the signal inputted to the CPU is L for the tray upper limit position.
R1 is the current-limiting resistor of the light emitting diode. R6 is the load resistor of the sensor.
5) Paper surface sensor 1 (FSLD1)
The paper surface sensor 1 (FSLD1) employs the photo interrupter in which the light emitting diode and the photo transistor are integrated.
The paper surface is detected by interruption of lights with the lever-type actuator.
By use of Q16, the logic of signal when the connector is disconnected is made the same as when light is emitted to the sensor.
Signals are inputted to the CPU (IC10-88pin) through the noise filter of R17 and C5.
The logic of the signal inputted to the CPU is H when light is interrupted, and L when light is emitted to the sensor.
R5 is the current-limiting resistor of the light emitting diode.
R15 is the load resistor of the sensor.
MX-FNX1/MX-PNX1 ELECTRICAL SECTION 10 – 1
6) Paper surface sensor 2 (FSLD2)
The paper surface sensor 2 (FSLD2) employs the photo interrupter in which the light emitting diode and the photo transistor are integrated.
The paper surface is detected by interruption of lights with the lever-type actuator.
Signals are inputted to the CPU (IC10-89pin) through the noise filter of R18 and C6.
The logic of the signal inputted to the CPU is H when light is interrupted, and L when light is emitted to the sensor.
R10 is the current-limiting resistor of the light emitting diode.
R16 is the load resistor of the sensor.
Stapler HP sensor (FSTHPD)
Alignment plate HP sensor F
(FFJHPD)
Alignment plate HP sensor R
(FRJHPD)
The logic of the signal inputted to the CPU is L at the front side alignment guide home position.
R21 is the current-limiting resistor of the light emitting diode.
R25 is the load resistor of the sensor.
10) Alignment plate HP sensor R (FRJHPD)
The alignment plate HP sensor R (FRJHPD) employs the photo interrupter in which the light emitting diode and the photo transistor are integrated.
The home position is detected by interruption of lights with the actuator of the light-shielding plate.
Signals are inputted to the CPU (IC10-58pin) through the noise filter of R30 and C10.
The logic of the signal inputted to the CPU is L at the rear side alignment guide home position.
R22 is the current-limiting resistor of the light emitting diode.
R26 is the load resistor of the sensor.
Inlet port sensor (FED)
7) Stapler HP sensor (FSTHPD)
Stapler HP sensor (FSTHPD) employs the photo interrupter in which the light emitting diode and the photo transistor are integrated.
The home position is detected by interruption of lights with the actuator of the light-shielding plate.
Signals are inputted to the CPU (IC10-18pin) through the noise filter of R27 and C7.
The logic of the signal inputted to the CPU is H at the stapler unit home position.
R19 is the current-limiting resistor of the light emitting diode.
R23 is the load resistor of the sensor.
Empty sensor (FSTPD)
Roller up/down sensor (FRLD)
Take-up belt sensor (FBRD)
8) Empty sensor (FSTPD)
The empty sensor (FSTPD) employs the photo interrupter in which the light emitting diode and the photo transistor are integrated.
Paper empty is detected by interruption of lights with the levertype actuator.
By use of Q16, the logic of signal when the connector is disconnected is made the same as when light is emitted to the sensor (paper empty).
Signals are inputted to the CPU (IC10-90pin) through the noise filter of R28 and C8.
The logic of the signal inputted to the CPU is H when paper is provided in the process tray, and L when paper is not provided.
R20 is the current-limiting resistor of the light emitting diode.
R24 is the load resistor of the sensor.
9) Alignment plate HP sensor F (FFJHPD)
The alignment plate HP sensor F (FFJHPD) employs the photo interrupter in which the light emitting diode and the photo transistor are integrated.
The home position is detected by interruption of lights with the actuator of the light-shielding plate.
Signals are inputted to the CPU (IC10-57pin) through the noise filter of R29 and C9.
MX-FNX1/MX-PNX1 ELECTRICAL SECTION 10 – 2
11) Inlet port sensor (FED)
The inlet port sensor (FED) employs the photo interrupter in which the light emitting diode and the photo transistor are integrated.
The inlet port is detected by interruption of lights with the levertype actuator.
Signals are inputted to the CPU (IC10-71pin) through the noise filter of R37 and C11.
The logic of the signal inputted to the CPU is H when paper is provided, and L when paper is not provided.
R31 is the current-limiting resistor of the light emitting diode.
R34 is the load resistor of the sensor.
12) Roller up/down sensor (FRLD)
The roller up/down sensor (FRLD) employs the photo interrupter in which the light emitting diode and the photo transistor are integrated.
The roller up/down is detected by interruption of lights with the lever-type actuator.
Signals are inputted to the CPU (IC10-59pin) through the noise filter of R38 and C12.
The logic of the signal inputted to the CPU is L when the roller is at the upper standby position.
R32 is the current-limiting resistor of the light emitting diode.
R35 is the load resistor of the sensor.
13) Take-up belt sensor (FBRD)
The take-up belt sensor (FBRD) employs the photo interrupter in which the light emitting diode and the photo transistor are integrated.
The take-up belt is detected by interruption of lights with the lever-type actuator.
Signals are inputted to the CPU (IC10-61pin) through the noise filter of R39 and C50.
The logic of the signal inputted to the CPU is L when the takeup belt is on the upper side.
R33 is the current-limiting resistor of the light emitting diode.
R36 is the load resistor of the sensor.
Stapler
Alignment plate position sensor
(FJPD)
Stapler home sensor
(FSHPD)
14) Alignment plate position sensor (FJPD)
The alignment plate position sensor (FJPD) employs the photo interrupter in which the light emitting diode and the photo transistor are integrated.
The alignment plate position is detected by interruption of lights with the lever-type actuator.
Signals are inputted to the multi-plexer (IC14-12pin) through the noise filter of RA4.1 and C58.
The logic of the signal inputted to the CPU is L when the paper rear edge stopper is provided at the opening of the stapler.
R103 is the current-limiting resistor of the light emitting diode.
R104 is the load resistor of the sensor.
15) Stapler home sensor (FSHPD)
The stapler home sensor (FSHPD) is the built-in sensor of the stapler unit.
The home position is detected by the open-collector output with the circuit in the unit.
Signals are inputted to the multi-plexer (IC14-1pin) through the noise filter of RA4.4 and C59.
The logic of the signal inputted to the CPU is H at the stapler mechanism home position.
16) Self priming sensor (FSTD)
The self priming sensor (FSTD) is the built-in sensor of the stapler unit.
Self priming is detected by the open-collector output with the circuit in the unit.
Signals are inputted to the multi-plexer (IC14-5pin) through the noise filter of RA4.2 and C60.
The logic of the signal inputted to the CPU is H in the READY state.
17) Staple empty sensor (FSD)
The staple empty sensor (FSD) is the built-in sensor of the stapler unit.
Staple empty is detected by the open-collector output with the circuit in the unit.
Signals are inputted to the multi-plexer (IC14-2pin) through the noise filter of RA4.3 and C61.
The logic of the signal inputted to the CPU is L in case of staple empty.
18) Front cover switch (FDSW)
The front cover switch (FDSW) employs a micro switch to detect open/close of the front cover.
This switch is provided with +24V. By opening the open/close section, the contact is opened to function as a switch.
When the switch is turned ON, +24V is applied to the cathode of ZD2, supplying a base current to Q2 to turn ON Q2. Then open/close signal is inputted to the CPU (IC10-19pin). This signal is commonly used with the inner punch +5V supply signal.
The logic of the signal inputted to the CPU is H when the front cover is open, and L when the front cover is close.
c. Motor drive circuit
1) Transport motor (FRM) drive circuit
Transport motor
(FRM)
Not installed
This circuit controls rotation, stop, rotating direction, and current of the transport motor (FRM), and is composed of the CPU (IC10), the DA converter (IC11), and the constant-current chopper system driver IC (IC5). The motor rotating speed is controlled with the stepping motor drive signal (R_MOT_CLK) outputted from the CPU (IC10-22pin), and the motor rotating direction is controlled with the signal
(R_MOT_CW/CCW) outputted from the CPU (IC10-21pin).
The analog signal (R_MOT_REF) outputted from the DA converter (IC11-3pin) is divided into a certain voltage with R70 and R71. The divided voltage is inputted to IC5-7pin to set the motor current value.
MX-FNX1/MX-PNX1 ELECTRICAL SECTION 10 – 3
2) Bundle exit motor (FAM) drive circuit
This circuit controls rotation/stop rotating direction and current of the bundle exit motor (FAM), and is composed of the CPU (IC10), the DA converter (IC11), and the constant-current chopper system driver IC (IC8). The motor rotating speed and the rotting direction are controlled with the stepping motor drive excitement pattern signal (T_MOT_A, *A, B, *B) outputted from the CPU (IC10-79, 80, 81, 82pin).
The analog signal (T_MOT_REF) outputted from the DA converter (IC11-5pin) is divided into a certain voltage with R74 and R75. The divided voltage is inputted to IC8-3, 14 pin to set the motor current value.
Bundle exit motor (FAM)
Not installed
3) Roller up/down motor (FSWM) drive circuit
This circuit controls rotation/stop and the rotating direction of the roller up/down motor (FSWM) and the motor current, and is composed of the CPU (IC10), the DA converter (IC11), and the constant-current chopper system driver IC (IC16). The motor rotating speed and the rotating direction are controlled with the stepping motor drive excitement pattern signal (RO_MOT_A, *A, B, *B) outputted from the CPU
(IC10-75, 76, 77, 78pin).
The analog signal (RO_MOT_REF) outputted from the DA converter (IC11-4pin) is divided into a certain voltage with R90 and R114. The divided voltage is inputted to IC16-3, 14pin to set the motor current value.
Roller up/down motor (FSWM)
4) Staple shift motor (FSM) drive circuit
MX-FNX1/MX-PNX1 ELECTRICAL SECTION 10 – 4
Not installed
Staple shift motor (FSM)
Not installed
This circuit controls rotation/stop and the rotating direction of the staple shift motor (FSM) and the motor current, and is composed of the
CPU (IC10), the DA converter (IC11), and the constant-current chopper system driver IC (IC4). The motor rotating speed and the rotating direction are controlled with the stepping motor drive excitement pattern signal (ST_MOT_PA, PB, EA, EB) outputted from the CPU (IC10-
45, 46, 47, 48pin).
The analog signal (ST_MOT_REF) outputted from the DA converter (IC11-18pin) is divided into a certain voltage with R64 and R65. The divided voltage is inputted to IC4-3, 4pin to set the motor current value. The logic of the standby signal (MOT_STY) outputted from the DA converter (IC11-7pin) is H when the motor can be operated (READY).
5) Alignment motor F (FFJM) drive circuit
6) Alignment motor R (FRJM) drive circuit
Alignment motor F (FFJM)
Not installed
Alignment motor R (FRJM)
Not installed
This circuit controls rotation/stop and the rotating direction of the alignment motor F (FFJM) and the motor current, and is composed of the
CPU (IC10), the DA converter (IC11), and the constant-current chopper system driver IC (IC17). The motor rotating speed and the rotating direction are controlled with the stepping motor drive excitement pattern signal (J1_MOT_PA, PB, EA, EB) outputted from the CPU (IC10-
49, 50, 51, 52pin).
The analog signal (J1_MOT_REF) outputted from the DA converter (IC11-19pin) is divided into a certain voltage with R125 and R126. The divided voltage is inputted to IC17-3, 4pin to set the motor current value. The logic of the standby signal (MOT_STY) outputted from the
DA converter (IC11-7pin) is H when the motor can be operated (READY state).
This circuit controls rotation/stop and the rotating direction of the alignment motor R (FRJM) and the motor current, and is composed of the
CPU (IC10), the DA converter (IC11), and the constant-current chopper system driver IC (IC18). The motor rotating speed and the rotating direction are controlled with the stepping motor drive excitement pattern signal (J2_MOT_PA, PB, EA, EB) outputted from the CPU (IC10-
53, 54, 55, 56pin).
The analog signal (J2_MOT_REF) outputted from the DA converter (IC11-2pin) is divided into a certain voltage with R127 and R128. The divided voltage is inputted to IC18-3, 4pin to set the motor current value. The logic of the standby signal (MOT_STY) outputted from the
DA converter (IC11-7pin) is H when the motor can be operated (READY state).
MX-FNX1/MX-PNX1 ELECTRICAL SECTION 10 – 5
7) Staple motor (FFSM) drive circuit
Staple motor
(FFSM)
This circuit controls rotation/stop and the rotating direction of the staple motor (FFSM), and is composed of the CPU (IC10) and the FET
(Q10, 11, 12, 13). The DC motor is controlled with the staple motor (FFSM) drive normal rotation signal, the reverse rotation signal, and the brake signal outputted from the CPU (IC10-5, 8, 9pin).
To protect the motor and the mechanism, the current limit circuit is provided, which supplies the motor drive OFF signal when the current flowing through the detection resistors R78 and R79 exceeds 3.8A, restricting the current not to exceed 3.8A.
8) Tray motor (FTLM) drive circuit 9) Fan (FFAN) drive circuit
Tray motor (FTLM)
Fan (FFAN)
This circuit controls the tray motor (FTLM) rotation, stop, and rotating direction, and is composed of the CPU (IC10) and the
DC motor driver IC (IC19). The CPU (IC10-69, 70pin) outputs the tray motor (FTLM) drive normal rotation signal, the reverse rotation signal, and the brake signal to control the DC motor. In addition, the current limiting circuit is formed with R129, R130,
R131, and R132 for the current flowing through the motor not to exceed 0.65A.
This circuit controls the fan (FFAN) rotation, stop, and rotating direction, and is composed of the CPU (IC10) and the digital transistors (Q14, Q18). The DA converter (IC11-13pin) outputs the fan (FFAN) drive signal to drive the motor. The fan lock signal is inputted through the noise filter of R168 and C130 to the
CPU (IC10-20pin) by the open drain output of the fan built-in circuit.
The logic of the signal inputted to the CPU is H when locked.
MX-FNX1/MX-PNX1 ELECTRICAL SECTION 10 – 6
d. Flapper solenoid (FINRPS), belt separation solenoid (FBRS), paper surface detection solenoid (FSLS), paddle one-rotation solenoid (FPDS) drive circuit
Flapper solenoid
(FINRPS)
Belt separation solenoid
(FBRS)
Paper surface detection solenoid (FSLS)
Paddle one-rotation solenoid (FPDS)
This circuit controls attachment and release of the flapper solenoid (FINRPS), the belt separation solenoid (FBRS), the paper surface detection solenoid (FSLS), and the paddle one-rotation solenoid (FPDS).
The CPU (IC10-24, 26) outputs the drive signal of the flapper solenoid (FINRPS) and the paddle one-rotation solenoid (FPDS) to turn ON Q23 and Q20 to attach the solenoid.
The CPU (IC10-27,28) outputs the drive signal of the belt separation solenoid (FBRS) and paper surface detection solenoid (FSLS) to turn on
Q19 and Q22 to attach the solenoid.
The drive signal of the flapper solenoid (FINRPS) and the paper surface detection solenoid is a PWM signal. After completion of attachment, the flapper solenoid (FINRPS) duty is 20%. Paper surface detection solenoid (FSLS): Duty is reduced to 50% and the solenoid temperature rise is reduced to keep attachment.
e. Reset circuit f. EEPROM circuit
Not installed
This circuit generates the reset signal and supplies it to the CPU when the power is turned ON and when the power voltage fall is detected.
IC13-6pin (OUT) is normally at HIGH level after turning ON the power. When, however, +5V power voltage falls to 4.05V or less because of power OFF or any other reasons, IC13-6pin is driven to
LOW level, resetting the CPU.
This circuit is composed of EEPROM which stores data and the peripheral circuit.
IC12 is a memory which stores the adjustment values of the inner punch transmission-type optical sensor and the alignment plate position, and it sends/receives data to/from the CPU through the 4wire type serial interface. The data stored once are kept undeleted even when the power is turned OFF.
IC12-1pin (CS) is the chip select pin and is at HIGH level when data are sent or received.
IC12-2pin (SK) is the serial clock pin. Serial data are inputted to this pin and sent in synchronization with the clock.
IC12-3pin (DI) is the serial data input pin, and IC12-4pin (DO) is the serial data output pin.
MX-FNX1/MX-PNX1 ELECTRICAL SECTION 10 – 7
g. Rush current limit circuit
Main unit
Punch position sensor (FPHPD)
Front cover switch (FDSW)
Rear position sensor (FPRPD)
Horizontal shift HP sensor (FPSHPD)
This circuit limits a rush current flowing through the current-regenerating capacitor in the motor drive system to a certain level. It is composed of the posister (PTH2) which limits a current and the
FET (Q3) which flows a current in the steady state.
From when the front cover switch (FDSW) is closed to when the cathode voltage of ZD1 reaches the zener voltage by the time constant of R42 and C14, the base current is not supplied to Q1, turning OFF Q1 and Q3. During this period, a current flows through
PTH2 to charge the current regenerating capacitor.
After the current regenerating capacitor is fully charged, when the cathode voltage of ZD1 exceeds the zener voltage by the time constant of R42 and C14, the base current is supplied to Q1 to turn ON
Q1 and Q3. The current flowing through PTH2 flows through Q3, releasing the current limit operation.
The circuit composed of PTH1 and D1 immediately removes electric charges accumulated in C14 when the front cover switch
(FDSW) is opened. This circuit allows the rush current limit operation for instantaneous open/close of the cover.
B. MX-PNX1A/B/C/D
(1) General
This circuit controls the punch function of paper discharged from the main unit.
It is composed of circuits which process signals from sensors and the inner finisher and the circuit which drives the motors.
(2) Circuit descriptions a. Sensor input circuit
Full sensor (FPDD)
1) Full sensor (FPDD)
The full sensor (FPDD) employs the photo interrupter in which the light emitting diode and the photo transistor are integrated.
The full state is detected by interruption of lights with the lightshielding plate. By use of Q8, the logic when the connector is disconnected is made the same as when light is emitted to the sensor (full).
Signals are inputted through the noise filter of R10 and C2 to the multiplexer (IC9-4pin).
The logic of a signal inputted to the CPU on the inner finisher circuit is fixed to H when the punch dust container is full.
R2 is the current limit resistor of the light emitting diode, and
R6 is the load resistor of the sensor.
2) Punch position sensor (FPHPD)
The punch position sensor (FPHPD) employs the photo interrupter in which the light emitting diode and the photo transistor are integrated.
The full state is detected by interruption of lights with the lightshielding plate. By use of Q9, the logic when the connector is disconnected is made the same as when light is emitted to the sensor (when punching).
Signals are inputted through the noise filter of RA11.2 and C55 in the inner finisher circuit to the CPU (IC10-87pin).
The logic of a signal inputted to the CPU is fixed to H at the home position, and L when punching.
R1 is the current limit resistor of the light emitting diode, and
R97 (in the inner finisher circuit) is the load resistor of the sensor.
3) Rear position sensor (FPRPD)
The rear position sensor (FPRPD) employs the photo interrupter in which the light emitting diode and the photo transistor are integrated.
The rear position is detected by interruption of lights with the light-shielding plate.
Signals are inputted through the noise filter of RA11.3 and C56 in the inner finisher circuit to the CPU (IC10-16pin). The logic of a signal inputted to the CPU is H when light is shielded and
L when light is emitted to the sensor.
R4 is the current limit resistor of the light emitting diode, and
R98 (in the inner finisher circuit) is the load resistor of the sensor.
4) Horizontal shift HP sensor (FPSHPD)
The horizontal shift HP sensor (FPSHPD) employs the photo interrupter in which the light emitting diode and the photo transistor are integrated.
The home position is detected by interruption of lights with the light-shielding plate.
Signals are inputted through the noise filter of RA11.4 and C57 in the inner finisher circuit to the CPU (IC10-17pin). The logic of a signal inputted to the CPU is H when light is shielded and
L when light is emitted to the sensor.
R58 is the current limit resistor of the light emitting diode, and
R99 (in the inner finisher circuit) is the load resistor of the sensor.
MX-FNX1/MX-PNX1 ELECTRICAL SECTION 10 – 8
5) Paper rear edge sensor (FPPEND) and paper horizontal resist sensor (FPPD1 – 6)
This circuit is a transmission-type optical sensor circuit using the LED PWB and the photo transistor PWB.
Paper is detected when the light path is interrupted by paper passing between the photo transistor PWB and the LED PWB.
The light emitting circuit of LED1 – 6 is composed of the CPU (IC10) on the inner finisher circuit, the DA converter (IC11), the multiplexer
(IC7) on the above punch PWB, the operation amplifier (IC10, 11), and the transistors (Q7, 9, 10, 11). The analog signal (DA_COM) and the select signals (A1, B1, C1) are inputted to the multiplexer (IC7-3, 9, 10, 11pin) to select the light emitting circuit. The DA adjustment value outputted from the multiplexer (IC7-1, 5, 12, 13, 14, 15pin) is used to adjust the current flowing through the LED via the operation amplifier and the transistor. R30, 3, 42, 43, 44, 45 are the LED current limit resistors.
The light emitting circuit of YK_LED is composed of the CPU (IC10) on the inner finisher circuit, the DA converter (IC11), the operation amplifier (IC11) on the above punch PWB, and the transistor (Q7). The analog signal (YK_LED_DA : DA adjustment value) adjusts the current flowing through the LED via the operation amplifier and the transistor. R63 is the LED current limit resistor.
The light receiving circuit of B5R, 16K-R, A4R, B4R, LTR-Y, A3 is composed of the CPU (IC10) on the inner finisher circuit, the comparator
(IC9), the multiplexer (IC9) on the above punch PWB, and the operation amplifier (IC12, 13).
The select signal (A1, B1, C1) inputted to the multiplexer (IC9-9, 10, 11pin) is used to select the light receiving circuit. The sensor output is inputted to the multiplexer (IC9-1, 5, 12, 13, 14, 15pin) through the operation amplifier, and the analog signal (AN_COM1) is inputted to the
CPU through the comparator (IC9). R46, 53, 54, 55, 56, and 57 are the load resistors of the photo transistor.
The light receiving circuit of YK_PTR_AN is composed of the CPU (IC10), the comparator (IC9), and the operation amplifier (IC11) on the above punch PWB. The analog signal (YK_PTR_AN) is inputted from the comparator (IC9) through the operation amplifier (IC11) to the
CPU. R65 is the load resistor of the photo transistor. The logic of the signal inputted to the CPU is L when paper is provided.
The threshold voltage of the comparator on the inner finisher circuit is 5V divided with R100 and R101.
MX-FNX1/MX-PNX1 ELECTRICAL SECTION 10 – 9
b. Motor drive circuit
1) Punch horizontal resist motor (FPSM) drive circuit
Punch horizontal resist motor
(FPSM)
Not installed
This circuit controls the punch horizontal resist motor (FPSM) rotation/stop, the rotating direction, and the motor current, and is composed of the CPU (IC10) on the finisher circuit, the DA converter (IC11), and the constant-current chopper type driver IC (IC2) in the above circuit.
The stepping motor drive excitement pattern signal (YI_MOT_PA, PB, EA, EB) outputted from the CPU (IC10-83, 84, 85, 86pin) is used to control the motor rotating speed and the rotating direction.
The analog signal (YI_MOT_REF) outputted from the DA converter (IC11-6pin) is divided to a fixed voltage with R17 and R18. This divided voltage is inputted to IC2-3, 4pin to set the motor current value. The logic of the standby signal (MOT_STY) outputted from the DA converter (IC11-7pin) is H when the motor can be operated.
2) Punch motor (FPNM) drive circuit
Punch motor (FPNM)
This circuit controls the punch motor (FPNM) rotation/stop, and the rotating direction, and is composed of the CPU (IC10) on the finisher circuit and the FET (Q1, 2, 3, 4). The CPU (IC10-98,99,100pin) outputs the punch motor (FPNM) drive forward rotation signal, the reverse rotation signal, and the brake signal to control the DC motor.
MX-FNX1/MX-PNX1 ELECTRICAL SECTION 10 – 10
c. Transmission type sensor circuit
1) LED circuit
This circuit is composed of the paper rear edge sensor
(FPPEND) on the inner punch circuit and the light emitting
(LED) circuit of the paper horizontal resist sensors (FPPD1 –
6) circuit.
Turning ON/OFF of LED1 – 7 are controlled by the paper rear edge sensor (FPPEND) and the paper horizontal resist sensors (FPPD1 – 6) circuit.
2) Photo transistor (PTR) circuit
This circuit is the light receiving (PTR) circuit of the paper rear edge sensor (FPPEND) and the paper horizontal resist sensor
(FPPD1 – 6) circuit on the inner punch circuit. When light is received from the LED, the collector signal flows through PT1
– 7.
MX-FNX1/MX-PNX1 ELECTRICAL SECTION 10 – 11
2. Block diagram
A. MX-FNX1
Main unit
TxD
RxD
DTR
DSR
RESET
TULS
TCKS
JHPS1
JHPS2
ENTS
RUDS
KKBS
JIS
TLLS
TPES
RHDS1
RHDS2
STHPS
EMPS
Inner finisher
Communication circuit
EE
PROM
Sensor
I/O circuit
CPU
Driver circuit
ST
MOT
TRY
MOT
J1
MOT
J2
MOT
RO
MOT
T
MOT
H
MOT
P_SOL
S_SOL
BR_SOL
F_SOL
FAN
Stapler unit
DC+24V
DC+5V
F_SW
DC+5V
DC+24
SW open/close detection circuit
Rush current prevention circuit
5V power interruption circuit
Drawer connector
DC+24
DC+5V
PBA -CONT
Punch unit
MX-FNX1/MX-PNX1 ELECTRICAL SECTION 10 – 12
B. MX-PNX1A/B/C/D
Inner finisher
Punch unit
PBA -PTR
PBA -LED
FULS
PIS
REARS
YHPS
Sensor
I/O circuit
DC+24V
DC+5V
Drawer connector
PBA-PUNCH
Driver circuit
PUN
MOT
Y
MOT
MX-FNX1/MX-PNX1 ELECTRICAL SECTION 10 – 13
D
3. Actual wiring diagram
A. MX-FNX1
8
MX-FNX1
7
C
B
(FULD)
Tray intermediate lower limit sensor
(FMLLD)
(FLLD)
Tray paper empty sensor
(FBED)
Paper surface sensor 1
(FSLD1)
Paper surface sensor 2
(FSLD2)
(FSTHPD)
(FSTPD)
Alignment plate
HP sensor F (FFJHPD)
Alignment plate
HP sensor R (FRJHPD)
A
8
6
7 6
MX-FNX1/MX-PNX1 ELECTRICAL SECTION 10 – 14
5
5
4 3
Adjustment plate position sensor
(FJPD)
2 1
1/1
D
(FFAN)
Stapler shift motor (FSM)
(FTLM)
Alignment motor F (FFJM)
Alignment motor R (FRJM)
Roller upper/lower motor (FSWM)
Bundle exit motor (FAM)
Transport motor (FRM)
C
B
A
4 3 2
MX-FNX1/MX-PNX1 ELECTRICAL SECTION 10 – 15
1
B. MX-PNX1A/B/C/D
MX-FNX1/MX-PNX1 ELECTRICAL SECTION 10 – 16
advertisement
Related manuals
advertisement
Table of contents
- 3 PRODUCT OUTLINE
- 4 SPECIFICTIONS
- 4 1. MX-FNX1
- 4 2. MX-PNX1A/B/C/D
- 6 EXTERNAL VIEW AND INTERNAL STRUCTURE
- 6 1. Identification of each section and functions
- 6 A. Internal structure
- 6 B. Sensors and switches
- 9 C. Motors, solenoids, and PWB
- 11 OPERATIONAL DESCRIPTIONS
- 11 1. Electrical mechanism diagram
- 11 A. Transport, paper exit section
- 12 B. Staple section and aligment section
- 13 C. Paper exit tray section
- 14 D. Punch unit (MX-PNX1A/B/C/D)
- 15 2. General
- 15 3. Outline of the transport path
- 16 4. Non-sort mode
- 16 A. Reception of paper discharged from the main unit
- 16 B. Paper exit
- 16 5. Offset mode
- 16 A. Reception of paper discharged from the main unit
- 16 B. Paper take-up and alignment
- 17 C. Aligned paper exit
- 17 6. Staple mode
- 17 A. Reception of paper discharged from the main unit
- 18 B. Paper take-up, alignment and staple
- 18 C. Aligned and stapled paper exit
- 19 7. Punching process
- 19 A. Reception of paper discharged from the main unit
- 19 B. Punching process 1
- 19 C. Punching process 2
- 20 DISASSEMBLY AND ASSEMBLY
- 20 1. MX-FNX1
- 20 A. Exterior
- 21 B. Transport section, paper exit section
- 25 C. Process tray section
- 26 D. Staple section
- 27 E. Paper exit tray section
- 29 F. Others
- 30 2. MX-PNX1A/B/C/D
- 30 A. Punch unit (MX-PNX1A/B/C/D)
- 33 MAINTENANCE
- 33 1. Maintenance system table
- 34 ADJUSTMENTS
- 34 1. Setting item list
- 34 2. Details
- 36 SELF DIAGNOSTICS AND TROUBLE CODES
- 36 1. Trouble code and troubleshooting
- 36 A. MX-FNX1
- 38 B. MX-PNX1A/B/C/D
- 39 ELECTRICAL SECTION
- 39 1. Circuit descriptions
- 39 A. MX-FNX1
- 46 B. MX-PNX1A/B/C/D
- 50 2. Block diagram
- 50 A. MX-FNX1
- 51 B. MX-PNX1A/B/C/D
- 52 3. Actual wiring diagram
- 52 A. MX-FNX1
- 54 B. MX-PNX1A/B/C/D
- 55 PARTS GUIDE